EarthLinked SCW Series Programming manual

SCW-410-QS (05/12) Copyright 2012 Earthlinked Technologies, Inc.
EarthLinked®
SCW Series Compressor Unit
R-410A
Quik-Start Instructions
CONTENTS
PAGE
Pre-Installation
3
Placement & Mechanical Information
5
System Application Options
12
Antifreeze Protection
13
Electrical and Sound Data
14
•230-1-60 Internal Wiring
15
•230-3-60 Internal Wiring
17
•
Field Wiring Diagram
19
System Start-Up
21
•Evacuation/Charging
21
•
Final Charge
(Heat/Cool and Cool Only)
23
•
Final Charge
(Heat Only)
29

SCW-410-QS (05/12)
Disclaimer
Proper installation and servicing of the EarthLinked®Heating and Cooling System is essential to its
reliable performance. All EarthLinked®systems must be installed and serviced by an authorized,
trained technician who has successfully completed the training class and passed the final
examination. Installation and service must be made in accordance with the instructions set forth in
this manual and the current EarthLinked Heating and Cooling Systems Installation, Operation and
Maintenance Manual. Failure to provide installation and service by an authorized, trained installer
in a manner consistent with the subject manuals will void and nullify the limited warranty coverage
for the system.
READ THE CURRENT EarthLinked Heating and Cooling Installation, Operation and
Maintenance Manual FOR COMPLETE INSTALLATION DETAILS.
EarthlinkedTechnologies shall not be liable for any defect, unsatisfactory performance, damage or
loss, whether direct or consequential, relative to the design, manufacture, construction, application
or installation of the field specified components.
Earthlinked Technologies, Inc.
4151 South Pipkin Road
Lakeland, Florida 33811
tel. 863-701-0096 ● fax 863-701-7796
info@earthlinked.com ● www.earthlinked.com
CSI # 23 80 00

SCW-410-QS (05/12) Page 3
Pre-Installation
Upon receipt of the equipment, carefully check the shipment against the bill of lading. Reference
EarthLinked®matching system component model numbers in Figure 1. Make sure all units have
been received and model numbers are the same as those ordered.
Compressor
Unit
1
Auxiliary Cooling
Module
3 Earth Loop2
Cathodic Protection
System
-024 ACM-1836C -024-C CPS-1830
-036 -036-C CPS-3642
-048 ACM-4272C -048-C CPS-4872
-060 -060-C CPS-4872
-068 -072-C CPS-4872
1. All series Compressor Units: SC, SD, SCW
Contained in each compressor package:
•compressor unit
•four L-shaped hold down brackets
•service valves-liquid and vapor
•adapters for service valves and earth loop line set
•product literature
2. All series Earth Loops: V1, D1, T1, V1.5, D1.5, V2, D2, D3, H1, H5
3. ACMs are for SC, SD and SCW compressor units only.
Note: Desuperheater and all EarthLinked®thermostats can be
utilized throughout capacity range.
Figure 1. Model Numbers
Guidelines for the general layout of the system components are shown in Figures 2a and 2b.
Before placing the compressor unit (outside or indoors), review the guidelines in Figures 2a and
2b, and the information regarding the Auxiliary Cooling Module and Heating Performance
Enhancement Control following Figure 2b.

SCW-410-QS (05/12) Page 4
Figure 2a. General System Layout
Figure 2b. Typical SCW Compressor Unit Primary Circuit Plumbing

SCW-410-QS (05/12) Page 5
Placement and Mechanical Information
EarthLinked®compressor units may be located outside or inside the building, following these
guidelines.
OUTSIDE
Locate compressor unit:
•On a standard HVAC condensing unit pad, resting on firm, level, settled ground.
•Same as for INSIDE placement. See below.
INSIDE
Locate compressor unit:
•On a solid, level hard surface. If compressor unit is to be fastened, see Figure 3 for bracket
installation.
•Where compressor unit sound and vibration will not disturb human activities. Compressor unit
may be located in garage, basement, crawl space or utility room. Avoid placing compressor unit
in kitchen, bedroom, family/living/dining room areas.
•In a condensate pan.
•On vibration pads.
•Attic installations, where necessary, must include a drip pan, anti-vibration pads and are to be
suspended from the rafters with suspension isolators.
•For SD compressor units (which have potable domestic water connections) where the
surrounding air temperature remains above 40°F.
•Where suggested clearance is 3 feet on both sides, top and front, for access. However, local
codes and applicable regulations take precedence. Clearance from back panel to wall and
minimum side clearance should be at least one foot. See Figure 4 for details.

