Bioprom MPT-AIR BIO PID User manual

OPERATION MANUAL FOR
AIR BIO PID
ELECTRONIC CONTROL UNIT FOR
SOLID FUEL BOILER

2
CONTENTS
1 Introduction ....................................................................................................................4
1.1 Product purpose and delivery set.................................................................................4
1.2 Installation requirements.............................................................................................4
2 Description and operation ..............................................................................................8
2.1 Description of the controller components and control elements.................................8
2.2 Main display view and description..............................................................................8
2.3 Boiler temperature setting ...........................................................................................9
2.4 Boiler temperature adjustment (hot water supply)....................................................10
2.5 Work priority selection..............................................................................................11
3 User menu.....................................................................................................................12
3.1 Burner startup............................................................................................................13
3.2 Shutdown...................................................................................................................13
3.3 PID mode setting up..................................................................................................13
3.3.1 Internal screw operation setting up ........................................................................14
3.3.2 Fuel delivery parameter setting up.........................................................................15
3.3.3 Fan adjustment........................................................................................................16
3.3.4 Burner cleanup setting up.......................................................................................17
3.3.5 Start/stop mode setting up......................................................................................17
3.4 Date/time ...................................................................................................................18
3.5 Manual control...........................................................................................................19
4. Service menu...............................................................................................................20
4.1 Safety.........................................................................................................................20
4.2 Flame start-up menu..................................................................................................22
4.2.1 Fan adjustment........................................................................................................23
4.2.2 Flame start-up completion......................................................................................24
4.2.3 Fuel delivery...........................................................................................................25
4.2.4 Internal screw .........................................................................................................26
4.3 Pump switch-on temperature.....................................................................................26
4.4 Flameout time............................................................................................................28
4.5 Operation capacity setup in «standby» mode............................................................28
5 Thermostat and gsm module hookup ...........................................................................29
6 Application instructions................................................................................................29
6.1 Operating restrictions ................................................................................................29
6.2 Installation rules ........................................................................................................29
6.3 Alarm signs, error messages......................................................................................30
7 Technical maintenance.................................................................................................32
7.1 Safety.........................................................................................................................32
7.2 Safety fuse replacement.............................................................................................32
7.3 Sensor location ..........................................................................................................32
7.4 STB safety thermostat ...............................................................................................33
7.5 Technical maintenance procedure.............................................................................33
7.6 Storage instructions...................................................................................................33
8 Warranty obligations....................................................................................................33
9 Transportation...............................................................................................................34
10 Unit disposal...............................................................................................................35

3
11 Regulatory history......................................................................................................35
12 Information on prices and purchase conditions .........................................................35
13 Performance data........................................................................................................36
WARRANTY TICKET...................................................................................................39

4
1 INTRODUCTION
1.1 Product Purpose and Delivery Set
AIR BIO PID control unit (hereinafter referred to as Controller) is designed for
control of the Central Heating Boiler equipped with the burner and worm feeder. The
Controller controls smooth change of the fan power, Central Heating pump and hot
water supply pump switch on, as well as widely used in pellet burners with automatic
firing. Owing to the capability of connecting expansion modules to AIR BIO PID
Controller via RS 485 interface, the Controller is able to operate the mixer valve of
three-or-four-way valve and the additional mixing pump. In addition, GSM module can
be connected to the Controller, and this module is used for control of the boiler
operation through mobile network.
AIR BIO PID Controller can also work along with the room thermostat working
based on the principle: on/off.
AIR BIO PID controls two independent processes:
а) temperature regulation:
PID algorithm sets the required boiler capacity to obtain the needed temperature,
what results in no violent changes of temperature in the chimney hole as well as in the
combustion chamber. The burning process can be permanent without breaks with
capacity from 5% (keeping fire state) up to 100% (maximum boiler capacity).
б) combustion process regulation:
Automatic fuel dosing. The software automatically changes fuel amount.
AIR BIO PID Controller is manufactured and released in the metal housing as a
standalone unit for installation on the boiler or in any other place convenient for you.
AIR BIO PID delivery set includes:
central heating temperature sensor - 4m long;
hot water supply temperature sensor - 4m long;
basket temperature sensor - 2m long;
flue gas temperature sensor - 4m long;
burner connecting cord - 2m long;
power-supply cord –2m long;
safety cutoff 10А – 2 ea;
clamp for fastening temperature sensors, metal –2 ea.
1.2 Installation Requirements
Hookup diagram for the control unit is shown on Picture 1.
While installation and operation it is recommended to adhere to the following
rules:
all installation works associated with installation/removal of the unit or
electric wiring shall be carried out only after power cut;
prior to start of controller operation it is recommended to get familiar with the
enclosed Operation Manual very thoroughly;
when hooking up the Controller make sure the electric parameters of the
supply main correspond with the Controller's operating range;

