BSi ROFI Specification sheet

QM-Nr: FB_BMA_01-R-0804engl_3
Erstellt/
Prepared
: am/
on:19/11/2015
Genehmigt/
Approved: am
/
on19/11/2015
1 / 16
b ROFI S.A.R.L.
OPERATING AND INSTALLATION MANUAL
ROFI
Standard Valves
Content Page
1 Introduction...............................................................................................................................3
2 General In ormation ..................................................................................................................4
2-1 Marking..................................................................................................................................5
2-2 Notes on possible dangers .....................................................................................................5
2-2-1 Significance s mbols and explanator notes on safet information .....................................................
5
2-2-2 Qualified Personnel .............................................................................................................................
6
2-2-3 Notes to safe use as directed ..............................................................................................................
6
2-2-4 Notes to safe operation........................................................................................................................
6
2-2-5 Notes to dangerous operation .............................................................................................................
6
3 Notes to sa e transport and storage ........................................................................................7
3-1 Transport ...............................................................................................................................7
3-2 Storage ..................................................................................................................................7
4 Details on sa e installation .......................................................................................................7
4-1 Planning and installation ........................................................................................................8
4-1-1 Installing position .................................................................................................................................
9
4-1-2 Spindle operated Valves......................................................................................................................
9
4-1-3 Non-return Valves................................................................................................................................
9
4-1-4 Strainers ..............................................................................................................................................
9
4-2 Differential pressure ...............................................................................................................9
4-3 Temperature changes ............................................................................................................10
4-4 Additional instructions for installation ......................................................................................10
4-4-1 Flanged Valves....................................................................................................................................
10
4-4-2 Valve with butt-weld or socket-weld ends ............................................................................................
10
4-4-3 Gear operated and actuated Valves ....................................................................................................
11
4-4-4 Insulation .............................................................................................................................................
11
4-4-5 External moving parts ..........................................................................................................................
11
5 Valve operation .........................................................................................................................11
5-1 Bolt torques, shutting and opening torques.............................................................................11
5-2 Cleaning (Pickling) .................................................................................................................11
5-3 Venting ..................................................................................................................................12
5-4 Heating and cooling rates.......................................................................................................12
5-5 Additional operating rules .......................................................................................................12
5-6 Function testing......................................................................................................................12

QM-Nr: FB_BMA_01-R-0804engl_3
Erstellt/
Prepared
: am/
on:19/11/2015
Genehmigt/
Approved: am
/
on19/11/2015
2 / 16
b ROFI S.A.R.L.
Content Page
5-7 Checking during and after first operation ................................................................................12
6 Maintenance ..............................................................................................................................13
6-1 Gland packing, Bonnet-flange-seals and Replacement ...........................................................13
6-2 Recommended lubricants.......................................................................................................14
6-3 Lubricant of spindle thread .....................................................................................................14
7 Troubleshooting table...............................................................................................................15
8 Spare parts ................................................................................................................................16
9 Guarantee / Warranty................................................................................................................16

QM-Nr: FB_BMA_01-R-0804engl_3
Erstellt/
Prepared
: am/
on:19/11/2015
Genehmigt/
Approved: am
/
on19/11/2015
3 / 16
b ROFI S.A.R.L.
1. Introduction
Industrial valves made b compan ROFI
S.A.R.L. are designed according to International norms such
as DIN-Standards, EN-Standards and according to the Technical Rules like AD and the European
Pressure Vessel Guideline 97/23/EG, etc.. Design, manufacture and testing of these valves was carried
out on condition that the valves are operated under normal operating conditions. Normal operating
conditions contain for example the following:
• operation with liquid or gaseous media, without special corrosive, chemical or abrasive influences.
• frequenc of temperature-change of app. 3°C – 6°C per minute
• usual flow rates, depending on the kind of medium and the range of application of the valve.
• operation without additional outer influences like pipeline-forces, vibrations, wind load stressing,
earthquake, corrosive environment, fire, operation load stressing, disintegration pressure of
unstable fluorides, etc.
If the purchaser expects stresses deviating from the normal operating conditions he has to indicate these
requirements unambiguousl and completel in the enquir as well as in the order. This would allow us, as
the valve manufacturer, to work out corresponding measures and to suggest them to the customer. These
measures could be for example:
• special choose of the bod material.
• higher wall-thickness.
• protection of areas which are endangered b wear.
• special gaskets and bolt connections.
• special operation instructions depending on the medium and the kind of operation.
• special coatings
• additional equipment to avoid excessive overpressure.
• special design for control operation,
• etc.
During planning and installation of the pipeline the customer should take measures which minimize
additional dangers and pressures on the valves, on the piping s stem and on the environment, for
example b :
• installation of vibration dampers
• consideration of a securit final position in case of breakdown of energ
• taking measures to ensure the safe drainage of dangerous media in case of leakage,
• etc.

