Ag Leader DirectCommand User manual

DirectCommand Installation
Croplands Sprayer Kit Ag Leader Technology
PN: 2006343 Rev. A February 2013 Page 1 of 10
This DirectCommand Kit also requires the installation of a
Display Kit and Display Cable Kit for Proper Operation
Note: Indented Items Indicate Parts Included in an Assembly listed Above
Part Name/Description Part Number QTY
DirectCommand Kit – Croplands Sprayer Kit 4200113 1
Cable Installation Kit 2000901-1 1
Mounting Kit – Large Module Mounting Plate 2001358 1
Dielectric Grease 2002872 1
Quick Reference Guide – DirectCommand Sprayer 2006310 1
Installation Instructions 2006343 1
Liquid Product Control Module 4000394 1
Cable – CAN Bus Stub, LCM, 8in 4000450-1 1
Implement Cable, 12ft 4000726-12 1
Cable – CAN/Power with Implement Connection 4001979-12 1
Cable – Croplands Sprayer adapter (6ft) 4003667-6 1
CAN Switch Box Kit 4100879 1
Hardware Kit 2001352-1 1
Dust Plug – Deutsch, DT, 6 Pin 2002899-6 1
Plug – 4 Pin ITT Cannon 4000136 1
Dust Plug – Deutsch, DT, 12 Pin 2002899-12N 1
Y-Splice 4000137 1
Bracket Display Switchbox 4001657 1
Switch Console 4000400 1

Ag Leader Technology DirectCommand Installation
Croplands Sprayer Kit
Page 2 of 10 February 2013 PN: 2006343 Rev. A
Important
Notices You will save time and prevent wrong installation of components by closely
following these step-by-step instructions. If you have questions call Ag
Leader Technology at 515-232-5363 Ext 1
Direction words (LEFT and RIGHT) are commonly used when describing an
installation procedure. Interpret direction words as if standing behind
equipment and looking forward
Signal words (CAUTION, IMPORTANT and NOTE) are provided to draw
attention to information that is important for the safe/correct installation and
operation of this product
•CAUTION – will alert you to situations that will impact the physical
safety of you or others
•IMPORTANT – will alert you to the potential for damage to the product
or loss of data
•NOTE – will provide you with additional information to simplify a
procedure or clarify a process
Read all instructions first to familiarize yourself with the installation
procedures
Keep parts list and installation instructions for use as a reference after
completing the installation
This DirectCommand Kit fits the following machines:
MY2012 & Newer Pegasis 8000L Broadacre Sprayer
Section
Contents
Section Heading
Page
Common Components 3
System Layout 4
Safety Notices 5
Installing the CAN Switch Box 6
Installing the Liquid Control Module 7
Installing the CAN Bus Harnesses 8
Installing the Croplands Adapter Harnesses 9
Setting up the Display 10

DirectCommand Installation
Croplands Sprayer Kit Ag Leader Technology
PN: 2006343 Rev. A February 2013 Page 3 of 10
Common
Components This section contains illustrations of components common to all
DirectCommand Installations. The purpose is to ensure proper identification
and installations in the sections that follow.
1.
Terminator
PN: 4000141
2.
Plug
PN: 4000136
3.
Y
-
Splice
PN:
40000137
1.
Liquid Control Module
PN: 4000394

Ag Leader Technology DirectCommand Installation
Croplands Sprayer Kit
Page 4 of 10 February 2013 PN: 2006343 Rev. A
System
Layout

DirectCommand Installation
Croplands Sprayer Kit Ag Leader Technology
PN: 2006343 Rev. A February 2013 Page 5 of 10
Safety Notices
CAUTION:
Hydraulic equipment should be on safety stops, hydraulic
pressure relieved with machines systems turned off and all machine motion
stopped before starting work.
CAUTION: Be sure to wear proper eye protection when using any power
tools, such as when drilling any mounting holes.
IMPORTANT: Check behind vehicle and implement panels for any holes,
wiring or controls that could be damaged when drilling any holes.
IMPORTANT: Disconnect the Display, DirectCommand components and
any sensors from electrical system when welding on equipment or jump
starting unit to prevent component damage due to power surges or excessive
current.
IMPORTANT: If using a non Ag Leader GPS receiver, make sure to install a
Null Modem Cable, included in the Display Kit, to prevent damage to the
Display or GPS receiver.
IMPORTANT: Use Dielectric grease to coat the seals and terminals of each
connector that will be exposed to weather or chemicals as you plug them in.
NOTE: Be sure to follow the alignment keys on the plugs and the receptacles
carefully. Do not use excessive force when mating connectors.

