Circor SPENCE E5 Instruction manual

1
Valve Ends ASME/ANSI Pressure PSIG (bar) Temperature °F (°C)
CAST IRON
Class 250 NPT 250 (17.2) @ 450 (232)
B16.1 Class 125 Flanged 125 (8.6) @ 450 (232)
B16.1 Class 250 Flanged 250 (17.2) @ 450 (232)
CAST STEEL
B16.34 Class 300 NPT 300 (21.0) @ 600 (315)
B16.34 Class 150 Flanged 150 (10.3) @ 500 (260)
B16.34 Class 300 Flanged 300 (21.0) @ 600 (315)
SD 3005A
TYPE E5 Main Valve
SPECIFICATION
The Spence type E5 Main Valve is self-operated, external pilot type, single seat-
ed, diaphragm actuated, normally closed design. The valve will function quickly
and shut tight on dead end service. Internal parts including seats, discs and
stems are of stainless steel. The diaphragm is a balanced Hycar material
designed for high lift but low differential. There is an external condensation
chamber supplied. The main valve spring shall operate on a 5 psi minimum
differential. There are no springs in the steam flow path and no stuffing box.
Canadian Registration # OC 0591.9C
Printed in the U.S.A. SD3005A/0607
DIMENSIONS (inches) AND WEIGHTS (pounds)
CAPPROX.WT
AIntegral Mount D*
Iron,Brz.
Iron Steel
SIZE ANSI ANSI ANSI BStd. CI Stl. ANSI SCR
Stl.ANSI
ANSI ANSI ANSI ANSI
NPT 125 250 Mount 125 250 NPT 125 250 150 300
3/443/4——6
7/827/835/831/2111/4111/423 — — — —
(19) (111) — — (175) (73) (92) (89) (286) (286) (10) — — — —
15
3/851/266
7/835/843/843/8115/8115/824 30 33 35 39
(25) (137) (140) (152) (175) (92) (111) (111) (295) (295) (11) (14) (15) (16) (18)
11/461/263/471/491/841/844
5/8131/2131/249 46 49 58 63
(32) (165) (171) (184) (232) (105) (102) (117) (343) (343) (22) (21) (22) (26) (29)
11/271/467/873/891/843/841/2513
5/8135/853 58 68 67 74
(38) (184) (175) (187) (232) (111) (114) (127) (346) (346) (24) (26) (31) (30) (34)
27
1/281/2911
1/851/455
5/8161/4161/484 90 97 113 120
(51) (191) (216) (229) (283) (133) (127) (143) (413) (413) (38) (41) (44) (51) (55)
21/2—9
3/810 111/853/453/8616
1/2161/2— 97 112 130 135
(64) — (238) (254) (283) (146) (137) (152) (419) (419) — (44) (51) (59) (61)
3 — 10 103/4131/265/863/8719
1/4191/4— 148 170 210 226
(76) — (254) (273) (343) (168) (162) (178) (489) (489) — (67) (77) (95) (103)
4—11
7/8121/2131/275/865/8818
3/8233/8— 208 293 307 330
(102) — (302) (318) (343) (194) (168) (203) (467) (594) — (95) (133) (139) (150)
5—13
5/8141/2131/281/273/883/4183/4233/4— 240 333 335 366
(127) — (346) (368) (343) (216) (187) (222) (476) (603) — (109) (151) (152) (166)
6—15
1/816 163/410 7 — 231/2273/8— 348 616 560 503
(152) — (384) (406) (425) (254) (178) — (597) (695) — (158) (280) (254) (274)
8 — 19 20 163/4111/291/4—23
3/4295/8— 650 814 795 862
(203) — (483) (508) (425) (292) (235) — (603) (752) — (295) (370) (361) (392)
10 — 235/825 20 133/4——30
3/4353/8— 910 1130 1345 1420
(254) — (600) (635) (508) (349) — — (781) (899) — (414) (513) (611) (645)
12 — 261/228 243/4157/8——39
3/4393/4— 1580 1920 1990 2160
(305) — (673) (711) (629) (403) — — (1010) (1010) — (718) (872) (904) (982)
*Add 150% to D dimension for stem removal clearance.
SEAT REGULATOR SIZE
FACTOR 3/411
1/411/222
1/23 4 5 6 8 10 12
Full 7.6 11.7 18.9 27.4 43 67 95 159 258 350 665 1018 1611
Normal 5.7 10.0 13.4 19.8 25 35 59 120 176 228 366 525 952
RATED FLOW COEFFICIENTS (Cv)
C
A
B
D
FIGURE 1

2
The regulator is operated by initial steam or fluid pres-
sure. It is normally closed, being held so by initial pres-
sure on the disc and by an internal main spring. When
the pilot is opened (see pilot instructions), initial pres-
sure flows through the pilot to the No. 8B tee.
Bleedport No. 4A restricts the flow and pressure
builds under the diaphragm and opens the main valve.
The No. 5A elbow steadies the operation of the regu-
lator.
Delivery pressure feeds back through the control pipe
to the pilot diaphragm. As this pressure approaches a
balance with the thrust of the adjusting spring, the
pilot throttles the loading pressure. In turn, the main
valve takes a position established by the loading pres-
sure where just enough steam flows to maintain the
set delivery pressure.
CONDENSATE CHAMBER
Main valves with large internal volumes, or valves used
in relatively high pressure or superheat, may require
more water than can be condensed from radiation
alone. Live steam will rapidly degrade the rubber
diaphragm of an E5 and generally yield poor control in
other main valves. To prevent this from happening, the
Condensation Chamber and the base are primed with
water before start-up. As the pilot opens, medium
pressure steam flows to the Condensation Chamber
condensing the vapor in the presence of the prime and
larger radiational area. The condensate exits the
chamber through a No. 5B Open Elbow directed to the
No. 5A Restriction Elbow in the hood. This condensate
collecting under the diaphragm creates a loading
pressure which forces the valve open.
