DI MPU01 User manual

825B122A
DI MPU01 Transit time ultrasonic lowmeter
Features
• Pipe dimension range: DN20 ÷ DN4000
• Transmitter protection class: IP66
•Transducer protection class: IP68
• Display: backlighted 2x20 alphanumeric digit
• Keypad: 4 keys
• Housing material: printing aluminium
• Displayed data: instantaneous owrate;
ow totalizer
• Mounting: wall
• Analog Output: Sel. 4÷20mA or 0÷20mA
• Accuracy: ±1%
• Repeatability: ±0,2%
• Linearity: ±0,5%
• Basic measurement period: 500ms
• Serial port: RS485
• Communication protocol: MODBUS RTU
or ASCII+ (opt.)
•Programmable frequency output: 0÷5000Hz
•Relay output: n.1 for pulse totalizer or alarm
• Medium speed range: ±12m/s
• Unit working temperature: -20÷60°C
• Instrumenthumidity: noncondensing85%RH(40°C)
• Sensors working temperature:
TS-2/TM-1/TL-1 -30 ÷ +90°C
TS-2 HT/TM-1HT -30 ÷ +160°C
TC1/TLC-2 -40 ÷ +160°C
• Sensor cable std. length: 5m
• Power s.: 230Vac or 10÷30Vdc (depending on model)
• Dimensions: 200x120x77mm
•Weight without sensors: 1Kg

Pag. 2 of 52
- Working principle
Where:
= sonic section angle
M = sonic section length
D = pipe internal diameter
T1 = sound transit time from the upstream transducer to the transducer downstream
T2 = sound transit time from the downstream transducer to the transducer upstream
∆T = Tup-Tdown
1. WORKING PRINCIPLE
The meter is designed to measure the uid velocity inside a pipe.
The clamp-on transducers models allow an easy installation.
The transit time ow meter uses two ultrasonic transducers that function as transmitters and receivers.
They are installed externally to the pipe at a specic distance from each other. They can be installed at Vmode (2
sonic section), at W mode (4 sonic section) or at Z mode (1 sonic section). The installation method choice depends
on the pipe and the uid characteristics. The instrument measures the transit time via the two transducers that
alternatively transmit and receive a sound pulses sequence. The difference in the measured transit time is directly
related to the uid velocity in the pipe, as shown in gure 1
Compact system for conductive and
non-conductive fluids, even with the
suspendedmaterialpresence(<10g/l;<Ø1mm)
Measuringrangesfrom<0,2m3/hto>30000m3/h
Applicable to various pipes mate-
rials (eg. SS316, copper, plastic,
etc.), with or without an inner lining
Power supply 85 ÷ 265Vac or 10÷30Vdc
The instrument is composed by a digital converter and two clamp-on or insertion type ultrasonic transducers.
The instrument calculates the instantaneous ow rate value by measuring the ight time difference of the ultrasonic
pulses.
Fig. 1

