BW SENSING GI540 Series User manual

GI540 Serials
High Precision FOG Integrated
Navigation System
Technical Manual

GI540
High Precision FOG Integrated Navigation System
Applications
●Antenna stabilization platform,drone flight control
●Navigation and control of AGV
●Attitude measurement and orientation reference
BW-GI540 is a high-performance high-precision fiber micro-inertial navigation system developed
by Bewis for aviation mapping, unmanned aerial vehicles, sea-based and roadbed fields. Built-in
three-axis gyroscope (single-axis fiber, dual-axis MEMS) The three-axis accelerometer includes a
BD/GPS/GLONAS three-mode receiver that measures the speed, position, and attitude of the
carrier.
The BW-GI540 is equipped with a new integrated navigation sensor fusion algorithm engine. It is
optimized for multipath interference and can meet the needs of long-term, high-precision and
high-reliability navigation applications in urban and outdoor complex environments. The product
supports a variety of sensors such as GNSS/odometer/DVL/barometric altimeter and has excellent
scalability. It combines inertial measurement with satellite navigation and odometer information
through multi-sensor data fusion technology. These can greatly improve the system's geographical
adaptability.
BW-GI540 integrated navigation system adopts coupling technology. It combines high-precision,
professional-grade, multi-channel, dual-antenna single-frequency carrier phase and pseudo-range
GPS receivers with high-precision fiber inertial measurement units.It has the characteristics of small
size, light weight and high performance.
Introduction
BEWIS SENSING TECHNOLOGY LLC
www.bwsensing.com Tel: +86 510 8573 7158

GI540
High Precision FOG Integrated Navigation System
Interface
characteristics
Power supply
Electrical interface
Data update rate
Environment
Operating temperature
Storage temperature
Size
Weight
Connector
-40°C ~ +60°C
-55°C ~ +85°C
Φ89mm×118 mm(designable)
≤600 g
Y11P-1210ZK10
Physical
characteristics
Attitude accuracy
(2m baseline)
Satellite signal loss
Rolling attitude accuracy
Pitch attitude accuracy
0.1 deg
0.15deg /5min;1.5 deg /1h
≤0.8 deg
≤0.8 deg
Combined external
GPS
Speed accuracy
Single point positioning accuracy
Directional accuracy
0.1m/s
DGPS accuracy 0.5m
/RTK accuracy 2cm
0.1deg,(2m baseline )
Measuring range
Azimuth
Roll angle
Pitch angle
Angular velocity
Acceleration
±180 deg
±90 deg
±90 deg
±300 deg/s
±4 g
9~36 VDC, ≤8 W @ 24VDC
RS422
100 Hz @ 115,200 baud rate
Performance Specifications
Specifications
BEWIS SENSING TECHNOLOGY LLC
www.bwsensing.com Tel: +86 510 8573 7158

GI540
High Precision FOG Integrated Navigation System
Product Size
Product Size:Φ89× 118(mm)
BEWIS SENSING TECHNOLOGY LLC
www.bwsensing.com Tel: +86 510 8573 7158
Note: Unfilled dimensional tolerances are performed in accordance with GB/T1804-2000 Class C.

GI540
High Precision FOG Integrated Navigation System
BEWIS SENSING TECHNOLOGY LLC
www.bwsensing.com Tel: +86 510 8573 7158
Product installation
The correct installation method can avoid measurement error. The inertial measurement unit
produces an absolutely smooth surface by grinding on the underside and measuring surface for
installation .The following points should be made when installing the sensor:
Finally,after the product is tightly attached,screws should be used to fix the IMU to ensure tight
fixation,smooth conduct and stable rotation.Measurement errors caused by acceleration and
vibration should be voided.Bear in mind that the screw only plays a fixed role and doe not have a
positioning function.The screw hole of the IMU is processed into an elliptical shape for easy
adjustment.
First of all, to ensure that the sensor mounting surface and the measured surface completely close,
the measured surface should be as horizontal as possible, so that we can reduce installation error.
