Eoslift H10J Installation and operating instructions

OPERATION&SERVICE MANUAL
MODEL:H10J
MANUAL STACKER
Eoslift Automation Technology Corp.
No.99, Yanjia Road, Yuantong Town, Haiyan, Zhejiang

1.Structural Data Form
EJ(Single frame)
1
1 Structural Data Form
2 Safety Guidance
3 Maintenance
4 To Adjust Release Device
5 Trouble Shooting
6 Parts List
Page 1
Page 2
Page 3
Page 3
Page 3
Page 5
CONTENTS
Model
Manufacturer
Load Capacity
Inner Width of Legs
Outer Width of Legs
Min.Fork Height
Lift Height
Min.Mast Height
Fork Length
Fork Width
Fork Thick
Fork Ajustable
Load wheels
Steer wheels
Overall Length
Turning Radius
lb
B1(in.)
B2(in.)
H1(in)
H(in.)
H2(in.)
L(in.)
W(in.)
T(in.)
B3(in.)
in.
in.
L1(in.)
R(in.)
H10J
EOSLIFT
2200
33-49
41-57
1.4
63
80
42
3.9
1.4
8.3-33
φ
φ7 .1×2
65
51
2 .8×2 .8

3. Maintenance
3.1 Hydraulic oil - Check the oil level every six months. The oil must be hydraulic oil: ISO VG32, its viscosity
should be 32 CST at 100℉ total volume is about 4.2 qts. use temperature 0°F - 120 F R eplace the
hydraulic oil (every 12 months).
3.2 Daily check and maintenance - Check the stacker daily. Special attention should be paid to the
wheels, the axles, as thread, rags, etc., it may block the wheels, the fork and the mast, the chain,
the battery should be checked, too. The forks should be unloaded and lowered in the lowest
position when the job is over.
3.3 Lubrication - Use motor oil or grease to lubricate all movable parts.
°
5.Troubles shooting
2
3
4.To adjust release device
On the draw-bar of this hand stacker, you can find the control handle (① on Page21) which can be regulated in
three positions: LOWER = to lower the forks; NEUTRAL = to move the load, and LIFT = to raise the fork.
These three positions have been pre-posited at the factory. If however they have been changed, you can
adjust according to following step:
4.1 If the forks elevate while pumping in the NEUTRAL position, turn the adjusting nut( on Page21) on the
adjusting bolt (⑨on Page21) clockwise or turn the adjusting screw (⑨on Page10) clockwise until pumping
action does not raise the forks and the NEUTRAL position functions properly.
4.2 If the forks descend while pumping in the NEUTRAL position, turn the nut ( on Page21) or the screw (⑨on
Page10) counter-clockwise until the forks do not lower.
4.3 If the forks do not descent when the control handle (①on Page21) is in the LOWER position, turn the nut (
on Page21 )or the screw(⑨on Page10) clockwise until raising the control handle (①on Page21) lowers the
forks. Then check the NEUTRAL position according to item 4.1 and 4.2 to be sure the nut ( on Page21) and
the screw (⑨on Page10) is in the proper position.
4.4 If the forks do not elevate while pumping in the LIFT position, turn the nut ( on Page21) or the screw( ⑨on
Page10) counter-clockwise until the forks elevate while pumping in the LIFT position. Then check the LOWER
and NEUTRAL position according to item 5.1, 5.2 and 5.3.
⑯
⑯
⑯
⑯
⑯
NO. Trouble Possible cause Fixing methods
1 - The hydraulic oil is low
2
2.1 Operator should read all warning signs and instructions here and on the stacker before using it.
2.2 Do not operate a stacker unless you are familiar with it and have been trained or authorized to do so.
2.3 Do not operate a stacker unless you have checked its condition. Give special attention to the chain, wheels,
handle, guide frame, pilot wheel, mast, battery, etc.
2.4 Do not use on a slopping surface, rough, explosive or dangerous environment.
2.5 Do not lift people using the forks.
2.6 While lifting the forks, do not allow anyone to stand under or around the forks.
2.7 The operator should use safety shoes and gloves to protect against crushing or cutting hands or feet. Keep
feet out from underneath the load.
2.8 Do not move the stacker when the goods are lifted to the height more than 2 feet.
2.9 While the goods are being transported or lifted, all people should stay a minimum of 2 feet away from
stacker.
2.10 The weight of goods should be evenly distributed on the two forks, do not use only one fork. The center of
gravity of goods should be in the center of two forks.
2.11 Do not load beyond the maximum capacity according to the capacity diagram. Heavy loads should not be
allowed to remain on the forks for a long time after operation is over.
2.12 Before using or charging it, check the battery connection.
2.13 Charging should be in dry and ventilated location, and far away from any fire.
2.14 Keep the forks in the lowest position when not in use.
2.15 Do not use the truck when traveling on semi trailers.
2.16 Do not use the truck in a potentially explosive atmosphere.
2.17 Do not use the truck as a vehicle jack.
2.18 Do not use under windy conditions.
2.19 Do not use the truck in places insufficiently illuminated.
2.20 Do not use the truck with guarding removed.
2.21 Stacker should be parked on a smooth & level place, keep power off, lower the forks to the min. height, and
press on the brake. Stacker should not be parked in an unsafe area such as busy streets, intersections, narrow
roads, blind curves, slopes, soft ground, place that are flammable or fire fighting access.
2.22 In unknown environment, the operator should be careful while operating the pallet truck.
2.23 Unauthorized truck modification is not permitted. No modifications or alterations to a powered industrial
truck, which may affect, for example, capacity, stability or safety requirements of the truck, shall be made
without the prior written approval of the original truck manufacturer, its authorized representative, or a
successor thereof. This includes changes affecting, for example braking, steering, visibility and the addition of
removable attachments. When the manufacturer or its successor approve a modification or alteration, they shall
also make and approve appropriate changes to capacity plate, decals, tags and operation and maintenance
handbooks. Only in the event that the truck manufacturer is no longer in business and there is no successor in
the interest to the business, the user may arrange for a modification or alteration to a powered industrial truck,
provided, however, that the user shall: a) Arrange for the modification or alteration to be designed, tested and
implemented by an engineer(s) expert in industrial trucks and their safety. b) Maintain a permanent record of the
design, test(s) and implementation of the modification or alteration. c) Approve and make appropriate changes
to the capacity plate(s), decals, tags and instruction handbook. d) Affix a permanent and readily visible label to
the truck stating the manner in which the truck has been modified or altered together with the date of the
modification or alteration, and the name and address of the organization that accomplished the tasks.
2.Safety Guidance
The forks cannot be
lifted to max. height -Add oil - remove screw on top
of pump to add oil. Do not over
fill.
The forks cannot
be lifted
-The hydraulic oil is low
The oil has impurities
The adjusting nut is too high
and keeping the pump
Valve stuck open
Bleed the air from the system
-
-
-
-
-
-
-
Fill oil to proper level
Change the oil
Adjust the nut or screw to
proper level and remove the air
in the system
Squeeze and hold the lever
while pumping the handle
10 - 20 times

