dacell AM-1000 User manual

MODEL : AM-1000
DYNAMIC STRAIN AMPLIFIER
USER’S MANUAL
DACELL CO.,LTD.
Address: 681-1, Cheoksan-Ri, Nami-Myeon, Cheongweon-Gun,
Chung-Buk, 363-810 Korea
TEL: 82-43-260-2242
FAX: 82-43-260-2245
http://www.dacell.com
E-Mail: [email protected]

1
CONTENTS
1. FOREWORD ⋅⋅⋅⋅⋅⋅⋅⋅⋅⋅⋅⋅⋅⋅⋅⋅⋅⋅⋅⋅⋅⋅⋅⋅⋅⋅⋅⋅⋅⋅⋅⋅⋅⋅⋅⋅⋅⋅⋅⋅⋅⋅⋅⋅⋅⋅⋅⋅⋅⋅⋅⋅⋅⋅⋅⋅⋅⋅⋅⋅⋅⋅⋅⋅⋅⋅⋅⋅⋅⋅⋅⋅⋅⋅⋅⋅⋅⋅⋅⋅⋅⋅⋅⋅⋅⋅⋅⋅⋅⋅⋅⋅⋅⋅⋅⋅⋅⋅⋅⋅⋅⋅⋅⋅⋅⋅⋅⋅⋅⋅⋅⋅⋅⋅⋅⋅⋅ 2
2. SPECIFICATION ⋅⋅⋅⋅⋅⋅⋅⋅⋅⋅⋅⋅⋅⋅⋅⋅⋅⋅⋅⋅⋅⋅⋅⋅⋅⋅⋅⋅⋅⋅⋅⋅⋅⋅⋅⋅⋅⋅⋅⋅⋅⋅⋅⋅⋅⋅⋅⋅⋅⋅⋅⋅⋅⋅⋅⋅⋅⋅⋅⋅⋅⋅⋅⋅⋅⋅⋅⋅⋅⋅⋅⋅⋅⋅⋅⋅⋅⋅⋅⋅⋅⋅⋅⋅⋅⋅⋅⋅⋅⋅⋅⋅⋅⋅⋅⋅⋅⋅⋅⋅⋅⋅⋅⋅⋅⋅⋅⋅⋅⋅ 3
3. COMPOSITION ⋅⋅⋅⋅⋅⋅⋅⋅⋅⋅⋅⋅⋅⋅⋅⋅⋅⋅⋅⋅⋅⋅⋅⋅⋅⋅⋅⋅⋅⋅⋅⋅⋅⋅⋅⋅⋅⋅⋅⋅⋅⋅⋅⋅⋅⋅⋅⋅⋅⋅⋅⋅⋅⋅⋅⋅⋅⋅⋅⋅⋅⋅⋅⋅⋅⋅⋅⋅⋅⋅⋅⋅⋅⋅⋅⋅⋅⋅⋅⋅⋅⋅⋅⋅⋅⋅⋅⋅⋅⋅⋅⋅⋅⋅⋅⋅⋅⋅⋅⋅⋅⋅⋅⋅⋅⋅⋅⋅⋅⋅⋅⋅⋅⋅⋅ 6
3-1. FRONT PANEL ⋅⋅⋅⋅⋅⋅⋅⋅⋅⋅⋅⋅⋅⋅⋅⋅⋅⋅⋅⋅⋅⋅⋅⋅⋅⋅⋅⋅⋅⋅⋅⋅⋅⋅⋅⋅⋅⋅⋅⋅⋅⋅⋅⋅⋅⋅⋅⋅⋅⋅⋅⋅⋅⋅⋅⋅⋅⋅⋅⋅⋅⋅⋅⋅⋅⋅⋅⋅⋅⋅⋅⋅⋅⋅⋅⋅⋅⋅⋅⋅⋅⋅⋅⋅⋅⋅⋅⋅⋅⋅⋅⋅⋅⋅⋅⋅⋅⋅⋅⋅⋅⋅⋅⋅⋅⋅⋅ 6
