Desoutter EAP1.5-15 Series User manual

© Copyright 2009, Desoutter St Herblain France
All rights reserved. Any unauthorized use or copying of the contents or
part thereof is prohibited. This applies in particular to trademarks, model
denominations, part numbers and drawings. Use only authorized parts.
Any damage or malfunction caused by the use of unauthorised parts is
not covered by Warranty or Product Liability.
Desoutter - ZAC de la Lorie - 38 rue Bobby Sands
BP 10273 - 44818 Saint-Herblain Cedex - France
www.desouttertools.com
Part no
Issue no
Language
Date
Page
6159936431
05
English
09/2009
1 / 23
EAP/EDP
Operator's Manual
N° 6159936431-05

EAP/EDP
Part no 6159936431
Issue no 05
Language English
Date 09/2009
Page 2 / 23
CHAPTER 1 - SAFETY INSTRUCTIONS
1 - SCOPE .................................................................................................................................................3
2 - GENERAL INSTRUCTIONS .............................................................................................................3
3 - PERSONAL SAFETY .........................................................................................................................3
3.1 - Earthing connection .....................................................................................................................3
3.2 - Differential circuit-breaker ..........................................................................................................3
3.3 - Power supply ...............................................................................................................................3
4 - TOOL USE HAZARDS ......................................................................................................................3
5 - TOOL CARE AND SERVICE ............................................................................................................3
CHAPTER 2 - DESCRIPTION AND OPERATION
1 - GENERAL ...........................................................................................................................................4
1.1 - Mains supply ...............................................................................................................................4
1.2 - Features .......................................................................................................................................4
1.3 - Operating temperature .................................................................................................................5
1.4 - Description ..................................................................................................................................6
1.4.1 - Report LEDs .......................................................................................................................6
1.4.2 - Operator interface ...............................................................................................................6
CHAPTER 3 - START-UP
1 - ON RECEIVING THE TOOL .............................................................................................................7
2 - INSTALLATION ................................................................................................................................7
CHAPTER 4 - PROGRAMMING
1 - PROGRAMMING DIRECTLY ON THE TOOL ...............................................................................8
1.1 - Description ..................................................................................................................................8
1.2 - Main programming procedure .....................................................................................................8
1.2.1 - Programming mode ............................................................................................................8
1.2.2 - Parameter choice .................................................................................................................9
1.2.3 - Torque .................................................................................................................................9
1.2.4 - Unit .....................................................................................................................................9
1.2.5 - Learning ..............................................................................................................................10
1.2.6 - Speed ..................................................................................................................................10
1.2.7 - Parameter validation ...........................................................................................................11
2 - PROGRAMMING USING THE CVIP Pocket SOFTWARE .............................................................11
CHAPTER 5 - TIGHTENING RESULTS
1 - TIGHTENING RESULTS ON THE TOOL ........................................................................................12
1.1 - Report LEDs ................................................................................................................................12
1.2 - Buzzer ..........................................................................................................................................13
1.3 - Display ........................................................................................................................................13
1.3.1 - Tightening results ...............................................................................................................13
1.3.2 - Faulty operations ................................................................................................................13
2 - TIGHTENING RESULTS ON THE PDA ..........................................................................................13
CHAPTER 6 - MAINTENANCE
1 - MAINTENANCE LIGHT ...................................................................................................................14
2 - TORQUE TRANSDUCER CALIBRATION ......................................................................................14
3 - ERRORS ..............................................................................................................................................14
4 - TOOL OVERVIEW .............................................................................................................................14
5 - ELECTRICAL CONNECTIONS ........................................................................................................14
APPENDIX 1 - ERROR TABLE .................................................................................................................15
APPENDIX 2 - PART LIST..........................................................................................................................20

EAP/EDP
Part no 6159936431
Issue no 05
Language English
Date 09/2009
Page 3 / 23
CHAPTER 1 - SAFETY INSTRUCTIONS
1 - SCOPE
This tool has been designed to assemble and disassemble screws in wood, metal and plastic materials. No other use will be per-
mitted. For professional use only.
2 - GENERAL INSTRUCTIONS
General safety instructions are collected in the 6159930690 safety booklet.
Specific instructions are given below.
SAVE THESE INSTRUCTIONS CAREFULLY
3 - PERSONAL SAFETY
3.1 - Earthing connection
3.2 - Differential circuit-breaker
Always use a differential circuit breaker to protect the operator from electric shock. A differential circuit breaker in the
power supply to the tool detects any insulation defect between the phases of the network and the earth and immediately cuts off
the power supply to the tool.
3.3 - Power supply
Always use the cord supplied with the tool to connect to the mains power supply or CP Data Transfer Unit (DTU) only.
Do not modify the cord or use it for other purposes. Use only genuine CP replacement parts. Failure to follow these instruc-
tions may result in electric shock.
4 - TOOL USE HAZARDS
The selection of the tool takes account of the operating conditions as stated by the user, who shall not exceed the operating limits
as specified by the manufacturer at the time of the selection (see "Max duty cycle" file on the CDRom supplied).
Any excessive internal temperature of the tool electric motor if higher than 60°C is detected and stops the tool. It can start again
only if the temperature decreases to under 50°C.
Although our cables are designed to work under drastic conditions, we recommend that you check the following points for longer
service life:
• bending radii should not be lower than 10 times the cable diameter,
• friction with the outer sheath should be restricted,
• any direct pull on the cable should be avoided.
5 - TOOL CARE AND SERVICE
Only experienced and qualified personnel (authorised electricians) are entitled to open and have access to the inside of
the tool. If in doubt, return the tool to a CP-authorized service centre (contact your local CP Sales for details).
Disconnect from power supply and wait one minute before commencing service operations. Failure to wait one minute may
result in electric shock from undischarged capacitors.
Beware hot components. There is a risk of burning by internal components which can reach 75°C (170°F). Allow to cool before
handling.
To reduce risk of injury, everyone using, installing, repairing, maintaining, changing accessories on, or working
near this tool must read and understand the safety instructions before performing any such task. Failure to follow
all instructions listed below, may result in electric shock, fire and/or serious personal injury.
WARNING: this power tool must be earthed.