Pag. 3 of 52
- Features
2. FEATURES
Pipe
Material Carbon Steel; Stainless Steel; Cast Iron; Ductile Iron; Copper; PVC; Aluminium;
Asbestos; FiberGlass-Epoxy; Other
Pipe Ø range 20÷4000mm
Inner lining None, No Liner; Tar Epoxy; Rubber; Mortar; Polypropylene; Polystyrol; Polysty-
rene; Polyester; Polyethylene; Ebonite; Teon; Other
Pipe length Upstream pipe straight section of 10÷40D. Downstream pipe straight section
greater than 5D.
NB - The pipe straight section, downstream of a pump, must be greater than 20D.
Measured
uids
Kind Water (General); Sea Water; Kerosene; Gasoline; Fuel Oil; Crude Oil; Propane
(-45°C); Butane (0°C); Other Fluid; Diesel Oil; Castor Oil; Peanut Oil: Gasoline
#90; Gasoline #93; Alcohol; Water (125°C)
Suspended solids Homogeneous uids, even with material in suspension with a concentration less
than 20g/l and particle size less than 1mm.
NB - Avoid the ice formation inside the pipe at low temperatures
Temperature Depending on the used ultrasonic transducer model (see pages 4 and 5)
Flow velocity ±0,01m/s ÷ ±12m/s
Direction Direct and reverse ow rate measurement and separate totalization
Data
Converter
Unit
Accuracy ±1%
Working
conditions Temperature: -20°÷+85°C; humidity: 85% non-condensing (for applications in
conditions different from the standard, specify when ordering)
Analog output Opto-isolated with congurable mode: 4÷20mA; 0÷20mA; 0÷20mA Via RS232; 4÷20mA
vs Sound; 20÷4÷20mA; 0÷4÷20mA; 20÷0÷20mA; 4÷20mA vs vel.
Max. load: 1000ohm
OCT output
Passive opto-isolated: Vmax: 30Vdc; Imax 100mA
Alarm output or pulse output from ow totalizer with settable pulse width in
6÷1000ms range
Relay output N.1; Max. 125Vac 1A; 30Vdc 2A
Alarm output or pulse output from ow totalizer
Serial port RS485. Comunication protocol: MODBUS RTU; MODBUS ASCII
keyboard 4 keys
Display backlighted 2x20 alphanumeric digit LCD
Display data Simultaneous display of:: instantaneous ow rate (-99999.99÷+99999.99m3/h); ow to-
talizers (-19999999.99÷+19999999.99m3); total operating time displayable via
keyboard command
Data storage Flow Totalizer, total operating time and all system conguration parameters. Stor-
age on E2PROM
Power supply
(dependingonmodel) 230Vac ±15% 50÷60Hz; consumption: 3VA.
10÷30Vdc; consumption: 2W
Protection IP66; the transparent protective cover use is recommended (p.n. 546A103N)
Tab. 1

Pag. 4 of 52
- Transducers
3. TRANSDUCERS
Transducer Type Caratteristiche
TS-2
Dimensions
Pipe Ø range 20÷100mm (¾” ÷ 4”)
Temperature -30 ÷ +90°C
Menu 23 >19. Clamp-On TS-2
TS-2-HT
Dimensions
Pipe Ø range 20÷100mm (¾” ÷ 4”)
Temperature -30 ÷ +160°C
Menu 23 >19. Clamp-On TS-2
TM-1
Dimensions
Pipe Ø range 50÷700mm (2” ÷ 40”)
Temperature -30 ÷ +90°C
Menu 23 >16. Clamp-On TM-1
TM-1-HT
Dimensions
Pipe Ø range 50÷700mm (2” ÷ 40”)
Temperature -30 ÷ +160°C
Menu 23 >16. Clamp-On TM-1
Tab. 2

Pag. 5 of 52
- Transducers
Transducer Type Caratteristiche
TL-1
Dimensions
Pipe Ø range 300÷4000mm (3” ÷ 160”)
Temperature -30 ÷ +900°C
Menu 23 >20. Clamp-On TL-1
TC-1
(standard)
Dimensions
Pipe Ø range 80÷4000mm (3” ÷ 160”)
Temperature -40 ÷ +400°C
Max pressure 1.6Mpa (16bar)
Menu 23 >17. Insertion TC-1
TLC-2
(for
non-metallic
pipes)
Dimensions
Pipe Ø range 80÷4000mm (3” ÷ 160”)
Temperature -40 ÷ +400°C
Max pressure 1.6Mpa (16bar)
Menu 23 >21. Insertion TLC-2 Tab. 3

Pag. 6 of 52
- Dimensions/Electrical connections
5. ELECTRICAL CONNECTIONS
5.1 Connections
1) Separate the engine control cables or power cables from the DIMPU connection cables.
2) Remove the caps from the cable glands and open the cover by unscrewing the screws.
3) Lead the cables into the transmitter through the cable glands
4) Close the cap and tighten the cable glands
The immunity to electromagnetic interference is in accordance with directives
Fig. 2
Fig. 3

