EMF Motor SQML Series User manual

Operating Instructions
SQML
Gearless Lift Motor
www.emfmotor.com
ver.2015.0.0

1 www.emfmotor.com
CONTENTS
1- ABOUT SQML LIFT MOTORS 02
2-GENERAL INFORMATION 03
2.1 Technical Support 03
2.2 General 03
3- SAFETY 04
3.1 General Remarks 04
3.2 General Warnings 04
3.3 User Responsibilities 05
3.4 Safety Instructions 05
4-STORAGE and TRANSPORT 07
4.1 Storage 07
4.2 Transport 07
5- TECHNICAL INFORMATION 08
5.1 EMF SQM100 Series 08
5.2 EMF SQM132 Series 08
5.3 EMF SQM160 Series 09
5.4 EMF SQM200 Series 09
5.5 Power Box Connection 10
5.6 Protection Class 11
5.7 Motor Plate Data 11
6- INSTALLATION 12
6.1 General 12
6.2 Recommendations for Installation 12
6.3 Mounting of the Motor 14
6.4 Mounting of Rope Protection Clamps 14
6.5 Encoder Connection 15
7- COMMISSIONING 16
7.1 Power Connection 16
7.2 Before Initial Start-up 18
7.3 Encoder Connection 18
7.4 Encoder Replacement 19
7.5 Mechanical Brake 21
7.6 Brake Test Procedure according to EN81-1 22
7.7 Brake Micro switch Test 23
7.8 Half-Load Test 23
7.9 Emergency Rescue 23
7.10 Safety Contactor Circuit (Braking circuit) 24
8-SERVICE, MAINTENANCE and TROUBLESHOOTING 25
8.1 Points to Take into Consideration During Service and Maintenance 25
8.2 Spare Parts 26
8.3 Maintenance Intervals 26
8.4 Problems, Causes and Solutions 27
8.5 Certifications 28

2 www.emfmotor.com
1- ABOUT SQML LIFT MOTORS
SQML lift motors are designed for rope lifts used without reducers.
This machine consists of a torque motor with permanent magnets, a brake system, a
sheave and feedback equipment.
Thanks to LiProKa principle, EMF lift motors have a precision control, a low noise level,
a high travelling comfort and a very compact design.
EMF Motors are manufactured by our ISO 9001 certified company, using materials
conforming TSE and DIN standards.
Thanks to the certified brake system, the cabin security level is high.
The technical data on the motor plate indicates the limits specified for the correct
operation of the motor.
The life of the SQML motor is 20000 hours.
EMF reserves the right to make modification on any part of the motor in order to enhance
safety and performance.
All product names and trademarks in this document are registered.

3 www.emfmotor.com
2-GENERAL INFORMATION
2.1 Technical Support
You can contact us about any matter.
EMF
MO
T
OR
Address
Ramazanoğlu Mah. Sanayi Cad. No: 9 TR34906 Pendik / İSTANBUL /TÜRKİYE
T
el
+90 216 595 19 00
Fax
+90 216 595 19 01
E-mail
W
ebsit
e
www.emfmotor.com
2.2 General
This manual is prepared for the qualified personnel who plan, install, commission and
service the lift system. This user manual contains important rules concerning personnel
safety as well as security. Please read all the general safety warnings carefully and keep
this user manual at a safe and easily accessible place for future reference.
The user is responsible for ensuring that the manual has been read and well understood
by the employees in order to prevent any injury or damage and to ensure the safe
operation of the motor.
EMF Motor San. ve Tic. A.Ş. shall not be liable for any damage or disruption caused by
disregard of this manual.
The information in the manual can not be used or reproduced by third parties without
permission. The copyright of the operation instructions of SQML lift motor belongs to
EMF Motor San. ve Tic. A.Ş.

4 www.emfmotor.com
3- SAFETY
3.1 General Remarks
This manual contains important warnings concerning product safety as well as your own
safety. Please read the ‘General Safety Warnings’ for the necessary safety precautions.
Keep this manual at a safe place for easy access.
WARNING!
‘Warning’ sign; motor can be damaged if necessary precautions are not
taken.
CAUTION!
‘Caution’ sign; you may suffer physical injuries if necessary precautions
are not taken.
MECHANICAL HAZARD!
‘Mechanical Hazard’ signs; work accidents may occur if ignored.
RISK OF ELECTRIC SHOCK!
‘Risk of electric shock’ sign; work accidents may occur if ignored.
MAGNETIC FIELD WARNING
‘Magnetic field warning’ sign; high magnetic field effect may arise if
ignored.
INFORMATION
‘Information’ signs contain recommendations for the user.
HIGH TEMPERATURE
‘High temperature’ sign; burn hazard due to temperature on motor
surface.
3.2 General Warnings
EMF motors can only be ready for use after being mounted on the platform where they
will be used and the necessary safety precautions are taken. Installation, maintenance,
and electrical connections can be made only by qualified personnel.

