Benezan Electronics Triple BEAST User manual

Benezan Electronics
Hard- and software development
Triple Beast Installation Guide
Nicolas Benezan, Stauffenbergstr. 26, 72108 Rottenburg
Phone: +49 (0) 7457/946365 0 benezan-electronics.de
Page
TripleBeast+BOB Installation.docx22.09.2020
Triple BEAST
Bene’s Advanced Stepper Drive
3-axis high performance power amplifier
for stepper motors with
integrated interface card
Installation manual
Brief product description
The "Triple BEAST" is a complete stepper motor controller for three axes. All components for the control of a small milling,
engraving or turning machine are integrated in a housing with dimensions of only 100x102x55mm. Only a power supply unit for
the power supply is still required. The effort for mounting, wiring and the possibilities for errors are thus reduced to a minimum.
The Triple BEAST offers all the advantages of the individual BEAST power amplifier at extremely low cost, such as very quiet
motor running with continuous sinusoidal commutation and complete short-circuit and overload protection. Only the maximum
current and the maximum operating voltage are limited to 5A and 55V compared to the "big brother". For applications with 4
axes, or if a more powerful motor is required, a connection option for an additional output stage is available.
Due to high efficiency and a sophisticated thermal concept, only little heat loss is generated, so that despite the small
dimensions, practically no overheating problems occur.

Benezan Electronics
Hard- and software development
Triple Beast Installation Guide
Nicolas Benezan, Stauffenbergstr. 26, 72108 Rottenburg
Phone: +49 (0) 7457/946365 0 benezan-electronics.de
Page
TripleBeast+BOB Installation.docx22.09.2020
Safety Instructions
The Triple-BEAST stepper motor controller may only be installed and commissioned by
qualified personnel. Please read the operating instructions carefully and follow all instructions
exactly. Improper installation or operation of the device can cause damage to the electronics
or the machine and can result in dangers to the health of the operating personnel. The system
manufacturer, who assembles the electronics and other components to form the overall
system, and the system operator are responsible for compliance with the legal regulations.
Caution: Danger to life! Operate the device exclusively with a voltage source isolated
from the mains supply and ensure that the limit values specified in the technical data are observed! Machine, motor and housing
must be grounded according to the regulations. Devices operated with mains voltage must be checked and approved by a
specialist. Make the first tests with disassembled motors or remove drive belts or couplings. This prevents injuries or damage due
to unexpected movements of the machine.
System requirements
To obtain a functional drive system, the following components are required in addition to the Triple-BEAST control:
1. One to three two-phase stepper motors with a rated current between 1.4 and 5A (up to 6A with restrictions). Three- or five-
phase motors or high-impedance motors from printers and disk drives are not suitable.
2. A power supply unit for the voltage supply. with an output voltage between 24 and 55V. Stabilization is not absolutely
necessary. More detailed selection criteria are listed in the chapter0.
3. A signal source for the step and direction signal to control the power amplifier. This can be a PC with appropriate software,
optionally with additional hardware (e.g. smoothstepper).
Recommended motors
The table below lists some recommended combinations with motors from Benezan Electronics. The applications mentioned above
only represent an approximate selection. If you wish a more precise calculation of the drives, please contact Benezan Electronics.
Motor
Type
Dimensions
Phase
current
Operating
voltage
Application
HS56-
0818
56 x 56mm
1,8A
24..48V
Miniature machines, pick & place, cutting and pen plotters
HS56-
1442
56 x 76mm
4,2A
24..48V
Small to medium-sized milling and engraving machines in aluminium
profile design
HS60-
2150
60 x 90mm
5,0A
48..55V
Small to medium-sized milling and engraving machines in aluminium
profile design
HS86-
3263
86 x 78mm
5,0A
48..55V
Milling machines for metal working, larger portal machines, plasma
cutting machines
The Triple BEAST control also works with many motors from other manufacturers. Please make sure, however, to use only
modern hybrid motors that are suitable for microstep operation. The best results and highest dynamics are achieved with motors
with flange sizes from 56 to 60mm and phase currents from 3 to 5A. The operation of larger motors with 86mm flange dimension
is possible, but with restrictions. For motors with 6A rated current the full torque is not reached, because the output stage only
delivers max. 5A. With large motors with 4A rated current, high speeds cannot be achieved due to the high inductance.
If you need high torque and high speed at the same time, it is advisable to use a BEAST single output stage, which allows
higher operating voltage and motor currents up to 10A. If only one motor with higher power is required, for example for a heavy
Z-axis, the combination with Triple-BEAST and single BEAST as 4th axis is possible.

Benezan Electronics
Hard- and software development
Triple Beast Installation Guide
Nicolas Benezan, Stauffenbergstr. 26, 72108 Rottenburg
Phone: +49 (0) 7457/946365 0 benezan-electronics.de
Page
TripleBeast+BOB Installation.docx22.09.2020
Installation
Connections Overview
All terminal numbers are numbered from top to bottom as
shown in the adjacent figure. Reference switch inputs (8-pin
terminal X3, top left)
No.
