CONTINENTAL AIRCRAFT ENGINE A65 Series User manual

Publication M-0 CHANGE 4
©2017 CONTINENTAL MOTORS JUL 2017
CONTINENTAL AIRCRAFT ENGINE
MAINTENANCE
MANUAL
STANDARD PRACTICE
FOR SPARK IGNITED ENGINES
Technical Portions Accepted by the Federal Aviation Administration

A Standard Practice Maintenance Manual
CHANGE 4 31 Jul 2017
Supersedure Notice
This manual incorporates maintenance and service information contained in Continental Motors Service
Documents common to the horizontally opposed, spark ignition, AvGas aircraft engines conforming to Type
Certificate held by Continental Motors. This document is supplemental to the Instructions for Continued
Airworthiness provided in the manuals listed in Section 1-1.1. Instructions contained in the Service Documents
listed in Section 1-2.4 are superseded by instructions in this manual upon release, except for those Mandatory
Service Bulletins (MSBs) and Critical Service Bulletins (CSBs).
Effective Changes for this Manual
0 ................15 April 2016 4................... 31 Jul 2017
1 ................ 30 May 2016
2 .................30 Sep 2016
3 ................. 15 Jan 2017
List of Effective Pages
Document Title: Standard Practice Maintenance Manual
Publication Number: M-0 Initial Publication Date: 15 April 2016
Page Change Page Change Page Change Page Change
Cover............................4 2-9 thru 2-12.................0 6-7................................ 0 6-53 thru 6-66............... 0
A................................... 4 2-13 ..............................3 6-8 thru 6-10 ................ 3 6-67.............................. 1
B................................... 4 2-14 thru 2-24...............0 6-11 thru 6-15 .............. 0 6-68 thru 6-95............... 0
C (blank).......................1 3-1 thru 3-2...................0 6-16 thru 6-17 .............. 2 6-96..............................1
i thru ii...........................0 3-3 ................................3 6-18.............................. 4 6-97.............................. 0
iii thru xviii.....................1 3-4 ................................0 6-19 thru 6-22 .............. 0 6-98 thru 6-100............. 3
1-1 ................................0 3-5 thru 3-6...................4 6-23.............................. 2 6-101............................ 1
1-2 thru 1-3...................4 3-7 thru 3-8...................3 6-24 thru 6-29 .............. 0 6-102............................ 0
1-4 thru 1-10.................0 3-9 ................................1 6-30.............................. 2 6-103............................ 1
1-11 ..............................4 3-10 thru 3-24...............0 6-31.............................. 0 6-104 thru 6-115........... 0
1-12 ..............................4 4-1 thru 4-2...................0 6-32.............................. 4 6-116 ............................ 1
1-13 thru 1-16...............0 5-1 thru 5-8...................0 6-33 thru 6-48 .............. 0 6-117 thru 6-132........... 0
2-1 ................................0 6-1 thru 6-2...................0 6-49 thru 6-50 .............. 4 6-133 thru 6-135........... 1
2-2 thru 2-4................... 1 6-3 ................................2 6-50.1 thru 6-50.2 ........ 4 6-136............................0
2-5 thru 2-6...................0 6-4 thru 6-5...................3 6-51.............................. 0 6-137 thru 6-138........... 1
2-7 thru 2-8................... 1 6-6 ................................1 6-52.............................. 3 6-139............................ 0
Published and printed in the U.S.A. by Continental Motors
Available exclusively from the publisher: P.O. Box 90, Mobile, AL 36601
Copyright © 2016, 2017 Continental Motors. All rights reserved. This material may not be reprinted, republished, broadcast, or otherwise altered
without the publisher's written permission. This manual is provided without express, statutory, or implied warranties. The publisher will not be
held liable for any damages caused by or alleged to be caused by use, misuse, abuse, or misinterpretation of the contents. Content is subject to
change without notice. Other products and companies mentioned herein may be trademarks of the respective owners.

Standard Practice Maintenance Manual B
31 Jul 2017 CHANGE 4
List of Effective Pages, cont.
Page Change Page Change Page Change Page Change
6-140 ............................1 7-24.............................. 1 10-94 thru 10-95 .......... 3
6-141 ............................0 7-25 thru 7-30 .............. 0 10-96 thru 10-99 .......... 0
6-142 ............................3 8-1 thru 8-15 ................ 0 10-100 thru 10-101 ...... 3
6-143 thru 6-145...........0 8-16.............................. 2 10-102 thru 10-103 ...... 0
6-146 ............................3 8-17 thru 8-26 .............. 0 10-104 thru 10-106 ...... 4
6-146.1 added ..............3 9-1................................ 1 10-107 thru 10-108 ...... 0
6-146.2 added ..............3 9-2 thru 9-6 .................. 0 11-1 thru 11-8............... 0
6-146.3 added ..............3 10-1 thru 10-2 .............. 0 12-1.............................. 1
6-146.4 added ..............3 10-3.............................. 1 12-2 thru 12-12 ............ 0
6-146.5 added ..............3 10-4 thru 10-8 .............. 0 A-1 thru A-6.................. 0
6-146.6 added ..............3 10-9 thru 10-10 ............ 2 B-1 ............................... 1
6-147 ............................3 10-11............................ 1 B-2 thru B-7.................. 0
6-148 ............................2 10-12............................ 2 B-8 ............................... 4
6-149 thru 6-151...........0 10-13............................ 2 B-9 thru B-15................ 0
6-152 ............................2 10-14............................ 3 B-9 thru B-16................ 0
6-153 thru 6-154...........1 10-15............................ 1 C-1 thru C-4 ................. 0
6-155 ............................0 10-16 thru 10-18 .......... 2 C-5 thru C-6 ................. 4
6-156 ............................1 10-19 thru 10-21 .......... 0 C-7 ............................... 3
6-157 ............................0 10-22............................ 1 C-8 thru C-9 ................. 1
6-158 ............................3 10-23 thru 10-24 .......... 0 C-10 thru C-18 ............. 0
6-159 ............................1 10-25............................ 1 C-19 ............................. 1
6-160 thru 6-164...........0 10-26 thru 10-32 .......... 0 C-20 thru C-23 ............. 0
6-165 ............................3 10-33............................ 4 C-24 ............................. 4
6-166 thru 6-171...........0 10-34............................ 0 C-25 thru C-26 ............. 0
6-172 ............................1 10-34.1 thru 10-34-2.... 4
6-173 thru 6-174...........0 10-35 Blank added....... 4
7-1 thru 7-2...................0 10-36............................ 4
7-3 thru 7-5...................4 10-37............................ 0
7-6 thru 7-7...................0 10-38............................ 3
7-8 ................................1 10-39 thru 10-40 .......... 1
7-9 ................................0 10-41 thru 10-62 .......... 0
7-10 ..............................1 10-63............................ 3
7-11 thru 7-17 ...............0 10-64 thru 10-69 .......... 0
7-18 ..............................3 10-70............................ 3
7-19 thru 7-23...............0 10-71 thru 10-93 .......... 0

C Standard Practice Maintenance Manual
CHANGE 1 30 May 2016
Intentionally Left Blank