3-2. BACK PANAL ⋅⋅⋅⋅⋅⋅⋅⋅⋅⋅⋅⋅⋅⋅⋅⋅⋅⋅⋅⋅⋅⋅⋅⋅⋅⋅⋅⋅⋅⋅⋅⋅⋅⋅⋅⋅⋅⋅⋅⋅⋅⋅⋅⋅⋅⋅⋅⋅⋅⋅⋅⋅⋅⋅⋅⋅⋅⋅⋅⋅⋅⋅⋅⋅⋅⋅⋅⋅⋅⋅⋅⋅⋅⋅⋅⋅⋅⋅⋅⋅⋅⋅⋅⋅⋅⋅⋅⋅⋅⋅⋅⋅⋅⋅⋅⋅⋅⋅⋅⋅⋅⋅⋅⋅⋅⋅⋅ 7
3-3. DESCRIPTION ……………⋅⋅⋅⋅⋅⋅⋅⋅⋅⋅⋅⋅⋅⋅⋅⋅⋅⋅⋅⋅⋅⋅⋅⋅⋅⋅⋅⋅⋅⋅⋅⋅⋅⋅⋅⋅⋅⋅⋅⋅⋅⋅⋅⋅⋅⋅⋅⋅⋅⋅⋅⋅⋅⋅⋅⋅⋅⋅⋅⋅⋅⋅ 8
4. HOW TO OPERATE ⋅⋅⋅⋅⋅⋅⋅⋅⋅⋅⋅⋅⋅⋅⋅⋅⋅⋅⋅⋅⋅⋅⋅⋅⋅⋅⋅⋅⋅⋅⋅⋅⋅⋅⋅⋅⋅⋅⋅⋅⋅⋅⋅⋅⋅⋅⋅⋅⋅⋅⋅⋅⋅⋅⋅⋅⋅⋅⋅⋅⋅⋅⋅⋅⋅⋅⋅⋅⋅⋅⋅⋅⋅⋅⋅⋅⋅⋅⋅⋅⋅⋅⋅⋅⋅⋅⋅⋅⋅⋅⋅⋅⋅⋅⋅⋅⋅⋅⋅⋅⋅⋅⋅⋅⋅⋅⋅⋅ 11
4-1. POWER CONNECTION⋅⋅⋅⋅⋅⋅⋅⋅⋅⋅⋅⋅⋅⋅⋅⋅⋅⋅⋅⋅⋅⋅⋅⋅⋅⋅⋅⋅⋅⋅⋅⋅⋅⋅⋅⋅⋅⋅⋅⋅⋅⋅⋅⋅⋅⋅⋅⋅⋅⋅⋅⋅⋅⋅⋅⋅⋅⋅⋅⋅⋅⋅⋅⋅⋅⋅⋅⋅⋅⋅⋅⋅⋅⋅⋅⋅⋅⋅⋅⋅⋅⋅⋅⋅⋅⋅⋅⋅⋅⋅⋅⋅⋅⋅⋅⋅11
4-2. SENSOR CONNECTION ⋅⋅⋅⋅⋅⋅⋅⋅⋅⋅⋅⋅⋅⋅⋅⋅⋅⋅⋅⋅⋅⋅⋅⋅⋅⋅⋅⋅⋅⋅⋅⋅⋅⋅⋅⋅⋅⋅⋅⋅⋅⋅⋅⋅⋅⋅⋅⋅⋅⋅⋅⋅⋅⋅⋅⋅⋅⋅⋅⋅⋅⋅⋅⋅⋅⋅⋅⋅⋅⋅⋅⋅⋅⋅⋅⋅⋅⋅⋅⋅⋅⋅⋅⋅⋅⋅⋅ 11
4-3. INPUT HIGH LEVEL VOLTAGE⋅⋅⋅⋅⋅⋅⋅⋅⋅⋅⋅⋅⋅⋅⋅⋅⋅⋅⋅⋅⋅⋅⋅⋅⋅⋅⋅⋅⋅⋅⋅⋅⋅⋅⋅⋅⋅⋅⋅⋅⋅⋅⋅⋅⋅⋅⋅⋅⋅⋅⋅⋅⋅⋅⋅⋅⋅⋅⋅⋅⋅⋅⋅⋅⋅⋅⋅⋅⋅⋅⋅⋅⋅⋅⋅⋅⋅⋅⋅⋅⋅ 14
4-4. NOTES FOR SELECTING SENSOR CABLE ⋅⋅⋅⋅⋅⋅⋅⋅⋅⋅⋅⋅⋅⋅⋅⋅⋅⋅⋅⋅⋅⋅⋅⋅⋅⋅⋅⋅⋅⋅⋅⋅⋅⋅⋅⋅⋅⋅⋅⋅⋅⋅⋅⋅⋅⋅⋅⋅⋅⋅⋅⋅⋅⋅⋅⋅⋅⋅ 14
