ClimateCraft MatrixMonitor V2 User manual

Installation,Operationand
MaintenanceManual
MatrixMonitor™V2
Thisistheinstallation,maintenanceandoperationmanualfortheClimateCraft®MatrixMonitor™airflowmonitoringsystem
forfanarrays.

MatrixMonitor™ IOM - Rev 4 - 4/11/2013 Page 1
Contents
Introduction .................................................................................................................................................. 3
...................................................................................................................... 3
Control Unit............................................................................................................................................... 3
Embedded Control System ....................................................................................................................... 3
Power Supply ............................................................................................................................................ 4
Key Pad Display ......................................................................................................................................... 4
Piezometric Pressure Port......................................................................................................................... 5
Fan Sensor................................................................................................................................................. 5
Fan Array Pressure Rise Sensor................................................................................................................. 7
User Interface ............................................................................................................................................... 8
Set Up Procedure ........................................................................................................................................11
Set the Array Data................................................................................................................................... 12
Set Up Array 1 .....................................................................................................................................12
Set the Number of Fans ...................................................................................................................... 12
Select the Fan Model .......................................................................................................................... 13
Select the Wheel Width...................................................................................................................... 14
Set the Array Name............................................................................................................................. 15
Set the Sensor Position ....................................................................................................................... 16
Set the Optional Dampers...................................................................................................................17
Set the Fan Status ...............................................................................................................................18
Set Up Array 2 .....................................................................................................................................19
Set the Control Data................................................................................................................................20
Scale the Flow Signal........................................................................................................................... 21
Scale the Pressure Signal ....................................................................................................................21
Select the Flow Units .......................................................................................................................... 22
Enable Modbus Communication with BMS ........................................................................................22
Set the Baud Rate for the RS485 communication line........................................................................23
Set Parity for the RS485 communication line .....................................................................................23
Set the device ID for BMS communication ......................................................................................... 24
Set the Vibration Alarm Limits............................................................................................................24
Grease Life Timer................................................................................................................................ 25
Starting the Grease Life Timer ............................................................................................................25
Set the real time clock ............................................................................................................................31
Time and Date.....................................................................................................................................31

MatrixMonitor™ IOM - Rev 4 - 4/11/2013 Page 2
Display Information..................................................................................................................................... 33
Display Airflow ....................................................................................................................................33
Display Individual Fan Details .............................................................................................................34
Display Time/Date...............................................................................................................................38
Communication Status........................................................................................................................ 38
Vibration Data..................................................................................................................................... 39
Motherboard Data..............................................................................................................................41
Lubrication Status ...............................................................................................................................41
Software Version................................................................................................................................. 42
Vibration Monitoring .................................................................................................................................. 43
Lubrication Monitoring ............................................................................................................................... 44
Throat and Cone Tap Flow Range ............................................................................................................... 46
Interface to Building Management System ................................................................................................47
Hard Wired Connections......................................................................................................................... 47
Modbus® Communications.....................................................................................................................48
Trouble Shooting Guide .............................................................................................................................. 54
Repair and Replacement............................................................................................................................. 58
Remove the Swing out Graphic Panel..................................................................................................... 58
Power Supply ..........................................................................................................................................59
Mother Board..........................................................................................................................................60
Clock Battery........................................................................................................................................... 61
Embedded Processor Board....................................................................................................................62
Keypad Display Unit ................................................................................................................................ 62
Fan Sensor............................................................................................................................................... 63
Array Pressure Rise Sensor .....................................................................................................................64
Replace or Install a Wiring Connector for an FSB ...................................................................................64
Replacement parts list ............................................................................................................................ 66
System Specifications.................................................................................................................................. 67
Sample Wiring Diagram ..............................................................................................................................68
Modbus® Register List.................................................................................................................................69
ClimateCraft® Service.................................................................................................................................. 75

MatrixMonitor™ IOM - Rev 4 - 4/11/2013 Page 3
Introduction
The ClimateCraft® is a digital instrument that monitors the operation of ClimateCraft®
FanMatrixfan arrays. A fan array will have two or more fans operating in parallel to provide airflow in
an air handling system. MatrixMonitorsolves the problems of monitoring the airflow of multiple fans
by combining the individual fan airflow readings into a combined reading for the array. MatrixMonitor
provides additional added value features to aid in the operation and maintenance of your fan array.
These features include fan failure detection, surge detection, vibration monitoring and lubrication
monitoring.
MatrixMonitor™ Components
Control Unit
The control unit contains the embedded control system, the
12VDC power supply and the keypad display unit. These parts
are enclosed in a polycarbonate NEMA 4X enclosure with a clear
hinged cover that allows visual inspection of the keypad display
unit while closed. The keypad display unit is mounted on a swing
out dead front panel. Opening the dead front panel allows
access to the embedded control system and power supply. The
parts in the control unit are described separately below.
Embedded Control System
The embedded control system used in the Matruses
a Rabbit® RCM3000 control module made by Digi International.
The control module is mounted on a custom motherboard that
provides all of the input and output connections. It is mounted on the back side of the swing out dead
front panel directly behind the keypad display unit. Swinging the panel out exposes the motherboard
and the control module that is mounted on it. The interface connections to the fan and pressure
transducers and the field connections to the building
management system (BMS) are made on the mother board
with the pull off terminal strips provided. This design provides
easy access to the wiring connections and internal components
of the control unit.
The control unit supplies power to the fan sensors and the
array pressure rise sensor and communicates digitally with
those devices over an EIA/TIA 485 2 wire multi-point
communication line. It can monitor one or two fan arrays with
as many as 49 fans in each array.
Control Unit
Embedded Control Module

