Interroll RollerDrive EC5000 AI User manual

INSPIRED BY EFFICIENCY
Operating manual
RollerDrive EC5000 AI/BI
24 V/48 V DC, Analogue Interface/Bus Interface

Manufacturer details
Interroll Engineering GmbH
Höferhof 16
42929 Wermelskirchen
Germany
Tel.: +49 (0) 2193 23 0
Fax: +49 (0) 2193 2022
www.interroll.com
Content
We strive for the accuracy, timeliness and completeness of the information and have carefully prepared the contents
in this document. Regardless of this, errors and changes are expressly reserved.
Copyright/industrial property rights
Any texts, images, graphics and the like, as well as their arrangement, are subject to protection under copyright and
other laws of protection. The reproduction, modication, transmission or publication of any part of this document or of
the entire document in any form is prohibited.
The document serves the exclusive purposes of information and of operation in accordance with the regulations and
does not justify any counterfeiting of the products concerned.
All signs contained in this document (protected marks, such as logos and trade names) are the property of Interroll
Holding AG, CH or of third parties and must not be used, copied or distributed without prior written consent.
Online version - only suitable for color printing!

Version 2.4 (03/2020) Online
Translation of the original operating manual 3 of 54
Contents
1 About this document 7
1.1 Information about this operating manual 7
1.2 Warning notices in this document 8
1.3 Symbols 9
2 Safety-related information 10
2.1 State of the art 10
2.2 Proper use 10
Application eld 10
2.3 Improper use 11
2.4 Qualication of personnel 11
2.5 Dangers 12
Injury to persons 12
Electricity 12
Rotating parts 12
Heat 12
Work environment 12
Faults in operation 12
Maintenance 13
Unintentional start-up 13
2.6 Interface to other devices 13
2.7 Operating modes/operating phases 13
Standard operation 13
Special operation 13
2.8 Applicable documentation 14
3 Product information 15
3.1 Components 15
Colour rings on the connectors 15
3.2 Product description 16
Overload protection 16
3.3 RollerDrive EC5000 BI with CAN bus 18
Service life indicator lights 18
Health indicator lights 19
Various operating modes 20

4 of 54
Version 2.4 (03/2020) Online
Translation of the original operating manual
Contents
3.4 Rating plate 21
3.5 RollerDrive EC5000 as a replacement for RollerDrive EC310 22
3.6 Product identication 23
3.7 Technical specications 24
EC5000 20 W – AI/BI – 24 V DC 24
EC5000 35 W – AI/BI – 24 V DC 25
EC5000 50 W – AI/BI – 24 V DC 26
EC5000 20 W – AI/BI – 48 V DC 27
EC5000 35 W – AI/BI – 48 V DC 28
EC5000 50 W – AI/BI – 48 V DC 29
3.8 Performance data 30
EC5000 20 W – 24 V DC/48 V DC 30
EC5000 35 W – 24 V DC/48 V DC 31
EC5000 50 W – 24 V DC/48 V DC 32
3.9 Control systems for the RollerDrive EC5000 33
3.10 RollerDrive connector AI 34
3.11 RollerDrive connector BI 35
3.12 Dimensions of the motor shaft 36
3.13 Dimensions of the bearing housings on the non-cable side 36
EC5000 IP66 38
4 Transport and storage 39
4.1 Transport 39
4.2 Storage 39
5 Assembly and installation 40
5.1 Warning notices for installation 40
5.2 Installing the RollerDrive 41
Installing the attachment shaft 41
Attaching the non-cable side 42
Securing the RollerDrive in the side prole 43
5.3 Installation tool (accessory) 44
5.4 Warning notices for electrical installation 45
5.5 Electrical installation 45

Version 2.4 (03/2020) Online
Translation of the original operating manual 5 of 54
Contents
6 Start-up and operation 46
6.1 Warning notices for start-up and operation 46
6.2 Start-up 46
Check before the initial start-up 46
6.3 Operation 47
Check before every start-up 47
6.4 Procedure in the event of accidents or faults 47
7 Maintenance and cleaning 48
7.1 Maintenance 48
Checking the RollerDrive 48
Replacing the RollerDrive 48
7.2 Cleaning 48
8 Assistance in the event of faults 49
8.1 Troubleshooting 49
9 Decommissioning and disposal 50
9.1 Decommissioning 50
9.2 Disposal 50
10 Appendix 51
10.1 Accessories 51
Interroll control systems 51
Interroll High Performance power supply unit 51
RollerDrive extension cable 51
PolyVee belt 52
PolyVee clamping aid 52
PolyVee nger guard 52
Tool 52
10.2 Translation of the original Declaration of Conformity 53


