Bernard Controls AT LOGIC v2 User guide

AT LOGIC v2
RANGE
Start Up Guide
SUG_17011_EN - Ind. E
Art: 5100582


English
3
TABLE OF CONTENTS
DEFINITIONS---------------------------------------------------------- 5
1SAFETY ---------------------------------------------------------- 6
2PACKAGING, STORAGE AND MAINTENANCE----------------- 6
2.1 Packaging
2.2 Storage
2.3 Maintenance
3ACTUATOR INSTALLATION ------------------------------------ 8
3.1 Mounting the actuator on the valve
3.2 Opening the control compartment
3.3 Electrical wiring
3.4 Closing the control compartment
3.5 Wiring the external ground terminal
4ACTUATOR CONTROLS----------------------------------------15
4.1 Control panel
4.2 Control modes
4.3 Local control with the Control panel
4.4 Local control with the Smartphone application
4.5 Remote controls
4.6 Analog Input/Output (OPTION)
5COMMISSIONING -----------------------------------------------23
5.1 Setting the display language
5.2 Valve tags
5.3 Actuator Commissioning setting
5.4 Setting the buttons and display
5.5 Setting Remote commands

English
4
5.6 Setting the Analog Input/Output function (OPTION)
5.7 Setting the Relays configuration
5.8 Setting the forced local mode with BC App
6OPERATION ----------------------------------------------------63
6.1 Emergency Manual Command
6.2 Local control operation
APPENDIX ------------------------------------------------------------64
I. Starting with BC App
II. Alarms and Settings menu tree (options not detailed)
III. Diagnostic and Alarms list
IV. Factory data menu tree

English
5
DEFINITIONS
Tip or info.
Warning requiring a check and/or a compulsory action.
!
Warning requiring a check and/or a compulsory action on
the device because of risks of damages for the device or
danger for the staff working on the device.

English
6
1SAFETY
This device complies with current applicable safety standards.
The installation, maintenance, and use of this unit require a skilled
and trained personnel.
Please carefully read this whole document before mounting and
powering the actuator.
2PACKAGING, STORAGE AND MAINTENANCE
2.1 Packaging
The AT actuator packaging is comprised of a corrugated, double wall
cardboard box strapped on a pallet. For certain non-EU countries or
upon request, the pallets are heat treated to the NIMP 15 standard
and IPPC-stamped.
This packaging is identical for shipping by road, air or sea, unless
otherwise mentioned in the contract.
2.1.1 Check identification sticker
The information on the nameplate sticker on the side of the actuator
should match your order.
The QR code on this sticker can be used to identify the actuator.
2.2 Storage
Actuators should be stored under a shelter, in a clean and dry place,
and at a stable ambient temperature.
•Avoid placing the actuator directly on the floor.
•Check that the cable entry plugs are correctly tightened.
•Check that the cover screws are correctly tightened to ensure
weatherproof sealing of the cover.
AT actuators include electrical components and lubricated gears. If
the actuator is incorrectly stored, regardless of its weatherproof
enclosure, alterations may occur, such as oxidation, galling, and
other.
The heating resistance should be connected to the power supply,
especially if the storage place is wet.

English
7
What to check before mounting on the valve, after storage
1. Visually check the electrical equipment for traces of
corrosion, humidity, etc.
2. Check that there are no oil leaks.
3. Manually operate buttons, selectors, etc., to ensure proper
mechanical functionality.
4. Manually operate the actuator in both directions for a couple
of turns.
What to check on pre-installed actuators
If you expect a long delay between actuator valve mounting and
electrical wiring, visually check that the cable entries and cover are
tightly closed.
2.3 Maintenance
All AT actuators feature lifetime lubrication. They require no
specific maintenance under the condition that they were correctly
commissioned and operated under their intended use.

English
8
3ACTUATOR INSTALLATION
3.1 Mounting the actuator on the valve
The actuator should be secured directly to the valve using proper
bolts or via a proper interface.
After assembly, the actuator can operate in any position.
If needed, the orientation of the display can be modified to keep a
normal reading orientation (see §5.4.3).
3.2 Opening the control compartment
Open the control compartment and remove the cover in order to wire
the actuator.
When opening the compartment, unplug the control panel cable
from the main board in order to avoid damaging it.
How to remove the cover
1. With a 10 mm angled
socket wrench or flat-
blade screwdriver,
unscrew the 4 screws
securing the cover to
the housing.
2. Pull out the cover
along its axis.
3. When the cover plug is
accessible, unplug it
from the main board.
4. Remove the cover completely.
However:
•Do not lift or handle the actuator by its handwheel to avoid shaft
and gear damage.
•Cable glands must not be oriented upwards (loss of
watertightness).
•It is recommended not to position the motor downwards.

