coval LEMCOM User manual

1 1 (YE)
TX+
M8
2 3 (WH)
RX+
3 6 (BU)
RX-
4 2 (OG)
TX-
Shield
RJ45
Ethernet ports
(embedded switch)
1 (BR) 24 V DC
M8
2 (WH) NC*
3 (BU) GND
4 (BK) NC*
*NC: Not Connected
24 V DC
power supply
+
M8 COVAL bus
termination
Power supply Rear connector
1 (BR) 1
24 V DC
M8
2 (WH) 2
CAN_H
3 (BU) 3
GND
4 (BK) 4
CAN_L
M8
COVAL bus connectors
Fieldbus connectors
COVAL bus
(com + 24 V DC)
I
Consommation de courant d’un îlot LEMCOM / Current consumption of a LEMCOM island
Stromverbrauch einer LEMCOM-Inselanlage / Consumo di corrente di un’isola LEMCOM / Consumo de corriente de un grupo LEMCOM
Nombre de modules / Number of modules / Anzahl Module
Quantità moduli / Número de módulos 1 2 3 4 5 6 7 8 9 10 11 12 13 14 15 16
Consommation maximale de courant (mA) alimentation 24 V / Maximum
current draw (mA) 24 V supply / Max. Stromaufnahme (mA), bei 24 V /
Consumo massimo di corrente (mA) alimentazione 24 V / Consumo
eléctrico máximo (mA) alimentación 24 V
150 250 350 450 550 650 750 850 950 1050 1150 1250 1350 1450 1550 1650
B
Quick Start Guide
v04 - 03/2020
A
ZA des Petits Champs 26120 Montélier France
Tel : +33 (0)4 75 59 91 91 - www.coval.com
LEMCOM modules
QSG EIP LEMCOM EN (v04-2020) - 1 -
I - ELECTRICAL CONNECTIONS
A- Wiring instructions
Factory fieldbus (EtherNet/IP™) is connected to one of the 2 ports of the embedded Ethernet
switch (shielded M8/RJ45 cable).
Connect the “COVAL bus” using the provided bridge connectors or M8/M8 female cable for re-
mote modules.
24V DC power supply is connected to the rear connector of the last secondary module of the
island (or to the rear connector of master module if used as standalone LEMCOM) through the
COVAL bus termination cable.
Standalone secondary module or “Secondary only” island?
Refer to chapter VI for wiring and initial setup.
The LEMCOM vacuum pump must be used with power supply units that provide
a Protective Extra Low Voltage (PELV) and with an isolation of the supply voltage
according to EN60204.
This guide provides first-time users with information on wiring the different modules of a
LEMCOM island and on setting up the LEMCOM.
EN
B- Consumption
The LEMCOM structure implies that all vacuum generators connected together on the COVAL
bus are electrically supplied by the same power source. The consumption table(left) must be fol-
lowed when calculating the required power supply voltage and amperage.

BUS BUS
BUS
COVAL Bus
COVAL Bus
BUS
- LEMCOMs
- …
24V DC
LEMC--X---Y2GLEMC--X---Y2GB6
LEMC--X---Y2G3x LEMC--X---Z2GB3 LEMC--X---Z2G
II
➍ ➎ ➏
➊ ➋ ➌
LEMCOM Quick Start Guide
QSG EIP LEMCOM EN (v04-2020) - 2 -
II - CONFIGURATIONS AND ACCESSORIES
LEMCOM is based on an innovative product architecture:
The master module manages the fieldbus communication, handles secondary module man-
agement and is a complete vacuum pump. Its two communication ports ensure the continuity
of the fieldbus.
The secondary modules are interconnected with the master module via the COVAL bus.
The link between the master module and the secondary modules is handled by an M8 bridge
connector for island configurations or by a standard M8/M8 cable for configurations using re-
mote modules.
➊Cat 5 shielded Ethernet cable: M8, straight, female, 4-pin – RJ45, straight, male, 8-pin –
suitable for drag chain use
CDM8RJ45L2: length 2 m.
CDM8RJ45L5: length 5 m.
CDM8RJ45L10: length 10 m.
➋Cat 5 shielded Ethernet cable: M8, straight, female, 4-pin, on both ends – suitable for
drag chain use
80003053: length 1 m.
➌“COVAL bus” bridge connector
80001231
➍120 Ω“COVAL bus” termination: M8, straight, female, 4-pin – M8, plug, male, 4-pin
80002303: length 0.2 m.
The COVAL bus is based on a CAN architecture and requires
the addition of a bus termination to ensure proper communi-
cation between the secondary and master modules.
It takes the form of an M8 male/M8 female cable that includes a 120 Ωline termination
resistor.
It must be integrated on the last secondary of the COVAL bus, between the module’s rear con-
nector and the 24 V DC power supply.
When using a stand-alone master module, this termination is not required.
➎Power supply cable: M8, straight, female, 4-pin – open end
CDM8: length 2 m.
CDM8N: length 0.5 m.
➏M8/M8 “COVAL bus” cable: M8, straight, female, 4-pin – M8, straight, female, 4-pin
CDM8FFL05: length 0.5 m.
CDM8FFL1: length 1 m.
CDM8FFL2: length 2 m.
CDM8FFL4: length 4 m.
Other lengths available upon request.
One “master” module controls up to 15 secondary modules.