Standard Practice Maintenance Manual 1-1
15 April 2016
Introduction
Chapter 1. Introduction
1-1. Scope and Purpose of This Manual
This manual provides maintenance instructions for spark ignition, Standard Practices
operating on aviation gasoline (AvGas). These Instructions for Continued Airworthiness
(ICA) are supplied to the owner with the engine. Instructions in this manual are standard
practices, with differences identified by model, for A-65, A-75, C-75, C-85, C-90, C-125, C-
145, E-165, E-185, E-225, O-200, GO-300, O-300, IO-240, IOF-240, IO-346, IO-360,
LTSIO-360, TSIO-360, O-470, IO-470, TSIO-470, GTSIO-520, IO-520, LTSIO-520, TSIO-
520, IO-550, IOF-550, TSIO-550, TSIOF-550, TSIOL-550 and TIARA (6-285 and 6-320)
series aircraft engines. For information specific to the Continental Motors engine series,
accessories, or the airplane, refer to the appropriate manual. For the specific instructions
regarding the electronic equipment on FADEC engines, or for unlisted engine models, refer
to the primary ICA.
A list of tools for all applicable engines is provided in Chapter 2. Consumables items, such
as lubricants, sealants, and adhesives are listed in Chapter 3. Airworthiness limitations are
in Chapter 4. Chapter 5 contains generic installation instructions applicable to our engines.
Chapter 6 provides schedule inspection and service intervals and instructions, as well as
unscheduled maintenance instructions. Chapter 7 contains general engine operating
instructions, applicable to all models. Chapter 8 contains engine troubleshooting
instructions. Engine preservation and storage instructions are in Chapter 9. Non-overhaul
engine part replacement instructions are in Chapter 10. Chapter 11 contains Non-
Destructive Inspection guidelines. Chapter 12 contains part cleaning instructions.
Appendix A contains a glossary of common terms and acronyms used throughout the
manual; Appendix B provides torque specifications, and Appendix C contains
maintenance standards.
1-1.1. Instructions for Continued Airworthiness
Continental Motors Part No. M-0, is supplemental, as defined by Title 14 CFR§33.4, to
the maintenance and overhaul manuals listed below. Together, this manual and those listed
below comprise the instructions for continued airworthiness for applicable engines. This
manual, and the overhaul manuals and component service manuals (as applicable to
engine specification) listed below are delivered to the customer with the engine. Service
documents and Airworthiness Directives may also affect ICAs. Refer to Section 1-2.5 for
instructions to check current publication status.
Part No. Title Applicability
M-2 Maintenance and Overhaul Manual O-200-D, X
M-6 Maintenance and Overhaul Manual IO-240
M-7 Maintenance and Overhaul Manual IO-360
M-11 Maintenance Manual IO-520 Permold
M-16 Maintenance and Overhaul Manual IO-550 Permold
M-18 Maintenance and Overhaul Manual TSIO-550 Permold

1-2 Standard Practice Maintenance Manual
CHANGE 4 31 Jul 2017
Introduction
M-22 Maintenance and Overhaul Manual IOF-240
M-24 Maintenance Manual IOF-550-A, B, C, G, N, P & R
M-26 Maintenance and Overhaul Manual TSIOF-550
OH-15 Overhaul Manual TSIOL-550-C
OH-24 Overhaul Manual IOF-550
OMI-15 Operation, Maintenance and TSIOL-550-C
Installation Manual
X30008 Overhaul Manual A-65, A-75
X30010 Overhaul Manual C-75, C,85, C90, O-200-A, B
X30013 Overhaul Manual C-125, C-145, O-300
X30016 Overhaul Manual E-165, E-185, E-225
X30019 Overhaul Manual GO-300
X30027 Overhaul Manual IO-346
X30033 Overhaul Manual TSIO-470
X30039 Overhaul Manual IO-520
X30045 Overhaul Manual GTSIO-520
X30144 Overhaul Manual TIARA 6-285 and 6-320
X30531 Alternator Service Instructions Continental alternators
X30571 Maintenance and Operator’s Manual TSIO-360-LB
X30574 Overhaul Manual TSIO-520-B, BB, BE, D, DB,
DB, E, EB, J, JB, K, KB, L,
LB, N, NB, U, UB, VB,
WB Permold series
X30575 Overhaul Manual LTSIO-520-AE
TSIO-520-C, CE, G, H, M, P,
R, T, AE, AF Sandcast series
X30586 Overhaul Manual O-470-A, B, E, G, J, K, L, M
R, S, U
X30588 Overhaul Manual IO-470-C, D, E, F, G, H, J, K,
L, M, N, P, R, S, U, V, VO
X30592 Starter Service Instructions Energizer® starters
X30596 Overhaul Manual LTSIO-360-EB, KB & RB,
TSIO-360-A, AB, B, C, CB,
D, DB, E, EB, F, FB, G, GB,
H, HB, J, JB, K & KB, LB,
MB, SB

Standard Practice Maintenance Manual 1-3
31 Jul 2017 CHANGE 4
Introduction
X30596S1 Overhaul Manual LTSIO-360-RB,
TSIO-360-RB
X30600 Overhaul Manual TSIOL-550-A
X30601 Maintenance and Operator’s Manual TSIOL-550-A
X30605 Maintenance Manual IO-550-D, E, F & L
X30607 Overhaul Manual IO-550-D, E, F & L
X30645 Maintenance Manual LTSIO-360-RB
TSIO-360-RB
X30672 Maintenance Manual TSIO-360-MB, SB
1-1.2. Advisories
This manual utilizes three types of advisories; defined as follows:
WARNING
A warning emphasizes information which, if disregarded, could
result in severe injury to personnel or equipment failure.
CAUTION: Emphasizes certain information or instructions, which if
disregarded, may result in damage to the engine or accessories.
NOTE: Provides special interest information, which may facilitate
performance of a procedure or operation of equipment.
Warnings and cautions precede the steps to which they apply; notes are placed in the
manner which provides the greatest clarity. Warnings, cautions, and notes do not impose
undue restrictions. Failure to heed advisories will likely result in the undesirable or unsafe
conditions the advisory was intended to prevent. Advisories are inserted to ensure
maximum safety, efficiency, and performance. Abuse, misuse, or neglect of equipment can
cause eventual engine malfunction or failure.
1-1.3. Effectivity Symbols
Variations in engine configuration may require specific instructions or illustrations. When
information pertains to only a subset of the applicable engine models, an effectivity
symbol will precede the information. Effectivity symbols found in this publication are:
Forward Mounted Gear Driven Alternator
Aft Mounted Gear Driven Alternator
Energizer Starter
SkyTec Starter
FWDFWD
AFTAFT
EZREZR
SKYSKY

1-4 Standard Practice Maintenance Manual
15 April 2016
Introduction
1-1.4. Using this Manual
This manual, the primary engine ICA listed in Section 1-1.1, applicable FAA ADs and
Continental Motors service documents, the accessory manuals listed in Table 1-2, and all
changes incorporated in the ICAs as revisions constitute the Instructions for Continued
Airworthiness (ICAs) prepared by Continental Motors and accepted by the FAA. We
prepared this manual in a user-friendly format suited equally for electronic viewing and
print. Illustrations in this manual are for reference only, depicting the most prominent
configuration in the engine series. Consult the electronic illustrated parts catalog for
engine model-specific illustrated parts breakdowns. The current information available
from Continental Motors must be used to perform engine service, repair or overhaul.
Continental Motors provides Instructions for Continued Airworthiness based on the
design, testing, and certification of engines and parts for which Continental Motors is the
holder of the Type Certificate (TC) or Parts Manufacture Approval (PMA) issued by the
Federal Aviation Administration (FAA).
WARNING
Continental Motors Instructions for Continued Airworthiness
are applicable only to Continental Motors engines conforming
to the approved, type certified engine model configuration.
Continental Motors ICAs must not be used for aftermarket
parts or products modified by Supplemental Type Certificate.
Installation of aftermarket parts on a Continental Motors engine constitutes a deviation
from type-design criteria. Continental Motors has not participated in design, test, or
certification of any aftermarket parts. Continental Motors does not provide product
manufacturing specifications to aftermarket parts manufacturers and accepts no liability
for the suitability, durability, longevity, or safety of such parts installed on Continental
Motors engines. Installation of aftermarket parts on a Continental Motors engine must be
performed using Instructions for Continued Airworthiness prepared by the manufacturer
and approved by the FAA for the subject installation. For work with the engine installed in
the aircraft, the aircraft maintenance manual may also be required to gain access to,
perform maintenance, or install some items. Use only the current information from the
aircraft manufacturer.
Exploded assembly illustrations accompany instructions throughout the manual. Parts in
illustrations (Figure 1-1) are identified with either alpha or numerical callouts (indexes).
Corresponding parts listings follow the illustrations for reference. The first time
instructions refer to an illustration, the figure number is identified in parentheses, followed
by the callout. In subsequent parts references, only the callout will be specified unless the
referenced illustration changes.

