Electronic Research Group EC130 User manual

Electronics Research, Inc. • 7777 Gardner Road • Chandler, IN 47610-9219 • USA
+1 812 925-6000 (tel) • +1 812 925-4030 (fax)
Your Single Source for Broadcast Solutions™ • Call Toll-free at 877 ERI-LINE • Visit Online at www.eriinc.com
Technical Manual
for
ERI Model EC130
RF Dual Switch Controller
TM_EC130
June 30, 2022

Page 2 of 28
Technical Manual for ERI Model EC130 RF
Switch Controller
Part Number: TM_EC130_RF_Switch_Controller
Copyright 2022 by Electronics Research, Inc. Chandler, Indiana, USA
No part of this publication may be reproduced, stored in a retrieval system, or
transmitted, in any form or by any means - electronic, mechanical, recording, or
otherwise - without the prior written permission of Electronics Research, Inc.
Many of the designations used by manufacturers and sellers to distinguish their
products are claimed as trademarks. Where these designations appear in this
instruction book, and Electronics Research, Inc., Inc. was aware of the trademark claim,
the designations have been marked with the © symbol.
While every precaution has been taken in the preparation of this instruction book,
Electronics Research, Inc. assumes no responsibility for errors or omissions, or for
damages resulting from the use of the information contained herein.

Technical Manual for ERI Model EC130 RF Switch Controller TM_EC130
Page 3 of 28
Table of Contents
Technical Manual for ERI Model EC130 RF Switch Controller..................................2
Preface...........................................................................................................................5
Returns and Exchanges...............................................................................................5
Unpacking....................................................................................................................5
Technical Assistance....................................................................................................5
Purpose of this Manual.................................................................................................5
Warning Regarding Personnel Risks ...........................................................................6
First-Aid........................................................................................................................6
General Information......................................................................................................8
Switch Controller Description.......................................................................................8
RF Switch Requirements..............................................................................................9
Specifications...........................................................................................................9
Installation ...................................................................................................................10
READ BEFORE APPLYING POWER........................................................................10
AC Power...................................................................................................................10
Switch Control Cable (SWA or SWB).........................................................................10
Preparing a switch to be used with the EC130.......................................................10
Wiring the Transmitter Interlock Circuit ......................................................................11
Wiring the SNMP Remote Control Interface...............................................................11
Wiring the RF Power Detection Interface...................................................................11
Operation.....................................................................................................................13
Front Panel Operation................................................................................................13
Menu Navigation....................................................................................................13
SNMP Network Configuration Setup..........................................................................17
Troubleshooting .........................................................................................................20
Transmitter Interlock and Switch Motor Drive Control................................................21
Remote Control..........................................................................................................23
Bypass Switch Controller ...........................................................................................23
EC130 Accessories.....................................................................................................24
Parts List and Drawings .............................................................................................25
Figures
Figure 1 Switch Controller Front Panel............................................................................8
Figure 2 Switch Controller Rear Panel............................................................................8
Figure 3 RF Switch Control Cable Wiring......................................................................10
Figure 4: Switch Port Diagram (Shown in position 2)....................................................12
Figure 5: Power Meter Pinout Connection.....................................................................12
Figure 6: Power Sample Placement Best Practice........................................................12

Technical Manual for ERI Model EC130 RF Switch Controller TM_EC130
Page 4 of 28
Figure 7: Main Menu .....................................................................................................13
Figure 8: Confirm Menu.................................................................................................14
Figure 9: Power Meter Menu.........................................................................................14
Figure 10: Power Meter Offset Menu ............................................................................15
Figure 11: Power Meter Offset Menu Example .............................................................15
Figure 12: Power Meter Menu Example........................................................................16
Figure 13: Power Meter Trip Menu................................................................................16
Figure 14: SNMP Configuration Utility Main Interface...................................................18
Figure 15: Set Communication Default Network Parameters........................................18
Figure 16: Switch Controller Interlock Circuit ................................................................21
Figure 17: Alternative Wiring Diagram Interlock Circuit.................................................22
Figure 18: Drawing........................................................................................................26
Figure 19: EC130 Schematic ........................................................................................27
Figure 20: EC130-PC1 Interface Board Schematic.......................................................28
Tables
Table 1: SNMP Read Table ..........................................................................................19
Table 2: SNMP Write Table...........................................................................................20
Table 3: Interlock Bypass Logic Table...........................................................................23
Table 4: Parts List .........................................................................................................25