III RJ45/M8
cable
M8 COVAL bus
termination
24 V DC
power supply
1
2-1 2-2
v2.1.7
3-1 3-33-2
LEMCOM Quick Start Guide
QSG EIP LEMCOM EN (v04-2020) - 3 -
III- IP SETUP INSTRUCTIONS
1- Plug the power supply to the last secondary module or to the rear connector of the master
module (if standalone LEMCOM). Set up a direct cable connection between the LEMCOM mod-
ule and a computer using an M8/RJ45 cable.
2- Set the computer’s IP address to: 10.3.182.10
2-1 Control panel > Network and internet > Network Connections.
Ethernet > Properties
2-2 IP address: 10.3.182.10
The computer and the LEMCOM module must be on the same network.
The IP address of the LEMCOM master module is factory set to 10.3.182.163.
In order to use the LEMCOM, its IP address must be set up according to your net-
work configuration.
3- Download and start LEMCOM Manager software
Download it from the COVAL website:
https://doc.coval.com/lemcom/
3-1 Select Configuration Mode.
3-2 Enter password “coval”, select “EtherNet/IP”, then click OK.
3-3 Default IP address 10.3.182.163 is automatically selected. Click OK to connect to the LEMCOM
module.

LEMC60X…
60% max. vacuum
LEMC90X…
90% max. vacuum
L1/h1 35 % / 10% 65 % / 10%
L2/h2 45 % / 10% 75 % / 10%
Auto-blow OFF
Auto-blow duration 500 ms
ASC ON
DIAG ECO ON
Maximum number of bounces 2
DIAG ECO analysis time(s) 1
Custom LED mode BL1
Valve status mode MD1
IV
4-1
4-2
SET
button
MS
led
LEMCOM Quick Start Guide
QSG EIP LEMCOM EN (v04-2020) - 4 -
4- Replace the default IP address by the one that will be used on your factory network.
4-1 Open the network settings screen by clicking on .
4-2 Set IP address, subnet mask and default gateway.
Click OK. The module restarts with the new settings.
Back to default IP address
To reinitialize the IP address to the default IP 10.3.182.163, please follow these steps:
5-1 Unplug the power cable
5-2 Press and hold the “SET” button on the master module
5-3 Plug the power cable back in
5-4 Release the button when MS LED starts flashing (green).
IP address is now 10.3.182.163.
INCORRECT SETTINGS INDICATION
If the recommendations provided above are not observed when configuring a LEMCOM
module, the MS LED of the corresponding module will flash in red.
IV- FACTORY SETTINGS
The LEMCOM provided to you has been configured with default settings that suit most appli-
cations. Depending on the chosen model (LEMC60X or LEMC90X), the LEMCOM module is
configured as shown opposite.
Recommendations
Default vacuum parameters may need to be adjusted to perfectly suit the requirements of your
application. If this is the case, we recommend observing the following conditions:
L2-h2 > L1 regulation zone should be above the “object gripped” threshold
h1<L1 hysteresis should be lower than “object gripped” threshold
h2<L2 hysteresis should be lower than “regulation” threshold
In case of rough or porous product handling, disable ASC to avoid vacuum pilot from turning
ON and OFF frequently.

