DART Controls 530B Series User manual

530B CONTROL SERIES
P.O. Box 10
5000 W. 106th Street
Zionsville, Indiana 46077
Phone (317) 873-5211
Fax (317) 873-1105
www.dartcontrols.com
Instruction Manual
Variable Speed DC Control
LT530B (0505)
CONTROLS
A-5-3271B

TABLE OF CONTENTS
WARRANTY ......................................................................................................................................................................................................... 1
INTRODUCTION .................................................................................................................................................................................................. 2
COMMONLY ASKED QUESTIONS ................................................................................................................................................................... 2
BASIC MODEL SELECTION .............................................................................................................................................................................. 2
CONTROL FEATURES ....................................................................................................................................................................................... 3
OVERALL CONTROL DIMENSIONS ............................................................................................................................................................. 3-4
SPEEDPOT MOUNTING DIMENSIONS ............................................................................................................................................................. 4
MOUNTING INSTRUCTIONS ............................................................................................................................................................................. 4
WIRING PROCEDURE ......................................................................................................................................................................................... 4
TERMINAL STRIP WIRING - P1 ......................................................................................................................................................................... 5
TERMINAL STRIP WIRING - P2 ...................................................................................................................................................................... 5-6
SETTING INPUT VAC .......................................................................................................................................................................................... 6
SWITCH LADDER CIRCUIT DIAGRAMS .......................................................................................................................................................... 6
“RE” CONTROL PANEL IDENTIFICATION ..................................................................................................................................................... 6
INITIAL START-UP .............................................................................................................................................................................................. 7
TRIMPOT ADJUSTMENT PROCEDURE ........................................................................................................................................................ 7-8
TRIMPOT SETTING CHART .............................................................................................................................................................................. 8
1.5 AND 3.0 HORSEPOWER - MODEL 533BC ................................................................................................................................................. 8
BASIC HOOK-UP DIAGRAM WITHOUT OPTIONS ................................................................................................................................... 9-10
530BC, 533BC & 530BRC HOOK-UP DIAGRAMS .................................................................................................................................... 9
PILOT RELAY SWITCHING .......................................................................................................................................................................... 9
530BRE HOOK-UP DIAGRAM ................................................................................................................................................................... 10
JU2 JUMPER WIRE SELECTION CHART ...................................................................................................................................................... 10
CONTROL MODIFICATIONS ...................................................................................................................................................................... 10-11
TWO SPEED OPERATION ......................................................................................................................................................................... 10
DYNAMIC BRAKING ................................................................................................................................................................................... 10
TACHOMETER FEEDBACK & FOLLOWER ............................................................................................................................................ 11
INHIBIT INSTRUCTIONS ............................................................................................................................................................................ 11
OPTIONS ....................................................................................................................................................................................................... 11-15
-4 OPTION .................................................................................................................................................................................................... 11
-5 OPTION .................................................................................................................................................................................................... 12
-7 / -11 / -15A OPTIONS .............................................................................................................................................................................. 13
-36M / -38M OPTIONS ............................................................................................................................................................................ 14-15
IN CASE OF DIFFICULTY ................................................................................................................................................................................ 15
FUSING ............................................................................................................................................................................................................... 15
SPECIFICATIONS .............................................................................................................................................................................................. 16
530B SERIES PARTS PLACEMENT & LIST ................................................................................................................................................... 17
530B SERIES SCHEMATIC ............................................................................................................................................................................... 18
PRODUCT LINE ............................................................................................................................................................................ BACK COVER
WARRANTY
Dart Controls, Inc. (DCI) warrants its products to be free from defects in material and workmanship. The exclusive remedy for this
warranty is DCI factory replacement of any part or parts of such product which shall within 12 months after delivery to the purchaser
be returned to DCI factory with all transportation charges prepaid and which DCI determines to its satisfaction to be defective.
This warranty shall not extend to defects in assembly by other than DCI or to any article which has been repaired or altered by
other than DCI or to any article which DCI determines has been subjected to improper use. DCI assumes no responsibility for
the design characteristics of any unit or its operation in any circuit or assembly. This warranty is in lieu of all other warranties, express
or implied; all other liabilities or obligations on the part of DCI, including consequential damages, are hereby expressly excluded.
NOTE: Carefully check the control for shipping damage. Report any damage to the carrier immediately. Do not attempt to operate
the drive if visible damage is evident to either the circuit or to the electronic components.
All information contained in this manual is intended to be correct, however information and data in this manual are subject to change
without notice. DCI makes no warranty of any kind with regard to this information or data. Further, DCI is not responsible for any
omissions or errors or consequential damage caused by the user of the product. DCI reserves the right to make manufacturing
changes which may not be included in this manual.
WARNING
Improper installation or operation of this control may cause injury to personnel or control failure. The control must be installed in
accordance with local, state, and national safety codes. Make certain that the power supply is disconnected before attempting to
service or remove any components!!! If the power disconnect point is out of sight, lock it in disconnected position and tag to prevent
unexpected application of power. Only a qualified electrician or service personnel should perform any electrical troubleshooting
or maintenance. At no time should circuit continuity be checked by shorting terminals with a screwdriver or other metal device.
1

Notes:
1) 1/8 - 1.0 h.p. uses 115VAC input, 0-90VDC output and 100VDC field; 1/4 - 2.0 h.p. uses 230VAC input, 0-180VDC output and 200VDC field
2) 1.5 h.p. uses 115VAC input, 0-90VDC output and 100VDC field; 3.0 h.p. uses 230VAC input, 0-180VDC output and 200VDC field
INTRODUCTION
The 530B Series is a high performance, dual voltage versatile DC motor control which provides a wide range of standard features,
with many options that extend its capabilities. The 530B Series will operate 1/8 through 1.0 horsepower at 115VAC input, and 1/
4 through 2.0 horsepower at 230VAC input. A chassis only model is available to operate a 1.5 horsepower motor at 115VAC input,
or 3.0 horsepower at 230VAC input. Reference “Basic Model Selection” guide.
The 530B Series consists of three basic types:
C= Chassis mounted, no enclosure, no power relay's.
RC = Chassis mounted, no enclosure, with power relay's.
RE = Plastic enclosure with power relay's - Nema 4/12 standard.
The 530B Series is designed for Permanent Magnet, Shunt Wound, and some Universal Series (AC/DC) motors in the above
horsepower ranges. The 530B Series incorporates transient voltage protection with adjustable Current Limit and AC fuses for
protection. Minimum and Maximum speeds are easily adjusted by trimpots, as is the I.R. Compensation. Acceleration and
Deceleration are fully adjustable via individual trimpots.
COMMONLY ASKED QUESTIONS
Q. Can I run two or more motors from the same drive?
A. Not recommended. The I.R. Compensation (regulation) and Current Limit circuits would have difficulty sensing the different
load on each motor.
Q. Can I change the horsepower of my motor and still use the same control?
A. Yes, provided you do not deviate outside the horsepower range for the voltage you are using. The trimpots would need
readjustment; see “Trimpot Chart” for approximate settings.
Q. Can I use the 530B Series as a Current Follower?
A. Yes, there is a field installable -5 or -7 option shown in "Options" section.
Q. Can I use the 530B Series on Tachometer feedback?
A. Yes, see +Tach (P2-9) under “Terminal Strip Wiring - P2”.
Q. Can I use the Stop (P2-11), Start (P2-13), and Common (P2-12) to stop-start the control on the “C” chassis version?
A. No. Terminals P2-11, P2-12, and P2-13 are only active on the relay versions; “RE” and “RC”. These terminals are
non-operative on the “C” version.
Q. Can the 530B Series be used as a Voltage or Tachometer Follower?
A. Yes. The voltage must be ungrounded and no more than +12 VDC (See “Terminal Strip Wiring” for proper hook-up).
Q. How would I proceed to stop/start the 530B Series with my own relay?
A. You can use the contact of your relay in place of the AMP REF to REV 1 (P2-2 to P2-7) jumper wire. Since this is a low
level signal (12 volts at 2mA), you must use a logic type relay (preferably gold contacts). This cannot be done on controls
using some options. Consult your Dart Representative if options are involved.
Q. Why is a jumper wire between AMP REF (P2-2) and REV 1 (P2-7) needed on drives with no options?
A. REV 1 (P2-7) and REV 2 (P2-8) are two identical stop inputs. One of these must be held low (to Amp Ref P2-2) for the control
to run. If the drive has no options, this must be jumpered to satisfy the “OR” gate. This requirement is satisfied by some
options. For these options, a connection must be made to these terminals. Instead of a jumper wire, the option is wired
to these terminals. (See “Jumper Wire Selection”).
BASIC MODEL SELECTION
115/230 VAC INPUT 0-90/0-180 VDC OUTPUT 100/200 VDC FIELD
RELAY RELAY
HP RANGE 1CHASSIS CHASSIS ENCLOSED
1/8 - 2.0 530BC 530BRC 530BRE
115/230 VAC INPUT 0-90/0-180 VDC OUTPUT 100/200 VDC FIELD
RELAY RELAY
HP RANGE 2CHASSIS CHASSIS ENCLOSED
1.5 and 3.0 533BC Not Available Not Available
2

