EASY DRIVE GT610 Series User manual

GT610/GT620 Series High Performance Servo Driver User Manual
- 1 -
Preface
Thank you for your selecting GT610/GT620 Series Servo Driver Products of
Shenzhen Easydrive Electrical Co., Ltd.GT610/GT620 series servo driver has
realized complete closed-ring servo control of spindle motor, integrating speed
control and position control, which could realize processings such as
high-precision turning, milling and grinding etc., and is more competitive than
traditional variable-frequency drive in heavy cut aspect, meanwhile, for its
outstanding control performance, it could make the spindle possess servo function,
participate interpolation control of coordinate axis, and accomplish functions such
as rigid tapping and thread cutting etc. Its unique position control function, could
meet requirements on high-class equipment in processing center and turning
center etc. It could be used in application occasions such as machine tool spindle
and textile machine etc. It is a high-performance AC induction motor servo driver.
Before using GT610/GT620 series servo driver, users and related technicians need
to carefully read this user manual, to guarantee correct installation and operation
of the servo driver, so as to make it exert the best performance.
This user manual is subject to change without notice, please refer to the latest
version.

GT610/GT620 Series High Performance Servo Driver User Manual
- 2 -
Readers
This user manual is suitable for the following persons.
Servo driver installers, engineering technicians (electrical engineers and electrical
operators etc.), and designers. Please make sure that this manual could reach final
users.
Conventions in this Manual
Symbol Conventions
Note: Occasions which may cause injuries to medium or slight extent
because of failing to operate according to requirements.
Danger: Occasions which may cause death or heavy injury because of
failing to operate according to requirements.
Notices:
When get the product, please confirm
Notice
1.
Please do not install any damaged driver or driver lack of parts. Any
personal injury shall be prevented.

GT610/GT620 Series High Performance Servo Driver User Manual
- 3 -
Installation
Notice
1.During transportation, please support the bottom of the machine. The
danger of legs hurt
by falling main body may exist for only holding the
panel.
2.
Please install on material panels such as metal panels which are
nonflammable etc. Installation on flammable material
s, may cause fire
danger.
3.When more than one driver are installed into the same control cabinet,
please set a cooling fan, and make inlet air temperature under 40℃.For
overheat may cause fire or other accidents.
Wiring
Danger
1.Before wiring, please make sure the input power has been switched off.
There’re dangers of electric shock and fire.
2.Please ask electrical engineering technicians to carry out wiring. There’re
dangers of electric shock and fire.
3.Grounding terminals shall be grounded reliably. There’s danger of electric
shock.
4.When emergency stop terminal is connected, make sure to check whether its
motion is effective or not. There’s danger of injury.(Wiring responsibility
shall be undertaken by users)
5.
Please do not touch output terminal directly, keep driver’s output terminal
from connecting with outer shell, and no short circuit connection shall be
allowed between output terminals. There’re dangers of electric shock and
short circuit.

GT610/GT620 Series High Performance Servo Driver User Manual
- 4 -
Notice
1.Please verify whether rated voltage of AC main circuit coincides with that of
the driver. There’re dangers of injury and fire.
2.Do not carry out breakdown test on driver. It will cause damages to
semi-conductor components etc.
3.
Please connect braking resistors or braking units according to wiring
diagram. There’s danger of fire.
4.Please use screwdriver fastening terminals with specified torque. There’s
danger of fire.
5.Do not connect input power cable to output U, V, and W terminals. Voltage
added on output terminals may cause internal damages to the driver.
6.Do not connect phase-
shifting capacitor and LC/RC noise filter into output
circuit. It will cause internal damages to the driver.
7.Do not connect electromagnetic switches or electromagnetic contactors into
output circuit. When the driver is running with load, surge current produced
by motions of electromagnetic switch and electromagnetic contactor may
cause over-current protecting circuit motion of the driver.
Maintenance and Check
Danger
1.
Do not touch connecting terminals of the driver, for there’s high voltage on
them. There’s danger of electric shock.
2.
Before power on, please be sure to install the panel, and make sure to power
off during dismantling the panel. There’s danger of electric shock.
3.Non-professional technicians shall not carry out any maintenance or check.
There’s danger of electric shock.

