Cascadia PM Series Instructions for use

7929 SW Burns Way Phone: 503 344-5085
Suite F
1/14/2021 RMS PM Hardware User Manual 1 of 54
PM/RM/CM200
Hardware User Manual
Revision 3.3
0A-0001-01
Everything you need to know to install, set up, and calibrate the PM and
RM family of AC drives on asynchronous and PM synchronous motors
in your Electric or Hybrid vehicle

7929 SW Burns Way Phone: 503 344-5085
Suite F
1/14/2021 RMS PM Hardware User Manual 2 of 54
Table of Contents
1. SAFETY FIRST:............................................................................................................ 3
2. FUNCTIONAL OVERVIEW: ......................................................................................... 4
3. INSTALLING THE PM DRIVE: ..................................................................................... 5
3.1 Liquid Cooling Connections: ...................................................................................................................7
3.2 PM100/PM150 External Signal Connectors: ........................................................................................ 10
3.2.1 J1 – 35p AMPSEAL Plug 776164-1 with crimp contact 770854-1.................................................. 10
3.2.2 J2 – 23p AMPSEAL Plug 770680-1 with crimp contact 770854-1.................................................. 12
3.3 PM250 External Connections:............................................................................................................... 13
3.4 RM100 Signal Connections ................................................................................................................... 16
3.5 RM300 Signal Connections ................................................................................................................... 18
3.6 PM500 Signal Connections ................................................................................................................... 21
3.7 CM200 Signal Connector ....................................................................................................................... 24
3.8 External Power Connections: ............................................................................................................... 28
3.6.1 DC+ / DC-:....................................................................................................................................... 28
3.6.2 Phase A / Phase B / Phase C: ......................................................................................................... 30
3.6.3 Pre-Charge Circuit: .......................................................................................................................... 30
3.6.4 Main Contactor: ............................................................................................................................... 32
3.6.5 Main Fuse: ....................................................................................................................................... 32
3.6.6 Passive Discharge of the High Voltage DC Bus: ............................................................................. 32
3.6.7 12V Power: ...................................................................................................................................... 33
3.6.8 Grounding ........................................................................................................................................ 35
3.9 Typical Application Wiring Diagram: .................................................................................................... 36
3.7.1 Controller 12V Power Wiring ........................................................................................................... 37
3.7.2 Pre-charge Circuit ............................................................................................................................ 39
3.7.3 Analog/Digital Vehicle Control ......................................................................................................... 40
3.7.4 Motor Control (Typical Wiring) ......................................................................................................... 41
3.7.5 CAN Interface .................................................................................................................................. 42
3.7.6 RS-232 Interface.............................................................................................................................. 42
3.7.7 Encoder Interface (Not included on RM100/RM300): ..................................................................... 43
3.7.8 Resolver Interface:........................................................................................................................... 44
4. VEHICLE INTERFACE SETUP .................................................................................. 45
4.1 Analog Inputs: ........................................................................................................................................ 45

7929 SW Burns Way Phone: 503 344-5085
Suite F
1/14/2021 RMS PM Hardware User Manual 3 of 54
4.2 Digital Inputs:.......................................................................................................................................... 48
4.3 Digital Outputs........................................................................................................................................ 51
REVISION HISTORY ......................................................................................................... 53
1. Safety First:
ATTENTION
When you see this sign, PAY ATTENTION! This indicates that something
important is about to be said, that concerns your safety and the proper
operation of the equipment.
DANGER
When you see this sign, you are being alerted to an IMMEDIATE DANGER
that could cause severe injury or even death. You MUST review these
sections carefully an do everything possible to comply with installation and
operation requirements, or you risk injury or death to yourself or anyone
else who uses the equipment or the vehicle. Failure to comply with safety
requirements will void all warranties and could expose you as the installer
to liability in the event of an injury. Use the equipment in the manner in
which it was intended.
CAUTION
When you see this sign, you are being advised that the issue under
discussion has a serious safety or equipment reliability implication. Use
caution and be conservative. Use equipment in the manner described in
this User’s Manual.
Safety is entirely the responsibility of the installer of this equipment. Cascadia Motion has
done everything it can to ensure that the traction controller itself conforms to international
standards for safety. This does NOT mean that your installation will be safe, or that it
will not interfere with other systems on board your vehicle. It is your responsibility as the
installer to review this entire User’s Manual, to understand the implications of each and
every section, and to know what might be unique about your system application that
presents a unique hazard or potential safety issue – and to solve it.
Cascadia Motion is committed to helping you solve these problems, but cannot take
responsibility for the application of this traction controller. We can only promise to meet

