BLUEPRINTLAB REACH ALPHA RS1-1100 Use and care manual

REACH ALPHA
INTEGRATION MANUAL
www.blueprintlab.com
tel: +61 (2) 9519 7651
|
email: info@blueprintlab.com

2blueprintlab.com
Contents
1 OVERVIEW 4
1.1 Product Features 4
1.2 Reach Product Codes 5
2 SINGLE & DUAL FUNCTION MANIPULATORS 5
2.1 Specifications 5
2.2 Interfacing 6
3 REACH ALPHA 5 7
3.1 Dimensions and Coordinates 7
3.2 Specifications 8
3.3 Interfacing 9
4 BENCH SETUP 11
5 CONTROL 18
5.1 Control Panel 18
5.2 Human Machine Interface (HMI) 20
5.2.1 Manual Mode 20
5.2.2 Controller Mapping in Manual Mode 21
5.2.3 Kinematics Mode (Global Coordinates) (Pro Only) 21
5.2.4 Controller Mapping in Kinematics (Global) Mode (Pro Only) 22
5.2.5 Kinematics Mode (End-Effector Coordinates) (Pro Only) 23
5.2.6 Controller Mapping in Kinematics (End-Effector) Mode (Pro Only) 24
5.3 HMI Advanced Setup 24
5.3.1 Gamepad Advanced Setup 24
5.3.2 3D Mouse Advanced Setup 26
5.4 Master Arm Control 27
6 PLATFORM INSTALLATION 28

2 3
6.1 Hardware Mounting Setup 28
6.2 Software Setup for Hardware Constraints and Requirements via
Reach Control
30
7 ADDITIONAL REACH CONTROL WIDGETS 36
7.1 Monitor Panel 36
7.2 Measure Tool 36
7.3 Data Logger 37
7.3.1 First Time Setup or Editing of Data Logger Settings 37
7.3.2 After First Time Setup 38
7.4 Camera 39
7.5 Light 40
8 MAINTENANCE 40
8.1 Reach Control - Software Update 41
8.2 Firmware - Online Update 42
8.3 Firmware - Local Update 44
8.4 Configuration File Upload 45
8.5 Module Replacement 47

4blueprintlab.com
The Reach System is the world’s smallest, lightest subsea manipulator system. We designed this advanced
manipulator to open new possibilities for remote intervention and inspection in harsh environments. This
manual predominantly applies to the Alpha 5 (often termed ‘manipulator’ in this document) but applies
more generally to other Reach Mini actuators (e.g. 3 or 4-Function variants) as well.
1 Overview
Modular by Design
Underwater Ready
Full Control
Small Size
The modular design allows for rapid OEM upgrades and repairs.
Compatibility between modules increases reliability across the entire
range and allows for ease of customization. Interchangeable end-
effectors allow for quick mission-specic t outs.
The Reach Alpha is capable of operating at depths of 300m for
extended periods of time. Each unit undergoes rigorous testing prior
to shipping to ensure seal and structural integrity when operating in
harsh environments. Our products have been validated by customers
around the world and have logged over 1000 hours at depth.
Position, speed and current feedback extends the Reach Mini
manipulator abilities to performing delicate tasks. Proprietary control
algorithms ensure accurate response and enhanced control through
multiple human machine interfaces.
A standard external diameter of 40mm and weight of less than 900g
in water, the Reach Alpha provides unparalleled functionality for
unmanned remotely operated vehicles where size and weight are
critical.
1.1 Product Features