OPERATING PRINCIPLE
Globe Valve
Gate Valve
Long
Radius
Elbow
D2
Gate Valve
At least 20 Pipe Diameters (D2)
To first turn or secondary PRV on control valve
At least 10 Pipe Diameters (D1)
Straight run, full size
Avoid bull-headed connection to
low pressure steam main when
reduction in noise level is important
Strainer
Gate Valve
D1
Drip and Trap Do not insulate
below this line or any
part of the pilot 1/4" Sensing Pipe - Pitch away
from Pilot. Avoid water pockets
connect to D2 pipe where shown
Spence Pressure Regulator
- allow clearance above
and below for maintenance.
4 Pipe diameters
(D2) Minimum
Drip and trap ahead
of rise in piping or
secondary PRV or
control valve
Preferred transition - 15"
max. total included angle
RECOMMENDED INSTALLATION
FIGURE 2

3
START-UP AND SETTING
Before placing the E5 valve in service, its base and
condensation chamber must be primed (with water) in
order to avoid damage to the diaphragm.
On pressure reducing valves like the E5D, use bypass
line to fill the delivery system and raise pressure slight-
ly below the normal requirement. Close pilot by releas-
ing compression on adjusting spring. See Figure 3.
Open 1/4" control pipe valve. See Figure 4. Crack out-
let stop valve. Crack inlet stop valve. Blow down
strainer.
Caution: Never open a reducing valve without posi-
tive indication that the high side is clear of conden-
sate.
Open inlet stop valve and gradually compress adjust-
ing spring until the valve opens and takes control at
Adjusting
Nut Adjusting Spring
8B Tee 4A Bleedport
Do not insulate
below this line
Condensation
Chamber Bend
Condensation
Chamber
5B Open Elbow
Restriction Bend 5A Restriction Elbow
FIGURE 3
REGULATOR ASSEMBLY FOR TYPE E5 MAIN VALVE
WITH CONDENSATION CHAMBER
1/4"
Control
Pipe
desired pressure. Alternately choke down on the
bypass line and open outlet stop valve until the regu-
lator is operational. See individual instructions for
other pilots.
HYDROSTATIC TEST PROCEDURE
Install pilot according to instructions. Fully compress
pilot spring and open inlet and outlet stop valves
before filling system. SLOWLY fill system from inlet
or high pressure side of regulator. Bleed off trapped
air. SLOWLY develop test pressure up to 300 PSIG
MAXIMUM. If a higher presure is required
CONTACT FACTORY FIRST.
Test pressures may cause normally acceptable leak-
age at the diaphragm joint. Consult factory for hydro-
static test for other types of regulators.
“WARNING: This product operates in pipelines or with equipment that carries fluids
and/or gasses at elevated temperatures and pressures. Caution should be taken to
make sure that the equipment is installed correctly and inspected regularly. Caution
should also be taken to protect personnel from fluid or gas leakage.”

4
INSTALLATION
PLANNING
Locate the valve in a straight run of horizontal pipe.
Allow headroom above the valve for access through
the blind flange. Provide clearance for stem withdraw-
al underneath. Prevent water hammer and erratic
operation by installing traps to provide proper
drainage before and after the valve and before sec-
ondary PRV or control valve. Avoid damaging effects
of scale and dirt in pipe lines by using a strainer as
shown in Figure 2. Provide a 3-valve by-pass to facili-
tate inspection without interrupting service.
To eliminate excessive noise and erratic regulation
with steam and other compressible fluids, enlarge the
delivery pipe size to effect a reasonable flow velocity
at the reduced pressure. A tapered transition is rec-
ommended. If possible, avoid a sharp turn close to the
regulator outlet and a bull-headed tee connection to
the low pressure main.
Install initial and delivery pressure gages to indicate
performance. If the pressure rating of the delivery sys-
tem or connected equipment is less than the initial
steam pressure, provide a safety valve.
MAIN VALVE
Flush the piping system thoroughly to clear it of weld-
ing beads, scale, sand, etc. Mount the main valve with
diaphragm chamber down and arrow on body pointing
in the direction of flow. Screwed end valves should be
mounted in unions.
PILOT
Mount the pilot on either side of the main valve by
means of 1/4" nipple and union provided. Make this
connection to the 1/4" pipe tap at the inlet of the main
valve as shown in Figure 4.
Fit No. 4A bleedport fitting into the 1/8" pipe tap at the
outlet of the main valve body. Note bleed orifice in this
fitting – vital to operation of regulator.
Fit No. 8B tee into 1/8" pipe tap in pilot. Select tap fac-
ing downstream.
Fit No. 5A elbow containing restriction orifice into 1/8"
pipe tap on underside of main valve diaphragm cham-
ber. If the initial pressure or pressure drop is less than
15 psi, a No. 5B open elbow is used.
Connect tubing bends as illustrated in Figure 3 and
Figure 4. Valves with condensation chamber are fitted
up according to Figure 3.
CONTROL PIPE
Use 1/4" pipe for this line, shown on Figure 4, which
connects the pilot diaphragm chamber to the desired
point of pressure control. Take the control at a point of
minimum turbulence. Avoid control immediately at the
valve outlet or after a turn. When the delivery pipe
expands in size, select a spot at least 4 pipe diameters
beyond the point of enlargement. Pitch away from
pilot to avoid erratic operation and excessive fouling.
Eliminate water pockets. Locate delivery pressure
gage in control pipe to show pressure actually reach-
ing pilot diaphragm.
FIGURE 4
TYPICAL INSTALLATION
VIEW FACING INLET
4A Bleedport
Type D Pilot 1/4" Control Pipe
Fill with water before
placing valve in service
5A Restriction
5/16" O.D.
Tubing 5B Elbow
Condensation
Chamber
5B Elbow
8B Tee
1/4" Union Pipe

5
TROUBLE SHOOTING
FAILURE TO OPEN OR SAGGING DELIV-
ERY PRESSURE
1. Adjusting spring on pilot may have been tampered
with.