Version 2.4 (03/2020) Online
Translation of the original operating manual 7 of 54
About this document
1 About this document
1.1 Information about this operating manual
This operating manual covers the following Interroll motor rollers:
• RollerDrive EC5000 AI with analogue interface, 24 V DC and 48 V DC
• RollerDrive EC5000 BI with digital CANopen bus interface, 24 V DC and 48 V DC
in three dierent power levels (see „Product description“ on page 16).
In the course of this manual, the term "RollerDrive" will sometimes be used, or alternatively the type designation
"EC5000".
The operating manual is a component of the product and contains important advice and information regarding the
dierent operating phases of the RollerDrive. It describes the RollerDrive at the time of shipping from Interroll.
The currently applicable version of this operating manual can be found online at: www.interroll.com/support/
All the information and advice in this operating manual has been compiled with respect to applicable standards and
regulations as well as the current state of the art.
For special versions, in addition to this operating manual, particular contractual arrangements and technical
documents apply.
¾To ensure safe and faultless operation and to full any warranty claims that may apply, read this operating
manual rst and observe its instructions.
¾Keep this operating manual within close reach of the RollerDrive.
¾Pass this operating manual onto every subsequent owner or user.
The manufacturer assumes no liability for damage and malfunctions that occur as a result of non-
compliance with this operating manual.
Should you still have any unanswered questions after reading this operating manual, please contact Interroll
customer service. Contact details for your region can be found online at www.interroll.com/contact/

8 of 54
Version 2.4 (03/2020) Online
Translation of the original operating manual
About this document
1.2 Warning notices in this document
Warning notices are provided in the context in which danger can occur and describe the nature of the danger in
question. They are structured according to the following examples:
SIGNAL WORD
Type and source of hazard
Consequence(s) in the event of non-compliance
¾Measure(s) for avoiding hazard
Signal words indicate the type and severity of the consequences if measures to avoid the hazard are not observed.
DANGER
Denotes an imminent hazard.
If measures to avoid the hazard are not observed, death or severe injury will occur.
¾Preventive measures
WARNING
Denotes a potentially hazardous situation.
If measures to avoid the hazard are not observed, death or severe injury may occur.
¾Preventive measures
CAUTION
Denotes the possibility of a hazardous situation.
If measures to avoid the hazard are not observed, minor or moderate injury may occur.
¾Preventive measures

Version 2.4 (03/2020) Online
Translation of the original operating manual 9 of 54
About this document
NOTE
Denotes a situation that can lead to material damage.
¾Preventive measures
1.3 Symbols
This symbol indicates useful and important information.
üThis symbol indicates a requirement that must be fullled before carrying out assembly or repair work.
This symbol indicates general information relating to safety.
¾This symbol indicates an action that needs to be performed.
•This symbol indicates a listed item.

10 of 54
Version 2.4 (03/2020) Online
Translation of the original operating manual
Safety-related information
2 Safety-related information
2.1 State of the art
The RollerDrive EC5000 has been constructed with respect to applicable standards and the current state of the art
and has been delivered in a condition that is safe to operate. Nevertheless, hazards can occur as a result of use.
Non-compliance with the instructions in this operating manual can result in life-threatening injuries.
In addition, the applicable local accident prevention regulations for the area of application and general safety
regulations must be adhered to.
2.2 Proper use
The RollerDrive may only be used in an industrial environment for industrial purposes within the stipulated
performance limits that are given in the technical specications.
It must be integrated into a conveyor unit or conveyor system before commissioning.
Application eld
Drive for unit load conveyor technology, such as for the transportation of cardboard boxes, containers, barrels,
workpiece carriers or tyres.
The RollerDrive is suitable for:
• Zero-pressure roller conveyors
• Entry conveyors
• Roller conveyor curves
• Small belt conveyors
Depending on the area of application of the RollerDrive, PolyVee, round or toothed belts as well as chains can be
used for the power transmission.