Secondly,when the product is installed,the bottom surface of the IMU and the body should be
coincident,and it is gently pushed to make the measurement surface of the IMU coincide with that of
the machine body,so that both surfaces are tightly attached,and there is no angle in Fig.A and
Fig.C.The correct installation is shown in Fig.B and Fig.D.
the measured surface the measured surface
C D
the measured surface the measured surface
AB
uneven surface
generates the
angle
uneven surface
generates the
angle

GI540
High Precision FOG Integrated Navigation System
Debugging software
Software usage steps:
①
②
③
Ensure that the inertial navigation is absolutely static,correctly connect the serial port hardware of
the integrated navigation,and connect the power supply.
Select the computer serial port and baud rate and click to connect to the serial port.
Enter the correct geographic latitude,click Inertial Navigation Start→Command Input,the working
status on the screen shows static alignment,and the working state becomes INS navigation.At this
time,the inertial navigation enters the working state and can be used.
Electrical connections
Data cable RS422 interface definition, DB9 female:
DB9 connector pin Interface definition Remarks
1 R+Receive +
2 R-Receive -
3 T+Transmit +
4 T-Transmit -
BEWIS SENSING TECHNOLOGY LLC
www.bwsensing.com Tel: +86 510 8573 7158

GI540
High Precision FOG Integrated Navigation System
Protocol
After the system is powered on, the normal operating time is 20Hz frequency, RS422 communication 115200bps,
n, 8, 1 broadcast broadcast navigation data, 48 bytes per frame data as shown in the following table:
