Challenge DOCUTRIM Technical reference manual

The
Challenge Machinery Company provides owner's
manuals on its products solely as a courtesy to its customers.
See the information below before using this manual.
These manuals are for reference only. These manuals include products which are non-
current, unsupported or no longer produced by The Challenge Machinery Company, and are
provided solely as an accomodation to our customers. By providing these manuals, The
Challenge Machinery Company makes no representation or warranty as to the products,
their current condition, or their suitability or fitness for use in any particular application, which
are the sole and independent responsibility of the product owner and user.
Older products may not comply with current safety procedures, guidelines or regulations,
and it is the product owner's and user's responsibility to evaluate the suitability and fitness of
the products in their current use and application. The Challenge Machinery Company makes
no representation, warranty or recommendation regarding any modifications which may be
required on non-current or unsupported products. The Challenge Machinery Company
assumes no liability for any modification or alteration to any Challenge product, and any such
modification or alteration to any Challenge product is not authorized by The Challenge
Machinery Company. The availability of these manuals is solely for the purpose of providing
reference information for the products.
This
manual
may not be
complete
in all aspects of
product
maintenance
and
repair.
All
products should be used only by qualified and properly trained personnel, following proper
safety procedures. All products should be regularly inspected and maintained, and their condition,
application and use should be periodically evaluated by qualified personnel. Only qualified and
properly trained technicians should perform maintenance,
repair
and replacement
procedures. Attempting
t
hese procedures without proper training
may
cause
machine
damage or
operator
injury!
Products
may be
unsupported by The Challenge Machinery Company
due to age or the
unavailability
of parts from their
original manufacturer.
No parts or
product support
will be
available
to repair or
maintain unsupported
products.
Older
products
may not be UL
listed (if
the product does not have a UL label it is not a listed product), and may not comply with
applicable installation or other regulations or requirements if
relocated
to a new
facility.
Many
municipalities require
a
product
to be UL
listed
before
an
electrician
will
connect
power
to them. Often the cost of updating an older product to comply with current safety regulations is
greater than the value of the product.

The
Challenge Machinery Company provides owner's
manuals on its products solely as a courtesy to its customers.
See the information below before using this manual.
These manuals are for reference only. These manuals include products which are non-
current, unsupported or no longer produced by The Challenge Machinery Company, and are
provided solely as an accomodation to our customers. By providing these manuals, The
Challenge Machinery Company makes no representation or warranty as to the products,
their current condition, or their suitability or fitness for use in any particular application, which
are the sole and independent responsibility of the product owner and user.
Older products may not comply with current safety procedures, guidelines or regulations,
and it is the product owner's and user's responsibility to evaluate the suitability and fitness of
the products in their current use and application. The Challenge Machinery Company makes
no representation, warranty or recommendation regarding any modifications which may be
required on non-current or unsupported products. The Challenge Machinery Company
assumes no liability for any modification or alteration to any Challenge product, and any such
modification or alteration to any Challenge product is not authorized by The Challenge
Machinery Company. The availability of these manuals is solely for the purpose of providing
reference information for the products.
This
manual
may not be
complete
in all aspects of
product
maintenance
and
repair.
All
products should be used only by qualified and properly trained personnel, following proper
safety procedures. All products should be regularly inspected and maintained, and their condition,
application and use should be periodically evaluated by qualified personnel. Only qualified and
properly trained technicians should perform maintenance,
repair
and replacement
procedures. Attempting
t
hese procedures without proper training
may
cause
machine
damage or
operator
injury!
Products
may be
unsupported by The Challenge Machinery Company
due to age or the
unavailability
of parts from their
original manufacturer.
No parts or
product support
will be
available
to repair or
maintain unsupported
products.
Older
products
may not be UL
listed (if
the product does not have a UL label it is not a listed product), and may not comply with
applicable installation or other regulations or requirements if
relocated
to a new
facility.
Many
municipalities require
a
product
to be UL
listed
before
an
electrician
will
connect
power
to them. Often the cost of updating an older product to comply with current safety regulations is
greater than the value of the product.
NOTICE: UNSUPPORTED PRODUCT!
NO TECHNICAL SUPPORT AVAILABLE!
NO REPAIR PARTS AVAILABLE!

Instruction and
Parts Manual
This safety alert symbol means CAUTION OR WARNING-PERSONAL SAFETY INSTRUC-
TION. Personal injury may result if safety precautions are not carefully read before attempt-
ing to operate or repair this machine. See SAFETY PRECAUTIONS, page vii.
•This machine is designed for ONE PERSON OPERATION ONLY!
•Always DISCONNECT THE POWER before working on this machine.
•DO NOT OPERATE WITH ANY GUARDS REMOVED! Replace all guards before operating.
•NEVER BYPASS SAFETY DEVICES OR INTERLOCKS!
•PINCH POINT - Keep hands from under transport clamp.
SAFETY ALERT
SERIAL NO-
MODEL-
DD
DD
DOCUOCU
OCUOCU
OCUTT
TT
TRIMRIM
RIMRIM
RIMTMTM
TMTM
TM
DOCUMENTDOCUMENT
DOCUMENTDOCUMENT
DOCUMENT
TRIMMERTRIMMER
TRIMMERTRIMMER
TRIMMER
Patent No. 5,694,823
This manual covers serial numbers 9712329E & up.
ALWAYS GIVE THE SERIAL NUMBER OF YOUR MACHINE WHEN WRITING.
Sold and serviced by
THE CHALLENGE MACHINERY COMPANY
1433 Fulton Avenue/Grand Haven, Michigan 49417-1594 U.S.A.
ChallengeMachinery.com F.400-E
NOTICE: UNSUPPORTED PRODUCT!
NO TECHNICAL SUPPORT AVAILABLE!
NO REPAIR PARTS AVAILABLE!