7929 SW Burns Way Phone: 503 344-5085
Suite F
1/14/2021 RMS PM Hardware User Manual 4 of 54
the specifications for this product and that it meets international safety standards when
used in accordance with the instructions in this Manual.
2. Functional Overview:
The PM controller family is intended as a traction controller for EV and HEV drive
systems, and includes both the motor control function and a rudimentary vehicle
controller strategy in the same box. The motor control is a torque commanded, vector
control technology has been used on AC Induction and PM Synchronous motors in
many applications.
The RM100 controller family is intended for the same type of EV/HEV applications
however it has a much more limited set of inputs and outputs. The limited set of I/O
prevents it from being properly used in the VSM mode where analog and digital inputs
are used to control the operation of the inverter. The RM100 controller is intended for
applications where CAN communications is used to control the controller.
The motor control subsystem firmware is mated to a vehicle controller firmware
implemented in the DSP controller. This vehicle controller subsystem handles the
driver interface (accel and decel / brake pedal inputs, Fwd/Rev controls, etc) and the
vehicle interface (power sequencing, built in test, fault handling and safety issues). It is
essentially a state machine in front of the motor controller firmware with a defined
interface between the two software processes.
By default, out of the box the parameters are set up in Torque Control Mode, with
default motor parameters loaded. The parameters must be changed to match the load
motor and operating characteristics before running for the first time. These parameters
personalize the drive to the motor and the vehicle.
User Controls Vehicle Control
Firmware
Motor Control
Firmware
Motor

7929 SW Burns Way Phone: 503 344-5085
Suite F
1/14/2021 RMS PM Hardware User Manual 5 of 54
3. Installing the PM Drive:
The PM controller has 4 mounting locations, one at each corner. Mounting orientation
is not critical. The controller should be mounted in a location that is not exposed to
direct spray from water. Each mounting hole is sized to handle up to a M10 socket
head cap screw.
See PM250 Datasheet for more information on mounting the PM250.
PM100 Dimensions – top and side views

7929 SW Burns Way Phone: 503 344-5085
Suite F
1/14/2021 RMS PM Hardware User Manual 7 of 54
3.1 Liquid Cooling Connections:
The controller must be cooled by passing liquid through it. The controller includes two ports
to be used for liquid cooling. The fluid direction for the PM250 inverter is marked into the
case of the inverter. The PM100 and PM150 has a more symmetrical design and is less
sensitive to fluid direction. However, it is preferred that the rearmost plenum (the ports
furthest from the 3 AC output terminals) be the fluid inlet, as this keeps the coolest fluid near
the DC Link capacitor assembly. The PM250 has markings on the housing that indicate the
required direction of the coolant through the inverter. See table below for coolant
specifications:
Coolant Type
50/50 mix ethylene glycol (antifreeze) / water or propylene
glycol / water; with Aluminum corrosion inhibitor additive
Coolant Temperature
-30°C to +80°C full power
Operation -40.. -30; +80.. +100°C with de-rated output
Coolant Flow Rate
8 – 12 LPM (2 – 3 GPM), PM100/PM150/RM100/CM200
20 – 30 LPM (5 – 6 GPM), PM250, RM300
Pressure Drop
PM100, 0.3 bar (4.4 psi) @ 8 LPM @ 25°C
PM150, 0.4 bar (5.8 psi) @ 8 LPM @ 25°C
PM250, 0.9 bar (13 psi) @ 20 LPM @ 25°C
RM100, 0.06 bar (0.8 psi) @ 8 LPM @ 25°C
RM300, TBD
CM200, 0.2 bar (2.9 psi) @ 8 LPM @ 25°C
Port Size
PM100 and PM150, AN-6
PM250, SAE ORB -10
RM100, Custom O-ring port, the following options are provided
to be installed in the unit, each kit includes materials for both
ports.
- ARaymond NT100 / 16mm Straight, CM p/n G1-0023-01
- ARaymond NT100 / 16mm 45deg, CM p/n G1-0024-01
- ARaymond NT100 / 16mm 90deg, CM p/n G1-0025-01
- 16mm / 5/8” Hose Barb, CM p/n G1-0026-01

7929 SW Burns Way Phone: 503 344-5085
Suite F
1/14/2021 RMS PM Hardware User Manual 8 of 54
RM300, Custom O-ring port. The RM300 comes standard
with an adapter that has a 25.4mm / 1 inch hose barb. The
cooling port adapters are included in kit p/n G1-0031-01.
CM200, SAE ORB -06
RM100 Coolant Port Options (Does not apply to PM100/PM150/PM250/RM300/CM200)
ARaymond NT100 / J20 Straight, CM Kit G1-0023-01
ARaymond NT100 / J29 90 degree, CM kit G1-0025-01
ARaymond NT100 / J30 45 degree, CM kit G1-0024-01

