BOSSCO 355AA User manual

AUTOMATIC NORMALLY CLOSED SOLENOID VALVE FOR GAS
CE-51BS3422/ED05
355AA
DN 32 - DN 40 - DN 50 - DN 65 - DN 80
DN 100 - DN 125 - DN 150
P.max: 360 mbar
MADE IN ITALY
EN
EC approval according to EN 161, compliant with Regulation (EU) 2016/426

2
EN
INDEX
pag.
English ........................................................................................................................................................ 3
Drawings...................................................................................................................................................... 13
Dimensions (table 1) ..................................................................................................................................... 17
Spare coils and connectors (table 2) ............................................................................................................... 18
SIL Level (table 3) ......................................................................................................................................... 19
Diagram ....................................................................................................................................................... 19

3
EN
1.0 GENERAL INFORMATION
This manual shows you how to safely install, operate and use the device.
The instructions for use ALWAYS need to be available in the facility where the device is installed.
ATTENTION: installation/wiring/maintenance need to be carried out by qualified staff (as explained
in section 1.3) using appropriate personal protective equipment (PPE).
For any information pertaining to installation/wiring/maintenance or in any case problems that cannot be resolved with the use
of the instructions, it is possible to contact the manufacturer from the address and phone numbers provided on the last page.
1.1 DESCRIPTION
Normally closed automatic fast opening solenoid valves for gas. They open the flow of gas when the coil is electrically powered
and close them when power is disconnected. They can be controlled by pressure switches, thermostats, etc.
They can be equipped with CPI switches to control the valve’s obturator position (closed) remotely. The CPI can also be
installed at a later time ONLY IF the device is set-up properly (cap under the valve body). Further information regarding the
CPI switch is available in 6.0.
Reference standards: EN 161 - EN 13611.
1.2 KEY OF SYMBOLS
1.3 QUALIFIED STAFF
These are people who:
•Are qualified to carry out product installation, assembly, start-up and maintenance;
•Know the regulations in force in the region or country pertaining to installation and safety;
•Are trained in first aid.
1.4 USING NONORIGINAL SPARE PARTS
•To perform maintenance or replace parts (ex. coil, connector, etc.) ONLY manufacturer-recommended parts can be used.
Using different parts not only voids the product warranty, it could compromise correct device operation.
•The manufacturer is not liable for malfunctions caused by unauthorised tampering or use of non-original parts.
1.5 IMPROPER USE
•The product must only be used for the purpose it was built for.
•It is not allowed to use different fluids than those expressly stated.
•The technical data set forth on the rating plate must not be exceeded whatsoever. The end user or installer is in charge of
implementing proper systems to protect the device, which prevent exceeding the maximum pressure indicated on the rating
plate.
•The manufacturer is not responsible for any damage caused by improper use of the device.
ATTENTION: Attention
is drawn to the technical
details intended for
qualified staff.
DANGER: In the event of
inobservance, this may cause damage
to tangible goods, to people and/or
pets.
DANGER: In the event
of inobservance, this may
cause damage to tangible
goods.

4
EN
2.0 TECHNICAL DATA
• Use : non-aggressive gases of the three families (dry gases)
• Ambient temperature (TS) : -20 ÷ +60 °C
• Supply voltages (see table 2) : 24 V/50 Hz - 110 V/50-60 Hz - 230 V/50-60 Hz*
• Supply voltage tolerance : -15% ... +10%
• Electric wiring : cable gland PG 11
• No. cycles/hour** :
DN 32 - DN 40 - DN 50 - DN 65 - DN 80 - DN 100
~195 (ON time 5s - OFF time 13.5s)
DN 125 - DN 150 ~90 (ON time 10s - OFF time 30s)
• Absorbed power : see table 2
• Maximum operating pressure : 360 mbar
• Opening time : <1 s
• Closing time : <1 s
• Protection rating : IP65
• Class : A
• Mechanical resistance : Group 2
• Rp Threaded connections : (DN 32 - DN 40 - DN 50) according to EN 10226
• Flanged connections to be coupled with PN 16 flanges
: (DN 65 - DN 80 - DN 100 - DN 125 - DN 150) ISO 7005 / EN 1092-1
• NPT threaded or ANSI 150 flanged connections : on request
• Filter element : 1 mm wire mesh on connections DN 32 - DN 40 - DN 50
filtering 50µm on DN 65 - DN 80 - DN 100
filtering 10µm on DN 125 - DN 150
• In compliance with : Regulation (EU) 2016/426 (Appliances burning gaseous fuels)
Directive EMC 2014/30/EU - Directive LVD 2014/35/EU
Directive RoHS II 2011/65/EU
* Only single-phase, the device does not work if powered with three-phase voltage.
** For cycles/hours with ON/OFF times different from those indicated, contact our technical office
2.1 MODEL IDENTIFICATION
See Table 2 on page 18.
2.2 SIL LEVEL
The SIL level of the stand-alone solenoid valve is SIL 2; when two solenoids are installed in series and the relative leak test
(Valve Proving System), certified according to EN 1643, the achieved level is SIL 3, as set forth in EN 676:2008. The solenoid
valve has PL d level. For further data refer to the SIL LEVEL table (table 3).

