Coleman Air C440-HVAD User manual

1
C
oleman
A
ir
C440-HVAD
Digital Diversion Controller
•
Fully digital user interface.
• Solenoid based with 3-stage charge control.
• No jumpers or potentiometers need to be set.
• LCD 2 x 16 back-lit display.
• Both manual and automatic equalize modes are available.
• Dual shunts for monitoring both solar and turbine amperage and wattage.
• Automatic nominal battery voltage detection.
• Nearly all charge parameters can be managed through the user interface.
• Relay on time can be controlled and set for diversion times up to several hours.
• Upper and lower set points can both be set.
• Automatic LCD back light dimming to save energy.
• Dual Truck Star breakers, one each for your turbine input and diversion output.
• 12, 24 or 48-volt battery systems.
• Vented cover.
• Modular PCB Layout.
The C440-HVAD balances
the tried and true with the
newest technologies, resulting
in a super capable diversion
controller for your alternate
energy system that’s easy to
use and even easier to love.
Visit ColemanAir.us for the
most current information.

2
Quick Start:
All user settable parameters as well as additional information are accessible via the user
interface which consists of the LCD screen and the three buttons located on the front cover.
Pressing any key during the normal operation of the unit will cause the main menu to be
displayed. Depressing the right/left buttons will scroll through the menu options. Entering the
“Enter” button will cause that menu option or value to be selected. Use of the up/down menu
increases and decreases the current menu value. Pressing the up button exits the menu (unless
you are currently modifying a value, in which case it will increase the value. First press “Enter”
to select the current value, and then press the up button to exit the menu).
The Red LED on the front of the unit indicates an error of some nature. The exact cause of the
error will be shown on the LCD screen (unless you have activated one of the menu options).
The Green LED on the front cover is lighted when the unit is first turned on and also any time
the charge performance is considered high enough to complete the current charge cycle. If the
solar/turbine power is not adequate to complete the charge cycle, the cycle will be extended and
the mode timer will not count down. When this green LED is lighted, the charger is able to pass
enough current to the batteries to complete a full charge of the batteries.
The internal LED on the upper left of the large PCB board (motherboard) is lighted when the
solenoid is engaged.
The red LED on the small daughter board is lighted when there has been an over-voltage detected. To clear an over-
voltage condition, all power to the unit must be disconnected for at least 10 seconds. Once power is re-applied, the
unit should clear the fault. Over-voltage condition
s should be addressed by ensuring your wind turbine and/or
solar inputs never exceed 100 volts and both wind and solar are never enabled without first ensuring the controller
is powered up and running from the batteries.
The Coleman Air C440-HVAD can handle 12, 24 or 48-volt systems. When power is first
applied to the unit, the microprocessor analyzes the battery voltage and automatically determines
the battery bank nominal voltage. You do not need to set any jumpers or make any manual
selections; this is fully automatic.
More Features:
• Reverse polarity protected – This unit will not be damaged if you inadvertently reverse the battery sense lines.
• Over Voltage protection. The circuit board is protected against over voltage.
• Steel enclosure - with multiple conduit openings.
• Large terminals - that can actually terminate large wire.
• Pre-wired for both solar and wind. Super easy terminations and hookup. Saves hours of time and trouble not having
to interconnect all of these components.
•
Custom settings a
re saved.
The settings and parameters you enter are saved to eeprom incase of a power outage.

3

4
The HVAD Menu
is selected by pressing any button on the front panel. Pressing the right/left buttons will scroll
through the menu options at the current level. Pressing the “Enter” button will cause that menu option or value to be
selected and/or displayed. Use of the up/down menu increases and decreases the current menu value. Pressing the up
button exits the menu (unless you are currently modifying a value, in which case it will increase the value. First press
“Enter” to select the current value, and then press the up button to exit the menu).
For example: To change the float set point of the controller. Press the “Enter”, “Up/Down” or “Scroll” button on the
front panel. The Charge submenu will then be displayed. Press the “Enter” or “Down” button to enter the submenu.
Press the “Scroll” button towards the right two times. This will display the float set point along with the current value
of the set point. Press the “Up/Down” button to alter this value to the desired voltage. Press the “Enter” button to save
this value. Press the “Up/Down” button upwards to exit the menu system. You could also of course continue to alter
more values and/or view other settings.

5
Charge modes and set points:
As introduced above, the HVAD is fully configurable through the front panel buttons and display. There are no
jumpers that need to be set or potentiometers that need to be adjusted. All configurable options are reachable via the
menu system. This menu system is comprised of a main menu and several submenus as depicted above in the menu
layout graphic. Each submenu allows you to either set a particular value, view information, or perform specific
actions, like running a solenoid test or starting the equalize mode. Most of these menu items are self-explanatory and
will not be discussed in detail; however, there are some features and settings that deserve greater explanation.
First and foremost, you generally do not need to change anything. When the controller is first powered up, it
analyzes the current battery voltage to determine whether the battery bank is a 12, 24 or 48-volt bank. If your battery
bank nominal voltage has changed sine the last time the unit was powered up, then the microprocessor will reset all
values to the factory defaults and store the new information. These factory defaults are normally perfectly adequate
for a lead acid battery bank used with most solar and wind installations. Changes to the settings are therefore only
required when your requirements are different in one manner or another from what has been set by the factory. The
controller is basically plug-and-play! Factory defaults can be viewed in the technical specifications page in this
manual.
Although the HVAD is a solenoid-based “Diversion Controller”, it is capable of simulating a 3-stage charge controller
due to the fact that the controller can track both a bulk and float setting. The word simulating is used because no
solenoid or relay based controller can react to instantaneous changes of the battery voltage or limit the current flow in
the same manner as a PWM controller can. This said, the controller is a VERY capable mechanical controller that
does have the ability to track multiple voltages and react accordingly. Additional charging logic has also been added
including such features as re-bulking, an absorb mode that allows for automatic adjustments due to changes in solar
illumination (low current) as well as offering both a manual and automatic equalize. So, this is no stripped down
mechanical controller … but what is a 3-stage charge controller?
The main advantage to solid-state controllers and the very capable HVAD is that they offer more advanced charging
modes than single stage, i.e., mechanical controllers. We will briefly discuss the three stage charging modes.
•
Bulk Charge
•
Absorption Charge
•
Float Charge
The HVAD is capable of providing these 3 stages:
The 1
st
stage in a 3 stage charging mode is the Bulk Charge: In this mode, most (if not all) of the available current is
sent to the batteries to raise the battery voltage up to the bulk set point. This mode brings the battery to about 80% of
its capacity. Generally the bulk charge voltage is set to between 14 and 15 volts, with 14.4 volts often used as a
standard. There is really no perfect voltage setting here as there are many factors involved. The ambient temperature,
the size of the energy sources vs. the battery bank size, the desired length of time in this mode, the cost of the energy
(if it is supplemented by the grid or generator, etc.). Simply stated, the bulk charge gets the battery up to a mostly full
state at a quick but healthy rate.
The 2
nd
stage of the 3 stage charging mode is the Absorption Charge: Once the bulk mode set point is reached, the
charger attempts to hold and track this value. The absorption mode uses the same set point as the bulk mode with the
difference being that the battery voltage is no longer rising up to the set point; but instead, it is being maintained at
that set point. Due to the chemical nature of the battery, this constant voltage causes the charge current to drop as the
battery reaches a “full” state of charge. The factory default for the absorption mode is set to 120 minutes, which under
sufficient solar/turbine energy input is ample to charge most battery banks.