7929 SW Burns Way Phone: 503 344-5085
Suite F
1/14/2021 RMS PM Hardware User Manual 9 of 54
For proper operation of the inverter the coolant must flow at a rate equal to or above the
minimum specified flow rate at all times that the motor is enabled. The flow rate should not
be reduced when the inverter is “not being run hard”. The design of the heat exchanger
does not allow for reduced or no coolant flow. It is possible to adjust the fan speed on the
coolant radiator as needed depending on the operating conditions of the inverter.
Since the maximum coolant temperature is less than the boiling point of water the cooling
system does not need to be operated under pressure. Other devices (e.g. motor, charger,
DC/DC converter) that are added in series with the inverter increase the total pressure drop
of the system. Even simple fittings and hose length will contribute to the total system
pressure drop. The total system pressure may add up to a level that is beyond the
capability of the chosen pump. The best practice is to measure the actual coolant flow
after the system has been assembled.
Certain pump types are not capable of driving any significant pressure. A pump may have
a high flow rate, but it may not be able to drive any substantial pressure. The PM250 unit
has an especially high pressure drop. An example pump suitable for the PM250 is the
EMP WP 29. Pump suitable for the PM100/PM150/RM100/CM200 is the Bosch PCE-XL
(see Cascadia Motion website).
As noted above proper coolant flow is essential to the operation of the inverter. If the flow
rate is not sufficient the power module internal to the inverter can be damaged even though
the indicated power module temperatures are below an over-temperature threshold. The
power module temperature sensors are located in such a way that they are much closer to
the temperature of the coolant than they are to the temperature of the transistors
and diodes used inside the power module.
Loss of coolant for even a few seconds can result in failure of the power module.
Cascadia Motion recommends that the user install a device to ensure that the coolant pump
is operating properly at all times when the inverter is enabled. The inverter should be
immediately stopped if the coolant is not flowing.
There are many ways that coolant flow could be measured. A flow sensor could be added
to the cooling loop. Often these types of sensors produce a pulse output. To read the
pulse output would require the use of a device to interpret this signal (Cascadia Motion does
not supply this).

7929 SW Burns Way Phone: 503 344-5085
Suite F
1/14/2021 RMS PM Hardware User Manual 10 of 54
Another option is to monitor the pressure in the cooling system. Typically the inverter would
be placed near the end of the cooling loop, just before the radiator. So a typical cooling
loop might look like pump outlet, inverter, radiator/reservoir, pump inlet. Typically the
reservoir is at ambient error pressure. So the inverter should be at a pressure that is higher
than ambient. If a pressure switch is placed at the input coolant port of the inverter it
should be able to detect that coolant is flowing.
Various types of coolant pressure switches exist. If a type is used that closes the switch
when the pressure is above a certain level is used then this could be inserted in series with
the ground connection of the forward/reverse switches (for VSM mode applications) or just
connected directly to one of the inputs for monitoring via CAN.
A pressure switch that closes when the pressure is above about 6 psi (~0.4 bar) should be
suitable for the PM100 and PM150. For the PM250 the required pressure is higher and
should be about 10 psi (~ 0.7 bar).
3.2 PM100/PM150 External Signal Connectors:
Two sealed automotive connectors are provided to connect to the internal I/O resources. J1
and J2 are standard AMPSEAL connectors by AMP/Tyco:
3.2.1 J1 – 35p AMPSEAL Plug 776164-1 with crimp contact 770854-1
GEN2 refers to PM100 Units w/ serial number less than 344
GEN3 refers to PM100 Units w/ serial number of 344 or greater and all PM150 units
Pin #
Pin Name
Description
Notes
1
XDCR_PWR
+5V @ 80mA max
Accel Pedal Power
13
AIN1
Analog Input 1 0-5VFS
Accel Pedal wiper
24
AIN2
Analog Input 2 0-5VFS
Motor Temperature Sensor
2
AGND
Analog Ground
Accel Pedal GND
14
XDCR_PWR
+5V @ 80mA max
Spare 5V transducer power
25
AIN3
Analog Input 3 0-5VFS
Brake Pedal
3
AIN4
Analog Input 4 0-5VFS
15
AGND
Analog Ground
26
XDCR_PWR
+5V @ 80mA max
Spare 5V transducer power
4
RTD1
1000 Ohm RTD Input

