CMP Panther 55-0045 User guide

1
MODEL 55-0045
MOTOR LIFT
INSTALLATION
AND
OPERATING INSTRUCTION
For outboards up to 35HP weighing up to 263 pounds.
This motor lift is designed for clamp screw type outboards only.
651.486.2010
MARINETECH PRODUCTS, INC
1360 East County Road E
VADNAIS HEIGHTS, MN 55110
www.marinetechproducts.com
REV 12/15
99-55288
1.604.940.2010 | sales@cmpgroup.net

2
INTRODUCTION
Congratulations, you have just purchased one of the finest auxiliary outboard motor lifts available
today. With proper installation and care, this motor lift will provide you with years of trouble free use
and performance.
Please take a few moments to review the information contained in this booklet to familiarize yourself
with the installation procedures suggested to successfully mount your new motor lift. Installation is
easy particularly when you know each step ahead of time.
BEFORE USING YOUR MOTOR LIFT READ THE OPERATING TIPS (PG. 10) FOR
PRECAUTIONS WHEN USING YOUR MOTOR LIFT ON THE WATER AND WHEN
TRAILERING YOU BOAT
MOTOR LIFT OWNER’S MANUAL
Warning! Completely read and understand these instructions before attempting to install and use
this motor lift. Harm to you and damage to your boat could occur if you do not follow these directions.
Safety precautions should be adhered to when removing and installing the motor to install this motor
lift.
-If you have questions and feel that you can not properly install this motor lift … STOP
immediately and call us at 651-486-2010.
Failure to follow these instructions exactly could result in permanent damage to your hydraulic
pump.
-DO NOT connect large red and black cables from the pump relay harness to the battery until
all other installations are complete.
If you encounter problems after installation is complete, please refer to our “Troubleshooting” section
in the back of the manual.
If you have questions call 651-486-2010.
KEEP THIS MANUAL WITH THE BOAT FOR FUTURE REFERENCE.
MAINTENANCE
To keep motor lift operating properly, follow all maintenance procedures in this manual.
-Maintain fluid level to bottom of fill plug on engine side of pump reservoir.
-Before each and every use, check the mounting bolts at motor plate engine side and transom
side.

3
GETTING STARTED
Here is a Parts List followed by a list of the tools, equipment, hardware & supplies that you will need:
PARTS LIST
[1] Motor Lift
[2] Pump relay harness
[3] Relays (2)
[4] Rocker switch assembly with wiring harness
[5] Spacer Block (Shim)
[6] Manual
[7] Safety Cable
Tools and Equipment:
1. Electric drill with 1/8, 3/16, 3/8 and 1/2 inch drill bits
2. Two ¾ inch wrenches
3. A Phillips head screw driver
4. For heavier motors, a hoist to lift the motor while installing the bracket
Hardware and Supplies: (not included)
4 –½ inch diameter stainless steel Hex Cap Screws of the appropriate length***
4- ½ inch stainless steel Nylon insert nuts
8 –½ inch stainless steel flat washers
1 –Tube of clear RTV silicon for sealing the transom mounting holes (recommended)
1 –Tube of dielectric grease for the electrical connections (recommended)
2 –Security bolts that match the clamp bracket on your motor (recommended)
*** For proper bolt length selection see the information on the following page. ***
CAUTION! On the hydraulic motor, DO NOT make an electrical connection to the boat’s
battery until all of the following steps are followed and you are instructed to do so in section (Making
Electrical Connections). Failure to follow these instructions could result in an electrical short or
damage to the hydraulic motor and/or boat components.