QM-Nr: FB_BMA_01-R-0804engl_3
Erstellt/
Prepared
: am/
on:19/11/2015
Genehmigt/
Approved: am
/
on19/11/2015
4 / 16
b ROFI S.A.R.L.
The guidance for installation, operation and maintenance of ROFI
Valves contained in this manual, is
intended for use with our standard products. It ma also be used with special valves provided the special
additional instructions are observed. These are available on request. These instructions should ensure
trouble-free fitting and safe operation of our valves, and form also the basis for an guarantee claims that
might arise.
Attention !
In terms o their hazard potential, valves and associated ittings should be treated on a
par with pressure vessels. Their design, installation and maintenance should there ore be based
not just on these instructions but also on the relevant Accident Prevention Regulations, Codes o
Practice and specialist literature. The handling and use o valves and ittings should only be
entrusted to properly trained personnel.
2. General In ormation
The design of the valve depends upon the use and is beneath the responsibilit of the bu er. With the
application for mediums and temperatures which differ from the t pe description, it has to be consulted
with the manufacturer or the distributor respectivel . The operating instruction is made for valves - gate
valves, globe valves, ball valves, swing check valves, strainers. It refers to valid standards and rules and
regulates order, fitting and operation. The instructions cannot replace qualified personnel. Technical
changes at the valves as well as changes of this description are in the responsibilit of the manufacturer.
All valves are provided according to DIN EN 19 with sprinkled or rather stamped signs for the nominal
pressure (PN), nominal diameter (DN), construction materials, manufacturer's mark, and as far as
necessar with a directional marker. Before leaving the factor the are tested according to DIN 3230 (or
corresponding special agreements) with 1,5 fold nominal pressure for safet and tightness of the bod b
internal pressure test. The seal is tested in an case, if nothing else has been agreed, with 1-fold nominal
pressure.

QM-Nr: FB_BMA_01-R-0804engl_3
Erstellt/
Prepared
: am/
on:19/11/2015
Genehmigt/
Approved: am
/
on19/11/2015
5 / 16
b ROFI S.A.R.L.
2.1. Marking
Additional to the marking according to EN 19, the nameplate on the product is containing the following
information:
• Name of manufacturer
• T pe
• Epsilon in hexagon
• II 2G c X T
2
)
• CE-Mark
2
) The highest surface temperature of the valve is given b the fluid and b the existing ambient temperature and has
to be defined b the end-user.
Letter X:
The end-user has to mention the highest surface temperature of the unit in relation to the highest temperature of the
fluid clearl on the valve’s nameplate.
B marking the product with the CE-mark we declare the conformit with the European Pressure
Equipment Directive 97/23/EG.
B marking these products of group II - belonging to the product-categor 2G referring to chapter II article
8 according to Directive 94/9/EG - with the EX mark, we declare the conformit with the ATEX Directive
94/9 EG for the use in hazardous areas.
2.2. Notes on possible dangers
2.2.1. Signi icance symbols and explanatory notes on sa ety in ormation
In these Operating and Installation Instructions dangers, risks and items of safet information are
highlighted to attract special attention. Information marked with the above s mbol and
“ATTENTION!”
describe practices, a failure to compl with which can result in serious injur or danger of death for users
or third parties or in material damage to the s stem or the environment. It is vital to compl with these
practices and to monitor compliance. All other information not specificall emphasised such as transport,
installation, operating and maintenance instructions as well as technical data (in the operating instructions,
product documentation and on the device itself) must also be complied with to the fullest extent in order to
avoid faults which in turn can cause serious injur to persons or damage to propert .
ATTENTION
! Warning of general danger

QM-Nr: FB_BMA_01-R-0804engl_3
Erstellt/
Prepared
: am/
on:19/11/2015
Genehmigt/
Approved: am
/
on19/11/2015
6 / 16
b ROFI S.A.R.L.
2.2.2. Quali ied Personnel
Are persons who are familiar with installation, assembl , start-up and operation of the product and have
the qualifications corresponding to their responsibilities.
2.2.3. Notes to sa e use as directed
The valves are mainl used to shut-off, to control, to prevent back-flow and to filter diverse fluids in piping
s stems and are onl allowed to use in-between the frame of their technical data.
Swing Check Valves and Check Valves can onl be used with fluids which doesn’t cause an explosive
mixture or atmosphere in the interior.
Attention !
• Re er to the data sheet or applications, limits on use and possibilities.
• Certain media require or preclude the use o special materials.
• The valves are designed or standard operating conditions. I conditions exceed these
requirements, e.g. aggressive or abrasive media, the operator should state the higher
requirements when ordering.
2.2.4. Notes to sa e operation
According to Categor 2, ROFI
Valves can be used in hazardous areas of zone 1 or 2. These are areas
where an explosive atmosphere of gases, steams and fogs occur from time to time
2.2.5. Notes to dangerous operation
Electrostatic insulating fluids can cause different charges in the fluid when flowing through the valve.

