CGM MDR-01 User manual

Operation’s manual Rheometer MDR-01
1
1. Specifications
- Reference Standard
ISO 6502, ASTM D5289
- Pressure system
Air cylinder system
- Die configuration
Biconical Die, close die system, sealed
- Temperature System
PID Microprocessor Controlled
Probe RTD Pt 100 Ω(Class A)
- Temperature range
Room Temp. (+25 °C) to 250 °C
Resolution 0.1
°C Units °C/ °F
- Oscillation frequency
100 cpm. (1.667 Hz)
- Oscillation angle
0.5°±0.03°, 1°±0.03°
- Drive Motor
Servo Motor
- Torque Measurement
Torque Transducer (Direct Torque Measurement)
- Torque Calibration
Standard Torque Reference value
- Operation Panel
Capacitive Touch Screen, 5 Inches (Standalone)
- Measured Time
1/60 sec, 1/100 sec
Unit (min-min/ min-sec/ sec)
- Communication Data
RS-232
- Associated program (Option)
Data Process Software
- Power Supply
220 VAC ±10 VAC, 50/60 Hz, 6 A
- Air Pressure
4.0 bar to 5.0 bar
- Dimension
Width 50.0 cm., Depth 54.5 cm., Height 105 cm.
- Weight
140 kg.

Operation’s manual Rheometer MDR-01
2
2. Components
1
2
5
3
6
4
Figure 1 Front image of the MDR-01
Figure 1, illustrates the components of the front perspective of the MDR -01, as follows;
No. 1: The Upper Plate, which consists of the Upper die, Heater, and Probe Sensor
No. 2: The Lower Plate, which consists of the Lower die, Heater, and Probe Sensor
No. 3: Display panel
No. 4: Emergency Stop button
No. 5: On/Off plate switch
No. 6: On/Off motor switch

Operation’s manual Rheometer MDR-01
3
8
7
9
10 11
Figure 2 Internal Components of the MDR-01
Figure 2, illustrates the internal components of the MDR -01, as follows;
No. 7: Servo Motor
No. 9: Transformer
No. 8: Thermostat
No. 10: Adjustable leg stand
No. 11: Main control panel

Operation’s manual Rheometer MDR-01
4
12
14 13
Figure 3 Side image of the MDR-01
Figure 3, illustrates the side perspective of the MDR -01, as follows;
No. 12: RS323 outlet for connection to a computer or printer
No. 13: Power outlet (220 VAC)
No. 14: On/Off breaker switch

Operation’s manual Rheometer MDR-01
5
15
18 16
17
Figure 4 Rear image of the MDR-01
Figure 4, illustrates the rear components of the MDR -01, as follows;
No. 15: Air Muffler
No. 16: Air ventilator
No. 17: Air intake, which is connected to the Air Regulator
No. 18: Air Regulator

Operation’s manual Rheometer MDR-01
6
3. Installation
3.1) For the installing technician
1. Set the device to a level position
3.2) For users
1. Site preparation for the installation of MDR-01
- Grounded power outlet with a 220 VAC 50Hz/60Hz capacity, that can
discharge at no less than 6 Amp
- Compressed air supply of at least 4-5 bars
- Support structure to place the MV-01, which can withstand a weight of
200 kg. or more.
2. Installation instructions for the Rheometer MDR-01
- Recommended to be used in conjunction with a UPS with a minimum
capacity of 1.5KVA or more.
- Recommended to be installed in rooms with temperature and humidity
control.

Operation’s manual Rheometer MDR-01
7
4. How to use the touch screen panel of the Rheometer MDR-01
After powering up the MDR-01, the main screen display will be as indicated in
Figure 5, which is used for monitoring and tracking of the test results. The main functions
will consist of Testing, Condition, Calibrate, and Configuration.
Figure 5 Image of the Main Screen display
1. Testing Displays the results of the test in a graphical format.
2. Condition Sets the conditions or state of the sample to be tested.
3. Calibrate Sets the testing and calibration of the TORQUE STANDARD
4. Configuration Monitors the status and parameter settings, and stores them in
the device’s memory.
4.1) Testing
By pressing the “Testing” button, will enter into the testing mode, in which the
function consists of 4 sections; STANBY, RESULT, GRAPH, and CLOSE. See
Figure 6.