MatrixMonitor™ IOM - Rev 4 - 4/11/2013 Page 4
A second EIA/TIA 485 (RS485) 2 wire multi-point communication line is provided for communication to
the building automation system (BMS) using the Modbus RTU protocol.
The control unit firmware is written to flash memory on the Rabbit RCM3000 module. It is self-
contained, universal and upgradeable on site
from set up menus accessed by the key pad display. There is only one active version of the firmware at
any given time and there are only a few parts necessary to make the system work. This makes it easy to
keep the system up and running with minimum number of spare parts. If your site has multiple air
regardless of how
varied the air handling units are in capacity and configuration.
Power Supply
system is a 100 watt Mean Well Direct model
RS-100-12. It is a switching power supply that
provides 12 volts DC to the embedded
control system, the fan sensor boards and the
array pressure rise transducers. It accepts
input voltage from 88 VAC to 264VAC at 47
Hz to 63 Hz. The power supply is mounted to
the backplane of the control enclosure. The
AC supply power connections are made
directly to the appropriate terminals on the
power supply.
WARNING
disconnected.
Failure to disconnect power before servicing can cause severe personal injury or death.
Key Pad Display
The key pad display unit has a backlit 122 x 32 pixel LCD graphic display, 7 signal
LEDS (1 red, 4 green, 2 yellow), and a 7 switch key pad. The unit plugs into the
backside of the motherboard through the onboard connectors.
The signal LEDS on the front of the key pad display unit are programmed to provide
specific information. The red LED is turned on if there is a fan failure. The 4 green
airflow analog output signal. The closer the actual array airflow is to the maximum
The first (left) yellow LED is turned on if one
Key Pad Display

MatrixMonitor™ IOM - Rev 4 - 4/11/2013 Page 5
or more fans go into surge. The second yellow LED (right) is turned on if the determines
that there is a problem in reading any of the transducers. If a transducer has gone bad or a signal has
reached the maximum making it impossible to calculate the actual flow or pressure this LED will be lit. It
will also light when the grease monitor trips or the fan vibration limits are exceeded.
The keys along with text prompts from the graphic display are used to configure the control to the
application through menu driven setup screens and display real time fan array performance information
screens.
Piezometric Pressure Port
The piezometric pressure port is a pressure tap that is usually inserted into
the throat of the fan inlet cone at its smallest diameter. The tap connection
fitting is on the high pressure side of the cone. The tap is piped from the
downstream side of the cone through the back plate of the fan so that
connection can be made to the pressure transducer located on the inlet
side of the fan air seal wall. If the design flow through the fan is higher than
the rating of the pressure transducer on the fan sensor board (FSB) an
alternate low pressure tap placed higher on the cone will be used. Only one
port will be connected to the pressure transducer on the FSB. The taps are
mounted on the inlet cone with the port end exposed to the flow side of
the inlet cone. They are press fit into the cone and the connection
side is on the
high pressure
side of the inlet cone. The fan sensors are mounted
on the inlet side of the fan back plate so the
pressure tubing that connects to the pressure tap is
routed to the inlet side of the back plate through a
bulkhead connector. The connection is made to the
low pressure side (negative side) of the pressure
transducer on the FSB. The high pressure side of
the pressure transducer is left open to sense the
fan inlet pressure. Throat and
Cone Tap Flow Range
information about when the throat tap or the cone tap should be
used.
Fan Sensor
The fan sensor is a custom assembly that contains the special MEMS pressure transducer, a temperature
transducer, a tri-axial accelerometer, and a high performance 32 bit RISC microcontroller to read and
process the transducer data and communicate with the host. The fan sensor board (FSB) has the
pressure transducer mounted on the top side and the components and connection points on the bottom
side. It is designed to mount on a standard 2 x 4 outdoor utility electrical box. The pressure transducer
Connection to Throat Tap
Location of Pressure Taps