6
The final stage is the Float Charge: This mode is the charge mode that the battery is under most of the time for a
properly designed system. Once the batteries are brought to a full state of charge, the float charge mode maintains the
batteries at a voltage level of around 13.2 to 13.7 volts (for a flooded, 12 volt lead acid battery. By applying the
required amount of charge current to offset any load the battery might be powering, as well as overcoming the
batteries natural self-discharge, the batteries longevity is greatly increased.
Another charge mode incorporated by many chargers (and the HVAD) is the equalize charge. This mode is not a part
of the normal charge cycle, but is instead initiated (either manually or automatically based on a timer) to help mix the
electrolytes of the battery. During normal use, the battery’s chemical mix becomes stratified. (Separated from top to
bottom). An equalize charge uses approximately 10 percent higher voltage to help mix these elements in the battery.
Equalize charging also helps bring all of the batteries in a multi-battery bank to an equal state. Most people agree that
an equalize charge should be run once every 10 to 40 days, for 2 to 16 hours. During this charge cycle quite a lot of
gassing will occur, which causes the fluids to be mixed and the plates to be "cleaned". An equalize charge is not
recommended for sealed batteries.
The HVAD also incorporates a “ReBulk” set point. Should the battery voltage drop to the “ReBulk” set point for
more than a few seconds, the controller will exit the current charge mode and start a new bulk mode. If the Bulk
mode is already active, then the controller will restart the countdown timer to force a new full-length bulk mode
charge.
The HVAD incorporates the 3 stage algorithm discussed here with the some limitations that are due to the fact that the
controller uses a mechanical switch. The primary limitation is the number of times per minute the solenoid can be
switched on and off without damage or premature failure to the solenoid. This limits the controller in systems that
have small battery banks and high current charge sources. When such a condition exists, the controller will not be
able to react as quickly as a solid-state controller and may allow the voltage to rise or fall further than optimal. To
alleviate this condition, it is recommended that your charge source(s) not exceed the battery bank’s amp-hour capacity
by more than four times. That is, this controller is best suited to a system where the combined solar/wind energy is
not capable of fully charging the battery bank faster than 4 hours. Higher current sources will tend to whip the
voltages up and down, with a loss of efficiency. A PWM or MPPT controller would be a better choice in this
environment. That said, the HVAD is very suitable for systems that incorporate larger wind turbines and/or smaller
solar systems that are properly matched to their battery bank.
The HVAD excels when used in conjunction with a wind/hydro turbine to run diversion loads.
The HVAD is a diversion controller by design. A diversion controller is very well suited to wind and hydro systems
in that these energy sources need (or should) stay connected to the battery at all times, whereas solar can be
disconnected without problems. The HVAD takes “diversion” to a new level by incorporating the 3 stages, equalize,
configurable cycle times and many features not seen before in a diversion controller. The following section will
explain some of the settable features that allow the HVAD to excel as a diversion controller yet is used as a solar
disconnect controller as well.
1. Setting up the charge parameters. See the technical specifications pages for the factory defaults. If you
need to alter any charge settings, simply select the charge menu choice from the main menu and scroll though
the submenu to select and alter the values. There are very few limits placed on the values you set, other than
you cannot set a float set point higher than the bulk, or the bulk higher than double the battery system voltage
etc. Once you set or reset these settings, you should monitor the controller and see that these settings are
working to achieve the results you require.
The factory time setting for the absorption is 120 minutes. This value can be changed as required. This
timer is performance based. The microprocessor uses multiple algorithms to determine if during the last
minute the batteries actually realized a certain level of charging. The main consideration is whether the
controller was able to reach and hold the upper set point. If the performance during the last minute for the

