Degelman Pro-till 20 Programming manual

OPERATOR & PARTS
MANUAL
DEGELMAN INDUSTRIES LTD.
BOX 830-272 INDUSTRIAL DRIVE,
REGINA, SK, CANADA, S4P 3B1
FAX 306.543.2140 PH 306.543.4447
1.800.667.3545 DEGELMAN.COM
143354 v1.1


PRO-TILL QUICK-START GUIDE*
AConnect Hydraulics
DEPTH
WINGS
TRANSPORT
JACK
3
4
2
14
1
3
2
FLOAT
FLOAT
3 3
4
22
1
11
1
* Refer to operators manual for
complete safety and operation info.
• Hydraulic Connections & Hoses
• Working points & pins
• Hubs & Spindles
• Tire Pressure: 58 PSI (400 kPa)
• Check for missing, worn or
damaged parts.
Maintenance
(Check Machine Daily)
PITCH
ADJUSTMENT
PITCH
ADJUSTMENT
143357 v1.1

BPut in Field Position
iv)
i)
ii)
iii) v)
FMAX Transport Speed: 40 km/h (25 MPH)
DTest. Check. Adjust.
10-12 MPH
100m
ERaise for Headland Turns.
1
CSet Cutting Depth
3
2
Scraper Position Overview (Rubber Rollers)
Storage
Position
Maintenance
Position
Engaged
Position
Remove the 4 bolts to rotate into
or out of “Storage position”,
then re-install.
Loosen the 4 bolts to rotate up into
“Maintenance
position”
& secure.
Loosen the 4
bolts to rotate
downward.
Set the scraper
clearance
(1/4” to 3/8”).
Properly
tighten.
Set Gap distance
at 1/4” to 3/8”
from roller surface.
(Start with 8stops
per cylinder, test
depth & adjust)
(IMPORTANT: Add depth
stops starting from depth plate end )
22
1”
3
3
Depth Adjustment
(2 Inner Wheel Cylinders)
Typically
Set to 2”
1
Pitch Adjustment
(2 Outer Cylinder
Adjustment Rods)

IMPORTANT:
READ MANUAL
* Reference Sheet Quick-Start Guide
OPERATORS SECTION - TABLE OF CONTENTS
IMPORTANT Safety Notice
Introduction 1
Safety 2
Hook-Up 4
Transport 5
Transport to Field Position 6
Field to Transport Position 7
Operation 8
Pre-Operation Checklist 8
Operation Guidelines / Suggestions 9
Setting Disc Depth 10
Scraper Settings 12
Service & Maintenance 13
Maintenance Checklist 14
Repair - Wheel Hub 17
Repair - Wire Ring Hyd Cylinder 18
Repair - Pressed Bushing 19
PARTS SECTION - TABLE OF CONTENTS
Pro-Till Section Overview 21
Hitch Pole Frame Components 22
Wheel & Rockshaft Components 24
Center Frame Components 25
Wing Frame Components 26
Disc Gang Assembly & Components 27
Roller Frame Components 28
Cylinders 29
Hydraulic Routing 30
Light Routing & Components 34
Warranty 36
DEGELMAN INDUSTRIES LTD.
BOX 830-272 INDUSTRIAL DRIVE,
REGINA, SK, CANADA, S4P 3B1
FAX 306.543.2140 PH 306.543.4447
1.800.667.3545 DEGELMAN.COM

IMPORTANT SAFETY REMINDER
Changing Discs and Servicing
The best position to safely change
or service the discs on the Pro-Till
is when it is secured in the winged
forward transport position.
DANGER - NEVER PARK, UN-HOOK, or
SERVICE Pro-Till with REAR WINGS RAISED
DANGER
If the front hitch becomes disconnected in this
position the front hitch will raise suddenly and
the back of the machine will drop!

-1-
143354 - PRO-TILL (08-September-2017)
Introduction
OPERATOR ORIENTATION - The directions left, right, front and rear, as mentioned throughout the manual,
are as seen from the tractor drivers’ seat and facing in the direction of travel.
CONGRATULATIONS on your choice of a Degelman PRO-TILL to complement your farming operation. It has
been designed and manufactured to meet the needs of a discerning agricultural market. Degelman PRO-TILL
shreds heavy fall residue, opens up spring fields, levels ruts, destroys clods and produces an absolutely perfect
seed bed. Degelman PRO-TILL is the fastest and most versatile piece of tillage equipment you will ever own.
Use this manual as your first source of information about this machine.
TO THE NEW OPERATOR OR OWNER - Safe, efficient and trouble free operation of your Degelman PRO-TILL
requires that you and anyone else who will be operating or maintaining it, read and understand the Safety,
Operation, Maintenance and Troubleshooting information contained within this manual.
By following the operating instructions in conjunction with a good maintenance program your machine will
provide many years of trouble-free service. Keep this manual handy for frequent reference and to pass on to
new operators or owners. Call your Degelman Dealer if you need assistance, information, or additional copies
of the manual.
Front Hitch
Hyd.
Jack
Center Frame
Hitch Pole Frame
RH Wing
Roller Assembly
LH Wing
Roller Assembly
LH Wing
Frame
RH Wing
Frame
LH SIDE RH SIDE