5 www.emfmotor.com
INFORMATION
Read the operating instructions before the commissioning.
Safe, correct and proper installation of the motor is the responsibility of the lift company.
Do not forget that the motors cause mechanical movement.
All the parts and installations of the lift must be designed, manufactured and installed in
accordance with applicable norms and regulations for the reliable and safe operation of
the motors.
3.3 User Responsibilities
Mechanical and electrical issues, which have to be taken into consideration regarding
commissioning, operating, maintenance and failures, are explained in the related sections
of the manual.
MECHANICAL HAZARD!
Do not forget that the motors cause mechanical movements! The rotating
parts of the motor (e.g. rope and sheave) need to be enclosed as required
to prevent possible accidents.
CAUTION!
Unconscious use of EMF motors can pose a danger for people and
equipment. Installation, commissioning, maintenance and repairs should
be done only by trained personnel.
3.4 Safety Instructions
No modifications that can alter the operation characteristics can be made on the general
structure of the motor or on the brake. Tampering with the red sealed screws on the motor
will void the guarantee. Such tampering can also hazardous conditions with respect to
safety. No welding process shall be carried out on the motor, nor the motor shall be used
as an grounding point for a welding process. This may damage the bearings and magnets
of the motor. The motors must be kept free from excessive pollution and mechanical
strain.
WARNING!
Do not use a damaged motor.
If you receive a damaged motor, please contact the transport company.

6 www.emfmotor.com
Excessive pollution, dust, chips, oil, water and similar liquids can cause negative effects
on the motor and the brake assembly. Therefore, the motors must be cleaned regularly,
and the surface of the motor must be protected against such effects.
The motor must not be connected directly to the main power grid without a driver! The
motor must be connected to a suitable driver, and it shall never be operated without
taking all safety precautions and making the necessary driver adjustments. All the metal
parts of lift installations must be grounded. The grounding connection must be connected
to the motor driver. The grounding line must absolutely be separate from the neutral line.
The length of the motor cable shall not exceed 25 m.
CAUTION!
Driver (inverter) settings and identification of encoder angle must be
carried out separately for each motor. Otherwise, dangerous and
uncontrolled accelerations may occur.
According to the national and international color code directives, the NEUTRAL line
must be blue and the GROUND line must be green-yellow.
There is a risk of electric shock in cases of short circuits in the stator. The electrical
system connected to the motor must be de-energized carrying out any work on the motor.
If there is a damage to the motor cables, the cables must not be touched until the power
is cut off. The cables can only be changed after power is cut off.
Touching the body of the motor before it cools can cause burns. In case of extreme
heating (100 °C) or abnormal noise during motor operation, deactivate the motor
immediately. Check the possible motor failures section and contact with the
manufacturer if necessary.
The surfaces of the motor must be kept clean. Insufficient heat transmission on motor
surfaces may reduce the life of the motor. The motors can be damaged if necessary
precautions are not taken. The motor heat sensor must absolutely be connected to the
necessary protective circuit.
MAGNETIC FIELD WARNING
Strong Magnetic Field!
The distance between the motor and persons who have cardiac
pacemakers must be at least 0,5 m.

7 www.emfmotor.com
Do not ignore the attractive force of the magnetic field and do not approach the motors
with tools or devices that might be affected by the magnetic field (watches, digital
devices, iron or steel tools).
4- STORAGE and TRANSPORT
WARNING!
If any damage is observed on the motor, do not start the motor. Check the
packing of the motor, and if you see any damage that might have occurred
during transport, report the situation to the transport company. Shipping
damages are not covered by our guarantee! Avoid excessive loads and
vibrations.
4.1 Storage
Please pay attention to the storage warnings on the packaging. The storage areas must
be moisture-free and thermally balanced. The storage must be away from chemical
reactions. The motor must be kept in its original packaging and away from moisture to
prevent rust until the installation.
The storage time should not be too long (Maximum 1 year is recommended). The brakes
must be released and the shaft must be manually rotated before the installation.
4.2 Transport
Do not store or transport the SQML motor which is removed from its packaging.
Damaged packaging must be replaced immediately. If the motors aren’t packed properly,
then they won’t be protected against sudden impacts. Dangerous and sudden actions can
cause accidents.
Use safety shoes and gloves during transportation. Maximum weight that the personnel
can carry must be considered. The motor and the equipments may be heavier than 13 kg.
Please use only lifting equipment with sufficient capacity during loading, unloading and
transport.
When you are lifting with the workshop hoist, only use the lifting eyelets on the block.
Please pay attention not to damage the motor with ropes and chains during loading,
unloading and transport, especially the brake and the encoder assembly must be
protected against sudden impacts.

