Cera System CeraValve KST Series Troubleshooting guide

Tel +49 (0) 3 66 01 9 19-0
Fax +49 (0) 3 66 01 9 19-77
Dok.-No.
BA-KST 10-02.2
CERAVALVE
Ball Valve – KST
Page 1 of 6
Operations and Maintenance Instruction
1 Transport
Upon receipt, please check the valve with eventual equipment (Actuator, etc.) for any
damage which may have occurred during shipment.
When shipping the valve, it should be made sure that it is secured on a pallet
avoiding it to slide or fall over during transport. If transporting or lifting the valve with
a rope or hook, it should be attached in a way avoiding that the valve accidentally
slips sidewards.
Do not use any lifting tackle (rope, chain, sling..) through the open valve.
2 Safety indication
If operating temperatures are > 50 °C, protection against accidental contact and
spray -risk has to be applied.
Connecting the electrical- or electro pneumatic- connections has to be carried out by
authorized professional staff only.
When operating (on - off cycling) the valve while not flanged in line, do never attempt
to touch the inside of the ball (bore).
In case of toxic, corrosive and explosive fluids, respective guidelines need to be
followed. When disassembling the valve, make sure that possible contaminated
residues are disposed off as hazardous waste.
3 Installation
Pipeline
Install the valve into the line so that the arrow on the valve body points into the flow
direction. Should the actuator be too heavy, separate bear up support may be
required.
Install the valve without strain and tension. Additional forces by the pipeline are not
allowed (see DIN 2502).
The ball valve should be flanged in by using standard gaskets.
Make sure that the gaskets are not damaging the ceramic inlet and outlet
liners of the valve.

Tel +49 (0) 3 66 01 9 19-0
Fax +49 (0) 3 66 01 9 19-77
Dok.-No.
BA-KST 10-02.2
CERAVALVE
Ball Valve – KST
Page 2 of 6
Bolting torque
M 6
M 8
M10
⇒
⇒
⇒
6 Nm
13 Nm
26 Nm
M 12
M 16
M 20
⇒
⇒
⇒
47 Nm
118 Nm
240 Nm
M 24
M 27
M 30
⇒
⇒
⇒
410 Nm
605 Nm
830 Nm
Actuator
When mounting an actuator, the factory recommended mounting kit (yoke and
adapter) should be used. Once the actuator has been mounted, it should be made
sure that there is enough overlapping (between ball and seats) in the closed position
and that in the open position no offset is seen (full flow at 100% open). This can be
fine tuned with the mechanical end bolts on the actuator.
Please make sure that these torque limits are not exceeded.
Valve Size Max. acceptable torque
M max in Nm
DN 15 40
DN 25 100
DN 40 160
DN 65 180
DN 80 190
DN 100 230
DN 150 500
Torque values
DN 200 -
For electric actuators: Do not change the setting of the limit switches.
For pneumatic actuators: Respect indicated air supply pressure and do not add
springs without prior checking with the valve manufacturer.
4 Start-up
Before start-up, test the ball valve operation (open / close). In case of higher
operating temperatures, the valve should be tested again at operating temperature
conditions.
In case of sudden thermal shocks be advised that different ceramic
materials tolerate sudden temperature changes differently.
Please respect the following limits of ∆T: Al
2
O
3
app. 120 K
ZrO
2
app. 250 K
SiSiC app. 350 K
SiC app. 350 K
Si
3
N
4
app. 450 K

Tel +49 (0) 3 66 01 9 19-0
Fax +49 (0) 3 66 01 9 19-77
Dok.-No.
BA-KST 10-02.2
CERAVALVE
Ball Valve – KST
Page 3 of 6
More information on the ceramic material used in a particular job number can be
found in the technical specification of the job number
The valve is only to be used in specifically determined pressure-, temperature- and
fluid conditions.
Immediately after shut down, the valve should be flushed in a partly open
position.
Depending on the process fluid and conditions, such a flushing process should be
done regularly.
The operation of the ball valve and the validity of the warranty depends on the
process conditions the valve is exposed to. Never alter the process conditions as this
may void warranty and jeopardize safety.
(comp. also TAG plate and / or indication on valve body).
5 Maintenance
Following 1 - 2 years of operation a revision is recommended.
Disassembly and assembly must be done when valve is not pressurised.
Damage to the valve following imprudent maintenance practices could
void warranty ! Electrical- and electro-pneumatic - actuators have to be
disconnected.
Only original spare and wear parts should be used (see your specific parts list).
Prior to maintenance the valve should be flushed thoroughly in order to remove
foreign objects and residue particles.