Standard Practice Maintenance Manual 1-11
31 Jul 2017 CHANGE 4
Introduction
1-2.4.1. Service Documents Incorporated in this Manual
Applicable technical maintenance and service information contained in the Service
Documents listed below, relevant to the engine models covered by this engine manual,
have been incorporated in this M-0 Standard Practice Maintenance Manual. This manual
supersedes and retires these older Service Documents (where applicable) excluding
Mandatory Service Bulletins (MSBs) and Critical Service Bulletins (CSBs) identified
with an asterisk below.
The full content of active Continental Motors Service Documents is available at
www.continentalmotors.aero. Refer Section 1-3, “Contact Information” for Continental
Motors web site details.
Table 1-1. Service Documents Incorporated in Manual
Service Document Subject Affected Chapter
M67-12, Overboost of Turbocharged Engines Unscheduled Maintenance 6
M72-17R1, Maximum Weight Difference Between
Connecting Rods and Pistons in the Same Engine
Parts Replacement 10
M76-4, Propeller Shaft or Crankshaft Oil Seal
Replacement
Unscheduled Maintenance 10
M76-8, Intake Valve Change Unscheduled Maintenance 10
M77-3, Use of Alternate Fuels in Engines Originally
Certified for 80/87, 91/96 and 100/130 Grade Fuels
Engine Operation 7
M84-5, Gear Driven Alternator Inspection Procedure Alternator Replacement 10
M85-10, Cylinder Hold Down Nuts Cylinder Replacement 10
M87-15, Alternator Ground Strap Alternator Replacement 10
M88-9, Lightning Strikes Unscheduled Maintenance 6
M88-10, Contaminated Fuels Unscheduled Maintenance 6
M89-7R1, Engine Operation after Cylinder
Replacement and/or Major Overhaul
Unscheduled Maintenance 7
M89-9, Excessive Crankcase Pressure Unscheduled Maintenance 8
M90-17, Crankcase Inspection Criteria Scheduled Maintenance 6
SIL93-11B, Service Document Format Service Documents 1
SIL93-15, General Practices for Installation of Lock
Wire, Tab Washers, and Cotter Pins
Standard Practices Appendix C
* MSB94-8D, Magneto to Engine Timing Scheduled Maintenance 6
SB95-2, Inspection and Maintenance of Engine Control
Cables and Linkage
Inspection 6
SB95-3B, Alternator/Generator Drive Coupling Alternator Maintenance 6, 10
SIL95-5, Hose and Tubing Installation Hose and Tubing installation Appendix C
SB96-7D, Torque Limits Fastener Torque Appendix B
* MSB96-10B, Crankshaft Ultrasonic Inspection Engine Overhaul or Crankshaft
Repair
10

1-12 Standard Practice Maintenance Manual
CHANGE 4 31 Jul 2017
Introduction
* Documents remain active in the service bulletin set.
SB96-11B, Propeller Strikes and Hydraulic Lock Unscheduled Inspection 6
SB96-12, Cylinder Continued Airworthiness Scheduled Inspection 6 & 10
SID97-2B, Design, Operation Maintenance and
Warranty of Cylinders
Engine Maintenance 6
SID97-3G, Continuous Flow Fuel Injection Systems
Adjustment Specifications and Instructions
Operational Checks and
Adjustments
6
SID97-4F, Cylinder Bore and Piston Fit Specifications Overhaul & Service Limits 10
SB97-6B, Mandatory Replacement Parts Engine Inspection & Assembly Appendix C
SIL98-9E, Time Between Overhaul Periods Scheduled Maintenance 6
SIL99-1, Engine Preservation for Active and Stored
Aircraft
Engine Preservation and Recovery 9
SIL99-2C, Sealants, Lubricants and Adhesives
Authorized by CMI
Materials 3
SB00-3A, Crankshaft, Counterweight and Connecting
Rod Repair Information
Repair Specifications 10
SIL00-9A, Engine Data Plates Data Plate Replacement Appendix C
SIL00-11B, Release of new Cylinder Induction Port
Drain Connector
Cylinder Assembly 10
SIL03-1, Cold Weather Operation - Engine Preheating Engine Operation 7
SIL03-2C, Currently Active Approved Spark Plug
Application
Spark Plugs 6
SB03-3, Differential Pressure Test and Borescope
Inspection
Inspection Criteria 6
SIL04-12A, Authorized Engine Adjustments,
Component Replacement and Repositioning
Engine Specification 5
SB05-2, Overspeed Limitations Unscheduled Maintenance 6
* CSB08-3C, Throttle & Mixture Control Levers Fuel Injection System Assembly 6
SB08-13, Induction System Hose and Clamp
Installation
Induction System Inspection &
Assembly
6
SB11-3, Alternator and Drive Coupling Installation Alternator Replacement 6, 10
SIL13-2A, Alternator Instructions for Continued
Airworthiness
Alternator Replacement 6, 10
SB14-8, Exhaust Flange to Cylinder Installation Exhaust System Installation 10
SB16-3, Turbocharger Check Valve Inspection and
Cleaning
Exhaust System Inspection 6
Table 1-1. Service Documents Incorporated in Manual
Service Document Subject Affected Chapter

Standard Practice Maintenance Manual 3-5
31 Jul 2017 CHANGE 4
Lubricants, Sealants, and Adhesives
654663 Loctite 30516 Gasket Sealant
(with P/N 641543 Silk Thread)
Crankcase parting face
Apply according to assembly
instructions
Starter adapter to accessory case
Accessory drive adapter
Pressure oil pump covers
Pressure scavenge pump covers
657042 Loctite 565 Adhesive Sealant Use on all pipe threads to oil coolers
and other oil sources
All models (use sparingly on
male threads only)
N/A Miller-Stephenson MS-122AD Ignition harness terminals at magneto
block end & spark plug / ECU terminals All models
N/A Loctite 592 Teflon PS/T Pipe
Sealant
Use on all pipe threads except as noted
elsewhere
All pressure relief valve housing threads
Permold 2 studs engine mount 1-3-5
side bottom
All models, where applicable
All threaded fasteners installed in a stud
hole through to an oil source
Apply before installing threaded
fastener
Table 3-5. Lubricants
CM
Part
Number
Type Application Remarks
646943 Loctite 76732 Anti-Seize
Lubricant
Fuel injector nozzles
(at cylinder head) See Figure 3-1
Mechanical tachometer drive housing
threads not connected through to an oil
source.
At engine assembly
Exhaust studs (applied to nut end
before torque), exhaust slip joints All except TSIOL550
Vernatherm plug At engine assembly
All 0.3125 and larger studs unless
otherwise noted
At engine assembly
At engine assembly
Throttle body air reference fittings Where applicable
Oil sump return fitting IO360ES3B, 14B, &
IO360HB9B
654468 Shell #5 MIL-G-3545-C Grease
Fuel injection linkages At engine assembly
Throttle & mixture control linkages
Apply at pivot points during
assembly and periodic
maintenance
654514 CRC 336 Rust Preventative
Compound Spray exhaust end of turbocharger After engine test
654561
Shell Gadus S2 V220 2
formerly
Shell Alvania # 2
Light coat at contact point between nut
seat and ignition lead ferrule All models, where applicable
Apply to oil seal lip only (alternator seal)
LTSIO360E, EB, RB;
TSIO360E, EB, F, FB, GB, KB,
LB
Apply to crankshaft nose oil seal lip All models
Table 3-4. Sealants
CM
Part
Number Type Application Remarks

