Burk 8681 Operating manual

Additional Instructions for
Type 8681 büS/CANopen
Type 8681 (büS/CANopen)
Control Head
Design: büS/CANopen

We reserve the right to make technical changes without notice.
Technische Änderungen vorbehalten.
Sous resérve de modification techniques.
© Bürkert Werke GmbH & Co. KG, 2017 - 2019
Operating Instructions 1905/07_EN_00810569 / Original DE

3
Control Head Type 8681(büS)
Contents
1 OPERATING INSTRUCTIONS ........................................................................................................................................................6
2 BASIC SAFETY INSTRUCTIONS .................................................................................................................................................7
3 GENERAL INFORMATION ................................................................................................................................................................9
3.1 Conformity / Standards ......................................................................................................................................................9
3.2 Approvals ...................................................................................................................................................................................9
4 QUICKSTART FOR INITIAL START-UP ..................................................................................................................................10
5 CHANGES CONCERNING BÜS/CAN OPEN DESIGN ..................................................................................................11
5.1 “Autotune functions” – with reference to the Basic OI for Type 8681 ...................................................11
5.2 “Setting colour combinations” – with reference to the Basic OI for Type 8681 ...............................11
5.2.1 Device-specific LED mode “8681 Classic Mode” ..............................................................................13
5.2.2 NAMUR mode .......................................................................................................................................................13
5.2.3 Valve mode ............................................................................................................................................................14
5.2.4 Valve mode + Errors .........................................................................................................................................15
5.2.5 Valve mode + Errors + Warnings ..............................................................................................................15
5.2.6 Display mode “Fixed colour” ........................................................................................................................16
5.3 “Blinking pattern & fault signalling” – with reference to the Basic OI for Type 8681 ....................17
5.3.1 Position feedback in normal operation...................................................................................................17
5.3.2 Feedback in case of Errors / Warnings ..................................................................................................17
5.3.3 Localisation function .........................................................................................................................................19
5.4 “Signal priorities” – with reference to the Basic OI for Type 8681 ..........................................................20
5.4.1 When several states overlap for one valve ..........................................................................................20
5.4.2 When position feedback overlaps ............................................................................................................21
5.5 “Display of the status LEDs for bus error” – with reference to the Basic OI for Type 8681 ..................23
5.6 Further help ..........................................................................................................................................................................24
5.6.1 Links to different operating instructions ................................................................................................24
5.6.2 Firmware updates ..............................................................................................................................................24
6 BÜS/CAN OPEN-DESIGN ...........................................................................................................................................................25
6.1 Definition ...............................................................................................................................................................................25
english
Type 8681 büS/CANopen

4
6.2 Network principle / Interfaces .....................................................................................................................................25
6.3 Gateway ..................................................................................................................................................................................26
6.4 Electrical connection options .......................................................................................................................................26
6.5 büS/CANopen specification .........................................................................................................................................27
6.5.1 General data ..........................................................................................................................................................27
6.5.2 Total line length and drop line lengths of the bus cables ............................................................27
6.6 Electrical data of the control head ............................................................................................................................28
6.7 Safety position if the bus fails .....................................................................................................................................29
6.8 Design aid ...............................................................................................................................................................................29
6.9 Installation – Safety instructions ................................................................................................................................30
6.10 Gateway installation ..........................................................................................................................................................30
6.11 Electrical installation - büS/CANopen ...................................................................................................................30
6.11.1 Electronic module büS/CANopen: ..........................................................................................................31
6.11.2 Terminal strip configuration: .........................................................................................................................31
6.11.3 Details on the DIP switches for colour coding: ..................................................................................32
6.12 Network topology of a büS/CANopen system ....................................................................................................32
6.13 Configuring the Node ID / baud rate .......................................................................................................................33
6.13.1 Setting the baud rate ........................................................................................................................................33
6.13.2 Setting the büS/CANopen address (Node ID) ...................................................................................34
6.13.3 Factory settings of the control head regarding the gateway configuration........................36
6.13.4 Central configuration management (Configuration client) ..........................................................37
6.14 Changing the gateway IP address ...........................................................................................................................37
6.14.1 Changing the gateway IP address using web server .....................................................................37
6.14.2 Changing the gateway IP address using “Bürkert Communicator” ........................................39
6.14.3 Changing the gateway IP address via Logix Designer ...................................................................40
6.14.4 Changing the gateway IP address using RS Linx .............................................................................43
6.15 Registration of a gateway via Logix Designer .....................................................................................................44
6.16 Installation of a gateway via Logix Designer .......................................................................................................45
6.17 Configuration of the control head network ...........................................................................................................47
6.17.1 “Hide function” via software “Logix Designer” ...................................................................................47
6.17.2 “Hide function” via “Bürkert Communicator” ......................................................................................48
6.18 Description of the (cyclical) I/O data .......................................................................................................................50
english
Type 8681 büS/CANopen

5
6.19 Access to parameters (Read / Write) ......................................................................................................................50
6.19.1 Parameter – reading via Logix Designer ...............................................................................................51
6.19.2 Parameters – writing via Logix Designer ...............................................................................................52
6.19.3 Access to parameters via Bürkert Communicator ...........................................................................53
6.19.4 Access to further parameters (cyclic and acyclic) ...........................................................................53
7 ACCESSORIES ..................................................................................................................................................................................54
8 CABLING EXAMPLES ........................................................................................................................................56
english
Type 8681 büS/CANopen

6
Operating instructions
1 OPERATING INSTRUCTIONS
Keep these instructions in a location which is easily accessible to every user and make these instructions available
to every new owner of the device.
WARNING!
The operating instructions contain important safety information!
Failure to observe these instructions may result in hazardous situations.
`The operating instructions must be read and understood.
Symbols:
DANGER!
Warns of an immediate danger!
`Failure to observe these instructions will result in death or serious injuries.
WARNING!
Warns of a potentially dangerous situation!
`Failure to observe these instructions may result in serious injuries or death.
CAUTION!
Warns of a possible danger!
`Failure to observe this warning may result in a moderate or minor injury.
NOTE!
Warns of material damage!
`Failure to observe these instructions may result in damage to the device or the system.
Indicates important additional information, tips and recommendations.
Refers to information in these operating instructions or in other documentation.
` Highlights instructions to avoid a danger.
→Designates a procedure which you must carry out.
english
Type 8681 büS/CANopen

