Brofer MDF25L User manual

2
FIRE DAMPERS CERTIFIED ACCORDING TO
EN 15650 SERIE MDF25L
0497/CPR/5136
INDEX
1. SPECIFICATIONS/GENERAL INFORMATION pag 3
2. NORMATIVE REFERENCES 3
3. PRECAUTIONS FOR HANDLING AND INSTALLATION 4
4. MAINTENANCE 4
5. WALL INSTALLATION 5
6. CEILING INSTALLATION 5
7. LIGHT WALL INSTALLATION 6
8. SUGGESTIONS 6
9. OPERATING CONTROLS 7
10. MECHANICAL FUSE REPLACEMENT 8
11. OPERATION DATA AND WIRING MANUAL CONTROLS 9
12. OPERATION DATA AND WIRING MOTORIZED CONTROLS 10

3
1. SPECIFICATIONS/GENERAL INFORMATION
Fire damper suitable for installation on a wall, light wall and ceiling made from duct and galvanized steel compo-
nents, calcium silicate blade mono slab sp. 25 mm with perimeter seals to ensure sealing requirements to cold and
hot smoke. The control device ( manual with electromagnetic release or motorized ) consists of a plate removable and
replaceable even after installation, on which they are installed all the elements necessary for the proper operation and
functioning of the fire damper; the particular geometry of the control mechanism, prevents that the pressure present
in the duct (up to 500 Pa) opening the blade if not acting directly from the reset lever. When installation is completed,
the command will be out of the masonry simplify any post-installation actions. The dampers, installed according to
the instructions in this manual , are used in HVAC systems by restoring the partitioning between two rooms, ensuring
perfect insulation from heat and smoke seal. The installer has the obligation to follow the installation procedures
and use of the equipment described in this manual, in order to comply with the same conditions as the samples
to be tested. Any deviation from the instructions, affect the validity of the certification of the product and the
declaration of correct installation.
2. NORMATIVE REFERENCES
Fire dampers tested according EN 1366/2 and classified according to EN 13501/3.
Legend
E = integrity I = thermal insulation S = smoke seal
Ve= vertical installation ho= horizontal installation io = side exposed to fire indifferent
MA = manual reset device SE = device with servomotor
CLASSIFICATION OF RESISTANCE
SUPPORT EI 120 S - 500 Pa EI 90 S - 500 Pa
Aerated concrete wall thickness 100 mm
(Vei o)
from 100x200 to 800x600
MA/SE
from 100x200 to 800x600
MA/SE
Aerated concrete slab thickness 150 mm
(hei o)
from 100x200 to 800x600
MA/SE
from 100x200 to 800x600
MA/SE
Gypsum plasterboards type F wall thickness 100 mm*
(Vei o)
from 100x200 to 800x600
MA/SE
from 100x200 to 800x600
MA/SE
Gypsum plasterboards type F thickness 100 mm
(Vei o) -from 100x200 to 800x600
MA/SE
* Need to use thermo expanding gasket model LFC

4
3. PRECAUTIONS FOR HANDLING AND INSTALLATION
CAUTION!
•All operations of handling and installation shall be made with the blade of the fire damper in the closed position
(our standard delivery).
•All operations of connection power line must be performed by qualified service personnel.
•Keep clean the connecting end from residues of cement to securely connect the rest of the duct.
• Avoid any deformation of the duct and / or obstacle inside the duct which may prevent the successful rotation of
the blade.
•Check that there are no external obstacles (cables, pipes, etc...) to prevent the correct operation of the controls
outside of the duct.
•Keep the most accessible as possible to the control side in order to ensure the necessary space usage and mainte-
nance of the damper.
4. MAINTENANCE
Is advisable to periodically run a check the correct operation of the actuating and signal the damper. In particular,
check the correct and complete opening and closing of the blade: for the operation of the controls follow the instruc-
tions listed “CONTROL OPERATION.” Also check that the warning devices at the beginning and ending are in good
condition and working properly.
DIMENSIONAL
MDF 25 L Istruzioni di installazione e uso MDF 25L (rev.1-01/2016)
brofer.it pag. 3/7
MANUTENZIONE
Non è richiesta particolare manutenzione. E’ comunque consigliabile eseguire periodicamente un controllo del corretto
funzionamento dei dispositivi di azionamento e segnalazione della serranda. Verificare in particolare la corretta e
completa apertura e chiusura della pala di otturazione: per l’azionamento dei comandi attenersi a quanto indicato a
pagina 4 nel paragrafo “FUNZIONAMENTO COMANDI”. Controllare altresì che i dispositivi di segnalazione di inizio e
fine corsa (dove presenti) siano in buono stato e funzionino correttamente.
DIMENSIONALI
INSTALLAZIONE IN PARETE IN MURATURA
1 –Prima di procedere con l’installazione, verificare l’integrità della serranda, il corretto posizionamento dell’otturatore in
posizione di chiusura e il funzionamento del comando
2 –Prevedere un’apertura sulla parete (fig.1) avente dimensioni maggiorate rispetto alle dimensioni nominali della
serranda (vedi tabella 1 in base al tipo di installazione scelto).
3 - Posizionare al centro dell’apertura la serranda e facendo attenzione che la pala in posizione di chiusura sia parallela
alla parete. Mantenere l’asse di rotazione della pala orizzontale o verticale come da prove eseguite. Rispettare le
sporgenze indicate in fig.2 –tabella 1
4 –Fissare la serranda alla parete con le apposite staffe, successivamente riempire con malta cementizia classe M10
per l’installazione (fig.3).
Fig. 1
Fig. 2
Riempimento
Malta cementizia
Classe M10
Fig. 3