4
BEFORE STARTING
Selecting the Mounting position
The Panther Model 45 Motor Lift is designed so that the motor must be mounted near or at the top of
the transom. The unit should be mounted so that the prop will have sufficient depth when the motor is
lowered into the water. Once you have selected the best mounting position, be sure to check inside the
transom to make sure that there is adequate clearance for the bolts and nuts and that the transom is
sufficiently reinforced for mounting the bracket.
How to measure for transom mounting bolts
Because each transom is different, you will need to determine the right length of mounting bolts. For
installations where mounting holes will be drilled, you can take this measurement after the holes have
been drilled. Simply measure the thickness of the transom and add 2 inches.
Make sure motor hoses and cables are long enough for set back
This motor lift bracket places your outboard several inches farther away from the controls, battery and
gas tank. Check to make sure that each of these cables and hoses has the required amount of slack. An
easy way to check this is to unclamp the outboard from the boat and secure it to an engine hoist.
Simply move the motor hoist back several inches with all of the hoses and cables still connected. If it
can be moved so that there is adequate slack in the cables, the motor lift will work.
MOUNTING THE MOTOR LIFT BRACKET
1. Hold the bracket in the selected location on the transom. Check to make sure that the hole
placement will not interfere with any moldings, rivets, etc.
2. Make sure the bracket is level. Once positioned, use the transom plate as a template and mark
two upper and the three lowest holes. The three lowest holes MUST be used. The bottom hole
must be flat against the mounting surface. The entire lower tab mount must make contact with
the boat.
3. Using a 3/16 bit, drill a pilot hole in each location to make sure the holes are properly aligned
and that there will be no interference with the mounting bolts. Finish drilling the holes with a
½ inch drill bit.
4. Before mounting the unit, apply a bead of RTV silicone sealant around the edge of each hole to
insure a watertight seal.
5. To mount the Motor Lift bracket to the transom use five ½ inch diameter stainless steel bolts
with washers and nylon locking nuts. Start by placing a bolt with a washer into each of the
upper mounting holes. Stick a piece of tape over the head of each bolt to hold them in place,
then lift the unit up to the transom, align the bolts and slide the unit into place. Install the
washers and the nuts inside the boat. Do not tighten the nuts completely until the lower bolts
have been installed.
6. Complete the installation by inserting the three lower mounting bolts, together with
washer and the nylon locking nuts. Tighten each bolt evenly, taking care not to
over torque the nut to the point where the transom or the bracket could be
damaged.
7. Do not weld or attach anything to the bracket.

5
MOUNTING THE MOTOR
1. Your motor lift bracket is supplied with a plastic 2 X 3 shim to help mount the
motor to the bracket.
2. Place the shim on the inside of the motor plate, under the lip, and hold it in
place while placing the motor over the top edge of the bracket. Snug the motor
clamps against the shim.
3. Attach the electrical components, and slowly run the motor up to a full tilt position to make
sure that there is sufficient clearance for the clamp bracket and the clamp handles. Reposition
the motor as necessary.
4. Tighten the motor clamps securely. Use cable ties or other means to secure the
clamp handles to prevent accidental loosening during operation.
5. Make sure to install the security bolts in the outboards lower clamp brackets. This is very
important to prevent the outboard motor from sliding up and off the clamping block. After the
motor is clamped to the Panther lift, use the outboards cast in security holes in the lower clamp
brackets to guide a 5/16” drill bit through the Panther motor plate, then install the 5/16” bolts,
washers, and nyloc nuts to secure the outboard to the Panther motor mount. In some cases a 3/8”
bolt may be required.
ELECTRICAL CONNECTIONS
This unit is designed to operate off of a standard 12 volt battery and is generally connected to the boats
main starting battery. The wiring is laid out below for illustration. The motor lift is outside the picture
on the top connected by the two bullet connectors.
Follow the instructions on the next page:

6
1. Install the two relays into the two sockets of the main pump relay harness.
2. Connect blue and green pump motor connectors coming from motor lift to blue and green
connectors of relay harness (shown as Relay Harness Leads above). Use a small amount of
dielectric grease with each of the connectors and plug them together. (It is also recommended
that these connections be wrapped with a waterproof tape or shrink tube.
3. Connect the blue/white stripe and green/white strip connectors to the blue/white stripe and
green/white strip connectors of the rocker switch (control system) wiring harness assembly.
4. Connect the two Black ring terminal wires from the relay harness to the negative (-) terminal of
the 12V Battery. Connect the two remaining Red ring terminal wires to the positive (+)
terminal of the 12V Battery.
5. Test the unit by running it up and down to make sure that there is adequate slack in the leads.
Connect the red lead to the positive (+) terminal and the black lead to the negative (-) terminal.
6. If the unit runs satisfactorily, disconnect the battery terminal wires and begin mounting the
rocker switch and relay harness per the steps outlined below.

