Condor 900 191 - V1.0 User manual

Reprinting, even in part, is permitted only with the express approval of the manufacturer. Subject to technical changes.
Operating Instructions
“Ebb-Flow”
Riding Arena Control System
with
Touch TFT Display
Version: 26/01/2021 Version: 900 191 Condor GB – V1.0
GLP: from HW 2.30
CPU: from HW 1.10
SW: V0.06
These operating instructions refer exclusively to the electronic control system and
contain important information and safety comments. These operating instructions
must be read and followed before the installation, electrical connection and
commissioning are completed.
Descriptions and instructions in these operating instructions refer to the standard version of
the control system. These operating instructions do not include all design details and variants,
nor all possible coincidences and events, that could possibly occur during installation,
operation or maintenance. Improper use, any modifications or combination with non-original
parts could cause damage to the equipment and/or bodily injury.
The use of skilled personnel is a prerequisite for operating the controls. Please contact the
manufacturer if you find that you are missing any information or instructions in these
operating instructions.
In the case of failure to comply with these operating instructions the manufacturer assumes no
responsibility for the control system.
Telefon +49 (0)2587 89 - 0
Telefax +49 (0)2587 89 - 140
http://www.condor-cpc.com
Condor Pressure Control GmbH
Warendorfer Straße 47-51
D-59320 Ennigerloh

Operating Instructions (GB)
900 191 - V1.0
_________________________________________________________________________________
Page 1
CONTENT
Page
1. General notes 3
2. Safety instructions 3
2.1
Identifying instructions in the operating instructions 3
2.2
Personnel qualifications 3
2.3
Risks in case of non-observance of these safety warnings 3
2.4
Safety awareness at work 4
2.5
Safety warnings for the operating company / operator 4
2.6
Safety warnings for installation and maintenance work 4
2.7
Unauthorised modification and production of spare parts 5
2.8
Impermissible operating modes 5
3. Transport and in-transit storage 5
3.1
Transport 5
3.2
In-transit storage 5
4. General description of the control system 5
5. Installation / assembly 6
5.1
Surrounding conditions 6
5.2
Control system assembly notes 6
5.3
Immersion probe assembly notes 6
6. Electrical connection of base circuit board 7
6.1
Connection diagram of the front base circuit board (GLP) 7
6.2
Back of base circuit board (GLP) 8
6.3
Wiring colours 10
6.4
External shutdown / remote shutdown / dry run protection 10
6.5
External alarm 10
7. Operation and displays of the control board (CPU) 11
7.1
Overview of back of control board 11
7.2
Overview of front of control board 12
7.3
Operation 13
7.4
Main display – Symbols 14
7.5
Main menu – Symbols 16
7.6
Display release and password 17
7.7
Selection and function keys 18
7.8
Pump-out symbols and their meaning 19
7.9
Pump-out operating mode 19
7.10
Infeed symbols and their meaning 20
7.11
Infeed mode 20
8. Functional description 21
8.1
Infeed 21
8.2
Pump-out 22
8.3
Level settings 23
8.4
Fault messages and alarms 23

Operating Instructions (GB)
900 191 - V1.0
_________________________________________________________________________________
Page 2
9. Fuse protection and optional accessories 24
9.1
Power unit 24
9.2
Fuse protection provided by customer 24
9.3
24 VAC transformer 24
9.4
Circuit breaker, emergency off 24
9.5
Residual current circuit breaker (RCCB) 24
9.6
Overvoltage protection 24
9.7
Battery module* 24
10. Main display 25
10.1
Main display overview 25
10.2
Pump-out 29
10.2.1 Pump-out function operating data 29
10.2.2 General pump-out settings 30
10.3
Infeed 31
10.3.1 Infeed function operating data 31
10.3.2 General infeed settings 32
10.4
Level monitoring – 4…20mA 33
10.5 Error messages 34
10.6 Maintenance 35
11. Main menu 36
11.1
Main menu overview 36
11.2
Setup submenu 37
11.3
Maintenance submenu 40
11.4
Alarms submenu 41
11.5
USB submenu 43
12. Functional description winter operation 44
12.1 Manual control 45
12.1 Automatic control 45
13. Commissioning / recommissioning 46
14. Decommissioning 46
15. Servicing 46
16. Technical data 47
17. List of faults and declaration 48
18. Declaration of conformity 49
19. Notes 50