EAP/EDP
Part no 6159936431
Issue no 05
Language English
Date 09/2009
Page 4 / 23
CHAPTER 2 - DESCRIPTION AND OPERATION
1 - GENERAL
EAP/EDP tools are electric fastening tools directly supplied by mains. They are fitted with a torque transducer for high-precision
torque control. Main parameters (torque; speed) can be adjusted directly on the tool using a display and 3 programming keys. It
is also possible, whatever the option, to completely programme the tool and to save the parameters using a PDA (Personal Digital
Assistant) via a wireless connection between the tool and the PDA.
There are several options:
1.1 - Mains supply
There are 2 types of tools:
• one tool which works with 230 VAC mains voltage, ± 8%, 50/60Hz
• one tool which works with 115 VAC mains voltage, ± 8%, 50/60Hz
Although the peak power can reach 2 kW during the final speed phase, it is recommended to adjust the power circuits according
to the maximum average power.
The average power input depends on the tool type, the assembly type and the tightening rate. However, for heat dissipation rea-
sons, the maximum average power can not exceed 0.3 kW.
1.2 - Features
Values measured in individual work places may be higher than the declared values. The actual exposure values and risk of harm
experienced by an individual user are unique and depend upon the way the user works, the workstation design, as well as upon
the exposure time and the physical condition of the user.
We, CP, cannot be held liable for the consequences of using the declared values, instead of values reflecting the actual exposure,
in an individual risk assessment in a work place situation over which we have no control.
"Standard" (T) screwing with a preset torque value,
informing the user that the assembly has been properly carried out.
"Advance" (TA) ensuring that the assembly has been properly carried out through:
• torque control,
• checking rotation angle,
informing the user that the assembly has been properly carried out.
Protection level IP40 These declared values were obtained by laboratory type testing in
compliance with the stated standards and are not adequate for use in
risk assessments.
EN 60745 Noise level < 70 dBA
EN 60745 Vibration level < 2.5 m/s²
www.desouttertools.com
EAP 1.5 - 15 - T 2
Motor type
Tool type
A=angle-head
D=straight
Vo l t a g e
1=115 VAC
2=230 VAC
Tool option
T=Standard
TA=Advance
Maximum torque in Nm

EAP/EDP
Part no 6159936431
Issue no 05
Language English
Date 09/2009
Page 5 / 23
1.3 - Operating temperature
Considering its technology, the temperature of the tool naturally increases during tightening cycles. Best tightening rates are
reached with an ambient temperature of 20°C. The performance of the tool is decreased by approximately 50% for an ambient
temperature of 40°C. The maximum operating temperature is 45°C.
For further information, refer to "Max duty cycle" file on documentation CD-ROM.
Models Torque
(Nm)
Maximum speed
(rpm)
AB H LOut-
put
Weight
min max 115VAC 230VAC mm " mm " mm " mm " kg lb
EAP1.5-15-* 3 15 569 1016 28 1.103 27 1.064 45.5 1.793 534.5 21.059 Ø 3/8" 1.85 4.07
EAP1.5-20-* 5 20 416 742 28 1.103 27 1.064 45.5 1.793 534.5 21.059 Ø 3/8" 1.85 4.07
EAP1.5-26-* 5 26 322 575 28 1.103 27 1.064 45.5 1.793 534.5 21.059 Ø 3/8" 1.85 4.07
EAP2-20-* 5 20 858 1320 28 1.103 27 1.064 45.5 1.793 559.5 22.044 Ø 3/8" 2.0 4.40
EAP2-30-* 6 30 660 1016 28 1.103 27 1.064 45.5 1.793 559.5 22.044 Ø 3/8" 2.0 4.40
EAP2-40-* 8 40 521 802 35 1.379 27 1.064 51.5 2.029 570 22.458 Ø 3/8" 2.1 4.62
EAP2-65-* 15 65 330 507 40 1.576 30.5 1.202 57.5 2.266 581.5 22.911 Ø 3/8" 2.2 4.84
* = T for "Standard", TA for "Advance"
230VAC model Torque (Nm) Maximum speed
(rpm)
L Output Weight
min max 115VAC 230VAC mm " kg lb
EDP1.5-15-* 3 15 567 1012 491.5 19.3651 Hex 1/4" F 1.7 3.74
EDP2-24-* 5 24 900 1385 516.5 20.3501 Hex 1/4" F 1.8 3.96
EDP2-33-* 6 33 658 1012 508.5 20.0349 Ø 3/8" 1.85 4.07
EDP2-43-* 8 43 510 784 508.5 20.0349 Ø 3/8" 1.85 4.07
* = T for "Standard", TA for "Advance"
H
Ø47
(1.85")
Ø46
(1.81")
Ø68
(2.68")
ØB
Ø53
(2.08")
12
L
ØA
3/8"
Ø47
(1.85")
Ø46
(1.81")
Ø68
(2.68")
Ø60
(2.36")
Ø53
(2.08")
L
Ø3/8"
12 20
Hex. 1/4" F
Ø34
(1.34")
Ø34
(1.34")

EAP/EDP
Part no 6159936431
Issue no 05
Language English
Date 09/2009
Page 6 / 23
1.4 - Description
1.4.1 - Report LEDs
The operator is informed at a glance of the tightening results
through report LEDs. They can have three colours (green, yel-
low and red) and are located on the upper part of the tool and
on both sides of the tool. They are off during the tightening and
turn on after the tightening.
1.4.2 - Operator interface
Push/Pull detachable mains power cord
Run Reverse button
Operator interface
Trigger
Report LEDs
Description Function
Direction of rota-
tion
Modifying the direction of rotation.
When the tightening direction is ena-
bled, the lights are off. When the run
reverse direction is enabled, the red and
green lights are flashing.
Programming
button
Entering the programming mode and
validate.
Button +
Changing parameter or increasing the
value. Reading the torque setting in con-
trol mode.
Button -
Changing parameter or decreasing the
value. Alternately reading the speed set-
ting (1 to 10), the rundown speed (rpm)
and the final tightening speed (rpm) in
control mode.
Maintenance
warning light
Showing that the number of cycles is
higher than the number programmed
and that it is time to perform control or
maintenance operations.
Access code
parameter light
Showing that the parameter is selected.
For safety reasons an access code must
be entered before modifying the param-
eters.
Torque parame-
ter light
Showing that the parameter for display-
ing and modifying the final torque value
and the torque unit is selected.
Learning parame-
ter light
Showing that the parameter which,
when a torque value has been entered, is
used for measuring the assembly speci-
fications and for optimising all the
adjustment parameters (rundown thresh-
old, speed, angle tolerance) is selected.
Tightening time and overheating are
then optimised for tightening accuracy.
Speed parameter
light
Showing that the parameter is selected.
10 speed levels for adjusting speed got
by learning. The rundown speed and the
tightening speed are adjusted at the
same time.
Communication
light
All parameters can be programmed and
saved using a PDA (Pocket PC). The
data transfer between both devices is
made through radio frequency waves
using Bluetooth protocol; the light is
flashing as long as the communication
lasts.
Display
Displaying the tightening reports (OK,
NOK, tightening faults, operating
errors) and the main parameters of the
tool.
Description Function