QM-Nr: FB_BMA_01-R-0804engl_3
Erstellt/
Prepared
: am/
on:19/11/2015
Genehmigt/
Approved: am
/
on19/11/2015
7 / 16
b ROFI S.A.R.L.
3. Notes to sa e transport and storage
3.1. Transport
When loading or unloading ensure that the valves are not thrown or subjected to sudden knocks. Large
valves should be handled with hemp or s nthetic ropes slung to the oke arms or the bonnet flange.
Valves with actuators should be slung using a three-point suspension at the main connection nozzle and
the oke arms or oke head (note centre of gravit ). Special e ebolts must be used when supplied with
heav valves.
To avoid damages at the sealing areas during transport and storage the valves are supplied in closed
position – except of Ball Valves and Swing Check Valves. Locking caps defend the flange openings from
pollution. The valves ma not be damaged upon transport and storage. For this reason the are coated
against corrosion with a primer coat. For further protection the valve has to be adapted in the plant
according to the operating conditions.
3.2. Storage
On site the valves must be stored so as to be protected against mechanical damage and/or corrosion. The
preferable storage condition is in closed rooms with ambient temperature. Flanges or weld ends can be
sealed using plugs, lids, plastic caps or oil paper. Internal surfaces can be treated with preservatives or
moisture absorbers. The protective packaging we provide must be left intact during storage and removed
prior to installation or operation respectivel .
4. Details on sa e installation
During installation and operating, the corresponding valve manuals have to be taken into consideration.
An electro-static conductive connection from the valve to the earthing-potential must be given.
During installation of electrical valves, EN 60079-14 has to be taken into consideration.
Special requirements of the t pe testing certificates for the installed valves, e.g. electric actuators have to
be taken into consideration.
The valve-actuators has to be conform to the European Directive 94/9/EG (ATEX).
In explosive areas, the electrical equipment installed must be in accordance with the corresponding
categor (2 / 3) – EN 50014.
The installation of the electrical device must be in accordance with DIN VDE 0100 and EN 60079.

QM-Nr: FB_BMA_01-R-0804engl_3
Erstellt/
Prepared
: am/
on:19/11/2015
Genehmigt/
Approved: am
/
on19/11/2015
8 / 16
b ROFI S.A.R.L.
4.1. Planning and installation
The designer, contractor and/or end user are basicall responsible for positioning, installing and operating
the valves in the piping s stem. Here are some notes for guidance:
Attention !
Planning and installation errors can a ect the proper operation o valves and may even
constitute a major hazard potential (e.g. incorrect positioning o check valves, wrong direction o
low in gate valves with relie port, etc.)
A number of possible causes of damage are described below in chapter 7, but the list does not require to
be complete due to the great man possible planning, installation and maintenance errors. If in doubt, ask
us. Permitted operating limits for valves are shown in the relevant pressure-temperature tables.
Before fitting the transport securing and locking caps at the flange openings have to be removed and the
valves have to be cleaned - especiall the sealing areas. Upon mounting it has to be paid attention to the
fact that all sealings are centred at the joining flanges. The pipe rela ing is to be done in such a wa that
harmful thrusts and bending stresses will be kept awa from the bod . While coating the plant, gland bolt
nuts and stems are not allowed to be painted. If construction work is still done near or above the valve,
this is to be covered from dust, sand, or part of building materials (e.g. with a plastic wrap).
Gate valves, Ball valves and Globe valves are fitted with vertical stem, because thereb the abrasion
appearing with movement and due to possible bending of stem (b the weight of wedge, sealing discs,
plugs, or the flow power) is reduced or the possibilit of seizing is largel diminished. The fitting of globe
valves is done with entering of the through flow medium under the plug, onl with globe valves with
pressure relief plug the entr has to be done over the plug (see marker). With gate valves it is irrelevant in
which direction the through flow is done.
Check valves in straightwa form can onl be fitted in horizontal pipelines.
Swing check valves and swing check valves with lever and weight can be fitted in horizontal or vertical
pipelines (medium from below).
Strainers must be fitted that wa that the screen shows down. Upon fitting the flow direction has to be
considered (directional marker).

QM-Nr: FB_BMA_01-R-0804engl_3
Erstellt/
Prepared
: am/
on:19/11/2015
Genehmigt/
Approved: am
/
on19/11/2015
9 / 16
b ROFI S.A.R.L.
4.1.1. Installing position
4.1.2. Spindle operated Valves
All spindle-operated valves are designed to "shut" when the hand-wheel is turned clockwise and "open"
when the hand-wheel is turned counter-clockwise. When the valve is fitted into a horizontal pipe-spool it
should be positioned with the spindle vertical or the bonnet flange horizontal so far as possible. When
spindle-operated valves (globe valves, gate valves etc.) are fitted with their spindle on the skew or pointing
verticall down, dirt particles can be collected inside the bod where the spindle passes through to the
packing gland. These particles can cause damage to the spindle, back seal or gland packing and this t pe
of position should therefore be avoided wherever possible. Bellows sealed valves should be fitted
verticall if possible. An other position can cause deposits in the folds of the bellows, and hence
premature wear.
4.1.3. Non-return Valves
Non-return valves can be fitted in pipe s stems horizontall , verticall or at an oblique angle. For vertical
or oblique fitting the valve will onl operate properl when the direction of flow is from bottom to top. For
horizontal or oblique positions the bonnet flange must be in a horizontal position in relation to the pipe
direction. In case of check valves with lever and weight or spring to close or damping device which are
fitted in a non horizontal piping it should be assured b reconstruction that the closing or damping device
action is not disturbed. Swing check valves with outside control mechanism, equipped with hinge and
counterweight, shock absorber or spring should be positioned in such wa that the shut-off functions of
these extra devices are alwa s secured.
4.1.4. Strainers
Before installing a strainer take into consideration about grade of filtering. Leave sufficient space to
remove the screen basket during installation in pipelines. Make sure that the trap is installed to suit the
direction of flow. The screen basket should never be at top, otherwise dirt will fall back into pipe. If water
hammer is possible due to condensation in steam lines, never install the trap with the screen basket at the
bottom, but install it in a horizontal wa .
4.2. Di erential pressures
As a rule globe valves are installed such that the shut-off pressure is under the disc. When using our
standard globe valves up to PN 160, ensure that the maximum allowable shut-off differential pressure
(pressure under the disc) corresponds to DIN 3356 Part 3. For greater shut-off differential pressures these
valves must be fitted with pre-lift disc and installed such that the pressure is above the disc. Opening of
the pre-lift disc pressurizes the connected s stem. Once the pressure is balanced, the valve's main shut-
off disc can be opened. In order to avoid undesirable pressure surges when opening large valves with
high differential pressures, or to warm up graduall the connected pipelines, suitable b passes opened
before the main valve should be provided.