-2-
143354 - PRO-TILL (08-September-2017)
CAUTION
DANGER
WARNING
The Safety Alert Symbol identifies important
safety messages applied to the PRO-TILL and in this
manual. When you see this symbol, be alert to the
possibility of injury or death. Follow the
instructions provided on the safety messages.
The Safety Alert Symbol means:
ATTENTION!
BECOME ALERT!
YOUR SAFETY IS INVOLVED!
DANGER: Indicates an imminently hazardous situation
that, if not avoided, WILL result in death or serious injury
if proper precautions are not taken.
WARNING: Indicates a potentially hazardous
situation that, if not avoided, COULD result in death or
serious injury if proper precautions are not taken.
CAUTION: Indicates a potentially hazardous situation
that, if not avoided, MAY result in minor or moderate
injury if proper practices are not taken, or, serves as a
reminder to follow appropriate safety practices.
Why is SAFETY important to YOU?
3 BIG Reasons:
•Accidents Can Disable and Kill
•Accidents Are Costly
•Accidents Can Be Avoided
Note the use of the Signal Words: DANGER, WARNING, and CAUTION with the safety messages.
The appropriate Signal Word has been selected using the following guidelines:
SAFETY ALERT SYMBOL
SIGNAL WORDS
Safety

-3-
143354 - PRO-TILL (08-September-2017)
1. Read and understand the Operator’s
Manual and all safety signs before
operating, maintaining or adjusting.
2. Install and properly secure all shields and
guards before operating. Use hitch pin with a
mechanical locking device.
3. Have a first-aid kit available for use
should the need arise and know
how to use it.
4. Have a fire extinguisher available
for use should the need arise and
know how to use it.
5. Wear appropriate protective gear.
This list includes but is not limited to:
• A hard hat
• Protective shoes with slip resistant soles
• Protective glasses or goggles
• Heavy gloves
• Wet weather gear
• Hearing protection
• Respirator or filter mask
6. Clear the area of people, especially small
children, and remove foreign objects from the
machine before starting and operating.
7. Do not allow riders.
8. Stop tractor engine, set park brake, remove
ignition key and wait for all moving parts to
stop before servicing, adjusting, repairing or
unplugging.
9. Review safety related items with all operators
annually.
YOU are responsible for the safe operation and
maintenance of your Degelman PRO-TILL.
YOU must ensure that you and anyone else who
is going to operate, maintain or work around
the PRO-TILL be familiar with the operating and
maintenance procedures and related SAFETY
information contained in this manual.
This manual will take you step-by-step through
your working day and alerts you to all good safety
practices that should be adhered to while operating
this equipment.
Remember, YOU are the key to safety. Good safety
practices not only protect you but also the people
around you. Make these practices a working
part of your safety program. Be certain that
EVERYONE operating this equipment is familiar
with the recommended operating and maintenance
procedures and follows all the safety precautions.
Most accidents can be prevented. Do not risk injury
or death by ignoring good safety practices.
• PRO-TILL owners must give operating
instructions to operators or employees
before allowing them to operate the
PRO-TILL, and at least annually thereafter
per OSHA regulation 1928.51.
• The most important safety device on this
equipment is a SAFE operator. It is the
operator’s responsibility to read and
understand ALL Safety and Operating
instructions in the manual and to follow
these. All accidents can be avoided.
• A person who has not read and
understood all operating and safety
instructions is not qualified to operate the
machine. An untrained operator exposes
himself and bystanders to possible serious
injury or death.
• Do not modify the equipment in any way.
Unauthorized modification may impair the
function and/or safety and could affect the
life of the equipment.
• Think SAFETY! Work SAFELY!
Safety
SAFETY GENERAL SAFETY