7
MOUNTING THE RELAY HARNESS
WARNING! Do not connect relay harness to battery until entire assembly and controls are
mounted and ready. Severe damage to pump and controls could occur.
A. Find suitable place to mount relay harness. A dry place, typically the rear compartment is
recommended.
B. Mount relay harness using mounting holes located on relay harness bracket. Drill holes and bolt
relay harness securely in place.
WARNING! When drilling the holes, BE SURE not to drill through the hull or side wall.
INSTALLATION OF ROCKER CONTROL SWITCH
CAUTION! Before cutting any holes in mounting
surface check area behind mounting surface for obstructions.
(Cable braces, wiring, etc.)
DRILLING TIPS:
If mounting surface is fiberglass, apply masking tape to the surface that is to be cut to prevent
mounting surface from chipping or cracking. If the mounting surface is vinyl covered, remove the
vinyl from the surface to be cut using a razor blade to keep vinyl from tearing.
NOTE: The toggle control switch can be flush mounted or surface mounted depending on location
chosen. In either case, the toggle control switch should be positioned within easy reach of the boats
operator and within reach of the motor lift pump relay harness.

8
FLUSH MOUNTING ROCKER CONTROL SWITCH
NOTE: Mounting surface must be a minimum of 1/16th inches (1.6 mm) or a maximum of ½”.
(12.7 mm) thick for toggle control switch assembly to tighten securely.
1. Using a 2-1/8th inch (54 mm) hole saw, drill out marked area of mounting surface.
2. Route toggle control switch harness through bezel retainer.
NOTE: The bezel retainer is mounted onto the switch bezel before placement into opening. A gap
between the bezel and the bezel retainer must be 1/8” (3.2 mm) greater than the thickness of the
mounting surface.
3. Attach the bezel retainer to bezel using (2) screws.
4. Install switch harness through mounting surface. NOTE: Install into position by placing
pressure on screw heads to maintain a gap between bezel retainer and bezel. Push the
assembly into the opening and then tighten screws securely.

9
SURFACE MOUNT ROCKER CONTROL SWITCH
1. Route toggle control switch harness through surface mounting adapter.
2. Mark and drill pilot holes in the mounting surface using 3/31” (2.4mm) drill bit. Route wiring
harness though notch in mounting adapter. Secure switch assembly to mounting surface with self
tapping screws as shown. Tighten securely.
CONNECT RELAY HARNESS POWER CABLES TO CRANK BATTERY
A Attach large red and black leads from relay harness to crank battery.
Red to positive (+) ------Black to negative (-)
HYDRAULIC MOTOR LIFT LUBRICATION
CAUTION! The oil in the motor lift hydraulic system is under pressure when the jack plate is in
any position other than fully elevated (“UP”), or the hydraulic ram fully extended. Open the yellow
fill cap only when hydraulic ram has been fully extended.
1. Cycle the Motor Lift several times from the full down to full up position.
2. With Motor Lift in the “Full-up” (hydraulic, ram fully extended) position, slowly remove
yellow fill cap and check hydraulic fluid level. If needed, fill to the bottom of threads in oil
reservoir. (Use Power Trim and Steering Fluid or Dextron III ATF Fluid.)

10
WARNING!Personal injury or boat damage could occur if interference exists using the motor lift.
Carefully check to make sure that the motor lift and outboard components have adequate clearance in
all operation modes.
IMPORTANT! Check clearance of all mounting hardware after installation and before water
testing.
MOTOR LIFT CLEARANCE TESTS
1. Test the outboard trim with the motor lift half way down. NOTE: The propeller must be “UP”
so it does not hit the ground
2. If the outboard is equipped with a trim limit switch, make sure that when the outboard is tilted
all the way up, the steering system components do not come in contact with the motor lift.
3. With the motor lift half way down, trim the outboard upward and turn the steering wheel side to
side. Make sure the outboard motor does not contact the motor lift, transom, or steering
components.
4. Repeat the above test with the motor lift in the full down position. If you have interference,
DO NOT WATER TEST THE BOAT! Unbolt the outboard and raise to the next set of
mounting holes or install a trim limit switch to ensure no interferences. If changes were
necessary, retest clearances. NOTE: After motor lift installation and prior to operating boat,
determine the outboard engines required water pressure. This information may be found in the
outboard owner’s operation manual or service manual. If the boat is not equipped with a water
pressure gauge, it is recommended that one be installed prior to using a motor lift.
CAUTION! Damage to outboard will occur if proper water pressure is not maintained.
Raising the outboard too high will result in a water pressure drop and overheating of the outboard
will occur. Proper water pressure must be maintained at all times during operation of the outboard.
NOTE: After determining proper operating height, again check for proper outboard
clearances.
ADDITIONAL SAFETY ITEMS
When using the motor lift on open water, attach the included Outdoor Motor
Safety Cable (see picture on left—part #55-0415) to the boat and motor lift.
This is a vinyl coated 3/32” diameter, 50” long heavy duty steel cable with one
loop and one snap hook.