F.400-E/NOV 97
ii
INTRODUCTION
WELCOMEto the family of Challenge® users. Challenge has been developing and manufacturing Graphics Arts
Equipment for over 100 years and is today one of the world’s leading producers and distributors of Paper Cutters,
Paper Drills and Bindery Equipment.
THE CHALLENGE REPUTATIONis important to you as a user for the continuous, ready availability of parts and
service.
THIS MANUAL is designed to help you get the most from your Challenge equipment. Keep this manual in a safe,
convenient place for quick reference by operators and service personnel.
SAFETY ALERT! This symbol meansCAUTION OR WARNING: Personal safety instructions! Pay
special attention to the instructions in bold type. Personal injury may result if the precautions are not
read and followed.
READ THIS MANUAL BEFORE OPERATING! Follow precautions and instructions given and you should have
years of trouble-free operation. If after reading the manual questions still remain, contact your Authorized Chal-
lenge Dealer.
FOR PARTS AND SERVICE contact the Authorized Challenge Dealer from whom you purchased your machine.
Use the illustrations and parts lists at the back of this manual to identify the correct parts needed. Always give
the SERIAL NUMBER and MODEL of your machine to insure that the correct parts are sent as soon as pos-
sible.
Take a few minutes right now to RECORD YOUR MACHINE SERIAL NUMBER in the space provided on the
front cover of this manual. Also be sure to fill out the warranty card accompanying this manual and return it
DIRECT TO CHALLENGE.
If you bought a used machine, it is important to have the following information on record at Challenge. Copy this
page, fill in the information and send it care of: The Challenge Service Department, 1433 Fulton Avenue, Grand
Haven, MI 49417-1594.
CHALLENGE MODEL SERIAL NUMBER
ATTN COMPANY
ADDRESS
CITY STATE ZIP
PHONE DATE INSTALLED
DEALER’S NAME AND CITY
PLEASE REVIEW THE ENCLOSED WARRANTY SHEET!
It is very important that you read and understand the conditions outlined in the Warranty Information Sheet. It is
in an envelope attached to the outside of the shipping container.
The Warranty Information Sheet must be filled out completely, returned, and be ON-FILE at THE CHALLENGE
MACHINERY COMPANY in order for the warranty to be issued for this machine.
WARRANTY INFORMATION
Challenge® is a registered trademark of The Challenge Machinery Company. 1433 Fulton Street, Grand Haven, MI 49417.
Copyright © 1997 by The Challenge Machinery Company. All rights reserved. Printed in the U.S.A.
NOTICE: UNSUPPORTED PRODUCT!
NO TECHNICAL SUPPORT AVAILABLE!
NO REPAIR PARTS AVAILABLE!

iii
F.400-E/NOV 97
PACKING LIST
STANDARD ITEMS
Qty. Part Description Part No.
2 Knife 41001
4 Knife Bolts, 3/8-16 x 1” H-6918-608
4 Knife Washers, Special 8815
3 Cutting Stick (in addition to one installed) 4168
1 False Clamp Plate (installed) 41032
1 Tool Kit 20-2150-6
1 - Cutting Stick Puller 5064
2 - Knife Lifters S-1245-5
4 - Knife Screws H-6918-608
4 - Knife Washers 8815
1 - 3/16" Hex Wrench W-130
1 - 1/8" Allen Wrench W -141
1 - 3/32" Allen Wrench W -154
1 - 5/32" Allen Wrench W -137
1 - 5/16" Hex ‘ L ’ Wrench 41087
2 - Door Key S-1839-5
2 - Start/Stop Key S-1839-4
1 Waste Cart 41058
OPTIONAL EQUIPMENT
1 Two-up Book Block Split K-41132-1
1 False Clamp Plate Pad Replacement Kit K-41118
1 Maintenance Kit - Basic K-41090
1 Maintenance Kit - Extended K-41091-2
NOTICE: UNSUPPORTED PRODUCT!
NO TECHNICAL SUPPORT AVAILABLE!
NO REPAIR PARTS AVAILABLE!

F.400-E/NOV 97
iv
SPECIFICATIONS
CAPACITY/SIZES:
Pile Size (height) 1.75” 44 mm
Book Trim Sizes
spine to face – min. 5.25” 134mm
spine to face – max. 9.20” 233mm
top to bottom – min. 8.00” 204mm
top to bottom – max. 12.60” 320mm
Two-up Book Block Splits Option
length – min. 11.00” 280mm
length – max. 12.60” 320mm
width – min. 5.25” 134mm
width – max. 9.20” 233mm
CYCLE TIME:
Book Cycle Time (approx.) 20 seconds
SPECIFICATIONS:
Height 521/4" 132.6cm
Width 40" 101.6cm
Depth 37" 94.0cm
(will pass through standard 32"/81.3cm door)
Weight 837 lb. 377 kg.
Shipping Weight (approx.) 950 lb. 431 kg.
Maximum Operating Altitude 4000 ft. 1.2 km.
Noise Emissions Under 70 DB(A)
ELECTRICAL:
230 volt (±10%), 15 amp, 50/60 Hz., 1 phase, AC
Maximum overcurrent protective device: 15 amps
FEATURES:
LCD Display, Memory for Thirty (30) User Programmable
Book Sizes
Challenge reserves the right to make changes to any product or specification without notice and without incurring
responsibility to existing units.
NOTICE: UNSUPPORTED PRODUCT!
NO TECHNICAL SUPPORT AVAILABLE!
NO REPAIR PARTS AVAILABLE!

v
F.400-E/NOV 97
TABLE OF CONTENTS
INTRODUCTION............................................................................................ ii
PACKING LIST .............................................................................................. iii
STANDARD ITEMS ....................................................................................... iii
SPECIFICATIONS ......................................................................................... iv
SAFETY PRECAUTIONS............................................................................. vii
POWER DISCONNECT PROCEDURE ....................................................... vii
WARNING LABEL DEFINITIONS ............................................................... viii
1.0 INSTALLATION .................................................................................... 1-1
1.1 Uncrating........................................................................................ 1-1
1.1.1 Installation Using Fork Truck ................................................ 1-1
1.1.2 Installation Using "Ramp" ..................................................... 1-2
1.2 Chip Chute & Cover Installation ..................................................... 1-3
1.3 Hydraulic Check ............................................................................. 1-4
1.4 Assembly ....................................................................................... 1-4
1.5 Cleaning ......................................................................................... 1-4
1.6 Power Hookup................................................................................ 1-4
2.0 OPERATION ........................................................................................ 2-1
2.1 ON/OFF - Keyswitch ...................................................................... 2-1
2.2 Footswitch ...................................................................................... 2-1
2.3 Keyboard ........................................................................................ 2-1
2.3.1 Function Keys ....................................................................... 2-1
2.4 Display ........................................................................................... 2-2
2.5 Programming Jobs ......................................................................... 2-2
2.5.1 Job Select Mode ................................................................... 2-2
2.5.2 Job Edit Mode ....................................................................... 2-2
2.5.3 Job Run Mode ...................................................................... 2-3
2.6 Setup Mode .................................................................................... 2-3
2.6.1 Operator Setup Mode ........................................................... 2-3
2.6.2 Maintenance Setup Mode ..................................................... 2-4
2.7 Diagnostic Error Codes .................................................................. 2-5
3.0 KNIFE INSTALLATION/CHANGING ..................................................... 3-1
3.1 Knife removal ................................................................................. 3-1
3.2 Knife installation ............................................................................. 3-2
3.3 Knife Care Tips .............................................................................. 3-3
3.3.1 Knife Blade Life ..................................................................... 3-3
3.3.2 Cutting Stick.......................................................................... 3-4
3.3.3 Bevel Angle........................................................................... 3-4
3.3.4 Helpful Suggestions .............................................................. 3-4
3.3.5 Knife Care ............................................................................. 3-4
4.0 MAINTENANCE ................................................................................... 4-1
4.1 Troubleshooting .............................................................................. 4-2
4.2 Routine Maintenance ..................................................................... 4-3
4.2.1 Weekly .................................................................................. 4-3
4.2.2 Monthly ................................................................................. 4-4
4.2.3Yearly .................................................................................... 4-4
4.3 Hydraulic System ........................................................................... 4-4
4.3.1 Recommended Hydraulic Oils .............................................. 4-5
4.4 Adjustments ................................................................................... 4-6
4.4.1 Clamp Up/Knife Up Proximity Switches ................................ 4-6
4.4.2 Knife Down Proximity Switch ................................................ 4-6
4.4.3 Knife Latch Adjustment Procedure........................................ 4-6
4.4.4 Knife Latch Proximity Switch ................................................. 4-7
4.4.5 Positive Trolley Limit and Linear Preset Proximity Switches.. 4-7
NOTICE: UNSUPPORTED PRODUCT!
NO TECHNICAL SUPPORT AVAILABLE!
NO REPAIR PARTS AVAILABLE!

