Comprag A9013 User manual

+7 (800) 777-83-75(звонок бесплатный)
www.v-p-k.ru A9013
©Comprag ®. All rights reserved.
No part of the text and /or diagram may be reprinted or used without the prior written permission of Comprag.
The manufacturer reserves the right to make changes to a product design in order to enhance its technological
and operational parameters without notifying the user.
The product type may considerably differ to that displayed in documents.

+7 (800) 777-83-75(звонок бесплатный)
www.v-p-k.ru A9013
Table of contest
1.
Safety guidelines
1.1 Symbols used in the instructions
1.2 General safety guidelines
1.3 Safety precautions for start-up
1.4 Safety precautions during operation
1.5 Safety precautions for maintenance and repair
2.
Technical data and functional description
2.1 Technical data
2.2 General description
2.3 Function diagram and main components
2.4 Functional description
2.5 Control system
2.6 Electrical diagram and main components
2.7 Electrical connection values
3.
Start up
3.1 Lifting and carrying
3.2 Dimensions
3.3 Requirements on installation area
3.4 Connection to the compressed airline
3.5 Connection to power supply
4.
Operation
4.1 Controller and operating panel
4.2 Error indication
4.3 Starting the compressor
4.4 Switching off the compressor
5.
Maintenance
5.1 Maintenance schedule
5.2 Checking oil level
5.3 Checking drive belt
5.4 Replacing oil and oil filter
5.5 Replacing air filter
5.6 Changing drive belt
5.7 Changing air-oil separator
5.8 Cleaning radiator
5.9 Checking suction valve
5.10Servicing bearings of electric motor
6.
Fault handling
6.1Faults and corrective actions
7.
Storage and disposal
7.1Storage conditions
7.2 2 Disposal of oils and process condensate
EN

+7 (800) 777-83-75(звонок бесплатный)
www.v-p-k.ru A9013
1.
Safety guidelines
1.1
Symbols used in the instructions.
Lethal hazard.
Warning.
Attention.
1.2
General safety guidelines.
Carefully familiarise yourself with the technical documentation,
operating instructions and safety guidelines. Most accidents as-
sociated with the use of compressor equipment occur as a result
of non-compliance with safety guidelines. Prevent hazards from
developing and adhere to the safety guidelines. The main rules
are given in the following section.
The user is solely liable for injuries or damages which occur due
to non-compliance with safety guidelines during installation, op-
eration or servicing, as well as unauthorised use of equipment!
1. The operator must stringently adhere to safety guidelines provided for by these instruc-
tions and local legislation!
2. When choosing between these safety guidelines and the regulations provided for by
local legislation, those rules which provide for more stringent requirements shall apply.
3. Only trained maintenance personnel with the relevant level of professional training are
permitted to operate, service and repair Comprag equipment.
4. Compressed air flowing immediately from the compressor may contain oil and impurities

+7 (800) 777-83-75(звонок бесплатный)
www.v-p-k.ru A9013
and is not suitable for breathing! Compressed air has to be purified to an air purity grade
suitable for breathing, in accordance with the standards prescribed by local legislation.
5. Compressed air is an extremely hazardous energy source. Compressed air must not be
used for unintended purposes! Do not use it to clean clothing and footwear and never
point compressed air hoses at people and animals! When using air to clean equipment,
take extra caution and wear safety goggles!
6. All maintenance, repair, setup and installation work etc. must be performed while the
equipment is turned off, disconnected from the power source, with compressed-air hos-
es disconnected from the equipment, and with the use of safety goggles! Ensure that
equip- ment is disconnected from the compressed air system and is not under pressure.
1.3
Safety precautions for start-up
The user is solely liable for injuries or damages which occur due to
non-compliance with safety guidelines during installation, operati-
on or servicing, as well as unauthorised use of equipment!
1. Equipment must only be unloaded/loaded using the appropriate handling devices or hoisters.
Equipment must not be manually lifted or moved. Do not leFVe equipment sus- pended. Use
a helmet during unloading operations.
2. Arrange the equipment in a dry and clean facility which provides shelter from precipi- tation.
The facility must be well ventilated, and forced ventilation should be provided if necessary.
3. Worn, damaged or spoiled compressed-air hoses should not be used. Ensure that hoses cor-
respond to the equipment in terms of nominal diameter and working pressure.
4. When using several compressor stations in a system, each compressor must hFVe a manually
operated valve for cutting off any of the compressors in the case of emergency.
5. Explosive and fire-hazardous admixtures such as solvent vapours and carbon dust etc.must
not be released into the atmosphere.
6. Ensure unrestricted access to the compressed-air hose from the compressor. Do not clutter it
and do not store flammable materials in its immediate vicinity.
7. Do not pinch or deform the compressed-air feed hoses.
8. Do not cover holes used to provide equipment with air for cooling. Ensure the facility is well
ventilated.

+7 (800) 777-83-75(звонок бесплатный)
www.v-p-k.ru A9013
9. When using remote control, the equipment must give a legible and clear warning of this:‘AT-
TENTION: this machine is being controlled remotely and may start operating without warning!’
An operator who is remotely controlling equipment must ensure that no installation or other
work is being performed with the equipment at that moment. Once the equip- ment is turned
off remotely, the operator must ensure that the equipment is actually turned off!
10. Equipment must be earthed. Provide short-circuit protection. The starting knife switch must
be in the immediate vicinity of the equipment and protect against unauthorised start-up.
The user bears full responsibility for compliance with the operat-
ing condi- tions of the electrical motor installed in the equipment.
Equipment must be used with protection devices. The protection devices
must protecttheelectricmotor fromshortcircuits,overloading(systematic
and start-up)and open-phaseconditions.Installationof protectiondevices
is the responsibility of the user.
11. There must be an information plate affixed next to the control panel on equipment with an in-
dependent control system featuring an automatic restart function: ‘ATTENTION: This machine
may start operating without warning!’
12. Any tanks and vessels working under pressure must be fitted with safety-relief valves! Unau-
thorised installation, disassembly or adjustmentof attached safety-relief valves is not allowed.
1.4
Safety precautions during operation.
The user is solely liable for injuries or damages which occur due to
non-compliance with safety guidelines during installation, opera-
tion or servicing, as well as unauthorised use of equipment!
1. Ensure that hoses correspond to the equipment in terms of nominal diameter and working
pressure. Check the attachment of every hose coupling before start-up. An insecurely fas-
tened hose may cause serious injury.
2.
Never turn on equipment if you suspect the presence of highly flammable impurities in the air!
3. The operator remotely controlling equipment must ensure that no installation or other
work is being performed with the equipment at that moment! An information plate must
be affixed to the equipment in relation to this: ‘ATTENTION: this machine is being controlled
remotely and may start operating without warning!’
4. An operator is not allowed to operate equipment if the operator is fatigued, in a state of
intoxication from alcohol, drugs or medicine that reduces the body’s reaction time.
5. The equipment must not be operated if parts of the casing hFVe been removed. Doors or
panels may be opened for short durations for inspection and scheduled checks. It is advis-
able to wear hearing protection.