GT610/GT620 Series High Performance Servo Driver User Manual
- 5 -
Notice
1.CMOS integrated circuit has been installed on keyboard, control circuit
board and driving circuit, please take caution during usage. Do not touch the
circuit board directly with your fingers, for electrostatic induction may
damage integrated chips on circuit board.
2.
When powered on, please do not change wiring or dismantle terminal
connection. During running, please do not check signals. For it will damage
the equipment.

GT610/GT620 Series High Performance Servo Driver User Manual
- 6 -
Table of Contents
Chapter I Servo Driver Introduction.............................................................................. 8
1.1 Model Description......................................................................................... 8
1.2 Driver Nameplate .......................................................................................... 8
1.3 Product Series................................................................................................ 9
1.4 Technical Specification.................................................................................. 9
1.5 Braking Resistor Model Selection ............................................................... 11
Chapter II Interface and Wiring................................................................................... 12
2.1 Input/Output Control Terminal Interface Theory......................................... 12
2.2 Wiring and Terminal Description................................................................. 22
2.3 Terminal Wiring Layout............................................................................... 29
Chapter III Installation Dimension.............................................................................. 31
Chapter IV Operation and Debugging......................................................................... 32
4.1 Display Panel and Function Introduction..................................................... 32
4.2 Debugging Guide......................................................................................... 34
Chapter V Parameter Table.......................................................................................... 38
5.1 Debugging Parameter Table......................................................................... 38
5.2 Display Monitoring Parameters................................................................... 52
5.3 Alarm Failure Parameters ............................................................................ 54
Chapter VI Parameter Instructions .............................................................................. 55
6.1 Group F0 - System Parameter Instructions.................................................. 55
6.2 Group F1 - Motor Parameter Description.................................................... 64
6.3 Group F2 - DI/DO Terminal Defined Parameter Description...................... 66
6.4 Group F3 - Acceleration/Deceleration Parameter Description..................... 73
6.5 Group F4 - Speed Ring Parameter Description............................................ 74
6.6 Group F5 - Position Ring Parameter Description......................................... 75
6.7 Group F6 - AI/AO Terminal Parameter Description.................................... 78

GT610/GT620 Series High Performance Servo Driver User Manual
- 7 -
6.8 Group F7 - Pulse Setting and Electronic Gear Ratio Parameter Description 83
6.9 Group F8 - Spindle Positioning and Gear Ratio Parameter Description ...... 85
6.10 Group F9 - Communication Parameter Description................................... 86
Chapter VII Troubleshooting....................................................................................... 88
7.1 Failure Reasons and Countermeasures......................................................... 88
7.2 Failure Inquiry............................................................................................. 92
Chapter VIII Application Functions ............................................................................ 93
8.1 Trial-run Operation...................................................................................... 93
8.2 Speed Control .............................................................................................. 96
8.3 Position Control......................................................................................... 101
8.4 Positioning Control.................................................................................... 102
8.5 Carry Control............................................................................................. 108
8.6 Swing Control............................................................................................ 109
8.7 Rigid Tapping ............................................................................................ 110
Chapter IX Communication Instructions....................................................................111
9.1 MODBUS Communication Protocol ..........................................................111
9.2 GT610/GT620 Communication Protocol................................................... 114
9.3 GT610/GT620 Parameter Communication Address .................................. 128
9.4 Communication Application Examples:..................................................... 130
Maintenance Agreement............................................................................................ 135
Warranty.................................................................................................................... 136
Memorandum............................................................................................................ 137

GT610/GT620 Series High Performance Servo Driver User Manual
- 8 -
Chapter I Servo Driver Introduction
1.1 Model Description
GT620 - 4 T 0075 M
Spindle Servo Series
610
621
620
622
610 Series
621 Series
620 Series
622 Series
Code
4
Voltage Level
380V
Code
T
Input Voltage
3-phase
Code
M
Configurable Encoder
Photoelectric Encoder
R
P Electromagnetic Encoder
Code
0022
Adaptable Motor
2.2KW
0037 3.7KW
0055 5.5KW
0075 7.5KW
Rotary Transformer
Fig. 1-1
1.2 Driver Nameplate
Fig. 1-2

