Corsair M25Y User manual

INTRODUCTION
Thank you for choosing our engine the CORS-AIR M 25 Y We invite
you to spend some time reading this manual, which will let you discover
all the features of your engine Advices on maintenance and operation
will help you to have a reliable engine and to preserve your investment
Furthermore, we invite you to deliver this manual together with the
engine if you sell it, so it can be useful for the next owner as well The
manufacturer and the resellers are ready to answer your questions and,
if necessary, to solve every problem, because YOUR AND THE OTHER
PEOPLE’S SAFETY IS THE MOST IMPORTANT THING FOR US
IDENTIFICATION OF THE OWNER
Owner
Address
Serial number
Reseller
Address
Owner’s signature
Reseller’s signature and stamp
Date of sale
The Company reserves the right to make technical and aesthetic changes without notice in order to improve the quality of the
product

Cors-Air M25Y / Black Devil
TECHNICAL FEATURES
Cycle 2 strokes
Total displacement 172,5 c c
Bore 65 mm
Stroke 52 mm
Compression ratio
11:1
Peak rpm 7 500 rpm
Cooling by air
Piston of light alloy with 2 piston ring of cast iron S10 crominium-
plated
Cylinder Nickasil Coated
lining
Head of die-casted light alloy with high percentage of silicon
Crankcase molten in alloy G –Al Si 9 UNI 3051
Connecting rod of steel 18 Ni Cr Mo 5 forged and
copper- plated with rolls fit for
high speed
Carburettor diaphragm
Feeding reed valve with 4 petals on the crankcase
Electronic ignition type CDI (electric version) type TCI (manual version)
Regulation of spark advance 18° at 7000
rpm
Spark plug NGK B9ES
Reduction with belt Poly-V from 1 to 2 2 to 1 to 2 6
Cylinder head temperature max 200°C
Fuel mixture of premium petrol 98 octane and oil at 2%
Oil synthetic top-quality oil for 2-strokes engines
Expenditure from 2,5 to 4,5 liter/hour depending from the load and the speed
Fixing to the frame 5 rubber antivibration mounts
Rotation counterclockwise in front of the propeller

ASSEMBLY:
You can install the engine on the frame by using 4 rubber mounts of 40 mm
between the back flange and the engine mount It is PEREMPTORY to install also
the 5th rubber mount (20x30), fixing it in the proper hole located under the
reduction flange, through an angular square This device will permit to evenly
distribute the vibrations of the engine on every part of the frame
To attach the propeller use only bolts of class 10/8 (100 Kg) and make sure that
their length is enough to exit from the reductor-pulley Tighten the 6 bolts M8 in a
cross, at 1 5 Kg m (15Nm) Re-check the torque of the bolts after the first hour of
engine’s working
We suggest not to use a variable pitch carbon prop, because the big hub pushes the
prop too forward, with possible damages to pulley and bearings
For the connection between the carburetor and the fuel tank use a proper hose of
the right diameter (1,2 times the max expenditure per hour, that means sending 11
liters/hour) The length of the fuel line must not be more than 80 cm
It is advisable to install a manual primer bulb to get the fuel to the carburetor
before for starting This device will allow the fuel to arrive to the carburettor,
protecting in this way the battery
IMPORTANT NOTES
DO NOT try to start the engine without the propeller
DO NOT start the engine with loose bolts or parts, since this can cause the
detaching of the propeller, the ovalization of the propeller holes, the damage of the
electric start and the breakage of the rubber mounts
IMPORTANT! BEFORE FLYING CHECK ALWAYS EVERY PART OF YOUR
CRAFT, FROM ENGINE TO FRAME
Verify that there are no damaged electric wires, that there are no leaks from hoses,
tank, carburettor or engine’s crankcase, that the propeller is not damaged or loose,
that the exhaust-pipe has no cracks, that the frame is not bent or broken because of
falls, that rubber mounts are not cracked, that the reduction belt is not loose and
every bolt is tight Finally you can start the engine, leaving it to warm up at a speed
of 2 200 to 2 700 rpm with head temperature at least 120 °C
FUEL
Use for the mixture only premium gas for cars 98 octane, together with good-
quality, synthetic oil for mixtures at a quantity of 2% (DO NOT USE MIXTURE
MAIN TORQUES Kg m (Nm)