11
IMPORTANT NOTE:
Trailering with the motor on the lift is NOT RECOMMENDED. MarineTech
Products will not be held responsible for damages or injuries incurred when trailering with the
motor attached to the 55-0045 motor lift.
TROUBLE SHOOTING
PROBLEM POSSIBLE SOLUTIONS:
1. Motor Lift a. Cycle motor lift up and down six to eight times. If noise continues
groans or chatters follow steps b and c.
when operating b. Be certain your battery is sufficiently charged to power the electric
motor properly.
c. Turn to page 9 and follow lubrication procedures. You may need to
cycle the motor lift several times to work the grease into the
bushings.
d. Turn to page 9 and follow the procedure for adding hydraulic fluid to
the pump reservoir. You may need to cycle the motor lift several
times to work the air out of the system.
2. Motor lift will not a. Check to be sure your key switch is on.
go up or down. b. Check to make sure your battery has a sufficient charge.
c. Check 20 amp fuse attached to Rocker Control Switch (certain
models).
d. Check power connection at the key switch to be sure you have proper
(+) and (-) connections.
e. Check hydraulic pump and motor power connection at the battery.
f. Check all wire connections and connectors.
g. Check to make sure the relays are making proper contact.
h. Check for boat circuit breakers or fuses that may have been tripped.
i. If motor runs but motor lift does not move: see trouble shooting
section 5.
3. Motor runs but motor a. Check hydraulic hose connections to be sure they are tight (do not
lift does not move. over tighten).
b. Check hydraulic fluid level, see page 9 for filling instructions. You
may need to cycle the motor lift several times to work the air out of
the system.
4. Motor lift motor Check hydraulic fluid level, see page 9 for filling instructions. You
and pump makes may need to cycle the jack plate several times to work the air out of the
a gurgling sound. system.

12
5. Motor Lift goes in the Check the blue and green wires to be sure they are connected to the
the wrong direction same color termination points. Reversing these wires will cause the
when operated: motor lift to operate in the wrong direction.
6. Prop is cavitating. a. Adjust motor plate setting down, you may be running your engine
too high.
b. Check to be sure your prop has not been damaged.
c. Check to be sure your trim has not been set too high.
d. Check for obstructions to water flowing from your boat hull to your
engine lower unit such as speedometer pick up, depth sounding
transducers and water surface temperature pick ups. All such items if
located improperly can cause aeration of the water which can result
in prop cavitations.
7. Motor lift binds. a. Check tightness of all bolts and screws. Tighten any bolts or screws
that are loose. Check periodically if problem persists and remove
bolts and add red permanent Loc-Tite, reinsert bolt or screw and
tighten. If significant damage has occurred to the motor lift
structure, contact the manufacturer.
b. Turn to page 6 and follow lubrication procedures. You may need to
cycle the motor lift several times to work the grease into the
bushings.
c. Check for foreign objects lodged in your motor lift. Never run
motor lift with hands close to motor lift!
d. Check hydraulic fluid level; see page 9 for filling instructions. You
may need to cycle the motor lift several times to work the air out of
the system.
8. Motor Lift dead a. Check fuse—a 10 Amp fuse is located at the end of the rocker switch
cable near the red (+) terminal of the battery.
b. Check to be sure that all connectors are making proper contact and
are not corroded.
c. Check battery condition –is the battery fully charged.
d. Check for electrical shorts or opens. A short should cause the fuse to
blow. An open will cause it not to operate, but will not blow the
fuse.
9. Motor Lift stops a. Check wires for intermittent open (an open may occur do to
running vibration).
intermittently b. Check relays for proper contact or corrosion.
c. Check wire termination points for proper contact.