F.400-E/NOV 97
vi
TABLE OF CONTENTS
(continued)
4.4.6 Rotational Proximity Switch ................................................... 4-8
4.4.7 Hydraulic Valve Adjustments................................................. 4-8
4.4.8 Pneumatic Adjustments ........................................................ 4-9
5.0 PARTS LIST AND SEQUENCE OF OPERATIONS .............................. 5-1
MAIN ASSEMBLY - FRONT VIEW ...................................................... 5-2
MAIN ASSEMBLY - SIDE VIEW .......................................................... 5-4
MAIN ASSEMBLY - TABLE VIEW ........................................................ 5-6
MAIN ASSEMBLY - PLUMBING SCHEMATIC ..................................... 5-8
PNEUMATIC SEQUENCE OF OPERATION ....................................... 5-9
MAIN ASSEMBLY - TABLE VIEW ...................................................... 5-10
MANIFOLD ASSEMBLY..................................................................... 5-12
HYDRAULIC SEQUENCE OF OPERATION ...................................... 5-13
HYDRAULIC POWER UNIT KIT ........................................................ 5-14
ELECTRICAL SEQUENCE OF OPERATION .................................... 5-15
BASIC MACHINE SCHEMATIC ......................................................... 5-17
POWER PANEL ASSEMBLY ............................................................. 5-18
PCB ASSEMBLY - POWER PANEL CONTROL ................................ 5-20
LED INDICATOR INFORMATION ...................................................... 5-21
CONTROL CONSOLE ASSEMBLY ................................................... 5-22
POWER PANEL LABEL ..................................................................... 5-23
KNIFE LATCH ASSEMBLY ................................................................ 5-24
FOOTSWITCH ASSEMBLY ............................................................... 5-25
TILT TABLE KIT ................................................................................. 5-26
TRANSPORT BELT REPLACEMENT/ADJUSTMENT ...................... 5-27
DOCUTRIM REPAIR KITS ................................................................. 5-28
SAFETY SYSTEM TESTS ................................................................. 5-29
NOTICE: UNSUPPORTED PRODUCT!
NO TECHNICAL SUPPORT AVAILABLE!
NO REPAIR PARTS AVAILABLE!

vii
F.400-E/NOV 97
SAFETY PRECAUTIONS
• This machine is designed and safeguarded for ONE PERSON operation. NEVER operate the trim-
mer with more than one person.
• Safety is the responsibility of the user of this machine. Use good judgement and common sense when
working with and around this machine.
• READ and understand all instructions thoroughly before using the trimmer. If questions still remain,
call your Authorized Challenge Dealer - fingers and hands are too valuable to risk experimentation.
• Only authorized and properly instructed persons should operate the trimmer.
• DO NOT ALTER SAFETY MECHANISMS, they are for your protection and should not be altered or
removed. Severe lacerations or dismemberment could result.
• DISCONNECT POWER before cleaning, lubricating, servicing or making adjustments not requiring
power. Turn the key to the off position and disconnect the power plug, see Disconnect Procedure
below.
• Lock the trimmer and remove the key when not in use, see "Main Power–Keyswitch", page 2-1.
• Be sure the trimmer is properly grounded, Power Hookup, page 1-4.
• Be sure there is sufficient power to operate the trimmer properly.
• Observe all caution plates mounted on this trimmer.
• Keep foreign objects off table and away from trimmer blade.
• BE EXTREMELY CAREFUL when handling and changing the trimmer knife. Severe lacerations or
dismemberment could result from careless handling procedures, see page 3-1.
• Keep the floor around the trimmer free of trim, debris, oil and grease.
• When servicing or replacing hydraulic and pneumatic parts, loosen the connections slowly to release
pressure. Never loosen connections with the machine running.
• If the trimmer sounds or operates unusually, turn it off and consult the troubleshooting section of this
manual. If the problem cannot be corrected have it checked by a qualified service person.
• CRUSH HAZARD, keep hand and fingers from under the clamp when clamping paper.
NEVER ATTEMPT TO REACH INTO THE CUTTING AREA!
POWER DISCONNECT PROCEDURE
The socket-outlet shall be installed near the equipment and shall be easily accessible. For maximum safety when
making adjustments or repairs to your machine, be sure to disconnect the power cord. In addition, the machine
switch should be turned to the OFF position and the keys should be held by the person servicing the machine.
Power Disconnect
Switch
(Fig. i)
This safety symbol means CAUTION/WARNING - PERSONAL SAFETY INSTRUCTION. Read
the instructions because it has to do with safety. Failure to comply with the following instruc-
tions may result in personal injury.
NOTICE: UNSUPPORTED PRODUCT!
NO TECHNICAL SUPPORT AVAILABLE!
NO REPAIR PARTS AVAILABLE!

F.400-E/NOV 97
viii
CRUSH HAZARD
PINCH HAZARD
CUT/CRUSH HAZARD
SHOCK HAZARD
SHOCK HAZARD
HAZARDOUS AREA
Keep hands from under paper clamp.
Use two hands when lowering cover. The cover be-
comesheavierwhen itnearstheclosed position. Lower
the cover slowly!
Severelacerationscould result. Keephandsawayfrom
the blade and the clamp.
Disconnect power before removing cover. Replace
coverbeforeoperation.
Disconnect power before removing cover. Replace
coverbeforeoperation.
Disconnect power before cleaning, servicing, or mak-
ingadjustmentsnot requiringpower. Donotalter safety
guards or devices, they are for your protection. Re-
place all guards, do not operate with any guards re-
moved.
WARNING LABEL DEFINITIONS
NOTICE: UNSUPPORTED PRODUCT!
NO TECHNICAL SUPPORT AVAILABLE!
NO REPAIR PARTS AVAILABLE!

