Cleco B1-C Series User manual

For additional product information visit our website at http://www.apextoolgroup.com
Parts Manual
823108
05/10/2011
B1-C & BR-C Series
Scalers
XX - XXX - XX - XXX - K
Tool Series
B1 = Shank (Square Chisel)
BR = Shank (Round Chisel)
Tool Type
C = Chisel
CNB = Chisel and Needle Scaler
Throttle
BV = Pistol
LT = Lever
PT = Push
Nose Type (CNB Models only)
RD = Round
RET = Rectangular
Option
K = Kit: Case, Scaler, Whip Hose, Extra Needle Set, 2 Chisels, Chisel Retainer parts

2
throttle moves freely and returns to closed position). Being
carefulnottoendangeradjacentpersonnel,cleartheairhose
of accumulated dust and moisture. Attachment of a quick-
disconnect air coupling directly to the inlet threads of a
percussion tool can cause wear and failure of the coupling.
Shouldthecouplingfail,severeinjurycanresultfromthehose
end violently whipping about. If a quick-disconnect air cou-
pling is used, separate the coupling from the tool with a whip
hose(1.5 feetminimum). Onlyuse awhip hosewith fittingsof
hardenedsteelor other material which is atleastcomparably
resistant to shock. Do not use hose to lift or lower tool.
Cracked chisels or implements are
hazardous. Visually inspect the chisel
or implement for cracks before use.
Make a practice of having all chisels magnifluxed before
resharpening. Destroy and discard any chisel or implement
that shows a crack.
Correctselectionofthechiselorotherimplementisimportant.
Dull edges on the chisel or moil point cause the energy of the
percussion blow to be absorbed by the tool itself, instead of
the workpiece, increasing the chance of chisel breakage.
When operating percussion tools in explosive or flammable
environments, use only non-sparking chisels or implements
such as those made from beryllium copper. Also, do not use
cupped rivet sets with Cleco percussion tools to drive nails.
Blows not centered on the nail can cause the nail to ricochet
off the work and strike the user.
Beforeremovingatoolfromservice,aftercompletingajob,or
changingchiselsorotherbits,makesuretheairlineisshutoff
and drained of air. This will prevent the tool from operating if
Safety Recommendations
Foryoursafetyandthe safetyof others,readandunderstand
thesafetyrecommendationsbeforeoperatinganypercussion
tool.
Always wear protective equipment and clothing.
For additional information on eye protection, refer to Federal
OSHA Regulations, 29 CFR, Section 1910.133, Eye and
Face Protection, and ANSI Z87.1, Occupational and Educa-
tional Eye and Face Protection. This standard is available
fromtheAmericanNationalStandardsInstitute,Inc.,11West
42nd Street, New York, NY 10036.
Hearing protection is recommended in high noise areas
(above85 dBA). Closeproximity of additionaltools, reflective
surfaces, process noises, and resonant structures can sub-
stantially contribute to the sound level experienced by the
operator. For additional information on hearing protection,
refertoFederalOSHARegulations,29CFR,Section1910.95,
Occupational Noise Exposure, and American National Stan-
dards Institute, ANSI S12.6, Hearing Protectors.
Gloves and other protective clothing should be worn as
required.Properlyfitted glovescushionvibrationandprotect
the fingers from pinching, scuffing and scraping and must be
used when guiding the chisel on a workpiece.
Cleco percussion tools are designed to operate on 90 psig
(6.2 bar) maximum air pressure. Excessive air pressure can
damage the plunger and increases sound levels. Installation
ofafilter-regulator-lubricatorintheairsupplylineaheadofthe
tool is highly recommended. Before the tool is connected to
the air supply, check the throttle for proper operation (i.e.,
WARNING
!
WARNING!
Explosive Hazard.
Use only nonsparking chisels or
implements in explosive or
flammable environments.
Impact Hazard. Ejected chisels can cause
serious injury or even death.
Disconnect air before changing chisels.
Do not operate unless chisel is in contact
with workpiece.
Do not point tool in direction of any person.
Use safety retainers on tool and retainer
type chisels.
WARNING!
Erect barriers to protect persons in
surrounding or lower work areas.
WARNING!
Impact resistant eye protection
must be worn while operating
or working near this tool.
CAUTION!
Personal hearing protection is
recommended when operating
or working near this tool.
WARNING!
Compressed air hazard.
Compressed air can cause loss
of eyesight, bleeding or injection
of foreign material into the body
or blood.
Never use compressed air to clean
off clothing or direct it at any person.
Quick Disconnect Coupling Quick Disconnect Coupling
Do not use! OK
Coupling Nipple Whip Hose
Coupling Nipple