3-6 Standard Practice Maintenance Manual
CHANGE 4 31 Jul 2017
Lubricants, Sealants, and Adhesives
656817 Super Molyshield Grease
Starter worm gear & bevel gear teeth All models during engine
assembly
Needle bearings and ball bearings
Valve stems
Accessory drive splines and couplings Where applicable
Idler gear and pin 470, 520, 550
Magneto rubber drive bushings All models
Oil seal lips only
Fuel injection controls, o-rings, springs,
shafts, and bushings
Except 360, TSIO520D,
GTSIO520K, which use 50W
motor oil
Oil pumps (pressure & scavenge) Coat gear cavity during pump
assembly
Adapter (tach reduction) TSIO & LTSIO360
N/A
Use only manufacturer’s
recommended spark plug
thread lubricant
Spark plugs All models
N/A
Chesterton #995 Release
Agent
or WD-40
Induction system hoses and flex duct
connections, pipe plugs in throttle body
units
All models
N/A Dow Corning No. 4
Rubber oil seal of spin-on oil filters. Do
not apply to oil filter P/N 658753,
658754, or 658755 filters with anti-stick
coating on seal. All models where applicable
Governor pad gaskets (both sides)
Starter adapter cover o-rings
N/A Dow Corning G-N Paste Camshaft lobes and tappet faces During engine assembly
N/A LPS 2 Throttle and Mixture Control Valves
Linkages
Apply at pivot points during
maintenance
N/A Lubriplate 630 AA (optional) Throttle and Mixture Control Valves
Linkages
Apply at pivot points during
assembly
N/A Lubriplate 930 AA O.D. of valve guides All models during valve guide
installation
N/A Mouse Milk Wastegate butterfly and linkage
Carbon solvent used on
turbocharged engines during
preventive maintenance
N/A SAE J1966 Grade 50
Aviation Oil
Quill Shaft Springs GTSIO520
Crankshaft bearings
Connecting rod bearings During engine assembly
Prop driver, driven gears & bearings
Camshaft bearings
Tachometer gears & adapters
Accessory spur gear teeth
Prop governor transfer collar & sleeve
Starter cone, bushing & nut
Starter clutch spring (ID & OD)
Table 3-5. Lubricants
CM
Part
Number
Type Application Remarks

Standard Practice Maintenance Manual 6-17
30 Sep 2016 CHANGE 2
Engine Inspection and Service
TSIO-520-BE 600
2600
-
38.0
5.5 - 7.0
25.0 - 28.0
-
12.7 - 14.1
-
214 - 224
-
36.5 - 38.2
TSIO-520-C, H 600
2700
-
32.5
5.5 - 7.0
29.0 - 32.0
-
15.3 - 17.2
-
160 - 170
-
27.3 - 29.0
TSIO-520-CE 600
2700
-
37.0
5.5 - 6.5
33.0 - 36.0
-
16.2 - 18.0
-
215 - 225
-
36.6 - 38.3
TSIO-520-D, DB 600
2700
-
32.5
5.5 - 7.0
29.0 - 32.0
-
13.3 - 15.1
-
160 - 170
-
27.3 - 29.0
TSIO-520-E, EB 600
2700
-
34.5
5.5 - 6.5
31.0 - 34.0
-
15.6 - 17.7
-
175 - 185
-
29.8 - 31.5
TSIO-520-G 600
2700
-
35.0
5.5 - 6.5
31.0 - 34.0
-
15.8 - 17.6
-
181 - 191
-
30.8 - 32.5
TSIO-520-J, JB 600
2700
-
36.0
5.5 - 6.5
31.0 - 34.0
-
16.9 - 18.7
-
170 - 178
-
29.0 - 30.3
TSIO-520-K, KB 600
2700
-
33.0
5.5 - 7.0
29.0 - 32.0
-
15.1 - 17.4
-
163 - 175
-
27.8 - 29.8
TSIO-520-L, LB 600
2700
-
38.0
25 Minimum
45.0 - 55.0 MFG10 -
180 - 190
-
30.7 - 32.4
TSIO-520-M, R 600
2700
-
36.5
5.5 - 6.5
33.0 - 37.0
-
16.9 - 19.9
-
170 - 186
-
29.0 - 31.7
TSIO-520-N, NB 600
2700
-
38.0
5.5 - 6.5
32.0 - 35.0
-
16.9 - 19.9
-
170 - 186
-
28.9 - 31.7
TSIO-520-P 600
2700
-
36.5
5.5 - 6.5
33.0 - 37.0
-
18.4 - 19.9
-
180 - 186
-
30.7 - 31.7
TSIO-520-T 600
2700
-
39.5
5.5 - 6.5
33.0 - 37.0
-
16.3 - 18.1
-
185 - 195
-
31.5 - 33.2
TSIO-520-UB 600
2700
-
36.0
5.5 - 6.5
33.0 - 37.0
-
14.4 - 16.0
-
195 - 205
-
33.2 - 34.9
TSIO-520-VB 600
2700
-
40.5
5.6 - 6.5
36.0 - 39.5
-
16.9 - 18.7
-
200 - 210
-
34.1- 35.8
TSIO-520-WB 600
2700
-
39.5
25 Minimum
45.0 - 55.0
-
MFG11
-
190 - 200
-
32.4 - 34.1
GTSIO-520-C 525
2400
-
34.5
4.0 - 7.0
30.0 - 33.0
-
16.5 - 17.5
-
215 - 225
-
36.6 - 38.3
GTSIO-520-D, H 467
2267
-
39.5
4.0 - 7.0
30.5 - 35.0
-
15.7 - 17.3
-
250 - 260
-
42.6 - 44.3
GTSIO-520-F, K11 600
2267
-
44.5
6.75 - 7.25
38.0 - 41.0
-
17.4 - 18.8
-
300 - 310
-
51.1 - 52.8
GTSIO-520-L, N11
GTSIO-520-M
467
2234
39.0
40.0
4.0 - 7.0
29.5 - 35.0
-
16.4 - 17.9
-
255 - 265
-
43.4 - 45.1
GIO-550-A 600
2267
- 25 Minimum
45 - 55
-
MFG11
-
175 - 185
-
29.8 - 31.5
IO-550-A 6600
2700
-
-
8.0 -10.0
32.0 - 36.0
-
17.7 -20.0
-
142 - 150
-
24.2 - 25.6
IO-550-B 6600
2700
-
-
8.0 -10.0
29.2 - 36.2
-
16.5 - 18.4
-
146 - 156
-
24.9 - 26.6
Table 6-4. Fuel System Adjustment Values
Idle and FULL POWER Fuel Pressures and Flows
Engine1Prop.
RPM
Manifold
Absolute
Pressure
(MAP)
Unmetered
Pump PSI2
Metered
Nozzle
PSI3
Fuel
(lbs/hr)4
Fuel
(gal/hr)4

