Caron Measurement & Controls TC-200 User manual

Top Cut Sampler Model TC200 Pressurized
TOP CUT
SAMPLER
TC-200 User Manual
CARON MEASUREMENT
& CONTROLS
September 2016
Tyler Palinkas

Caron Measurement & Controls | www.caroncontrols.net
2
TABLE OF CONTENTS
CHAPTER 1SAFETY.............................................................................................................. 3
SECTION 1.1 SAFETY PRECAUTIONS ................................................................................. 3
CHAPTER 2OPTIONAL ACCESSORIES................................................................................... 4
SECTION 2.1 MOUNTING................................................................................................... 4
SECTION 2.2 FLOW SIGNAL .............................................................................................. 4
SUBSECTION 2.2.1 PNEUMATIC..................................................................................... 5
SUBSECTION 2.2.2 FLOW SWITCH ................................................................................. 5
SUBSECTION 2.2.3 DRY CONTACTS............................................................................... 5
SUBSECTION 2.2.4 DIRECT EXTERNAL PNEUMATIC ...................................................... 5
SECTION 2.3 INSULATED &HEATER ENCLOSURE............................................................. 5
CHAPTER 3TOP CUT OPERATION ........................................................................................ 6
SECTION 3.1 SCHEMATIC DRAWINGS................................................................................ 7
SECTION 3.2 INSTALLATION ........................................................................................... 10
SECTION 3.3 CALIBRATION............................................................................................. 11
SECTION 3.4 STARTUP PROCEDURE ................................................................................ 15
SECTION 3.5 PREVENTATIVE MAINTENANCE................................................................... 16
CHAPTER 4TROUBLESHOOTING......................................................................................... 17

Caron Measurement & Controls | www.caroncontrols.net
3
CHAPTER 1……………………………………………….SAFETY
SECTION 1.1 SAFETY PRECAUTIONS
-THE INTERNAL TIMER BATTERY SHOULD ONLY BE CHANGED IN A SAFE
ENVIRONMENT. VERIFY THAT AN EXPLOSIVE ATMOSPHERE IS NOT
PRESENT.
-WHEN SAMPLE IS NOT IN USE ENSURE THAT ALL SWITCHES ARE SET TO
OFF WHEN SAMPLER IS NOT IN USE. THE INTERNAL TIMER SWITCH
SETTING “0” AND THE MASS SAFETY SHUTOFF IN THE “OFF” POSITION.
-THE SAMPLER ENCLOSURE SHOULD BE VENTED INDEPENDENTLY TO A
SAFE LOCATION AND A MINIMUM OF 1.5M FROM ANY ELECTRICAL
ENCLOSURE.

Caron Measurement & Controls | www.caroncontrols.net
4
CHAPTER 2………………………….….OPTIONAL ACCESSORIES
SECTION 2.1 MOUNTING
THE TOP CUT SAMPLER CAN BE MOUNTED IN VARIOUS CONFIGURATIONS.
WALL MOUNTING TABS ARE SHIPPED WITH THE STANDARD SAMPLER
PACKAGE. OPTIONALLY AVAILABLE IS A UNIVERSAL STAND, ALLOWING
THE SAMPLER TO BE LOCATED ON ANY LEVEL SURFACE. CUSTOM BUILT
STANDS ARE AVAILABLE UPON REQUEST.
SECTION 2.2 FLOW SIGNAL
IN ORDER FOR THE SAMPLER TO ACCURATELY SAMPLE IN PROPORTION TO
FLOW, A BOOLEAN (TRUE OF FALSE) FLOW CONDITION SIGNAL CAN BE
SUPPLIED TO THE SAMPLER. THE INTRINSICALLY SAFE ELECTRONICS CAN
TAKE SIGNAL FROM ANY ISOLATED DRY CONTACT. ANY EXTERNAL
WIRING SHOULD BE DONE USING BLUE CABLE TO INDICATE INTRINSIC
WIRING, AS WELL AS MAINTAINING ISOLATION FROM ANY NON-INTRINSIC
WIRING. A CLOSED LOOP CONDITION INDICATES FLOWING, WHILE OPEN
INDICATES NOT FLOWING.
SUBSECTION 2.2.1 PNEUMATIC
OUR STANDARD SAMPLER IS EQUIPPED WITH A PNEUMATIC
PRESSURE SWITCH WHICH ACCEPTS A 30PSI SIGNAL TO INDICATE A
FLOWING CONDITION. THE SIGNAL CAN COME DIRECTLY FROM A
LEVEL CONTROLLER OUTPUT, OR VIA SOLENOID VALVE
CONTROLLED BY A PLC FOR FLOW PROPORTIONAL SAMPLING.

