delta-mobrey Sentry Series Guide

www.delta-mobrey.com
IOM-SENTRY-Ex-C: MAY 2020
Installation, Operation &
Maintenance Instructions
Sentry Series
Models P01, P02, P03 (Pressure Switches)
Models D01, D02, D03 (Differential Pressure
Switches)
Models T01, T02 (Temperature Switches)
General
The unit is manufactured, checked and supplied in
accordance with our published specification, and
when installed and used in normal or prescribed
applications, with the lid in place and within the
parameters set for mechanical and electrical
performance, will not cause danger or hazard to life
or limb.
THE USERS ATTENTION IS DRAWN TO
THE FACT THAT, WHEN THE UNIT IS
‘LIVE’ WITH RESPECT TO ELECTRICAL
OR PRESSURE SUPPLIES, A HAZARD
MAY EXIST IF THE UNIT IS OPENED OR
DISMANTLED.
UNITS MUST BE SELECTED AND
INSTALLED BY SUITABLY TRAINED AND
QUALIFIED PERSONNEL IN
ACCORDANCE WITH APPROPRIATE
CODES OF PRACTICE SO THAT THE
POSSIBILITY OF FAILURE RESULTING IN
INJURY OR DAMAGE CAUSED BY
MISUSE OR MISAPPLICATION IS
AVOIDED.
Operating Principles
Pressure Switch models P0* and Differential
Pressure Switch models D0* are diaphragm
operated switches.
These diaphragms generate a force proportional to
the applied pressure and are balanced by a user
adjustable control spring. When the force exceeds
that created by the control spring, the diaphragm
moves causing a push rod to actuate a snap-acting
micros-witch.
Temperature models T01 & T02 work in the same
way as the Pressure models with the exception that
the applied pressure comes from the expansion of a
vapour enclosed in either a rigid stem or semi-rigid
thermal system.
CERTIFICATIONS
Flameproof models carry the following label
markings:
This equipment may be used in zones 1 & 2 with
gases groups IIA, IIB & IIC and dusts groups IIIA,
IIIB & IIIC for temperatures classes T1, T2, T3, T4,
T5 & T6.
Intrinsic Safety Model
Input limitations for intrinsic safety:
Ui = 30V, Ii = 300mA, Pi = 0.6W
This equipment may be used in zones 0, 1 & 2 with
gases groups IIA, IIB & IIC and dusts groups IIIA,
IIIB & IIIC for temperatures classes T1, T2, T3, T4,
T5 & T6.
Special Conditions of Use
Intrinsically safe models
1. The Sentry Pressure, Differential Pressure
and Temperature Switches must not be
installed in a location where moving dust flow
can generate an electrostatic charge on the
equipment.
2. The Sentry range of pressure switches may be
provided with an aluminium alloy or stainless steel
enclosure. For models that have an aluminium
enclosure, identified in the model number by
5xxxxxxxxxxxxxxxx where 'X' describes other
parameters of the equipment, the enclosure must be
installed in such a manner that it is protected from
sources of impact and friction when installed in its
end-use application.
INSTALLATION
Mounting (All models)
The instruments are designed to be mounted
vertically with the process connection underneath.
However, mounting up to 45° from the vertical in any
plane is acceptable, although a small calibration
shift may occur.

www.delta-mobrey.com
IOM-SENTRY-Ex-C: MAY 2020
Use only certified adaptors for Zone 1/Div 1.
Unused entries are to be fitted with suitably certified
stopping plugs.
The three switch terminals are clearly marked
“NORMALLY CLOSED”, “NORMALLY OPEN” and
“COMMON”.
The following diagram can be used as a guide for
wiring.
Insert bare wires fully into the terminal block and
tighten securely. Keep wiring tails to a minimum and
check that wires do not interfere with the operating
mechanism. Use the earthing / grounding points
provided.
BEFORE CLOSING THE LID:
• ENSURE WIRE IS CLEAR OF ALL
MOVING PARTS.