5
avoid to hook up the unit to the same electric circuit along with engines and
other devices causing impulse interferences (e.g. washing machines, refrigerators, etc.);
it is necessary to switch off power prior to connect any wires and secondary
devices to the unit;
in order to completely switch off the unit, it is required to pull out the plug
from the socket, in particular when the unit is not operating for some period of time;
it is recommended to protect power cable from damages, and no items shall
be installed or located on the power cable;
all connections shall be carried out in accordance with the electric installation
diagram and local norms on electric installations;
it is prohibited to touch contacts or other voltage-carrying controller
components;
installation and removal of the standalone unit as well as all the electric
wiring shall be carried out by the qualified electrician in accordance with the current
norms;
outlets for connecting external devices to the controller are on the back panel
of the unit (Picture 2);
the manufacturer is not responsible for damages associated with improper
connection of devices to the controller;
in case of having any doubts regarding safe connection of the unit and its
operation, it is recommended to get in touch with the supplier or controller
manufacturer;
the controller shall be used for its intended purpose only;
it is prohibited to make any changes in electrical and mechanical knots of
AIRBIOPID; such changes might result in improper controller operation or its
breakdown;
it is prohibited to shove any items through holes, e.g. ventilation ones, to the
internal space of the unit, such actions might result in short circuit, electric shock, fire
or controller damage;
it is prohibited to allow water, moisture, dust to go inside the unit; it might
result in short circuit, electric shock, fire or controller damage;
it is prohibited to allow the unit to undergo strikes or vibration;
it is required to obligatory switch off the controller prior to any action on
preservation;
it is prohibited to use gasoline, solvents and other chemical agents for
cleaning the controller casing, they may cause damage to the unit casing. We
recommend to use soft cotton cloth;
it is prohibited to use the controller with damaged cables (wires); the damaged
cable shall be replaced by a special service company, the cable shall be new with the
same parameters as the original one;
all service operations except for cleanup, replacement of safety appliances
and parameter adjustment shall be performed by the certified service center or the
manufacturer’s service company.

6
Picture 1 - AIR BIO Hookup Diagram
Picture 2 –Controller Back Panel
1-Hot Water Supply sensor.
2-Central Heating sensor.
3-Basket sensor.
4-Flue gas sensor.
5-Burner connecting cord.
6-Controller power supply.
7-Room thermostat connecting cord.

7
1.3 AIR BIO PID Application Benefits
If using AIR BIO PID Control Unit for the solid fuel boiler the operator gets the
following advantages:
fuel significant saving; because there is a capability to control burning
intensiveness;
capability to adjust Hot Water Supply temperature;
capability to adjust Central Heating temperature;
capability to adapt boiler operation to different types of fuel;
safety: if Central Heating heat carrier starts boiling or temperature sensor
breaks, the safety system described in Item 3.3 is actuated.
ecology: low level of dust and gases harmful for the environment, low
temperature of flue gases.

8
2 DESCRIPTION AND OPERATION
2.1 Description of the Controller components and control elements
Picture 3 –Controller External View
Power switch is intended for switching ON/OFF AIR BIO PID Control unit.
Safety fuse connector; thermal fuse is installed into the connector. The
connector is located on the external panel of the unit to simplify the process of safety
fuse replacement.
Control unit screen displays the boiler operation mode. When entering the
«MENU» it displays the menu items and modes for setting up the respective items.
Multifunctional control element (encoder) includes the menu item selection
button and a dial to go through the menu. Dial turning on the main screen –change of
settings of central heating temperature. By pressing the dial (encoder) you will switch
on the controller menu.
2.2 Main Display View and Description
AIR BIO PID Controller display shows boiler operation current status (Picture 4):