7
absorb mode is considered adequate, the timer will be decremented by one minute. If on the other hand, the
performance is below the standard, the timer will not be decremented, which can result in a charge cycle that
lasts much longer to ensure the batteries actually receive the best charge possible in less than optimal charging
conditions.
The green LED on the front cover will be lighted when the processor determines the performance is
high and off when the performance is not high enough to properly charge the batteries. This allows you to
quickly visualize the real time charging performance that the controller is detecting. Often the green LED will
blink on and off randomly and rapidly as the solar/wind energy fluctuates.
2. Turning on or off the Equalize mode. By default, the equalize mode is not enabled. To start a manual
equalize, select the Equalize submenu, scroll right or left to the “Start Equalize?”. When this submenu is
displayed, press the “Up/Down” button to select “YES” and then press the “Enter” button to request this mode.
The equalize mode will then be queued. The controller will not actually start the equalize mode until the bulk
set point has been reached. Once the mode is started, the countdown timer will start and the mode will stay in
affect until the timer expires. The length of time in this mode is controlled by the “Equalize Minutes” submenu
option. The equalize mode is not performance based and will not be restarted automatically due to low current
conditions.
The automatic equalize: Changing the Equalize days from “0” to any number up to 90 will enable this
feature. The equalize function will then run once the day timer has been triggered and the bulk set point has
been achieved. The equalize will not actually start if the bulk set point is not achievable via the solar/turbine
charge inputs.
3. The Advanced Menu. The factory settings for the HVAD are to engage and disengage the solenoid as soon
as the currently active set point (bulk, float, equalize), is reached and to allow the battery voltage to drop by no
more than 6% from that setting. In addition, the microprocessor will attempt to track these set points as much
as possible but will not allow an enabled state of the solenoid of less than two seconds. Given these settings,
the controller may turn on and off the solenoid several times per minute. This is great if you want to keep the
batteries as close to the set point as possible, but not suitable if the primary purpose of the controller is to run a
pump, grid tied inverter, perhaps even Bitcoin mining equipment or any other real world load that needs to be
engaged for a longer period of time in order to be useful. This is where the advanced menu is used.
a) The relay offset setting: This setting allows you to specifically set the “lower set point” for any mode
based on a percentage of the upper set point. For example. The factory setting for this value is 6% and
the factory set point for the bulk mode in a 12-volt system is 14.4 volts. Given these two values, the
upper set point will be 14.4 volts and the lower set point will be a drop of 6% (or 94% of the upper set
point), yielding a lower set point of 13.4 volts. This means that the solenoid will be enabled when the
battery voltage rises to 14.4 volts and disabled when the battery bank drops to 13.4 volts. These upper
and lower voltages will cycle back and forth as the solenoid is engaged and disengaged; providing
there is adequate charge current to raise the battery voltage to the upper trip point. This distance
between the upper and lower trip point is called hysteresis and is necessary in a solenoid-based
controller. The hys-ter-e-sis width can be narrowed (the lower set point is brought upwards) by
lowering the relay-offset percentage. In the same manner, a higher percentage will yield a lower low
set point. The lower the set point, the longer the solenoid will stay engaged waiting for the battery to
drop. This setting alone can often be used to control a pump or similar device, where you desire to run
the load as long as the batteries are not depleted past a certain point.
b) The Minimum relay on time. This 2
nd
advanced solenoid parameter allows setting a minimum enable
time of the solenoid from 2 seconds up to many minutes. This setting can therefore allow a particular
load to be turned on for a minimum of, for example, 10 minutes, without regard to the lower set point.
During this time, the microprocessor still monitors the battery bank and will exit this timer if the
battery drops considerably and is considered by the controller to be depleted. The processor, based on

8
the bulk set point you have entered, automatically calculates this depleted value set point to protect (as
much as possible) the battery from an over-discharge.
Please note: A lead-acid battery’s life is greatly reduced when the level of discharge is quite deep or the
battery is allowed to enter into a “dead battery” state. You should familiarize yourself with the parameters
for your particular battery before setting these advanced parameters.
4. The View Submenu: The view menu allows you to view the real time voltage and amperage of the connected
solar and or turbine energy sources. The controller incorporates two shunts, allowing it to measure both solar
and turbine amperages simultaneously. This feature is new to the HVAD, whereas previous controllers were
only able to display the amperage for a single input.
Note: If you do not utilize both wind and turbine inputs, it is possible (perhaps likely), that there will be a
small amount of current that is displayed for the unused input. For instance, if you are using only the solar
input, the controller may sense a few tenths of an amp on the turbine input. This is normal as there are stray
currents in any system where large amperages are involved.
Please note these very important electrical concepts: When the solenoid is not enabled, the solar panels are
effectively wired directly to the batteries through the normally closed contacts of the solenoid, just as if you
had hooked the positive of the solar panel directly to the positive of the battery bank. This means that the solar
voltage and the battery voltage will be identical at that time. The solar panels will move the voltage of the
batteries up and the batteries will have moved the solar panel voltage down until they reach an equilibrium
based on ohms law. This means, the controller cannot report the VOC (voltage open circuit) of the solar panel
input when it is connected to the batteries. The solar VOC reading will only be accurate when the solenoid is
enabled! Hint: Run the test cycle to watch how the enable/disable of the solenoid affects the solar voltage.
This same concept applies to the turbine input; however, the turbine input is never disconnected from the
batteries, therefore the turbine voltage is always identical to the battery voltage and therefore it is not reported
separately by the controller.
Another concept to understand is that the solar voltage will always be the same as the battery (and turbine)
voltage when you do not have an active solar input. This seems impossible, yet due to the same fact that the
solar input is tied to the battery positive via the normally closed contacts of the solenoid, the controller will
“see” the battery voltage on the solar input, with no way to determine if it is battery voltage or solar voltage.
When the solenoid is enabled, the solar voltage will be “floating” (it is not connected to anything) without an
active input and may not be considered accurate at that time, as there can be stray inductances present.
Essentially, if you do not have any solar hooked up, then just ignore any voltage readings the controller may
display for the solar input.
The current reading (amperage) of the solar and turbine inputs will be zero (or very close to zero), if there is no
active input for that source. When the solenoid is enabled, the solar current will drop to zero. When the
solenoid is not enabled, the solar input will be at its maximum. Both turbine and solar amperage readings
should always be accurate within a few percent, regardless of the active inputs (solar only, turbine only, or
both active). Voltages can be misleading due to the concepts discussed above, so using amperages is the key
to determining the performance of the inputs.
Other Menus and Submenus:
In addition to changing the charging parameters, the menu system can be used to view the maximum voltages and
amperages reached during the active charge cycle. These values are reset each time the charge mode is changed (a