-4-
143354 - PRO-TILL (08-September-2017)
Raised
Position
The PRO-TILL should always be parked on a level, dry
area that is free of debris and foreign objects. Follow this
procedure to hook-up:
1. Clear the area of bystanders and remove foreign
objects from the machine and working area.
2. Make sure there is enough room to back the tractor
up to the trailer hitch.
3. Start the tractor and slowly back it up to the hitch point.
4. Connect the hydraulic.
• Use a clean cloth or paper towel to clean the couplers
on the ends of the hoses. Also clean the area around
the couplers on the tractor. Remove the plastic plugs
from the couplers and insert the male ends.
• Be sure to match the pressure and return line to one
valve bank.
• Hoses have be labelled in a suggested order of
priority from most used to least:
(1) Depth (2) Wings 3) Transport (4) Jack
5. Use the hydraulic jack controls to raise or lower the
hitch to align with the drawbar.
IMPORTANT: Close the ball valve to prevent accidental
operation of this circuit. Ensure ball valve handle remains
in closed position.
WARNING:Tractor MUST be equipped with a clevis
hitch to prevent unit from tipping upward while folding
into and out of transport. A safety chain must also
always be properly installed.
6. Slowly back tractor up to align the hitch.
7. Install a drawbar pin with provisions for a mechanical
retainer such as a KLIK pin. Install the retainer.
8. Install a safety chain between the tractor and the hitch.
9. Connect lights (electrical socket plug) to tractor.
10. Raise the hydraulic hitch jack.
11. When unhooking from the tractor, reverse the above
procedure.
HOOK-UP / UNHOOKING
Hook-Up
WARNING/DANGER:Never disconnect Pro-Till
from tractor if rear sections of machine are partially
raised. Negative Hitch Weight may result, the hitch
pole may suddenly raise, and the rear section would
come crashing down. Only disconnect when unit is on
level ground in the proper transport or field position.
WARNING/DANGER:Tractor MUST be properly
equipped with a clevis hitch and safety chain to
prevent Negative Hitch Weight occurring when
raising or lowering the rear sections. If the unit is not
properly attached to the tractor with a clevis hitch and
safety chain, the negative hitch weight could result in
the hitch pole suddenly raising and the rear section to
come crashing down.

-5-
143354 - PRO-TILL (08-September-2017)
1. Read and understand ALL the information in
the Operator’s Manual regarding procedures
and SAFETY when operating the PRO-TILL in the
field/yard or on the road.
2. Check with local authorities regarding machine
transport on public roads. Obey all applicable
laws and regulations.
3. Always travel at a safe speed. Use caution when
making corners or meeting traffic.
4. Make sure the SMV (Slow Moving Vehicle) sign,
and all the lights and reflectors that are required
by the local highway and transport authorities
are in place, are clean and can be seen clearly
by all overtaking and oncoming traffic. Be
sure to check with local highway authorities
and comply with their lighting and transport
requirements.
5. Keep to the right and yield the right-of-way to
allow faster traffic to pass. Drive on the road
shoulder, if permitted by law.
6. Always use hazard warning flashers on tractor
when transporting unless prohibited by law.
7. Always use a pin with provisions for a
mechanical retainer and a safety chain when
attaching to a tractor or towing vehicle.
TRANSPORT SAFETY
Use the following guidelines while transporting the
PRO-TILL:
1. Use a safety chain and a pin with provisions for
a mechanical retainer.
2. Ensure Pro-Till is in the full transport position with
the wing rollers secure and properly in place.
3. Ensure debris that may fall or become dislodged
during transport is removed.
4. Be sure hazard lights are flashing and SMV
decal is visible.
5. MAXIMUM RECOMMENDED TRANSPORT
SPEED: MAX 40 km/h or 25 mph.
(Road Conditions, Field speeds may be lower.)
Due to weight of the machine and tire ratings,
do not exceed the recommended maximum
speeds or severe tire damage / excessive wear
may occur.
IMPORTANT: UNDER NO
CIRCUMSTANCES SHOULD
THERE EVER BE RIDERS WHILE
THE PRO-TILL IS IN TRANSPORT.
TRANSPORTING
RIDERS
Transport

-6-
143354 - PRO-TILL (08-September-2017)
3
Transport to Field Position Overview
TRANSPORT TO FIELD POSITION
B. Slightly extend the Transport Cylinders (#3) just
enough to remove the weight of wings off from
the wing transport carriers. Do not lift more than
needed.
IMPORTANT:DO NOT fully extend the transport
cylinders at this point. Follow proper procedures to
prevent possible equipment damage or failure.
D. After fully opening the wings, extend the Transport
Cylinders (#3) to completely lower the Pro-Till rear
frame sections to the ground.
NEVER LIFT WINGS!
Unfold using the Wing Cylinders (2),
then lower all rear sections using
the Transport Cylinders (3).
A. On level ground,
position the Pro-Till
so it is straight in-line
behind the tractor.
FOLLOW PROCEDURE BELOW:
C. Extend the Wing Cylinders (#2) to fully open the
wings behind the machine.
1”
3
22
E. Place both the Transport Cylinders (#3) and the
Wing Cylinders (#2) into the FLOAT position before
operation.
IMPORTANT:
The Transport & Wing Cylinders
MUST both be in the "FLOAT"
position in order for the Pro-Till
to properly contour the ground
and to avoid possible cylinder
or equipment damage.
3
2