QM-Nr: FB_BMA_01-R-0804engl_3
Erstellt/
Prepared
: am/
on:19/11/2015
Genehmigt/
Approved: am
/
on19/11/2015
10 / 16
b ROFI S.A.R.L.
4.3. Temperature changes
To prevent damage and leakage due to rapid heating, the valves should be provided with properl
designed b passes or drains that open at the right time. The usual temperature rise rates in power station
duties for example are of the order of 3-6 degrees C per minute. If more rapid warming rates are
anticipated, we should be consulted regarding the appropriate measures to be taken. Frequent operation
through broad temperature ranges at high rates of temperature change can lead to premature fatigue
(relaxation) of the bonnet flange bolts among other components. If in doubt, ask our advice.
4.4. Additional instructions or installation
As a general rule the direction of flow is marked b arrows in accordance with DIN EN 19. In case of
doubt, refer to the relevant sectional drawings. Alwa s allow for adequate access clearance in the
planning and installation phase for eas assembl and disassembl of internal valve parts. Valves should
never be taken as fixed reference points within pipe s stems, and substantial pipe loadings on valves
should therefore be avoided. Exceptions to this rule are subject to our specific approval for each individual
case. It has to be on a case-b -case basis because the forces resulting, for example, from shear, bending
and torsional stresses as well as temperature gradients var according to dut and installation, and occur
in a variet of combinations. We are therefore not able to make an generalizations. Before fitting the
valve in position, remove the flange- or butt weld end protectors and moisture absorbers, if provided. The
valve must be free from foreign matter of an nature. Cleanliness is the cardinal rule when fitting valves. If
the pipe ends require machining, chips and other foreign matter must be carefull removed. The pipe ends
must be properl aligned so as to prevent the valve being subjected to unnecessar strain. Brickla ing or
painting should not be carried out in the vicinit of installed valves until stuffing boxes, spindles and valve
position indicators (if fitted) have been properl protected against soiling. Valves are despatched from our
works with a high shut-seal propert . This is a qualit feature that can onl be maintained if care is taken
during installation and subsequent operation to prevent the ingress of foreign matter into the valve and
hence damage to seats and other areas.
4.4.1. Flanged Valves
The sealing faces of flanged valves must be clean and in good condition. Before bolting-down, flanges
must be correctl aligned. When bolting-down, all flange boreholes must be used at all times. For initial
fitting, threads can be smeared with graphite or mol bdenum-di-sulphide to stop seizure - do not use oils
or greases. Never use damaged parts such as bolts, nuts or washers. Make sure that materials are
suitable and correct for the job. Tighten bolts evenl and in cross-sequence using the correct tools to the
correct torques (see chapter 5.1).
4.4.2. Valve with butt-weld or socket-weld ends
The piping contractor is responsible for welding the valves into the pipeline and an necessar heat
treatment. Gate and Globe valves should be lightl closed to prevent damage to the seating surfaces and
stem caused b thermal expansion during the socket welding process. Never attach the welding cable
(opposite pole) to the bonnet, spindle or an other places on the valve assembl ! This could cause spots
of arcing on the spindle or seat faces. The weld cable should be attached to a bright area on the valve
bod or, even better, to the pipe itself. For valves with socket weld ends, the socket depth of the pipe ends
should be selected in accordance with codes of practice, and unacceptable weld-seam stresses prevented
b leaving a gap between pipe end and socket seat.