2. Initial pressure may be down due to partially closed
supply valve, clogged strainer or other obstruction.
3. Orifice in No. 5A restriction elbow may be plugged.
No. 4A bleedport fitting may have been omitted and
an open coupling substituted.
4. Control pipe may be plugged. Most likely points of
obstruction are at shutoff valve and entrance to
delivery main.
5. Main diaphragm may be broken. Test with air or
water before dismantling.
FAILURE TO CLOSE OR OVER-RIDING
DELIVERY PRESSURE
1. Adjusting spring on pilot may have been tampered
with.
2. Orifice in bleedport No. 4A may be plugged.
3. By-pass valve may be leaking.
4. On pressure regulators like the E5, the main valve or
pilot may be held open by foreign matter in seat. To
determine which valve leaks, first close stop valve
and 1/4" control pipe valve. Then remove bleedport
bend so pilot will exhaust to atmosphere. Crack
inlet stop valve. Steam will issue from No. 8B tee.
Release compression on adjusting spring to see if
pilot closes tight. Open and close several times to
wash seat. Steam blowing back from bleedport
means main valve disc is held open by foreign mat-
ter. Steam may wash the obstruction from the seat
if the valve is made to open wide. This can be
accomplished, even at light loads, if the control
point is beyond the outlet stop valve. Reassemble
bleedport bend and place regulator in operation.
Then, slowly open and close outlet stop valve.
MAINTENANCE
INSPECTION
Under normal conditions, complete dismantling at
regular intervals is not recommended. A valve kept
relatively free of dirt will function for years with min-
imum attention.
After the first few days of operation and twice a
year, the following should be checked.
1. Inspect for dirt collected at bleedport No. 4A and
restriction elbow No. 5A.
2. Inspect all joints for leakage. Keep bolts tight.
Never allow a leak to persist.
DISMANTLING MAIN VALVE
Connect a source of air or water pressure which
can be adjusted by hand to the No. 5A restriction
elbow. See Figure 5. Apply pressure to valve so
diaphragm will push on stem preventing it from
turning while removing stem nuts. Usually 50 to 60
psi will suffice. Use penetrating oil on the threads.
See Figure 5.
FIGURE 5

6
VALVE SETTING
Valve setting is gaged at K to establish correct stem
length and diaphragm position. Dimension “K” is sup-
plied with each replacement stem. For metal dia-
phragm valves, “K” is cast on the upper face of pres-
sure plate (15) (Fig. 6).
To install new stem (12), fasten disc (7) (see Fig. 7)
firmly on stem with stem nut. Insert stem and disc
assembly in valve and screw on pressure plate (15).
Omit spring (13) for this operation. Hold disc on seat
and adjust position of pressure plate until valve setting
“K” is reached. Push pressure plate against stops in
base (11). Remove disc, drop out pressure plate and
stem, drill and insert dowel pin (14) to lock the joint.
Grind off stem projection flush with face of pressure
plate.
VALVE TRAVEL SETTING
SIZE TOTAL GROOVE DRILL
TRAVEL PIN SIZE
3/4 1/4 1/8 X 11/16 1/8
1 5/16 1/8 X 11/16 1/8
11⁄43/8 5/32 X 13/16 5/32
11⁄27/16 5/32 X 13/16 5/32
2 9/16 5/32 X 15/16 5/32
21⁄211⁄16 3/16 X 15/16 3/16
31
3⁄16 3/16 X 13⁄83/16
41
1⁄16 1/4 X 13⁄41/4
51
5⁄16 5/16 X 13⁄45/16
61
9⁄16 5/16 X 2 5/16
82
1⁄16 3/8 X 2 3/8
10 29⁄16 3/8 X 21⁄23/8
12 31⁄16 1/2 X 23⁄41/2
FIGURE 6
REPLACING SEAT RINGS
These joints should be made up with Copaltite,
Permatex or equal high temperature gasket com-
pound. Remove old compound from body and seat
ring with a wire brush. Apply new compound sparing-
ly to both parts, threads and shoulders. Let stand until
tacky before assembling.
GRINDING IN (Lapping)
Seats and discs should never require more than the
lightest touch up with very fine (400 grit) grinding com-
pound. Heavy grinding will produce galling, wider
seating surface and a groove in the disc, all of which
tend to cause leakage. Reface a damaged surface
before attempting to grind it in. Grind sparingly.
Main stem (12) shown on Figure 6 is slotted for rotation
with a screwdriver, Valve spring (13) is omitted from
the assembly during grinding. Slip the stem into its
normal position. apply compound to the disc, place it
on the stem and tighten with one stem nut.
After grinding, disassemble and clean all parts.