7
Basic safety instructions
2 BASIC SAFETY INSTRUCTIONS
These safety instructions do not make allowance for any
• eventualities and events which may occur during installation, operation and maintenance of the devices.
• local safety regulations which the operator is responsible for observing, also in relation to the installation personnel.
DANGER!
Danger from high pressure!
`Before loosening lines and valves, turn off the pressure and vent the lines.
WARNING!
Danger due to electric voltage!
`Before reaching into the system (apart from the teach-in procedure in a non-explosive atmosphere), switch
off the voltage and secure to prevent it from being switched on again!
`Observe the applicable accident prevention and safety regulations for electrical equipment!
General hazardous situations.
To prevent injuries:
`Ensure that the system cannot be activated unintentionally.
`Installation and maintenance work as well as operator actions may only be carried out by authorized and suit-
ably qualified technicians using the appropriate tools.
`Do not make any unauthorized internal or external changes to the device!
`The process is restarted in a defined or controlled manner after an interruption in the power supply or pneu-
matic supply.
`The device may be installed and operated only when in perfect condition and in consideration of the operat-
ing instructions.
`The general rules of technology apply to application planning and operation of the device.
NOTE!
Electrostatic sensitive components / modules!
• The device contains electronic components which are sensitive to electrostatic discharge (ESD). Contact with
electrostatically charged persons or objects may be hazardous to these components. In the worst case scenario,
they will be destroyed immediately or will fail after start-up.
• Observe the requirements in accordance with EN 61340-5-1 to minimise or avoid the possibility of damage
caused by a sudden electrostatic discharge!
• Ensure that you do not touch the electronic components when the power supply voltage is applied!
english
Type 8681 büS/CANopen

8
Basic safety instructions
NOTE!
Risk of damage to property!
• Do not connect any mechanically rigid connection parts, in particular those with long lever arms, as such con-
nections could generate torques that might damage the control head.
• Do not supply the medium connections of the system with liquids or aggressive or flammable media!
• Do not subject the housing to mechanical loads (e.g. by placing objects on it or standing on it).
• Do not make any unauthorised external changes to the housings of the device. Do not paint housing parts or
screws.
• Only use compatible cleaning agents for cleaning the securely closed control head and always rinse thoroughly
with clean water.
english
Type 8681 büS/CANopen

9
General information
3 GENERAL INFORMATION
These Additional Instructions are an supplement to the basic operating instructions for Type 8681.
They only describe the extensions and specifications for Type 8681 büS/CANopen.
“büS” (Bürkert system bus) stands for the communication bus developed by Bürkert and is based on the
CANopen protocol.
The following examples refer to the application of the EtherNet/IP protocol using a Bürkert gateway. The following
bus systems are also supported by the Bürkert Gateway:
PROFINET, Modbus/TPC, PROFIBUS DPV1, EtherCAT, CC-Link - corresponding configurations on request.
3.1 Conformity / Standards
The Control Head Type 8681 büS/CANopen complies with the EU directives according to the EU Declaration of
Conformity.
The applied standards, which are used to demonstrate compliance with the EU Directives, are listed in the EU
Prototype Examination Certificate and/or the EU Declaration of Conformity.
3.2 Approvals
The Control Head Type 8681 büS/CANopen is not authorised for those application areas which are described by
the ATEX Directive and the directives for the Underwriters Laboratories (UL) and Factory Mutual (FM).
english
Type 8681 büS/CANopen

10
Quickstart for initial start-up
4 QUICKSTART FOR INITIAL START-UP
“büS” (Bürkert system bus) stands for the communication bus developed by Bürkert and is based on the CANopen
protocol. The following steps refer to the application of the e.g. EtherNet/IP protocol using a Bürkert gateway pre-
configured for a maximum of 63 control heads.
For other gateway configurations (e.g. in conjunction with ELEMENT positioners), the specific documentation for
preconfigured Bürkert gateways must be observed.
After mounting the control heads (Type 8681 büS/CANopen) in the network, the following operations must first
be carried out on the control heads:
1.) Addressing of the control heads
According to chapter “6.13.2 Setting the büS/CANopen address (Node ID)” each control head in the network must
be assigned its own unique address (Node-ID).
When using a preconfigured gateway: For easy commissioning, each control head should be assigned its unique
node ID between 1 and 63 using the DIP switches. This allows the preconfigured communication settings between
the gateway and each control head to be used. The factory setting (address “0” = softwareconfigurable address/
node ID) should not be used furthermore.
When using a non-pre-configured gateway or when using the factory setting “0” (software-configurable
address/node ID): A device configuration via Bürkert Communicator on site is required for commissioning each
control head (see also section “6.13.3” on page 36 ).
Error-free parameter access by the Logix Designer: To ensure this, the new addresses should be selected
clearly arranged and in sequence (starting with “1” and without gaps in the numerical series!).
Any change of the device address requires a device restart.
2.) Setting the baud rate
Set the baud rates according to chapter “6.13.1 Setting the baud rate”. The combination of cable lengths and baud
rate is very important (see chapter “6.5.2 Total line length and drop line lengths of the bus cables”).
The baud rate of all devices connected to the network (including the gateway) must be the same .
Any change of the baud rate requires a device restart.
3.) “Hiding” of non-existent devices
If less than 63 devices are assigned to the gateway, the non-existent devices must be “hidden” at the gateway, both
outputs AND inputs - see chapter “6.17 Configuration of the control head network”, either using the Logix-Designer
(“6.17.1”) or Bürkert Communicator (“6.17.2”).
After the changes have been made, a device restart is required.
4.) Careful closing of the electrical connections
Due to moisture (including steam) in the system, all electrical connections (M12 plug-in connections) must be
firmly screwed on with 0.6 (+0.1) Nm. All open electrical connections must be well “sealed” with protective
caps (see information box in chapter “6.2 Network principle / Interfaces” and also chapters “7 Accessories” and
“8 Cabling examples”.
english
Type 8681 büS/CANopen