8 www.emfmotor.com
5- TECHNICAL INFORMATION
5.1 EMF SQML100 Series
For motor dimensions, please see Annex-A
For actual motor dimensions, please visit www.emfmotor.com.
5.2 EMF SQML132 Series
For motor dimensions, please see Annex-A
For actual motor dimensions, please visit www.emfmotor.com.

9 www.emfmotor.com
5.3 EMF SQML160 Series
For motor dimensions, please see Annex-A
For actual motor dimensions, please visit www.emfmotor.com.
5.4 EMF SQML200 Series
For motor dimensions, please see Annex-A
For actual motor dimensions, please visit www.emfmotor.com.

10 www.emfmotor.com
5.5 Power Box Connection
Drw-1
See 7.1 Power Connection

11 www.emfmotor.com
5.6 Protection Class
Motor IP54
Encoder (mounted) IP64
Brake (electrical) IP54
Brake (mechanical) IP10
Brake (micro switch) IP67
5.7 Motor Plate Data
Drw-2

12 www.emfmotor.com
Drw-3
6- INSTALLATION
6-1 General
Contractor Company is responsible for all electrical connections, installation and
commissioning of the motor. These operations must be carried out by trained personnel.
Please contact EMF if you have any problems related with the motor.
WARNING!
Interventions on the lift motor and equipment will void the guarantee.
Before commencing the installation, the motor must be checked against transport
damages.
The ambient temperature of the motor must be 0 °C - +40 °C, excessive humidity or
water may cause motor failures.
The mechanical patented brake of the motor is TÜV (ABV 766 / 2) certified and its
settings must be made at our factory. The customer shall not make any further
adjustments.
CAUTION!
In case of any interventions on the setting screws on the brake, the brake
may malfunction and cause safety problems. Any intervention on the
motor brake will void the guarantee.
6.2 Recommendations for Installation
Motor and driver unit must be installed inside an appropriate structure or enclosed lift
cabin, and they shall be positioned so as to prevent excessive dust, liquids (water, oil,
etc) and foreign substances on the motor (See Chapter5.6).There must be sufficient space
around the motor for air circulation. The distance between the motor and the wall must
be 150 mm at least in order to access the encoder in case of need.
No welding process shall be carried out on the motor, nor the motor shall be used as an
grounding point for a welding process. This may damage the bearings and magnets of
the motor.

13 www.emfmotor.com
WARNING!
The terminal box cover must be kept closed during the installation of the
motor, because foreign objects could get in if the cover is open.
Suitable lifting equipment should be used when installing the motor. During the
installation, lever, hammer and similar tools should not be used. Especially the encoder
of the motor should not be subjected to impacts, because it has a sensitive electronic and
mechanical structure. Also the motor shaft should not be subjected to sudden impacts.
The motor can be connected horizontally or laterally. In case of lateral connection, the
bottom part of the motor must be supported and fixing bolts must not be exposed to the
shear force.
Drw-4
If the sheave has more rope channels than the actual number of ropes, the ropes must be
in the middle canals of the sheave or the channels closest to the motor shall be used.
The electrical connection must be made according to the connection diagram (see
Chapter 7.1). Motor supply and brake electrical cables must be laid inside a cable duct,
and the encoder cable must be laid inside a separate cable duct. In order to prevent
interference in encoder, it should not be laid side by side with the supply cables.
RISK OF ELECTRIC SHOCK!
To prevent risk of fire or electric shocks, never expose the motor to rain
or splashing water. Do not touch the motor with wet hands. Before
carrying out any work on the motor, you must shut down the main supply
circuit breaker of the system. Never intervene the cables while the motor
and its driver are energized.