6-18 Standard Practice Maintenance Manual
CHANGE 4 31 Jul 2017
Engine Inspection and Service
IO-550-C 6600
2700
-
-
8.0 -10.0
31.6 - 37.8
-
17.6 - 19.6
-
152 - 160
-
25.9 - 27.3
IO-550-D, E, F, L 6600
2700
- 8.0 - 10.0
32.0 - 36.0
-
17.2 - 20.0
-
143 - 155
-
24.4 - 26.4
IO-550-G 600
2500
-
-
8.0 -10.0
22.0 - 26.0
-
14.7 - 16.0
-
125 - 130
-
21.3 - 22.1
IO-550-N, P, R 600
2700
-
-
8.0 -10.0
28.0 - 30.0
-
19.0 - 21.3
-
150 - 160
-
25.6 - 27.3
TSIO-550-B 600
2700
-
38.0
7.0 - 9.0
32.0 - 36.0
-
15.3 - 16.9
-
241 - 252
-
41.0 - 42.9
TSIO-550-C 600
2600
-
35.5
7.0 - 9.0
26.0-29.0
-
12.7 - 13.9
-
212 - 224
-
36.1 - 38.1
TSIO-550- E 600
2700
-
38.5
7.0 - 9.0
32.0 - 36.0
-
15.3 - 16.9
-
244 - 254
-
41.5 - 43.3
TSIO-550- G 600
2700
-
34.0
7.0 - 9.0
20.5 - 28.5
-
12.4 - 13.6
-
201 - 211
-
35.2 - 35.9
TSIO-550-G
MOONEY 12
600
2500
-
33.5
7.0-9.0
20.0-23.0
-
10.4-11.6
-
177-180
-
30.0-30.7
TSIO-550- K, N 600
2500
-
37.5
7.0 - 9.0
20.5 - 28.5
-
14.2 - 14.8
-
210 - 220
-
35.8 - 37.5
TSIOL-550-A 600
2600
-
35.0
5.5 - 6.5
32.5 - 35.5
-
17.0 - 19.0
-
170 - 180
-
29.0 - 30.7
TSIOL-550-B 600
2700
-
35.0
6.0 - 8.0
36.0 - 40.0
-
20.0 - 22.5
-
175 - 185
-
29.8 - 31.5
TSIOL-550-C 600
2600
-
39.5
6.0 - 8.0
37.0 - 40.0
-
15.0 – 16.5
-
204 - 216
-
34.8 – 36.8
1. The setup procedures contained in this bulletin are only for use on engines that have not been modified from their original configuration as
shipped from the factory by Continental Motors. Engines which have been modified by the installation of aftermarket components such as
turbo-normalizing systems, turbocharging systems, intercoolers, after-coolers, fuel nozzles, etc., whether by STC or field approval, must
use the instructions provided by the STC holder or installer. CM will not accept responsibility or liability for any modified engine set up
according to the instructions contained in these instructions.
2. FULL POWER unmetered fuel pump pressure limits are provided for reference only. Use metered fuel pressure specifications for adjust-
ments at full power.
3. Use for full power, maximum RPM adjustment only. All other parameters for reference only, Footnote 2 applies.
4. May be determined using a calibrated in-line flow measuring device. Otherwise use metered fuel pressure specifications. Refer to Aircraft
Manufacturer's Maintenance Manual for method of verifying accuracy of fuel flow indicator.
5. IO-360-DB engine model specifications equipped with altitude compensating fuel pumps; Flight Test (Section 7-2.4.2) required after fuel
system adjustment.
6. Engine model equipped with altitude compensating fuel pump; Flight Test (Section 7-2.4.2) required after fuel system adjustment.
7. This engine is installed in Cirrus SR20 aircraft. IO-360-ES engines has been derated by Cirrus from original 210 HP at 2800 RPM to 200 HP
at 2700 RPM. Engine data plate reflects original CM data of 210 HP at 2800 RPM. Refer to Cirrus SR20 Maintenance Manual and POH.
8. Engine model certified for five minute rated takeoff power at 2800 RPM. Max. continuous power is 2600 rpm.
9. Refer to the aircraft manufacturer's instructions for adjustment procedures.
10. Refer to the aircraft manufacturer's instructions for adjustment procedures.
11. Refer to the aircraft manufacturer's instructions for adjustment procedures.
12. TSIO-550-G installed in Mooney aircraft has been rated to a power level that is less than the approved Type Certificate Data Sheet. Refer to
the Mooney Aircraft Maintenance Manual for setup instructions.
Table 6-4. Fuel System Adjustment Values
Idle and FULL POWER Fuel Pressures and Flows
Engine1Prop.
RPM
Manifold
Absolute
Pressure
(MAP)
Unmetered
Pump PSI2
Metered
Nozzle
PSI3
Fuel
(lbs/hr)4
Fuel
(gal/hr)4

Standard Practice Maintenance Manual 6-31
15 April 2016
Engine Inspection and Service
6-4.7.5. Magneto RPM Drop Check
WARNING
Absence of RPM drop during magneto check may be an
indication of a faulty ignition circuit (Hot Magneto). Should the
propeller be turned by hand (as in during preflight), the engine
could inadvertently start and cause personal injury or death.
Flight is prohibited until the condition is corrected.
CAUTION: When operating on single ignition, some RPM drop and
slight engine roughness as each magneto is switched off should be
noted. Excessive (greater than 150 RPM) RPM drop may indicate a
faulty magneto or fouled spark plugs.
NOTE: If the engine runs roughly after single magneto operation,
increase engine speed to 2200 RPM in the BOTH position and lean the
mixture control until the RPM peaks for ten seconds before returning to
the full rich position to clear the spark plugs and smooth operation before
returning to single magneto operation.
Procedure
1. Start the engine according to the “Engine Start” instructions in Section 7-3.2.
RESULT: No defects noted. Allow the engine oil to warm to normal (100°F (38°C)
for turbocharged engines or 75°F (24°C) operating temperature.
CAUTION: Avoid prolonged single magneto operation to preclude
spark plug fouling.
NOTE: In the instructions below, the term “Magneto Switch” applies to
the method the aircraft manufacturer uses to control the magnetos. Some
manufacturers use a wafer switch to control the starter with four
additional positions for magneto control, labeled OFF, L, R and BOTH.
Toggle switches may be used to accomplish the same action. Adjust
instructions according to the available aircraft controls.
2. Throttle............................................................. 1700 RPM
3. Magneto Switch ............................................... R
RESULT: RPM drop does not exceed 150 RPM; record Left Magneto channel drop
result. Maximum allowable RPM drop spread between magneto channels is 50
RPM.
4. Magneto Switch ............................................... BOTH
5. Magneto Switch ............................................... L
RESULT: RPM drop does not exceed 150 RPM; record Right Magneto channel drop
result. Maximum allowable RPM spread between magneto channels is 50 RPM.
6. Magneto Switch ............................................... BOTH
7. Throttle............................................................. Reduce to IDLE
8. If no further checks are required, proceed to “Engine Shutdown” on page 32.