9
Picture 4 –AIR BIO PID Main Display
2.3 Boiler Temperature Setting
Boiler temperature setting is carried out by turning an encoder dial.
Picture 5 –Boiler Temperature Change
Decrease of the boiler temperature value up to the point when icon
appears on the display will result in boiler switch off. This function is applied in case if
the second system which warms water (hot water supply) is used in the central heating

10
system. (This function is used in summer time only. This function is impossible if the
hot water supply temperature sensor is not hooked up to the controller).
2.4 Boiler Temperature Adjustment (hot water supply)
For changing boiler heating parameters it is required to go to the Controller
menu (Picture 6):
Picture 6 –Controller Menu
By turning an encoder dial, select icon, , «Hot Water Supply Setting».
When pressing on a dial the boiler setting menu will open (Picture 7).
Hot Water Supply operating parameters are set in this menu. Boiler heating
temperature - from 40°Сto 80 °С, with a step of 1°С; pump hysteresis –1°Сto 10°С,
with a step of 1°С.
Picture 7 –Hot Water Supply Parameter Menu

11
By turning an encoder you select the needed parameter of Hot Water Supply
(the selected element is outlined by red rectangle). To change it you shall press fast on
the encoder, figures will change their color to red –you may change the parameter. By
turning an encoder you set the needed parameter value. By pressing the encoder for the
second time you confirm the parameter change, figures will again change color to black.
Once all the parameters are set up, you go back to the main menu by selecting icon ,
by means of the encoder and press encoder button.
2.5 Work Priority Selection
To select the operation mode you shall go to the main menu and select icon, ,
«Operation mode»(Picture 8).
Picture 8 –Main Menu (operation mode selection)
Operation mode selection menu will open if you press fast a dial (Picture 9).
Picture 9 –Boiler Operation Mode Menu

12
The menu includes three operation mode icons. To select the mode you turn the
encoder right/left for searching the needed mode and then press the encoder button.
, house heating, , parallel pumps, , Hot Water Supply priority.
3 USER MENU
To enter the user menu when you are on the main screen, (Picture 4) press the
encoder button. User menu will pop up on the screen (Picture 6):
Hot Water Supply temperature –Hot Water Supply
parameter setting menu, item 3.4.
Operation Mode –boiler operation mode selection, item 3.5.
PID mode setting –used for setting up boiler operation
parameters during combustion process. Here you can set up
parameters of time and breaks between fuel supply as well as
fan capacity, operation time for the internal screw.
Forced operation –this function is used for switching the
burner from firing mode to operation mode. It can be used only
for forced transition to operation.
Firing/Flameout –used for starting the burner operation
mode. When burner is operating –for switching off. Icon will
turn to .
Service menu –entry according to the code. Contains other
menus. Menu is open after entering digital code.
Manual operation –used for checking up all the connected
boiler mechanical parts.

13
EXIT –return to the controller main screen. It is not used
while selecting operation mode and burner startup, return to the
main screen is carried out automatically.
3.1 Burner startup
AIR BIO PID Controller is able to automatically control flame startup process
and shutdown process in pellet burners.
To begin flame startup process it is required to go to the controller main menu,
select menu item «Firing», and press the encoder button. The Controller will go
back to the main screen (Picture 4), and “Firing/Flameup”, operation mode icon will
pop up in the upper part of the screen. If the firing is successful the Controller moves to
the operating mode and starts implementing the task on temperature selection. icon
will pop up on the screen.
The Controller carries out three attempts of firing, if it fails, there will be a
message about an error on the screen being accompanied by sound alarm.
3.2 Shutdown
This function is intended to stop burner operation. This process takes different
amounts of time (see item 5.4 «Flameout time»).
To begin the shutdown process it is required to press encoder button, main menu will
open, by turning encoder select menu item «Flameout», and press the encoder
button. The Controller will go back to the main screen, and “Flameout” operation
mode icon will pop up in the upper part of the screen.
3.3 PID Mode Setting Up
The boiler operation parameters during the fuel combustion process are set up in
this menu. The following items are included:
Internal screw –operation time for the internal screw is set
up.
Fuel Delivery –operation time and breaks of screw feeder
are set up.