7.50
0.20
TOP VIEW
6.70
9.00
6.30
7/32 DIA.
(4 SLOTS)
END VIEW
2.00
CONTROL FEATURES
INPUT VOLTAGE SELECTION SWITCH
- Switch selectable between 115 VAC and 230 VAC input.
MIN SPEED
- (Minimum speed) Allows adjustment of the motor speed when the speedpot is set at minimum. This permits the user
to eliminate the “Deadband” on the main speed control, permitting zero calibration. Clockwise rotation of the “MIN” trimpot
increases output VDC.
ACCEL
- (Acceleration) Allows adjustment of the motor acceleration from a minimum of 0.3 seconds to a maximum of 12 seconds.
The -15A option extends the maximum acceleration time to 30 seconds.
DECEL
- (Deceleration) Allows adjustment of the motor deceleration from a minimum of 0.6 seconds to a maximum of 12 seconds.
The -15A option extends the maximum deceleration time to 30 seconds.
MAX SPEED
- (Maximum speed) Allows adjustment of the motor speed when the speedpot is set at maximum (CW). This permits
the user to eliminate the “DEADBAND” of the speedpot, providing full speed at maximum rotation. Rotation of the “MAX” trimpot
in the clockwise direction increases maximum output VDC.
I.R. COMP
- (Speed Regulation) Allows adjustment of the circuitry that
controls the speed regulation of the motor. This feature controls
armature speed by changing the armature voltage to compensate
for increased or decreased motor loading. Clockwise rotation of the
“I.R. COMP” trimpot will increase gain compensation.
CUR. LIM.
- (Current Limit) Provides protection from excessive arm-
ature current by limiting the maximum armature current the control
can provide. This enables adjustment of the maximum torque the
motor can deliver. Set Current Limit (CUR. LIM.) at 125% of the rated
motor current. Clockwise rotation of the “CUR. LIM.” trimpot increas-
es the torque (current) the control will provide.
TACH INPUT SELECTION
- Factory set at 3V per 1000 RPM, jumper
selectable (JU3) to 7V per 1000 RPM. Refer to “Tach Feedback”
section in “Control Modifications” for more information.
TERMINAL STRIP P1
- Barrier type terminal strip provides for connec-
tion of AC lines, motor leads, motor field (if necessary), and earth
ground.
TERMINAL STRIP P2
- Barrier type terminal strip provides for connec-
tion of speed potentiometer and any accessories and/or jumper
wires which control the drive.
RELAY
- (Power Interrupt Relay's) Available only on the “RC” and the
“RE” versions, the relay's permits the switching of AC power with a
low current signal. For the “RE” version, the relay's will not allow start
up after power failure without manually restarting.
3
“C” and “RC”
SERIES HOUSING
DIMENSIONS
OVERALL CONTROL DIMENSIONS
P3
AC FUSES
RELAY
RELAY
RELAY
TACH INPUT
SELECTION
JU3
115
+3V+7
P2
P1
CUR LIMMIN ACCEL DECEL MAX IR COMP
OVER CUR OUT
AMP REF
POT LO
POT WIPER
POT HI
SPARE
REV 1
REV 2
+TACH
PILOT LAMP
STOP
COMMON
START
-13
-12
-11
-10
-9
-8
-7
-6
-5
-4
-3
-2
-1
PROVIDES SUPPORT
AND TRIGGERING FOR
OPTIONS
INPUT VOLTAGE
SELECTION SWITCH
GND AC AC +A -A -F +F
-1 -2 -3 -4 -5 -6 -7

7.50
0.20
BOTTOM VIEW
6.70
9.00
6.30
7/32 DIA.
(4 SLOTS)
10.00
0.50
2.63
3.88
0.87
6.02
1.13
2.502.13 .875 DIA.
(2 HOLES)
SIDE VIEW
END VIEW
4.64
MOUNTING INSTRUCTIONS
1. Four 7/32" slots are provided for control mounting.
2. The 530B Series chassis can be used as a template.
3. Use standard hardware to mount.
4. For the “RE” version ONLY: Two 7/8" diameter holes are provided in one endplate to facilitate wiring. This allows for easy
connection of 1/2" conduit.
NOTE: For enclosed models using 1 h.p. 90V or 2 h.p. 180V motors, the control MUST be mounted vertically.
CAUTION:
DO NOT ATTEMPT TO PERFORM HI-POT TEST ACROSS AC LINES WITH THE CONTROL IN CIRCUIT.
THIS WILL RESULT IN IMMEDIATE OR LONG TERM DAMAGE TO THE CONTROL.
WIRING PROCEDURE
1. Size all wires which carry armature or line current to handle currents AS SPECIFIED BY NATIONAL, STATE, AND/OR LOCAL
CODES. All other wires may be # 20AWG or smaller as permitted by local code.
2. Control wire (Pot, Tach, etc.) should be separated from all the Armature, Field (if Shunt Wound), and the AC wires when routed
in conduits or in wire trays. The enclosed version has two holes on one endplate for this purpose.
4
DO NOT MOUNT CONTROL WHERE AMBIENT TEMPERATURE IS OUTSIDE RANGE OF -10° to 45° C. (15° to 115° F.)
SPEEDPOT
(5K 2W)
CUSTOMER'S
MOUNTINGBRACKET
DIALPLATE
2.00" dia.
LOCK
WASHER
O-RING
HEX NUT
SPEEDPOT
KNOB
.437
3/8
DIA.
5/32
DIA.
SPEEDPOT LOCATOR HOLE DIMENSIONS
.500 .370 .370
1.240
1.250
.250 Dia.
EXPLODED VIEW
SPEEDPOT
MOUNTING
DIMENSIONS
(For “C” and “RC” versions)
CUSTOMER'S MOUNTING BRACKET
“RE” SERIES
HOUSING
DIMENSIONS
(Control dimensions continued)

5(P2 wiring continued)
530B Series
TERMINAL STRIP WIRING - P1
CAUTION: BE SURE CONTROL HOUSING IS PROPERLY GROUNDED.
The 530B Series uses a 7 position barrier type terminal strip to handle the power connections.
P1-1
(EARTH GROUND) - Ground the control by connecting the ground wire to this terminal. NOTE: Terminals P1-5 (-ARM)
and P2-2 (AMP REF) are electrically the same, which is the common reference point (low voltage common) for the control
logic. The EARTH GROUND terminal (P1-1) is electrically different from common. If connected together, either at the
amplifier or in any other fashion, fatal or hazardous operation may occur and permanent damage to the control WILL result!
P1-2
(AC1) 115VAC - Connect incoming hot AC (black wire) to this terminal. NOTE: This is fused (F1) on the control.
(AC1) 230VAC - Connect either hot side.
P1-3
(AC2) 115VAC - Connect the neutral AC (white wire) to this terminal. NOTE: This is fused (F2) on the control.
(AC2) 230VAC - Connect either hot side.
P1-4
(+ ARMATURE) - Connects to the plus (+) Armature wire on the motor. 0-90VDC for 115VAC input or 0-180VDC for 230
VAC input. See “SPECIFICATIONS” for output rating.
CAUTION: ARMATURE CONNECTION MUST NOT BE SWITCHED OR BROKEN WHILE CONTROL IS ON
OR SERIOUS DAMAGE TO THE CONTROL MAY RESULT.
P1-5
(- ARMATURE) - Connects to minus (-) Armature wire (also considered circuit common) on the motor.
P1-6
(- FIELD) - Connect minus (-) Field wire of the Shunt Wound motor (not used on PM motors).
FIELD VOLTAGE TABLE
Model # VAC Input VDC Field
115 100
230 200
P1-7
(+ FIELD) - DO NOT use for Permanent Magnet motor. This supplies + Field voltage for a Shunt Wound motor. See chart
above for dual voltage Field Wound motors. This output is rated at 1 Amp for 530B series controls and 1.5 Amps for the
533B control. For motors with dual voltage field (ie. 50/100V or 100/200V), make sure the highest value is connected.
TERMINAL STRIP WIRING - P2
The 530B Series uses a 13 position barrier type terminal strip for control connections.
CAUTION: NONE OF THE P2 TERMINALS SHOULD BE EARTH GROUNDED!
P2-1
(OVER CURRENT OUT) - Can be used to signal that the control is in current limit. It can also signal other devices or alarms.
This is a low level logic signal which goes “high” when the current limit amplifier is in current limit. The logic of this control
is +12 volts, while the output at this terminal is approximately 1.5 volts through a 1000Ωresistor when in Current Limit.
P2-2
(AMP REF) - This is the common point of the logic. It is used as common with OVER CURRENT OUT (P2-1), +TACH (P2-
9), REV 1 (P2-7), REV 2 (P2-8), and WIPER (P2-4). NOTE: Never connect this terminal to earth ground !! Serious damage
and injury may result !! This terminal is electrically the same point as -ARM (P1-5).
P2-3
(SPEEDPOT LO) - Connects to the low side (orange wire) of the 5K Speedpot (normally the CCW end). This input is raised
and lowered by the MIN trimpot. Electronic speed input voltage (voltage follower) may be referenced to Speedpot LO if
the MIN trimpot adjustments are to be active. Otherwise, inputs may be referenced to AMP REF (P2-2), which will bypass
the MIN trimpot. INPUT MUST NOT BE GROUNDED !
CAUTION FOR VOLTAGE FOLLOWER APPLICATIONS:
THE INPUT CONNECTION TO THE SPEEDPOT MUST NOT BE GROUNDED !!
SERIOUS DAMAGE TO THE CONTROL MAY RESULT FROM A GROUNDED INPUT.
P2-4
(SPEEDPOT WIPER) - Connects to the wiper (red wire) of the Speedpot (center lead). Use this input for the plus (+) side
of voltage follower operation or tach follower. The minus (-) side connects to AMP REF (P2-2). INPUT MUST NOT BE
GREATER THAN +12V MAXIMUM AND MUST NOT BE GROUNDED !
P2-5
(SPEEDPOT HI) - Connects to high side (white wire) of the Speedpot (CW end). This is internal +12 volts. INPUT MUST
NOT BE GROUNDED !
P2-6
(SPARE) - This terminal is not connected to the control circuit. It can be used as a terminal for field modifications.

START-STOP SWITCH
MOMENTARY SWITCH TURNS
CONTROL ON AND OFF
SPEED POTENTIOMETER
5000& 2W SPEEDPOT
CONTROLS MOTOR SPEED
POWER ON INDICATOR
HIDDEN LED INDICATOR LAMP
010
46
28
ON
ON
OFF
CONTROLS
P2-7
(REV 1) - REV 1 and REV 2 are identical quick stop inputs. One of them must be held low (to AMP REF) before the control
will operate. The two are diode separated to form an “OR” gate. Since -ARM (P1-5) is also low in the system, these two
inputs can be wired to the motor side of a reversing switch or relay. During the period of switching, neither input will be
low, which will instantly return the set speed to zero and reset the acceleration ramp.
P2-8
(REV 2) - Identical to REV 1 (P2-7).
P2-9
(+TACH) - Connect +Tach from a DC tachometer for tachometer feedback. The minus (-) lead from the tachometer goes
to AMP REF (P2-2). Output voltage from the tachometer at full speed can range from 6 to 12 volts. The scale is corrected
using the JU3 jumper selectable setting of 3V/7V per 1000 RPM and the MAX speed trimpot. A 3 volt per 1000 RPM OR
7 volt per 1000 RPM tachometer should be used.
P2-10
(PILOT LIGHT) - Connecting point for on-off neon indicator lamp. The remaining lead will be connected to P2-11.
P2-11
(STOP) - Install one or more normally closed stop switches (in series) between STOP (P2-11) and COMMON (P2-12).
Not active on “C” version.
P2-12
(COMMON) - Mid point of Start-Stop switches. Not active on “C” version.
P2-13
(START) - Install one or more normally open start switches (in parallel) between START (P2-13) and COMMON (P2-12).
Not active on “C” version.
(P2 wiring continued)
SETTING INPUT VAC
For use with 110 through 130 VAC inputs, slide 115/230 VAC input voltage selector switch completely to the left as shown below
left. For use with 208 through 240 VAC inputs, slide the same selector switch completely to the right as shown below right.
SWITCH LADDER CIRCUIT DIAGRAMS
6
“RE” CONTROL PANEL IDENTIFICATION
Note:
An incorrect setting of the input
VAC selector switch will result in
damage to the controller.
115V
230V
START
STOP
P2-13 P2-12
STOP STOP
P2-11
START-STOP
WIRING
MOMENTARY START
SWITCH
MOMENTARY STOP
SWITCH STARTSTOP
P2-13 P2-12 P2-11
START-STOP WIRING
(WITH 3 STATIONS)
Warning:
This diagram is for
"RC" and "RE" versions
ONLY! DO NOT use
on "C" version.