6-32 Standard Practice Maintenance Manual
CHANGE 4 31 Jul 2017
Engine Inspection and Service
6-4.7.6. Engine Shutdown
Procedure
1. Perform a normal engine shutdown according to the “Engine Shutdown”
instructions in Section 7-3.4.
2. Remove installed test equipment.
a. Disconnect the metered fuel pressure test hose from the aircraft fittings.
b. Disconnect the unmetered fuel pressure test hose from between the fuel pump
and the fuel control assembly.
c. Remove any fittings added to adapt the plumbing to the test equipment.
3. Reconnect and torque the fuel system hoses to Appendix B specifications.
a. Connect the unmetered pressure hose between the fuel pump and the fuel control
assembly.
CAUTION: Use only P/N 639494 cap on the tee fitting. Installation
of a pipe thread cap on the flared fitting may damage the fitting.
b. Install the protective caps (P/N 639494) (or airframe-installed fitting to cockpit
metered pressure gauge) on the fuel manifold valve (metered pressure) or throttle
body inlet tee (metered pressure) fittings, if equipped, and torque the cap to
standard torque for a #4 steel fitting in Table B-8.
4. Leak Check
a. Master Power Switch .................................. ON
b. Mixture........................................................ FULL RICH
c. Boost Pump Switch (if equipped)............... ON
d. Throttle........................................................ WIDE OPEN
e. Check for leaks in the following areas and correct any discrepancies before
releasing the engine for flight:
1) Induction System
2) Exhaust System
3) Fuel System
4) Lubrication System
f. Boost Pump................................................. OFF
g. Throttle........................................................ IDLE
h. Mixture........................................................ IDLE CUT-OFF
i. Master Power Switch .................................. OFF

Standard Practice Maintenance Manual 6-49
31 Jul 2017 CHANGE 4
Engine Inspection and Service
6-4.8.2. Oil Change
Perform an oil change within 30 minutes of engine shutdown (to obtain a useful oil
sample) according to the oil changes intervals specified in Section 6-2.
NOTE: More frequent oil changes are recommended under extreme usage
(flight training, shuttle service, or crop dusting) or adverse (desert or
arctic climates) weather conditions.
Procedure
1. Place a catch basin, approved for collecting oil, beneath the oil sump. Remove the
oil sump drain plug (Figure 6-7 through Figure 6-22), or quick drain fitting, and
drain the oil into the catch basin.
2. Collect an oil sample according to the “Oil Sample Collection” instructions in
Section 6-4.8.4. Inspect the oil sump drain plug for evidence of wear material. Metal
fragments on the drain plug may indicate excessive wear or part disintegration.
Evidence of bronze in the oil sump suggests piston pin bushing loss. Remove the
cylinders and inspect the piston pin bushings for proper installation according to
instructions in Section 10-10.
CAUTION: Dispose of used engine oil in accordance with local
environmental standards.
NOTE: Continental Motors recommends customers submit a sample of
the oil drained during each oil change, or if engine trouble is suspected,
for spectrographic oil analysis. The first three samples establish the oil
analysis trend baseline.
The amount of wear material present in new, rebuilt, or overhauled
engines is typically greater during the engine break-in period, tapering off
during subsequent oil changes. If the amount of wear material does not
decrease during subsequent oil changes, note the wear material
characteristics (refer to Section 6-4.8.5, “Oil Trend Monitoring and
Spectrographic Oil Analysis”) and troubleshoot the engine according to
instructions in Chapter 8.
3. Oil Filter or Integral Screen Change
Engines covered in this manual are equipped with either a screw-on, disposable oil
filter or an integral screen (Figure 6-23). Maintenance pertaining to the filter media
is listed in the “Engine Inspection and Maintenance Schedule” in Section 6-2. To
change disposable filters, follow the instructions in step a; for the integral screen,
follow the instructions in step b.
a. Remove the oil filter (Figure 6-8 through Figure 6-22).Cut the oil filter in two
parts using an Oil Filter Can Cutter (P/N CT-923 (Table 2-1, “Special Tools
List”)).
1) Inspect the oil filter element for metal debris trapped within the filter to
assess the engine condition. If debris is found, wash the filter media in a clean
glass container to determine content. Use a magnet to differentiate the ferrous
materials from non-ferrous particulate.

6-50 Standard Practice Maintenance Manual
CHANGE 4 31 Jul 2017
Engine Inspection and Service
2) New, rebuilt, or overhauled engines exhibit more wear material during the
break-in period; material found in the filter media will diminish over time. If
wear material in the oil filter does not diminish, or increases, note the
characteristics of the wear material (Section 6-4.8.5, “Oil Trend Monitoring
and Spectrographic Oil Analysis” ) and troubleshoot the engine according to
instructions in Chapter 8.
Figure 6-23. Disposable Oil Filter and Integral Screen
b. If the engine is equipped with an integral oil screen (Figure 6-23), cut the safety
wire from the oil screen and remove the fastening hardware. The integral screen
is not disposable, rinse the integral screen with mineral spirits over filter paper to
clean the media. Use a magnet to differentiate the ferrous materials from non-
ferrous particulate.
4. Install the oil filter or screen. For disposable filters, follow the instructions in step a;
for the integral screen, follow the instructions in step b.
NOTE: Spin-on oil filters are available with an anti-stick coating on the
gasket. Part numbers 658753, 658754, and 658755 oil filters feature a a
dry graphite coating and are designed to be installed dry. Before applying
any lubricant to the oil filter gasket, read the manufacturer’s instructions
(Figure 6-23.1) on the oil filter. Application of any form of lubricant to
the gasket of the anti-stick spin-on oil filter will defeat the anti-stick
properties.
a. Read the oil filter label to determine the gasket type and proceed with installation
according to the filter manufacturer’s instructions. Install the new oil filter;
torque the filter to Appendix B specifications and safety wire the filter according
to instructions in Appendix C-3.
b. After thorough cleaning, install a new copper gasket on the oil screen flange and
install the oil screen in the oil pump, or oil screen adapter. Place a new copper
gasket on the plug (or oil temperature sensor provided by aircraft manufacturer)
and thread the screen (or plug) into the housing. Torque to Appendix B
specifications and safety wire according to instructions in Appendix C-3.

Standard Practice Maintenance Manual 6-50.1
31 Jul 2017 CHANGE 4
Engine Inspection and Service
5. Reinstall the oil drain plug with a new crush washer (gasket) according to
instructions in Appendix C-10.1; torque the drain plug to Appendix B specifications
and safety wire the drain plug according to instructions in Appendix C-3.
6. Add fresh oil and check the oil level according to instructions in Section 6-4.8.1.
7. Check for oil leaks according to instructions in Section 6-4.8.3.
Figure 6-23.1. Oil Filter with Anti-Stick Gasket Label (typical)

