EarthLinked Technologies Prime-025 Programming manual

PSD-QS (02/16) ©2016 EarthLinked Technologies, Inc.
PrimeSeries
PSDGeothermal HeatingandCoolingSystem
Quick-Start Instructions

PSD-QS (02/16) Page 2
Table of Contents
List of Revisions.................................................................................................................................4
Model Nomenclature .......................................................................................................................5
Safety................................................................................................................................................6
Equipment Manuals.........................................................................................................................6
Installation ........................................................................................................................................7
1) Component Matching...............................................................................................................7
2) Compressor Unit Placement ....................................................................................................8
3) Refrigeration............................................................................................................................9
4) System Applications and Electrical.........................................................................................13
5) SureStart................................................................................................................................19
Features.................................................................................................................................19
Operation...............................................................................................................................19
Flash Codes –Single Phase..................................................................................................21
Flash Codes –Three Phase...................................................................................................22
6) Internal Heat Recovery System..............................................................................................23
Earth Loop Protection System .......................................................................................................26
1) Anode Wire Installation..........................................................................................................26
2) EPS Operation and Service ...................................................................................................31
3) Current Verification................................................................................................................32
Start-Up Process.............................................................................................................................33
1) System Leak Check...............................................................................................................33
2) Evacuation.............................................................................................................................36
3) Initial Charge..........................................................................................................................38
4) Final Charge..........................................................................................................................40
Troubleshooting.............................................................................................................................45
1) Compressor...........................................................................................................................45
2) System...................................................................................................................................49
Commissioning Document ............................................................................................................52
Tools and Equipment.....................................................................................................................59
Triple Evacuation............................................................................................................................60

PSD-QS (02/16) Page 3
List of Figures
Figure 1. Matching Component Model Numbers..................................................................................7
Figure 2. General Layout of System Components ..............................................................................8
Figure 3. Compressor Unit Bracket Installation....................................................................................9
Figure 4. Compressor Unit Clearance..................................................................................................9
Figure 5. PSD Connections ...............................................................................................................10
Figure 6. Line Set Sizes.....................................................................................................................12
Figure 7. PSD Electric Box Components & Electrical Data ................................................................14
Figure 8. PSD Compressor Unit Electrical Schematic, 230-1-60........................................................15
Figure 9. PSD Compressor Unit Electrical Schematic, 230-3-60........................................................16
Figure 10. PSD Air Heating/Cooling/Water Heating Application.........................................................17
Figure 11. PSD Air Heating/CoolingWater Heating Field Wiring Diagram..........................................18
Figure 11a. SureStart Mode of Operation..........................................................................................20
Figure 12. Standard Storage Water Heater –Service Connections ..................................................23
Figure 13a. GSTE Storage Water Heater - Service Connections......................................................24
Figure 13b. GSTE Storage Water Heater –Tank Top View..............................................................24
Figure 14. Compressor Cabinet Socket/Cap.....................................................................................26
Figure 15. Disassembled Plug Connector.........................................................................................27
Figure 16. Anode Wire Insertion .......................................................................................................28
Figure 17. Install the Plug Insert .......................................................................................................29
Figure 18. Engage the Gland Nut .....................................................................................................29
Figure 19. Secure the Anode Wire....................................................................................................30
Figure 20. The Plug and Socket Joint...............................................................................................30
Figure 21. Electric Box with EPS Components .................................................................................31
Figure 22. EPS Current Ratings .......................................................................................................32
Figure 23. Test for DC Current .........................................................................................................32
Figure 24. PSD Internal Flow Schematic ..........................................................................................34
Figure 25. PSD Piping.......................................................................................................................35
Figure 26. Evacuation of PSD System...............................................................................................37
Figure 27. Initial Charge of PSD System............................................................................................39
Figure 28. Final Charge of PSD System...........................................................................................41
Figure 29. Charging to the Middle Sight Glass..................................................................................42
Figure 30. Charging to the Top Sight Glass......................................................................................42
Figure 31. Pressure-Temperature for R-410A....................................................................................43
Figure 32. Start-Up Process ..............................................................................................................44
Figure 33. Compressor Unit Voltage Information..............................................................................46

PSD-QS (02/16) Page 4
Figure 34. Compressor Motor Circuit Testing....................................................................................47
Figure 35. Compressor Motor Grounded Winding Test.....................................................................48
Figure 36. System Troubleshooting Chart.........................................................................................49
List of Revisions
Revised electrical drawings
Revised charging method due to elimination of TXV
Removed the requirement to add 1,000 BTUH to the Heating Load for each
occupant if domestic water heating by Heat Recovery Module (HRM) is part
of the system. See Technical Bulletin TEC-021616
Units now feature a nano Programmable Logic Controller (PLC) which allows
the following features:
True two-speed system
Automatically controls Heating and Cooling staging both of the
Geothermal system and the Auxiliary Heat
Comes with Dual fuel mode capability - Gas or Electric
Thermostat-agnostic: works with most thermostats on the market.
Minimum requirement: single stage Heat/Cool thermostat
Eliminates the need for external balance point control or for an
outdoor sensor
Zoning-friendly for air applications (relies on a damper zone)