3
thought to contribute to the conditions. Any user suffering
prolonged symptoms of tingling, numbness, blanching of
fingers, clumsiness or weakened grip, nocturnal pain in the
hand, or any other disorder of the shoulders, arms, wrists, or
fingersisadvisedtoconsultaphysician.Ifitisdeterminedthat
the symptoms are job related or aggravated by movements
and postures dictated by the job design, it may be necessary
forthe employerto takesteps toprevent furtheroccurrences.
Thesestepsmightinclude,butarenotlimitedto,repositioning
the workpiece or redesigning the workstation, reassigning
workerstootherjobs,rotatingjobs,changingworkpace,and/
or changing the type of tool used so as to minimize stress on
the operator. Some tasks may require more than one type of
tool to obtain the optimum operator/tool/task relationship.
• Tasks should be performed in such a manner
that the wrists are maintained in a neutral
position, which is not flexed, hyperextended,
or turned side to side.
• Stressful postures should be avoided. Select
a tool appropriate for the job and work
location.
Work gloves with vibration reducing liners and wrist supports
are available from some manufacturers of industrial work
gloves.Toolwrapsandgripsarealsoavailablefromanumber
of different manufacturers. These gloves, wraps, and wrist
supports are designed to reduce and moderate the effects of
extended vibration exposure and repetitive wrist trauma.
Sincetheyvarywidelyindesign,material,thickness,vibration
reduction,andwrist support qualities, itisrecommended that
the glove, tool wrap, or wrist support manufacturer be con-
sultedforitemsdesignedforyourspecificapplication.Proper
fit of gloves is important. Improperly fitted gloves may
restrict blood flow to the fingers and can substantially
reduce grip strength.
This information is a compilation of general safety practices
obtainedfromvarioussourcesavailableatthedateofproduc-
tion. However, our company does not represent that every
acceptable safety practice is considered herein, or that ab-
normal or unusual circumstances may not warrant or require
additional procedures. Your work may require additional
specific safety procedures. Follow these procedures as re-
quiredbyyourcompany. Formoreinformation,seethelatest
edition of ANSI B186.1, Safety Code for Portable Air Tools,
available from the American National Standards Institute,
Inc., 11 West 42nd Street, New York, NY 10036.
thethrottleisaccidentlyengaged.Useofaself-relievingvalve
within reach of the user of the tool is highly recommended.
Do not operate or trigger any percussion tool unless the
chisel, scaling tool, rivet set, or other implement is in the tool
andincontactwiththeworkpieceorworksurface.Neverpoint
any percussion tool in the direction of another person or
yourself, or deliberately eject a chisel. Failure to do so can
cause serious injury and/or damage the tool.
Chisel or rivet set retainers are recommended and furnished
asstandard equipment.Periodicinspection ofthe retainer
forwearordamageisrecommendedsincethesedevices
can receive heavy abuse, particularly if the tool is run off
the workpiece. Damaged retainers are dangerous, and
can allow the ejection of a chisel or other implement.
They must be replaced as necessary. Only use safety
retainer type chisels, as shown in the operating instruc-
tions and service manual. Also, it is good safety practice to
erect suitable barriers to protect persons in surrounding or
lower work areas from possible ejected tools.
Some individuals
may be suscep-
tible to disorders
of the hands and
arms when per-
forming tasks
consisting of
highly repetitive
motions and/or
exposure to ex-
tended vibration.
Cumulative
trauma disorders such as carpal tunnel syndrome and ten-
donitis may be caused or aggravated by repetitious, forceful
exertions of the hands and arms. Vibration may contribute to
a condition called Raynaud’s Syndrome. These disorders
developgraduallyover periods of weeks, months, andyears.
It is presently unknown to what extent exposure to vibrations
or repetitive motions may contribute to the disorders. Heredi-
tary factors, vasculatory or circulatory problems, exposure to
cold and dampness, diet, smoking and work practices are
Safety Recommendations
Repetitive work motions and/or vibration
may cause injury to hands and arms.
Use minimum hand grip force.
Keep body and hands warm and dry.
Avoid anything that inhibits blood circulation.
Avoid continuous vibration exposure.
Keep wrists straight.
Avoid repeated bending of wrists and hands.
WARNING!
BAD POSTURE
GOOD POSTURE
0
90
45
Self-Relieving
Valve
Filter
Regulator Lubricator
Tool
Hose
Coupling
INDIVIDUAL WORK STATION
Quick Disconnect
Coupling