During maintenance the sealing set and the wear parts of the valves should be
inspected carefully and eventually be replaced. Sealing and packing set should in
general be replaced after one year in operation.
In case of malfunction of the valve the following points listed under 5.1 should be
checked. Revision and maintenance works should only be performed by qualified
personnel.

Tel +49 (0) 3 66 01 9 19-0
Fax +49 (0) 3 66 01 9 19-77
Dok.-No.
BA-KST 10-02.2
CERAVALVE
Ball Valve – KST
Page 4 of 6
5.1 Testing points in case of malfunction
Malfunction
Possible cause
Remedy
Actuator supply air too low
Check air supply, increase it to max
while respecting the max. allowable
torque of the ceramic ball valve.
Spring force too low
Check with supplier, event. add
spring(s)
Electric actuator not
performing
Check limit switches and power
supply
Foreign objects (larger
particles) inside the valve.
Take the valve out of line,
disassemble and clean it.
Valve does not
move
(nor close
nor open)
Fluid crystallized between
stem and valve body
jamming stem movement.
Remove actuator, unbolt bonnet
flange, pull out stem, clean stem
and body, replace gaskets if
necessary.
Same causes as mentioned
here above
Same remedies as mentioned
above
Valve moves in
a jerky motion
(not smoothly)
Positioner not working
properly
Check with supplier
Increased seat
leakage
Solid particles lodged
between ball and seats
Operate (stroke) the valve up to
three times, if leakage persists,
change wear parts (seats and ball)
Defective O-rings
Check and replace gaskets (O-
rings) as needed.
Leakage to the
outside
Flange bolts untight
Check bolting, tighten it as needed.

Tel +49 (0) 3 66 01 9 19-0
Fax +49 (0) 3 66 01 9 19-77
Dok.-No.
BA-KST 10-02.2
CERAVALVE
Ball Valve – KST
Page 5 of 6
5.2 Disassembly
1.
Remove actuator
2.
Turn ball in closed position, loosen Allen screws, remove bonnet flange and
pull stem out
3.
Put valve on its downstream flange, loosen hexagon nut and loosen upstream
flange from body
4.
Remove upstream seat from the socket
5.
If the wear sleeves are eroded or damaged, remove them with the help of a
wooden tool (eg. hammer)
6.
Remove ball and socket carefully from the valve body
7.
Lift body up from downstream flange
8.
Remove seat from downstream flange
9.
Remove all o-rings from the body parts as well as the support ring and the
bearing bush from the bonnet flange
10.
Clean all valve parts
5.3 Assembly
1.
Check all ceramic components for wear, replace those necessary
2.
Sealing and packing should always be replaced after disassembly
3.
Glue (eg. Silicon or ceramic glue) the ceramic wear sleeves into the flanges.
Make sure that the ceramic sleeves are aligned to the flange end toward the
seat side and that they are 0.3 – 0.5 mm lower than the flange face (pipe side)
4.
Insert o-ring and the downstream seat into the downstream flange

Tel +49 (0) 3 66 01 9 19-0
Fax +49 (0) 3 66 01 9 19-77
Dok.-No.
BA-KST 10-02.2
CERAVALVE
Ball Valve – KST
Page 6 of 6
5.
Put the socket on the seat in a way that the socket bore (stem passage) is
aligned to the flat surface of the flange
6.
Insert o-ring into the downstream flange and put the body on it. Align body and
socket over the side bores of the flange
7.
Put ball through the socket onto the seat and turn the ball so that its stem-slot
is aligned with the sideward boreholes
8.
Push stem with mounted o-rings through body and socket into the balls stem-
slot
9.
Put upstream seat on socket
10.
Put the double end studs through the bore holes of the downstream flange
11.
Insert o-rings into the upstream flange and place it on the body over the spring-
loaded seat. Align flat surfaces of body and flange
12.
Tie body parts with the double end studs, hexagon nuts and washers together
lightly
13.
Push support ring over the stem, place bearing bush and o-rings into the
bonnet flange then place bonnet over the stem on the flat surface of the
flanges. Make sure that the flat surfaces are properly aligned
14.
Tighten bonnet flange
with
Allen screws
and tighten body parts with double
end studs (see table for torque values)
15.
Tighten Allen screws on the bonnet flange thoroughly
16.
Manual operation trial (open & close the valve)
17.
Mount, calibrate and connect actuator according to manufacturer guidelines.
Respect flow direction when calibrating the actuator
18.
