CONTINENTAL AIRCRAFT ENGINE C75 Series User manual

Publication M-0 CHANGE 2
©2016 CONTINENTAL MOTORS SEP 2016
CONTINENTAL AIRCRAFT ENGINE
MAINTENANCE
MANUAL
STANDARD PRACTICE
FOR SPARK IGNITED ENGINES
Technical Portions Accepted by the Federal Aviation Administration

A Standard Practice Maintenance Manual
CHANGE 2 30 Sep 2016
Supersedure Notice
This manual incorporates maintenance and service information contained in Continental Motors Service
Documents common to the horizontally opposed, spark ignition, AvGas aircraft engines conforming to Type
Certificate held by Continental Motors. This document is supplemental to the Instructions for Continued
Airworthiness provided in the manuals listed in Section 1-1.1. Instructions contained in the Service Documents
listed in Section 1-2.4 are superseded by instructions in this manual upon release, except for those Mandatory
Service Bulletins (MSBs) and Critical Service Bulletins (CSBs).
Effective Changes for this Manual
0 ................15 April 2016
1 ................ 30 May 2016
2 .................30 Sep 2016
List of Effective Pages
Document Title: Standard Practice Maintenance Manual
Publication Number: M-0 Initial Publication Date: 15 April 2016
Page Change Page Change Page Change Page Change
Cover............................2 3-6 thru 3-8...................0 6-30.............................. 2 6-140............................ 1
A...................................2 3-9 ................................1 6-31 thru 6-66 .............. 0 6-141 thru 6-147........... 0
B...................................2 3-10 thru 3-24...............0 6-67.............................. 1 6-148............................ 2
C (blank).......................1 4-1 thru 4-2...................0 6-68 thru 6-95 .............. 0 6-149 thru 6-151........... 0
i thru ii........................... 0 5-1 thru 5-8...................0 6-96.............................. 1 6-152............................ 2
iii thru xviii.....................1 6-1 thru 6-2...................0 6-97 thru 6-98 .............. 0 6-153 thru 6-154........... 1
1-1 thru 1-10.................0 6-3 ................................2 6-99 thru 6-101 ............ 1 6-155............................0
1-11 thru 1-12...............2 6-4 thru 6-5...................0 6-102............................ 0 6-156............................ 1
1-13 thru 1-16...............0 6-6 ................................1 6-103............................ 1 6-157............................ 0
2-1 ................................ 0 6-7 ................................0 6-104 thru 6-115 .......... 0 6-158 thru 6-159........... 1
2-2 thru 2-4...................1 6-8 ................................1 6-116............................ 1 6-160 thru 6-171........... 0
2-5 thru 2-6...................0 6-9 thru 6-15.................0 6-117 thru 6-132 .......... 0 6-172............................ 1
2-7 thru 2-8...................1 6-16 thru 6-17...............2 6-133 thru 6-135 .......... 1 6-173 thru 6-174........... 0
2-9 thru 2-24.................0 6-18 thru 6-22...............0 6-136............................ 0 7-1 thru 7-2................... 0
3-1 thru 3-4...................0 6-23 ..............................2 6-137 thru 6-138 .......... 1 7-3................................ 1
3-5 ................................ 1 6-24 thru 6-29...............0 6-139............................ 0 7-4 thru 7-7................... 0
Published and printed in the U.S.A. by Continental Motors
Available exclusively from the publisher: P.O. Box 90, Mobile, AL 36601
Copyright © 2016 Continental Motors. All rights reserved. This material may not be reprinted, republished, broadcast, or otherwise altered
without the publisher's written permission. This manual is provided without express, statutory, or implied warranties. The publisher will not be
held liable for any damages caused by or alleged to be caused by use, misuse, abuse, or misinterpretation of the contents. Content is subject to
change without notice. Other products and companies mentioned herein may be trademarks of the respective owners.

Standard Practice Maintenance Manual B
30 Sep 2016 CHANGE 2
List of Effective Pages, cont.
Page Change Page Change Page Change Page Change
7-8 ................................1 A-1 thru A-6 ................. 0
7-9 ................................0 B-1 ............................... 1
7-10 ..............................1 B-2 thru B-7 ................. 0
7-11 thru 7-23 ...............0 B-8 ............................... 1
7-24 ..............................1 B-9 thru B-16 ............... 0
7-25 thru 7-30...............0 C-1 thru C-5 ................. 0
8-1 thru 8-15.................0 C-6 thru C-9 ................. 1
8-16 ..............................2 C-10 thru C-18............. 0
8-17 thru 8-26...............0 C-19 ............................. 1
9-1 ................................1 C-20 thru C-26............. 0
9-2 thru 9-6...................0
10-1 thru 10-2...............0
10-3 ..............................1
10-4 thru 10-8...............0
10-9 thru 10-10.............2
10-11.............................1
10-12 ............................2
10-13 ............................2
10-14 ............................2
10-15 ............................1
10-16 thru 10-18...........2
10-19 thru 10-21...........0
10-22 ............................1
10-23 thru 10-24...........0
10-25 ............................1
10-26 thru 10-37...........0
10-38 thru 10-40...........1
10-41 thru 10-103.........0
10-104 ..........................1
10-105 ..........................0
10-106 ..........................1
10-107 thru 10-108.......0
11-1 thru 11-8 ...............0
12-1 ..............................1
12-2 thru 12-12.............0

C Standard Practice Maintenance Manual
CHANGE 1 30 May 2016
Intentionally Left Blank

Standard Practice Maintenance Manual 1-11
30 Sep 2016 CHANGE 2
Introduction
1-2.4.1. Service Documents Incorporated in this Manual
Applicable technical maintenance and service information contained in the Service
Documents listed below, relevant to the engine models covered by this engine manual,
have been incorporated in this M-0 Standard Practice Maintenance Manual. This manual
supersedes and retires these older Service Documents (where applicable) excluding
Mandatory Service Bulletins (MSBs) and Critical Service Bulletins (CSBs) identified
with an asterisk below.
The full content of active Continental Motors Service Documents is available at
www.continentalmotors.aero. Refer Section 1-3, “Contact Information” for Continental
Motors web site details.
Table 1-1. Service Documents Incorporated in Manual
Service Document Subject Affected Chapter
M67-12, Overboost of Turbocharged Engines Unscheduled Maintenance 6
M72-17R1, Maximum Weight Difference Between
Connecting Rods and Pistons in the Same Engine
Parts Replacement 10
M76-4, Propeller Shaft or Crankshaft Oil Seal
Replacement
Unscheduled Maintenance 10
M76-8, Intake Valve Change Unscheduled Maintenance 10
M77-3, Use of Alternate Fuels in Engines Originally
Certified for 80/87, 91/96 and 100/130 Grade Fuels
Engine Operation 7
M84-5, Gear Driven Alternator Inspection Procedure Alternator Replacement 10
M87-15, Alternator Ground Strap Alternator Replacement 10
M88-9, Lightning Strikes Unscheduled Maintenance 6
M88-10, Contaminated Fuels Unscheduled Maintenance 6
M89-7R1, Engine Operation after Cylinder
Replacement and/or Major Overhaul
Unscheduled Maintenance 7
M89-9, Excessive Crankcase Pressure Unscheduled Maintenance 8
M90-17, Crankcase Inspection Criteria Scheduled Maintenance 6
SIL93-11B, Service Document Format Service Documents 1
SIL93-15, General Practices for Installation of Lock
Wire, Tab Washers, and Cotter Pins
Standard Practices Appendix C
* MSB94-8D, Magneto to Engine Timing Scheduled Maintenance 6
SB95-2, Inspection and Maintenance of Engine Control
Cables and Linkage
Inspection 6
SB95-3B, Alternator/Generator Drive Coupling Alternator Maintenance 6, 10
SIL95-5, Hose and Tubing Installation Hose and Tubing installation Appendix C
SB96-7D, Torque Limits Fastener Torque Appendix B
* MSB96-10B, Crankshaft Ultrasonic Inspection Engine Overhaul or Crankshaft
Repair
10
SB96-11B, Propeller Strikes and Hydraulic Lock Unscheduled Inspection 6

