DAV TECH PCP User manual

PCP VOLUMETRIC PUMP DRIVE
Operating
instructions
DAV TECH SRL
Via Ravizza, 30 - 36075 Montecchio Maggiore (VI) - ITALIA
Tel. 0039 0444 574510 - Fax 0039 0444 574324

Operating instructions
Index
1 INTRODUCTION pag. 3
1.1 The manual
1.2 Warranty
1.3 Goods receipt
2 TECHNICAL DESCRIPTION pag. 3
2.1 Operation
2.1 Technical specifications
3 SAFETY STANDARDS pag. 4
3.1 Safety notes
4 INSTALLATION pag. 10
4.1 Panel installation
4.2 Thermal dissipation
4.3 Electrical connections
4.4 Power supply
4.5 Ground connections
4.6 Power connector
4.7 Control connector
5 CONNECTION DIAGRAM pag. 16
5.1 Power disconnect-switch
5.2 Encoder signals
5.3 Drive logic
5.4 Interfacing via Profinet
5.5 Interfacing via Modbus Tcp/Ip
6 CONNECTION BETWEEN DRIVE AND PUMP pag. 23
7 WIRING DIAGRAM pag. 24

PCP VOLUMETRIC PUMP DRIVE
1 INTRODUCTION
1.1 The manual
The user manual is the document that accompanies the pump from the moment of its construction and for the entire period of
use, it is therefore an integral part of the pump. The manual must be read before undertaking any operation involving the pump.
The manual must be readily available to personnel assigned to use and maintenance of the pump. The user and the person
responsible for use are required to know the contents of this manual. Reproduction of any part of this manual, in any form,
without the express written permission of DAV Tech is prohibited. The texts and illustrations contained in the manual are not
intended to be binding, DAV tech reserves the right, at any time and without notice, to make any changes to improve the product
or for constructive or commercial needs.
1.2 Warranty
The warranty is valid for a period of 12 months starting from the commissioning date and in any case not later than 15
months from the delivery date. Interventions carried out during the warranty period do not in any way extend the warranty
period. The seller is not liable for defects due to the normal wear of parts which, by their nature, are subject to wear.
1.3 Goods receipt
Upon receipt of the goods, check that:
• The packaging is intact.
• The exact correspondence of the ordered material.
The original drive configuration must definitely not be changed.
2 TECHNICAL DESCRIPTION
2.1 Operation
The controller was created to manage the movement of a PCP pump with DC motor with feedback from an encoder.
The DMD1204PN controller has Profinet IO and Modbus TCP / IP connectivity via ethernet, this allows the drive to be controlled
by most PLCs.
The device internally manages a “ Modbus Server” in addition to the IO Device, it must therefore be interrogated by another
Client device to read and write data.
The configuration of the Profinet interface can be managed directly from the development PLC tool used, as the functions for
assigning the device name and ip address are standard and are already managed directly by the drive.
The parameterization and the programming of the drive is simple and fast thanks to DC Control, the Tool supplied with an
advanced graphic interface for Windows able to communicate with the drive both with USB and with Ethernet.
The drive already contains a software that manages the PCP pump in all its aspects, enabling, dispensing, suck-back function,
possible outlet valve etc., this program can be parameterized with the variables exchanged with the PLC via Profinet or Modbus
TCP / IP.
2.1 Technical specifications
pag.3
Output current
Rated current ARMS 4
Peak current ARMS 8
Supply
Voltage range VDC +24 .. 85
Rated voltage VDC +65
Current control
Type Dual MOSFET H-bridges
Frequency KHZ 20 (50 µs)
PWM outputs 20 KHz center-weighted PWM
Protections
Short circuit, overvoltage, undervoltage, | T, pursuit, position
Feedback Incremental line driver or push pull encoder (PNP o NPN)
Input digital general
purpose
Number 9 + 3 (superimposed on the service inputs)
Type PNP TTL compatible up to +30 VDC
Function configurable via software
Output digital general
purpose
Number 4
Type PNP +24 VDC
Current mA 100 per channel
Protection Temperature, short circuit
Function Configurable via software
Service Digital Input
Number 6 (superimposed on general purpose inputs)
Type PNP o NPN da 5 a 30 VDC
Current consumption mA 8
“High” / “Low” level
threshold VDC > + 2,2/ < + 0,8
Features High-speed inputs
Analog input
Number 3 (optional)
Resolution bit 12
Range VDC 0 ... +10 (+/- 10V optional on Ana.inp. and Ana.inp.1)

Operating instructions
It is recommended to follow the instructions below in order to avoid damage to the system, the device,
or injury to the technician, or to other people during operation.
Throughout this manual, the following symbols are used to indicate the possible danger levels if the
installation instructions are not followed.
The following symbols indicate the operations that must be done and the prohibited operations.
The following symbols are used to indicate information useful for a correct installation. (Assistance)
DANGER
Indicates conditions that could result in death or serious injury if the given precautions are
not observed.
NOT ALLOWED
Indicates prohibited actions that must NEVER be performed.
ATTENTION
Indicates conditions that could result in death or serious injury if the given precautions are
not observed.
OBLIGATORY
Indicates actions that MUST be performed.
3 SAFETY STANDARDS
IMPORTANT
Indicates important information to be memorized including precautions such as displaying
alarms to avoid damaging devices.
INFORMATION
Indicates additional information.