4-5. NOTES FOR DYNAMIC MEASUREMENT ⋅⋅⋅⋅⋅⋅⋅⋅⋅⋅⋅⋅⋅⋅⋅⋅⋅⋅⋅⋅⋅⋅⋅⋅⋅⋅⋅⋅⋅⋅⋅⋅⋅⋅⋅⋅⋅⋅⋅⋅⋅⋅⋅⋅⋅⋅⋅⋅⋅⋅⋅⋅⋅⋅⋅⋅⋅⋅⋅⋅⋅⋅ 14
4-6. NOTES FOR STATIC MEASUREMENT⋅⋅⋅⋅⋅⋅⋅⋅⋅⋅⋅⋅⋅⋅⋅⋅⋅⋅⋅⋅⋅⋅⋅⋅⋅⋅⋅⋅⋅⋅⋅⋅⋅⋅⋅⋅⋅⋅⋅⋅⋅⋅⋅⋅⋅⋅⋅⋅⋅⋅⋅⋅⋅⋅⋅⋅⋅⋅⋅⋅⋅⋅⋅⋅⋅⋅⋅⋅ 15
4-7. Output CONNECTION⋅⋅⋅⋅⋅⋅⋅⋅⋅⋅⋅⋅⋅⋅⋅⋅⋅⋅⋅⋅⋅⋅⋅⋅⋅⋅⋅⋅⋅⋅⋅⋅⋅⋅⋅⋅⋅⋅⋅⋅⋅⋅⋅⋅⋅⋅⋅⋅⋅⋅⋅⋅⋅⋅⋅⋅⋅⋅⋅⋅⋅⋅⋅⋅⋅⋅⋅⋅⋅⋅⋅⋅⋅⋅⋅⋅⋅⋅⋅⋅⋅⋅⋅⋅⋅⋅⋅⋅⋅⋅⋅⋅⋅⋅⋅⋅ 15
4-8. CONTROLLING PROPER SENSOR VOLTAGE⋅⋅⋅⋅⋅⋅⋅⋅⋅⋅⋅⋅⋅⋅⋅⋅⋅⋅⋅⋅⋅⋅⋅⋅⋅⋅⋅⋅⋅⋅⋅⋅⋅⋅⋅⋅⋅⋅⋅⋅⋅⋅⋅⋅⋅⋅⋅⋅⋅⋅⋅⋅⋅⋅ 15
4-9. BRIDGE BALANCE⋅⋅⋅⋅⋅⋅⋅⋅⋅⋅⋅⋅⋅⋅⋅⋅⋅⋅⋅⋅⋅⋅⋅⋅⋅⋅⋅⋅⋅⋅⋅⋅⋅⋅⋅⋅⋅⋅⋅⋅⋅⋅⋅⋅⋅⋅⋅⋅⋅⋅⋅⋅⋅⋅⋅⋅⋅⋅⋅⋅⋅⋅⋅⋅⋅⋅⋅⋅⋅⋅⋅⋅⋅⋅⋅⋅⋅⋅⋅⋅⋅⋅⋅⋅⋅⋅⋅⋅⋅⋅⋅⋅⋅⋅⋅⋅⋅⋅⋅⋅⋅⋅ 16
4-10. GAIN CONTROL ⋅⋅⋅⋅⋅⋅⋅⋅⋅⋅⋅⋅⋅⋅⋅⋅⋅⋅⋅⋅⋅⋅⋅⋅⋅⋅⋅⋅⋅⋅⋅⋅⋅⋅⋅⋅⋅⋅⋅⋅⋅⋅⋅⋅⋅⋅⋅⋅⋅⋅⋅⋅⋅⋅⋅⋅⋅⋅⋅⋅⋅⋅⋅⋅⋅⋅⋅⋅⋅⋅⋅⋅⋅⋅⋅⋅⋅⋅⋅⋅⋅⋅⋅⋅⋅⋅⋅⋅⋅⋅⋅⋅⋅⋅⋅⋅⋅⋅⋅⋅⋅⋅⋅ 16
4-11. FILTER CONTROL⋅⋅⋅⋅⋅⋅⋅⋅⋅⋅⋅⋅⋅⋅⋅⋅⋅⋅⋅⋅⋅⋅⋅⋅⋅⋅⋅⋅⋅⋅⋅⋅⋅⋅⋅⋅⋅⋅⋅⋅⋅⋅⋅⋅⋅⋅⋅⋅⋅⋅⋅⋅⋅⋅⋅⋅⋅⋅⋅⋅⋅⋅⋅⋅⋅⋅⋅⋅⋅⋅⋅⋅⋅⋅⋅⋅⋅⋅⋅⋅⋅⋅⋅⋅⋅⋅⋅⋅⋅⋅⋅⋅⋅⋅⋅⋅⋅⋅⋅⋅⋅ 17

