Challenge EH-3C User manual

The Challenge Machinery Company
6125NortonCenterDrive
Norton Shores, MI 49441-6081 USA
ChallengeMachinery.com
F. 352-KO
August 2003
Serial Numbers 995774 & Up
MODEL EH-3C
PAPER DRILLING
MACHINE
Sold and Serviced by
OPERATION
MANUAL

F.352-KO/EH-3C DRILL/AUG 03
ii
INTRODUCTION
WELCOME tothe familyof Challenge®users. Challenge hasbeen developingand manufacturingGraphics Arts
Equipmentfor over 100years andis todayone of the world’s leadingproducers anddistributors of Paper Cutters,
PaperDrillsandBindery Equipment.
SAFETYALERT! This symbol meansCAUTION OR WARNING: Personal safety instructions! Pay
special attention to the instructions in bold type. Personal injury may result if the precautions are not
readand followed. SeeSAFETY PRECAUTIONS,pagev.
•This machine is designed forONEPERSON OPERATION ONLY!
•Always DISCONNECT THE POWER before working on this machine.
•DO NOT OPERATEWITH ANY GUARDS REMOVED! Replace allguardsbeforeoperating.
•CRUSH HAZARD - Keep hands, hair, cleaning rags, & loose clothing away from drills.
READ THIS MANUAL BEFORE OPERATING! Follow precautions and instructions given and you should have
years of trouble-free operation. If after reading the manual questions still remain, contact your Authorized Chal-
lengeDealer.
FOR PARTS AND SERVICEcontactthe AuthorizedChallenge Dealerfrom whomyou purchasedyour machine.
Use the illustrations and parts lists at the back of this manual to identify the correct parts needed. Always give
the SERIAL NUMBER and MODELof your machine to insure that the correct parts are sent as soon as possible.
Take a few minutes right now to RECORD YOUR MACHINE SERIAL NUMBERin thespace providedon thefront
coverof this manual. Alsobe sure tofillout thewarrantycard accompanyingthismanual andreturnitDIRECT TO
CHALLENGE.
If you bought a used machine, it is important to have the following information on record at Challenge. Copy this
page, fill in the information and send it care of: The Challenge Service Department, 6125 Norton Center Drive,
NortonShores, MI 49441-6081.
CHALLENGEMODEL SERIALNUMBER
ATTN COMPANY
ADDRESS
CITY STATE ZIP
PHONE DATEINSTALLED
DEALER’SNAME ANDCITY
Challenge® is a registered trademark of The Challenge Machinery Company. 6125 Norton Center Drive, Norton Shores, MI 49441-6081.
Copyright © 2003 by The Challenge Machinery Company. All rights reserved. Printed in the U.S.A.
PLEASE REVIEW THE WARRANTY SHEET!
It isvery important that you read and understand the conditions outlined in the Warranty Information Sheet. It is
in an envelope attached to the outside of the shipping container.
The Warranty Information Sheet must be filled out completely, returned, and be ON-FILE at THE CHALLENGE
MACHINERY COMPANY in order for the warranty to be issued for this machine.
WARRANTY INFORMATION

iii
F.352-KO/EH-3C DRILL/AUG 03
TABLE OF CONTENTS
INTRODUCTION........................................................................................... ii
SAFETYPRECAUTIONS ..............................................................................v
CAUTION: POWERLOCK-OUTPROCEDURE .............................................v
WARNINGLABELDEFINITIONS..................................................................vi
SPECIFICATIONS ....................................................................................... vii
PACKINGLIST .......................................................................................... viii
1.0INSTALLATION.................................................................................... 1-1
1.1UNCRATINGTHEPAPERDRILL ................................................... 1-2
1.2INSTALLINGTHETABLEANDBACKGAUGE ................................ 1-2
1.3INSTALLINGTHEDRILLBLOCKSANDDRILLS ............................ 1-3
1.4HYDRAULIC LEVELCHECK......................................................... 1-3
1.5 HOOKINGUP THEPOWER LINE ................................................. 1-3
1.6INSTALLINGTHECHIPCONTAINER ............................................. 1-3
2.0OPERATION ....................................................................................... 2-1
2.1STARTINGTHEMACHINE ............................................................ 2-1
2.2OPERATINGTHEDRILL ............................................................... 2-1
2.3ADJUSTINGTHEVERTICALSTROKE .......................................... 2-1
2.4SETTINGTHEDISTANCEBETWEENDRILL HEADS .................... 2-1
2.5SETTINGTHEBACKGAUGEPOSITION ....................................... 2-1
2.6USINGTHESIDE GUIDE .............................................................. 2-2
2.7ADJUSTINGTHESTROKE SPEED ............................................... 2-2
2.8REMOVINGTHECUTTING BLOCKS ............................................ 2-2
2.9REMOVINGDRILLS FROMTHESPINDLE.................................... 2-2
2.10DRILLINGTIPS ........................................................................... 2-3
3.0ACCESSORIES .................................................................................. 3-1
3.1GENUINE CHALLENGE HOLLOWDRILLS.................................... 3-1
3.2CHALLENGEDRILL-EASELUBRICANTSTICK ............................. 3-1
3.3CHALLENGEDRILLING BLOCKS ................................................. 3-1
3.4HANDI-SHARPDRILLSHARPENER ............................................. 3-2
3.5HOLLOW DRILLSHARPENER /CHIPREMOVER ........................ 3-2
3.5.1UsingtheChip Remover ....................................................... 3-2
3.5.2Using theDrill Sharpener ..................................................... 3-2
3.6RIGHT-SIDESIDEGUIDEKIT ........................................................ 3-3
3.7AUTO-TRIPBACKGAUGE ............................................................ 3-3
3.7.1 Setting the side guide stops................................................. 3-3
3.8FIXED GAGES ............................................................................. 3-4
3.9TWO-HANDCONTROLKIT ........................................................... 3-5
3.10DRILLSHIELD KIT ...................................................................... 3-6