EAP/EDP
Part no 6159936431
Issue no 05
Language English
Date 09/2009
Page 7 / 23
CHAPTER 3 - START-UP
1 - ON RECEIVING THE TOOL
Check that the following items are included in the kit supplied with the tool:
• the certificate of conformity,
• the safety instructions,
• the CDROM,
• the operator's manual.
On delivery, a separate kit can be provided according to the country of destination. The kit includes the following items:
• the mains cord.
2 - INSTALLATION
Install the necessary accessories:
• rotating suspension device
• double safety device
•…
Make sure that the operating voltage specified on the tool corresponds to the voltage of the electric network.
Make sure that the protection devices of the line are appropriate to the tool and that the safety instructions are respected.
The Standard and Advance tools are directly connected to the mains. No other connection is required.
Advance tools connected to the Data Transfer Unit controller have the same functions as the Data Transfer Unit. See correspond-
ing documents.
Switch the tool on:
To switch the tool on, you must make the electric connections in the following order:
• connect the mains cord to the tool,
• then connect the mains plug to the electric network.
Adjust the tool:
• enter the access code,
• set the torque,
• carry out the learning sequence directly on the assembly,
• check and validate the adjustment (see “PROGRAMMING,” page 8).
The tool is ready to operate.
This is the easier and the faster method; however the tool can be programmed from a PDA.
The tool connector must never be connected or disconnected when the tool is on.
The factory access code is 122.
www.desouttertools.com
EAP 1.5 - 15 - T 2

EAP/EDP
Part no 6159936431
Issue no 05
Language English
Date 09/2009
Page 8 / 23
CHAPTER 4 - PROGRAMMING
1 - PROGRAMMING DIRECTLY ON THE TOOL
1.1 - Description
The tool has been designed for an easy, optimum, fast and secured start-up. The parameters directly programmable from the tool
are:
• the access code which authorises parameter modification,
• the tightening torque and its unit,
• the learning mode,
• the speed adjustment.
1.2 - Main programming procedure
1.2.1 - Programming mode
1 Press for at least 3s to reach the programming
mode. The access code parameter is displayed (set
up to 0).
This step is disabled if the "Locked in programming" option has been selected through the PDA; in this case
the parameters cannot be modified directly from the tool. The tool displays for a few seconds, then
returns to the control mode.
2 Change this value using or until the access
code is displayed (122 by default).
• continuous action -> fast scrolling
• short action -> step by step modification.
The access code can be changed using the PDA (see
corresponding manual).
3 Press to validate. If the access code is not correct, E201 is displayed and all the parameter LEDs light up
for a few seconds, then the tool returns to control mode.

EAP/EDP
Part no 6159936431
Issue no 05
Language English
Date 09/2009
Page 9 / 23
1.2.2 - Parameter choice
From the programming mode, press or to scroll the parameters.
When you press they are displayed in the following order:
To modifiy the parameter, press .
The flashing display shows that the value can be modified.
1.2.3 - Torque
1.2.4 - Unit
1 torque 2 unit 3 learning
4 speed 5 to quit without saving parameters.
By default the torque unit is the Nm. If the unit is
different, it is recommended to modify it before
programming the torque.
1 From the torque mode, press or to pro-
gramme the value (between 0 and the maximum
torque of the tool).
2 Press to validate.
1 From the unit mode, press or to programme
the unit (Nm; Ftlb; Inlb).
2 Press to validate.
Current value
Current unit
Current level

EAP/EDP
Part no 6159936431
Issue no 05
Language English
Date 09/2009
Page 10 / 23
1.2.5 - Learning
Learning begins.
1. Tighten the first assembly. Result 1:
2. Tighten the second assembly. Result 2:
3. Tighten the third and last assembly. Result 3:
Then you can:
• either press for at least 3s to go back in tightening mode,
• or briefly press to modify the speed parameter.
1.2.6 - Speed
It is recommended to use the learning function to programme the tool. This function is used to easily optimise all
the tightening parameters, including parameters which can only be reached through the PDA (run down torque,
angle tolerance, etc.). If at the end of the learning you are not satisfied with the speed level, you can change it by
selecting the speed parameter.
If you perform the learning with only one assembly, you can loose it using .
If during the learning the result is not OK, the tool goes back to the beginning of the learning process.
If after the 1st or the 2nd tightening you do not want to go on, press . Then the tool goes back to the beginning
of the learning process.
The speed level is set automatically when the assembly is learnt. It is modified when the speeds learnt are not com-
pletely satisfactory.
The speed level can be set between 1 and 10 (1=slow, 10=fast). For each speed level there are one rundown speed
and one final tightening speed. The display displays successively the speed (1 to 10), the rundown speed (rpm) and
the final tightening speed (rpm). These speed pairs are optimised for each tool type and to match all types of assem-
bly. Thus the tightening is more precise, the operator comfort is improved, the operation shocks are reduced, the
cycle time is optimised and the tool overheating is reduced.
1 From the speed mode, press or to choose
the speed level.
2 Press to validate.
End of step 1 Torque Angle
End of step 2 Torque Angle
Learning is done. Torque Min. angle tolerance
Speed parameter
display
Max. angle tolerance

EAP/EDP
Part no 6159936431
Issue no 05
Language English
Date 09/2009
Page 11 / 23
Manual speed adjustment:
When it is not possible to learn the joint, it is possible to adjust the speed according the joint hardness. It is suggested to use angle
values of the following table. Angles are defined as the bolt rotation from 50% to 100% of the target torque.
1.2.7 - Parameter validation
To save the parameters, press for at least 3 seconds.
The tool goes back in tightening mode and is ready to tighten.
By default, if no key is pressed during 60s, the tool goes back in tightening mode without saving parameters.
To quit quickly the programming mode without saving parameters:
2 - PROGRAMMING USING THE CVIP Pocket SOFTWARE
You can programme the tool using a PDA with the CVIP Pocket software. With the PDA, you can read, modify and save all the
tool parameters, as well as create new tightening programmes and download a programme in the tool.
With the CVIP Pocket software, you can also read the tightening results from a tool.
The wireless communication between the tool and the PDA is made using a Bluetooth protocol.
For further information, refer to the CVIP Poket software manual supplied with the software CD-ROM.
Degrees from
50 to 100%
0-10 10-25 25-46 40-70 70-105 105-147 147-189 189-245 245-297 >297
Speedlevel12345678910
1 From the parameter choice mode, press or
until "ESC" is displayed.
2 Press to validate.