Operation’s manual Rheometer MDR-01
8
A
Figure 6 shows the main display of the Testing mode
Figure 7 shows the resulting display when A is selected
Note: Pressing A area on touch screen for switching the display between Figure 6
and Figure 7.

Operation’s manual Rheometer MDR-01
9
4.1.1) STANBY is the ready function, waiting for the samples to be tested.
See example below.
Figure 8 shows the display screen in the STANBY mode
4.1.2) RESULT, will show the test results, as can be seen in Figure 9.
Figure 9 shows the display of the RESULT function
Components of the Test results
1. MH : Value of highest torque
2. ML : Value of lowest torque

Operation’s manual Rheometer MDR-01
10
3. ts1 : Scorch time 1, time from the start where torque equal
ML to the time where torque equal ML+1
4. ts2 : Scorch time 2, time from the start where torque equal
ML to the time where torque equal ML+2
5. tc10 : Cure time at 10%
6. tc50 : Cure time at 50%
7. tc90 : Cure time at 90%
Note: Cure time 100% is time from the start of the test where lowest torque
value (ML) is reached highest torque value (MH)
4.1.3) GRAPH, displays the sample test results in a graphical format and its
associated numerical values, as shown in Figure 10
Figure 10 displays the GRAPH function
4.1.4) CLOSE, controls the On/Off function of the Plate and Die
Status
RED, Plate has been closed, and sample testing is in progress.
GREEN, Plate is open, and sample testing is waiting to be tested

Operation’s manual Rheometer MDR-01
11
4.2) Condition
When “Condition” is selected, you will enter into the Condition page, which will
display the conditions of the sample test. The parameters can be adjusted to suit the
test sample, as shown in Figure 11
Clears the parameters
Returns to the previous menu
Confirms the value entry
Figure 11 shows the main Condition display
4.2.1) How to Use
To enter or modify the values to any functions, proceed according to the
following steps;
1. Entering the parameters, and how to correct it.
Select the required parameter >> enter the value >> Select “E” to
confirm.
2. To clear the parameters.
Select the required parameter >> Select “Clear” (the value will be reset
to 0).

Operation’s manual Rheometer MDR-01
12
4.2.2) Functions
1. Time Set : is the function that determines the time required to test the
sample (with a range of 0–99 minutes) .
For example; to set the time for 1 minute, just press “1” and then “E” to
confirm.
2. Temp Set : is the function that determines the temperature to test the
sample (with a range of 0–250 ºC).
For example; to set the temperature for 150ºC, just press “150” or “150.0”
and then “E” to confirm.
3. Preheat time : is setting preheat time function before testing.
Starts from plate is closed. (ranges 0-99 seconds).
Note: The use of this function must be used under the
calibration by an experienced engineer.
4. Stability temp : is the function that configures the operating
functioning temperature while the device is operating. It will provide
alerts on the status of the temperature (ranges from 0–9 ºC).
For example; to set the temperature for 1ºC, just press “1” and then
“E” to confirm.
5. Time Stability: is setting duration function. When the temperature is
reached the set point on Testing screen, ‘Ready’ will be shown for
notice the user, machine is ready. (ranges 0-999 seconds x 0.1).
For example; to set the time for 1 second, just press “1” or 1.0 and
then “E” to confirm.
6. Test mode : is testing method function. 2 modes as follows;
1) Time : Testing time depend on Time Set values.
2) Peak time : Testing time will be stopped when MH values
indicated.

Operation’s manual Rheometer MDR-01
13
7. I-Time : is starting time function before finding ML values.
Starts from plate is closed. (ranges 0-99 seconds)
For example; to set the time 13 seconds, just press “13”and then “E”
to confirm. The machine will be started after plate was closed 13
seconds.
4.3 Calibration
Selecting “Condition” will enter into the Calibrate screen, which consists of 6
components; Utility, Calibration, Motor, Platens, and Clamp, as shown in Figure 12.
Figure 12 shows the main Calibrate screen
4.3.1) adjusts the Rheo Linearity function
Note: The use of this function must be used under the calibration by an
experienced engineer.
4.3.2) adjusts the Torque Reference function. When
selected, the screen will be shown as Figure 13.