Caron Measurement & Controls | www.caroncontrols.net
5
SUBSECTION 2.2.2 FLOW SWITCH
A STAINLESS STEEL FLOW SWITCH CAN BE
WIRED TO THE SAMPLER TIMER TO INDICATE A
FLOWING CONDITION. THIS ALLOWS FOR A
COMPLETELY SELF CONTAINED ELECTRICAL
FLOW SIGNAL SYSTEM. NO NEED FOR
EXTERNAL POWER OR LOGIC. THE FLOW
SWITCH REQUIRES A 1-1/2”NPT CONNECTION ON THE TOP OF A
HORIZONTAL SECTION OF PIPE.
SUBSECTION 2.2.3 DRY CONTACT
THE TOP CUT SAMPLER CAN ALSO UTILIZE ANY ISOLATED DRY
CONTACT TO INDICATE FLOW. CARE MUST BE TAKEN TO FOLLOW
CEC GUIDELINES TO MAINTAIN INTRINSIC SAFETY. PLEASE
CONTACT A MEMBER OF OUR TEAM FOR MORE INFORMATION ON
THIS CONFIGURATION.
SUBSECTION 2.2.4 DIRECT EXTERNAL PNEUMATIC
A DIRECT EXTERNAL PNEUMATIC CONTROL SIGNAL CAN ALSO BE
USED TO ACTUATE THE PUMP. WITH THIS OPTION, THE UNIT WILL
BE EQUIPPED WITH A SELECTION VALVE TO ALTERNATE FROM
INTERNAL TIMER CONTROL, TO EXTERNAL CONTROL, BYPASSING
THE ELECTRONIC TIMER COMPLETELY. SEE SCHEMATICS IN
SECTION 3.1 FOR MORE INFORMATION.
SECTION 2.3 INSULATED AND HEATED ENCLOSURE
FOR OUTDOOR OPERATION THE TOP CUT SAMPLER IS AVAILABLE WITH
AN INSULATED AND HEATED ENCLOSURE. THE THERMOSTAT
CONTROLLED HEATER WILL MAINTAIN ABOVE FREEZING TEMPERATURES
INSIDE THE SAMPLER. THE HEATER REQUIRES A 120-240VA C POWER
SOURCE. PLEASE CONTACT THE SALES DEPARTMENT FOR MORE
DETAILED HEATER SPECIFICATIONS.

Caron Measurement & Controls | www.caroncontrols.net
6
CHAPTER 3…………………………………TOP CUT OPERATION
THE TOP CUT SAMPLER ELECTRONICS OPERATE ON ONE 6 VOLT PC915
ALKALINE BATTERY. OPERATING LIFE OF THE BATTERY VARIES WITH SAMPLING
FREQUENCY, BUT WILL GENERALLY LAST 6 TO 18 MONTHS.
THE SAMPLER OPERATES ON A TIME BASED INTERVAL. THE BUILT IN TIMER IS
TRIGGERED WHEN THE LOOP IS CLOSED ACROSS FLOW SIGNAL INPUT
TERMINALS (FLOW SIGNAL OPTIONS LISTED IN SECTION 2.2). THE TIMER IS
RETENTIVE IN-BETWEEN CYCLES OF THE FLOW SIGNAL INPUT. THIS MEANS
THAT IF THE SIGNAL INPUT IS OPENED BEFORE THE TIMER RUNS OUT, THE TIMER
WILL PAUSE, AND RESUME FROM THE REMAINING TIME THE NEXT TIME THE
INPUT IS CLOSED.
WHEN THE FLOW CONDITION INPUT IS CLOSED, THE TIMER BEGINS TO COUNT.
WHEN THE TIME SETTING IS REACHED, THE PULSE VALVE WILL SWITCH ON FOR
2 SECONDS, THEN OFF AGAIN FOR 2 SECONDS, AT WHICH POINT THE TIMER WILL
RESET AND START COUNTING UNTIL THE INPUT GOES OPEN. IN THE ON
POSITION, THE PULSE VALVE STROKES THE SAMPLE PUMP AND PUSHES THE
SAMPLE FLUID THROUGH THE BACKPRESSURE VALVE AND INTO THE SAMPLE
CONTAINER. WHEN OFF, THE PUMP RETURNS TO ITS RESTING POSITION,
DRAWING ANOTHER SAMPLE FROM THE PROCESS.
THE INTERVAL TIME SETTING IS SELECTABLE FROM THE 8 POSITION SWITCH
INSIDE THE SAMPLER TIMER BOX. SETTING 0 IS RESERVED FOR THE OFF
POSITION, WHILE 1 THROUGH 7 ARE PROGRAMMABLE SET POINTS. THE SET
POINTS ARE SET UP CUSTOM FOR EACH UNIQUE INSTALLATION AND ARE
MARKED IN SHIPPING HOURS PER DAY. THE TIMER CHIPS ARE FIELD
REPLACEABLE TO ACCOMMODATE CHANGES IN PROCESS CONDITIONS. FOR
MORE INFORMATION PLEASE CONTACT OUR SUPPORT TEAM.
TIME SETTING SHOULD BE SET TO FILL THE SAMPLE CONTAINER WITH 7.2L OF
FLUID AT THE END OF THE CHOSEN SAMPLE PERIOD. A SAFETY SHUTOFF VALVE
IS USED TO DISABLE THE SAMPLE PUMP WHEN THE SAMPLE CYLINDER REACHES
7.2L. BECAUSE THE SAFETY SHUTOFF USES WEIGHT OF THE SAMPLE CONTAINER
TO GAUGE ITS CONTENTS, IT NEEDS TO BE CALIBRATED TO ACTUAL SAMPLE
DENSITY (SEE SECTION 3.3.1).