Version 2.4 (03/2020) Online
Translation of the original operating manual 11 of 54
Safety-related information
2.3 Improper use
Any use that goes beyond the proper use is considered improper, unless this has been authorised by Interroll
Engineering GmbH where applicable.
Any modication by conversion to the RollerDrive or attachment to the RollerDrive is prohibited!
The equipment must not be installed in areas in which substances could form explosive atmospheres/dust atmospheres
or for application in the medical/pharmaceutical sector.
It is considered improper use to install the equipment in exposed spaces that are open to potentially adverse weather
conditions, or areas in which the technology would suer from the prevailing climactic conditions and could potentially
malfunction as a result.
The RollerDrive is not intended for use by private end users. The equipment must not be used in a residential
environment without further examination and without the use of EMC protective measures that have been adapted
accordingly.
The RollerDrive is not suitable for transporting people.
It must not be used as a safety-relevant component or for performing safety-relevant functions.
2.4 Qualication of personnel
Non-qualied personnel are unable to identify risks and are therefore exposed to higher levels of danger.
¾Only qualied personnel may be assigned with the tasks outlined in this operating manual.
¾The operating company is responsible for ensuring that personnel adhere to the locally valid rules and
regulations for working in a safe and risk-aware manner.
This operating manual is intended for the following target audiences:
Operators
Operators are trained in how to operate and clean the Interroll RollerDrive and follow the safety regulations.
Service engineers
The service engineers have a specialist technical education or have successfully completed a training course from the
manufacturer. They carry out repair and maintenance work.
Qualied electricians
Qualied electricians have a specialist technical education. Moreover, due to their knowledge and experience as well
as knowledge of applicable regulations, they are able to carry out work on electrical equipment in an appropriate
manner. They are able to identify hazards independently and prevent electrical damage to persons and property.
All work on electrical equipment must generally only be performed by a qualied electrician.

12 of 54
Version 2.4 (03/2020) Online
Translation of the original operating manual
Safety-related information
2.5 Dangers
Here, you will nd information about the dierent types of dangers or damage that can occur in connection
with the operation of the RollerDrive.
Injury to persons
¾Maintenance, installation and repair work on the unit must only be carried out by authorised technical
personnel in compliance with the applicable provisions.
¾Before switching on the RollerDrive, ensure that no unauthorised personnel are situated in the vicinity of the
conveyor/conveying system.
Electricity
¾Installation and repair work must only be carried out when the system has been disconnected from the power
supply.
¾Switch o the power to the RollerDrive and ensure that it cannot be unintentionally switched on again.
Rotating parts
¾Keep ngers and hair away from moving parts.
¾Persons with long hair should wear a hair net.
¾Close-tting work clothing should be worn.
¾Do not wear items of jewellery such as necklaces or bands.
Heat
¾Do not touch the RollerDrive during operation. In applications with high switching cycles, the temperature of the
tube can reach up to 60 °C.
Work environment
¾Remove any materials and objects that are not required from the working area.
Faults in operation
¾Regularly check the RollerDrive for visible damage.
¾In the event that smoke begins to form, unusual sounds are heard or the material to be conveyed becomes
jammed or develops defects, switch o the power to the RollerDrive immediately and ensure that it cannot be
unintentionally switched on again.
¾Immediately contact specialist personnel to determine the cause of the malfunction.

Version 2.4 (03/2020) Online
Translation of the original operating manual 13 of 54
Safety-related information
Maintenance
¾Since the product in question requires no maintenance, it is sucient to simply examine the RollerDrive for
visible damage on a regular basis.
¾Never open up the RollerDrive.
Unintentional start-up
¾Ensure that the RollerDrive cannot be switched on unintentionally, particularly during assembly and
maintenance work or in the event of a fault.
2.6 Interface to other devices
The integration of the RollerDrive into a conveyor system can create additional potential hazards. Such potential
hazards are not covered by this operating manual and must be analysed during the development, installation and
commissioning of the conveyor system as a whole.
¾Following the integration of the RollerDrive into a conveyor system, the entire system must be checked for any
new potential hazards that may be present before the conveyor is switched on.
2.7 Operating modes/operating phases
Standard operation
Operation in the installed condition at the end customer as a component in a conveyor in an overall system.
Special operation
Special operation encompasses all operating modes/operating phases that are necessary to guarantee and maintain
safe standard operation.
Special operating mode Comments
Transport/storage -
Assembly/commissioning In de-energised state
Cleaning In de-energised state
Maintenance/repair In de-energised state
Fault location -
Troubleshooting In de-energised state
Decommissioning In de-energised state
Disposal -