English
9
3.3 Electrical wiring
3.3.1 Components (with cover open)
1–Terminal block for control
2–Push-on connectors for power
3–External ground terminal
4–Internal ground terminal
5–Cable entries
6–Main board
7–4-Relay board (OPTION)
8 –AI/AO board (OPTION)
9 –Bus board (OPTION)
10 –Modular reduction gear
The control panel board is attached to the actuator cover.
!
Do not supply the wires with electrical power before the wiring is
finished and the control compartment is closed.
Make sure to cut off the actuator’s power supply when opening the
control compartment.
1
2
3
4
5
6
7
10
8
9

English
10
3.3.2 Installing the cable glands
AT actuators are fitted with 2×M16 and 3×M20 cable entries.
How to install the cable glands
For each cable entry used
1. Remove the plug from the cable
entry with a 19 mm (M16 entry) or
23 mm (M20 entry) open-end
wrench.
2. Separate the sealing nut from its
cable gland.
3. Screw and tighten the cable gland
into the cable entry.
4. Insert the sealing nut on the cable
and pass the cable through the cable gland.
3.3.3 Wiring power and control cables
Terminal board
On a side of the electronics
assembly there are:
•a screw terminal block to
connect command and
signaling (A).
•3 push-on connectors to
connect the power supply
(B).
Control terminals: 1-36
Power connectors (3Ph/1Ph)
•3Ph: L1, L2, L3 with phase
correction
•1Ph: L (Live), N (Neutral)
Unused entries must be kept closed using plugs as they are part of
the components allowing the actuator to be rated with IP68
protection.
B
A

English
11
Internal ground terminal
The ground terminal is a tapered hole in the plate, located under
the terminal board at its left.
How to wire the actuator
The wiring must be done according to the wiring diagram of the
actuator.
1. Make sure that the power supply voltage matches the
information on the nameplate located on the side of the
actuator.
2. Separate the female part of the push-on connector from the
male part which is fixed to the board.
3. Using a crimping tool, connect the power supply to the female
push-on connectors.
4. Place back the female connectors on the male connectors
marked L1, L2 & L3 (3Ph) or L, N (1Ph), depending on the
power supply phase.
5. Using a crimping tool, attach the end of the ground cable to
the ring lug
6. Using a 4 mm hex key, secure the ground cable to the ground
terminal.
7. Using a 3×0.5 mm flat-blade screwdriver, connect the control
and signaling wires to terminals 1 to 36.
8. Tighten the sealing nut on the cable gland when the wiring is
complete.
9. Make sure that all cable glands are correctly tightened.

English
12
3.3.4 Power supply board
The power supply board
supplies the actuator with
electrical power.
The power characteristics
are factory set according to
the order.
Fuse
There is a fuse at the upper left angle of the board (see picture
above).
Its characteristics are as follows:
Fuse current
500 mA
Fuse size (mm)
(inches)
6.3×32
¼’’×1-¼’’
Voltage rating VAC
500 V
Blow characteristic
Fast acting
Breaking current capacity current AC
1 kA
3.3.5 Relays
The AT Logic is equipped with a Fault relay and 3 signaling relays.
See list of Fault relay Alarms in Appendix III. This list
cannot be modified.
Customizable relays
Out of the 3 signaling relays, one is customizable. A 4-Relay board
can be added as an option (each relay is customizable).
To see possible settings and set relays, see §5.7.

English
13
3.3.6 Positioner board (OPTION)
The positioner board is
assembled on the main board.
It is possible to pick between mA
and Vusing the small switch at
the base of the board.
3.3.7 Heating resistance
Each actuator includes a heating resistance.
As soon as the actuator is installed in the field, it is required to
supply the resistance to prevent condensation.
•Immediately put the cover back in place after installation and
make sure that its seal is clean. Never leave the actuator’s
electrical components without their protection cover.
In case of water intrusion:
•Dry the electrical components before putting back the cover.
•Check the electrical insulation.

English
14
3.4 Closing the control compartment
Make sure to re-plug the cover wire on the mainboard, otherwise
the control panel (see §4.1) will not work.
How to close the electrical compartment
1. Plug the cover wire on the mainboard.
1. Put back the cover, making sure that the screen is correctly
oriented for operation, and place it on the housing.
2. With a 10 mm angled socket wrench or flat-blade
screwdriver, secure the cover to the housing with the
4 screws.
3.5 Wiring the external ground terminal
1. Crimp the end of the ground cable with a
6 mm ring lug.
2. Using a 5 mm Allen key, fix the ground
cable on the housing next to the cable
entries (see image opposite).