DECOMPRESSOR (only hand start version) 2,0 20
NUTS TO FIX THE HEAD 2,2 22
NUTS TO FIX HALF-CRANKCASE 2,5 25
BOLTS TO FIX THE BACK FLANGE TO THE CRANKCASE 2,0 20
NUTS TO FIX THE PINION TO THE FRONT PART OF THE DRIVE SHAFT 4,5 45
NUTS TO FIX BACK PART OF DRIVE SHAFT TO IGNITION HANDWHEEL (manual version) 3,5 35
NUTS TO FIX BACK PART OF DRIVE SHAFT TO IGNITION HANDWHEEL (electric version) 1,2 12
GAP BETWEEN COIL AND HANDWHEEL 0 4 mm

ALREADY DONE AT PETROL PUMPS) IMPORTANT: with very hot climate
and high temperatures use PERCENTAGE 2 2%
When you prepare the mixture, make sure that the can has not dirt or water in it,
put always the oil first and mix thoroughly
Never run the engine without the air-filter, because dirt and dust raised by the
propeller can damage it
ADJUSTMENT OF THE CARBURETTOR
The carburettor has two mixture adjustment screws, 1 marked L adjusting low
speed and 1 marked H for high speed
In order to make the adjustment, gently tighten clockwise then unscrew: L screw
from 3/4 (three quarter) to one turn, H screw from 1 1/4 (one and a quarter) to 1
1/2 (one and a half) turn -adjustment with filter Air Box (Kart model), we advise
this kind of air-filter- Furthermore, we advise to put a small security-cable on the
air filter, on the muffler, to avoid that it can come off, and on the three springs of
the exhaust These adjustments can be different on the basis of weather conditions
and flight altitudes Ideal mixture is reached when the insulator of the spark
plug is coffee brown; if the colour is black, the mixture is too rich, therefore turn
screw H clockwise 1/8 round per time If the spark plug is grey/white, the mixture
is lean, therefore turn screw H and L counterclockwise always 1/8 round per a
time Remember that if the mixture is too lean, THE PISTON CAN SEIZE You
can see better the colour of the spark plug by keeping the engine for 20 seconds at
maximum speed and switching it off suddenly without letting it slow down Once
you have found the perfect mixture do not change it unless you change flight place
or climate conditions, since register screws can be damaged by continuous
adjustments
RUNNING-IN
All CORS-AIR engines, before being delivered, are subject to a severe quality-
check, in order to verify if all the components respect the fixed parameters, but a
further running-in is anyway necessary A GOOD RUNNING-IN WILL
PROLONG THE LIFE OF YOUR ENGINE
Go to a quiet place, put a thick rubber carpet under your craft to avoid that stones
or other things damage the propeller by putting it on earth and let the engine work
at a speed of 2500 rpm for 5 minutes, then regulate speed at 3000/3500 rpm for 15
minutes, then at 4000 rpm for other 15 minutes Switch off the engine and check
that there are no loose nuts or bolts and that every component is ok BE
CAREFUL NOT TO TOUCH HOT PARTS (POWER UNIT AND EXHAUST
PIPE) Start the engine again and take it step by step to 4000 rpm for 5 minutes,
then accelerate to 4500 rpm for 15 minutes During the first 10 hours, do not
subject the engine to extreme efforts and speed Also during normal use eccessive
loads (ex tandems with passenger) can force the engine with possible damages to
the engine itself ALWAYS CHECK at sight your craft before and after every
flight, for loose parts or damage After each flight, in the version with
decompressor, clean the head from possible oil residues During the run-in period
vary the power often for a proper piston ring setting

MAINTENANCE
- Every 20 hours:
Check the condition and gap (0 7 mm) of the spark plug
Clean the air-filter, the carburettor filter placed at the end of the fuel pipe and the
filter of the fuel tank
Check the torque of every bolt
Tighten head nuts (in cross order) with a Torque Wrench at 2 2 Kg m (22Nm)
Check the tension and condition of the reduction belt
Check fuel lines
Check the wiring
Check that the cord of the starter has no abrasions
Grease the link-sphere between the manifold and the exhaust pipe with lubricating
copper-grease suitable for high temperature (up to 1100°) If you can’t find it on
the market , please ask to your dealer
- Every 50 hours
Same controls of the 20 hours and furthermore:
Check the torque of the engine’s crankcase nuts
Change spark plugs