1-12 Standard Practice Maintenance Manual
CHANGE 2 30 Sep 2016
Introduction
* Documents remain active in the service bulletin set.
SB96-12, Cylinder Continued Airworthiness Scheduled Inspection 6 & 10
SID97-2B, Design, Operation Maintenance and
Warranty of Cylinders
Engine Maintenance 6
SID97-3G, Continuous Flow Fuel Injection Systems
Adjustment Specifications and Instructions
Operational Checks and
Adjustments
6
SID97-4F, Cylinder Bore and Piston Fit Specifications Overhaul & Service Limits 10
SB97-6B, Mandatory Replacement Parts Engine Inspection & Assembly Appendix C
SIL98-9E, Time Between Overhaul Periods Scheduled Maintenance 6
SIL99-1, Engine Preservation for Active and Stored
Aircraft
Engine Preservation and Recovery 9
SIL99-2C, Sealants, Lubricants and Adhesives
Authorized by CMI
Materials 3
SB00-3A, Crankshaft, Counterweight and Connecting
Rod Repair Information
Repair Specifications 10
SIL00-9A, Engine Data Plates Data Plate Replacement Appendix C
SIL00-11B, Release of new Cylinder Induction Port
Drain Connector
Cylinder Assembly 10
SIL03-1, Cold Weather Operation - Engine Preheating Engine Operation 7
SIL03-2C, Currently Active Approved Spark Plug
Application
Spark Plugs 6
SB03-3, Differential Pressure Test and Borescope
Inspection
Inspection Criteria 6
SIL04-12A, Authorized Engine Adjustments,
Component Replacement and Repositioning
Engine Specification 5
SB05-2, Overspeed Limitations Unscheduled Maintenance 6
* CSB08-3C, Throttle & Mixture Control Levers Fuel Injection System Assembly 6
SB08-13, Induction System Hose and Clamp
Installation
Induction System Inspection &
Assembly
6
SB11-3, Alternator and Drive Coupling Installation Alternator Replacement 6, 10
SIL13-2A, Alternator Instructions for Continued
Airworthiness
Alternator Replacement 6, 10
SB14-8, Exhaust Flange to Cylinder Installation Exhaust System Installation 10
Table 1-1. Service Documents Incorporated in Manual
Service Document Subject Affected Chapter

Standard Practice Maintenance Manual 6-3
30 Sep 2016 CHANGE 2
Engine Inspection and Service
•Overhauled or repaired in a manner that is inconsistent with the specifications,
limits, and instructions provided in the CM Instructions for Continued
Airworthiness and FAA Airworthiness Directives
6. The “Hobbs Meter” is commonly used by the aviation industry as an acceptable
device to record time elapsed while electrical power is applied to the device. The
conditions under which the Hobbs Meter records operation vary widely within the
aviation industry. Continental Motors does not specify a method to record engine
operating hours, rather, Continental Motors defers to the end application installer.
NOTE: TBO periods specified in this document are only estimates and do
not reflect warranty periods. For engine warranty coverage, refer to the
original Aircraft Engine Warranty received with the engine.
Table 6-1. Engine Time Between Overhaul (TBO)
ENGINE MODEL SEE NOTE
HOURS/YEARS
ENGINE
S/N BEFORE
1006000
ENGINE
S/N 1006000
AND LATER
A65, A75 and C75, C85, C90 Series 11800/12
O-200-A, B 1, 2 1800/12 2000/12
O-200-D 1
2000/12 2200/12
IO-240-A, B 1, 2
IOF-240-B 1, 2
IO-346-A 11500/12
C125, C145 Series and O-300-A, B, C, D 11800/12
GO-300-A, C, D, E 11200/12
IO-360-A, AB, B, C, D, G, H, J, K 11500/12
IO-360-CB, DB, GB, HB, JB 1, 2 1500/12 1700/12
IO-360-AF, ES, KB 1, 2 2000/12 2200/12
TSIO-360-A, AB, B, C, D, E, F, H 1
1400/12
LTSIO-360-E 1
TSIO-360-CB, DB, HB, JB 1, 2 1400/12 1600/12
L/TSIO-360-EB, FB, GB, KB, LB, MB, RB, SB 1, 2 1800/12 2000/12
E165, E185, E225 Series 1
1500/12
O-470-A, B, E, G, N, P 1
O-470-J, K, L, M, R, S 1, 2 1500/12 1700/12
O-470-U 1, 2, 3 2000/12 2200/12
IO-470-C, D, E, F, G, H, J, K, L, M, N, P, R, S, U, V, VO 1, 2 1500/12 1700/12
TSIO-470-B, C, D 11400/12
IO-520-B, BA, C, M 11700/12
IO-520-A, BB, CB, D, E, F, J, K, L, MB 1, 2 1700/12 1900/12
L/IO-520-P 1, 2 2000/12 2200/12

6-4 Standard Practice Maintenance Manual
15 April 2016
Engine Inspection and Service
GTSIO-520-F, K 11200/12
GTSIO-520-C, D, H 1, 4
1600/12
GTSIO-520-L, M, N 1
TSIO-520-B, D, E, J, K, L, N 11400/12
TSIO-520-BB, C, DB, EB, G, H, JB, KB, LB, M, P, R, T 1, 2 1400/12 1600/12
TSIO-520-NB 1, 2,
1600/12 1800/12
TSIO-520-M, P, R 1, 2, 5
TSIO-520-AF, CE, UB, VB, WB 1, 2
L/TSIO-520-AE 1, 2
2000/12 2200/12
TSIO-520-BE 1, 2
IO-550-A, B, C, D, E, F, L 1, 2 1700/12 1900/12
IO-550-G, N, P, R 1, 2
2000/12 2200/12
IOF-550-N 1, 2
TSIO-550-B, E 1, 2 1600/12 1800/12
TSIO-550-C, G, K, N 1, 2
2000/12 2200/12
TSIOF-550-D, J, K, P 1, 2
TSIOL-550-A, B, C 1 2000/12
1. If an engine consistently accumulates 40 or more hours per month since being placed in service, add 200 hours to recom-
mended TBO.
2. Engines with Serial Number 1006000 or higher include an additional 200 hours to TBO (as noted in Table 1, column 3).
3. Applies to: new and rebuilt O-470U Model Specifications 11, 12, 13, 14, 17, 18, and subsequent numbers manufactured, new
or rebuilt, or overhauled (2002 or later).
4. Applies to GTSIO-520-C, D, H engine models listed utilizing cylinder part number 653453, or superseding (cylinder produc-
tion released APRIL 1993-verify part number on cylinder flange). Also, all parts must be replaced as directed by the applica-
ble current service bulletins, illustrated parts catalogs, and overhaul manuals. A log book entry is required.
5. Applies to new and rebuilt TSIO-520-M Spec. 6, 7, and 8; TSIO-520-P Spec. 5 and 6; TSIO-520-R Spec. 7, 9, 10, and 11, or
new and rebuilt TSIO-520-M, P, and R model engines with subsequent specification numbers.
Table 6-1. Engine Time Between Overhaul (TBO)
ENGINE MODEL SEE NOTE
HOURS/YEARS
ENGINE
S/N BEFORE
1006000
ENGINE
S/N 1006000
AND LATER