11
Changes concerning büS/CAN open design
5 CHANGES CONCERNING BÜS/CAN OPEN
DESIGN
This chapter describes changes affecting the Control Head Type 8681 büS/CANopen design with reference to
the Basic Operating Instructions (OI) for Type 8681.
5.1 “Autotune functions” – with reference to the Basic
OI for Type 8681
The optical feedback signals for the autotune mode and the autotune functions of type 8681 büS/CANopen are
different from the standard models of type 8681.
For the autotune functions, first enter the Autotune mode (T2+T3 for min. 2.5 s), then choose one of the 6 Auto tune
functions:
Teach
button
Mode Activa-
tion
duration
optical
feedback
for “Autotune
mode active”
Teach
button
Function Activa-
tion
duration
optical
feedback
for “Autotune
function active”
T2 + T3 Autotune
mode 2.5 s
red +
yellow +
green
flashing
sequentially
(500 ms per
colour)
+
T1 Autotune 1
0.5 s
red +
yellow +
green
flashing
sequentially
(200 ms per co-
lour) *)
T2 Autotune 2
T3 Autotune 3
T1 + T2 Autotune 4
T1 + T3 Autotune 5
T2 + T3 Autotune 6
*) This display for “Autotune function active” applies only to the display mode “device-specific LED mode”
(“8681 Classic 0 ... 15”) – see chapter “5.2.1”.
In the case of other display modes of the device status LED (Top LED) – compare chapter “5.2.1” – the colour
and blinking pattern display differs for the “Autotune function active”. See also:
- NAMUR mode (chapter “5.2.2”) – displayed in color orange as “function check”.
- valve mode (chapter “5.2.3”) – no display
- valve mode + errors (chapter “5.2.4”) – no display
- valve mode + errors + warnings (chapter “5.2.5”) – displayed in color orange as “function check”
5.2 “Setting colour combinations” – with reference to
the Basic OI for Type 8681
Position feedback (S1, S2, S3, S4IN) of the process valve as well as error and warning messages are displayed
by means of the device status LED (Top LED) in different colours and partially blinking patterns. Different display
modes and colour combinations can be selected for Type 8681 büS/CANopen.
This display mode and the colour coding of the büS/CANopen devices can be switched using the 6 DIP switches
for colour coding on the electronic module (see “Fig. 6” on page 31).
(As of firmware version B.02.00.00 the following applies “Tab. 1”.)
english
Type 8681 büS/CANopen

12
Changes concerning büS/CAN open design
DIP1 DIP2 DIP3 DIP4 DIP5 DIP6 Description of the display modes of the device status LED (Top LED)
X X X X 0 0 8681 “Classic Mode”:
the colour combinations for the position and error feedback are set using DIP
switches 1 to 4 as described in the Basic Operating Instructions, chapter
“Setting colour combinations” – see also chapter “5.2.1”
1 1 11 1 0Factory settings: software-configurable display mode:
display mode of the device status LED can be selected by firmware:
- Device-specific LED mode (8681 Classic 0 ... 15) – see chapter “5.2.1”
- NAMUR mode – see chapter “5.2.2”
- Valve mode – see chapter “5.2.3”
- Valve mode + errors – see chapter “5.2.4”
- Valve mode + errors + warnings (factory setting) – see chapter “5.2.5”
- Fixed colour – see chapter “5.2.6”
- (Top) LED off (there is no feedback via Top LED)
(In the Bürkert Communicator the display modes can be found under:
General settings -> Parameters -> Status LED -> Mode)
PLEASE NOTE:
Hardware-configured values (that means: set via DIP switches) overwrite the
software-configured display mode!
1 1 0 0 10NAMUR mode:
The device status is displayed according to NAMUR NE 107 – see chapter
“5.2.2”
10 1 1 10Valve mode:
Display of the position feedback – see chapter “5.2.3”
1 1 01 1 0Valve mode + errors:
Display of the position and error feedback – see chapter “5.2.4”
1 1 1 010Valve mode + errors + warnings:
Display of the position and error feedback as well as warnings – see chapter
“5.2.5”
X X X X X X all other combinations: (Top) LED off
Tab. 1: Colour combinations / colour coding / display modes for Type 8681büS/CANopen
english
Type 8681 büS/CANopen

13
Changes concerning büS/CAN open design
5.2.1 Device-specific LED mode “8681 Classic Mode”
This display mode of the device status LED for the position feedback (S1, S2, S3, S4IN) of the process valve
matches the display mode of the “classic” Control Heads Type 8681 (24 V DC, AS-i, DeviceNet, 120 V AC). The
colour coding is set using DIP1 to 4 - see Basic Operating Instructions, chapter “Setting colour combinations”.
If the display mode is selected using software – e.g. via Bürkert Communicator (General Settings/Parameters/
Status LED) or via the network (e.g. via Logix Designer) – the parameter “8681 Classic X” can be selected under
“device-specific LED mode”. Which DIP switch position corresponds to the respective parameter is listed in ”Tab. 2”:
S1 S2 S3 S4 Error DIP1 DIP2 DIP3 DIP4 Designation of the
device-specific LED
mode
green yellow green red 0 0 0 0 8681 Classic 0
yellow green yellow red 1 0 0 0 8681 Classic 1
green red green yellow 0 1 0 0 8681 Classic 2
red green red yellow 1 1 0 0 8681 Classic 3
green yellow yellow red 0 0 1 0 8681 Classic 4
yellow green green red 1 0 1 0 8681 Classic 5
green red red yellow 0 1 1 0 8681 Classic 6
red green green yellow 1 1 1 0 8681 Classic 7
green yellow green green red 0 0 0 1 8681 Classic 8
yellow green yellow yellow red 1 0 0 1 8681 Classic 9
green red green green yellow 0 1 0 1 8681 Classic 10
red green red red yellow 1 1 0 1 8681 Classic 11
green yellow yellow yellow red 0 0 1 1 8681 Classic 12
yellow green green green red 1 0 1 1 8681 Classic 13
green red red red yellow 0 1 1 1 8681 Classic 14
red green green green yellow 1 1 1 1 8681 Classic 15
Tab. 2: Colour combinations / colour coding for Type 8681 büS/CANopen - device-specific LED mode “8681 Classic X”
5.2.2 NAMUR mode
The device status LED (Top LED) display the device status, they change colour according to NAMUR NE 107
(edition 2006-06-12). There is no feedback on the process valve positions (S1, S2, S3, S4IN).
This display mode can be configured by software (DIP 1 to 6: 111110) or can be fixed as of firmware revision
B.02.00.00 using DIP switches (DIP 1 to 6: 001110) – compare “Tab. 1”.
If several device statuses exist simultaneously, the device status with the highest priority is displayed. The priority is
determined by the severity of the deviation from controlled/normal operation (red LED = failure = highest priority) –
see “Tab. 3”.
english
Type 8681 büS/CANopen