MatrixMonitor™ IOM - Rev 4 - 4/11/2013 Page 6
ports are accessible for connecting to the piezometric port. The FSB acts as the box cover. When it is
removed the switches and connections are accessible.
The fan sensors are mounted on the entering air side of the fan back panel. There is one fan sensor for
every fan in the array. The low pressure port (-) of the pressure transducer is connected to the
is open to sense the air pressure at the inlet of the fan.
The fan sensor is mounted on the fan back plate so that the accelerometer can sense the fan vibration.
The FSB microcontroller continuously reads the tri-axial accelerometer data and performs a real time
FFT on the data stream to convert the information from the time domain to the frequency domain
where it can be analyzed. Each fan sensor has a temperature transducer and the host computer in the
control unit calculates the average of all of the sensors in the
array to determine the entering air density for the airflow
calculation. Only the system with the worst vibration needs to
be monitored, substantially reducing the data collection effort.
Each fan sensor board (FSB) is connected to the control unit
through a common dual twisted pair plenum rated cable
(Belden 1325A or equal). One twisted pair is used to supply
12VDC power to the FSB units. The other twisted pair is used
for digital communications between the FSB units and the
cable connection is made at the CPU which goes to the first
FSB on the chain. From there the cable goes to the next FSB
unit. This connection sequence continues until all if the FSB
units are connected. There is no need to maintain a particular
order of connection between specific FSB units because the
control unit can address each unit individually.
The connection from the cable to the FSB unit is
made with a 4 position feed through insulation
displacement connector. The cable wires run
unbroken from the control unit to the last FSB unit
on the chain. This insures the reliability of the
connections. Each twisted pair is foil wrapped and
there is a tinned copper bleed wire running through
the cable in continuous contact with the foil shields
on each twisted pair. At each FSB connection box
the cable jacket and the foils shields are removed to
give access to the conductors. The bleed wire is
never cut. It is connected to ground in the control
unit and runs continuously to the end of the cable where it is left unattached. Each 4 pin conductor has
Fan Sensor

MatrixMonitor™ IOM - Rev 4 - 4/11/2013 Page 7
a strain relief cover attached to keep incidental wire movement from pulling on the connection pins
which insures a good electrical connection between the cable conductors and the connector.
There is a dual DIP switch mounted on the component side of the FSB assembly. This switch is to
activate the line termination resistors.
NOTICE
The dual Dip switches should be in the off position on all of the FSB units except for the
last unit on the cable.
The last FSB unit on the cable should have the switches turned on to tie in the line termination resistors.
It is possible (but not necessary) to have two cables run out from the control unit. A unit with two arrays
might be wired where one cable goes to a first array and the second cable goes to the second array. This
architecture is important when large numbers of fans are used because it increases the ability to deliver
power to the FSB units. When two cables are used the line termination switches must be switched on
for the FSB units on the end of each line. In this case the FSB line termination jumpers on the mother
board in the control unit must be removed.
There are two rotary switches mounted on the component side of the FSB units. These switches provide
the FSB unit with an ID which it uses to communicate with the control unit. These switches must be set
in a specific sequence for the MatrixMonitorto function properly. For array 1, the fan sensor switches
49. The FSB unit on fan 1
reserved for the array pressure rise sensor (see below). Each fan must have a fan sensor. The numbering
If the MatrixMonitorcontrol unit is tied to a second fan array, as might be the case if the AHU has a
reserved for fan array 2. ID 50 is reserved for the pressure rise sensor of the second fan array. To get the
switch setting for the FSB units in fan array 2 simply add 50 to the fan number. Otherwise the
sequencing and restrictions are exactly the same as for fan array 1.
Fan Array Pressure Rise Sensor
The same FSB assembly used for the fan sensor is also used for the fan array
pressure rise sensor. The pressure rise sensor is mounted to the fan air seal wall
on the air inlet side. The high pressure port (+) of the pressure transducer is
connected to the downstream side of the fan air seal wall with flexible tubing to
a bulkhead connector. The low pressure port is left open to reference the air
pressure entering the fan array.
Each array connected to the MatrixMonitorcontrol unit must have a pressure
sensor. The switch setting for the pressure rise sensor on array 1 is 00. If there
is a second array connected to the

MatrixMonitor™ IOM - Rev 4 - 4/11/2013 Page 8
The pressure rise sensor FSB units are connected to the connection cable in exactly the same manner as
the fan sensor FSB units. They do not need to be located on the cable in any particular order.
User Interface
MatrixMonitoruses a hierarchical menu structure
to allow the user to access the considerable amount
of information available about the performance of
the fan array and to configure the unit to any
conceivable ClimateCraft® fan array.
When the unit powers up a sign on message appears.
The sign on message will display the ClimateCraft®
logo and the message string ClimateCraft
MatrixMonitor V2.nn scroll horizontally across
the screen from left to right. The last letters in the
scrolling message are the version level of the
software that is installed on your equipment.
MatrixMonitor is fully functional while this screen is
up and will perform all of its monitoring and
communication functions. Communications with the
building management system (BMS) are active.
The keys have graphic symbols on them that are designated in the software with the following meaning:
= Left -= minus 1 + = plus 1
= enter
These keys along with prompts given on the graphic display allow you to navigate the menu structure of
the MatrixMonitorin order to set up the system and display the performance information for the fan
arrays it monitors.
There are seven signal LED lamps on the front of the keypad display unit that
provide valuable information about the fan array. See the section above titled
“Key Pad Display” for a detailed description about the function of the signal
LEDs.
Press the(enter) key when the sign on message is active and you will get the main menu screen.