13
AVAILABLE ACCESSORIES
Wireless Remote
55-0105* (*Ask for required special adaptor wire P/N 99-0045 pictured below)
Control your motor lift from anywhere within the boat without the hassle of tripping over wires. 50ft
operating range. Powered from a standard A23 - 12V battery. Can be used on any Panther Trim and
Tilt unit or any product that has a two prong molded connector. Enhance the performance of your
Panther Products and especially the 55-0045 Motor Lift by going wireless.
WARNING: Never operate the wireless remote from outside the boat.
Wireless Installation: (see picture on Page 14)
1) Remove rocker switch assembly (leave the pump relay harness attached to pump).
2) Locate adapter cord. It is the two wire red/black cable with the two prong molded
connector on one end and two bullet connectors on the opposite end.
3) Plug the two prong molded connector into cord coming directly from wireless receiver unit.
4) Attach the other end of the adaptor cord to the pump relay harness cable. The red wire
from the wireless receiver unit plugs into the green wire of the pump relay harness. The
black wire from the wireless receiver plugs into the blue wire on the pump harness relay.
5) Attach the red ring terminal to the (+) Positive post on the 12V Boat Battery.
6) Attach the black ring terminal to the (–) Negative post on the 12V Boat Battery.

14
WIRELESS REMOTE TROUBLE SHOOTING
Weak Signal:
1. Battery may be low. To replace battery, remove the screw on the back of the
transmitter. Remove the back cover carefully, noticing how the rubber membrane is
seated in the case. Remove and replace the battery. Reinstall back cover making sure
that the rubber membrane is seated in the case. Install screw and carefully tighten.
Do not over tighten. Dispose of old battery properly. During periods of long
inactivity, it is recommended to remove the battery.
2. Receiver is obstructed. Move receiver in a direct line with the transmitter. Make
sure antenna is not obstructed.
3. Programming the transmitter to the receiver.
1. Disconnect power to receiver (either positive or negative terminal).
2. Enable the transmitter by pressing the power button, the LED will flash twice.
3. Hold down either directional button on the transmitter.
4. While holding down button connect power for about one second.
5. You should hear a relay on the receiver “click”.
6. Release button and fully reconnect power.
7. Your transmitter is now programmed to the receiver.

SERVICE AND WARRANTY
Should your unit ever require service, please do not return the product to your dealer. Please call the number
below for special instructions on shipping and handling. Please call between 9:00 am - 5:00 pm (Pacic Time)
Monday through Friday. If service is required and covered by warranty, it will be repaired or replaced as
described below. If service is required and not covered by warranty, (such as damage caused from improper
trailering or from water intrusion through the breather tube), replacement parts are available for purchase
and may be paid for by Visa or MasterCard.
The warranty coverage on this equipment is limited to the terms set forth below:
CMP Group Ltd. warrants this product to be free of defects in material and workmanship for a period of ONE
(1) YEAR from the date of original retail purchase. Positive proof of date of purchase is required for warranty
service. If service is required and covered by warranty, the unit will be repaired or replaced with new or factory
rebuilt parts at no charge. The defective components must be returned to the address specied, with shipping
charges prepaid. Be sure to include your name, address, telephone number and a copy of the sales receipt
showing the date of original retail purchase. All sales receipts are subject to verication.
This warranty does not apply if the unit has been damaged by accident, abuse, misuse, poor installation or
misapplication, or if it has been modied from its original condition, or if any serial number has been removed
or defaced or altered. This warranty does not cover any expense to remove or reinstall the unit or any of its
components. If a returned unit is not covered by warranty, the sender will be notied and given an estimate
of the charges to repair or replace the unit, together with the return shipping charges.
THIS WARRANTY DOES NOT COVER SPECIAL, INCIDENTAL, OR CONSEQUENTIAL DAMAGES RESULTING FROM
ANY BREACH OF WARRANTY, OR UNDER ANY OTHER LEGAL THEORY, INCLUDING BUT NOT LIMITED TO
DAMAGE TO OR REPLACEMENT OF OTHER EQUIPMENT AND PROPERTY. THE WARRANTY AND REMEDIES SET
FORTH ARE EXCLUSIVE AND IN LIEU OF ALL OTHERS, WHETHER ORAL OR WRITTEN, EXPRESS OR IMPLIED. DUE
TO THE SPECIAL AND UNIQUE CONDITIONS THAT MAY EXIST IN EACH APPLICATION, THE MANUFACTURER
SPECIFICALLY DISCLAIMS ANY AND ALL IMPLIED WARRANTIES OF MERCHANTABILITY AND FITNESS FOR A
PARTICULAR PURPOSE. NO DEALER, AGENT OR EMPLOYEE IS AUTHORIZED TO MAKE ANY MODIFICATION,
EXTENSION OR ADDITION TO THIS WARRANTY.
Some states do not allow exclusion of incidental or consequential damages, so the above exclusions may not
apply to you. This warranty gives you specic legal rights, and you may also have other legal rights, which may
vary from state to state.
1.604.940.2010 | sales@cmpgroup.net
Table of contents
Popular Lifting System manuals by other brands