14
Changes concerning büS/CAN open design
Colour*) Prio-
rity
Description Meaning
red 1 Failure, error, malfunction Controlled operation is not possible due to a malfunction in
the device or its peripheral devices.
orange 2 Function check Work is being carried out on the device; controlled operation
is therefore not currently possible
(this includes “Autotune function active”).
yellow 3 Out of specification The ambient conditions or process conditions for the device
are outside the specified area
(this includes “Teach or Autotune function required”).
blue 4 Maintenance required The device is in controlled operation, but a function is pres-
ently restricted.
→Service the device!
green 5 Diagnostics active
(controlled operation)
Device is operating faultlessly (controlled). Status changes
are indicated in different colours.
Messages are transmitted via a fieldbus if connected.
Tab. 3: Description of the colours in display mode “NAMUR”
*) If a control head is connected to the Bürkert Communicator, this control head “flashes” (single flash) in the particular co-
lour of the device status – see also the chapter on Localisation function “5.3.3”.
5.2.3 Valve mode
The device status LED (Top LED) display the position feedback (S1, S2, S3) of the process valve and the
feedback S4IN from the external initiator.
The position feedback is displayed as shown below in “Tab. 4”. There is no display of error and warning messages
in this mode.
This display mode can be configured by software as of firmware revision B.02.00.00 (DIP 1 to 6: 111110) or can
be fixed using DIP switches (DIP 1 to 6: 011110) – see “Tab. 1”.
Position Process valve
position, e.g.:
Colour Blinking pattern of the
position feedback
S1 closed green *) continuously lit
S2 open yellow *) continuously lit
S3 Cycle stroke green *) continuously flashing slowly **)
(250 ms ON, 250 ms OFF)
S4IN ext. Initiator,
active
green *) continuously flashing quickly **)
(125 ms ON,125 ms OFF)
If there is no position feedback (S1 to S4IN), i.e. the process valve is in intermediate positions of the defined
teach points, the Top LED is off *) ***).
Tab. 4: Description of the colours and blinking patterns in “valve mode” display mode
*) Factory settings (other selectable colours for S1 to S4IN and also for the intermediate positions:
white, green, blue, yellow, orange, red, (Top) LED off)
**) Factory settings (other selectable blinking patterns: [continuously lit], [125 ms ON + 125 ms OFF],
[250 ms ON + 250 ms OFF])
***) Blinking pattern for the selected colour for the intermediate positions: continuously lit
english
Type 8681 büS/CANopen

15
Changes concerning büS/CAN open design
5.2.4 Valve mode + Errors
The device status LED (Top LED) display the position feedback (S1, S2, S3) of the process valve and the
feedback S4IN from the external initiator as well as error messages.
The position feedback is displayed as shown below in “Tab. 5”.
If an error (i.e. internal error, bus error, error with teach or Autotune function, positions measuring sys tem signal
error) occurs, this is also displayed alternately according to the diagram: 1 second position feedback / 1 second
error display.
This display mode can be configured by software as of firmware revision B.02.00.00 (DIP 1 to 6: 111110) or can
be fixed using DIP switches (DIP 1 to 6: 101110) – see “Tab. 1”.
Position Process valve
position, e.g.:
Colour Blinking pattern of the
position feedback
Fault indication
S1 closed green *) continuously lit is lit red alternating with colour from S1
S2 open yellow *) continuously lit is lit red alternating with colour from S2
S3 Cycle stroke green *) continuously flashing slowly **)
(250 ms ON, 250 ms OFF)
is lit red alternating with colour from S3
S4IN ext. Initiator,
active
green *) continuously flashing quickly **)
(125 ms ON,125 ms OFF)
is lit red alternating with colour from
S4IN
If there is no position feedback (S1 to S4IN), i.e. the process valve is in intermediate positions of the defined
teach points, the Top LED is off *) ***).
Tab. 5: Description of the colours and blinking patterns in “valve mode + errors” display mode
*) Factory settings (other selectable colours for S1 to S4IN and also for the intermediate positions:
white, green, blue, yellow, orange, red, (Top) LED off)
**) Factory settings (other selectable blinking patterns: [continuously lit], [125 ms ON + 125 ms OFF],
[250 ms ON + 250 ms OFF])
***) Blinking pattern for the selected colour for the intermediate positions: continuously lit (alternating with pos-
sible error messages)
5.2.5 Valve mode + Errors + Warnings
The device status LED (Top LED) display the position feedback (S1, S2, S3) of the process valve and the
feedback S4IN from the external initiator as well as error and warning messages.
The position feedback is displayed as shown in “Tab. 6”.
If an error or a warning occurs (see colour assignment below “Tab. 6”), this is also displayed alternately:
1 second position feedback / 1 second error or warning display.
This display mode can be configured by software as of firmware revision B.02.00.00 (DIP 1 to 6: 111110) or can
be fixed using DIP switches (DIP 1 to 6: 110110) – see “Tab. 1”.
english
Type 8681 büS/CANopen