Navigaon data
Byte number Content Data type Byte count
1-2 Frameheader: 0X5A0X A5 Byte 2
3
Workingstatus:0- Monitoring
status,1-Stacalignment,2-INS
navigaon
Byte 1
4-5 Ineralpitchangle([-90,90]
degrees) in units of 0.01 degrees
Short int (low byte first,high byte
last)
2
6-7
Ineralguiderollangle
([-180,180]degrees), unit 0.01
degree
2
8-9
Ineralazimuth([-180,180]
degrees),northto eastis -, north
to west is +, unitis 0.01degrees
2
10-11
neralX-axisangularvelocity
Wx(degree/s) in units of 0.01
deg/s
2
12-13
neral Y-axis angular velocity
Wy(degree/s) in units of 0.01
deg/s
2
14-15
neral Z-axis angular velocity
Wx(degree/s) in units of 0.01
deg/s
2
16-17 Ineral X-axis acceleraon Ax(m/
s / s), unit0.01m / s/ s 2
18-19 Ineral Y-axisacceleraonAy (m /
s / s), unit 0.01m / s/ s 2
20-21 Ineral Z-axis acceleraon Az (m /
s / s), unit0.01m / s/ s 2
22-23 Speed aer GPS satellite
posioning, unit 0.1 m / sec 2
24-25
GPS trackangle([-180,180]
degrees), north to the east is -,
north to west is +, the unit is 0.1
degrees
2
26-27 GPS satellite number 2
28-29 GPS altude, unit 0.1 m 2
30-33 Latude aer GPS satellite
posioning, unit degree
Float(low byte first, high byte
aer), value range [-90,90]
degrees, the north latude is +
and the south latude is -.
4
34-37 Longitude aer GPS satellite
posioning, unit degree
Float (low byte first, high byte
aer), value range[-180,180]
degrees, east longitude is +,west
4
BEWIS SENSING TECHNOLOGY LLC
www.bwsensing.com Tel: +86 510 8573 7158

GI540
High Precision FOG Integrated Navigation System
Executive standard