Standard Practice Maintenance Manual 6-15
15 April 2016
Engine Inspection and Service
6-4.7.1. Fuel Injection System Specifications
NOTE: Engines may not reach rated full power RPM during ground run-
up due to atmospheric, environmental, or configuration limitations. This
condition is normal, occurring most often when operating naturally
aspirated engines configured with a fixed pitch propeller. A correction
factor must be applied to reduce the fuel pressure to the lower maximum
RPM observed during fuel system adjustments on the ground. See
Section 6-4.7.1.1 for RPM correction factors.
Table 6-4. Fuel System Adjustment Values
Idle and FULL POWER Fuel Pressures and Flows
Engine1Prop.
RPM
Manifold
Absolute
Pressure
(MAP)
Unmetered
Pump PSI2
Metered
Nozzle
PSI3
Fuel
(lbs/hr)4
Fuel
(gal/hr)4
IO-240-A, B 1000
Table 6-6
29.5
Table 6-6
9.4- 9.8
Table 6-6
-
Table 6-6
-
65 - 70
-
11.0 - 11.9
IO-346-A, B 600
2700
- 7.0 - 7.5
19.0 - 21.0
-
12.5 - 14.0
-
78 - 85
-
13.3 - 14.5
IO-360-A, AB, C, CB, D5, DB5, G, GB, H, HB 600
2800
- 7.0 - 9.0
24.0 - 27.0
-
15.8 -18.2 100 - 106 17.0 - 18.1
IO-360-AF 600
2800
- 7.0 - 9.0
23.0 - 26.0 14.3 - 16.5
-
100 - 107
-
17.0 - 18.1
IO-360-ES 6600
2800
- 7.0 - 9.0
23.0 - 26.0 14.3 - 16.5
-
100 - 107
-
17.0 - 18.1
IO-360-ES (Cirrus - Sea Level) 6, 7 600
2700
- 7.0 - 9.0
21.0 - 24.0 13.8 - 15.5
-
96 - 102
-
16.4 - 17.4
IO-360-ES (Cirrus - 1500 ft press. alt.) 6, 7 600
2700
- 7.0 - 9.0
19.0 - 22.0 13.3 - 14.6
-
94 - 98
-
16.0 - 16.7
IO-360-J, JB 600
2600 8
- 7.0 - 9.0
24.0 - 27.0
-
15.8 -18.2
-
100 - 106
-
17.0 - 18.1
IO-360-K, KB 600
2600
- 7.0 - 9.0
21.0 - 24.0 14.3 - 16.3
-
93.5 - 97.5
-
15.9 - 16.6
TSIO-360-A, AB 600
2800
-
32.0
6.5- 7.5
27.2 - 31.2
-
15.8 - 16.7
-
119 - 124
-
20.1 - 21.0
TSIO-360-B, BB 600
2800
-
32.0
6.5 - 7.5
27.2 - 31.2
-
15.8 - 16.7
-
115 - 124
-
20.1 - 21.0
TSIO-360-C, CB 600
2800
-
37.0
6.5 - 7.5
34.0 - 37.0
-
16.7 - 19.3
-
135 - 145
-
23.0 - 24.7
TSIO-360-D, DB 600
2800
-
36.0
6.5 - 7.5
34.0 - 37.0
-
16.7 - 19.3
-
135 - 145
-
23.0 - 24.7
TSIO-360-E, EB, LTSIO-360-E, EB 700
2575
-
40.0
6.25 - 6.75
43.0 - 46.0
-
15.8 - 18.3
-
130 - 140
-
22.1 - 23.8
TSIO-360-F, FB 700
2575
-
41.0
6.25 - 6.75
40.0 - 43.0
-
15.8 - 18.3
-
130 - 140
-
22.1 - 23.8
TSIO-360-G, GB 700
2700
-
40.0
6.25 - 6.75
45.0 - 49.0
-
16.7 - 19.3
-
135 - 145
-
23.0 - 24.7
TSIO-360-H, HB 600
2800
-
34.5
6.5 - 7.5
29.0 - 33.0
-
14.9 - 17.3
-
125 - 135
-
21.3 - 23.0