Pag. 7 of 52
- Electrical connections
5.3 POWER CONNECTION
5.3.1 Supply voltages in AC
5.2 Recommendations for external mounting
- or electrical connections, use a cable with a 6÷10mm outer diameter and fully tighten the M18 cable gland
- Securely close the cover
- position the cable so that it forms a downward curve at the M18 output (Fig.4); in this way the condensation and/or
rain water will tend to drop from the curve bottom
- place the transparent cover for protection
Fig. 5

Pag. 8 of 52
5.4 TRANSDUCER CONNECTION
- Electrical connections
5.3.2 Supply voltage in 10÷30Vdc
Fig. 6
Fig. 7

Pag. 9 of 52
- Electrical connections
5.5 OUTPUT SIGNALS CONNECTION
5.5.1 Analog output
5.5.2 Pulse output
Fig. 8
Fig. 9

Pag. 10 of 52
- Electrical connections
5.5.3 Relay output
5.5.3 MODBUS port
Fig. 10
Fig. 11

Pag. 11 of 52
- Introduction
6. INTRODUCTION
The instruement ow measurement system is composed of a digital converter and two ultrasonic transducers.
The instrument uses the uid transit time, measured inside a pipe of cylindrical section, to calculate the instantaneous
ow rate value. The DSP technology, Digital Signal Processing, ensures system low sensitivity to any potential
interference factors .
6.1 Turn on the digital converter
The DIMPU system standard power supply is 230Vac or 10÷30Vdc.
Before connection check the supply voltage.
When switched on, a program for self-diagnostic controls the hardware and the software. In case of malfunction, an error
message is displayed. After checking, the system will display the last selected menu before turning off, for example,
if the menu “02” was the last selected menu (from now on indicated with M02), the instantaneous ow rate and direct
totalizer will be directly displayed.
During the sliding and/or displaying of the various windows menu, the measurement is not interrupted. Only when the
user sets the new pipe parameters (and each time the instrument is turned on), the DIMPU initiates a check-up
for the signal reception automatic optimization, that status will be displayed at the top right of the display, *R means
normal status.
In case of re-positioning of the transducers, the instrument will automatically adjust the signal reception.
All congurations set by the user are stored in memory, but it’s good to make sure that the menu M26, “Default Settings”
is set to “0. Use RAM Settings”
6.2 keyboard DIMPU
has 4 buttons:
Press to activate the programming or displaying menu direct selection
Press : - select to the previous menu (during normal menu displaying)
- edit the selected digit (during menu programming or selecting)
- select the previous option (during menu programming)
Press : - select the next menu (during normal menu displaying)
- select the digit to the right (during menu programming or selecting)
- select the next option (during menu programming)
Press : - access to the programming menu (during the programming menu displaying)
- conrms the entered or selected data (during the programming menu)
6.3 Menus
The menus are numbered from M00 to M99 and from M+0 to M+9.
There are two ways to select a menu:
1) Direct access, press followed by the number of the desired menu. For example, to select M11 (the pipe outer
diameter) press in the order: (enables the menu direct selection), (edit the selected digit), (select the
digit to the right), (edit the selected digit), (conrms the entered data)
2) Search using or . Each time is pressed, will access to the previous menu (for example, to switch from
M12 to M11), and each time is pressed, will access to the next menu (for example, to switch from
M11 to M12)
There are three menus types:
1) programming menu with alphanumeric or numeric settings (eg. pipe outer diameter, M11)
2) programming menu with option selection (eg. pipe material, M14)
3) displaying menu (eg. instantaneous ow rate and forward ow totalizer, M02)