2
1. FOREWORD
Dynamic Strain Amplifier DN-AM1000 is composed as the following features.
• This device amplifies minute voltage signals of strain gauge type sensor or all types
of transducer to display and output as in voltage.
• Shunt CAL feature is installed.
• Electronic Auto Zero Balance method is used for Zero Span.
• This device can use connection for Quarter, Half, Full bridge type of strain
gauge
• It is designed to install on standard 19” Sub rack.
2. SPECIFICATION
○
1 Measurement marks : 1CH / EA
○
2 Measuring method : Deflection Method
③ Working Gauge : 120Ω, 350Ω
④ Gauge rate : 2.00
⑤ Bridge voltage (B.V/V) : DC 1V, 2V, 5V, 7.5V, 10V
⑥ Measuring range
Bridge Voltage Measuring range
10V…………………… 2000 µstrain
5V…………………… 4000 µstrain
2V…………………… 10000 µstrain
⑦ Zero adjustment range
Auto - ± 10 %
Zero - ± 1 %

3
⑧ Equilibrium control method
Automatic equilibrium control (Auto) –Extent : ± 4000µstrain
Time : about 1 second
Back up : semi-perma-nent.
Passivity fine control (Zero ADJ) : ± 1V
○
9 Max. Sensitivity (At 100µstrain input)
Bridge Voltage Output
10V…………………… 5V
5V…………………… 2.5V
2V…………………… 1V
○
10 Output
OUT1 : ± 10V (more than 200Ω load)
OUT2 : ± 10V (more than 2kΩ load)
○
11 Non-linearity : ± 0.01% F.S
○
12 Calibration (CAL)
Extent : 1% F.S
1.0mV/V : 2000µstrain
0.1mV/V : 200µstrain
○
13 Sensitivity adjustment (GAIN)
X1, X10,X100,X400, X1000 within ± 1% at error each point
(SPAN) X1 ~ X11 continuous variableness
(FINE) X1 ~ X2 continuous variableness
○
14 S/N 비 (Input conversion numerical value) : more than 54dB (1kHz)
CMRR (Input conversion numerical value) : more than 100dB (1kHz)
○
15 Response frequency characteristic
DC~100kHz (GAIN : 1000, Reduction : -3dB)
DC~20kHz (GAIN : 1000, Reduction : -0.1dB)
○
16 Low Pass Filter
(L.P.F) Frequency: 10, 100, 1K, 10K, PASS 5 stages
About decrease : within -6dB/oct

4
○
17 Temperature range for use
0 ~ +60°C
○
18 Effect by temperature change
Zero drift : within ± 1 µstrain/°C
Sensitivity change: ± 0.03% F.S/°C
○
19 Effect by electric power change (About ± 10% change in supply voltage)
Zero drift: within ± 0.05% F.S
Sensitivity change: within ± 0.05% F.S
○
20 MONITOR : Digital Voltage Display
Over 10V will be displayed in 10.00 (increased or decreased in each 0.01)
Less 10V will be displayed in 0.000 (increased or decreased in each 0.001)
Voltage on OUT1 will be displayed in Digital.
○
21 Supply Voltage
AC100/220V ± 10% 60Hz
○
22 External Size and Weight
128.4 (H) × 43.2 (W) × 198 (D) mm
1000g
○
23 OPTION
Output: OUT1 ± 100mA output

5
3. Composition
3-1. Front Panel
○
1 Symbol (-) display
○
2 Voltage display
○
3 Zero hand-operated control volume
○
4 Zero auto control switch
○
5 L.P.F switch
○
6 Bridge voltage selecting switch
○
7 Bridge voltage fine control volume
○
8 Bridge voltage senscing selecting
switch
○
9 Internal CAL Bridge resistance
selecting switch
○
10 CAL Strain value switch
○
11 GAIN selecting switch
○
12 GAIN control volume
○
13 GAIN fine control volume
○
14 Power lamp
○
15 Power switch
○
16 Sensor input voltage monitor terminal
○
17 Sensor output voltage monitor
terminal
○
18 Signal output monitor terminal

6
3-2.Back Panel
○
19 Low-current output (load more than 2kΩ)
○
20 High-current output (load more than 200Ω)
○
21 Sensor input connector
○
22 Case earth terminal
○
23 Fuse
○
24 Power selecting switch
○
25 Power input connector

7
3-3. Description
○
1 Symbol (-) display
This symbol lamp will be lighted when the output voltage is become less than
0V.
○
2 Voltage display
Output voltage is displayed as in 4 Digit -7 Segment LED.
When output voltage is over 10V or below -10V, it will be displayed as +/-
10.00 and the rest section will be displayed as in +/- 9.000V.
○
3 Zero Hand-operated control volume
It is a volume to control the offset of residual quantity after finishing the auto
zero control.
Control range is within ± 1V.
○
4 Zero auto control switch
Use this switch to carry out auto zero control.
When this auto switch is pressed, “Auto” will appear on the LED and then
zero will be set.
○
6 Bridge voltage selecting switch
This switch is to select the bridge supply voltage.
You can make your selection for the supply voltage among DC 1V, 2V, 5V,
7.5V, 10V.
○
7 Bridge voltage fine control volume
This controls establishing bridge voltage precisely.
○
8 Bridge voltage senscing selecting switch
When select by EXT mode as switch to compensate bridge voltage by
Cable's resistance change, bridge voltage by Cable length change moves
automatically and is corrected.
○
9 Internal CAL Bridge resistance selecting switch
This switch is to select the bridge resistance while you are doing bridge
calibration.
○
10 CAL Strain value switch
It is a shunt switch to calibrate the bridge in two different types - 2000µ and
200µstrain.
○
11 GAIN selecting switch