Operation’s manual Rheometer MDR-01
14
A
B
C
Figure 13 shows the main display of the Configuration Torque
- Select A area to set Torque Standard unit for Calibrate
(dNm, lbin, and kg-f).
- Select B area to set STD Torque value according to Correction
Torque Standard value for Calibrate.
- Select C area to set Warm up time (Torque Standard warming).
To enter or modify the values to any functions, proceed according to the
following steps;
1. Entering the parameters, and how to correct it
Select the required parameter >> enter the value >> Select “Enter” to
confirm.
2. Using the “Clear” button to clear the parameters
Select the required parameter >> Select “Clear” (the value will be reset
to 0).
3. Using the “Back” button
To edit a numeric value, such as 100.0 to 125.0, select the required
parameter field >> select “Back” to the required location >> enter the
value >> select “Enter” to confirm.

Operation’s manual Rheometer MDR-01
15
4.3.3) is torque calibration sensor function of MDR-
01 with Standard torque. To enable the operators to correctly calibrate
the device.
4.3.4) Checking the operating status of the device.
Function Status
Response
OFF
ON
When “Motor” is selected, the color of the
button will change to red, and the motor will
start to rotate.
When “Platens” is selected, the color of the
button will change to red, and the front panel
of the device will be opened.
4.4 Configuration
When “Configuration” is selected, the Configuration section will appear, which
consists of 7 functions; Temp. Parameter, Temp. Auto tune, Temp. Offset, I/O
Check, Machine Check, Communication Check, and Instrument setting, as shown in
Figure 14.
Figure 14 shows the main Configuration screen

Operation’s manual Rheometer MDR-01
16
4.4.1) Temp. Parameter
Temp. Parameter, will display the functions for monitoring the operating
temperature range, as shown in Figure 15.
Figure 15 shows the Temp. Parameter screen
4.4.2) Temp. Auto tune
Temp. Auto tune, is used to adjust the temperature controls, as shown in
Figure 16
Note: The use of this function must be used under the calibration by an
experienced engineer.
Figure 16 shows the Temp. Auto tune screen

Operation’s manual Rheometer MDR-01
17
4.4.3) Temp. Offset
Temp. Offset, is used to the parameters of the temperature, as shown in
Figure 17.
Note: The use of this function must be used under the calibration by
an experienced engineer.
Figure 17 shows the Temp. Offset screen
4.4.4) I/O Check
I/O Check, is used to verify the status of the various buttons, as shown in
Figure 18.
Note: The use of this function must be used under the calibration by
an experienced engineer.
Figure 18 shows the I/O Check screen

Operation’s manual Rheometer MDR-01
18
4.4.5) Machine Check
Machine Check, is used to verify the status of the test device, as shown in
Figure 19.
Note: The use of this function must be used under the calibration by
an experienced engineer.
Figure 19 shows the Machine Check screen
4.4.6) Output
Output, is used to setting the connected external device, as shown in
Figure 20.
Figure 20 shows the Output screen

Operation’s manual Rheometer MDR-01
19
4.4.7) Communication Check
Communication Check, is used to check on the communication status of the
connected internal and external test device, as shown in Figure 21
Note: The use of this function must be used under the calibration by
an experienced engineer.
Figure 21 shows the Communication Check screen