1-1
F.400-E/NOV 97
(fig. 1-5)
Chip Chute
Rivets
1.0 INSTALLATION
1.1 Uncrating
Your machine has been carefully packaged to prevent
damage during shipping. Inspect all shipments as soon
as they are received. Note any damage on the freight
bill and notify the claims department of the carrier
within 15 days. Claims for damage are the respon-
sibility of the receiver – inspect promptly. Check
the contents of the crate against the packing list on
page iii of this manual.
The DocuTrim weighs approximately 837 lbs./377 kg.
DO NOT risk personal injury or damage by attempting
to move machinery with makeshift equipment or in-
adequate manpower.
This machine is shipped on a wooden skid and is en-
closed in a protective wooden box. The waste cart is
contained in a separate carton strapped to the top of
the main container. The tool kit, knives and spare cut-
ting sticks are shipped inside the machine.
1. Remove the left and right crate sides first. Each
side is held on with approximately 20 screws.
2. Remove the two boards that are screwed to the
front and rear of the crate (these are the only
boards fastened with screws). This will allow ac-
cess to the inner bracing and allow you to pry the
machine up to remove the braces underneath.
3. While holding the inner bracing, have someone
remove the mounting screws at each of the out-
side corners of the crate (there are two screws at
each corner). Remove the inner braces.
1.1.1 Installation Using Fork Truck
(Figures 1-2 to 1-5)
1. Open the rear access doors using the key sup-
plied in the plastic bag with the manual and re-
(fig. 1-2)
Lag Bolt Location
four (4) places
(fig. 1-3)
Extend Forks
to Rear
Frame Member
(fig. 1-4)
Chip Chute
Removed to
Pass
Through
32"(82cm)
Doorway
(fig. 1-1)
NOTICE: UNSUPPORTED PRODUCT!
NO TECHNICAL SUPPORT AVAILABLE!
NO REPAIR PARTS AVAILABLE!

F.400-E/NOV 97
1-2
Lag Bolt Location
four (4) places
(fig. 1-6)
(fig. 1-7)
Remove
Nails
holding
Runners to
Skid
Runner
Locations
(fig. 1-8)
Remove braces as
machine is lifted
Runner is used as pry bar to lift
machine & remove braces.
move the accessory items.
2. The machine is attached to the shipping skid with
four lag bolts screwed through the machine base
(fig. 1-2). Open the front and rear access doors,
locate and remove the lag bolts.
3. The skid is designed to allow a fork truck access
under the machine (fig. 1-3). Make sure forks
extend far enough under the DocuTrim to sup-
port the rear frame. Use fork extensions if nec-
essary. Lift the trimmer off the skid and gently
lower it to the floor.
4. The machine may now be rolled into position. The
DocuTrim will fit through a standard 32" (82cm)
door if you open the rear access doors (fig. 1-4)
and remove the chip chute. The chute is held in
position with reusable, plastic rivets (fig. 1-5). Sim-
ply pull the rivets out to remove the chute. Re-
place the chute by reinserting the rivets and close
the access doors.
5. Once positioned, the casters may be locked into
position by flipping down the locking levers on the
wheel hubs.
1.1.2 Installation Using "Ramp"
(Figures 1-6 to 1-13)
1. Open the rear access doors using the key sup-
plied in plastic bag with the manual, and remove
the accessory items.
2. The machine is attached to the shipping skid with
four lag bolts screwed through the machine base
(fig. 1-6). Remove the front cover and open the
rear access doors, then locate and remove the
four lag bolts.
3. The two runners are attached alongside the ma-
chine (fig. 1-7). They must be removed and lo-
cated at the front of the machine skid as shown
(fig. 1-11).
4. Two wooden braces run under the machine and
must be removed to allow the machine to be rolled
off the skid. After removing the runners, use one
to pry the machine up and remove the braces (fig.
1-8).
5. Connect the runners to the skid with four nails
included in the manual packet with the keys. Po-
sition the runners in front of the skid and secure
by placing the nails through the predrilled holes
and hammer into the skid (fig. 1-9).
(fig. 1-9)
Secure Runner
with Nails
inserted in
predrilled holes
NOTICE: UNSUPPORTED PRODUCT!
NO TECHNICAL SUPPORT AVAILABLE!
NO REPAIR PARTS AVAILABLE!

1-3
F.400-E/NOV 97
Chip Chute
Rivets
(fig. 1-14)
Waste Chute
(fig. 1-12)
Chip Chute
Removed to
Pass
Through
32"(82cm)
Doorway
(fig. 1-11)
Roll Machine down
Runners
(fig. 1-10)
Align Wheels to
Runner
Chip Chute
Cover (1/2)
(fig. 1-13)
Mounting
Locations
(top and side)
6. Align the casters so the machine will roll straight
down the runners (fig. 1-10).
7. Use two people, one at each side, and gently roll
the machine down the runners (fig. 1-11)
8. The trimmer may now be rolled into its final oper-
ating position. The DocuTrim will fit through a
standard 32" (82cm) door if you open the rear
access doors (fig. 1-12) and remove the chip
chute. The chute is held in position with reus-
able, plastic rivets (fig. 1-13). Simply pull the riv-
ets out to remove the chute. Replace the chute
by reinserting the rivets and close the access
doors.
9. Once positioned, the casters may be locked into
position by depressing the locking levers on the
wheel hubs.
1.2 Chip Chute & Cover Installation
Your machine has been shipped with the chip chute
and covers removed to conserve on shipping space
and to allow the machine to pass through a standard
size 32" (82cm) doorway. You will find these inside of
the machine located with the other accessories.
1. Located in the cutouts of the two rear doors is the
hardware for mounting the covers. Remove the
hardware using the 1/8" hex wrench supplied in
the tool kit.
2. Position covers as shown in (fig. 1-13) and attach
with the hardware supplied.
3. Install the chip chute. Locate and remove the plas-
tic rivets mounted in the waste chute (fig. 1-14).
Align chip chute mounting holes with those of the
waste chute and reinsert the rivets. Simply press
in until the rivet snaps into position.
NOTICE: UNSUPPORTED PRODUCT!
NO TECHNICAL SUPPORT AVAILABLE!
NO REPAIR PARTS AVAILABLE!