pag.5
Read the following instructions in their entirety before checking the products at the time of delivery,
before transport and storage, installation, wiring, operation, inspection, and disposal.
PCP VOLUMETRIC PUMP DRIVE
Make sure you have correctly connected the connectors and fixed the cables.
Incorrect wiring can cause electric shock, fire, equipment damage or injury.
Do not expose cables to sharp objects or edges, excessive pressures or traction, or to objects that
could cause them to be crushed.
Breakage or misplacement of a cable can cause electric shock, fire, equipment damage or injury.
Do not touch any rotating part of the motor when the drive and the
motor itself are operational.
Not observing this rule can cause injury.
Wait at least 5 minutes after switching off before removing, modifying wiring, or inspecting the
device. Only specialized personnel can perform these operations.
Not observing this rule can cause electrical shocks.
Never touch the inner parts of the drive.
Failure to observe this warning can result in injury.
Do not remove cables, connectors, protective or optional elements while the power supply is on, or in
the absence of the appropriate safety systems.
Failure to observe this warning can cause electric shock or equipment damage.
Do not approach the machine immediately after resetting a momentary power failure, to
avoid unexpected restarts.
Failure to observe this warning can result in injury.
Do not touch the motor or the drive during operation. The surface may reach high
temperatures.
Not observing this warning can cause burns.
Do not subject the product to water, corrosive liquids, flammable gases or combustible
gases.
Not observing this rule can cause fires.
DANGER
rotor

Operating instructions
During installation, protections must be provided for over-currents, for electricity leakage,
for over-temperatures, as well as emergency stop devices.
Failure, in the absence of protection, can cause electrical shock, injury or fire.
Strictly follow the instructions and procedures contained in this manual to verify the
correct installation.
Malfunctions that occur, due to incorrect installation, damage the equipment and can cause accidents or serious
injuries.
Installation, wiring, and consultancy relating to inspections and malfunctions must only be
carried out by authorized personnel.
Failure to observe this warning can cause electrical shock, injuries, fires, damage, or malfunctions.
Install an emergency stop device on the machine to ensure its safety.
Failure to observe this warning can cause electric shock, injury, fire.
Applications and installations must meet all applicable safety requirements.
Failure to observe this warning can result in injury.
Make sure that the devices have been properly grounded. Connect the grounding terminal,
in compliance with the regulations for electrical installations. (Ground resistance <100Ω)
Not observing this rule can cause electrical discharges.
Use properly sized equipment for the type of load to be handled.
Failure to observe this warning can result in equipment damage or injury.
Do not carry the drive or motor holding it by the cables or the motor shaft.
Failure to observe this warning can result in malfunctions or injuries.
REQUIRED
ATTENTION

pag.7
PCP VOLUMETRIC PUMP DRIVE
Do not apply loads higher than those indicated in the technical documentation.
Failure to observe this warning can result in malfunctions or injuries.
Do not cover the drive inputs, outputs and ventilation slots and prevent foreign bodies, such
as metal or liquid fragments, from entering the product.
Failure to observe this warning can cause deterioration of the internal components with consequent fires or
malfunctions.
DAV Tech products are precision equipment. Avoid violent shocks during transportation,
installation, and operation.
Failure to observe this warning can cause malfunctions.
Do not store or install the product in the following places:
• Places with temperature outside the allowed ranges.
• Places with humidity levels outside the allowed ranges.
• Places subject to condensation formation due to thermal excursions.
• Places exposed to corrosive, explosive or flammable gases.
• Places exposed to dust, saline agents, or metal powders.
• Places exposed to water, oils or chemical agents.
• Places subject to shock or vibration.
Failure to observe this warning can result in malfunctions or damage to the product.
Do not step or place heavy objects on the product.
Failure to observe this warning can result in malfunction or injury.
Be sure to comply with all the installation conditions.
Failure to observe this warning can malfunction, fire or electric shock.
Power the drive only with voltages isolated from the mains voltage and included within the
admissible limits.
Failure to observe this warning can cause malfunctions, fires or electric shocks.
Make sure you have connected the product correctly.
Failure to observe this warning can cause malfunctions.
Keep the specified distances between the drive and other devices.
Failure to observe this warning can cause malfunctions or fires.