Genie
Genie gS-1530/32 Service and repair manual
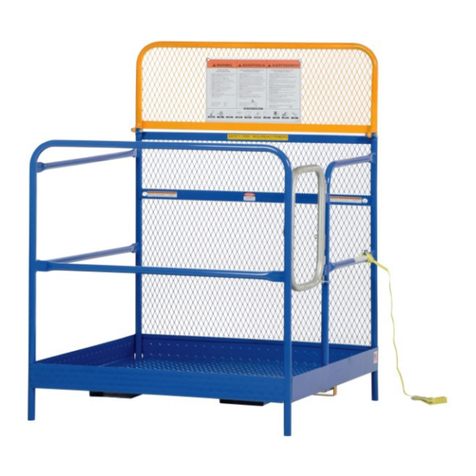
Vestil
Vestil WP Series instruction manual
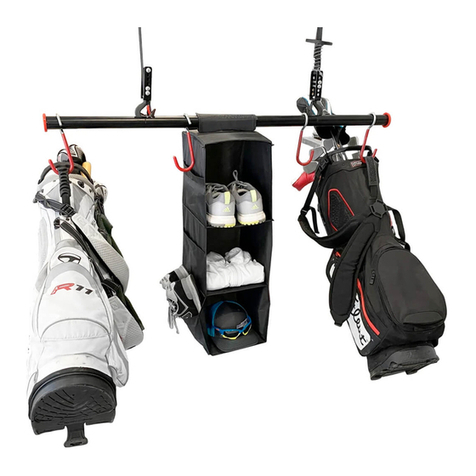
Proslat
Proslat GARAGE GATOR 68223 ASSEMBLY INSTRUCTIONS, USE & CARE GUIDE AND WARRANTY