PSD-QS (02/16) Page 5
Model Nomenclature
PSD
- 050
- 1
C
PRIME SERIES
HEAT/COOL
NOMINAL CAPACITY
COMPRESSOR,
VOLTS-PHASE-HZ
REFRIGERANT
025 = 25,000 BTUH = 2.0 TONS
030 = 30,000 BTUH = 2.5 TONS
036 = 36,000 BTUH = 3.0 TONS
040 = 40,000 BTUH = 3.3 TONS
050 = 50,000 BTUH = 4.2 TONS
060 = 60,000 BTUH = 5.0 TONS
1 = 230-1-60
1 = 230-3-60
C = R-410A
Disclaimer
Proper installation and servicing of the EarthLinked®Heat Pump is essential to its reliable
performance. All EarthLinked®systems must be installed and serviced by a technician authorized by
Earthlinked Technologies. Installation and service must be made in accordance with the instructions
set forth in this manual. Failure to provide installation and service by an ETI authorized installer in a
manner consistent with this manual will void and nullify the limited warranty coverage for the system.
EarthlinkedTechnologies shall not be liable for any defect, unsatisfactory performance, damage or
loss, whether direct or consequential, relative to the design, manufacture, construction, application or
installation of the field specified components.
Earthlinked Technologies, Inc.
4151 S. Pipkin Road
Lakeland, Florida 33811 USA
phone: 863-701-0096 | toll-free: 866-211-6102
General Info: info-question@earthlinked.com
www.earthlinked.com
CSI # 23 80 00

PSD-QS (02/16) Page 6
Safety
Warning, Caution and Important notices appear throughout the manual. Read these items carefully
before attempting installation, servicing or troubleshooting the equipment.
Equipment Manuals
The following is a listing of the equipment installation manuals that are provided with each component
specified for this EarthLinked®system.
Series AVS and AVV Air Handler
Series CCS Cased Coil
Series HCM Hybrid Cooling Module
Series GSTE Storage Water Heater
Earth Loop Specification and Installation Manual
Earth Loop Protection Kit Installation Manual
IMPORTANT!
Notification of installation, operation or maintenance information which
is important, but which is not hazardous.
WARNING!
Indicates a hazardous situation, which if not avoided will result in
serious injury or death, or equipment or property damage.
CAUTION!
Indicates a potentially hazardous situation or an unsafe practice, which
if not avoided, may result in injury, or equipment or property damage.
IMPORTANT!
Read and follow all installation instructions in these manuals,
appropriate for the EarthLinked®system being installed, BEFORE
initiating the Start-Up procedure.

PSD-QS (02/16) Page 7
Installation
1) Component Matching
Upon receipt of the equipment, carefully check the component model numbers by referencing
Figure 1, to ensure that all components of the system match.
Prime
Compress.
Unit1
Air Handler
Cased Coil
Hybrid Cooling
Module
Earth Loop2
ETI
Model
Arcoaire
Model
ETI
Model
Arcoaire
Model
-025
AVS-0025-C*
FEM4P3600AL
CCS-0025-C*
EAM4X36L21A
HCM-1836C
-024-C
-030
AVS-0030-C*
FEM4P4200AL
CCS-0030-C*
EAM4X42L24A
-030-C
-036
AVS-0036-C*
FEM4P4800AL
CCS-0036-C*
EAM4X48L24A
-036-C
-040
AVS-0040-C*
FEM4P4800AL
CCS-0040-C*
EAM4X48L24A
-042-C
-050
AVS-0050-C*
FEM4X6000BL
CCS-0050-C*
EAM4X60L24A
HCM-4272C
-048-C
-060
AVS-0060-C*
FEM4X6000BL
CCS-0060-C*
EAM4X60L24A
-060-C
1. Contained in each compressor package:
compressor unit
four L-shaped hold down brackets
product literature
2. All series Earth Loops
Figure 1. Matching Component Model Numbers
Guidelines for the general layout of the system components are shown in Figure 2. Before placing the
compressor unit (outside or indoors), review the guidelines in Figure 2.
Warning!
WEAR ADEQUATE PROTECTIVE CLOTHING AND PRACTICE ALL
APPLICABLE SAFETEY PRECAUTIONS WHILE INSTALLING THIS
EQUIPMENT. FAILURE TO DO SO MAY RESULT IN EQUIPMENT
AND/OR PROPERTY DAMAGE, PERSONAL INJURY OR DEATH.