Operating Instructions (GB)
900 191 - V1.0
_________________________________________________________________________________
Page 3
1. General notes
The control system has been developed according to the state of the art, was manufactured
with the greatest of care and is subject to continuous quality controls.
The purpose of these operating instructions is to make it easier to get to know the device and
to make full use of its intended applications.
These operating instructions contain important information for a safe, proper and economical
operation of the devices. You must follow these operating instructions to ensure a reliable,
long service life for the devices and to avoid hazards.
The operating instructions do not take into account any location provisions, which are the
responsibility of the operating company, as well as the installation personnel.
The devices must not be operated above the values stated in the technical documentation
regarding operating voltage, nominal frequency of the network, ambient temperatures,
switching performance and other instructions contained in the operating instructions.
Should there be additional information or instructions required, or in the event of a claim,
please contact the manufacturer.
2. Safety instructions
This documentation refers exclusively to the control system and contains basic instructions
that must be observed during the installation, operation and maintenance thereof. Therefore it
is essential that these operating instructions are read by the technician and other responsible
specialist personnel/operators before installation and commissioning; it must be available at
the system's operating site at all times.
You must not only observe the general safety warnings given in the main "Safety" section, but
also the special safety warnings included under the following main points.
2.1 Identifying instructions in the operating instructions
The safety information given in these operating instructions, which can cause danger to
persons upon failure to observe, are specially marked with the following symbols.
Warning of common hazards Warning of high voltage
2.2 Personnel qualifications
The operation, maintenance, inspection and installation personnel must have the appropriate
qualifications for their specific work. The scope of responsibility, competence and supervision
of the personnel must be defined in detail by the operating company. Should the staff not have
the proper knowledge, additional training and instructions must be scheduled. Furthermore,
the operating company carries the responsibility that the content of these operating
instructions is fully understood by the staff.
2.3 Risks in case of non-observance of these safety warnings
Non-observance of the safety warnings may lead to hazards for personnel, as well as for the
system itself. Non-observance of safety warnings will result in loss of any rights to claim
damages.
In particular, non-observance may lead to incidents such as the following:
- Failure of key functions of the device
- Failure of prescribed methods for monitoring
- Danger to personnel by electrical forces

Operating Instructions (GB)
900 191 - V1.0
_________________________________________________________________________________
Page 4
2.4 Safety awareness at work
The safety warnings listed in these operating instructions, the existing national regulations for
the prevention of accidents, and also any additional internal work, operating and safety
instructions by the operating company must be observed.
It is essential to switch off all power before opening the device!
2.5 Safety warnings for the operating company / operator
Any electrical energy hazards are to be prevented (for details, please refer to the country-
specific regulations and the regulations of your local energy companies). The operating
company is to make sure that the control system is secured against access by unauthorised
personnel.
2.6 Safety warnings for installation and maintenance work
The operating company has to ensure that all maintenance, inspection and assembly work is
performed by trained and qualified personnel which was adequately informed through
intensive study of these operating instructions.
As a rule, work on the device may only be performed in a de-energised state. Immediately
after completion of this work the safety and protective system must be attached again or their
function restored. Before a restart, the points listed in the commissioning section must be
observed.
The currently applicable regulations (EN, VDE, …) as well as all regulation of the local energy
suppliers must be observed. Commissioning may only be completed once these have been
met.
For the following tasks, it is essential to follow the documentation of all
accessory parts.
Before the system is put into service and the mains voltage is switched on, the following must
be ensured.
•The controls and connection cables must not show any noticeable defects.
•All connection bolts and terminals must be checked for tightness before commissioning
and re-tightened to the prescribed torque if necessary.
•Routing and design of all cables and lines has to comply with the current regulations.
Particular attention must be paid to avoiding increased mechanical stresses on cable
entry plates, e.g. caused by insufficiently fixed or improperly strain-relieved cables.
•The mains connection and the connection of all accessory components, like the pump(s),
for instance, have to be implemented by professionals.
•On-site fuse protection has to be done in accordance with valid regulations and particular
circumstances.
•All miscellaneous connections are carried out correctly and professionally.
•The device is properly closed and unused cable glands are covered.
•The system is properly protected.