4
OPERATING INSTRUCTIONS
CHISEL REMOVAL Turn off the air and drain the air
hosebeforeremovinganychiselor
implement.OnlyusednotchedB1-
C safety retainer chisels with B1-C scalers and notched
BR-CsafetyretainerchiselswithBR-Cscalers.(Seepage
6)
B1-C MODELS:
Turnofftheairanddraintheairhosebeforeattemptingto
removechisel.Pushthetangontheretainer,No.832956,
away from the barrel (as shown below) to remove the
chisel.
BR-C MODELS:
Turnoffairanddrainairhosebeforeattemptingtoremove
chisel. Rotate the retainer, No. 869314, 90°or 1/4 turn in
eitherdirection(asshownbelow)andtoremovethechisel.
Rotate the retainer back to its in-line position with the
barrel after chisel replacement.
The B1-C and BR-C series scalers are designed to oper-
ateon90psig air pressureusinga5/16"I.D.hoseupto8'
inlength.Ifadditionallengthisrequired,a3/8"I.D.orlarge
hose should be connected to the 5/16" hose.
The air hose should be cleared of accumulated dirt and
moisture,thenone-half(1/2)teaspoonof10Wmachineoil
shouldbepouredintothetool'sairinletbeforeconnecting
the hose to the tool.
IMPORTANT: The handle should be checked after the
first eight (8) hours and occasionally thereafter to make
sure it is tight.
LUBRICATION
Anautomaticin-linefilter-lubricatorisrecommendedasit
increases tool life and keeps the tool in sustained opera-
tion.Thein-linelubricatorshouldberegularlycheckedand
filled with a good grade of 10W machine oil. Never use a
heavy oil, as this will cause a loss of efficiency. Proper
adjustmentofthein-linelubricatorisperformedbyplacing
asheetof papernexttotheexhaustportsandholdingthe
throttleopenforapproximately30seconds.Thelubricator
isproperlysetwhenalightstainofoilcollectsonthepaper.
Excessive amounts of oil should be avoided.
If the operation of the scaler becomes sluggish or erratic,
pour one teaspoon of kerosene into the air inlet and
operate the tool for a few seconds. Lubricate the tool as
explained above after flushing.
STORAGE
Intheeventthatitbecomesnecessarytostorethetoolfor
an extended period of time (overnight, weekend, etc.), it
should receive a generous almount of lubrication at that
timeand again whenreturned to service.Store the toolin
a clean and dry environment. Alternatively, chippers and
scalers may be put in a bucket of kerosene or light oil for
extended periods of storage such as weekends or plant
shutdowns.
Neveruseaheavyoil,asthiswillcausealossofefficiency.
If the operation of the scaler becomes sluggish or erratic,
pour one teaspoon of kerosene into the air inlet and
operate the tool for a few seconds. Lubricate the tool as
mentionedaboveafterflushing.Thetoolshouldalwaysbe
lubricated before storage and when being returned to
service.
Eye protection must be worn when disassembling tool or when air line is turned on. A
self-relieving valve in close proximity to the repair station to bleed off air is recom-
mended.
WARNING
!
TURN 90°OR 1/4 TURN
TO RELEASE CHISEL
BR-C SERIES SCALER
PUSH TO
RELEASE CHISEL
B1-C SERIES SCALER
WARNING
!