Pag. 12 of 52
- Installation
7. INSTALLATION
7.1 Measuring point Selection
The transducers must be mounted on a pipe section which allows to respect the minimum distance between the element
of resistance to ow, such as curves or derivations, and the measuring point. See the following table
Flow resistance element Upstream side Downstream side
90° curves
T junction
Adaptors
Valves
Pumps
In the event that the minimum values shown in table 4 can not be met, it is necessary to adopt every mechanical
devices to mitigate the ow turbulence and improve the homogeneity of the ow velocity in the pipe. One of the best
devices is the transducers upstream installation of a uid threads rectier, which allows to have a straight section
length of the pipe less than indicated.
The pipe where the transducers are placed must have the following characteristics:
- smooth surface without rust or other surface deterioration;
- circular cross section
The ideal points for the transducer positioning are:
- hydraulic circuit lowest point (g.12-a);
- vertical pipes with the upward ow (g.12-b);
- inclined pipes with the upward ow (g.12-c);
- vertical open drain pipes with a section restriction to avoid sudden pipe emptying
during ow measurement (g.13)
Correct transducers positioning example
Correct transducers positioning example
Tab. 4
Fig. 12
Fig. 13

Pag. 13 of 52
- Installation
In the case of a horizontal pipe, the transducers positioning should be between ± 45 ° relative to the horizontal center
line of the pipe. This is to avoid that any air bubbles can interfere with the ow velocity detection, Furthermore, in the
case of buried pipe must observe the following measures:
with insertion type transducers L>600mm; with clamp-on type transducers L>400mm
Transducers positioning on a horizontal tube
The transducers positioning points to be avoided are:
- vertical pipes with the downward ow, because they may not be completely lled with uid (g.16)
- inclined pipes with the downward ow, because they may not be completely lled with uid (g.16)
- the transducers must never be placed in the highest point of the concerned hydraulic circuit, because there is greater
chance that in that pipeline section will create air pockets (g.17)
- vertical open drain pipes without a section restriction to avoid sudden pipe emptying during ow measurement
(g.17)
Positioning to avoid example Positioning to avoid example
7.2 Positioning distance
The value (calculated automatically by the system) shown in menu M25 refers to the “Lout” mounting distance between
the two transducers, as shown in the following gures
Fig. 14 Fig. 15
Fig. 16 Fig. 17
Fig. 18 Fig. 19

Pag. 14 of 52
7.3 V installing
Is the installation method for pipes with diameters in the DN50÷250 range
- Installation
7.4 Z installing
Is the installation method for pipes with diameters in the DN300÷400 range
7.5 W installing
Is the installation method for pipes with diameters in the DN20÷50 range
Fig. 20
Fig. 21
Fig. 22

Pag. 15 of 52
- Installation
7.6 Insertion transducer installation
Steps required for proper installation:
1 - with encased pipe, check that there is the minimum space required for the transducers installation (g.23)
2 - with encased pipe, check that the free section length of the pipe is the minimum required (g.24)
3 - Procuring the necessary equipment for drilling the pressure pipes
4 - Set the pipe parameters: in the menu M23 choose the option 17 or 21 (TC-1 or TLC-2 insertion transducer);
in the menu M24 choose 1. (Z installation) and in the menu M25 check the positioning distance
5 - Determine the best location for installation on pipe
6 - Installing the ball valve base
1. ultrasonic transducer signal emitter
2. ball valve base
3. ball valve
4. male thread for drill
5. sealing nut
6. head with terminals for electrical connection
7. connection cable
7.6.1 - Base valve Fixing
1. pipe
2. ball valve base
3. ball valve
4. drill bit Ø19mm
5. drill chuck
6. seal gland
7. drill rod
8. power drill
Fig. 24
Fig. 25 Fig. 26
Fig. 27
Fig. 28
Fig. 23

Pag. 16 of 52
- Installation
1) Weld or x the valve base on the pipe (2 in gure 27).
2) Screw the ball valve (3 in gure 27) and tighten to ensure the seal. The valve must be opened
3) Insert the drill bit in the ball valve and tighten the seal gland (6 in gure 28) on the male threads (4 in
gure 27),so that there is no leakage. Fasten the power drill to rod (7 in gure 28).
4) Turn on the drill and drill pipe
5) Unscrew the seal gland and slowly pull out the drill; as soon as possible, close the ball valve to avoid leakage.
6) Use a meter, or a caliper to measure the A dimension.
Slowly insert the transducer into the valve support and open the ball valve.
Measure the distance “L” between the outer surface of the pipe and the upper part of the head of the transducer.
L=A-pipe thickness
The transducer insertion will be installed properly when the C dimension (in gure 29) will be equal to 0 (zero),
ie when L=A-B
To check the transducers ultrasonic signal emitting orientation (1 in gure 27), check that: :
1) the outputs cables of both transducers are oriented orthogonally to the pipe axis
2) the outputs cable on the transducers have the same direction
Fig. 29
Fig. 30
Fig. 31