14 of 54
Version 2.4 (03/2020) Online
Translation of the original operating manual
Safety-related information
2.8 Applicable documentation
The RollerDrive EC5000 is part of the Interroll DC Platform, consisting of:
• Interroll High Performance power supply unit HP5424 or HP 5448 (24 V DC/48 V DC)
• Interroll MultiControl AI/BI
• RollerDrive EC5000 AI/BI (24 V DC/48 V DC)
• Interroll DriveControl 20/54/2048
Also ensure that you adhere to the information given in the operating manuals of the connected devices.
Further notes on operating and programming the RollerDrive can be found in the „MultiControl / RollerDrive - Start-
up and Programming” supplement.
The latest version of this supplement can be found online at: www.interroll.com/support/

Version 2.4 (03/2020) Online
Translation of the original operating manual 15 of 54
Product information
3 Product information
3.1 Components
1 Roller 4 Bearing seat with rating plate
2 Motor 5 Motor shaft
3 Bearing 6 Motor connector with colour ring and cable
Colour rings on the connectors
The motor connector features a colour ring in order to make the various versions of the RollerDrive EC5000 easily
distinguishable from one another.
Colour ring RollerDrive version
White Analogue interface, 24 V DC
Grey Bus interface, 24 V DC
Black Analogue interface, 48 V DC
Yellow Bus interface, 48 V DC

16 of 54
Version 2.4 (03/2020) Online
Translation of the original operating manual
Product information
3.2 Product description
The RollerDrive EC5000 can be used in both straight and curved sections and ensures a constant conveyor speed.
Motors, motor electronics and gears are installed in the RollerDrive.
Both interface versions (analogue/CAN bus) of the RollerDrive EC5000 are available in three dierent power levels:
• 20 W
• 35 W
• 50 W
Overload protection
The EC5000 has multiple overload protection systems:
Stall timing
When the RollerDrive starts, the revolutions of the installed motor are monitored. If the motor does not reach a certain
speed within a specied time, an error signal is set.
This error signal is automatically reset after 10 seconds.
How the EC5000 AI behaves: Once the target value is reapplied, the RollerDrive attempts to start again.
How the EC5000 BI behaves: The RollerDrive is ready to be acknowledged.
Heavy running detection
If the RollerDrive rotates 50% slower than specied for a dened period, an error signal is set.
In the case of the EC5000 BI, there is another adjustable warning limit with corresponding message before shutdown
takes place.
The error signal is automatically reset after 10 seconds.
How the EC5000 AI behaves: Once the target value is reapplied, the RollerDrive attempts to start again.
How the EC5000 BI behaves: The RollerDrive is ready to be acknowledged.

Version 2.4 (03/2020) Online
Translation of the original operating manual 17 of 54
Product information
Temperature monitoring
The temperature of the motor installed in the RollerDrive is monitored in addition to the temperature of the motor
electronics. If the maximum permitted temperature is exceeded, the RollerDrive is switched o and an error signal is
issued. Once the overheated components have cooled down, the error signal will be reset.
How the EC5000 AI behaves: Once the target value is reapplied, the RollerDrive attempts to start again.
How the EC5000 BI behaves: The RollerDrive is ready to be acknowledged.
WARNING
How the EC5000 AI behaves with overload protection:
The signals from the overload protection functions are automatically reset. If the target value is still applied, the
RollerDrive may start up again unintentionally.
¾Troubleshooting must be carried out via the control system.
Holding brake (zero motion hold)
The RollerDrive EC5000 is equipped with an electronic holding brake that allows it to be used in sloped and
ascending conveyors.
EC5000 AI:
Holding brake active when no start signal is present.
EC5000 BI:
Holding brake active in "Operational" mode and target value "0".
If the power supply system fails, the holding brake will no longer take eect as the brake is not mechanical.
Energy recovery system
The RollerDrive recovers energy when braking the conveyed material. This results in the motor and motor electronics
heating up less and improves the energy balance of the system. The Interroll control systems are equipped with a
circuit that prevents an increase of voltage in the power supply.
If motor control systems are used without a voltage limiter (brake chopper), it must be ensured that the
power supply units used are suitable for energy recovery (up to 35 V / 60 V).
We recommend using the Interroll High Performance power supply units.