+7 (800) 777-83-75(звонок бесплатный)
www.v-p-k.ru A9013
In some types of equipment, open doors or removal of panels du-
ring operation may lead to overheating.
6. Personnel in conditions or a facility where the sound pressure level reaches or exceeds
90 dB (A), must wear ear protectors.
7. If the air used for cooling equipment is used while the facility is being heated, undertake
measures for it to be filtered so that it is suitable for breathing.
8. Regularly check that:
•safety devices and attachments are in place;
•all hoses and pipes are in good condition and sealed;
•there are no leaks;
•brackets and structural components are tightened;
•all electrical cables and contacts are in good condition and safe to use;
•safety devices are fully functional and there is no contamination etc;
•all structural components are in working order, with no signs of wear and tear.
1.5
Safety precautions for maintenance and repair
The user is solely liable for injuries or damages which occur due to
non-compliance with safety guidelines during installation, operati-
on or servicing, as well as unauthorised use of equipment!
1.
Only original spare parts and ancillary items may be used. Using spare parts from other man-
ufactures may lead to unpredictable results and consequently accidents.
2.
When performing installation and repair work, always wear goggles!
3.
Before connecting or disconnecting equipment, disconnect it from the main pneumatic sys-
tem. Ensure that the hoses aren’t under pressure!
4.
Before beginning installation or other work, ensure that equipment is not pressurised. Instal-
lation work must not be carried out on equipment under pressure.
5.
All maintenance work should be carried out only when the temperature of all structural ele-
ments falls to room temperature.
6.
Never use highly flammable solvents or carbon tetrachloride for cleaning structural elements.
When wiping, take precautions against the poisonous vapours of cleaning fluids.
7.
Whencarryingoutinstallationand repairwork,an informationplateshouldbe affixedto thecontrol
panelto warnagainstunauthorisedstart-up.For example,“Do notturnon.Personneloperating!”

+7 (800) 777-83-75(звонок бесплатный)
www.v-p-k.ru A9013
8.
The operator remotely controlling equipment must ensure that no installation or other work is
being performed with the equipment at that moment! An information plate must be affixed to
the equipment in relation to this: See 1.3.9.
9.
Maintain cleanliness in the facility where the equipment is installed. Close open inlets and out-
lets during installation with dry clothes or paper to prevent rubbish entering the equipment.
10.
Welding or other similar operations must not be carried out in the immediate vicinity of the
equipment and vessels under pressure.
11.
If there is any suspicion of overheating, combustion or other emergency, turn off the equip-
ment. Immediately disconnect it from the power supply. Do not open the doors of equipment
until the temperature falls to room temperature, in order to prevent burns or injury.
12.
Naked flames must not be used as a light source for inspecting and checking equipment.
13.
Never use caustic solvents, which may damage materials of the pneumatic system
14.
After performing installation or other work, ensure that no instruments, rags or spare parts
hFVe been left inside the equipment.
15.
Pay particular attention to the safety-relief valves. Thoroughly inspect them and remove
any dust and dirt. They must not be allowed to suffer any loss in function under any circum-
stances. Remember that your safety depends on their functionality!
16.
Before beginning work in normal mode after maintenance or repair work, check that the
working pressure, temperature and other characteristics are correctly set. Ensure that all
control devices are installed and functioning properly.
17.
When replacing filters, separators etc., wipe away dust, dirt and oil residue from the area
where they are installed with a dry cloth.
18.
Protect the motor, air filter, electrical components and control components etc. from com-
ing into contact with condensate. For instance, blow down with dry air.
19.
Use protective gloves during installation and repair work in order to FVoid burns and injury
(for instance, during oil change).

+7 (800) 777-83-75(звонок бесплатный)
www.v-p-k.ru A9013
2.
Technical data and functional description
Entitlement to free handling of faults arising during the guarantee pe-
riod is forfeited when:
-No warranty service coupon for the compressor or it is filled out
incorrectly
-
No records for the compressor’s scheduled maintenance are entered
in the compressor’s service book
-
Unoriginal parts and lubricants are used
2.1
Technical data
Article
Model
Drive
power,
compressor
(kW)
Max. operat-
ing pressure
(bar)
Output
(m3/min)
Rated
voltage,
compressor
(phase/V/Hz)
Noise
(dB)
Screw
connection
Oil
capacity,
liter
11410904
A7508
75
5-8
12,40
3/380/50
75
2"
35
11410905
A7510
5-10
10,80
11410914
A9008
90
5-8
14,70
75
11410915
A9010
5-10
12,80
2.2
General description
The A-Series oil-filled screw compressor series is designed for uninterrupted and efficient-
compressed-air production.
The A-Series compressor is an electric motor-operated, intake-regulated, belt-driven and air-
cooled compressor, enclosed in a sound-insulated canopy. An electronic controller i-Log with
an LCD indicator panel is provided, including start and stop buttons and an emergency stop
button. Pressure and temperature relays are used for system control and protection.

+7 (800) 777-83-75(звонок бесплатный)
www.v-p-k.ru A9013
2.3
Function diagram and main components
Fig. 2.3 Function diagram A75-90
Main components
1
Electric motor
11
Min. Pressure valve
2
Belt drive
12
Non-return valve
3
Air end
13
Heat-exchanger, Air section
4
Air filter
14
Heat-exchanger, Oil section
5
Intake valve
15
Thermostatic valve
6
Air-Oil separation tank
16
Oil filter
7
Safety valve
17
Drain valve
8
Air-Oil separator
18
Oil filling plug
9
Throttle valve
19
Oil level sight glass
10
Non-return valve
20
Air outlet valve
Air ffow
Temperature sensor

+7 (800) 777-83-75(звонок бесплатный)
www.v-p-k.ru A9013
2.4
Functional description (see Fig. 2.3)
Air flow:
Air drawn through Air filter (4) and open Intake valve (5) into compressor Air-end (3) is compressed.
Compressed air and oil flow into Air-Oil separation tank (6). The air is discharged via Min. Pressure
valve (11) through Heat-exchanger (13) towards the Air Outlet Valve (20).
Oil flow:
Air pressure forces oil from the air-oil separation tank (6) through the heat-exchanger (14) and
the oil filter (16) to the compressor air-end (3) and the lubrication points. In the air-oil separation
tank (6), most of the oil is removed centrifugally; the rest is removed by the air-oil separator (8).
The oil system is fitted with a thermostatic valve (15). When the oil temperature is below the
set-point of the thermostatic valve, the thermostatic valve shuts off the oil supply from oil heat-ex-
changer (14). The thermostatic valve starts opening the supply from heat- exchanger (14) when
the oil temperature exceeds the valve’s setting. The setting of the thermostatic valve depends on
the model. See table Technical Data.
Cooling system:
The cooling system comprises a combined air section (13) and an oil section (14) heat- exchanger.
A cooling fan, equipped with a separate electric motor, generates the cooling air in order to cool
the heat-exchanger.
2.5
Control system
Fig. 2.5 Control system
3 4