6-50.2 Standard Practice Maintenance Manual
CHANGE 4 31 Jul 2017
Engine Inspection and Service
Intentionally Left Blank
This manual suits for next models
32
Table of contents
Other CONTINENTAL AIRCRAFT ENGINE Engine manuals
Popular Engine manuals by other brands
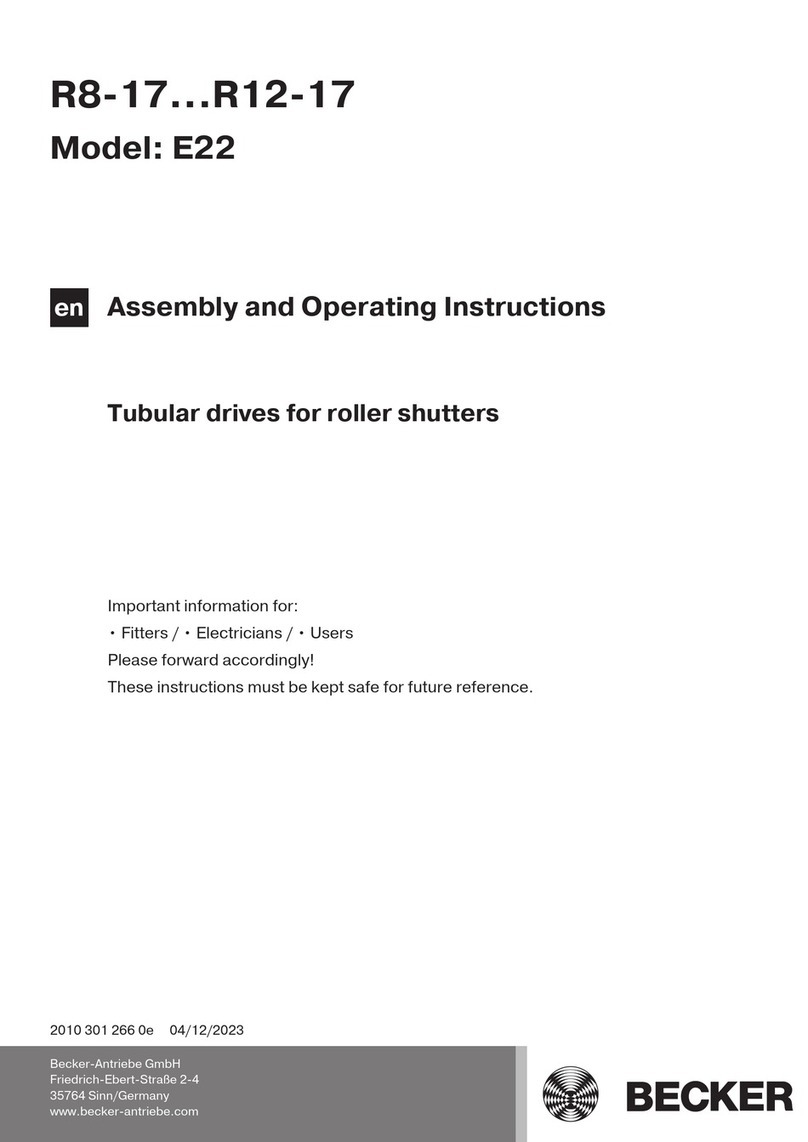
Becker
Becker R8-17-E22 Assembly and operating instructions
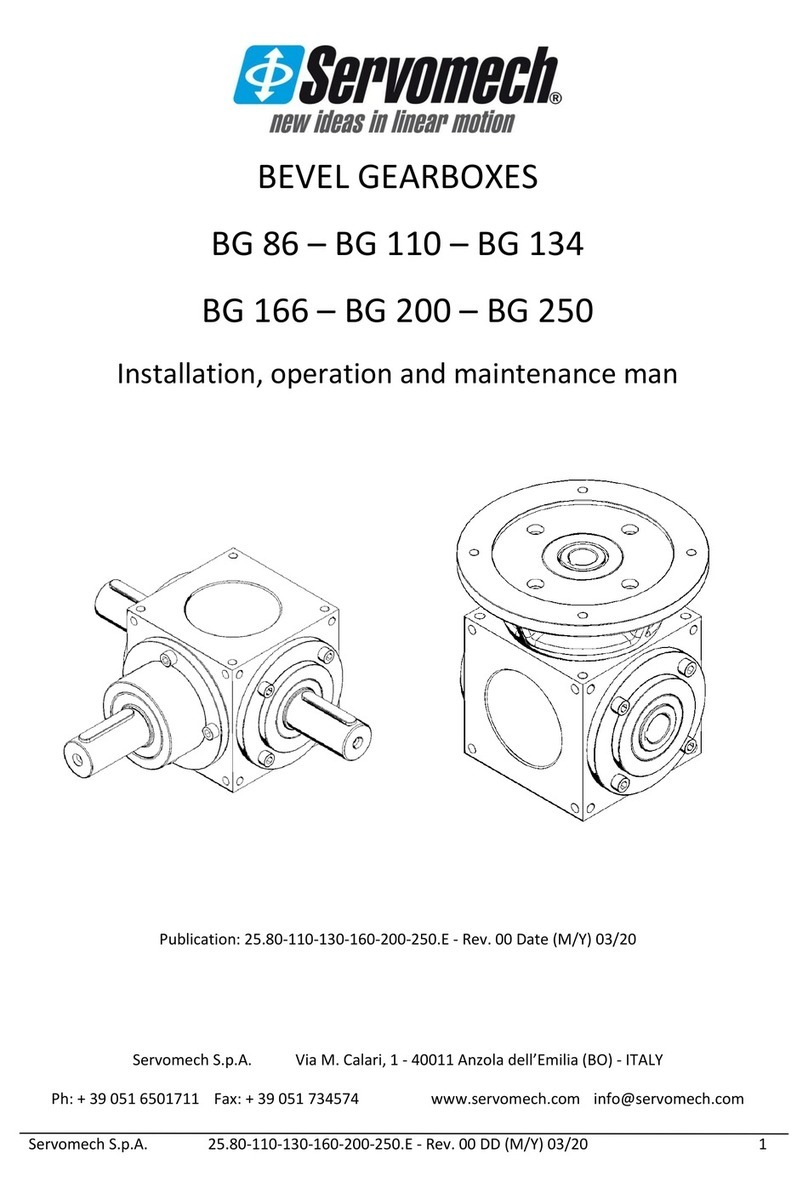
Servomech