14
Fan Adjustment –maximum and minimum capacity of fan
operation is set up.
Cleanup –setup of parameters for firebox cleanup.
Capacity, % –used for setting up controller operation
parameters in manual mode. Allows presetting burner capacity
and hysteresis of exit from «Standby»mode.
Back –return to previous menu.
EXIT –return to the Controller main screen. It is not used
while selecting operation mode and burner startup, return to the
main screen is carried out automatically.
3.3.1 Internal Screw Operation Setting Up
To change internal screw operation parameters it is required to go to the menu
«PID mode settings»and select menu item «Internal Screw», , press the encoder
button –the window for setting up time of fuel delivery to the furnace will open
(Picture 10).
To change the value you shall press the encoder button –figures will change
their color to red, you set the needed parameter value and confirm it by repeatedly
pressing the encoder button –figures will return their color. Operation time is changed
within limits from 1 to 99 seconds.
To leave the internal screw setup window, move the cursor - frame to icon
«Back», , and press the encoder button, the Controller will go back to menu « PID
mode settings».

15
Picture 10 –Internal Screw Operation Setup Window
3.3.2 Fuel Delivery Parameter Setting Up
To change fuel delivery parameter it is required to go to the menu «PID mode
settings», select menu item «Fuel Delivery», , press the encoder button –fuel
delivery parameter setup window will open (Picture 11).
Picture 11 –Fuel Delivery Parameter Setup Window

16
Change of parameter value is similar to item 3.3.1.
Parameter value limits:
operation time of fuel delivery screw, seconds: 1-99;
interval between fuel portions, seconds: 1-99.
To leave the fuel delivery setup window, move the cursor –frame to icon
«Back», , and press the encoder button, the Controller will go back to menu « PID
mode settings».
3.3.3 Fan Adjustment
To change maximum and minimum fan capacity it is required to go to the menu
«Fan Adjustment». By turning encoder select menu item «Fan Adjustment», , press
the encoder button –fan operation parameter setup window will open (Picture 12).
Picture 12 –Fan Adjustment Window
Change of parameter value is similar to item 3.3.1.
Parameter value limits:
minimum fan capacity,%: 1-98;
maximum fan capacity,%: 1-99.

17
To leave the fan adjustment window, move the cursor –frame to icon «Back»,
, and press the encoder button, the Controller will go back to menu «PID mode
settings».
3.3.4 Burner Cleanup Setting Up
To change time and periodicity of cleanup it is required to go to the menu
«Cleanup». By turning encoder select menu item «Cleanup», press the encoder
button –burner cleanup parameter window will open (Picture 13).
Picture 13 –Burner Cleanup Parameter Setup Window
Change of parameter value is similar to item 3.3.1.
Parameter value limits:
interval of cleanup switch on, portions: 1-99;
operation time, seconds: 1-99.
To leave the cleanup window, move the cursor –frame to icon «Back», , and
press the encoder button, the Controller will go back to menu «PID mode settings».
3.3.5 Start/Stop Mode Setting Up
Start/Stop mode is used for the controller operation with the preset capacity up
to achieving the setup temperature, after that there will be transition to ”Maintaining”

18
status where the burner operates with 5% (operation capacity can be changed, see Item
5.5) of capacity without fuel supply. Once temperature is dropped up to hysteresis value
from the preset one, «Firing»mode switches on and controller operation repeats.
This mode switches on by setting up the capacity parameter other than «0»
(from «20» to «99»). Start/Stop mode setup menu item is shown on Picture 14.
Picture 14 –Start/Stop Mode Setup
3.4 Date/Time
There is built-in calendar and clock in the Controller. To change date and time it
is required to go to the menu «Date/Time». By turning encoder select menu item
«Service Menu», , press the encoder button –code entry window will open (Picture
16). It is required to enter code 1111, the Controller will go to menu «Date/Time»
(Picture 15).
To change date it is required to move the cursor-frame to date display and press
the encoder button. By turning encoder set up the needed year, and press the button to
confirm. Once the year is confirmed you shall set up a month, if it is required - and
press the encoder button. And after that you set up a date (current date).
To change time it is required to move the cursor-frame to time display and press
the encoder button. First you enter hours, and then minutes.