MAINTENANCE
15
11
12
13
14

7
Inner Valve Assembly
Sizes 3/8" - 11⁄2" Port Inclusive Internal Balanced Integral Mounted Blind Flange
23
24 25
12
26
5
7
9
PARTS DIAGRAMS
FIGURE 7

8
Item Valve Size
No Part Name Material 3/4 1 11⁄411⁄22 2.5 3
1 Blind Flg Stud 125 lb STEEL — 04-10118-00 04-05442-00 04-05443-00 04-10119-00 04-10119-00 04-05443-00
Blind Flg Stud 250 lb STEEL 04-05516-00 04-10118-00 04-05442-00 04-05443-00 04-10119-00 04-05447-00 04-10119-0
2 Blind Flg Nut 125 lb STEEL — 05-02851-00 05-02854-00 05-02856-00 05-02860-00 05-02860-00 05-02856-00
Blind Flg Nut 250 lb STEEL 05-02847-00 05-02851-00 05-02854-00 05-02856-00 05-02860-00 05-02862-00 05-02860-00
3 Blind Flg 125 lb CI — 04-02173-00 04-02176-00 04-02178-00 04-02180-00 04-02185-00 04-02157-00
Blind Flg 250 lb CI 04-02171-00 04-02173-00 04-02176-00 04-02178-00 04-02180-00 04-02183-00 04-02186-00
Blind Flg 250 lb Brz 04-02172-00 04-02174-00 04-02177-00 04-02179-00 04-02181-00 — —
4 Blind Flg Gasket Grafoil 05-02381-01 05-02362-01 05-02382-01 05-02365-01 05-02366-01 05-02367-01 05-02369-01
5 Stem Nut “F” port STEEL 05-02969-00 05-02970-00 05-02970-00 05-02971-00 05-02971-00 05-02971-00 05-02973-00
6 Muffling Plate “F” port CI — — — — 04-03550-01 04-03515-00 04-03516-00
7 Integral Disc “F” port SS 04-01813-02 04-01832-02 04-01850-02 04-01870-02 04-01888-02 04-01906-01 04-01918-00
Integral Disc “F” port Stellited 04-01814-02 04-01833-02 04-01851-03 04-01871-02 04-01889-02 04-01907-00 04-01919-00
8 Pipe Plug 1/4" NPT STEEL 04-03772-00 04-03772-00 04-03772-00 04-03772-00 04-03772-00 04-03772-00 04-03772-00
9 Seat Ring “F” port SS 04-04075-01 04-04084-01 04-04092-01 04-04096-01 07-40405-05 07-40412-00 07-40422-00
Seat Ring “F” port Stellited 04-04076-01 04-04085-01 04-04093-01 04-04097-01 07-40404-01 07-40410-00 07-40423-00