5
EN
3.0 COMMISSIONING THE DEVICE
3.1 OPERATIONS PRIOR TO INSTALLATION
•It is necessary to close the gas upstream of the valve prior to installation;
• Make sure that the line pressure DOES NOT EXCEED the maximum pressure declared on the product label;
•Any protective caps (if any) must be removed prior to installation;
•Valve pipes and insides must be clear of any foreign bodies;
If the device is threaded:
make sure that the pipe thread is not too long, to prevent damaging the body of the device when screwing it on;
If the device is flanged:
•make sure the inlet and outlet counter-flanges are perfectly coaxial and parallel in order to prevent unnecessary
mechanical stress to the body. Also calculate the space to insert the seal gasket;
•With regard to tightening operations, equip yourself with one or two calibrated torque wrenches or other controlled
locking tools;
•The safety regulations on handling loads in force in the country of installation must be complied with. If the device to
be installed exceeds the weight allowed, suitable mechanical equipment and adequate slings must be used. Necessary
precautions must be taken during the handling phases so as not to damage/ruin the external surface of the device;
•In accordance with EN 161 a suitable filter must be installed upstream of a gas closing safety device;
•With outdoor installation, it is advisable to provide a protective roof to prevent rain from damaging the electrical parts of
the device;
•Prior to carrying out any electrical wiring operations, make sure that the mains voltage matches the supply voltage indicated
on the product label;
•Cut out power prior to proceeding with wiring;
•According to the plant geometry, check the risk of explosive mixture arising inside the piping;
•If the solenoid valve is installed near other devices or as part of an assembly, compatibility between the solenoid
valve and this other device must be evaluated beforehand;
•Avoid installing the solenoid valve near surfaces that could be damaged by the coil temperature;
•Provide a protection against impacts or accidental contacts if the solenoid valve is accessible to unqualified
personnel.

6
EN
3.2 INSTALLATION (see examples in 3.4)
Threaded devices:
•Assemble the device by screwing it, with the correct seals, onto the plant with pipes and/or fittings whose threads are
consistent with the connection being attached.
•Do not use the coil (4) as a lever to help you screw it on, only use the specific tool;
•The arrow, shown on the body (7) of the device, needs to be pointing towards the application;
Flanged devices:
•Assemble the device by flanging it, with the correct seals, onto the plant with pipes whose flanges are consistent with the
connection being attached. The gaskets must be free from defects and must be centred between the flanges;
•If, after installing the gaskets, there is still an excessive space in between, do not try to reduce the said gap by excessively
tightening the bolts of the device;
•The arrow, shown on the body (7) of the device, needs to be pointing towards the application;
•Insert the relative washers inside the bolts in order to prevent damage to the flanges during tightening;
•When tightening, be careful not to “pinch” or damage the gasket;
•Tighten the nuts or bolts gradually, in a “cross” order (see the example below);
•Tighten them, first by 30%, then by 60%, and finally 100% of the maximum torque (see the table below according to
EN 13611);
Diameter DN 65 DN 80 DN 100 DN 125 DN 150
Max. torque (N.m) 50 50 80 160 160
•Tighten each nut and bolt again clockwise at least once, until the maximum torque has been achieved uniformly;
Common procedures (threaded and flanged devices):
•The device can also be installed vertically without prejudicing correct operation. It cannot be put in
upside down (with the coil (4) pointing downwards);
•During installation, avoid debris or metal residues from getting into the device;
•To guarantee mechanical tension-free assembly, we recommend using compensating joints, which
also adjust to the pipe’s thermal expansion;
•If the device is to be installed in a ramp, it is the installer’s responsibility to provide suitable supports or correctly sized
supports, to properly hold and secure the assembly. Never, for any reason whatsoever, leave the weight of the ramp only on
the connections (threaded or flanged) of the individual devices;
•In any case, following installation, check the tightness of the plant;
•Wiring cannot have cables connected directly to the coil. ALWAYS and ONLY use the connector/electronic board
recommended by the manufacturer;
•Wire the terminal board (31) with a cable 3x1 mm²,
outside Ø between 8.3 and 9.5 mm using the relative
terminals for cables, as shown in the general figure on
the side. The cable to use must have double sheathing,
be suitable for use outdoors, with minimum voltage of
500V, and minimum temperature of 105°C;

7
EN
1
2345
9
10
11
piping
applicaon
discharge in
open air
internal thermal unit
external roof
87
6
9
12
3.4 GENERAL EXAMPLES OF INSTALLATION
EXAMPLE 1
1. 355AM... Manual reset solenoid valve
2. Jerk ON/OFF valve
3. Gas filter
4. OPSO shut off valve
5. Pressure regulator
6. 355AA... fast opening automatic solenoid valve
7. Solenoid valve control device
8. Relief valve
9. Pressure gauge and relative button
10. Gas detector
11. Remote jerk ON/OFF valve lever control
12. Expansion joint/anti-vibration mount
To wire the solenoid valve (see the images below):
a. Loosen the 4 fastening screws (1);
b. Remove the cover (2) and loosen the cable gland (3);
c. Pass the cable through the cable gland (3), leaving a suitable length at the end to facilitate wiring to the terminal
board without tensioning or forcing;
d. Secure the cables (duly crimped) to the terminal board (31), connecting terminals 1 and 2 to the power supply and
the earthing cable to the terminal . IMPORTANT: respect the polarity with 24 Vdc power supply;
e. Use a 22mm commercial spanner to secure the cable gland (3) , ensuring the product has a protection rating of IP65;
f. Secure the cover (2) with the 4 fastening screws (1). Make sure to place the rubber sealing gasket (33) correctly in
order to ensure product rating of IP65;
•The valve needs to be earthed either through the pipe or through other means (eg cable jumpers).
3.3
INSTALLATION IN PLACES WHERE THERE IS THE RISK OF EXPLOSION (DIRECTIVE 2014/34/EU)
The solenoid valve is not suitable for use in potentially explosive areas.
abc
f
e
d