+7 (800) 777-83-75(звонок бесплатный)
www.v-p-k.ru A9013
The compressor is provided with a controller (2) to control parameters, which in automatic mode
tracks consumer air consumption.
Main operating mode:
Upon start-up, the frequency inverter accelerates the compressor over 15 seconds to the maximum
permitted frequency. Pressure builds up to the specified target value. When it is reached, the compres-
sor maintains the set pressure by varying the current signal coming from the frequency inverter. If the
consumption of compressed air increases, the frequency coming from the frequency inverter also in-
creases and thus the rotation of the main motor shaft. If the consumption of compressed air decreas-
es, the frequency coming from the frequency inverter also decreases. However, the compressed-air
pressure remains constant. When the off button is pressed, the frequency inverter lowers the frequen-
cy over 15 secondsto the minimum permitted frequency and switchesoff the compressor.
Unloading:
When air consumption by the consumer is lower than the lowest possible compressor output, the pneu-
maticsystempressurereachesthespecifiedmaximum.Thesolenoidvalveisnotenergised,anditopens.
1. Pressureis fedto thethrottle(5) of thesuctionvalve(1),andthethrottleis closed.Airintakeceases.
2. The discharge valve (7) opens and releases the internal pressure, unloading the system and the
separator tank (4).
3. The system pressure stabilises, no air is consumed and the compressor switches to standby
mode: the motor does not switch off.
The standby mode time before shutdown or turning on of the compressor can be set on the controller
according to consumption requirements.
Loading:
As air consumption increases, the pneumatic system pressure falls to the minimum set threshold,
and the solenoid valve (3) is energised and closes. Pressurised air to the throttle (5) ceases and the
throttle closes. The discharge valve (7) closes. Air enters the air end (6). The compressor switches
to loading mode.

+7 (800) 777-83-75(звонок бесплатный)
www.v-p-k.ru A9013
2.6
Electrical diagram and main components
Fig. 2.6 Electrical diagram A75-90
Main components
2.7
Electrical connection values
Voltage (V)
Frequency (Hz)
A75..
A90..
Мaterial - copper. Cable size (mm²)
380 / 400
50
70
95
Fuse value (A)
380 / 400
50
160
200
"RS-485"
3 X 380-415VAC
К1---К4
Contactor
YA
Solenoid valve
М1, М2
Electric motor
QS
Automatic power switch
Т
Temperature sensor
CT1, CT2
Current Transformer
I/P
Pressure sensor
R,C
RC elements
SB
Emergency stop
Tr
Transformer
F1, F2
Fuses
i-LOG
Controller

+7 (800) 777-83-75(звонок бесплатный)
www.v-p-k.ru A9013
3.
Start up
3.1
Lifting and carrying
Allliftingshouldbecarriedoutusingaforklifttruckwithacarryingcapacity
suitedtothecompressor.Liftingmaybecarriedout withloadingcranes,
winches and other machinery, using a crossbeam with the right length.
Local safety guidelines for lifting hFVe to be observed.
For transport with a forklift truck, use the rigging holes in the frame. The compressor has slotted
rigging holes with width C –fig. 3.1. Move the compressor carefully.
Fig. 3.1 Lifting and carrying A75-90.
A,mm
B, mm
C, mm
D, mm
F, mm
G, mm
H, mm
L, mm
350
676
180
758
1790
1890
1490
1960
C C

+7 (800) 777-83-75(звонок бесплатный)
www.v-p-k.ru A9013
3.2
Dimensions
Fig. 3.2 Dimension drawing A75 –90.
Model
Compressor dimensions
Length
L, mm
Width
D, mm
Height
H,mm
Weight,
kg
A75
1490
1960
1790
1580
A90
1690
Packaging dimensions
A75
1580
2090
1970
1620
A90
1740
3.3
Requirements on installation facility
Fig. 3.3 Installation facility proposal A75 –90.
1. Air inflow
2. Air outflow
Ensure that the floor of the facility can withstand the weight of the compressor. Install the
compressor on a level surface that is able to bear its weight. Adjust the horizontal axis of the
compressor using a levelling instrument. If the compressor is not anchored to the base on
which it is installed, the tilt angle with respect to the horizontal surface must not exceed 3°.
2
1
1500
1500

+7 (800) 777-83-75(звонок бесплатный)
www.v-p-k.ru A9013
If the compressor is anchored to the base on which it is installed, the tilt angle with respect to
the horizontal surface must not exceed 7°. Install the compressor in a facility where precip-
itation cannot reach. Choose a facility for installing the compressor with a minimum level of
dust. Install the compressor at least 1,5 m from walls.
If multiple compressors are installed, there should be a 1,5 m minimum distance between
each compressor. There should be a 4 m safety distance from the area of the operated equip-
ment connected to the compressor. The facility in which the compressor is installed must be
fitted with a combined extract-and-input ventilation system.
The facility where the compressor is installed should be provided
with air inflow equivalent to twice the compressor’s capacity.
The volume of extraction ventilation must not exceed 40% of the air inflow capacity of the input
ventilation in a facility where the compressor is installed and fitted with an extract- and input ven-
tilation system.
The compressor should not be installed in a facility where the temperature may drop below +5°С.
In order to extract hot air flowing out the compressor, an air duct may be used that is up to 3 m in
length and with a cross section 20% larger than that of the air-outflow orifice from the compressor’s
radiator. If an air duct longer than 3 m is used, additional duct fans should be used.
3.4
Connection to the compressed airline
Provide the throughput capacity of the compressed-air line in accordance with the perfor-
mance of the compressor. In order to FVoid damage associated with seal failure of the com-
pressed-air line, the compressor should be connected via a flexible hose. All components of
the compressed-air line must hFVe a working pressure no less than the compressor’s nominal
pressure. Use a pressure vessel with a capacity corresponding to the compressor’s perfor-
mance and the compressed air consumer.
3.5
Connecting to power supply
The compressor is not supplied with a power cable. The cable size must be chosen to ensure
that the maximum voltage drop not exceed 5 % of the nominal voltage value. Cable length
must not exceed 25 m. Ambient temperature in the facility must not exceed 40°C. The cable
must be sheathed with a fire retardant compound. An isolating switch must be fitted within
reach of the compressor to facilitate connection and maintenance.
The compressor must be earthed and protected against short cir-
cuits in each phase, impermissible voltage fluctuation and phase
failure.
The power cable has to be fed into the compressor.

+7 (800) 777-83-75(звонок бесплатный)
www.v-p-k.ru A9013
Fig. 3.5 Power cable connection
Removetheleftsidepanel,passthecableunderthecompressorintotheorifice(1)andcableglang(2).
The earth wire of the power cable must be connected to the corresponding earthing bolt 3.
4.
Operation
Non-qualified personnel must not be allowed to operate the com-
pressor.
4.1
Control panel
The frequency-controlled compressors A30 and A90 are equipped with an electronic i-Log control.
The electronic i-Log control maintains the network pressure between the programmable limit values by
automatically adjusting the compressor speed. Operating data such as operating times and system
statusesarealso recorded.