F.400-E/NOV 97
1-4
Footswitch
Connection
(fig. 1-16)
Hydraulic
Tank
Dip
Stick
(fig. 1-15)
(fig. 1-17)
Interlock Switch
Wire Connectors
1.3 Hydraulic Check
The hydraulic reservoir holds 4 quarts (3.8 liters) of
hydraulic fluid. It is filled with Rykon 100 hydraulic fluid.
Check before operation and once a week under normal
cutting loads. An oil cross reference chart is provided
in section 4.3.1 of this manual. Open the rear access
doors and unscrew the cap on top of the hydraulic tank,
(fig. 1-15). Fluid level should be within 1/8" (3mm) of
end of dip stick (check with dip stick cap screwed in).
Avoid overfilling as this could cause leakage when hot.
Close and latch the rear doors.
1.4 Assembly
Items that need to be installed are the cover interlock
switch, footswitch, and knife. See the Knife Installation
and Changing (page 3-1) for installation instructions.
The footswitch cable is connected to the socket on the
lower front corner of the right hand side of the ma-
chine. Carefully align the polarity notch (fig. 1-16). Plug
the pin into the socket and tighten the locking ring. The
footswitch may be positioned where it is most conve-
nient for the operator. The cover interlock switch is lo-
cated in a bag attached to the manual, along with keys
and door wrench. Open the rear doors and raise the
cover. The switch mounting bracket and connecting
wires are located at the top right corner of the stand (fig.
1-17). Press the switch into the bracket and attach wires
#40 & #41 to the two center terminals of the switch.
Close the cover slowly and check the alignment of the
switch with the actuator attached to the underside of
the cover.
1.5 Cleaning
Wipe off all machine panels and clean the table sur-
face.
1.6 Power Hookup
Machines are shipped with both 50 hz and 60 hz style
plugs. Connect the proper cord for your application as
shown in figures 1-18 and 1-19. If your socket/outlets
are a different configuration, have your DocuTrim dealer
install the proper plug required. Power to the machine
is then controlled by the switch on the right hand side
of the machine (fig. 1-20).
CAUTION: NEVER MODIFY POWER
CONNECTORS. Always use proper
electrical connectors. Electrical shock
could occur with improper connections.
NOTICE: UNSUPPORTED PRODUCT!
NO TECHNICAL SUPPORT AVAILABLE!
NO REPAIR PARTS AVAILABLE!

1-5
F.400-E/NOV 97
(fig. 1-20)
Power Disconnect
Switch
(fig. 1-18)
(fig. 1-19)
NOTICE: UNSUPPORTED PRODUCT!
NO TECHNICAL SUPPORT AVAILABLE!
NO REPAIR PARTS AVAILABLE!

F.400-E/NOV 97
1-6
NOTES
NOTICE: UNSUPPORTED PRODUCT!
NO TECHNICAL SUPPORT AVAILABLE!
NO REPAIR PARTS AVAILABLE!

2-1
F.400-E/NOV 97
Keyboard
Display Power/STOP
Keyswitch
2.0 OPERATION
Do not attempt to operate this machine until you have
thoroughly read and understand all of the following in-
structions. Call your authorized Challenge dealer if you
still have any questions.
2.1 ON/OFF - Keyswitch
Once the DocuTrim is positioned and hooked up to a
power source, the DocuTrim can be turned on and off
using the large red emergency stop button on the con-
trol panel (fig. 2-2). It is keyed so that by depressing
the button and removing the key, unauthorized use of
the trimmer is prevented. Pressing it at any time in a
cycle stops all motion.
Depress the stop button and remove the key any time
the trimmer is not being used or will be left unattended
for an extended period of time.
Turning the key releases the stop button and connects
power to the machine components. The control panel
display will light up and the compressor will come on
(provided all the doors are closed).
2.2 Footswitch
The footswitch is used to initiate a cycle while the
operator’s hands are free to load and hold the stock in
position. While the safety beams across the loading
opening are broken, the clamp will only operate under
low pressure (about 60 lbs/27.2 kg of force). After the
operator’s hands are removed, the pneumatic trans-
port cylinder increases it’s clamp force to full power
and the cut cycle is initiated.
In Setup Mode, the footswitch is used to send the knife
up or down after selecting the appropriate function.
2.3 Keyboard
The sixteen button keyboard on the control panel (fig.
2-2 & 2-3) enables the operator to conveniently pro-
gram and operate the DocuTrim. For specific functions,
please refer to the detailed instructions that follow.
2.3.1 Function Keys
JOB Key
This key allows the operator to toggle through job po-
sitions stored in the memory.
EDIT Key
The EDIT key allows the operator to make changes to
the programs stored in the memory.
(fig. 2-2)
(fig. 2-3)
Blank
(No Function)
Transport
Clamp
Control
Panel
Power/STOP
Button
Side
Guide
Footswitch
(fig. 2-1)
NOTICE: UNSUPPORTED PRODUCT!
NO TECHNICAL SUPPORT AVAILABLE!
NO REPAIR PARTS AVAILABLE!

F.400-E/NOV 97
2-2
CLEAR Key
The CLEAR key is used to erase entries. In Job Select
Mode, pressing the CLEAR key will select a new job
position.
ENTER Key
The ENTER key is used to store the desired param-
eter into memory. It is also used to enter machine func-
tions such as "Run", "Knife Down", or "Knife Up".
2.4 Display
The DocuTrim has a two line Display that indicates to
the operator the mode of operation and displays vari-
ous prompts and instructions for machine Setup, Job
Selection, Editing, and Running a job.
The first three characters of the top line will indicate
the mode of operation (JOB for Job Select Mode or
Job Edit Mode and RUN for Job Run Mode). Follow-
ing the mode indication is a double digit number that
indicates the job number (01–30). The next position
shows the A & B dimensions of the current job. The
last position on the top line is a small graphic which
indicates the type of job stored at that position (double
bar indicates the book spine, single bars indicate sides
which have a programmed cut).
The lower line will provide the operator with prompts
and instructions depending on what function the ma-
chine is in.
2.5 Programming Jobs
Whenever the DocuTrim is powered up, the display
will show the following:
A timer begins to count down and the machine will not
operate until it reaches zero. This allows the air com-
pressor to reach full capacity. Once the timer reaches
zero, the display will be activated in Job Select Mode
and the last job that was in use at the time the DocuTrim
was turned off will be displayed.
2.5.1 Job Select Mode
Job Select Mode is entered after power is turned on
and the timer has reached 0. It can also be entered
from Job Run Mode by pressing the JOB key. Once in
Job Select Mode, there are two ways to select a job:
1) Continue to press the JOB key to toggle through
jobs 01 through 30, or 2) Select a specific job by press-
ing the CLEAR key and the desired job number (enter
a 0 before single digit positions), then press the EN-
TER key. Once the job has been selected, press the
ENTER key again to enter Job Run Mode or the EDIT
key to enter Job Edit Mode.
2.5.2 Job Edit Mode
Job Edit Mode can be entered from either Job Select
Mode or Job Run Mode by pressing the EDIT key. In
Job Edit Mode the display will look similar to the follow-
ing:
Press “1” to view/edit options (described below) or press
ENTER to bypass options and edit the book dimen-
sions. If “1” is pressed, the following be displayed:
Press the “1” key for two-up splits (cutting paper in half)
or the “0” key to program (or edit) a regular book trim-
ming sequence.
“1” Two-up Block Split Option
Use this option for two-up block splits (cutting
paper in half). Selecting this option will bring up
the following display:
PLEASE WAIT
150
JOB 01 8.50✳11.00
SELECT JOB.
Operation
Mode
Job
Number
A & B
Dimensions
Job
Graphic
Prompts & Instructions
(fig. 2-4)
JOB 01 8.50✳11.00
1=OPTIONS ENT=ALL 3 SIDES
JOB 01 8.50✳11.00
SPLIT PILE? 1=YES 0=NO
JOB 01 8.50✳11.00
ENTER WIDTH_
NOTICE: UNSUPPORTED PRODUCT!
NO TECHNICAL SUPPORT AVAILABLE!
NO REPAIR PARTS AVAILABLE!