5
5. WALL INSTALLATION
1 Before proceeding with the installation, verify the integrity of the damper, the correct positioning of the blade in the
closed position and operation of the command.
2Provide an opening in the wall (Figure 1) having larger dimensions than the nominal size of the damper (see table
1 according to the type of installation).
3Positioning the damper at the center of the opening and making sure that the blade in the closed position is parallel
to the wall. Maintain the axis of rotation of the blade horizontally or vertically as from tests carried out.
Observe the projections shown in Figure 2 Table 1
4 Fix the damper to the wall using the brackets, then fill with cement mortar class M10 (Fig. 3.1)
6. CEILING INSTALLATION
1 Before proceeding with the installation, verify the integrity of the damper, the correct positioning of the blade in the
closed position and operation of the command.
2Provide an opening in the floor (fig.1A) having larger dimensions than the nominal size of the damper (see table 1
according to the type of installation).
3 Place the center of the opening the damper, taking care that the plane containing the blade in the closed position
is parallel to the slab, and comply with the protrusions shown in fig.2 Table 1.
4 Fix the damper to the floor with the brackets, then fill with cement mortar class M10.
fig. 1 fig. 2
fig. 2A
fig. 3
Fill with mortar
class M10
fig. 1A fig. 3A
fill with mortar
class M 10

6
7. LIGHT WALL INSTALLATION
1 Before proceeding with the installation, verify the integrity of the damper, the correct positioning of the blade in the
closed position and operation of the command.
2Provide an opening in the wall (fig.1A) having larger dimensions than the nominal size of the damper (see table 1
according to the type of installation).
3Apply band expanding around the entire perimeter of the damper. Place the center of the opening the damper and
making sure that the blade in the closed position is parallel to the wall. Maintain the axis of rotation of the blade
horizontal as from tests carried out. Observe the projections indicated in fig.2A Table 1.
4Fix the damper to the wall using the brackets, then fill with cement mortar class M10 and dab from both of the sides
of the wall with the plasterboard thickness 12.5mm.
fig. 2Afig. 1A fig. 3A
perimeter expanding band
fill with mortar
class M 10
plasterboard
dab thickness
sp. 12,5 mm
Table 1
Certified Installation P (mm) S1 (mm) S2 (mm) Quote X Quote Y
Wall - aerated concrete 100 175 25 120 120
Light wall - Plasterboard 150 150 0 120 120
Ceiling - aerated concrete 100 175 25 100 100
8. SUGGESTIONS
After installation it is recommended to perform a function test by checking the correct rotation of the blade and the
efficiency of the command (manual or motorized). It can be done in manual version rearming, with the lever, the
damper and pressing the test button simulating so the operation. In the motorized version act on the lever of the
thermoelectric fuse.