V
LEMCOM master LEMCOM secondary module
O1 O1
SET SET
Gv Gv
G1 G1
MS MS
B1 B1
G2 G2
NS NS
O2
O3
LEMCOM Quick Start Guide
QSG EIP LEMCOM EN (v04-2020) - 5 -
V- FRONT PANEL INDICATOR
Colors: Ox (Orange) - Gx (Green) - Bx (Blue) - MS, NS (Red/Green).
Ref. Related to Meaning
O1 Parts
handling ON: Blow-off command enabled / otherwise OFF
G1 Parts
handling ON: vacuum is generated / otherwise OFF
Gv Parts
handling
Gv provides an indication of the vacuum valve status:
If Normally Closed (NC) valve Gv behaves as G1
If Normally Open (NO) valve Gv OFF: vacuum is generated / otherwise
ON
G2 Parts
handling ON: Object gripped signal (vacuum level > L1 threshold) / otherwise OFF
B1 Custom
led
LED configurable according to customer requirements (refer to main user
manual / section 4.1 for detailed meaning)
MS Module
Status
Indicates the current status of the device (refer to main user manual /
section 4.2 for detailed meaning)
NS Network
Status
Indicates the current status of the EtherNet/IP or COVAL bus network
interface (refer to main user manual / section 4.3 for detailed meaning).
O2/O3 Ethernet
network
Ethernet link / activity - Left Port (02), Right Port (03)
OFF : No network connection
Steady ON: Network connection OK but no activity
Blinking: Network connection is OK and activity
SET Setting
button
Master module: IP address reset
Secondary module: COVAL bus address assignment and reset

COVAL Bus
BUS
24 V CC
BUS
VI 1
STANDALONE
MASTER
STANDALONE
SECONDARY MODULE
SECONDARY MODULES
ISLAND
MASTER
L1: 65 h1: 10
L2: 75 h2: 10
SF AUTO 1500
ASC DIAG/E
MODULES
2 3
45
LEMCOM Quick Start Guide
QSG EIP LEMCOM EN (v04-2020) - 6 -
VI- COVAL BUS ADDRESS ASSIGNMENT
Standalone secondary module or modules of a “secondary only” island are factory set to address
#16 to avoid any address conflict.
User must assign a valid and unique address (#1 to #15) to each secondary module to
make them “visible” on the COVAL bus. LEMCOM Manager software or web server can be used
to complete this operation.
1- Wire the modules.
Connect secondary module(s) to the master LEMCOM module using M8/M8 female cables.
2- Connect to the master module using LEMCOM Manager software.
Default password: coval
3- Assign an address.
Click on the button of the first blank slot, then click OK.
4- Follow the instructions.
5- Repeat these steps with a different address for each secondary module that is to be add-
ed to the COVAL bus.
NOTES
-Press and hold SET button (on a secondary module) during power-up to reinitialize its
address to #16 (release the button when MS LED starts flashing).
-Access to “Configuration Mode” in LEMCOM Manager is password-protected. Default
password is : coval