16
Changes concerning büS/CAN open design
Position Process valve
position, e.g.:
Colour Blinking pattern of the
position feedback
Fault indication Warning display
S1 closed green *) continuously lit is lit red
(= error
colour ***)) alter-
nating with colour
and any blinking
pattern of the
position (S1 or S2
or S3 or S4IN)
is lit in the
warning
colour ****)
alternating with
colour and any
blinking pattern of
the position (S1
or S2 or S3 or
S4IN)
S2 open yellow *) continuously lit
S3 Cycle stroke green *) continuously flashing slowly **)
(250 ms ON, 250 ms OFF)
S4IN ext. Initiator,
active
green *) continuously flashing quickly **)
(125 ms ON,125 ms OFF)
If there is no position feedback (S1 to S4IN), i.e. the process valve is in intermediate positions of the defined
teach points, the Top LED is off *).
(Blinking pattern for the intermediate positions with selected colour (different from the factory setting “(Top)
LED off”): continuously lit, alternating with possible warning or error messages)
Tab. 6: Description of the colours and blinking patterns in “valve mode + errors + warnings” display mode
*) Factory settings (other selectable colours for S1 to S4IN and also for the intermediate positions:
white, green, blue, yellow, orange, red, (Top) LED off)
**) Factory settings (other selectable blinking patterns: [continuously lit], [125 ms ON + 125 ms OFF],
[250 ms ON + 250 ms OFF])
***) Error colour: red (internal error, bus error, error with teach or Autotune function, positions measuring
sys tem signal error)
****) Warning colours: (firmly specified):
Orange:
Function check (service mode/manual override active, Autotune function active)
Yellow: Out of specification (storage error of the operating hour/cycle counter, Teach
or Autotune function required (no position taught))
Blue: Maintenance required (Service/maintenance notification)
5.2.6 Display mode “Fixed colour”
A fixed colour can be assigned to the device - however this is possible only in software configurable display mode
(DIP 1 to 6: 111110). There is no display of process valve positions or error/warning messages in this mode –
compare “Tab. 1”.
Bürkert Communicator can be used to select the following colours:
white, green, blue, yellow, orange, red, teal, pink (factory settings: (Top) LED off).
english
Type 8681 büS/CANopen

17
Changes concerning büS/CAN open design
5.3 “Blinking pattern & fault signalling” – with reference
to the Basic OI for Type 8681
The device status LED (Top LED) display the position feedback (positions) S1, S2, S3 of the process valve, the
feedback S4IN from the external initiator as well as error and warning messages, partly using special “blinking pat-
terns”. How these are displayed, depends on the selected display mode of the device status LED.
5.3.1 Position feedback in normal operation
No. Blinking pattern ON OFF Note
1ON continuously lit in the respective
position colour:
Signal from S1 and S2 (factory settings)
2250 ms 250 ms continuously flashing in the respective
position colour:
Signal from position S3 (factory settings)
3125 ms 125 ms continuously flashing in the respective
position colour:
Signal from the external initiator S4 (factory settings)
Tab. 7: Position feedback in normal operation
Software can used to assign in part also other colours and blinking patterns to some display modes – compare
chapter “5.2”.
5.3.2 Feedback in case of Errors / Warnings
If the position feedback in controlled/normal operation and error/warning displays occur at the same time, these
are not displayed at all for some display modes or alternately for other display modes – see the following table
(“Tab. 8”) and also the blinking patterns in Tab. 9 (see on the next pages).
Display mode Position
feedback
Errors (E)+
warnings (W)
Special characteristics
“Device-specific”
(“8681 Classic”)
yes yes alternately:
2 seconds position feedback (see “5.4.2”) /
2 seconds error/warning display (see “5.4.1”)
NAMUR no yes only device status displays - see chapter “5.2.2”
Valve mode yes no see chapter “5.2.3” and “5.4.2”
Valve mode + errors yes yes (Errors) alternately:
1 second position feedback (see “5.4.2”) /
1 second error display – see chapter “5.2.4”
Valve mode + errors +
warnings
yes yes ( Errors +
Warnings)
alternately:
1 second position feedback (see “5.4.2”) /
1 second error/warning display – see “5.2.5”
“Fixed colour” no no permanently selected colour displaying – see “5.2.6”
“LED off” no no no displays
Tab. 8: Display behaviour of the different display modes with regard to position, error, warning
english
Type 8681 büS/CANopen

18
Changes concerning büS/CAN open design
In addition to the position feedback signals, the errors and the device status in the various display modes are also
indicated by means of different blinking patterns.
Display of device status / errors / warnings
No.
Blinking pattern / colour
(for reasons of space the
“colour of the valve position”
is designated
as position
colour)ON OFF Note
Classic *)
NAMUR *)
VM *)
VM+E *)
VM+E+W *)
1
in position colour
100
ms
100
ms
3 x flashing:
Teach-In confirmation
xxxxx
(after successful teaching: colour for
position 1 and 2 continuously ON)
xxx
2
in error colour
100
ms
100
ms
3 x flashing:
- if target could not be located in the
measuring area during teaching or
- if teach position is too close
(±0.5 mm) to a previously defined
teach position or
- if magnetic manual override is used,
even though manual override function
was disabled by software
xxxxx
3
in position colour
125
ms
125
ms
Continuous flashing:
Signal from the external initiator S4
(factory settings – comp.
line 3 in “Tab. 7”)
x x x x
4
in position colour
250
ms
250
ms
Continuous flashing:
Signal from position 3 (factory settings
– comp. line 2 in “Tab. 7”)
x x x x
5
in error colour
250
ms
250
ms
Continuous flashing:
- Teaching does not occur or
- Autotune function error or
- Teach Reset implemented or
- Bus error or
- Position measuring system signal
error (from firmware B.02.00.00) or
- Device Reset implemented
x
6
in error colour
50
ms
450
ms
Continuous flashing:
Device in service mode /
manual override active
x
7
in error colour
450
ms
50
ms
Continuous flashing:
Internal error
x
english
Type 8681 büS/CANopen