PSD-QS (02/16) Page 8
Figure 2. General Layout of System Components
2) Compressor Unit Placement
EarthLinked®compressor units may be located inside or outside. If outside, place
compressor unit on a standard HVAC outdoor unit pad. If inside, place it on a level, hard
surface. If the compressor unit is to be fastened down, see Figure 3 for bracket
installation.
Avoid placing the compressor unit in or near the living area of the residence.
Attic installations must include a condensate pan with drain, and suspension from rafters
with suspension isolators.
Clearance around the unit for service is illustrated in Figure 4. However, local codes and
applicable regulations take precedence.
PSD Compressor Unit must be placed in an environment in which the surrounding air
temperature does not drop below 40°F.
If the compressor unit or other refrigerant-containing system components are located
indoors, they shall be in a location which (1) is an unoccupied space, or (2) is served by
the circulating air system, or (3) provides 280 cu. ft. of open space per nominal ton of rated
system capacity. The 2012 International Mechanical Code defines residential occupancy
as including permanent provisions for living, sleeping, eating, cooking, and sanitation.
Consult local code authorities to define unoccupied space for the specific installation.

PSD-QS (02/16) Page 9
Figure 3. Compressor Unit Bracket Installation
Figure 4. Compressor Unit Clearance
Placement instructions for other pieces of equipment that make up the EarthLinked®System are
included with those pieces of equipment and are listed in this manual under Equipment Manuals.
3) Refrigeration
After the EarthLinked®compressor unit and other system components are placed, the refrigeration
system tubing is run from the compressor unit to the other components, as appropriate. Figure 5
illustrates the refrigeration and electrical connection points for the compressor unit.
IMPORTANT!
EarthLinked®compressor units that provide space cooling shall be
equipped with an EarthLinked® Hybrid Cooling Module (HCM) when:
(1) Required by the performance tables OR where BOTH of the
following circumstances occur:
(2) Ambient outdoor temperatures have exceeded the outdoor summer
design temperature conditions for a continuous system run time of
at least 7 hours, coupled with the conditions described in (3).
(3) Low thermal conductivity soils that do not effectively absorb and
dissipate heat. Examples of such soils are light dry soil or dry
sand, peat and organic soils dry clay soils and hardpan.
ALSO
EarthLinked®compressor units that provide space heating shall be
equipped with a Heating Performance Enhancement (HPE) control
when required by the performance tables.

PSD-QS (02/16) Page 10
PORT
FUNCTION
TYPE OF
CONNECTION
SIZE, INCHES
-025
-030
-036
-040
-050
-060
A
Electrical, Power
1-1/4” Hole
1
1
1
1
1
1
B
Electrical, Control
7/8” Hole
3/4
3/4
3/4
3/4
3/4
3/4
1
AH/CC/HWM Liquid
Braze
1/2
1/2
1/2
1/2
1/2
1/2
3
EL Liquid*
Braze
3/8
3/8
1/2
1/2
1/2
1/2
4
Anode Socket
---
---
---
---
---
---
---
5
EL Vapor*
Braze
5/8
3/4
3/4
3/4
7/8
7/8
6
AH/CC/HWM Vapor
Braze
3/4
3/4
3/4
7/8
7/8
7/8
7
DWT Supply
Braze
1/2
1/2
1/2
1/2
1/2
1/2
8
DWT Return
Braze
1/2
1/2
1/2
1/2
1/2
1/2
9
Electrical, control
---
---
---
---
---
---
---
10
Electrical, control
---
---
---
---
---
---
---
N = Nameplate and other information
*Line set sizes with provided compressor unit adapters
LEGEND
AH –Air Handler
CC –Cased Coil
EL –Earth Loop
HWM –Hydronic Water Module
HWT –Hydronic Water Tank
DWT –Domestic Water Tank
Figure 5. PSD Connections

PSD-QS (02/16) Page 11
Compressor units are shipped from the factory with a low pressure nitrogen holding charge. Carefully
relieve the holding charge when the compressor unit is being prepared to connect refrigerant system
piping.
Caution!
This compressor unit is equipped with Copeland Ultra 32-3MAF Polyol
Ester Oil (POE). This is the only brand and type of oil that is
recommended for use with ETI compressor units.
POE oil absorbs significant amounts of moisture from the air very
rapidly. Exposure of the POE oil to air must be minimized. Even a few
minutes of exposure to air can be harmful to the system.
After the initial nitrogen holding charge has been released from the
compressor unit, it is critical that air not be allowed to enter the
compressor unit during the process of preparing compressor unit
refrigerant connections (tube cutting, deburring, cleaning, brazing, etc).
To ensure air does not enter the compressor unit while preparing
refrigerant connections, “trickle” dry nitrogen through the compressor
unit, entering at the access port nearest the Active Charge Control
(ACC), to keep airborne moisture out of the compressor unit and the
POE oil.
Complete preparing and brazing all compressor unit refrigerant
connections at one setting to minimize exposure of open connections
to air. Failure to implement the above precautions will result in an
extended period of time to effectively evacuate the system, and may
adversely affect system performance and cause system failure.
Caution!
REFRIGERANT PIPING CONNECTIONS
Refrigerant joints are to be brazed with 15% silver content brazing
alloy, utilizing the NITROGEN BRAZING PROCESS.
NITROGEN BRAZING PROCESS
PURPOSE:
Utilize the NITROGEN BRAZING PROCESS on all brazed refrigerant
piping connections. This process eliminates oxidation products from
inside joint surfaces.
TECHNIQUE:
“Trickle” nitrogen gas at 1-2 psi pressure through the joint area being
brazed, to displace the oxygen. When oxygen has been displaced,
turn off the nitrogen, and relieve the pressure at the joint to
atmospheric prior to brazing.
CONSEQUENCES:
Failure to displace oxygen with nitrogen at the brazed joint will result
in particulate matter being released into the system. The result is
discoloration of refrigerant oil, contamination of the system and
possible system failure.