F.352-KO/EH-3C DRILL/AUG 03
iv
NOTES

v
F.352-KO/EH-3C DRILL/AUG 03
SAFETY PRECAUTIONS
•This machine is designed and safeguarded for ONE PERSON operation. NEVER operate the machine
with more than one person.
•Safety of this machine is the responsibility of the user and operator. Use good judgement and com-
mon sense when working with and around this machine.
•READ and understand all instructions thoroughly before using the machine. If questions still remain,
call your Authorized Challenge Dealer - Failure to understand operating instructions may result in
personal injury.
•Only trained and authorized persons should operate the machine.
•DO NOT ALTER SAFETY GUARDS OR DEVICES, they are for your protection and should not be altered
or removed. Severe lacerations could result.
•DISCONNECT POWER before cleaning, lubricating, servicing, or making adjustments not requiring
power. See Power Lockout Procedure below.
•HIGH SPEED DRILL - Keep rags, loose clothing and long hair away form rotating drill. Personal injury
could result from items being caught on drill.
•ALWAYS WEAR SAFETY GLASSES when operating the drill machine.
•Have your electrician make sure the machine is properly grounded.
•Have your electrician check for sufficient power to operate the machine properly.
•OBSERVEALLCAUTIONPLATESANDLABELSon this machine.
•KEEP FOREIGN OBJECTS off table and away from drill.
•BE EXTREMELY CAREFUL when handling and changing the drills. Severe lacerations or dismember-
ment could result from careless handling procedure.
•KEEP THE FLOOR around the machine free of trim, debris, oil and grease.
•When replacing hydraulic parts, loosen the connections slowly to release pressure. Never loosen
connections with the machine running.
•If the machine sounds or operates abnormally, turn it off and consult the Trouble Shooting section of
this manual. If the problem cannot be corrected, have it checked by a qualified service person or
your Authorized Challenge Dealer.
•CRUSH HAZARD, keep feet off the pedal when handling paper under the clamp. DO NOT REST FOOT
ON PEDAL at any time!
•DO NOT REACH UNDER THE DRILL AND CLAMP AREA!
•DO NOT OPERATE WITH ANY GUARDS REMOVED! Replace all guards after adjusting, lubricating or
servicing the machine.
•SEVERE LACERATIONS - Contact with high speed drill could cause severe injury. Always turn ma-
chine off and wait for drill to stop before removing drill bits. Keep hands away from drill(s) when
operating.
CAUTION: POWER LOCK-OUT PROCEDURE
For maximum safety when making adjustments or
repairs to your machine, be sure to lock out the
main power control switch to which the machine
is connected. The switch should be thrown to the
OFF position and a padlock placed in the loop.
The key should be held by the person servicing
the machine.
(fig. i)
This safety symbol means CAUTION/WARNING - PERSONAL SAFETY INSTRUCTION. Read
the instructions because it has to do with safety. Failure to comply with the following instruc-
tions may result in personal injury.

F.352-KO/EH-3C DRILL/AUG 03
vi
CUT/CRUSHHAZARD
SINGLEOPERATOR
SHOCKHAZARD
SHOCKHAZARD
HAZARDOUSAREA
Keephands fromunder drills.
Donot operatewith morethan oneperson.
Disconnectpowerbeforeremovingcover. Replacecover
beforeoperation.
Disconnectpowerbeforeremovingcover. Replacecover
beforeoperation.
Disconnectpowerbefore cleaning, servicing,ormaking
adjustments not requiring power. Do not alter safety
guards or devices, they are for your protection. Re-
place all guards, do not operate with any guards re-
moved.
WARNING LABEL DEFINITIONS

vii
F.352-KO/EH-3C DRILL/AUG 03
SPECIFICATIONS
Drilling
NumberofDrillHeads 3
DrillBitSizes Available 1/8” to 1/2” (3 mm to 13 mm)
Range Between Drills 23/4” to 41/2” (7 cm to 11 cm)
RangeBetweenOutsideDrills 51/2” to 9” (14 cm to 23 cm)
MaximumDrilling Capacity (PileHeight) 21/2”(63 mm)
BackgaugeAdjustment Range(Std. Backgauge) 0 to 5” (0 to 13 cm)
Auto Trip Backgauge (Optional) 0 to 41/2” (0 to 11cm)
Side guide Adjustment Range 0 to 14” (0 to 37 cm)
VerticalAdjustmentofIndividual Heads 1/4”(6mm)
Dimensions
Table Size 191/2” x 311/2” (50 cm x 80 cm)
Table Height 37” (94 cm)
OverallHeight 591/4”(151cm)
FloorSpaceNeeded 36” x 411/2” (91 cm x 105 cm)
NetWeight (Approximate) 525 lbs (236 kg)
Shipping Weight (Approximate) 570 lbs (257 kg)
Electrical
208/230 Volts, 18 Amps, 1 Phase, 50/60 Hz, AC. Service size 30 Amps.
Challenge reserves the right to make changes to any product or specification without notice and without
incurring responsibility to existing units.

F.352-KO/EH-3C DRILL/AUG 03
viii
PACKING LIST
Part No. Description Qty.
Basic Machine ....................................................................1
5700 Backgauge Assembly .........................................................1
5734 Table Assembly ..................................................................1
A-5874 Chip Bag ............................................................................1
KK-281-2 Knockout, Cutting Block ......................................................3
KK-473-3 Drill Blocks, 3” (1 doz).........................................................1
CD-4-2-1/2 Hollow Drills, 1/4” Diameter.................................................3
CD-5-2-1/2 Hollow Drills, 5/16” Diameter...............................................3
K-85 Drift Hole Cover ..................................................................3
A-4950-2 Hand Drill Sharpener / Chip Remover .................................1
4688 Lubrication Stick .................................................................1
4687 Drill Drift .............................................................................1
W-141 1/8” Allen Wrench ...............................................................1
W-130 3/16” Allen Wrench .............................................................1
W-137 5/32” Allen Wrench .............................................................1
5841 .018” Shim ..........................................................................3
5841-1 .035” Shim ..........................................................................3
DrillBlocks
Drill
Sharpener
DriftHole
Covers
Allen Wrenches
Shims
Lubrication
Stick
Drill Drift
Hollow Drills

1-1
F.352-KO/EH-3C DRILL/AUG 03
1.0 INSTALLATION & SETUP
(fig. 1-1)
1.0 INSTALLATION
Refer to figure 1-1 on this page as well as the parts
lists and drawings in the back of this manual for part
identification and orientation, if necessary.
All guards and instruction plates are installed for your
safety and information and must remain on the ma-
chine as shipped from the factory.

F.352-KO/EH-3C DRILL/AUG 03
1-2
1.0 INSTALLATION & SETUP
UsingAuto-TripBackgauge:
Attach the backgauge assembly to the table and set
bothsides to the6” position (asshownin fig.1-5).Next,
position the table so that the front surface of the back-
gauge is 1-7/8” from the front of each pull down shaft
(seefig.1-5). Now tightenthefront twotable-mounting
screws. Thenmovethebackgauge forward andtighten
the rear two screws.
1.1 UNCRATING THE PAPER DRILL
This machine is shipped on a wooden skid and is en-
closed with a protective corrugated cover. It is held
onto the skid with plastic straps. Remove the straps
and carefully cut the corrugated cover down the side
andunwrapitfromaroundthemachine. Thetable,back-
gauge, and other accessories are packed in separate
boxesand are securedto themachine. Remove these
and carefully position the machine on the floor. Imme-
diatelyafteruncrating, checkoffparts received against
the packing list. Also, examine for any physical signs
of damage incurred during shipping. The machine is
inspectedbefore andafter itis cratedat ourplant. The
responsibility for filing a claim against the carrier for
damages incurred during shipment rests with the re-
ceiverof goods(FOBour factory).
Cleanall partswith acommercial cleaningsolvent be-
fore installing or using the machine.
1.2 INSTALLING THE TABLE AND
BACKGAUGE
Locate the four (4) table mounting bolts, washers, &
nuts shipped in the table drawer. Set the table assem-
blyin placeandattach usingthe hardwareasshown in
figure1-2, butleavethe hardware loose.
Using Standard Backgauge:
Attach the backgauge assembly to the table and set
both sides to the 6-7/8” position (as shown in fig. 1-3).
Next, position the table so that the back surface of the
backgaugecomes incontact withthe frontof eachpull
down shaft (fig. 1-4). Now tighten the front two table-
mounting screws. Then move the backgauge forward
and tighten the rear two screws.
(fig. 1-4)
Pull Down
Shaft
(fig. 1-2)
(fig. 1-5)
Ruler set
to 1-7/8”
Pull Down
Shaft
Backgauge
set to 6”
(fig. 1-3)
Set to 6-7/8”