GT610/GT620 Series High Performance Servo Driver User Manual
- 9 -
1.3 Product Series
Power (kw) 2.2 3.7 5.5 7.5
Adapter Motor Function (kw) 2.2 3.7 5.5 7.5
Output
Voltage (V) Three-phase 0 ~ Rated input voltage
Rated Current (A)
8.4
12.5
15
20
Overload Capacity 130%10 min., 150%1 min., 175%15 s
Input Rated Voltage/Frequency Three-phase 380V; 50Hz/60Hz
Allowable Voltage Range -10%~15% of rated voltage
Braking Unit
Standard Built-in
Protection Grade IP20
Cooling Mode
Forced Air Cooling
1.4 Technical Specification
Output
Max. output voltage
Outlet
Input voltage 380V corresponds to max.
output 390V Outlet
Max. output speed (rpm)
30000rpm
Input Rated voltage/frequency Three-phase 380V; 50Hz/60Hz
Frequency variation range ±5%of rated frequency
Control
Characteristics
Control mode
SVC (Sensorless vector control); VC
(Sensor vector control)
Speed adjustment range 1: 10000(VC)
Speed control precision ±1rpm
Position control precision ±1Pulse
Rotation speed set
resolution Digital quantity 1rpm

GT610/GT620 Series High Performance Servo Driver User Manual
- 10 -
Braking mode Energy-consuming braking: External
braking resistor
Input/Output
Interface
Digital quantity input 8-way optical coupler input; input mode:
PNP, NPN optional
Digital quantity output 3-
way open circuit collector output;
+24V DC, 50mA
Analog quantity input
2-way: 0~±10V
Relay output
2-way: AC250V, 3A; DC30V, 1A
Encoder input interface 1:Max. receiving frequency 500kHz, 5V
Pulse input interface 1:Directional pulse or orthogonal pulse,
5V
Encoder output interface 1:Max. receiving frequency 500kHz, 5V
Bus interface
RS485 standard
Spindle
Function
Speed control
Range: 0~30000rpm; Rotation:forward
and backward; speed instructs:Analog
quantity and pulse
Accurate stop positioning Precision± 1Pulse; position adjustment:
User parameter settings
Rigid tapping
Able to interface with multiple domestic
and imported systems, tapping error ±2%
Other functions C-axis control, thread cutting, electronic
gear and swing control
Motor overload
If regulation time of overload alarm is
exceeded, an alarm will be output; set by
parameters
Input phase failure
abnormality
When input phase fails, output a phase
failure alarm.

GT610/GT620 Series High Performance Servo Driver User Manual
- 11 -
Use
Environment
Use location
No dust, corrosive gas or flammable gas.
Temperature Derating use between −10~+40
℃
+40~+50 ℃.
Humidity
5
~
95%, no condensation is allowed.
Vibration Vibration frequency ≤ 20Hz: 9.8m/s2;
20Hz≤vibration frequency≤50Hz: 2m/s2
1.5 Braking Resistor Model Selection
Servo Driver Model
Braking Resistor Min.
Power
Braking Resistor
Min. Value Qty.
GTXX-4T0022 500W 55Ω 1
GTXX-4T0037 800W 55Ω 1
GTXX-4T0055 1200W 35Ω 1
GTXX-4T0075 1500W 35Ω 1
Remarks:
◆Braking resi stor val ue shal l be equal to or larger than standard resistor value in
the above table, otherwise, it will cause damages to braking pipe.
◆Try to avoid using wire-wound resistor, with a relatively large spurious
inductance, which will damage driver braking pipe, when used on machine tool,
wire-wound resistor itself may also produce electricity leakage or overheat to burn
equipment.
◆I t i s better to sel ect l arger brak i ng resi stor pow er, braki ng resi stor pow er i n the
above table shall be calculated according to braking sustaining time within 30s, if
braking sustains, larger resistor power shall be needed.
◆For machine tool needs to brake frequently, braking resistor heating will
become serious, please keep away from driver installation position, and install a
radiator fan.
◆Standard product will not provide braking resistor.

GT610/GT620 Series High Performance Servo Driver User Manual
- 12 -
Chapter II Interface and Wiring
2.1 Input/Output Control Terminal Interface Theory
2.11 Input Terminal Interface Theory
This series servo driver’s multi-functional input terminal adopts a full-bridge
rectifier circuit. PLC is the public terminal of DI1~DI8, and PLC terminal could
adopt PNP mode or NPN mode for connection. The mode of DI1~DI8 to connect
with external interface is very flexible. Typical wiring methods are as follows:
1) Connection mode using a 24V internal power supply of the servo driver, and
adopting switch control is as shown in Fig. 2-1 (Note: Connecting wire between
PLC and 24V terminal shall be reliably connected).
+
-
+
-
24V
COM
PLC
DI1
DI8
+ -
24V DC
5V
5V
Driver Internal Circuit
External Wiring
K1
K8
Fig. 2-1 Connection Mode Using Internal Power Supply Switch Control
2) Connection mode using an external power supply, and adopting switch control
is as shown in Fig. 2-2 (Note to remove the connecting wire between PLC and
24V terminal).