+7 (800) 777-83-75(звонок бесплатный)
www.v-p-k.ru A9013
4.1.1
i-Log control panel
Fig. 4.1.1 i-Log control panel
Start compressor
Up or increase value
Stop compressor
Down or reduce value
Back to the main menu
Save setting
Accept value / manually switch between loaded and idle running
4.1.2
LCD indicator
Power indicator (red): The indicator lights up when the control is switched on and
the power supply is connected.
Power indicator (green): The indicator lights up when the motor is running.
Alarm/error indicator (red). Alarm (warning): The indicator flashes and the ma-
chine continues to run. Error: The indicator is permanently lit, there is an accom-
panying acoustic signal and the machine switches off. The error message can be
acknowledged after the cause of the error has been resolved. In order to acknowl-
edge the error message, press and hold the ‘back to main menu’ button .
LED indicators.
When switched on, the LCD display shows the following:
COMPRAG SCREW
AIR COMPRESSOR

+7 (800) 777-83-75(звонок бесплатный)
www.v-p-k.ru A9013
The main parameters of the compressor are displayed after 5 seconds:
21°C 0.00HZ
0.0BAR 0RPM
STOP
C01 LOKAL
Main menu: Click in order to bring up the options menu:
RUN PARAMETERS
USAGE PARAM
FACTORY PARAM
Includes current values (available for viewing)
Includes operating settings of the main parameters (available for viewing,
changes password-protected)
Forservicingmode(viewwithpassword).Modificationonlypossiblebymanufacturer
ADJUST. PARAM
Basicsettingsandmaintenancehourcounter(Passwordprotected)
Description of the parameters. Run parameters:
Select the run parameters using the up and down buttons and enter . Current values
are displayed.
M1 AND FAN CUR
TOTAL RUN TIME
THIS RUN TIME
MAINTEN. PARAM
ERRORS HISTORY
SERIAL NUMBER
THIS ERROR
COM. STATUS
Theothermenushaveasimilarstructure.
Selecttheline“M1 AND FANCUR ”and press .
M1(A) AND FAN(A)
Phase current of main motor and fan motor
A: 000.0 000.0
B: 0.0 0.0
C:0.0 0.0
TOTAL RUN TIME
TOTAL RUN TIME:
Total running hours (main engine running).
TOTAL LOAD TIME:
Total operating time under load (main engine running+ suction valve open).
THIS RUN TIM
THIS RUN TIME:
The current operating time from the last start.
THIS LOAD TIME:
Current running time under load

