BTM Tog-L-Loc User manual

®
CORPORATION
733679
Covers Standard Bayonet Style Hand Held Clinch Units.
User Guide: Bayonet Units

TABLE OF CONTENTS
Section 1: 1.0 Tog-L-Loc/Lance-N-Loc Overview
1.1 General Terms & Conditions of Sale
Section 2: 2.0 Safety
Section 3: 3.0 Start-up Procedure
Section 4: 4.0 Bleeding Air from the Gun
Section 5: 5.0 Operation
Section 6: 6.0 Tooling Information & Tool Change
6.1 Joint Adjustment Procedure
6.2 Tooling Component Record (Optional)
6.3 Tog-L-Loc/Lance-N-Loc User’s Guide
Section 7: 7.0 Pneumatic Circuit
Section 8: 8.0 Gun Assembly Drawing
8.1 Booster Assembly Drawing
Disclaimer: BTM Reserves the right to ammend the contents of this manual without notice. Contact BTM to verify the latest revision.
IMPORTANT!
Read this manual completely prior to operation of the system.
CONTENTS

clamps
draws
locks
The rst step in the
Tog-L-Loc® process
involves clamping of
the material with a
punch side stripper.
TOG-L-LOC®PROCESS
Next, the punch draws
the material into the
die.
As the material ows
into the die, the
die blades expand,
allowing the metal
to ow into a strong
circular interlock.
BTM’s patented Tog-L-Loc®sheet metal joining
system is the simple solution for fastening
plain or coated sheet metals. Tog-L-Loc® forms
a strong, leakproof joint without welding or
riveting in almost any combination of ductile
sheet metals. The Tog-L-Loc®system is widely
used in the manufacture of automobiles,
appliances, furniture, electrical products,
building supplies, and more.
®
®
Lance-N-Loc®is a sheet metal clinching
system which creates a strong mechanical
joint without the use of external fasteners or
welding. The metals are lanced and squeezed
to form an interlock below the bottom layer of
the sheet metal.
Lance-N-Loc® is good for joining harder
materials, multiple layers, and is ideal for use
where electrical conductivity is required.
The final result is a joint with a greater width
than the drawn section of the metals. This
accounts for the high strength of Lance-N-
Loc® joints. The entire sequence takes place
in a single press stroke.
clamps
draws
locks
The rst step in the process
involves the clamping of the
material with a punch side
stripper.
LANCE-N-LOC®PROCESS
Next, the punch draws the
material into the die.
As the material ows into
the die, the die blades
expand, allowing the
metal to ow into a strong
interlock below the bottom
sheet.
Note: Lance-N-Loc®is not leak proof. See Tog-L-Loc®.
1.0 TOG-L-LOC/LANCE-N-LOC OVERVIEW
START UP PROCEDURE

2.0 SAFETY
USER RESPONSILBILITY: Each person who is to operate or maintain the Tog-L-Loc unit must be
familiar with these, and all other, safety precautions before attempting to use or to service the press
equipment. The owner of the equipment is responsible to train and supervise all personnel as to
safety precautions.
DANGER: NEVER place hands, ngers, or other body parts in the path of the die and the ram. Accidental
operation or damaged and worn control devices can result in severe injuries. ALWAYS use tongs, or
other inserting devices, to place materials in the press operating area. DO NOT operate with a second
person holding the parts in the unit for joining.
SAFETY GLASSES: Wear safety glasses while operating this system.
SAFETY CONTROL INTEGRITY: Do not alter the control systems, or safety guarding, in any way.
SAFETY CONTROL MAINTENANCE: If a control or operating switch is damaged, or fails to work
properly, discontinue use immediately and do not use until the controls are repaired, or replaced and
the machine is tested by a qualied, machine maintenace engineer.
EQUIPMENT REPLACEMENT PARTS: Use only original BTM hoses and components with this
system.
WORK MATERIAL COMPATIBILITY: Do not attempt to join materials other than those specied by
BTM for your tooling.
SAFETY

3.0 START UP PROCEDURE
Hang the Booster as shown.
Gun should operate lower
than booster.
Start-up continues on the next page.
Read all safety instructions before operating the unit!
1. After removing your Tog-L-Loc/Lance-N-Loc system from its shipping box, make sure that you have
received two sets of Tog-L-Loc, or Lance-N-Loc, tooling. One set is already installed in the gun. The
second set should be in a package attached to the gun. Remove the second set of tooling and store
it aside.