Caron Measurement & Controls | www.caroncontrols.net
7
SECTION 3.1 SCHEMATIC DRAWINGS
ITEM
DESCRIPTION
1
PROGRAMMABLE SAMPLER TIMER
2
SAMPLE PUMP
3
7.2L SAMPLE CONTAINER
4
SAMPLE PUMP CONTROL SOLENOID
5
SAFETY SHUTOFF VALVE.DISABLES SAMPLE PUMP WHEN SAMPLE CONTAINER
REACHES A CERTAIN WEIGHT.
6
BACKPRESSURE REGULATING VALVE.PREVENTS SAMPLE FROM FREE FLOWING
THROUGH PUMP.
7
SAMPLE DIVERT VALVE.SELECT SAMPLE TO OPERATING OR TEST CONTAINER.
8
FLOW SIGNAL INPUT DEVICE (STANDARD PNEUMATIC SHOWN.SEE SECTION 2.2
FOR MORE OPTIONS)
9
SAMPLE INLET FILTER
10
OPTIONAL DIRECT EXTERNAL CONTROL 3-WAY VALVE
FIGURE 3.1.1

Caron Measurement & Controls | www.caroncontrols.net
8
FIGURE 3.1.2

Caron Measurement & Controls | www.caroncontrols.net
9
FIGURE 3.1.3

Caron Measurement & Controls | www.caroncontrols.net
10
SECTION 3.2 INSTALLATION
PROPER INSTALLATION IS INTEGRAL TO RELIABLE AND ACCURATE OPERATION
OF YOUR TOPCUT SAMPLER. THE FOLLOWING INFORMATION IS MEANT TO
ASSIST YOU IN SETTING UP THE SAMPLER FOR OPTIMAL OPERATION.
FIRST STEP IS TO FIND AN APPROPRIATE LOCATION FOR THE SAMPLE POINT. IT IS
IMPORTANT TO SELECT A SAMPLE POINT WHERE THE PRODUCT WILL BE WELL
MIXED. WE RECOMMEND THE USE OF A STATIC MIXER UPSTREAM OF THE
SAMPLE POINT FOR MOST APPLICATIONS. VARIOUS SIZES AND STYLES OF MIXER
ARE AVAILABLE; CONTACT OUR SALES DEPARTMENT FOR MIXER AND SAMPLE
QUILL OPTIONS. WHEN INSTALLING THE SAMPLE QUILL, THE BEVELED EDGE
SHOULD FACE UPSTREAM, AGAINST FLOW. IDEALLY THE QUILL SHOULD BE
MOUNTED OFF THE TOP OF THE PIPE. SEE FIGURE 3.2.1 BELOW.
FIGURE 3.2.1
ANOTHER POINT TO CONSIDER WHEN SELECTING A SAMPLE POINT LOCATION IS
THE SAMPLER ITSELF. FIND A SECURE MOUNTING LOCATION FOR THE SAMPLER
AS CLOSE TO THE SAMPLE POINT AS POSSIBLE.

Caron Measurement & Controls | www.caroncontrols.net
11
CONNECT THE SAMPLE PROBER THE FITTING ON THE SAMPLER MARKED
SAMPLE USING 1/4” OR 3/8” TUBING.
CONNECT A CLEAN, DRY 30PSI SUPPLY TO THE FITTING MARKED SUPPLY.
CONNECT THE FLOW INDICATION SIGNAL TO THE SAMPLER. THIS WILL VARY
DEPENDING ON THE SAMPLER CONFIGURATION.
-IF CONFIGURED WITH PNEUMATIC SIGNAL, TUBE THE 10-30PSI SIGNAL TO
THE FITTING MARKED SIGNAL ON THE SAMPLER
-IF CONFIGURED WITH ELECTRONIC SIGNAL, CONNECT THE SIGNAL WIRES
FROM THE DRY CONTACT SWITCH TO THE INPUT TERMINALS USING THE
CONDUIT CONNECTION ON THE SAMPLER. ENSURE A WATERTIGHT CABLE
CONNECTOR IS USED.
SECTION 3.3 CALIBRATION
BEFORE INITIAL USE, AND PERIODICALLY THERE ARE 3 KEY POINTS ON THE
SAMPLER THAT SHOULD BE CALIBRATED TO ENSURE ACCURATE AND RELIABLE
OPERATION.
IMPORTANT: BEFORE PERFORMING A CALIBRATION, FOLLOW THE STARTUP
PROCEDURE IN THE NEXT SECTION. THE SYSTEM NEEDS TO BE PURGED WITH
FLUID FOR A SUCCESSFUL CALIBRATION.
SUBSECTION 3.3.1 SAMPLE VOLUME
THE SAMPLE PUMP SHOULD ACCURATELY TAKE A 1ML SAMPLE EVERY
STROKE (UNLESS OTHERWISE CONFIGURED). FOR ACCURATE RESULTS,
THE PUMP AND THE SAMPLE TUBING MUST BE PROPERLY PURGED OF
ALL TRAPPED AIR. FOLLOW THE PROCEDURE IN SECTION 3.4 STEP 4 FOR
PURGING UNIT. TO CALIBRATE THE SAMPLE VOLUME FOLLOW THESE
STEPS:
1) TURN THE 8 POSITION SWITCH ON THE TIMER TO THE 0
POSITION, TURNING THE SAMPLER OFF.