8
EN
4.0 FIRST STARTUP
•Before start-up make sure that all of the instructions on the rating plate, including the direction of flow, are
observed;
•After gradually pressurising the plant, check tightness and operation of the solenoid valve by supplying/cutting
off the electricity.
4.1 - RECOMMENDED PERIODIC CHECKS
•Use a suitable calibration tool to ensure the bolts are tightened as indicated in 3.2;
•Check tightness of the flanged/threaded connections on the system;
•Check tightness and operation of the solenoid valve;
It is the responsibility of the final user or installer to define the frequency of these checks based on the severity of the service conditions.
5.0 MAINTENANCE
If the coil and/or electronic board/connector need to be replaced:
•Before performing any operation, make sure that the device is not electrically powered;
•Since the coil is also suitable to be permanently powered, high coil temperature in case of continuous operation is
entirely normal. It is advisable to avoid touching the coil with bare hands after a continuous power supply lasting
longer than 20 minutes. In case of maintenance, wait for the coil to cool down or, if necessary, use suitable protection;
NOTE: The coil and/or electronic board/connector replacement operations need to be carried out taking care to ensure the
product’s IP65 rating.
123
5
4
7
6
13
piping
applicaon
discharge in
open air
internal thermal unit
external roof
8
9
Power
12
12 11 10
EXAMPLE 2 (Burner Gas Train)
1. Gas filter
2. OPSO shut off valve
3. Pressure regulator
4. Minimum pressure switch
5. 355AA... fast opening automatic
solenoid valve
6. Maximum pressure switch
7. Slow opening automatic solenoid valve
8. External reset
9. Burner control
10. Valve proving system
11. Relief valve
12. Pressure gauge and relative button
13. Gas detector

9
EN
g. Loosen the 4 fastening screws (1) of the cover (2);
h. Remove the over (2) and loosen the cable gland (3) with a 22mm commercial spanner;
i. Loosen the screws of the main terminal board (31)and remove the existing electric wiring by extracting the cables from
the terminal board and cable gland (3);
j. Using an 8 mm socket spanner, loosen the fastening nut (28) and remove it together with the toothed washer (27);
k. Remove the connector/board (30) as shown in k.Loosen the screws from the rear terminal board (32)and remove the
two wires that come out;
l. Wire the two wires coming out from the rear terminal board (32) of the new connector/board.
IMPORTANT: Being careful not to pinch the two cables, in the centre pin (29) insert: the new connector/board +toothed
washer (27) + nut (28). With an 8mm socket spanner, tighten the nut (28);
Proceed as specified in points c-f in section 3.2.
ghi
lk
j
5.1 - CONNECTOR/ELECTRONIC BOARD REPLACEMENT
12728
30
31332 29 3
32
30
20 4
fig. 1

10
EN
5.2 - REPLACING THE COIL
Remove the fastening ring nut (20)
with a 35mm commercial spanner
Remove the O-Ring (19) Extract and remove the coil (4)
Now proceed with replacing the coil Loosen the nut (I) with a 35mm
commercial spanner
Remove the coil from the threaded
bar (III)
Remove the washer (
II
)
Insert the new coil and position the
O-Ring
Tighten and secure the fastening
ring nut again with a 35 mm
commercial spanner
a
mn o
r
q
p
stu
I) Fastening nut
II) Washer
III) Threaded bar
Complete coil
(including connector/board)
supplied as a spare part
•On completion of the above operations, proceed with wiring the coil just installed, as shown in 3.2