1-3
F.352-KO/EH-3C DRILL/AUG 03
1.0 INSTALLATION & SETUP
Note: Furtheradjustments may benecessary once the
machine is ready to drill. See Table Position Adjust-
ment (section 4.3.1).
1.3 INSTALLING THE DRILL BLOCKS
AND DRILLS
Placethe drill block knock-outs inposition (refertofig.
1-1 if necessary). Now set the three drill blocks place.
Checktoseeif theblocksareflushwiththe table.Place
shims under the blocks if necessary.
Insert the tapered head of the hollow drills into the
spindles. Besure thatthe drift hole covers are in place
before operating the machine (fig 1-1). The drift hole
coversprevent paper chipsfrom flying outwhiledrilling.
1.4 HYDRAULIC LEVEL CHECK
Checkthelevelof theoilinthehydraulicreservoir. This
check is made by first removing the louvered panel at
the left side of the stand (two screws hold it in place)
andlocatingthebreathercaponthetopofthe reservoir.
The breather cap has a dip stick attached for checking
the oil. When screwed in (and then removed to check)
there should be approximately an 1/8” (3 mm) of oil on
the stick. Some machines are equipped with a clear
reservoir in which case the oil level can be checked by
visuallyinspectingthe oillevel. Thereisa full levelline
markedon the reservoir. Recommendedoils are found
in the maintenance section of this manual (section
4.5.1).
1.5 HOOKING UP THE POWER LINE
The EH-3C is factory wired for 208/230 Volt, 1 phase,
50/60 hz. operation. It is the customer’s responsibility
to wire the machine for the rated voltage using a 30
Ampcircuit(minimum). Therecommendedcircuitover-
loadprotectiondeviceshouldbe20Amps.Therecom-
mended wire size for this hookup is #10 gauge.
CAUTION: Always disconnect the
power when cleaning, servicing, or
lubricatingyour drill, see LockOut Pro-
cedures, page v.
CAUTION: Always handle drills with
care to avoid severe lacerations. Even
dull drills are sharp enough to cause
lacerations.
(fig. 1-6)
(fig. 1-7)
IMPORTANT: Select the proper transformer primary
tap 208 or 230 Volts to match the voltage supplied
to the machine (fig. 1-6).
Itisalso importantthattheproper linevoltagebemain-
tained. Failureto do sowill result inimproperoperation
of the machine (see the troubleshooting section of this
manualfor specific problems). Itmay benecessary to
providea separatebranch powerline forthe machine.
Since the standard machine is intended for a single
phase hookup, simply fasten either wire of the power
cordto eitherterminalof thestarter andtheground wire
tothe designated terminal(fig. 1-7).
1.6 INSTALLING THE CHIP CONTAINER
Thechipcontaineris installedbyslippingitover thetwo
hooksprovided onthe rearof themachine.

F.352-KO/EH-3C DRILL/AUG 03
1-4
1.0 INSTALLATION & SETUP
NOTES

2-1
F.352-KO/EH-3C DRILL/AUG 03
2.0 OPERATION
2.0 OPERATION
2.1 STARTING THE MACHINE
The power for this machine is supplied by two motors;
one is for the hydraulic power pack, the other is for the
spindle. They are both started and stopped simulta-
neously by a single set of start-stop buttons located on
the stand under the table (fig. 1-1). Be sure both mo-
tors are operating before trying to drill paper.
2.2 OPERATING THE DRILL
Pressingdown onthe foot switchactivates thehydraulic
unit which brings the drill heads (and drills) down to
the table. When the drills reach the bottom of their
stroke, they will automatically return the “up” position.
(Note: The vertical stroke of the drills must be set be-
fore drilling to provide the proper drill depth. See sec-
tion 2.3 for adjustment procedures). The pedal must
be released and depressed again before drilling the
next set of holes, assuring full control and allowing no
repeat stroke. By releasing the pedal, the operator
can stop the drills in their downward stroke at any time
allowing them to return to their normal position, thus
preventing costly errors. NEVER REST YOUR FOOT
ON THE TREADLE WITHOUT INTENDING TO
BRING DOWN THE DRILLS!
2.3 ADJUSTING THE VERTICAL STROKE
Theverticalstrokeofthemachinedeterminesthe exact
depth the drills will reach at the bottom of their stroke.
Wheneverinstallinganewsetofdrills,theverticalstroke
mustbe adjustedbefore drilling.
The two outside heads are provided with independent
heightadjustmentwhile thecenterheadworks fromthe
center overall adjusting screw. This is necessary be-
cause of the variance in length of the drills. Start by
adjusting the center head to its highest point. This is
accomplished by turning the drill depth adjustment
screw (fig. 1-1) counterclockwise until it stops turning.
Then adjust the side heads all the way up by turning
the knurled ring on the heads clockwise (use the pro-
vided drill drift in the holes if necessary). Now, with
the new drills in the place, put two or three sheets of
paperunder theheads. The centerspindleshould then
be adjusted so that the center drill just cuts through
the paper. Too deep will cause a ragged hole in the
bottomsheets as wellas ashorter drill life from drilling
intothe cutting block. Afterthe centerdrill is adjusted,
each outside spindle can be adjusted. Turn counter-
clockwise to lower and clockwise to raise. No locking
isnecessary. Once all threedrills areset, drill through
a full lift of paper. A final adjustment of the drill depth
adjusting screw may be necessary to obtain the best
results.
2.4 SETTING THE DISTANCE BETWEEN
DRILL HEADS
This machine incorporates three drilling heads operat-
ing on three belt-driven spindles. The center head is
stationary while the two outside heads have a lateral
adjustment of 13/4” each.
This provides an adjustment range of 23/4” to 41/2” (7
cm to 11 cm) between the center drill and either of the
outsidedrills, or a range of 51/2” to9” (14cm to23 cm)
between the two outside drills.
The lateral adjustment is accomplished by loosening
the clamp knob (a black, plastic hand knob) located at
the rear of each outside head, and then turning the 4-
lobed, black knob located at the outside of each head.
Thismovestheheadsalongashaft.Ascaleand pointer
located at the front of the heads gives a reading in
inchesand millimeters ofthe centerline relationshipto
the center head. When a setting is made, make cer-
tain that the clamp knob is tightened again.
Any combination of three heads can be used, that is
one, two, or three holes may be drilled if desired. It is
recommended,howeverthatno more thantwohalfinch
hollow drills be used at the same time.
2.5 SETTING THE BACKGAUGE
POSITION
The backgauge position is adjusted by first loosening
the two thumb screws under the table. This will allow
thebackgauge tomovefreely. Then usethe twoscales
on the top of the table to set the backgauge to the de-
sired position. The scales read in inches and millime-
ters and will give the distance from the edge of the
sheet to the center of the holes. Be sure the 1” (2.5
cm) square pieces mounted to the backgauge are
alignedon topof thescales toprovide the proper read-
ing (fig. 1-1). Tightenthe thumbscrewswhen finished.
CAUTION: Always wear safety glasses
when operating this machine.