MatrixMonitor™ IOM - Rev 4 - 4/11/2013 Page 9
The main menu is the highest menu in the structure and is your starting point for navigating through the
display and set up screens. The main menu of the is as follows:
Menu Lines Displayed ……………….. Screen Type (Screen Function)
<<< Main Menu >>>
1. Display Airflow (Airflow, Pressure Rise, Temperature, Fan Speed)
2. Array 1 Fans (Airflow & Piezometric Pressure by fan for array 1)
3. Array 2 Fans (Airflow & Piezometric Pressure by fan for array 2)
4. Array 1 Options Setup submenu (Fan set up data for array 1)
5. Array 2 Options Setup submenu (Fan set up data for array 2)
6. Control Setup Setup Submenu (Control set up data)
7. Clock Settings Setup Submenu (Set time and Date)
8. Display Time and Date (Current Time and Date)
9. Comm Status (Communication performance overall & each FSB)
10. Array 1 Vibration (Peak vibration levels per fan for array 1)
11. Array 2 Vibration (Peak vibration levels per fan for array 2)
12. Mother Board Data (Board temp, barometric press, FSB current & volts)
13. Grease Life Data (Airflow, Pressure Rise, Temperature, Fan Speed)
14. About (Sign on message with firmware version number)
Only 4 lines of data will fit on the graphic display so 11 of
the 15 lines of data are not visible. Use the keys
to scroll through the main menu and expose all of the
menu items. As you scroll through the menu, the display
will invert the pixels for an individual menu line as you
scroll. In this text we will refer to that line as the
. There are four types of screens used
Submenu screens, and Setup screens. When you are in
the main menu or on any sub-menu, pressing the
(enter) key will close the menu you are in and open the
display, setup, or submenu screen that was highlighted.
Display screens are used to display useful information
about the performance for the fan arrays) attached to
The lay out and data presented
vary by screen type and function. Pressing thekey when on any display screen, will close the current
display screen and return to the main menu. On the display screens that provide data for individual fans
Array 1 Options and keys are used to scroll between fans. When multiple
Array 1 Vibration) the and
scroll between data items. Each screen will give specific instructions on the navigation keys used in that
display function. The instructions are on the bottom 1 or 2 lines of the display.

MatrixMonitor™ IOM - Rev 4 - 4/11/2013 Page 10
Submenu screens are used for set up functions to simplify the collection of data. They allow branching
to setup screens for entering individ
the array(s) used with it. The submenu screens function in the same way as the main menu screen. In
order to exit a submenu screen and return to the main menu the last menu item in each submenu
Return to Main (enter) key to return to
the main menu. At the time you exit any submenu screen and return to the main menu, the set up data
collected will be saved to flash memory set up files. You will be able to see this because the display will
Saving SettingsThese files are read when the
MatrixMonitor powers up so the system
knows the configuration of the fan array(s).
Setup screens are used to input the data
the attached fan arrays and control
environment. They are used to set the time
and date of the real time clock, to set the
vibration alarm limits and reset the grease life
monitor. The setup screens are accessed
through the main menu or a submenu and are
used to select a single configuration or
sequential data points. The + and keys are
used to scroll through data selections or enter
numbers. The(enter) key is used to select
that data choice and return to the main or
submenu. When thekey is pressed the data selected by the setup screen becomes live data and is
immediately used in any ongoing calculations, alarm checks, or data collection processes.
NOTICE
reads data from the sensors, computes the airflow and other performance information, sets the analog and
relay outputs and maintains communications with the BMS. When any of the set up screens is active, these
functions are suspended until the setup procedure is completed.
On the setup and display screens, there will be information prompts to aid you in navigating through the
screens to get the information you are looking for and to tell you how to change the set up information.
These prompts will be on the third or fourth line of the display and will interactively change depending
on the key strokes you make.

MatrixMonitor™ IOM - Rev 4 - 4/11/2013 Page 11
Set Up Procedure
M for the fan array(s) and building management system it is used
with. Each fan array has a unique collection of fans and options. This information must be input into the
factory installed the configuration is done at ClimateCraft® before the unit is shipped. The only thing
that might be required to do on the job site would be to set the local time and to set the scaling factors
for the analog output signals if they are used by the building management system (BMS).
If it is necessary to replace the Rabbit RCM3000 control module it will be necessary to configure the
system after the module is replaced. The setup data is stored in the flash memory of the control module
and will be lost when the replacement is made. When the firmware is installed default setup data for a
basic one array and one fan unit is stored in the setup data file in flash memory.
This section will step you through the set up process. Make sure to read the
above before you attempt to do the set up. It will explain the conventions used and menu structure
employed. It is not necessary to execute the complete set up procedure if all of the set up data does not
need to be modified. If you need to change a
specific data item you can use the menu structure
to go directly to the specific setup screen you need,
update the information, and return without
changing anything else. For practical purposes, this
section is written as though you were doing a
complete set up on a new system.
If you need to check what configuration data is
step
through the set up screens to see the data entered.
The set up screens will always display the
information currently used.
There is a substantial amount of information
required to complete this setup. All of this
information is available in the submittal information shipped with the unit. If you do not have the
submittal call ClimateCraft® customer service for a copy or make a request providing unit tagging and
serial number via our website at www.climatecraft.com.
NOTICE
Remember! When the set up screens are active in the user interface the main functions of the
them!