-7-
143354 - PRO-TILL (08-September-2017)
NEVER LIFT WINGS!
Lift rear sections using the Transport
Cylinders (3), then fold the wings forward
using the Wing Cylinders (2).
Field to Transport Position Overview
FIELD TO TRANSPORT POSITION
FOLLOW PROCEDURE BELOW:
E. With the wings in the
proper position, retract the
Transport cylinders (#3) fully
lowering the wings onto the
wing transport carriers.
D. When the wings get close to the wing transport
carriers, you may need to slightly extend the
Transport cylinders (#3) so the rollers can reach
the correct position.
1”
Wing
Transport
Carrier
3
May need to
raise over hump
33
IMPORTANT:DO NOT retract the Wing cylinders to
raise the wings at this point. Follow proper procedures to
prevent possible equipment damage or failure.
B. Retract the Transport cylinders (#3), fully raising
the complete rear section.
NOTE:It is important to fully raise the disc frames
up as high as possible as it puts the rollers and
wheels in the correct position for low transport.
A. In field position, fully extend the Depth (#1)
cylinders (Wheels & Rollers) to completely raise the
disc frames.
22
C. After raising all the rear sections, retract the
Wing cylinders (#2) to bring both wings inward
towards the frame.

-8-
143354 - PRO-TILL (08-September-2017)
Before operating the machine and each time thereafter,
the following areas should be checked off:
1. Inspect the machine per the schedule outlined in
the “Maintenance Section”.
2. Use only a tractor with adequate power to pull the
PRO-TILL under ordinary operating conditions.
NOTE: It is important to pin the drawbar in the
central location only.
3. Ensure that the machine
is properly attached to
the tractor using a clevis
hitch, safety chain and
a drawbar pin with
provisions for a mechanical retainer. Make sure
that a retainer such as a Klik pin is installed.
WARNING:Negative Hitch Weight may occur
when raising or lowering the rear sections. If the
unit is not properly attached to the tractor with a
clevis hitch and safety chain, the negative hitch
weight could result in the hitch pole to suddenly
raise and the rear sections to come crashing down.
4. Before using, inflate tires to:
Tires (382 FLOTRUCK):
600/50 R22.5: 58 PSI (400 kPa)
5. Check oil level in the tractor hydraulic reservoir.
Top up as required.
6. Inspect all hydraulic lines, hoses, fittings and
couplers for tightness. Tighten if there are leaks.
Use a clean cloth to wipe any accumulated
dirt from the couplers before connecting to the
tractor’s hydraulic system.
7. Inspect the condition/wear of the discs. If needed
or desired, adjust the Disc Cutting Depth as
outlined in the adjustments section. If excessive
disc wear is evident, replacement may be
required. Refer to maintenance section.
PRE-OPERATION CHECKLIST
It is important for both personal safety and maintaining
good operational condition of the machine that the pre-
operational checklist be followed.
1. Read and understand the Operator’s Manual
and all safety signs before using.
2. Stop tractor engine, set park brake, remove
ignition key and wait for all moving parts to
stop before servicing, adjusting, repairing or
unplugging.
3. Keep hands, feet, hair
and clothing away
from all moving and/
or rotating parts.
4. Do not allow riders on the PRO-TILL tractor
during operation or transporting.
5. Keep all shields and guards in place when
operating (if applicable).
6. Clear the area of all bystanders, especially
children, before starting.
7. Do not operate machine on overly steep side hills
or slopes.
8. Be careful when working around or maintaining
a high-pressure hydraulic system.
Ensure all components are tight and in good
repair before starting.
OPERATING SAFETY
Although there are no operational restrictions on the
PRO-TILL when it is new, there are some checks that
should be done when using the machine for the first
time, follow this procedure:
IMPORTANT:It is important to follow the Break-In
procedures especially those listed in the “Before using”
section below to avoid damage:
A. Before using:
1. Read Safety Info. & Operator’s Manual.
2. Complete steps in “Pre-Operation Checklist”.
3. Lubricate any grease points.
4. Check all Bolt Tightness.
5. Adjust Disc Cutting Depth as outlined in
the “Setting Disc Depth” section.
B. After operating for 2 hours:
1. Check all hardware. Tighten as required.
2. Check all hydraulic system connections.
Tighten if any are leaking.
BREAK-IN
Operation