F.352-KO/EH-3C DRILL/AUG 03
2-2
2.0 OPERATION
2.6 USING THE SIDE GUIDE
To adjust the position of the side guide, loosen the two
black knobs until the side guide is free to slide side-
ways. Slide the side guide to the desired position and
thentighten the twoknobs. For certainhole positions,
it may be necessary to remove the rectangular spacer
from the side guide assembly (fig. 2-1).
2.7 ADJUSTING THE STROKE SPEED
Thehydraulic unitis equippedwith anadjustable valve
forregulating the speedon thedrill stroke (up and down
travel). Soft stocks such as mimeographs, etc., are
aptto wrinkle athigh speeds,and the speed should be
set to a point where the best results are obtained.
Thisadjustmentis madebyturningthe adjustablevalve
(located on the right side of the drilling machine stand)
counterclockwise to reduce speed and clockwise to
increase speed (fig. 2-2)
(fig. 2-1)
(fig. 2-2)
2.8 REMOVING THE CUTTING BLOCKS
Each cutting block is removed by inserting your fin-
gers in the hole provided in the frame (under the table)
and pushing up on the cutting stick knock out. There
arethree holes;one on eachside ofthe frame andone
in the front.
2.9 REMOVING DRILLS FROM THE
SPINDLE
Remove the drift hole cover from the spindle to ex-
pose the drift hole. Then, with the flat side down, in-
sert the drill drift into the hole and lift upward. The
upward movement forces the drill down and releases
it from the spindle.

2-3
F.352-KO/EH-3C DRILL/AUG 03
2.0 OPERATION
2.10 DRILLING TIPS
Important! To prevent the drill from overheating, always avoid drilling too slowly. The drill stroke speed should
be set at the fastest speed possible that still allows the drills to cut easily through the paper.
Slotted Holes - Instead of punching slotted holes for five and seven hole universal binding work, save time and
cost by drilling a 1/2” (1.3 cm) diameter hole in place of the slot. The slot is only intended to allow the post or ring
to be used in either location, and the large hole permits this.
Plastic Bindings - Drilling holes for plastic bindings, instead of punching them, is practical and saves a great deal
oftime, particularly on long run jobs.
Keep Drills Sharp - A dull drill is the major cause of drill breakage and production tie-ups. Usually after three
hoursof drilling,depending onthe typeofpaper beingprocessed, thedrill shouldbe sharpened. Adulldrill results
in poor quality work.
Keep Drills Clean - A dirty and rusty drill will not permit the free upward passage of the drill chips. Pressure built
upby aclogged drillwillsplit orbreak thedrill. To keepit free from dirt orrust, cleanthe drillof allchips aftereach
use and apply a light oil to the inside and outside. Drills should be cleaned out immediately after each use. This
isparticularly trueif acoated orvarnished stock hasbeen drilled. Onthese jobsthe coatingon thechips frequently
fuse the chips into one solid mass when the drill cools, causing breakage the next time the drill is used.
Lubricate Drills - Lubrication assists in the passage of the chips and helps avoid overheating of the drills. Use
readilyavailable stick lubricants for thispurpose. Hold theend ofthe stick against the sideof therotating drill. Be
sure to touch the cutting edge with the lubricant also. Wipe off excess oil before drilling. CARE MUST ALWAYS
BETAKENWHENHANDLINGDRILLS.
Keep Spindle Clean -Clean outthe drillspindle frequently. Thiswill preventany buildupin thespindle ofthe drill.
Set the Drills Correctly - Do not cut too deeply into the cutting block. The drill should just touch the block and
cleanly cut through the bottom sheet. During drilling, do not set the drill deeper into the block but change the
position of the block frequently. Drilling deeper into the block dulls the drills quickly. Use a piece of chipboard
underneath your stock. This will make handling the stock easier and will ensure that the last sheet is cut cleanly
through.
Check for Drill Wobble-Ifspindles arebadlyworn orbent through misadjustment,have themreplacedimmedi-
ately. A wobbly or loosely held drill can break.
Check Your Drill Sharpener - The cutting edge of the sharpening bit should be inspected frequently to make
certain that it is sharp and free of nicks. Never let a drill drop onto the sharpening bit. It will chip the sharpening
edge. Use gentle pressure when sharpening - let the sharpening bit do the work. Carefully check the sharpness
of the drill after sharpening. The cutting edge should be razor sharp.
Check Belt on the Drilling Machine -Thebelt shouldbe kepttight toassure properspeed ofthe drill. Whenthe
drill slows down, it acts more like a punch which results in poor quality work and drill breakage.
Justalittle timeandeffort takenwitheach use ofyourpaper drillingmachineshould result introublefree operation
overmany years.