11
EN
5.3 - REPLACING THE FILTER ELEMENT (DN 65 - DN 80 - DN 100 - DN 125 - DN 150)
If internal checks must be carried out, before carrying out any operations:
•Close the gas upstream of the valve;
•Make sure there is no pressurised gas inside the device.
NOTE: given its weight, it is recommended to carry out the following operations after having removed the coil (see
paragraph 5.2 - images m-n-o-p-t-u coil removal and repositioning)
•Loosen the fastening screws (17 ) and very carefully remove the cover (6) from the valve body (7);
•Extract the filter element (15) and check its condition. Blow it and clean it and, if necessary, replace it (see fig. 6 and 7 for
positioning);
•Check the status of the cover’s O-Ring (16) and replace, if necessary;
•Make sure the cover’s O-Ring (16) is inside the provided groove;
•Reassemble the cover (6) and secure it in its original position, being very careful not to “pinch” or damage the O-ring (16)
during tightening;
•Tighten the screws gradually, following a “cross” pattern, until the torque (tolerance -15%) indicated in table 4 on page 19 is
reached. Use a calibrated torque wrench to do this;
•Check the body/cover seal;
NOTE: for internal inspections, it is recommended to:
•also check the obturator’s (10) integrity and, if necessary, replace the rubber seal (12);
•replace the seals before reassembling.
6.0 - CPI SWITCH
The microswitch that signals the closed position (CPI SWITCH) is a magnetic proximity sensor with a normally open contact. It
provides a signal when the valve obturator closes.
If the solenoid valve comes with CPI, the position of the sensor is already calibrated and set, therefore, for operation you simply
need to connect it to the power supply.
If it comes separately and is installed at a later time on a solenoid valve with CPI set-up, follow the instructions provided in
paragraph 6.2
6.1 - CPI SWITCH TECHNICAL DATA
• Ambient temperature : -20 ÷ +60 °C
• Switchable voltage : max 1000 V (dc or ac peak)
• Switchable current : max 1 A (dc or ac peak)
• Switchable power : max 40W ohmic
• Resistance : 200 mΩ
• Protection rating : IP65
• Cable length : max 5m
6.2 - CPI SWITCH INSTALLATION and CALIBRATION
It is necessary to close the gas prior to installation.
NOTE: CPI connector (23) wiring must be do ensuring a product rating of IP65;
• Remove the cap (11 ) under the valve body (7) and remove the aluminium washer (found between the cap and body);
• Instead of the cap (11 ), tighten the CPI ring nut kit (21). Make sure that between body (7) and kit (21) there is the new
aluminium washer or an O-Ring (25);
• Tighten the CPI ring nut kit (21) to the valve’s body (7) with a special commercial spanner;
• Before wiring the CPI connector (23), unscrew and remove the central screw (36);
• Connect the CPI connector (23) terminals 1 and 2 in series to the signalling device. Use proper cable terminals (see the
figures in 3.2);
• Wire the CPI connector (23) with 2x1mm² cable with external Ø of 6.7 mm. The cable must be in double sheath, suitable
for outdoor use, with a minimum voltage of 500V and a temperature of at least 90°C;
• Secure the CPI connector (23), tightening (recommended tightening torque 0.4 N.m ± 10%) the centre screw (36);
• To calibrate the microswitch, loosen the fastening nut (22) and position (by screwing on or off) the adjustment ring nut (24)
so that, with the solenoid valve in a closed position, the CPI provides the signal;
• Secure the adjustment ring nut (24) in that position by tightening the nut (22);
• The kit is now installed. Open and close the solenoid valve (by supplying and cutting off power) 2-3 times to make sure the
microswitch is signalling correctly.
CPI wiring diagram
open valve / open contact
closed valve / closed contact
SPST

12
EN
7.0 TRANSPORT, STORAGE AND DISPOSAL
• During transport the material needs to be handled with care, avoiding any impact or vibrations to the device;
• If the product has any surface treatments (ex. painting, cataphoresis, etc) it must not be damaged during transport;
• The transport and storage temperatures must observe the values provided on the rating plate;
• If the device is not installed immediately after delivery it must be correctly placed in storage in a dry and clean place;
• In humid facilities, it is necessary to use driers or heating to avoid condensation;
• At the end of its service life, the product is to be disposed of in compliance with the legislation in force in the country where
this operation is performed.
8.0 WARRANTY
The warranty conditions agreed with the manufacturer at the time of the supply apply.
For damage caused by:
•Improper use of the device;
•Failure to observe the requirements described herein;
• Failure to observe the regulations pertaining to installation;
• Tampering, modification and use of non-original spare parts;
are not covered by the rights of the warranty or compensation for damage.
The warranty also excludes maintenance work, other manufacturers’s assembling units, making changes to the device and
natural wear.
9.0 RATING PLATE DATA
The rating plate data (see example provided here) includes the following:
• Manufacturer’s name/logo and address
• Mod.: = device name/model followed
by the connection diameter
• CE-51BS3422/ED05 = certification pin number
• Cl. A = Seal strength in counterflow at 150 mbar in
accordance with EN 161
• Gr. 2 = Mechanical resistance group 2 in accordance with EN 161
• EN 161 = Product reference regulation
• P.max = Maximum pressure at which product operation is guaranteed
• IP.... = Protection rating
• 230V.... = Power supply voltage, frequency (if Vac), followed by electrical absorption
• Example of electrical absorption indication: 290/75 VA indicates 290 VA at start, 75 VA at steady state
• TS = Temperature range within which product operation is guaranteed
• = Conformity with Regulation (EU) 2016/426 followed by Notified Body No.
• year = Year of manufacture
• Lot = Product serial number (see explanation below)
• U2002 = Lot issued in year 2020 in the 2nd week
• 1728 = progressive job order number for the indicated year
• 00002 = progressive number referring to the quantity of the lot
Mod.: 355AA DN 80 35500088
CE-51BS3422/ED05 Cl.A Gr.2 EN 161 P. max:360 mbar
IP65 - 230 V/50-60 Hz 290/75 VA TS: -20+60 °C
year: 2020 Lot: U2002 1728/00002
CODE:
0051
Lodge Way House, Lodge Way,
Harlestone Road,
Northampton NN5 7UG.

13
EN
fig. 2
DN 32 - DN 40 - DN 50

14
EN
fig. 3
DN 65 - DN 80 - DN 100

15
EN
fig. 4
DN 125 - DN 150

16
EN
15
34
15
34
35
35
35
fig. 5
fig. 6
DN 65 - DN 80 - DN 100
fig. 5: view from above without cover
Position the filter element (15), making sure it is
between the relative guides (34).
DN 125 - DN 150
fig. 6: view from above without cover
Position the filter element (15), making sure
it is inserted between the relative guides (34)
and check that the fins (35) are secured well
to the valve body.