PSD-QS (02/16) Page 12
The compressor unit has factory installed service valves on the earth loop vapor and liquid stubouts,
outside the compressor unit.
For the installation of system components requiring refrigeration connections, refer to Figure 6 for line
set sizes and the appropriate installation manual(s) following Figure 6.
LINE SET ADAPTERS REQUIRED FOR THE AIR HANDLER, CASED COIL, HYDROINIC
WATER MODULE AND DOMESTIC WATER MODULE ARE FIELD SUPPLIED. CHECK ALL
APPROPRIATE COMPRESSOR UNIT STUB-OUT TUBING SIZES FOR REQUIRED FIELD
SUPPLIED ADAPTERS!
EARTHLOOP, AIR HANDLER, CASED COIL LINE SETS
HWM LINE SETS
COMPRESSOR
UNIT SIZE
LINE SET O.D., INCHES
HWM
MODEL
LINE SET O.D., INCHES
LIQUID*
VAPOR*
LIQUID*
VAPOR*
2.0 Tons (-025)
3/8
5/8
-1836
3/8
1/2
2.5 Tons (-030)
3/8
3/4
-1836
3/8
1/2
3.0 Tons (-036)
1/2
3/4
-1836
3/8
1/2
3.3 Tons (-040)
1/2
3/4
-4248
1/2
5/8
4.2 Tons (-050)
1/2
7/8
-5472
1/2
5/8
5.0 Tons (-060)
1/2
7/8
-5472
1/2
3/4
*Liquid and Vapor lines must BOTH be insulated with Armaflex® or equivalent with at least 1/2” wall thickness for the full
length of the line set.
Figure 6. Line Set Sizes
Series AVS Air Handler
Series CCS Cased Coil
SD Series Heating Option Kit, SDHO-1872
Series HCM Hybrid Cooling Module
Earth Loop Specification and Installation Manual
After installing and nitrogen brazing the HVAC system components and compressor unit service
valves, turn the Service Valves to Full Open and pressurize the refrigeration system to 150 psig with
dry nitrogen and a trace of refrigerant. Valve off the nitrogen Tank from the HVAC system
components and check joints with a sensitive Electronic Leak Detector to ensure they are sealed.
Repair any leaks and re-test as appropriate.

PSD-QS (02/16) Page 13
4) System Applications and Electrical
The PSD compressor unit electrical box major components and electric data for all compressor sizes
are shown in Figure 7.
The SureStart Module is a factory installed component that (1) reduces compressor starting current
and (2) reduces compressor starting torque, thus reducing stress on the compressor at start-up.
The Earth Loop Protection Control System, comprised of the EPS Power Supply, EPS Module and
EPS Fuse is in the contained within the electric box. This system is factory wired and ready to be
connected to the anode wire through an external electrical connection on the backside of the
compressor cabinet. The anode wire connection is detailed in a later section of this manual.
PSD Heating and Cooling System electrical and application illustrations are as follows.
Figure 8. PSD Compressor Unit Electrical Schematic, 230-1-60
Figure 9. PSD Compressor Unit Electrical Schematic, 230-3-60
Figure 10. PSD Air Heating/Cooling/Water Heating System Application
Figure 11. PSD Air Heating/Cooling/Water Heating System Field Wiring Diagram