7
9. COMMAND OPERATION
Manual command
Rearmament:
•From the unlocked position (Figure 4), where the indicator on the rearmament lever is positioned on the symbol] - [,
turn the lever 90 ° clockwise making sure that the command locks into place opening (fig.5 ), the indicator is located
on the lever on the symbol] I [.
Manual closure:
•Turn the button highlighted in Figure 6.
Manual control with electroma
Reset:
• Activate the state of the electromagnet opening and closing the power circuit of the same depending if the model of
electromagnet is normally energized or de-energized.
•Lift the metal lever (fig. 7 / fig. 8) on the cover of the control unit until it stops.
• Reset the damper as shown in the previous section.
Manual opening (test):
•Operate the test button shown in fig.6.
Closure normally energized electromagnet:
•Power the electromagnet (to perform a
function test unhook the power supply)..
Closure normally de-energized electromag-
net:
•Switch off the power of the electromagnet
(to perform a function test hook the power
supply).
fig. 4 fig. 5 fig. 6
fig. 7 fig. 8
Operation with servo motor
Reset:
• Insert into the slot on the servomotor appropriate key supplied and turn it clockwise until the indicator in position
90 °.
• Perform a fast rotating counterclockwise to lock the actuator in the open position.
Manual opening (test):
• Insert into the slot on the servomotor appropriate key supplied and turn it counter-clockwise approximately ½ turn
in order to engage the return spring that will bring in automatic servo motor in the closed position and the indicator
at 0 ° position.
Motorized opening (test):
• Turn the lever on the thermoelectric fuse located next to the servomotor or disconnect power.

8
10. MECHANICAL FUSE REPLACEMENT
CAUTION!
All operations of connection or maintenance must be carried out with the damper closed and de-energized.
Operation
Fuse replacement is required every time the peak temperature within the duct, has exceeded the specified degrees
Celsius on the same fuse. A tab shows the status of the fuse (fig. 9), when the body disappears into the plastic fuse
holder (fig. 10), it is necessary to replace the fuse.
fig. 9 fig. 10
MDF 25 L Istruzioni di installazione e uso MDF 25L (rev.1-01/2016)
brofer.it pag. 6/7
SOSTITUZIONE DEL FUSIBILE MECCANICO
Avvertimento !
Tutte le operazioni di collegamento o manutenzione devono essere effettuate con serranda chiusa e in assenza di
tensione.
Funzionamento
La sostituzione del fusibile si rende necessaria ogni volta che la temperatura di picco all’interno della condotta, abbia
superato i gradi centigradi indicati sul fusibile stesso. Una linguetta indica lo stato del fusibile (fig.9), quando scompare
dentro il corpo in plastica porta fusibile (fig.10), è necessaria la sostituzione del fusibile.
Procedimento:
- Assicurarsi che la serranda sia disarmata verificando visibilmente che l’indicatore sulla leva indichi il simbolo ]-[
presente sul carter. In caso contrario, agire sul pulsante di test per chiudere manualmente la serranda.
- Rimuovere la copertura plastica trasparente svitando la vite di fissaggio centrale (fig.11)
- Svitare le 2 viti con testa a croce ed estrarre il meccanismo di rilascio dalla piastra.
- Sostituire il fusibile comprimendo la molla e agganciandolo ai due perni sporgenti (fig.12)
Fig. 9
Fig. 10
Fig. 11
Fig. 12
Copertura
trasparente
Vite di fissaggio
centrale
Vite di fissaggio
meccanismo
di rilascio
Procedure:
•Make sure the damper is unarmed
verifying visibly that the indicator on
the lever indicates the symbol] - [on
the carter. Otherwise, act on the test
button to manually open the damper.
• Remove the clear plastic cover by
unscrewing the central fixing screw
(fig. 11).
•Unscrew the 2 screws and remove the
release mechanism from the plate.
•Replace the fuse by compressing the
spring and hooking the two protru-
ding pins (fig. 12).
fig. 11
fig. 12
Central
fixing screw
Fixing screw
release
mechanism
Clear plastic
cover