INITIAL START UP
1. Check to see that the 115/230 VAC selection switch is set for the desired input voltage.
2. Recheck all wiring. Accidental grounds, loose or pinched wires on armature or speed potentiometer wires may damage the
control when power is applied.
3. See “ADJUSTMENT PROCEDURE” and observe the WARNINGS pertaining to cover removal for adjustments.
4. Preset trimpots for your horsepower by using the “TRIMPOT CHART”. NOTE: Options may change the trimpot setting from
this chart. If your control has an option, be sure to carefully read the section in “OPTIONS” that pertains to your option.
5. Turn speed potentiometer to zero (fully CCW).
6. Turn power on and advance speedpot while observing motor.
7. If motor rotation is incorrect, turn power off at external disconnect and reverse the +ARM and -ARM connections.
8. If operation is satisfactory, no re-adjustments are needed.
9. If instability or surging is observed, or if maximum speed is higher than desired, proceed to “ADJUSTMENT PROCEDURE”.
10. For other problems, see section “IN CASE OF DIFFICULTY”.
7(Adjustment procedure continued)
WARNING:
WHEN MAKING AN ADJUSTMENT, ALWAYS USE A SCREWDRIVER WITH AN INSULATED SHAFT TO AVOID THE
SHORT CIRCUITING OF PC BOARD COMPONENTS. WHENEVER THE CONTROL COVER IS REMOVED, IT MUST BE
SUPPORTED TO AVOID ACCIDENTAL CONTACT BETWEEN CONTROL CHASSIS AND LIVE COVER COMPONENTS.
TRIMPOT ADJUSTMENT PROCEDURE
Four adjustments (MIN., MAX., I.R. COMP., and CUR. LIM.) are checked at the factory using a typical motor. Use the “TRIMPOT
CHART” to adjust the trimpots to the approximate setting for your horsepower. The other two adjustments (ACCEL and DECEL),
are the Acceleration and Deceleration adjustments and should be set for your particular application requirements. The “TRIMPOT
CHART” is approximate and is valid when using a speedpot or a 0 to 12VDC input signal to control the speed. Operation of the control
beyond ±10% of normal line voltage is not recommended and could result in readjustments. These settings are permanent; periodic
readjustment is normally not needed. (NOTE: Use only an ungrounded voltmeter).
MAX.
Sets maximum motor speed when speedpot is at 100% CW rotation. Clockwise rotation increases maximum
motor speed.
1) Turn drive power OFF!
2) Connect a DC voltmeter; plus to +ARM and minus to -ARM.
3) Set meter voltage range for either 90 VDC or 180 VDC.
4) With no load on the motor, adjust the MAX trimpot to the rated armature voltage as seen on the meter.
NOTE: A tachometer or strobe may be used in place of a meter. Follow the above steps, but adjust the MAX trimpot
to the rated motor base speed, indicated by tach or strobe.
MIN.
Sets minimum motor voltage when Speedpot is set at zero. Clockwise rotation of the MIN. trimpot will in-
crease the minimum motor voltage.
1) Set Speedpot to zero (fully CCW).
2) With no load on the motor, adjust the MIN trimpot clockwise until the motor starts to rotate.
3) Slowly back off the trimpot in the CCW direction until the motor stops.
NOTE: If motor rotation is desired at zero Speedpot setting, adjust the MIN trimpot clockwise until the desired
minimum speed is reached.
I.R. COMP.
Provides a means of improving speed regulation in the armature feedback mode. If a change in motor speed
during a load change is of no concern, rotate this trimpot fully CCW.
1) Set speedpot at 50%.
2) Observe motor speed during a no load condition.
3) Apply a full load to the motor.
4) Adjust the I.R. COMP. trimpot clockwise (while the load is applied) until the no load motor speed is obtained.

CUR. LIM.
Limits DC motor armature current (torque) to prevent damage to the motor or control. The current limit is
set for 125% of the rated motor current. Clockwise rotation of this trimpot increases the armature current
(or torque produced).
1) Turn drive power OFF!
2) Connect a DC Ammeter in series with the +ARM line (between +A on motor and +ARM on the control). Preset the
current limit trimpot CCW.
3) Turn power on and set speedpot to 50%.
4) Increase the motor load until the motor stalls (zero RPM).
5) Set CUR. LIM. trimpot by adjusting CW to 125% of the rated motor armature current (see “TRIMPOT CHART”).
ACCEL
Allows adjustment of acceleration by user.
1) Clockwise trimpot rotation increases length of acceleration time needed for the control to reach full speed.
DECEL
Allows adjustment of deceleration by user.
1) Clockwise trimpot rotation increases length of deceleration time needed for the control to reach zero speed.
8
(Adjustment procedure continued)
MIN ACCEL DECEL MAX I.R. CUR LIM HP VOLTS
1/8115
1/6 115
1/4 115
1/3 115
1/2 115
3/4 115
1.0 115
1/4 230
1/3 230
1/2 230
3/4 230
1.0 230
1.5 230
2.0 230
NOTES: These settings apply when usinga 5000Ωspeedpot. This chart cannot be used with certain Options (refer to Option section)
3.0 230
MIN ACCEL DECEL MAX I.R. CUR LIM HP VOLTS
1.5 115
TRIMPOT SETTING CHART
1.5 and 3.0 HORSEPOWER - MODEL 533BC
For 1.5 and 3.0 horsepower applications, the model 533BC control has the following restrictions:
●Available in chassis (C) mount only.
●The 1.5 horsepower model is available in 115 VAC input at 0-90 VDC out, while the 3.0 horsepower model is available in
230 VAC input at 0-180 VDC out.
●Relay, start-stop, reversing, dynamic braking & jogging are not available from factory (they are customer supplied and wired).
●The isolation boards (-5 and -7 options) are available.

9
BASIC HOOK-UP DIAGRAMS WITHOUT OPTIONS
(If options are included on your control, see the option section of this manual).
PILOT RELAY SWITCHING
(Customer supplied wiringfor the “530BRC” version)
-10 -11 -12 -13
P2
MOMENTARY ON-OFF SWITCH(ES)
N.C.
STOP
N.O.
START
After loss of incomingAC power, unit
will not restart until start switch is closed.
-10 -12 -13
P2
SPST SWITCH*
Unit will self-start
when switch is closed.
-11 A jumper wire may
be used in place of
the SPST switch. If
wired with a jumper,
the control will always
be on whenever AC in-
put voltage is applied.
-10 -12 -13
P2
OPTIONAL PILOT LAMP
Pilot Lamp
(rated for
line voltage).
-11
115V
P3 PROVIDES SUPPORT
AND TRIGGERING FOR
OPTIONS
OVER CUR OUT
AMP REF
POT LO
POT WIPER
POT HI
REV 1
START
red
orange white
SPEEDPOT
MIN
ACCEL
DECEL
MAX
IR COMP
CUR LIM
-13-12-11-10-9-8-7-6-2-1
P2
P1
EARTH
GROUND
VAC INPUT
VAC INPUT
DC MOTOR
OPTIONAL:
FOR SHUNT
WOUND
MOTORS ONLY
+-
FUSES
RELAY
-1
-2
-3
-4
-5
-6
-7
AC (N)
+ARM
-ARM
-FIELD
+FIELD
GND
AC (L)
-5-4-3
= customer supplied wiring
= factory supplied wiring
SPARE
REV 2
JUMPER WIRE (JU2)
PILOT LAMP
STOP
COMMON
+TACH
INPUT
VOLTAGE
SELECTOR
SWITCH
not active on
C version
Model 530BC and 533BC ("C Version")
115V
NOTE:
FOR HOOK-UP OF CUSTOMER PROVIDED
PILOT RELAY SWITCHING(see diagram below)
P3
PROVIDES SUPPORT
AND TRIGGERING FOR
OPTIONS
OVER CUR OUT
AMP REF
POT LO
POT WIPER
POT HI
REV 1
START
red
orange white
SPEEDPOT
MIN
ACCEL
DECEL
MAX
IR COMP
CUR LIM
-13-12-11-10-9-8-7-6-2-1
P2
P1
EARTH
GROUND
VAC INPUT
VAC INPUT
DC MOTOR
OPTIONAL:
FOR SHUNT
WOUND
MOTORS ONLY
+-
FUSES
RELAY
RELAYS
-1
-2
-3
-4
-5
-6
-7
AC (N)
+ARM
-ARM
-FIELD
+FIELD
GND
AC (L)
-5-4-3
= customer supplied wiring
= factor
y
su
pp
lied wirin
g
SPARE
REV 2
JUMPER WIRE (JU2)
PILOT LAMP
STOP
COMMON
+TACH
INPUT
VOLTAGE
SELECTOR
SWITCH
Model 530BRC ("RC Version")

NOTE: Jumper wires may be required on terminal strip P2 for the control to operate (refer to jumper chart below).
As explained in the “COMMONLY ASKED QUESTIONS” section, REV 1 (P2-7) and REV 2 (P2-8) are both stop inputs. One of
these inputs must be held low to AMP REF (P2-2) for the control to operate. Jumpering is necessary between AMP REF and REV
1 or REV 2 to satisfy the “OR” gate. An option board may be installed on the control satisfying the “OR” gate. This jumper (between
P2-2 and P2-7) is called JU2. For inhibiting with soft start and fast stop, the JU2 jumper may be replaced by a SPST switch.
YES = JUMPER REQUIRED NO = JUMPER NOT USED
OPTION DESCRIPTION PAGE # JUMPER “C” “RC” “RE”
NONE STOCK CONTROL 9-10 JU2 YES YES YES
-4 JOG 11 JU2 YES YES YES
-5/-7 CURRENT FOLLOWER 12-13 JU2 YES YES YES
-36M/-38M FWD / REV with ZERO SPEED and D.B.R. 14-15 JU2 NO NO NO
NOTE: Installing JU2 jumper when not required may cause permanent damage to control.
JU2 JUMPER WIRE SELECTION CHART
CONTROL MODIFICATIONS
10 (Continued on following page)
Model 530BRE ("RE Version")
115V
P3 PROVIDES SUPPORT
AND TRIGGERING FOR
OPTIONS
OVER CUR OUT
AMP REF
POT LO
POT WIPER
POT HI
REV 1
START
red
orange white
SPEEDPOT
MIN
ACCEL
DECEL
MAX
IR COMP
CUR LIM
-9-8-7-6-2-1 P2
P1
EARTH
GROUND
VAC INPUT
VAC INPUT
DC MOTOR
OPTIONAL:
FOR SHUNT
WOUND
MOTORS ONLY
+-
FUSES
RELAY
RELAYS
BLACK
RED
WHITE
START
STOP
MOMENTARY
ACTION SWITCH
PILOT
LAMP
-1
-2
-3
-4
-5
-6
-7
AC (N)
+ARM
-ARM
-FIELD
+FIELD
GND
AC (L)
-5-4-3
= customer supplied wiring
= factory supplied wiring
SPARE
REV 2
JUMPER WIRE (JU2)
PILOT LAMP
STOP
COMMON
+TACH
INPUT
VOLTAGE
SELECTOR
SWITCH
-13-12-11-10
BLACK
BLACK
Two pot operation is done usingtwo 10KΩ
speed potentiometers in parallel (both HI’s
to P2-5, both LO’s to P2-3). The WIPER is
switched usinga SPDT switch.
TWO SPEED OPERATION
A DPDT switch is used to inhibit the control and to connect the
DBR. Typical values for the DBR (dynamic brake resistor) are 5
for 115V, 10 for 230V (both 35Ωto 50Ω). Note that motor horse-
power, inertia, and cycle
time effect sizingof the
DBR.
NOTE: On -15A Option,
Decel must be fully CCW
to use with DBR.
DYNAMIC BRAKING
-4
-3
-5
W
HI
LO
W
HI
LO
P2
HI
SPDT
TWO 10K SPEEDPOTS
W
LO
HI
P1
-5
MOTOR
DYNAMIC
BRAKE
RESISTOR
-4
DPDT
+TACH
-7
-6
-4
-3
-5
P2
-8
-9