Technical Manual for ERI Model EC130 RF Switch Controller TM_EC130
Page 5 of 28
Preface
Returns and Exchanges
Damaged or undamaged equipment should not be returned unless written approval and
return authorization has been received from Electronics Research, Inc. Special shipping
instructions and coding will be provided in said return authorization to assure proper
handling. Complete details regarding circumstances and reasons for return should be
included in the return request. Custom equipment or special order equipment is not
returnable. In those instances where return or exchange of equipment is at the request
of the customer, or of convenience to the customer, a restocking fee will be assessed.
All returns will be sent freight prepaid and properly insured by the customer. When
corresponding with Electronics Research, Inc., always specify the order number or
invoice number to which the shipment applies.
Unpacking
Carefully unpack the equipment and perform a visual inspection to determine if any
damage occurred during transit. Retain the shipping materials until it has been
determined that all received equipment is undamaged. The carrier may inspect the
packing material as part of the claim process. Retain and use the packing lists to help
locate and identify any and all components and assemblies that are removed for
shipping purposes and must be reinstalled upon receipt of the unit. Any shipping
supports and/or packing materials should be removed.
Technical Assistance
Electronics Research, Inc. technical support can be reached during normal business
hours (7:30 AM –4:00 PM US Central Time) via telephone at +1 (812) 925-6000 or FAX
at +1 (812) 925-4030. You may address correspondence to:
Technical Support
Electronics Research, Inc.
7777 Gardner Road
Chandler, Indiana 47610 USA
Purpose of this Manual
This manual is intended as a general guide for trained and qualified personnel who are
aware of the dangers inherent in handling potentially hazardous electrical/electronic
circuits. It is not intended to contain a complete statement of all safety precautions that
should be observed by personnel in using this or other electronic equipment.
The information provided in this manual, technical or otherwise, is not intended as a
design guide and should not be construed as such. This manual is not intended to
provide complete or exhaustive information regarding the general theory behind or the
operation of RF electronic equipment, electromagnetism, or any electronic component
or system that requires specialized instruction or education in order to thoroughly

Technical Manual for ERI Model EC130 RF Switch Controller TM_EC130
Page 6 of 28
understand its operation. In short, this manual is intended as a basic guide to the
operation of the components described herein for specifically trained and qualified
personnel only.
Warning Regarding Personnel Risks
The installation, operation, maintenance and service of this equipment involve risks both
to personnel and equipment, and must be performed only by qualified personnel
exercising due care. ERI, Inc. shall not be responsible for injury or damage resulting
from improper procedures or from the use of improperly trained or inexperienced
personnel performing such tasks.
During installation and operation of this equipment, local building and electrical codes
and fire protection standards must be observed. The following National Fire Protection
Association (NFPA) standards are recommended as reference:
1. Automatic Fire Detectors, No. 72E
2. Installation, Maintenance, and Use of Portable Fire Extinguishers, No. 10
3. Halogenated Fire Extinguishing Agent Systems, No. 12A
Do not remove, short-circuit, or tamper with interlock switches on access covers, doors,
enclosures, gates, panels or shields. Keep away from live circuits, know your equipment
and don't take chances.
First-Aid
Personnel engaged in the installation, operation, maintenance or servicing of this
equipment are urged to become familiar with first-aid theory and practices. The
following information is not intended to be complete first-aid procedures; it is a brief and
is only to be used as a reference. It is the duty of all personnel using the equipment to
Warning
THE CURRENTS AND VOLTAGES IN THIS EQUIPMENT ARE DANGEROUS.
PERSONNEL MUST AT ALL TIMES OBSERVE SAFETY WARNINGS,
INSTRUCTIONS AND REGULATIONS.
Warning
ALWAYS DISCONNECT POWER BEFORE OPENING COVERS, DOORS,
ENCLOSURES, GATES, PANELS OR SHIELDS. ALWAYS USE GROUNDING
STICKS AND SHORT OUT HIGH VOLTAGE POINTS BEFORE SERVICING. NEVER
MAKE INTERNAL ADJUSTMENTS, PERFORM MAINTENANCE OR SERVICE
WHEN ALONE OR WHEN FATIGUED.
Warning
IN CASE OF EMERGENCY ENSURE THAT POWER HAS BEEN DISCONNECTED.

Technical Manual for ERI Model EC130 RF Switch Controller TM_EC130
Page 7 of 28
be prepared to give adequate Emergency First Aid and thereby prevent avoidable loss
of life.
Treatment of Electrical Burns
1. Extensive burned and broken skin
•Cover area with cleanest available sheet or cloth.
•Do not break blister, remove tissue, remove adhered particles of clothing, or
apply any salve or ointment.
•Treat victim for shock as required.
•Arrange transportation to a hospital as quickly as possible.
•If arms or legs are affected keep them elevated.
Note: If medical help will not be available within an hour and the victim is conscious and
not vomiting, give him a weak solution of salt and soda: 1 level teaspoonful of salt and
1/2 level teaspoonful of baking soda to each quart of water (neither hot or cold). Allow
victim to sip slowly about 4 ounces (a half of glass) over a period of 15 minutes.
Discontinue fluid if vomiting occurs. Do not give alcohol.
2. Less severe burns - (1st & 2nd degree)
•Apply cold (not ice cold) compresses using the cleanest available cloth article.
•Do not break blisters, remove tissue, remove adhered particles of clothing, or
apply slave or ointment.
•Apply clean dry dressing if necessary.
•Treat victim for shock as required.
•Arrange transportation to a hospital as quickly as possible
•If arms or legs are affected keep them elevated.
Reference: [American Red Cross Standard First Aid and Personal Safety Manual
(Second Edition)