6-16 Standard Practice Maintenance Manual
CHANGE 2 30 Sep 2016
Engine Inspection and Service
TSIO-360-JB 600
2800
-
37.0
6.5 - 7.5
34.5 - 37.5
-
16.7 - 19.3
-
134 - 145
-
22.8 - 24.7
TSIO-360-KB, L/TSIO-360-KB 700
2800
-
40.0
6.5 - 7.5
36.0 - 39.0
-
17.7 - 21.2
-
140 - 155
-
23.8 - 26.4
TSIO-360-LB 700
2700
-
40.0
6.25 - 6.75
34.0 - 38.0
-
14.7 - 16.7
-
135 - 145
-
23.0 - 24.7
TSIO-360-MB 700
2700
-
36.0
6.25 - 6.75
28.0 - 32.0
-
13.6 - 15.3
-
125 - 135
-
21.3 - 23.0
L/TSIO-360-RB 700
2600
-
38.0
25 Minimum
35.0 - 45.0 MFG9
-
-
140 - 150
-
23.3 - 25.5
TSIO-360-SB 700
2600
-
39.0
6.25 - 6.75
31 - 36
-
15.1 - 17.8
-
131 - 151
-
22.3 - 25.7
O-470-GCI 600
2600
- 9.0 - 11.0
23.8 - 25.3
-
14.7 - 16.9
-
122 - 129
-
20.8 - 22.0
IO-470-C, G, P, R 600
2600
- 9.0 - 11.0
24.7 - 27.7
-
14.8 - 17.3
-
123 - 130
-
21.0 - 22.1
IO-470-D, E, F, H, L, M, N, S, U 600
2625
- 9.0 - 11.0
25.0 - 28.0
-
15.0 - 17.5
-
124 - 131
-
21.1 - 22.3
IO-470-J, K 600
2600
- 5.5 - 7.0
24.7 - 27.7
-
14.8 - 17.3
-
123 - 130
-
21.0 - 22.1
IO-470-V 600
2625
- 6.5 - 7.5
28.3 - 29.8
-
17.8 - 18.8
-
123.5 - 131
-
21.0 - 22.3
IO-470-VO 600
2625
- 6.5 - 7.5
28.8 - 31.0
-
17.8 - 18.8
-
132 - 137.5
-
22.5 - 23.4
GIO-470-A 450
2400
- 9.0 - 11.0
26.0 - 28.0
-
15.5 - 16.5
-
145 - 155
-
24.7 - 26.4
TSIO-470-B, C, D 600
2600
-
35.0
5.5 - 6.0
28.0 - 30.0
-
15.0 - 17.0
-
145 - 155
-
24.7 - 26.4
IO-520-A, J 600
2700
- 9.0 - 11.0
29.0 - 32.0
-
15.9 - 18.2
-
136 - 146
-
23.2 - 24.9
IO-520-B, BA, BB C, CB 600
2700
- 9.0 - 11.0
28.0 - 31.0
-
14.9 - 17.2
-
136 - 146
-
23.2 - 24.9
IO-520-D, F, K, L 600
2850
- 9.0 - 11.0
30.0 - 33.0
-
17.0 - 19.4
-
143 - 153
-
24.4 - 26.1
IO-520-E 600
2850
- 9.0 - 11.0
29.0 - 32.0
-
16.1 - 18.3
-
143 - 153
-
24.4 - 26.1
IO-520-M, MB 600
2700
- 6.0 - 7.0
29.0 - 32.0
-
16.7 - 19.3
-
136 - 146
-
23.2 - 24.9
IO-520-P, LIO-520-P 600
2500
- 6.0 - 7.0
26.2 - 26.9
-
14.3 - 16.2
-
130 - 140
-
22.1 - 23.9
TSIO-520-AE, LTSIO-520-AE 600
2400
-
32.5
7.5 - 8.5
34.5 - 38.0
-
15.2 - 16.5
-
160 - 165
-
27.3 - 28.1
TSIO-520-AF 600
2700
-
35.5
5.5 - 6.5
35.0 - 39.0
-
18.4 - 19.9
-
180 - 186
-
30.7 - 31.7
TSIO-520-B, BB 600
2700
-
32.0
5.5 - 7.0
29.0 - 32.0
-
16.0 - 17.9
-
165 - 175
-
28.1 - 29.8
Table 6-4. Fuel System Adjustment Values
Idle and FULL POWER Fuel Pressures and Flows
Engine1Prop.
RPM
Manifold
Absolute
Pressure
(MAP)
Unmetered
Pump PSI2
Metered
Nozzle
PSI3
Fuel
(lbs/hr)4
Fuel
(gal/hr)4

Standard Practice Maintenance Manual 6-17
30 Sep 2016 CHANGE 2
Engine Inspection and Service
TSIO-520-BE 600
2600
-
38.0
5.5 - 7.0
25.0 - 28.0
-
12.7 - 14.1
-
214 - 224
-
36.5 - 38.2
TSIO-520-C, H 600
2700
-
32.5
5.5 - 7.0
29.0 - 32.0
-
15.3 - 17.2
-
160 - 170
-
27.3 - 29.0
TSIO-520-CE 600
2700
-
37.0
5.5 - 6.5
33.0 - 36.0
-
16.2 - 18.0
-
215 - 225
-
36.6 - 38.3
TSIO-520-D, DB 600
2700
-
32.5
5.5 - 7.0
29.0 - 32.0
-
13.3 - 15.1
-
160 - 170
-
27.3 - 29.0
TSIO-520-E, EB 600
2700
-
34.5
5.5 - 6.5
31.0 - 34.0
-
15.6 - 17.7
-
175 - 185
-
29.8 - 31.5
TSIO-520-G 600
2700
-
35.0
5.5 - 6.5
31.0 - 34.0
-
15.8 - 17.6
-
181 - 191
-
30.8 - 32.5
TSIO-520-J, JB 600
2700
-
36.0
5.5 - 6.5
31.0 - 34.0
-
16.9 - 18.7
-
170 - 178
-
29.0 - 30.3
TSIO-520-K, KB 600
2700
-
33.0
5.5 - 7.0
29.0 - 32.0
-
15.1 - 17.4
-
163 - 175
-
27.8 - 29.8
TSIO-520-L, LB 600
2700
-
38.0
25 Minimum
45.0 - 55.0 MFG10 -
180 - 190
-
30.7 - 32.4
TSIO-520-M, R 600
2700
-
36.5
5.5 - 6.5
33.0 - 37.0
-
16.9 - 19.9
-
170 - 186
-
29.0 - 31.7
TSIO-520-N, NB 600
2700
-
38.0
5.5 - 6.5
32.0 - 35.0
-
16.9 - 19.9
-
170 - 186
-
28.9 - 31.7
TSIO-520-P 600
2700
-
36.5
5.5 - 6.5
33.0 - 37.0
-
18.4 - 19.9
-
180 - 186
-
30.7 - 31.7
TSIO-520-T 600
2700
-
39.5
5.5 - 6.5
33.0 - 37.0
-
16.3 - 18.1
-
185 - 195
-
31.5 - 33.2
TSIO-520-UB 600
2700
-
36.0
5.5 - 6.5
33.0 - 37.0
-
14.4 - 16.0
-
195 - 205
-
33.2 - 34.9
TSIO-520-VB 600
2700
-
40.5
5.6 - 6.5
36.0 - 39.5
-
16.9 - 18.7
-
200 - 210
-
34.1- 35.8
TSIO-520-WB 600
2700
-
39.5
25 Minimum
45.0 - 55.0
-
MFG11
-
190 - 200
-
32.4 - 34.1
GTSIO-520-C 525
2400
-
34.5
4.0 - 7.0
30.0 - 33.0
-
16.5 - 17.5
-
215 - 225
-
36.6 - 38.3
GTSIO-520-D, H 467
2267
-
39.5
4.0 - 7.0
30.5 - 35.0
-
15.7 - 17.3
-
250 - 260
-
42.6 - 44.3
GTSIO-520-F, K11 600
2267
-
44.5
6.75 - 7.25
38.0 - 41.0
-
17.4 - 18.8
-
300 - 310
-
51.1 - 52.8
GTSIO-520-L, N11
GTSIO-520-M
467
2234
39.0
40.0
4.0 - 7.0
29.5 - 35.0
-
16.4 - 17.9
-
255 - 265
-
43.4 - 45.1
GIO-550-A 600
2267
- 25 Minimum
45 - 55
-
MFG11
-
175 - 185
-
29.8 - 31.5
IO-550-A 6600
2700
-
-
8.0 -10.0
32.0 - 36.0
-
17.7 -20.0
-
142 - 150
-
24.2 - 25.6
IO-550-B 6600
2700
-
-
8.0 -10.0
29.2 - 36.2
-
16.5 - 18.4
-
146 - 156
-
24.9 - 26.6
Table 6-4. Fuel System Adjustment Values
Idle and FULL POWER Fuel Pressures and Flows
Engine1Prop.
RPM
Manifold
Absolute
Pressure
(MAP)
Unmetered
Pump PSI2
Metered
Nozzle
PSI3
Fuel
(lbs/hr)4
Fuel
(gal/hr)4