Genie
Genie GS-2668 DC Operator's manual
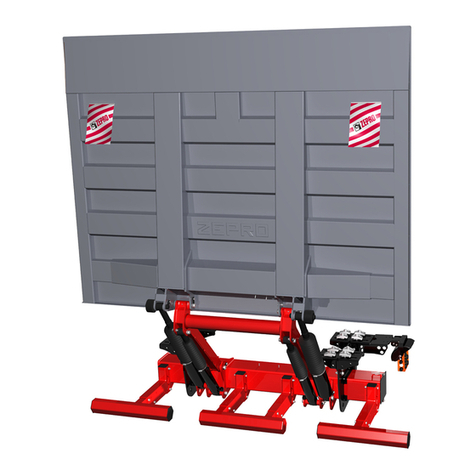
Zepro
Zepro ZN 2500-130 Installation instruction
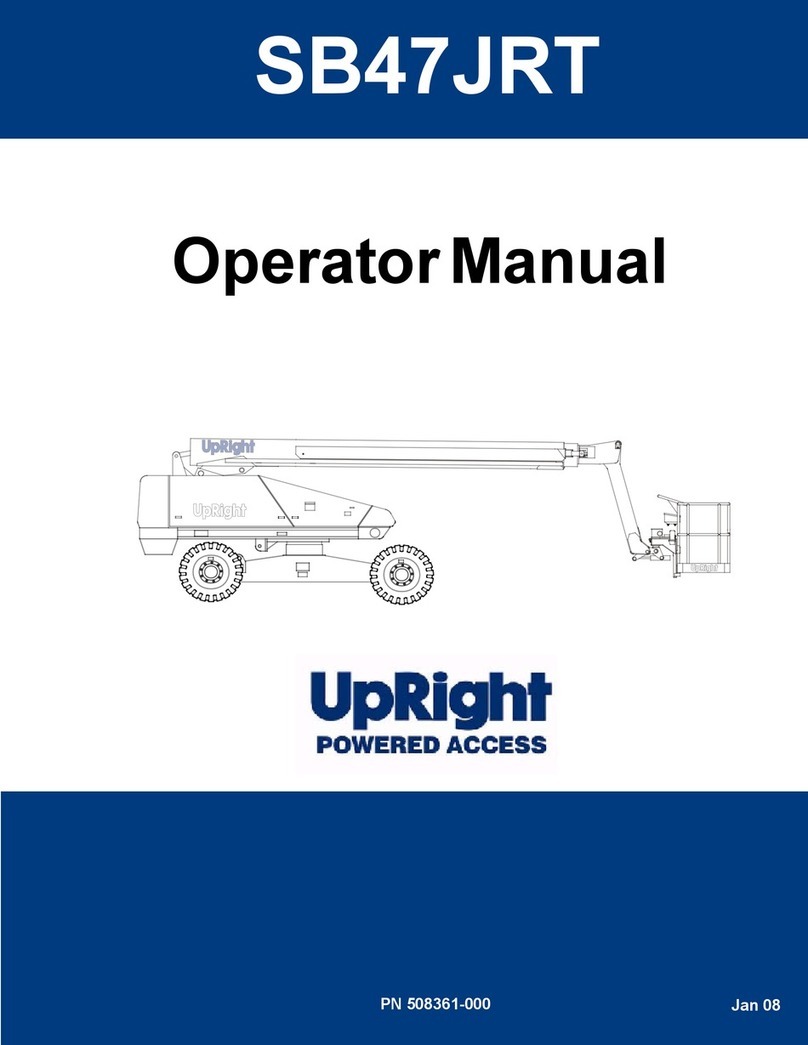
Upright
Upright SB47JRT Operator's manual
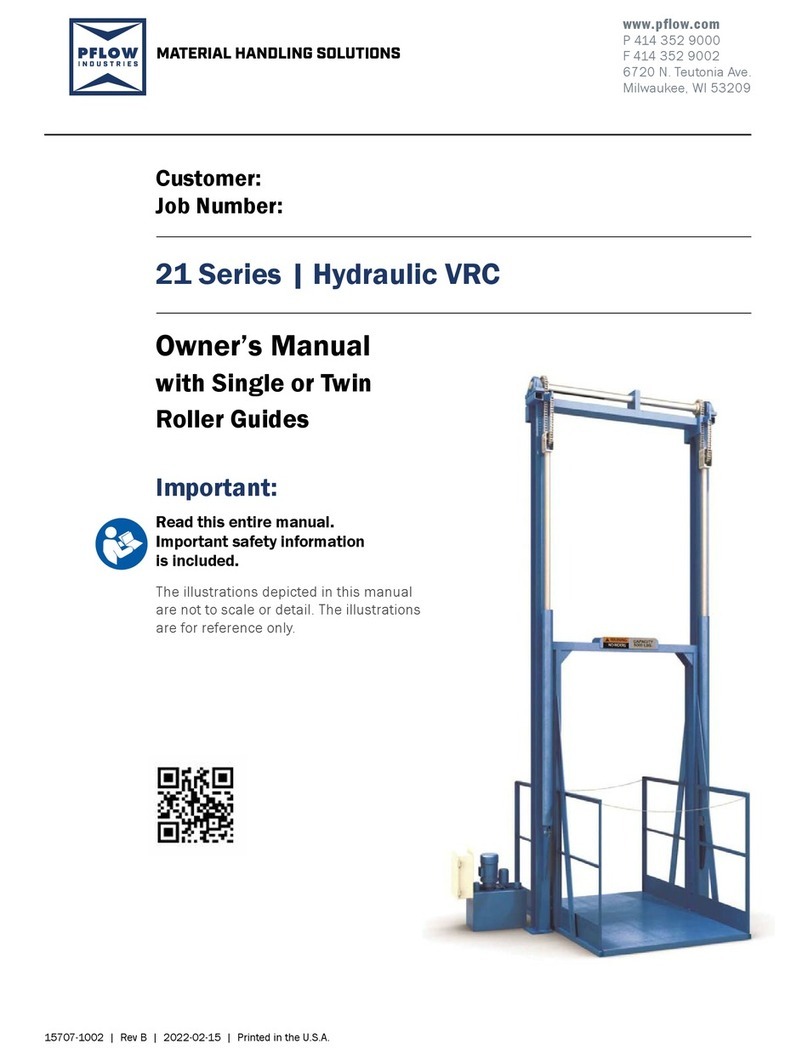
PFlow Industries
PFlow Industries 21 Series Hydraulic VRC owner's manual
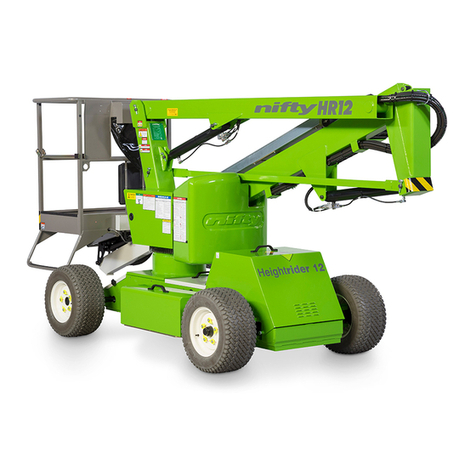
nifty
nifty HR12 operating instructions
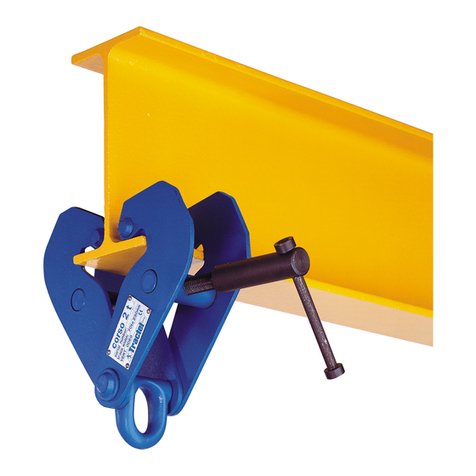
Tractel
Tractel Corso LT-10B Operation and maintenance manual