9
change from the bulk mode to the absorb mode for example). They are also reset when the controller is powered up.
These values can be helpful in determining the performance of the charging sources.
Another submenu option is the “Start Test?” feature. To select this feature, press any button on the front panel,
scroll right or left to the Diagnostics menu, press the down button to select the “Start Test?” feature. Press the
“Up/Down” button either direction until “YES” is displayed, then press “Enter”. The controller will now enable and
disable the solenoid 5 times, using two-second intervals. During this time, the battery voltage, solar voltage, solar
amperage and turbine amperage will be displayed in an alternating and repeating pattern that allows you to see each of
these values during both the enabled and disabled state of the solenoid. As discussed above, if you have an active
solar input, you would expect to see the solar amperage at its maximum when the solenoid is disabled and at zero
when the solenoid is enabled. The voltage for the solar input should read the same as the battery voltage when the
solenoid is not enabled, but rise to the VOC of the solar panels when the solenoid is enabled.
During the test, all LEDs on the front cover will be lighted when the solenoid is enabled and off when the solenoid is
disabled. The green LED on the upper left of the main circuit board (motherboard) inside the controller will also be
cycled on and off during the test.
The turbine amperage
(see bullets below)
will not change substantially during the cycling of the solenoid since the solenoid
does not connect or disconnect the turbine input from the battery.
A few exemptions to monitor during the test:
•
If you have a large diversion load connected to the controller, then the turbine amperage may increase when
the solenoid is engaged due to the fact that the turbine will now be connected to both the battery and diversion
load, allowing more current to flow from the turbine. This is normal.
•
If the solenoid contacts are defective, then you may hear the solenoid’s coil pull in (as normal), but see no
difference in the solar amperage or solar voltage during the test. This generally indicates the normally closed
contacts of the solenoid are not actually closing and opening, but instead staying connected or disconnected.
Please note, there is a possibility that there is no active solar input, so be sure that during the time the
solenoid is not enabled, you see the VOC of the solar panels. This value is normally 1.5 – 2 times the
battery voltage.
•
Should the solenoid not enable or disable during the test, then the solenoid’s coil may be defective. There is
also the possibility that the main circuit board is not proving enough current to the solenoid. Check that the
green LED on the upper left of the motherboard is cycled on and off during the test. With a voltmeter, check
that there is at least 10 volts on the coil (top two smaller terminals) of the solenoid, when the solenoid is
engaged. (Use caution not to touch other components with your meter leads or fingers.)
•
The solenoid cannot be properly controlled if your battery voltage is very low (less than 10.5 volts). So
running a test during a low voltage condition may not render useful information.
If during the test, you determine the solenoid contacts have failed or the solenoid cannot be engaged and you have
verified that the controller is powered up with a sufficient amount of power (at least 10.5 volts) and have verified that
all solar and turbine inputs are normal, then replacing the solenoid is indicated. Refer to the Replacing the Solenoid
section in the later part of this manual for further instruction.
Resetting to factory defaults:
If for any reason you wish to start over with all configuration settings and parameters, then simply select the “Reset
Defaults?” submenu, choose “YES”, then press “Enter”. All configuration settings will be reset to the factory
defaults. This reset is also performed anytime the batteries nominal voltage (12, 24 or 48-volt) changes from the last
time the unit was powered up. This means if you change your battery bank from a 12-volt system to a 48-volt system,
then the microprocessor will automatically initiate a reset to factory defaults for the currently detected battery bank.

10
About load diversion:
The basic operating philosophy of a diversion controller is quite simple. Monitor the battery voltage, and if it should
rise to a predetermined level, connect a diversion load or “Dummy Load”, of sufficient size, to the battery or energy
source to prevent the battery voltage from increasing any further. This is a very simple, yet very effective way of
preventing battery overcharging. All alternate energy systems should have some form of battery overcharge
protection.
Several schools of thought on the subject.
1. The source of power (wind turbine, solar panels etc.) -- should remain connected to the batteries while the
dump load controller is actively dumping the excess voltage.
2. The source should be diverted to the load directly and disconnected from the batteries.
We happen to believe that is far better to leave the wind turbine connected to the batteries at all times. Why?
When you remove the battery from a wind turbine and send it's power directly to a load, then it sees for all
practical purposes a short circuit (depending on the resistance of the load and lead wires.) This may cause the
turbine blades to slow dramatically and in some cases bring it to a halt. This braking action can cause heat
build up in the stator if it is repeated every few seconds or so (if the battery is just a little over the top). When
you allow the turbine to see the batteries, along with the load, the turbine remains more within its design
realm -- always a good thing.
Please note: this controller does not include a blocking diode or an A/C to D/C rectifier, as these are specific to your
application. If you are using the controller with a DC turbine or solar panels, you may need to purchase a blocking
diode. A/C turbines require rectification from A/C to D/C.
FAQ: Do I need a diversion load for a wind turbine?
Yes. Diversion controllers work by diverting excess energy from the wind turbine to a diversion or “dummy load”.
This diversion allows the turbine to remain under a load at all times. A solar panel may be safely disconnected from
the batteries, but an active wind turbine should never be disconnected from its load (battery/diversion load). When a
wind turbine is not loaded, it can easily speed out of control in high wind events, which can lead to catastrophic failure
of the turbine as well as the possibility of damage and injury to other property and people. It is very important that
your turbine has a very reliable load at all times.
Please see our FAQs located on our website, www.ColemanAir.us for more information on this subject and
many others.
Diversion Load Types
A diversion load needs to be larger (by at least 10-20%), than the sum total of all your solar/wind/hydro charge
sources combined that will be routed through the diversion load. When the diversion load is too small, battery voltage
may continue to rise even when the diversion is active. It is also important to use a load that is not likely to fail. Light

11
bulbs and similar such loads are not good diversion (dummy) loads, since they will fail and you may be left with no
method to dump the excess energy going into your batteries.
It is commonly thought that a standard 120vac, 2000 watt heating element (readily available from your local hardware
store), would make a good load; however, in reality, they are not well suited, as it takes several of these elements to
actually be effective in lower voltage systems. A 2000 watt, 120VAC element will not dissipate 2000 watts at lower
voltages. You will need to install multiple elements in parallel to achieve the desired load specifications.
Please use the following chart as a quick guide in using a 2000-watt, 120 VAC heating elements.
60Vdc dump (48Vdc system) -- 500 Watts -- 8.3 amps
30Vdc dump (24Vdc system) -- 125 Watts -- 4.2 amps
15Vdc dump (12Vdc system) -- 35 Watts – 2.1 amps
120Vac -- 2000 Watts, at 16.7 amps
Basically, a standard 2000-watt, 120 VAC element, in a 12-volt system will only dissipate 35 watts.
Water heating elements designed specifically for 12, 24 and 48-volt systems are by far a better choice.
A very acceptable diversion load is a power resistor. These can be obtained via your Coleman Air dealer. Various
wattages are available as either completed load centers or individual power resistors.
Product Code: L675W12V
45A/12V 675 Watt Diversion Dummy Load Resistor Heater -- For 12 volt systems
Product Code: 2R100W
2 Ohm, 100 Watt power resistor for 12v systems.
Place multiple resistors or load centers in parallel for a higher wattage load. When you place the same value resistors
in parallel, you double the wattage rating, and ½ the resistance. This is a safe method of doubling the
wattage/amperage handling capability of your diversion load.
Note: you cannot simply use a lower value resistance without also increasing the wattage rating of your
resistor. For instance, attempting to use a single 500 watt power resistor of 2 ohms on a 48 volt battery system (60v
dump), will result in the dissipation of 1800 watts, however the resistor is only rated at 500 watts, and will be
destroyed. A diversion load is not required for solar only systems.
Please visit our online store for a selection of diversion loads, diodes and rectifiers.