PSD-QS (02/16) Page 14
Compressor
Unit Model
Compressor
Model
Voltage/Phase/
Hz
Voltage
LRA
RLA
MCA
MFS
Min.
Max.
-025-1C
ZPS26K5E-PFV
230-1-60
207
253
73.0
14.6
18.0
30
-025-2C
ZPS26K5E-TF5
230-3-60
207
253
58.0
9.6
12.0
20
-030-1C
ZPS30K5E-PFV
230-1-60
207
253
83.0
17.0
21.0
35
-030-2C
ZPS30K5E-TF5
230-3-60
207
253
73.0
12.9
16.0
25
-036-1C
ZPS35K5E-PFV
230-1-60
207
253
96.0
20.0
25.0
40
-036-2C
ZPS35K5E-TF5
230-3-60
207
253
88.0
15.8
19.0
30
-040-1C
ZPS40K5E-PFV
230-1-60
207
253
104.0
23.6
29.0
45
-040-2C
ZPS40K5E-TF5
230-3-60
207
253
83.1
15.6
19.2
30
-050-1C
ZPS51K5E-PFV
230-1-60
207
253
152.9
30.2
37.0
50
-050-2C
ZPS51K5E-TF5
230-3-60
207
253
110.0
18.4
23.0
35
-060-1C
ZPS60K5E-PFV
230-1-60
207
253
179.2
33.1
41.0
60
-060-2C
ZPS60K5E-TF5
230-3-60
207
253
136.0
19.6
24.0
35
LRA = Locked Rotor Amps
RLA = Rated Load Amps
MCA = Minimum Circuit Ampacity
MFS = Maximum Fuse or HACR Circuit Breaker Size
(External)
AWS = Consult NEC and Local Codes
Figure 7. PSD Electric Box Components & Electrical Data

PSD-QS (02/16) Page 15
Figure 8. PSD Compressor Unit Electrical Schematic, 230-1-60

PSD-QS (02/16) Page 16
Figure 9. PSD Compressor Unit Electrical Schematic, 230-3-60

PSD-QS (02/16) Page 17
Figure 10. PSD Air Heating/Cooling/Water Heating Application

PSD-QS (02/16) Page 18
Figure 11. PSD Air Heating/CoolingWater Heating Field Wiring Diagram

PSD-QS (02/16) Page 19
5) SureStart
Features
SureStart is a factory installed soft starter that reduces light flicker caused at start-up by scroll
compressor motors. This control has the following features:
60 to 70% reduction in direct in-rush current
Under voltage protection
Motor reversal protection
Self-adjusts for optimal start performance
50/60 Hz compatible
ETL, CE, EMC and RoHs compliant
Tolerant to “dirty power” conditions
Fault LED
Internal current limiting
SureStart is factory wired for the appropriate power supply.
Operation
When the system control calls for compression operation, the compressor contactor will energize. If
the supply voltage is less than “minimum start-up voltage”, a 50 second delay is initiated. At the end
of the delay, another attempt will be made to start the compressor unless the supply voltage remains
unchanged. See Figure 11a for the SureStart Mode of Operation.
SureStart uses an optimated starting process that learns the starting characteristics of the
compressor to further refine the starting cycle on each recurring start.
If the compressor fails to start, the module will terminate the start attempt after 1 second and initiate a
3 minute lockout before attempting a restart.
While the compressor is running,, if supply voltage falls below the “shutdown on low voltage” limit for
2 seconds, SureStart will stop the compressor and initiate a 3 minute lockout. A restart will be initiated
after 3 minutes if the supply voltage is equal to or greater than the “minimum startup voltage”. This is
done to protect the compressor against a sudden drop in supply voltage.
SureStart is able to detect an interruption in power, when the interruption is 0.1 seconds or longer.
When a power interruption is detected, it will shut down the compressor for 3 minutes. A power
interruption that is shorter than 0.1 seconds may result in the compressor running backwards.
SureStart is able to determine if the compressor is running backwards. If this condition is detected,
the control will stop the compressor for 3 minutes before restart is initiated.
If the run capacitor if faulty or has failed, SureStart will shut down the compressor for 3 minutes before
initiating a restart.

PSD-QS (02/16) Page 20
Figure 11a. SureStart Mode of Operation
This manual suits for next models
5
Table of contents
Popular Heating System manuals by other brands
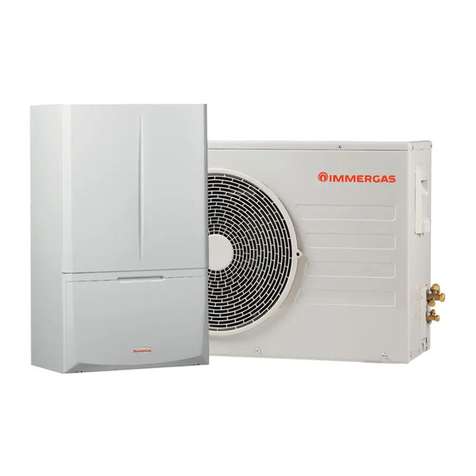
Immergas
Immergas BASIC MAGIS PRO Instructions and warnings