GT610/GT620 Series High Performance Servo Driver User Manual
- 13 -
PLC
DI1
DI8 +
-
+
-
5V
Servo Internal Circuit
24V DC
External Wiring
K8
K1
Fig. 2-2 Connection Mode Using an External Power Supply Switch Control
External Control Adopts NPN/PNP Control Mode:
1)Connection mode using a +24V power supply inside the driver, and
adopting an NPN-typed output external controller is as shown in Fig. 2-3.
1
8
External Control Interface
Shielding Wire Near-end Grounded
24V
COM
PLC
DI1
DI8
+ -
24V DC
+
-
+
-5V
5V
Driver Internal Circuit
Fig. 2-3 Connection Mode Using a +24V Internal Power Supply of the Driver
2)Connection mode using a +24V internal power supply of the driver, and

GT610/GT620 Series High Performance Servo Driver User Manual
- 14 -
adopting a PNP type external controller (Note to remove the connecting wire
between PLC and 24V terminal, to short-circuit PLC and COM terminal), as
shown in Fig. 2-4.
1
8
External Control Interface
Shielding Wire Near-end Grounded
24V
COM
PLC
DI1
DI8
+ -
24V DC
+
-
+
-5V
5V
Driver Internal Circuit
Fig. 2-4 Connection Mode Using a +24V Internal Power Supply of the Driver
3)NPN connection mode using an external power supply: (Note to remove
the connecting wire between PLC and 24V terminal), as shown in Fig. 2-5.
1
8
External Control Interface
Shielding Wire Near-end Grounded
PLC
DI1
DI8 +
-
+
-
5V
5V
24V
Driver Internal Circuit
Fig. 2-5 Connection Mode Using an External Power Supply

GT610/GT620 Series High Performance Servo Driver User Manual
- 15 -
4)PNP connection mode using an external power supply (Note to remove the
connecting wire between PLC and 24V terminal), as shown in Fig. 2-6.
1
8
External Control Interface
Shielding Wire Near-end Grounded
PLC
DI1
DI8
+
-
+
-
5V
5V
24V
Driver Internal Circuit
Fig. 2-6 Connection Mode Using an External Power Supply
2.12 Digital Quantity Output Interface Theory
1) Multi-functional output terminals D01, D02 and D03 (N/A temporarily) could
use 24V internal power supply of the driver, and connection methods include the
following:

GT610/GT620 Series High Performance Servo Driver User Manual
- 16 -
Connection method I:
DO1/DO2/DO3
CME
24V
Relay
5V
Servo Internal Circuit External Circuit Interface
COM
Fig. 2-7 Connection Method I Using Servo Internal Power Supply
Connection mode II:
DO1/DO2/DO3
CME
COM
Relay
5V
Servo Internal Circuit External Circuit Interface
24V
Fig. 2-8 Connection Method II Using Servo Internal Power Supply
2) Multi-functional output terminals D01, D02 and D03 (N/A temporarily) could
also use a 24V external power supply, and connection methods include the
following:

GT610/GT620 Series High Performance Servo Driver User Manual
- 17 -
Connection mode I:
DO1/DO2/DO3
CME
Relay
5V
Driver Internal Circuit External Circuit Interface
24v
Fig. 2-9 Connection Method I Using Servo External Power Supply
Connection method II:
DO1/DO2/DO3
CME
Relay
5V
Driver Internal Circuit External Circuit
Interface
24v
Fig. 2-10 Connection Method II Using Servo External Power Supply
2.13 Analog Quantity Input/Output Interface
1) For AI1/AI2 analog voltage input, the connection mode using a ±10V internal
power supply of the servo driver to connect to an external potentiometer is as
shown in Fig. 2-11.