The customer supplied SPST switch is connected in series
between the speedpot HI (P2-5) and the +TACH terminal
(P2-9). To inhibit, speedpot HI is closed to the +TACH term-
inal. To restart, the switch is returned to open. NOTE: The
control will stop and start fast.
INHIBIT (USED INDEPENDENTLY)
The customer supplied SPST switch is connected
in series between the speedpot HI terminal (P2-5)
and speedpot HI. To inhibit, the SPST switch
contacts are opened. To restart, the switch is
returned to the closed position. NOTE: The control
will soft stop and soft start through the acceleration
setting.
INHIBIT (USED WITH SPEEDPOT)
Improves speed regulation to –1/2% of base speed.
TACHOMETER FEEDBACK
Allows control output to follow tachometer voltage.
TACHOMETER FOLLOWER
NOTE: NEED 1% OR LESS - TACH OUTPUT RIPPLE
NOTE: Permits starting and stopping of motor without breaking AC lines. In the event of SCR failure or false triggering, the
Inhibit circuit will not stop motor.
TACHOMETER
P2-4 POT WIPER
P2-3 POT LO
+
-
12 VDC at FULL SPEEDTACHOMETER
P2-9 +TACH
P1-5 -ARM / AMP REF
+
-
6/12 VDC at BASE SPEED (3/7 VDC
at 1000 RPM for 1800 RPM MOTOR).
Refer to CONTROL FEATURES .
-7
-6
-4
-3
-5
P2
SPST
SPEEDPOT
+TACH
WIPER
LO
HI
-8
-9
-4
-3
-5
P2 SPEEDPOT
WIPER
LO
HI
SPST
“CONTROL MODIFICATIONS” continued
-4 Option See below for installation and availability
Jog
This option is factory installed on the “RE” version only. “S2” is located on the cover and disables the latch circuit of the power relay's,
allowing the power switch to jog the drive. The “C” and “RC” versions use customer supplied switch and wiring, in addition the “C”
version uses a customer supplied relay.
11
OPTIONS
NOTE: All options are specified by a suffix to the model number. This suffix starts with a dash (-). The more popular options are
described on the following pages. When a combination of two or more of these options are used, the wiring procedure is beyond
the scope of this manual. Please contact your Distributor or Representative.
Always use a shielded wire when connecting to the inhibit terminal. The shield should be connected to the -Armature or Common of the control.
P2
-1 -2 -3 -4 -6 -7 -8-9
-5 -12-11
RED
WHITEORANGE
RED
-13
SPEEDPOT BLACK
JU2 JUMPER WIRE *
LO W HI
S2
SPST
SWITCH
NOTES:
For "RE" version, S1, S2
and pilot lamp are
FACTORY PROVIDED.
S1
START
STOP
YELLOW
For "C" and "RC" versions,
S1, S2, and pilot lamp are
CUSTOMER PROVIDED.
* This jumper wire is
not used with some
other options. Consult
factory if more than one
option is being wired.
Using JU2 jumper when
not required may cause
permanent damge to the
control.
WHITE
BLACK
BROWN
BLACK
MOMENTARY ACTION SWITCH
PILOT
LAMP
-10

-13-12-11-10-9-8-7-6-2-1
JUMPER WIRE
(
JU2
)
*
-5-4-3 P2
CURRENT
SOURCE
LINEARITY ADJUSTMENT
+-
P16
250/500
-1 -2
125
(530B SERIES TERMINAL STRIP)
-5 Option Available on “C” and “RC” models only
∗
Isolated 4-20 ma.Signal Follower
Factory or Field installed
12
Setting the Min, Max and Linearity Trimpots.
1. Preset the multi-turn Linearity trimpot on the –5 option board full CW, set the Min trimpot full CCW and set the Max trimpot
at about 50% rotation.
2. Input a 4 ma. current signal to the control and turn the Min trimpot CW to your desired minimum output voltage or to deadband
(the point just before you begin to get an output).
3. Input a 20 ma. current signal to the control and set the Max trimpot to the desired maximum speed setting.
4. With 20 ma. still going to the control, turn the Linearity trimpot CCW until your output speed starts to decrease. Then slowly
turn it back CW until you just reach your maximum speed setting.
For enclosed models use -7 option.
Input impedance: 500 ohms or less
This option replaces the speedpot with a 4-20 ma. signal to control speed. The current signal input can be either grounded or
ungrounded. The board sets on spacers screwed to terminals P1-3, P1-4, and P1-5 on the main board using long screws. The
current source connects to the + and - two position terminal strip (P16-1 and -2) on the -5 option board.
The Linearity trimpot on the -5 option board is set at the factory for proper linearity, however this trimpot may need to
be re-set after tuning the controls Max and Min trimpot settings for your specific application. If needed then refer to the setup
procedure below.
4 to 20 mA .......... -5
DO NOT USE TRIMPOT CHART TO
ADJUST MIN AND MAX TRIMPOTS
ON MAIN BOARD. IF ADJUSTMENT
IS NEEDED THEN REFER TO THE
SETUP PROCEDURE BELOW.
* Note: This jumper wire is not used with some options. Consult factory if more than one option is being wired. Using the JU2 jumper
wire when not required may cause permanent damage to the control.

13
DO NOT USE TRIMPOT CHART TO ADJUST MIN AND MAX
TRIMPOTS ON MAIN BOARD. IF ADJUSTMENT IS NEED
THEN REFER TO THE SETUP PROCEDURE BELOW.
This option allows the control to be run in either the
Manual mode via a speed pot or the Auto mode via the 4-20 ma.
signal. The current signal input can be either grounded or
ungrounded. The board sets on spacers screwed to terminals
P1-3, P1-4, and P1-5on the main board using long screws. The
current source connects to the + and - two position terminal strip
(P16-1 and -2) on the -7 option board.
This option includes a Balance trimpot which is used
to scale the maximum speed in the manual mode. It is factory
set so the maximum speed in manual equals the maximum
speed in automatic.
The Linearity trimpot on the -7 option board is set at the factory for proper linearity, however this trimpot may need to
be re-set after tuning the Max and Min trimpot settings on the control or if the Balance trimpot on the –7 must be reset for your
specific application. If needed then refer to the setup procedure below.
Setting the Min, Max, Balance and Linearity Trimpots.
1. Preset the multi-turn Linearity trimpot and the Balance trimpot on the –7 option board full CW, set the Min trimpot full CCW
and set the Max trimpot at about 50% rotation.
2. Input a 4 ma. current signal to the control and turn the Min trimpot CW to your desired minimum output voltage or to deadband
(the point just before you begin to get an output).
3. Input a 20 ma. current signal to the control and set the Max trimpot to the desired maximum speed setting.
4. Switch the control to the Manual mode setting and adjust the Balance trimpot CCW as needed to attain your required manual
mode maximum output speed. (Adjustable form 50 to 100% of maximum Auto mode setting)
5. Switch the control back to Auto mode. With 20 ma. still going to the control, turn the Linearity trimpot CCW until your
output speed starts to decrease. Then slowly turn it back CW until you just reach your maximum speed setting.
-13-12-11-10-9-8-6-1
JUMPER
WIRE (JU2) *
-5-4-3 P2
SPDT SWITCH
RED
LO
HI
W
RED
from P2-4 of 530B
CURRENT
SOURCE
LINEARITY ADJUSTMENT
+-
P16
BALANCE
ADJUSTMENT
WHITE
RED
ORANGE
SPEEDPOT
250/500
125
-2 -7
MANUAL
AUTO
-1 -2
(530B TERMINAL STRIP)
-11 Option Field installed - ordered as separate item
Ten Turn Speedpot Available on “C” and “RC” models only
Provides for a finer control of speed. Installation is the same as the standard speedpot.
-15A Option Factory installed
Extended Accel / Decel Available on all models
Extends acceleration / deceleration to 30 seconds (linear ramp).
-7 Option Factory or Field installed Chassis unit
Isolated 4-20 ma. Signal Follower
Factory only on Enclosed models
with Auto / Manual Switch Available on all models
* Note: This jumper wire is not used with some options. Consult factory if more than one option is being wired. Using the JU2 jumper
wire when not required may cause permanent damage to the control.
Input impedance equals 500Ωor less 4 to 20 mA .......... -7