QM-Nr: FB_BMA_01-R-0804engl_3
Erstellt/
Prepared
: am/
on:19/11/2015
Genehmigt/
Approved: am
/
on19/11/2015
11 / 16
b ROFI S.A.R.L.
Weld the connection as ollows:
1) Remove all grease, oil or paint from the pipe that is to be welded into the valve and from the valve
end connections.
2) Insert the pipe into the valve end connection until it bottoms out in the socket weld bore.
3) Withdraw the pipe 1/16” so that a gap remains between the pipe and the bottom of the socket
weld bore to prevent cracks (ASME B16.11). Tack the pipe into the valve and complete the fillet
weld.
NOTES:
A minimum o two layers should be used or all socket welds. This will decrease the chance o
leaking even i one pass contains a weld de ect.
- Where possible, welding should be done in the flat or horizontal position. Where vertical welding is
necessar , progression should be upward (vertical down welding is prone lack-of-fusion).
4.4.3. Gear operated and actuated Valves
These valves must be fitted with their spindles vertical, otherwise the drive must be additionall supported
in such a wa that it is able to follow an changes in position of the valve during operation (caused b the
piping s stem). If no extra support or suspension is desired, this must have our specific approval for the
case in question. The direction of rotation: clockwise = shut; counter clockwise = open, also applies for
back gear hand wheels and the manual emergenc operation of electric actuators. The specific torques of
electric actuators normall are set in the factor . The closing of ROFI
valves is controlled b torque
switches, eventuall additionall secured b limit switches. Opening of the valve is generall controlled b
limit switches onl . Wiring diagrams for the actuators are present in their connection boxes. The guidelines
of the actuator manufacturer alwa s have to be respected. In case of gate valves with pressure sealed
bonnets an end stop installed on the stem will prevent the wedging of the discs in case of a too high
closing torque of the actuator. The shut-off action of the electric actuator in the closing direction is
controlled b travel limitation; - the torque switch gives additional securit .
4.4.4. Insulation
If valves are insulated, care must be taken to ensure that the stuffing box area and pressure relief devices
remains accessible for checks during operation.
4.4.5. External moving parts
Valves with external moving parts e.g. swing check valves with lever and counterweight, alwa s have to
be secured b means of protective caps.
5. Valve operation
5.1. Bolt torques, shutting and opening torques
If required, we will give advice on the bolt tightening torques as well as the opening and closing forces of
valves depending on t pe and dut (pressure-temperature).
5.2. Cleaning (Pickling)
Owing to the wide variet of pickling processes it is not possible to make an generalization on this point.
Suffice it to sa that the process must be selected in accordance with the materials to be pickled. The
pickling contractor will be responsible for the pickling medium and process. The valve should be full

QM-Nr: FB_BMA_01-R-0804engl_3
Erstellt/
Prepared
: am/
on:19/11/2015
Genehmigt/
Approved: am
/
on19/11/2015
12 / 16
b ROFI S.A.R.L.
opened during pickling to prevent the pickling medium penetrating the packing area. Flushing should be
done with the valve half-shut to facilitate thorough flushing of the internal surfaces.
5.3. Venting
In accordance with the relevant Accident Prevention Regulations (UVV) valves and fittings should be
vented b means of speciall fitted vent pipes or stuffing box connections. Venting b slackening off the
bonnet flange or the stuffing box gland is not permitted and can cause danger. If vents are required as
non standard extra, we recommend that these be fitted in our works.
5.4. Heating and cooling rates
To avoid damaging the valve bod material or flange connections the normal plant-related heating and
cooling rates must be observed. If in doubt, consult us (see chapter 4.3)
5.5. Additional operating rules
Manual shut-off valves are right-hand or clockwise shutting. Back gears and remote drives are designed to
retain this direction of rotation. Because valves are frequentl subjected to high temperatures and develop
surface and radiated heat as a result, protective clothing (especiall gloves) should be worn. This is also
recommended when operating valves where leaks can allow hazardous media (e.g. steam, acids) to
escape. Hand wheels of electric actuators are for emergenc operation onl ; the are disengaged during
normal operations and can be engaged when required.
Attention
!
Valves with hand wheel must only ever be manually operated. The use o bars or pipes to
increase leverage can damage the unit and cause an accident through slippage or ailure, and is
not permitted.
Where b passes or drain valves are fitted to prevent temperature shocks to piping downstream or for
other reasons, these secondar fittings must be operated before the main valve. For setting, maintenance
and operation of actuators, refer to the manufacturer's instruction manual.
5.6. Function testing
After installation, the valve must be function tested prior to initial operation. The valve, whether manuall
operated or driven, should be opened and shut at least once.
5.7. Checking during and a ter irst operation
During operation the tightness of the stuffing box and bonnet flange as well as the pipe connection flanges
must be monitored. If necessar bolts should be further tightened (see points 3.7 and 4.1). Left
unattended, leaks can cause erosion of the seal faces and seals and hence lead to permanent leakage.
Seal tightness should be checked after a while since seals and bolts etc.. are apt to settle during initial
operation, especiall at high temperatures.