MatrixMonitor™ IOM - Rev 4 - 4/11/2013 Page 12
Set the Array Data
The array data setup is accomplished through by using the Array 1 OptionsArray 2 Options
Array 1 OptionsAll of the setup
The default setting for Array 2 is 0 fans. it needs to look at only one
fan array and some of the display screens and setup screens are altered to simplify the layout for
displaying information for just one array instead of two. If there is only one array attached to the control
Set Up Array 1
4. Array 1 Options
Press the(enter) key and the Array 1 Options
Menu Lines Displayed ……………….. Screen Type (Screen Function)
<< Array 1 Options >>
1. Number of Fans (sets the number fans in the array)
2. Fan Model (selects the fan model used in the array)
3. Wheel Width (selects the wheel width of the fans)
4. Array Name Setup (assigns a name for the array)
5. Sensor Position (selects the piezometric tap location-throat or cone)
6. Dampers (assigns backdraft dampers to the array)
7. Set Fan Status (sets the operational status of each fan in the array)
8. Return to Main
You can navigate from this submenu screen to enter all of the setup information for array 1.
Set the Number of Fans
The number of fans on Array 1 can be set from 1 to 49 fans. MatrixMonitor will poll the FSB
communication has been lost to the fans FSB and flag an error. If the number entered is smaller than the
all of the FSBs and the airflow calculation will be incorrect. This
setting needs to be the total number of fans in the array even if
Set the Fan Status
You can count the fans to get this information. It is also available
in the submittal documents for the air handling unit on the fan
performance data sheet. If there is more than one array in the air
handling unit make sure you identify the correct performance
data sheet.

MatrixMonitor™ IOM - Rev 4 - 4/11/2013 Page 13
Array 1 Options2. Number of Fans(enter) key and the
fan quantity setup screen will appear. The first line on the screen will display the array name if it has
Fan Array 1Select the Array Name. The
Select Number of Fans: 1l reflect the
current setting. The default setting for the number of fans is 1. If the controller has been previously set
up some other number may appear.
The bottom two lines are the navigation aids. Use the + and - keys to select the correct number of fans.
When you press the keys the displayed number at the end of line two will change reflecting the current
selection. The number will scroll between 1 and 49 and wrap around these values. A + keystroke when
the display shows 49 will result in a display of 1. Similarly, a keystroke when the display shows 1 will
result in a display of 49. Holding either + or - key down for over 1 second will result in a fast scroll mode.
When the displayed number on line 2 is correct press thekey to confirm the selection and return to
the submenu. The change in the number of fans will take effect as soon as control is passed to the
submenu screen.
Select the Fan Model
This selects the Fanse the
appropriate flow constants and fan data stored in the softwcan
calculate the correct airflow, surge curve and backflow from the piezometric port pressure readings.
This information is available in the submittal
documents for the air handling units. It will be on
the fan performance data sheet. Make sure you
identify the correct fan array if there is more than
one in the unit.
Array 1 Options
2. Fan Model(enter) key and the
fan model setup screen will appear. The first line
on the screen will display the array name if it has
been set. The default name setting for array 1 is
Fan Array 1
second line on the screen will read Model = 12 x
100
form of the fan model number. The number
before the x is the nominal fan wheel diameter.
The number after the x is the wheel width
expressed as a percentage of the width of a full width wheel. The default valu12 x
100
previously set up some other model number might appear but the structure will be the same. This
screen will not affect the wheel width portion of the model number. That information is adjusted in the
next menu selection (3. Wheel Width)

MatrixMonitor™ IOM - Rev 4 - 4/11/2013 Page 14
The bottom two lines are the navigation aids. Use the + and - keys to select the nominal fan diameter.
When you press the keys, the number displayed after the = and before the x will change reflecting the
current selection of nominal fan wheel diameter. The number will scroll to display all of the nominal fan
diameters currently available on ClimateCraft® fan arrays. It will wrap around these values.
When the model displayed on line 2 is correct, press the(enter) key to confirm the selection and
return to the submenu. The change in the model will take effect as soon as control is passed to the
submenu screen.
Select the Wheel Width
This selects the wheel width of the fans installed in the fan array. This data is used to select the correct
measured on each fan. It compares the airflow of each fan to the others and uses the array pressure rise
information to determine if a fan is operating in surge. If a fan is found to be in surge, the control will
stored values for surge curves to help determine
if a fan is in surge. It needs to know the wheel
width in order to select the proper surge curve.
partial width wheels to achieve high static
pressure at relatively low flow rates where full
width wheels might be in surge.
NOTICE
If the wheel width input is not set
properly, MatrixMonitor might improperly
identify fans operating is surge.
This information is available in the submittal documents for the air handling units. It will be on the fan
performance data sheet. Make sure you identify the correct fan array if there is more than one in the
unit.
Array 1 Options, scroll down to 3. Wheel Width(enter)
key and the wheel width setup screen will appear. The first line on the screen will display the array
Fan Array 1Array
Wheel Width = 100
the current selection for wheel width. The default value is 100. This may display some other value if the
control unit has been previously set. The number represents the width of the wheel as a percentage of a
full width wheel. 100 would be a full width wheel and 50 would represent a wheel width that is 50% of
the full width wheel.