EAP/EDP
Part no 6159936431
Issue no 05
Language English
Date 09/2009
Page 12 / 23
CHAPTER 5 - TIGHTENING RESULTS
1 - TIGHTENING RESULTS ON THE TOOL
1.1 - Report LEDs
Advance tool (TA) - Torque control + Angle monitoring
Standard tool (T) - Torque control
The operator is informed at a glance of the tightening
results through report LEDs (green, yellow and red).
Torque
Disassembly limit
Max (105%)
Target torque
Min (95%)
Angle threshold (50%)
Measurement start (15%)
Angle
Low High
0 °
RED
YELLOW + RED
YELLOW
GREEN
Run Down torque
Torque
Disassembly limit
Max (105%)
Target torque
Min (95%)
Measurement start (15%)
Angle
0 °
RED
YELLOW + RED
YELLOW
GREEN
Run Down torque

EAP/EDP
Part no 6159936431
Issue no 05
Language English
Date 09/2009
Page 13 / 23
1.2 - Buzzer
At the end of each tightening, a sound informs the operator of the tightening result:
• 1 beep -> tightening correct
• 2 beeps -> tightening not correct or faulty operation
• 3 beeps -> end of tightening sequence ("Data Transfer Unit" only)
Each user will estimate if these sounds are useful for him/her. They can be disabled separately using the CVIP software (see
"CVIP Poket software" manual).
1.3 - Display
At the end of each tightening, alternatively torque, angle (TA version) and possible faulty operations are displayed.
1.3.1 - Tightening results
1.3.2 - Faulty operations
Faulty operations are coded so that the operator can efficiently locate the default. To know the signification of each code, see
"ERROR TABLE," page 15.
2 - TIGHTENING RESULTS ON THE PDA
When the CVIP software is installed on the PDA and when the Bluetooth communication is initialised, you can read the tighten-
ing result:
• overall result,
• torque value (reminder of minimum and maximum tolerances),
• angle value (reminder of minimum and maximum tolerances).
This function is used to compare tool results with a reference torquemeter, particularly in tightening adjustment. Results are not
stored in the PDA. For further information, refer to "CVIP Poket software" manual.
LEDs colour Interpretation Action
Green The torque and the angle are inside the programmed limits. None (tightening correct)
Yellow The minimum torque value has not been exceeded. The screw has
undergone no stress, the tightening operation has been stopped too
soon.
The operator can tighten
again.
Yellow + red The torque and angle results are near the desired values. The screw
has undergone no stress.
The operator can unscrew then
tighten the assembly again.
Red The torque has reached the disassembly limit (assembly damage
limit) or the angle is greater than the maximum angle when the
torque is correct. There is a great risk that the screw has undergone
permanent strain.
Loosen the assembly and
repair
Tightening correct Torque low Torque high Angle low
Angle high
Torque > disassembly limit
Approach unfinished Overspeed

EAP/EDP
Part no 6159936431
Issue no 05
Language English
Date 09/2009
Page 14 / 23
CHAPTER 6 - MAINTENANCE
1 - MAINTENANCE LIGHT
The tool is fitted with a maintenance alarm which goes on as soon as the tool has performed a
programmed number of cycles. This means that it is time to perform maintenance operation.
This alarm does not stop the tool, the operator can go on working but he/she is to inform the main-
tenance department.
The number of cycles is set to 250,000 by default; it can be modified using CVIP Pocket software.
However, you are advised to perform the following operations:
2 - TORQUE TRANSDUCER CALIBRATION
The tool can be only calibrated using the CVIP Pocket software (see corresponding manual).
3 - ERRORS
In the case of tool faulty operation, error codes are displayed. These error codes can also be read on the CVIP Pocket result screen,
which specifies the error type plaintext.
For further information, see “ERROR TABLE”, page 15.
You can find an error log in chronological order in the PDA's "Maintenance" menu.
4 - TOOL OVERVIEW
For disassembly and part replacement, see “PART LIST”, page 20.
5 - ELECTRICAL CONNECTIONS
See “PART LIST”, page 20.
Cycles
LEVEL 1
Replace Angle Head
Pinion - KIT 17
LEVEL 2
Replace keypad-KIT 3
Replace protection-KIT 14
LEVEL 3
Replace planetary
reduction gears-KIT 12
CALIBRATION
500 000
1 000 000
1 500 000
2 000 000
2 500 000
3 000 000
When the maintenance operation is done, reset the counter using the CVIP software in order to turn off the light.