8
It is the switch to control GAIN and it can be controlled as in X1, X10, X100,
X400, X1000 times.
○
12 GAIN control volume
It is a volume to control GAIN and it can be continuously controlled as in 을
from X1 up to X11 times.
○
13 GAIN fine control volume
It is a volume for the fine control of GAIN. It can be continuously controlled
as in from X1 up to X2 times.
○
14 Power lamp
This lamp shows you the power supply to Amplifier.
○
15 Power switch
This switch is to supply power to Amplifier.
○
16 Sensor input voltage monitor terminal
This can monitor Sensor input voltage
○
17 Sensor output voltage monitor terminal
This can monitor Sensor output voltage
○
18 Signal output monitor terminal
This can monitor output voltage of Amplifier.
○
19 Low-current output (more than 2kΩ load) connector
It is the final output signal of Amplifier and also low-current output.
You can use this more than 2kΩ load.
○
20 High-current output (more than 200 Ω load) connector
It is the final output signal of Amplifier and also high-current output.
You can use this on more than 200Ω load.
○
21 Sensor input connector (MS connector)
You can use Full bridge, Half bridge, Quarter bridge and Potentiometer
Voltage input ,etc
○
22 Case earth terminal
Connects and uses with outside ground in case of biographical environment
with noise is bad.
○
23 Fuse
It is a fuse to protect from outside excess current. AC 220V 0.5A)

9
○
24 Power selecting switch
It is a selection (AC 110V, 220V) switch.
AC 220V when deliver from a warehouse.
○
25 Power input connector
This connector is to supply external AC power.

10
4. 조작 방법
4-1. How to operate
○
1 Please only use the exclusive AC code (3-tube) for the power cord. When AC
is not grounded, please make the connection by using the ground connector
which is located on the backside of lamp.
○
2 Please check the AC power selecting switch and then supply power to the
device. If the lamp is not lighted, please check the fuse and power selecting
switch.
4-2. Sensor connection
Connector is MIL-C- MS3112(14-19) connector of MIL-C-26482 Series. (contact
resistance, insulation resistance is superior)
<MS3112 14-19>
Pin No. Use
A Excitation +
B Excitation Sense +
C Excitation –
D Excitation Sense -
E Signal +
F Signal -
G Shield
H HB
J D350Ω
K D120Ω
L R3
M null
N R4
P null
R null
S null
T null
U null
V Chassis GND

11
ST-AM1000 INTERNAL CIRCUIT
Internal Dummy External Dummy
Quarter Bridge connection

12
Prefered Alternate
Half Bridge connection
4 Gauge Transducer
Full Bridge connection

13
4-3. High Level Voltage input
This device can measure the signal that inputted in DC (DCDT, High level,
Thermocouple etc).
For the measurement, following conditions should be satisfied.
○
1 On Common mode, the amp input should be as ± 10V. Please be careful since
when over ± 10V is inputted, the signal source will be cut off.
○
2 When Thermocouple temperature sensor is used, an error in measurement can
be occurred since the temperature-electromotive force might be generated on
the commissure between the connector pin of amplifier and thermocouple lead
wire. Therefore, you should do the cold junction compensation or you should
carry out the measurement in the place where without such a big temperature
change.
○
3 The input stage of amplifier are “+SIG”, “-SIG”. Since their minimum input
current is originated by this input impedance, it should be over 50mA to carry out
the measurement.
4-4. Notes for selecting sensor cable
The each space for selecting sensor cable should be:
○
1 electrically isolated.
○
2 Cable resistance should be small.
○
3 The cable resistance of the internal lines should be regular.
○
4 It is better to use the shield cable.
4-5. Notes for Dynamic measurement
Strain gauge or Transducer (located at the end of the measurement lead cable) is
exposed to various electric devices and equipment and also receive the analogue
frequency (50kHz, 60kHz) noise from the line power. Therefore, please carry out
the following procedures to minimize this kind of happening.
○
1 Please prepare for the shield cable. (If the shield cable cannot be ready,
please make the lead cable as shortest as possible.)

14
○
2 The shield cable should be connected to the ground and input connector.
○
3 The cable resistance of the internal cables should be regular.
○
4 It’s better to use the shield cable.
○
5 All wires should be built in the clean environment for the measurement.
(Please avoid using transformer, motors, relay and high voltage cable where
the magnetic field can be easily generated. If it is necessary to use one of
them, please use any structure for the protection.)
○
6 If you use a long wire, please use a balanced leading line so that you can
minimize the noise.
4-6. Notes for Static measurement
You must make sure that the cable resistance between each gauge lead wire is
regular. If it is not, the measurement value can be changed by the surrounding
temperature. Please pay your special attention for this point.
Please carry out the following procedures.
○
1 You must us 3-line for Quarter Bridge.
○
2 To minimize the effect by the temperature change, it is ideal to put all the used
lead wire in the same wire bunch.
○
3 To build the precise data when you use a long wire, please do the
compensation considering the resistance of lead.
(Example : The thickness, length of the wire and its proper resistance etc)
4-7. Output connection
Output ± 10V can read the voltage output value as in oscilloscope, volt meter and
A/D board as BNC connector.
4-8. Controlling proper sensor voltage
Sometimes when you do the stress analysis, the high proper voltage to the active
gauge might be required. When the proper voltage is high, the output will be big
so that you do not have to amplify too much. But when the high voltage is applied