GT610/GT620 Series High Performance Servo Driver User Manual
- 18 -
3
1
2
AI1/AI2
+10V
GND
10k Potentiometer
External Circuit Interface Driver Internal Circuit
R1
R4
R2
R3
Note: When using analog voltage, it is required to connect short circuit cap of J9/J8 to
pin 1 and 2, and jumper terminal corresponding to AI1 is J9, while jumper terminal
corresponding to AI2 is J8.
J10/J9/J8
-10V
Fig. 2-11 Analog Voltage Input Using an Internal Power Supply
2) For AI1/AI2 analog voltage input, the mode using a 10V external power supply
connecting to a potentiometer is as shown in Fig. 2-12.

GT610/GT620 Series High Performance Servo Driver User Manual
- 19 -
3
1
2
AI1/AI2
GND
10k Potentiometer
External Circuit Interface Driver Internal Circuit
R1
R4
R2
R3
Note: When using analog voltage, it is required to connect short circuit cap of J9/J8 to pin 1 and 2,
and jumper terminal corresponding to AI1 is J9, while jumper terminal corresponding to AI2 is J8.
J10/J9/J8
24V
Fig. 2-12 Analog Voltage Input Port Using an External Power Supply
3) AI1/AI2 analog current signal (4mA-20mA) input wiring is as shown in Fig.
2-13.
3
1
2
AI1/AI2
GND
External Circuit Interface Driver Internal Circuit
R1
R4
R2
R3
4-20mA Current Supply
J9/J8
Note: When using current input, it is required to connect short circuit cap of
J9/J8 to pin 2 and 3, and jumper terminal corresponding to AI1 is J9, while
jumper terminal corresponding to AI2 is J8.
Fig. 2-13 Analog Current Signal Input