F.352-KO/EH-3C DRILL/AUG 03
2-4
2.0 OPERATION
NOTES

3-1
F.352-KO/EH-3C DRILL/AUG 03
3.0 ACCESSORIES
1/8”3/16”1/4”9/32”11/32”13/32”1/2”
5/32”7/32”17/64”5/16”3/8”7/16”
3.1 GENUINE CHALLENGE HOLLOW DRILLS
In 13 Standard Sizes For Every Drilling Need
Alldrills carriedin stockby localChallenge dealers(17/32” &9/16” available by special order).
3.2 CHALLENGE DRILL-EASE
LUBRICANT STICK
Cat. No. 4688
This lubricating stick provides a dry stainless lubricant
which has many uses throughout the printing plant. It
is specially recommended for use on hollow drills for
easierdrilling,particularlywhendrillingclaycoatedstock.
Iteliminates bindingand excessive heatingof thedrill.
Will not discolor the stock.
CAREMUSTALWAYS BE TAKEN WHEN USING
STICKAND HANDLING DRILLS.
3.3 CHALLENGE DRILLING BLOCKS
Cat. No. KK-473-3
These Challenge 3” End-Wood Drilling Blocks are for
roundhole drillingoperations. Sold inpackages of12.
HOLLOW DRILLS
Diameter x Drill Capacity Cat. No.
1/8” x5/8” (3.2 x 16 mm).................... CD-2-3
5/32” x 11/8” (4 x 29 mm).................... CD-52
3/16” x 15/8“ (4.8 x 41 mm) ................. CD-3
7/32” x 2” (5.6 x 51 mm) .................... CD-72
1/4” x 2” (6.3 x 51 mm) ..................... CD-4
1/4” x 21/2” (6.3 x 63.5 mm) ............... CD-4-21/2
17/64” x 2” (6.7 x 51 mm) ................... CD-174
9/32” x 2” (7.1 x 51 mm) .................... CD-92
5/16” x 2” (7.9 x 51 mm) .................... CD-5
5/16” x 21/2” (7.9 x 63.5 mm) .............. CD-5-21/2
11/32” x 2” (8.7 x 51 mm) ................... CD-112
3/8” x 2” (9.5 x 51 mm) ..................... CD-6
3/8” x 21/2” (9.5 x 63.5 mm) ............... CD-6-21/2
13/32” x 2” (10.3 x 51 mm) ................. CD-132
7/16” x 2” (11.1 x 51 mm) .................. CD-7
1/2” x 2” (12.7 x 51 mm) ................... CD-8
1/2” x 21/2” (12.7 x 63.5 mm) ............. CD-8-21/2
Specialorder drills
17/32” x 2” (13.5 x 51 mm) ................. CD-172
9/16” x 2” (14.3 x 51 mm) .................. CD-9
TEFLONCOATEDHOLLOWDRILLS
Diameter x Drill Capacity Cat. No.
1/8” x5/8” (3.2 x 16 mm).................... TCD-2-3
5/32” x 11/8” (4 x 29 mm).................... TCD-52
3/16” x 15/8“ (4.8 x 41 mm) ................. TCD-3
7/32” x 2” (5.6 x 51 mm) .................... TCD-72
1/4” x 2” (6.3 x 51 mm) ..................... TCD-4
1/4” x 21/2” (6.3 x 63.5 mm) ............... TCD-4-21/2
17/64” x 2” (6.7 x 51 mm) ................... TCD-174
9/32” x 2” (7.1 x 51 mm) .................... TCD-92
5/16” x 2” (7.9 x 51 mm) .................... TCD-5
5/16” x 21/2” (7.9 x 63.5 mm) .............. TCD-5-21/2
11/32” x 2” (8.7 x 51 mm) ................... TCD-112
3/8” x 2” (9.5 x 51 mm) ..................... TCD-6
3/8” x 21/2” (9.5 x 63.5 mm) ............... TCD-6-21/2
13/32” x 2” (10.3 x 51 mm) ................. TCD-132
7/16” x 2” (11.1 x 51 mm) .................. TCD-7
1/2” x 2” (12.7 x 51 mm) ................... TCD-8
1/2” x 21/2” (12.7 x 63.5 mm) ............. TCD-8-21/2
3.0ACCESSORIES

F.352-KO/EH-3C DRILL/AUG 03
3-2
3.0 ACCESSORIES
3.4 HANDI-SHARP DRILL SHARPENER
Cat. No. 57100
TheHandi-Sharpmountsontheedgeoftableor bench.
A dull hollow drill bit is placed in the holder, and the
cutting bit is pushed against the end of the hollow drill
untilitsspring bottomsout. Thespring preventsexces-
siveforcefrombeingappliedwhilesharpening. Turning
thehandle whileapplying ahoneproduces afine edge.
Item Cat. No.
Replacement Cutting Bit 6469
Adapter for other style drill bits 57114
3.5 HOLLOW DRILL SHARPENER / CHIP REMOVER
For fast, easy drill sharpening and chip removal
CAUTION: Drills are sharp even after use. Be careful to keep edge
away from your body. To prevent personal injury and/or damage to
the drill, ALWAYS keep drills in protected area.
3.5.1 Using the Chip Remover
1. CAREFULLYplace ahollow drillin theholder sec-
tion as shown, and insert the holder (with drill) into
the chip remover end as shown.
(cut-away view)
(cut-away view)
NOTE: Chip remover is only for use with hollow drill diameters 3/
16” and larger
2. Firmly tap the entire assembly on a solid surface
to remove the chips from the hollow drill.
3.5.2 Using the Drill Sharpener
1. CAREFULLYplace ahollow drillin theholder sec-
tion as shown, and insert the holder (with drill) into
the sharpener end as shown. Be very careful to
bring the drill and cutting tool together with out
bumping. The cutting tool is made of GLASS
HARD material and may be chipped.
2. USECLOCKWISE ROTATIONwhile maintaining
an even pressure, until the hollow drill is sharp-
ened (usually two or three turns). The cutting tool
seldom requires replacing, but when it does be-
come necessary, the bit can be ordered through
your Challenge Dealer (Cat. No. 4952).

3-3
F.352-KO/EH-3C DRILL/AUG 03
3.0 ACCESSORIES
Thisoptional backgaugeassemblyprovides additional
versatilityto theEH-3C. The automatictrip ontheside
guide permits step and repeat type of operation with a
minimum distance between holes of3/8” (9.5mm) with
the standard stops or 1/4” (6.3 mm) minimum by the
use of a fixed gage, available as optional equipment.
As each set of holes is drilled, the side guide is auto-
matically tripped, and as soon as the drills clear the
stock on their up stroke, the guide is free to move to its
next stop. This is accomplished by pushing the stock
totheleftandmovingtheguideatthesametime. When
drilling one, two or three holes only, that fall within the
9” (23 cm) limitations of the machine, the automatic
trip bracket (located at the left of the machine) can be
turned so that it does not engage the trip lever.
3.7.1 Setting the side guide stops
First set the rear gage to the desired back margin. Be
sure both sides are set to the same dimension and
tighten the two thumbscrews. Next, remove the guide
shaft and set the guide stops to the desired distance
betweenholes (ascalein theguide shaftisprovided for
this purpose). The guide shaft is then replace in the
rear gage and final adjusting or centering of holes is
accomplished with the knurled screw at the extreme
leftend ofthe guideshaft.
The automatic trip gage comes equipped with seven
stops. Additional stops can be purchased at a very
nominalprice. Challengefixed indexgagesarerecom-
mendedwhere the samejob isto be handled over and
over again. They are easily and quickly attached and
removed. NOTE: Whendrilling narrow strips,the side
guideroller assemblyshould bemounted onthe inside
of the side guide assembly.
3.6 RIGHT-SIDE SIDEGUIDE KIT
Cat. No. K-5731
This kit includes all of the parts and hardware neces-
sary to add a right-hand sideguide to your existing
backguage. When used in conjunction with the left-
handsideguide,multiple holepatternscanbe drilledby
shifting the stock from one sideguide to the other be-
tween drilling cycles.
3.7 AUTO-TRIP BACKGAUGE
Cat. No. A-4615-9