Operation’s manual Rheometer MDR-01
20
No. 1
Displays the Torque value
No. 2
Displays the temperature of the Upper Die and lower Die
No. 3
Menu Bar
No. 4
Test elapsed time (Mins:Secs)
No. 5
Name of the test sample
No. 6
Set the highest value of the graph in the Y axis. (Torque)
5. How to use the Computer System Operations
Double-click on the “RHEO” icon to activate the system, which will display
the main operating screen, as shown in Figure 22.
5.1) Main Menu descriptions RHE
O
1 2 3 4
5
6
7
8
9
Figure 22 Main Menu of the system
10
From Figure 22, the main components of the Main Menu can be explained, as follows;
Table of contents
Popular Measuring Instrument manuals by other brands
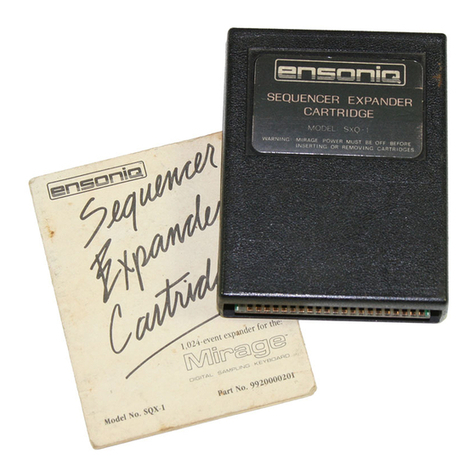
ENSONIQ
ENSONIQ SQX-1 operating instructions
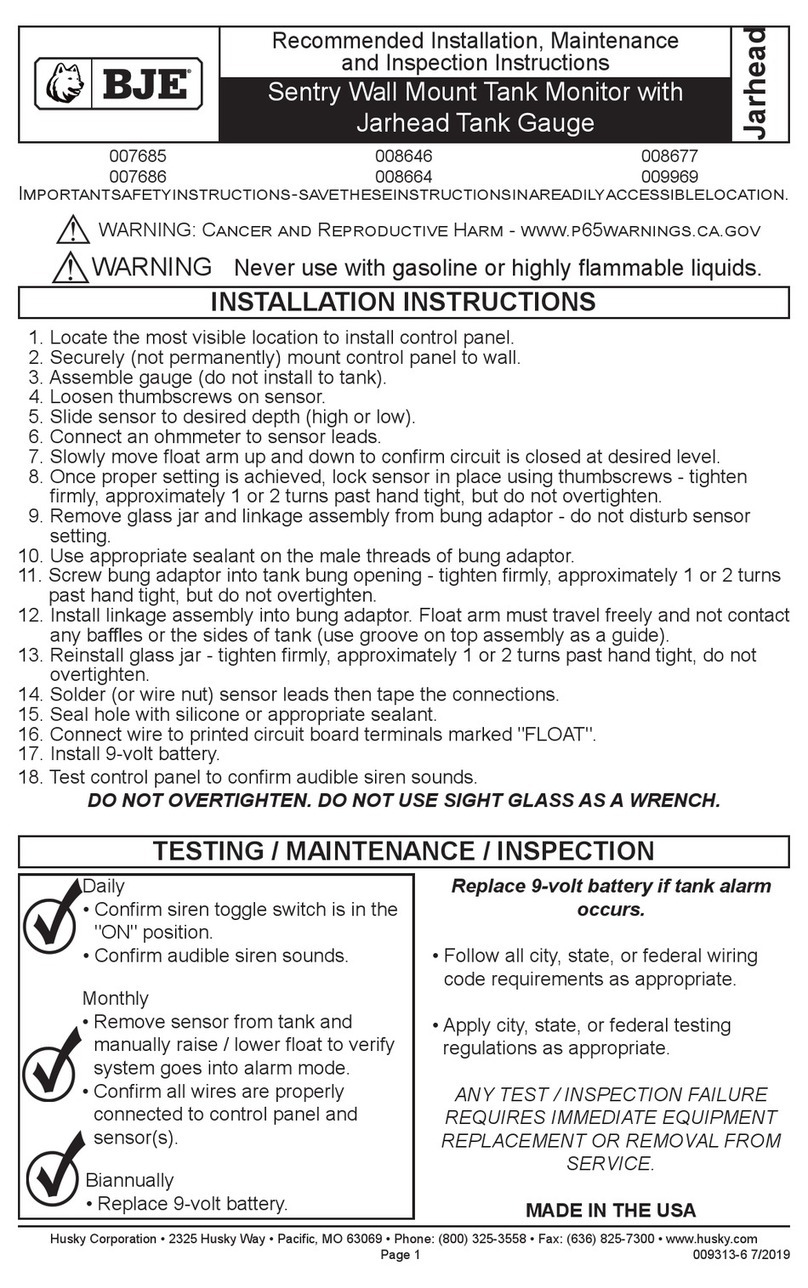
BJE