10 Body 250 lb Scr CI 04-00639-00 04-00640-00 04-00643-00 04-00646-00 04-00649-00 — —
Body 125 lb Flg CI — 04-00641-00 04-00644-00 04-00647-00 04-00650-00 04-00653-00 04-00655-00
Body 250 lb Flg CI — 04-00642-00 04-00645-00 04-00648-00 04-00651-00 04-00652-00 04-00654-00
11 Base 125 lb CI — 04-00546-00 04-00518-00 04-00518-00 04-00521-00 04-00548-00 04-00520-00
Base 250 lb CI 04-00546-00 04-00546-00 04-00518-00 04-00518-00 04-00521-00 04-00548-00 04-00520-00
12 Stem 125 lb SS — 04-05242-01 04-05246-01 04-05383-01 04-05265-01 04-05391-01 04-05382-01
Stem 250 lb SS 04-05232-01 04-05242-01 04-05246-01 04-05383-01 04-05265-01 04-05391-01 04-05382-01
Steam Internal balance SS 04-05643-00 04-11180-00 04-05645-00 04-03132-00 04-05647-00 04-11182-00 04-07194-00
13 Main spring STEEL 05-05072-01 05-05072-01 05-05071-01 05-05071-01 05-05073-01 05-05073-01 05-05047-00
14 Groove Pin STEEL 05-03245-00 05-03245-00 05-03248-00 05-03248-00 05-03249-00 05-03252-00 05-03253-00
15 Pressure Plate CI 04-03697-00 04-03680-00 04-03698-00 04-03688-00 04-03673-00 04-03633-00 04-03681-00
16 Diaphragm Bolt 125 lb STEEL — 05-04774-00 05-04780-00 05-04780-00 05-04780-00 05-04780-00 05-04785-00
Diaphragm Bolt 250 lb STEEL 05-04774-00 05-04774-00 05-04780-00 05-04780-00 05-04780-00 05-04780-00 05-04785-00
17 Diaphragm Hycar 05-01600-00 05-01600-00 05-01601-00 05-01601-00 05-01602-00 05-01602-00 05-01603-00
18 Hood 125 lb CI — 04-02630-00 04-02629-00 04-02629-00 04-02638-00 04-02638-00 04-02634-00
Hood 250 lb CI 04-02630-00 04-02630-00 04-02629-00 04-02629-00 04-02638-00 04-02638-00 04-02634-00
19 Diaphragm Nut 125 lb STEEL — 05-02874-00 05-02877-00 05-02877-00 05-02877-00 05-02877-00 05-02881-00
Diaphragm Nut 250 lb STEEL 05-02874-00 05-02874-00 05-02877-00 05-02877-00 05-02877-00 05-02877-00 05-02881-00