Ag Leader Technology DirectCommand Installation
Croplands Sprayer Kit
Page 6 of 10 February 2013 PN: 2006343 Rev. A
Installing the
CAN Switch
Box
Parts Required for
Procedure:
From CAN Switch Box Kit:
Hardware Kit PN: 2001352-1
Dust Plug – Deutsch, DT, 6 Pin PN: 2002899-6
Plug – 4 Pin ITT Cannon PN: 4000136
Dust Plug – Deutsch, DT, 12 Pin PN: 2002899-12N
Y-Splice PN: 4000137
Bracket Display Switchbox PN: 4001657
Switch Console PN: 4000400
Step-by-Step
instructions for
installing the
CAN Switch Box
1. Place the display face down on a stable surface. Align the holes of
the Bracket Display Switchbox PN: 4001657, and RAM Base PN:
4000280 with the threaded holes on the display.
2. Secure the Bracket and RAM Base to the display using the 6mm
Phillips head screws with lock washers from Hardware Kit PN:
2001352-1.
3. Locate the Switch Console PN: 4000400, align the two threaded
holes in the Switch Console with the two holes of the previously
installed Bracket Display Switchbox.
4. Secure the Switch Console using the 6mm Phillips head screws with
lock washers from Hardware Kit PN: 2001352-1.
5. When finished mounting should be as shown in the figure below.
6. Route the opposite end of the Switch Console towards the Display
Cable.
7. Locate the Y-splice PN: 4000137, connect the single end of the Y-
splice to the Black 4-pin CANNON receptacle on the display cable.
8. Connect the Black 4-pin CANNON receptacle from the Switch
Console to the Gray 4-pin plug on the Y-splice.

DirectCommand Installation
Croplands Sprayer Kit Ag Leader Technology
PN: 2006343 Rev. A February 2013 Page 7 of 10
Installing the
Liquid Control
Module
Parts Required for Procedure:
From DirectCommand Kit:
Mounting Kit – Large Module Mounting Plate PN: 2001358
Liquid Product Control Module PN: 4000394
Step-by-Step
instructions for
installing the
Liquid Control
Module
1. The Liquid Control Module may be mounted at the operator’s
discretion. Make sure the module is mounted in a location where
adapter cabling will reach.
2. If mounting the Liquid Control Module on an existing plate, using the
module as a template, drill ¼” diameter holes in the plate. Use ¼”
stainless steel hardware provided in the Hardware Kit PN: 2001354-1
to secure the module into place.
3. If mounting the Liquid Control Module on a chassis, the Large Module
Mounting Kit PN: 2001358 may be used for toolbars up to a 6” x 6”
square tube.

Ag Leader Technology DirectCommand Installation
Croplands Sprayer Kit
Page 8 of 10 February 2013 PN: 2006343 Rev. A
Installing the
CAN Bus
Harness
Parts Required for Procedure:
From DirectCommand Kit:
Dielectric Grease PN: 2002872
Y-splice PN: 4000137
Terminator PN: 4000141
Cable – CAN Bus Stub, LCM, 8in PN: 4000450-1
Implement Cable, 12ft PN: 4000726-12
Cable – CAN/Power w/ Implement
Connection PN: 4001979-12
Optional Parts Purchased Separately
Cable – CAN Bus Power Extension, 6ft PN: 4000724-6
Cable – CAN Bus Power Extension, 12ft PN: 4000724-12
Cable – CAN Bus Power Extension, 24ft PN: 4000724-24
Cable – CAN Bus Power Extension, 36ft PN: 4000724-36
Step-by-Step
instructions for
installing the
CAN Bus
Harnesses
1. Locate the CAN/Power with Implement Connection Cable PN:
4001979-12, connect the Black 4-pin CANNON Receptacle to the
open side of the Y-splice previously installed on the display cable.
2. Connect one of the Gray 2-pin Deutsch receptacles to the Gray 2-pin
Deutsch plug of the Power Cable PN: 4002016-x.
3. Route the opposite end of cable PN: 4001979-12 to a location near the
hitch point of the tractor/implement securing the cabling using zip ties
to avoid pinch points.
4. Locate the Implement Cable PN: 4000726-12, connect the Black AMP
receptacle to the Black AMP plug on cable PN: 4001979-12.
If distance between Tractor/Implement connection and Liquid
Control Module exceeds 12ft, install an optional CAN Bus Power
Extension cable PN: 4000724-x.
5. Route the opposite end of cable PN: 4000726-12 towards the Liquid
Control Module, connect the Gray 2-pin Deutsch plug to the mating
Gray 2-pin Deutsch receptacle hardwired into the Liquid Control
Module.
6. Locate the CAN Bus Stub PN: 4000450-1, connect the Black 4-pin
CANNON receptacle to the Gray 4-pin plug of the Y-splice PN:
4000137.