Caron Measurement & Controls | www.caroncontrols.net
12
2) REMOVE THE CAP FROM THE SAMPLE TEST PORT AND PLACE A
100ML GRADUATED CYLINDER (OR SIMILAR) UNDERNEATH THE
OPENING.
3) MOVE THE DIVERT VALVE TO SEND THE SAMPLE TO THE TEST
PORT.
4) TURN THE 8 POSITION SWITCH ON THE TIMER TO POSITION 7
(TEST).
5) IF THE FLOW SIGNAL INPUT IS INDICATING FLOW, THE UNIT
WILL START SAMPLING AND PROCEED TO STEP 6. IF NOT PRESS
THE TEST BUTTON FOR TWO SECONDS, AND RELEASE FOR 2
SECONDS TO TAKE A SAMPLE.
6) FILL THE CONTAINER WITH 10 SAMPLES AND MOVE THE
SWITCH BACK TO THE 0 POSITION.
7) THE SAMPLE SHOULD HAVE INCREASED 1ML EVERY STROKE,
ENDING AT 10ML MORE THAN THE INITIAL POSITION. IF THIS IS
NOT THE CASE, ADJUST THE SAMPLE ADJUST KNOB ON
THE SAMPLE PUMP SLIGHTLY. EMPTY THE TEST CYLINDER AND
REPEAT FROM STEP 4.
SUBSECTION 3.3.2 SAFETY SHUTOFF
THE SAFETY SHUTOFF VALVE IS DESIGNED TO DISABLE THE SAMPLE PUMP
WHEN THE SAMPLE CONTAINER IS FULL. IMPROPER SETUP CAN RESULT IN
LOW SAMPLE VOLUME OR A SPILL CAUSED BY OVERFILL. THE VALVE
TYPICALLY COMES PRESET, BUT SHOULD BE SET TO ACTUAL PROCESS
FLUID DENSITY. FOLLOW THESE STEPS TO SET UP THE VALVE.
1) PLACE THE EMPTY CONTAINER AND CONNECT THE SAMPLE
HOSE TO THE CONTAINER. IMPORTANT: MAKE SURE
ANYTHING THAT WOULD BE ON THE CONTAINER OR TRAY
DURING OPERATING CONDITIONS IS PRESENT DURING
CALIBRATION. ANYTHING THAT WOULD AFFECT THE WEIGHT
NEEDS TO BE CONSIDERED.
2) OPEN THE LID OF THE CONTAINER, MAKING SURE TO LEAVE IT
HANGING SOMEWHERE ON THE CONTAINER OR TRAY.

Caron Measurement & Controls | www.caroncontrols.net
13
3) GATHER 7.2L OF ACTUAL PROCESS FLUID OF THE DENSITY THE
SAMPLE WOULD SEE DURING OPERATION.
4) MAKE SURE THE SAFETY SHUTOFF SWITCH IS IN THE ON
POSITION.
5) WHILE KEEPING AN EYE ON THE SAFETY SHUTOFF, BEGIN
POURING THE PROCESS FLUID INTO THE SAMPLE CONTAINER,
SLOWING DOWN WHEN THE SAMPLE CONTAINER GETS CLOSE
TO 7.2L.
6) THEY SAFETY SHUT OFF VALVE SHOULD SNAP TO THE OFF
POSITION JUST AS THE CONTAINER REACHES 7.2L. IF THIS IS
TRUE, CALIBRATION IS COMPLETE. IF IT TRIPPED EARLY
PROCEED TO STEP 7, IF IT DID NOT TRIP AT ALL, PROCEED TO
STEP 8.
7) WITH THE FULL 7.2L IN THE CONTAINER, LIFT THE TRAY
SLIGHTLY AND RESET THE SAFETY SWITCH. LOOSEN THE
LOCKNUT ON THE SPRING ADJUST BOLT AND BACK THE
ADJUSTMENT NUT OFF LOOSENING THE SPRING UNTIL YOU ARE
ABLE TO LOWER THE TRAY AND THE SSV DOES NOT TRIP.
8) WITH THE TRAY FULLY SUPPORTED BY THE SPRING LOOSEN THE
LOCKNUT ON THE SPRING ADJUST BOLT (IF YOU HAVEN’T
ALREADY DONE SO) AND BEGIN TO TIGHTEN THE ADJUSTMENT
NUT, TIGHTENING THE SPRING. CONTINUE SLOWLY
TIGHTENING THE NUT, WATCHING THE SSV, UNTIL IT TRIPS.
STOP TIGHTENING AND SECURE THE LOCKING NUT. THE SPRING
SHOULD NOW BE CLOSE THE 7.2L SETTING, BUT CALIBRATION
IS NOT YET COMPLETE.
9) REMOVE AND COLLECT A SMALL PORTION OF THE SAMPLE
FROM THE CONTAINER AND RESET THE SAFETY SHUT OFF.
10) REPEAT STEP 5, THEN MOVE TO STEP 11
11) IF THE SAFETY SHUT OFF DID NOT SNAP JUST AS THE
CONTAINER REACHED 7.2L CONTINUE TO STEP 12. IF IT DID,
CALIBRATION IS COMPLETE
12) LOOSEN THE ADJUSTMENT LOCKNUT AND MAKE A SMALL
ADJUSTMENT TO THE ADJUSTMENT NUT. IF THE SSV TRIPPED