Change the petals of the reed valve
Check the reduction belt and the play of the pulley and change them in case of
need
Check the conditions of the starter gears (version with electric start)
Once a year (independently from flight hours) change the diaphragm of the
carburettor
N B It is advisable to keep records of all maitenance in a log book for the engine It
is also advisable to install an instrument (CHT) to control the head temperature at
sight
TENSION OF THE REDUCTION BELT DRIVE - USE CAUTION
Attention: a belt which is “over tensioned” can do permanent damage to the
bearings inside of the pulley hubs and drive shaft Therefore we strongly suggest
for you to follow carefully these instructions
Before adjusting the belt take a felt pen or marker and make a small sign on the
cam shaft and on the front of the reduction plate This is your Zero or start point
and from here you will be able to clearly see how much you move the eccentric
tensioning cam in relation to the reduction plate Remember “these are Fine
adjustments” and we suggest not to rotate the cam any more than 1 mm per
adjustment After each adjustment you can try to start the engine and check the
result If the engine does not start well then it usually means the belt is still too
loose and is slipping - in this case repeat the operation by tensioning the belt
another 1 mm Consider that if the belt slips a little, but the engine still starts fine,
then the tension is correct Belt tension always increases automatically when the
engine is running because of thermal expansion in the pulleys Once you have
found the correct tension , do not adjust it any more In case of doubts please
contact your paramotor dealer – or JPX Italia

To adjust the belt do the following:
Loosen the safety bolt located high up behind the reduction mounting plate and the
side bolt Once these are loosened the you can turn the cam with a n 27 mm size
wrench - careful to observe the 1 mm increments Once you have finished turning
the cam remember to re-tighten the safety bolts, first the back bolt, by keeping
firm the cam with the wrench, and then the side bolt
IGNITION (ONLY FOR ENGINE WITH HAND START)
In case the coil and/or the handwheel must be changed, it is compulsory to turn to
your dealer or to trained personnel, even if this operation can appear simple at the
first sight, since the timing of the engine, if wrong, can change the performance
and cause damage to the engine To check the timing: the distance between the coil
and the flywheel magnet is 0,40 mm
STORAGE OF THE ENGINE FOR A LONG TIME
In case the engine is not used for a long time, act like this:
Empty the fuel tank, included the fuel lines and the carburetor
Disassemble the battery (version with electric start)
Unscrew the spark plug and pour into the hole a teaspoon of oil for engines, then
re-install the spark plug letting the propeller turn slowly by hand for 2 or 3 times
completely
Disassemble the propeller
Loosen the reduction belt
Plug the hole of the exhaust pipe
Cover everything with a blanket and put it in a dry place
Once a month charge the battery and let the pinion of the drive shaft turn by hand
2 or 3 times completely
WARRANTY
CORS-AIR engines are manufactured with top-quality material, therefore
warranty is valid also for their accessories
DURATION OF WARRANTY
1 YEAR beginning from the date of sell or exit from JPX ITALY
Warranty includes spare parts and labour, transport excluded
WARRANTY IS VOID IN THE FOLLOWING SITUATIONS:
- Alterations to the engine not approved by JPX Italia.
- Wear & tear of components of the engine due to the instructions within the product
manual not being adhered to.
- Accidental falls or dropping of the engine or its components.
- verheating and seizure of the engine due to prolonged high speed running of the
engine, running with excessive loads, running with inadequate loads, running with
insufficient oil in the petrol (for a wrong tuning of the carburettor) or running with
petrol only (oil mixture omitted).

- The presence of dirt, sand or foreign bodies in the carburettor of the engine.
- Corrosion through bad storage of the engine or inadequate preparation for storage of
the engine.
- Running the engine without an air-filter fitted to the carburettor.