-9-
143354 - PRO-TILL (08-September-2017)
Operation
1. Place both the Wing
Cylinders (#2) and the
Transport Cylinders (#3)
into the FLOAT position
before operation.
IMPORTANT:The
Transport Cylinders and
Wing Cylinders MUST
both be in the FLOAT
position for the PRO-TILL to contour properly and to
avoid possible cylinder or equipment damage.
2. Maximum operating speed is recommended at
approximately 12 to 14 mph.
Minimum operating speed is recommended at
approximately 7 mph.
3. When making headland turns, the operator
may wish to slightly raise the disc sections by
activating the Depth Cylinders (#1). Remember to
lower after coming out of the turn.
4. Each time you start a new field you may need
to adjust the cutting depth depending on the type
of crop residue or soil conditions. The operator
can adjust the cutting depth by raising/lowering
the front or rear sets of discs by following the
guidelines in the “Setting Disc Depth” section.
5. After making adjustments to the cutting depth it
is recommended to bring the Pro-Till up to speed
(10-12mph) to test the depth setting by driving
about 100m (cutting performance changes
dramatically from a slow speed to high speed).
Stop, check depth and cut of field, re-adjust the
height higher or lower, if needed, based on your
preference. Remember: Removing one depth stop
lowers cutting depth 1/2” deeper, Adding one
depth stop raises discs up 1/2” higher.
6. Check/adjust the deflector shield height setting.
7. Harder, packed soil may require additional
passes for optimum results. It is recommended
to do a second pass at an angle to the original
pass.
OPERATING GUIDELINES

-10-
143354 - PRO-TILL (08-September-2017)
Disc Depth
Adjustment
IMPORTANT: You may need to adjust the deflector
height according to soil penetration. Best setting is
when deflector runs just slightly above the ground.
RECOMMENDED PROCEDURE TO SET DEFLECTOR HEIGHT:
1-Run the machine with discs set to the proper depth.
2-Stop the machine.
3-Adjust the height so the deflector is running just
slightly above the ground.
Adjust "Deflector Angle" when
the Pitch of the Frame is adjusted.
Note: If running Nose up or Nose down,
adjust the deflector angle accordingly.
Typically
Set to 2”
Pitch
Adjustment
Dirt Deflector
DEPTH SETTING OVERVIEW
Adjusting the disc cutting depth is accomplished by
adding or removing a number of spacers from the two
wheel cylinders.
The spacers limit the stroke distance of the cylinders,
changing the amount that the disc frames are lowered.
Each spacer that is added to the cylinders raises the
frame height by 1/2”. Therefore, to lower discs deeper
into the soil, you would remove one spacer for each
1/2” of depth change required.
A typical recommended penetration depth of 2” is
suggested. This depth, however, can be adjusted to the
operators needs and preferences or based on different
crop varieties and soil conditions.
PITCH ADJUSTMENT
Some operators may also prefer to adjust the front or rear
frame disc sections to run slightly higher than the other.
Adjustments to the front to rear disc section height or
"pitch" are done with the threaded pitch adjustment rods:
• Shortening adjustment rod length:
- Lowers the Rear Discs
- Reduces Roller Pressure
• Lengthening adjustment rod length:
- Raises the Rear Discs
- Increases Roller Pressure
NOTE: As the discs wear with usage, the disc depth
settings will also need to be adjusted accordingly.
Use the following as a guideline for setting depth:
1. Drive the PRO-TILL onto level ground. For initial
setup, try "8 Depth Stops" on each cylinder
stop.
2. Fully retract the Depth (#1) cylinders to lower
rear frame to ground.
3. Check the penetration depth of the front and
rear row of discs. Take note of how much you
would like to raise or lower both the front and
rear disc sections - round to the nearest 1/2”.
4. Fully raise the frame back off the ground by
extending the Depth (#1) cylinders.
5. Adjust Disc height at the two front wheel cylinder
positions.
Lower Discs - Remove one Depth Stop for each 1/2”
Raise Discs - Add one Depth Stop for each 1/2”
6. Repeat above procedure until proper depth is
achieved.
7. Adjust Dirt Deflector height as shown below.
SETTING DISC DEPTH & DIRT DEFLECTOR
(Start with 8stops
per cylinder, test
depth & adjust)
(IMPORTANT: Add depth
stops starting from depth plate end )
Operation
NOTE: For better
performance, adjust
pitch slightly down
(lengthen rod length)
to increase roller
pressure.