Caron Measurement & Controls | www.caroncontrols.net
14
EARLY, TIGHTEN THE NUT. IF IT DID NOT TRIP, LOOSEN THE
NET.
13) SECURE THE LOCKNUT AND GO BACK TO STEP 9 AND
CONTINUE.
SUBSECTION 3.3.3 BACKPRESSURE REGULATOR
THE BACKPRESSURE REGULATING VALVE IS DESIGNED TO PREVENT FREE
FLOW OF THE PROCESS FLUID THROUGH THE PUMP. NORMALLY IT IS SET
TO THE MOP OF THE PROCESS. THE PUMP AND TUBING SHOULD BE
PROPERLY PURGED (SECTION 3.4, STEP 4) PRIOR TO PERFORMING THIS
STEP.
NOTE: THIS VALVE SHOULD COME PRESET FROM FACTORY AND SHOULD
NOT REQUIRE ADJUSTMENT UNDER NORMAL CONDITIONS. THIS SECTION
ALSO ASSUMES PRIOR KNOWLEDGE OF SAMPLER OPERATION.
1) SWITCH TIMER TO 0 POSITION
2) DIVERT THE SAMPLE TO A TEST CONTAINER USING THE TEST SAMPLE
OUTLET LINE.
3) LOOSEN LOCKNUT ON BACKPRESSURE VALVE.
4) SWITCH TIMER TO TEST MODE AND MONITOR GAUGE.
5) ADJUST BACKPRESSURE VALVE IN TO RAISE PRESSURE AND OUT TO
LOWER. THE VALVE SHOULD MAINTAIN THE DESIRED SET POINT IN
BETWEEN PUMP CYCLES. DURING A PUMP STROKE, IT SHOULD READ
SLIGHTLY HIGHER.
6) RETURN TIMER TO 0 POSITION
7) TIGHTEN LOCKNUT AND TAG SWITCH.
8) DIVERT SAMPLE BACK TO CONTAINER AND RETURN TIMER TO
OPERATING SET POINT.

Caron Measurement & Controls | www.caroncontrols.net
15
SECTION 3.4 STARTUP PROCEDURE
THE FOLLOWING PROCEDURE SHOULD BE PERFORMED PRIOR TO FIRST USE AND
WHENEVER ANYTHING THAT COULD AFFECT THE SAMPLER OPERATION IS
CHANGED. FOR EXAMPLE, ANYTHING THAT WOULD INTRODUCE AIR TO THE
PROCESS UPSTREAM OF THE SAMPLE POINT CAN CAUSE THE SAMPLER TO
BECOME AIR LOCKED.
1) CHECK AND ENSURE ALL FITTINGS AND CONNECTIONS ARE TIGHT.CLOSE ALL
VALVES AND SET THE SAMPLE DIVERT VALVE TO THE SAMPLE CONTAINER.
2) SET THE 8POSITION SWITCH TO THE “0”POSITION.
3) OPEN THE SAMPLE POINT VALVE.
4) PURGE SYSTEM:TO PURGE SYSTEM,PLACE A CONTAINER UNDERNEATH THE
PUMP BLEED VALVE AND SLOWLY OPEN ½TO 1TURN.ALLOW FLUID TO FLOW
OUT INTO THE CONTAINER UNTIL A CONSTANT AIR FREE STREAM IS OBSERVED.
PROCEED TO TIGHTEN THE BLEED VALVE.
5) CAREFULLY REMOVE THE CAP ON THE TEST SAMPLE OUTLET LINE AND PLACE A
JUG UNDERNEATH.SLOWLY MOVE THE DIVERT VALVE TO THE TEST OUTLET
POSITION.
6) OPEN THE AIR SUPPLY TO THE SAMPLER AND VERIFY THE SET PRESSURE OF
30PSI.SWITCH SAFETY SHUTOFF SWITCH TO THE ON POSITION.
7) SET THE 8POSITION SWITCH TO POSITION 7. IF THE FLOW SIGNAL DEVICE IS
INDICATING FLOW,THE PUMP WILL BEGIN TO STROKE.IF NOT,PRESS THE TEST
BUTTON FOR 2SECONDS AND RELEASE FOR A MINIMUM OF 2SECONDS TO
MANUALLY STROKE THE SAMPLE PUMP.CONTINUE TO SAMPLE UNTIL
CONTINUOUS AIR FREE SAMPLES ARE OBSERVED FROM THE TEST SAMPLE
OUTLET.
8) VERIFY 1MLPER SAMPLE.FOR HELP ON THIS STEP SEE “SAMPLE VOLUME”
CALIBRATION IN SECTION 3.3.1. ONCE COMPLETE,RETURN THE 8POSITION
SWITCH TO THE 0POSITION AND REPLACE THE CAP ON THE TEST SAMPLE
OUTLET LINE.
9) INSTALL EMPTY SAMPLE CONTAINER AND CONNECT QUICK CONNECT IF NOT
ALREADY INSTALLED.
10) MOVE DIVERT VALVE TO THE SAMPLE CONTAINER POSITION.
11) SET 8POSITION SWITCH TO THE DESIRED SET POINT.MONITOR SAMPLER TO
VERIFY PUMP OPERATION WHILE RUNNING.