12
Installing and hooking up your HVAD Controller:
To help prevent over-voltage, always hookup the controller to the batteries (and power it up) before enabling
your turbine or solar energy sources. The controller cannot engage its protective circuits if there is no
connection to the battery bank.
A free spinning turbine can instantly generate very high voltages, which can damage many of the components
within the controller if the controller is not first powered up.
Inspect the unit when it first arrives. Please contact your dealer immediately if any problems are found.
Install the HVAD controller indoors only.
The controller should be connected as close to the battery bank
as possible, using large insulated copper wire.
A common installation method is to mount the controller on the wall, often reinforced with plywood or similar
material, in a room specifically built for your alternate energy equipment. A garage or similar room is also fine.
Installations in your living area are not recommended! Large currents and voltages are passed through the unit,
there is a noise emitted during the normal cycling of the solenoid, not to mention that multiple LEDs that will blink
constantly as the unit is operating, which may be less than inviting in your living space.
Do not install the controller in a very small area that does not allow for proper ventilation. Absolutely do not install
the controller in a “battery box” without substantial ventilation. Lead acid batteries expel hydrogen to the air as
they charge, which can be ignited by the solenoid during normal operation.
The controller has four holes on the back of the unit that accommodate 12 gauge screws or similar to be used to
securely fasten the unit to the wall. The unit may be installed on a flat horizontal surface; however it may be difficult
to use the front panel buttons and display. When mounting vertically, the inputs of the controller should always be
oriented downwards (with the vent upwards), to ensure the unit is able dissipate any captive heat.
Use large gauge wire to hook up the controller to your battery bank. If you will be using the controller at amperages
above 60 amps, then it is vital that you use only high quality terminal connections crimped, screwed or soldered to the
copper wire, and bolted tightly to the input connections of the controller. (Aluminum wire is not recommended.) Do
not attempt to wrap large wire (larger than 8 gauge) directly around the mounting post of the controller. Significant
heat can result from a poor connection, leading to multitude of failures such as melted insulation, burnt out
components; or worse, a full-fledged fire.
Again, do not install under size wire, it is utterly dangerous! See the NEC wire charts to determine your minimum
safe wire gauge for the amperage of your system and energy sources. Both the negative and positive wire going to
your battery bank must be sized properly and fully capable of handling the combined current of your wind and solar
energy sources. If there is a diversion load, then this amperage must also be factored in. This single wire pair must
carry all of the charge and discharge current of all connected loads and inputs. Note: When the solenoid is enabled,
the solar energy is disabled; however, any diversion load will then be active and possibly drawing power from the
battery.
Any wire that leaves an energy source MUST have a breaker or fuse. Do not run a wire from your battery bank
that is not protected against over current. This means you need a breaker or fuse between the battery bank and
controller. The breakers inside the HVAD do not fulfill this purpose. The left breaker on the inside of the unit fulfils
the purpose of having an over-current protection for your diversion load, therefore no additional breaker is needed
from the controller to the diversion load.

13
Inspectors generally insist that a breaker or disconnect be located as close to the energy source as possible and may
also insist on a 2
nd
breaker or disconnect near its final termination point. Please consult NEC regulations and your
local inspector to determine the requirements in your area. These subjects are outside of the scope of this manual;
however, it is your responsibility to ensure your unit is installed safely!
Solar panels and Wind/Hydro turbines are energy sources. A breaker or fuse is required between these devices and
any other components (including the HVAD). Do not hook up a wire from any energy source into the HVAD
without the ability to quickly and safely disconnect the input. All inputs need fuses or breakers!
Wiring the controller.
Please refer to the large hookup diagram at the beginning of this manual.
The positive wire from the battery (which is routed through a breaker) is connected to the left most bottom terminal.
Please remove the nut and washer and place your wire terminal under the washer but above the large red wire that is
already present.
The solar panels connect to the 2
nd
terminal from the left (through a breaker of course.).
The wind/hydro energy source connects to the 3
rd
terminal from the left (via a breaker).
The three terminals on the far right are shared negatives. Connect at least one large wire from one of these terminals
to the negative post (or buss) of your battery bank. Solar and hydro negative leads can be wired here as well;
however, it is generally better to wire them directly to the negative post (or buss) of the battery bank.
As mentioned above, when the solenoid is not enabled, the solar input is electrically connected via the normally
closed (connected) contacts of the solenoid, to the positive post (buss) of your battery bank. This means that the solar
positive is hooked directly to your battery positive during the idle state of the solenoid. When the solenoid is engaged
(the coil is active), the solenoid’s bottom contacts open and disconnect the electrical connection from the solar panels
to your battery bank.
The wind/hydro input is not switched (disconnected and connected) by the solenoid. This input is always connected
directly to your battery bank. The only electrical reason this input is provided at the controller is for monitoring
purposes. As the current passes though the controller (and the turbine shunt located on the upper right of the
controller), the microprocessor is able to determine the current flow of your turbine. This input also passes though the
breaker on the right side of the unit. This breaker allows the turbine input to be disconnected for diagnostic purposes,
but again, this does not fulfill the requirement of having an over-current protection device between the turbine and the
controller.
The diversion load (real or dummy) if used, must be hooked to the middle two terminals on the left side of the unit.
Most resistive devices (heaters) are not polarity sensitive; so in this case, it does not matter which terminal is wired to
which input of the load. Other loads, such as inverters, pumps, power supplies etc, are polarity sensitive and must be
hooked up with the correctly polarity. The upper terminal (of these two terminals) is the positive connection. This is
the terminal that has the aluminum strap connected to it that crosses over the top of the solenoid. The lower terminal
is the negative terminal for your load and is electrically connected to the three terminals on the lower left of the
controllers. The normally open contacts of the solenoid (the two that stick out the sides of the solenoid), are used to
control the diversion load. The diversion load is enabled (connected to the battery) when the solenoid is enabled.
No diversion load is required for a solar only installation. When the batteries reach the trip point, the solar energy
will be disconnected from the batteries until the batteries drop. Diversion loads can however be used with solar only
installations and/or solar/hydro combined installations when the excess energy is desired to run “real” loads. In this