15
to the gauge with low resistance, an error in measurement can be occurred since
the joule heat might be generated on the gauge. So the most suitable condition
should be found since the resistance on the gauge and proper voltage are very
important. In addition to the gauge with high resistance (over 350Ω) or the long
and wide gauge, you can increase the proper voltage at the place where the
heat-sinking (aluminum etc) easily can be done.
Please avoid increasing the proper voltage with the gauge below 120Ω or at the
place where the heat-sinking cannot be done such as plastic.
Normally the gauge proper voltage should be 10%~100% of the recommended
voltage from the gauge.
Maximum Metallic (foil) gauge can be normally 50% ~ 75% for the stability and
good S/N (signal to noise).
Exclusive voltage should be applied for the semi conductive gauge.
To control the sensor proper voltage of the amplifier, please turn the bridge
voltage switch.
4-9. Bridge balance
Generally, when the bridge balance is too much out, you cannot carry out the
measurement for the wide range since the measurement value will be clipped.
Also you should compensate the bridge balance since a damage can be made on
hardware.
For the compensation, please press the Auto switch on the front side of amplifier
then “Auto” will be lighted on the voltage LED to calibrate the balance
automatically.
Please control the volume for the rest output voltage to set Zero.
4-10. GAIN control
Firstly, please turn the gain switch in a clockwise to set (X1, X10, X100, X400,
X1000) gain.
Or you can turn 10-turn volume so that you can control gain (X1 ~ X11).
The gain noise is originated by input voltage. So when the input voltage is
increased, the noise will be increased accordingly. So please set the gain
according to the size of sensor.
While you are carrying out stress analysis, please compensate as following so that

16
you can get the precise information. (in case 1 active gauge is used)
6
10
4
−
××××=
µε
K
AVVout B
Vout : Output voltage of amplifier
VB : Bridge proper voltage
A : Amplifier gain
K : Gauge factor
For the Transducer, please use the following formula by using the output value
you know.
EX) 2mV/V
3
10−
×××= KAVVout B
Vout : Output voltage of amplifier when the maximum output of transducer
is inputted
VB : Bridge proper voltage
A : Amplifier gain
K : Output sensitivity of transducer (mv/V)
For shunt compensation, error can be occurred by wiring, bridge resistance or
proper voltage while stress analysis is being done. So shunt compensation is
very important when you set the amplifier gain. Also when you use the analogue
transducer (force, torque and pressure etc), please fully understand the size of
transducer and the form of output so that you can select correct amplifier gain
accordingly.
4-11. Filter control
As standard, ST-AM1000 has 2 pole standard low-pass filter installed.
Controllable switch is located on the front side of amplifier and the signal noise is
10Hz, 100Hz, 1kHz, 10kHz. Wide-band can be controlled by band pass. This cut-
off frequency is normally originated in 30% (-3dB) of output. For control, please
turn the rotary selector switch located on the front side of the amplifier.