4 5
2 Single & Dual Function Manipulators
Throughout this manual, actuators will be referred to by their product codes as listed below.
¹The rate and torque relationship can be congured to suit a specic application. Please contact us to
discuss your solution.
²The RS1 Series can operate as low as 10V. However, voltages below 18V will result in a decrease in max rate.
RS1-1100 - Single Function Rotate Stage
RS1-1400 - Single Function Bend Stage
RS1-1300 - Single Function Linear Stage
RS1-2140 - Dual Function Rotate/Bend Stage
RS1-2130 -Dual Function Rotate/Linear Stage
RS1-5001 - 5 Function Manipulator
1.2 Reach Product Codes
2.1 Specifications
Specication RS1-1100 RS1-1400 RS1-1300 RS1-2140 RS1-2130
Weight Air 200g 320g 220g 360g 360g
Weight Water 100g 220g 130g 220g 250g
Dimensions 98xΦ40mm 140xΦ40mm 103xΦ40mm 165xΦ40mm 117xΦ40mm
Torque/Force¹ 0.6Nm 10Nm 600N 10Nm/1Nm 0.6Nm/600N
Rate¹ 90-20°/s 60°/s 2.5mm/s 60°/s 60°/s / 2.5mm/s
Travel 360° Cont 360° Cont 22mm 330° x 360° Cont 330° x 22mm
Specication RS1-1100 RS1-1400 RS1-1300 RS1-2140 RS1-2130
Depth 300m Below Sea Level
Temperature -30°c to +45°C -30°c to +45°C -30°c to +35°C -30°c to +35°C -30°c to +35°C
Shock 200Gs/1ms
Housing Material Hard Anodised 6061 Aluminium
Specication RS1-1100 RS1-1400 RS1-1300 RS1-2140 RS1-2130
Voltage Range² 18-30V DC
Power(max) 6W 11W 6W 11W 11W
Communication Full Duplex RS232 or Half Duplex RS485
Mechanical
Environmental
Electrical

6blueprintlab.com
Mechanical
Electrical
All actuators have the same mounting ange. This is to allow for easy integration of the entire range. Our
tailormade mounting kit allows for the quick swap out between various components or the simple rotation
of a single axis unit.
The standard connector interface for RS1 range is a 5-PIN HUMG SeaCon Connector. The mating
connector is a 5 Pin HUMG CCP. It is important that the serial device and the RS1 Actuator share a
common ground. Failing to do so could damage the device.
When using a RS485 version Pin 4 is A and Pin5 is B
2.2 Interfacing
Figure 1. Mounting Flange Dimensions
Figure 2. Mounting Kit Dimensions (Optional)
Figure 3. 5 Pin HUMG SeaCon Connector RS232 - Male Face View

6 7
3.1 Dimensions and Coordinates
Figure 4. Joints and Origin Figure 5. Joint Limits
Figure 6. Zero Point/ Travel/ Direction & Zero Point
Figure 7. Axis Length
3 Reach Alpha 5

8blueprintlab.com
3.2 Specifications
Specication Joint A Joint B Joint C Joint D Joint E
Weight Air 1250g
Weight Water 880g
Dimensions 570xØ40mm (Mounting Base to Jaw Tip)
Max Lift (Full Reach) 2Kg
Torque/Force1 600N 0.6Nm 10Nm 10Nm 10Nm
Rate 3mm/s 50°/s 30°/s 30°/s 30°/s
Travel 22mm 330° 200° 200° 350°
Depth 300m Below Sea Level
Temperature -10°c to +45°C
Shock 200Gs/1ms
Housing Material Hard Anodised 6061 Aluminium
Voltage Range 18-30V DC (Lower voltage is allowed, but will limit speed)
Power(max) 35W
Communication Full Duplex RS232 or Half Duplex RS485
Connector Teledyne 6 Pin IE(W)-55 Impulse
Kinematic, Dynamic, and Other Properties
The Blueprint Lab Github repository contains documents regarding the Kinematic and Dynamic properties
of Reach System manipulators.
Available at: https://github.com/blueprint-lab
Mechanical
Environmental
Electrical

8 9
3.3 Interfacing
Mechanical
Electrical
The Reach Alpha offers a variety of mounting congurations. These are easily implemented using the
supplied two-part mounting kit. This kit is designed to absorb moderate shock to help protect the Reach
Alpha from external impact.
The standard interface for the Reach Alpha is a Teledyne 6 Pin IE(W)-55 Impulse Connector. The mating
connector is a Teledyne 6 Pin IE(W)-55 Impulse CCP Connector. It is important that the serial device and
the Reach Alpha share a common ground. Failing to do so could damage the device.
NOTE: If your whip has a Brown cable this is a legacy conguration. Please contact Blueprint Lab for the
interface information.
Figure 9. IMPULSE IE55 CCP Dimensions (mm)
Figure 8. Mounting Dimensions of Mounting Kit