Operating Instructions (GB)
900 191 - V1.0
_________________________________________________________________________________
Page 5
2.7 Unauthorised modification and production of spare parts
Any modifications or changes to the control system are permitted only after consultation with
the manufacturer. Original spare parts are provided for safety reasons. The use of other parts
can make void the liability for the consequences arising from this.
2.8 Impermissible operating modes
The reliable operation of the control system can only be guaranteed if used as intended only.
The limit values given in the documentation must in no case be exceeded.
3. Transport and in-transit storage
3.1 Transport
Professional transport of the device is required. The control system was checked for
compliance with all specified data before shipment. The control system is therefore known to
be in good electrical and mechanical condition upon receipt. Please check the control system
for transport damage upon acceptance. In the event of a complaint, a damage report must be
drawn up together with the supplier.
3.2 In-transit storage
In-transit storage must be in a dry place, without jolting and, whenever possible, in the original
packaging. The ambient temperatures must not be outside the range of -20°C to +70°C.
4. General description of the control system
The control system automatically regulates the irrigation and de-watering of riding surfaces
with a specific substrate (draining system).
The optimal water level is manually adjusted and then automatically regulated by means of a
measuring signal from a hydrostatic measuring probe.
This ensures consistent humidity over the entire riding surface.
The unit is operated or configured via a TFT touch colour display.
These operating instructions describe the control functions in particular.
Further information is provided in the documents and drawings included with the control
system.
When parameters or menu settings are changed, it is possible that these
are not processed immediately by the control system. In such cases,
please reboot the control system.

Operating Instructions (GB)
900 191 - V1.0
_________________________________________________________________________________
Page 6
5. Installation / assembly
5.1 Surrounding conditions
•Dry and frost-proof
•Adequate ventilation
•The control system installation must be flood-proof
•The technical data, especially the maximum permissible ambient temperature, must
be observed.
•The control system must not be exposed to direct sunlight.
5.2 Control system assembly notes
The device is intended for wall mounting. Assembly may take place via the existing holes in
the housing or via the associated wall straps, if present. The installer is responsible for
selecting the appropriate material for attachment. Make all the necessary electrical
connections after assembly.
Attention!
You must be careful to not let any moisture into the control system during any kind of work on
the system. Ingress of moisture must be prevented during assembly and/or as long as the
electrical connections of the control system are exposed through an open door, even with only
light precipitation, e.g. by covering it with a tarpaulin. After completed installation and also in
case of longer breaks, close the cover.
The enclosure door must be firmly closed to be in compliance with the
respective protection rating! Unused fittings must be closed off with a
blind plug!
Should the electrical connection not be completed immediately after the mechanical
installation, possible ingress of moisture via open cable fittings must be prevented with
temporary bungs.
5.3 Immersion probe assembly notes
The function of the immersion probe is mostly independent of the installation position.
The protective cap may only be removed immediately before installation
in order to protect the process connection and the pressure diaphragm.
To prevent measurement errors and damage, the immersion probe should
be installed in a flow- and turbulence-free location, or in a guide tube!

Operating Instructions (GB)
900 191 - V1.0
_________________________________________________________________________________
Page 7
6. Electrical connection of base circuit board
The electrical hook-up to the control system depends on the equipment, the number of pump
connections and the desired functionalities. Please refer to the respective chapters or any
separately included wiring diagrams for special wiring specifications.
6.1 Connection diagram of the front base circuit board (GLP)
Designation Explanation
GLP (A2 / X2) Base circuit board
F1 / N Mains connection 2x 230V AC / 1A
F1 Control fuse 230 V / inertia 3.15 A
B11 – B12 Jumper bar Not used
B21 – B22 Jumper bar Not used
11 / 12 / 14 Alarm relay 1
Potential-free changeover contacts21 / 22 / 24 Alarm relay 2
31 / 32 / 34 Alarm relay 3
HW+ / HW- Separate high water float switch
ME1+ / ME1- Signal input 1 External shutdown / frost monitor mode
ME2+ / ME2- Signal input 2 External error
4…20mA Analogue input Connection for level probe 4 ... 20 mA
Stagnation pressure Plug-in base pressure module Not used
24V+ / 24V- 24V DC outgoing circuit max. 0.5 A Connection of a flashing signal / horn
DAC+ / DAC- Analogue output 4..20 mA Forwarding of the fill level signal
Fig. Terminals X2
Fig. Terminals X2