- Miss-assembly of engine parts or components not assembled by JPX Italia but by the
manufacturer of the paramotor or by the end user, supplied disassembled for packing
and transport purposes.
- Corrosion of the engine or components emanating from stone chips or any other
impact or abnormal stress damage.
- Work other than the maintenance set out in the product manual having been carried
out on the engine by anyone other than JPX Italia or official dealers.
- Incidental or consequential loss or damage.
- Service bulletins from JPX Italia not having been adhered to.
- Engine used for racing use.
JPX ITALY AND ITS RESELLERS REMAIN AT YOUR DISPOSAL FOR
EVERY INFORMATION AND ADVICE ABOUT THE USE OF THE ENGINE
TROUBLE SHOOTING
THE ENGINE DOES NOT START
Check:
- switch on-off
- cable of the spark plug
- correct spark plug gap
- all the connections of the electric plant
- that fuel arrives correctly from the tank to the carburettor
FLOODED ENGINE
Dismantle the spark plug and dry it well ; before re-assembling it, let the propeller
turn slowly 2/3 times
THE ENGINE DOES NOT HOLD IDLE SPEED OR HAS AN IRREGULAR
SPEED
Clean and adjust the carburettor Check the reed valve petals are closing
completely Hold the reed up to a light and you should not see any light past the
petal seating area
THE ENGINE CANNOT REACH MAXIMUM SPEED
Check cable pulling throttle fully open