14 www.emfmotor.com
The supply cables to the motor must be grounded and shielded, the shielding and the
grounding connection must be connected to the grounding of the motor.
6.3 Mounting of the Motor
The motor must be fixed to the platform with 4 bolts. These bolts must be used with lock
washers.
Type SQML100… motors must be fixed to the working platform with 4 pcs M16 8.8
bolts. The tightening torque of the bolts is 210 Nm. The tightening depth of the fixing
bolts must be 36 mm at least and 57 mm at most.
Type SQML132… motors must be fixed to the working platform with 4 pcs M16 8.8
bolts. The tightening torque of the bolts is 210 Nm. The tightening depth of the fixing
bolts must be 36 mm at least and 57 mm at most.
Type SQML160… motors must be fixed to the working platform with 4 pcs M16 8.8
bolts. The tightening torque of the bolts is 210 Nm. The tightening depth of the fixing
bolts must be 36 mm at least and 57 mm at most.
Type SQML200… motors must be fixed to the working platform with 4 pcs M18 8.8
bolts. The tightening torque of the bolts is 290 Nm. The tightening depth of the fixing
bolts must be 36 mm at least and 57 mm at most.
The bolts must be tightened to the specified torques
with a torque wrench. The fixing platform of the
motor must be rigid and solid enough to withstand to
the created force. The unevenness of the mounting
surface shall not exceed 0,1 mm. Rubber cushions
must be used during installation in order to dampen
vibrations.
6.4 Mounting of Rope Protection Clamps
The sheave and diversion sheave are manufactured according to EN 81-1 standard. The
rope selection must also be done according to EN81-1 standard.
WARNING!
Ropes that are used with 210-240 mm sheaves must be manufacturer
certified.

15 www.emfmotor.com
The rope protection clamps prevent the ropes against slipping from the sheave. Rope
protection clamps must be dismounted before the assembly of the ropes. The distance
between the rope and the rope protection clamps must be adjusted to 2-3 mm and be
fixed.
6.5 Encoder Connection
The motor must be operated with encoder feedback. Never operate the motor with a
direct connection to the power grid!
The encoder behind the motor is supplied with a 5m signal cable. Encoder cable
terminations are given below. The encoder entry of the motor driver used must be made
as shown in the diagram and the shielding of the cable must be connected.
WARNING!
In order to provide for the proper operation of the electronic circuit, check
that the grounding of the motor and the driver complies with the appropriate
standard. The building must have a separate grounding line and this
grounding line must be connected to the system with a cable with correct
cross-section.
ECN413 (EnDat) Connection Diagram
Up: +5 VDC Supply

16 www.emfmotor.com
ERN487 (SinCos) Connection Diagram
Up: +5 VDC Supply
7- COMMISSIONING
Before commissioning, the installation of SQML lift motor must be completed with
attention to the conditions described in the previous sections.
The specifications of the driver used must comply with the values specified on motor
plate. Check the condition of the driver before connecting the power. In case of any
failure, the driver must not be installed.
Ambient Conditions:
• Motor and driver must be installed inside an appropriate structure or enclosed lift cabin.
• The installation must comply with the protection class. The motor must be protected
against falling of foreign materials (see Chapter 5-6).
• Do not operate the motor in explosive environments.
• The temperature must be between 0-40°C.
• Humidity ratio must not exceed 95% to prevent condensation.
• Altitude must not exceed 1000 m.
7.1 Power Connection
WARNING!
The motor must not be connected to the main grid without a driver! When
connecting to the motor driver, the U, V, W and motor grounding
connections must be made with a shielded cable of proper cross-section and
the shielding must be connected to the motor and driver.
The maximum cable length is 25 m, when used with a cable of proper cross-section.

17 www.emfmotor.com
The U, V and W motor supply cables must be connected in the same sequence at both
the motor and the driver side. Incorrect connection of the phases may lead to reverse
rotation or uncontrolled movement of the motor.
The driver must switch the motor contactors while the drive does not apply current, and
it must withdraw them before the motor is energized at restart. Otherwise, switching the
motor contactors while the motor is energized, especially at zero speed, can cause failure
of the driver and contactor.
According to customer’s request, the motors are equipped with a PTO thermostatic
switch (Klixon, 130 °C maximum electrical values 250VAC/2A/cos phi = 1). The
thermal protection device of the motor must be connected to the safety circuit and it must
stop the system in case the heat is above the limit level.
WARNING!
If the motor thermal protection is not connected to the safety system,
thermal protection will not be activated in case of overheating of the motor.
This situation can cause permanent damage on the motor.
The motor winding heat sensor and brake connections must be made according to the
diagram given below.
Drw-5