7929 SW Burns Way Phone: 503 344-5085
Suite F
1/14/2021 RMS PM Hardware User Manual 11 of 54
GEN2
4
GEN3
AOUT
Analog Output 0 – 5V
16
GEN2
RTD2
1000 Ohm RTD Input
16
GEN3
AIN6
Analog Input 6 0-5VFS
Available for user-defined
functionality
27
GEN2
RTD3
1000 Ohm RTD Input
27
GEN3
RLY6
Hi-Side Relay Driver
Available for user-defined
functionality, CAN control.
5
GEN2
RTD4
100 Ohm RTD Input
5
GEN3
RTD1
RTD Input (PT100 or
PT1000)
Software selectable input type.
17
AGND
Analog Ground
28
XDCR_PWR
+5V @ 80mA max
Spare 5V transducer power
6
GEN2
RTD5
100 Ohm RTD Input
6
GEN3
RTD2
RTD Input (PT100 or
PT1000)
Software selectable input type.
18
GEN2
<reserved>
DO NOT CONNECT
18
GEN3
AIN5
Analog Input 5 0-5VFS
Available for user-defined
functionality
29
GEN2
<reserved>
DO NOT CONNECT
29
GEN3
RLY5
Hi-Side Relay Driver
Available for user-defined
functionality, CAN control.
7
/PROG_ENA
Serial Boot Loader enable
19
AGND
Analog Ground
30
DIN1
Digital Input 1 – STG(1)
Forward Enable Switch
8
DIN2
Digital Input 2 - STG
Reverse Enable Switch

7929 SW Burns Way Phone: 503 344-5085
Suite F
1/14/2021 RMS PM Hardware User Manual 12 of 54
20
DIN3
Digital Input 3 - STG
Brake Switch
31
DIN4
Digital Input 4 - STG
REGEN Disable Input (if used)
9
DIN5
Digital Input 5 – STB(2)
Ignition Input (if used)
21
DIN6
Digital Input 6 - STB
Start Input (if used)
32
GEN2
<reserved>
DO NOT CONNECT
32
GEN3
DIN7
Digital Input 7 - STB
Available for user-defined
function.
10
GEN2
<reserved>
DO NOT CONNECT
10
GEN3
DIN8
Digital Input 8 - STB
Available for user-defined
function.
22
GND
Ground
33
CANA_H
CAN Channel A Hi
11
CANA_L
CAN Channel A Low
23
CANB_H
CAN Channel B Hi
34
CANB_L
CAN Channel B Low
12
TXD
RS-232 Transmit
35
RXD
RS-232 Receive
(1)– Switch to GND; (2) – Switch to Battery
3.2.2 J2 – 23p AMPSEAL Plug 770680-1 with crimp contact 770854-1
Pin#
Pin Name
Description
Notes
1
XDCR_PWR
+5V @ 80mA max
Encoder Power
9
ENCA
Encoder Channel A input
Used with Induction Motors
16
ENCB
Encoder Channel B input
2
ENCZ
Encoder Channel Z input
(Index)
10
GND
GND
Encoder GND
17
EXC
Resolver excitation output
Used with PM Motors
3
GND
Resolver excitation return

7929 SW Burns Way Phone: 503 344-5085
Suite F
1/14/2021 RMS PM Hardware User Manual 13 of 54
11
SIN
Resolver Sine winding +
18
/SIN
Resolver Sine winding -
4
COS
Resolver Cosine winding +
12
/COS
Resolver Cosine winding -
19
GND
Resolver Shield GND
5
<reserved>
DO NOT CONNECT
13
<reserved>
DO NOT CONNECT
20
<reserved>
DO NOT CONNECT
6
GND
Main 12V return
Chassis GND
14
GND
Main 12V return
Chassis GND
21
RLY1
Hi-Side Relay Driver
Pre-Charge Contactor Drive
7
RLY2
Hi-Side Relay Driver
Main Relay Drive
15
RLY3
Lo-Side Relay Driver
OK Indicator Drive / 12V Power
Relay Drive
22
RLY4
Lo-Side Relay Driver
Fault Indicator Drive
8
BATT+
Main 12V power source
12V Ignition Power Input
23
BATT+
Main 12V power source
12V Ignition Power Input
3.3 PM250 External Connections:
The PM250 has two external connectors. J2 is a 41 pin circular connector, J1 is a 26 pin
circular connector. J2 contains mostly signals that would go to the vehicle harness. J1
contains mostly signals that would go to the motor. A connector kit that contains both J1
and J2 can be purchased from Cascadia Motion as G1-0016-01.
J1 Connections
Pin#
Pin Name
Description
Notes
A
EXC
Resolver excitation output
Used with PM Motors
B
GND
Resolver excitation return
C
SIN
Resolver Sine winding +
D
/SIN
Resolver Sine winding -
E
COS
Resolver Cosine winding +
F
/COS
Resolver Cosine winding -
G
RTD1P
RTD1 Positive
Can be either PT100 or PT1000