10blueprintlab.com
Communication
The Reach Alpha communicates via a serial RS232 or RS485 interface. The serial connection should be
congured via the Reach Control software suite or manually using the following specication.
When using an RS232 device, the connection is full duplex whilst when using RS485 it is half duplex. The
Reach Alpha will respond to demands on either RS232 or 485 without needing to be congured. Data
being transmitted from the R5M will be done via both COM ports. For more information on the serial
protocol please refer to the Serial Protocol Document at https://github.com/blueprint-lab.
Figure 10. IMPULSE IE55 FEMALE Whip - Female Face View
Serial Specications
Baud 115200 bits/s
Word Length 8 bits (including parity)
Parity None
Stop Bits 1

10 11
4 Bench Setup
You Will Need
Prior to vehicle integration activities, a bench level test is recommended in the rst instance. This builds
familiarity from the ground up and assists with product acceptance. The following procedure will walk you
through the bench setup procedure.
• Reach Alpha manipulator
• Test Cable
• Power Supply or Battery
• PC or Laptop running Windows
• (Optional) 3D Mouse or Gamepad
• Supplied Break-out-board with USB cable or alternative serial connection (RS232 or RS485)
• An installation of Reach Control Lite (included with purchase) or Reach Control Pro
• Reach Alpha Mounting Kit
Step 1
Remove the manipulator and stand from the transport case and place on the bench. Loosen the mount
locking nut, rotate the manipulator 90 degrees to the upright position, align the pins and re-tighten.
Step 2
Ensure the manipulator is upright and free from obstruction. Connect the 6-Pin Female Impulse connector
to the 6-Pin Male connector on the rear of the manipulator by lining up, inserting and then rotating to
fasten.

12blueprintlab.com
Step 4 - Reach Control Setup
Step 5 - External Control Setup
Install the latest version of Reach Control by double clicking on the supplier installer .exe le and
following the installation wizard. Run the application on the completion of install or via the start menu.
Two external controllers can be used to control manipulators via Reach Control. These are the Gamepad
(eg. Xbox Controller) and the 3Dconnexion Spacemouse. To test these controllers, plug the controller into
your computer while running Reach Control and move the controller and buttons around. The arrows will
light up and the 2D animation will portray a simulated response (see Figure 11).
NOTE: If using the Master Arm controller, you can set that device up now, following the steps in the Master Arm
Operator’s Manual.
Figure 11. Space Mouse Simulation (Left), Gamepad Controller Simulation (Right). Kinematics icon will
only show in the full version of Reach Control
Step 3
Connect the Break-out-board to the PC/Laptop via the supplied USB cable. You may plug the USB into
either the RS232 or RS485 slot as both outputs are connected to the cable whip by default.
For users who are bypassing the Break-out-board and using their own serial connection setup, ensure that
TX of the manipulator goes to RX of the controller and vice versa.

12 13
Step 6 - Communication Setup
This step connects the control PC or Laptop to the manipulator. To access the CONNECTIONS setup tool,
see Figure 12.
Figure 13. CONNECTIONS options
1. Reach Control creates a single connection by default if no other connections were already setup.
2. Connections can be added by clicking on the “Add” button in the top left of the CONNECTIONS
panel. See Figure 13.
3. Set a connection name by typing into the “Name” textbox.
4. Set a connection method by clicking on the orange arrow on the “Method” Button. This will bring up
a list of the serial COM ports and the option to set UDP or TCP (IPv4) connections. Click on the COM
port name or the UDP/TCP options to set those connection methods.
5. TIP: One way to quickly determine the COM port number for a device is to compare the list of COM
ports with the serial connection plugged in and unplugged. The relevant COM port will be the one
that appears/disappears.
Figure 12. Connection Setup