Pag. 17 of 52
- Installation
4) Proceed to the electrical connection
7.7 Installation check-up
The signal reception power and quality (Q) can be checked through the installation check-up and it’s possible to make
the comparison of the measured ight time by the measuring range depending on the pipe diameter.
7.7.1 - Signal reception power - M90
The signal reception power, displayed to the menu M90 with UP and DN, is indicated by a three-digit number.
[00.0] means missing signal and [99.9] indicates the maximum measurable value.
Although the instrument is working properly with a signal power between 50.0 and 99.9, it is always recommended
to try to get a value as high as possible using the following methods:
(1) Select the most favorable installation position.
(2) Clean the pipe outer surface and apply more coupler grease.
(3) Move the transducers both vertically and horizontally while the signal reception control.
Mechanically lock the transducers when the detected power has reached its maximum value (always checking
that the distance between the two transducers is equal to that indicated in the menu M25)
7.7.2 - Signal quality (Q) - M90
Better the signal quality (Q value higher), better will be the ‘SNR and consequently the accuracy. In normal operating
conditions the Q value, displayed to the menu M90, is between 60 and 90. In the case of a lower value, check:
(1) Any interference with other instruments.
(2) The transducers coupling with the pipe surface ube (clean the pipe or add more coupler grease)
(3) The mounting position on the pipe
7.7.3 - Total transit time and Delta Time - M93
The numbers shown in the M93 are called total transit time and delta time. These values are fundamental to calculate
the ow rate inside the pipe.
The total transit time should remain stable or in any case subject to minimal variations.
If the delta time uctuates above 20% means that there are problems with the transducers installation.
Fig. 32
3) the inclined surfaces of the ultrasonic transducer
signal emitter (1 in gura 27) should be directed
towards each other
Fig. 31-a

Pag. 18 of 52
- Pipe Specications
8. PIPE SPECIFICATIONS
8.1 Outside pipe diameter
In the event that an appropriate instrument to measure the pipe outside diameter of the is not available (programming
in M11), proceed as follows:
- use a rope or paper tape or sheet
- wrap the pipe with rope or paper tape or sheet and mark the circumference point
- measure the length corresponding to the pipe circumference
- enter the measured value to “Pipe Outer Perimeter” menu (M10), DIMPU will automatically calculate the correct
pipe diameter value
8.2 Pipe thickness
Value measured on site using an appropriate tool (caliper, ecc.), or from the technical data of the hydraulic interested
(programming in M12). In the presence of tubes without inner lining, is possible to use the DIMPU thickness gauge.
8.3 Pipe material
Value detectable on site, or from the technical data of the hydraulic interested (programming in M14)
8.4 Materiale del rivestimento interno del tubo
Value detectable on site, or from the technical data of the hydraulic interested (programming in M15)
8.5 Spessore del rivestimento interno del tubo
Value measured on site using an appropriate tool (caliper, ecc.), or from the technical data of the hydraulic interested
(programming in M16).
Fig. 33
7.7.4 - Time ratio between the Measured Total Transit Time and the Calculated Time - M91
The value should be in the range 100±3%. If the value exceeds this range check:
(1) That the parameters have been entered correctly
(2) That the distance between the two transducers is the same as indicated in the menu M25
(3) That the transducers are installed in the right direction.
(4) That the positioning point was chosen in an appropriate manner and that the pipe has not changed shape.
(5) Inside the pipe there are no deposits.