+7 (800) 777-83-75(звонок бесплатный)
www.v-p-k.ru A9013
MAINTEN. PARAM
IN USAGE (H)
Time in operation (hours).
OIL FILTER:
Operating time
SEPARATOR:
Operating time
AIR FILTER:
Operating time
OIL:
Operating time
GREASE M1:
Operating time
BELTS:
Operating time
HISTORY OF ERRORS
THIS ERROR
COM. STATUS
COM. STATUS
This model is not used.
If there is no activity for 60 seconds in the current menu, the control will automatically return
to the main menu.
Description of the parameters. Usage parameters:
The contents of this menu item can be displayed, but modifications are password-protected.
Modifications may only be carried out by trained and qualified personnel.
Select the usage parameters using the up and down buttons and enter .
SET P, T, FREQ
SET TIME
OPERATION MODE
SEQ PARAM SET
RST MAINT TIME
MAX RUN TIME
USER PASS:
LANG.
Select „PRES/TEMP SET“ using the up and down buttons and enter . Current values
are displayed. (Below are the example set values for the compressor with the max. 8-bar operating
pressure).
P LOAD: --.- bar
Loading pressure
P ULD: --.- bar
Unloading pressure
T FAN ON: 0095°C
Switch-on temperature for the fan
T FAN OFF: 0060°C
Switch-off temperature for the fan
ERRORS HISTORY
5 last errors (see below).
THIS ERROR
Active error (see below)
Table of contents
Languages:
Other Comprag Air Compressor manuals
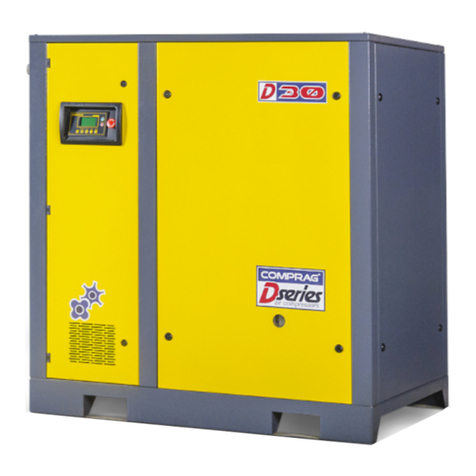
Comprag
Comprag D Series User manual
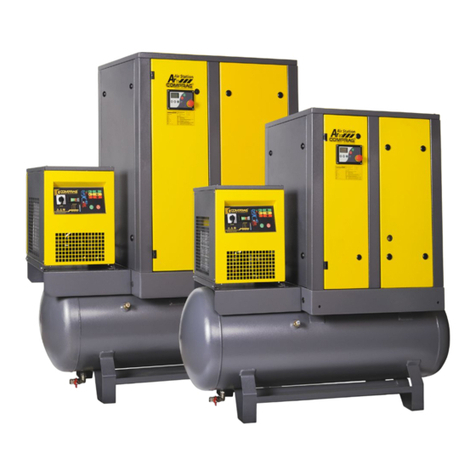
Comprag
Comprag A-Series User manual
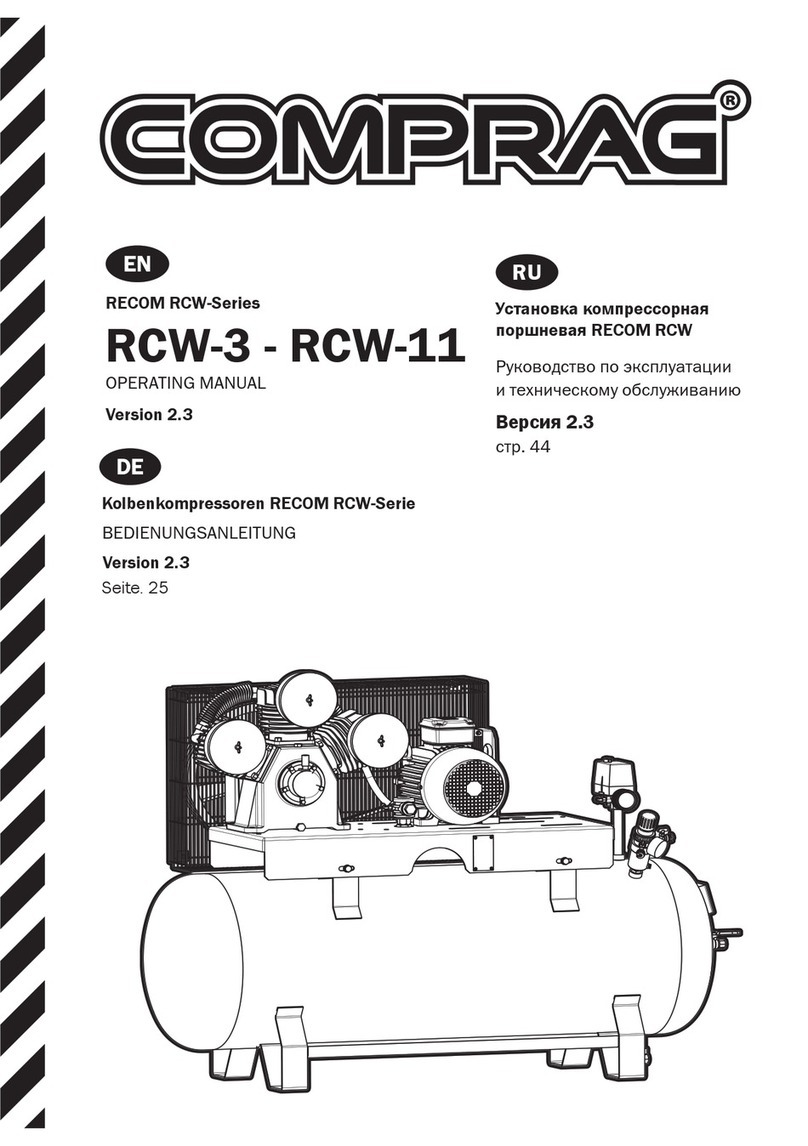
Comprag
Comprag RECOM RCW Series User manual
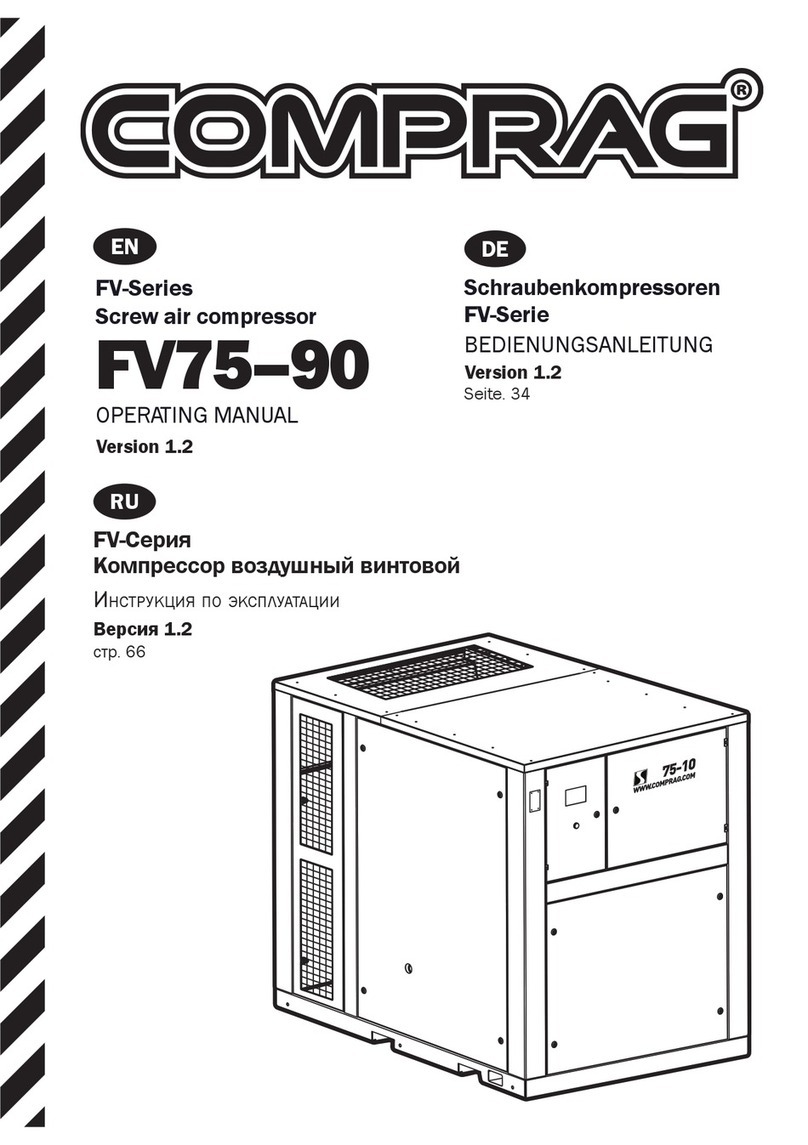
Comprag
Comprag FV Series User manual
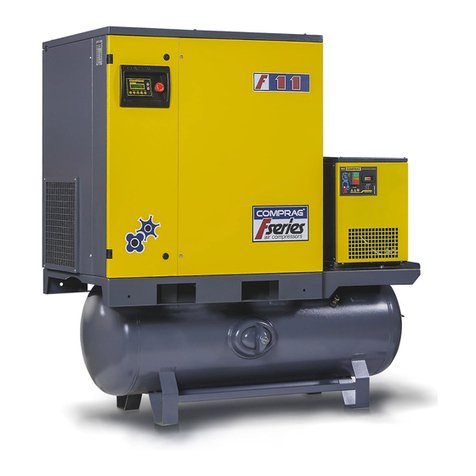
Comprag
Comprag F Series User manual
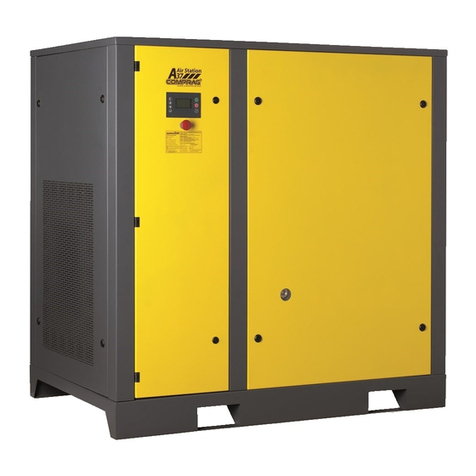
Comprag
Comprag A-Series User manual
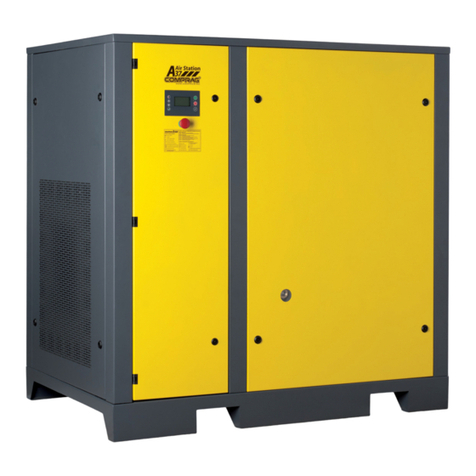
Comprag
Comprag A3008 User manual