Technical Manual for ERI Model EC130 RF Switch Controller TM_EC130
Page 8 of 28
General Information
This document provides technical information pertaining to the installation and operation
of the Electronics Research Inc. motorized RF dual switch controller.
Switch Controller Description
The EC130 motorized RF switch controller is designed to operate a two industrial
standard motorized waveguide or coaxial RF switch. The controller is contained in a
5.23-inch standard 19-inch rack mountable chassis. The front panel, shown in figure 1
below, has a key-lock selector switch and a red/green LED that indicates the RF
switch’s interlock status. The controller display shows both switch positions and
provides buttons to initiate a state change. The controller rear panel, shown in figure 2,
provides the status and control connection to the RF switch, a transmitter control
interlock circuit and a remote status and control interface. The transmitter control
interlock circuit is used to insure that RF power is removed from the RF switch before
changing its position. It will also prevent RF power from being applied when the switch
is not locked in an operating position.
Figure 1 Switch Controller Front Panel
Figure 2 Switch Controller Rear Panel

Technical Manual for ERI Model EC130 RF Switch Controller TM_EC130
Page 9 of 28
RF Switch Requirements
The controller requires that the motorized RF switch DC voltage matches the controller
DC voltage (either 12V or 24V available) The switch must have two form A (Normally
Open Contact) limit switches in each of its two positions. It is expected that the RF
switch control system will have a three terminal interface such that the switch is driven
by briefly applying the control voltage to two of the three pins. One pair will drive the
switch to position 1 and the other to position 2. The common pin is shared between the
remaining two pins and is connected to the negative terminal of the switch controller’s
power supply. See the controller circuit diagram in the Parts and Drawings section of
this manual for more details.
Specifications
AC Input
Voltage
84 to 264 VAC
Frequency
47 to 63 Hz
Current
1.2 A (120 VAC)
0.8 A (240 VAC)
DC Control Power
Voltage
12 or 24 VDC
Max Current
1.0 A (12 VDC)
0.5 A (24 VDC)
Environmental
Operating Temperature
0 to 50 C
Storage Temperature
-20 to 70 C
Humidity
30% to 85% (non-condensing)

Technical Manual for ERI Model EC130 RF Switch Controller TM_EC130
Page 10 of 28
Installation
Installation consists of mounting the controller box in a rack panel, supplying AC power,
connecting the controller to the RF switch, wiring the transmitter interlock circuit and
optionally wiring the remote control interface. This section describes how to do this.
READ BEFORE APPLYING POWER
The EC130 is capable of 12Vdc or 24Vdc operation of two switches. It is not capable of
controlling both a 12Vdc and a 24Vdc switch simultaneously. VERIFY the control
voltage required by the switch intended to control and toggle the slide switch on the
back panel to the appropriate voltage before powering the switch controller. Failure to
do this first step may DAMAGE the switch circuitry.
AC Power
AC power is supplied to the controller by means of a standard computer power cord. A
six foot cord is supplied with the controller.
Switch Control Cable (SWA or SWB)
The RF switch control cable is a standard Cat-5 or Cat-6 ethernet cable.
Figure 3 RF Switch Control Cable Wiring
Preparing a switch to be used with the EC130
The EC130 is designed to work with ERI “C” model switches. The EC130 and a “C”
series switch is plug-n-play after verifying the control voltage.
If a switch is being used that is not an ERI “C” model, use the diagram above to connect
the appropriate wires to the RF switch’s limit contactors. The EC130 will provide +24
Vdc to the common pin 7. In order for the RF Switch Status Indicator to provide
feedback and allow switching, the COM pin of the limit switch (pin 7) must be connected
directly to pin 8 by means of a jumper wire at the switch. This allows a +24Vdc signal