MatrixMonitor™ IOM - Rev 4 - 4/11/2013 Page 15
The bottom two lines are the navigation aids. Use the + and - keys to select the wheel width. When you
press the keys the number displayed after the = will change reflecting the current selection of nominal
fan wheel width. The number will scroll between 50 and 100 in increments of 5 and will wrap around
these values.
When the width displayed on line 2 is correct, press the(enter) key to confirm the selection and
return to the submenu. The change in wheel width will take effect as soon as control is passed to the
submenu screen.
Set the Array Name
The array name feat
Fan Array 1Fan Array 2
meaning to the function of the individual fan arrays installed in a unit and make it difficult to follow
Fan Array 1
display and setup screens can be selected from the following group:
Supply Fan Array
Return Fan Array
Exhaust Fan Array
Outside Fan Array
Fan Array 1
Setting this value is optional. It is not necessary for the control to function properly. It is recommended
if more than one array is monitored by the same control. It makes the data screens clear and easy to
use.
From Array 1 Options
4. Array Name
key and the array name setup screen will appear.
name selected from one of the labels above. The
Fan Array 1. (The default value
Fan Array 2 will be displayed
if the control has not been previously set up.
The bottom two lines are the navigation aids. Use
the + and - keys to select the array name. When
you press the keys, the description displayed on
line 2 will change reflecting the current selection
of the array name. Array 2 has the same selection
set of names available to use. Since it is undesirable to have two fan arrays with the same name on the
same air handling unit, the name selections between array 1 and array 2 are interlocked. If a name,
other than the default, is selected for array 1 that name is not available for selection for array 2. The

MatrixMonitor™ IOM - Rev 4 - 4/11/2013 Page 16
reverse is also true. If a name has been selected for array 2 that name will not be available for selection
for array 1. If a name is not available it will not show up as you scroll through the name selections.
When the array name displayed on line 2 is correct press the(enter) key to confirm the selection and
return to the submenu. The change in array name will take effect as soon as control is passed to the
submenu screen. If you enter or re-enter any of the Array 1 Options set up screens the first line of the
screen will now display the array name you just selected.
Set the Sensor Position
This selects the position of the piezometric flow tap.
The MEMS pressure transducer used on the FSB
assemblies to monitor the piezometric pressure
depression has a range of 0 to 14 inches WC. The
velocity increases and the static pressure decreases
as it flows through the cone until the minimum
diameter is reached. There is a well-defined
mathematical relationship between the geometry of
the inlet cone, the pressure depression at any point
along the cone and the air flowing through the cone.
By placing a static pressure probe at some point in
the inlet cone and measuring the pressure depression
between that probe and the fan inlet, the airflow can
be calculated.
In most cases 0 to 14 inches WC is sufficient for fan operating conditions used .
ClimateCraft® fans have the pressure tap installed at the minimum diameter, or throat, of the inlet cone
so that the maximum pressure signal is available. If a fan is expected to have abnormally high flow, the
piezometric pressure depression may be higher than 14 inches WC and outside of the range of the
sensor. In those cases, the tap is installed in the cone at a location before the minimum diameter
allowing the FSB pressure transducer to stay in range.
NOTICE
being used.
You can inspect the fans to determine which connection is made or you can get this information from
the bottom of the sheet. A sample of the wiring diagram is in the appendix of this manual. There may be
more than one fan array in the air handler so make sure you identify the correct wiring diagram for this
array. Throat and Cone Tap Flow Rangee basic information about
when the throat tap or the cone tap should be used.

MatrixMonitor™ IOM - Rev 4 - 4/11/2013 Page 17
Array 1 Options5. Sensor Position
(enter) key and the sensor position setup screen will appear. The first line on the screen will display the
array name. It should have been set in a Sensor
Loc = Throat. The description after the = sign is the current selection for the sensor location. The
ThroatThroatCone
The bottom two lines are the navigation aids. Use the + and - keys to select the sensor location. When
you press the keys the description displayed after the = will change reflecting the current selection of
the sensor location.
When the location displayed on line 2 is correct press thekey to confirm the selection and return to
the submenu. The change in sensor location will take effect as soon as control is passed to the submenu
screen.
Set the Optional Dampers
This sets a flag if back flow prevention dampers are installed. The dampers can be a control damper or
gravity operated back draft damper. The flag is either Yes or No for the entire array. This flag is used
when a fan failure is detected. If a back draft damper is not installed air back flows through a fan that is
off or has failed. The amount of air that back flows is calculated and then subtracted from the sum of
the flows from the operating fans which gives a true calculation of the airflow delivered by the array. If
back draft dampers are provided, the flow, in the fans that have failed or are turned off, is set to zero
and there is no air back flowing through them.
Array 1 Options
6. Dampers(enter) key
and the damper setup screen will appear. The first
line on the screen will display the array name. It
should have been set in a previous step. The second
Fan Dampers? = No
The description after the = sign is the current
selectionNo
NoYes
The bottom two lines are the navigation aids. Use
the + and - keys to YesNo. When you
press the keys the description displayed after the =
will change reflecting the current selection of the
backdraft damper flag.
When the backdraft damper flag displayed on line 2 is correct press thekey to confirm the selection
and return to the submenu. The change in sensor location will take effect as soon as control is passed to
the submenu screen.