Pag. 19 of 52
- Transducers positioning
9. TRANSDUCERS POSITIONING
9.1 Positioning type Selecting
The transducers positioning type selection, Z-Mode, or V-Mode or W-Mode, is a function of measuring pipe DN:
DN20÷50 - recommended installation: W (small pipe)
DN50÷250 - recommended installation: V
DN250÷4000 - recommended installation: Z
9.2 Marking positioning
After the pipe parameters and transducers positioning type programming, the conversion unit automatically calculates
the mounting axial distance between the two transducers: M25, Transducer Spacing.
The M25 value is used to mark out on the pipe the exact transducers positioning .
9.3 Marking tools
To trace on the pipe surface the transducers positioning points are sufcient simple tools, but effective at the same time:
- a paper roll piece (like that calculators) with a width greater than the pipe circumference, or a piece of continuous
form for printer according to the pipe diameter.
- a pencil or a thin tip pen
- a meter
Pencil Thin tip pen Meter paper roll for
calculators Continuous form
for printer
9.3 Marking modes
9.3.1 - Z mounting mode
For the transducers correct positioning, proceed as follows:
1) wrapping the pipe with the paper roll, or with the continuous form, making sure that the edges are perfectly
superimposed between them. With the pencil, or with the thin tip pen, draw the “r” circle on the pipe and, at the
same time, draw on the paper roll, the circumference measuring point.
Fig. 34
Fig. 35

Pag. 20 of 52
2) remove the paper roll and fold in half the portion corresponding to the circumference. Reposition the paper roll,
so as previously folded, on the pipe and draw a straight line, called “S”, perpendicular to the “r” circumference
line. The intersection point, called “a”, is the mounting position of a transducer.
- Transducers positioning
3) now extend the “S” straight line from the “a” point to a length equal to half the “r” circumference. Next, at 180
degrees on the circumference “r” from point “a”, draw a straight line, called “D”, parallel to the straight line “S”
and with equal length. The intersection point between the “D” straight line and the “r” circumference is called “b”.
4) now mark the “c” point on the “D” straight line, at a distance from “b” point equals the “Lout” measure previously
calculated and displayed by the conversion unit in M25. Now the mounting positions of both transducers are
known:
- point marked with the letter “a”
- point marked with the letter “c”
Fig. 36
Fig. 37
Fig. 38
Table of contents
Popular Measuring Instrument manuals by other brands
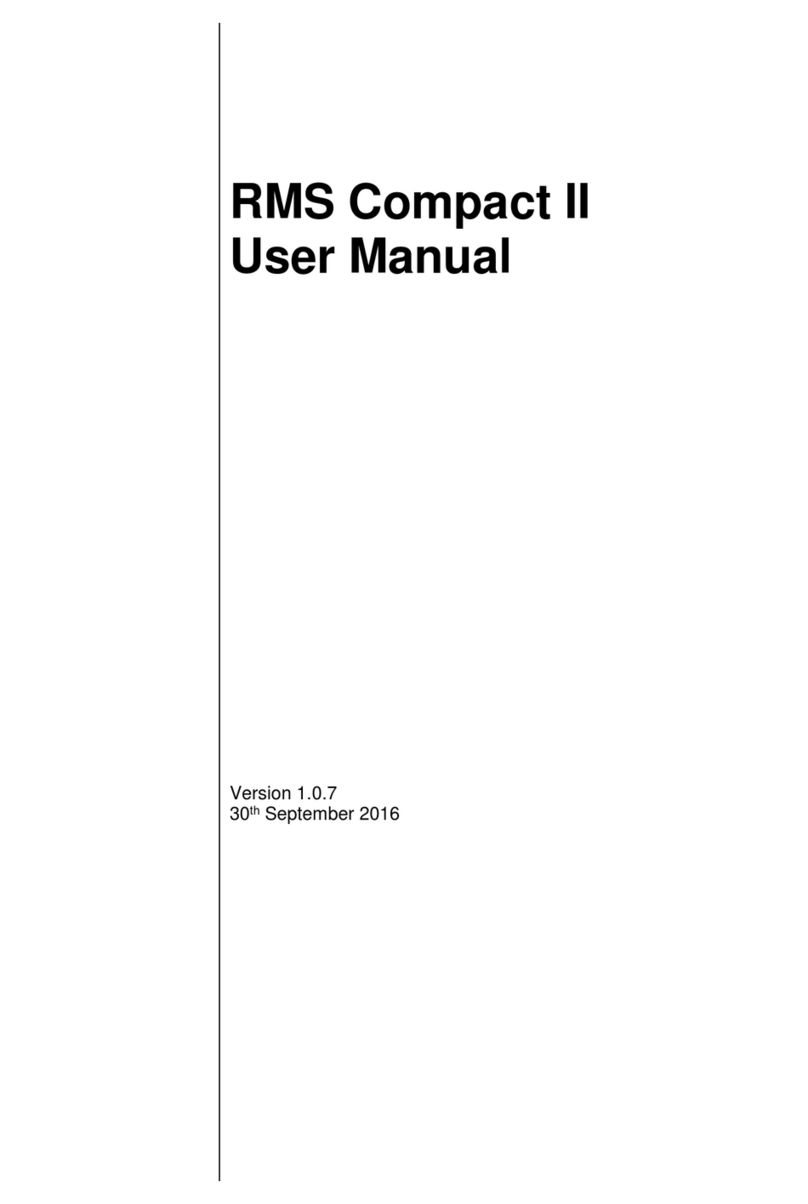
Panduit
Panduit RMS Compact II user manual
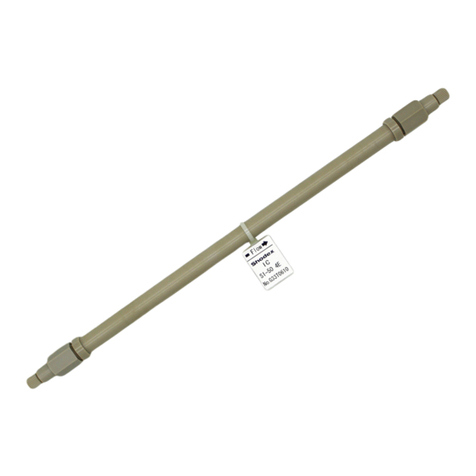
Shodex
Shodex IC SI-50 4E Operation manual