QM-Nr: FB_BMA_01-R-0804engl_3
Erstellt/
Prepared
: am/
on:19/11/2015
Genehmigt/
Approved: am
/
on19/11/2015
13 / 16
b ROFI S.A.R.L.
Attention !
Bolted connections must never be slackened on valves under pressure and only tightened
in case o emergency (e.g. leakage) in accordance with Accident Preventions Regulations (UVV),
permitted torque and under expert supervision using the proper tools.
Spring loaded stuffing boxes must also be checked for tightness during operation, and tightened as
necessar (see point 4.1). It should be noted that the stuffing box must seal without a major increase of
friction at the spindle. We recommend that regular checks be carried out during operation.
6. Maintenance
Because of their hazard potential valves are comparable with other pressure vessels and as such are
governed b the relevant Accident Prevention Regulations (UVV). Before undertaking maintenance and
assembl work, make sure that the valve is not under pressure or temperature and that the s stem before
and after the valve is completel blocked of. Valves must be regularl serviced to ensure trouble free
operation. T pical maintenance points include checking glands, lubricating spindles, function checks. At
less frequent intervals valves should be closel inspected for wear and shut down to change lubricants
and gland packing. It is not feasible to recommend specific intervals owing to the wide variet of unknown
factors involved, such as the position of the valve within the plant configuration, the medium, operating
c cle, temperature change loadings and so forth. The user should call upon his experience as plant
operator to specif inspection and maintenance intervals.
6.1. Gland packing, Bonnet- lange-seals and Replacement
The gland seals the gap between bod and spindles against loss of medium. The packing materials are
selected to suit the particular requirements - as far as known to us -and long life can normall be
anticipated. If packing does require replacement however, proceed as follows: The packing cavit must be
opened in accordance with the Accident Prevention Regulations (UVV) with the valve at ambient
temperature and not under pressure. The old packing must be removed completel before the new one is
fitted. The empt cavit and gland contact faces must be thoroughl cleaned. Ensure that the turndown
bolts on the gland ring are eased. If using slotted packing rings, the ring gaps must be offset b 120-180
degrees to one another. Once repacking is complete, operate the valve several times and if necessar the
gland bolts further tightened down (see point 4.1). The gland must be checked for tightness during
operation. If required it should be re-tightened since a leaking packing can be quickl destro ed b
erosion.
Attention !
It is not allowed to repack a valve when the valve is under pressure. Even when the valve
has a backseat device. Since the sealing e ect o this back seat can be greatly reduced a ter a
short time o operation through dirt, wear or corrosion, however with an attendant hazard or
itters when slacking o the gland screws.

QM-Nr: FB_BMA_01-R-0804engl_3
Erstellt/
Prepared
: am/
on:19/11/2015
Genehmigt/
Approved: am
/
on19/11/2015
14 / 16
b ROFI S.A.R.L.
6.2. Recommended lubricants
We recommend standard lubricants to DIN 51825. Never use mineral oils as lubricants. In cases where
stem nuts are equipped with ball- or needle bearings the use of lubricants containing solids (graphite,
copper etc..) is not allowed. The solid particles can damage the bearings. For lubrication of actuators, we
refer to the manufacturer's instructions.
6.3. Lubricant o spindle thread
The frequenc of spindle lubrication will depend on the valve operation c cle, its ambient conditions
(pollution, temperature) and the influence of the valve heat on the grease point. The spindle thread should
first be cleaned if heavil soiled, and the gland area protected accordingl . For hand operated valves, the
spindle thread should be brush-greased beneath the oke head (valve shut) and above the hand wheel
(valve open). For valves with back gear or electric actuator, the foregoing lubrication is carried out through
the hollow shaft of the actuator. After spindle lubrication, manual and electric operated valves should be
operated a number of times, and lubrication repeated if necessar . It is for the valve operator to specif
the intervals for lubrication of the spindle thread and of the thread bushing (depending on the operating
conditions of the valve).

QM-Nr: FB_BMA_01-R-0804engl_3
Erstellt/
Prepared
: am/
on:19/11/2015
Genehmigt/
Approved: am
/
on19/11/2015
15 / 16
b ROFI S.A.R.L.
7. Troubleshooting table
Fault Possible cause Corrective measures
No flow Flange covers have not been removed Remove flange covers
Flow too low Piping clogged Check piping s stem
Flange broken between unit
and piping
Bolts tighten unevenl
Mating flanges not properl aligned
Re-align piping and fit new valve.
Relie the pressure in the system irst !
Leaks across the gate Solid particles in the medium
Deformation of the seat faces due to
excessive tightening of the valve or due
to thermal stress
Erosion or corrosion caused for instance
b incorrect selection of valve size or
material
Re-grind seats, use spare parts only
by quali ied personnel !
Leaks through Bonnet and
Flange
Extreme temperature fluctuation or
vibration
Excessive pressure stresses on the
Bonnet Flange bolting
Inadequate maintenance
External influences
Failure of seal as result of insufficient
resistance to temperature or medium
Re-tightening of connection bolts
Replacement of the seal
Leaks through gland Inadequate maintenance
Wear of packing material
Failure of gland caused b the use of a
packing material without sufficient
resistance to temperature of the medium.
Retighten, repack or replace packing
Failure of actuators Please see and check the manual of the
manufacturer
For causes of trouble and remedial action, refer
to the manual supplied b the actuator
manufacturer. We strongl recommend that limit
switches or torque limiters are reset b properl
skilled personnel onl .