P1
P2
-1
-2
-3
-4
-5
-6
-7
-1
-2
MOTOR
A1
A2
AC
AC
-1 -3 -4 -5 -6 -9 -10 -11 -12 -13
-36M / -38M
OPTION
BOARD
530B
SERIES
BOARD
SPEEDPOT
COM
LO
WIPER
HI
P4
P5
TRANSISTOR "A" ON = FWD.
TRANSISTOR "B" ON = REV.
BOTH "A & B" OFF = DYNAMIC BRAKE
BOTH "A & B" ON = DISALLOWED STATE
(CUSTOMER SUPPLIED LOGIC = A & B)
-36M / -38M HOOK-UP FOR NPN OPEN COLLECTOR DIRECTIONAL CONTRO
L
AB
FWD
REV
-1 -2
NOTE:
INPUTS TO TERMINAL STRIP P5 CANNOT
BE REFERENCED TO EARTH GROUND!
WHITE
BROWN
-7 -8
BLACK
-3
-2
The -36M / -38M option automatically
“brakes” to zero speed before reversing.
The SPDT center-off switch is used to
select direction. When the direction is
reversed, relays K1, K2, and K3 connect
the dynamic brake resistor to the arma-
ture. The motor “brakes” and at zero
speed the relays reverse the armature
leads, causing the motor to rotate in the
opposite direction. When the switch is in
the center (STOP) position, the motor
armature is connected to the dynamic
brake resistor.
Notes: The start-stop switch is customer
provided on the “RC” version (see Hook-
up Diagrams for switch wiring). The “RE”
version requires a special cover that
must be ordered for field installed -36M
or -38M options. The Dynamic Brake
Resistor is mounted accordingly per
model (see above chart for placement).
VERY IMPORTANT:
DO NOT USE JU2 JUMPER WIRE with
this option. WHEN RETROFITTING,
JU2 JUMPER MUST BE REMOVED!!
-36M / -38M Option
Forward / Reverse with Zero Speed Factory or Field installed - see below
Detect and Dynamic Brake Available on all models except 3 H.P.
Option AC Input Installed DBR Value DBR location / placement
-36M 115VAC factory or field 5Ω30W option board mounted
-36MA 115VAC factory only 5Ω50W extrusion mounted
-38M 230VAC factory or field 10Ω30W option board mounted
-38MA 230VAC factory only 10Ω50W extrusion mounted
Warning: The addition of this option no longer allows for dual voltage operation of the 530B series board. The 115/230 VAC
input selector switch (530B series board) must be set for the proper VAC input rating of the -36M/-38M option being used.
-36M / -38M HOOK-UP USING SPDT SWITCH OR CONTACT
(-36M / -38M option continued)
14
IMPORTANT:
DO NOT
use JU2 jumper wire with this option.
When retrofitting, JU2 must be removed.
Warning:
The addition of this option no longer al-
lows for dual voltage operation of the 530B
series board. The 115/230 VAC input se-
lector switch (530B series board) must be
set for the proper VAC input rating of the
-36M/-38M option being used.
To identify JU2 jumper location, see “Ba-
sic Hook-up Diagrams Without Options”.
To identify JU2
jumper location,
see “Basic Hook-
up Diagrams With-
out Options”.
P1
P2
-1
-2
-3
-4
-5
-6
-7
-1
-2
MOTOR
A1
A2
AC
AC
-1 -3 -4 -6 -9
-36M / -38M
OPTION
BOARD
530B
SERIES
BOARD
LO
WIPER
HI
P4
P5
REV
-3
COM
FWD
-5 -12-11-10
RED
WHITE
BLACK
WHITEORANGE
RED
-13
BLACK
SPEED
POT
NOTE:
INPUTS TO TERMINAL STRIP P5 CANNOT BE REFERENCED TO EARTH GROUND!
-1 -2
brake
WHITE
BROWN
BLACK
-7 -8-2
reverse
forward
SPDT CENTER-OFF SWITCH
The switch is switching
+5 volts at 0.1mA.
Customer supplied switch
contacts should be rated
for this duty.
Terminal strip
positions P2-11,
P2-12, and P2-13
are innactive on
the C version.
DPDT MOMENTARY
ACTION SWITCH
(one normally open
and one normally
closed contact)
PILOT LAMP
RC* and RE versions only! All components located
inside dashed line are not applicable on C version.
* on RC version, customer su
pp
lies switchin
g
and wirin
g

P1
P2
-1
-2
-3
-4
-5
-6
-7
-1
-2
MOTOR
A1
A2
AC
AC
-1 -3 -4 -5 -6 -9 -10 -11 -12 -13
-36M / -38M
OPTION
BOARD
530B
SERIES
BOARD
SPEEDPOT
LO
WIPER
HI
P4
P5
-36M / -38M HOOK-UP FOR UNIDIRECTIONAL RUN / DYNAMIC BRAKE
REV
-1 -3-2
COM
FWD
NOTE:
INPUTS TO TERMINAL STRIP P5 CANNOT
BE REFERENCED TO EARTH GROUND!
WHITE
BROWN
-7 -8
SPST
SWITCH
CLOSED = RUN
OPEN = BRAKE
BLACK
-2
(-36M / -38M option continued)
FUSING
The motor and control are protected against overloads by the current limit circuit. Additional protection is provided through 2 fuses,
which are mounted on the main board. Use exact fuse replacements if the fuse requires changing. Before changing fuses, be sure
the power to the control is disconnected at the power source. Note: Both sides of VAC input are fused.
HP: 1/8 - 2.0 H.P. FUSE SIZE: 20 Amp FUSE TYPE: Bussman ABC-20 or Little Fuse 314020
HP: 3.0 H.P. FUSE SIZE: 20 Amp FUSE TYPE: Bussman ABC-20 or Little Fuse 314020
15
Warning:
The addition of this option no longer al-
lows for dual voltage operation of the 530B
series board. The 115/230 VAC input se-
lector switch (530B series board) must be
set for the proper VAC input rating of the
-36M/-38M option being used.
IMPORTANT:
DO NOT
use JU2 jumper wire with this option.
When retrofitting, JU2 must be removed.
To identify JU2 jumper location, see “Basic
Hook-up Diagrams Without Options”.
IN CASE OF DIFFICULTY
PROBLEM POSSIBLE CAUSE(S) CORRECTIVE ACTION(S)
Motor doesn’t operate
Armature output voltage
cannot be adjusted, out-
put is a constant DC level
Motor stalls or runs
very slowly with speed
control turned fully CW
Motor hunts
Repeated fuse blowing
Motor runs but will not stop
Replace fuse
Install proper service
Adjust speedpot CW to start
Replace motor brushes
See “JU2 Jumper Wire Selection Chart”
Check that the motor or load is connected
to Armature terminals
Check that speedpot low wire is connected
Should be above 104V or 208V
Reduce load or re-adjust Current Limit
Replace motor brushes
See “Adjustment Procedure”
See “Adjustment Procedure”
See “Adjustment Procedure”
Reduce Max trimpot setting
Reduce load
Relace motor brushes
Replace motor
Return for repair
Check “Terminal Strip Wiring” sections
Check wiring
Return for repair
Blown fuse
Incorrect or no power source
Speedpot set at zero
Worn motor brushes
Improper or missing jumpers
No motor or load connected
Speedpot low connection open
Low voltage
Overload condition
Worn motor brushes
Max. speed set incorrectly
Too much IR Comp
Motor is in Current Limit
Motor speed is above rated speed
Overload condition
Worn motor brushes
Defective motor
Failed electrical components
Incorrect wiring
Defective wiring
Failed component
After using this section, if control will still not operate, consult your Dart Distributor or Representative or return unit for repair.

WIDTH LENGTH DEPTH WEIGHT TYPE
ENGLISH 6.70"
6.70"
6.70"
9.00"
9.00"
10.00"
2.25"
2.25"
4.75"
40 oz.
41 oz.
56 oz.
C
RC
RE
171 mm
171 mm
171 mm
229 mm
229 mm
254 mm
51 mm
57 mm
121 mm
1134 gm.
1162 gm.
1422 gm.
C
RC
RE
METRIC
AC INPUT VOLTAGE ....................................................................................................................... ±10% of rated line voltage
ALTITUDE .............................................................................................................................. Up to 7,500 feet above sea level
CONTROL OVERLOAD CAPACITY ............................................................................................................. 200% for 1 minute
DIMENSIONS & WEIGHTS:
DRIVE SERVICE FACTOR ..................................................................................................................................................... 1.0
EFFICIENCY ............................................................................................................................................................. 85% typical
ELECTRICAL SPECIFICATIONS - TYPICAL CURRENT & HORSEPOWER RANGES:
FUSE PROTECTION ................................................................................................................. 2 AC line fuses (see "Fusing")
HUMIDITY ................................................................................................................................................. 99% non-condensing
INPUT FREQUENCY ............................................................................................................................................ 50 or 60 Hertz
MAXIMUM ARMATURE CURRENT - CONTINUOUS ......................................................... 10 ADC (2 H.P.); 15 ADC (3 H.P.)
PILOT LAMP (“RE” VERSION) ........................................................................................................................................... Neon
POWER DEVICES ........................................................................................................................... Packaged full wave bridge
SHUNT FIELD VOLTAGE .......... 100VDC for 115VAC in; 200VDC for 230VAC in; (1.0 A max. - 530B; 1.5 A max. - 533B)
SPEED CONTROL ......................................................................... Via 5KΩΩ
ΩΩ
Ω Potentiometer OR 0 to +10 VDC isolated signal
SPEED RANGE .................................................................................................................................................................... 50:1
SPEED REGULATION ................................................................................................................................. ±1% of base speed
TACHOMETER FEEDBACK ................................................................................ jumper selectable 3V or 7V per 1000 RPM
TEMPERATURE RANGE ............................................................................................. -10° to 45° C. ambient (15° to 115° F.)
TRANSIENT VOLTAGE PROTECTION ............................................................................................................................ G-Mov
TRIMPOTS:
ACCELERATION RANGE ................................................................................................... 0.3 to 12 seconds - adjustable
CURRENT LIMIT RANGE ......................................................................................................... 1 to 20 Amps (1/8 to 2 H.P.)
CURRENT LIMIT RANGE ...................................................................................................... 2 to 30 Amps (1.5 and 3 H.P.)
DECELERATION RANGE ................................................................................................... 0.6 to 12 seconds - adjustable
I.R. COMPENSATION RANGE .................................................................................... 1/8 through 2.0 h.p. (530B controls)
I.R. COMPENSATION RANGE ............................................................................................. 1.5 and 3.0 h.p. (533B control)
MAXIMUM SPEED RANGE ..................................................................................................... 60% to 120% of base speed
MINIMUM SPEED RANGE ..................................................................................................... 0 to 30% of maximum speed
TYPE RAMP OF ACCEL / DECEL .................................................................................................................................... Linear
SPECIFICATIONS
16
MAX AC AMPSH.P. MAX ARM AMPS MAX AC AMPS MAX ARM AMPS
1/8
1/6
1/4
1/3
1/2
3/4
1.0
1.5
2.0
3.0
1.80
2.60
3.50
4.40
6.50
9.30
13.20
21.50
--------
--------
1.40
2.10
2.70
3.40
5.00
7.20
10.20
14.70
-------
-------
------
------
1.80
2.20
3.30
4.80
6.50
9.70
12.90
22.00
------
------
1.40
1.70
2.50
3.70
5.00
7.50
9.90
15.00
115VAC INPUT / 0-90VDC OUTPUT 230VAC INPUT / 0-180VDC OUTPUT