Operating instructions
Securely connect the power terminals. Use cables with a section suitable for their use.
Failure to observe this warning can cause a fire.
Keep the power and signal lines at a distance of at least 300mm. Use twisted pairs or
shielded cables.
Failure to observe this warning can cause malfunctions.
Perform the motor operating tests only with the drive shaft disconnected from the machine.
Failure to observe this warning can cause serious injuries.
When disposing of the products, consider them as general industrial waste.

pag.9
PCP VOLUMETRIC PUMP DRIVE
General precautions
• The illustrations in this manual are typical examples and may differ from the product received.
• This manual is subject to change due to product improvements, specification changes or improvements to the manual.
• DAV Tech srl is not responsible for damage to things and / or people caused by incorrect installations and / or unauthorized
modifications of the product.
NOTE. Since the drives are of an integrated type, they need a new confirmation after installation in the final product.
European directives
DAV Tech automation products must be handled, installed, and maintained only by competent personnel
trained in the installation of automation components, and only for the purposes described in the user manual.
The technician must pay particular attention to potential risks caused by mechanical and electrical hazards.
It is very important that applications and installations meet all applicable safety requirements.
Each technician is obliged to take responsibility for verifying his / her knowledge and understanding of all applicable
safety standards.
Any use that does not comply with the safety requirements can damage the equipment and injure the user.
DAV Tech Srl will not be held responsible and will not assume any responsibility for damages caused by products
handled and / or installed improperly, or in cases where the customer has allowed, or performed, modifications
and / or repairs not authorized by DAV Tech Srl.
3.1 Safety notes
NORMATIVA
DESCRIZIONE DATA
89/336/EEC
EMC Directive 3-may1989
EN 55011
Limits and methods of measurement of ratio disturbance
characteristics of industrial, scientific and medical (ISM)
radio-frequency equipment 15-Sep-1998
93/68/EC
CE Marketing - Low voltage 22-Jul-1993
98/37/EC
Machinery 22-Jun-1998
EN 60204-1
Safety of machinery - Electrical equipment of machines 30-Jun-2006
2002/95/CE
RoHs Directive 27-Jan-2003

4 INSTALLATION
Operating instructions
FEATURE
SPECIFIC
Operating temperature
0°C ... +50°C
Cooling
Ventilate the drive in case of continuous operation
Operating humidity
95% relative or lower humidity (without condensation)
Storage temperature
-20°C ... +70°C
Storage humidity
95% relative or lower humidity (without condensation)
Place of installation
Free of corrosive gases
Free of dust and iron powder
Not subject to moisture or lubricating oil such as cutting oil
Altitude
1,000 m or less
Vibration resistance
4,9 m/s2
Shock resistance
19,6 m/s2
Operating conditions
Installation category (overvoltage category): III
Pollution degree: 2 or better
Protection class: IP3X (EN50178)
Place of installation
Installing in a control panel
Design the control panel size, module layout and cooling
method so that the temperature around the drive does not
exceed 50 ° C. Note: To increase product life and maintain
reliability, keep the temperature inside the control panel
below 40 ° C.
Installation near a heating
module
Minimize thermal radiation from the heating module and any
temperature rises caused by natural conversion, so that the
temperature around the drive does not exceed 55 ° C.
Installation near a vibration
source
Install a vibration damper below the drive to avoid subjecting
it to excessive vibration.
Installation in a place
exposed to corrosive gases
Corrosive gases do not have an immediate effect on the
device but, in the long term, cause malfunctions of the
electronic components. Take appropriate measures to avoid
the presence of corrosive gases.

pag.11
Le dimensioni sono espresse in mm.
PCP VOLUMETRIC PUMP DRIVE
FEATURE
SPECIFIC
Weight
320 g
Cover material
Complies with U.L. Spec 94 V-0 Flammability Rating

Operating instructions
4.1 Panel installation
If installed inside an electrical panel, leave a free space of at least 50 mm around the module in case
of the installation of a single drive. If more drives are installed, respect the minimum space, as shown
in the following figure, between two contiguous drives, in order to guarantee air flow and cooling of
the modules.
Do not cover the ventilation slots and prevent foreign bodies, such as metal fragments,
liquids or combustibles, from entering the product.
It is expressly forbidden to undertake actions aimed at modifying any mechanical part of
the drive.
Failure to observe this warning can cause internal components to deteriorate, resulting in fires or malfunctions.
ATTENTION
50mm min
(1.97 in min)
50mm min
(1.97 in min)
50mm min
(1.97 in min) 20mm min
(0.78 in min)
Ingresso flusso
dʼaria
Uscita flusso
dʼaria
OUTLET
AIR
INLET
AIR

pag.13
PCP VOLUMETRIC PUMP DRIVE
4.2 Thermal dissipation
The trend of the thermal dissipation in relation to the supplied current is shown below.
4.3 Electrical connections
Below is the trend of the thermal dissipation in relation to the supplied current.
• Avoid short-circuits, incorrect mass conductor connection, and polarity inversions.
• Check the voltage levels before plugging in the power connector.
• Always connect the ground terminal.
The electric current required to control the PCP pumps is 2.5 A.
ATTENTION
5
1,0 2,0 3,0 4,0 5,0 6,0 7,0
Amperes
Watts
10
15
20
25
30