Tuthill
Tuthill Fill-Rite 900 Series Owners installation, operation, and safety manual
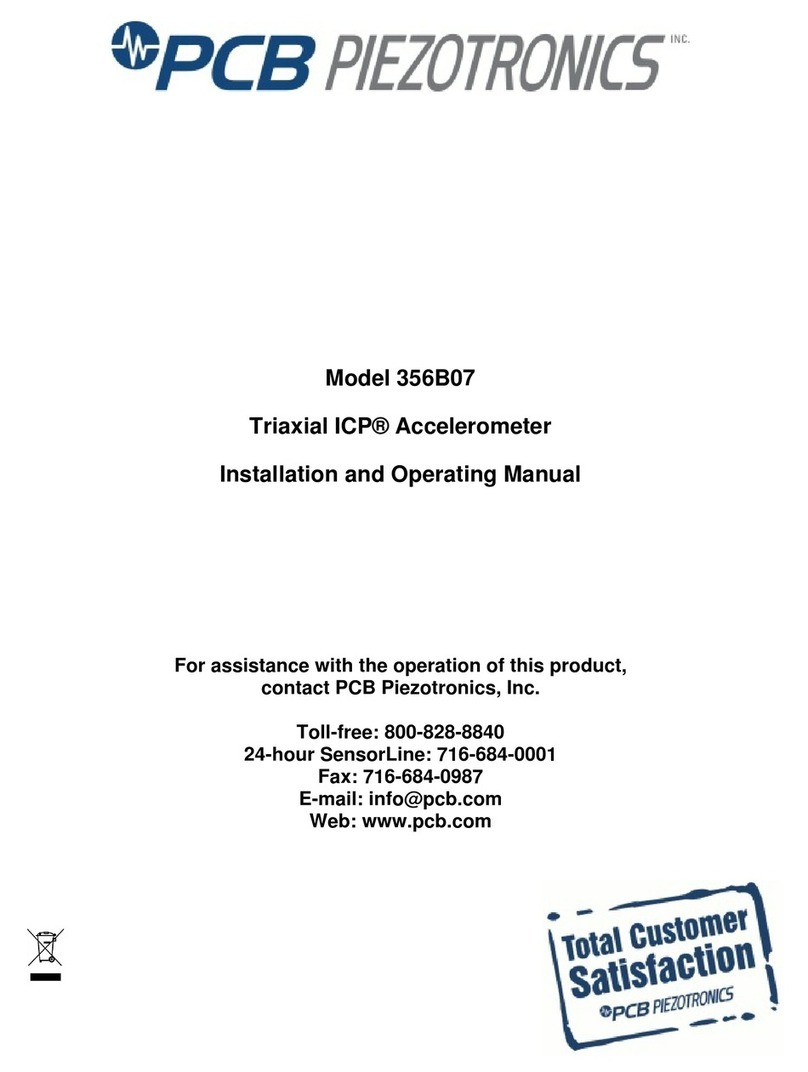
PCB Piezotronics
PCB Piezotronics 356B07 Installation and operating manual