Vestil
Vestil JMD-1000 owner's manual
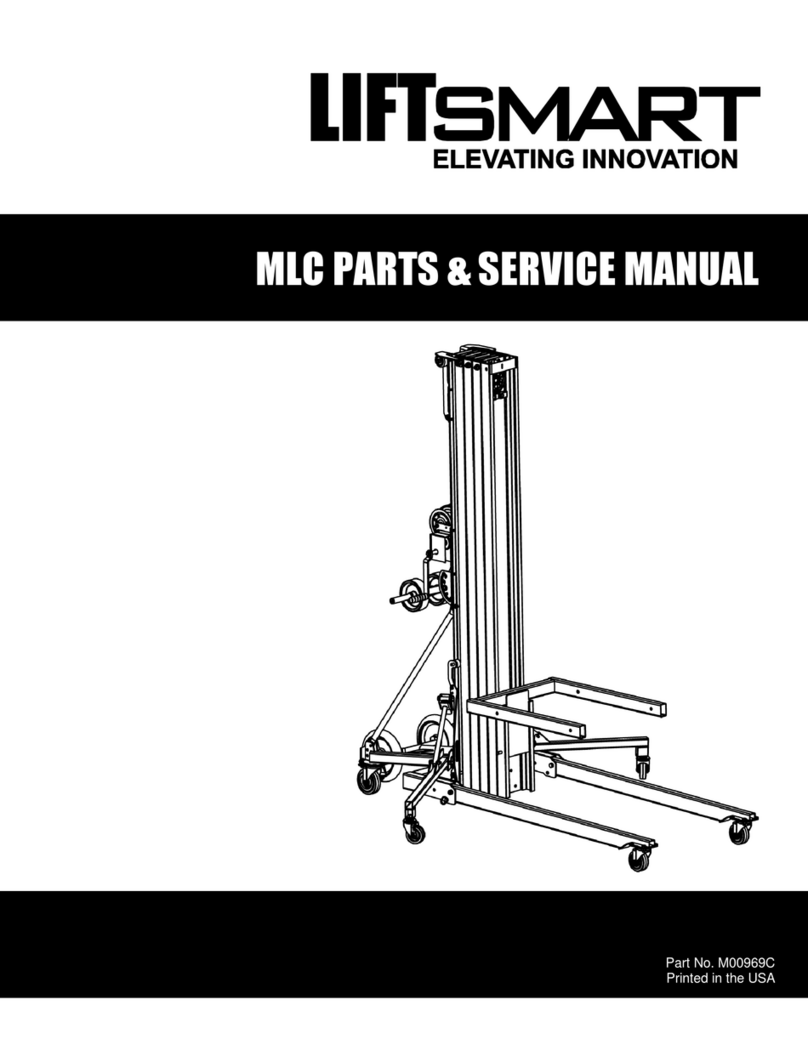
LiftSmart
LiftSmart MLC Parts and service manual

Challenger Lifts
Challenger Lifts 44018 Installation, operation & maintenance manual