-11-
143354 - PRO-TILL (08-September-2017)
Deflector Arm
Length Adjustment
Operation
SETTING ADJUSTMENT DISC SETTING DIRT DEFLECTOR ARM DISTANCE
DISENGAGING DIRT DEFLECTOR
This adjustable furrow reducer disc allows the
operator to adjust the end disc. It is typically set to
two inches higher than the other discs. If the cutting
depth is lowered and the end disc is leaving too
deep of a groove, the operator should adjust the
disc higher as needed for desired results.
The distance of the deflector arm has three possible
settings that can be adjusted depending on the disc/
frame pitch settings, soil conditions, and preference
of the operator. If the deflector is plugging or
restricting the flow of dirt and trash, you may wish
to move the deflector arm outward.
The dirt deflector may be disengaged or stored in
the upright position by removing the deflector arm
pin, rotating the deflector arm upward 180 degrees,
and re-installing the pin. If preferred, it could also
be completely removed by pulling the pin and
removing.

-12-
143354 - PRO-TILL (08-September-2017)
Operation
SETTING SCRAPER POSITIONSCRAPER POSITION OVERVIEW
Change into Storage Position:
• Loosen & remove the 4 bolts (2 per arm).
• Rotate section upward to new position.
• Reinstall bolts and tighten in place.
• Reverse procedure to put into working position.
Change into Maintenance Position (from engaged):
• Loosen the 4 bolts (2 per arm).
• Rotate section upward until top hole is open.
• Tighten bolts to secure and/or insert bolt or pin
(user supplied) into top hole to secure in position.
Change into Engaged Position (from maintenance):
• Loosen the 4 bolts (2 per arm).
• Rotate section down until scraper blades are at
desired distance from inner roller groove.
(1/4" to 3/8" is the recommended distance)
• Tighten bolts to secure in position.
Storage Position
Maintenance Position
Engaged Position
Gap Distance
1/4”-3/8”
Remove the 4 bolts
to rotate into or
out of “Storage
position”, then
re-install.
Retighten main
bolts or insert a
bolt/pin here to
hold in raised
position.
Hole for
holding in
position for
maintenance.
REVERSING SCRAPER BLADES
Double Sided Blades
Note: Complete section must be
changed at the same time when
blades are being reversed or
adjustment will not work properly.
Heavy Duty Replacement Scraper Blades
requires new hardware (Bolts & Locknuts)
Note: This is a replacement part only that
will work best only after roller has
been run and has relaxed into its
permanent shape. (Qty: 46 or 62)
573320 - HD Scraper Blade
118279 - Bolt, 1/2 x 1-1/2 GR8
118729 - Lock Nut, 1/2 Unitorque

-13-
143354 - PRO-TILL (08-September-2017)
1. Review the Operator’s Manual and all safety items
before working with, maintaining or operating the
PRO-TILL.
2. Stop the tractor engine, set park brake, remove
ignition key and wait for all moving parts to stop
before servicing, adjusting, repairing or unplugging.
3. Keep hands, feet, clothing and hair away from all
moving and/or rotating parts.
4. Clear the area of
bystanders, especially
children, when carrying
out any maintenance and
repairs or making any
adjustments.
5. Place safety stands or large blocks under the frame
before removing tires or working beneath the machine.
6. Be careful when working around or maintaining a
high-pressure hydraulic system. Wear proper eye
and hand protection when searching for a high
pressure hydraulic leak. Use a piece of wood or
cardboard as a backstop when searching for a pin
hole leak in a hose or a fitting.
7. Always relieve pressure before disconnecting or
working on hydraulic system.
8. Never disconnect Pro-Till from tractor if rear sections
of machine are partially raised. See warning below:
MAINTENANCE SAFETY
Service & Maintenance
• Make sure that all components in the hydraulic
system are kept in good condition and are clean.
• Replace any worn, cut, abraded, flattened or
crimped hoses and metal lines.
• Do not attempt any makeshift repairs to the
hydraulic lines, fittings or hoses by using tape,
clamps or cements. The hydraulic system operates
under extremely high-pressure. Such repairs will
fail suddenly and create a hazardous and unsafe
condition.
• Wear proper hand and eye
protection when searching for a
high-pressure hydraulic leak. Use
a piece of wood or cardboard as
a backstop instead of hands to
isolate and identify a leak.
• If injured by a concentrated high-pressure stream of
hydraulic fluid, seek medical attention immediately.
Serious infection or toxic reaction can develop from
hydraulic fluid piercing the skin surface.
• Before applying pressure to the system, make sure
all components are tight and that lines, hoses and
couplings are not damaged.
HYDRAULIC SAFETY
WARNING/DANGER:Never disconnect Pro-Till
from tractor if rear sections of machine are partially
raised. Negative Hitch Weight may
result, the hitch pole may suddenly
raise and the rear section would come
crashing down. Only disconnect when
unit is on level ground in the proper
transport or field position.