Follow the safety features ( protective grid, safety cover, earth connection)
Popular Control Unit manuals by other brands
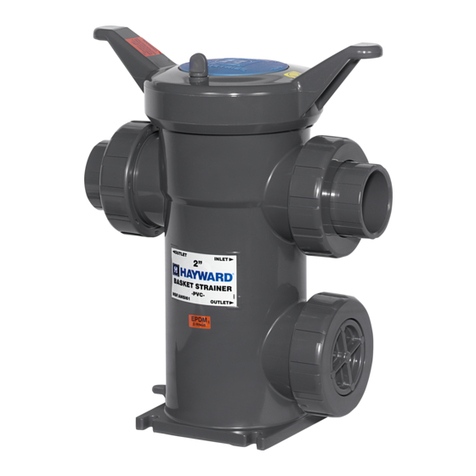
Hayward
Hayward PVC Series Installation, operation and maintenance instructions
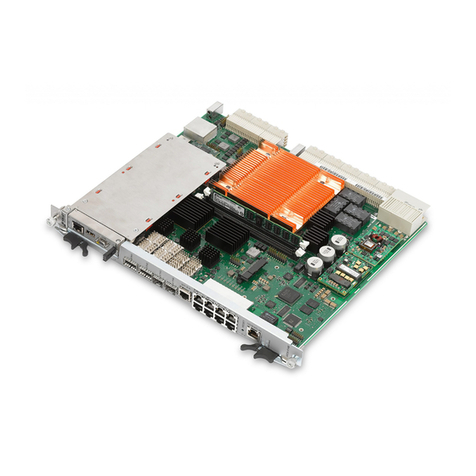
SMART Embedded Computing
SMART Embedded Computing RTM-ATCA-F140 Series Installation & use
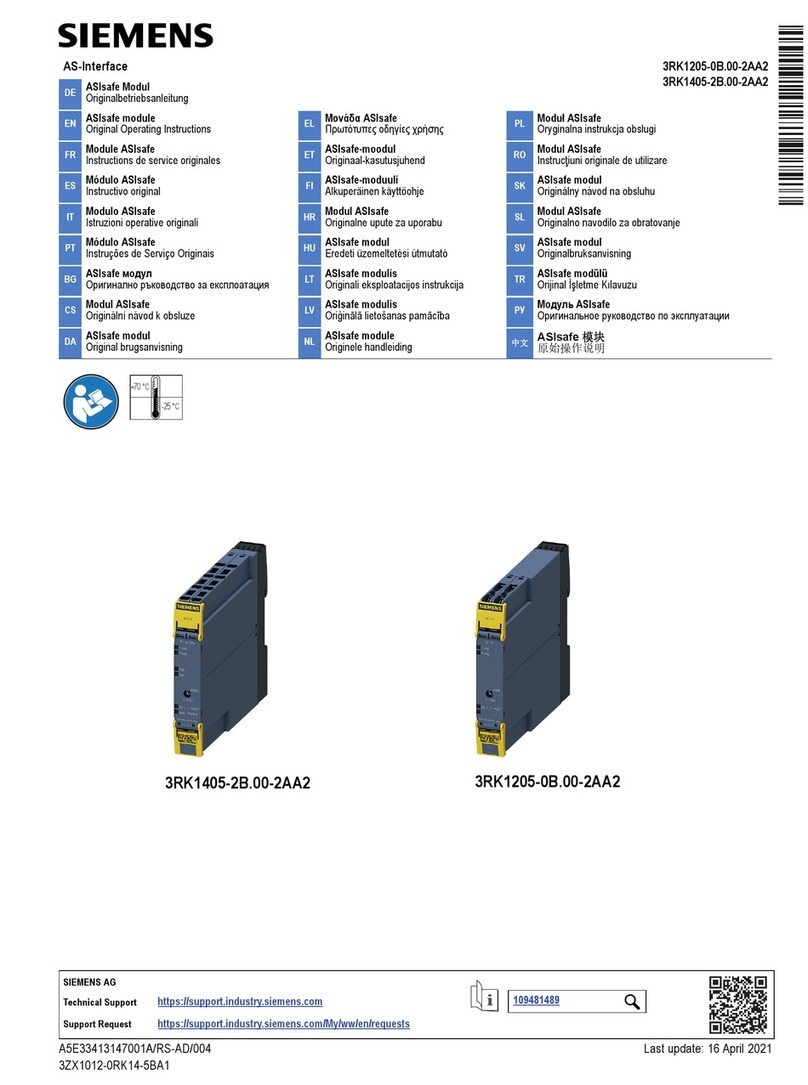