17
EN
fig. 1, 2, 3, 4, 5 and 6
1. Cover fastening screws
2. Electrical box cover
3. Cable gland
4. Coil
5. Closing spring
6. Valve cover
7. Valve body
8. Bottom sealing O-Ring
(on DN 65-80-100 only)
9. Bottom fastening screws
(on DN 65-80-100 only)
10. Obturator
11. Lower cap (on versions set-up for
CPI installation)
12. Sealing washer
13. Bottom (on DN 65-80-100 only)
14. Cap G 1/4
15. Filter element
16. Valve cover sealing O-Ring
17. Valve cover fastening screws
18. Electrical box cap
19. Coil O-Ring
20. Coil fastening ring nut
21. CPI kit ring nut
22. CPI fastening nut
23. CPI connector
24. CPI adjustment ring nut
25. Aluminium washer or O-Ring
26. Microswitch
27. Toothed washer
28. Connector/board fastening nut
29. Connector/board support pin
30. Connector/board (electronic)
31. Main power supply terminal board
32. Rear terminal board (coil)
33. Cover gasket
34. Filter element guides
35. Filter element fins
(on DN 125 - DN 150 only)
36. CPI connector centre screw
Table 1
Overall dimensions in mm
Threaded connections Flanged connections holes A B=(D+E) C D E F
Rp DN 32 - Rp DN 40 - - 160 210 140 37 173 108
Rp DN 50 - - 160 235 140 45 190 122
-PN 16 - ANSI 150
DN 65 4 290 317 211 89 228 141
-PN 16
DN 80 8310 325 211 97 228 141
-ANSI 150
DN 80 4 290 317 211 89 228 141
-PN 16 - ANSI 150
DN 100 8 350 388 254 105 283 167
-PN 16 - ANSI 150
DN 125 8 480 575 328 127 448 204
-PN 16 - ANSI 150
DN 150 8 480 579 328 131 448 204
The dimensions are provided as a guideline, they are not binding

18
EN
Table 2
Coils and connectors for 355AA solenoid valve
Valve code Connections Voltage Coil + connector code
(available as special order) Coil stamping Connector type
Absorbed power
VA*
35500203 Rp DN 32
24 V/50 Hz
B13138
BO-1015
24 Vac
DN 32 - 40 - 50
Energy Saving 24 Vac 97 / 4135500214 Rp DN 40
35500236 Rp DN 50
35500675 Rp DN 32
110 V/50-60 Hz
B13137
BO-1020
110 Vac
DN 32 - 40 - 50
Energy Saving 110 Vac 132 / 6035500686 Rp DN 40
35500697 Rp DN 50
35500044 Rp DN 32
230 V/50-60 Hz
B13136
BO-1030
230 Vac
DN 32 - 40 - 50
Energy Saving 230 Vac 82 / 3235500055 Rp DN 40
35500066 Rp DN 50
35500247 DN 65
24 V/50 Hz
B13055
BO-1115
24 Vac
DN 65 - 80
Energy Saving 24 Vac 185 / 50
35500258 DN 80
35500705 DN 65
110 V/50-60 Hz
B13092
BO-1120
110 Vac
DN 65 - 80
Energy Saving 110 Vac 260 / 70
35500716 DN 80
35500077 DN 65
230 V/50-60 Hz
B13054
BO-1130
230 Vac
DN 65 - 80
Energy Saving 230 Vac 290 / 75
35500088 DN 80
35500269 DN 100
24 V/50 Hz
B13057
BO-1215
24 Vac
DN 100
Energy Saving 24 Vac 120 / 35
35500738 DN 100
110 V/50-60 Hz
B13093
BO-1220
110 Vac
DN 100
Energy Saving 110 Vac 270 / 70
35500099 DN 100
230 V/50-60 Hz
B13056
BO-1230
110 Vac
DN 100
Energy Saving 230 Vac 270 / 70
35500280 DN 125
24 V/50 Hz
B13108
BO-2215
24 Vac
DN 100-125-150
Energy Saving 24 Vac 120 / 35
35500291 DN 150
35500749 DN 125
110 V/50-60 Hz
B13094
BO-2220
110 Vac
DN 100-125-150
Energy Saving 110 Vac 270 / 70
35500760 DN 150
35500107 DN 125
230 V/50-60 Hz
B13109
BO-2230
110 Vac
DN 100-125-150
Energy Saving 230 Vac 270 / 70
35500129 DN 150
* Example of electrical absorption indications: 270/70 VA indicates 270 VA on PTO, 70 VA at full speed

19
EN
Pressure drop diagram (calculated with P1 = 50 mbar)
Table 3
SIL LEVEL
Parameter Value
Hardware Failure Tolerance - HFT 0
Common Cause Failure - CCF in points 75
Safe Failure Fraction - SFF in % 65%
Expected Lifetime Cycles - B10d 251278
Expected Lifetime - T10d [years] 87
Probability of Dangerous Failures - PFHD[1/h] 1.33E-07
Performance Level - PL d
Safety Integity Level - SIL 2
Mean Time to Dangerous Failure - MTTFD[years] 860
DESIGNED LIFETIME
Designed operating cycles (According to EN 161) Time (years)
from 100.000 to 200.000 depends on diameter 10
Table 4
Vite / Screw M5 M6 M8 M10 M12
Max. torque (N.m)
Galvanised
6
10
25
49,5
84,5
Stainless Steel 4,5 7,5 18,5 37 63,5
dv = density relative
to the air
1) methane
2) air
3) town gas
4) lpg