-14-
143354 - PRO-TILL (08-September-2017)
The PRO-TILL should be carefully prepared for
storage to ensure that all dirt, mud, debris and
moisture has been removed.
Follow this procedure when preparing to store:
1. Wash the entire machine thoroughly using a
water hose or pressure washer to remove all
dirt, mud, debris or residue.
2. Inspect all parts to see if anything has become
entangled in them. Remove the entangled
material.
3. Lubricate hub and spindle grease fittings to
remove moisture
4. Inspect all hydraulic hoses, fittings, lines and
couplers. Tighten any loose fittings. Replace any
hose that is badly cut, nicked or abraded or is
separating from the crimped end of the fitting.
5. Touch up all paint nicks and scratches to prevent
rusting.
6. Select an area that is dry, level and free of
debris.
7. Store in either Transport or Field position.
8. Use hydraulic cylinder jack.
9. Oil any exposed chrome shafts on the hydraulic
cylinders to prevent rusting.
STORAGE
Service & Maintenance
MAINTENANCE CHECKLIST
After reviewing the Maintenance and Hydraulic
Safety Information, use the Maintenance Checklist
provided for regular service intervals and keep a
record of all scheduled maintenance:
( Initial break-in review. Read full section on pg.8 )
A. Before using:
1. Read Safety Info. & Operator’s Manual.
2. Complete “Pre-Operation Checklist”
3. Check all Bolt Tightness.
4. Adjust Disc Cutting Depth as outlined in
the “Setting Disc Depth” section.
B. After operating for 2 hours:
1. Check all hardware. Tighten as required.
2. Check all hydraulic system connections.
Tighten if any are leaking.
Maintenance Check - 10 Hours
• Check for worn or damaged parts
• Hydraulic fluid leaks
• Damaged hoses
• Check tire pressure:
Tires (382 FLOTRUCK):
600/50 R22.5: 58 PSI (400 kPa)
Maintenance Check - 50 Hours
• Grease hubs & spindles
• Check working points & pins
• Safety signs clean
Annually
• Bolt tightness
• Wheel bearings
IMPORTANT: Safely secure
Pro-Till in winged forward
transport position when
changing or servicing discs.
Other manuals for Pro-till 20
3
This manual suits for next models
1
Table of contents
Other Degelman Tiller manuals
Popular Tiller manuals by other brands
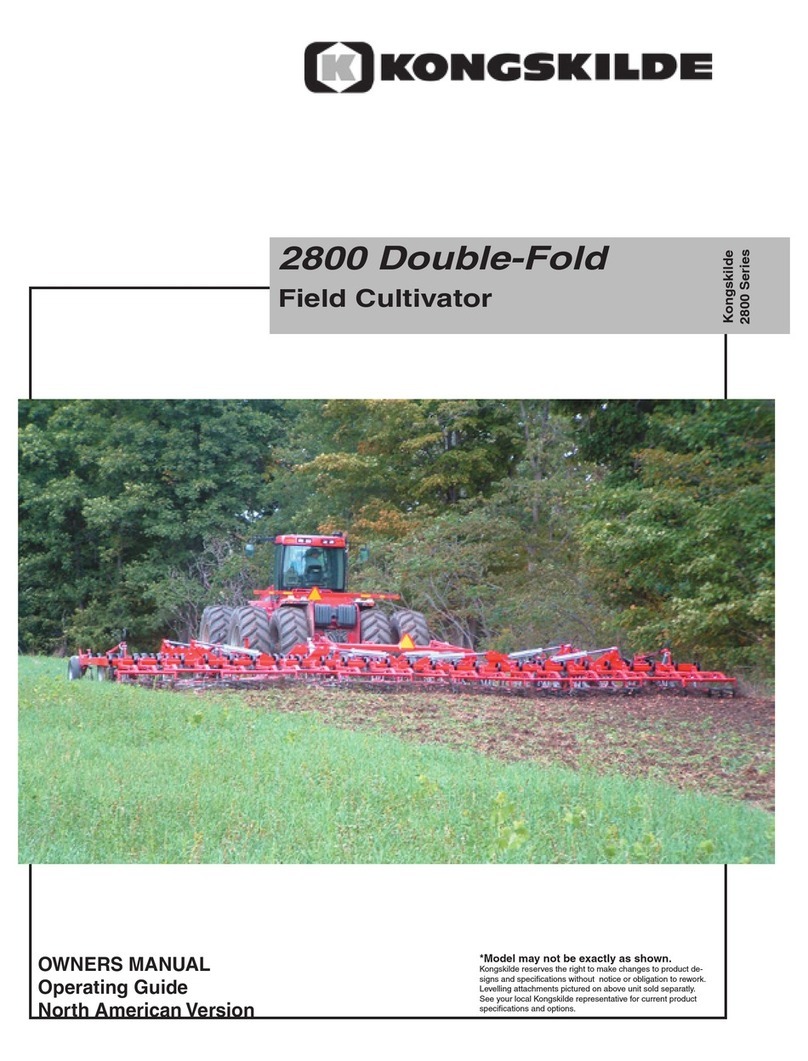
Kongskilde
Kongskilde 2800-10 owner's manual
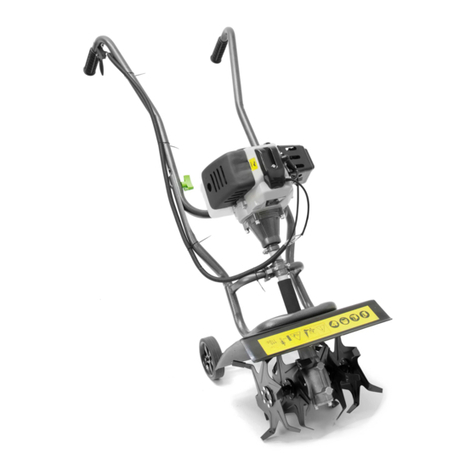
The Handy
The Handy THPMT instruction manual