6-18 Standard Practice Maintenance Manual
15 April 2016
Engine Inspection and Service
IO-550-C 6600
2700
-
-
8.0 -10.0
31.6 - 37.8
-
17.6 - 19.6
-
152 - 160
-
25.9 - 27.3
IO-550-D, E, F, L 6600
2700
- 8.0 - 10.0
32.0 - 36.0
-
17.2 - 20.0
-
143 - 155
-
24.4 - 26.4
IO-550-G 600
2500
-
-
8.0 -10.0
22.0 - 26.0
-
14.7 - 16.0
-
125 - 130
-
21.3 - 22.1
IO-550-N, P, R 600
2700
-
-
8.0 -10.0
28.0 - 30.0
-
19.0 - 21.3
-
150 - 160
-
25.6 - 27.3
TSIO-550-B 600
2700
-
38.0
7.0 - 9.0
32.0 - 36.0
-
15.3 - 16.9
-
241 - 252
-
41.0 - 42.9
TSIO-550-C 600
2700
-
35.5
7.0 - 9.0
32.0 - 36.0
-
15.3 - 16.9
-
212 - 222
-
36.1 - 37.8
TSIO-550- E 600
2700
-
38.5
7.0 - 9.0
32.0 - 36.0
-
15.3 - 16.9
-
244 - 254
-
41.5 - 43.3
TSIO-550- G 600
2700
-
34.0
7.0 - 9.0
20.5 - 28.5
-
12.4 - 13.6
-
201 - 211
-
35.2 - 35.9
TSIO-550-G
MOONEY 12
600
2500
-
33.5
7.0-9.0
20.0-23.0
-
10.4-11.6
-
177-180
-
30.0-30.7
TSIO-550- K, N 600
2500
-
37.5
7.0 - 9.0
20.5 - 28.5
-
14.2 - 14.8
-
210 - 220
-
35.8 - 37.5
TSIOL-550-A 600
2600
-
35.0
5.5 - 6.5
32.5 - 35.5
-
17.0 - 19.0
-
170 - 180
-
29.0 - 30.7
TSIOL-550-B 600
2700
-
35.0
6.0 - 8.0
36.0 - 40.0
-
20.0 - 22.5
-
175 - 185
-
29.8 - 31.5
TSIOL-550-C 600
2600
-
39.5
6.0 - 8.0
37.0 - 40.0
-
15.0 – 16.5
-
204 - 216
-
34.8 – 36.8
1. The setup procedures contained in this bulletin are only for use on engines that have not been modified from their original configuration as
shipped from the factory by Continental Motors. Engines which have been modified by the installation of aftermarket components such as
turbo-normalizing systems, turbocharging systems, intercoolers, after-coolers, fuel nozzles, etc., whether by STC or field approval, must
use the instructions provided by the STC holder or installer. CM will not accept responsibility or liability for any modified engine set up
according to the instructions contained in these instructions.
2. FULL POWER unmetered fuel pump pressure limits are provided for reference only. Use metered fuel pressure specifications for adjust-
ments at full power.
3. Use for full power, maximum RPM adjustment only. All other parameters for reference only, Footnote 2 applies.
4. May be determined using a calibrated in-line flow measuring device. Otherwise use metered fuel pressure specifications. Refer to Aircraft
Manufacturer's Maintenance Manual for method of verifying accuracy of fuel flow indicator.
5. IO-360DB engine model specifications equipped with altitude compensating fuel pumps; Flight Test (Section 7-2.4.2) required after fuel
system adjustment.
6. Engine model equipped with altitude compensating fuel pump; Flight Test (Section 7-2.4.2) required after fuel system adjustment.
7. This engine installed in Cirrus SR20 aircraft. IO-360-ES engines has been derated by Cirrus from original 210 HP at 2800 RPM to 200 HP at
2700 RPM. Engine data plate reflects original CM data of 210 HP at 2800 RPM. Refer to Cirrus SR20 Maintenance Manual and POH.
8. Engine model certified for five minute rated takeoff power at 2800 RPM. Max. continuous power is 2600 rpm
9. Refer to the aircraft manufacturer's instructions for adjustment procedures.
10. Refer to the aircraft manufacturer's instructions for adjustment procedures.
11. Refer to the aircraft manufacturer's instructions for adjustment procedures.
12. TSIO-550-G installed in Mooney aircraft has been rated to a power level that is less than the approved Type Certificate Data Sheet. Refer to
the Mooney Aircraft Maintenance Manual for setup instructions.
Table 6-4. Fuel System Adjustment Values
Idle and FULL POWER Fuel Pressures and Flows
Engine1Prop.
RPM
Manifold
Absolute
Pressure
(MAP)
Unmetered
Pump PSI2
Metered
Nozzle
PSI3
Fuel
(lbs/hr)4
Fuel
(gal/hr)4

Standard Practice Maintenance Manual 6-23
30 Sep 2016 CHANGE 2
Engine Inspection and Service
6-4.7.3. Oil Pump Operational Check
1. Perform a Maintenance Preflight Inspection according to Section 6-4.7.2.
2. Perform a normal “Engine Start” according to instructions in Section 7-3.2 and
“Ground Run-up” according to Section 7-3.3 to allow the engine to warm to normal
operating temperatures.
3. Oil Pressure...................................................... Check
RESULT: Verify oil pressure is between 30 and 60 psi (80 psi for TSIO-360-E, EB,
F, FB, GB, KB, LB, MB, RB & SB) which at cruise power RPM. If necessary, adjust
according to the “Oil Pressure Adjustment” instructions in Section 6-4.10.1. If no oil
pressure is noted, shut down the engine immediately and investigate the cause.
4. If no further checks are required, proceed to “Engine Shutdown” in Section 6-4.7.6.
6-4.7.4. Fuel System Operational Check
CAUTION: Fuel system operational check instructions in this
section and the adjustments in Section 6-4.10.2 apply only to
Continental Motors (CM) continuous flow fuel injection systems. For
engines equipped with carburetors or servo controlled fuel systems,
refer to aircraft and/or equipment manufacturer’s instructions.
A fuel system operational check is required after replacement of fuel injection system
components, such as the fuel pump, fuel manifold valve, or fuel injectors. The fuel system
setup is a critical component of proper engine operation.
Follow the test equipment setup instructions in Section 6-4.7.4.1. When the test equipment
is set up properly, proceed with the “Fuel System Operational Checkout Procedure” in
Section 6-4.7.4.3.
NOTE: Fuel system adjustments are interactive. Once begun, perform the
entire procedure for proper fuel injection system operation.
Required Test Equipment
•Portable Tachometer
•Model 20 ATM-C Porta Test Unit (Section 2-1)
OR
•Calibrated pressure gauges (Section 2-1)
NOTE: Pressure gauges must be accurate within +/- 1%. The calibration
period should not exceed one year.
•A calibrated 0-60 psi gauge, graduated in 1 psi increments, to measure unmetered
pressure.
•On naturally aspirated engines, a calibrated 0-30 psi gauge graduated in 0.2 psi
increments, to measure metered pressure, or
•On turbocharged engines, a calibrated differential pressure gauge, 0-30 psid
maximum, graduated in 0.2 psi increments.
•Two Part No. MS51523-B4 swivel tees, used to insert gauges in line with fuel
lines, for metered and unmetered pressure references.