SCW-410-QS (05/12) Page 6
•Where the total length of refrigerant line sets (from manifolds to compressor unit and from
compressor unit to air handler) do not exceed 125 feet, as shown in Figure 2a.
•Where the compressor unit is no more than 20 feet higher than the earth loop manifolds.
Compressor unit may be located lower than the earth loop manifolds. See Figure 2a.
•For SCW compressor units providing radiant panel hydronic hot water or chilled water, where
the hydronic primary circuit is adequately protected from freezing by providing adequate site-
specific antifreeze protection for the water circulating system.
Figure 3. Compressor Unit Bracket Installation
Figure 4. Compressor Unit Clearance

SCW-410-QS (05/12) Page 7
Compressor units are shipped from the factory with a low pressure nitrogen holding charge.
Carefully relieve the holding charge when the compressor unit is being prepared to connect
refrigerant system piping.
The compressor unit package contains a service valve kit and an adapter kit. The two service
valves are to be installed on the earth loop vapor and liquid connections of the compressor
unit, using the adapters to right-size to the proper earth loop line set.
Installation of the service valves will provide isolation of the earth loop system from the compressor
unit and provide easy access to the refrigerant system.
The service valve configuration provided is illustrated in Figure 4a. The ball valve stem is
accessed by removing the cap. The service port is equipped with a Schrader valve insert.
Figure 4a. Service Valve Orientation
Complete service valve installation instructions are contained in the Service Valve Kit Installation
Manual, included with the service valves.

SCW-410-QS (05/12) Page 8

SCW-410-QS (05/12) Page 9
Figure 5. SCW Connections for R-410A

SCW-410-QS (05/12) Page 10
Figure 6. SCW Internal Flow Schematic

SCW-410-QS (05/12) Page 11
Figure 7. SCW Piping

SCW-410-QS (05/12) Page 12
System Application Options
Figure 8. SCW Radiant Panel Hydronic Heating and Air (Chilled Water) Cooling

SCW-410-QS (05/12) Page 13
Antifreeze Protection
When SCW compressor units are applied to radiant panel hydronic heating and/or chilled water
cooling systems, the water circulating system must be protected from potential damage due to
freeze-up by utilizing an adequate antifreeze solution. The antifreeze protection is provided by the
installer prior to the EarthLinked®system start-up.
Propylene-glycol antifreeze solution with an inhibitor is the type of antifreeze solution required for
Earthlinked®products utilized in radiant panel hydronic heating and/or chilled water cooling
systems. These systems shall be freeze protected consistent with the application -specific
minimum temperature, as shown in the table below. Propylene-glycol antifreeze solutions should
always be in the range of 20% to 50% by volume, as indicated in the table.
TEMPERATURE, °F PROPYLENE GLYCOL, %
WATER SOLUTION
MULTIPLIER FACTOR (WSMF)
18
20
x 1.03
8
30
x 1.07
-7
40
x 1.11
-29
50
x 1.16
Propylene Glycol Freeze Protection Table
Propylene-glycol can be purchased in the straight form and mixed with an inhibitor prior to filling
the system, or it can be purchased as inhibited propylene-glycol. The following are examples of
manufacturers for the above:
Straight propylene-glycol: Chemical Specialties, Inc. (www.chemicalspec.com/spg.html)
Inhibitor: Nu-Calgon Products, Ty-lon B20 (www.nucalgon.com/products)
Inhibited propylene-glycol: Houghton Chemical Corp., SAFE-T-THERM®,
www.houghton.com/fluids/safe-t-therm/index.html)

SCW-410-QS (05/12) Page 14
General guidelines for introducing propylene glycol into the water circulating system follow. The
manufacturer’s specific instructions and industry standards always take precedence when
introducing propylene-glycol to the system.
•Calculate the quantity of inhibited propylene-glycol (fluid) required to achieve the
desired results.
•Introduce a sufficient quantity of water to the system and pressure check to ensure
a sealed system.
•Drain some water from the system to provide enough volume for the calculated
amount of fluid.
•Add the correct amount of fluid and any water needed to completely refill the
system, allowing for liquid expansion due to operating temperature.
•Circulate the inhibited propylene-glycol antifreeze solution for at least 24 hours to
ensure complete mixing. Check the liquid concentration to assure that the correct
mixture is obtained.
Electrical and Sound Data
Compressor
Model Voltage/Phase/Hz
Voltage
LRA RLA MCA MFS
Sound Pressure Level *
@10 ft, dB(A)
Min.
Max.
-024-1C 230-1-60 207 253 64.0 14.3 18.0 30 57.0
-024-2C 230-3-60 207 253 58.0 9.3 11.0 20 60.0
-036-1C 230-1-60 207 253 112.0 20.0 25.0 40 59.0
-036-2C 230-3-60 207 253 88.0 15.1 19.0 30 62.0
-048-1C 230-1-60 207 253 134.0 27.9 34.0 50 59.0
-048-2C 230-3-60 207 253 110.0 17.7 22.0 35 62.0
-060/-068-1C 230-1-60 207 253 178.0 28.3 34.8 50 63.0
-060/-068-2C 230-3-60 207 253 136.0 19.2 23.9 40 64.0
LRA = Locked Rotor Amps MFS = Maximum Fuse or HACR Circuit Breaker Size
RLA = Rated Load Amps (External)
MCA = Minimum Circuit Ampacity AWG = Consult NEC and Local Codes
*Data Source is published Copeland Compressor Sound Power Levels converted to Sound Pressure Level in
dB(A) at 10 Feet, having two reflective surfaces. Effects of ETI compressor unit cabinet and components not
included.
Figure 9. Compressor Unit Electrical and Sound Data