5
SERVICE INSTRUCTIONS
DISASSEMBLY
To disassemble the tool, remove the chisel retainer clip
and clamp the flats of the barrel in a soft-jawed vise.
Loosenthehandlelockingring,No.832882,andunscrew
andremovethehandle.Note:Handledisassemblyinstruc-
tions are found on pages 8, 9, and 10.
After the handle has been removed, the valve assembly,
consisting of the valve block, No. 832508, valve, No.
832196, and valve block button, No. 832173, may be
removedfromthebarrel.Thevalveassemblyispositioned
together by the two (2) valve block pins, No. 844652. The
valve assembly may be pulled apart to inspect the valve.
After the valve assembly has been removed, invert the
barrel and allow the plunger to drop out.
Ifeitherthebarrelsleeveorthetoolnoseneedsreplacing,
they should be pressed out the rear of the barrel.
REASSEMBLY
Thetoolisreassembledinthereverseorderofdisassem-
bly.Wash allparts thoroughly in a solvent and inspect for
damageorwear beforereassemblingthetool.Besureall
air passages in the barrel and valve assembly are free of
any dirt or foreign matter.
NOTE:Thescreenbushingshouldbecheckedandeither
cleaned or replaced if necessary.
If the handle does not position as desired with respect to
the chisel position, one or more handle positioning spac-
ers,No.832947,maybeplacedbetweenthevalveassem-
bly and the handle. Use one spacer for about every 30
degreesdesired.Alwaystightenthehandleintothebarrel
until the valve assembly is tight against the barrel sleeve
andthentightenthelockingring,No.832882.Afterthetool
isassembled, pour a few dropsof 10W machine oil in the
inlet bushing to ensure immediate lubrication of the com-
plete tool.
ThingstolookforwhenrepairingB1-CandBR-Cscalers:
(1) Worn out buffer, No. 833527, used in the B1,which
iscausedbyoperatingthetoolwithoutanyresistance
against the chisel.
(2) Excessive wear in the tool nose.
(3) Worn or scored plunger usually caused by foreign
particles entering the tool.
(4) Worn or scored bore in the barrel sleeve caused by
foreign particles entering the tool.
(5) Rings worn in the wafer valve.
Eye protection must be worn when disassembling tool or when air line is turned on. A
self-relieving valve in close proximity to the repair station to bleed off air is recom-
mended.
WARNING
!

6

7
PART NO.
832173
832196
832508
832943
832944
832945
842801
844652
861732
869314
869315
NAME OF PART
Valve Block Button
Valve
Valve Block
Barrel Sleeve
Plunger
Tool Nose
Tool Nose Key
Valve Block Pin
Barrel (incl 832943, 832945, 842801)
Driver Retainer
Retainer Clip
QTY.
1
1
1
1
1
1
1
2
1
1
1
The complete valve block can be purchased as a subassembly using
part no. 831109.
BR-C SERIES SCALER
BR-C SERIES SCALER
PART NO.
832173
832196
832373
832508
832554
832700
832956
832963
833527
842801
844652
861735
NAME OF PARTS
Valve Block Button
Valve
Plunger
Valve Block
Retainer Clip
Barrel Sleeve
Driver Retainer
Tool Nose
Retainer Buffer
Tool Nose Key
Valve Block Pin
Barrel (incl. 832700, 832963, 842801)
QTY.
1
1
1
1
1
1
1
1
1
2
1
1
The complete valve block can be purchased as a subassembly using part no.
831109. NOTE: A heavy-duty retainer clip, no. 832654, is available as an
accessory, but this clip cannot be used with the needle scaler attachment.
B1-C SERIES SCALER
B1-C SERIES SCALER

8
DISASSEMBLY INSTRUCTIONS FOR PT HANDLE
DlSASSEMBLY
Todisassemblethehandle.pushthecontrollingvalvehandle
832610, to the full open position and slide off the throttle
valvecasingretainerring833600.Removethethrottlevalve
casing.Unscrewthescreen bushingandsetscrew,thatwill
release the throttle valve assembly. The controlling valve
handle 832610, and throttle valve casing lock nut 843645,
may now be unscrewed from the throttle valve casing if
necessary. The screen bushing should be cleaned and
inspected before reassembly.
REASSEMBLY
The handle is reassembled in the reverse order of disas-
sembly. When assembling the throttle valve always use a
new throttle valve seal 844302.
To adjust the throttle valve for the desired power, loosen
throttlevalvecasinglocknut843645,andscrewthecontrol-
ling valve handle to a position so that the desired blow is
deliveredwhenthehandleisfullycompressed.Thentighten
the throttle valve casing lock nut to secure the controlling
valve handle in this position.
PART NO.
832095
832600
832610
832807
832882
833600
834878
841554
843645
844302
NAME OF PART
Throttle Valve Casing
Throttle Valve (incl. 844302-0)
Controlling Valve Handle
Handle
Handle Locking Ring
Throttle Valve Casing Retainer Ring
Set Screw
Screen Bushing
Throttle Valve Casing Lock Nut
"O"- ring 5/32 " x 9/32"
QTY.
1
1
1
1
1
1
1
1
1
1
831219 —Complete handle includes (Part Nos. 832610 - 832807 - 832882 - 833600 - 841554 - 832095 - 843645 - 832600 -
844302 - 834878)
PARTS LIST —FOR PT HANDLE