14
case, it is recommended that the solar positive be hooked up to the turbine input, not the solar input. This will prevent
the solar panel from being switched off when the solenoid is engaged. The downside to this is that the solar input will
obviously be “seen” by the controller as a turbine input, causing the solar amperage to be reported as turbine
amperage on the LCD. This however, may be absolutely acceptable to you if the primary function of the controller is
to control a real word load of some type and you want to utilize all available power at all times.
Grounding your HVAD and alternate energy system.
A properly grounded system is extremely important, for both safety and reliability. An ungrounded system is
significantly more likely to be damaged during an electrical storm than a properly grounded system.
Solar panels and wind turbines act as lighting antennas or “magnets” as they are always mounted in manner that
opens then up and elevates them in some manner or another which often makes them the most likely target for a
lightning strike.
It is important to note, that due to the relationship between the earth’s ground and the electrically charged sky during
an electrical storm, the lighting bolt does not actually seek the highest object, but the highest object actually attracts
the lighting bolt to it, with an initial burst of conductivity that starts from the ground up, not the sky down. So, putting
it simply, if you put a wind turbine up in the air and that tower is not grounded, then you can fully expect it to be hit
by a lighting strike, which will result in equipment failure. This is a “not if, but when” scenario and then “how often”.
When a lighting bolt hits an ungrounded tower, the entire voltage/current spike will travel down the wires that lead
directly to your HVAD controller, looking for a ground. On the way through, untold damage can be done. The
HVAD incorporates multiple over-voltage surge protection devices and circuits, but they may be no competition to a
direct lighting hit. Many of our controllers have survived direct lighting hits due to the internal protective circuits yet
the connected equipment like meters, inverters, etc. are damaged beyond repair. Proper grounding is paramount!
To make matters worse, the lighting strike does NOT have to be direct. Highly charged atmosphere may be present for
many miles around an active lighting area. This super charged air is more than sufficient to damage the sensitive
equipment used in an alternate energy systems, where the solar panels and towers act as antennas for this energy.
Additionally, indirect electrical charges can be present at other times, including a stand-storm, high wind event, very
low humidity conditions etc., that are more than sufficient to generate static electricity that far exceeds hundreds of
volts. Without grounding, this static electricity alone can damage any piece of equipment used in your system.
A properly grounded system is comprised of (at the very minimum) ground rounds and large (6 to 8 gauge) wire that
ties the enclosures and system negatives directly to the ground rod. Ground rods (plural) should be placed as close to
turbine towers and solar panel installation as possible. The towers and panels should be tied directly to the ground
rods, with few or no splices. The battery bank’s negative (or buss) should also be tied to a grounding rod.
There is a great deal of information on this subject and you really should take the time now to research this before you
learn it the hard way. This is knowledge you will be forced to garner, it’s really just a matter of being proactive or
reactive and then how costly will such an education be.
Please research “solar wind grounding” on your favorite search engine.
Please also see “ground loops” to ensure you are setting up a grounding system that is not subject to ground loops,
which can introduce a new set of problems.
An ungrounded system is also a safety hazard for a multitude of reasons that are outside of the scope of this manual.
No safety conscience installer will ever design and/or install a system that fails to include grounding.

15
Extended Diversion Mode -- EDM
The basic operating philosophy of a diversion controller is quite simple. Monitor the battery voltage, and if it should
rise to a predetermined level, connect a diversion load of sufficient size, to the battery or energy source to prevent the
battery voltage from increasing any further. The amount of time the diversion load is connected is generally only 2 to
30 seconds. In this amount of time, the battery voltage will have dropped enough to be back in the normal region. The
controller will continue to engage and disengage the solenoid as often as necessary to prevent battery overcharge. This
is the normal mode of operation. The microprocessor uses several advanced algorithms to prevent rapid relay cycle,
yet it is common for the solenoid to be engaged and disengaged a few times per minute. This constant attention keeps
the batteries very close to (or just below) the trip point you have set.
There are however, situations where you would really like the controller to engage the solenoid for a longer period of
time once the batteries get to a “full” state. This is what we call the Extended Diversion Mode. On the HVA and
previous analog controllers, the EDM mode was selected via a jumper. On the HVAD, which is fully digitally
configured, the EDM “mode” (to continue with the HVA legacy) can be configured much more specifically via the
user menu options (advanced menu). Via this menu option, you can set both the minimum time the relay should stay
engaged as well as how low the batteries will be allowed to drop (percentage based). Once the batteries reach the
upper trip point you have set (the same trip point as the non EDM mode), the controller will engage and disengage the
solenoid based on these advanced parameters. See the menu system in this manual for more information on how to
configure these settings.
The EDM mode is very useful for running such items as water pumps, small grid tie inverters, or even alt-currency
mining that you do not want turning on and off every few seconds. When you configure the EDM mode, the wiring
remains the same; the difference is that the load you connect will be engaged for a longer period of time.
It is very important that the load you choose is 100% dependable if this controller is being used to prevent battery
overcharge. If the load is not present, then your batteries will overcharge. Grid-tied inverters will not provide a load ti
to the controller if the grid fails (power outage due to thunderstorm etc.). Such a loss of load can also cause damage to
your wind turbine if it depends on this load.
If you will be using the EDM mode with a load that may not be present at all times, then it is important that you have
another controller in parallel that is also monitoring the system with a slightly higher trip point. This second, failsafe
controller will then divert the excess energy to a diversion load that is 100% dependable should the 1
st
controller’s
load not be present or capable of disbursing all of the excess energy.
As in the case with the normal mode, the load you connect cannot exceed the capacity of the solenoid. Do not attempt
to hookup highly inductive loads, as the solenoid will be damaged due to high currents during the motor start.

16
General Operating specifications
System Voltage
C440-HVAD Diversion Controller 12V 24V 48V
Minimum operating voltage
10.5v 10.5v 10.5v
Maximum allowable intermittent/surge voltage (1) 100v 100v 100v
Maximum input from solar panels (VOC)
24v 48v 96v
Preferred maximum input from solar
panels
21v 42v 84v
Maximum continuous solar charge amperage 125A 125A 125A
Maximum continuous diversion amperage
150A 150A 150A
Maximum surge solar charge amperage
440A 440A 440A
Maximum surge diversion amperage
(resistive) – Longer surges will be
restricted by the installed breakers.
440A 440A 440A
Energy consumed by the electronics (meters off, solenoid
off - standby current) < .1W < .15W < .3W
Energy consumed by the electronics (meters on, solenoid
on) < 1A < .75A < .5A
Minimum float setting (volts)
12.0 24 48
Maximum float setting (volts)
24 48 96
Factory default float setting (volts)
13.5 27 54
Minimum bulk setting (volts)
12 24 48
Maximum bulk setting (volts)
24 48 96
Factory default bulk setting (volts)
14.4 28.8 57.6
Time in absorption charge once bulk set point has been reached. 2 hours 2 hours 2 hours
Time in equalize charge once equalize set point has been reached.
2 hours 2 hours 2 hours
(1) -- Voltages spikes above 100v at the battery+ input terminal will trigger the over-voltage
protection circuitry causing the isolation circuit to be engaged. The red over voltage LED will be
lighted (on the small PCB board in the center of the unit). The controller must be un-
powered for
at least 10 seconds to clear this condition.