2. Visually inspect the system for damage due to shipping. If damage has occurred, call BTM
immediately.
3. Check hoses, yoke, and the compression mechanism regularly for damage or cracks. Discontinue
use if such conditions exist.
4. Remove the booster unit from the box and hang it from the hole in the handle. Make sure the
booster unit is securely hung and will not fall or injure someone. The booster should be higher than
the gun during operation.
Hang the Booster as shown. Gun should operate lower than booster.
START UP PROCEDURE

3.0 CONTINUED
5. The booster is shipped with oil in the reservoir. If the oil level is low, oil is added by removing the
plug at the top of the booster. The oil level should reach the bottom thread of the booster cap. Oil
should be properly handled, and disposed of.
Oil Level
Remove plug to
add oil
6. Connect your air line to the booster. BTM recommends that the system operates at 80 PSI (5.5 Bar).
Clean, dry air should be used. The removal of air supply is required before tool change or service.
7. Press the trigger on the gun and dry cycle the unit. If the unit fails to cycle, air needs to be bled
from the system. See section 4 on bleeding the gun.
Unit requirements:
Recommended Air Pressure: 80 PSI (5.5 Bar)
BTM recommends that clean, dry air is used.
Maximum Air Pressure: 90 PSI (6.2 Bar)
Recommended Oil: Amoco AW 32 to DTE 26 or any equivalent, non-foaming oil.
Oil should be handled and disposed of properly.
START UP PROCEEDURE

Recommended Air Pressure: 80 PSI (5.5 Bar)
BTM recommends that clean, dry air is used.
Maximum Air Pressure: 90 PSI (6.2 Bar)
Recommended Oil: Amoco AW 32 to DTE 26 or any equivalent, non-foaming oil.
Oil should be handled and disposed of properly.
4.0 BLEEDING THE GUN
1. Apply air pressure to the booster by squeezing the trigger. Do this between 5 and 10 times.
2. Press and hold the trigger
(Note: Do not release the trigger until the plug is tightened - See item 3).
3. CAUTION! The unit is under hydraulic pressure. Using a 5mm allen wrench, carefully turn the plug,
located at the center of the press unit’s endcap, counterclockwise by a small increment between
1/4 and 1/3 of a full turn. Some air and oil should be expelled from the press unit.
Note: If plug leaks oil after tightened,
discontinue use and call BTM to order
a replacement plug.
Loosen plug with
5 mm Allen wrench.
4. The bleeding procedure may need to be repeated several times to expel all of the air.
5. This procedure works best when the press unit is lower than the booster.
6. Check the oil level. Make sure the reservoir is lled so that the oil reaches the bottom thread on
the cap.
BLEEDING THE GUN

5.0 OPERATION
1. Verify that the metals to be joined are the same as specied on the tag afxed to the die
(Also see tooling information on section 6 of this manual).
2. Observe all safety instructions as described previously in this manual.
3. Always hold the unit perpendicular to the work in both directions.
THIS NOT THIS
4. Never attempt to make a Tog-L-Loc/Lance-N-Loc joint through another Tog-L-Loc/Lance-N-Loc joint,
spot weld, or other obstruction.
5. The trigger must be pressed and held throughout the cycle to operate the unit.
6. When metals of dissimiliar thickness are to be joined, the thicker layer should be to the punch
side for best results.
7. The die blade, punch, and stripper must be in place when joining metals. These components are
crucial to join quality.
8. Joint quality is monitored nondestructively by measuring the “button dimension” of the formed joint.
Read QUALITY CONTROL in the Tog-L-Loc/Lance-N-Loc user’s guide for more detailed information.
The button dimension is controlled by adjusting the air pressure (See section 6.1).
OPERATION

[50]
[70]
[90]
222
311
400
Peel
Shear
[265]
[360]
[390]
1178
1601
1734
BD +0,25
-0,00
6,3
6,7
6,9
[.250]
[.265]
[.275]
A(x2)
C.R.S.
0,6
0,75
1,0
mm in
[.024]
[.030]
[.040]
A (x2)
BD
®
Joint Type: 4,6 [.18”]
mm in lbs
Nlbs
N
6.0 TOOLING
Tog-L-Loc tools are preset by BTM to give best joining results with a specic range of metal type and
thickness, as charted above. Higher strenths for a specic metal thickness may be obtained with
optimized tooling from BTM. All Tog-L-Loc/Lance-N-Loc tools are marked with numbers for easy
identication.