Operating instructions
4.4 Power supply
The drive power supply will be 24VDC as it is also the rated voltage of the motor.
The drive has 2 separate power supplies, one for the logic and one for the power, this is to make
it possible to cut the power of the pump from a safety circuit, even if the pump is not considered
dangerous as it has no moving part on the outside. The maximum absorption for a PCP pump is
about 2.5 A while the drive logic is about 200-300mA.
It is advisable to use cables with a minimum section of 1 mm² for connections with a length of less
than 20 m and at least 2.5 mm2 in the case of connections with a longer length (maximum length
allowed = 20 m).
Use 4- core twisted pair and shielded cables.
4.5 Ground connections
It is preferable to use a ground bar that acts as a collector especially if there are several drives
connected.
It is important to connect to ground:
• the gnd of the power supply
• the drive housing
• the expected connection provided on the power terminal board
• the power cable screen (connected via the terminal of the power terminal board)
• the encoder cable screen.
4.6 Power connector
The power connector is used to:
• bring power to the drive
• connection of the motor power supply
The connector carries the following wire diameters and tips
1
0
m
m
1
0
m
m
CONDUCTOR CHARACTERISTICS
mm2
Rigid conductor section
0,2 - 2,5
Flexible conductor section
0,2 - 2,5
Flexible conductor cross section with cable lug without collar
0,2 - 2,5
Flexible conductor section with ferrule with collar
0,2 - 2,5
Stripping length or cable lug length
10

pag.15
PCP VOLUMETRIC PUMP DRIVE
4.7 Control connector
Instead, the control connector provides:
• to supply power to the IO side of the drive
• connection of the encoder signals
• connection of the digital inputs and outputs
• connection of the analog input
To reduce EMI disturbances, it is required to install a ferrite filter at a maximum distance of 150 mm
from the drive on the motor cable.
The filter is composed of low-grade ferrite which has high radio frequency losses; in this way the
filter works as a high impedance at those frequencies.
Recommended ferrites:
MANUFACTURER
FAIR-RITE
WüRTH ELEKTRONIK
Code
1463444 74271132
Outer diameter
23,7 mm 24,5 mm
Inner diameter
10,15 mm 8,5 mm
Length
39,4 mm 40,5 mm
25 MHz impedance
144 Ω 141 Ω
100 MHz impedance
240 Ω 241 Ω

Operating instructions
The digital outputs are protected against overloads (Max 500mA) and short-circuits; in case of
overload the output will switch off until the anomaly is removed.
If inductive loads, such as relays, solenoid valves, etc. have to be driven, connect a flyback diode in
parallel to the load.
ATTENTION
5 CONNECTION DIAGRAM
Typical connection
Stepper Motor Drive
SMD1204L_SSP
+H Vdc
Co mmon
GN D
24Vdc
GN D
Drive mo d.
D M D1 20 4 xI x x
M1. 9
M1. 8
M1.7
M1. 6
M1. 5
M1. 4
M1. 3
M2 .1
M2 . 2
M2 .28
M2 . 29
M2 .3
M2 .4
M2 .6
M2 .7
+
Co mmon
AC/ DC
suppl y
0V
24Vdc +
Co mmon
AC/ DC
suppl y
0V
+H Vdc
Green C h. A -
Blue Ch.B+
White C h. B -
Brown +5 V
SSP1 SSP2
Red GND
Yellow C h. A +
Black + Motor
Orange - Motor
Fer r it e
Gr ou nd
screen
Connect together all the common power supplies and signals, present in the terminal blocks.

pag.17
PCP VOLUMETRIC PUMP DRIVE
PIN Signal name Description
1
Reserved Do not connect
2
Reserved Do not connect
3
-M Motor power output
(-M)
4
+M Motor power output
(+M)
5
Shield Screen
6
Shield Screen
7
GND power Negative supply
voltages
8
+HV Positive supply
voltages
9
+24V Back-up Voltage back-up
referred to GND
PIN Signal name Description
1
+5 Vdc out (max 100mA) Uscita +5 Vdc (max 100 mA)
2
Common encoder Common encoder inputs
3
Motor encoder A- Channel A- motor encoder
4
Motor encoder B- Channel B- motor encoder
5
Motor encoder Z- Channel Z- motor encoder
6
Motor encoder A+ / Inp. 5 Channel A+ enc. motor / Input dig. 5
7
Motor encoder B+ / Inp. 6 Channel B+ enc. motor / Input dig. 6
8
Motor encoder Z+ / TOP
/ Inp. 7 Channel Z+ enc. motor / TOP input /
Digital Input 7
9
External encoder A+ / FLS / Input 8 Channel A+ external encoder / Forward
limit switch / Digital Input 8
10
External encoder B+ / BLS / Input 9 Channel B+ external encoder / Reverse
limit switch / Digital input 9
11
External encoder Z+ / Inp. 0 Z+ Channel External Encoder / Digital
Input 0
12
Digital input 1 Digital Input 1
13
Digital Output 0 Digital Output 0
14
+5 Vdc out (max 100mA) Output +5 Vdc (max 100 mA)
15
SSP_OK_IN Ticket SSP OK
16
+5 Vdc out (max 100mA) Output +5 Vdc (max 100 mA)
17
Common encoder Common encoder inputs
18
SSP_OK_OUT Output SSP OK
19
Analog output Analog output
20
Analog common Common analog in/out
21
Analog input Analog input
22
Ana. Inp.1 / Output 2 Analog input 1 / Output 2
23
Ana. Inp.2 / Output 3 Analog input 2 / Output 3
24
External encoder A- Channel A- external encoder
25
External encoder B- Channel B- external encoder
26
External encoder Z- External Z- encoder Channel
27
Digital input 2 / Output 6 Digital Input 2 / Digital Output 6
28
SSP IN 1 Input SSP 1
29
SSP IN 2 Input SSP 2
30
Digital output 1 Digital Output 1
Components identification
Power supply and motor
connector (M1)
Service input connector (M2)
1
M1
23456789
151
16 30
M2
1
M1
23456789
151
16 30
M2