14blueprintlab.com
6. If a UDP or TCP connection is required, the IP Address and Port boxes will appear where you can type
in the IPv4 IP Address and Port numbers.
NOTE: Reach Control can only act as a UDP or TCP client, not as a host.
7. If you are connecting via the RS232 bus on the manipulator, set the connection to full duplex by
clicking on the 2 reversed direction parallel arrows in the “Duplex” selector. If you are connecting via
the RS485 bus on the manipulator, set the connection to half duplex by clicking on the double-ended
arrow in the “Duplex” selector. The connection will assume it is half-duplex by default.
8. To the right of each Method button is the power icon. If the power icon is orange, then the connection
is active and connected. You can toggle the connection on and off by clicking the power icon.
9. Close the CONNECTIONS panel after conguration.
Step 7 - Vehicle Setup
This step congures the vehicle system (or bench setup) according to the manipulators, controllers, and
any other devices in use. To access the VEHICLE SETUP tool, see Figure 14.
For example: : If you have one Alpha 5 and one Master Arm, click on the “Add” button on the
bottom right product tab (RIGHT ARM). If not already set, select the product type you have (Alpha
5) via the Product Select dropdown list. On the top right, select the Controller Select dropdown
and click ‘Master Arm’.
Figure 14. VEHICLE SETUP access and tool
1. The VEHICLE SETUP panel will show a list of products and controllers that are bound to the
product. The RIGHT ARM tab will be shown as default, along with its RIGHT CONTROLLER tab.
2. Click on the “Add” button for each product you need. See Figure 15.

14 15
3. Set the product type you have, such as Alpha 5 or Alpha Dual Bend, by selecting it via the “Product
Select” dropdown.
4. Set your chosen products to their respective connections by via selecting it via the “Connection
Select” dropdown.
5. Select the controller method you wish to use via the “Controller Select” dropdown list. The “RIGHT
CONTROLLER” will be used to control the “RIGHT ARM”, and the “LEFT CONTROLLER” will be used
to control the “LEFT ARM”.
6. If you are using a Master Arm in the “LEFT CONTROLLER” or “RIGHT CONTROLLER” slots: The
‘Control State Indicator’ will appear if the master arm has been successfully connected. If the master
arm is in control, then the indicator will be orange. On-screen controls can be used if the master arm
is paused. The indicator will turn white if on-screen controls are being used, turning orange again if
the master arm is resumed.
7. If you are using a 7 function Master Arm and you are controlling an Alpha 5 in either the grabber or
probe congurations, you can congure the Master Arm’s control axis by clicking on the ‘Probe’ and
‘Grabber’ buttons.
Figure 15. VEHICLE SETUP options
Step 8 - 3D Manipulator Model Positioning
If you added more than manipulator, you may wish to move the 3D models representing the manipulators
in the background. To bring up the 3d model move arrows, click on the “3D Move Arrow” icon in Figure
16. Holding down and dragging the arrows will move the model along the axis of the arrow. Clicking the
“3D Move Arrow” icon again will remove the 3d model move.

16blueprintlab.com
If you are using a wall adapter connect the XT30 Connector as shown and then plug the adapter into the
wall.
Step 9 - Power Supply
Connect power to the Break-out-board via the supplied power adaptor.
In the case of a bench top power supply, connect the ground lead from the Alpha 5 to the GND of the
power supply. If you have made your own cable, ensure the Ground (GND) on the serial connector is
connected to the ground on the power supply. Connect the positive (PWR+) of the Alpha 5 to the positive
terminal of the power supply and turn on the power supply.
Figure 16. 3D Manipulator Model Positioning

16 17
Step 10 - Power On and Condition Check
Turn the power supply on.
Five seconds after powering the manipulator the MONITOR panel will begin to show data readings for all
joints on the manipulator. To access the MONITOR panel, see Figure 13.
If there is no update to the graphs in the MONITOR panel, ensure the manipulator is connected and
communicating with Reach Control
Figure 17. Monitor Panel
Step 11 - Control Check
The nal step in the bench test is to ensure that all joints are active, receiving commands, and responding
in the expected manner. Using a control method of your choice as detailed in Section 4 (we recommend
the software control panel), actuate each joint of the manipulator and ensure that the joint responds and
moves correctly.
This is the end of the bench test. You are now ready to further integrate and test the manipulator for your
specic application.