TOOL CHANGE PROCEDURE:
Please note: All tooling changes must be done with the press unit in the “open” position.
Removal of the air supply is required before the tool change or service begins.
Use a 2.5mm allen wrench to change the punch and die in the gun.
PUNCH CHANGE:
1. Remove the retaining screw with an allen wrench. Remove the punch from its pocket (It may be
necessary to pry with a wrench).
DIE CHANGE:
1. Remove the retaining screw with an allen wrench (It may be necessary to pry with a wrench).
2. When installing dies, care has to be taken so the springs are not damaged. Load the die on its
side, bottom rst, then slide the bottom of the die toward the front of the gun carefully, so that the
springs do not bend. Note: If the springs are bent, the die does not function properly and the gun
will form inferior joints.
BUTTON ADJUSTMENT:
Adjustment is achieved by increasing the air pressure to increase button size. Decreasing air pressure
decreases button size. Make tests joints until the desired button dimension is achieved.
TOOLING

6.1 JOINT ADJUSTMENT PROCEDURE
Please read all of the procedure before attempting this on your unit. If not, you may cause damage
to your tooling.
WARNING!
Start button adjustment at the lowerst possible air pressure to avoid damaging
the tooling. Increase the air pressure slowly to achieve a satisfactory joint, or
button size.
PLEASE NOTE: THIS PRESS UNIT USES AN AIR PRESSURE RANGE OF 50-90 PSI
TO ADJUST BUTTON SIZES:
Increase the air pressure to increase button size. Decrease the air pressure to decrease button size.
Button sizes are checked with a “Go-No Go” gage (One should be supplied with your unit, additional
gages can be purchased from BTM).
ADJUSTMENT PROCEDURE:
1. To achieve proper button sizes (As noted in the Tooling Component Record - Section 6.2), start at
the lowest operating air pressure (50 PSI).
2. Gradually increase air pressure, and check the button dimension frequently.
3. Repeat until button dimension is proper, or until you reach maximum operating PSI (90 PSI).
4. Mark air pressure at time of proper button dimension. Operate normally at this air pressure, do
not operate the unit above this air pressure.
(If you reach 90 PSI, and you have not made a proper button dimension, per the Tooling Component
Record, call BTM immediately, DO NOT go over 90 PSI.)
Whenever tooling is changed, test the joints to see that they are still proper. If they are not, repeat
the process above to nd correct air pressure.
JOINT ADJUSTMENT

SPRING-RETURN BOOSTER CYLINDER
(BTM No. 711100E)
BOOSTER INSERT VALVE
(BTM No. 017326)
PNEUMATIC MUFFLER
(BTM No. 000695)
AIR SUPPLY
3-WAY INSERT VALVE
(PUSH BUTTON)
(BTM No. 016121)
Please Note: The Push Button is not
considered part of the Booster and is
therefore not on the Booster drawing.
7.0 PNEUMATIC CIRCUIT
ALL PNEUMATIC SINGLE TRIGGER CONTROL UNIT
PNEUMATIC CIRCUIT

CORPORATION
®
BTM has a wide range of products to meet your needs including (but denitely not limited to):
PIN PRODUCTS
Pin Locator Clamps
BTMs’ Pin Locator Clamps and
Single Finger clamps are used
in stationary part nests, welding
xtures, transfer systems, robot
end effectors and numerous
other clamping applications.
These clamps locate and hold the
work while other operations are
performed.
Standard pin sizes range from
12.5mm - 40mm.
Precision Shot Pin cylinders
BTM’s Precision Part Locators are
used whenever your production
needs require locating precise
holes in a workpiece.
SHEET METAL JOINING
Lance-N-Loc®
BTM’s Lance-N-Loc® Joining
System produces clean, strong
and consistent joints in most
coated or uncoated metals.
Ways to Tog-L-Loc®
Press Brakes Handheld Units
Die Sets Universal Presses
Hydraulic Units
Tog-L-Loc®
BTM’s Tog-L-Loc®sheet metal
joining system is a cold forming
process that quickly joins pre-
painted, galvanized, coated, and
dissimilar metals.
www.tog-l-loc.com
PNEUMATIC CLAMPS & GRIPPERS
Light & Heavy Duty Clamps
Clamps range from light duty
omni-directional head clamps to
heavy duty precision sealed power
clamps.