9
DlSASSEMBLY
Unscrewing the throttle valve cap 832207, will allow the throttIe
vaIve spring 832078, and throttIe vaIve 834782, to be removed
fromthehandle.Usingasuitablepunch,driveoutthethrottlelever
pin 834848, and remove the throttle lever 834780.
The screen bushing 841553, may be unscrewed for cleaning and
inspection of the air screen.
REASSEMBLY
The handle is reassembled in the reverse order of disassembly.
The throttle valve seal 844302, should be replaced before reas-
sembly.
PART NO.
832078
832207
832882
832947
834780
834782
834848
841553
844302
869310
NAME OF PART
Throttle Valve Spring
Throttle Valve Cap(incl. "O"-ring)
Handle Locking Ring
Handle Positioning Spacer
Throttle Lever
Throttle Valve (incl. 844302)
Throttle Lever Pin
Screen Bushing
"O"-ring 5/32" x 9/32"
Handle
Handle subassembly 861731 includes —832078 - 832882 - 834780 - 834782 - 834848 - 841553 - 869310 - 832207)
* Number of spacers required is variable and are not included in the handle subassembly.
QTY.
1
1
1
*
1
1
1
1
1
1
DISASSEMBLY INSTRUCTIONS FOR C MODEL LT HANDLE
PARTS LIST —FOR C MODEL LT HANDLE

10
DISASSEMBLY
Todisassemblethehandle,pulltheregulatingvalvelocknut,No.832834,
away from the handle and turn in a counter-clockwise direction until the
regulating valve adjusting screw, No. 833616, can be removed. This will
allow the regulating valve cap, No. 833571, to be unscrewed. The nylon
sleeve, No. 865992, spring, No. 843262, throttle valve, No. 832091, and
the throttle valve pin, No. 832029, may now be removed from the throttle
valve casing, No. 832054.
Should it be necessary to replace the throttle valve casing, screw a 7/16-
20 bolt in the casing and using a suitable puller, remove it from the handle
The screen bushing, No. 841554, may be unscrewed for cleaning and
inspection of the air screen.
REASSEMBLY
The handle is reassembled in the reverse order of disassembly. Always
use new "0" rings to ensure a perfect seal.
PART NO.
832029
832054
832091
832128
832148
832211
832834
832882
832947
832948
833571
833583
833616
841554
843262
844301
844305
844307
865992
NAME OF PART
Throttle Valve Pin
Throttle Valve Casing
Throttle Valve (incl. 844301)
Throttle Lever Pin
Throttle Lever
Throttle Valve Pin Bushing
Regulating Valve Lock Nut
Handle Locking Ring
Handle Positioning Spacer
Handle (incl. 832211)
Regulating Valve Cap
Regulating Valve Spring
Regulating Valve Adjusting Screw
Screen Bushing
Throttle Valve Spring
"O"-Ring 1/8" x 1/4"
"O"-Ring 1/4" x 3/8"
"O"-Ring 3/8" x 1/2"
Nylon Sleeve
QTY.
1
1
1
1
1
1
1
1
**
1
1
1
1
1
1
1
1
2
1
PARTS LIST —BV HANDLE
DISASSEMBLY INSTRUCTIONS FOR BV HANDLE
831121
831411*
SUBASSEMBLIES
Handle
(Part Nos. 831411 * - 832029
832054 - 832091 - 832128 -
832148 - 832211 - 832882 -
832948 - 841554 - 843262 -
844307)
Adjusting Screw
(Part Nos. 832834 - 833571 -
833583 - 833616 - 844305 -
865992)
** Number of spacers required is variable and are not included in the backhead subassembly.