17
L.P.F Characteristic
GAIN Band Width Characteristic
Table of contents
Other dacell Amplifier manuals
Popular Amplifier manuals by other brands
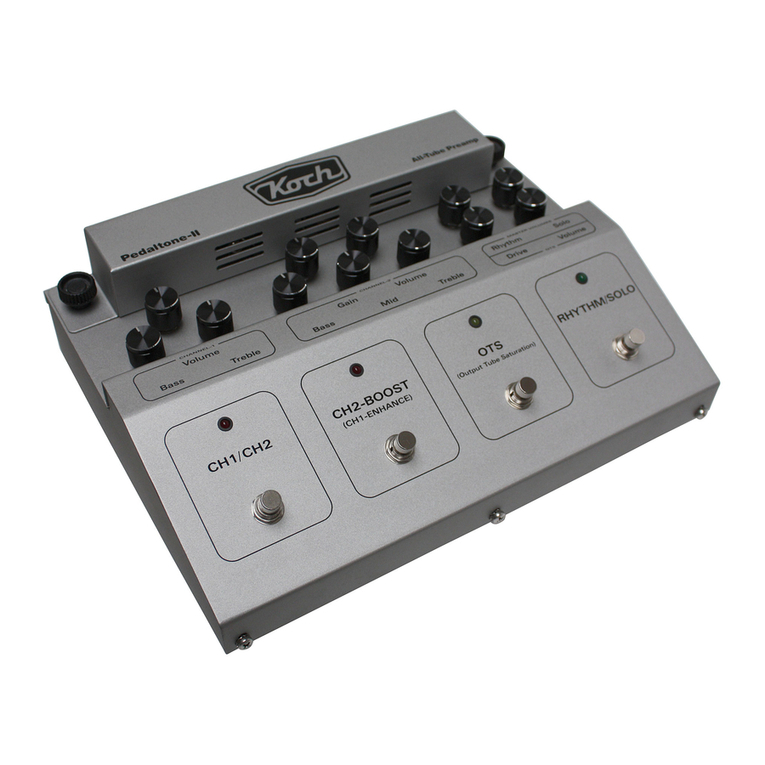
Koch Guitar Electronics
Koch Guitar Electronics Pedaltone operating instructions
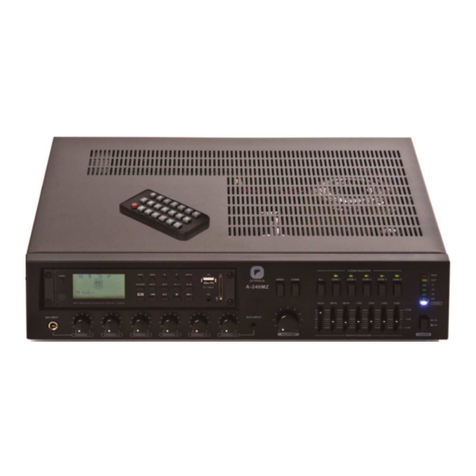
Optimus
Optimus A-240MZ Installation and operating instructions
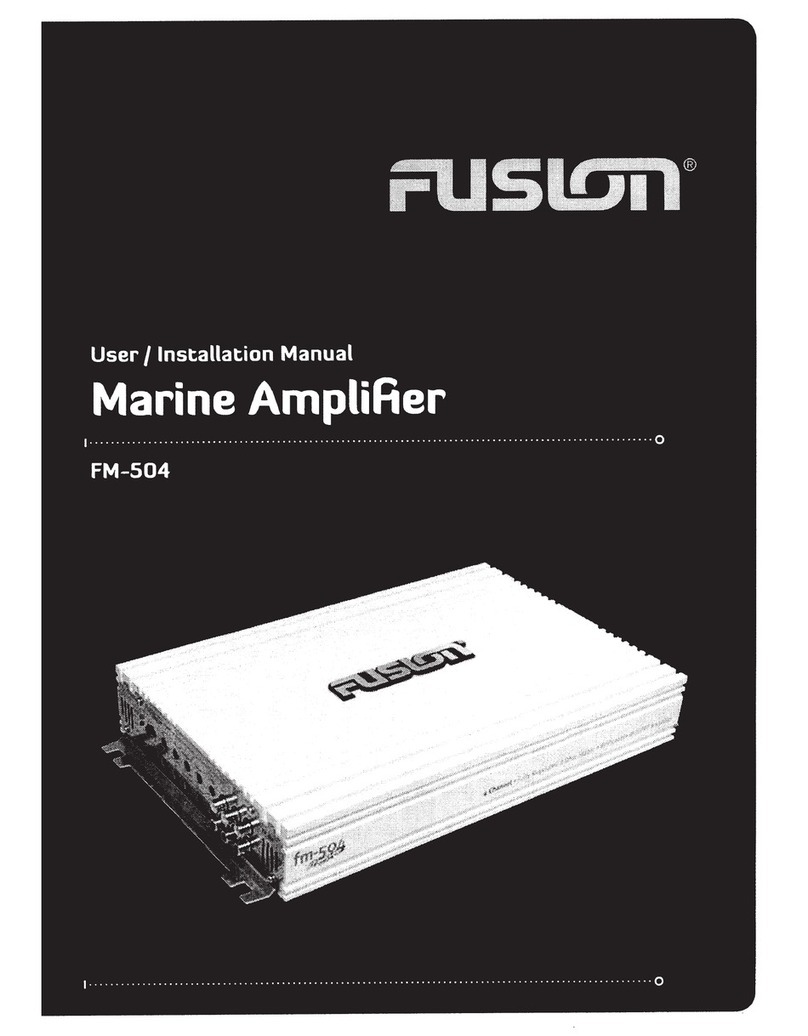
Fusion
Fusion FM-504 installation manual