19
Changes concerning büS/CAN open design
No.
Blinking pattern / colour
(for reasons of space the
“colour of the valve position”
is designated
as position
colour)ON OFF Note
Classic *)
NAMUR *)
VM *)
VM+E *)
VM+E+W *)
8
blue colour (position
feedback during OFF
phase)
1
sec.
3
sec.
Continuous flashing:
Service/maintenance notification (main-
tenance / service required)
(Position feedback occurs during OFF
phase)
x
9
alternately red / green
(500 ms per colour)
Continuous flashing:
Device Reset mode active
(for Device Reset press again within
10 s)
x x x x x
10
alternately red / yellow / green
(500 ms per colour)
Continuous flashing:
Autotune (selection) mode active
(for Autotune function press appro-
priate keys within 10 s)
x x x x x
11
alternately red / yellow / green
(200 ms per colour)
Continuous flashing:
Autotune function active
x
Tab. 9: Display behaviour of the different display modes with regard to, error, warning, status
*) These abbreviations mean: Classic – device specific LED mode (8681 Classic Mode X),
NAMUR – NAMUR mode (NAMUR NE 107),
“VM” – valve mode,
“VM+E” – valve mode with error messages,
“VM+E+W” – valve mode with error and warning messages
5.3.3 Localisation function
This function can be used to localise a device in the system via the control system (e.g. Bürkert Communicator).
When the localization function is activated, the device status LED (Top LED) begin to flash according to the
signal priority (see chapter “5.4”) and according to the following logic (see “Tab. 10”).
In the NAMUR mode, the device status is displayed as “single flashing”.
In the display modes VM+E and VM+E+W, any error or warning messages that may occur are displayed as
“single flashing” in the corresponding color alternating with the corresponding position feedback (S1, S2, S3 or
S4) – see “Tab. 10”.
english
Type 8681 büS/CANopen