●Enterprise Quality System Standard: ISO9001:2008 Standard(Certificate No.:10114Q16846ROS)
●CE certification (certificate number: 3854210814)
●ROHS (certificate number: SO81426003)
●GJB 2426A-2004 Fiber Optic Gyro Test Method
●GBT 18459-2001 sensor main static performance index calculation method
●JF 1059-1999 Evaluation and Expression of Measurement Uncertainty
●GBT 14412-2005 mechanical vibration and shock mechanical installation of accelerometer
●General requirements for GJB 450A-2004 equipment reliability
●Quality control of key parts and important parts of GJB 909A
●GJB 899 Reliability Qualification and Acceptance Test
●GJB 150-3A high temperature test
●GJB 150-4A low temperature test
●GJB 150-8A rain test
●GJB 150-12A dust test
●GJB 150-16A vibration test
●GJB 150-18A impact test
●GJB 150-23A Tilt and Swing Test
●GB/T 17626-3A RF electromagnetic radiation immunity test
●GB/T 17626-5A surge (hit) impulse immunity test
●GB/T 17626-8A power frequency magnetic field immunity test
●GB/T 17626-11A voltage dips, short interruptions and voltage changes immunity
●GB/T 2423.22-2012 Environmental testing Part 2:test method Test N:temperature
change(IEC 60068-2-14:2009,IDT)
●GB/T 10125-2012Artificial atmosphere corrosion test Salt spray test(ISO 9227:2006,IDT)
BEWIS SENSING TECHNOLOGY LLC
www.bwsensing.com Tel: +86 510 8573 7158

GI540
High Precision FOG Integrated
Navigation System
Wuxi Bewis Sensing Technology LLC
Address: Building 30, No. 58 Xiuxi Road, Binhu District, Wuxi City
Hotline: 400-618-0510
Tel: +86 510 85737178-801
Email: [email protected]
Website: www.bwsensing.com
Table of contents
Other BW SENSING Car Navigation System manuals