18blueprintlab.com
The joints of the manipulator can be manually controlled using the CONTROL panel. A graphic display
indicates the settings used to control joints, and sliders are available for changing the primary parameters.
To access the CONTROL panel, see Figure 18.
Dependant on the selected manipulator, different control arrows will appear around the 3D model of the
manipulator. On opening of the CONTROL panel, arrows will appear around each joint, where clicking
and/or holding on them will perform the selected action (see Figure 19). For rotate joints, clicking on the
arrows will rotate the joint in the direction of the arrow. Similarly, clicking on the jaw arrows will either
open or close the jaws.
5 Control
5.1 Control Panel
Figure 18. Control Panel access
Figure 19. Control Panel features

18 19
The selected action is determined by the active control mode, which is selected by the “Control Mode
Select” buttons (see Figure 19). The active control mode is determined by the orange “Control Mode
Select” button. The selectable control modes are:
1. Position Increment (POSITION): Click and releasing on the control arrows will increment the current
position of the joint by the determined “Position Increment” button number, in degrees.
2. Indexed Position Increment (JOG): Click and releasing on the control arrows will increment the
indexed position of the joint by the determined “Indexed Position” button number, in degrees. This
will only work if the manipulator is a kinematics device.
3. Velocity control (VELOCITY): Click and holding the control arrows will control the joint velocity, with a
value dependant on the value of the “Velocity Gain” slider (0-100%). Releasing the control arrows will
stop all movement of the manipulator.
The settings in the CONTROL panel (see Figure 19) are described below:
1. Position Increment Buttons: Pressing the control arrows while in “POSITION” mode will increment the
position by the value of the selected “Position Increment” button (in degrees).
2. Indexed Position Buttons: Pressing the control arrows while in “JOG” mode will increment the
indexed position value by the value of the selected “Indexed Position” button (in degrees). This will
only work if the manipulator is a kinematics device.
3. Velocity Gain Slider: Sets the speed of the joint when the control arrows are pressed.
4. Torque Output Slider: Set the percentage torque output of all the joints besides the jaw open and
close and inline rotate of all manipulators. It is recommended this remains at 50% when bench testing.
5. Grip Force Slider: Sets the amount of force applied by the jaws.
6. Product Selector: Dropdown box to select which product is the target of the Control Panel.
7. Position Preset Buttons: Click and holding the buttons will command the manipulator selected by the
“Product Selector” to move to the position preset with index given by the button’s number. Releasing
the button will stop the manipulator moving. These can be set in the Installation panel.