F.352-KO/EH-3C DRILL/AUG 03
3-4
3.0 ACCESSORIES
3.8 FIXED GAGES
For Fast, Accurate Hole Spacing
(For use with optional auto-trip backgauge only)
Thesefixed gages withpre-cut holespacings fiton the
side guide in place of the moveable stops. To use,
positionthe gageso that the right end lines upwith the
dimension on the scale for the centerline of the first
hole to be drilled. Use of the stops on fixed gages is
the same as using the adjustable stops.
In addition to 2-5 hole patterns, fixed gages are avail-
able from stock in the following standard types:
22-stopgage, 1/2”centers formulti-ringbinders
25-stopgage, 3/8”centers
25-stopgage, 1/4”centers
34-stopgage, 1/2”centers
46-stopgage, 3/8”centers
50-stopgage, 1/4”centers
Custom patterns can also be supplied, call for details.
Other manuals for EH-3C
1
Table of contents
Other Challenge Drill manuals
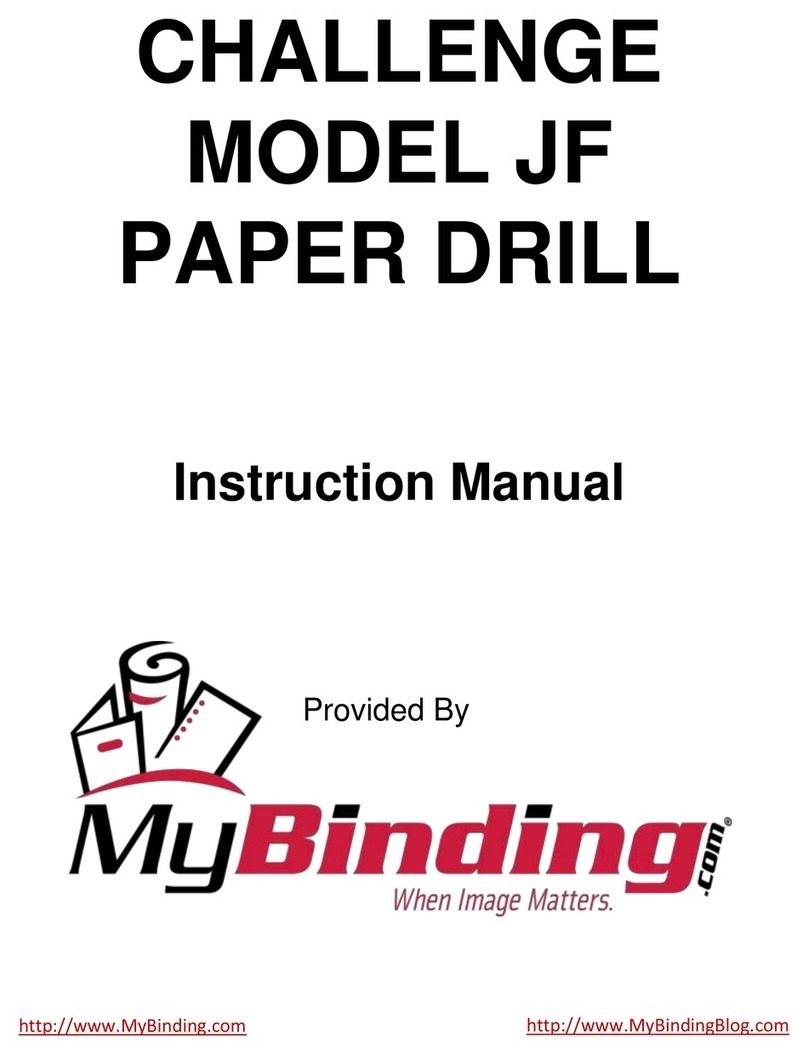
Challenge
Challenge JF User manual
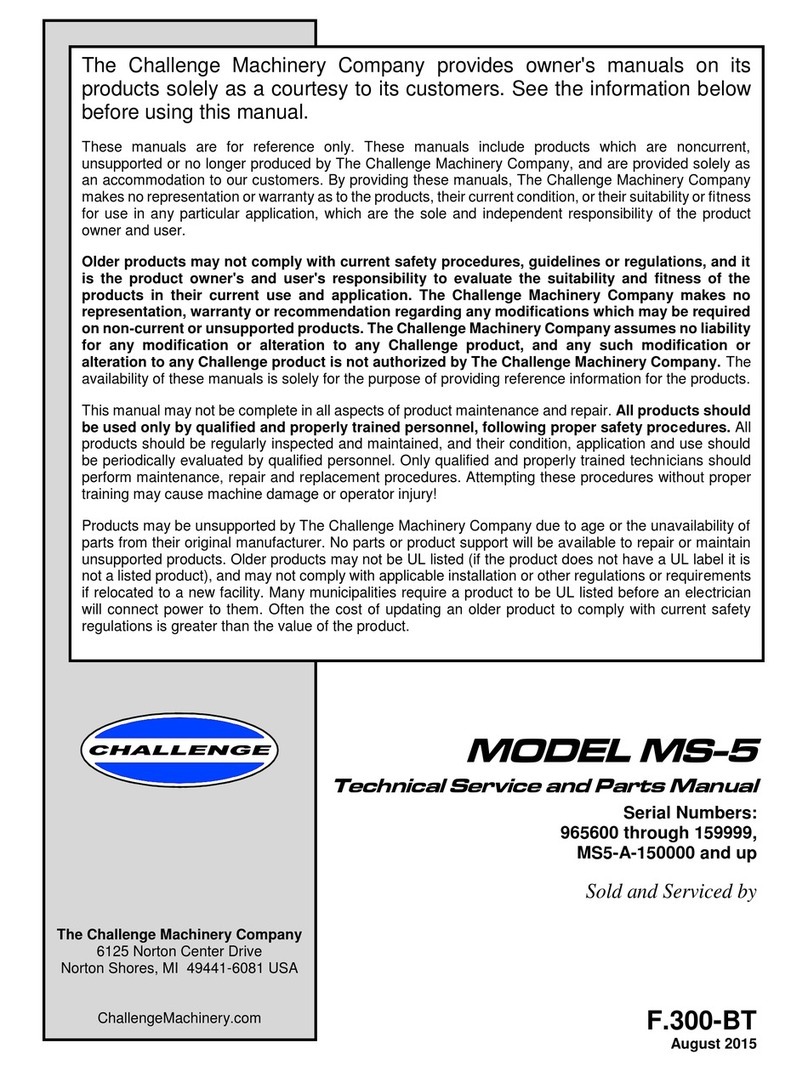
Challenge
Challenge MS-5 Guide