VII
LEMCOM Quick Start Guide
1
2-1 2-2
3
Property Description
Vendor name COVAL
Vendor ID 1350D
Device type 43D
Product name COVAL LemCom E/IP
Catalog ID LEMCOM
Request Packet Interval (RPI) ≥5 ms
Assembly
instance Type
Data
size
(bytes)
Description
101 INPUT 3 Gripping status (2 bytes)
Heartbeat (1 byte)
102 INPUT 19
Gripping status (2 bytes)
Heartbeat (1 byte)
Vacuumlevel (16 bytes)
140 INPUT 34
Heartbeat (1 byte)
Unused (1 byte)
Island composition (2 bytes)
Gripped information (2 bytes)
Regulation information (2 bytes)
Vacuumlevel-% vacuum (16 bytes)
Lost part alarm (2 bytes)
Regulation error alarm (2 bytes)
30MCycles alarm (2 bytes)
Temperature alarm (2 bytes)
Powersupply alarm (2 bytes)
141 INPUT 78
Heartbeat (1 byte)
Selected module in instance (1 byte)
Island composition (2 bytes)
Gripped information (2 bytes)
Regulation information (2 bytes)
Vacuumlevel-% vacuum (16 bytes)
Lost part alarm (2 bytes)
Regulation error alarm (2 bytes)
30MCycles alarm (2 bytes)
Temperature alarm (2 bytes)
Powersupply alarm (2 bytes)
---------------------------------------
Counter-external vacuum cmd (4 bytes)
Counter-internal vacuum cmd (4 bytes)
Counter-blow off cmd (4 bytes)
Counter-Handled parts (4 bytes)
Counter-Lost parts (4 bytes)
Counter-ASC regulation (4 bytes)
Counter-Regulation errors (4 bytes)
Counter-Local bus com error (4 bytes)
Counter-Field bus com error (4 bytes)
Counter-Power supply error (4 bytes)
Power supply (2 bytes)
Temperature (2 bytes)
Assembly
instance Type
Data
size
(bytes)
Description
100 OUTPUT 4 Vacuum control (2 bytes)
Blow-off control (2 bytes)
110 OUTPUT 6
Vacuum control (2 bytes)
Blow-off control (2 bytes)
Island restart (1 byte)
Unused (1 byte)
111 OUTPUT 6
Vacuum control (2 bytes)
Blow-off control (2 bytes)
Island restart (1 byte)
Module selection for diagnostic (1 byte)
112 OUTPUT 74
Vacuum control (2 bytes)
Blow-off control (2 bytes)
Island restart (1 byte)
Settings modification allowed (1 byte)
L1 threshold (16 bytes)
h1 threshold (16 bytes)
L2 threshold (16 bytes)
h2 threshold (16 bytes)
ASC option (2 bytes)
DIAG_ECO option (2 bytes)
Assembly
instance Type
Data
size
(bytes)
Description
160 CONFIG 166
L1 threshold (16 bytes)
h1 threshold (16 bytes)
L2 threshold (16 bytes)
h2 threshold (16 bytes)
ASC option (2 bytes)
DIAG_ECO option (2 bytes)
Max. bounces Nb (16 bytes)
DIAG_ECO analysis time (16 bytes)
Auto blow (2 bytes)
Auto blow duration (32 bytes)
Valves status (16 bytes)
Custom led mode (16 bytes)
QSG EIP LEMCOM EN (v04-2020) - 7 -
VII- EtherNet/IP™ communication
Please refer to the main user manual (ref. LMEIP-UK-x-1155UM0067) for detailed set-
up instructions, data mapping and general recommendations.
1- LEMCOM general properties
With respect to the EtherNet/IP network, the LEMCOM master module is an EtherNet/IP
adapter.
It receives implicit communication connection requests from an I/O scanner (the Programmable
Logic Controller) then produces or consumes its I/O data based on a Requested Packet Inter-
val (RPI) value.
2- I/O assembly instances
Input and output data refer to the master module and to the secondary modules that may be as-
sociated with it.
As an example:
“Vacuum Control” output data consists of 2 bytes and each bit toggles the vacuum of LEMCOM
module #0 (master) to #15 (last secondary).
“Vacuum level” input data consists of 16 bytes and each byte represents the instant vacuum
level (%) of LEMCOM module #0 to #15.
For best performance and sufficient diagnostic data, we recommended using I/O assembly
instances 140 and 110.
2-1 Input instances (Target > Originator)
Data sent from the LEMCOM island to the controller every ‘RPI’ ms.
Note: Input instance 141 is designed to be used with output instance 111.
2-2 Output instances (Originator > Target)
Data sent from the controller to the LEMCOM island every ‘RPI’ ms.
In this assembly, the first bit of byte 5 allows or rejects the modification of the LEMCOM module’s
settings. When it is enabled, the parameters data set defined in bytes 6 to 73 are automatically
sent to the LEMCOM master module every ‘RPI’ ms.
We highly recommend setting the “settings modification allowed” bit to ‘0’ in the PLC’s pro-
gram and only toggling it to ‘1’ when new settings must be applied.
3- Configuration instance
The configuration assembly instance 160 is used to transfer the vacuum settings to all LEMCOM
modules of an island (1 to 16 modules). The parameters are sent by the PLC to the master LEM-
COM module when the EtherNet/IP communication is established.
Please note that, unlike LEMCOM Manager, which warns the user in case of incorrect parame-
ters, the configuration assembly lets the user send any settings.This may lead to the appearance
of warnings on the module’s front panels (for example: threshold or hysteresis set to 0).
The output instance 112 is designed for specific applications that need to edit the
LEMCOM module’s parameters directly from the PLC or an EtherNet/IP HMI. It must
be used with special care.
If the configuration instance is used, please note that any modifications made to the
settings using LEMCOM Manager will be overwritten by the data of instance 160 the
next time communication is reset.