BJE 007685 Recommended Installation, Maintenance and Inspection Instructions
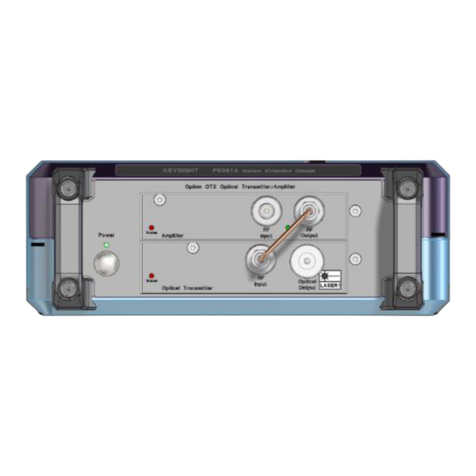
Keysight Technologies
Keysight Technologies P939 A Series user guide
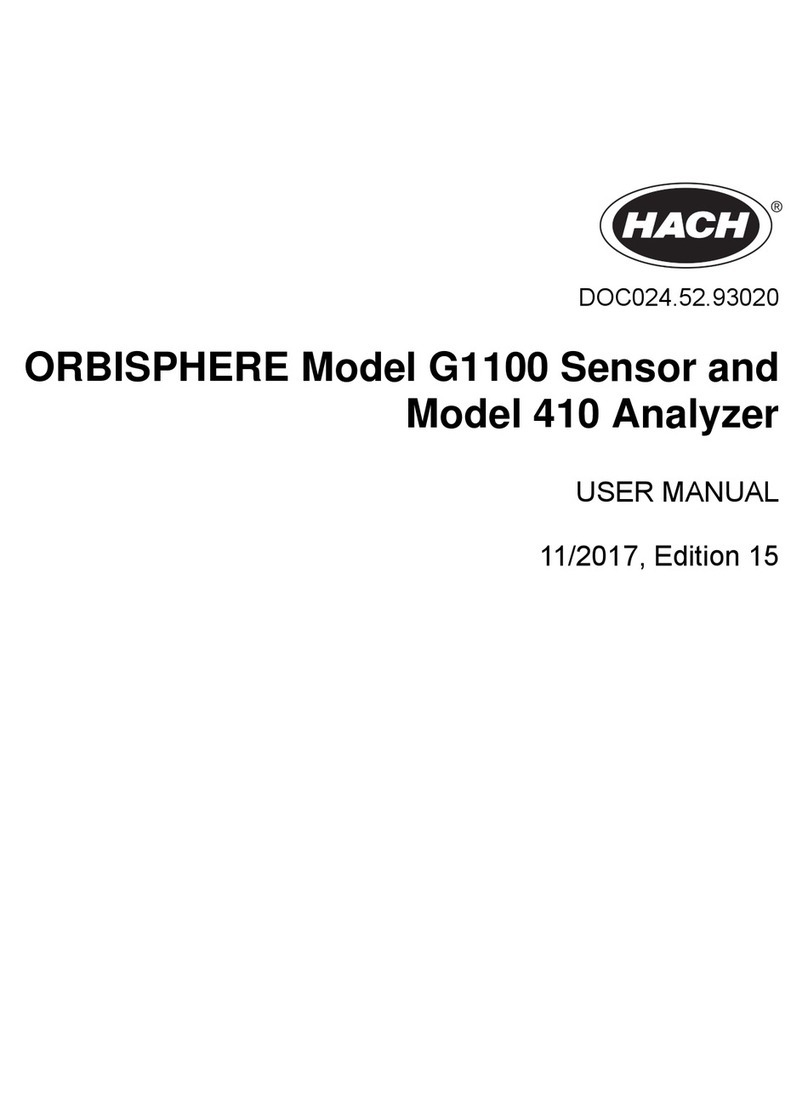
Hach
Hach ORBISPHERE G1100 user manual
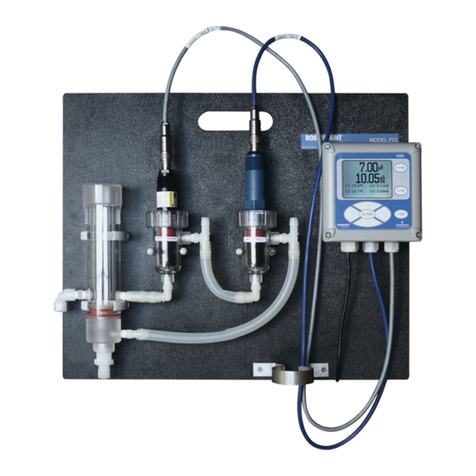
Emerson
Emerson Rosemount FCL Reference manual
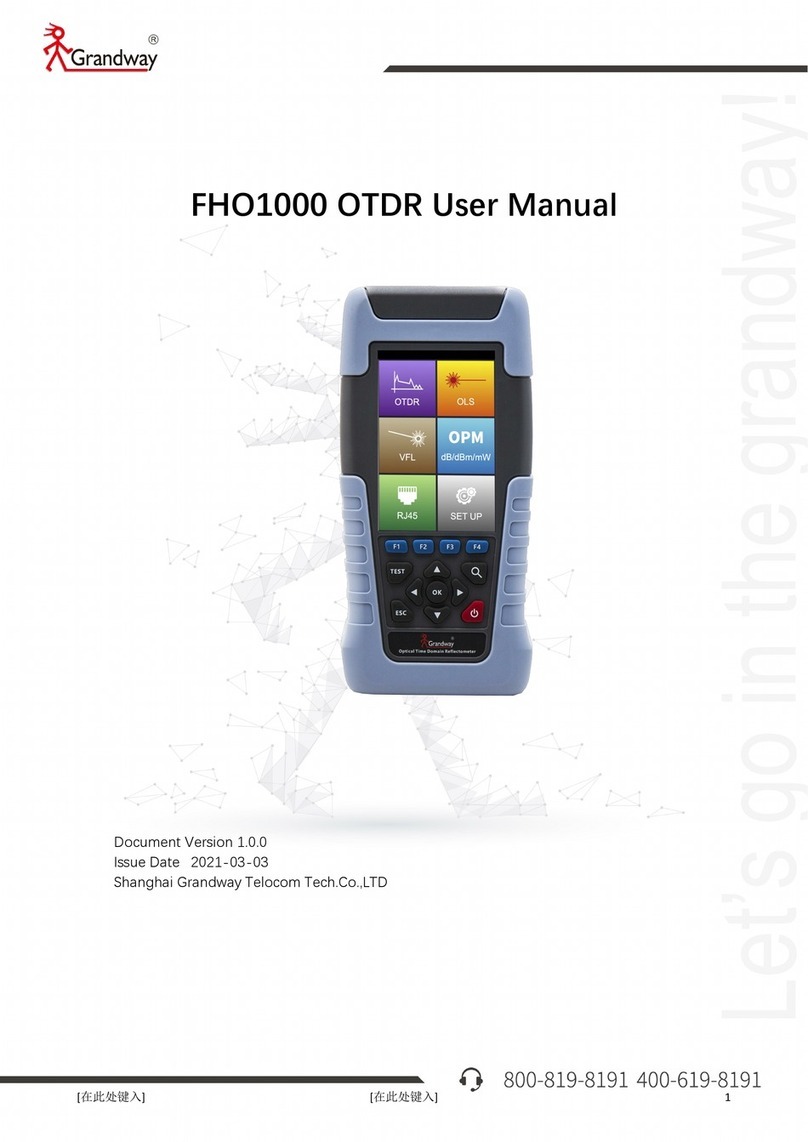
Grandway
Grandway FHO1000 user manual