Check that there is no dirt in the carburettor or tank-filter nor restrictions in the
fuel pipe, due to too tight curves, or air bubbles
Check the spark plug; is it’s worn, change it with one of the same brand and same
heat range
In case the head is dismantled to be decarboned, change both the head gasket and
the cylinder gasket

THE DECOMPRESSOR REMAINS BLOCKED
Detach the gum tube on the decompressor and inject inside 1 or 2 drops of
detergent Detach the spark plug cap and let the prop turn If this is not enough,
disassemble the decompressor with a tube wrench of 15, modified in the external
diameter with a lathe Remove encrustments from the decompressor and by
reassembling it, tighten it at 2 Kg/M or 20 Nm with a dynamometric wrench
SOME FINAL IMPORTANT ADVICE
NEVER switch on the engine with people near propeller, or to sides The
BREAKAGE of a propeller can cause very severe hurts even several metres away
DO NOT keep engine at peak rpm after the take off, except for the absolutely
necessary time and for emergencies (obstacles or sudden wind)
If you use big propellers, REMEMBER that cooling is not perfect flying at high
speed, so keep under control the temperature of the engine with proper
instruments (CHT) In addition, dismantle the propeller at regular intervals and
check that it is perfectly balanced, since an unbalanced propeller, even slightly,