Operating instructions
Il programma all’interno del drive prevede già le seguenti connessioni sul connettore M2:
PIN CONNECTION NAME PROGRAMME FUNCTION
1
5 VDC encoder 5 V encoder power supply (max 100mA)
2
GND encoder GND encoder
3
Channel A + encoder Channel A + encoder
4
Channel B + encoder Channel B encoder
5
Channel Z + encoder (Top) Not used
6
Channel A - encoder Channel A - encoder
7
Channel B - encoder Channel B - encoder
8
Channel Z - encoder Not used
9
Channel A + external encoder / input 8 Predetermined dispensing
10
Channel B + external encoder / input 9 Reset alarms
11
Z Channel + external encoder / input 0 Not used
12
Input 1 Enable
13
Output 0 Alarm
14
5 VDC 5 VDC (max 100mA)
15
Reserved Reserved
16
5 VDC external encoder Encoder power supply (max 100mA)
17
GND (connected internally to pin 20) GND
18
Reserved Reserved
19
Analog output Not used
20
Analog GND Analog GND
21
Analog input 0 (0-10V) Pressure sensor
22
Output 2 End of dispensing
23
Output 3 Dispensing in progress
24
Channel A - external encoder Not used
25
Channel B - external encoder Not used
26
Channel Z - external encoder Not used
27
Input 2 JOG dispensing
28
Input SSP1 Input 1 electronic power disconnector
29
Input SSP2 Input 2 electronic power disconnector
30
Output 1 Ready drive
All signals are PNP.

pag.19
PCP VOLUMETRIC PUMP DRIVE
The drive has been designed to perform all the dispensing functions necessary for a PCP pump,
these functions can all be parameterized via Modbus TCP IP, without this communication it will be
possible to use the drive with only one static data set.
By using the inputs or variables via Modbus it is possible to activate the following functions in the
drive:
Enable (Power Enable)
With input 1 it is possible to couple the pump motor, if the power supply is missing or the pump is
physically disconnected, the drive will give the power timeout alarm.
5.3 Drive logic
Using SSP 1 and SSP 2 input, it is possible to control the electronic disconnector integrated into
the drive with both 24 V signals and to supply the power stage of the drive.
5.1 Electronic power disconnector
The drive prepares a connection for the differential encoder signals, it is therefore possible to
connect the encoder line driver directly to the drive. It is possible to power the encoder directly
with 5V present on terminal board M2.
5.2 Encoder signals
Jog Dispensing
With input 2 it is possible to activate the pump to dose at constant speed, by turning off the
command the pump will stop immediately.
Predetermined dispensing
With input 8 it is possible to activate the dispensing of a set quantity, the input must be kept
active until the end of dispensing, the “End of dispensing” signal will then be activated when the
command is switched off.
Alarms reset
The designated input is input 9.
Suck back
The drive automatically performs the suck back (inversion of the rotation); whenever the controlled
pump stops, the direction of rotation is reversed with programmable speed and quantity.
INPUT PIN Description
IN 1
12 Enable
IN 2
27 Jog dispensing
IN 8
9 Predetermined dispensing
IN 9
10 Reset

Operating instructions
There are also 4 outputs that define the drive’s status:
Alarm
When 1 or more hardware alarms are active in the drive
Ready
When there are no alarms and the motor is in torque (enable active)
End of dispensing
Signal that activates at the end of a predetermined dispensing
Dispensing in progress
Signal that allows you to connect for example a solenoid at the output of the pump (with a
programmable delay)
The drive in the upper part has 2 ethernet ports which are related to a single network interface.
It is possible to insert one or more drives into the PLC network configuration using the supplied
GSDML file. The real time data exchange must be configured in the Drive using the “PROFIdrive
AEC Telegram 500 “ (programmable delay).
This telegram sets up the exchange of 10 INT32 variables for the inputs and 10 INT32 variables for
the outputs (40 + 40 Byte).
INPUT PIN DESCRIPTION
OUT 0
13 Alarm
OUT 1
30 Ready
OUT 2
22 End of dispensing
OUT 3
23 Dispensing in progress
5.4 Interfacing via Profinet
AZIONAMENTO POMPE VOLUMETRICHE PCP
pag. 23
INGRESSO
PIN
DESCRIZIONE
OUT 0
13
Allarme
OUT 1
30
Ready
OUT 2
22
Fine dosaggio
OUT 3
23
Dosaggio in corso
Interfacciamento via Profinet
Il drive nella parte superiore presente 2 porte ethernet che sono relative ad un’unica
interfaccia di rete. È possibile inserire uno o più drive nella configurazione di rete del
PLC utilizzando il file GSDML fornito. Lo scambio dati real time dovrà essere configurato
nel Drive utilizzando il “PROFIdrive AEC Telegram 500”.
Questo telegramma predispone lo scambio di 10 variabili INT32 per gli ingressi e 10
variabili INT32 per le uscite (40 + 40 Byte).
PLC
input
Variabili
drive
Modbus
Holding
register
Descrizione
Var_1
V111
4-1222
Status
Bit 0 allarme
Bit 1 Ready
Table of contents
Popular DC Drive manuals by other brands