ITI
ITI e-Gauge-lite Assembly manual
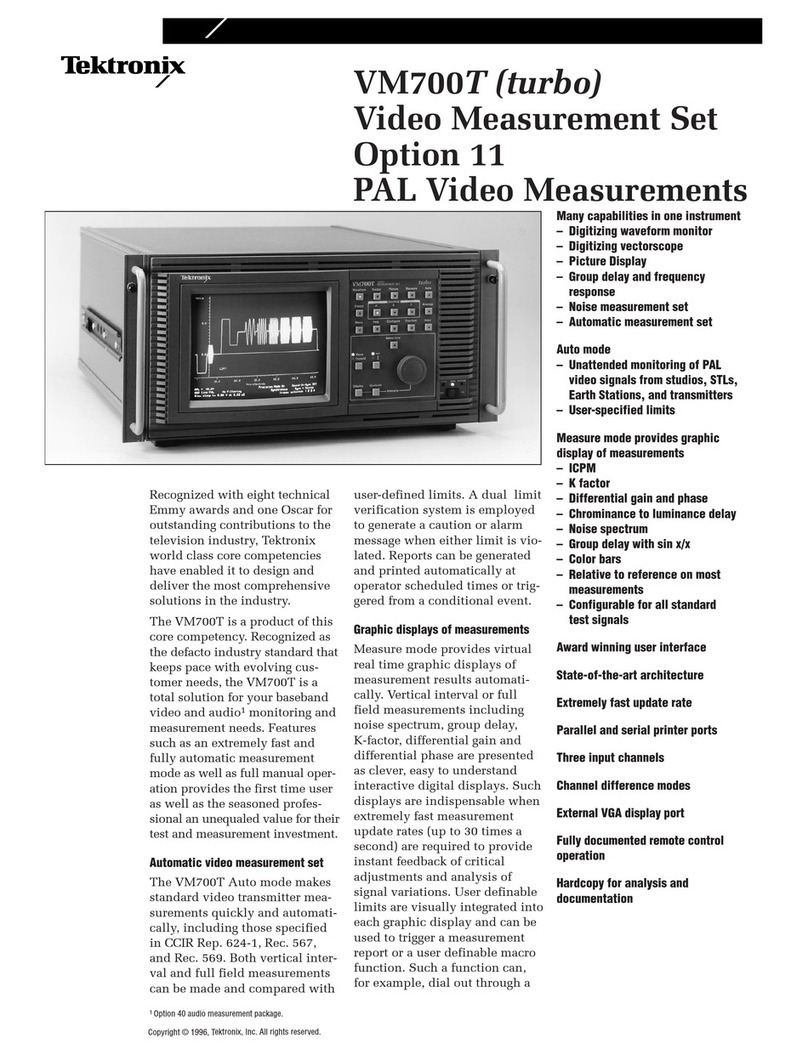
Tektronix
Tektronix VM700T Product information