Mod. IT391.00 E
We reserve the right to any technical and construction changes.
Registered Office: Travis Perkins PLC, Lodge Way House, Lodge Way, Harlestone Road, Northampton NN5 7UG.
Telephone Number: 0116 245 5500
Table of contents
Other BOSSCO Control Unit manuals
Popular Control Unit manuals by other brands
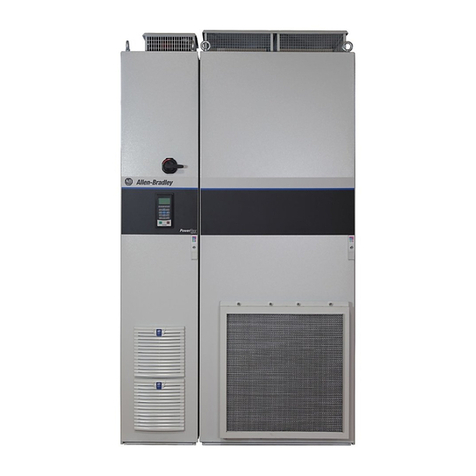
Rockwell Automation
Rockwell Automation Allen-Bradley PowerFlex 750 Series user manual
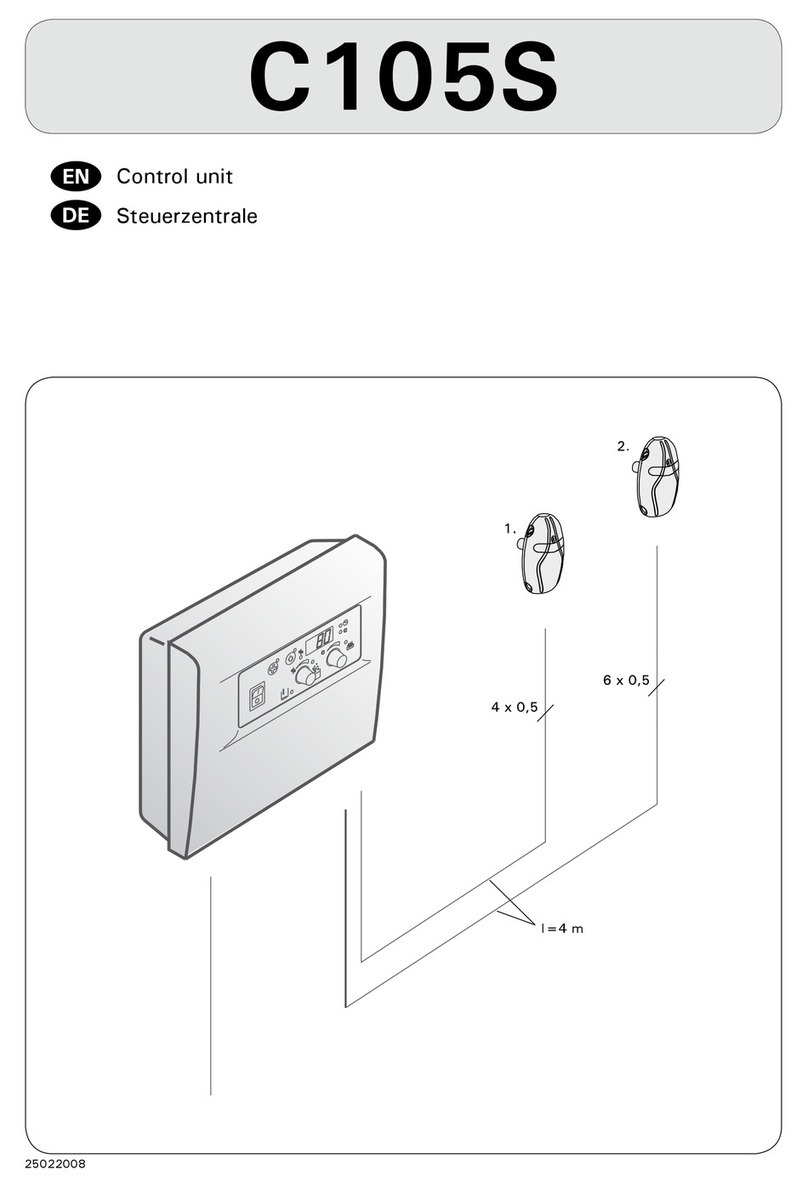
Harvia
Harvia C105S manual
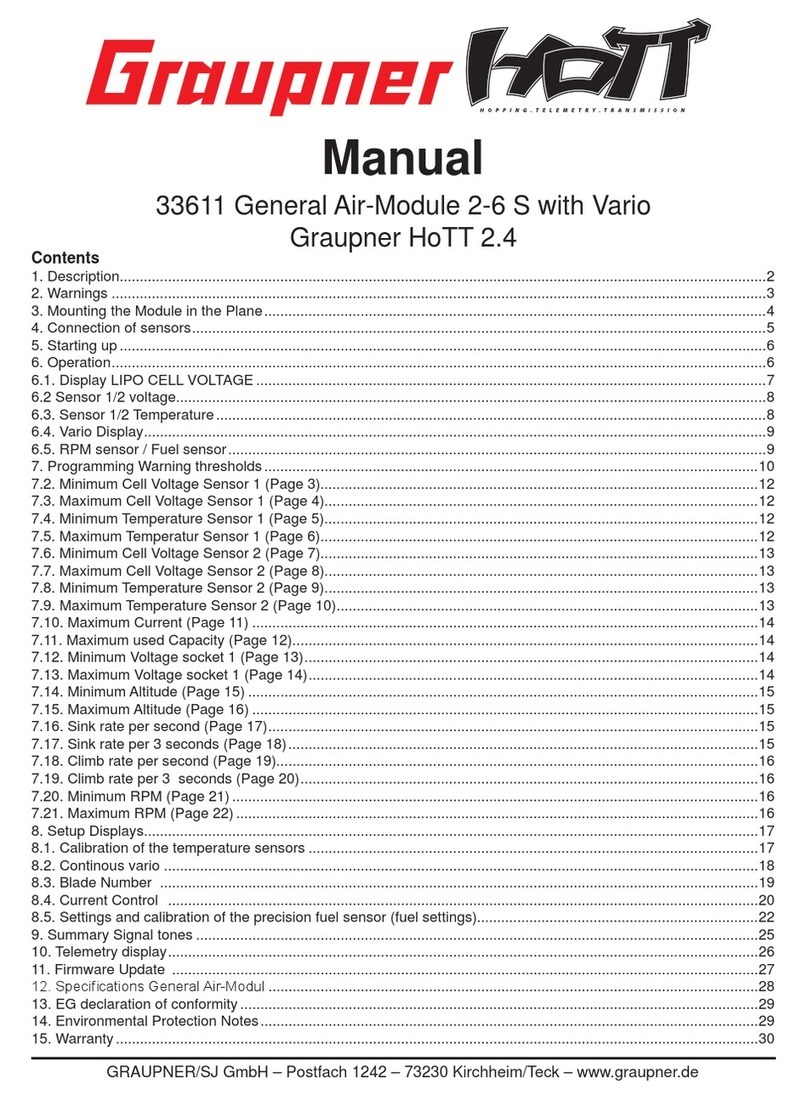
GRAUPNER
GRAUPNER HoTT 2.4 manual