EAP/EDP
Part no 6159936431
Issue no 05
Language English
Date 09/2009
Page 15 / 23
APPENDIX 1 - ERROR TABLE
Error Description Checking/Actions
Torque low The torque reached is lower than the torque minimum tolerance. The tool
stooping too soon could be due to an angle value equal or higher than the
safety angle (red report, look for causes in the assembly), to the operator
who released the throttle too soon (yellow report) or because the "Max
time" was reached (cycle time > programmed max time in the PDA).
Torque high The torque reached is higher than the maximum torque tolerance. The
torque tolerances could be too low, the tightening speed could be too
high (check the assembly / perform another learning for the assembly /
reduce the speed).
Angle low The angle reached is lower than the minimum angle tolerance. The
tightening rate of the assembly is higher than expected. This could be
due to faulty assembly (seizing, component missing / error, screw too
long in a blind hole), if not, it is necessary to readjust the angle
tolerances either by learning or by using the PDA.
Angle high The angle reached is higher than the maximum angle tolerance. The
tightening rate of the assembly is lower than expected. This could be due
to faulty assembly (faulty threads, screw of poor quality or
nonconforming), if not, it is necessary to readjust the angle tolerances
either by learning or by using the PDA.
Torque > disassembly limit The torque reached is higher than the disassembly limit. The
disassembly limit is positioned by default 20% above the target torque.
That means that the screw underwent permanent strain and that the
assembly needs to be repaired. Check the assembly (seizing, component
missing / error, screw too long in a blind hole). Check the level of the
disassembly limit with the PDA, it could be due to too high a speed.
Torque > Approach unfinished This means that the approach phase has been stopped too soon. Either
the screw is too short, or the number of rotations in the approach phase is
too high. Check the number of programmed rotations with the PDA. The
report LEDs reflect the state of the torque and angle values.
Torque > Overspeed The tool stopped after detecting a steep rise in the torque that,
considering the speed of the tool, could cause an overtorque beyond the
maximum charge and damage the torque transducer. This can happen
when the speed is much too fast for a hard joint or when the number of
rotations in the approach phase is insufficient. It could be a faulty
assembly, by default, reduce the speed or increase the number of
rotations in the approach phase. The report LEDs reflect the state of the
torque and angle values.
E1 Overcurrent on the power circuit.
The hardware limit has been
reached. As soon as the fault
appears, the tool stops
Turn off the tool and turn it on again in order to reset the fault. This
problem can result from programmed power too big for the tool. Try to
reduce the speed to make sure the fault has disappeared. If the fault still
appears when the tool is switched on and without pressing the trigger, the
power stage is faulty => contact our customer service.
E10 The connection with the Data
Transfer Unit controller having
already been set up, inexplicable
communication error with the Data
Transfer Unit controller
The Data Transfer Unit controller is still on but does not communicate
with the tool anymore. Faulty serial link => faulty cable/faulty Data
Transfer Unit/faulty tool.
E11 Bus voltage fault The bus voltage reflects the mains voltage after rectifying and filtering.
E11 fault means that the mains voltage is not appropriate for the voltage
announced in the tool. Make sure that the tool is adapted for the mains
voltage. Check the mains voltage. Check the mains cord.

EAP/EDP
Part no 6159936431
Issue no 05
Language English
Date 09/2009
Page 16 / 23
E12 Overheating of IGBT The IGBT dissipator temperature is higher than 80°C. Wait for the tool
to cool down. The tool can tighten again when the temperature is lower
than approximately 60°C. Usually this fault is preceded by the E411
fault and only occurs whent the IGBT fan is faulty. Check the fan
functioning.
E13 Engine not tuned This error appears after changing the DSP board and after initialising the
EEPROM to download the tool data. The tool does not start, the linearity
table and the engine offsets are not registered in the EEPROM. Tune the
engine from the PDA. This task can only be performed by those who
have attended the maintenance training course.
E201 Wrong access code This error appears for a few seconds when an incorrect access code was
entered. The tool returns automatically to control mode. Re-enter the
programming mode and enter the correct access code.
E300 Communication error with the PDA
- Size of received data over the
maximum authorized value
This could be due to a bug or interferences. Switch off the Bluetooth
radio of the PDA, switch off the tool and re-start.
E301 Communication error with the PDA
- No start flag on the first byte of the
frame
This could be due to a bug or interferences. Switch off the Bluetooth
radio of the PDA, switch off the tool and re-start.
E302 No communication with the
Bluetooth module
The tool does not work. The bluetooth module is faulty, contact our
customer service.
E350 Communication error with the DTU
- Size of received data over the
maximum authorized value
This could be due to a bug or interferences. Switch off the DTU and re-
start.
E351 Communication error with the DTU
- No start flag on the first byte of the
frame
This could be due to a bug or interferences. Switch off the DTU and re-
start.
E352 Communication error with the DTU
- Tool frame is not understood by the
DTU
This could be due to a bug or interferences. Switch off the DTU and re-
start.
E353 Communication error with the DTU
- CRC error
This could be due to a bug or interferences. Switch off the DTU and re-
start.
E404 Exceeding of the current threshold
forced in the power bus. Overcurrent
on the power circuit (software cut)
The power programmed is too large for the tool. For instance you can
reduce the speed. Turn off the tool and turn it on again in order to reset
the fault.
E405 Exceeding of the engine temperature
limit (80°) - The tool stops
instantaneously
Wait for the tool to cool down. The tool can tighten again when the
temperature is lower than 55°C. Usually this fault is preceded by the
E411 fault and only occurs when the engine temperature varies from less
than 60°C to more than 80°C in one cycle.
E406 Exceeding of the internal handle
temperature (80°C) - The tool stops
instantaneously.
Wait for the tool cool down. The tool can tighten again when the
temperature is lower than 55°C. Usually this fault is preceded by the
E412 fault. It only occurs when the handle temperature varies from less
than 60°C to more than 80°C in one cycle.
E407 Torque transducer compensation
fault. The measurement is out of
limits
A torque transducer compensation measurement (offset) is performed at
the beginning of each tightening. This fault means that the compensation
is out of limits by +/- 10% of the nominal load. That shows a torque
transducer zero drift. Make sure the tool is not under stress at the
beginning of the tightening.
E410 ADC reference value measurement
error
DSP reference voltage are faulty. This leads to errors in the measurement
of engine position, temperature, mains voltage, mains current.
Error Description Checking/Actions