Baxi
Baxi Valor Fires 540 quick guide

EBECO
EBECO Snowmelt Assembly instructions
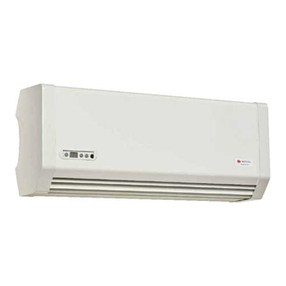
Myson
Myson 7-4 Installation & maintenance manual
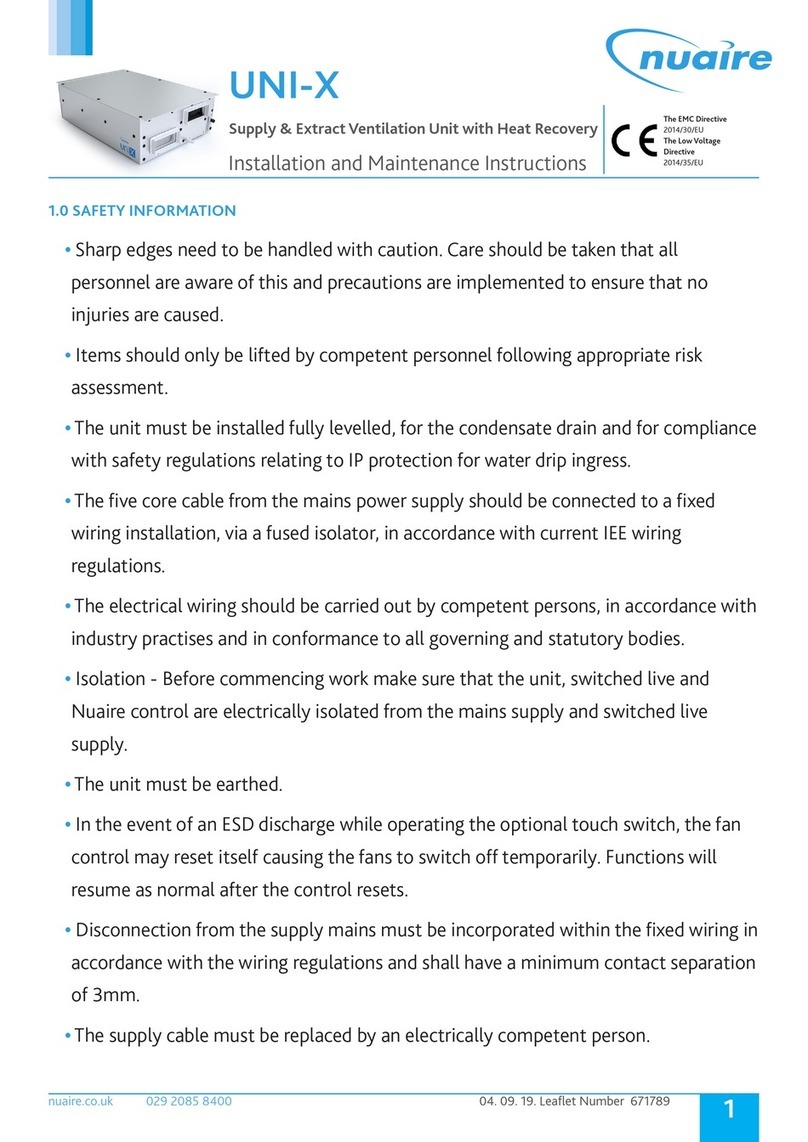
NuAire
NuAire UNI-X Series Installation and maintenance instructions
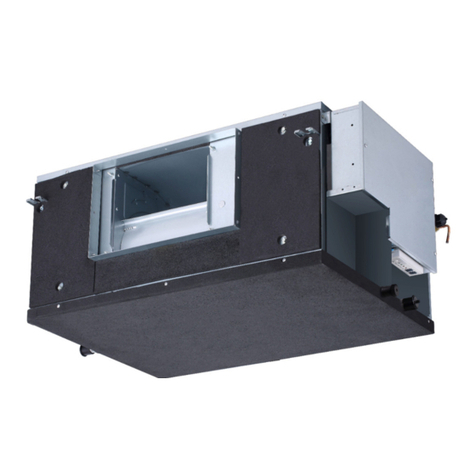