Comprag
Comprag A-Series User manual
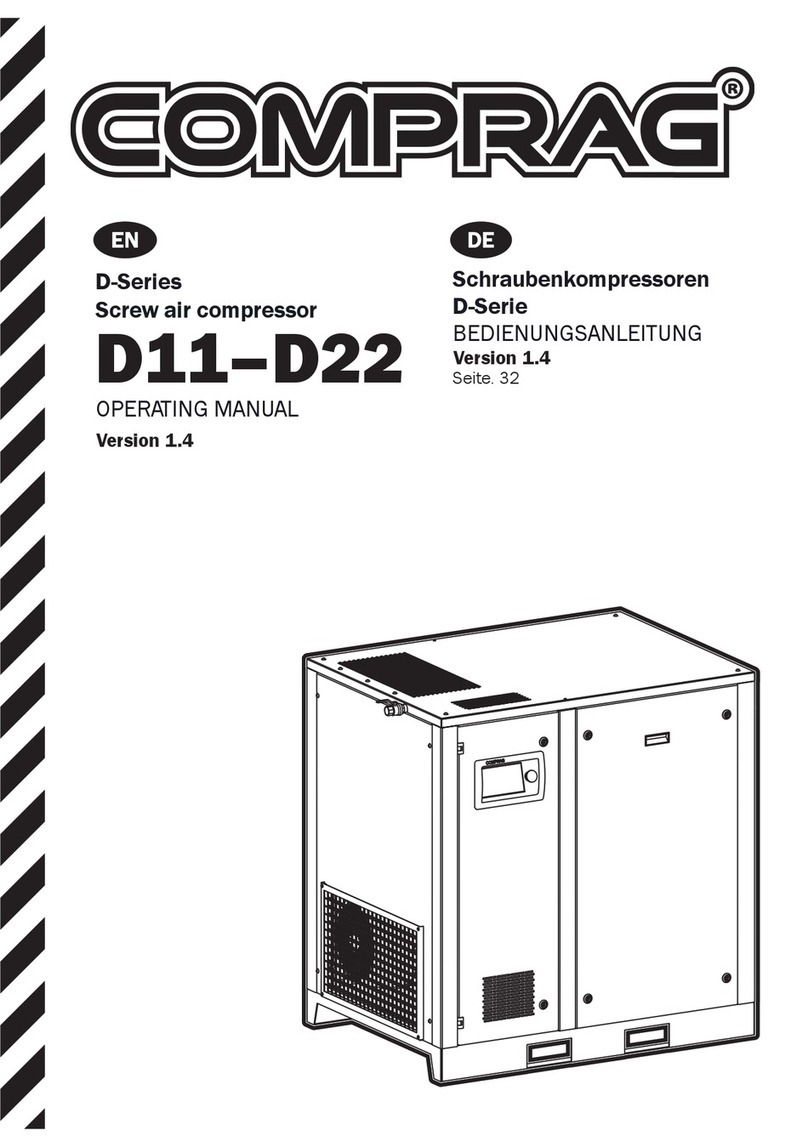
Comprag
Comprag D Series User manual
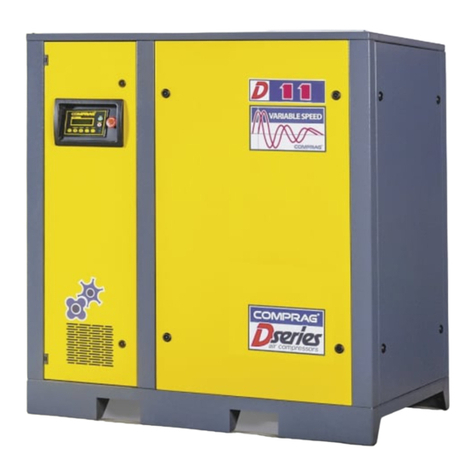
Comprag
Comprag DV Series User manual
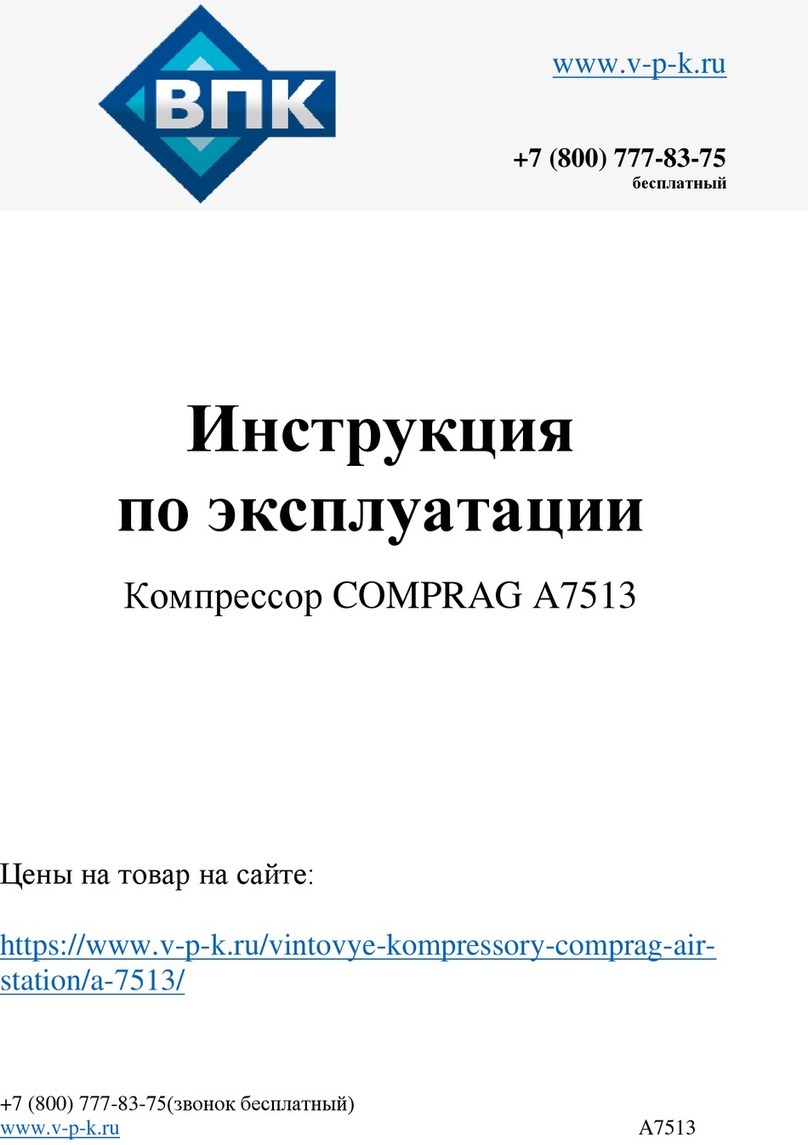
Comprag
Comprag A7513 User manual