Description
1
Reference switch X voltage output (+12 or +24V)
2
Reference switch X Signal input
3
Reference switch Y Voltage output (+12 or +24V)
4
Reference switch Y Signal input
5
Reference switch Z voltage output (+12 or +24V)
6
Reference switch Z Signal input
7
Reference switch 4th axis voltage output (+12/24V)
8
Reference switch 4th axis Signal input
Relay outputs
(6-pin terminal X4, bottom left)
No.
Description
1
230V~ L Input
2
230V~ N Input
3
Relay 1 L Output
4
Relay 1 N Output
5
Relay 2 L output
6
Relay 2 N output
Power supply
(2-pole terminal V, right side)
No.
Description
1
Motor voltage input(+24..+55V)
2
Ground 0V
Additional functions
(6-pole terminal X2, top right)
No.
Description
1
Ground 0V for brake
2
Holding brake Output
3
Analog output ground 0V
4
Analog output 0..10V
5
Emergency stop switch Input
6
Emergency stop switch +12V
output
Power supply
(5-pole terminal X1, bottom right)
No.
Description
1
5V output (max. 150mA)
2
Ground 0V
3
12V output (max. 300mA)
4
Ground 0V
5
24V input (15..55V,max.0,3A)
Motor connections
(4-pin terminals M1 to M3, right side)
No.
Description
1
Winding 1
2
3
Winding 2

Benezan Electronics
Hard- and software development
Triple Beast Installation Guide
Nicolas Benezan, Stauffenbergstr. 26, 72108 Rottenburg
Phone: +49 (0) 7457/946365 0 benezan-electronics.de
Page
TripleBeast+BOB Installation.docx22.09.2020
4
Assembly
The output stage is designed for mounting on a 35mm DIN rail ("top-hat rail") in a housing. Protect the unit from flying chips,
dust and cooling water. Damage caused by metal chips or moisture will void the warranty. Hook the controller into the rail with
the motor connections facing up, then press the heat sink firmly onto the rail until it clicks into place. Alternatively, it can also be
fastened from the rear with self-tapping self-tapping self-tapping screws B3.5x10 or spacer bolts on a mounting plate. In this case
the clip for the DIN rail must be removed. Attention - never use a longer screw than the one supplied (M4x16) to screw on the
clip. Otherwise they could damage the power components mounted on the inside of the heat sink.
Since the output stage becomes more or less hot during operation depending on the motor current, the following rules must be
observed during installation:
Make sure that there is free air circulation. The distance to other devices, housing wall, cable ducts, etc. should be at least 2 cm
on all sides.
If possible, the heat sink should be mounted vertically with vertical fins.
For motor currents up to a maximum of 3 x 4.2A, natural convection is sufficient, i.e. a fan is not required if the air circulation
is not obstructed by a housing that is too small.
For motor currents from 3 x 5A or >13A in total, supported cooling with a fan is advisable. A small processor fan for PCs, for
example, can be used for this purpose. A 12V connection is provided for the power supply of the fan (X1 terminals 2+3), which
can supply up to 300mA.
Overheating cannot lead to the destruction of the controller, because an integrated overtemperature protection switches off the
motor current when the maximum temperature is exceeded. Nevertheless, it is advisable not to operate the output stage
permanently at the upper temperature limit, as this will reduce its service life.
Power supply connection
The supply voltage must be between 24 and 55V. For most applications a 48V switch mode power supply is ideal because
these power supplies are small, light, relatively inexpensive and easy to connect. They are also overload-proof and usually have
inrush current limiting and mains filter already integrated.
However, a stabilized power supply is not necessarily required, an unregulated power supply consisting of transformer, rectifier
and filter capacitor is also suitable. Please note, however, that the voltage range must be maintained even with mains and load
fluctuations (usually ±10%). Also make sure you have suitable fuse protection. If necessary, inrush current limitation and an
interference filter may be necessary.
The maximum current with which the power supply unit is loaded is approx. 2/3 of the motor current. However, the continuous
load load is lower in most applications. For the operation of 3 motors with 4A each, for example, a power supply unit with 3 x 4A
x 2/3 = 8A peak current and about 5A continuous load capacity is sufficient. An electrolytic capacitor with about 4700μF at the
power supply output is recommended to keep voltage fluctuations small due to fast load changes.
Connect the positive pole of the power supply unit to terminal "V" connection 1 (on the side, labelled +24..55V) and the
negative pole to connection 2 (labelled GND). Attention, wrong polarity can damage the power amplifier, especially if the
power supply has no fast fuse or current limiter. Never connect or disconnect the supply connection under load. Do not switch
the secondary side of the power supply (DC voltage) with switches or fuses. The resulting arc can cause damage. Only switch
the power supply unit on and off on the primary side (mains AC voltage). The protection should also be provided on the primary
side. Please note that the negative connection (Power Ground) is connected to the heat sink and thus automatically to the housing
(potential earth).