7929 SW Burns Way Phone: 503 344-5085
Suite F
1/14/2021 RMS PM Hardware User Manual 14 of 54
H
RTD1N
RTD1 Negative
J
GND
GND
Encoder GND
K
HALL C
Hall Input C
L
HALL A
Hall Input A
For use with certain motors that
support Hall encoders.
M
ENCZ
Encoder Channel Z input
(Index)
N
ENC A
Encoder Channel A input
Quadrature encoder used with
Induction Motors
P
XDCR_PWR
+5V @ 80mA max
Encoder Power
R
RTD2P
RTD2 Positive
Can be either PT100 or PT1000
S
RTD2N
RTD2 Negative
T
GND
Resolver Shield GND
U
AIN2
Analog Input 2
Used with certain motors for
temperature sensing.
V
AIN4
Analog Input 4
Used with certain motors for
temperature sensing.
W
AGND
Analog Ground
Ground reference for use with
AIN2 and AIN4
X
XDCR_PWR
+5V @ 80mA max
For use with pull-up resistor.
Y
HALL B
Hall Input B
Z
GND
AA or a
ENCB
Encoder Channel B input
AB or b
AIN2PU
Pull-up resistor on AIN2
If connected to XDCR_PWR will
enable a 1K ohm pull-up resistor
to be connected to AIN2.
AC or c
AIN4PU
Pull-up resistor on AIN4
If connected to XDCR_PWR will
enable a 1K ohm pull-up resistor
to be connected to AIN4.
J2 Connections
Pin #
Pin Name
Description
Notes

7929 SW Burns Way Phone: 503 344-5085
Suite F
1/14/2021 RMS PM Hardware User Manual 15 of 54
A
CANB_H
CAN Channel B Hi
B
CANB_L
CAN Channel B Low
C
RLY2
Hi-Side Relay Driver
Main Relay Drive
D
RLY3
Lo-Side Relay Driver
OK Indicator Drive / 12V Power
Relay Drive
E
RLY5
Hi-Side Relay Driver
Available for user-defined
functionality, CAN control.
F
DIN1
Digital Input 1 – STG(1)
Forward Enable Switch
G
DIN2
Digital Input 2 - STG
Reverse Enable Switch
H
DIN5
Digital Input 5 – STB(2)
Ignition Input (if used)
J
DIN7
Digital Input 7 - STB
Available for user-defined
function.
K
GND
Main 12V return
L
GND
Main 12V return
M
BATT+
Main 12V power source
12V Ignition Power Input
N
BATT+
Main 12V power source
12V Ignition Power Input
P
AIN1
Analog Input 1 0-5VFS
Accel Pedal wiper
R
AGND
Analog Ground
Accel Pedal GND
S
AIN3
Analog Input 3 0-5VFS
Brake Pedal
T
AIN5
Analog Input 5 0-5VFS
Available for user-defined
functionality
U
AIN6
Analog Input 6 0-5VFS
Available for user-defined
functionality
V
AGND
Analog Ground
W
CANA_H
CAN Channel A Hi
X
GND
Ground
CAN B Shield
Y
RLY1
Hi-Side Relay Driver
Pre-Charge Contactor Drive
Z
RLY4
Lo-Side Relay Driver
Fault Indicator Drive
AA or a
RLY6
Hi-Side Relay Driver
Available for user-defined
functionality, CAN control.
AB or b
DIN3
Digital Input 3 - STG
Brake Switch
AC or c
DIN6
Digital Input 6 - STB
Start Input (if used)
AD or d
GND
Main 12V return

7929 SW Burns Way Phone: 503 344-5085
Suite F
1/14/2021 RMS PM Hardware User Manual 16 of 54
AE or e
BATT+
Main 12V power source
12V Ignition Power Input
AF or f
XDCR_PWR
+5V @ 80mA max
Accel Pedal Power
AG or g
AGND
Analog Ground
AH or h
XDCR_PWR
+5V @ 80mA max
Spare 5V transducer power
AI or i
XDCR_PWR
+5V @ 80mA max
Spare 5V transducer power
AJ or j
CANA_L
CAN Channel A Low
AK or k
GND
Ground
CAN A Shield
AM or m
RXD
RS-232 Receive
AN or n
DIN4
Digital Input 4 - STG
REGEN Disable Input (if used)
AP or p
DIN8
Digital Input 8 - STB
Available for user-defined
function.
AQ or q
/PROG_ENA
Serial Boot Loader enable
AR or r
TXD
RS-232 Transmit
AS or s
AOUT
Analog Output 0 – 5V
AT or t
GND
Ground
Serial I/O GND
3.4 RM100 Signal Connections
The RM100 uses a single 35 pin Ampseal connector for the I/O Signals. Mating connector
is Tyco part number 776164-1, mating contact is 770854-3 for 16-20 AWG wire. Must use
Tyco crimper 58529-1 (AMP Pro-Crimper II). A kit of the connector and contacts is
available from Cascadia Motion as part number G1-0021-01.
Pin #
Pin Name
Description
Notes
1
RLY1
(Pre-charge)
High Side Driver
If pre-charge function is used this
output serves as the pre-charge
contactor output.
2
AIN1
Analog Input 1 0-5VFS
Accel Pedal wiper
3
AIN2
Analog Input 2 0-5VFS
Motor Temperature Sensor
4
/PROG_ENA
Serial Boot Loader enable
This pin is grounded when power
is applied to enable
reprogramming of the firmware.
5
CANA_H
CAN Channel A Hi
CAN Communications channel
6
CANA_L
CAN Channel A Low