EAP/EDP
Part no 6159936431
Issue no 05
Language English
Date 09/2009
Page 17 / 23
E411 Exceeding of the maximum engine
temperature (60°C); the tool
completes the cycle in progress
Wait for the tool to cool down. The tool can tighten again when the
temperature is lower than 55°C. This means that the tool tightening rate
is too big or that the ambient temperature is higher than the usual
temperature. Make sure that the tightening rate is adapted to the
maximum tightening rate recommended by the manufacturer. Make sure
that the tightening parameters (run down torque, speed) have been
optimised. Perform a learning for the assembly.
E412 Handle overheating Never close up ventilation inlet, make sure the fan is in operation (a faint
noise is audible). The tool can tighten again when the temperature is
back to normal.
E416 Engine temperature sensor faulty The temperature sensor on the hall board registers an abnormal
temperature (T<-10°C ; T>110°C). The tool has stopped. Check the hall
board connection / change the hall board / contact our customer service.
E417 DSP board temperature sensor faulty The temperature sensor on the DSP board registers an abnormal
temperature (T<-10°C ; T>110°C). The tool has stopped. Change the
DSP board / contact our customer service.
E418 No communication with the torque
transducer
This error appears when the communication between the torque
transducer and the DSP is interrupted for any reason. It may be a flat
cable fault, a disconnection of the flat cable or a torque transducer
electronic fault.
>E500 E2PROM access error The tool data are no longer available (E2PROM access faulty, data
partially or totally modified or lost). Contact our customer service.
E501 Error of data size sent to the EEPROM
E502 Reading error of CRC on "Identification - Tool - Calibration" parameters
E503 Reading error of CRC on "Code - Station - Sequence - Cycle" parameters
E504 Reading error of CRC on "Maintenance" parameters
E511 Reading error of "Identification - Tool - Calibration" parameters
E512 Reading error of "Code - Station - Sequence - Cycle" parameter
E513 Reading error of "Maintenance" parameters
E514 Writing error of STATION parameter
E515 Writing error of ACCESS CODE parameter
E516 Writing error of CYCLE parameter
E517 Writing error of SEQUENCE parameter
E519 Writing error of the error table
E521 Writing error of the cycle manually set up
E522 Writing error of target torque when learning
E524 Software version
E525 Writing error of CALIBRATION parameters
E526 Writing error of the torque coefficient
E527 Writing error of linearity table
E528 Writing error of motor offset coefficients
E529 Writing error of CRC on "Identification - Tool - Calibration" parameters.
E530 Writing error of CRC on "Code - Station - Sequence - Cycle" parameters
E531 Writing error of CRC on "Maintenance" parameters
E532 Writing error of the tool option
E533 Writing error of the tool type
Error Description Checking/Actions

EAP/EDP
Part no 6159936431
Issue no 05
Language English
Date 09/2009
Page 18 / 23
Locking codes
E534 Writing error of approach torque
E536 Writing error of the error table
E666 Error in the linearity table This error can only appear at the end of the first phase of the engine
tuning. It could be an engine problem, it could be a magnet problem in
the engine shaft extension, the power module or the DSP board. Contact
our customer service.
E667 Error seeking zero position This error can only appear after the second phase of the engine tuning.
This can be a problem with the magnet in the engine shaft extension, or a
problem on the hall board. Contact our customer service.
E668 Error seeking offset evolution
according to speed
This error can only appear at the end of the third phase of the engine
tuning. This can be a problem with the magnet in the engine shaft
extension, or a problem on the hall board. Contact our customer service.
Codes Description Checking/Actions
0 1 Programming disabled Programming is disabled with the PDA (The box "Programming
authorisation" of Station menu \ General parameters", is not validated).
0 2 Loosening disabled The loosening direction is disabled with the PDA (The box "Run reverse
authorisation" of Station menu \ General parameters", is not validated).
When the tool is connected to a DTU, apply +24V signal on the
REVERSE VALIDATION input to enable the operator to loosen.
0 3 Lock on batch count NcyOK The box function "Lock on batch count NcyOK" is validated in the PDA,
Station menu \ DTU parameters. The tool is locked when the number of
cycles reaches the number of NcyOK programmed (see cycle screen of
the PDA). Apply a +24V signal on the RESET input of the DTU to
unlock the tool.
0 4 Lock on NOK The box function "Lock on NOK" is validated in the PDA, Station menu
\ DTU parameters. The tool is locked when a reject tightening report
appears. Apply a +24V signal on the REJECT ACKNOWLEDGE input
of the DTU to acknowledge the default.
0 5 Tool disabled The tool is locked by the SPINDLE ENABLED input of the DTU. Apply
24V to enable the tool to work.
0 6 Lock on External start cycle only The tool is locked by "External start cycle only" meaning the tool
triggers are not activated. To enable the tool triggers, with the PDA
(Station menu / DTU parameters) unselect "External start cycle only".
Error Description Checking/Actions

EAP/EDP
Part no 6159936431
Issue no 05
Language English
Date 09/2009
Page 20 / 23
APPENDIX 2 - PART LIST
6
8
7
3
5
4
2
9
9
9
15
17
17
19
16
20
10
10
14
11
11
18
17
1
13
12
1.9 Nm
10 mm3 0.9 Nm
LOCTITE 243
KLUBER Centroflex CX 4/375 AU
KLUBER Isoflex
NBU 15
10 mm3 0.9 Nm
LOCTITE 243
60 mm3 60 Nm
LOCTITE 243
10 mm3 0.7 Nm
LOCTITE 222
60 mm3 60 Nm
LOCTITE 243
10 mm3 20 Nm
LOCTITE 243
2.5 Nm
60 mm3 60 Nm
LOCTITE 243
AH1
AH2
AH3
LOCTITE 648
20 mm3
40 mm3
50 mm3
1 mm3 0.3 Nm
LOCTITE 243
30 Nm
30 Nm
40 Nm
LOCTITE 274
AH1
AH2
AH3
AH1
AH2
AH3
6153966075
6153966085
6153966095
100 mm3
130 mm3
150 mm3
AH1
AH2
AH3
2.7 g
4.5 g
8 g
2050478153
21
22
23
24
This manual suits for next models
10
Table of contents
Other Desoutter Measuring Instrument manuals
Popular Measuring Instrument manuals by other brands

Kipp & Zonen
Kipp & Zonen SGR series instruction manual
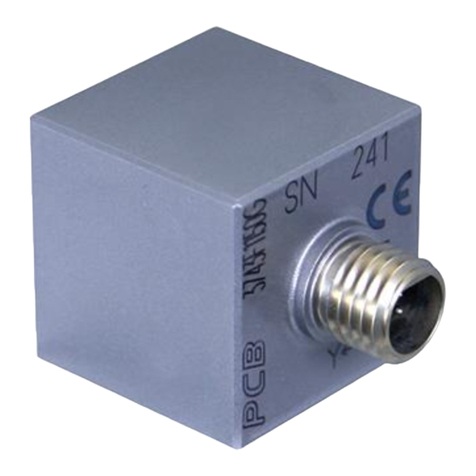
PCB Piezotronics
PCB Piezotronics 3743F1130G Installation and operating manual