Technical Manual for ERI Model EC130 RF Switch Controller TM_EC130
Page 11 of 28
to be read at the EC130 which indicates the switch is connected. This is already in
place if the EC200 Wiring harness is used with a “B”series ERI switch or an ERI “C”
series switch is used.
Wiring the Transmitter Interlock Circuit
The transmitter interlock circuit is used to turn the transmitter off before the RF switch is
driven and to keep the transmitter off until the switch is locked in a safe operating
position. This circuit is controlled by the PLC unit. See figure 15 &16 on pages 20 and
21 in the Operation section of this manual for a drawing of the actual circuit. This circuit
is terminated at terminals 1 and 2 connector labeled INTERLOCK on the rear panel of
the controller. This circuit should be connected to the appropriate control interface of the
transmitter that supplies the RF power that passes through the switch. The purpose of
this circuit is to insure that the transmitter is off or muted whenever the circuit is open.
The relays and switches in this passive circuit can handle 6 amps of either AC (up to
240 VAC) or DC (up to 28 VDC). A one second delay is programmed into the switching
logic to ensure the interlock is triggered prior to exercising the switch. A delay is also
programmed to close the interlock circuit one second after the switch has entered the
final position. To ensure the switch is in position, the switch position limit switches may
be wired in series with the switch controller Interlock connections. The limit switch
connections must be made at the switch. Refer to the switch manual to find the
appropriate connections.
Wiring the SNMP Remote Control Interface
The switch controller remote control interface is brought out through the rear panel via
an RJ45 Ethernet connector and can be connected to a switch or router to provide
remote access to the EC130 switch controller.
Wiring the RF Power Detection Interface
The RF power detection interface can be used with an ERI VDM303 Power Detector.
These power detectors are powered by a 24Vdc power supply, provided by the EC130
switch controller and provide a 4-20 mA signal. RF connections A1 and A2 should only
be place on ports 1 and 4, or 2 and 3 if both used. If a shorting cap is used on port 4, a
single power detector on port 1 is all that is needed. RF connections A1 and A2 will
only affect the operation of Switch A. Likewise, RF connections B1 and B2 will only
affect the operation of Switch B.

Technical Manual for ERI Model EC130 RF Switch Controller TM_EC130
Page 12 of 28
Figure 4: Switch Port Diagram (Shown in position 2)
Figure 5: Power Meter Pinout Connection
Figure 6: Power Sample Placement Best Practice

Technical Manual for ERI Model EC130 RF Switch Controller TM_EC130
Page 13 of 28
Operation
The operation of the EC130 switch controller is explained in this section.
Front Panel Operation
The front panel of the controller Menu Driven User Interface, a red/green LED and a 3-
position switch-lock.
The red/green LED shows the current status of the interlock. Green means the interlock
is active and the switches are in proper position and red shows that the interlock has
been interrupted because the switches are out of position.
The 3-position selector switch-lock sets the operating mode of the controller. When the
switch-lock is in the Local position both Remote and EXT control of the RF switch is
disabled although the red/green LED and User Interface will continue to show the RF
switch’s current position and interlock status. When in the LOCAL position the RF
switch may only be controlled by means of the front panel control interface. When in the
REMOTE position the switch may only be controlled by means of the controller’s remote
control interface. The control interface can still be navigated while in the REMOTE or
EXT positions.
Menu Navigation
The “A” and “B” buttons are action buttons when needed on each screen. The “-“ and
“+” buttons are used to increment or decrement through menus. The “Cancel” and “OK”
buttons denoted by a circular backwards arrow and checkmark, respectively, are used
to cancel or accept new settings to the switch controller.
Figure 7: Main Menu

Technical Manual for ERI Model EC130 RF Switch Controller TM_EC130
Page 14 of 28
The main screen shows the status for each switch. If a switch is not detected, and N/C
(not connected) status will show in lieu of a switch position.
Figure 8: Confirm Menu
Pressing the “A” action button while on the main screen when Switch A is connected will
initiate a switch change. The “OK” button needs to be selected within 10 seconds to
confirm the position change. If the switch is not connected, the action button will have
no effect. The “B” action button presents a similar dialog for a switch connected to the
switch B port.
Figure 9: Power Meter Menu
Pressing the “+” menu button will advance to the Power Meter screen. Power meters
A1 and A2 should be connected to opposing ports of switch A while power meters B1
and B2 should be connected to opposing ports of switch B. The power meters watch for
any power present on the switch and prohibit switching if the power is greater than 5 dB
from the noise floor. The power meters should be placed on voltage probes or forward
ports of directional couplers.

Technical Manual for ERI Model EC130 RF Switch Controller TM_EC130
Page 15 of 28
Figure 10: Power Meter Offset Menu
Pressing the “+” menu advance button again brings you to the offset menus for the
power meters. If desired, the coupling value of the directional coupler or voltage probe
can be added here to display a more accurate reading of power on the previous screen.
Each sensor has it’s own offset value. Pressing the “A” action button will increase the
offset value while pressing the “B” action button will decrease the offset value. These
values are read in dBm. The values are divided by 100 in order to get the actual dBm
readings.
Figure 11: Power Meter Offset Menu Example
The offset value shown in this image is equal to 20 dBm.
Changing these values has no bearing on whether power is present for switch control.
Pressing the “-“ menu button will return to the previous menu.