7929 SW Burns Way Phone: 503 344-5085
Suite F
1/14/2021 RMS PM Hardware User Manual 17 of 54
7
CANB_H
CAN Channel B Hi
Secondary CAN Communications
channel, currently not used.
8
CANB_L
CAN Channel B Low
9
CAN Shield
Connection of CAN cable shield.
10
TXD
RS-232 Transmit
Used for RMS GUI and C2prog
11
RXD
RS-232 Receive
Used for RMS GUI and C2prog
12
GND
RS-232 Ground
13
RLY2 (Main)
High Side Driver
If the pre-charge function is used
this output serves as the main
contactor output.
14
AIN3
Analog Input 3 0-5VFS
Brake Pedal
15
DIN1
Digital Input 1 – STG
Forward Enable Switch
16
DIN2
Digital Input 2 - STG
Reverse Enable Switch
17
/EXC
Resolver excitation return
18
COS
Resolver COS winding
19
SIN
Resolver SIN winding
20
RTD1-
Return side of RTD1
21
RTD2+
Positive side of RTD2
Temperature Sensor software
configurable for PT100 or
PT1000.
22
RTD2-
Return side of RTD2
23
XDCR_PWR
+5V
Transducer power output
24
BATT+
12V/24V Input
Input power for inverter. Must be
on a switched connection as this
input will always draw current.
25
BATT+
12V/24V Input
Redundant connection can be
used if desired of needed for
additional current capability.
26
BATT_RTN
12/24V Return
Normally tied to vehicle power
system chassis.
27
BATT_RTN
12/24V Return
Redundant connection can be
used if desired of needed for
additional current capability.

7929 SW Burns Way Phone: 503 344-5085
Suite F
1/14/2021 RMS PM Hardware User Manual 18 of 54
28
EXC
Resolver excitation
29
SHIELD
Resolver Cable Shield
connection
Resolver cable shield should
connected to this pin. Do not
connect the shield to the case of
the motor.
30
/COS
Resolver COS winding
return
31
/SIN
Resolver SIN winding return
32
RTD1+
Positive side of RTD1
Temperature Sensor software
configurable for PT100 or
PT1000.
33
HVIL IN
High Voltage Interlock Input
HVIL IN to HVIL OOUT is a circuit
loop that will read shorted when
all HV connectors are plugged in.
34
HVIL OUT
High Voltage Interlock
Output
35
AGND
Analog Ground
Ground reference from analog
inputs.
3.5 RM300 Signal Connections
The RM300 uses two connectors for the low voltage I/O signals. The 35 pin connector
(marked I/O on the housing) is for the signals related to the communications/control of the
inverter. The 14 pin connector (marked M on the housing) is for the motor related signals.
The 35 pin mating connector is Tyco part number 776164-1, the 14 pin mating connector is
776273-1, mating contact is 770854-3 for 16-20 AWG wire. Must use Tyco crimper
58529-1 (AMP Pro-Crimper II). A kit of the connector and contacts is available from
Cascadia Motion as part number G1-0030-01.
“I/O” Connector – Input / Output Connector
Pin #
Pin Name
Description
Notes
1
BATT+
12V/24V Input
Input power for inverter. Must be
on a switched connection as this
input will always draw current.