19
To leave date/time entry window move the cursor –frame to icon «Back», ,
and press the encoder button, the Controller will go back to the main menu.
Picture 15 –Date/Time Entry Window
3.5 Manual Control
Manual menu functions are used for forced switch-on of Controller power-
operated outlets.
!ATTENTION!
Manual control operates in standby mode only and is used for checkup of power-
operated outlets and for filling the screw feeder.
When in manual mode the Controller switches off all the power-operated outlets
(only control of burner emergency suppression is functioning).
Manual control includes the following elements:
Internal Screw–burner internal screw ON/OFF.

20
Fuel Delivery –screw feeder ON/OFF.
Fan –fan ON/OFF. Fan power is set up in %.
Tubular Heating Element–heating element outlet ON/OFF.
Central Heating Pump/Hot Water Supply Pump –central
heating pump ON/OFF/ Hot Water Supply Pump ON/OFF.
Back –return to previous menu.
EXIT –return to the Controller main screen. It is not used
while selecting operation mode and burner startup, return to the
main screen is carried out automatically.
4. SERVICE MENU
To enter the service menu you use the code, and when you enter it one of hidden
Controller menus will open.
4.1 Safety
Maximum permissible boiler, flue gases, pellet receiver temperature is set up in
the safety menu. When the permitted value data is obtained, the Controller will send an
alarm with indicating sign and move to «Flameout».
To enter the safety menu it is required to select item «Service Menu», , in
the main menu, and press the encoder button and enter code 2222 (Picture 16) in the
popped up window. By turning encoder select item «Safety», , and press the
encoder button –Controller will display the safety menu.
Table of contents
Popular Controllers manuals by other brands
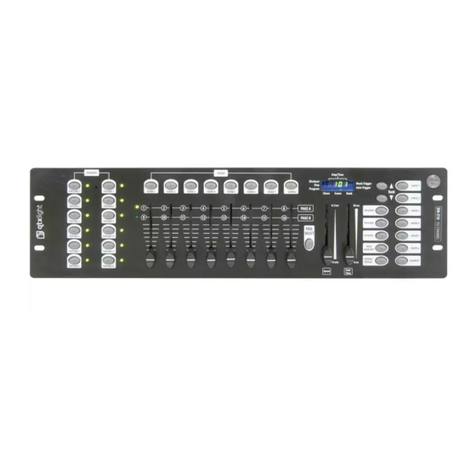
Qtx
Qtx DM-X10 user manual
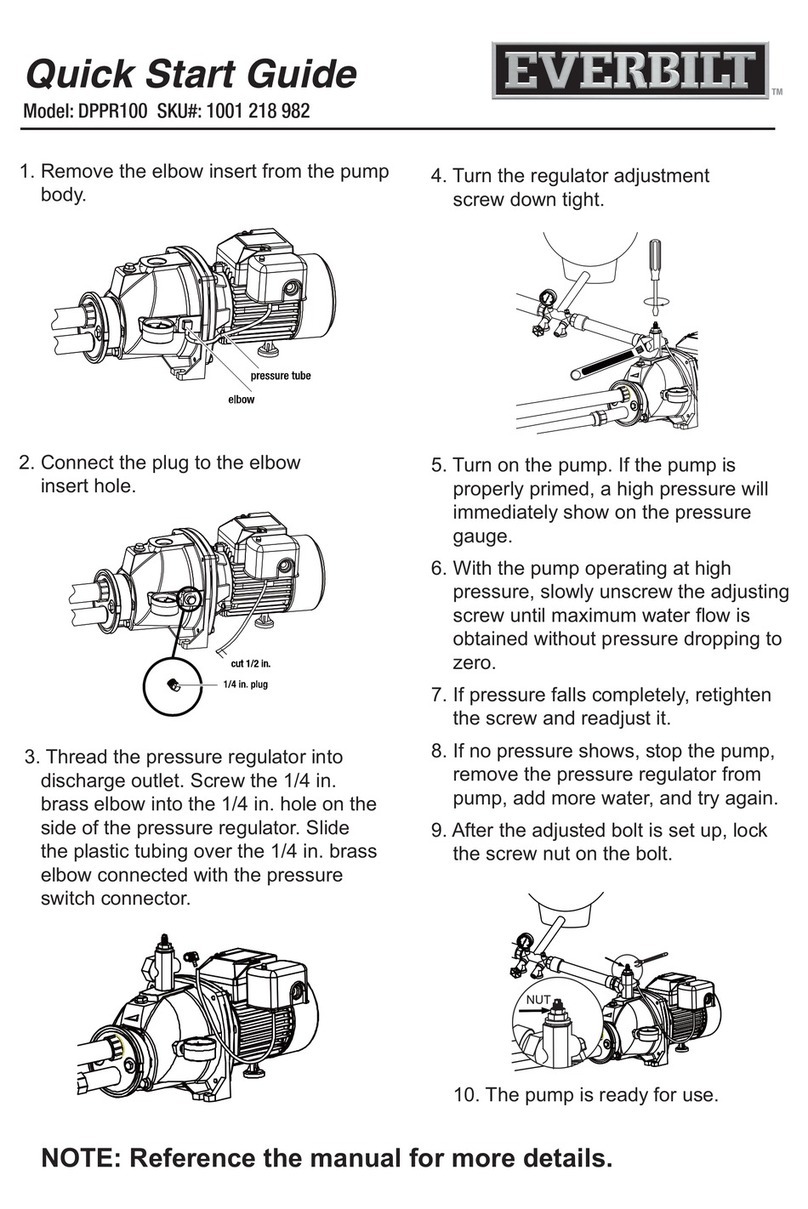
Everbilt
Everbilt DPPR100 quick start guide
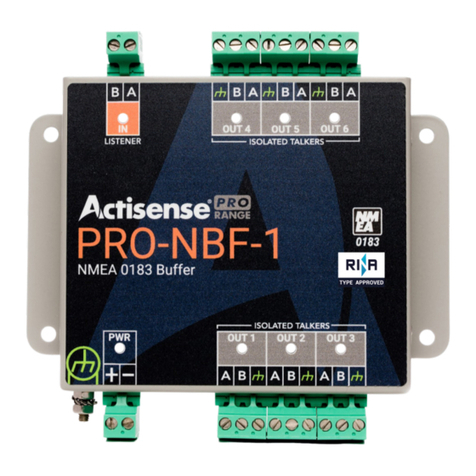
Actisense
Actisense Pro Series Install & user manual
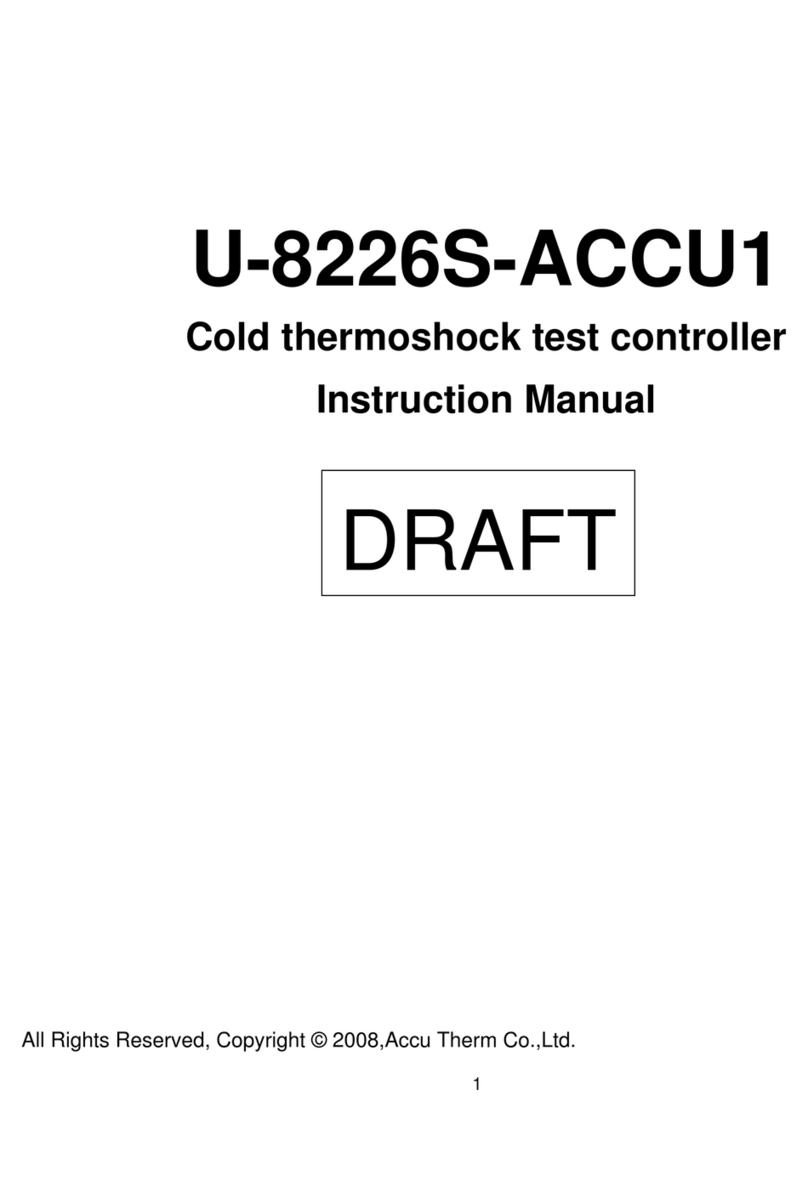
AccuTherm
AccuTherm U-8226S-ACCU1 instruction manual