Technical Manual for ERI Model EC130 RF Switch Controller TM_EC130
Page 16 of 28
Figure 12: Power Meter Menu Example
By changing the offset value, sensor A1 now has a 20 dBm higher noise floor. To
convert dBm to Watts, use the equation:
Figure 13: Power Meter Trip Menu
AFTER the OFFSET is adjusted, the TRIP level must also be adjusted. Notice the
output reading of the sensor on Menu 2 and adjust the trip level to be 5 dB (500) greater
than the expected OFF level. The EC130 will use this value to determine if the system
is safe for switching. If the level is set too low, the controller will not activate the
switches, but if it is set too high the controller could switch under power. The EC130 will
only activate a switch if the Interlock output is disengaged AND the power is below the
selected threshold. There is a 1 second delay to allow the sensor reading to settle.
Each power sensor has a menu for OFFSET and TRIP level.
If no sensors are being used, leave both OFFSET and TRIP set to 0. In this mode of
operation, only the Interlock status will verified before switching. The “cancel” button
will reset each of these menus to 0.

Technical Manual for ERI Model EC130 RF Switch Controller TM_EC130
Page 17 of 28
SNMP Network Configuration Setup
The EC130 Dual switch controller has SNMP monitoring and control capabilities. An
ADFWeb HD67164-232-485-B2 Modbus to SNMP converter is used to accomplish the
control capabilities. To configure the SNMP connection, download the Windows based
configuration software, SW67164, from ADFWeb at:
https://www.adfweb.com/home/download/download.asp#HD67164
Download the ERI EC130 Configuration file at:
https://eriinc.com/product/ec-series-motorized-switch-controllers/
Unzip the EC130 configuration file to the installation path. The default path is:
C:\Program Files (x86)\ADFweb\Compositor_SW67164\Projects
After running the configuration software, load the ERI Configuration file (Step 1).
Set the communication parameters (Step2) for the SNMP network for which the switch
controller is to be connected. The IP address, Subnet Mask, and Gateway should be
configured for the network it is attached. This menu also has the SNMP parameters. By
default, SNMP Protocol 2 is activated. SNMP Protocol 3 is also available and has
additional security options that need to be configured here if it is to be used.
The “Set Access” menu (Step 3) are preconfigured to communicate with the PLC
through the Modbus 485 Protocol. This menu should be left alone.
The “Set SNMP Access” menu (Step 4) is preconfigured with the addresses that will be
accessible to the SNMP master. If it is desired to change the descriptions of the
information on the network, it should be done here. Do not change the Bit
assignments. The Read Community are set to public by default in step 4 and the
Write Community is set to private and can be changed to increase security. These
community names will be needed when addressing the EC130 with the SNMP
manager. The community names function as a password to the data stream. Assign an
appropriate IP address to where the SNMP traps should be sent.
Save the SNMP MIB (Step 5) for use in the SNMP Manager and use a computer that is
connected to the SNMP controller to update the firmware (Step 6).Flash the firmware
in a short time after applying power to the EC130. If the power has been applied for
some time, you may need to unplug the unit and plug it back in before being able to
flash the new firmware.

Technical Manual for ERI Model EC130 RF Switch Controller TM_EC130
Page 18 of 28
Figure 14: SNMP Configuration Utility Main Interface
Figure 15: Set Communication Default Network Parameters
More detailed information on configuring the SNMP controller can be found at:
http://www.adfweb.com/download/filefold/MN67164_ENG.pdf

Technical Manual for ERI Model EC130 RF Switch Controller TM_EC130
Page 19 of 28
SNMP Default settings
IP Adress: 192.168.2.205
Subnet Mask: 255.255.255.0
Gateway: 192.168.2.1
Version 2
READ Community public
WRITE Community private
Modbus (Do not modify)
Serial: RS485
Baudrate: 9600
Parity: Even
Timeout: 1000 ms
Communication idle time: 100 ms
Table 1: SNMP Read Table
Variable
Description
Output Value
Trap
interlockStatus
Interlock
0 = Off Air 1 =
Normal
Yes, on Event
swApos1
Switch A in Position
1
0 = No 1 = Yes
Yes, on Event
swApos2
Switch A in Position
2
0 = No 1 = Yes
Yes, on Event
swBpos1
Switch B in Position
1
0 = No 1 = Yes
Yes, on Event
swBpos2
Switch B in Position
2
0 = No 1 = Yes
Yes, on Event
swAconnect
Switch A is
connected
0 = No 1 = Yes
Yes, on Event
swBconnect
Switch B is
connected
0 = No 1 = Yes
Yes, on Event
rfA1
A1 Power Sensor
Reading
Signed Integer,
dBm/100
Yes, 500 ms
Interval
rfA2
A2 Power Sensor
Reading
Signed Integer,
dBm/100
Yes, 500 ms
Interval
rfB1
B1 Power Sensor
Reading
Signed Integer,
dBm/100
Yes, 500 ms
Interval
rfB2
B2 Power Sensor
Reading
Signed Integer,
dBm/100
Yes, 500 ms
Interval
local
Local control
0 = No 1 = Yes
Yes, on Event
snmpRemote
SNMP Remote
Control
0 = No 1 = Yes
Yes, on Event
extRemote
EXT triggered
control
0 = No 1 = Yes
Yes, on Event