7929 SW Burns Way Phone: 503 344-5085
Suite F
1/14/2021 RMS PM Hardware User Manual 19 of 54
2
BATT+
12V/24V Input
Redundant connection can be
used if desired of needed for
additional current capability.
3
BATT_RTN
12/24V Return
Normally tied to vehicle power
system chassis.
4
BATT_RTN
12/24V Return
Redundant connection can be
used if desired of needed for
additional current capability.
5
AIN4
Analog Input 4 0-5VFS
6
GND
Digital Ground
Digital Ground, can be used for
digital inputs (STG types)
7
CANA_H
CAN Channel A Hi
CAN Communications channel
8
CANA_L
CAN Channel A Low
9
CANB_H
CAN Channel B Hi
Secondary CAN Communications
channel, currently not used.
10
CANB_L
CAN Channel B Low
11
CAN Shield
Connection of CAN cable shield.
12
DIN2
Digital Input 2 - STG
Reverse Enable Switch
13
RLY2 (Main)
High Side Driver
If the pre-charge function is used
this output serves as the main
contactor output.
14
/PROG_ENA
Serial Boot Loader enable
This pin is grounded when power
is applied to enable
reprogramming of the firmware.
15
XDCR_PWR
+5V
Transducer power output
16
AIN1
Analog Input 1 0-5VFS
Accel Pedal wiper
17
AIN3
Analog Input 3 0-5VFS
Brake Pedal
18
AIN6
Analog Input 6 0-5VFS
19
AGND
Analog Ground
Ground reference from analog
inputs. Do not connect to GND,
BATT_RTN, or chassis
20
GND
RS-232 Ground
21
RXD
RS-232 Receive
Used for RMS GUI and C2prog