17
530B SERIES PARTS PLACEMENT & LIST
R4
R3
R5
R9
C2 ++
C1
C7
C10+
C12
+
C11+
CR3
CR2
SW1
T1
D12
CR1
C3
C6 C4
C5
D11
D9
D10
D2
D1
R15
++
C13
C14
JU1
JU5
115V
1 2 3 4
5 6 7 8
JU3
CN1 JU6
R43
RESISTORS
CAPACITORS
MISCELLANEOUS
ACTIVE DEVICES
DIODES
R1
R2
R3
R4
R5
R6
R7
R8
R9
R10
R11
R12
R13
R14
R15
R16
R17
R18
R19
R20
R21
R22
R23
R24
R25
R26
R27
R28
R29
R30
R31
R32
R33
R34
R35
R36
R37
R38
R39
R40
R41
R42
R43
220K
5K TRIM (MIN)
47K
300K
10K
4.7K
250K TRIM (ACCEL)
1K
27K
4.7K
250K TRIM (DECEL)
1K
47K
4.7K
47Ω1/2W
91K 1/2W
180K 1/2W
470Ω
47K
6.8K
300K
1K
47K
470K
10K
680K
22K
2.2K
1K
220K
390Ω
390Ω
39K
1K TRIM (CUR)
2.2K
470Ω
50K TRIM (MAX)
100ΩTRIM (I.R.)
.SEE BELOW
100K
SEE BELOW
33K
100K
C1
C2
C3
C4
C5
C6
C7
C8
C9
C10
C11
C12
C13
C14
.01µF 63V
1µF 50V N.P.
.01µF 400V
.01µF 400V
.068µF 250VAC
.01µF 400V
.01µF 63V
NOT USED
.22µF 250V
150µF 16V
47µF 16V
470µF 50V
1µF 50V N.P.
.1µF 63V
D1
D2
D3
D4
D5
D6
D7
D8
D9
D10
D11
D12
D13
D14
D15
D16
S6A4
S6A4
1N4005
1N4005
1N914B
1N5233B
1N914B
1N5242B
1N4005
1N5233B
1N4005
1N4005
1N914B
1N4005
1N4005
1N4005
Q1
Q2
U1
U2
U3
U4
2N4124
LM78L12 REG.
LM358 IC
LM324 IC
3052 MOC
L512F BRIDGE
CN1
CR1
CR2
CR3
F1
F2
JU1
JU2
JU3
JU5
CT60R16USB CONNECTOR
T73 RELAY
SEE BELOW
SEE BELOW
20A FUSE
20A FUSE
SEE BELOW
WC16WH2.5SL JUMPER WIRE
(SEE MANUAL “JUMPER WIRES”)
3 POS. MALE CONN. W/JUMPER
SEE BELOW
ALL RESISTORS 1/8W UNLESS SPECIFIED.
U1
R2 R7 R11 R37 R38 R34
F1
Q1
C9
P2-13
P2-12
P2-11
P2-10
P2-9
P2-8
P2-6
P2-5
P2-4
P2-3
P2-1
D3
MOV1
P1-1 P1-2 P1-3 P1-4 P1-5 P1-6 P1-7
R39
U4
P2-7
P2-2
JU2
R8 R12 R36
R27
R35
R25
R1
R24
R20
R19
R42
R32
R31
R33
R6
R13
R14
D4
D6
D5
R10
U2
R28
R21
D7
U3
R30
R22
D13
D15
Q2
F2
D14
MOV3
MOV2
R17 R16
D8
D16
R18
P3
MIN ACCEL DECEL MAX I.R. COMP CUR LIM
GND AC AC +ARM -ARM -FIELD +FIELD
R41
R26
R40
R23
+3V
R29
530BC CHANGES:
CR2
CR3
JU1
JU5
R39
R41
NOT USED
NOT USED
RLB2503S RAIL
RLB2503S RAIL
.015Ω5W
1K 1/2W
+7V
JU6
MOV1
MOV2
MOV3
PCB
P1
P2
P3
SW1
T1
WC16GN3.5 WIRE
275V G-MOV
275V G-MOV
275V G-MOV
A-4-2563C PRINTED CIRCUIT
7 POS. TERMINAL STRIP
13 POS. TERMINAL STRIP
1/4" MALE SPADE PIN
115/230VAC SWITCH (DPDT)
DST428 TRANSFORMER
530BRC CHANGES:
CR2
CR3
JU1
JU5
R39
R41
T9A RELAY
T9A RELAY
NOT USED
NOT USED
.015Ω5W
NOT USED
530BRE CHANGES:
CR2
CR3
JU1
JU5
R39
R41
T9A RELAY
T9A RELAY
NOT USED
NOT USED
.015Ω5W
NOT USED
533BC CHANGES:
CR2
CR3
JU1
JU5
R39
R41
NOT USED
NOT USED
RLB2503S RAIL
RLB2503S RAIL
.005Ω5W
1K 1/2W
-6 OPTION CHANGES
C9
D13
R30
.033µF 400V
NOT USED
10K
-15A OPTION CHANGES
R13 180K

18
530B SERIES SCHEMATIC
AC2
SW
AC1
SW
8
4
+12V
WIPER
P2-4
+12V
3
2
1
+
-
6
5
7
+
-
R5
10K
R6
4.7K
ACCEL
R7
250K
R8
1K
C1
.01µF
63V
R12
1K
R9
27K
Q1
2N4124
DECEL
R11
250K
R10
4.7K D3
D4
D6
1N5233B
R14
4.7K
R13
47K
D5
1N914B
REV1
P2-7
REV2
P2-8
C2
1µF
50V N.P.
1-2
1-1
R4
300K
LO
P2-3
HI
P2-5
MIN
R2
5K
R3
47K
SPEED
POT
5K
9
10
8
+
-
2-3
12
13
14
+
-
2-4
4
L512F
4
L512F D11
1N4005 D12
1N4005
+ARM
P1-4
-ARM
P1-5
MOTOR
R17
180K
1/2W
R35
2.2K
R36
470W
MAX
R37
50K
R27
22K
4
L512F
R39
.015W
5W
AMP REF
R28
2.2K
D13
1N914B
C9
.22µF
250V
R29
1K
P2-1
C10
150µF
16V
R32
390W
R31
390W
C R LIM
R34
1K
4
L512F 4
L512F
AC2
AC1
OVER
C R. O T
P2-2
P2-9
+TACH
1N4005
C4
.01µF
400V
C6
.01µF
400V
MOV2
275V
G-MOV
C5
.068µF
250VAC
R16
91K
1/2W
C3
.01µF
400V
R15
47ý
1/2W
MOV1
275V
G-MOV
IR COMP
R38
100W
-FIELD
P1-6
SW
SW
R30
220K
R33
39K
+12V
R23
47K
R1
220K
R26
300K
+12V
1
2
3
3052 MOC
64
3
3052 MOC
5
6
7
-
+
2-2
R22
1K
P3
TRIGGER
1/4"
SPADE
3
2
1
-
+
2-1
4
11
+12V
R20
6.8K
R19
47K
+12V
R25
10K
R24
470K
C7
.01µF
63V
R21
300K
+12V
R18
470W
+NF
D8
1N5242B
AC2
SW
D1
S6A4
D2
S6A4
AC1
SW
MOV3
275V
G-MOV
D9
1N4005
D10
1N5233B
+FIELD
P1-7
-FIELD
+12V
D7
1N914B
CR3
CR2
CR1
F1
F2
AC2
AC1
P2-13
N.O.
N.C.
P2-12 P2-11
RE Version = factory supplied
RC Version = customer supplied
C Version = relay contacts are
replaced with jumper rails
AC2
AC1
SW
SW
P2-10
115VAC
NEON
LAMP
RE1
SW1
115/230VAC DPDT
SLIDE SWITCH
RE2 RE3
T73 T9A T9A
T1
DST428
+NF
D14
1N4005
D15
1N4005
C11
47µF
16V
+12V
C12
470µF
50V
Q2
LM78L12
D16
1N4005
P1-3
P1-2
P1-1
P2-6
N.C.
35
35
ccw ccw
ccw
CCW
CCW
CCW
in out
T9A
T9A
T73
-FIELD
R42
33K
J 3
C14
.1µF
63V C13
1µF
50V
R40
100K
R41
1K
1/2W
C
VERSIONS
ONLY
J 5 - C VERSIONS ONLY
J 1 - C VERSIONS ONLY
J 1
C VERSIONS ONLY 3V7V
J 4
J 6
R43
100K
R39
.005W
5W
533BC
VERSION
ONLY

In the event that a Product manufactured by Dart Controls Incorporated (DCI) is in need of
repair service, it should be shipped, freight paid, to: Dart Controls, Inc., 5000 W. 106th Street,
Zionsville, IN. 46077, ATTN: Repair Department.
ThoseordersreceivedfromanyonewithoutandexistingaccountwithDCIwillneedtospecify
if they will be paying COD or Credit Card (Master Card or Visa). This information is required
beforeworkcanbegin. IfyouhaveanaccountwithDartyourorderwillbeprocessedaccording
to the terms listed on your account.
Completedrepairsarereturned with aRepairReport that statestheproblem with thecontrol
andthepossiblecause.RepairordersarereturnedviaUPSGroundunlessotherarrangements
aremade.Ifyouhavefurtherquestionsregardingrepairprocedures,contactyourDartControls,
Inc. at 317-733-2133 Ext.460.
REPAIR PROCEDURE
Dart Controls, Inc.
Manufacturer of high qual-
ity DC and AC motor speed
controls and accessories
since 1963.
P.O. Box 10
5000 W. 106th Street
Zionsville, Indiana 46077
Phone: (317) 733-2133
Fax: (317) 873-1105
Indiana)productionandhead-
quarters facility - with over
2,000,000variablespeedunits
in the field.
In addition to the standard off-
the-shelfproducts,youcanse-
lect from a wide variety of op-
tions to customize controls for
your specific application. For
further information and appli-
cationassistance,contactyour
local Dart sales representa-
tive, stocking distributor, or
Dart Controls, Inc.
Dart Controls, Inc. is a de-
signer, manufacturer, and
marketer of analog and dig-
italelectronicvariablespeed
drives, controls, and acces-
sories for AC, DC, and DC
brushless motor applica-
tions.
Shown above is just a sam-
pling of the expanded line of
Dart controls that feature the
latestinelectronictechnology
andengineering.Productsare
manufacturedintheU.S.A.at
our Zionsville (Indianapolis,
YOUR MOTION SYSTEMS SOLUTION PROVIDER
700/COMMUTROLSERIES
DC BRUSHLESS
5 & 20 Amp for
12,24,& 36VDC Inputs
250G SERIES
AC INPUT - VARIABLE DC OUTPUT
1/50 HP through 2.0 HP
65 SERIES
DC INPUT - VARIABLE DC OUTPUT
CURRENT RATINGS OF 20, 40, AND
60 AMPS
DM SERIES
FIELD PROGRAMMABLE
DIGITAL TACHOMETER
MDP SERIES
PROGRAMMABLE
CLOSED LOOP DC
SPEED CONTROL
125D SERIES
AC INPUT - VARIABLE DC OUTPUT
1/50 HP through 1.0 HP
www.dartcontrols.com
ISO9001:2000 REGISTERED
This manual suits for next models
9
Table of contents
Other DART Controls DC Drive manuals
Popular DC Drive manuals by other brands