Comprag
Comprag D7510 User manual

Comprag
Comprag AV-Series User manual
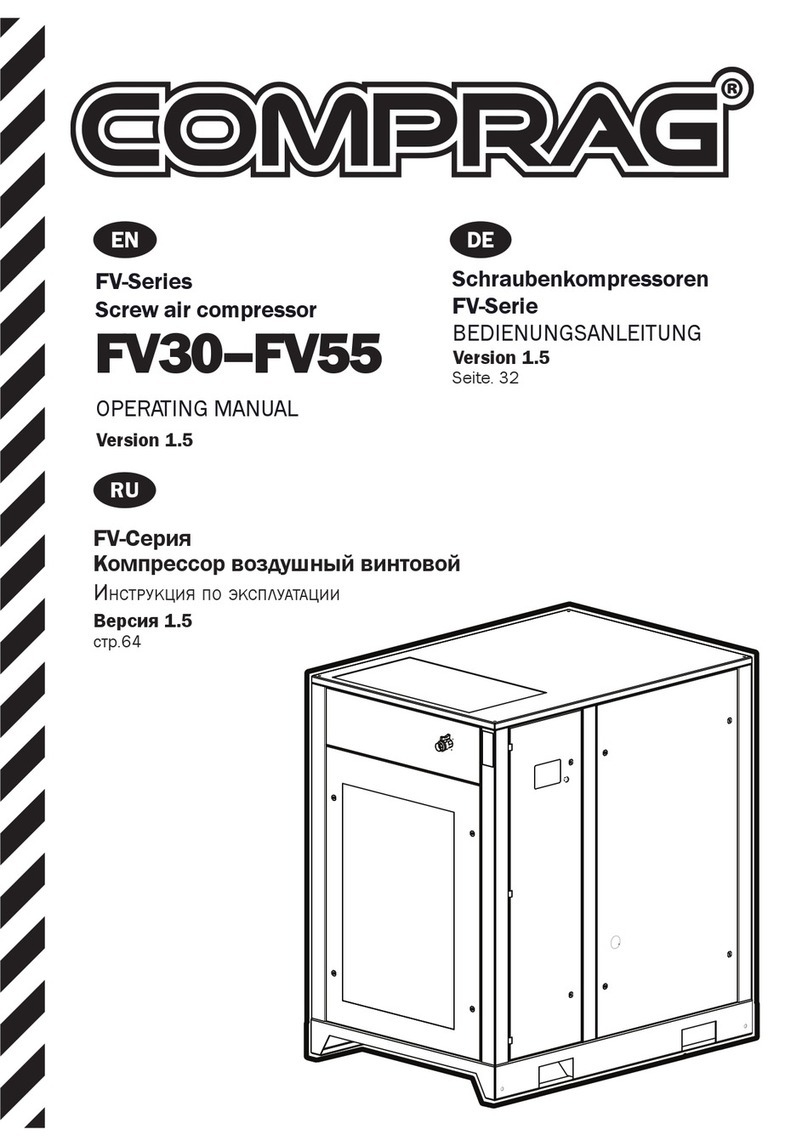
Comprag
Comprag FV30 User manual
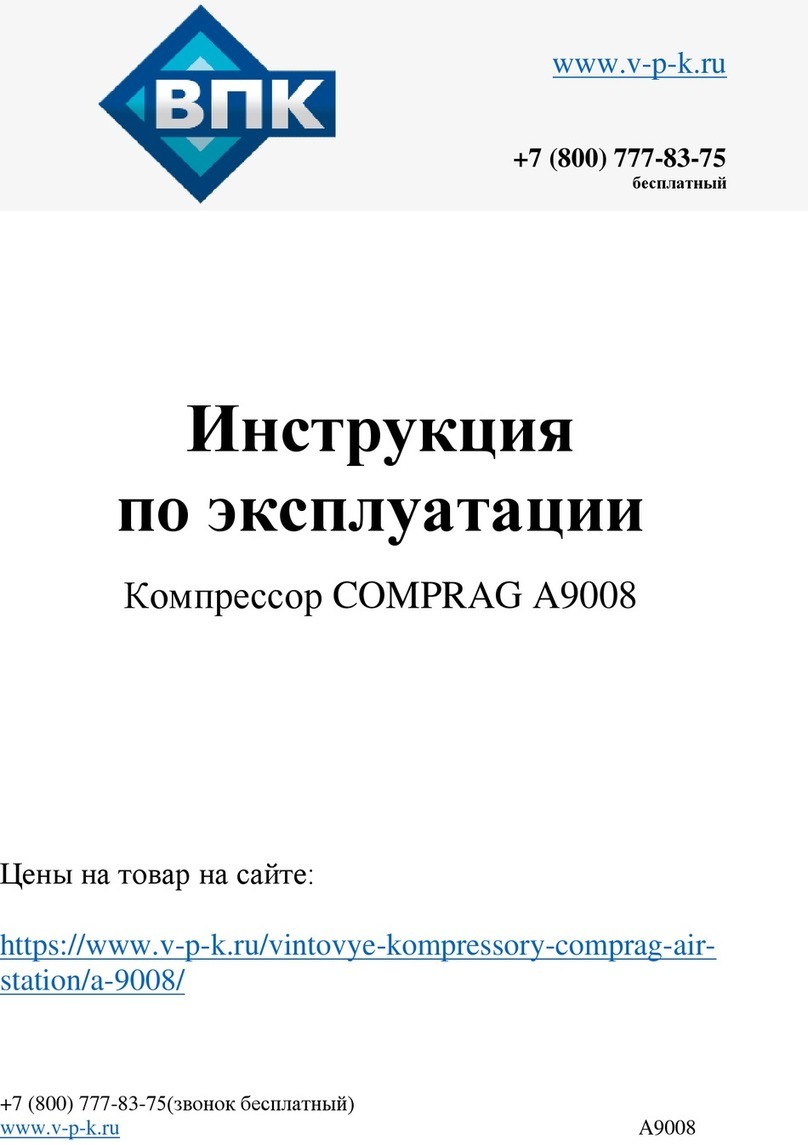
Comprag
Comprag A9008 User manual
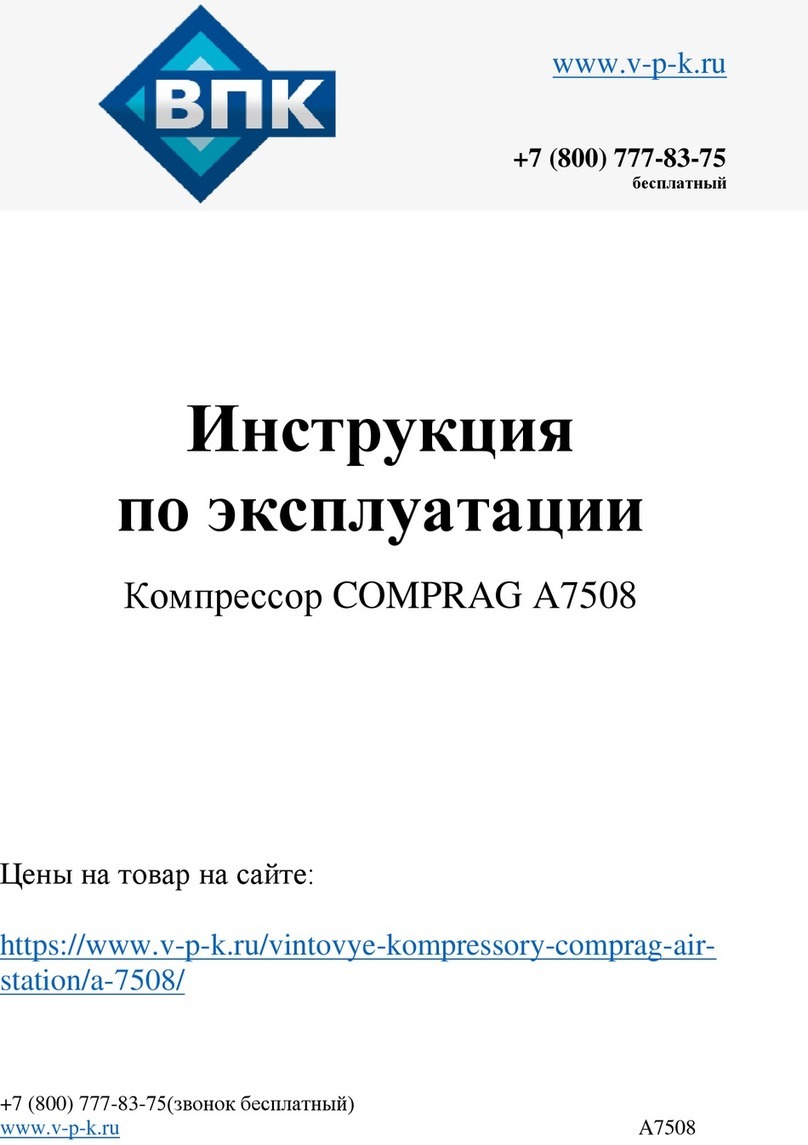
Comprag
Comprag A7508 User manual