18 www.emfmotor.com
7.2 Before initial start-up
Before initial start-up, check the following.
• The mechanical installation and electrical connections must be properly completed.
• The brake supply circuit must be able to supply adequate voltage and current.
• The driver that feeds the motor must be able to supply adequate current and voltage,
and the driver must be connected according to warnings specified in the operation
instructions of the driver.
• The thermostatic switch of the motor must be connected correctly.
• Proper insulation and operating conditions must be provided.
•The motor must be mounted horizontally and according to the warnings specified in
the related section.
• The safety circuits must be in operating condition.
• All leftover installation materials and other foreign materials must be removed.
• The safety contactor must be connected.
• The rope protection clamps must be connected and operating.
• The cable inlets must be sealed.
• The weights must be calculated according to the load values on the motor plate.
• The operating conditions must be in accordance with the information on the motor
plate.
• In driver (inverter) settings, the encoder angle must be calculated by the driver, the
motor should not be started before completing this procedure.
As well as the controls specified, the other controls required by the operating conditions
must be carried out by authorized personnel.
WARNING!
Encoder offset must be done rotational and without load on sheave.
Otherwise motor can be damaged and warranty will be voided.
7.3 Encoder Connection
CAUTION!
Remember that the phase order is directly related with the encoder angle.
Any change in phase order will change encoder angle and this can cause
uncontrolled motor operation and very high speeds.
The connection to the driver must be made according to the color codes in Encoder
Connection diagram in Chapter 6.5. The shielding of the encoder cable must be