9
11. OPERATION DATA AND WIRING MANUAL CONTROLS
Microswitches start and end of stroke
The signaling devices stroke end FCU and beginning stroke DCU are both
switches with two contacts independent of the type NC + NO. The first nor-
mally closed (NC) contacts 1 and 6, while the second normally open (NO)
contacts 2 and 5. At the click of the switch contact status is reversed, the
NC contact opens and the NO contact closes. Ex: contacts 1 and 6 (NC) is
connected to the relay that controls power to the fan, while contacts in 2
and 5 (NO) is connected to a warning light alarm. In this case the closure of
the damper, the fan will turn off and turn on the light. Technical data of the
switches.
- Cable section: 2.5 mm ² rigid - flexible with ferrule 1.5 mm² Operating tem-
perature: from - 25 °C to + 70 °C
Electromagnet device
If necessary, you can equip the damper of an electromagnet that allows you
to anticipate the closing of the damper with respect to the intervention of the
thermal fuse. Depending on the type of electromagnet (normally energized or
de-energized), sending or interrupting the electrical signal power, the damper
will close preventing the diffusion of cold smoke. In case of fire, the raising
of the temperature, the thermal fuse has priority of action compared to the
electromagnet. Technical data of the magnets.
- Holding force: 120N
- Degree of protection (En 60529): IP40
- Power consumption at 20 ° C: 1.6 W (lack) - 3.5 W (output)
- Operating Temperature: -30 ° C to +85 ° C
Start of the
race blade open
Electromagnet
MD
Power supply
DC 24 V or CA 20 V
End of the race
blade closed

10
12. OPERATION DATA AND WIRING MOTORIZED CONTROLS
The operation of the motor is given by the connection to the electricity network
(contacts 1 and 2) which brings the blade of the damper in the open position
and simultaneously charging the internal spring which stores the force re-
quired to close the duct in case of alarm or black- outs. The connection of the
two switches inside the motor can make flexible the rest of the system. For
example, by connecting the contacts S1 and S2 will be possible in the event
of closure of the damper, can shut down the unit for ventilation, while the
contacts S4 and S6 turn on a warning light. The thermoelectric device is com-
posed of three fuses: Fire dampers then become sensitive to the temperature
inside the duct (with fuses Tf and Tf 2 3 which can be substituted) and the
ambient temperature (Tf with fuse 1). The device cuts off in an irreversible
way, if not replacing the fuses , the supply line so that the servomotor leaving
overs, with the spring force, the blade in the closed position. It also has a
manually operated key that simulates the operation of the fuses allowing
testing of the damper. Its position outside the damper and fastening with
screws allows a safe temperature control and easy maintenance.
- 24V Connection: transformer
- 230V Connection: for the interruption
of the network must incorporate a device
which disconnects the phase conductors
(contacts opening min. 3mm)
Thernal fuse
Table of contents
Popular Fan manuals by other brands
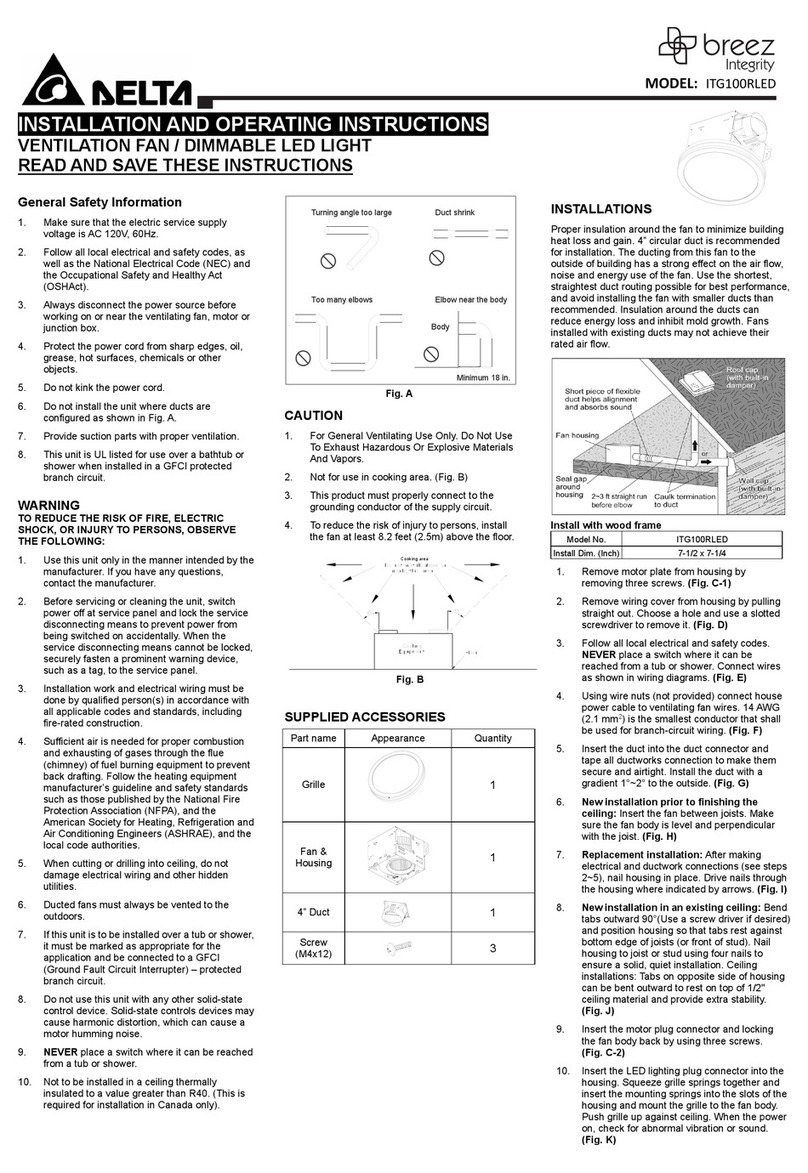
Delta
Delta BreezIntegrity ITG100RLED Installation and operating instructions