Mitsubishi Electric
Mitsubishi Electric MELSEC iQ-F FX5-4LC Hardware manual
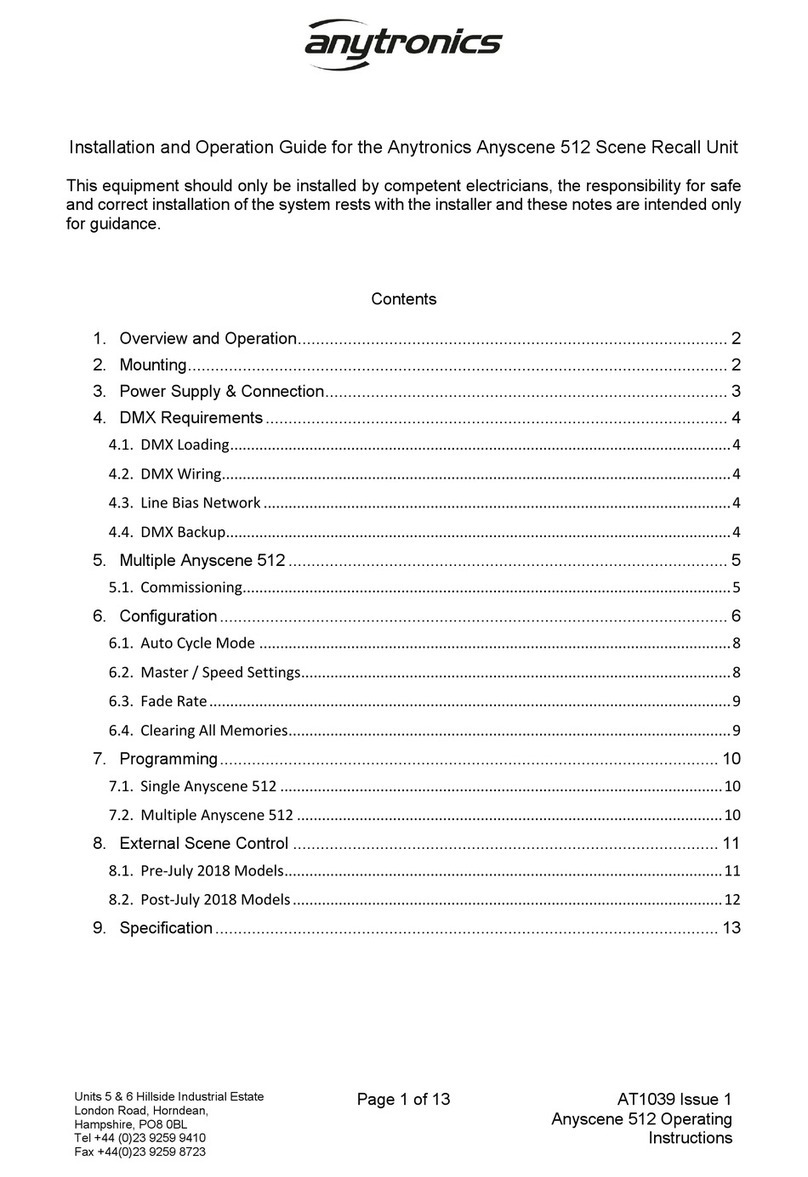
anytronics
anytronics Anyscene 512 Installation and operation guide