20 Pipe Plug 1/8" NPT STEEL 04-03769-00 04-03769-00 04-03769-00 04-03769-00 04-03769-00 04-03769-00 04-03769-00
21 Cond Chamber 125 lb STEEL — 08-02154-00 08-02157-00 08-02157-00 08-02160-00 08-02160-00 08-02165-00
Cond Chamber 250 lb STEEL — — 08-02157-00 08-02157-00 08-02160-00 08-02160-00 08-02165-00
22 Stem bushing STEEL — — — — — — —
23 Bal Cylinder Brz 04-01569-01 04-01570-01 04-01571-01 04-01572-01 04-01573-01 04-01574-01 04-07500-00
24 Sealing Ring EPT 05-04020-00 05-04027-00 05-04030-00 05-04036-00 05-04041-00 05-04049-00 05-04596-00
25 Bal Piston Brz 04-03336-00 04-03337-00 04-03338-00 04-03339-00 04-03340-00 04-03341-00 04-04594-00
26 Top Flange CI 04-02246-00 04-02248-00 04-02250-00 04-02252-00 04-02233-00 04-02259-00 04-02261-00
Item Valve Size
No. Part Name Material 4 5 6 8 10 12
1 Blind Flg Stud 125 lb STEEL 04-10119-00 04-10120-00 04-10120-00 04-10120-00 04-05453-00 04-05451-00
Blind Flg Stud 250 lb STEEL 04-05447-00 04-05448-00 04-05449-00 04-05455-00 04-05451-00 04-05451-00
2 Blind Flg Nut 125 lb STEEL 05-02860-00 05-02860-00 05-02860-00 05-02860-00 05-02860-00 05-02864-00
Blind Flg Nut 250 lb STEEL 05-02862-00 05-02862-00 05-02862-00 05-02862-00 05-02864-00 05-02864-00
3 Blind Flg 125 lb CI 04-02158-00 04-02160-00 04-02165-00 04-02167-00 04-02294-00 04-02168-00
Blind Flg 250 lb CI 04-02159-00 04-02161-00 04-02163-00 04-02166-00 04-02164-00 04-02168-00
Blind Flg 250 lb Brz — — — — — —
4 Blind Flg Gasket Grafoil 05-02371-01 05-02372-01 05-02374-01 05-02375-01 05-02376-01 04-02377-01
5 Stem Nut “F” port STEEL 05-02974-00 05-02975-00 04-02976-00 04-02977-00 04-02977-00 04-02978-00
6 Muffling Plate “F” port CI 04-03518-00 04-03519-00 04-03520-00 04-03524-00 04-03538-00 04-03539-00
7 Integral Disc “F” port SS 04-01931-00 04-01938-00 04-01995-00 04-01691-00 04-01953-00 04-01957-00