Siemens
Siemens AS-Interface ASIsafe 3RK1205-0B.00-2AA2 Original operating instructions

Avermedia
Avermedia NX215 manual

Lawler
Lawler 911E Installation & maintenance manual
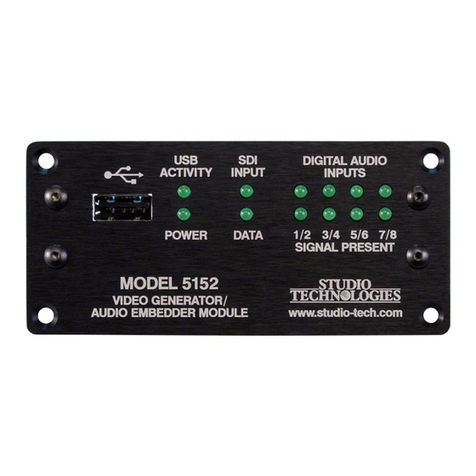
Studio Technologies
Studio Technologies 5152 user guide
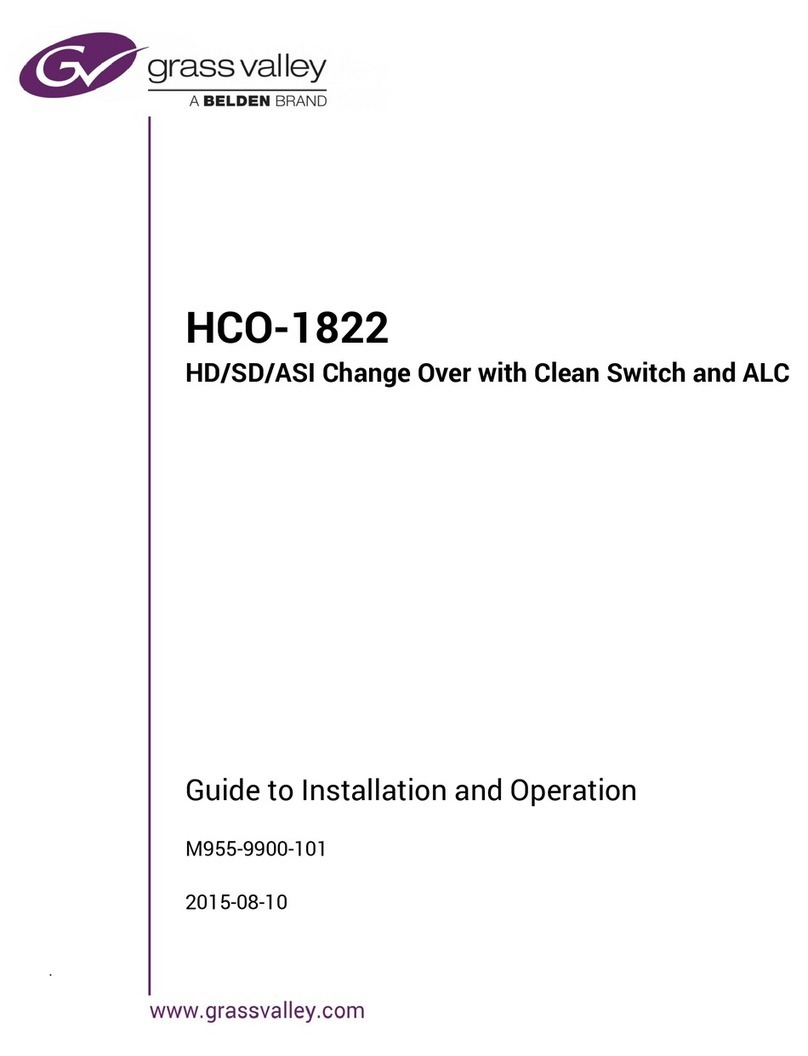
Belden
Belden Grass Valley HCO-1822 Guide to installation and operation
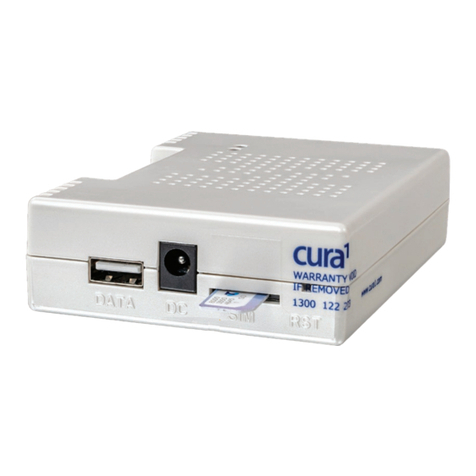