English
15
4ACTUATOR CONTROLS
4.1 Control panel
The AT LOGIC control panel consists of a screen, 2 control knobs, 1
control selection knob and 2 configurable LEDs.
Screen
The screen displays operating status or LOGIC menu
Control
selection
knob
The control selection knob allows to choose the one of the
following control modes:
•Local: the actuator is controlled using this Control
panel, or with a Smartphone via Bluetooth®
•Remote: the actuator is controlled remotely
•OFF: the controls are deactivated
The actuator is set to Local at startup.
The control mode can be locked with an optional padlock
at the bottom of the control panel.
Knobs
The knobs are used for operation (upper function) or
menu navigation (lower function). Once released, these
knobs return to the center position.
LEDs
The LEDs indicate the actuator status (CLOSED or OPEN
).
Default colors are red for CLOSED and green for OPEN.
They can be set according to the country’s standard (see
§5.4.4).
One LED will blink during operation according to the travel
direction, and both during Bluetooth® connection.
Display
Open / close &
navigation knob
LED 1 (green)
LED 2 (red)
Stop &
validation knob
Control mode
selection knob

English
16
4.2 Control modes
AT LOGIC can be locally or remotely controlled.
The control mode is set using the Control
selection knob on the control panel. It can be
locked using a padlock located at the bottom of
the control panel.
Modes are:
•Local mode with the control panel or with Smartphone via
Bluetooth® connection
•Remote mode
•Forced local mode when in Remote mode using the Application
➔This mode first needs to be authorized, see §5.8.
4.3 Local control with the Control panel
4.3.1 Operation
Operation screen indicates…
•Top: actuator ID and status icons
: warning / : alarm
: Bluetooth® activated
: Bluetooth® activated with device
connected
: Local command inhibited
•Center: current position of the valve,
either CLOSED, current percentage
between 0 and 100% depending on
the travel direction, or OPEN
•Bottom: torque level with a torque
gauge and an arrow marker to
indicate the set torque limit
Knobs use
Minimum pulse duration is 100 ms.
Left
knob
STOP
STOP
Opening
Closing
Right
knob

English
17
4.3.2 Menu
The Menu screen has 2 main sections:
-Diagnostic and Alarms
-Settings
The Menu screen has 2 main sections:
•Diagnostic and Alarms
•Settings is used to check or change
the actuator’s settings: valve tag,
password, torque limits, Bluetooth®,
etc.
The Factory data submenu contains
the actuator’s characteristics (see
Appendix IV).
How to use the knobs
Left
knob
Menu navigation
Right
knob
ESC
OK
(up)
(down)
Edition
(1 digit left)
➔(1 digit right)
−(decrease values)
+(increase values)

English
18
4.4 Local control with the Smartphone application
Using the Bluetooth® connection of the actuator, it can be operated
with the Bernard Controls smartphone application (BC App).
The application needs to be downloaded and installed on a phone to
connect to the actuator by entering an access code.
See Appendix I for preliminary steps.
4.4.1 Operation screen
Before operation
During operation
Status screen indicates:
•Top:
1. Access to main menu
2. Alternately valve tag and mainboard
reference, or control mode
3. Warnings or alarms (if any)
•Center: current position of the valve,
either CLOSED, opening percentage
between 0 and 100%, or OPEN.
The following functions are used to
operate the actuator:
−decreases / +increases the opening
target with one or several taps
closes / opens the valve
Only with the Positioner option:
<> drag to define the target position on
the dial
•Bottom: torque level with a torque gauge
•Bluetooth®is active on the actuator at delivery.
•Using the Local controls with BC App requires to have
Bluetooth® activated on your smartphone

English
19
4.4.2 Main menu
You can access the main menu anytime by tapping on .
The Main Menu has 3 main sections:
•Actuator
-Operate: actuator operation
-Diagnostic & status: status and
alarms used
-Settings: actuator settings
-Quit Actuator
•Account: account data
•Assistance: assistance information
4.4.3 Settings screen
From the main menu, you can access the settings.
The Settings Menu has 2 main sections:
•Top Section: access to main menu, then
valve tag and mainboard reference
•Settings list:
•Valve identification
•Commissioning of valve
•Inputs / Outputs / Bus
•Actuator local settings
•Access code definition
•Reset to factory data