VIII A 1-1
1-2
1-3
LEMCOM Quick Start Guide
QSG EIP LEMCOM EN (v04-2020) - 8 -
VIII - CONNECTING TO AN ALLEN BRADLEY PLC
Below you will find two methods used to quickly configure an Allen Bradley controller using
RSLogix5000.
A - Setup using LEMCOM
Electronic Data Sheet (EDS)
Installing a LEMCOM EDS file for the EtherNet/IP Module to be identified by Rockwell’s RSLinx
software makes programming easier, since the EDS file describes the objects, attributes and ser-
vices available in the device.
1- Install Electronic Data Sheet & create a New Module
Download the EDS from the COVAL website:
https://doc.coval.com/lemcom/
1-1 In RSLogix5000, go to Tools > EDS Hardware Installation Tool and follow the instructions
to import the EDS.
1-2 After defining the controller, right click on the “Ethernet” node below “I/O Configuration” and
select “New Module…”. Type “LEMCOM” in the filter box of the catalog, select the item
that shows up and click on “Create”. The window for defining a new module is displayed.
1-3 Fill in the Module properties (Name / Description / IP Address) and the connection settings
(I/O assembly instances) according to your needs.

2-1 2-2
B 1-1
1-2
LEMCOM Quick Start Guide
QSG EIP LEMCOM EN (v04-2020) - 9 -
2- Access LEMCOM I/O Data and write the PLC program
2-1 All Input/Output tags are automatically created and are visible in the Controller Tags win-
dow of RSLogix5000.
2-2 Write the PLC program that controls vacuum and blow-off, collects gripping status informa-
tion, instant vacuum level and more.
B - Manual setup using Generic Ethernet Module
Connection settings can be manually defined in RSLogix5000 or any other controller/robot soft-
ware using a Generic Ethernet Device.
1-1 Add a new Generic Ethernet Module to your project.
1-2 Give a name & description to the module, select the Comm Format SINT, enter LEMCOM’s IP
address and based on the tables of I/O assembly instances provided above, fill in the con-
nection parameters.
1-3 New I/O tags are created in the Controller Tags window of RSLogix5000. Refer to the main
user manual for detailed I/O mapping.

IX A
1 2
3Vacuum
level 0
%
Vacuum counter:
02 562 936
Gripping counter:
00 000 436
Blow off counter:
02 562 302
ASC counter:
00 000 206
External vacuum ctr: 02 562 392
Lost parts: 00 000 202
ASC errors: 00 000 037
Power errors: 00 004 460
Com. errors (local): 00 000 000
Com. errors (bus): 00 000 069
DIAGNOSTIC MASTER Reference:
LEMC90X14SY2GB
Serial number:
1604234
Firmware version:
01.00
Grip
ASC
Power supply:
23.2V
B
LEMCOM Quick Start Guide
QSG EIP LEMCOM EN (v04-2020) - 10 -
B- LEMCOM Webserver
Embedded web server enabling configuration, update, control and diagnosis of any given
LEMCOM island.
No software installation required.
NOTE: all configuration and diagnostic data are also accessible through EtherNet/IP. A dedicated
HMI can be developed by controls engineers to give access to LEMCOM settings, counters,
alarms, etc. by reading / writing I/O data.
These configuration tools must not be used during production as unexpected
hazardous motion of machinery may occur.
Download the latest versions of the Operating instructions, User Manual, Quick Start Guide,
LEMCOM Manager software and firmware updates from the COVAL website.
https://doc.coval.com/lemcom/
Do not forget to subscribe to our LEMCOM Technical Newsletter to stay informed about
new features, firmware updates, tutorials, etc.
https://www.coval-international.com/products/mini-vacuum-pumps-
with-fieldbus-communication-lemcom-series-3439.htm
IX- Configuration & diagnostics tools
LEMCOM modules can easily be configured, updated, controlled and diagnosed remotely using
one of the following tools. This flexibility enables LEMCOM users to adapt their modules to any
type of application without needing to perform any operations directly on the vacuum generators.
A- LEMCOM Manager
LEMCOM Manager is an easy-to-use configuration software for LEMCOM vacuum pumps. It al-
lows LEMCOM users to quickly:
- 1- Set vacuum parameters (Air Saving Control, regulation and gripping threshold, etc.)
- 2- Set network settings
- 3- Monitor vacuum, blow-off and gripping cycles, error counters, etc.
- Add, remove or replace secondary module(s) on the COVAL bus
- Import/export settings of a single unit or the whole island
- Export diagnostics data for COVAL technical support
- Update the firmware of master and secondary modules
- And more…
Communication between LEMCOM Manager and the EtherNet/IP™ master LEMCOM module is
based on a standard TCP/IP connection (TCP port 65000).
© COVAL - v4 - 03/2020 - The diagrams are not contractual.
COVAL may modify the product range and product characteristics without prior notice.
Table of contents
Popular Control Unit manuals by other brands