17
For indoor use only. Install in a non-corrosive, dry environment only.
External dimensions of the enclosure (Inches)
8.5 x 12.5 x 4.5
Minimum ambient air temperature -20F
*2) Maximum ambient air temperature
(150 Amps) 85F
*2) Maximum ambient air temperature
(100 Amps) 110F
Maximum ambient air temperature
(60Amps) 140F
Operations above or below the maximum temperature range may result in loss of accuracy and/or
a reduction in current handling capability
Designed for battery-based systems only.
These specifications and measurements are subject to periodic change without notice.
Replacing the Solenoid:
The solenoid is a mechanical switch that has a limited life expectancy that is dependent on many factors including, but
not limited to, the number of times it has cycled, the amount of amperage it must carry and switch, the voltage across
the terminals as well as ambient heat in the installation environment. In active systems, the solenoid will eventually
need to be replaced. Although we use only the highest quality silver contact solenoids available that support both
continuous and surge amperages that far exceed the design of this controller, it is a mechanical device that is subject to
failure. The higher the voltage and amperage of your system, the shorter the life expectancy of this solenoid is likely
to be. This controller should not be considered for use in solar systems where absolute reliability is required. No
mechanical switch can offer such a level of reliability. For such systems, our solid-state controllers (no relays or
solenoids) should be considered.
To replace the solenoid, 1
st
ensure all power is removed from the unit. 2
nd
, disconnect all of the wires and straps
that are tied to or bolted on to the solenoid. 3
rd
, using a Phillips head screwdriver, remove the two #10 screws that
fasten the solenoid to the back-plate. The HVAD uses Zimmerman nuts that will not fall out or turn as you remove
the screws. Once the solenoid is free, simply lift it out and replace it by reversing this procedure. Take special care
not to over-tighten the nuts on the terminals of the solenoid as they can be stripped and cross-threaded very easily.:
Automatic Nominal Battery Bank detection:
When power is first applied to the HVAD controller, the voltage of the connected battery bank is measured to
determine if the controller should operate in the 12, 24 or 48-volt mode. This process is automatic and eliminates the
need for manual jumper settings or other user intervention. This process; can however, report the wrong value to the
controller if the connected battery bank has been depleted beyond normal limits (A fully dead battery). For example, if
a 24-volt battery has been allowed to deplete to perhaps 15 volts and the controller is restarted during this period, then
the controller will assume it is connected to a 12-volt bank, not 24 volt. If this occurs, then simply increase the bulk
charge point and let the battery bank recharge. Once the battery is recharged within normal limits; use the menu
system to reset the factory defaults or simply restart your controller.