Morris
Morris 57314 instruction manual

bluelab
bluelab Soil pH Pen Care and use guide
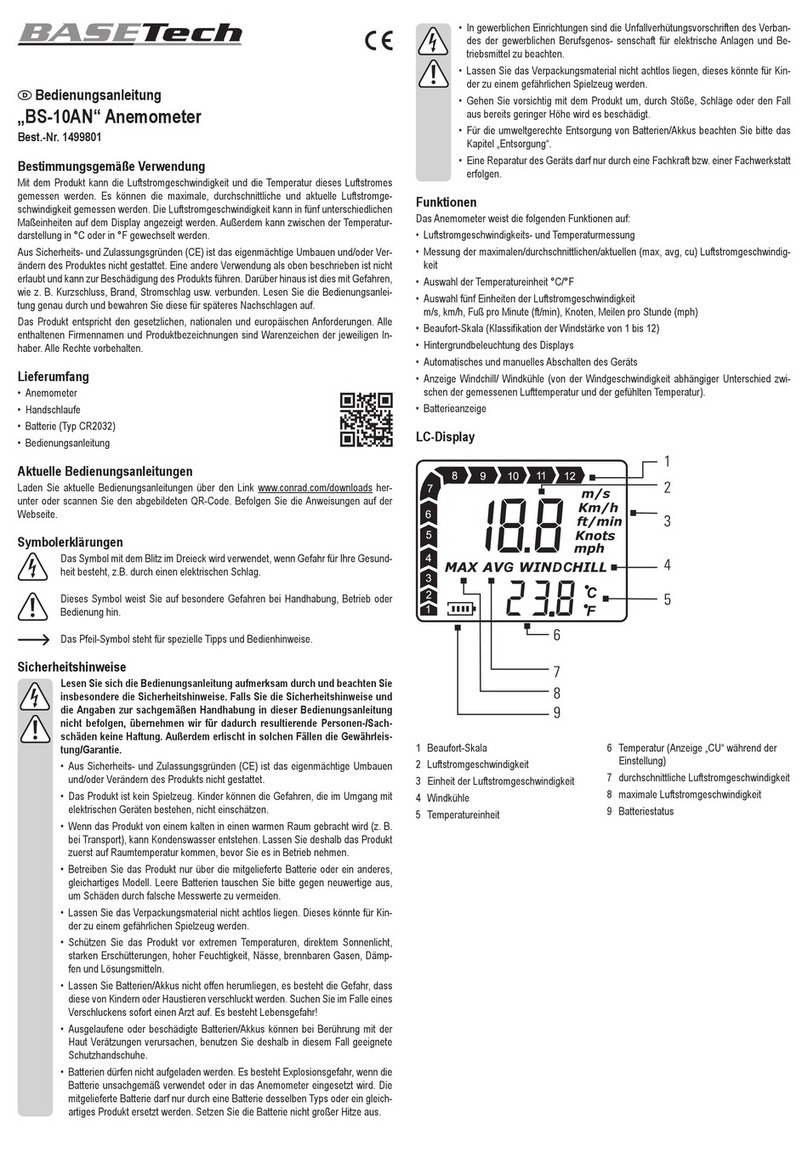
BASETech
BASETech BS-10AN operating instructions
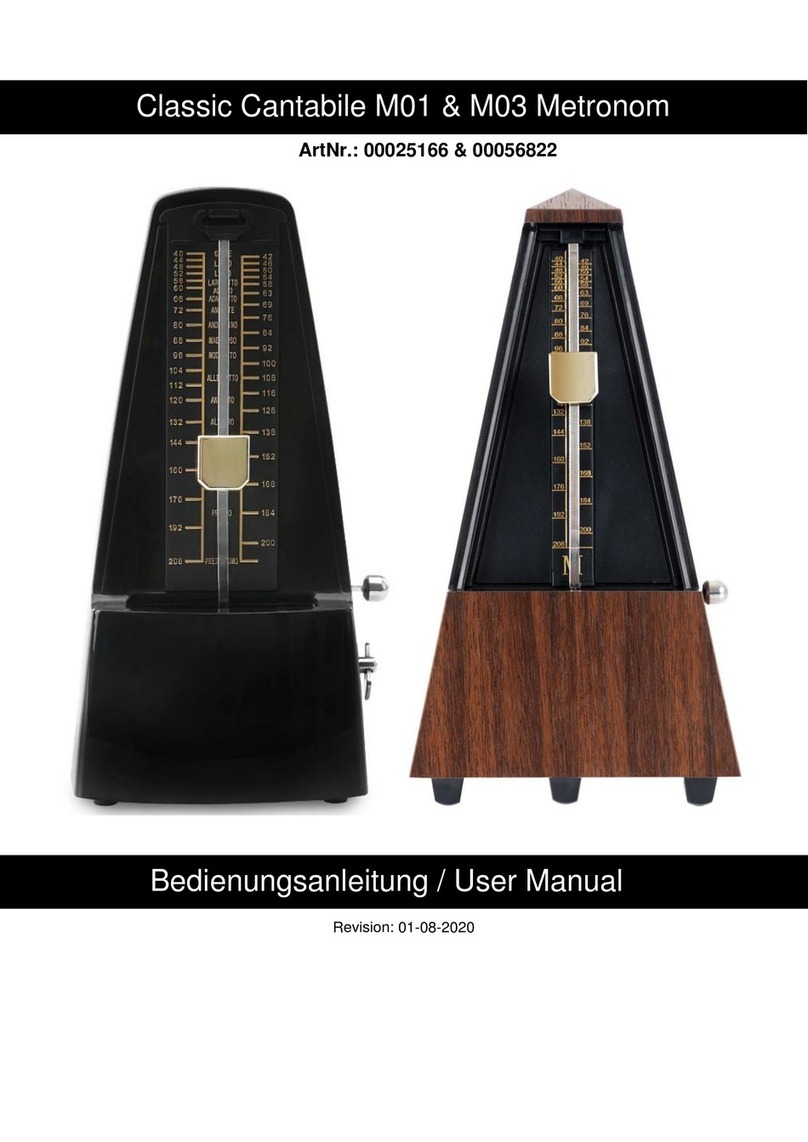
Classic Cantabile
Classic Cantabile M01 user manual
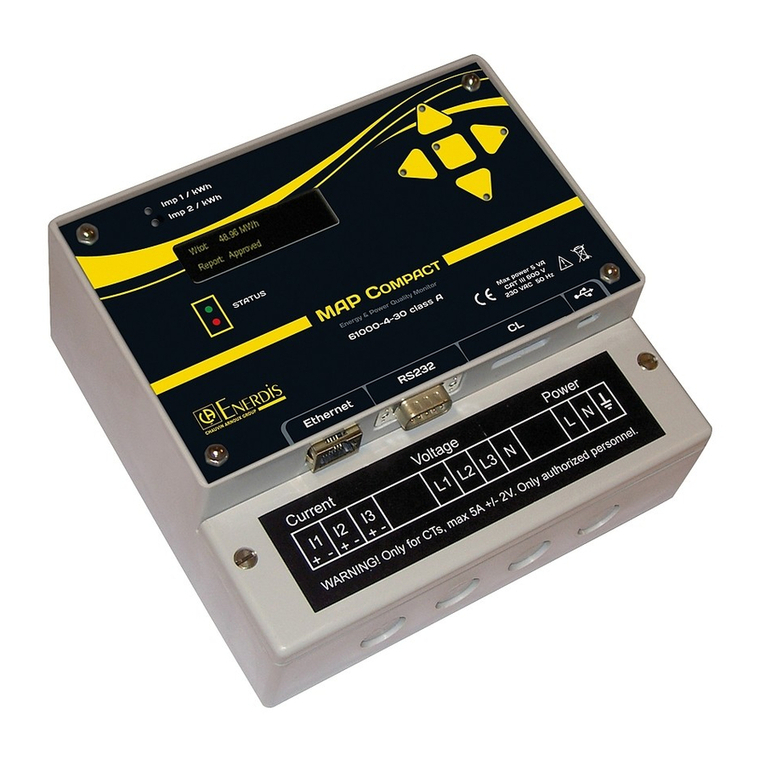
Chauvin Arnoux
Chauvin Arnoux MAP COMPACT Installation and operating manual
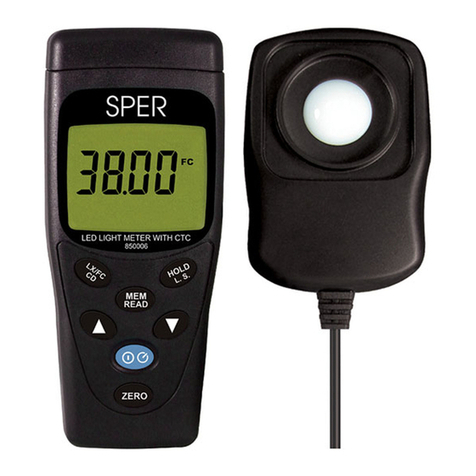
Sper scientific
Sper scientific 850006 Instruction Maual