Carrier
Carrier 40VMZ Installation and maintenance instructions
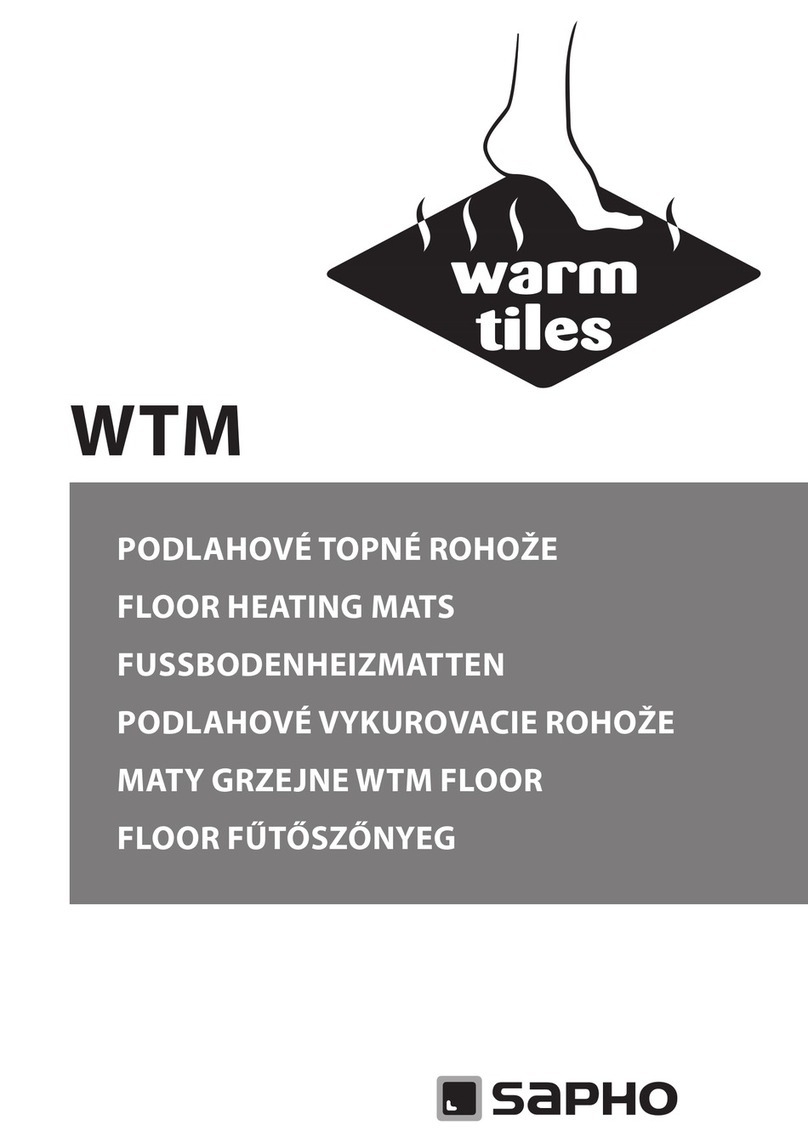
Sapho
Sapho WTM installation manual
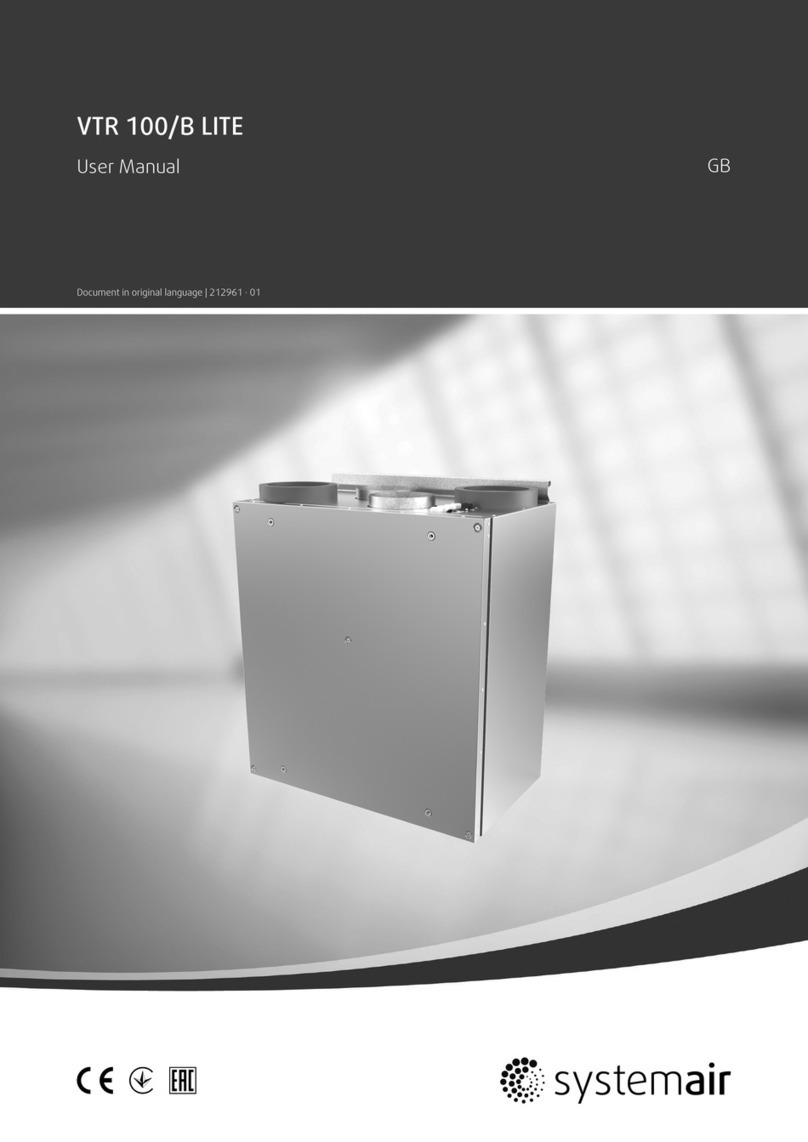
System air
System air VTR 100/B LITE user manual
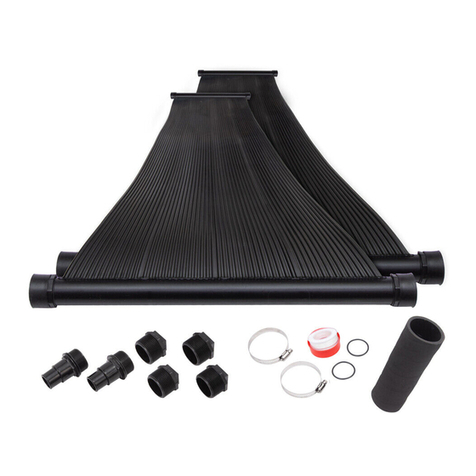
Sunsolar Energy Technologies