• ENSURE THAT WIRES DO NOT
TOUCH THE LID AS IT IS CLOSED.
Close the lid, being careful not to trap any wires in
doing so. Securely tighten the M3 lid locking screw
set provided using a 1.5mm hex key.
OPERATION
Adjustments
Pressure and Temperature Switches are supplied
calibrated at the midpoint of their range and to a
falling pressure or temperature unless otherwise
specified.
To re-calibrate:
1. Isolate the instrument from the process and
power.
2. Slacken the set point lock screw.
3. Using a suitable spanner, rotate the range
adjuster clockwise to increase the set point and
counter-clockwise to decrease the set point.
4. Tighten the set point lock screw.
5. Close the instrument lid and tighten lid lock screw
They can be mounted either direct to process, or to
a wall or panel using the mounting holes provided.
Select the mounting point so as to avoid excessive
shock, vibration or temperature fluctuation.
Instruments should be mounted to avoid excessive
heat transfer from the process lines or adjacent
plant. To avoid undue stresses being imparted to the
instrument when wall/panel mounted, it is
recommended that a short length of flexible line be
installed between the instrument and process line. If
sudden changes of pressure (pulsations) are likely
then we recommend that snubbers are fitted
between the process line and instrument. Use a
spanner to support the process connection when
fitting the instrument.
CHECK THE CONNECTION THREAD SIZE
AND SPECIFICATION ON THE UNIT TO
AVOID MIS-MATCHING WITH THE
PROCESS CONNECTION ADAPTOR. SEE
DIGIT 11 OF PRODUCT CODE.
Mounting (T01 - Rigid Stem)
Assemble the unit via a thermowell, using the
spanner facility provided and ensuring that:
a) the sensing bulb is fully immersed in
the process temperature
b) the sensing bulb does not bottom out in
the thermowell which could cause
damage
Mounting (T02 - Capillary system)
Mount the sensing bulb so that the capillary end is
above the bulb and the bulb is level with, or no more
than 250mm below the base of the instrument. The
stem is fitted with a sliding compression gland to
accommodate different thermowells.
Wiring
DISCONNECT ALL SUPPLY CIRCUITS
BEFORE WIRING
WIRE IN ACCORDANCE WITH LOCAL
AND NATIONAL CODES. USE CABLES
NO LARGER THAN 2.5 MM2 (14 AWG)
DO NOT EXCEED ELECTRICAL RATINGS
STATED IN LITERATURE AND ON
NAMEPLATES.
1 or 2 electrical entries are provided, into which
cable glands can be assembled. The thread type
and size is marked on the enclosure, just below the
connection. Select a suitable cable gland which will
maintain the IP rating of the instrument.
USE ONLY SUITABLY ZONE 1 CERTI-
FIED CABLE GLANDS OR STOPPING
PLUGS. CABLE TEMPERATURES MAY
EXCEED 80°C. USE ONLY CABLES WITH
SUITABLE OPERATING TEMPERATURE
RANGE.

IOM-SENTRY-Ex-C: MAY 2020
www.delta-mobrey.com
Replacement Parts
Use only factory authorised parts and the fitting in-
structions that are supplied.
Warranty
See Standard Conditions of Sale.
OPERATION
(Continued)
Note: For accurate setting of Pressure and
Differential Pressure models, a suitable pressure
gauge must be used in conjunction with the above
procedure. Do not attempt to set the switch outside
the scale limits. For Temperature models a suitable
calibrated temperature source should be used.
Though the unit may be set anywhere within its
range, for optimum performance, it is good practice
to have a set point value between 25% and 75% of
span.
The striker screw and lock nut are factory set and
should not be adjusted. Should these parts be
accidentally loosened, please contact Delta for
assistance.