W&T
W&T WuTooth 97100 manual

Environmental Express
Environmental Express OAKTON EC250 instruction manual
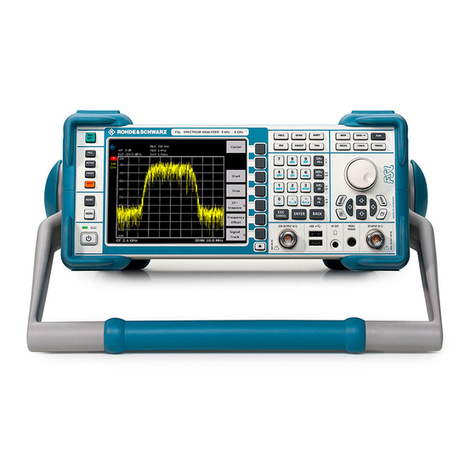
Rohde & Schwarz
Rohde & Schwarz R&S FSL3 operating manual
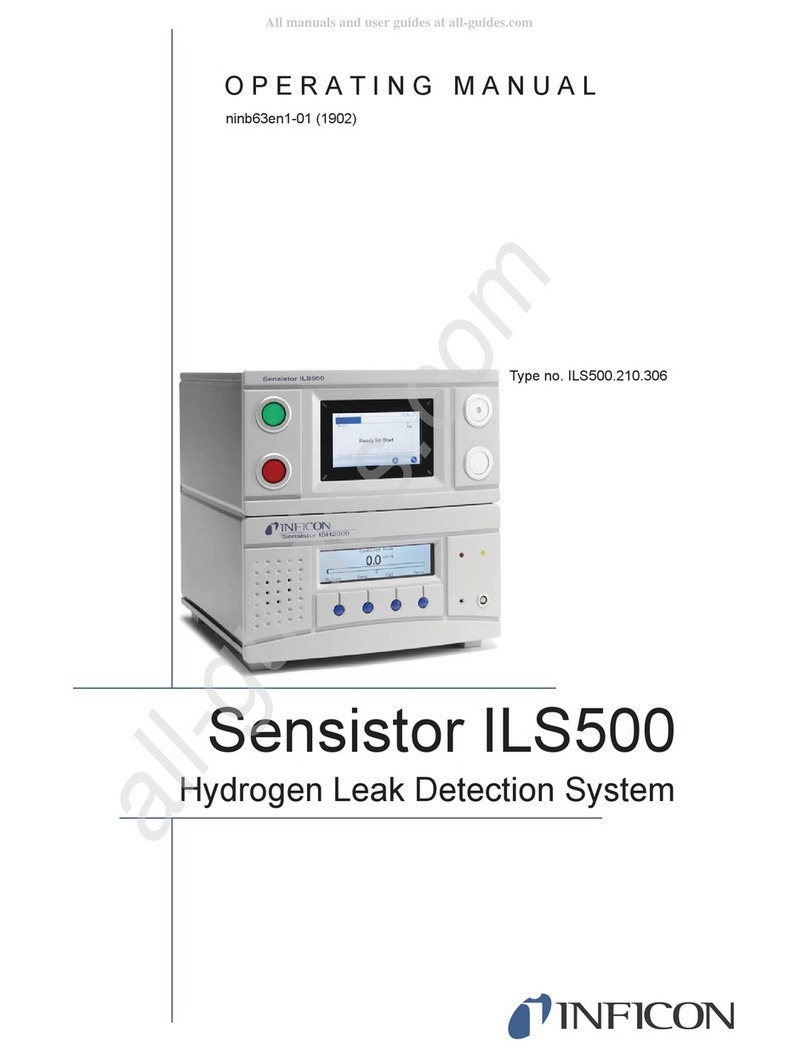
Inficon
Inficon Sensistor ILS500 operating instructions