2-3
F.400-E/NOV 97
Enter the width dimension (this is the side that
will be placed against the transport clamp). The
width must be between 5.25" and 9.2". Next en-
ter the length dimension (this is the dimension
that will be cut in half). The length must be be-
tween 11.0" & 12.6". Note: Pressing the ENTER
key without typing a dimension will keep the di-
mension already programmed.
“0” Book Trimming
Use this option for book trimming. Selecting this
option will bring up the following display:
Select which side(s) of your book you wish to trim
by answering yes (“1”) or no (“0”) to each ques-
tion. Figure 2-5 shows the book dimensions.
The job graphic (fig. 2-4) will be updated in the
upper right corner of the display after each selec-
tion is made.
Once the sides to be trimmed have been indi-
cated, the machine will ask the operator to enter
the dimension of each cut, as shown below:
Enter each dimension by typing a number then
pressing ENTER. If ENTER is pressed without
typing a number, the current value for that dimen-
sion will be entered.
NOTE – DIM E (height of the parent book) is not
asked for.
After the last item is entered, you will return to
Job Select mode.
2.5.3 Job Run Mode
To run a job, select the program you wish to run in Job
Select Mode and press the ENTER key. The machine
will then setup the transport and sideguide positions
for the selected job (provided the electric eye beams
are not broken).
If the program selected is a book trimming operation,
load the book(s) to be trimmed with the spine against
the transport clamp and the top of the book against the
side guide. Make sure the spine is square against
the transport clamp. While holding the book in posi-
tion, press and hold the footswitch. Once the book is
positioned correctly, remove your hands to allow the
clamp to increase to full pressure and start the cutting
cycle. Breaking the electric eye beams will cancel the
cut cycle and bring the transport clamp back to the
home position.
For a two-up split, load the pile with the width dimen-
sion against the transport clamp. Press and hold the
footswitch to bring the transport clamp down to hold
the paper. Removal of the hands will then initiate the
cut sequence. After the first half of the pile has been
presented for removal, remove the paper to signal the
machine to retrieve the half stored behind the knife.
To go to Job Edit Mode from Job Run Mode, simply
press the EDIT key. To return to Job Select Mode,
press the JOB key.
2.6 Setup Mode
The Setup Mode is divided into two areas, OPERA-
TOR and MAINTENANCE. Upon initial installation you
will need to use them to calibrate your DocuTrim and
make sure your book trimming is accurate.
2.6.1 Operator Setup Mode
To enter Operator Setup mode, you must first be in
Job Select Mode (see section 2.5.1). Enter Job #00
by pressing CLEAR then “00” then ENTER. You will
then be able to scroll through the different functions by
pressing the EDIT key. To exit Operator Setup mode,
scroll through the functions until the lower line reads,
“EXIT SET UP” and press the ENTER key. You will
then return to the Job Select mode. A description of
each function is given below:
1. Knife Down
This is used for setting the knife adjusters after
(fig. 2-5)
JOB 01 8.50✳11.00
CUT TOP (A) ? 1=YES 0=NO
JOB 01 8.50✳11.00
ENTER DIM A _
NOTICE: UNSUPPORTED PRODUCT!
NO TECHNICAL SUPPORT AVAILABLE!
NO REPAIR PARTS AVAILABLE!