Light & Heavy Duty Grippers
BTM’s Gripper line ranges from
compact light duty models to
locking & non-locking heavy duty
models.
Specialized Units
This manual suits for next models
1
Table of contents
Popular Power Tools manuals by other brands
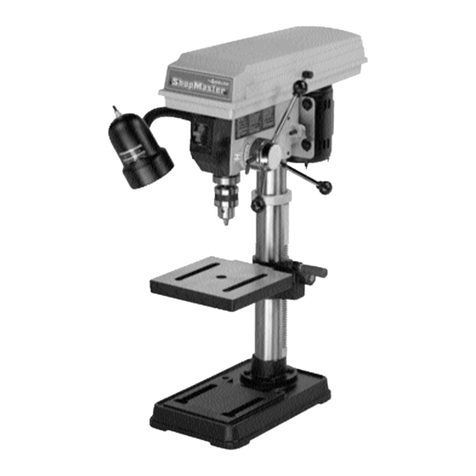
Delta
Delta ShopMaster 638517-00 instruction manual
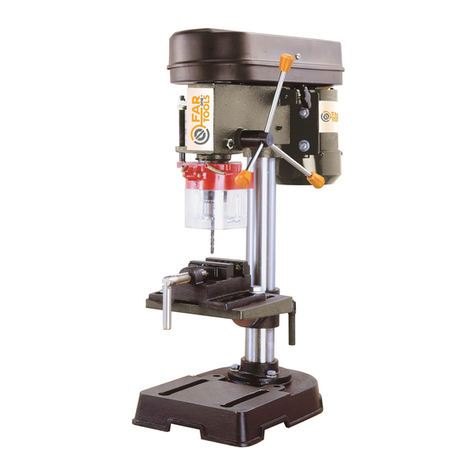
Far Tools
Far Tools P 13G manual
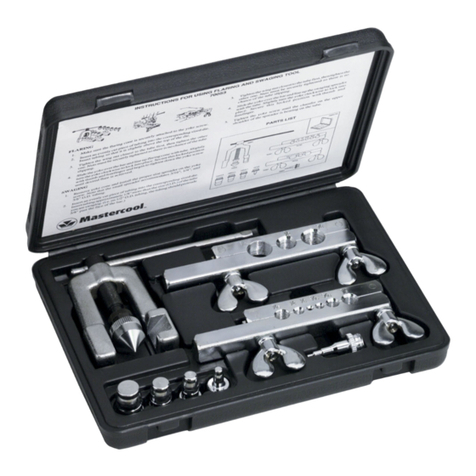
Master cool
Master cool 70053 operating instructions