19 www.emfmotor.com
connected also to the driver side. A grounding fault in the system may harm the encoder
and the driver.
Before operating the motor, the encoder offset angle must be determined in compliance
with the procedures explained in the manual. The motor shall not be started before the
encoder angle is identified by the driver.
Since the angle identified by the driver and the actual encoder angle will change during
the mechanical disassembly/assembly process, the angle has to be identified again after
such disassembly/assembly process.
If the length of the supplied 5 m cable will not be sufficient and an extension cable will
be required, the cable joint must not be made by hand or with a simple electric terminal;
it must be made with suitable connectors or by soldering. The extension cable to be used
must have compatible properties and cross-section with the original cable of the encoder,
and the isolation at the joints must be proper. Grounding connection must be made.
7.4 Encoder Replacement:
The encoder must be replaced as explained below. Otherwise, a wrong connection can
cause vibration, unstable working, uncontrolled movements and encoder failure.
Drw-6
Dismounting Process:
This manual suits for next models
4
Table of contents
Popular Engine manuals by other brands
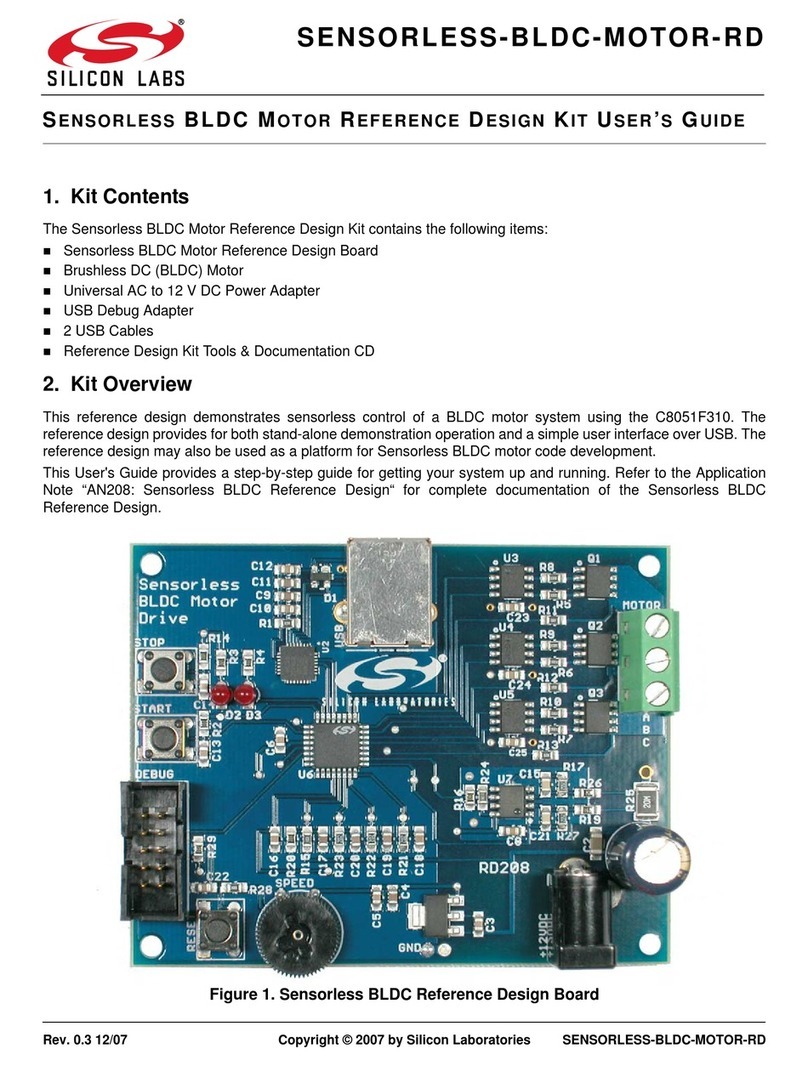
Silicon Laboratories
Silicon Laboratories SENSORLESS-BLDC-MOTOR-RD user guide
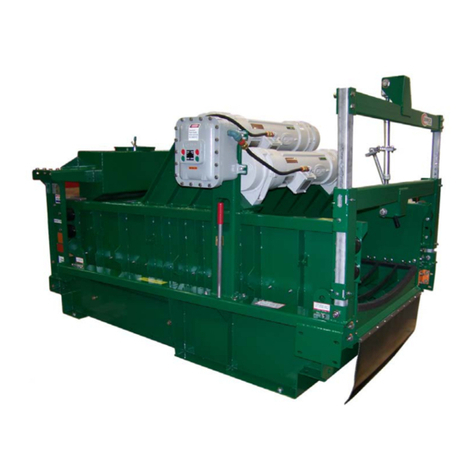
DERRICK
DERRICK HYPERPOOL SHAKER Maintenance & Operation Manual
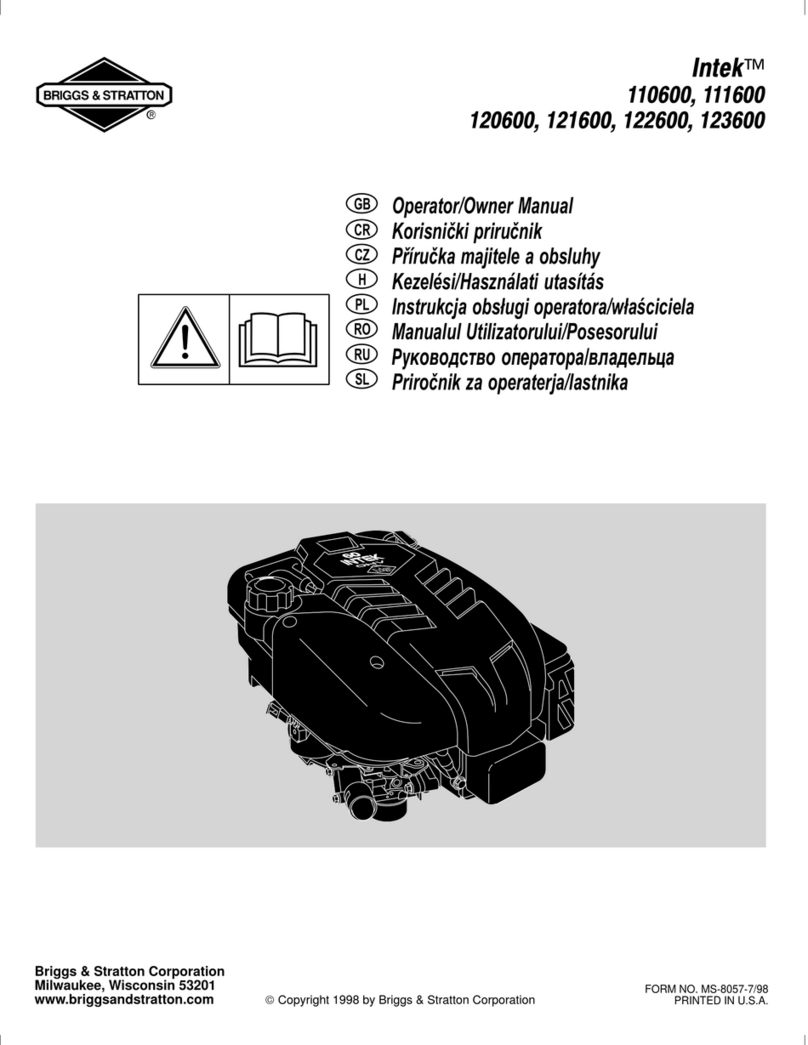
Briggs & Stratton
Briggs & Stratton Intek 110600 Operation and owner's manual