Operating Instructions (GB)
900 191 - V1.0
_________________________________________________________________________________
Page 8
6.2
Back of base circuit board (GLP)
In case of defect, it may be necessary to replace the base circuit board.
This requires function-critical components to be dismantled. Improper handling can
cause damage, which is not covered by the warranty. The board should be
replaced by the manufacturer if possible.
Only trained personnel is allowed to undertake the installation.
Section 1 shows the internal fuse F2 of the control electronics 1AT.
Fig. Back of base circuit board Fig. Image section 2
Description of image section 2
Item Designation Explanation
1
RJ 12 socket Connection for control board (CPU) cable
RJ 12 socket Reserve
2
DIP switch 1 Base circuit board 1 (GLP1) ON
DIP switch 2 Reserve OFF
DIP switch 3 Reserve OFF
DIP switch 4 Set terminal resistance ON
3
+24V Voltage output + 24 VDC 50 mA
GND Reference point for voltage outputs + 24 VDC / + 5 VDC
+5V Voltage output + 5 VDC (do not use)
4 10-pin box header Connection for battery module cable

Operating Instructions (GB)
900 191 - V1.0
_________________________________________________________________________________
Page 9
Fig. Image section 3
Description of image section 3
Item
Designation Explanation Description
1
L1 Not used Reserve
L2 Not used Reserve
L3 Not used Reserve
MS1 Signal input 1 Infeed fuse faulty
FI1 Signal input 2 Residual current circuit breaker 1
REF1 Reference point Signal inputs 1 & 2
S11 Continuous voltage output (230 V) Pump-out
S12 Output switched (230 V) Pump-out
LS Control voltage input (230 V)
GLP supply voltageNS Neutral conductor
NS Neutral conductor
2
MS2 Signal input 3 Pump-out fuse faulty
FI2 Signal input 4 Overvoltage protection triggered
REF2 Reference point Signal inputs 3 & 4
S21 Continuous voltage output (230 V) Infeed
S22 Output switched (230 V) Infeed

Operating Instructions (GB)
900 191 - V1.0
_________________________________________________________________________________
Page 10
6.3 Wiring colours
Colour
Application
black L1, L2, L3
light blue N and PEN
green/yellow PE
red Control voltage >50 V AC
Dark blue Control voltage <50 V DC
orange External voltage
white Measuring and control voltage / analogue signals
brown Control voltage <50 V AC
light blue with
explosion protection
Intrinsically safe circuit
6.4 External shutdown / remote shutdown / dry run protection
The control system can be caused to carry out a stop function via an external operating point.
The contacts (ME1+ / ME1-) must be closed via a potential-free contact for this.
All infeed and pump-out functions are disabled for the time during which the contacts are
closed.
Please note the further descriptions in Chapters 6.1, 11.2 and 12.0.
Attention! Terminal voltage 24 VDC.
6.5 External alarm
If the contact (ME2 + / ME2-) is closed via a potential-free contact, the error message
“External alarm” appears on the control system and is shown on the display.
Further functions of the control systems are not influenced by the error message.
If necessary, the message can be forwarded via an alarm relay available in the control
system. If a GSM modem is installed in the control system, forwarding via text message or e-
mail is also possible.
Attention! Terminal voltage 24 VDC.