Sunsolar Energy Technologies SQ-2212 Installation & operation manual
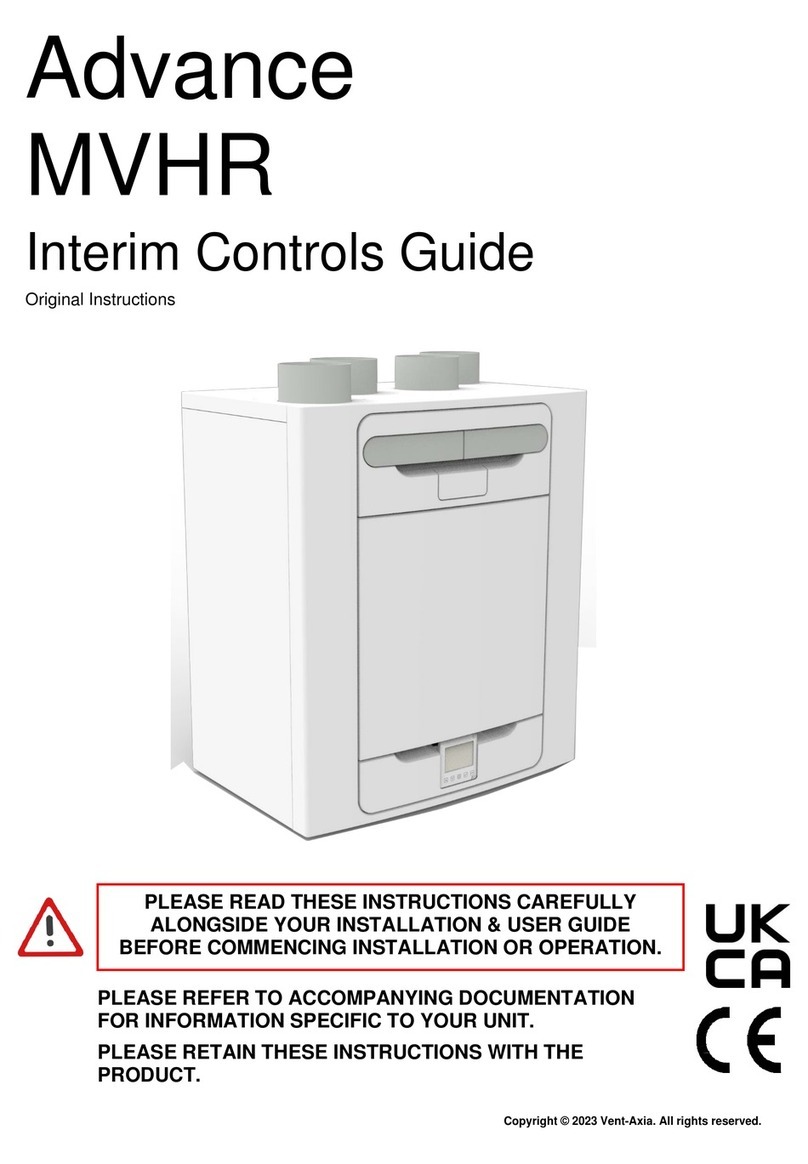
Vent-Axia
Vent-Axia Advance MVHR Original instructions

Koolance
Koolance ALH-2000 user manual
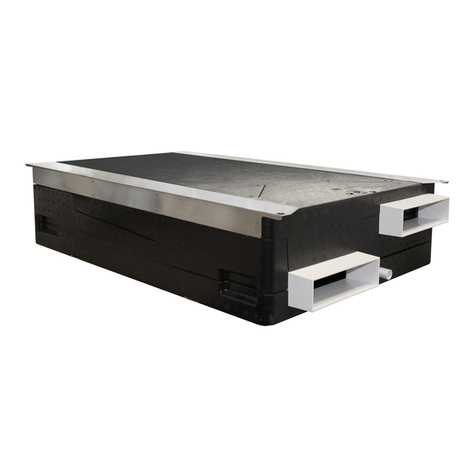
Vent-Axia
Vent-Axia Sentinel Kinetic 200ZP Installation & commissioning