Technical Manual for ERI Model EC130 RF Switch Controller TM_EC130
Page 20 of 28
Table 2: SNMP Write Table
Variable
Description
Write Value
togSwitch
Toggle Switch A or B
Momentary, <= 1s*
0x01 = Request Switch A to change
positions
0x02 = Request Switch A to change
positions
0x03 = Request BOTH Switch A and
Switch B to change positions **
0x04 = RESET Request bits
*Application note: Set up the SNMP command from the manager as follows.
Toggle Switch A
SET togSwitch 0x01 //Request State change on Switch A
DELAY 1s
SET togSwitch 0x04 //RESET Request bits
**Expected behavior of a dual switch command
If a 0x03 command is SET to initiate a state change on both Switch A and Switch B, the
controller will still restrict movement if power is present on A1 or A2 for Switch A, or B1
or B2 for Switch B. Therefore it is possible for Switch A to switch while Switch B does
not or for Switch B to switch while Switch A does not.
Sequential switching may be accomplished by triggering Switch A (0x01 followed by
0x04), checking for a position change on Switch A, and then initiating Switch B (0x02
followed by 0x04).
Troubleshooting
The SNMP controller responds to a PING, but cannot be programmed.
1) Remove power from the EC130 Switch Controller
2) Try reapplying power and programming. If this fails, move on to step 3.
3) Remove the top cover of the EC130 Switch Controller
4) The ADFWeb Modbus to SNMP converter is the white box located near the
center of the enclosure.
5) Release the rail securing the converter to the enclosure for easier access.
6) There are two DIP switches facing towards the front of the EC130 Switch
Controller, located on the same side as the Modbus 485 connections
a. Flip the 1st DIP switch into the OFF (UP) Position.
b. Reapply power
c. Use the default IP address to find the controller: 192.168.2.205