MatrixMonitor™ IOM - Rev 4 - 4/11/2013 Page 18
Set the Fan Status
correctly calculate the array airflow in the event that it
detects a fan is not operating and to properly set the fan failure alarm. The control unit monitors the
piezometric port pressure of each fan. When a fan fans not operating, the port pressure is considerably
lower than the other fans in the array which tells the control unit that the fan is not running.
The internal data stored for each fan model allow the control unit to calculate the amount of air flowing
backwards through the fan when it is not operating. Matrix monitor knows a back flow prevention
a fan is not operating.
If the fan statOn
alarm. A fan failure alarm will turn on the fan failure relay, light the red LED lamp on the keypad and
respond to a BMS inquiry that a fan failure has occurred. The calculated backflow will subtracted from
the flow totaled from the rest of the fans if back flow prevention dampers are not installed. If dampers
are installed, the flow for this fan is set to 0.
Offassumes that the fan is off for a reason and does not set a
fan failure alarm. The calculated backflow will subtracted from the flow totaled from the rest of the fans
if back flow prevention dampers are not installed. If dampers are installed, the flow for this fan is set to
0.
Blanked Off
assumes that the fan is off and a blank off plate has
been installed on the inlet to prevent backflow. The fan
failure alarm is not set and the flow for the fan is set to
0.
The OnOffatus is
for the user to inhibit the fan failure alarm. This is useful
after the failure has been acknowledged to clear the
alarm. It is also useful if a fan has been shut down for
capacity or maintenance purBlanked Off
status is for the same purpose but allows the control to
calculate array airflow correctly when the fan has a
blank off plate installed.
Array 1 Options7. Set Fan Status
(enter) key and the fan status setup screen will appear. The first line on the screen will display the array
Fan 1: On
The number before the colon (:) is the selected fan. This can be scrolled through all of the fans in the

MatrixMonitor™ IOM - Rev 4 - 4/11/2013 Page 19
array so that the status of each fan can be set individually. The description after the colon (:) is the
OnOn OffBlanked Off
The bottom two lines are the navigation aids.
number before the colon (:) will change when the keys are pressed changing the fan selection.
Use the + and - OnOffBlanked Off- keys the
description displayed after the colon (:) will change reflecting the current selection of the fan status flag
for the selected fan.
If the status of more than one fan needs to be changed, repeat this procedure until the status of all fans
is correct.
When you have finished adjusting the fan status flags press the(enter) key to confirm the changes
and return to the submenu. The fan status flag changes will take effect as soon as control is passed to
the submenu screen.
Return to Main Menu
Array 1 Options8. Return to Mainress the
(enter) key to return to the main menu. Before the systems transfers control to the main menu it saves
the array set up option data to a setup data file in the flash memory of the Rabbit RCM3000 control
Saving Settingshis.
Set Up Array 2
The set up procedure for Array 2 is almost identical to the
procedure for Array 1 so the instructions will not be duplicated
here. Instead we will describe the minor differences between
the set of Array 1 and Array 2.
The difference between Array 1 and Array 2 is that the number
of fans in Array 2 can be set to 0 and this setting affects the
way the control behaves. One is the minimum number of fans
in Array 1. Zero is the default value for the number of fans in
Array 2. When the number of fans in Array 2 is set to 0, the
control unit inhibits the display of any data for Array 2 and will
not allow any option data to be set. If you attempt to enter
any Array 2 set up screens when the number of fans is set to 0
you will get the following message:
Array2 : Not Set Up!
Select the Number of
Fans First!!
Any Key to Continue
Table of contents
Popular Measuring Instrument manuals by other brands