Comprag
Comprag AV30 User manual
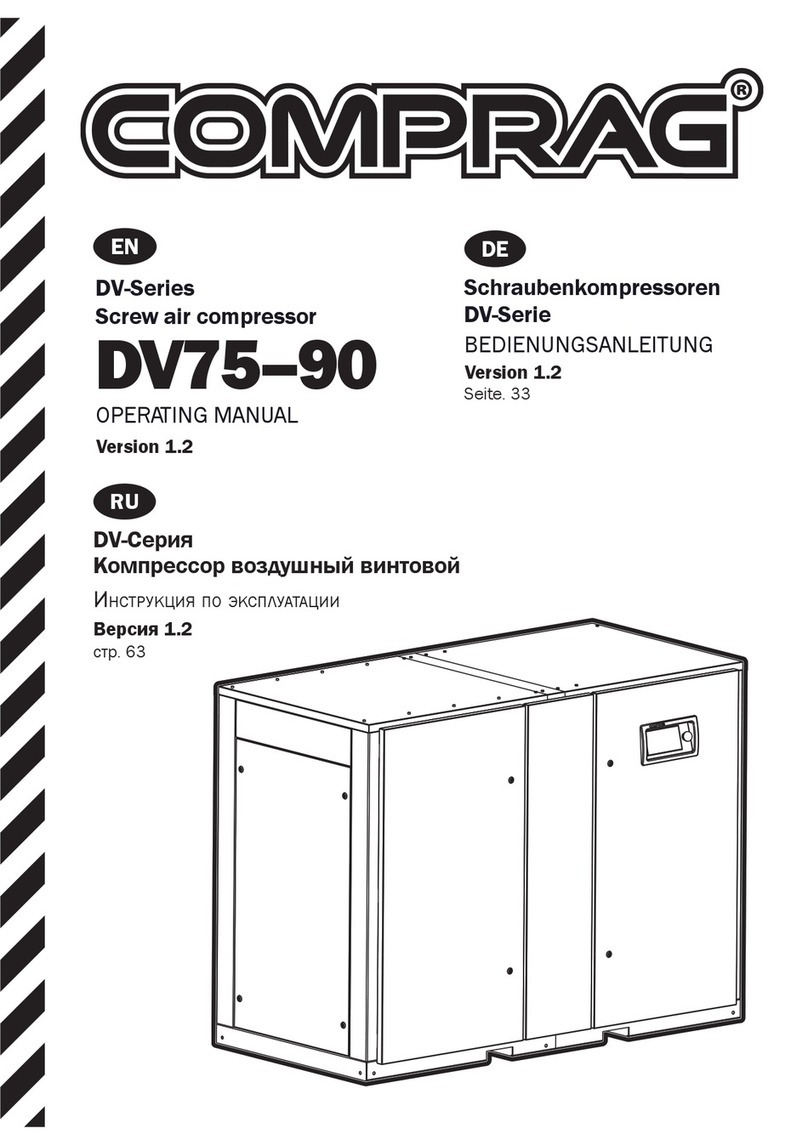
Comprag
Comprag DV7508 User manual
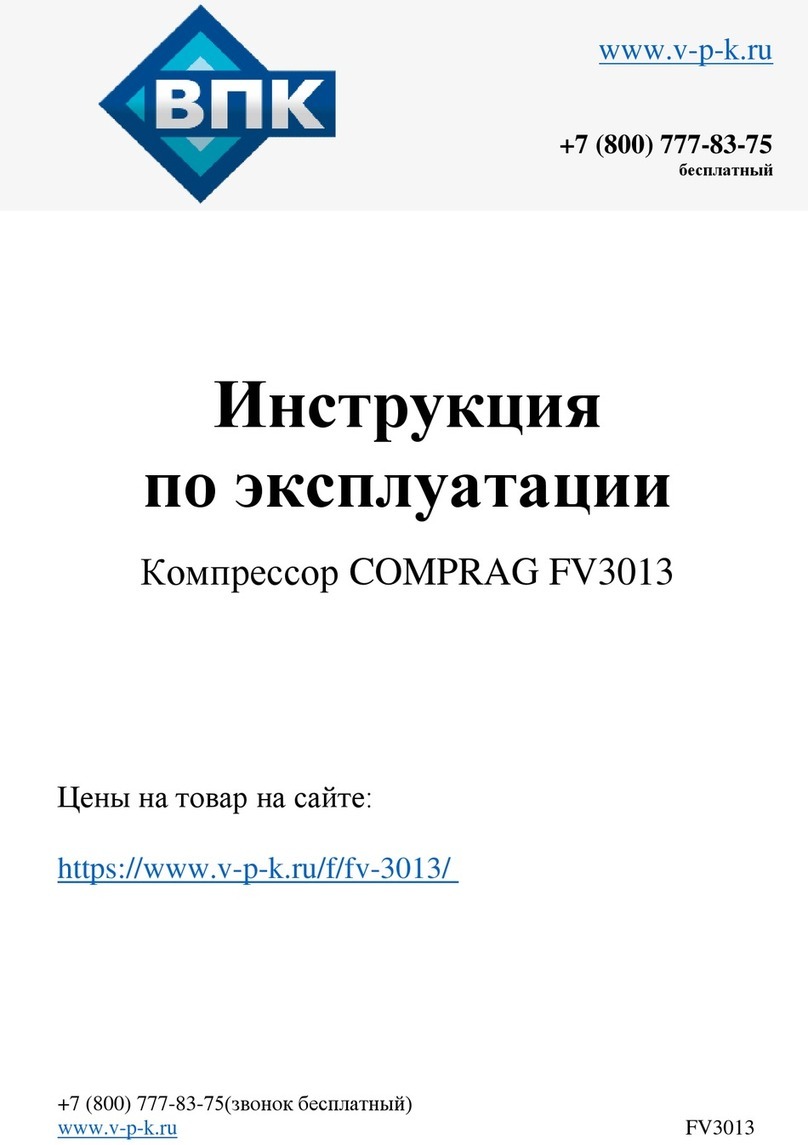
Comprag
Comprag FV3013 User manual

Comprag
Comprag A7510 User manual