18 of 54
Version 2.4 (03/2020) Online
Translation of the original operating manual
Product information
3.3 RollerDrive EC5000 BI with CAN bus
The CAN bus communication of the EC5000 BI is based on the following CAN/CANopen standards:
• ISO 11898-1 Road vehicles - Controller area network (CAN) - Part 1: Data link layer and physical signalling
• ISO 11898-2 Controller area network (CAN) - Part 2: High-speed medium access unit
• EN 50325 Industrial communications subsystem based on ISO 11898 (CAN) for controller-device interfaces -
Part1:Generalrequirements
• CiA 402 CANopen device prole for drives and motion control
CAN bus communication enables, among other things, the actual values of the RollerDrive to be read out (monitoring),
including:
• Number of starts/stops
• Operating hours (ready for operation)
• Runtime (time during which motor is rotating)
• Minimum temperature
• Maximum temperature
• Actual temperature
• Number of quick stops
• Average power
• Number of revolutions
So-called health indicator lights and service life indicator lights have also been integrated, which can be evaluated via
the connected Interroll MultiControl BI or a connected PLC.
Service life indicator lights
In accordance with statistically determined reference values, a signal is output when the RollerDrive reaches a service
life at which a replacement is recommended.
This is not a xed value that decreases with the runtime.
The expected service life increases or decreases depending on the load on the RollerDrive.
The service life indicator lights have two statuses:
Green The RollerDrive has not yet reached its expected service life.
Yellow The RollerDrive has reached its expected service life. Replacement is recommended.
Red This status is not used.

Version 2.4 (03/2020) Online
Translation of the original operating manual 19 of 54
Product information
Health indicator lights
So-called health or status indicator lights are used to monitor the current values of the RollerDrive.
Health indicator lights are used to check the
• Temperature
• Power
• Frequency of errors
Temperature
Green RollerDrive temperature OK.
Yellow The temperature of the RollerDrive has reached the warning limit.
Red The temperature of the RollerDrive has exceeded a critical value.
Power
Green The RollerDrive is working within the specied power limits.
Yellow The rated power of the RollerDrive has been exceeded.
Red The power of the RollerDrive is > 120% of the rated power.
Frequency of errors
The frequency of the following errors is monitored within a specied time frame:
• Heavy running
• Stall timing
• Overvoltage
• Undervoltage
Green Status of the RollerDrive OK.
Yellow The number of errors within the specied time frame has reached the warning limit.
Red The number of errors within the specied time frame has reached a critical limit.
The indicator lights are used purely for information purposes and do not result in the shutdown of the
RollerDrive.
The signals can be evaluated and processed via the connected control system.