Reliance electric
Reliance electric FlexPak 3000 instruction manual
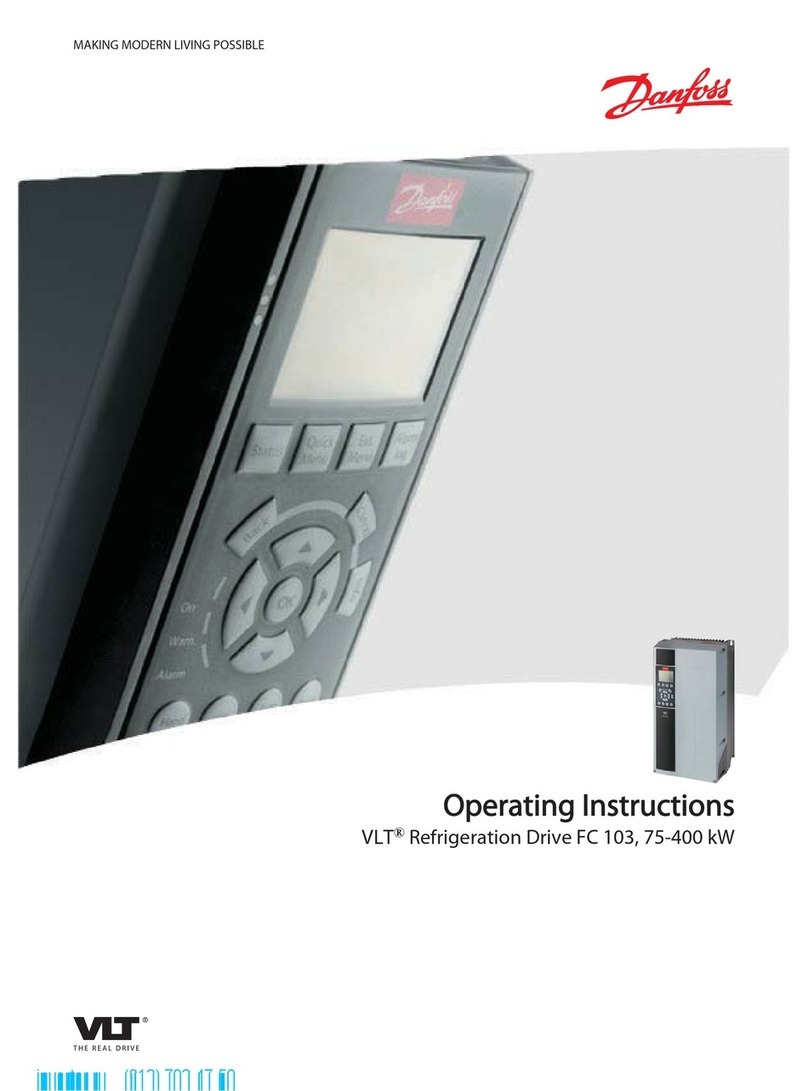
Danfoss
Danfoss VLT FC 103 operating instructions
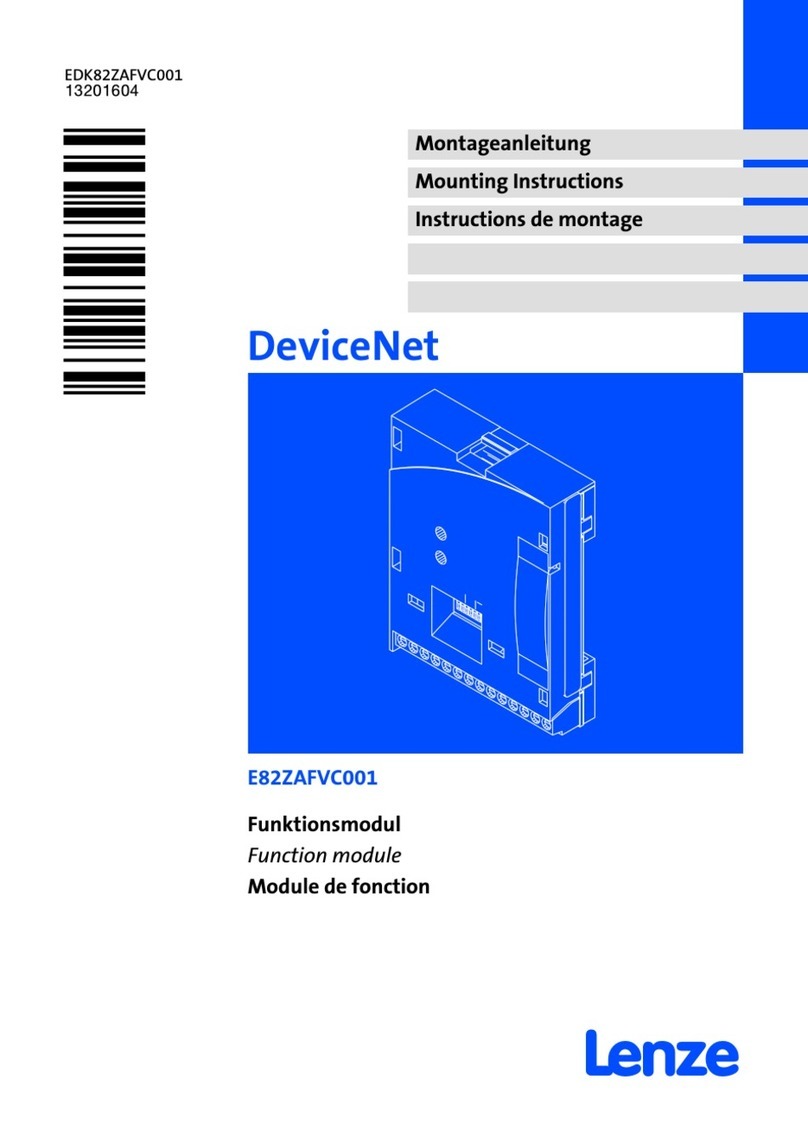
Lenze
Lenze E82ZAFVC001 Mounting instructions
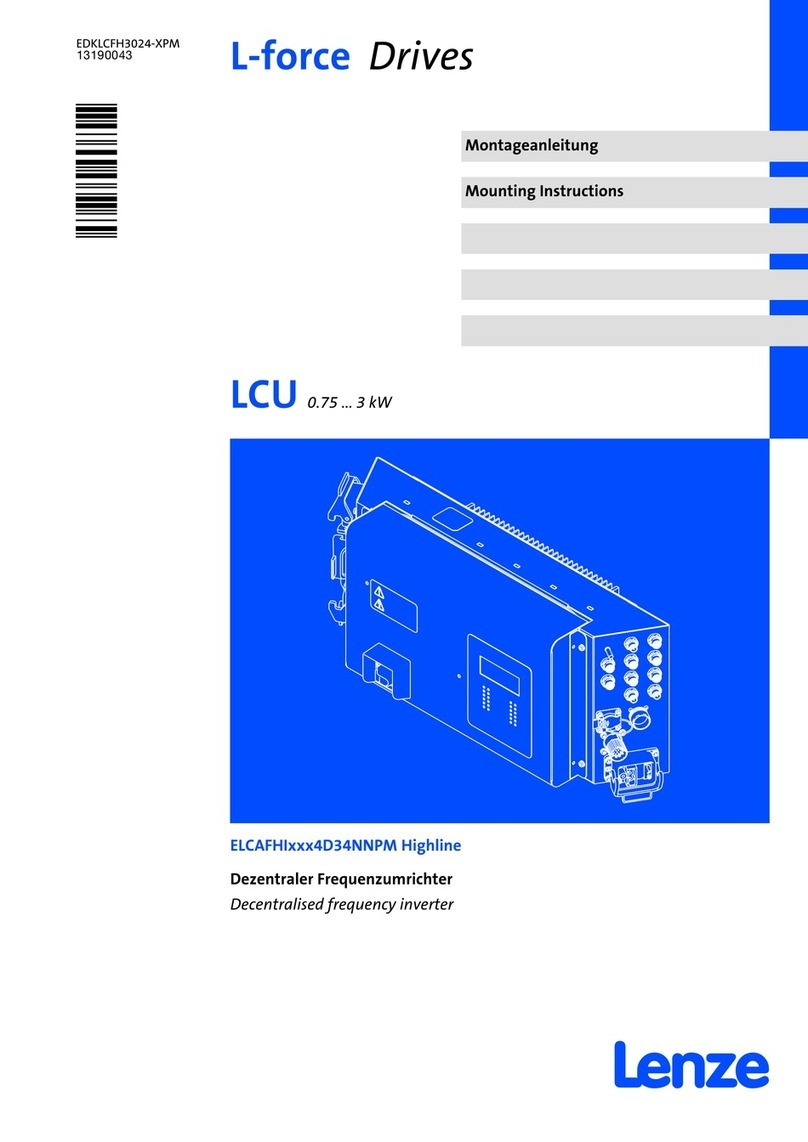
Lenze
Lenze L-force LCU Mounting instructions
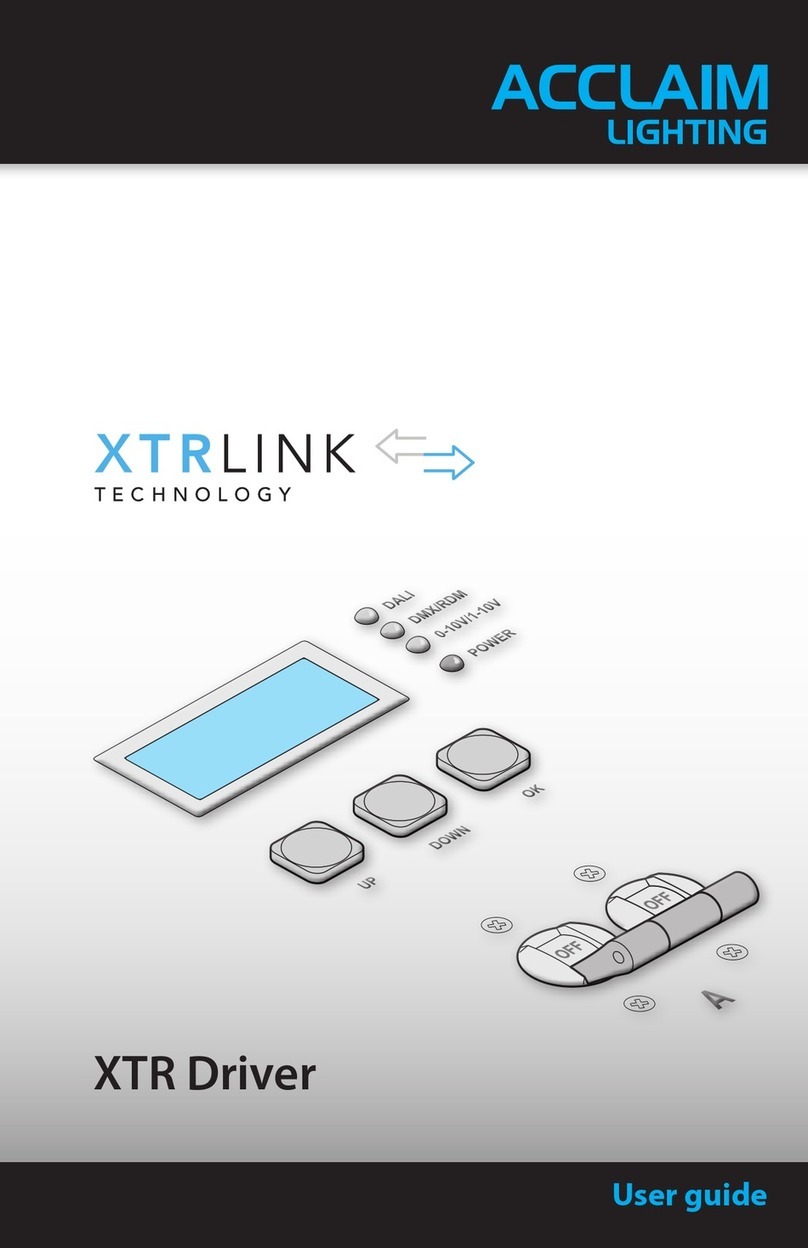
Acclaim Lighting
Acclaim Lighting XTR Driver user guide
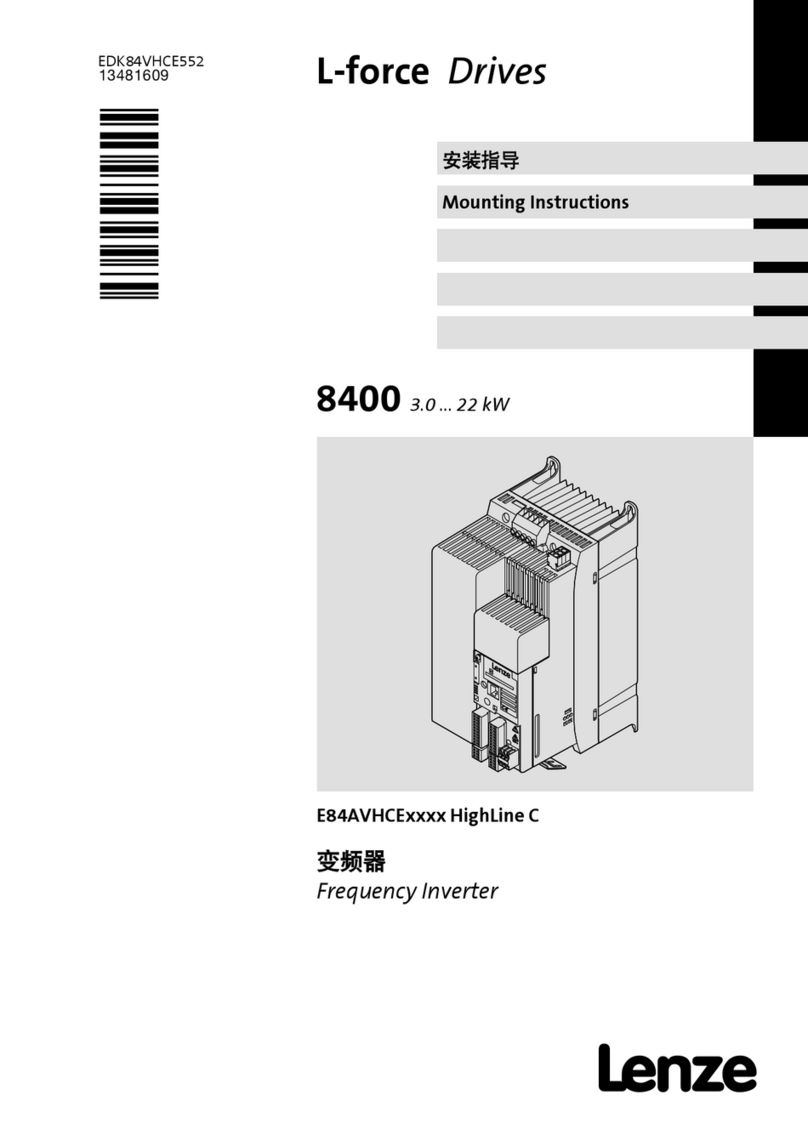
Lenze
Lenze L-force 8400 Series Mounting instructions