DoorHan
DoorHan DRIVE SHAFT-50PRO Installation and service instruction
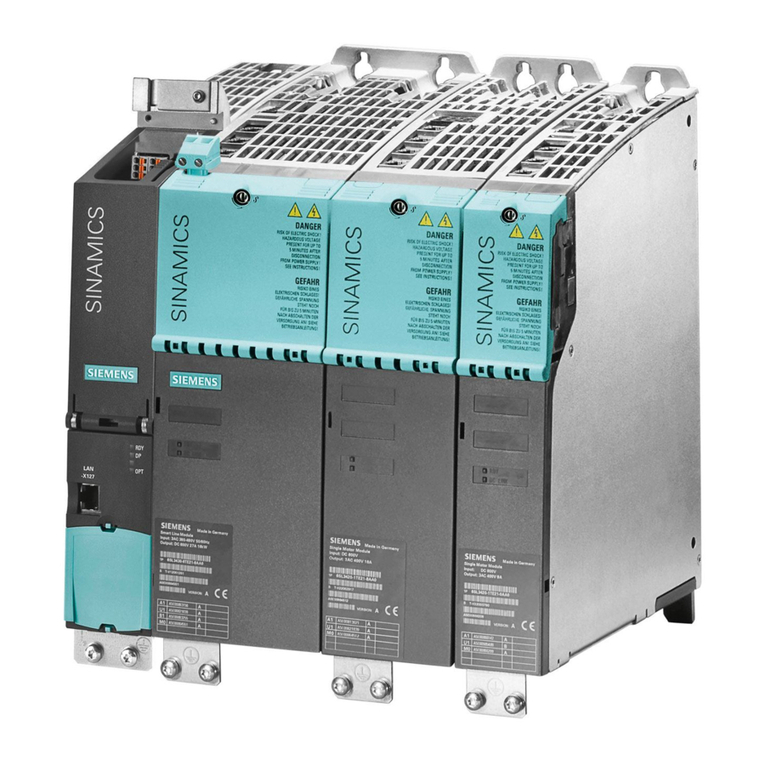
Siemens
Siemens SINAMICS S120 System manual