GEM
GEM R639 operating instructions
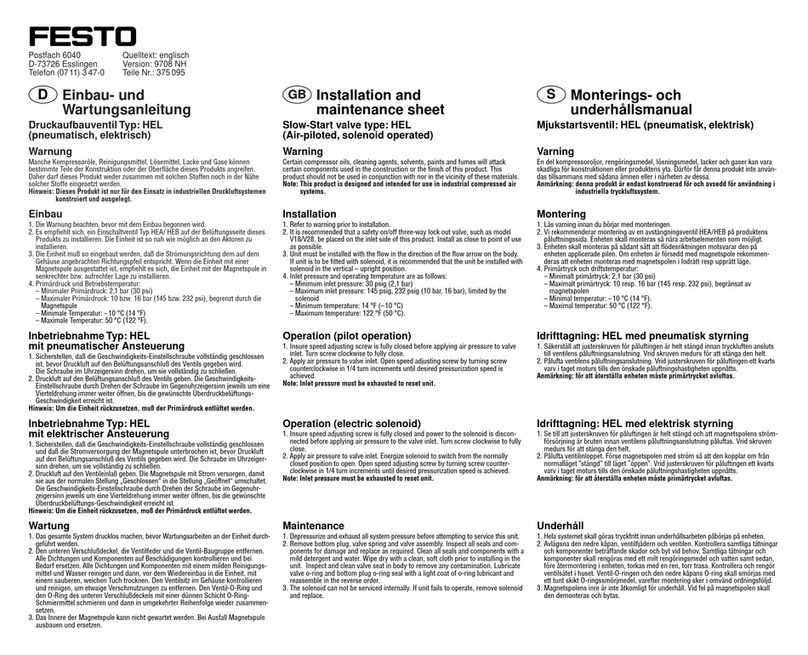
Festo
Festo HEL Series Installation and maintenance sheet
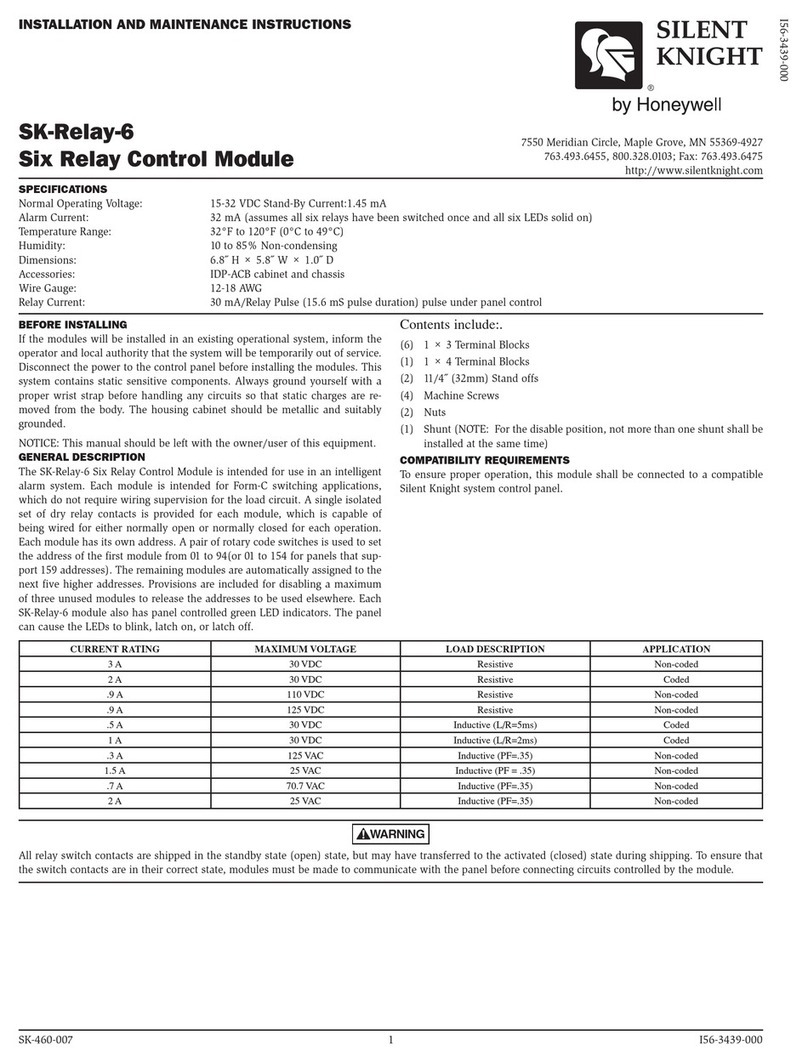
Honeywell
Honeywell Silent Knight SK-Relay-6 Installation and maintenance instructions