SCW-410-QS (05/12) Page 15
Figure 10. SCW Electrical Ladder Diagram (230-1-60)

SCW-410-QS (05/12) Page 16
Figure 11. SCW Electrical Schematic (230-1-60)

SCW-410-QS (05/12) Page 17
Figure 12. SCW Series 230-3-60 Electrical Ladder Diagram

SCW-410-QS (05/12) Page 18
Figure 13. SCW Series 230-3-60 Electrical Schematic

SCW-410-QS (05/12) Page 19
Figure 14. (Part 1 of 2) SCW Field Wiring Diagram
(Reference Figure 8)

SCW-410-QS (05/12) Page 20
Figure 14. (Part 2 of 2) SCW Field Wiring Diagram
(Reference Figure 9)
This manual suits for next models
1
Table of contents
Other EarthLinked Air Compressor manuals
Popular Air Compressor manuals by other brands

EKOM
EKOM DK50 4VR/50/M user manual

Metabo
Metabo Mega 600 D Original operating instructions

Ingersoll-Rand
Ingersoll-Rand XHP1070WCAT Operating, Maintenance & Parts Manual

California Air Tools
California Air Tools 60033CR owner's manual
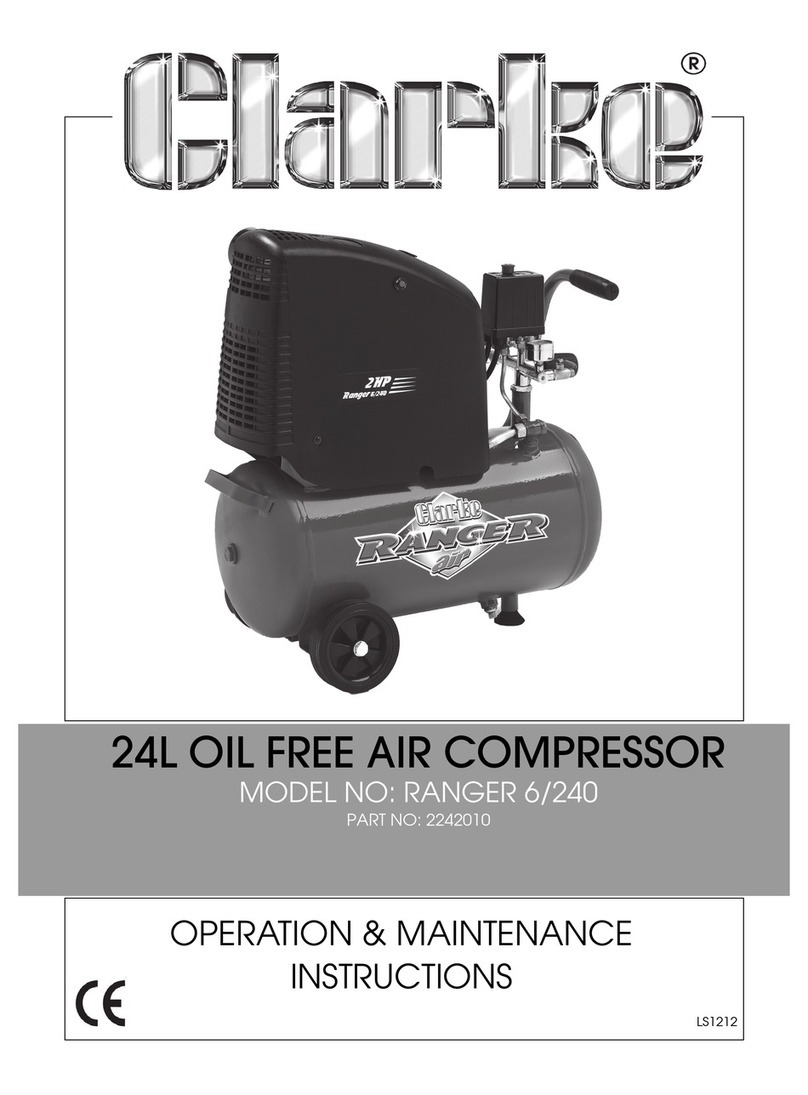
Clarke
Clarke RANGER 6/240 Operation & maintenance instructions
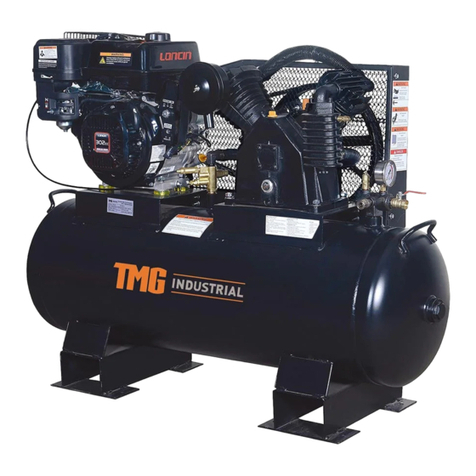
TMG
TMG TMG-GAC40 product manual