GT610/GT620 Series High Performance Servo Driver User Manual
- 20 -
4) AO1/AO2 port analog voltage (0-10v)/current (4-20mA) output interface is as
shown in Fig. 2-14.
3
1
2
GND
1k
1k
J11/J12
AO1/AO2
Note: When short circuiting pin 1 and 2 of short circuit cap of J11/J12, AO1 outputs a
0-10v analog voltage signal to GND, when short circuiting pin 2 and 3, it outputs a 4-
20mA current signal, and jumper terminal corresponding to AO1 is J11, while jumper
terminal corresponding to AO2 is J12.
Fig. 2-14 A01/A02 Analog Output
2.14 Pulse Quantity Input Interface
There’re two driving modes for pulse quantity input interface, which are namely:
(1) Differential driving mode; (2) single ended driving mode. These are shown in
ig. 2-15 and Fig. 2-16 respectively.
Upper Computer Side Driver Internal Circuit
PULS+
DIR-
DIR+
PULS-
EZ-
EZ+
Fig. 2-15 Input Pulse Quantity Differential Driving Mode
This manual suits for next models
1
Table of contents
Popular Servo Drive manuals by other brands
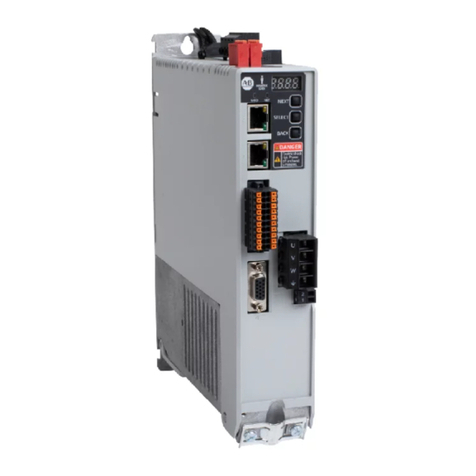
Rockwell Automation
Rockwell Automation Allen-Bradley Kinetix 350 installation instructions
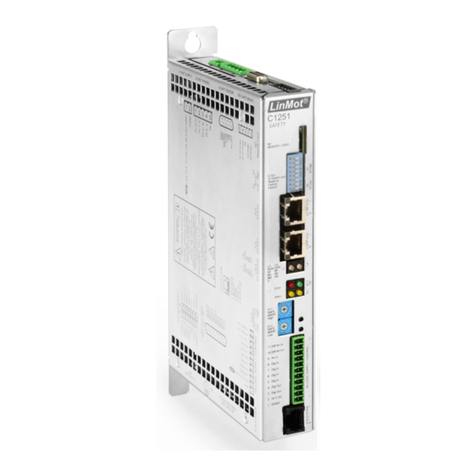
LinMot
LinMot C1251-MI-XC-2S-0E Series manual
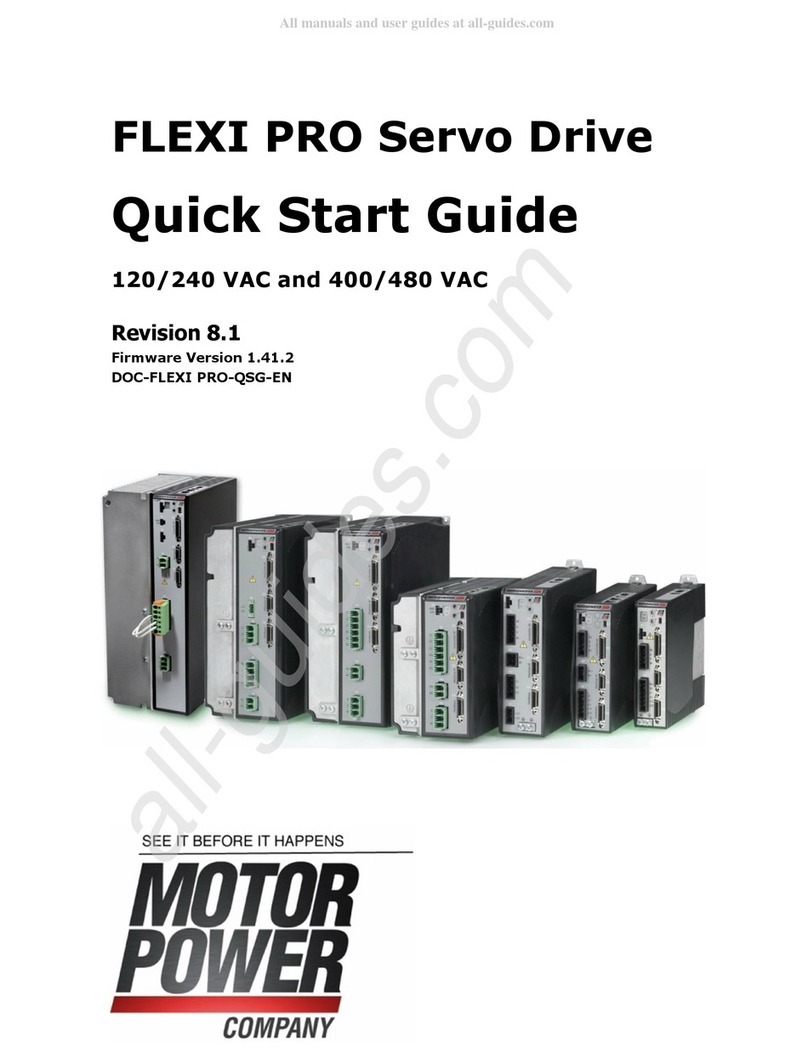
Motor Power Company
Motor Power Company FLEXI PRO Series quick start guide
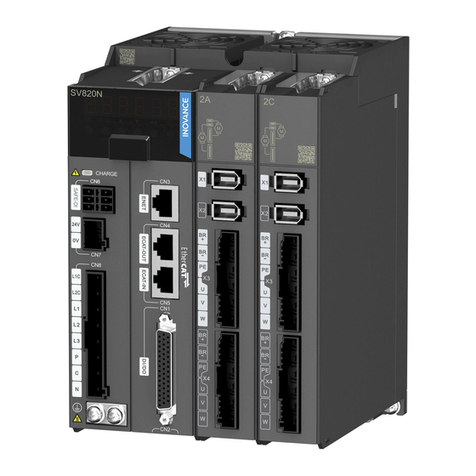
Inovance
Inovance SV820N Series manual
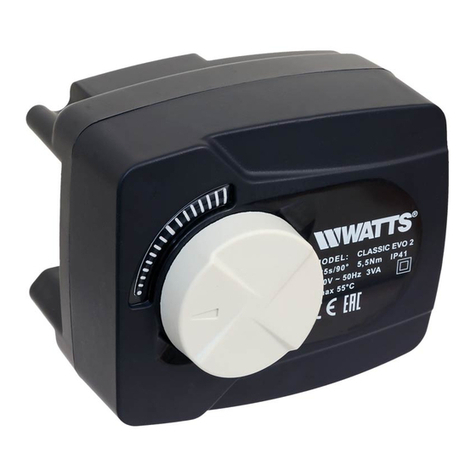
Watts
Watts CLASSIC EVO2-WK installation manual

Hiwin
Hiwin E Series user manual