For most applications, the power supply unit that supplies the motor voltage can also be used to supply the PC interface
(terminal X1). Connect the positive pole to X1 terminal 5 and the negative pole to terminal 4. Only if you use inductive proximity
switches with 24V and the motor supply voltage is higher than 24V, an extra 24V power supply unit is required. For details please
refer to the chapter "Limit switches".
Motor connection
When using prefabricated cables for stepper motors from Benezan Electronics the connection of the motors is very easy. Connect
the wires numbered 1..4 to the terminals M1, M2 or M3 marked A to D. Connect the cable lug of the shield connection to the flat
plug next to the terminal. Plug the XLR connector of the motor into the female connector on the other side of the cable - ready.
For motors from other manufacturers you must consult the relevant data sheet to identify the wire colours of the coil
connections. For motors with 4 connections you can also use a continuity tester. Connected terminals belong to the same coil.

Benezan Electronics
Hard- and software development
Triple Beast Installation Guide
Nicolas Benezan, Stauffenbergstr. 26, 72108 Rottenburg
Phone: +49 (0) 7457/946365 0 benezan-electronics.de
Page
TripleBeast+BOB Installation.docx22.09.2020
Connect the terminals of one coil to A and B, the terminals of the other coil to C and D. Interchanging the coils or the connections
of the same coil with each other only changes the direction of rotation, but does not affect the function. Only with crossed
connections (e.g. a coil at A-C or A-D) the motor does not work.
Settings and displays
The Triple-BEAST control has ten so-called piano switches on the left side to select the
operating mode of the power amplifiers and the phase current of the motors. A pressed
switch is switched on (1 = ON, in the picture to the left), in the upper position (in the
picture to the right) it is switched off (0 = OFF).
No.
Description
1
0 = Standard, 1 = Parameter setting via software instead of piano switch
(currently not supported)
2
Waveform: 0 = pure sine, 1 = sine with harmonics
3
Selection of motor current for axis no. 1 (X)(fine adjustment, see small table
below)
4
5
Selection of motor current for axis no. 2 (Y)(fine adjustment)
6
7
Selection of motor current for axis no. 3 (Z)(fine adjustment)
8
9
Microstep resolution: 0 = 1/10 (2000/rev), 1 = 1/5 (1000/rev)
10
Motor current range (rough adjustment): 0 = 1.4..3.2A, 1 = 2.5..5A
Switch No. 10 is used for rough selection of the motor current range for all axes
simultaneously. Simultaneous operation of very small and very large motors is therefore
not possible. Depending on the selected range, the fine adjustment can then be carried out
separately for each motor with the switches 2...8.
Switch No. 2 can be used to adjust the waveform of the motor current. Some motor
types do not have an exact sine wave but a waveform slightly distorted in the direction of a
triangle. The optimal waveform can be determined experimentally, and leads to a reduction
of vibrations in certain speed ranges.
Switch No. 9 is used to select the resolution. In normal position this is 1/10 microstep (corresponds to 2000 steps/revolution for
the standard motor with 200 full steps/revolution). When the switch is held down, it switches to 1/5 microstep (corresponds to
1000 steps/revolution).
While other stepper motor power stages often offer a confusingly large number of possible resolutions, this is not necessary
with the Triple-BEAST. Higher resolutions are usually only used to reduce disturbing jerking caused by single steps, while the
step size is then out of reasonable proportion to the accuracy of the mechanics, is basically useless and only unnecessarily
increases the required clock frequency. The Triple-BEAST power amplifier, on the other hand, does not need a finer subdivision
of the steps, because it is pleasantly quiet even with only 1/5 or 1/10 microstep. No single steps are noticeable because the motor
is driven with a continuous sine wave instead of a staircase function. For example, you can cover the speed range up to 1350/min
with 1/10 microstep at 45kHz clock frequency and still do not have to do without the quiet operation of finer resolution. For even
higher speeds or software that can only manage 20kHz or less, there is the 1/5 setting.

Benezan Electronics
Hard- and software development
Triple Beast Installation Guide
Nicolas Benezan, Stauffenbergstr. 26, 72108 Rottenburg
Phone: +49 (0) 7457/946365 0 benezan-electronics.de
Page
TripleBeast+BOB Installation.docx22.09.2020
Status LEDs
The status displays of the power amplifiers are located on the left side (see picture above right). The different colours or
combinations thereof indicate the following operating states:
LEDs
Lettering
Description
(green)
Running
Motor(s) running, no current reduction
(yellow)
Standby
Motors stand still, current reduction
(red blinking)
Fault Axis...
A single red flashing LED indicates a short circuit, overload or faulty
wiring on the corresponding motor. The other motors and the yellow or
green LED remain active.
(red blinking)
Fault Axis...
If all red LEDs flash simultaneously when the green and yellow LEDs
are switched off, the output stage is overheated. All motors are switched
off.
(yellow/red
alternating)
Fault Axis...
If the yellow and all red LEDs flash alternately, the power stage has been
deactivated due to overvoltage. The cause can be braking energy from the
motors or an incorrectly dimensioned power supply unit.