Johnson Controls
Johnson Controls PENN VFD68 Product bulletin
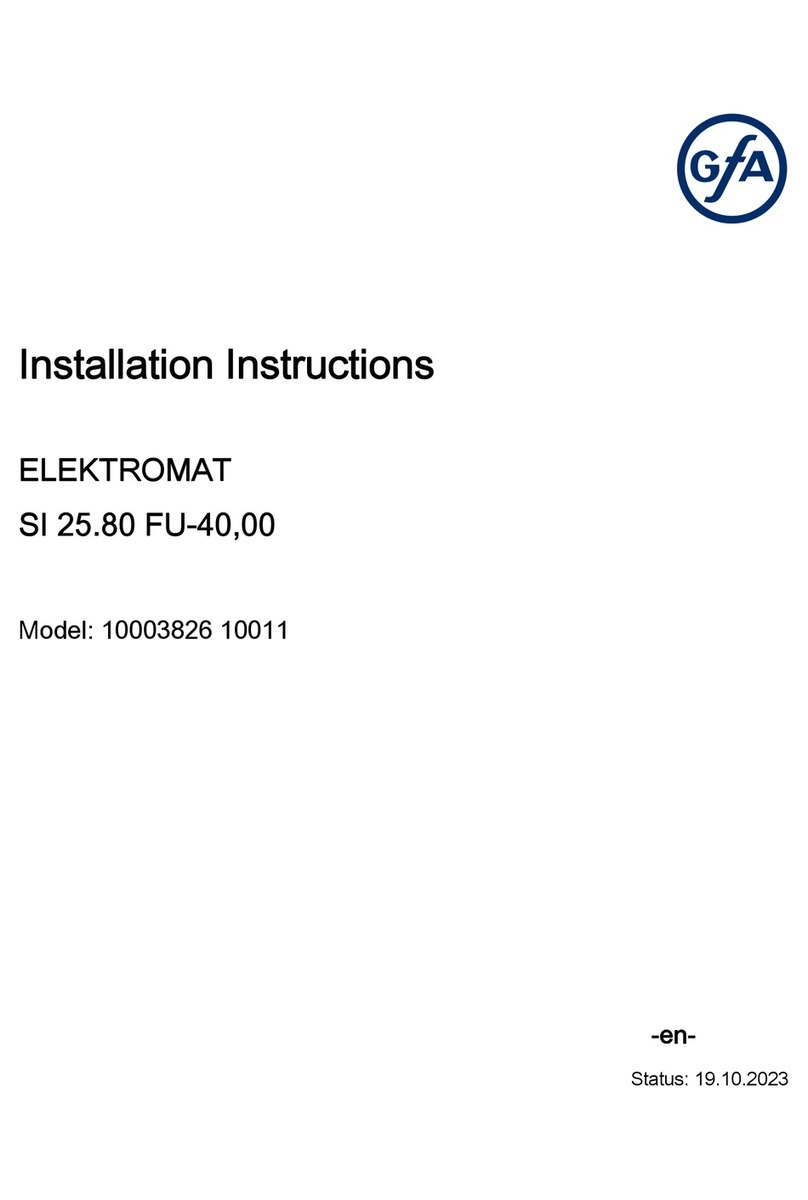
GFA
GFA ELEKTROMAT SI 25.80 FU-40,00 installation instructions
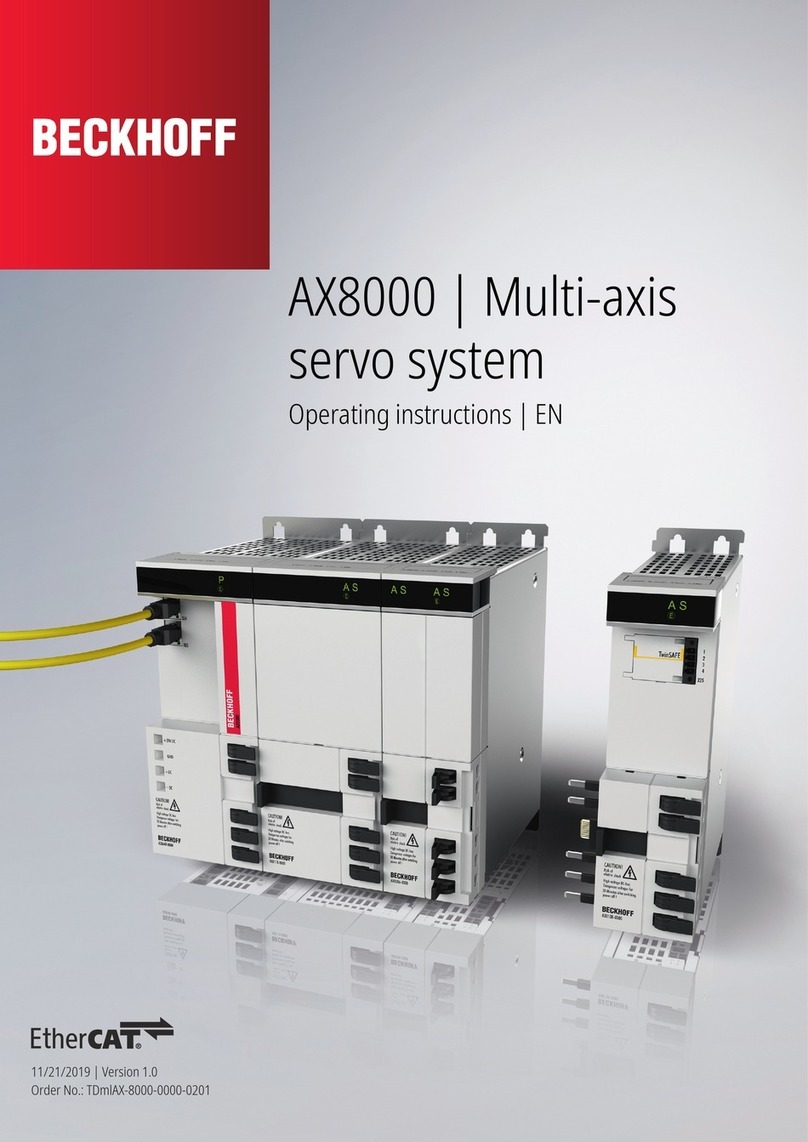
Beckhoff
Beckhoff AX8000 operating instructions
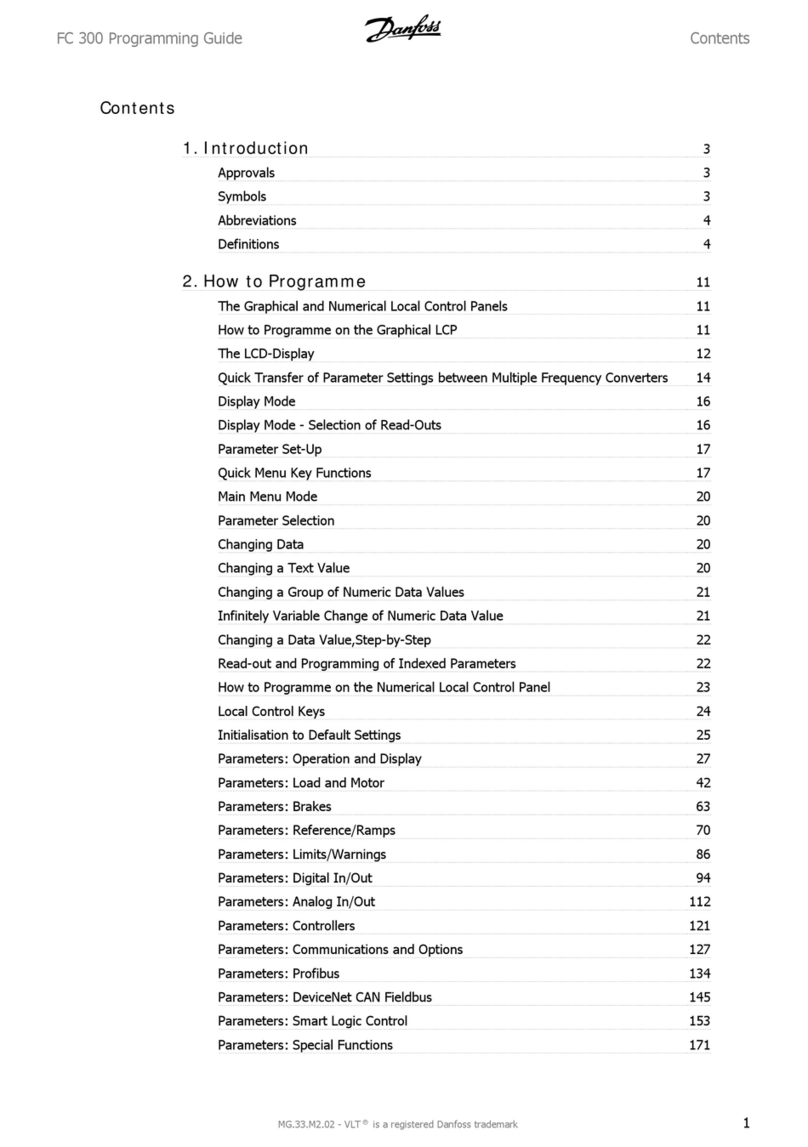
Danfoss
Danfoss FC 300 Programming guide