Challenge
Challenge Handy-Drill Technical reference manual
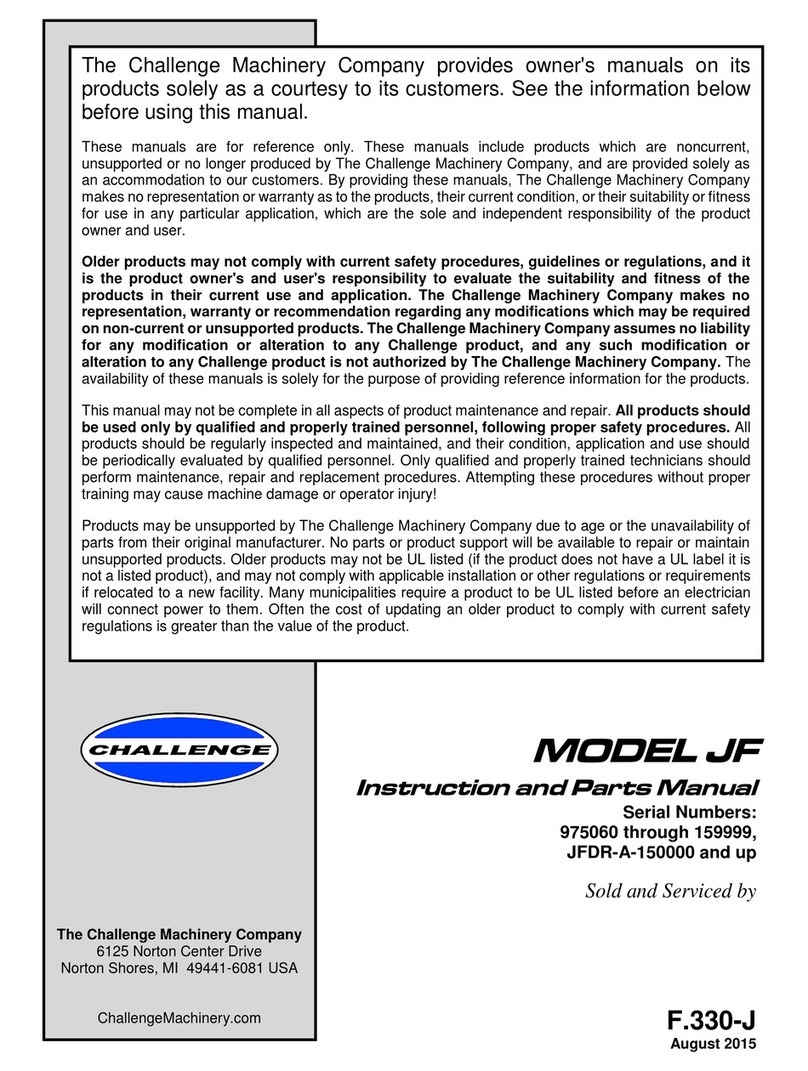
Challenge
Challenge JF Technical reference manual
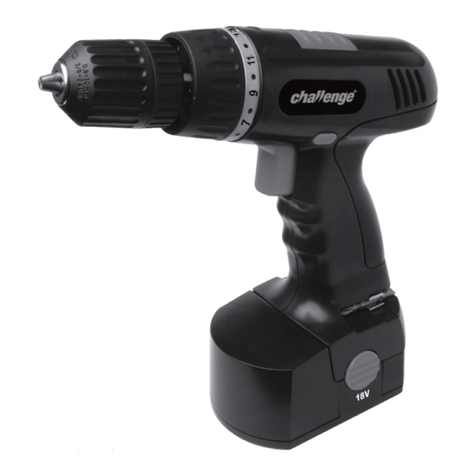
Challenge
Challenge CDT16180 User manual
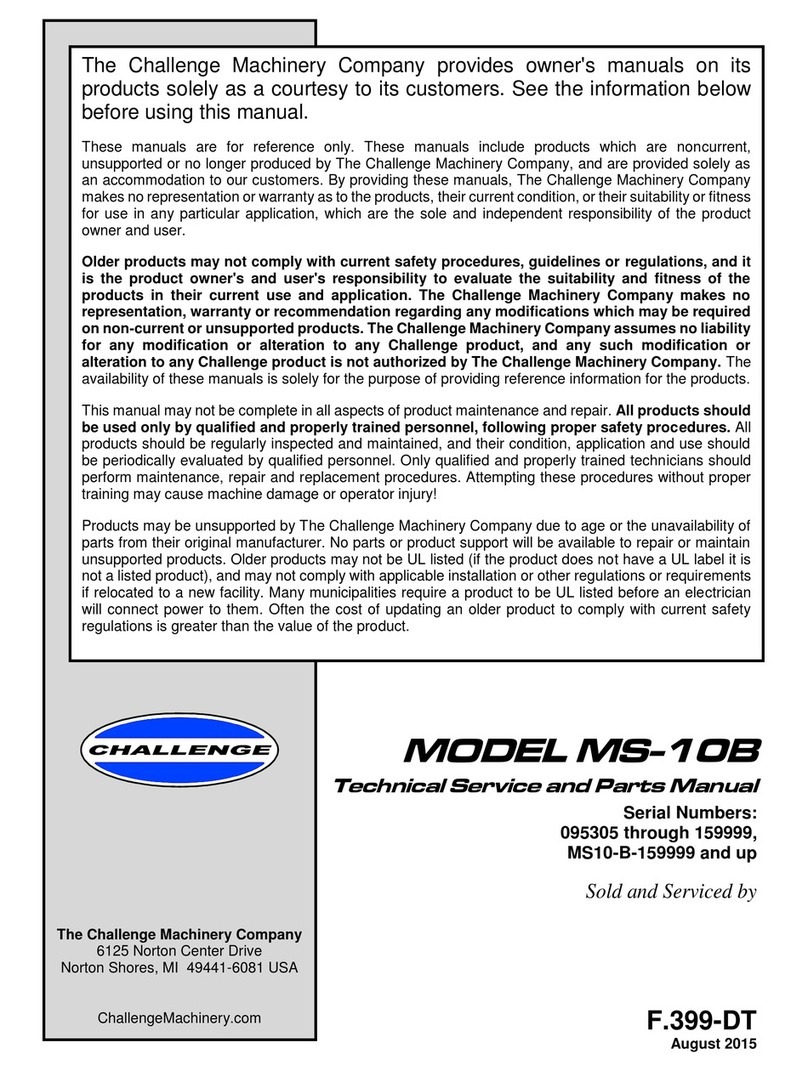
Challenge
Challenge MS-10B Guide