SEW-Eurodrive
SEW-Eurodrive CMP40 operating instructions
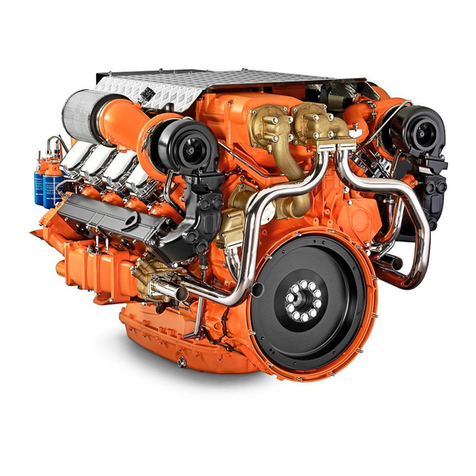
Scania
Scania DI16 Operator's manual

SOMFY
SOMFY LV25 installation guide

Lycoming
Lycoming O-320 76 Series Operator's manual
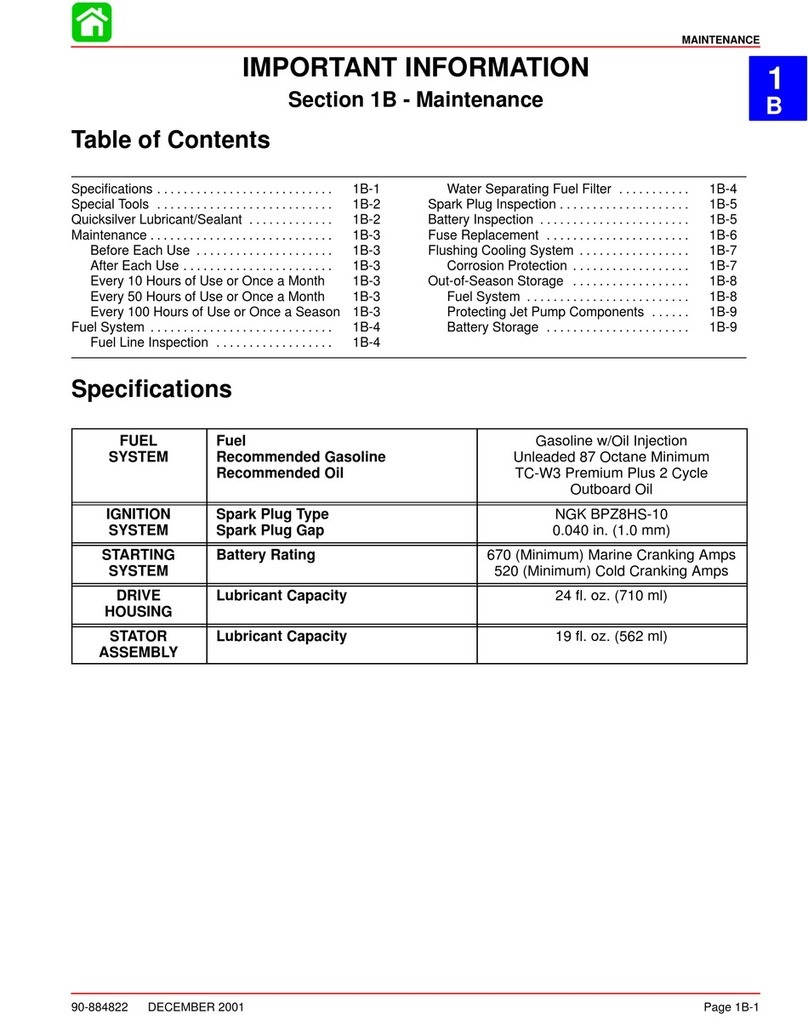
Mercury
Mercury 240 Jet Drive manual
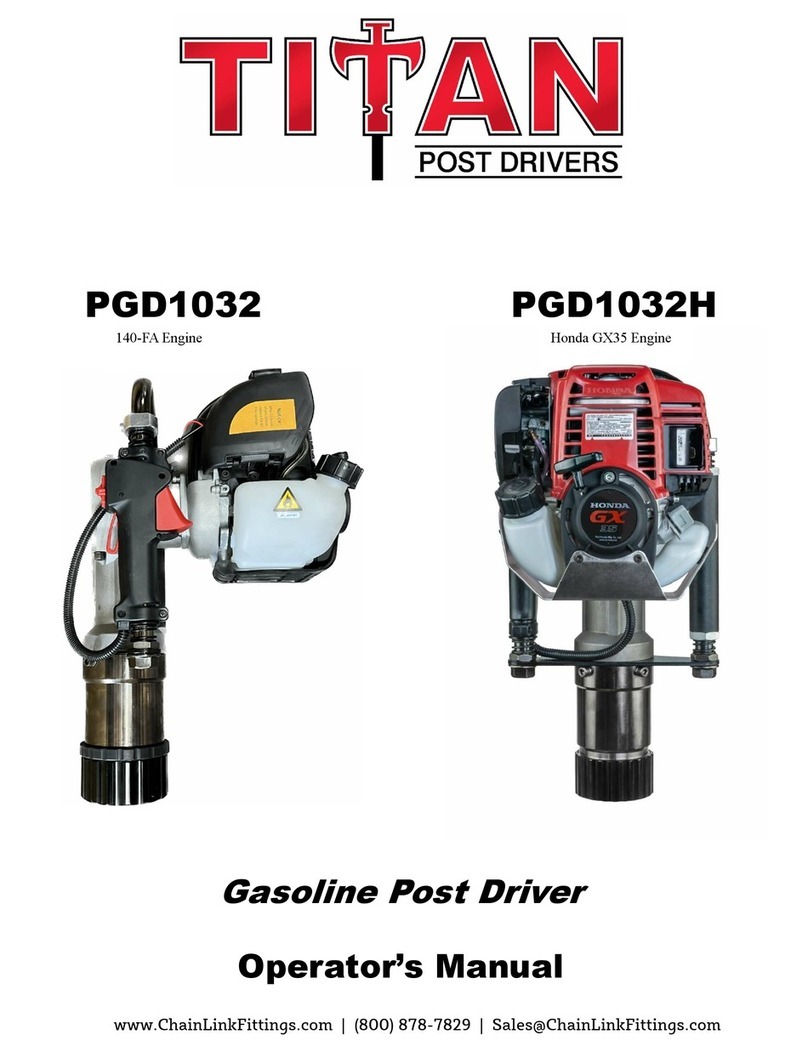