DirectCommand Installation
Croplands Sprayer Kit Ag Leader Technology
PN: 2006343 Rev. A February 2013 Page 9 of 10
7. Route the opposite end of the stub cable towards the Liquid Control
Module, connect the Gray 4-pin Deutsch plug into the receptacle
labeled CAN BUS on the Liquid Control Module.
Installing the
Croplands
Adapter
Cabling
Parts Required for Procedure:
From DirectCommand Kit:
Cable – Croplands Sprayer Adapter PN: 4003667-6
Step-by-Step
instructions for
installing the
Croplands
Adapter Cabling
1. Locate the Croplands Sprayer Adapter Cable PN: 4003667-6, connect
the Black 12-pin Deutsch plug into the receptacle labeled AUXILIARY
on the Liquid Control Module.
2. Connect the Gray 12-pin Deutsch plug into the receptacle labeled
BOOM on the Liquid Control Module.
3. Connect the Gray 8-pin Deutsch plug into the receptacle labeled
CHANNEL on the Liquid Control Module.
4. Connect the Gray 2-pin Deutsch receptacle to the Gray 2-pin Deutsch
plug on the Implement Cable PN: 4000726-12.
5. Route the opposite end of the Croplands Adapter Cable towards the
24-pin plug on the existing sprayer harness, connect the 24-pin
receptacle to the 24-pin plug of the existing sprayer harness.
6. Bundle cables and secure them as necessary with zip-ties from Cable
Installation Kit PN: 2000901-1.

Ag Leader Technology DirectCommand Installation
Croplands Sprayer Kit
Page 10 of 10 February 2013 PN: 2006343 Rev. A
Setting up the
Display Refer to the chart below for setting up the controller settings in the display:
Setting
Name
Default
Value Description
Control
Valve Bypass
Servo
Rate control is achieved through actuating a butterfly or ball valve found
in the return line to the solution tank. When the valve opens, the flow
decreases and when the valve closes the flow increases.
Valve
Response 1 40 Determines the speed of the servo valve when product control error
exceeds the Response Threshold setting. Decreasing the value will
cause the servo valve to run slower.
Valve
Response 2 10 Determines the speed of the servo valve when product control error is
less than the Response Threshold setting. Decreasing the value will
cause the servo valve to run slower.
Response
Threshold 5-10
Determines where the control system switches between using Valve
Response 1 or Valve Response 2 speed setting. Leaving all other valve
control settings at the default value and making a small adjustment to
this setting is usually all that is required to fine tune system
performance.
- Decreasing this value will have the overall effect of speeding up servo
valve response.
- Increasing this value will have the overall effect of slowing servo valve
response.
Allowable
Error 2% Determines the percent of error that is allowed prior to the product
control system making any flow rate corrections.
Auxiliary
Valve 1 Open When all boom sections are off, this setting opens an auxiliary valve to
route product back to the product tank.
Table of contents
Other Ag Leader Control Unit manuals
Popular Control Unit manuals by other brands
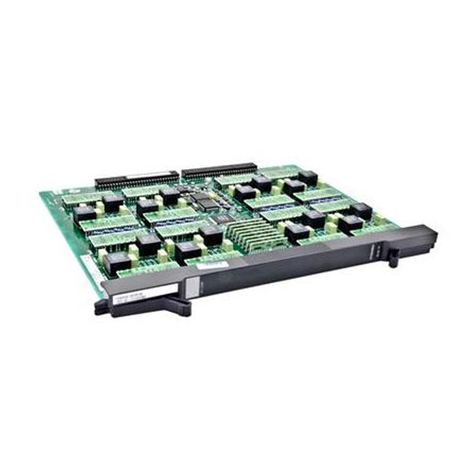
Lucent Technologies
Lucent Technologies Stinger STGR-LIM-AP-72 Module guide