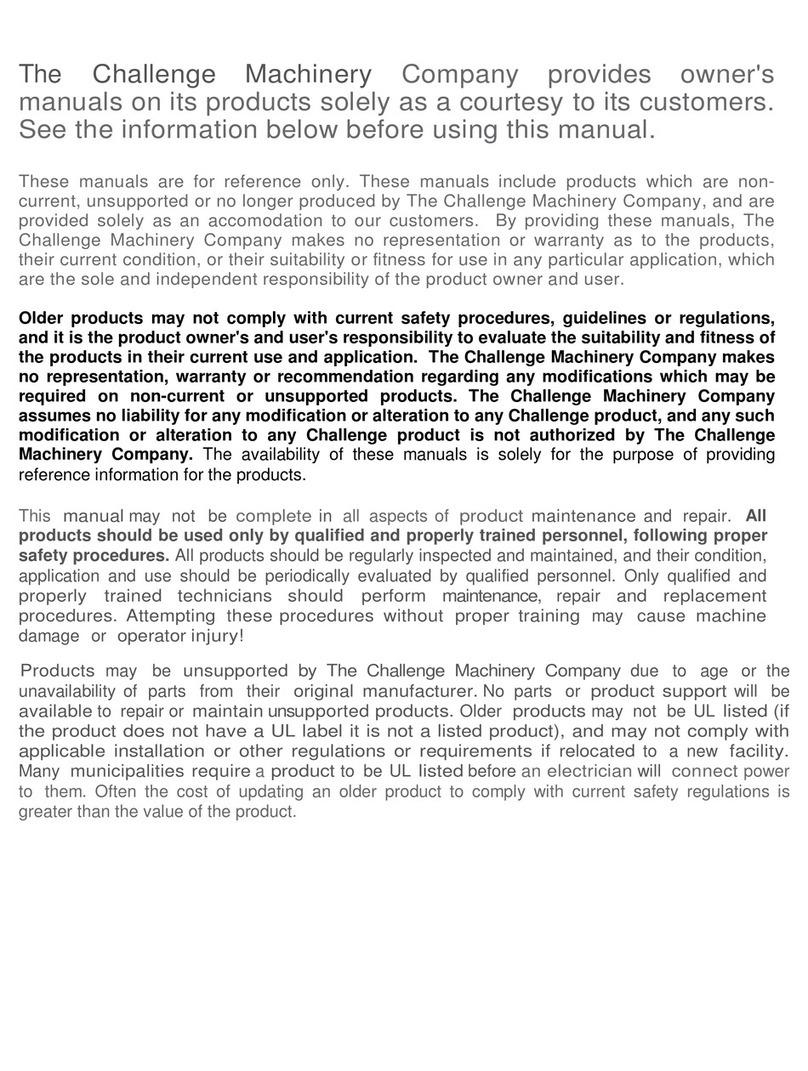
Challenge
Challenge EH-3C User manual
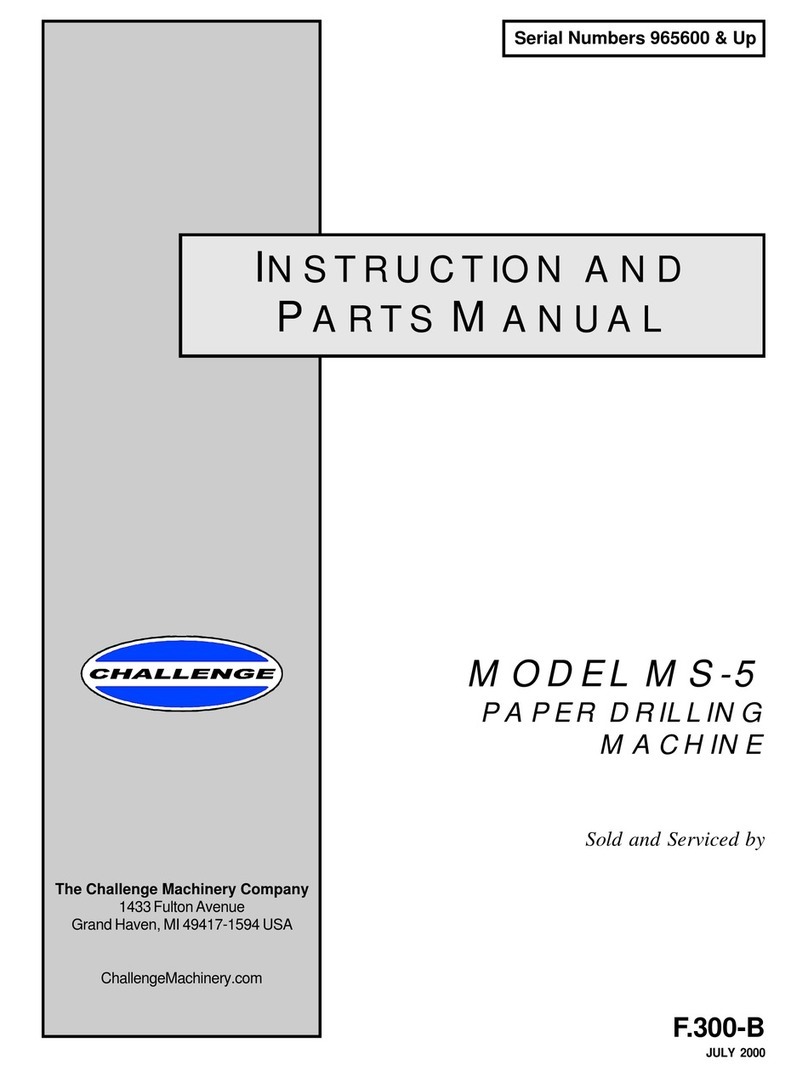
Challenge
Challenge MS-5 Technical reference manual
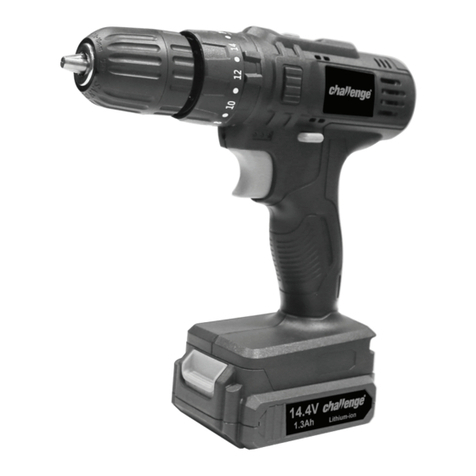
Challenge
Challenge SS20CHAMD User guide
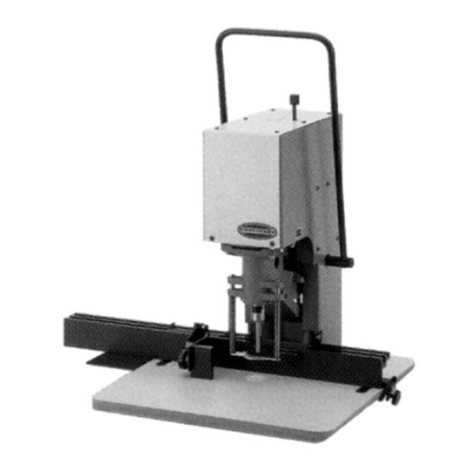
Challenge
Challenge JO Technical reference manual