Operating Instructions (GB)
900 191 - V1.0
_________________________________________________________________________________
Page 11
7.
Operation and displays
of the control board (CPU)
7.1 Overview of back of control board
1)
GSM modem Slot for an optional retrofittable GSM modem Chapter
11.2
2)
RJ12 socket For connection of signal line to base circuit
board
Chapter
6.2
3)
Internal alarm buzzer If a fault occurs an alarm tone will sound Chapter
11.4
4)
USB host connection For data exchange and software update via
USB stick
Chapter
11.6
5)
Network module Not used
6)
Lithium battery 3 V, type CR2032 Power reserve for clock and date
We recommend replacing the battery every five years. According to the Battery Act (BattG), waste batteries and
old batteries are to be returned to the retailer or to collection points.
RJ12 socket
2)
Internal buzzer
3)
USB host connection
4)
Lithium battery
6)
CR 2032 3V
Network module
5)
GSM modem
1)

Operating Instructions (GB)
900 191 - V1.0
_________________________________________________________________________________
Page 12
7.2 Overview of front of control board
Fig. Touch TFT display with LED fault (red)
Fig. Touch TFT display with LED ready (green)

Operating Instructions (GB)
900 191 - V1.0
_________________________________________________________________________________
Page 13
7.3 Operation
TFT display: Messages are rendered as symbols and plain text via the
colour display, in the selected language.
Operation: Using a stylus or finger, slight pressure is applied
to the display and the symbols. This is how individual functions
and settings are selected.
Main/load switch: This switch is used to turn the control system on/off.
See also Chapter 9.4.
Emergency switch – Water infeed: In case of failure of the control
electronics, the switch can be actuated to manually open (spring-return)
or switch off the valve for the water supply.
In normal operation, the automatic switch position should be
selected.
Mains voltage and a working backup fuse are required.
Emergency switch – Pumping out: In case of failure of the control
electronics, the switch can be actuated to manually switch the pump(s)
on or off.
In normal operation, the automatic switch position should be
selected!
Mains voltage and a working backup fuse are required.
After changing the parameters/menu settings, it is possible that
the control system initially fails to apply them. Reboot the control
system for the changes to take effect. This means that the supply
voltage and any installed battery module must be switched off
first. After restarting successfully, all parameters are overwritten
with the new data.
Operation as well as the user interface depends on the actual
equipment of the control system. Some functions are only
available after prior activation or with optional hardware.

Operating Instructions (GB)
900 191 - V1.0
_________________________________________________________________________________
Page 14
7.4 Main display – Symbols
A detailed explanation and settings are shown in Chapter 10.
1)
Optional accessories required.
The main display informs the operator of the
current status of the infeed, pump-out, fill level in
the pump shaft, pending faults and advanced
functions.
Click on the symbol to access additional functions
or information.
Some of the functions described here are only
available after prior activation or with the optional
hardware!
Main menu: Pressing this symbol will open the main menu, which
contains further submenus. All relevant settings are made here.
Battery charge level*: This symbol indicates the battery charge. A flash
is displayed over the symbol during charging. When the charge is
decreasing, the colour changes from green 100% > light green 75% >
orange 50% > red 25%. Click on the symbol for additional information.
Fault signals: If a fault occurs during operation of the control system, this
symbol is shown in the main display. Press this symbol to open the error
message menu.
Maintenance/service due: If a previously set maintenance date/service
is due, this symbol is shown and an interval tone sounds.
Click on the symbol for additional information.
GSM modem
1)
:If the control system is equipped with a GSM module,
this symbol is displayed after activation. Click on the symbol to open the
status display for further information.
Network module
1)
:

Operating Instructions (GB)
900 191 - V1.0
_________________________________________________________________________________
Page 15
Infeed symbol: The “Infeed” submenu opens when the symbol on the
display is pressed. One of the functions available here is manual mode.
Pump-out symbol: The “Pump-out” submenu opens when the symbol on
the display is pressed. One of the functions available here is manual
mode.
Fill level display: The fill level in the pump shaft is graphically displayed
as a bar graph here. The value next to the pump shaft shows the current
fill level and the set setpoint.
Press the shaft symbol to access the level monitoring submenu.
See Chapter 10.4 for more details
Current fill level in the pump shaft
Normal operation setpoint
Chapter 10.4
Summer mode setpoint
Chapter 12.0
Winter operation setpoint
Chapter 12.0
Adjusting the setpoint water level: The setpoint value for the water
level can be adjusted up or down using the two arrow keys next to the
level indicator.
The value can be limited via the min. and max. water level setting.
Changes in the target level are made after 15 sec. accepted and
saved.
The currently active setpoint value is shown in bold.
See Chapters 10.4 and 12.0 for more details
Summer/winter
operation
Normal operation
Alarm sound OFF: If this symbol is displayed, the alarm sound can be
switched off by pressing the symbol. Previously selected alarm relays are
also reset. Faults are not acknowledged.
Fault symbol: This fault symbol appears if a fault is present in the area of
the control or measuring system.