6-24 Standard Practice Maintenance Manual
15 April 2016
Engine Inspection and Service
•Hoses of sufficient length to allow personnel and equipment to perform the test at a
safe distance from the propeller arc and blast area.
•A digital hand-held tachometer, capable of verifying aircraft tachometer accuracy
prior to fuel system adjustment.
6-4.7.4.1. Fuel System Operational Checkout Setup Instructions
Important Setup Notes
CAUTION: For L/TSIO-360 and TSIO-520 engine models equipped
with a fixed (ground adjustable) exhaust bypass, verify the wastegate
is adjusted according to the aircraft manufacturer's instructions.
Failure to do so can result in an improperly adjusted fuel system and
possible engine damage.
1. Test gauge readings must be taken with the gauges held at the same height above the
ground as the fuel system component being measured.
2. Engine driven fuel pump output pressures vary with engine RPM. During ground
operation, full power RPM may not be obtained. Use the “Static RPM
Compensation” instructions found in Section 6-4.7.1.1 to correct the specified
metered pressures if full power RPM cannot be achieved.
3. On turbocharged engines, ensure manifold pressure is adjusted according to the
aircraft manufacturer’s instructions. Engine driven fuel pumps installed on
turbocharged engines are referenced to turbocharger compressor discharge pressure
(upper deck pressure) to achieve full power fuel pump pressure.
4. Turbocharged engines equipped with fuel pressure regulators must indicate a full
power metered pressure and fuel flow five (5) percent higher than the maximum
specified limit when the regulator is disconnected. This is required to ensure
adequate part-throttle fuel flow.
WARNING
Failure to properly support and stabilize component fittings
can result in fitting and/or component damage and loss of
system pressure.
Procedure
1. Perform a Maintenance Preflight Inspection according to Section 6-4.7.2.
2. Loosen and remove the unmetered fuel supply hose from either the fuel pump outlet
fitting, the fuel control unit inlet fitting, or the throttle body/metering unit inlet tee
(whichever is most accessible). Some engine models have a fuel pressure
connection fitting in the fuel control inlet screen that may be utilized for unmetered
pressure gauge attachment.
NOTE: Some installations may require multiple fittings to adapt the
metered and unmetered test equipment to the fuel injection system.
Connect the unmetered fuel supply hose to the straight end of the tee
connector.

Standard Practice Maintenance Manual 6-29
15 April 2016
Engine Inspection and Service
6-4.7.4.3. Fuel System Operational Checkout Procedure
Procedure
1. Set the aircraft brakes and block the aircraft main landing gear tires.
2. Verify the accuracy of the tachometer, manifold pressure gauge, and fuel flow
gauges prior to making any adjustments; replace faulty gauges.
3. Locate the IDLE speed stop screw (Figure 6-37 or Figure 6-39) on the throttle body
and turn it counter-clockwise two complete turns. During the operational check,
IDLE RPM will be controlled manually using the cockpit throttle control.
WARNING
Ensure the propeller area is clear before starting the engine.
4. Fuel Selector Valve .......................................... ON
5. Mixture Control ...............................................FULL RICH
6. Boost Pump (if equipped) ................................ AFM/POH
7. Perform a normal “Engine Start” according to instructions in Section 7-3.2 and
“Ground Run-up” according to Section 7-3.3 to allow the engine to warm to normal
operating temperatures.
NOTE: A puff of white smoke from a new or rebuilt engine, or an engine
returned from storage is normal. The source of the smoke is the remaining
preservation oil in the burning off in the combustion chamber. The smoke
should dissipate quickly; if smoke persists, shut down the engine and
investigate the cause.
CAUTION: Operating the engine without oil pressure will result in
engine malfunction or failure.
8. Throttle.............................................................600-1000 RPM (One minute)
RESULT: Operate the engine for one minute, gradually increasing the speed to 1000
RPM in 3 minutes.
9. Oil Temperature ...............................................Check
NOTE: Allow the engine oil to reach normal operating temperature
(100°F (38°C) for turbocharged engines or 75°F (24°C) for naturally
aspirated engines) before proceeding to the next step.
10. Boost Pump...................................................... OFF
11. Mixture Control ............................................... FULL RICH
12. Throttle.............................................................Set to IDLE RPM (Table 6-4)
13. Unmetered Fuel Pressure Gauge...................... Check
RESULT: Unmetered fuel pressure is within the range specified in Section 6-4.7.1.
Maintain engine speed until CHT is 250°F to 350°F (121°C to 177°C) and engine oil
temperature is 160°-180°F. Record the unmetered fuel pressure, regardless of
setting. If the unmetered fuel pressure is not within the limits specified in Section 6-
4.7.1, adjust the fuel pressure according to the instructions in Section 6-4.10.2.

6-30 Standard Practice Maintenance Manual
CHANGE 2 30 Sep 2016
Engine Inspection and Service
WARNING
Do not operate the engine at speeds above 1700 RPM until the
oil temperature reaches minimum takeoff temperature (100°F
(38°C) for turbocharged engines or 75°F (24°C) for naturally
aspirated engines) and oil pressure is within the normal
operating range. Operating at speeds above 1700 RPM before
reaching the minimum oil temperature may result in engine
malfunction or engine failure.
NOTE: To eliminate rough idling after mixture rise check, set engine
RPM to 1500-1800 RPM for 15 seconds before returning to IDLE RPM.
14. Mixture Control ............................................... Retard slowly to IDLE CUT-OFF
RESULT: Monitor engine RPM as mixture is leaned; stop leaning when maximum
RPM is achieved and record engine RPM. IDLE mixture rise should be 25 to 50
RPM (50-75 RPM for IO-240-B only) before beginning to drop toward zero. If
mixture rise is less that 25 RPM (50 for IO-240-B), the mixture is too lean. If the
mixture rise is more that 50 RPM(75 for IO-240-B), the mixture is too rich. Adjust
the idle mixture rise according to instructions in Section 6-4.10.2.
NOTE: The IDLE MIXTURE RISE is the difference (or RISE) between
the IDLE RPM at FULL RICH and the maximum achievable IDLE RPM.
15. Mixture Control ............................................... FULL RICH
16. Propeller Governor .......................................... WIDE OPEN
17. Throttle............................................................. WIDE OPEN
RESULT: Check the engine RPM with a portable tachometer. Record the engine
speed on the checklist. If the engine does not reach the rated, full power RPM,
calculate the corrected metered fuel pressure (Table 6-5 or Table 6-6).
NOTE: If no Manifold Pressure is provided for the engine model in
Table 6-4, skip step 18.
18. Manifold Pressure ............................................ Check
RESULT: Manifold pressure should equal the value specified for the engine model
in Section 6-4.7.1. If manifold pressure is not within the specified limits, adjust the
Wastegate Controller according to instructions in Section 6-4.10.3.
19. Metered Fuel Pressure Gauge ............................. Check
RESULT: The full power, metered fuel pressure should equal the value in Section 6-
4.7.1, with Table 6-5
or Table 6-6
correction factor, if applicable. Record the metered
fuel pressure, regardless of setting. If the full power, metered fuel pressure is not within
the specified limits, adjust the metered fuel pressure according to Section 6-4.10.2.
20. Throttle............................................................. Position to desired IDLE RPM
RESULT: adjust IDLE RPM according to instructions in Section 6-4.10.2.
21. Perform a “Flight Check”, if required, according to the instructions in Section 7-
2.4.2.
22. If no further checks are required, proceed to “Engine Shutdown” instructions in
Section 6-4.7.6.