QM-Nr: FB_BMA_01-R-0804engl_3
Erstellt/
Prepared
: am/
on:19/11/2015
Genehmigt/
Approved: am
/
on19/11/2015
16 / 16
b ROFI S.A.R.L.
8. Spare parts
With their sturd construction and use of high-qualit materials, ROFI
Valves have a long service life.
Nevertheless certain components can wear or fail because of:
• extremel frequent operation,
• excessive vibration in the piping s stem,
• excessive external stress on the valve, or
• inadequate maintenance.
Spare parts for components which the Client is able to fit himself using standard tooling are available from
ROFI S.A.R.L.. For storage and fitting we recommend close attention to the catalogue documents and
drawings. In terms of storage, it must be remembered that soft seals, certain plastics and lubricants can
deteriorate over long storage periods and will not function as required. For best results, store these
products in dr rooms at a temperature of approx. 20°C to achieve a storage life of 4 to 5 ears. When
ordering spare parts, ou should specif :
T pe of valve, diameter nominal, pressure rating, material, drawing number and- where possible - the
Purchase Order Number under which the valve was first supplied.
9. Guarantee / Warranty
The extent and period of warrant cover are specified in the "Standard Terms and Conditions of ROFI
S.A.R.L." valid at the time of deliver or, b wa of departure, in the contract of sale itself. We guarantee
freedom of faults in compliance with state-of-the-art technolog and the confirmed application. No
warrant claims can be made for an damage caused as the result of incorrect handling or disregard of
operating and installation instructions, datasheets and relevant regulations. This warrant also does not
cover an damage which occurs during operation under conditions deviating from those laid down b
specifications or other agreements. Justified complaints will be eliminated b repair carried out b us or b
a specialist appointed b us. No claims will be accepted be ond the scope of this warrant . The right to
replacement deliver is excluded. The warrant shall not cover maintenance work, installation of external
parts, design modifications or natural wear. An damage incurred during transport should not be reported
to us but rather to the competent cargo-handling depot, the railwa compan or carrier compan
immediatel or else claims for replacements from these companies will be invalidated.
Table of contents
Popular Control Unit manuals by other brands

Microhard Systems
Microhard Systems HP900 operating manual
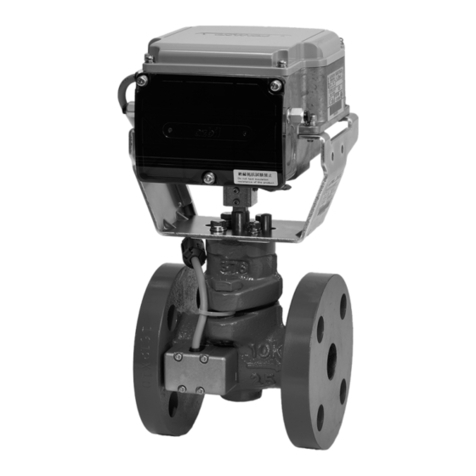
Azbil
Azbil ACTIVAL+ Intelligent Component Series Specifications & instructions

pumpa
pumpa PC-59 Translation of the original instruction manual
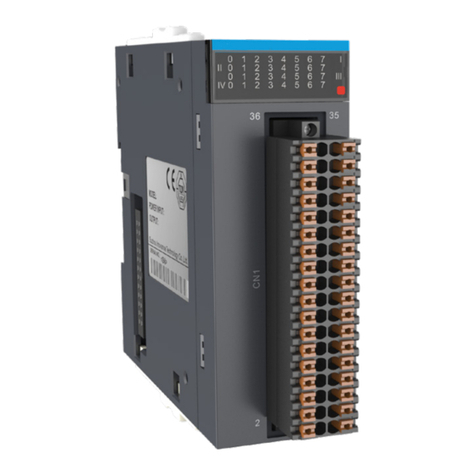
Inovance
Inovance GL10-0032ETN user guide