MAINTENANCE
Inspections should be carried out at quarterly to
yearly intervals depending upon operating
conditions. Isolate the unit from process and power
and remove the lid. Check all terminals for
tightness. Check that cable tails are not fouled or
chafed. Check for internal condensation. Check
that the gasket is seated properly in the lid recess
and is not worn. Keep the enclosure and lid clear of
dust build up.
It is recommended that instruments used to provide
an alarm are operated periodically to ensure they
are functioning correctly.
If further maintenance is required seek advice from
Delta Mobrey before attempting repair or
replacement of parts.
Should the diaphragm fail the process will vent to
atmosphere via a control orifice without pressuring
the switch enclosure. Periodically ensure the vent
area does not become blocked and vent plug has
not degraded. Ensure that the vent area is not
obstructed.

IOM-SENTRY-Ex-C: MAY 2020
www.delta-mobrey.com
DIMENSIONS
Model Range DIM A DIM B DIM C
P01 CC, CD, CE 215 88 -
A0, G3 215 63 -
P02 & P03 ALL 195 - -
D01 BC 258 162 89
D02 BD - CE 246 114 77
DC - EA 246 88 77
D03 0D - 0E 271 192 102
DC - EA 271 166 102
Model Probe Code DIM A
T01 & T02 ALL 195 + CAPILLARY/BULB LENGTH
This manual suits for next models
8
Other delta-mobrey Measuring Instrument manuals
Popular Measuring Instrument manuals by other brands
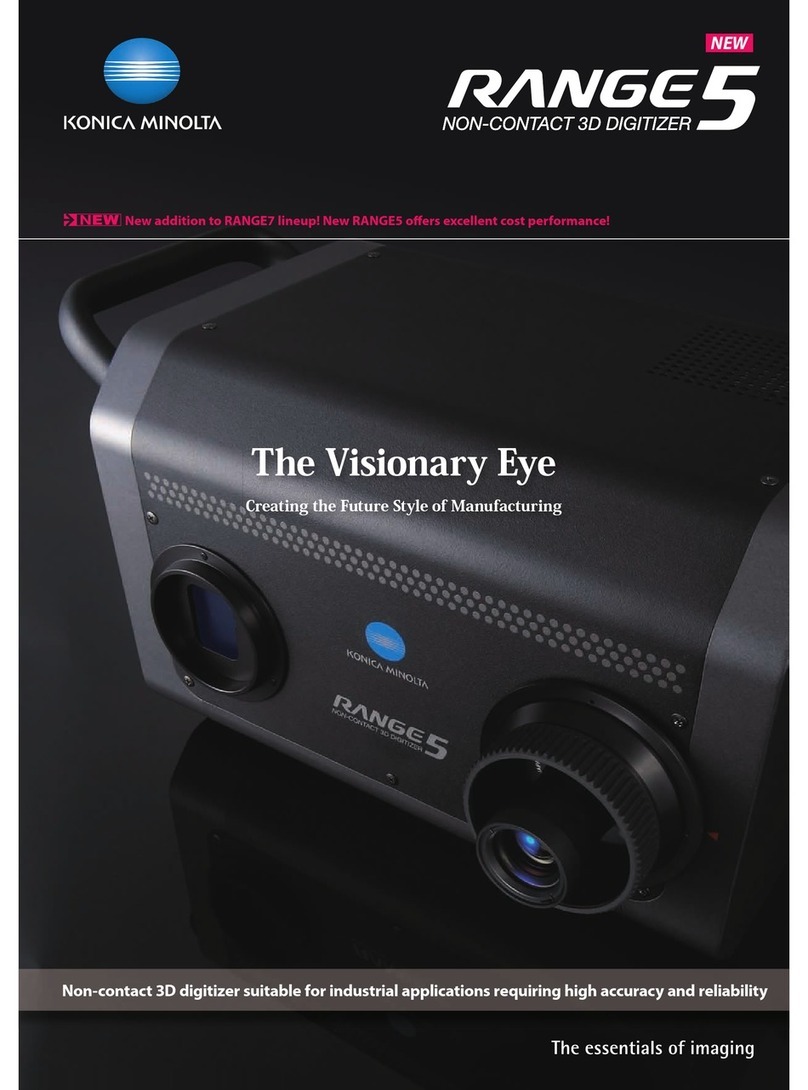
Konica Minolta
Konica Minolta RANGE 5 Brochure & specs
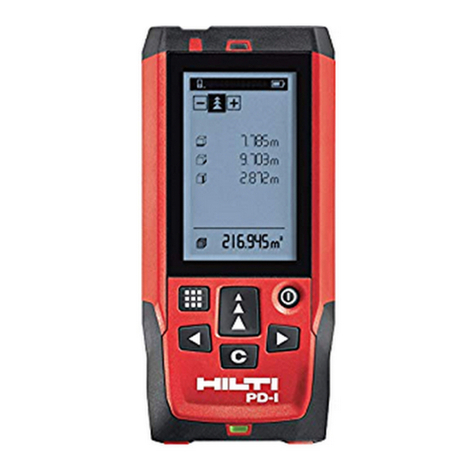
Hilti
Hilti PD-I manual

PCB Piezotronics
PCB Piezotronics IMI SENSORS 646B10 Installation and operating manual
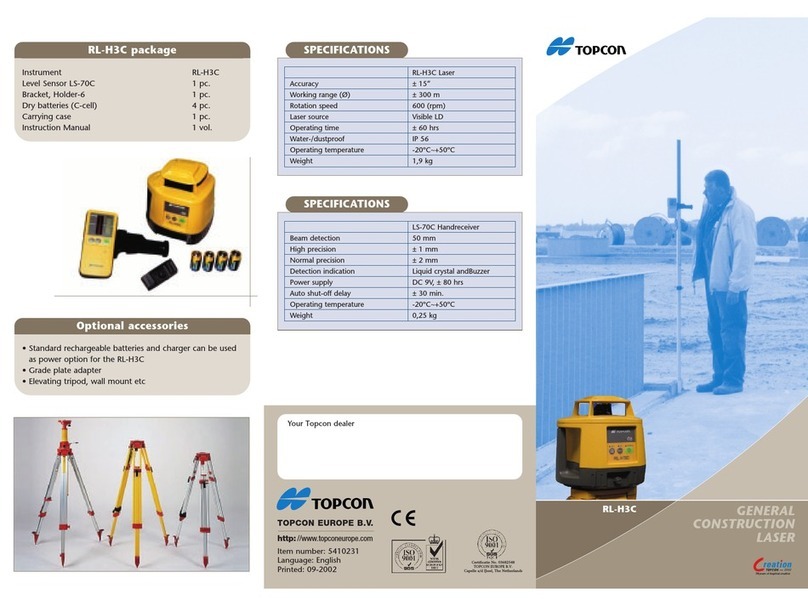
Topcon
Topcon RL-H3C instruction manual
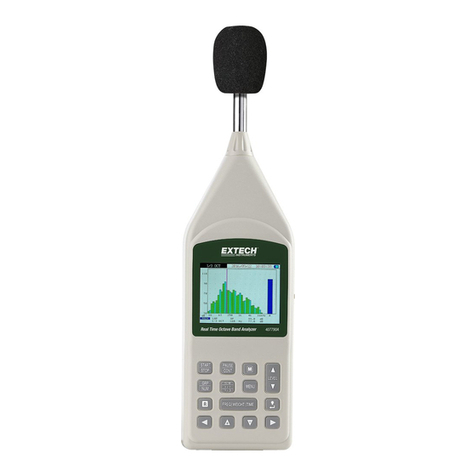
Extech Instruments