English
20
4.5 Remote controls
The AT LOGIC remote control system can be operated using an
external or internal voltage supply.
The input circuits are fully opto-isolated. The pulse command system
requires 4 connecting wires on the client terminal strip: Common,
STOP, OPEN, CLOSE. If the STOP local command button is not used,
do not connect the STOP wire. The OPEN (or CLOSE) contact must be
maintained to operate the actuator.
4.5.1 Single switch control (Dry Contact)
The actuator can be controlled via a single external switch.
Opening
Closing
O: Open
C: Close
•Switch closed: valve opens
•Switch open: valve closes
•Switch closed: valve closes
•Switch open: valve opens
The actuator must be configured for the priority type
required (open or close), see §5.5.3.
Table of contents
Popular Range manuals by other brands
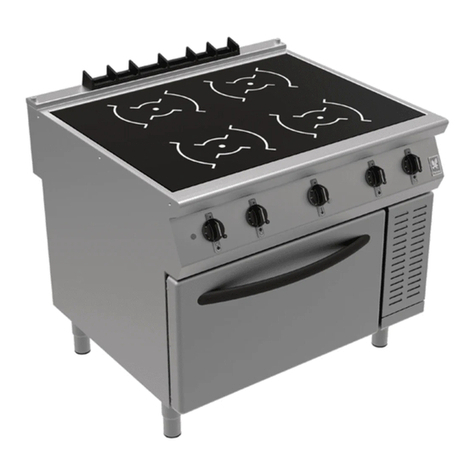
Falcon
Falcon i91104C User, installation and servicing instructions
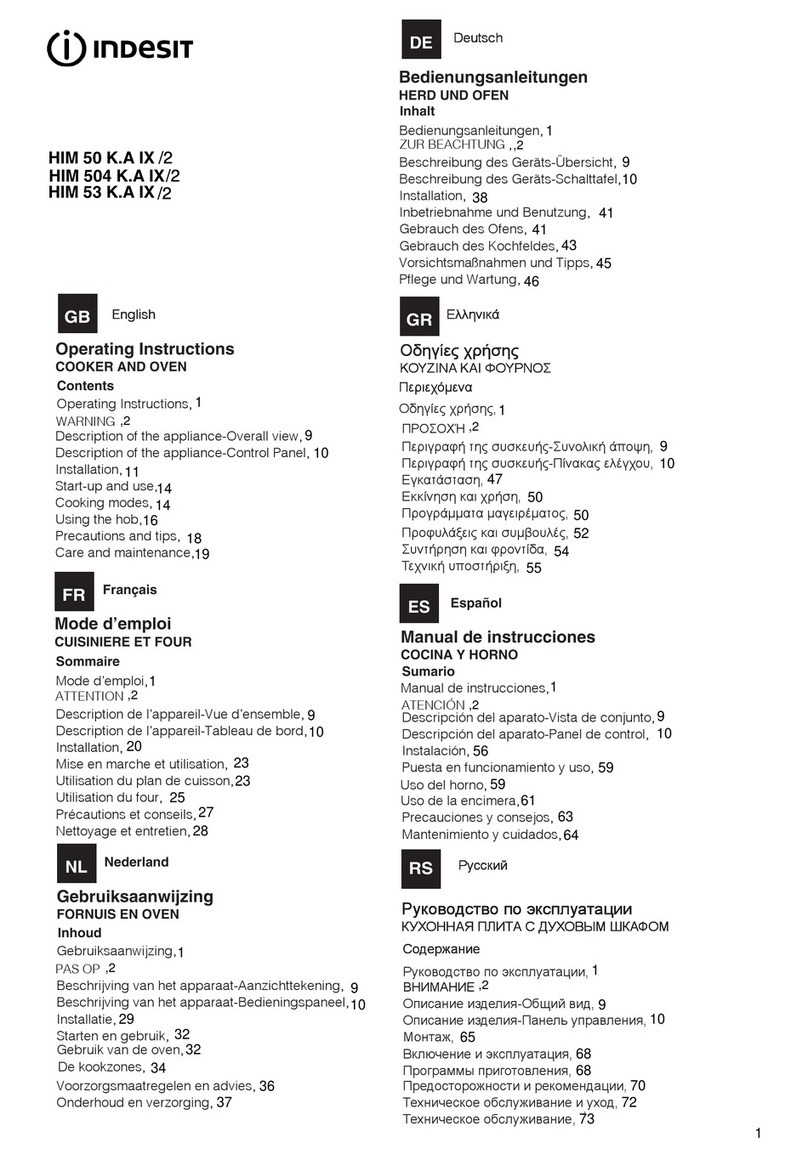
Indesit
Indesit HIM 50 K.A IX/2 operating instructions
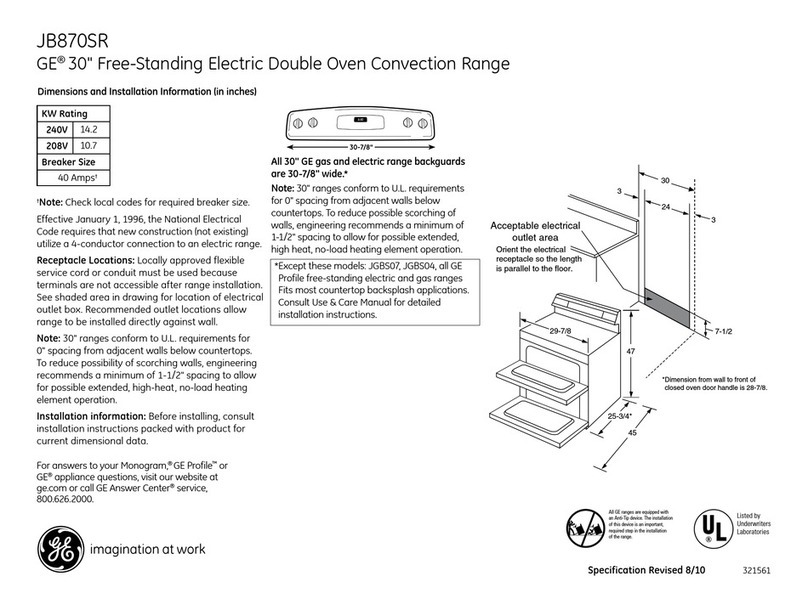
GE
GE JB870SRSS Dimensions and installation information