Leroy-Somer
Leroy-Somer FMV 2307 Installation and Maintenance
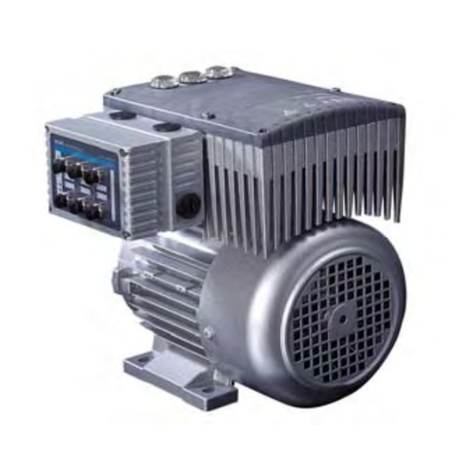
Nord Drivesystems
Nord Drivesystems SK CU4-DEV Supplementary manual
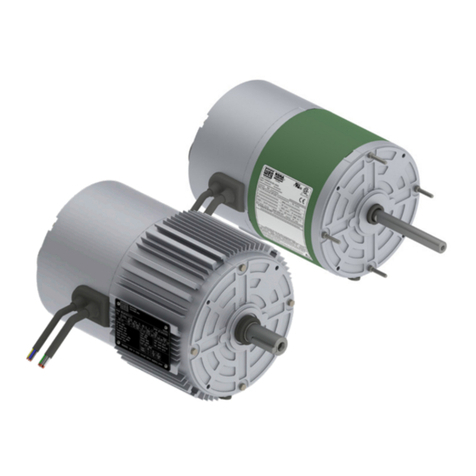
WEG
WEG WECM-AL80-85A2 Installation, operation and maintenance manual
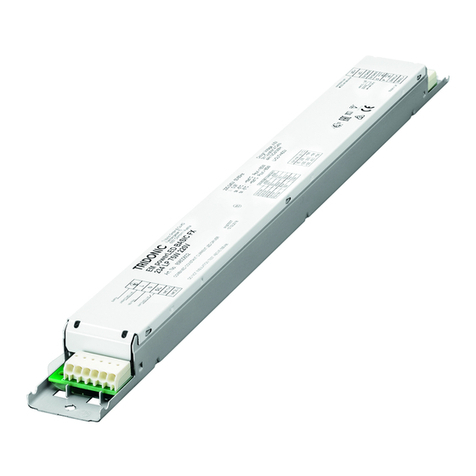
Tridonic
Tridonic EM powerLED BASIC FX lp 75 W manual
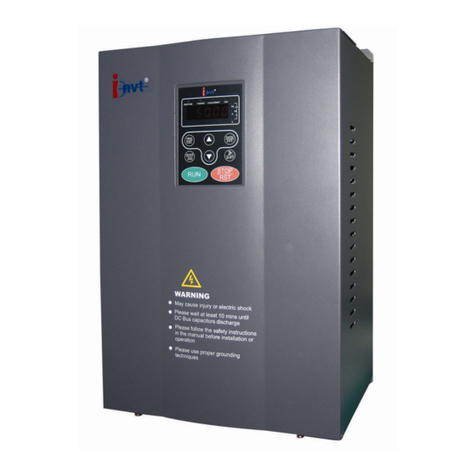
INVT
INVT CHV160 Operation manuals
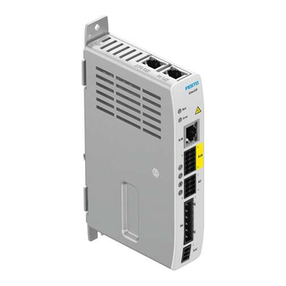
Festo
Festo CMMT-ST-SW Original instructions