20
Changes concerning büS/CAN open design
No. Blinking pattern Note
Classic *)
NAMUR *)
VM *)
VM+E *)
VM+E+W *)
1
every second:
1 x 25 ms ON
single flashing:
in white: no (taught)
position active
in colour from S1 or S2: S1 or S2 active
x x x x
in color of the device status
or in the error colour / warning colour
alternating with the position feedback signal
(S1, S2, S3, S4), if an error or warning message
is present
x
x x
2
every second:
2 x 25 ms ON
double flashing:
in colour from S3: S3 active
x x x x
3
every second:
3 x 25 ms ON
triple flashing:
in colour from S4: S4 active
x x x x
Tab. 10: Display behaviour during active localisation function
*) These abbreviations mean: see explanations below Tab. 9 (Page 19).
5.4 “Signal priorities” – with reference to the Basic OI
for Type 8681
5.4.1 When several states overlap for one valve
In this case the following priority list applies to the “device specific” display mode (“8681 Classic X”) :
1. Internal error: (error colour: 450 ms ON, 50 ms OFF)
2. Manual operating mode is active, e.g. by magnetic manual override - see chapter “18. Service mode/manual
override” (error colour: 50 ms ON, 450 ms OFF)
3. Other faults, e.g. position measuring system not taught, bus error or other
(see chapter “5.3” of these supplementary operating instructions)
4. Service / maintenance request (blue colour: 1 s ON, 3 s OFF)
The display logic described in chapter “5.2” applies to the other display modes; this is shown in detail in the
respective subchapters:
english
Type 8681 büS/CANopen
Table of contents
Popular Control Unit manuals by other brands
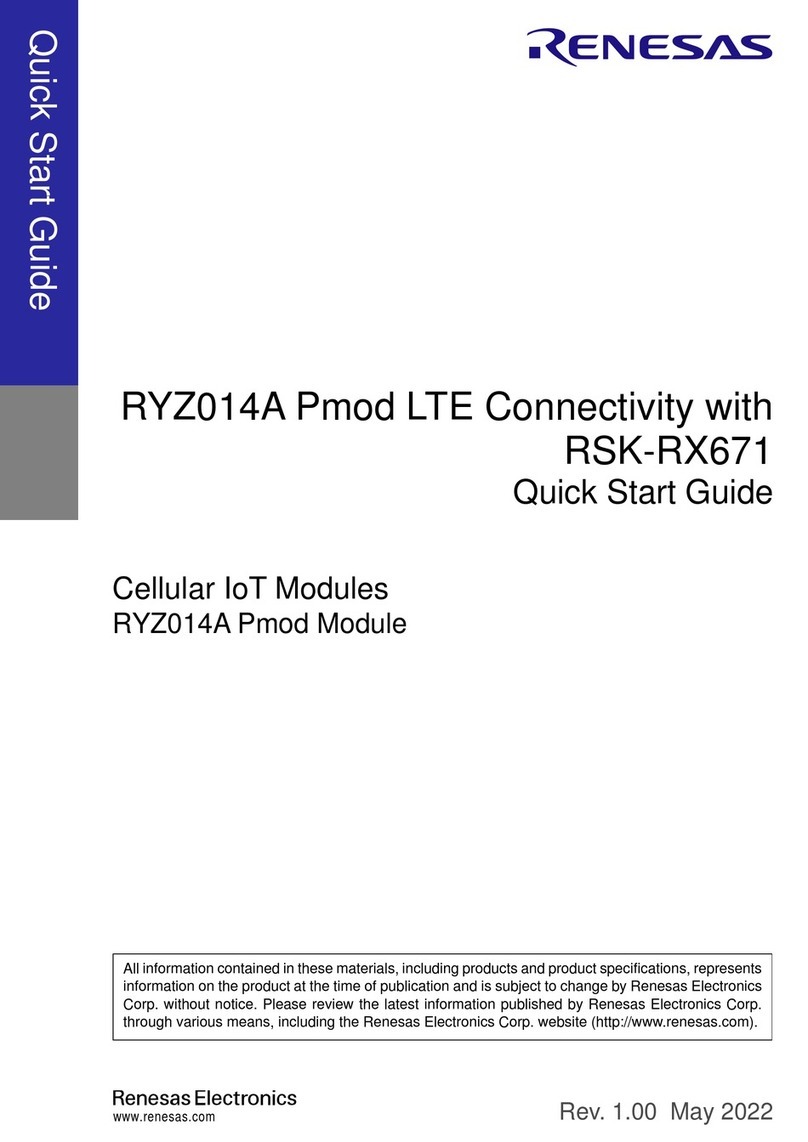
Renesas
Renesas RYZ014A quick start guide
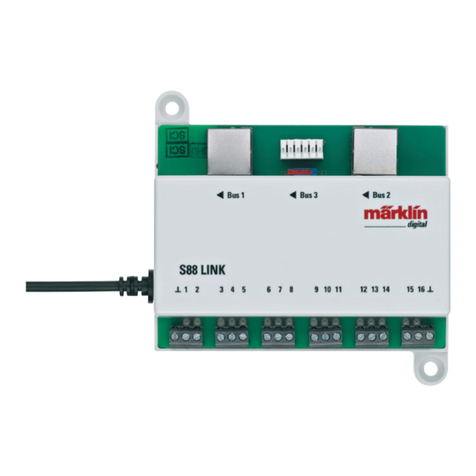
Marklin Digital
Marklin Digital L88 manual
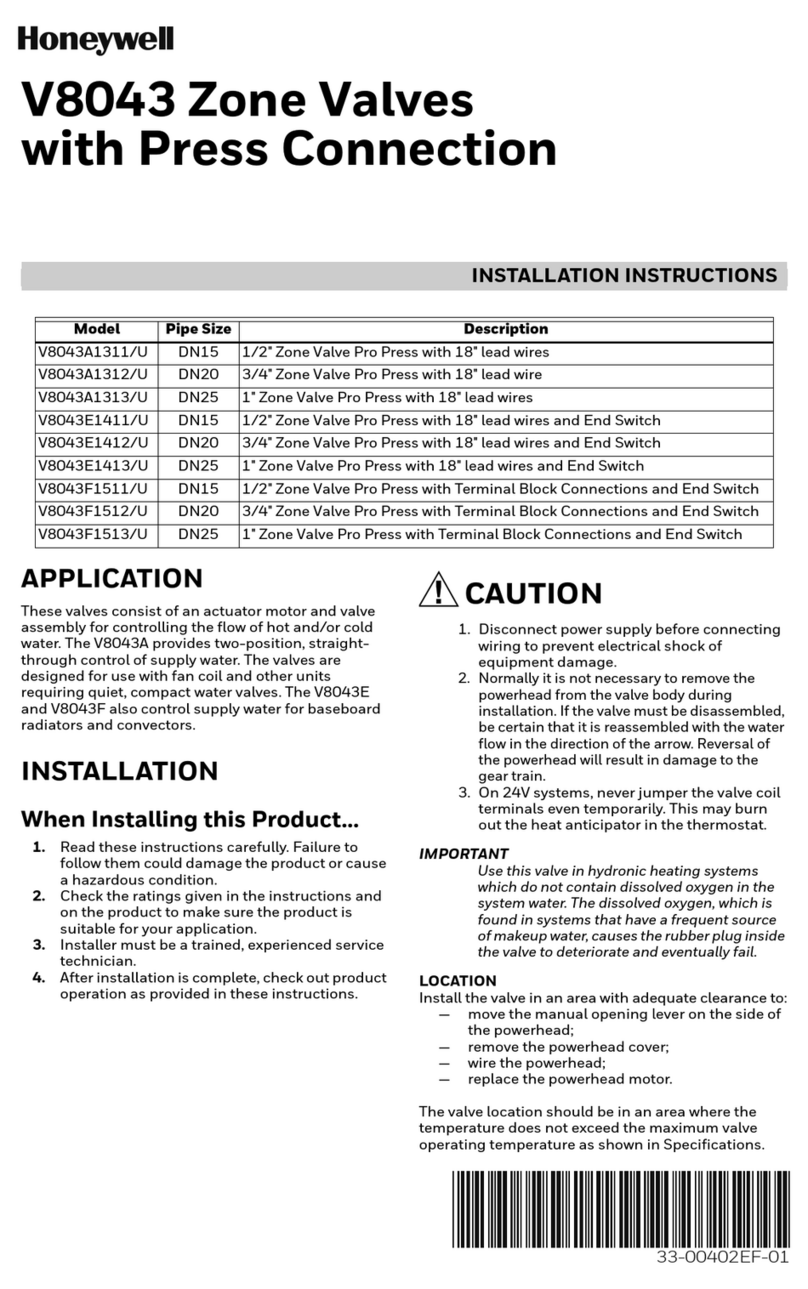
Honeywell
Honeywell V8043A1312/U installation instructions
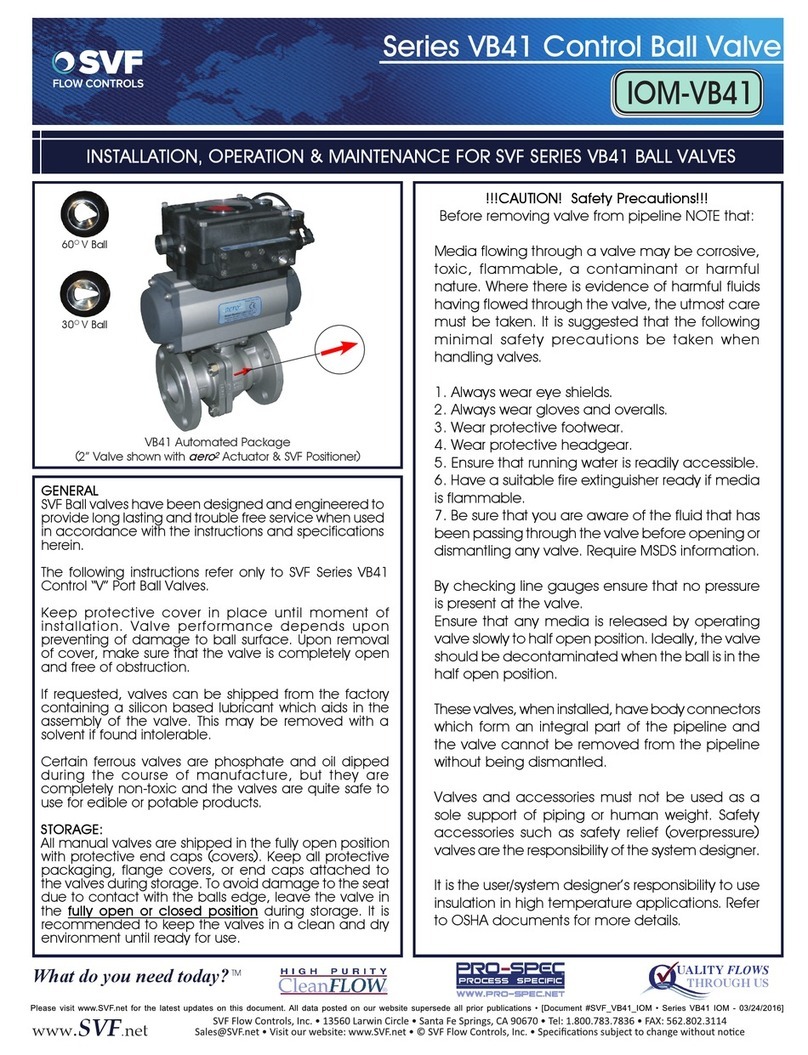
SVF
SVF VB41 Series Installation operation & maintenance
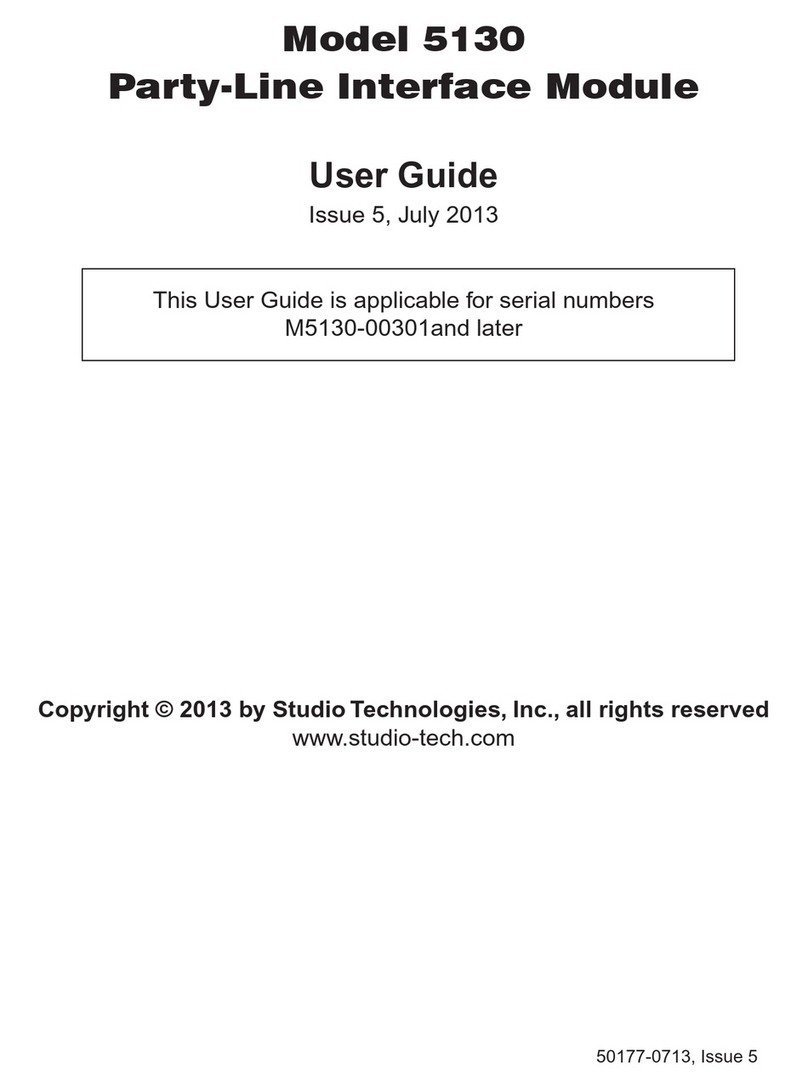
Studio Technologies
Studio Technologies 5130 user guide
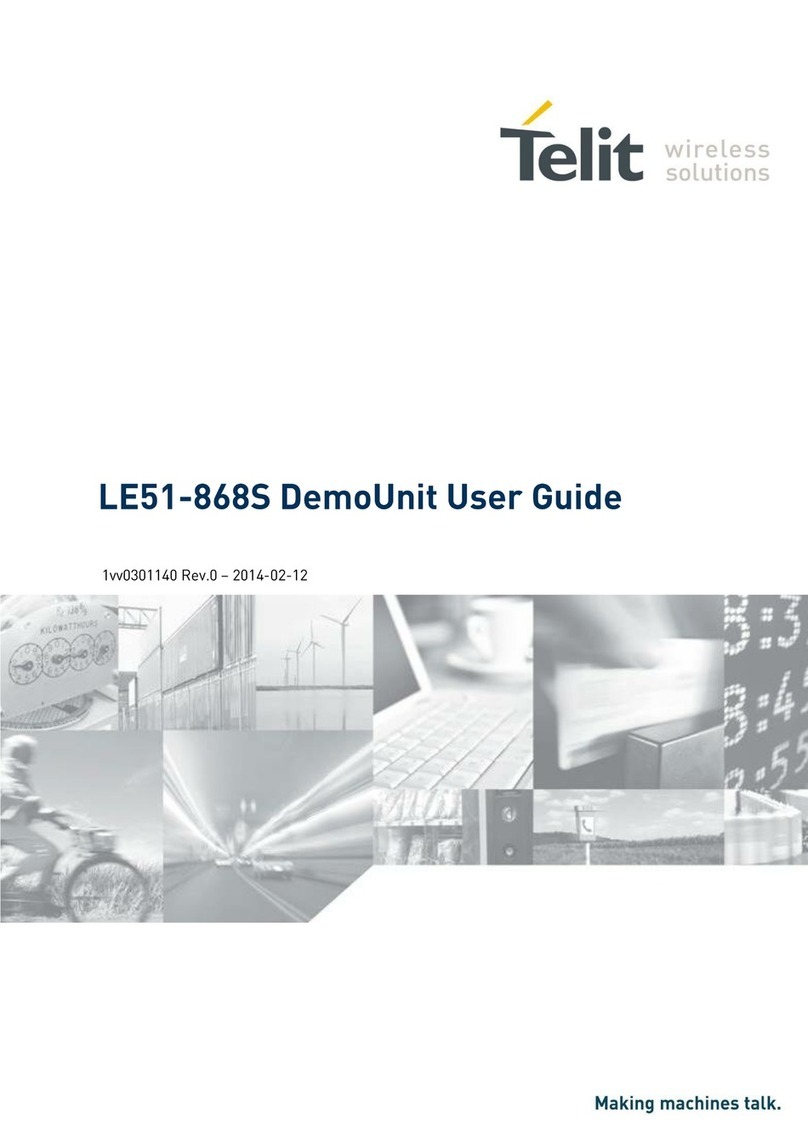
Telit Wireless Solutions
Telit Wireless Solutions LE51-868S DemoUnit user guide