Titan
Titan PGD1032 Operator's manual
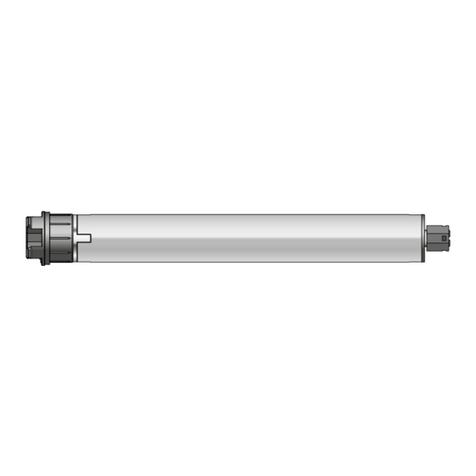
GEIGER
GEIGER PRO.TECline Spindle GB45 Series Original assembly and operating instructions
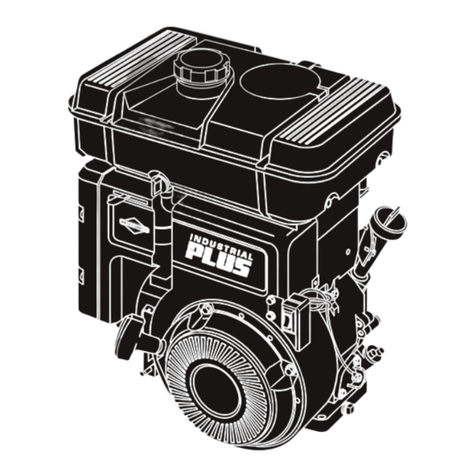
Briggs & Stratton
Briggs & Stratton 133400 Operating & maintenance instructions

Hatz Diesel
Hatz Diesel 1D41 S Operator's manual