Thermo Scientific
Thermo Scientific ETD Getting started guide
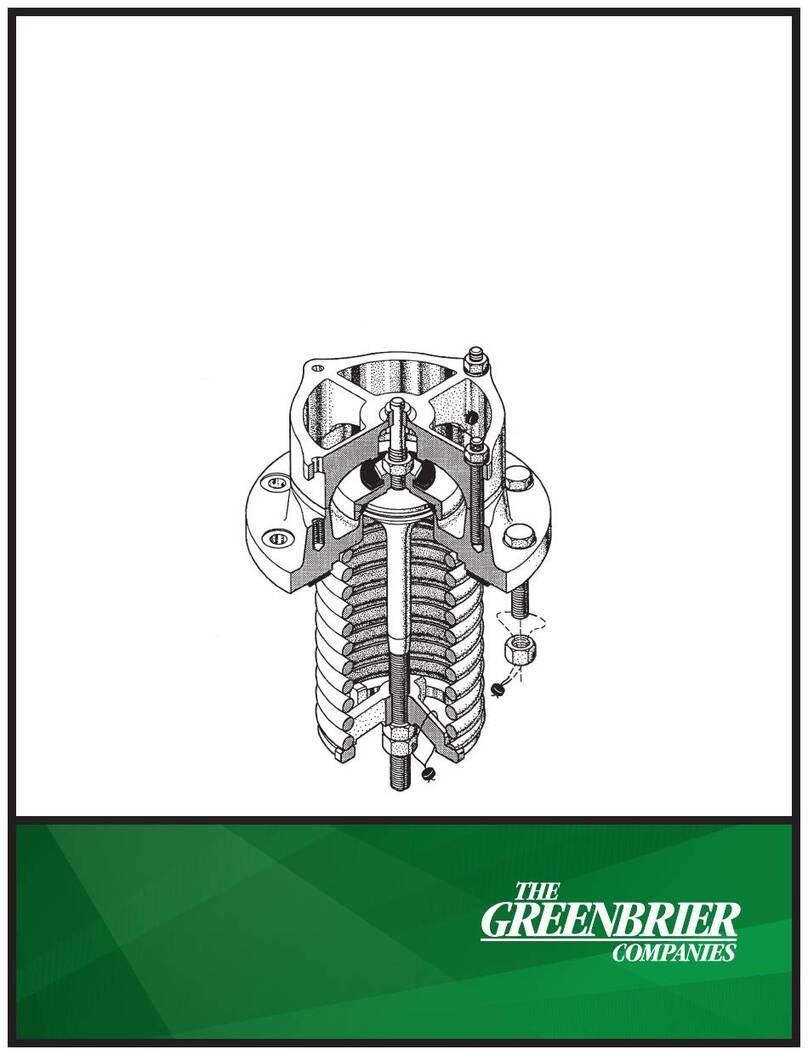
THE GREENBRIER COMPANIES
THE GREENBRIER COMPANIES ARI1118 Inspection and Maintenance Manual

GE
GE B90 UR Series instruction manual
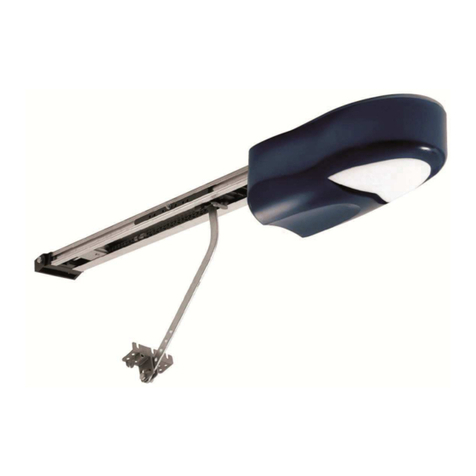
Allmatic
Allmatic CT ACTION 09 Instruction for the installation