Integral Disc “F” port Stellited 04-01932-00 04-01939-00 04-01996-00 04-07707-00 04-08268-00 04-08269-00
8 Pipe Plug 1/4" NPT STEEL 04-03772-00 04-03772-00 04-03772-00 04-03772-00 04-03772-00 04-03772-00
9 Seat Ring “F” port SS 07-40441-00 07-40450-00 07-40470-00 07-40483-00 07-44463-00 07-44465-00
Seat Ring “F” port Stellited 07-40449-00 07-40458-00 07-40469-00 07-40482-00 @-04464-00 @-04466-00
10 Body 250 lb Scr CI — — — — — —
Body 125 lb Flg CI 04-00659-01 04-00661-01 04-00662-00 04-00665-00 04-01273-00 04-06618-00
Body 250 lb Flg CI 04-00658-01 04-00660-01 04-00663-00 04-00664-00 04-00666-00 04-00667-00
11 Base 125 lb CI 04-00515-00 04-00515-00 04-00519-01 04-00519-01 04-00516-01 04-00524-02
Base 250 lb CI 04-00522-01 04-00522-01 04-00523-00 04-00523-00 04-00517-01 04-00524-02
12 Stem 125 lb SS 04-05281-00 04-05287-01 04-05374-00 04-05290-00 04-05296-00 04-05398-00
Stem 250 lb SS 04-05384-01 04-05386-01 04-05385-01 04-05388-01 04-05277-00 04-05398-00
Steam Internal balance SS 04-08233-00 04-05831-00 04-10709-00 04-07564-00 — —
13 Main spring STEEL 05-05062-00 05-05062-00 05-05039-00 05-05039-00 05-05040-01 05-05079-00
14 Groove Pin STEEL 05-03255-00 05-04686-00 05-03258-00 05-03302-00 05-03261-00 05-03263-00
15 Pressure Plate CI 04-03689-00 04-03683-00 04-03685-00 04-03682-00 04-03611-00 04-03690-00
16 Diaphragm Bolt 125 lb STEEL 05-04786-00 05-04786-00 05-04787-00 05-04787-00 05-04794-00 05-04798-00
Diaphragm Bolt 250 lb STEEL 05-04787-00 05-04787-00 05-04791-00 05-04791-00 05-04796-00 05-04798-00
17 Diaphragm Hycar 05-01604-00 05-01604-00 05-01605-00 05-01605-00 05-01606-00 05-01607-00
18 Hood 125 lb CI 04-02626-00 04-02626-00 04-02626-00 04-02627-00 04-02661-00 04-02637-00
Hood 250 lb CI 04-02633-00 04-02633-00 04-02632-00 04-02632-00 04-02628-00 04-02637-00
19 Diaphragm Nut 125 lb STEEL 05-02881-00 05-02881-00 05-02881-00 05-02881-00 05-02883-00 05-02883-00