F.400-E/NOV 97
2-4
installation of a new or sharpened knife. Select
this function by pressing the ENTER key and then
pressing the footswitch. The cutting clamp and
the knife will come down to the table and stay
down. Use the Knife Up function to return the
knife to its normal (up) operating position. Also
see Knife Installation & Changing section of this
manual.
2. Knife Up
After the knife adjustment and/or servicing have
been completed, select this function to return the
knife to its normal (up) operating position. When
prompted by the display to “SEND KNIFE UP?”,
press the ENTER key and then press the foot-
switch. The hydraulics will come on and the knife
and cutting clamp will rise to their up position.
3. Lock Memory
The DocuTrim memory may be locked or un-
locked by the operator to prevent unintentional or
unauthorized changes to stored programs. Press
the ENTER key at the "LOCK MEMORY ?"
prompt. At the "ENTER CODE" prompt, press
the three digit code, 5-0-1 and press the ENTER
key to lock or unlock the memory. Press the EDIT
key to continue on through the Setup Functions.
4. Language Selection
Simply press the number that corresponds to the
desired language. Press the Edit Key to advance
without making a change.
5. Knife Count
This function can be used to determine when the
blade should be changed. It displays the number
of knife strokes since it was last reset. Press the
CLEAR key to reset the counter after changing a
blade.
6. Book Count
This function can be used to keep track of the
number of books that have been cut. It counts
how many cutting cycles have been made since
it was last reset. It does not take into account mul-
tiple books cut per cycle – this must be kept track
of by the operator and calculated for a final count.
Press the CLEAR key to reset the cycle counter.
7. Exit Setup
Pressing the ENTER key at this prompt will exit
the Setup Mode.
2.6.2 Maintenance Setup Mode
To enter the MAINTENANCE SETUP mode, you must
first be in Job Select Mode (see section 2.5.1). Enter
Job #99 by pressing CLEAR then “99” then ENTER.
You will then be able to scroll through the different func-
tions by pressing the EDIT key. To exit the setup mode,
scroll through the functions until the lower line reads,
“EXIT SET UP” and press the ENTER key. You will
then be returned to the Job Select mode. A descrip-
tion of each function is given below:
1. Machine Count
This function displays the total number of knife
strokes on your machine. It can only be reset by
trained service personnel. Press the Edit key to
advance to the next function,
2. Setup Memory (Metric or Inch)
This function allows you to choose between Met-
ric or English (inch) modes of measurement and
at the same time, erases and restores the
memory to the factory default programs. Select
the measurement mode at initial installation –
changing modes will erase customized pro-
grams! Activating this function (selecting either
of the measurement options) will erase any cus-
tomized programming. In the inch mode, the dis-
play reads to the nearest 0.01 inch, while in met-
ric mode the display reads to the nearest 0.1 mm.
Follow the prompts to select the desired mea-
surement mode. Press “1” to use the Metric
mode, press “0” to select the English mode.
Press any other key to exit this function without
changing modes or erasing programs.
3. Rotation Comp
Rotation compensation is used to make sure the
transport clamp is square to the knife. Press the
ENTER key to access this function. With the
knife and clamp in the full up position, carefully
remove the cutting stick. Next, while at the front
of the machine, place a 1-1/2"(38mm) stack of
paper under the right hand side of the cutting
clamp (fig 2-6). Press the foot pedal and wait for
the machine cycle to stop. Place a drafting tri-
angle (supplied) flush against the knife and up
against the transport clamp (fig. 2-6). Press the
appropriate key (“1”=Clockwise, “2”=Counter-
clockwise) to rotate the transport head until the
triangle is flush to the face of the transport clamp.
Great care should be taken when making this
NOTICE: UNSUPPORTED PRODUCT!
NO TECHNICAL SUPPORT AVAILABLE!
NO REPAIR PARTS AVAILABLE!
Table of contents
Other Challenge Trimmer manuals
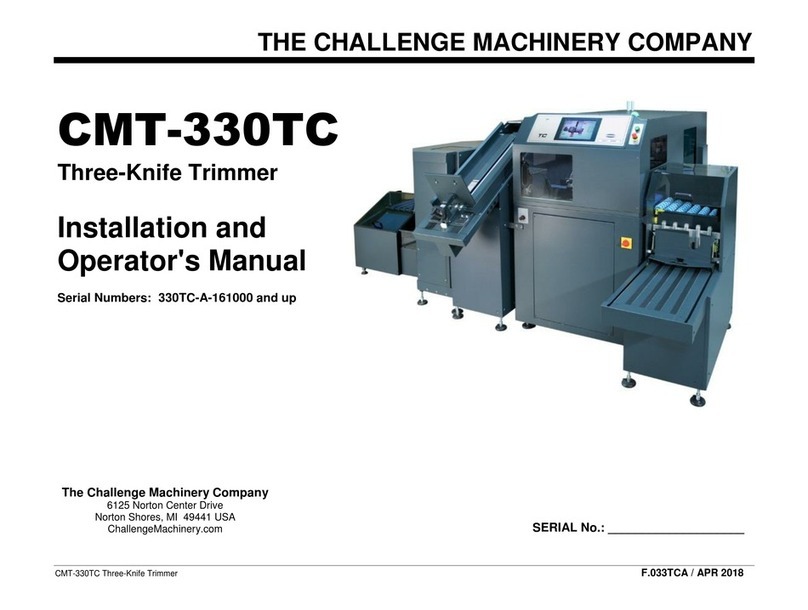
Challenge
Challenge CMT-330TC Setup guide
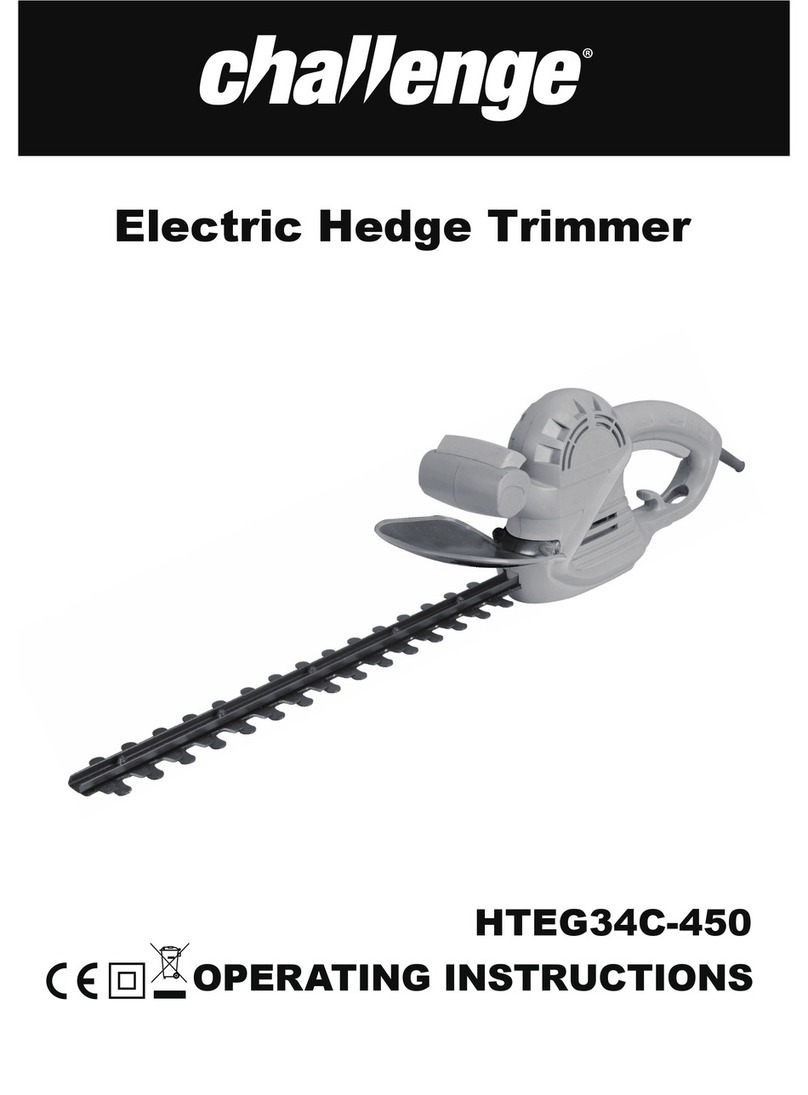
Challenge
Challenge HTEG34C-450 User manual