Reliance electric
Reliance electric AutoMax 57C430A instruction manual
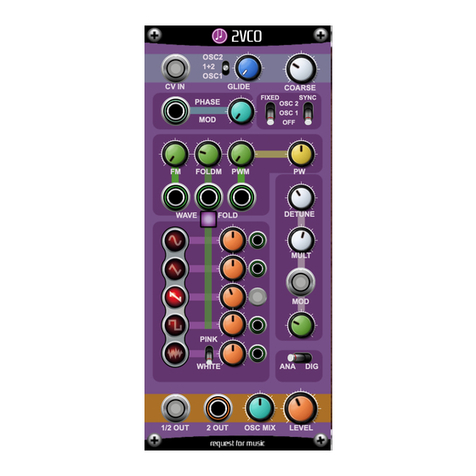
RFM
RFM 2VCO manual
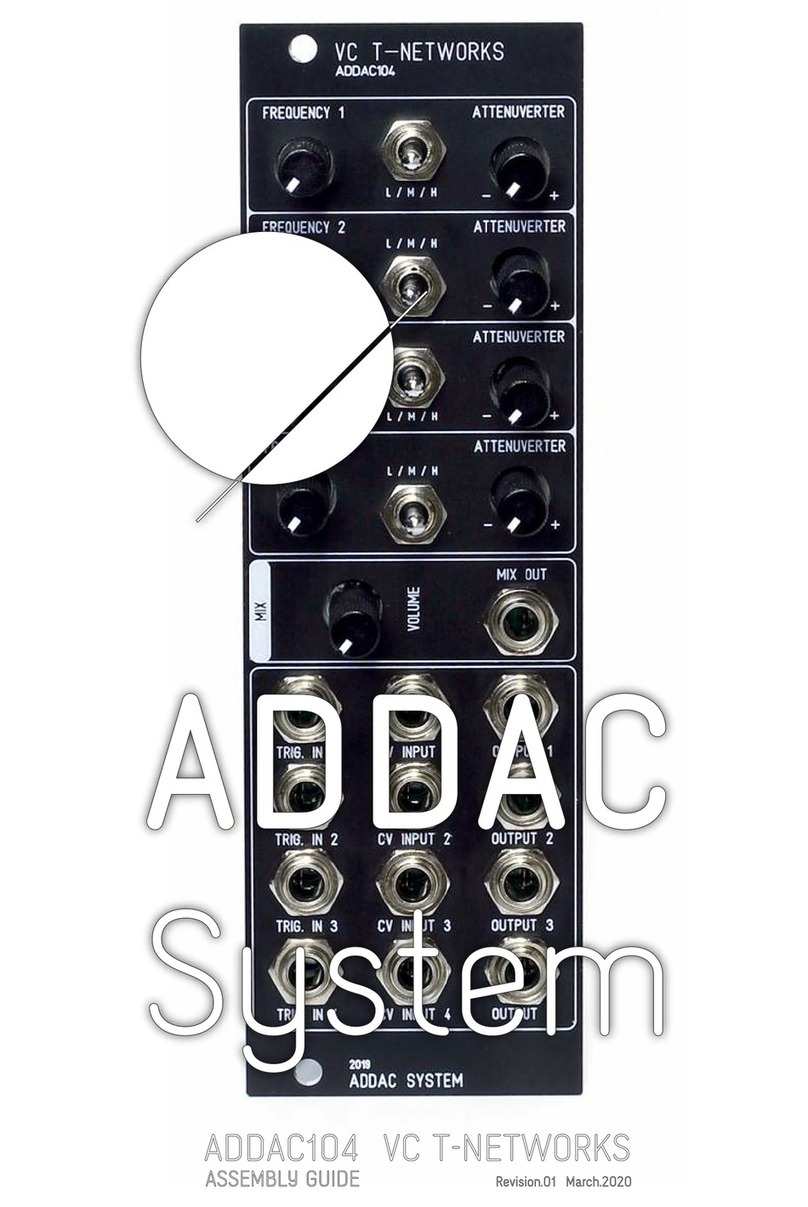
ADDAC System
ADDAC System ADDAC104 Assembly guide

hexinverter
hexinverter Mutant Hihats user guide
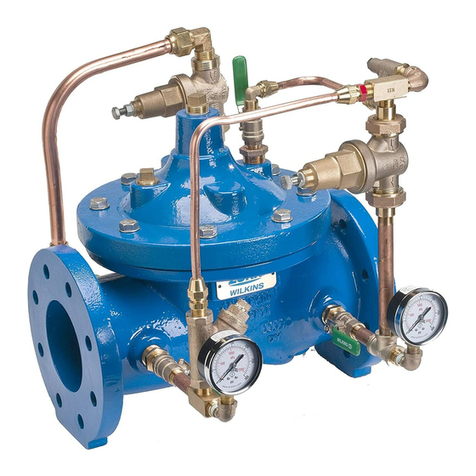
Zurn Wilkins
Zurn Wilkins 6-ZW209HP Installation, Troubleshooting, Maintenance Instructions