Cura1
Cura1 ENSIGN+ Setup instructions
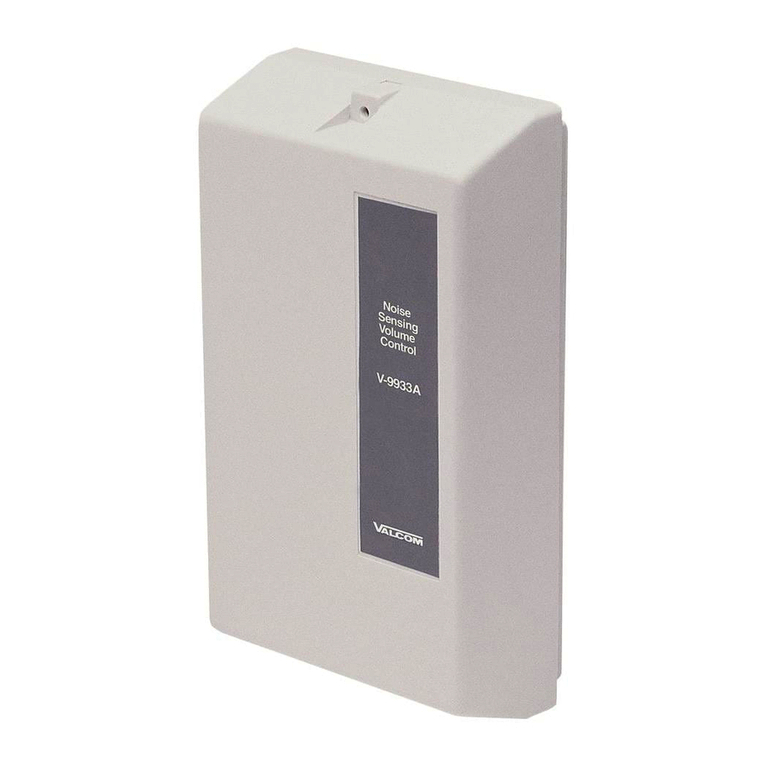
Valcom
Valcom V-9933A user guide
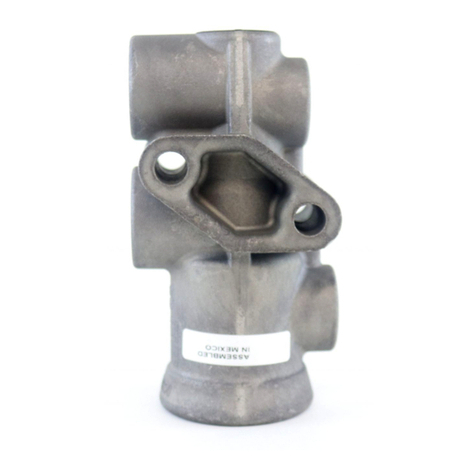
BENDIX
BENDIX TP-3 TRACTOR PROTECTION VALVE manual
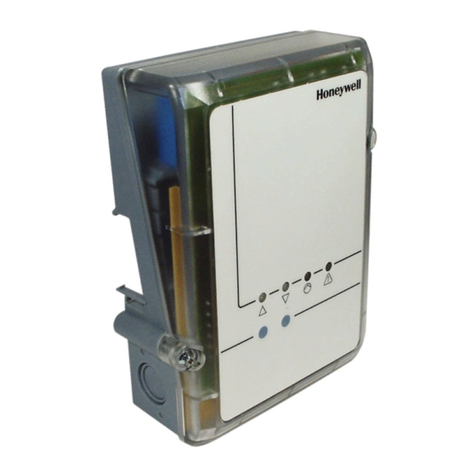
Honeywell
Honeywell HM 80 Installation and operation
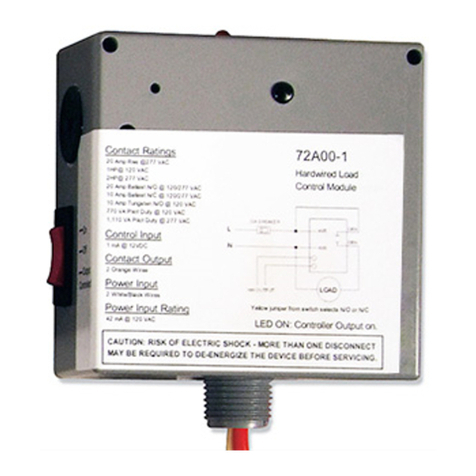
Leviton
Leviton 72A00-1 Installation instructions and user guide