Challenge
Challenge HTEG33-550 Operation instructions
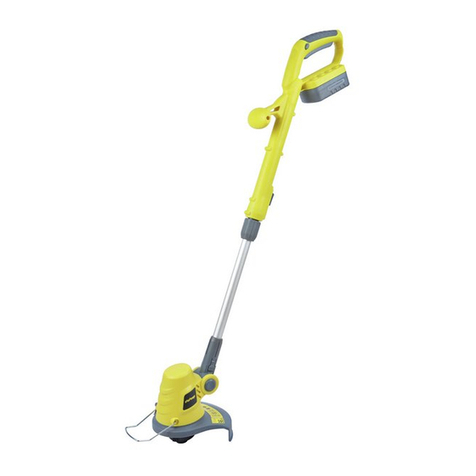
Challenge
Challenge N0E-15ET-230 Operation instructions
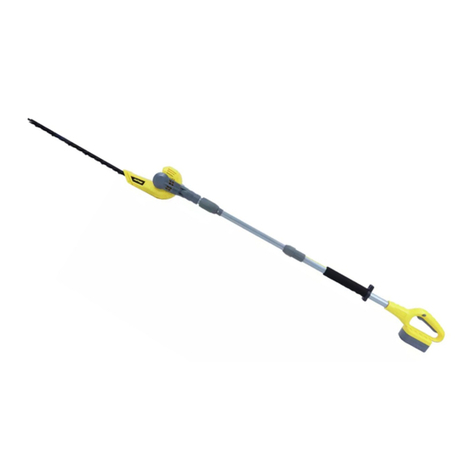
Challenge
Challenge M0E-9ET-410 Operation instructions
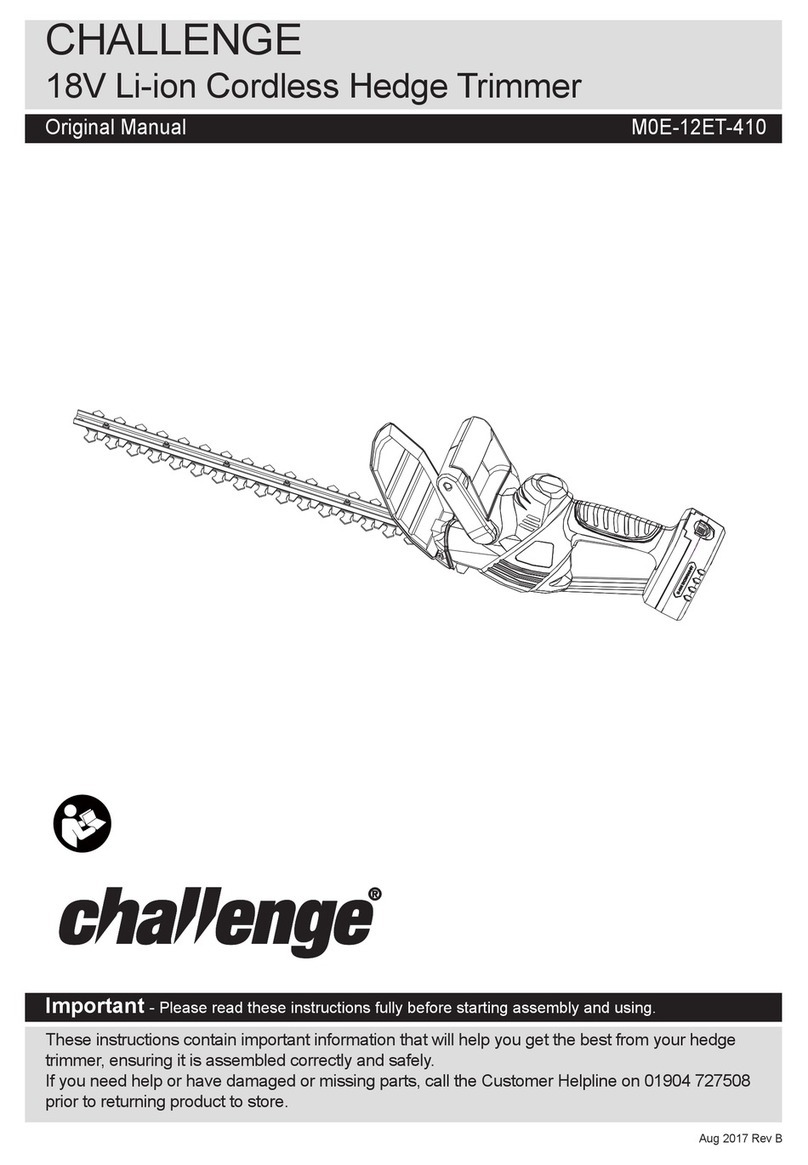
Challenge
Challenge M0E-12ET-410 Operation instructions

Challenge
Challenge N0E-2ET-230 User manual
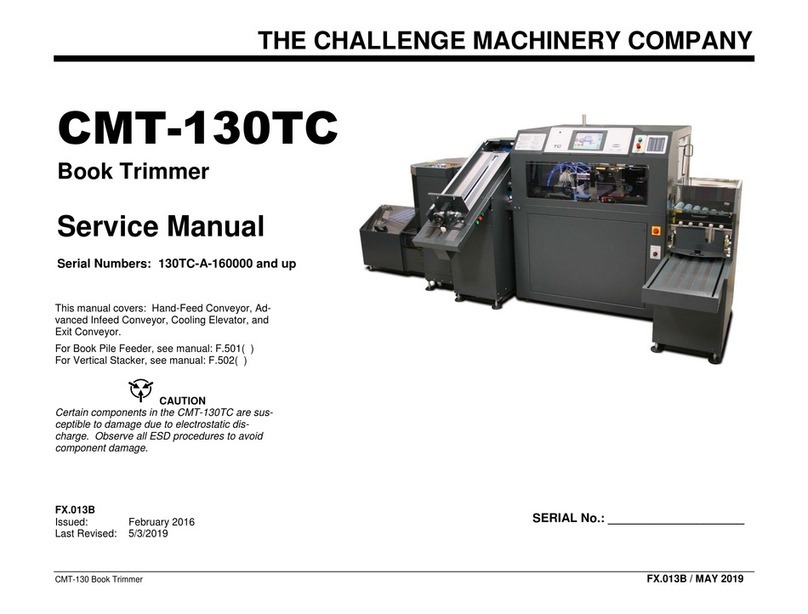
Challenge
Challenge CMT-130TC User manual
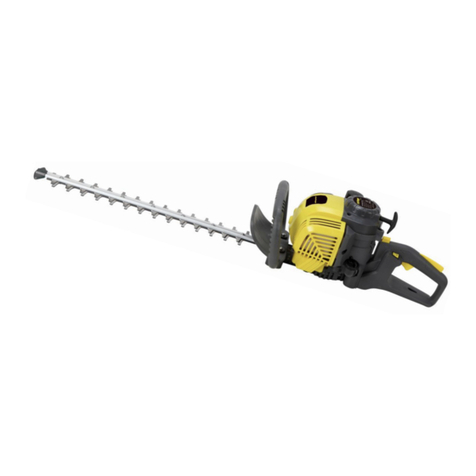
Challenge
Challenge YT9305-01 Operation instructions
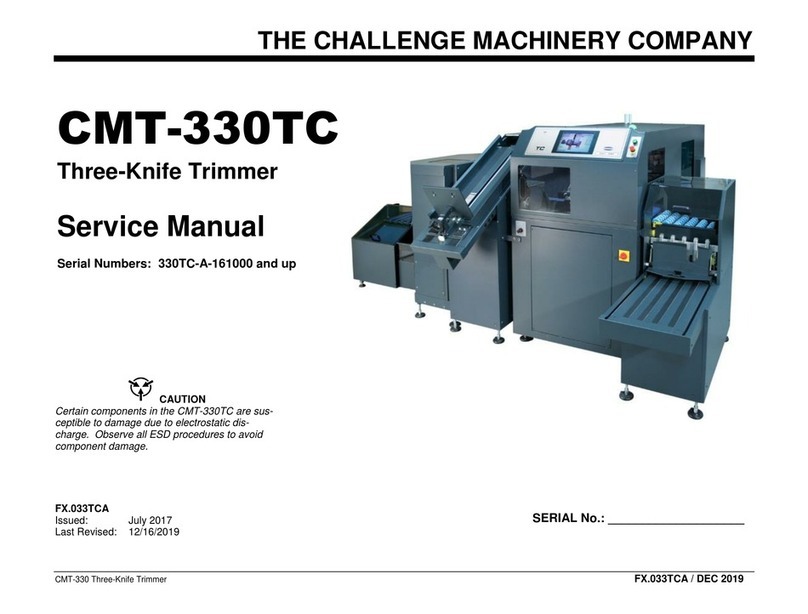
Challenge
Challenge CMT-330TC User manual