Eaton
Eaton XNE-1SWIRE user manual
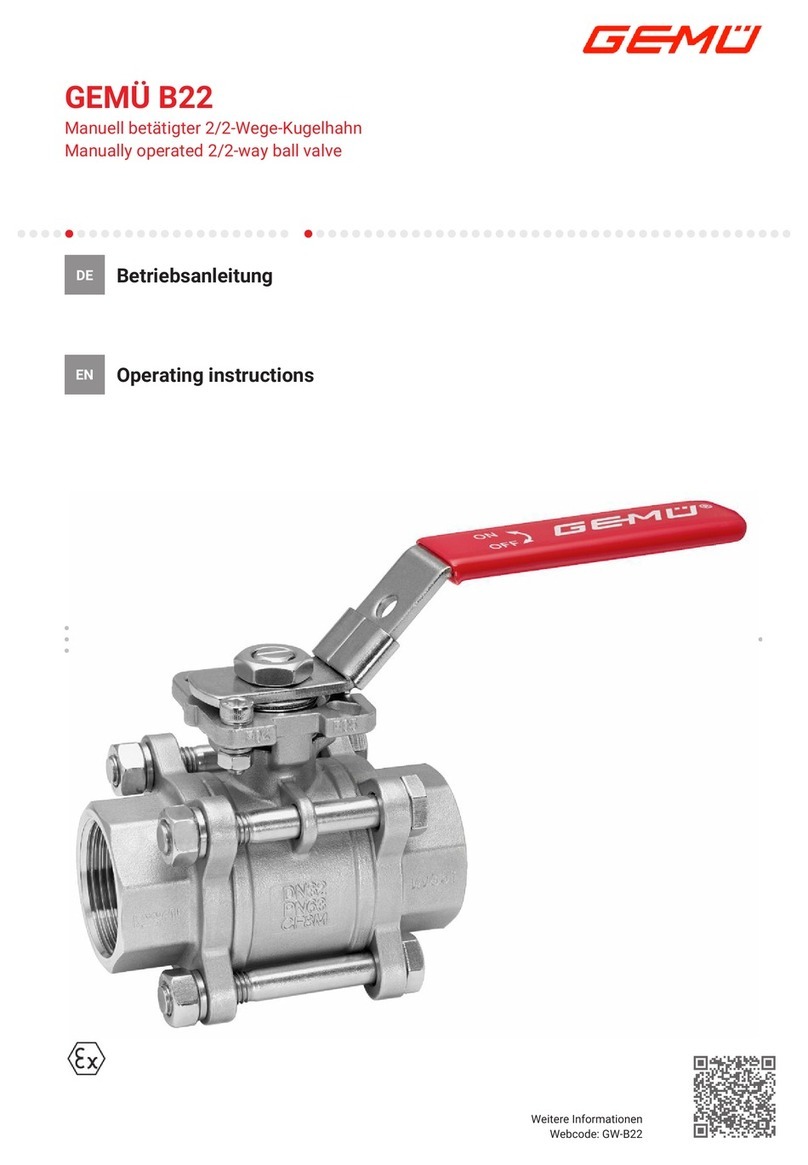
GEM
GEM B22 operating instructions
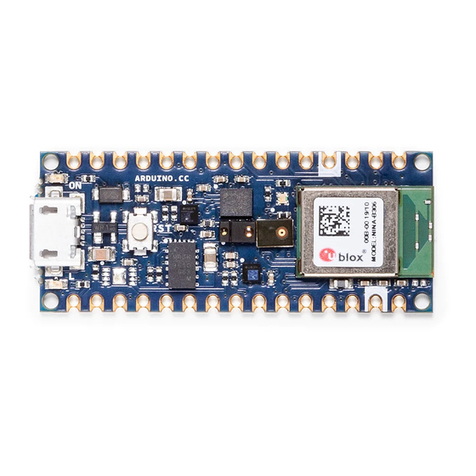
Arduino
Arduino Nano 33 BLE Product reference manual
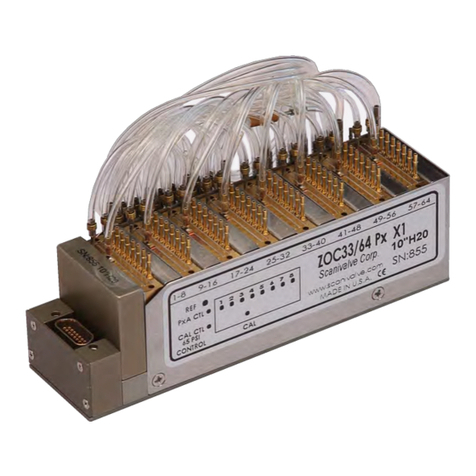
Scanivalve
Scanivalve ZOC 33/64Px Instruction and service manual
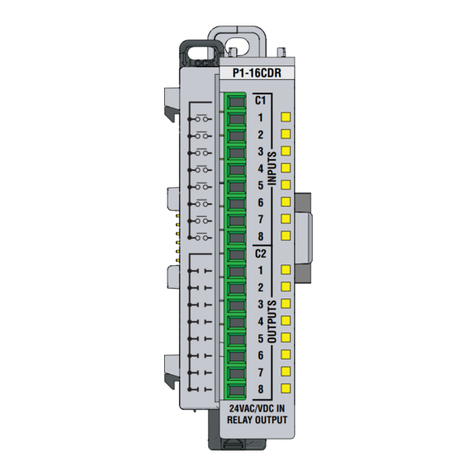
Automationdirect.com
Automationdirect.com Productivity 1000 P1-16CDR manual