The LEDs on the upper side indicate the status of the PC interface.
LEDs
Lettering
Description
1 (green)
Power
Power supply ok
2 (green)
Batch pump
Watchdog (charge pump) active
3 (red)
Drive fault
One or more output stages report an error
4 (red)
E-Stop
Emergency stop switch activated or line interrupted
5 (yellow)
Relay 1
Relay 1 switched on (spindle motor)
6 (yellow)
Relay 2
Relay 2 switched on (coolant or suction)
PC connection
The breakout board is connected to the PC with a parallel port cable (SUBD25 male/female). The cable should have all pins
connected through 1:1, especially all ground pins (18..25). The recommended maximum length is 3m.

Benezan Electronics
Hard- and software development
Triple Beast Installation Guide
Nicolas Benezan, Stauffenbergstr. 26, 72108 Rottenburg
Phone: +49 (0) 7457/946365 0 benezan-electronics.de
Page
TripleBeast+BOB Installation.docx22.09.2020
The pin assignment of the LPT port is designed for Mach3, EMC or WinPCNC. When using other programs (e.g. CNC-Profi,
PC-Lathe) an adapter plug may be required to adapt the pin assignment (so-called patch box). Please understand that Benezan
Electronics cannot support every program available on the market. The perfect function is only guaranteed together with Mach3.
The pin assignment is listed in the following table:
No.
Description
No.
Description
1
Spindle, relay1, PWM
14
Cooling, relay 2
2
Direction X
15
Reference switch 4th axis
3
Measure X
16
Watchdog, current reduction
4
Direction Y
17
PWM, current reduction
5
Bar Y
18
Signal ground
6
Direction Z
19
Signal ground
7
Measure Z
20
Signal ground
8
Direction 4th axis
21
Signal ground
9
4th axis cycle
22
Signal ground
10
Reference switch Z
23
Signal ground
11
Emergency stop
24
Signal ground
12
Reference switch Y
25
Signal ground
13
Reference switch X
Some pins have multiple assignments so that the interface can be adapted to different programs. The selection is made by the
jumpers directly next to the SUBD-25 connector. The contact pins are numbered from right 1 to left 11. A jumper always connects
two adjacent pins.
(2-1) If this jumper is inserted, the
watchdog is bridged, i.e. step signals
and relays can always be switched. This
is necessary for control software that
does not support a charge pump or
toggle signal. This has the disadvantage
that unwanted movements or switching
operations are triggered when booting
the PC, if the signals of the LPT port are
undefined, or dongle queries take place.
When the jumper is not inserted, the
watchdog is active and step signals and
relays are only "armed" if the software
outputs a valid charge pump signal.
(9..3) These contacts are jointly used
to configure the PWM signal, the
current reduction and the signal source
for relay 1. The following combinations
are possible:
8-7, 6-5, 4-3: Relay 1 on if
PWM>10%, current reduction
pin 17, PWM on pin 1,
watchdog pin 16
9-8, 7-6, 5-4: relay 1 at pin 1, PWM at pin 17, current reduction pin 16, no watchdog (1-2 bridges)
7-6, 5-4: relay 1 at pin 1, PWM at pin 17, no current reduction, watchdog pin 16
8-7, 5-4: relay at pin 1, no PWM, current reduction pin 17, watchdog pin 16
(16..12) These jumpers are used to set the supply voltage for the limit switches and to enable the fourth axis (see below)

Benezan Electronics
Hard- and software development
Triple Beast Installation Guide
Nicolas Benezan, Stauffenbergstr. 26, 72108 Rottenburg
Phone: +49 (0) 7457/946365 0 benezan-electronics.de
Page
TripleBeast+BOB Installation.docx22.09.2020
Reference switch inputs
Up to 4 switches or inductive sensors can be connected. If the 4th axis is not used or does not require a reference switch, a tool
length sensor can also be connected here, for example.
Mechanical switches or inductive proximity switches of the PNP type can be used. For mechanical switches the jumper 14-13
must be plugged in. In this case, the supply voltage at X1 is arbitrary (15..55V). A common power supply unit can be used for the
motor output stages.
If proximity switches are used, the jumper 13-12 must be plugged in and the supply voltage at X1 must be 24V. If the motor
voltage is higher, two separate power supplies are required. The sensors should be connected as follows: brown (+24V) to
terminal 1, 3, 5 or 7, blue to the ground connection of the power supply, black (signal) to terminal 2, 4, 6 or 8.
The inputs are inverting, i.e. the corresponding LPT pin is high when the switch input is open (low) and low when the switch
input is closed (high). Normally closed or normally open contacts can be used if the polarity is selected accordingly in the PC
software.
The switch inputs have a Schmitt trigger function and are interference suppressed with a low-pass filter, so that there is usually no
need to fear interference even with unshielded cables.
Additional functions
An emergency stop button and optionally a holding brake (Z-axis) and the speed signal for a frequency inverter are connected to
terminal X2.