Caron Measurement & Controls | www.caroncontrols.net
16
SECTION 3.4 PREVENTATIVE MAINTENANCE
THE FOLLOWING STEPS SHOULD BE PERFORMED PERIODICALLY TO MAINTAIN
RELIABLE SAMPLER OPERATION. OVER THE FIRST FEW WEEKS, CHECK MORE
FREQUENTLY AND TAKE THE TIME DO DEVELOP A MAINTENANCE SCHEDULE.
1) CHECK SAMPLE FILTER ELEMENT (IF INSTALLED). REMEMBER TO
PROPERLY PURGE PUMP AFTER ANYTIME THE SAMPLE LINE IS OPENED.
2) VERIFY SAMPLE VOLUME CALIBRATION.
3) CHECK TO MAKE SURE SAMPLE TRAY MOVES FREELY.
4) CHECK SAFETY SHUTOFF CALIBRATION.

Caron Measurement & Controls | www.caroncontrols.net
17
CHAPTER 3………………………………..…TROUBLESHOOTING
SYMPTOM
POSSIBLE CAUSE
SOLUTION
NO SAMPLE FLOW,BUT
PUMP IS STROKING
PUMP IS AIR LOCKED
PURGE SAMPLE PUMP.SEE
SECTION 3.4 STEP 4. CHECK
SAMPLE FILTER IF
INSTALLED.
SAMPLE LINE OR FILTER IS
PLUGGED
CLEAN SAMPLE FILTER AND
PURGE PUMP.
AVALVE IS CLOSED
CHECK VALVING
SAMPLE PUMP IS NOT
STROKING,BUT PUMP
CONTROL SOLENOID IS
MAKING CLICKING SOUND
INADEQUATE SUPPLY
PRESSURE
CHECK TO ENSURE 30PSI
SUPPLY TO SAMPLER
PLUGGED SIGNAL LINE
CHECK TO SEE IF IA SUPPLY
IS PRESENT RIGHT AT
SAMPLE PUMP DURING A
STROKE.TRACE PRESSURE
TO FIND BLOCKAGE.
SAMPLE PUMP IS NOT
STROKING,SOLENOID IS NOT
CLICKING
NO FLOW SIGNAL
TO TEST,SET TIMER TO
SETTING 7, AND JUMPER THE
FLOW SIGNAL INPUT
TERMINALS.IF PUMP
STROKES,CHECK FLOW
SIGNAL DEVICE
LOW BATTERY VOLTAGE
CHECK BATTERY VOLTAGE,
REPLACE IF NECESSARY
FAILED SOLENOID VALVE
CONTACT SALES
DEPARTMENT FOR
REPLACEMENT PARTS