20 of 54
Version 2.4 (03/2020) Online
Translation of the original operating manual
Product information
Various operating modes
The RollerDrive EC5000 BI can be operated in either speed or positioning mode.
This enables the RollerDrive to be moved with millimetre precision in certain applications.
For the positioning mode, the direction of rotation “clockwise” (default setting) must be selected in the
default settings!
CAN bus default settings
Node ID: 127 (LSS mode for dynamic address assignment)
Baud rate: 250 kbps
Default acceleration values for the RollerDrive EC5000 BI
The EC5000 BI is supplied with the following acceleration values for an optimum acceleration ramp.
Gear 9:1 13:1 18:1 21:1 30:1 42:1 49:1 78:1 108:1
Acceleration value in mm/s213,215 9149 6608 5664 3965 2832 2427 1525 1101
These values dene the fastest possible acceleration and are entered in the RollerDrive in SDO object "6083h".
Object
ID
Sub
index
Name Data
type
Acc Min. Max. Default Mappable
6083h 00h Prole acceleration UINT32 rw UINT32 UINT32 Gear-
dependent
RM
Further information on the CAN bus can be found in the "Interroll MultiControl BI" operating manual and
the "MultiControl / RollerDrive - Start-up and Programming" supplement.
The supplement document can be found in the download area at www.interroll.com
This manual suits for next models
1
Table of contents
Other Interroll DC Drive manuals
Popular DC Drive manuals by other brands
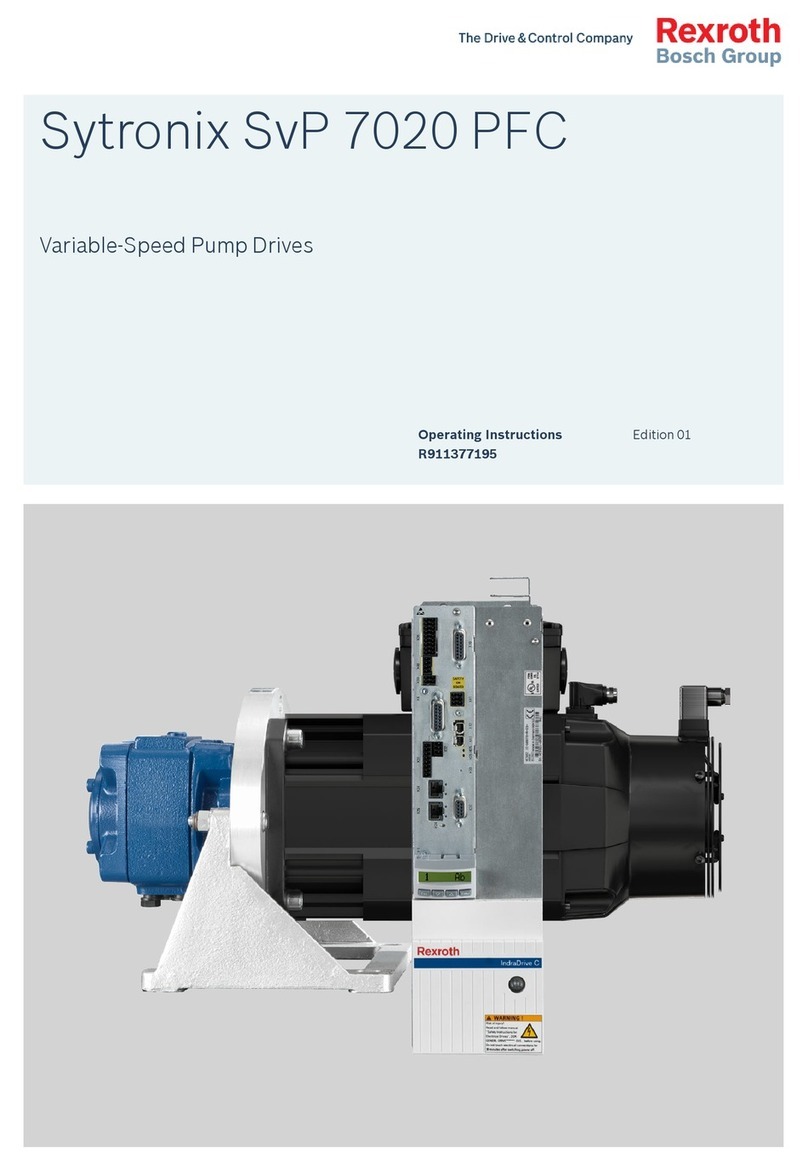
Bosch
Bosch Rexroth Sytronix SvP 7020 PFC operating instructions