Frigidaire
Frigidaire Gallery Professional Series owner's guide
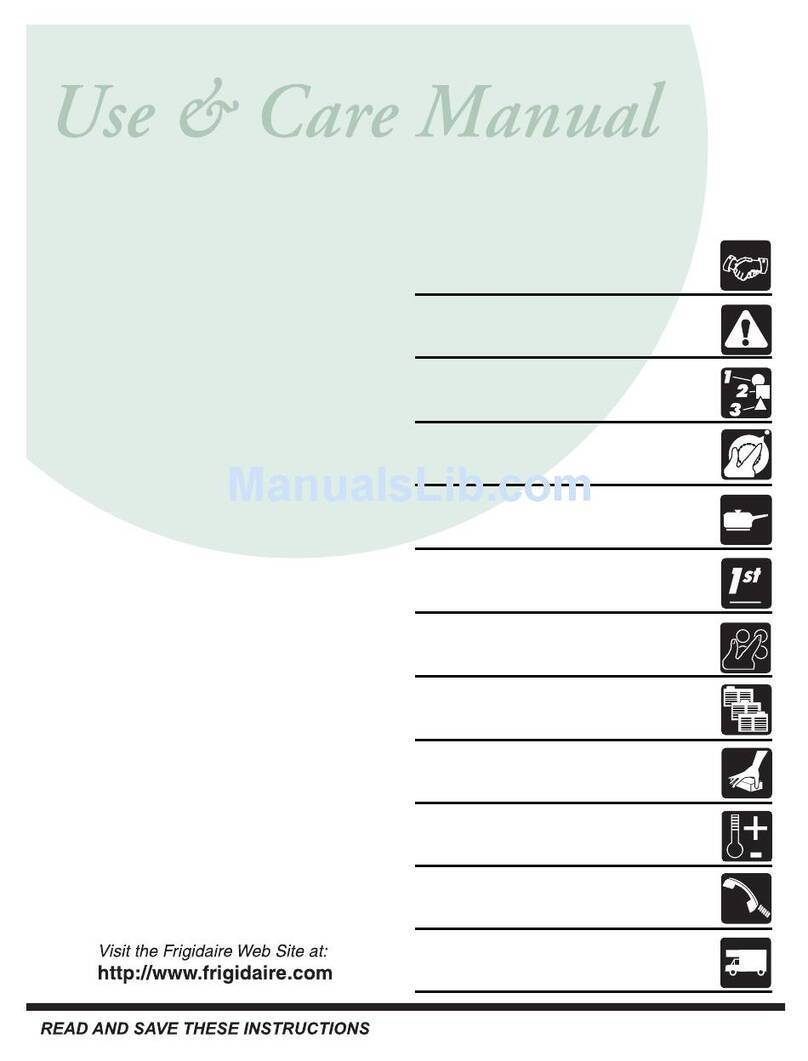
Frigidaire
Frigidaire 30" ELECTRIC DROP-IN RANGE Use & care manual

Whirlpool
Whirlpool SF195LEK Use and care guide