Emergency stop
The PC interface has several independent functions that serve to stop the machine in case of problems:
1. An emergency stop button (mushroom/panic button) must be connected to terminals X2.5 and X2.6. If the contact is
opened, relays 1 and 2 are forcibly switched off. A push-button emergency stop is indicated by LED No. 4 (red, see
figure page 6). Additionally an emergency stop is reported to the PC (LPT pin 11)
2. If the status output of one or more output stages reports an error or if this line is interrupted, an emergency stop signal is
sent to the PC. The power stage error is indicated by LED No. 3 (red). For the three internal power amplifiers there are
additional status LEDs on the left side.
3. In case of an emergency stop (no matter if mushroom button or status error) the relay for the holding brake is switched
off, so that the mechanical brake is blocked (if present).
4. If the watchdog is active (jumper 1-2 not plugged in), relay outputs and step signals are only enabled if a valid watchdog
signal is detected.
Speed control (analog output)
In order to be able to specify the speed for a frequency inverter, the control system has an analog output 0..10V. A voltage
proportional to the duty cycle of the PWM signal (PWM = pulse width modulation) is output at pin 1 or 17 of the LPT port. Here
0% (low) corresponds to a voltage of 0V, 10% corresponds to 1V, 20% corresponds to 2V etc. up to 100% and 10V.
The frequency of the PWM signal (PWM base frequency) should be at least 45Hz so that the ripple of the analog signal is not
too high. At Mach3 this allows a resolution of 10 bit at 45kHz kernel speed.
If all functions of the controller are needed at the same time, the number of available LPT pins will be limited. Therefore it is
possible not to switch relay 1 via an extra pin, but always when the analog signal is higher than 1V (see jumper page 7). This
means that only a single, common pin is required for speed and spindle start. The minimum pulse width should be set to 10% in
this case.
Holding brake
When using ball screws, smooth-running servomotors or very heavy Z-axes, an electromechanical holding brake must be provided
to prevent the vertical axis from moving down by itself when the drive is switched off. Such brakes are usually operated with 24V.
They are blocked when no voltage is applied and open when the voltage is switched on.
The breakout board has a relay output for such a holding brake. The brake is always switched on (released) when the power
supply is switched on and no emergency stop is active and no output stage reports an error.
The output has an integrated free-wheeling diode and is suitable for switching inductive loads. If the brake is to be operated
pneumatically, hydraulically or with a voltage other than 24V, an external contactor or solenoid valve is required. The output
voltage of the brake at X2 is always equal to the operating voltage at X1, i.e. if the motor supply voltage is greater than 24V, two
separate power supplies are required.

Benezan Electronics
Hard- and software development
Triple Beast Installation Guide
Nicolas Benezan, Stauffenbergstr. 26, 72108 Rottenburg
Phone: +49 (0) 7457/946365 0 benezan-electronics.de
Page
TripleBeast+BOB Installation.docx22.09.2020
Connection for 4th axis
An external power amplifier for a 4th axis can be connected to the RJ45 socket on the upper side. This can be a single BEAST, a
UHU or stepper motor output stage or a servo controller from another manufacturer. For BEAST or UHU a simple patch cable can
be used. When connecting external power amplifiers the following pin assignment applies:
No.
Description
1
Current reduction
2
Signal ground
3
Clock
4
+5V
5
Direction
6
+5V
7
Status (0=ok, 1=error)
8
Signal ground
If the output stage does not provide a status signal, pins 7-8 must be bridged or jumper 15-16 must remain plugged in. For BEAST
or UHU with status signal it should be disconnected.
Commissioning and troubleshooting
If you are using the control unit for the first time, please check the following points again before switching it on:
Are all terminal blocks correctly aligned in the slots?
Is the power supply (24 to 55V=) correctly connected (terminal X1 on top and terminal V on the right)?
If the supply voltage is higher than 28V, jumper JP3 must be set to position 13-14 (limit switch supply 12V).
Is the emergency stop switch connected? For test purposes only, a jumper may be connected between pins 5 and 6 of X2
as an alternative. An emergency stop switch is legally required on a machine.
Check again whether the setting of the remaining jumpers matches the pin assignment of your control software.
If these conditions are met, you can connect to the PC, switch on the supply voltage and start the control software. After activating
the software (at Mach3 you have to press the reset button) the state of the LED lights should be as follows
the two green LEDs "Power" and "Charge Pump" must light up,
the two red LEDs "Drive Fault" and "E-Stop" must be off
the two yellow LEDs Relay 1 and Relay 2 must be off.
If this is not the case, please refer to the chapter "Troubleshooting" below. If everything is in order, you can now check the
movement of the motors and the function of the relays and switches.

Benezan Electronics
Hard- and software development
Triple Beast Installation Guide
Nicolas Benezan, Stauffenbergstr. 26, 72108 Rottenburg
Phone: +49 (0) 7457/946365 0 benezan-electronics.de
Page
TripleBeast+BOB Installation.docx22.09.2020
Troubleshooting
The following table gives an overview of the most common errors and the possible causes.