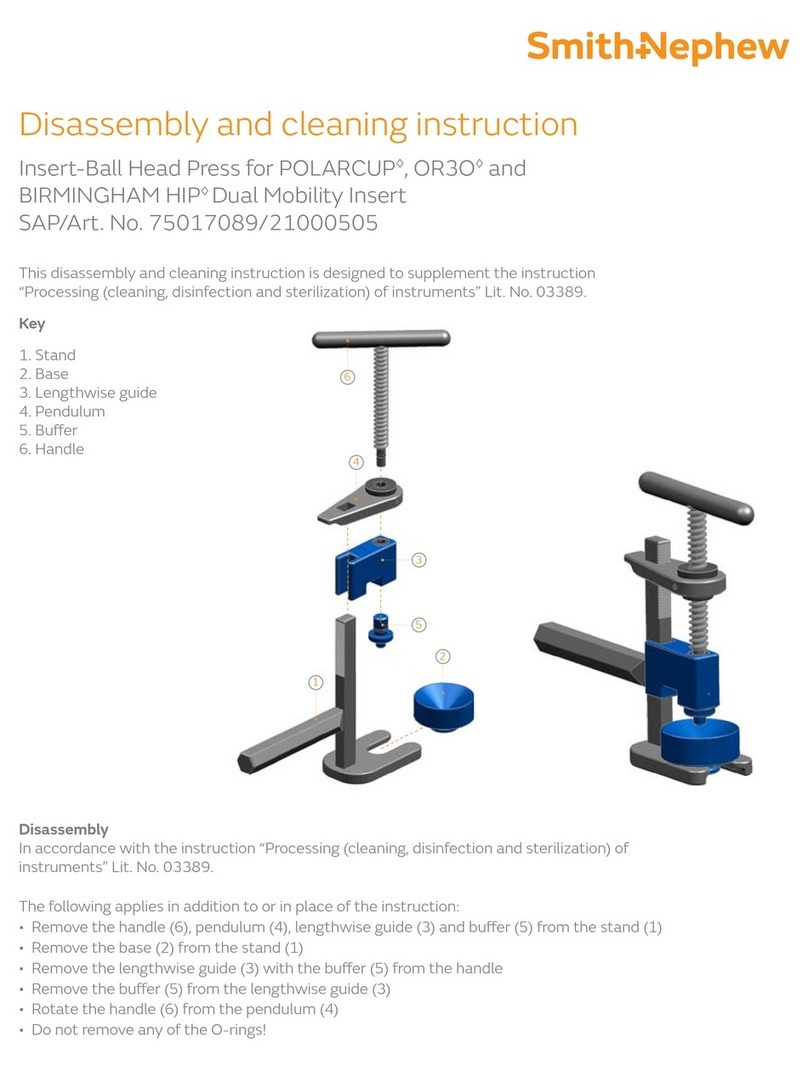
Smith & Nephew
Smith & Nephew BIRMINGHAM HIP Disassembly. & Cleaning Instructions

Mac allister
Mac allister MTC500 manual
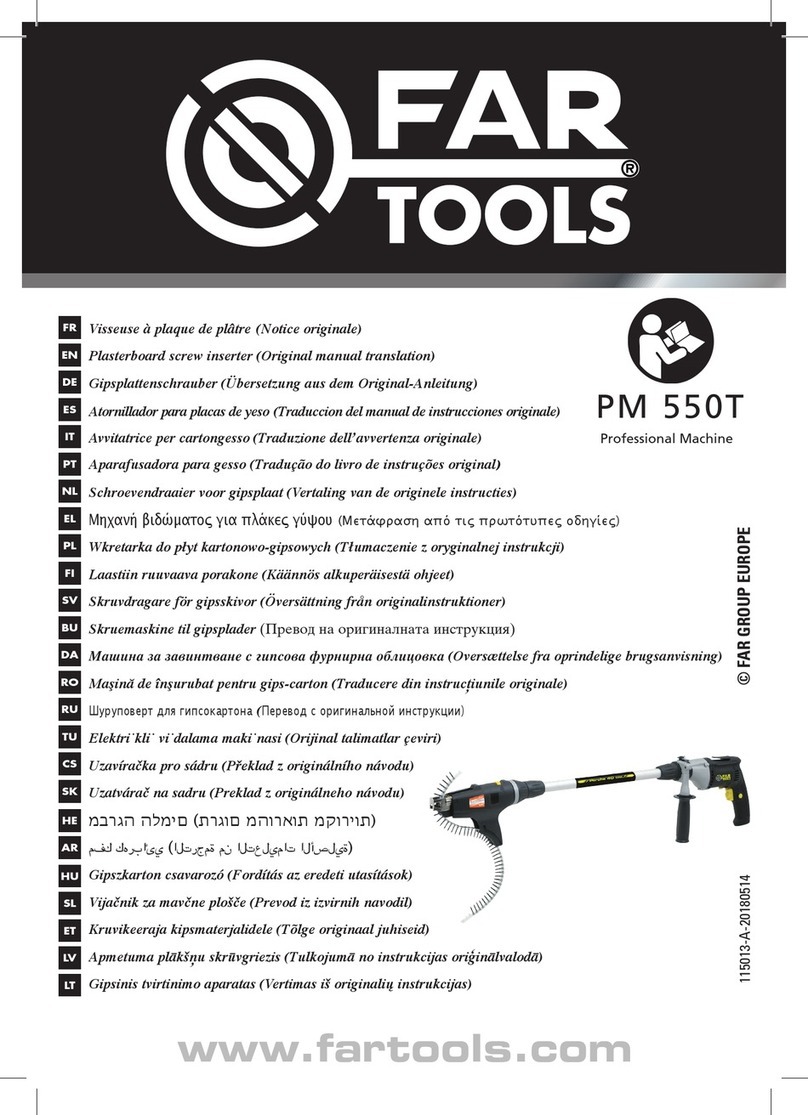
Far Tools
Far Tools PM 550T Original manual translation
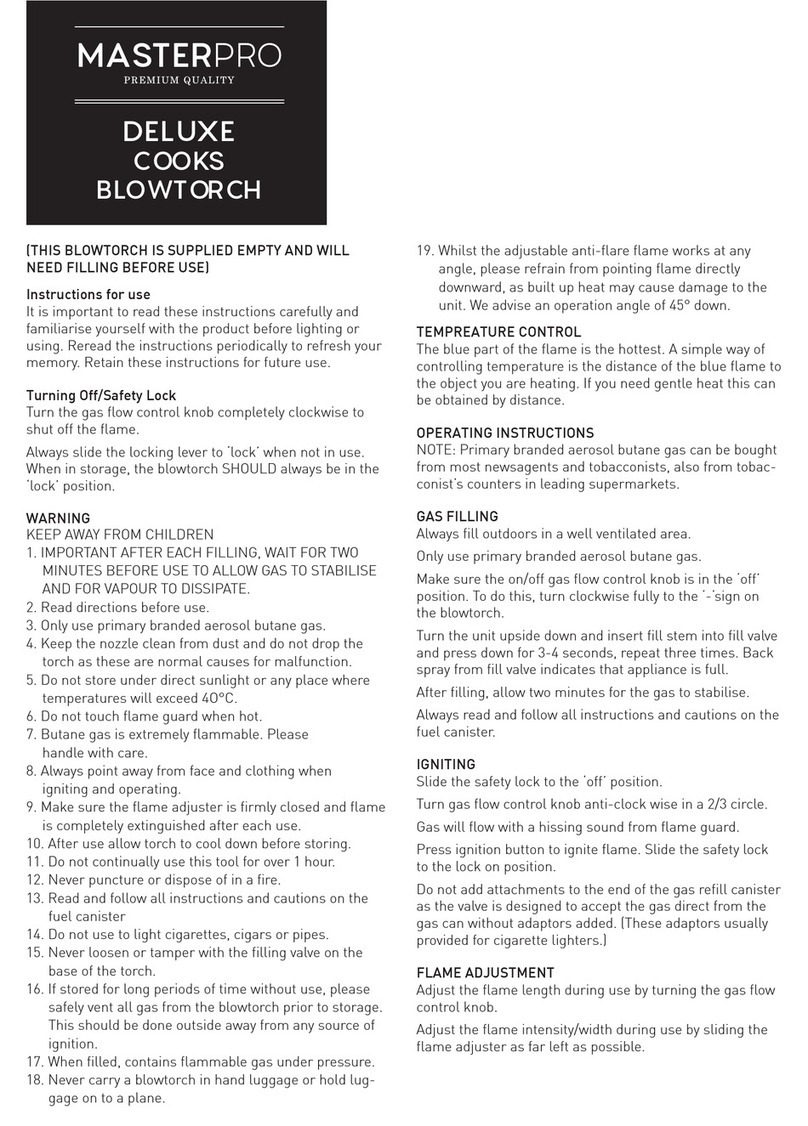