creates micro-vibrations which are not felt by the pilot, but can damage seriously
parts of the engine with consequent breakages Please do NOT forget that the
propeller has mass and a considerable inertial moment, so it’s advisable not to
vary suddently the RPM of the engine, both in flight and on the ground These
sharp and violent stresses could cause damages to the reduction, to the engine, to
the belt and also possible deformations to the fixing holes of the propeller
Once you have found the perfect carburation, DO NOT modify it unless you
change flying place going to much higher or lower altitudes or unless climate and
temperature are very different from the ones where you fly usually
DO NOT FLY in bad weather conditions, you’ll fly the day after REMEMBER:
FLIGHT IS FOR FUN, NOT FOR RISKING YOUR LIFE! HAVE A GOOD
FLIGHT AND ENJOY YOURSELF

1) HEAD
2) CYLINDER
3) PISTON COMPLETE OF PISTON-PIN AND LOCK
4) PISTON RINGS (N° 2 pcs together with the piston)
5) DRIVE SHAFT COMPLETE OF CONNECTING ROD
6) BEARING OF DRIVE SHAFT (n° Pcs 2)
7) HALF-CRANKCASE
8) HALF-CRANKCASE
9) TIE-ROD HEAD/CYLINDER (n° Pcs 4)
10) CRANCKASE STUD (n° Pcs 4)
11) GASKET OF THE HEAD
12) GASKET OF THE CYLINDER BED
13) JOINT DECOMPRESSOR WITH VALVE
14) DECOMPRESSOR
15) SEAL-RING OF DRIVE SHAFT (n° Pcs 2)
16) COVER OF BACK SUPPORT BASE
17) BACK SUPPORT BASE
18) STARTER
19) COUPLER FOR STARTER