No.
Symptom
Cause
1
LED "Power" (green) is not lit
Power supply (terminal X1 and terminal V on the right) not
connected or wrongly polarized.
2
LED "Charge Pump" (green) is
not lit
At pin 16 of the LPT port a square wave signal with >=10kHz
must be output. If the software does not support this, jumpers 1-2
must be inserted.
3
LED "Drive Fault" (red top) is
on, LEDs "Fault Axis 1-3" (red
side) are off
Jumper 15-16 is missing, the 4th axis is not (correctly) connected
or switched off
4
LED "Drive Fault" (red top)
lights up, LEDs "Fault Axis 1-3"
(red side) flash
One or more output stages report an error (overheating or short
circuit, see page 6)
5
LED "E-Stop" (red) lights up,
LED "Standby" (yellow) flashes
The emergency stop switch (X2 Pin 5 and 6) is not connected or
pressed.
6
Relays do not switch
a) yellow LEDs light up, but relays do not switch: see 5
b) yellow LEDs do not light up: Jumper incorrectly inserted or
software pin assignment not configured correctly
7
Motors do not turn
a) green LED "ChargePump" is not lit: see 2
b) Step/direction pins reversed? (LPT pins 2,4,6,8 = direction, pins
3,5,7,9 = step)
8
Frequency converter Speed
fluctuates
PWM frequency (base freq.) too low, min. 45Hz
9
No function of the emergency
stop signal (LPT pin 11)
Pin 11 must be configured as "active low" in the software, LED
"Drive Fault" (see 3) and "E-Stop" (see 4) must be off.
10
In case of "Reset" or emergency
stop the motors take one step
Polarity of step signal wrong (inverted)

Benezan Electronics
Hard- and software development
Triple Beast Installation Guide
Nicolas Benezan, Stauffenbergstr. 26, 72108 Rottenburg
Phone: +49 (0) 7457/946365 0 benezan-electronics.de
Page
TripleBeast+BOB Installation.docx22.09.2020
Configuration of the software
Example configuration Mach3
The pictures on the left show the
settings for the standard configuration
(jumpers 3-4, 5-6 and 7-8 inserted).
Further settings
XHome Pin 13
YHome Pin 12
ZHome Pin 10
AHome or length sensor
(sample) Pin 15
RelayControl:M3 and M4 →
Output#1M7 and M8 →
Output#2
Motor Control: √ Use
Spindle Motor Output √
PWM ControlPWM Base
Freq. = 45Minimum PWM =
10%
At Mach3 the pins for step and direction signals can be swapped as desired. This makes it possible to use the external, fourth axis
also as X, Y or Z, which is advantageous, for example, if the Z axis is particularly heavy and therefore requires more drive power.
Other control software
The TripleBeast also works well with NCdrive, EMC², WinPCNC and other CNC programs. For reasons of space, we will not go
into the configuration of this software here. If you have difficulties, please ask your dealer or Benezan Eectronics.

Benezan Electronics
Hard- and software development
Triple Beast Installation Guide
Nicolas Benezan, Stauffenbergstr. 26, 72108 Rottenburg
Phone: +49 (0) 7457/946365 0 benezan-electronics.de
Page
TripleBeast+BOB Installation.docx22.09.2020
Technical data
Absolute limit values
The following parameters must not be exceeded under any circumstances to prevent damage to the device:
Parameters
min.
max.
Unit
Operating voltage
-0.5
+63
V
Storage temperature
-40
+85
°C
Ambient temperature during operation
-20
+70
°C
Voltage at PC connection (SUBD25)
-0.5
+5.5
V
Voltage at limit switch inputs
-5
+63
V
Voltage at the relay terminals
30
Vdc
250
Vac
Current per relay contact (X4)
8
Aeff
Current at brake relay (X2)
5
A
Current at analog output 0..10V
20
mA
Electrical connection values
Parameters
min.
max.