German pool
German pool EFU-108 user manual

Ebmpapst
Ebmpapst A3G710-AO85-35 operating instructions
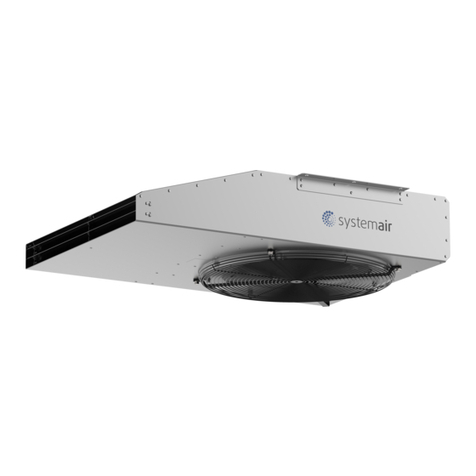
System air
System air IV Installation and operating instructions
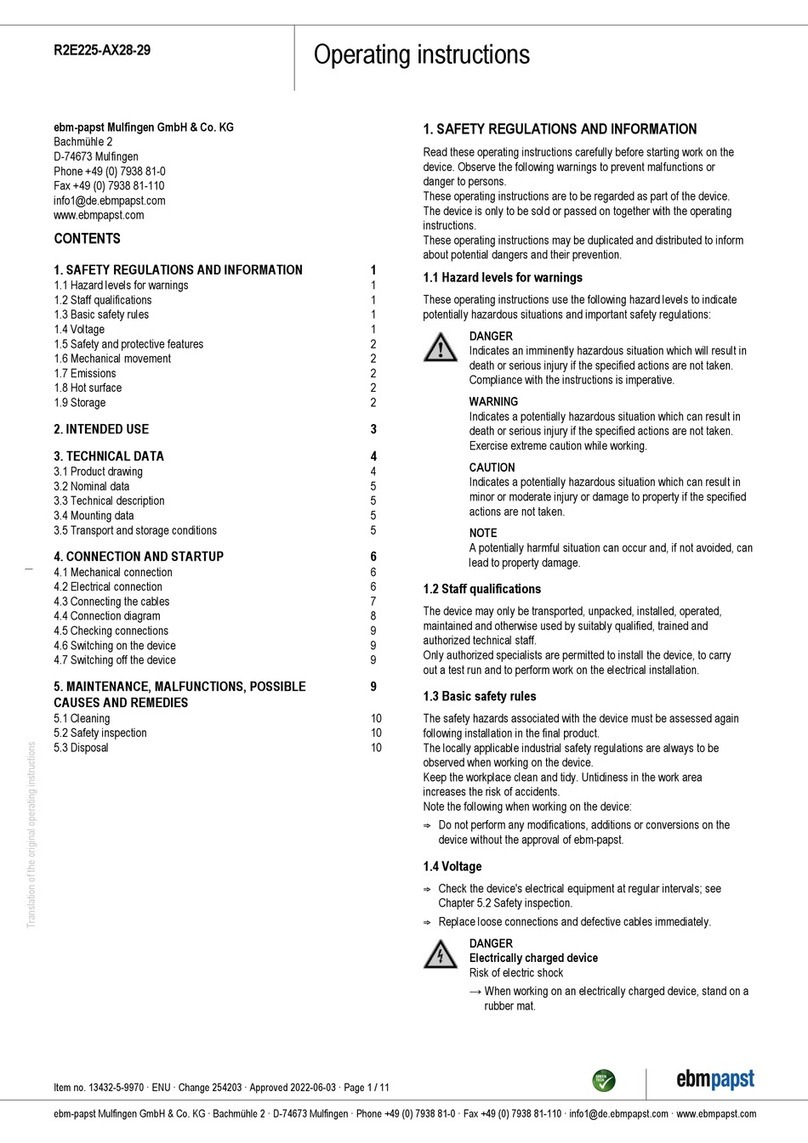
Ebmpapst
Ebmpapst R2E225-AX28-29 operating instructions