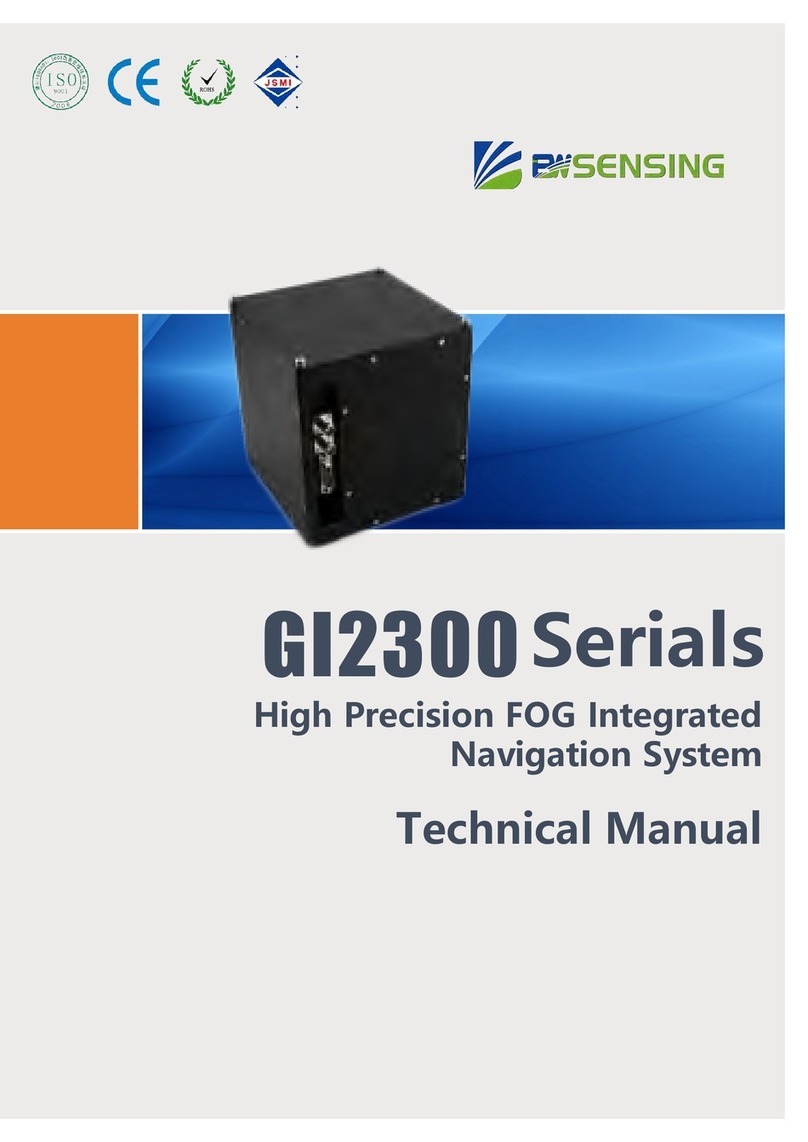
BW SENSING
BW SENSING GI2300 Series User manual

BW SENSING
BW SENSING GI810 Series User manual

BW SENSING
BW SENSING GI2400 Series User manual
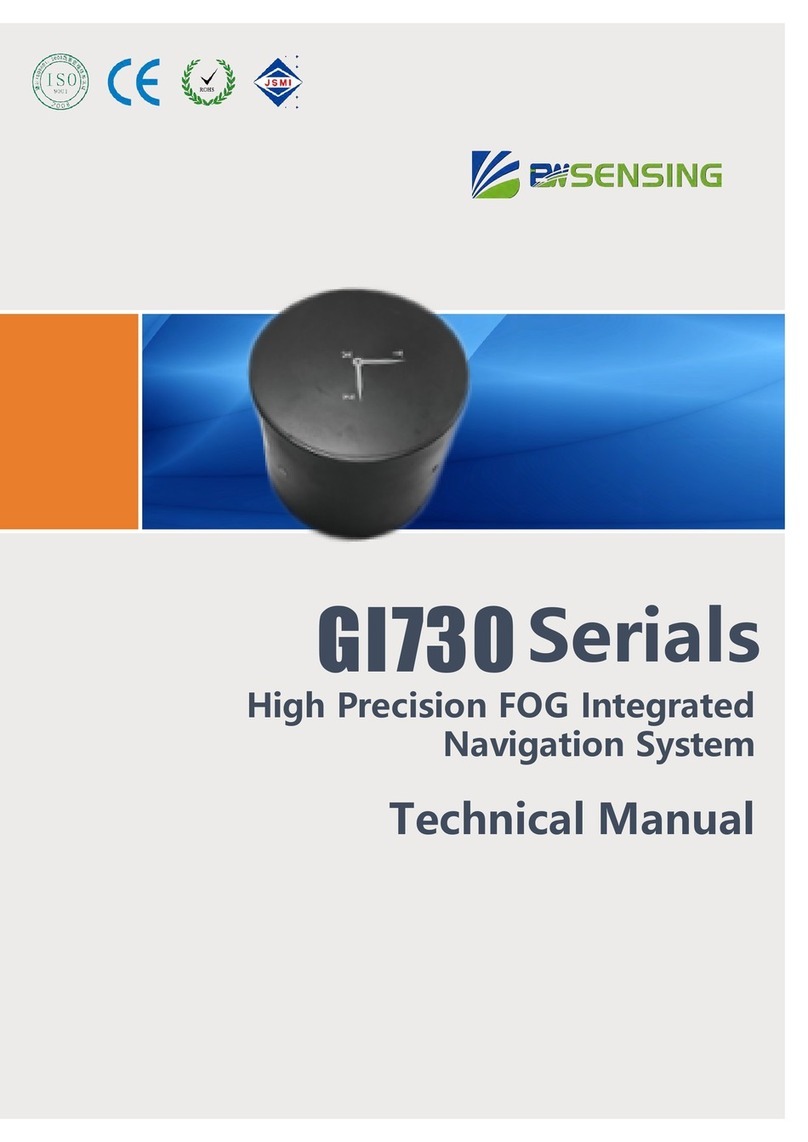
BW SENSING
BW SENSING GI730 Series User manual
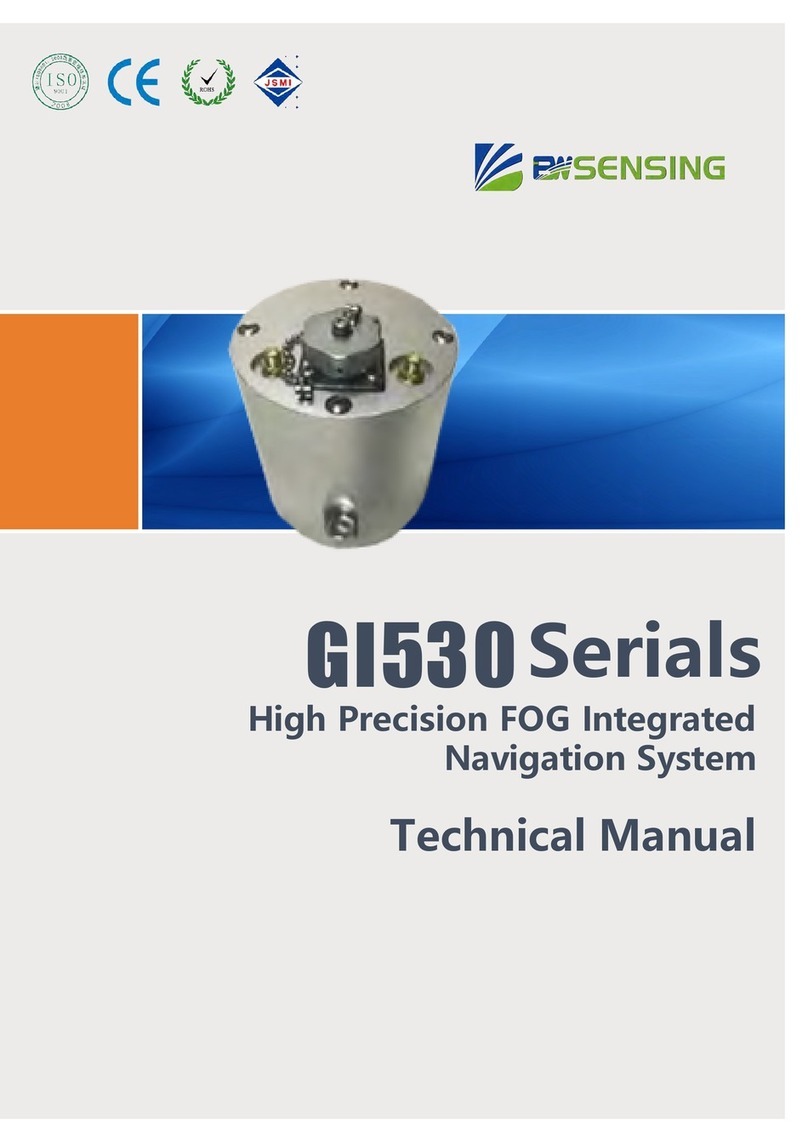
BW SENSING
BW SENSING GI530 Series User manual
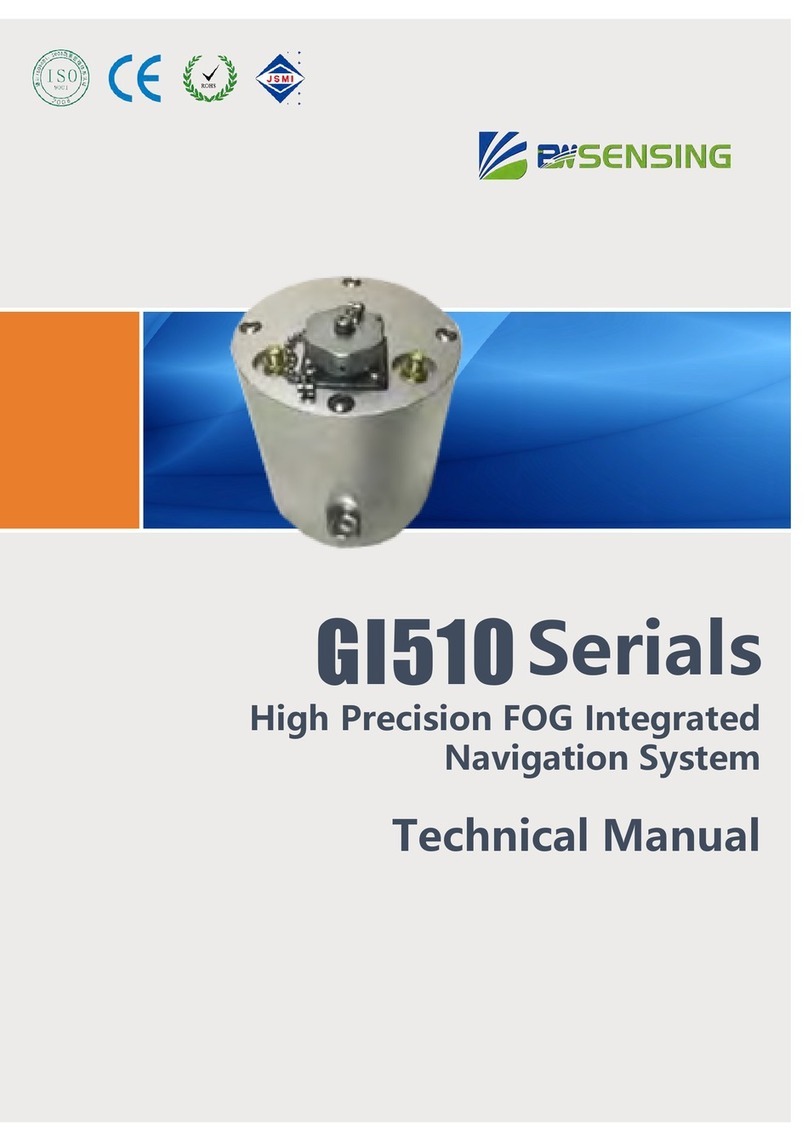
BW SENSING
BW SENSING GI510 Series User manual
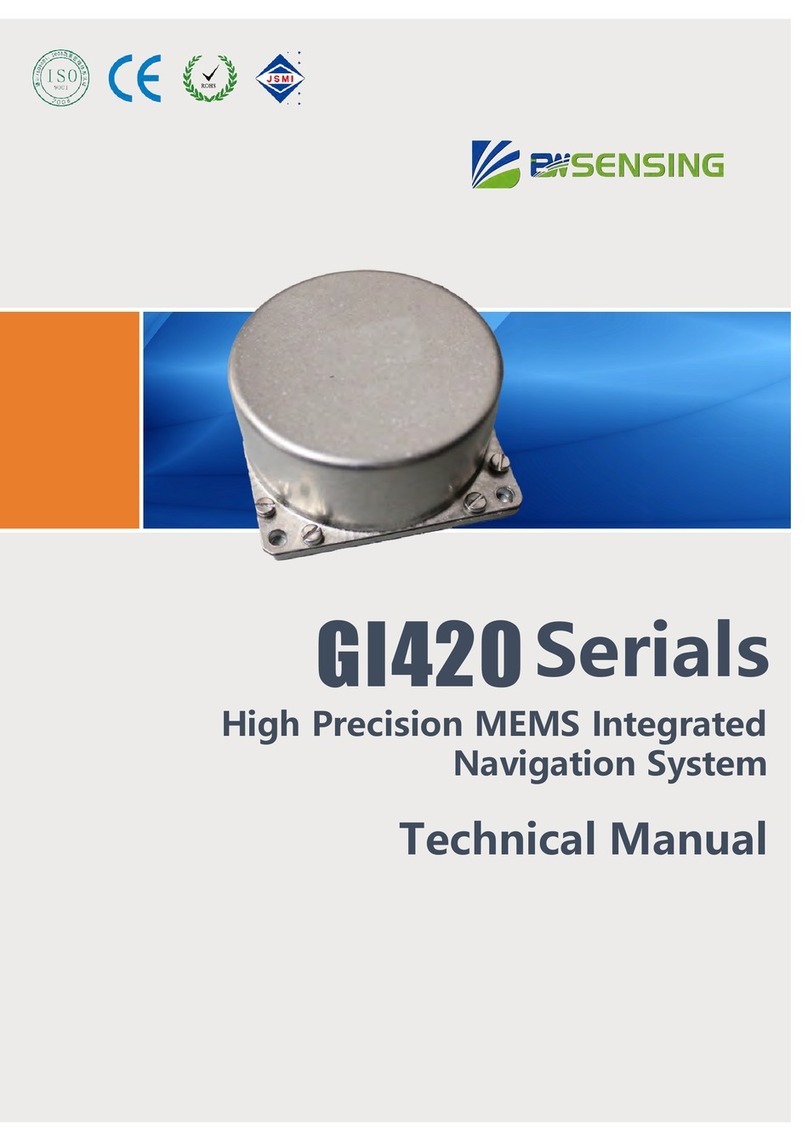
BW SENSING
BW SENSING GI420 Series User manual
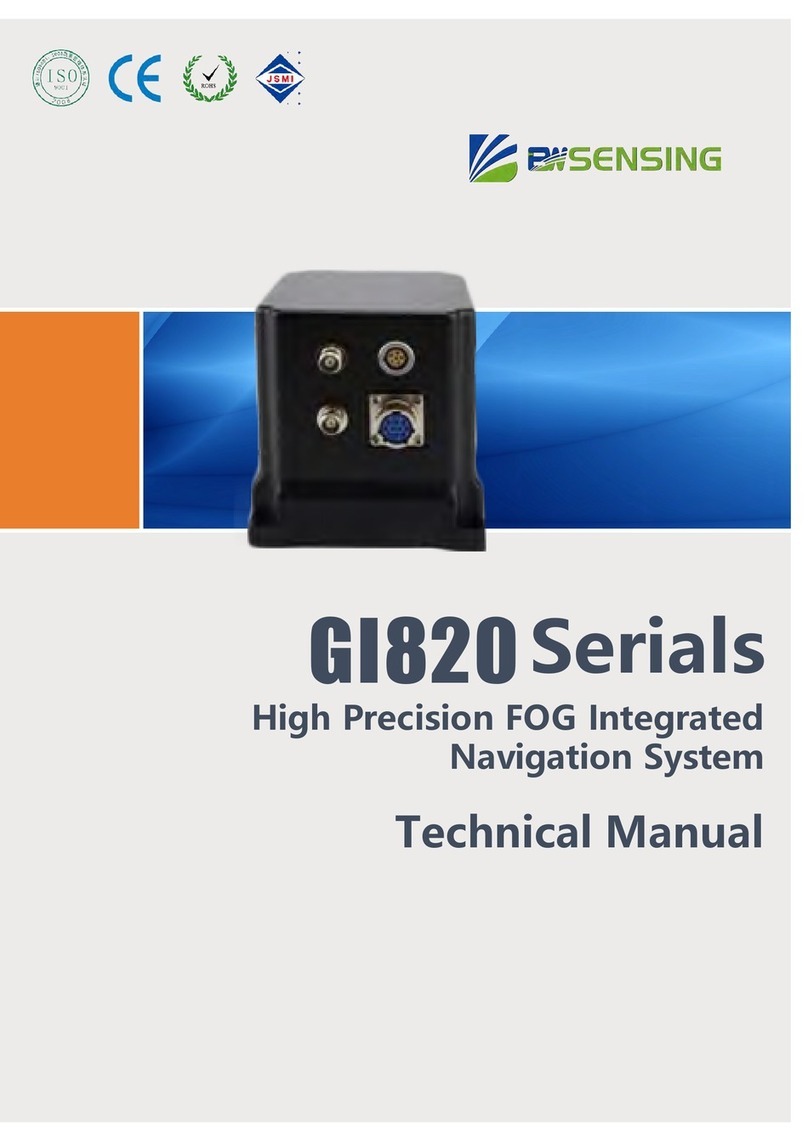
BW SENSING
BW SENSING GI820 Series User manual
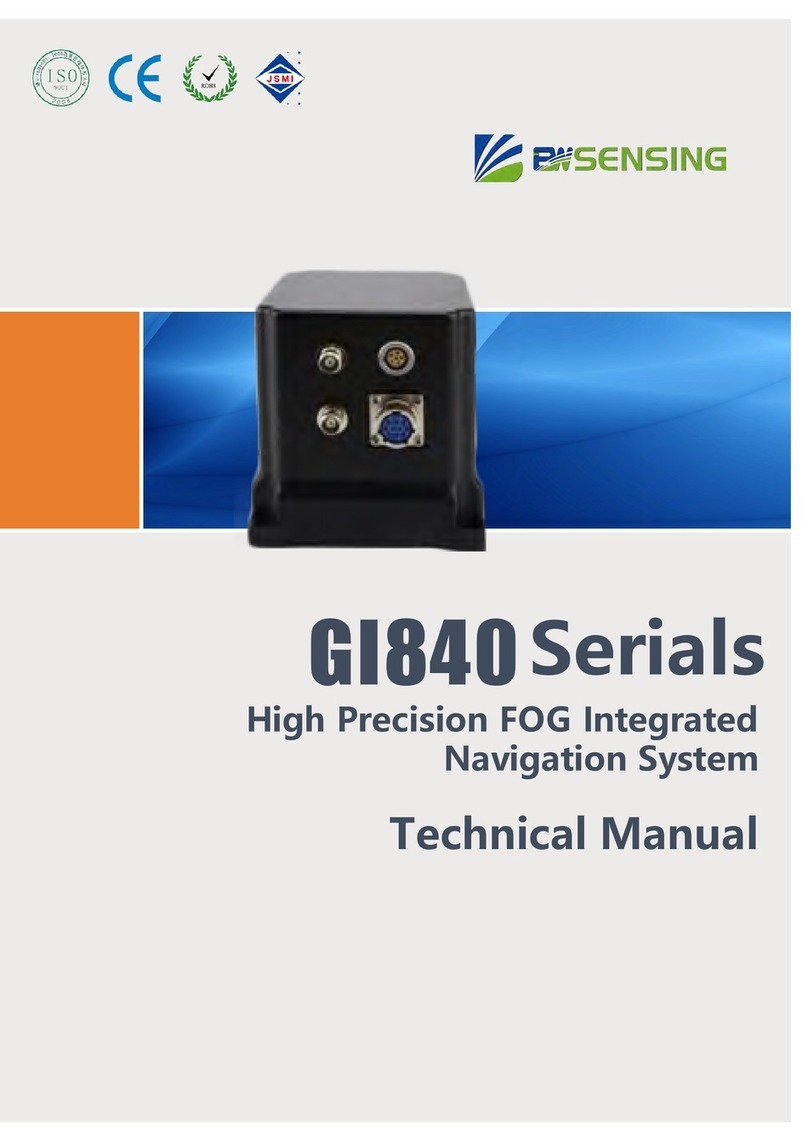
BW SENSING
BW SENSING GI840 Series User manual
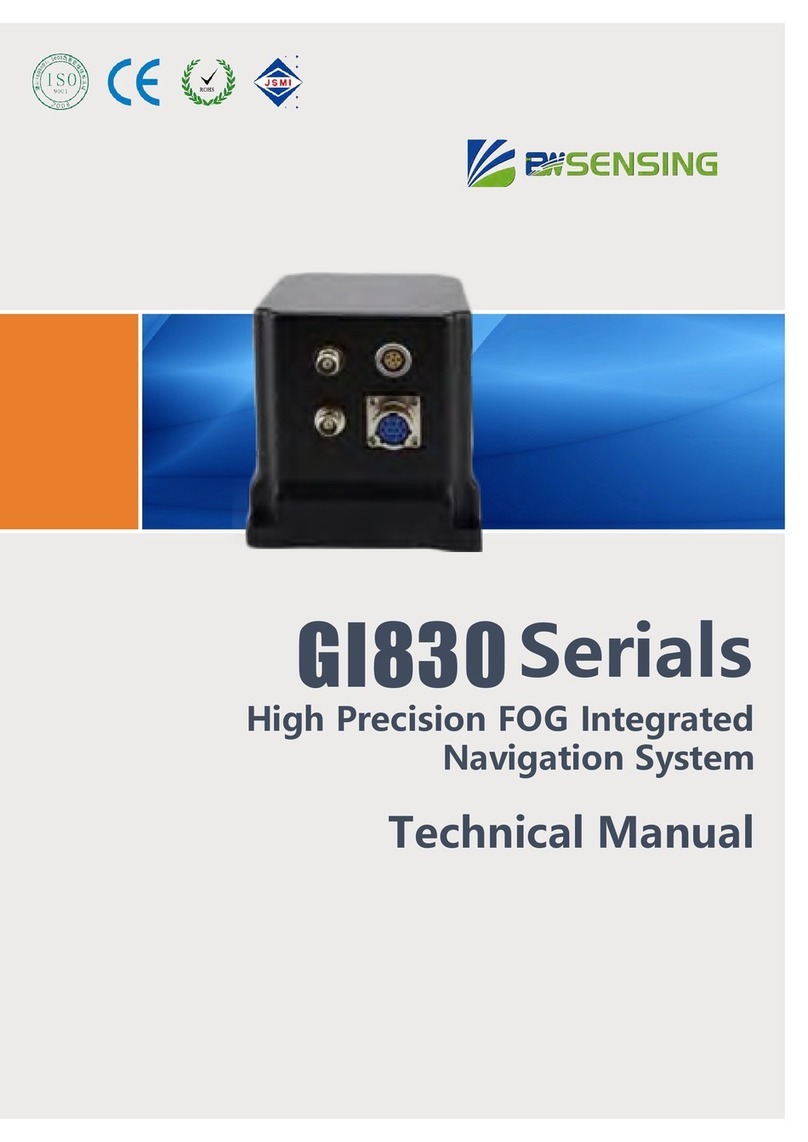
BW SENSING
BW SENSING GI830 Series User manual