Remington
Remington Garden Wizard 109312-01 owner's manual

Texas Equipment
Texas Equipment Vision 700 NC Assembly and use instructions
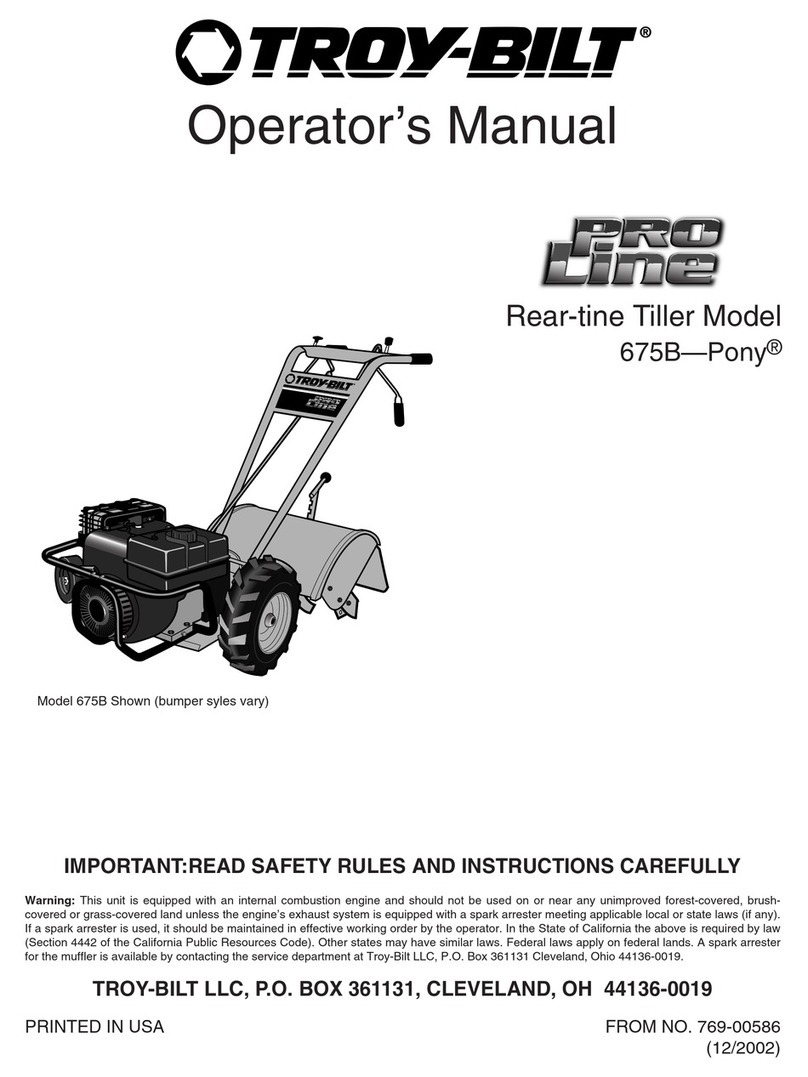
Troy-Bilt
Troy-Bilt 675B Pony Operator's manual

Land Pride
Land Pride FC10 Operator's manual