d. Reprogram and wait for “OK” signal
e. Remove power from the EC130 Switch Controller
f. When programming is complete, Flip the 1st DIP switch into the ON
(DOWN) position.
7) Replace mounting hardware for the SNMP converter
8) Replace enclosure lid
Table of contents
Popular Controllers manuals by other brands
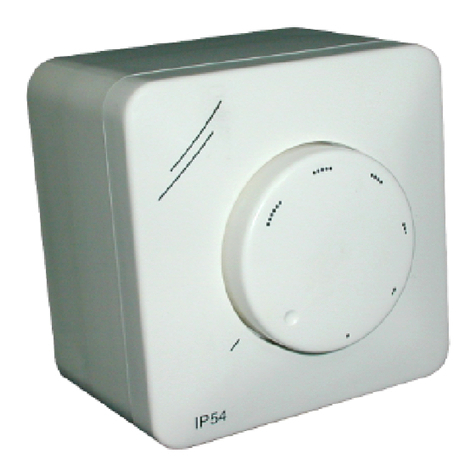
Axio
Axio AX-FC-MTY Series quick start guide
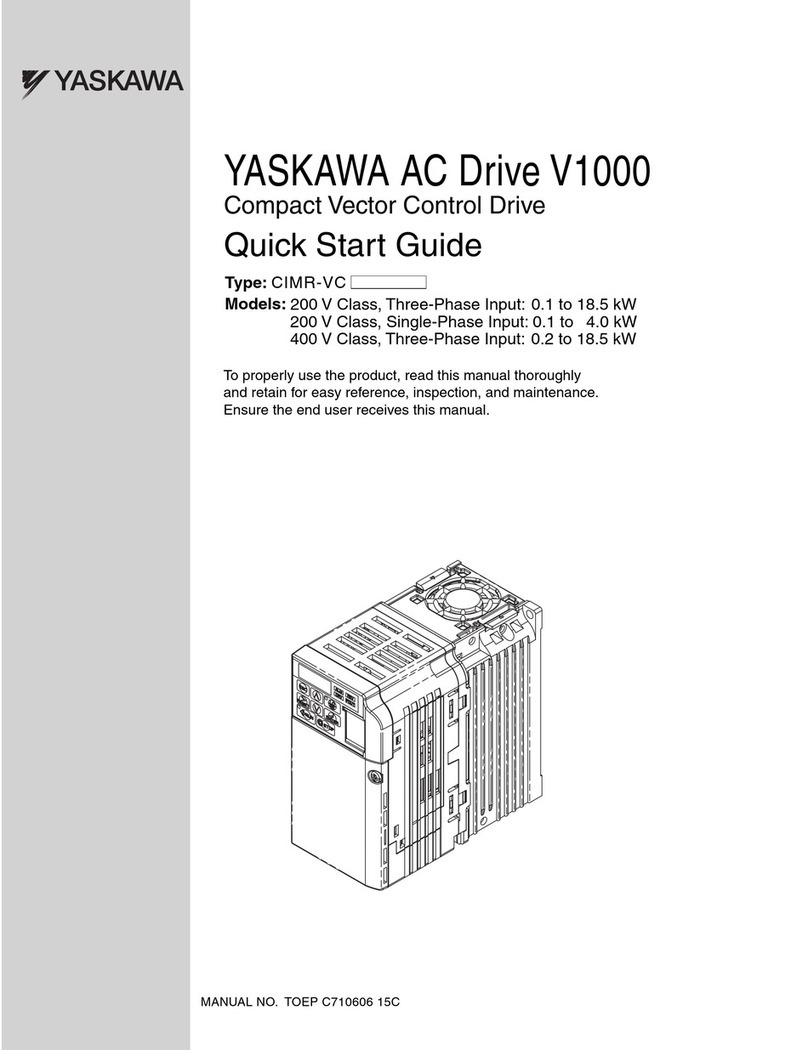
YASKAWA
YASKAWA CIMR-VC series quick start guide
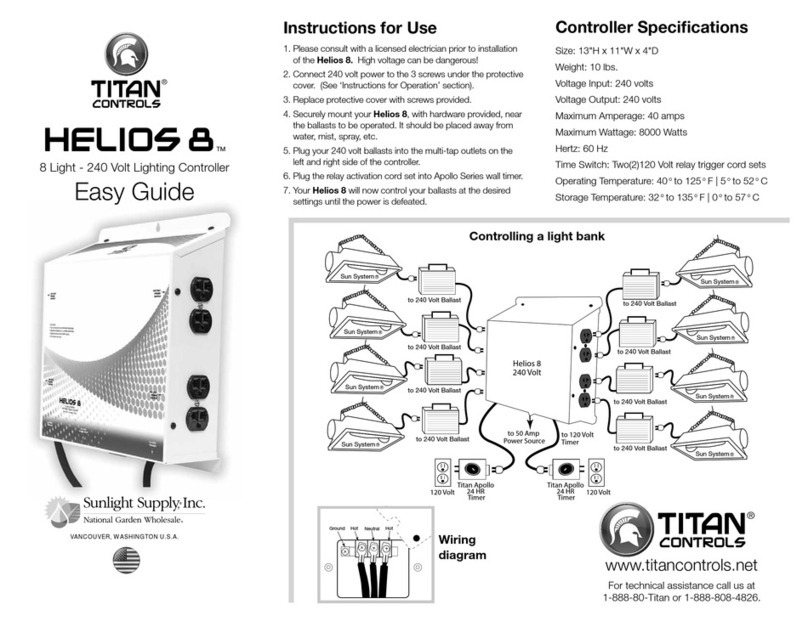
Sunlight Supply
Sunlight Supply TITAN CONTROLS HELIOS 8 Easy guide
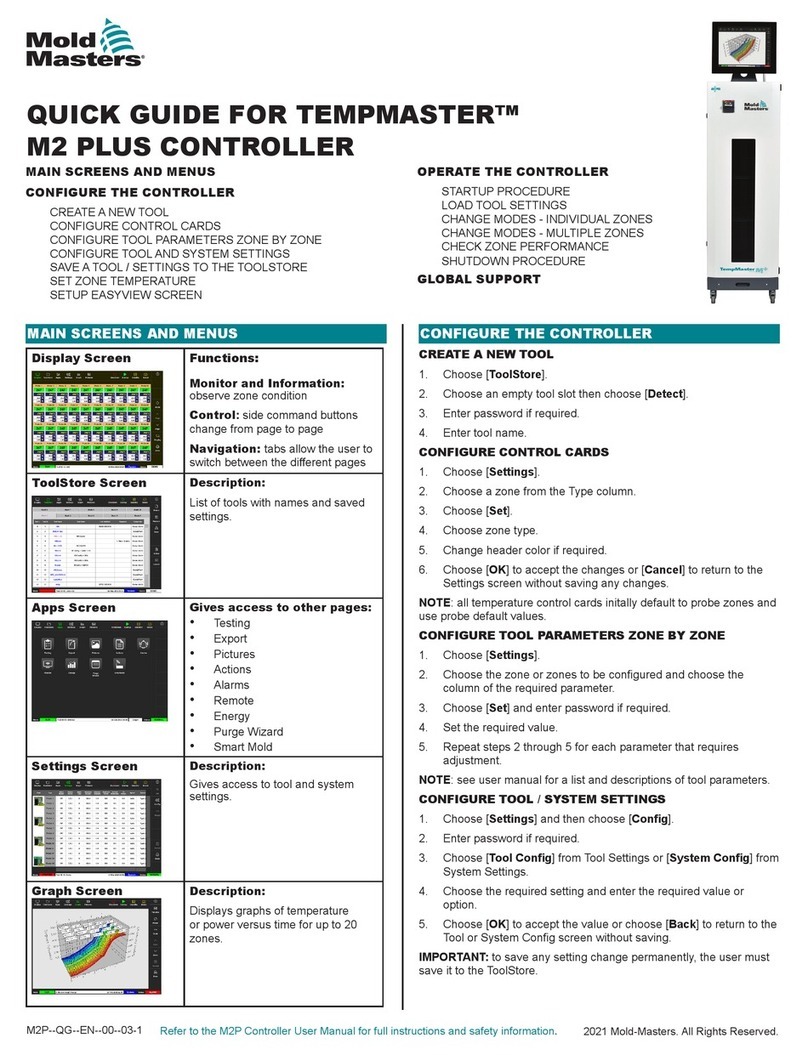
Mold-Masters
Mold-Masters TempMaster M2 Plus Series quick guide
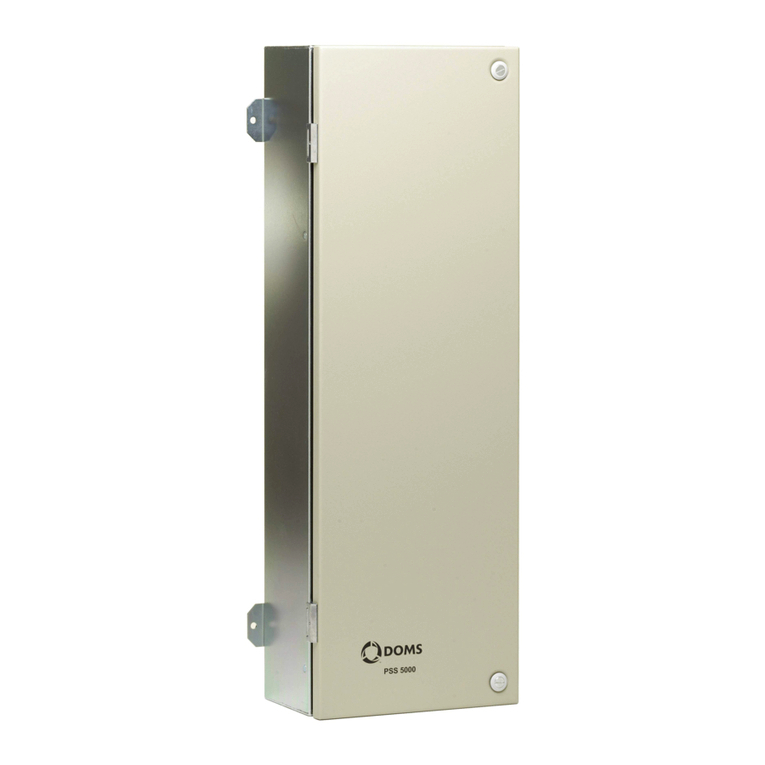
Doms
Doms PSS 5000 installation guide
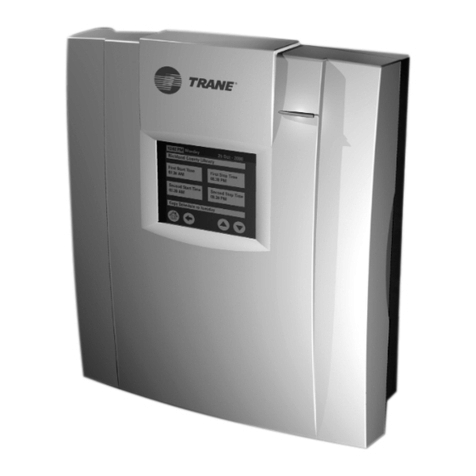
Trane
Trane Tracer MP581 installation instructions