Ebmpapst
Ebmpapst A4E450-AP01-20 operating instructions

Ebmpapst
Ebmpapst W1G250-HH37-52 operating instructions
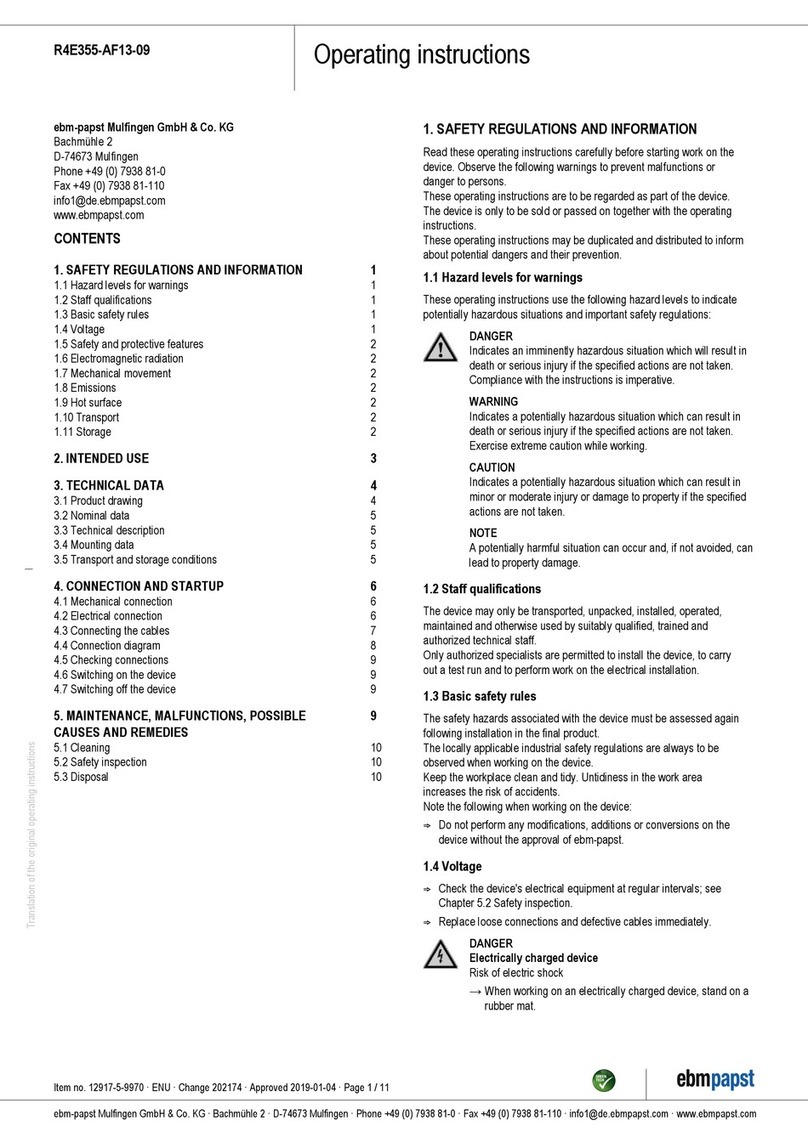
Ebmpapst
Ebmpapst R4E355-AF13-09 operating instructions

Ebmpapst
Ebmpapst A2D200-AA04-44 operating instructions

Ebmpapst
Ebmpapst D2E133-CI33-99 operating instructions

Air Naturel
Air Naturel air&me Naos user manual

Delta
Delta Breez GreenBuilder GBR100LED-DECOR instructions