20) HANDWHEEL
21) COIL
22) REED VALVE
23) FLANGE FOR CARBURETTOR BED
24) CARBUTETTOR
25) FLANGE AIR FILTER
26) ADJUSTER FOR ACCELERATOR WIRE
27) * PINION (50 or 52 2 mm)

28) * PULLEY (115 or 130 mm)
29) BEARING OF REDUCTION PULLEY (n° Pcs 2)
30) CAM OF THE PULLEY
N B BOLTS AND NUTS ARE NOT MENTIONED SINCE THEY ARE INCLUDED IN THE
PACKAGE OF THE SPARE PARTS
* FOR THE PIECES MARKED WITH AN ASTERISK PLEASE SPECIFY SIZE
PARTS FOR M25 BLACK DEVIL WITH ELECTRIC START
31) DRIVE SHAFT COMPLETE OF
CONNECTING ROD
32) ELECTRIC STARTER
33) FLANGE FOR ELECTRIC
STARTER
34) COVER OF BACK SUPPORT BASE
35) IGNITION
36) CHARGE REGULATOR
37) COIL
38) CROWN WHEEL COMPLETE OF
PINION
This manual suits for next models
2
Table of contents
Other Corsair Engine manuals
Popular Engine manuals by other brands
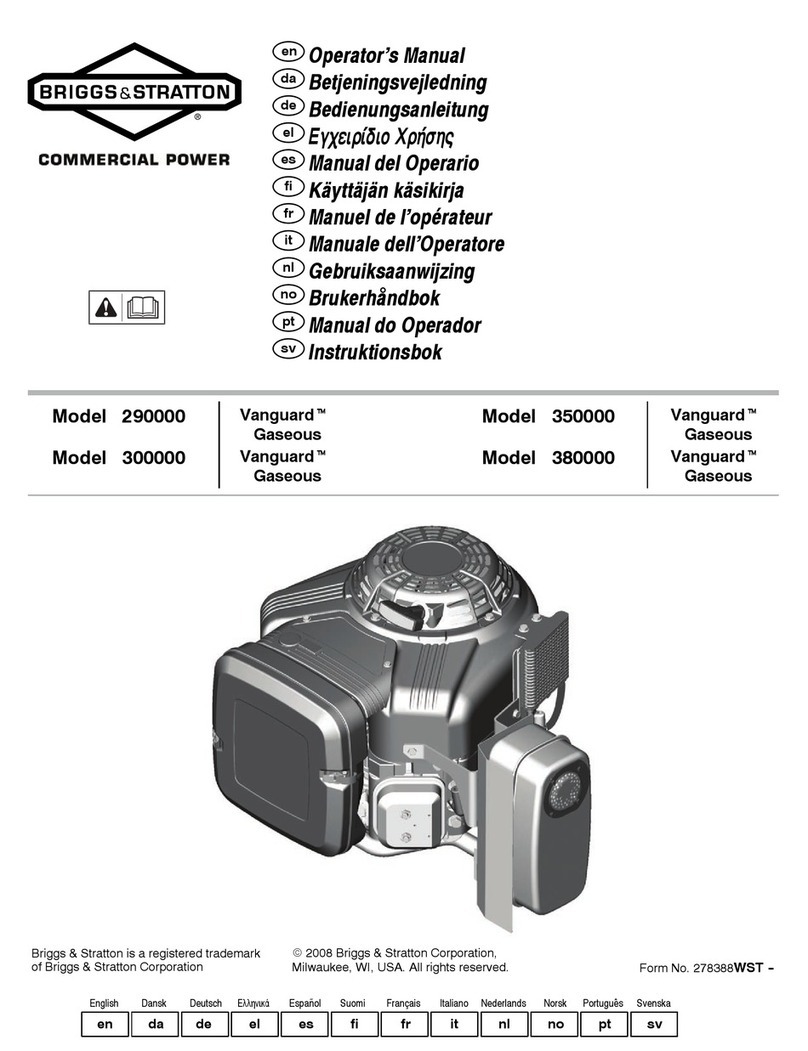
Briggs & Stratton
Briggs & Stratton Vanguard 290000 Operator's manual
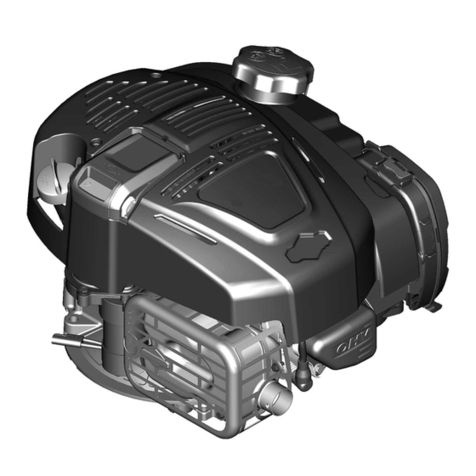
Briggs & Stratton
Briggs & Stratton 09000 Operator's manual
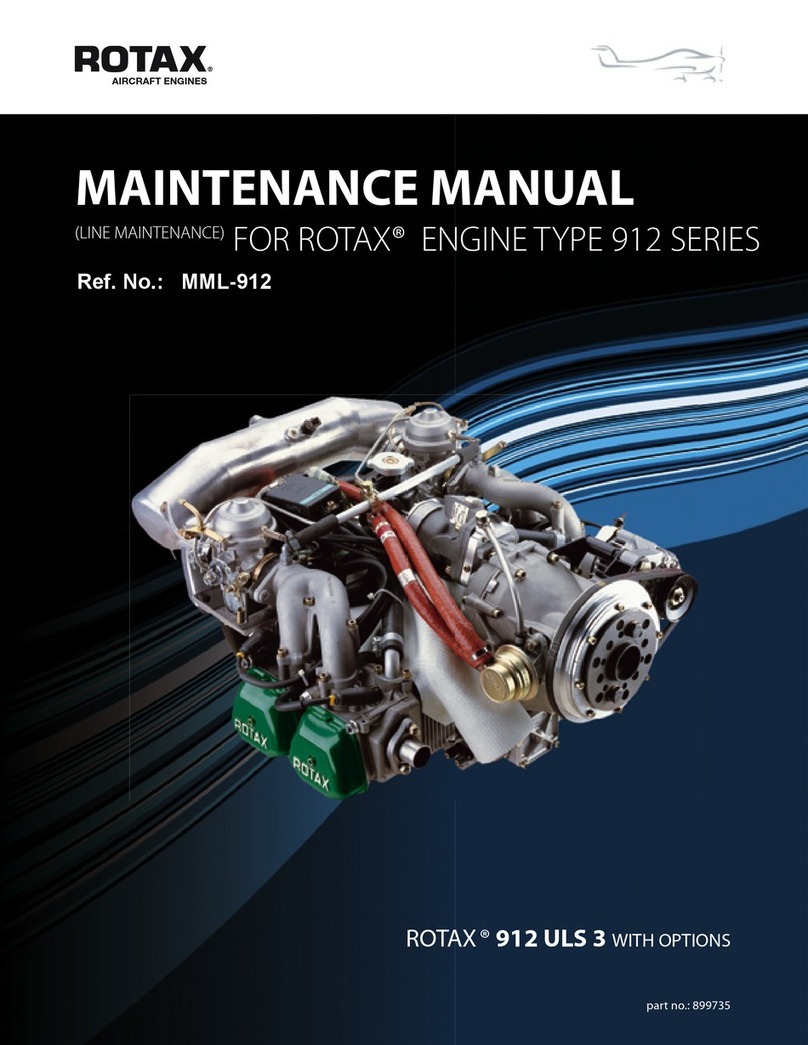
Rotax
Rotax MML-912 Maintenance manual
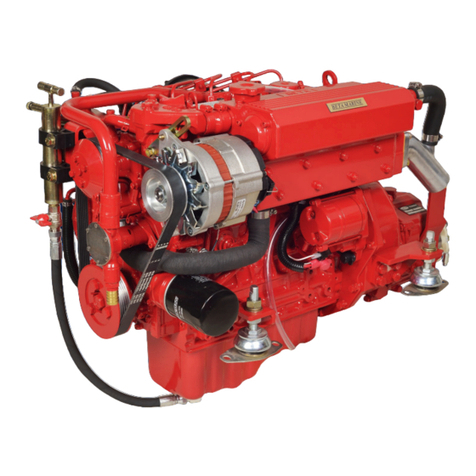
Beta Marine
Beta Marine Beta 14 installation guide
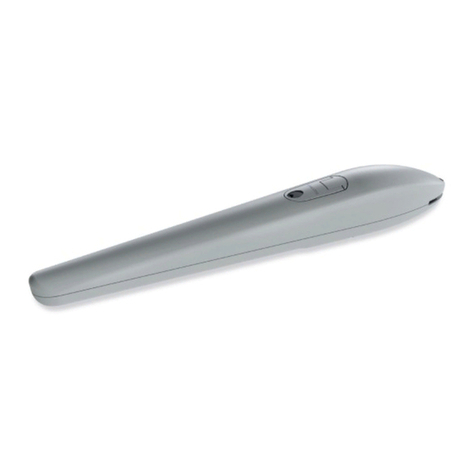
King gates
King gates Jet 230 F Installation and use instructions and warnings
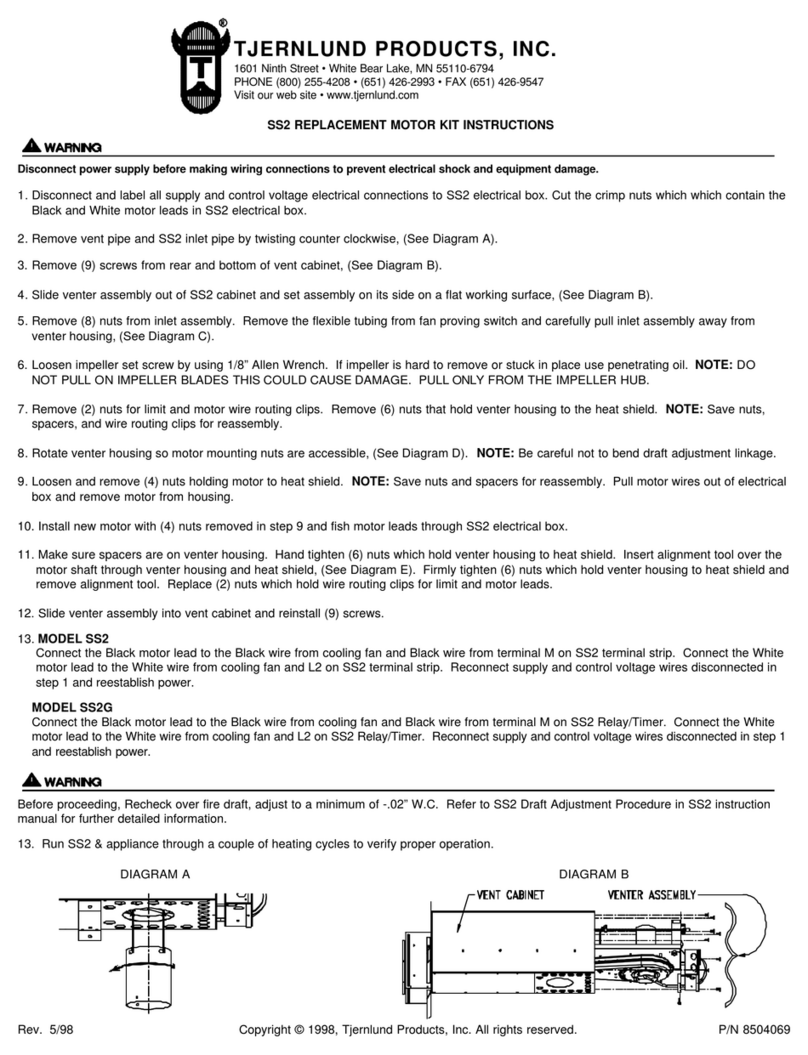
TJERNLUND
TJERNLUND SIDESHOT SS2 manual