11
NOTES

Sales & Service Centers
Note: All locations may not service all products. Please contact the nearest Sales & Service Center for
the appropriate facility to handle your service requirements.
Dallas, TX Detroit, MI Houston, TX Lexington, SC
Apex Tool Group Apex Tool Group Apex Tool Group Apex Tool Group
Sales & Service Center Sales & Service Center Sales & Service Center 670 Industrial Drive
1470 Post & Paddock 2630 Superior Court 6550 West Sam Houston Lexington, SC 29072
Grand Prairie, TX 75050 Auburn Hills, MI 48326 Parkway North, Suite 200 Tel: 800-845-5629
Tel: 972-641-9563 Tel: 248-391-3700 Houston, TX 77041 Tel: 803-951-7544
Fax: 972-641-9674 Fax: 248-391-7824 Tel: 713-849-2364 Fax: 803-358-7681
Fax: 713-849-2047
Los Angeles, CA Seattle, WA York, PA Canada
Apex Tool Group Apex Tool Group Apex Tool Group Apex Tool Group
Sales & Service Center Sales & Service Center Sales & Service Center Sales & Service Center
15503 Blackburn Avenue 2865 152nd Avenue N.E. 3990 East Market Street 5925 McLaughlin Road
Norwalk, CA 90650 Redmond, WA 98052 York, PA 17402 Mississauga, Ont. L5R 1B8
Tel: 562-623-4457 Tel: 425-497-0476 Tel: 717-755-2933 Canada
Fax: 562-802-1718 Fax: 425-497-0496 Fax: 717-757-5063 Tel: 905-501-4785
Fax: 905-501-4786
Germany England France China
Cooper Power Tools Cooper Power Tools Cooper Power Tools SAS Cooper (China) Co., Ltd.
GmbH & Co. OHG GmbH & Co. OHG a company of a company of
a company of a company of Apex Tool Group, LLC Apex Tool Group, LLC
Apex Tool Group, LLC Apex Tool Group, LLC 25 rue Maurice Chevalier 955 Sheng Li Road,
Industriestraße 1 C/O Spline Gauges 77330 Ozoir-La-Ferrière Heqing Pudong, Shanghai