Caron Measurement & Controls | www.caroncontrols.net
18
FAILED ELECTRONICS
TO TEST,SET TIMER TO
SETTING 7, AND JUMPER THE
FLOW SIGNAL INPUT
TERMINALS.IF PUMP
STROKES,ELECTRONICS ARE
OPERATIONAL.CONTACT
SALES DEPARTMENT FOR
REPLACEMENT PARTS
TOO LITTLE SAMPLE
VOLUME
SHIPPING LESS HOURS PER
DAY THEN SET POINT
MODIFY TIMER SETTING TO
LESS HOURS PER DAY
SAMPLE PUMP PARTIALLY
AIR LOCKED
PURGE SAMPLE PUMP.SEE
SECTION 3.4 STEP 4. CHECK
SAMPLE FILTER IF
INSTALLED.
SAMPLE VOLUME
CALIBRATION OUT
CHECK SAMPLE VOLUME
AND CALIBRATE IF
NECESSARY.SEE SECTION
3.3.1 (CHECK FOR AIR
LOCKED PUMP FIRST)
TOO MUCH SAMPLE VOLUME
SHIPPING MORE HOURS PER
DAY THEN SET POINT
MODIFY TIMER SETTING TO
MORE HOURS PER DAY
SAMPLE VOLUME
CALIBRATION OUT
CHECK SAMPLE VOLUME
AND CALIBRATE IF
NECESSARY.SEE SECTION
3.3.1
SAMPLE CONTAINER
OVERFILLS
SOMETHING EFFECTING
SAMPLE TRAY FROM MOVING
FREELY
MAKE SURE NOTHING IS
PLACED UNDERNEATH
SAMPLE TRAY.CHECK FOR
SMOOTH TRAY MOVEMENT
AND SAFETY SHUTOFF
OPERATION.
SAFETY SHUTOFF VALVE
OUT OF CALIBRATION
SEE SECTION 3.3.2 FOR
CALIBRATION
Table of contents
Popular Sampler manuals by other brands
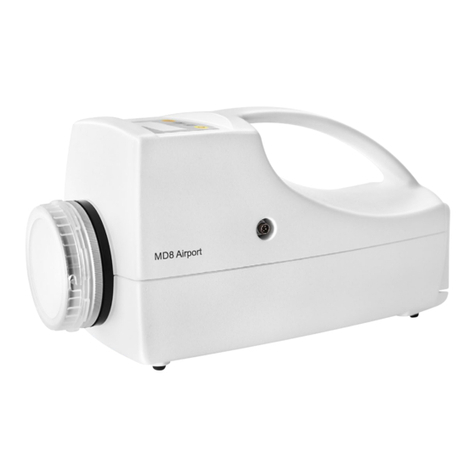
Sartorius
Sartorius MD8 Airport operating instructions
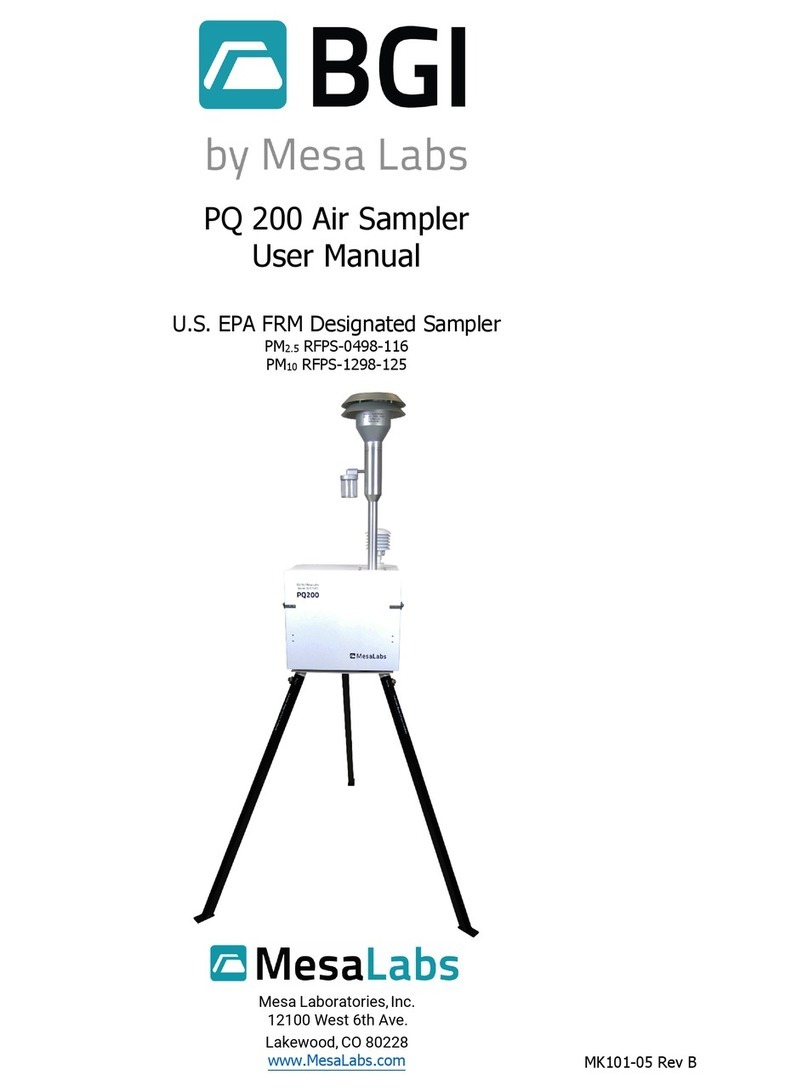
MESA LABORATORIES
MESA LABORATORIES PQ 200 user manual