7929 SW Burns Way Phone: 503 344-5085
Suite F
1/14/2021 RMS PM Hardware User Manual 20 of 54
22
TXD
RS-232 Transmit
Used for RMS GUI and C2prog
23
DIN1
Digital Input 1 – STG
Forward Enable Switch
24
RLY1
(Pre-charge)
High Side Driver
If pre-charge function is used this
output serves as the pre-charge
contactor output.
25
HVIL IN
High Voltage Interlock Input
HVIL IN to HVIL OOUT is a circuit
loop that will read shorted when
all HV connectors are plugged in.
26
HVIL OUT
High Voltage Interlock
Output
27
DIN3
Digital Input 3 – STG
Brake Switch
28
DIN4
Digital Input 4 – STG
29
DIN5
Digital Input 5 – STG
Can be used as Ignition Input, but
note the RM300 is a Switch To
Ground input which is different
than the PM family.
30
DIN6
Digital Input 6 – STG
Can be used as Start Input, but
note the RM300 is a Switch To
Ground input which is different
than the PM family.
31
DIN7
Digital Input 7 – STB
Switch To Battery input.
32
DIN8
Digital Input 8 – STB
Switch To Battery input.
33
XDCR_PWR
+5V
Transducer power output
34
GND
Digital Ground
Digital Ground, can be used for
digital inputs (STG types)
35
AGND
Analog Ground
Ground reference from analog
inputs. Do not connect to GND,
BATT_RTN, or chassis
“M” Connector – Motor connections connector
Pin #
Pin Name
Description
Notes
1
/EXC
Resolver excitation return
2
/SIN
Resolver SIN winding return
This manual suits for next models
6
Table of contents
Popular Controllers manuals by other brands
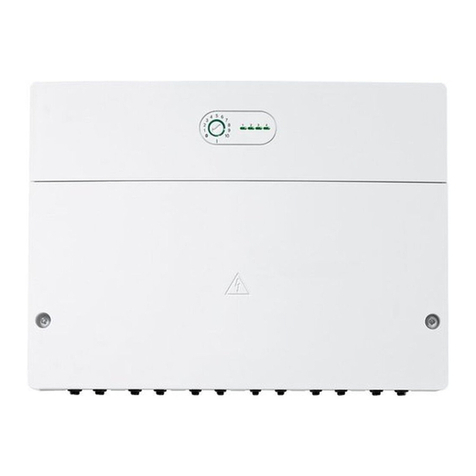
Bosch
Bosch ME 200 Installation instructions for contractors
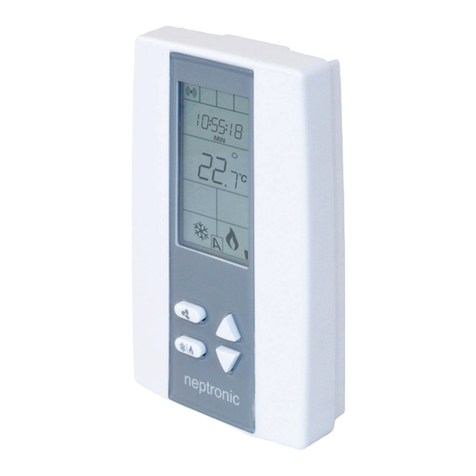
Neptronic
Neptronic TRO24T4XYZ1 Specification and installation instructions
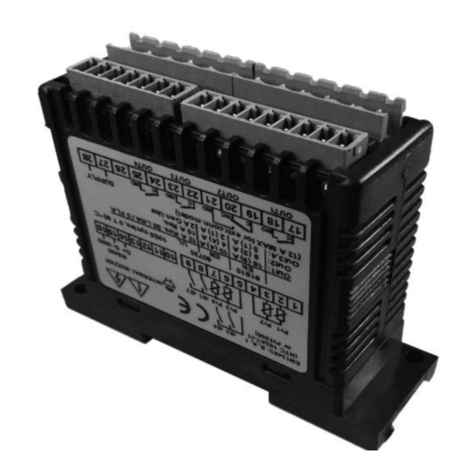
Ascon tecnologic
Ascon tecnologic X30 operating instructions
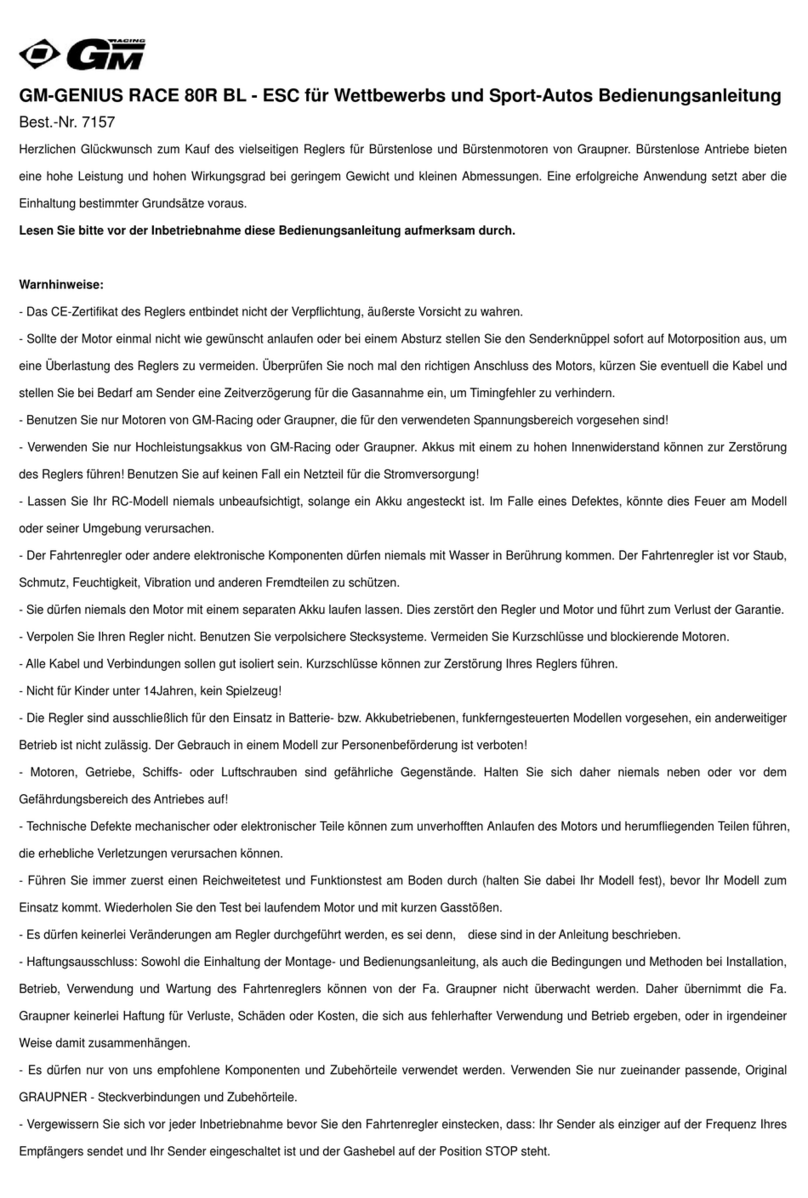
GM-Racing
GM-Racing GENIUS RACE 80R instruction manual

Döring
Döring WTR-U quick start guide
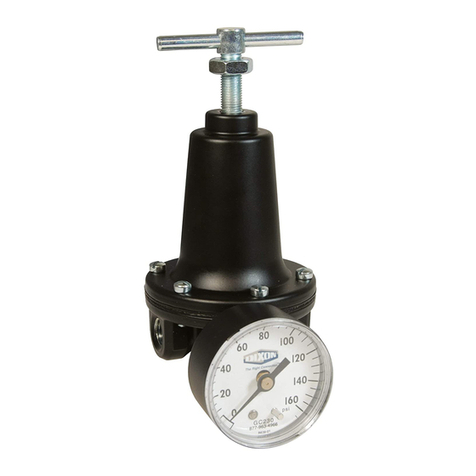
Dixon
Dixon R119 Series Installation & service instructions