20blueprintlab.com
Depending on the task being performed, the HMI panels offer the ability to quickly change the
responsiveness of the controller using the exponential settings.
In manual mode the joints are controlled independently, and commands do not make use of the
kinematics engine. By default, the controls of the 3D Mouse and Gamepad are pre-mapped to specic
functions. These can be changed in the settings panel. The mounting orientation selected during the
installation setup will dictate the direction of rotation (see Section 5).
• Slider to the left provides a small output demands for most of the controller input. Useful for ne-
tuned, slower control.
• When the Kinematics Icon (Reach Control Pro feature) is white the controller is being used in Manual
Mode.
5.2.1 Manual Mode
Figure 20. 3D Mouse Panel Figure 21. Gamepad Input
Reach Control can take controller demands from a 3D Mouse or Gamepad. (For Master Arm users, please
see Section 4.4)
When connecting either a 3D Mouse (Figure 20) or a Gamepad (Figure 21), the appropriate window will
appear and display feedback and control options. Moving the HMI in their respective axes will simulate
the movement on the manipulator simulation as well as highlight the controller input.
5.2 Human Machine Interface (HMI)
• The Slider in the centre is a linear mapping where 50% input will provide a 50% output. This is
standard mode.
• Slider to the right provides a large output demand for a small controller demand. Useful for fast,
responsive movements.
This manual suits for next models
4
Table of contents
Other BLUEPRINTLAB Robotics manuals
Popular Robotics manuals by other brands
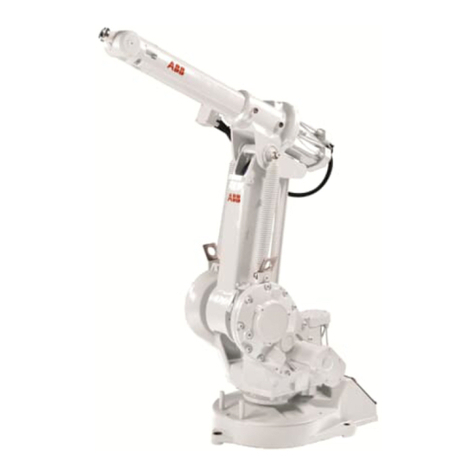
ABB
ABB IRB1410 product manual
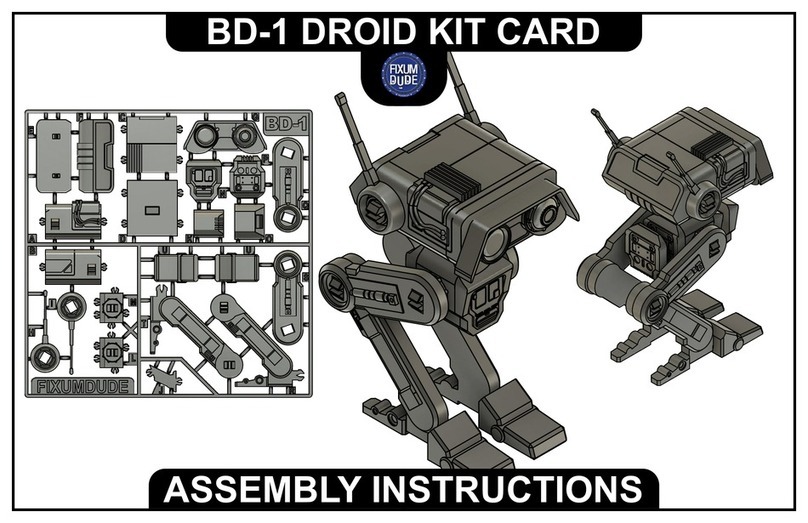
FIXUM DUDE
FIXUM DUDE BD-1 Assembly instructions
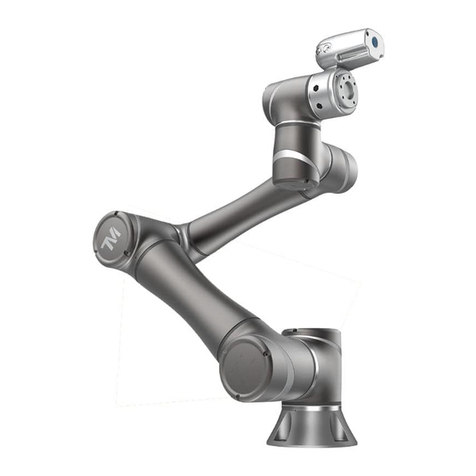
Techman Robot
Techman Robot TM5 Series Guide book

Tregaskiss
Tregaskiss TOUGH GUN I.C.E. Technical Guide Addendum

Dunlop
Dunlop EVO 4000 Assembly and operating instructions
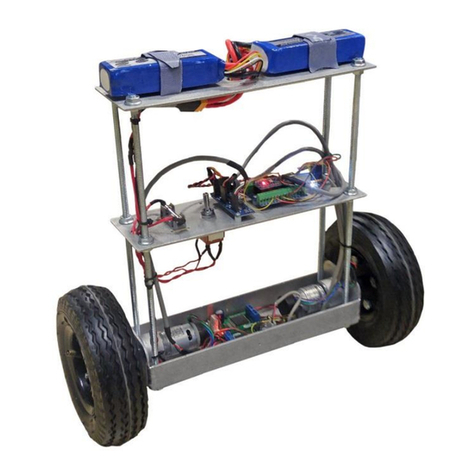
SuperDroid Robots
SuperDroid Robots 2WD Assembly and operation