Spectrex
Spectrex PAS-500 operating manual
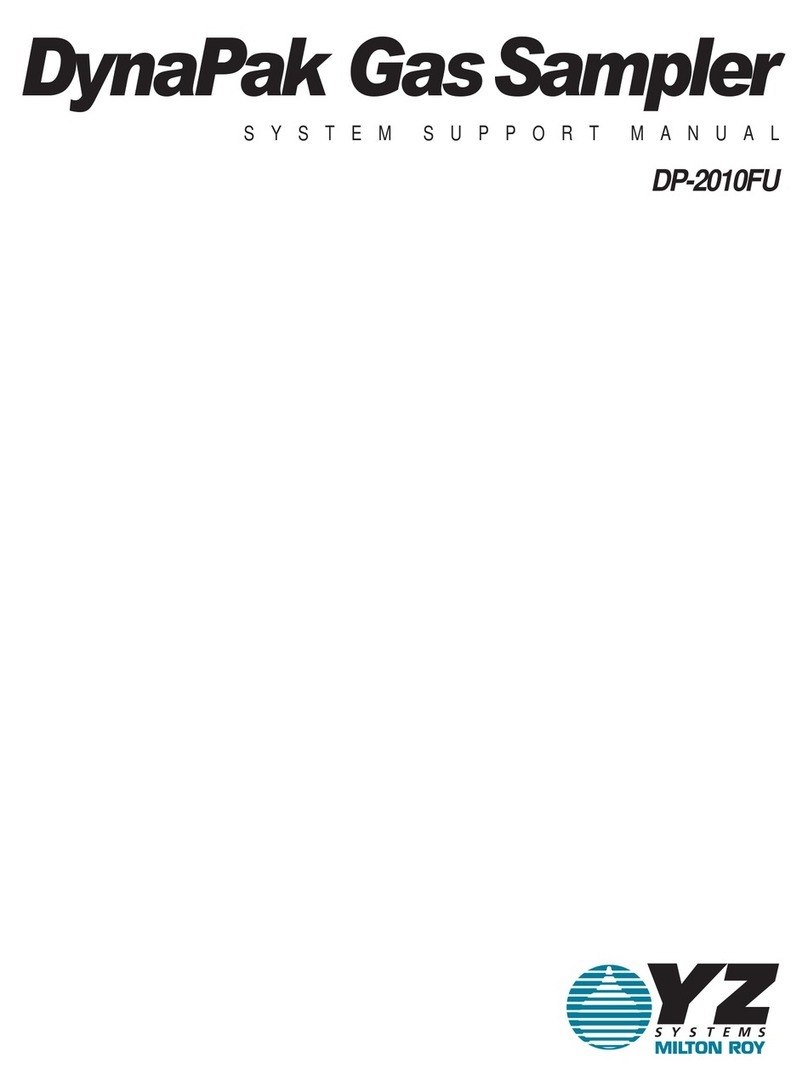
YZ Systems
YZ Systems DynaPak DP-2010FU Instructions & operating manual
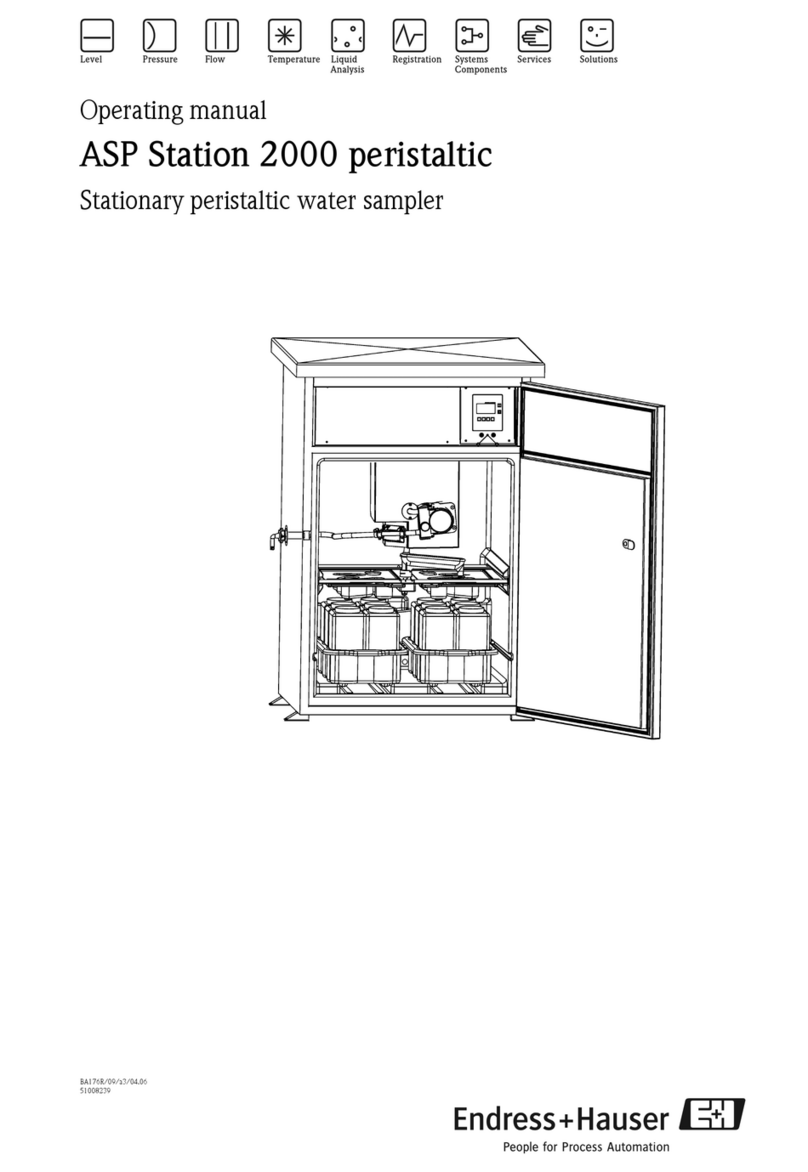
Endress+Hauser
Endress+Hauser ASP Station 2000 peristaltic operating manual
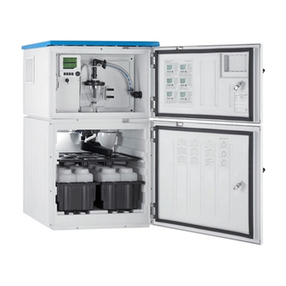
Endress+Hauser
Endress+Hauser Liquistation CSF48 operating instructions