Masterpro
Masterpro MPTORCH2 Instructions for use
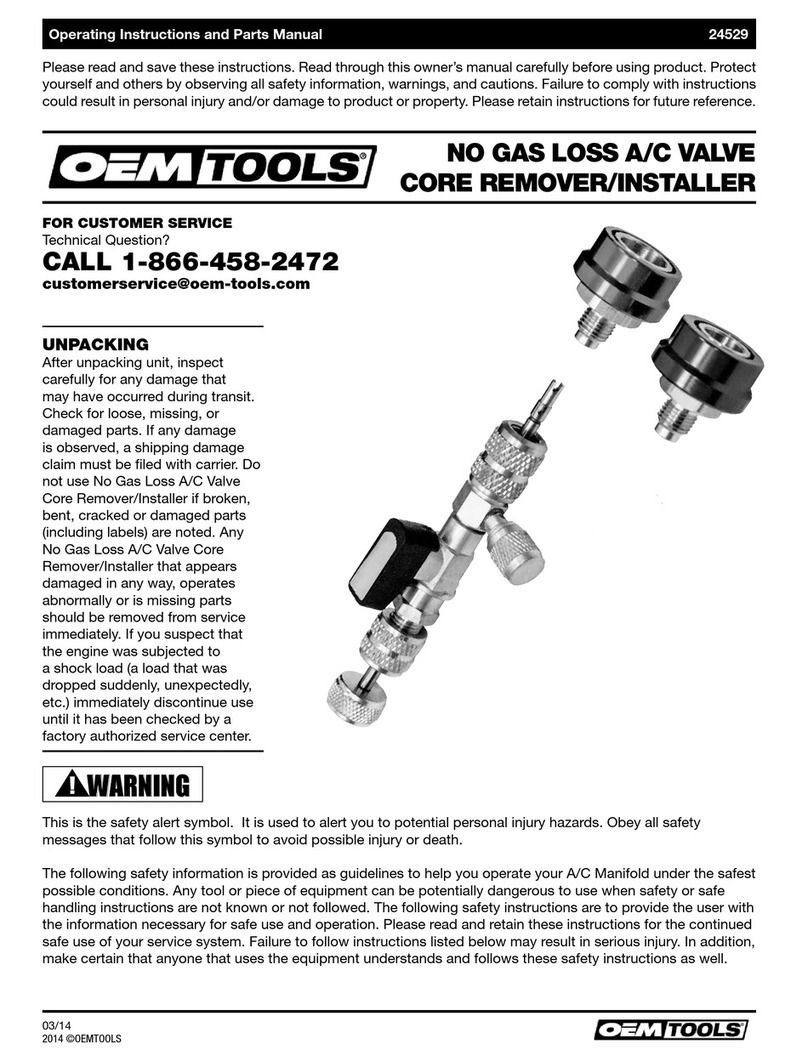
OEM Tools
OEM Tools 24529 Operating instructions and parts manual
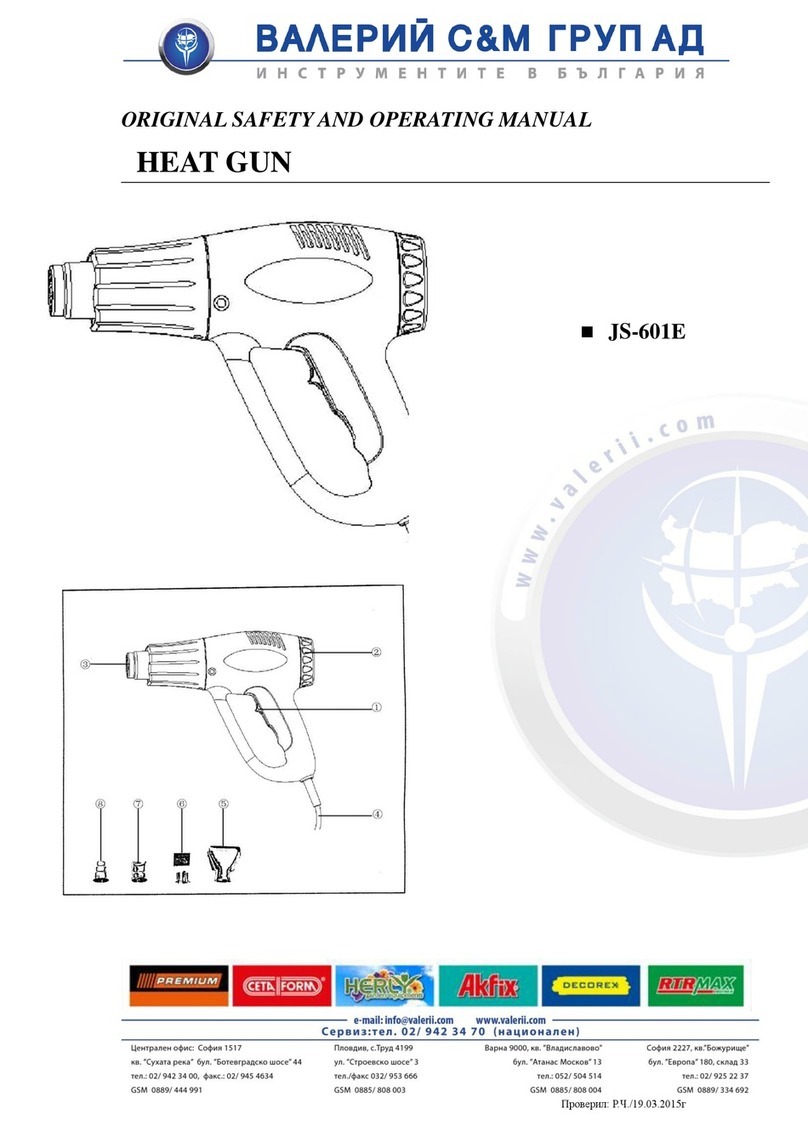
VALERII S & M GROUP