Unit
Operating voltage
+24
55
V
Power consumption without motors
80
mA
12V output max. load
300
mA
5V output max. load
200
mA
Ambient temperature
0
+50
°C
Level logical 0 for signal inputs
-0.5
+0.8
V
Level logic 1 for signal inputs
2.5
+5.5
V
Current consumption signal inputs at 0..5V
0
1
mA
Pulse width for step signal
2
µs
Setup time Direction signal valid until step1
2
µs
Hold time Step to direction signal Change
2
µs
Level logical 0 for status output
0.8
V
Level logical 1 for status output
3
V
Crotch frequency
0
200
kHz
Watchdog (Charge pump) Frequency
10
100
kHz
Delay time automatic current reduction
0.5
0.7
s
Threshold over temperature
70
85
°C
Current control accuracy
-10
+10
%
Cable cross section for terminals Supply
0.5
2.5
mm²
Cable cross section for terminals Motor
0.22
1
mm²
Number of microsteps per full step
5
10
-
Microsteps/revolution for standard motor1
1000
2000
-
1Step is executed on rising edge, i.e. transition from logical 0 to logical 1
1Standard motor: 1.8°/full step, 200 full steps/revolution
Other manuals for Triple BEAST
1
Table of contents
Other Benezan Electronics Control Unit manuals
Popular Control Unit manuals by other brands
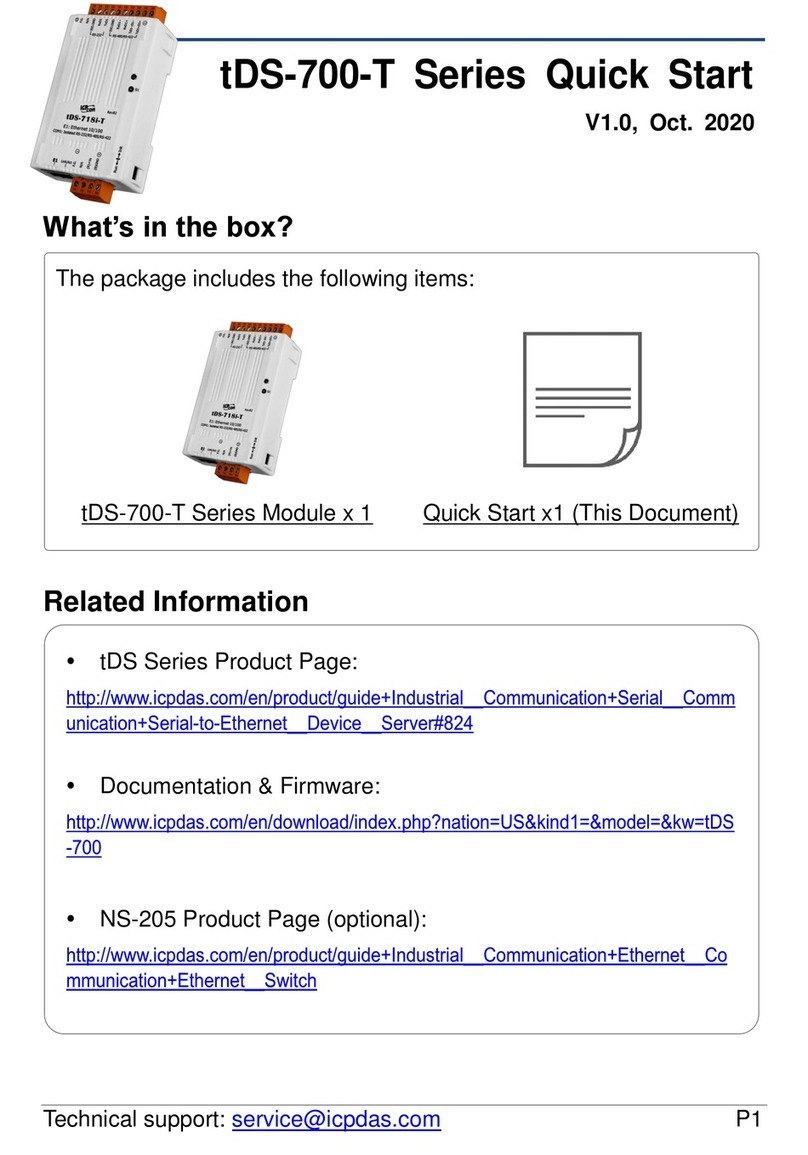
ICP DAS USA
ICP DAS USA tDS-700-T Series quick start
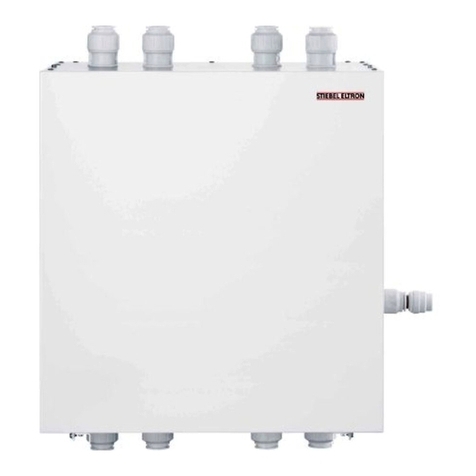
STIEBEL ELTRON
STIEBEL ELTRON WPAC 1 installation instructions
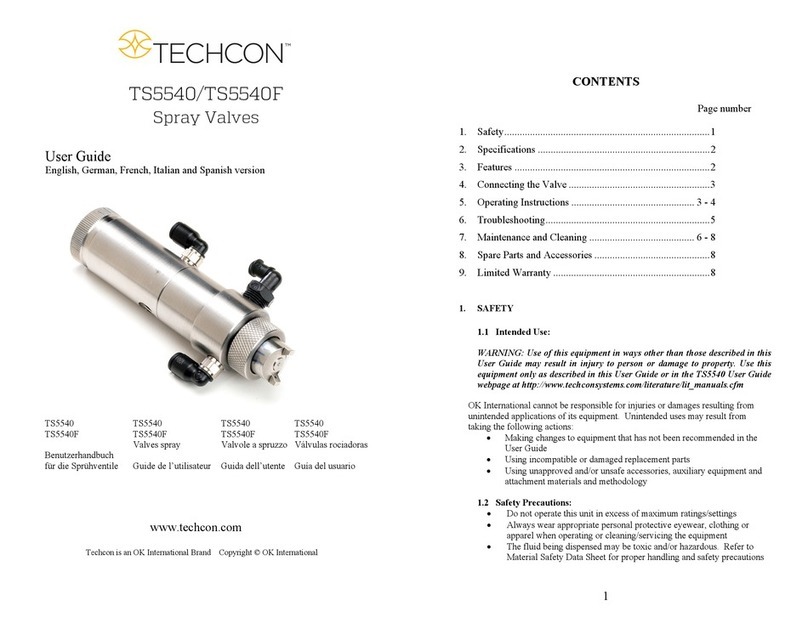
TECHCON
TECHCON TS5540 user guide
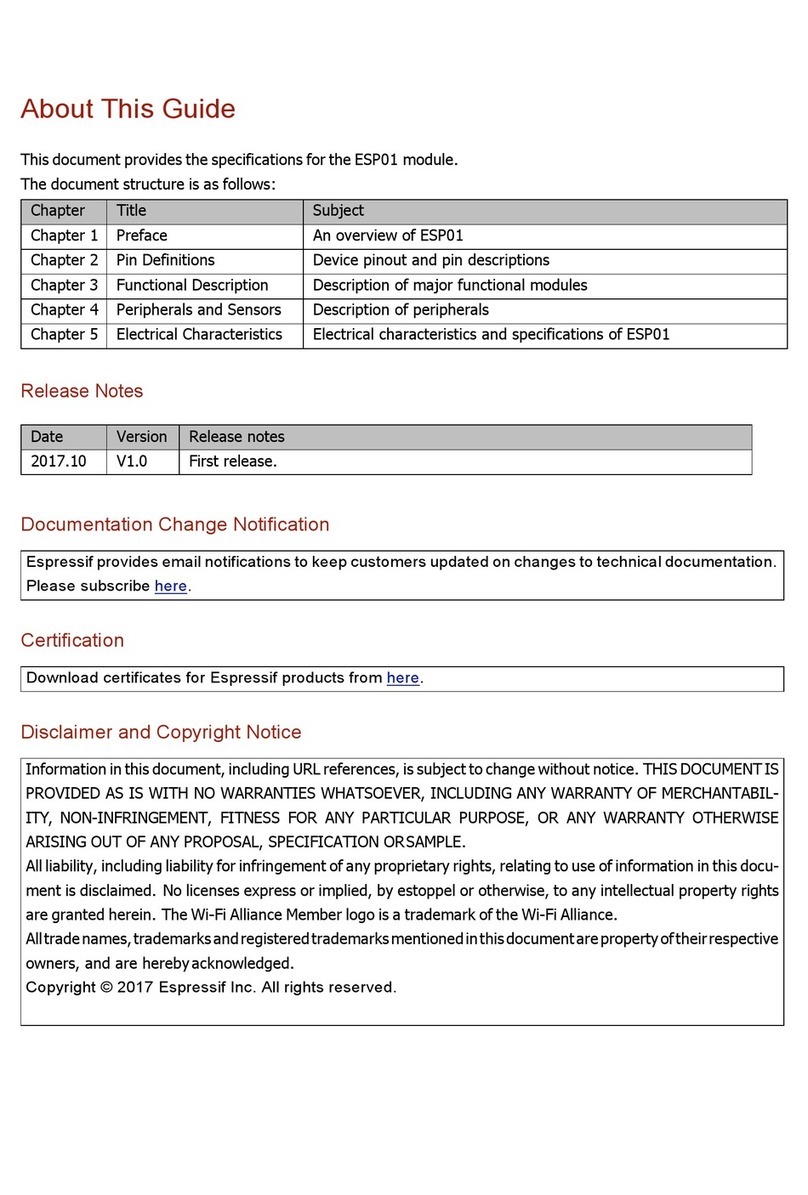
Espressif
Espressif ESP01 quick start guide

Telit Wireless Solutions
Telit Wireless Solutions GE864-QUAD V2 Hardware user's guide
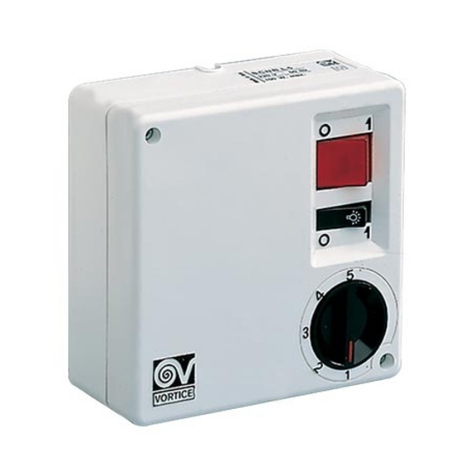
Vortice
Vortice SCNRL5 Instruction booklet