Televes
Televes 593501 instruction manual
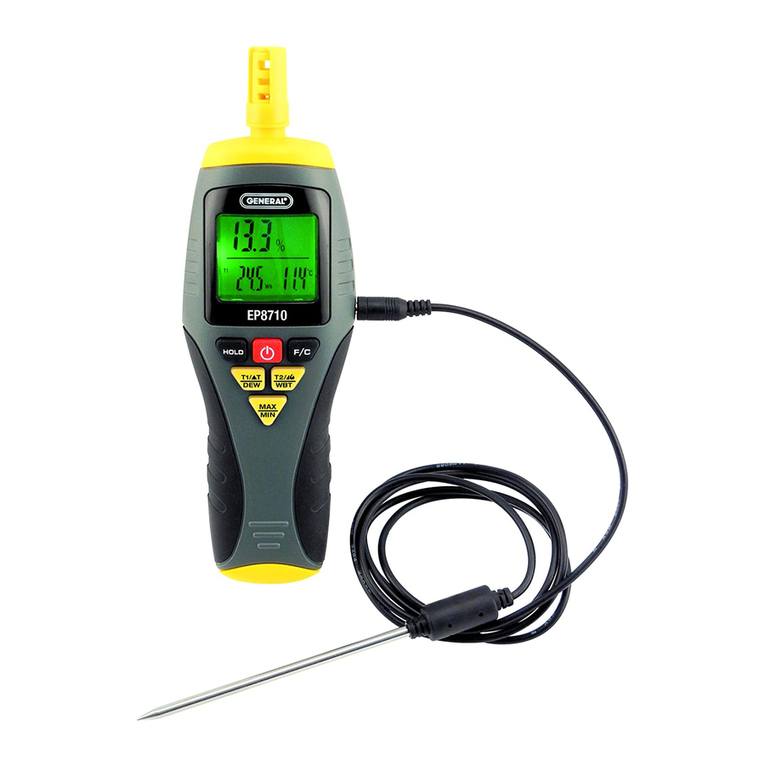
General
General EP8710 user manual

Büttner Elektronik
Büttner Elektronik Dometic MT iQ Basic Pro Installation and operating manual
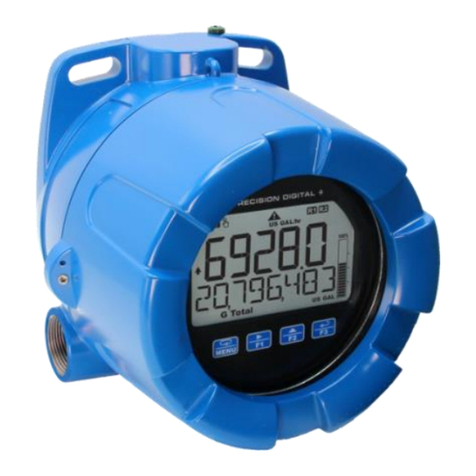
Precision Digital Corporation
Precision Digital Corporation PD6900 Series instruction manual
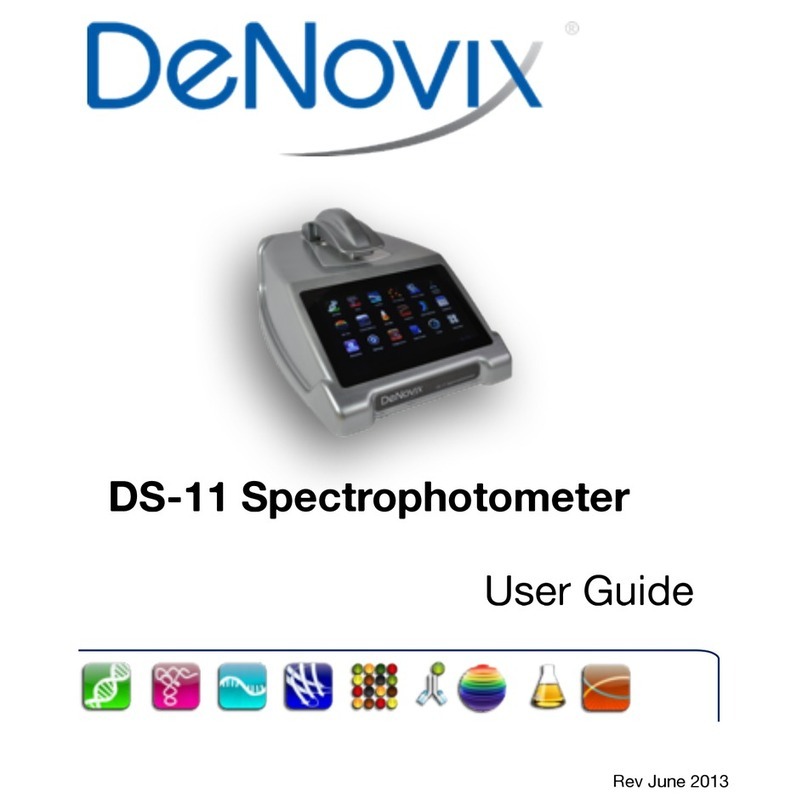
DeNovix
DeNovix DS-11 Series user guide
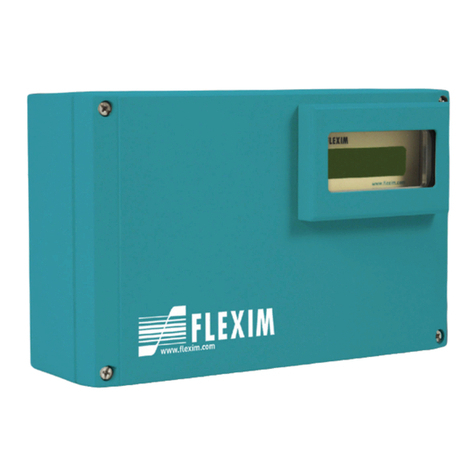
Flexim
Flexim PIOX S502ID Operating instruction