VALERII S & M GROUP JS-601D Safety and operating manual

EGAmaster
EGAmaster 57667 operating instructions
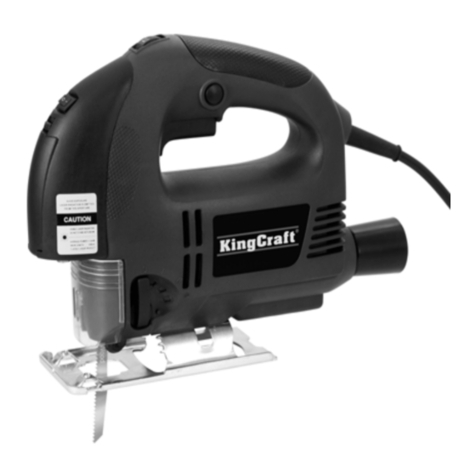
KING CRAFT
KING CRAFT MIQ-FE-65 instruction manual
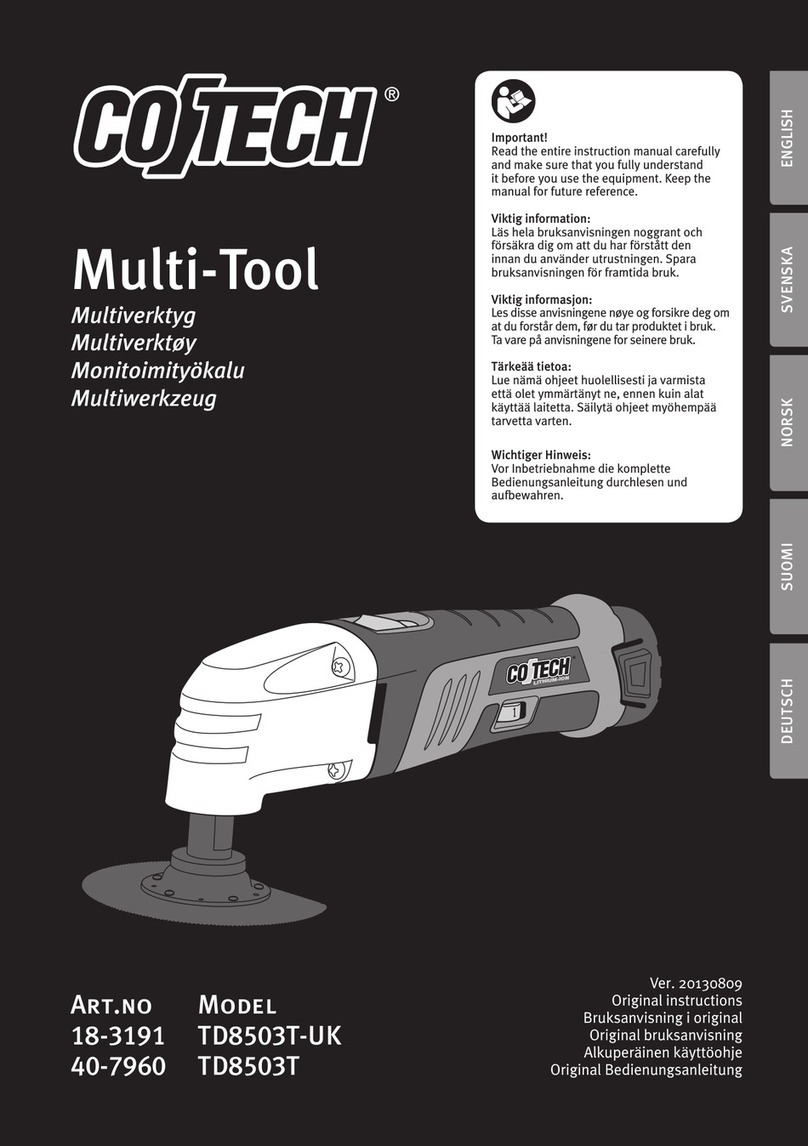
CO/Tech
CO/Tech TD8503T-UK Original instructions