Servomech BG 86 Installation, operation and maintenance manual
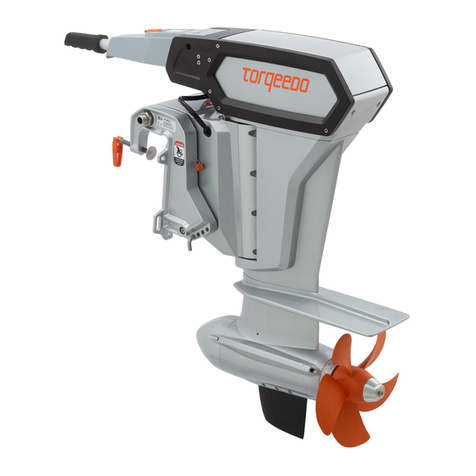
Torqeedo
Torqeedo Cruise 10.0 T Translation of the original operating instructions
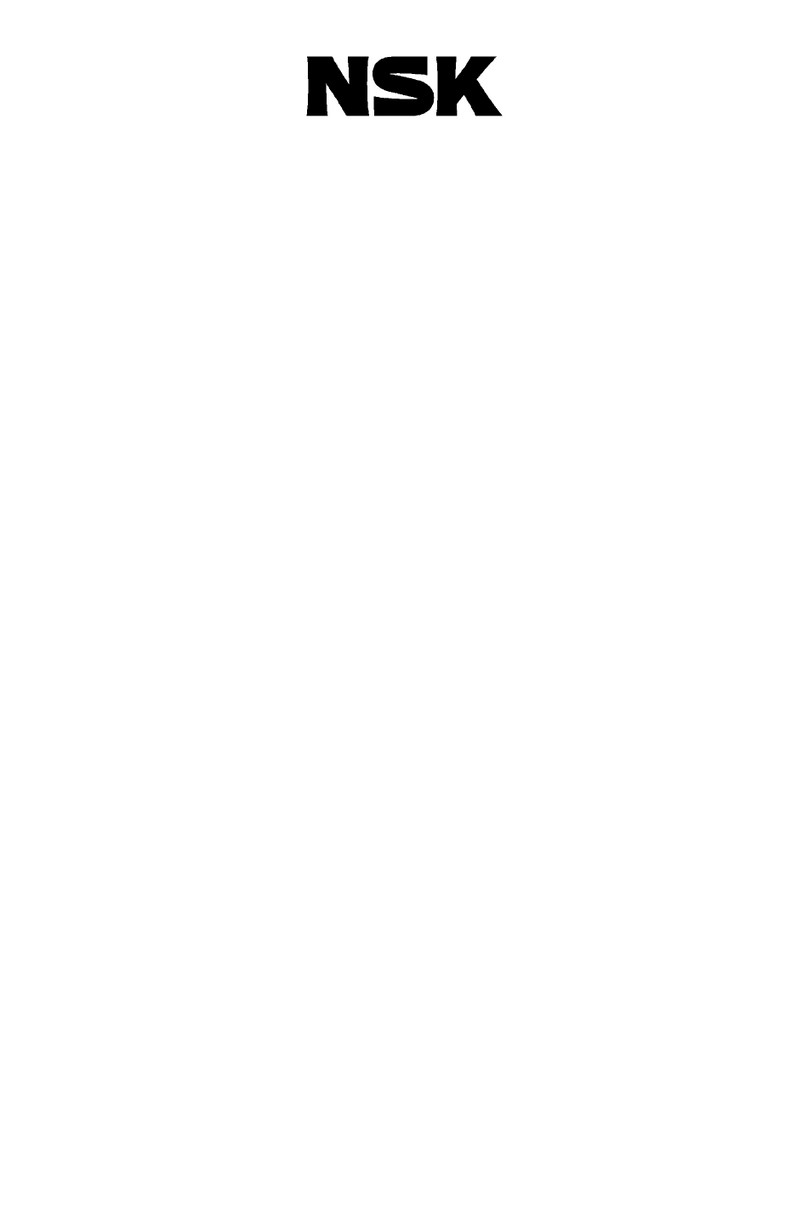
NSK
NSK Megatorque Motor EGA Startup guide
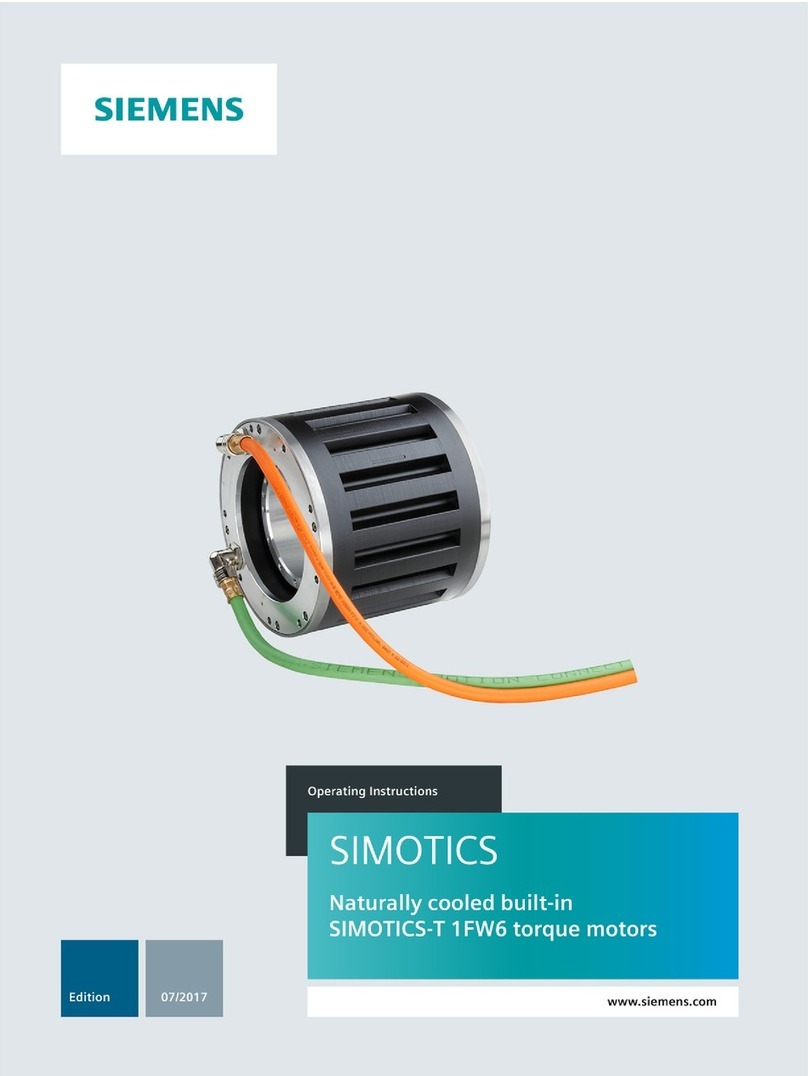
Siemens
Siemens SIMOTICS-T 1FW6053-B05-0F operating instructions
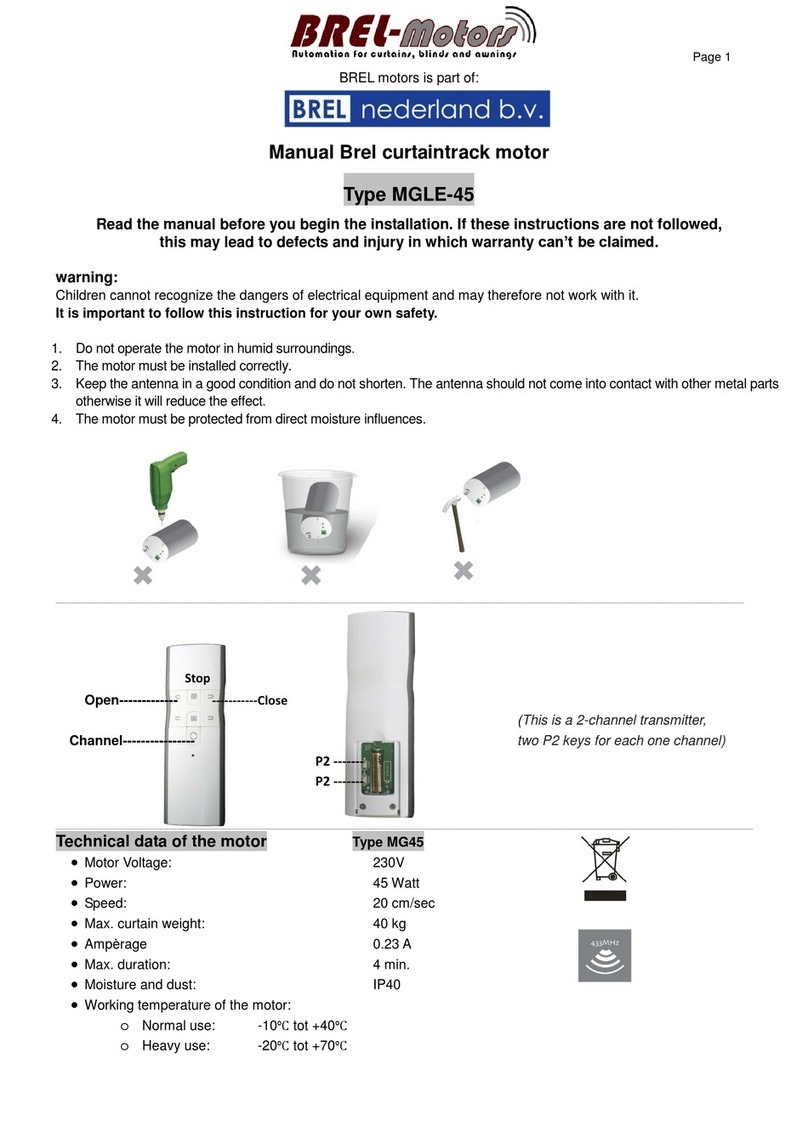
brel-motors
brel-motors MGLE-45 manual