Operating Instructions (GB)
900 191 - V1.0
_________________________________________________________________________________
Page 16
7.5 Main menu – Symbols
A detailed explanation and settings are shown in Chapter 11.
Setup: Settings that are rarely changed are configured in the setup menu
during commissioning.
e.g.: language, time and various optional special functions.
Servicing: This menu is used to set maintenance dates based on
operating hours or by date. Also located here is the fault list, information
on operating hours or switching cycles.
Alarms: This menu is used to configure the alarm relays and their
functioning. It is also possible to change alarm sounds and fault settings.
GSM modem*: If the control system is supplemented with an optional
GSM module, all relevant settings for operating the modem can be made
here.
*Detailed explanations are provided in the separate operating instructions
for the GSM modem!
Network module:
Admin: Factory menu. No settings possible!
USB: This symbol appears if a USB stick is plugged into the USB host
port during operation of the control system.
Data can now be written to or read from the stick via this menu.
Back: Press this symbol to exit the menu and return to the main menu or
main display.

Operating Instructions (GB)
900 191 - V1.0
_________________________________________________________________________________
Page 17
7.6 Display release and password
Mains delay 9 sec.
Tap to cancel
Mains delay: After a restart or a mains failure, the control
system will only start up after the set time has elapsed.
The countdown can be cancelled by tapping this field.
Externally deactivated: The control system has been
deactivated by an external potential-free contact on the ME1
input. After opening the contact, the control system starts with
the countdown of the mains delay.
Faults are still detected and reported.
Observe the description in Chapter 6.4.
Alarm sound off
Alarm sound off: The internal alarm sound is turned off by
tapping on this field.
If the alarm relays are set to "reset with buzzer", any external
visual alarms and horns are also switched off.
The display is protected against unintended operation through an automatic key lock.
The next three sections describe the available options of the display release.
Enable operation
Enable operation: If no password has been entered for the
control system, the field shown is displayed after actuating
the display.
Operation is enabled by pressing on this field.
If no input is made for a certain amount of time, the key lock
is reactivated automatically.
Enter password
Enter password: If the control system is protected by a
password stored in the setup menu, the field shown is
displayed after actuating the display.
After tapping the symbol, the field for inputting the password
appears.
Operation is enabled after correct password entry.
The key lock is activated automatically.
Enable limited operation?
Enable limited operation: When pressing the symbol, only
limited operation is enabled. Functions such as clock/date,
language, set point water level, manual-0-automatic mode
and error messages can be changed or operated.
All other functions can be read, but they are protected by the
stored password.
Note
Externally deactivated

Operating Instructions (GB)
900 191 - V1.0
_________________________________________________________________________________
Page 18
"Password" input field: If the shown "Password" input field
is displayed, the four-digit code for unlocking the user
interface can be entered here and confirmed with OK.
Correct password!
Correct password: If the correct password has been
entered, this message appears and the control system is
enabled.
Wrong password!
Wrong password!: The message shown on the left is
displayed if the wrong password code is entered.
You can then retry with the correct password.
If the wrong code is entered again,
"Enable limited operation" is initiated.
7.7 Selection and function keys
1)
Optional accessories required, functional description in the operating instructions for the GSM modem.
Return to the previously selected menu or abort if an entry is made.
Switch off internal acoustic alarm.
Resolved fault messages can be reset.
Confirmation of changed parameters.
Scroll menu up / In the main menu “Adjust water level setpoint upwards”
Scroll menu down / In the main menu “Adjust water level setpoint downwards”
Delete entry
Additional information and settings
Activate modem test function
1)