Dover
Dover PSG BLACKMER AIR VALVE Installation, operation and maintenance instructions

Ebyte
Ebyte AM22-12W2405V manual
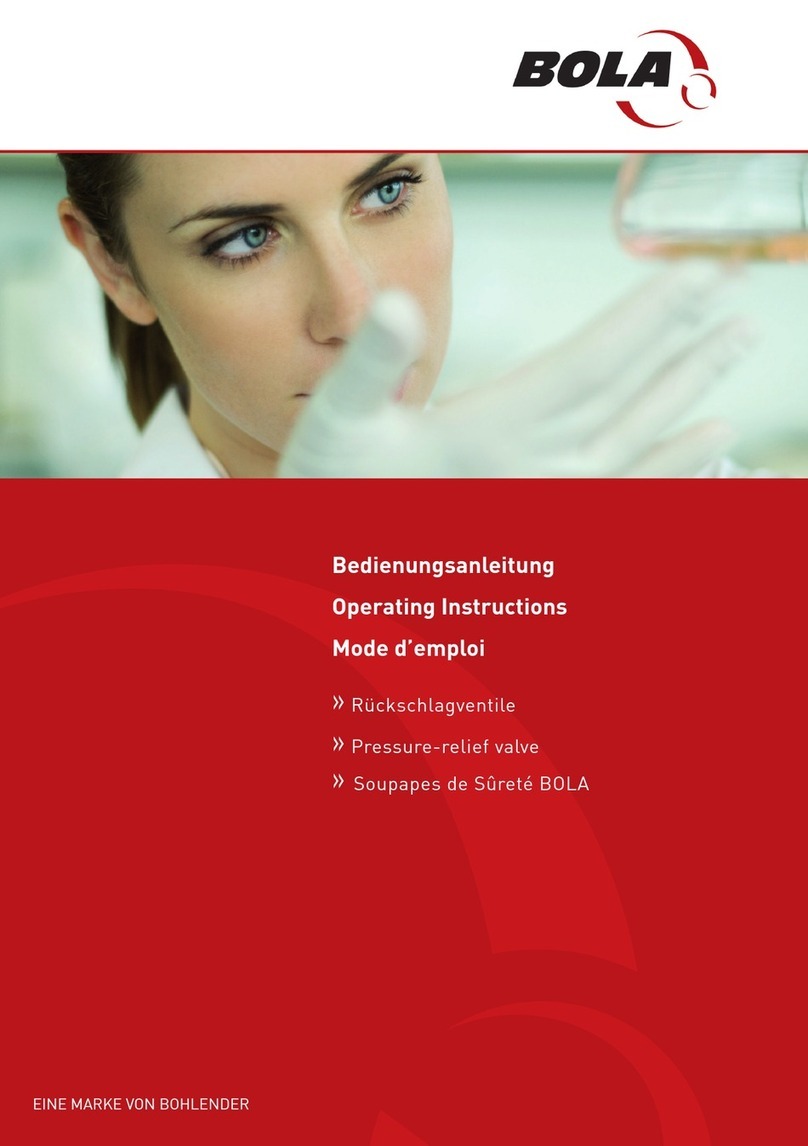
Bola
Bola E 680-21 operating instructions