AAMP Global
AAMP Global SLIMKEY2 Installation

HACH LANGE
HACH LANGE sc200 user manual

Radicom Research
Radicom Research RB8762C Series Designer's guide
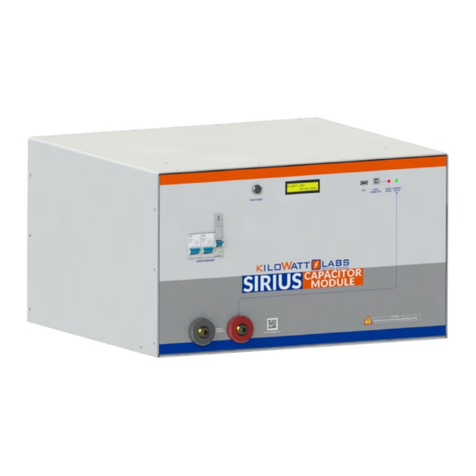
Kilowatt Labs
Kilowatt Labs 7100-48-B-2C-TM-SD-A-G user manual
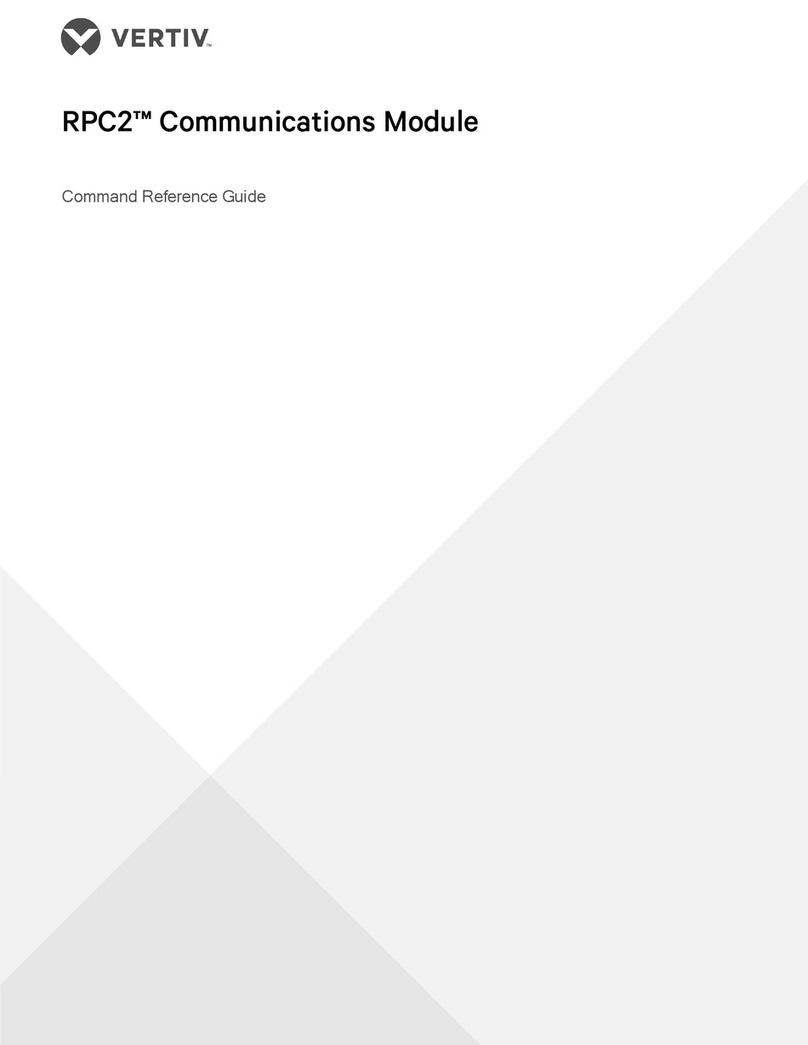
Vertiv
Vertiv LIEBERT RPC2 Command reference guide

Garmin
Garmin GIA 63 installation manual
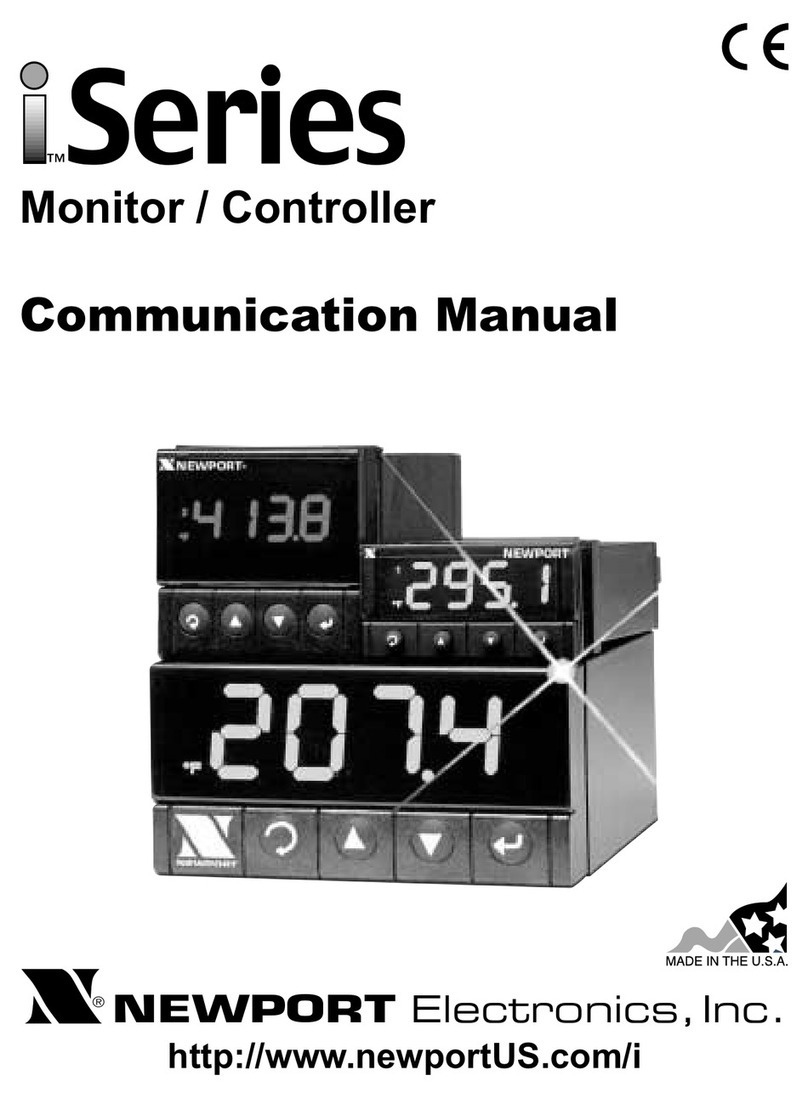
Newport Electronics
Newport Electronics iSeries Communications manual

CARLO GAVAZZI
CARLO GAVAZZI NA13CT user manual