Thermo Scientific
Thermo Scientific MasterFlex 850-1000 operating manual
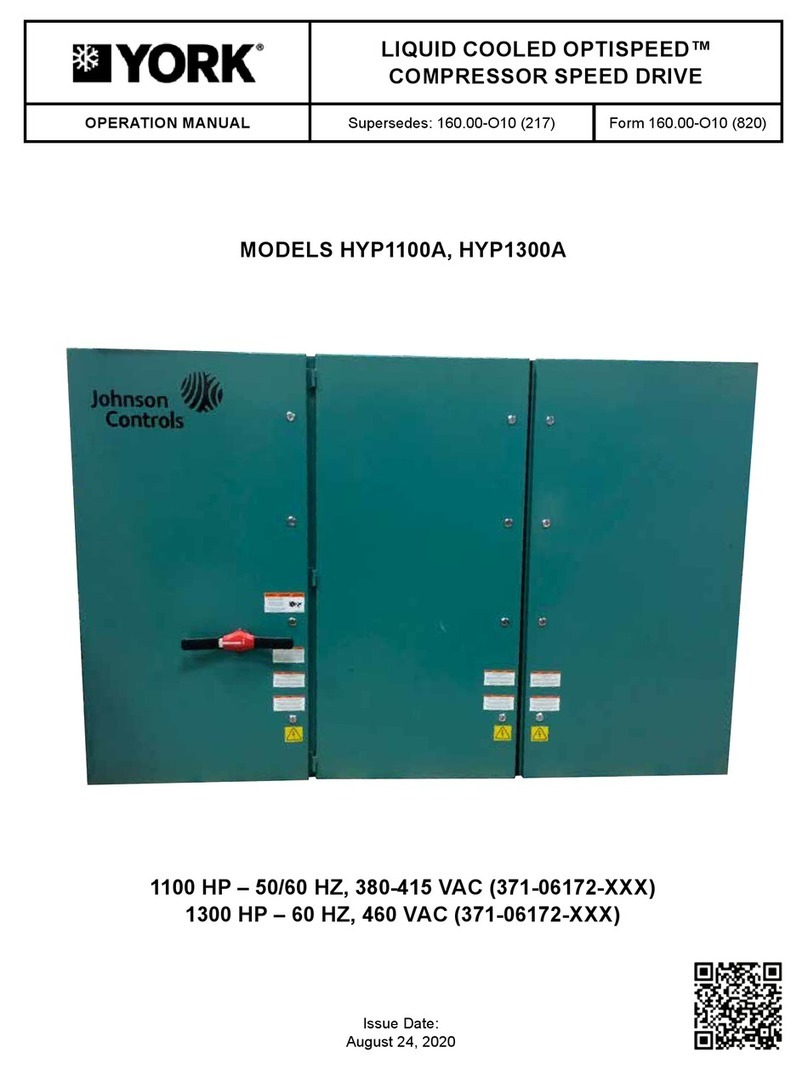
Johnson Controls
Johnson Controls YORK HYP1100A Operation manual
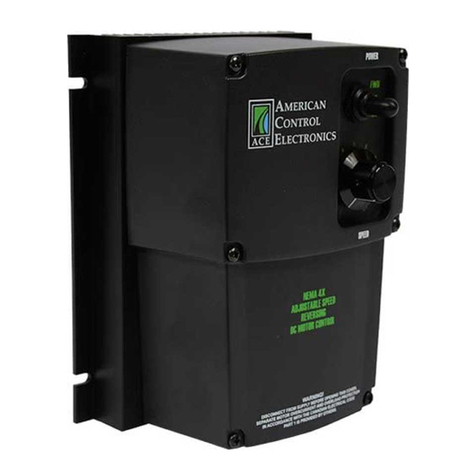
American Control Electronics
American Control Electronics PAT450-10 quick start guide
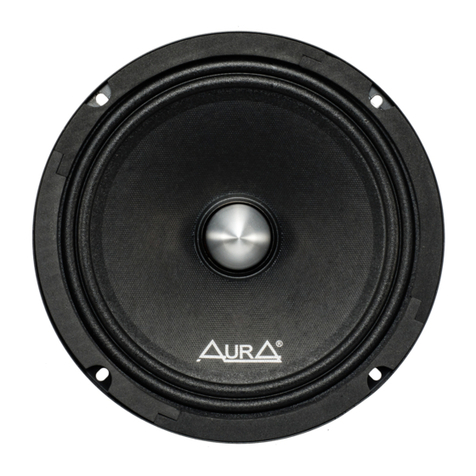
Aura
Aura VENOM-8 owner's manual
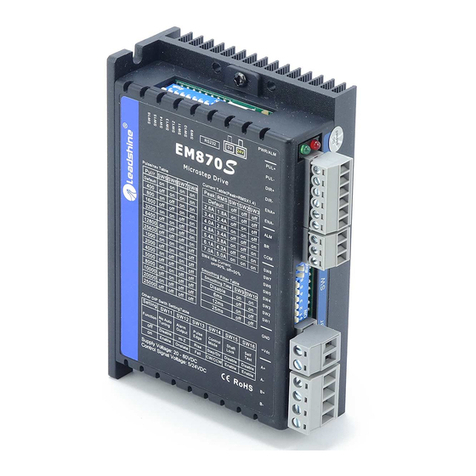
Leadshine
Leadshine EM870S user manual