73463 Westhausen Piccadilly, Tamworth France China 201201
Germany Staffordshire B78 2ER Tel: +33 1 6443 2200 Tel: +86-21-28994176
Tel: +49 (0) 73 63 81 0 United Kingdom Fax: +33 1 6443 1717 Fax: +86-21-51118446
Fax: +49 (0) 73 63 81 222 Tel: +44 1827 8741 28
Fax: +44 1827 8741 28
Mexico Brazil Hungary
Cooper Tools Cooper Tools Industrial Ltda. Cooper Tools Hungaria Kft.
de México S.A. de C.V. a company of a company of
a company of Apex Tool Group, LLC Apex Tool Group, LLC
Apex Tool Group, LLC Av. Liberdade, 4055 Berkenyefa sor 7
Vialidad El Pueblito #103 Zona Industrial - Iporanga Pf: 640
Parque Industrial Querétaro 18087-170 Sorocaba 9027 Györ
Querétaro, QRO 76220 SP Brazil Hungary
Mexico Tel: +55 15 2383929 Tel: +36 96 66 1383
Tel: +52 (442) 211-3800 Fax: +55 15 2383260 Fax: +36 96 66 1135
Fax: +52 (442) 103-0443
823108/Printed in USA 05/2011/Copyright © Apex Tool Group, LLC
Apex Tool Group, LLC
1000 Lufkin Road
Apex, NC 27539
Phone: 919-387-0099
Fax: 919-387-2614
www.apextoolgroup.com
Other manuals for B1-C Series
1
This manual suits for next models
1
Table of contents
Popular Media Converter manuals by other brands
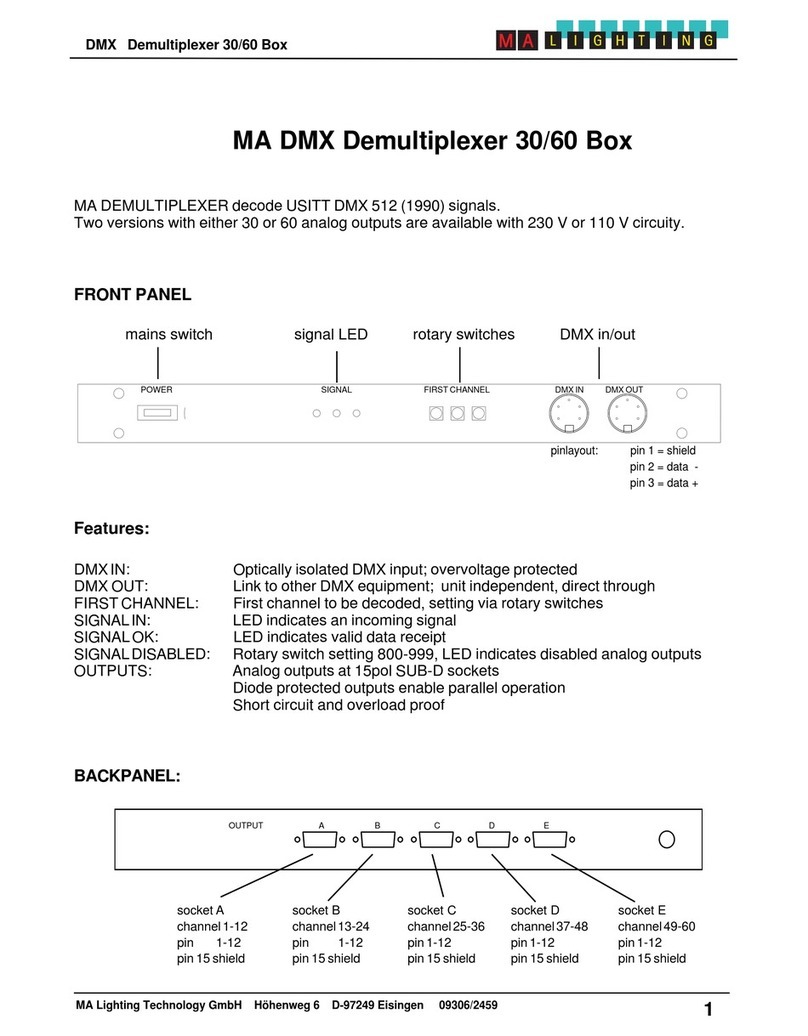
MA lighting
MA lighting Demultiplexer 30/60 Box Quick start quide
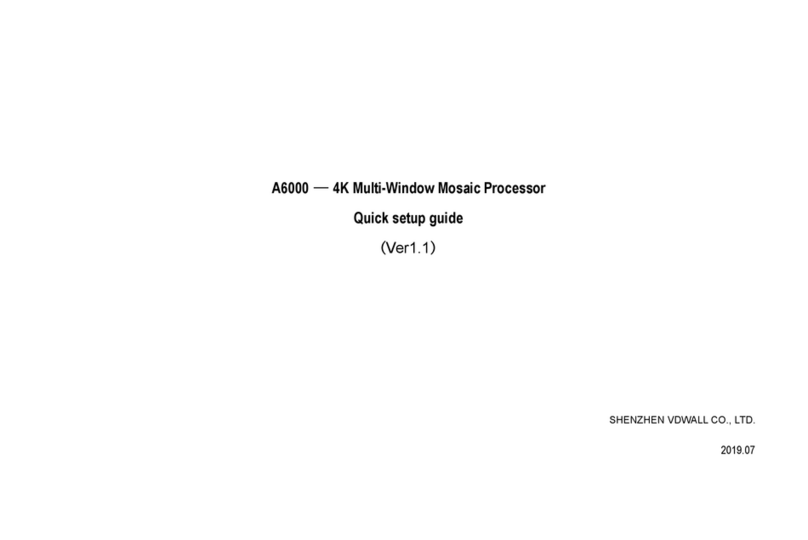
Shenzhen VDWALL
Shenzhen VDWALL A6000 Series Quick setup guide
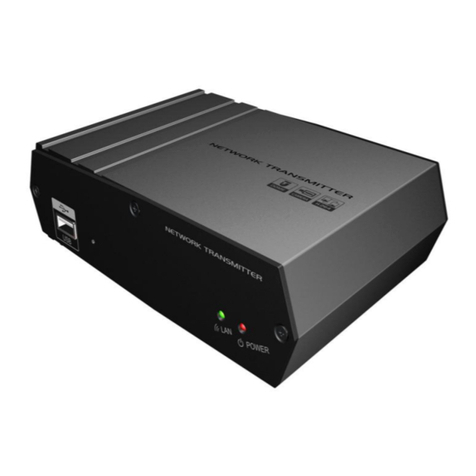
Vista
Vista VIP Kit2 VK2-ENCODER installation guide

Chicago Pneumatic
Chicago Pneumatic CP7120 Operator's manual

Icy Box
Icy Box IB-2536 user manual

Baumer
Baumer Hubner Berlin OG 70 Mounting and operating instructions