SEW-Eurodrive
SEW-Eurodrive MOVI-SWITCH 1E operating instructions
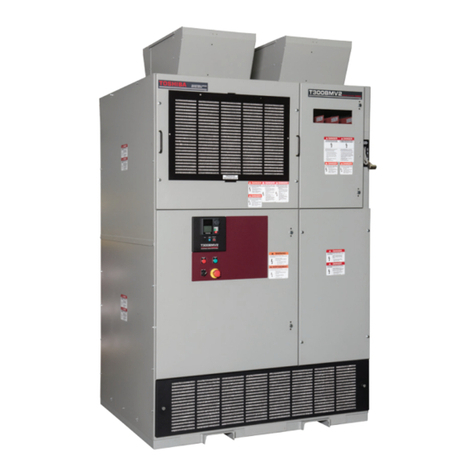
Toshiba
Toshiba T300BMV2 instruction manual
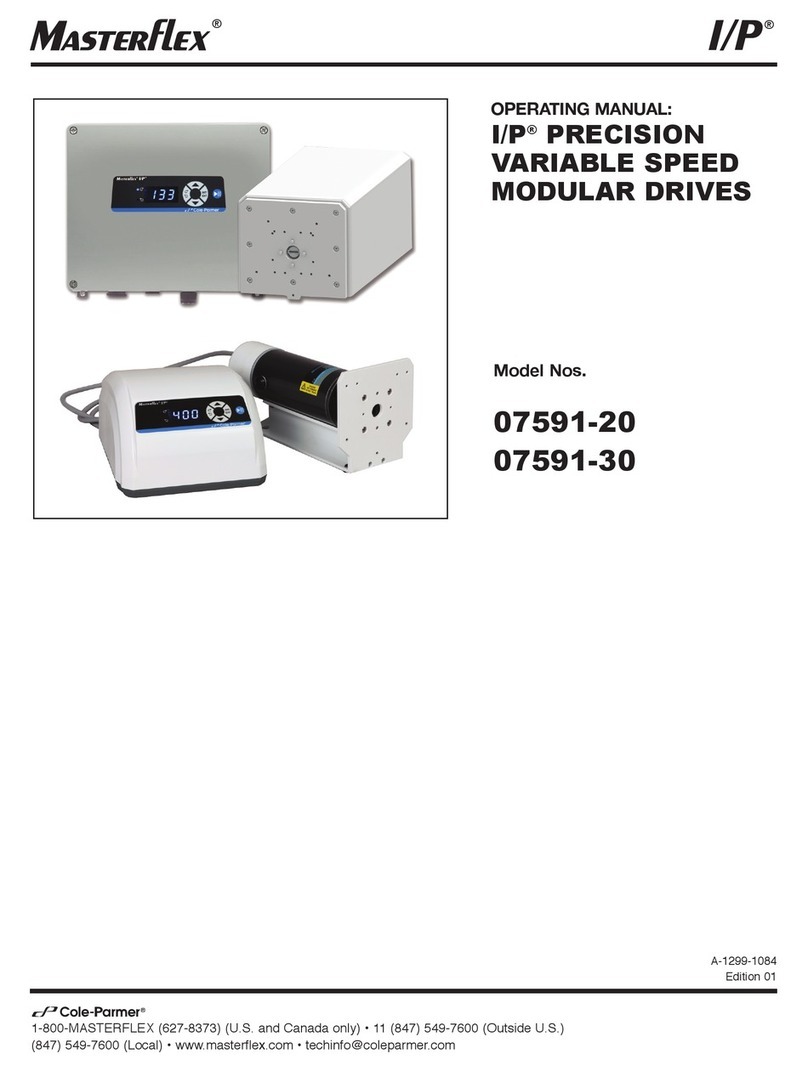
Cole Parmer
Cole Parmer Masterflex 07591-20 operating manual
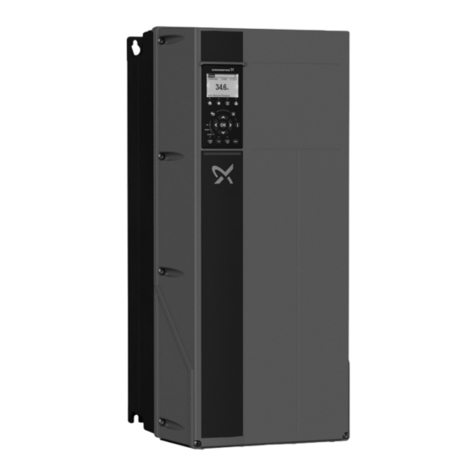
Grundfos
Grundfos CUE Installation and operating instructions
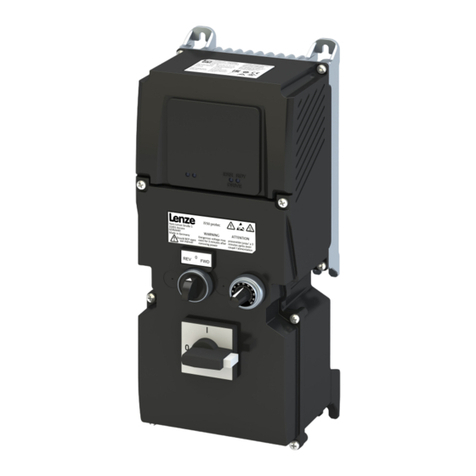
Lenze
Lenze EZAMBHXX028 Mounting instructions
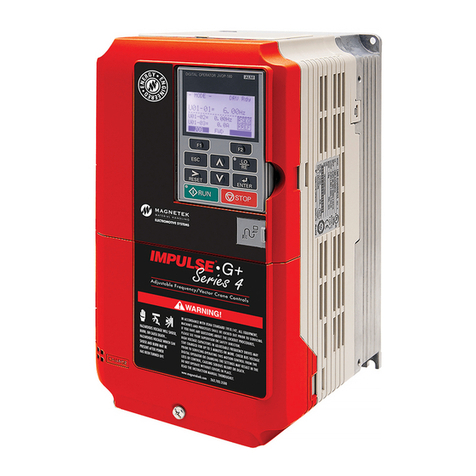
Magnetek
Magnetek Impulse G+ series 4 quick start guide