Standard Practice Maintenance Manual 6-147
15 April 2016
Engine Inspection and Service
20. Inspect the wastegate controller and fittings for physical condition and security. If
the wastegate controller exhibits physical damage, replace the wastegate controller
with a new, rebuilt, or serviceable unit. Inspect the wastegate controller hoses, or
tubes, for chafing, nicks, cuts or leaks; replace hoses exhibiting these conditions.
Inspect the wastegate controller reference hoses or tubes for bends, dents, nicks or
leaks; replace reference lines exhibiting these conditions.
21. Inspect the wastegate controller (Figure 6-56) housing for oil leaks around the
diaphragm, deck pressure sensing port, oil inlet, oil outlet, or adjustment screw. If
oil is leaking from a fitting, remove the fitting and replace O-rings, install and torque
the fitting to Appendix B specifications. If oil is leaking from the housing, replace
the wastegate controller with a new, rebuilt, or serviceable unit.
Figure 6-56 repeated for reference (typical sloped controller)
22. Inspect the overboost valve housing for cracks or physical damage; replace cracked or
damaged overboost valve assembly with a new, rebuilt or serviceable unit. Remove
accumulated debris from the overboost valve exposed bellows assembly shaft (behind
the housing flange) and housing according to instructions in the primary ICA (
Ref:
Section 1-1.1
). Inspect the mounting flange for fastener security; replace missing
fasteners; retorque loose overboost valve fasteners to Appendix B specifications.
23. Inspect the compressor housing V-band clamp, exhaust housing bolts and lock tabs
for security. Torque loose hardware to Appendix B specifications.
24. Reassemble the turbocharger and exhaust system.
a. Install the induction system air supply according to aircraft manufacturer’s
instructions.
b. Install the turbocharger compressor discharge duct and exhaust pipe/heater muff
according to the instructions in the primary ICA (Ref: Section 1-1.1) or the
aircraft maintenance manual.

6-148 Standard Practice Maintenance Manual
CHANGE 2 30 Sep 2016
Engine Inspection and Service
6-4.22. Alternator Inspection
Frequency
During 500-hour inspection
Procedure
1. Remove engine cowling and aircraft components necessary to gain access to the
alternator.
2. Remove the alternator according to instructions in Section 10-4.1.1 or Section 10-
4.1.1. Perform the “Alternator Drive Hub Inspection” in Section 6-4.22.1 or
Section 6-4.22.2 on all gear driven alternators. For belt driven alternator removal,
refer to the engine primary ICA (Ref: Section 1-1.1).
3. Inspect Continental Motors alternators according to the Alternator Service Manual
(“Related Publications” in Section 1-2.5); correct any discrepancies discovered
during the inspection. For engines equipped with Hartzell (Kelly) ES10024 consult
Hartzell Service Information Letter A-135 for one time inspection requirements. For
engines equipped with Hartzell (Kelly) ES-6012 or ES7024 belt driven alternators,
consult Hartzell Service Information Letters A-137 and A-138 for one time
inspection requirements. For additional instructions regarding Hartzell alternator
instructions for continued airworthiness, consult Section 10-4.3. Remove and
replace all other alternators with a new, rebuilt or serviceable alternators.
4. Install the serviceable alternator according to “Gear Driven Alternator Replacement,
Forward Mount” in Section 10-4.1 or “Gear Driven Alternator Replacement, Aft
Mount” in Section 10-4.2 after successfully completing the alternator
manufacturer's service and inspection requirements. For belt driven alternator
installation, refer to the engine primary ICA (Ref: Section 1-1.1).
5. Perform the instructions in the normal “Engine Start” (Section 7-3.2) and “Ground
Run-up” (Section 7-3.3) to verify alternator operation.
6. Install airframe components and cowling according to the aircraft manufacturer's
instructions.
6-4.22.1. Alternator Drive Hub Inspection
FWDFWD
Applicable Engines:
GTSIO-520-C, D, F, H, K, L, M, N, IO-520-B, BA, BB, C, CB, M, MB, NB, TSIO-520-B,
BB, BE, D, DB, E, EB, J, JB, K, KB, L, LB, N, NB, UB, VB, WB, IO-550-A, B, C, G, N,
P, R, IOF-550-B, C, N, P, R, TSIO-550- B, C,E, G, K, N, TSIOF-550-D, J, K, P,
TSIOL-550, A, B, C
NOTE: This procedure only applies to the direct drive alternator. The
alternator drive hub is designed to slip when abnormal torque is required
to rotate the alternator shaft.
Procedure
1. Remove the top spark plugs according to instructions in Section 6-4.9.2.
2. Remove the alternator according to the instructions in Section 10-4.2.1.

Standard Practice Maintenance Manual 6-151
15 April 2016
Engine Inspection and Service
torque or less. Replace the drive hub if slippage occurs under 100 inch
pounds of torque.
4) Install the serviceable drive hub on the alternator according to instructions in
Section 10-4.2.3.
b. Inspect the multi-part drive coupling:
1) Secure the alternator coupling gear (Figure 6-99) (5) in the jaws of a padded
vice, leaving the gear section free.
NOTE: At 500 Hours, replace the retainer and bushings regardless of
condition, on the multi-piece couplings.
2) Remove the sleeve (6), bushings (8), and retainer (7). Do not remove the
drive hub (1) unless damage is suspect. Discard the bushings (8) and retainer
(7).
3) Inspect the nut (3), gear (5) and sleeve (6) for wear and replace if necessary.
4) Install a new retainer (7) and two new bushings (8) in the hub (1) on the
alternator shaft. Install the sleeve (6) and gear (5) on the shaft and secure with
the nut (3).
5) Install the drive hub assembly according to instructions in Section 10-4.2.3.
Figure 6-99. Alternator and Coupling Assembly
6. Install the alternator according to instructions in Section 10-4.2.4.
7. Install the top spark plugs according to instructions in Section 6-4.9.2.
1 Drive Hub 3 Castellated Nut 5 Gear 7 Retainer
2 Woodruff Key 4 Cotter Pin 6 Sleeve 8 Bushings