18
OverVoltage:
To help prevent over-voltages, always power up the controller (ensure it is running on the batteries) before enabling
your turbine and/or solar panels. All solar panels and turbines must have a manual disconnect that allow you to safely
power up the controller and then and only then, enable the energy sources.
Version 6.01 and later of the C440-HVA and all versions of the C440-HVAD no longer use a fuse to protect against
over-voltage; instead, these controllers use a specialized over-voltage sensing circuit that is MUCH faster at detecting
and protecting against over-voltage conditions. This circuit will be engaged should the voltage rise above ~104 volts.
If this occurs, the O.V. LED will illuminate indicating the O.V. condition. You must remove power from the
controller to reset the O.V. circuit.
General Information:
All electronic components and terminals are isolated from the back-plate and steel enclosure preventing ground loops
as well as providing a small degree of lighting protection. Please read about proper grounding to ensure your system
is safe and protected from high voltages.
This unit is designed for mounting in a dry indoor environment. The enclosure will not protect the contents from
moisture. Please do not mount outdoors where rain, snow or high moisture content is a possibility.
** The solenoid in this unit has been tested to over 440 amps. We have installed two 150-amp breakers as a standard configuration.
This allows for 9000 watts of wind power in a 48-volt system, 4500 watts in a 24-volt system and 2250 watts in a 12-volt system.
Solar systems should be designed for no more than 125 amps continuous current. **
Higher voltage, higher amperage systems will result in a lower life expectancy of the solenoid. We recommend our
solid state controllers for larger solar systems, as they are designed specifically for moderate to large solar systems
and can switch on and off large solar currents many times per second for many years without failure of the solid-state
switching devices.
Note: Some of the circuit boards displayed may be from earlier version of this controller.
Modified 3/27/2017.
All of the content contained within the ColemanAir.us and mirroring websites as well as ColemanAir.us, Inc instructional material are subject
to copyright, trademark, service mark, trade dress and other intellectual property rights or licenses held by Coleman Air, Inc. Your use of the
trademarks, service marks, trade dress and copyrighted material and intellectual property displayed on this website and instructional material
is strictly prohibited. You may download, print and store selected portions of the Content, provided you (1) only use these copies of the
Content for your own personal, non–commercial use, (2) do not copy or post the Content on any network computer or broadcast the Content
in any media, and (3) do not modify or alter the Content in any way, or delete or change any copyright or trademark notice. No right, title or
interest in any downloaded materials is transferred to you as a result of any such downloading. ColemanAir, Inc. reserves complete title and
full intellectual property rights in any Content you download from this Web site or derived from our instructional materials. Except as noted
above, you may not copy, download, reproduce, modify, publish, distribute, transmit, transfer or create derivative works from the content.
Other manuals for C440-HVAD
1
Table of contents
Other Coleman Air Controllers manuals
Popular Controllers manuals by other brands
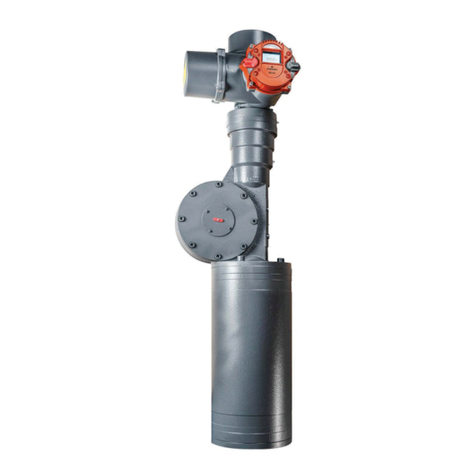
Emerson
Emerson Bettis RP4AF Installation, operation and maintenance manual
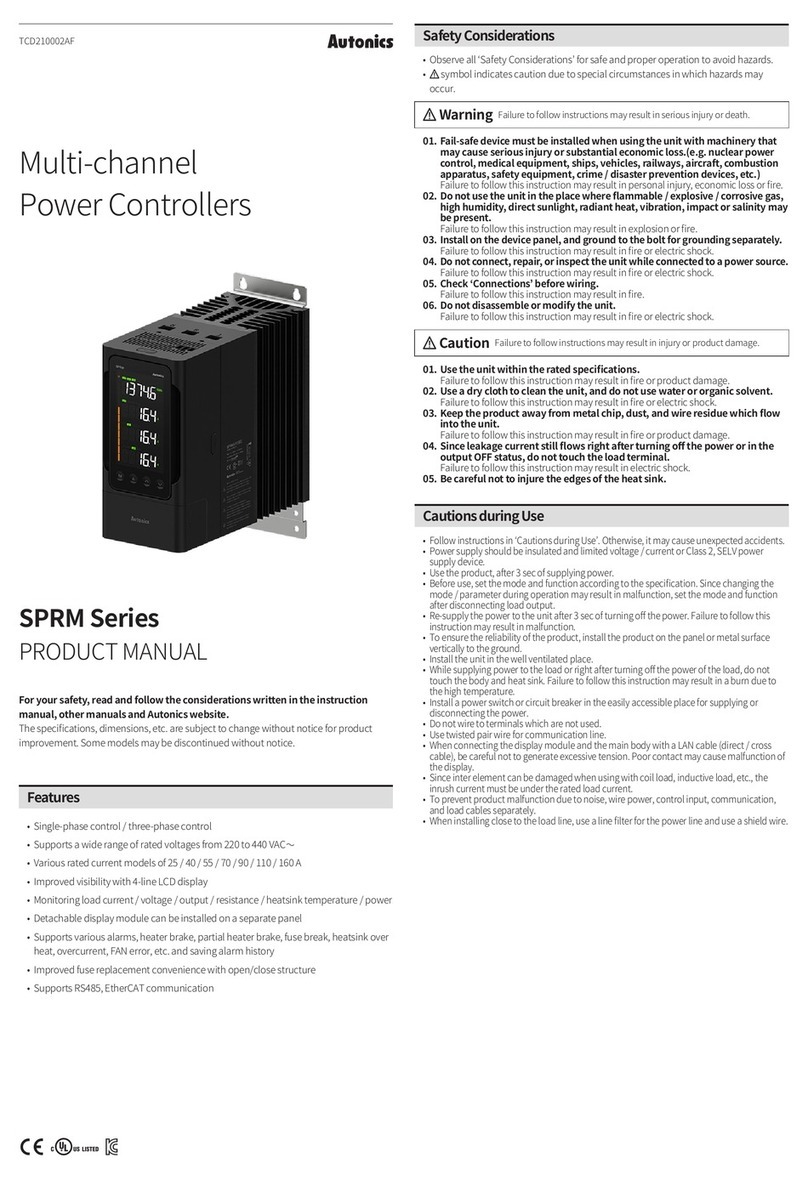
Autonics
Autonics SPRM Series product manual

Mode Lighting
Mode Lighting SceneStyLED4 user guide

Linear Technology
Linear Technology LT8611 manual

Nacon
Nacon MG-X Pro user manual
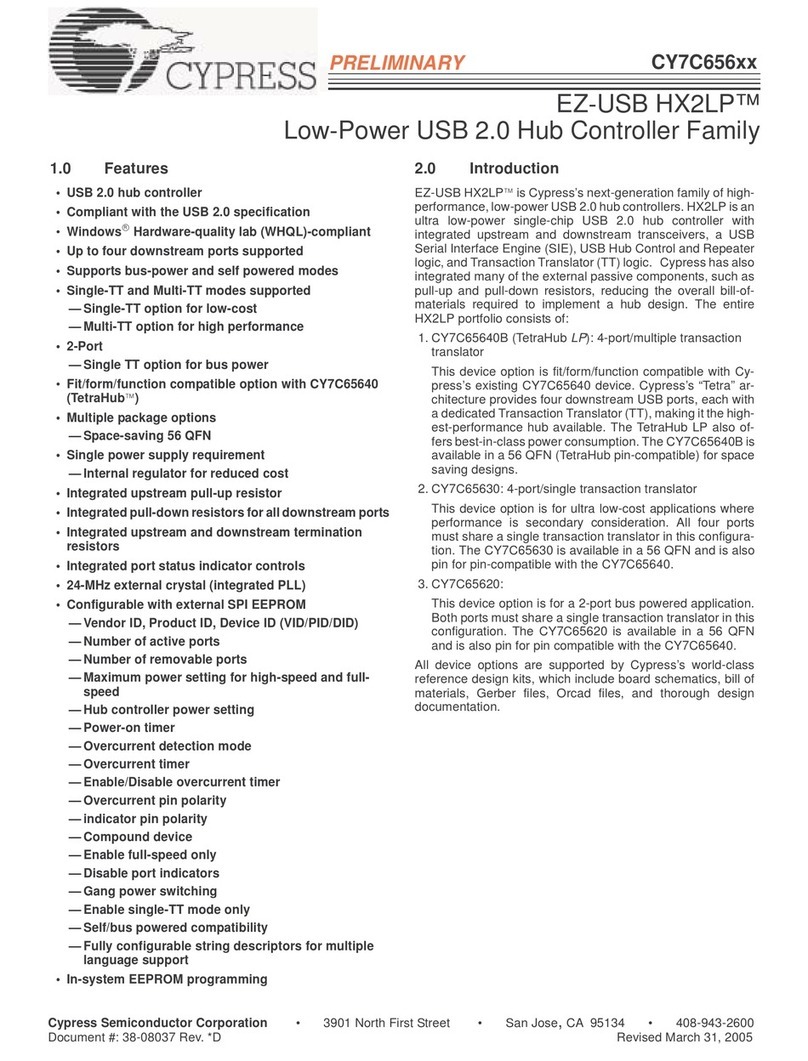
Cypress Semiconductor
Cypress Semiconductor CY7C656xx Specification sheet