Operating Instructions (GB)
900 191 - V1.0
_________________________________________________________________________________
Page 19
7.8 Pump-out symbols and their meaning
Pump-out symbol:
The symbol changes colour depending on the operating mode, thus indicating the
current status. The “Pump-out” submenu opens when the symbol is pressed.
Colour Operating mode Explanation
Ready Pump-out
Set point level reached. Waiting for request.
Grey
Fault
Pump-out faulty
Circuit breaker has tripped.
Check the relevant pump.
See Chapter 17.0.
Red
Off
Manual pump-out off
The function was manually switched off in the pump-out
menu.
Yellow
Automatic mode
Pump-out switched on
The level has exceeded the set level and the pump-out
function was automatically switched on.
Green
Manual mode
Pump-out manual mode switched on
The function was manually started in the pump-out menu.
Manual operation is limited to 1…120 seconds. The
function is then stopped and switched to automatic mode.
See Chapter 10.2.
Green
Winter operation
Pump-out switched off
The pump shaft is emptied to the set level and the infeed
function is switched off.
See Chapter 12.0.
Blue
7.9
Pump-out operating mode
The submenu shown on the left opens when the symbol is
actuated in the main display.
The operating mode for pumping out can now be changed here.
After actuation and if there are any faults on the pump, the keys
change their colour, among other things.
Manual pump-out off see also Chapter 7.8
Manual pump-out on see also Chapter 7.8
Automatic pump-out mode see also Chapter 7.8
Pump-out fault see also Chapter 17.0
Pump-out menu see also Chapter 10.2
Winter operation see also Chapter 12.0
Pump-out
Table of contents
Popular Control System manuals by other brands

LED-supplies
LED-supplies WiFi-104 manual

Meccanica SCOTTI
Meccanica SCOTTI CNC Table Programming manual
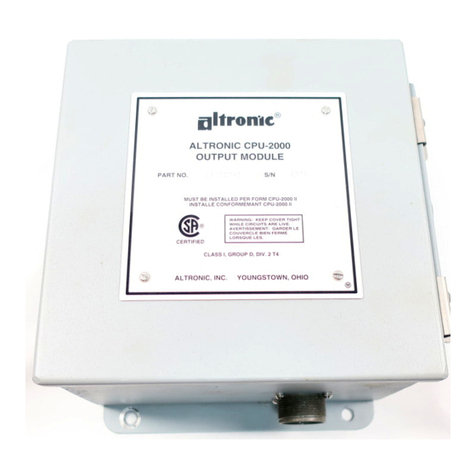
Altronic
Altronic CPU-2000 Service instruction
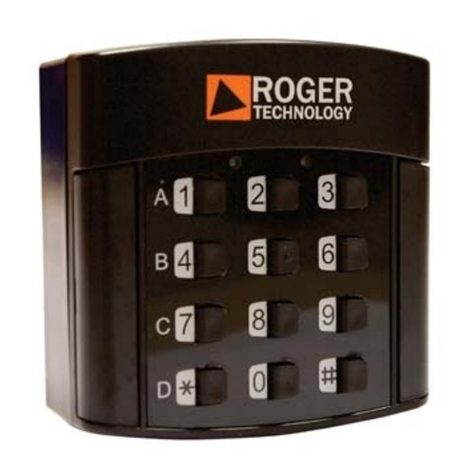
Roger
Roger H85/TDR Instruction and warnings for the installer

Elnur
Elnur G Control Hub Installation instructions and user guide
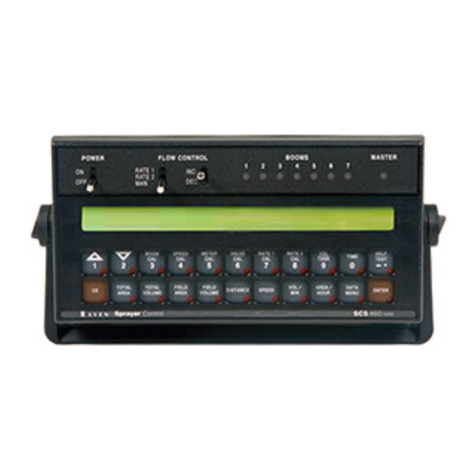
Raven
Raven SCS 460 Installation and service manual