6-152 Standard Practice Maintenance Manual
CHANGE 2 30 Sep 2016
Engine Inspection and Service
6-5. Unscheduled Maintenance
6-5.1. Propeller Strike
A propeller strike is any incident (whether or not the engine is operating) in which the
propeller contacts a foreign object that 1)results in the necessity to repair the propeller
blade(s) (other than minor blade dressing) or 2)results in loss of engine RPM at the time of
contact. Propeller strikes can cause engine and component damage even if the propeller
continues to rotate. This damage can result in catastrophic engine failure.
WARNING
Do not attempt to dress a propeller blade without consulting
the propeller manufacturer's instructions. Stresses imposed on
the propeller are more concentrated in areas that are nicked
and cut. They may act as stress risers. Stress risers weaken the
blade and can eventually cause the blade to fracture.
In cases where a small foreign object such as a small stone, strikes the propeller during
operation, inspect and repair the propeller according to the propeller manufacturer’s
instructions. If foreign object damage requires removal of the propeller for repair(s)
perform the “Propeller Strike Inspection” in Section 6-5.1.1.
6-5.1.1. Propeller Strike Inspection
Following any propeller strike, disassemble and inspect all rotating engine components
prior to further flight; correct all unserviceable conditions. Inspect all engine driven
components according to the manufacturer’s instructions for continued airworthiness.
Procedure
1. Remove the propeller; inspect according to propeller manufacturer’s instructions.
2. Remove the engine from the aircraft according to the instructions in Section 5-1.
3. Disassemble the engine completely according to instructions in the primary ICA
(Ref: Section 1-1.1).
4. Regardless of condition, replace all counterweight pins, bushings, end plates and
snap rings. Replace all connecting rod nuts and bolts, regardless of condition.
5. Thoroughly clean the crankshaft according to instructions in Chapter 12; all
surfaces, especially those forward of the front main bearing, must be free of paint,
sludge, or any substance that may mask cracks.
6. Perform a “Magnetic Particle Inspection” on the crankshaft, connecting rods, gears
and remaining steel internal engine parts according to instructions in Section 11-3.
7. Strip the crankcase of all paint and clean the crankcase thoroughly according to
instructions in Chapter 12; all surfaces must be free of paint, sludge, or any
substance that may mask reliable inspection.
8. Perform a “Fluorescent Penetrant Inspection” on the crankcase according to
instructions in Section 11-2, paying particular attention to the forward crankcase
bearing support and adjacent structure.
9. Inspect the remainder of the engine according to the instructions in the primary ICA
(Section 1-1.1).
This manual suits for next models
68
Table of contents
Other CONTINENTAL AIRCRAFT ENGINE Engine manuals
Popular Engine manuals by other brands
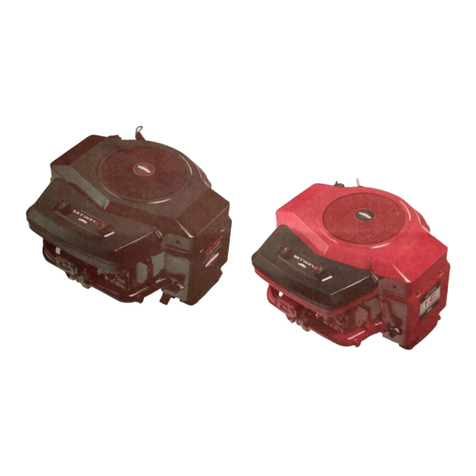
Briggs & Stratton
Briggs & Stratton 40A700 Series Operator owner's manual
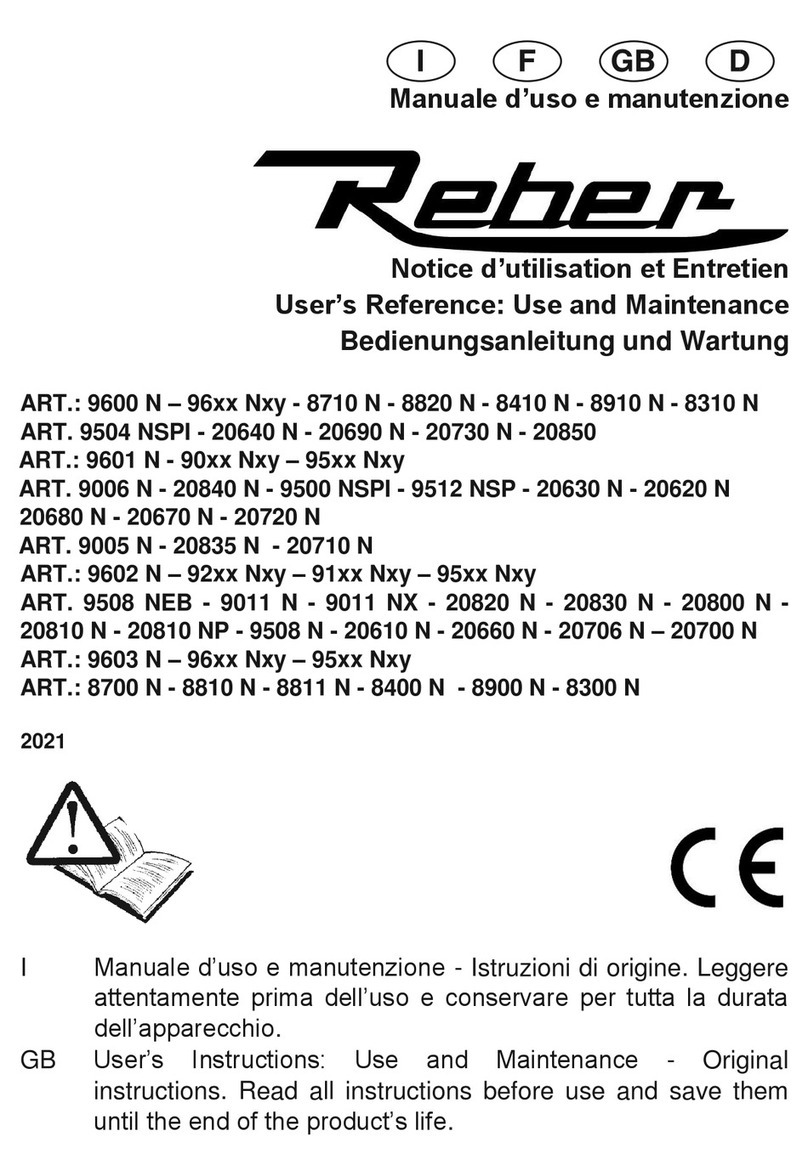
REBER
REBER 9504 NSPI User reference
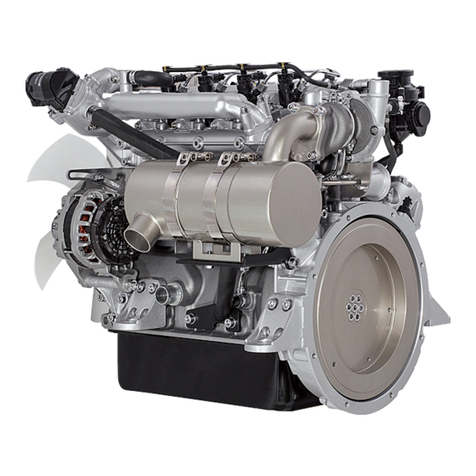
Hatz
Hatz 4H50TIC Operator's manual

Briggs & Stratton
Briggs & Stratton 91200 Series Operating & maintenance instructions

Briggs & Stratton
Briggs & Stratton 130G00 Repair manual
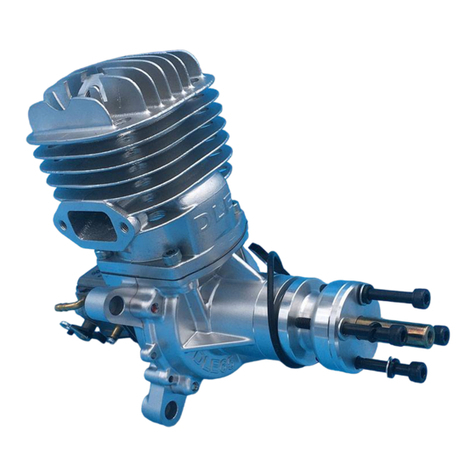
Booma-RC
Booma-RC DLE65 user manual