Extech Instruments 400790A user manual
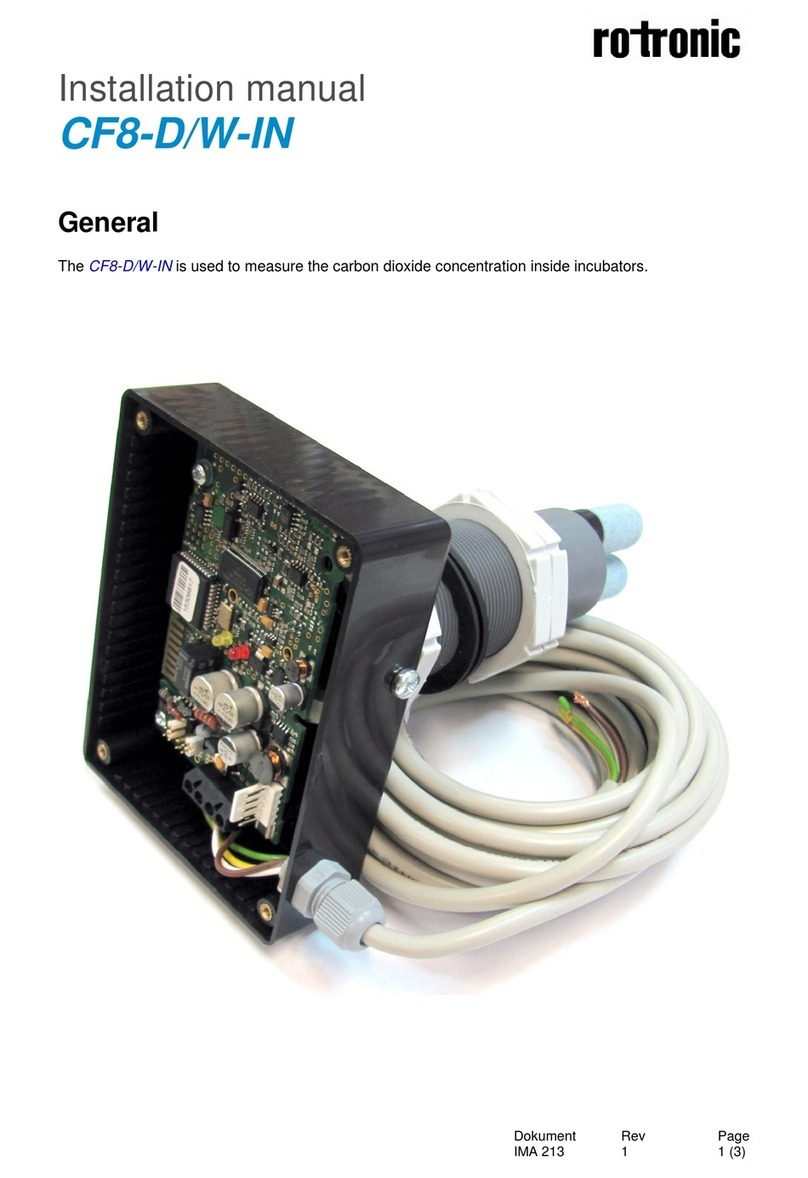
Rotronic
Rotronic CF8-D/W-IN installation manual
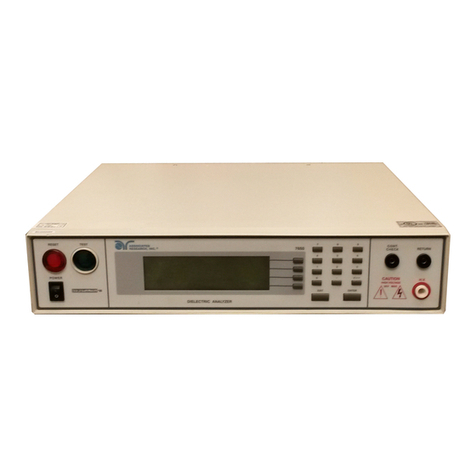
Associated Research
Associated Research 7620 HypotULTRA III Operation and service manual
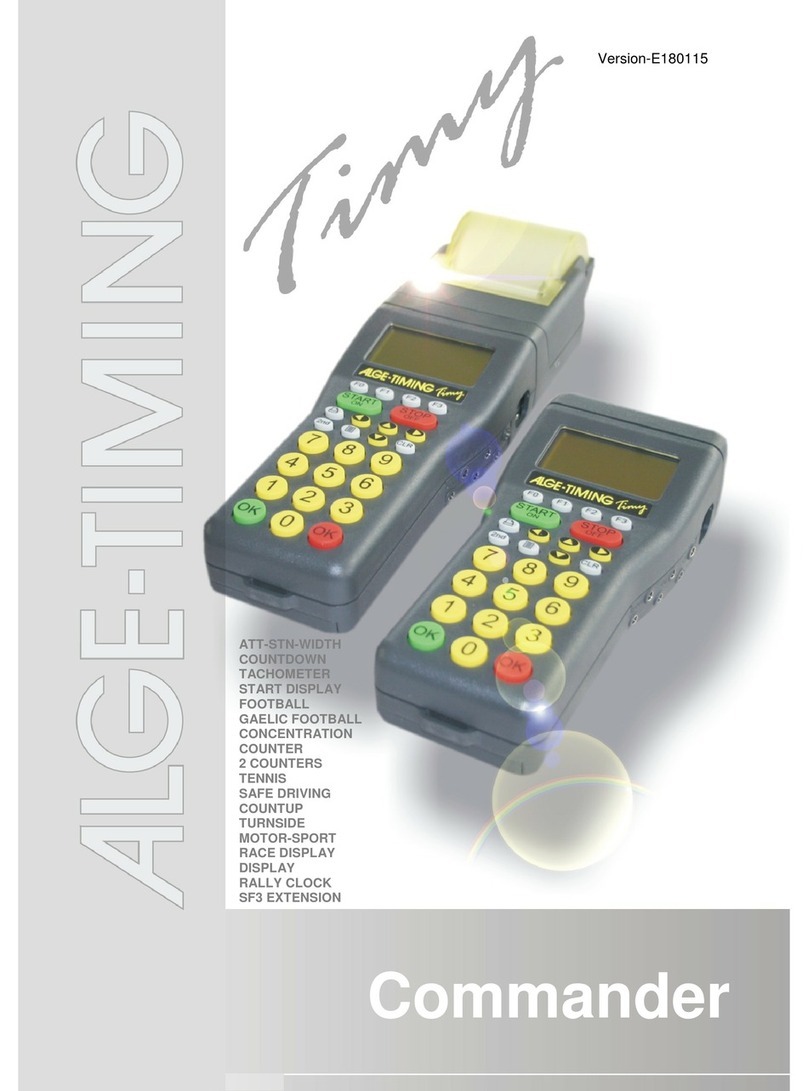
ALGE-Timing
ALGE-Timing Timy Commander manual

ROOTECH
ROOTECH ACCURA 3500 user guide

horiba
horiba LaquaTwin B-771 instruction manual
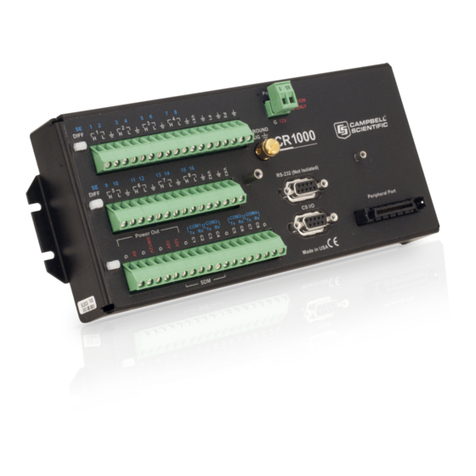
Campbell
Campbell CR1000 Operator's manual

PCB Piezotronics
PCB Piezotronics J353B33 Installation and operating manual