Diaphragm Nut 250 lb STEEL 05-02881-00 05-02881-00 05-02881-00 05-02881-00 05-02883-00 05-02883-00
20 Pipe Plug 1/8" NPT STEEL 04-03769-00 04-03769-00 04-03769-00 04-03769-00 04-03769-00 04-03769-00
21 Cond Chamber 125 lb STEEL 08-02165-00 08-02165-00 08-02167-00 08-02175-00 08-02177-00 08-02812-00
Cond Chamber 250 lb STEEL 08-02165-00 08-02165-00 08-02168-00 08-02175-00 08-02177-00 08-02812-00
22 Stem bushing STEEL — — — — 04-02307-00 04-06528-00
23 Bal Cylinder Brz 04-07248-00 04-07307-00 04-09568-00 04-07199-00 — —
24 Sealing Ring EPT 05-04528-00 05-04528-00 05-04530-00 05-04530-00 — —
25 Bal Piston Brz 04-07249-00 04-07301-00 04-09567-00 04-07198-00 — —
26 Top Flange CI 04-02263-00 04-02264-00 04-02266-00 — — —
PART NUMBERS
Table of contents
Other Circor Control Unit manuals
Popular Control Unit manuals by other brands

DIDIESSE
DIDIESSE Electronic System instruction manual

LEGRAND
LEGRAND On-Q lyriQ AU1001 Instruction/installation sheet
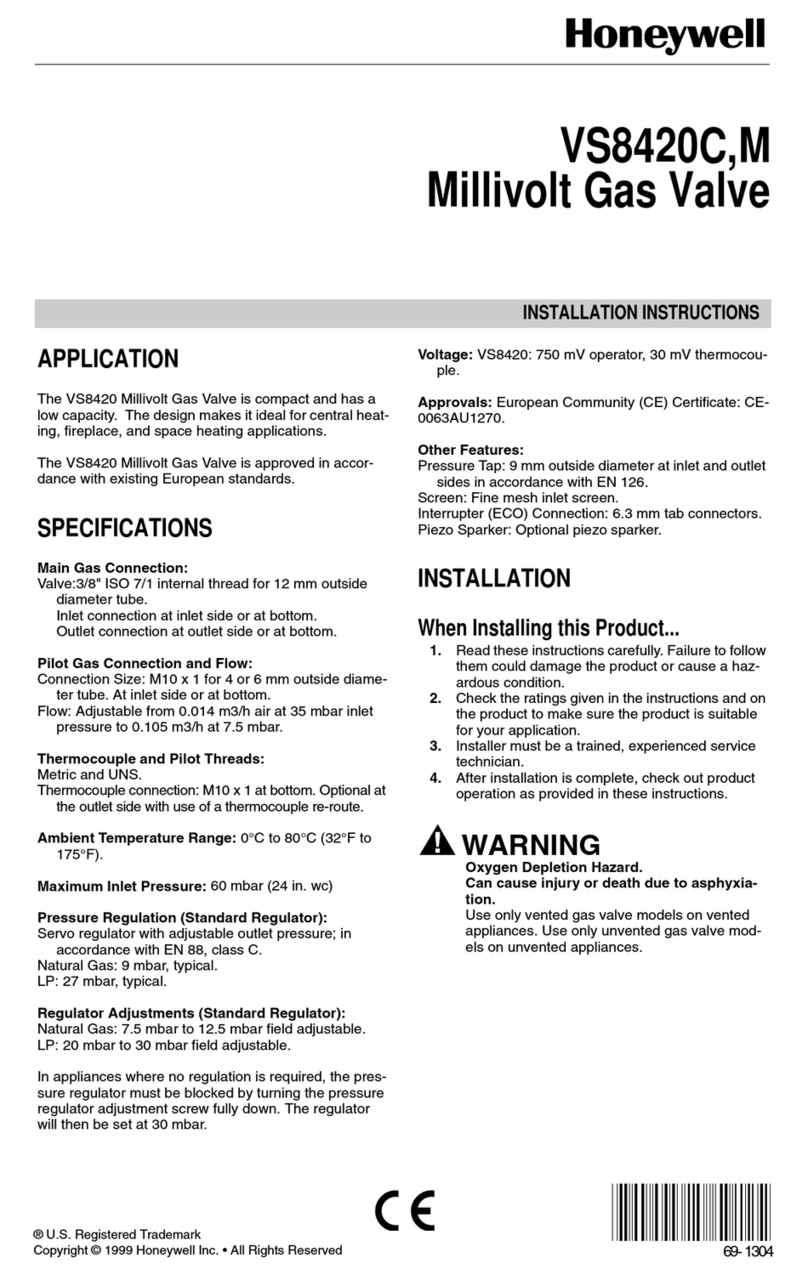
Honeywell
Honeywell VS8420C installation instructions

Burkert
Burkert 2000 INOX operating instructions
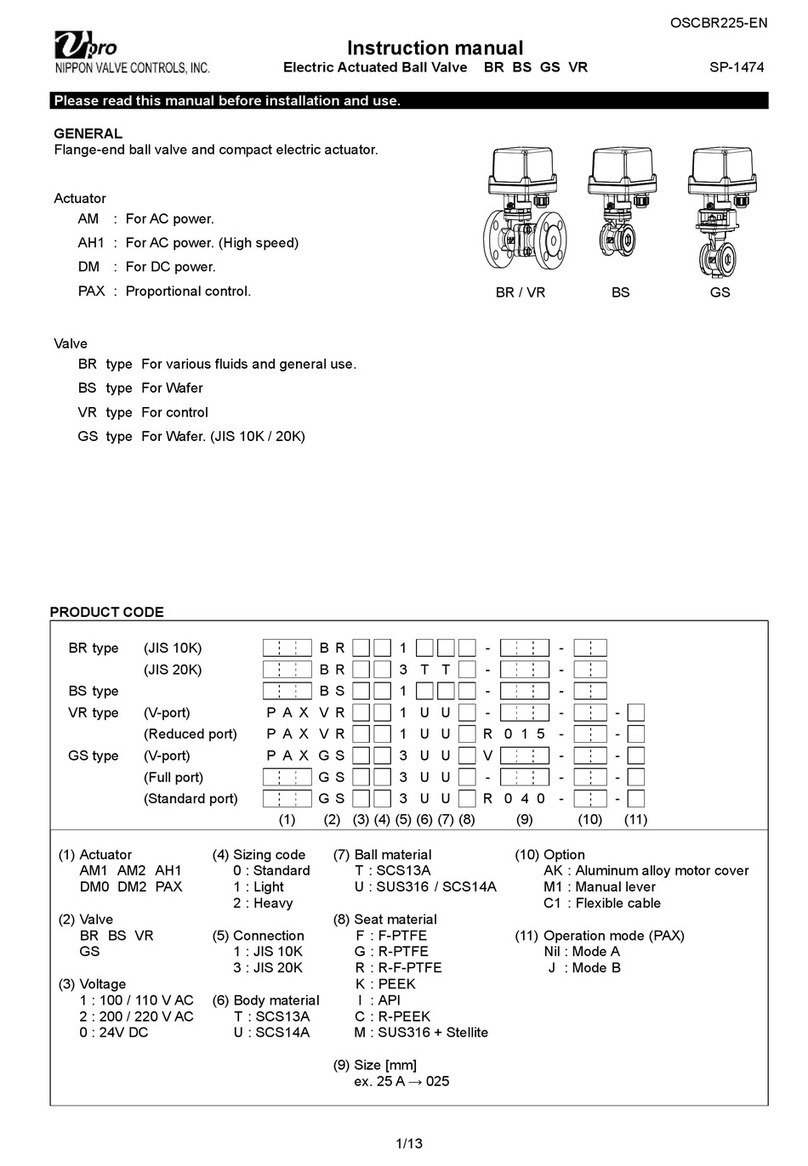
NIPPON VALVE CONTROLS
NIPPON VALVE CONTROLS Vpro BR instruction manual
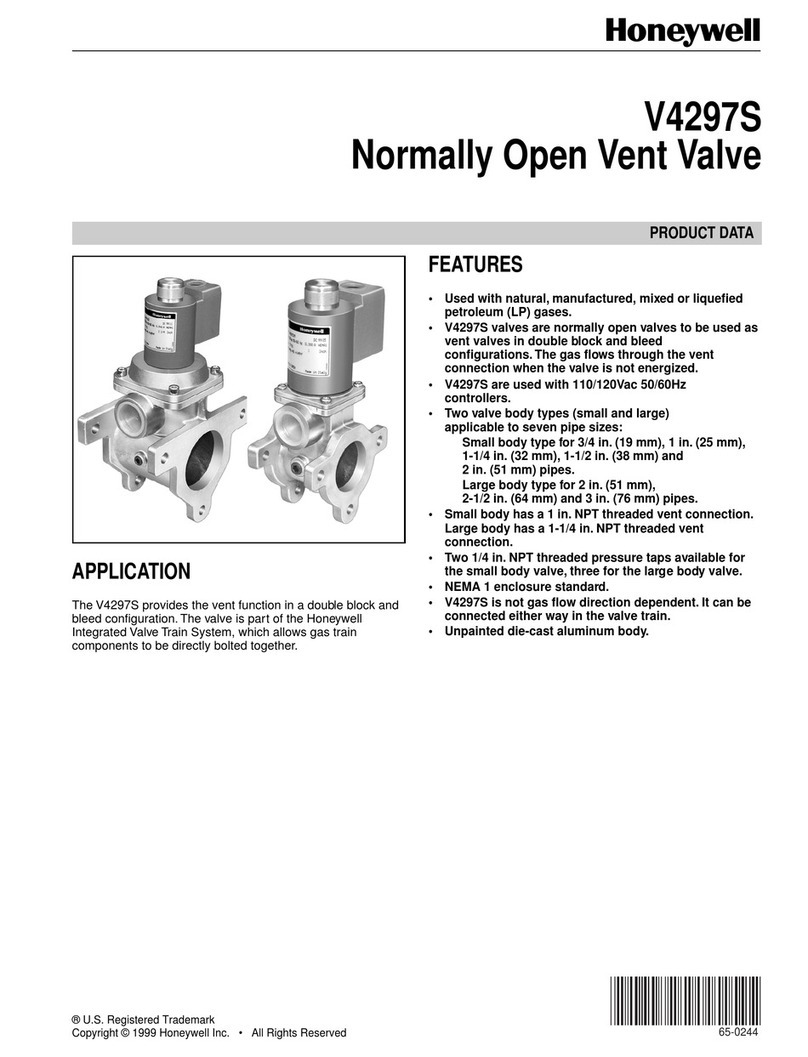
Honeywell
Honeywell V4297S Product data
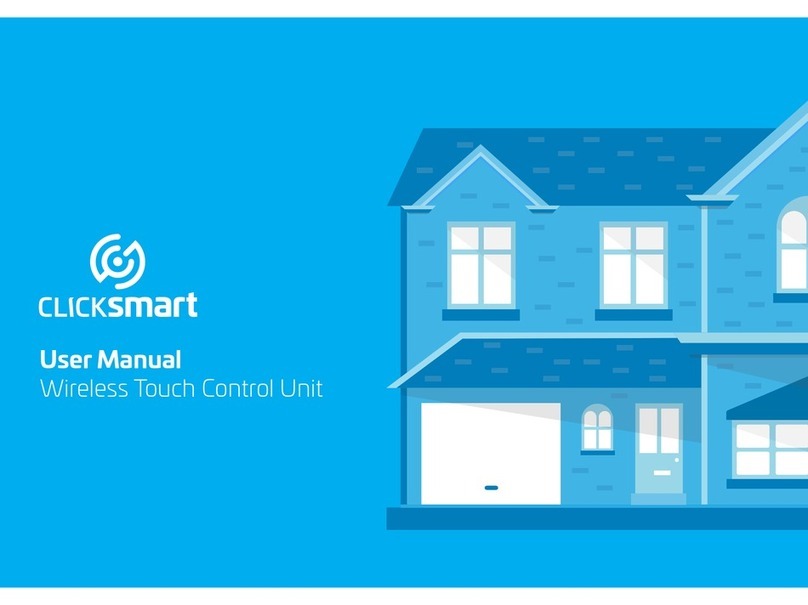
Click Lighthouse
Click Lighthouse ClickSmart user manual

Tektronix
Tektronix Keithley 7706 Instructions for use
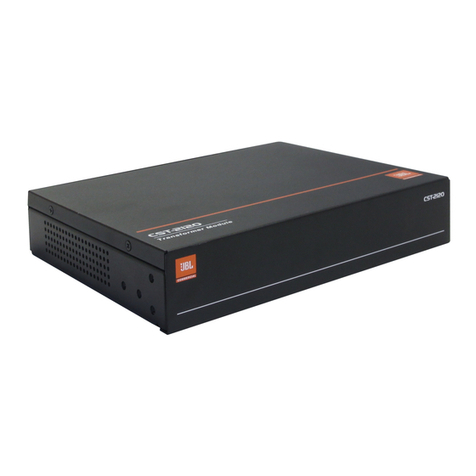
Harman
Harman JBL CST-2120 quick start guide
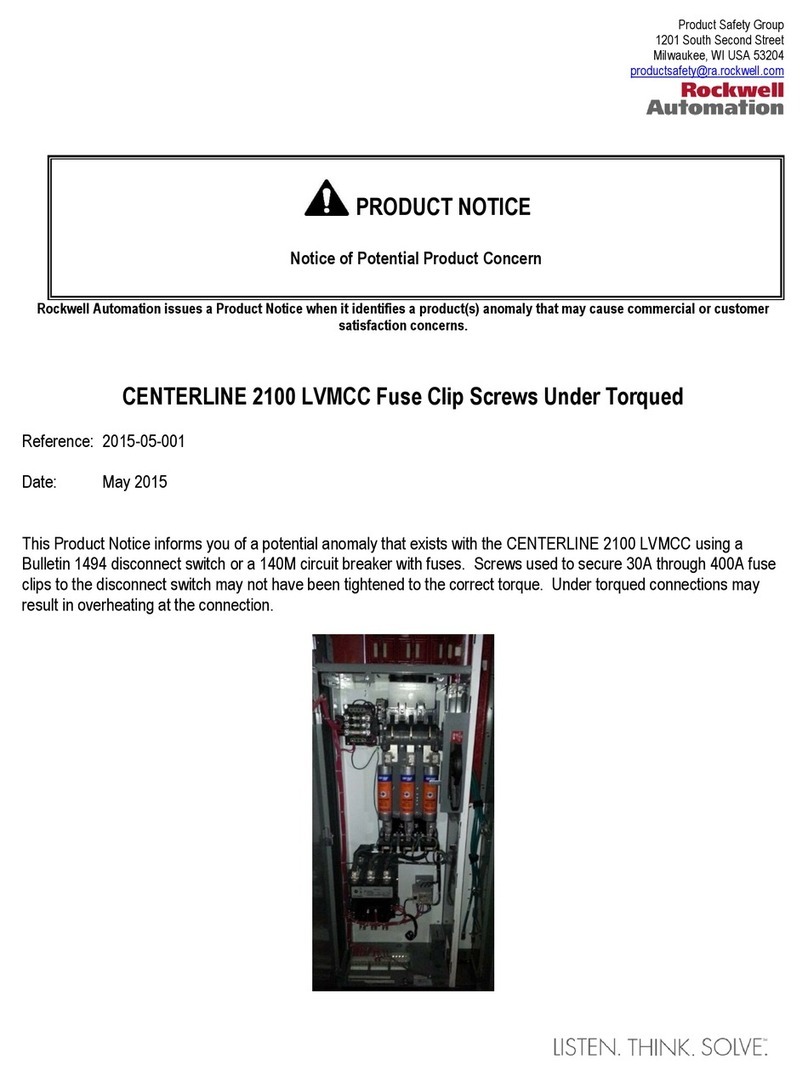
Rockwell Automation
Rockwell Automation CENTERLINE 2100 LVMCC PRODUCT NOTICE

thomann
thomann Harley Benton PA-250 user manual
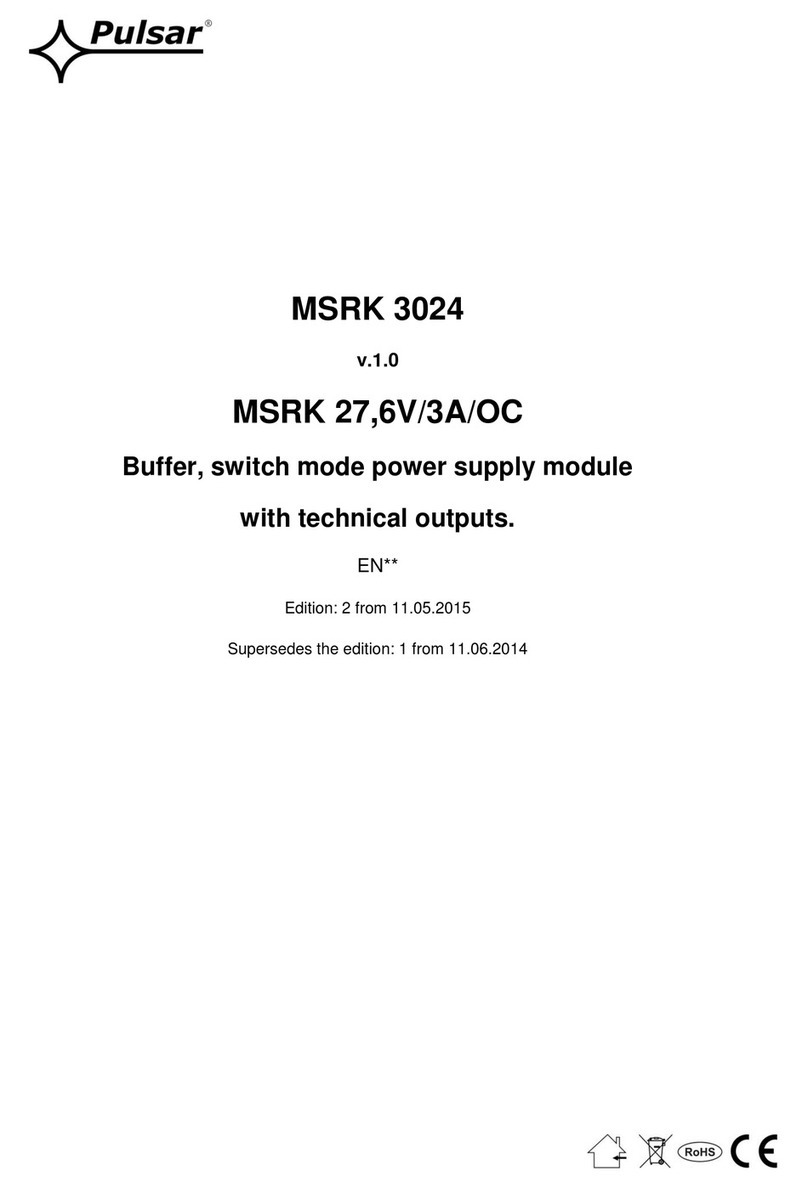
Pulsar
Pulsar MSRK 3024 Installation