Podium Pro Audio
Podium Pro Audio VX1000 user manual
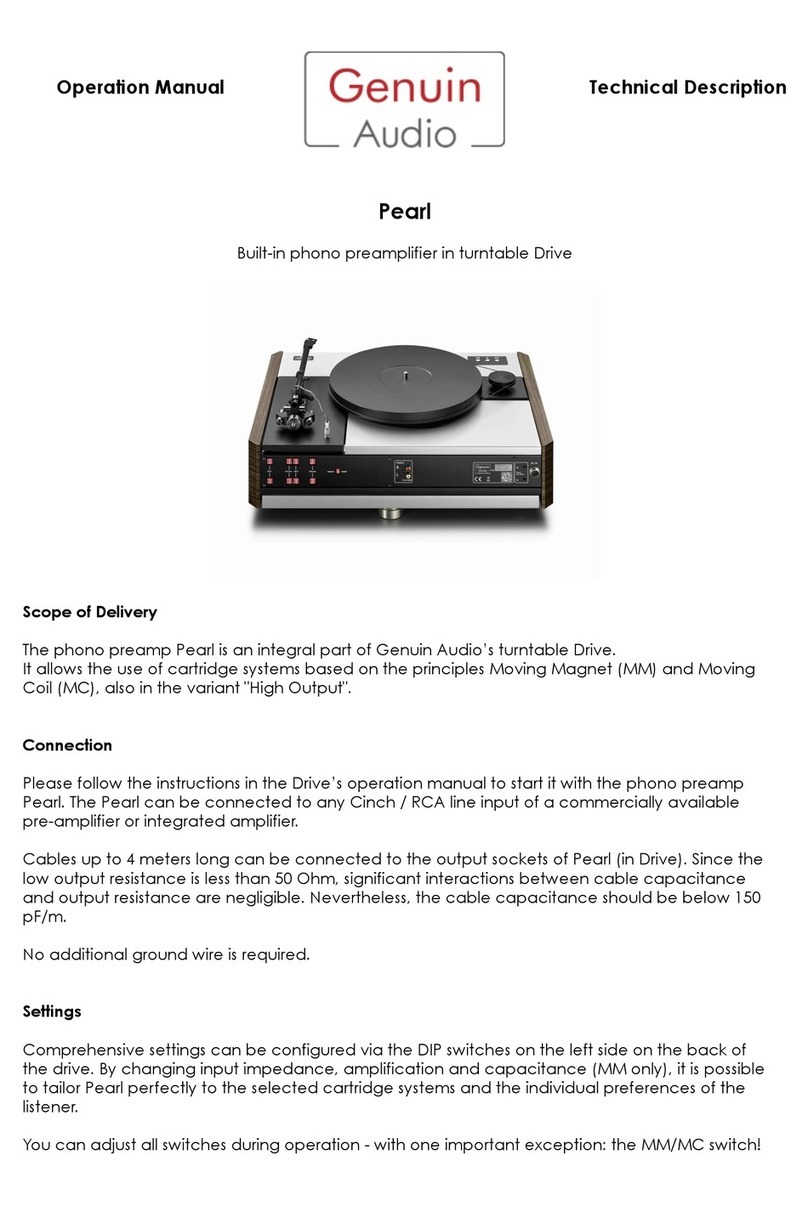
Genuin Audio
Genuin Audio Pearl Operation manual
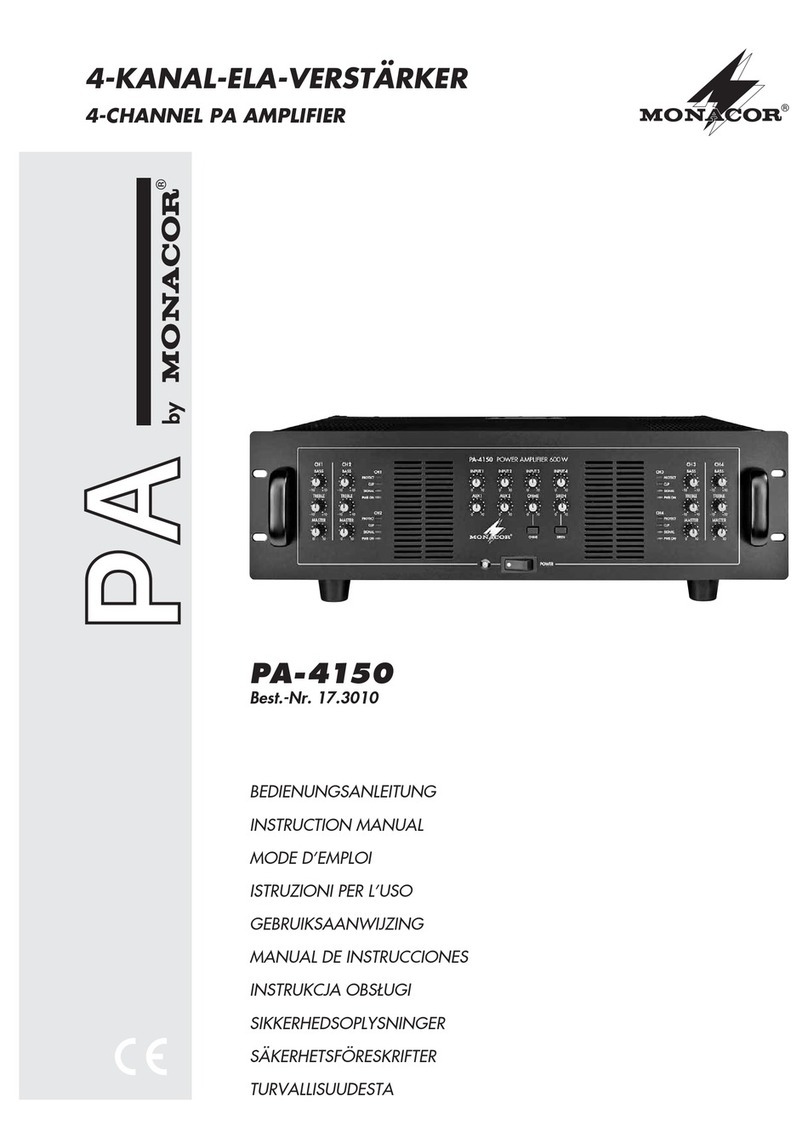
Monacor
Monacor PA-4150 instruction manual