4
5
5
NOTE: DO NOT ATTEMP TO REPAIR THE PALLET TRUCK UNLESS YOU
ARE TRAINED AND AUTHORIZED TO DO SO.
Front wheel assembly
6.Parts List
4
No. Part Number Description Qty.
1
2
3
4
5
WC 02000708
WC02000707
WC02000022
WE07000004
WC02000227
WC02000286
WC 02000259
The right fork leg welded,5012(1.0t)
The left fork leg welded,5012(1.0t)
deep groove ball bearing6204
Circlip for Shaft 20,black
iron corePU wheel φ70×70,PU red
nylon wheelφ70×70
steering wheel axle
1
1
4
4
2
2
3
The forks cannot
be descended
-The piston rod or pump is
deformed resulting from
partial loading, cargo slanting
to one side or over-loading
-The truck was stored with
the forks raised for extended
period of time and now it jams.
The adjusting nut or screw
is not in correct position
-
-
-
-
Replace piston rod and/or pump
Keep the forks at the lowest
setting while Not in use, and
keep parts lubricated.
Adjust the nut or screw at base
of handle
Leaks
-
-
Sealing parts worn or damaged
Some parts are cracked or worn
-Replace worn parts with new
parts
-Replace worn parts with new
parts
The Forks descend
without the release
valve activated
-Impurities in the oil cause the
release valve to be unable to
close tightly
-Some parts of the hydraulic
system are cracked or damaged
-Air present in the oil
-Sealing parts worn or damaged
-The adjusting nut or screw is
not in the correct position
-Replace with new oil
-Inspect and replace with new
parts
-Remove the air and check for
air leaks
-Replace with new parts
-Adjust the nut or screw at base
of handle

7
6
No. Part Number Description Qty.
WC 02000224
WC02000343
WE04000019
WC02000019
WC02000345
WC02000346
WC02000347
WE03000021
WE06000012
WC02000350
WC02000225
WC02000348
WC02000351
WC02000342
WE04000020
WC02000344
WC02000349
WE01000004
WE05000012
WE05000013
WE04000012
WE05000014
WC02000226
WC02000285
WC02000435
WC 02000022
GB276,deep groove ball bearing
6205,two-side dusty cover
gasket
Gb6173 Hex nut M22×1.5,galvanized
JB7940.4,Pressure distribution type
forced filling oil cup 6
pedal plate,galvanized
pinch roller,galvanized
axle,galvanized
GB70.1 Hex socket screw M6×20,
galvanized
Gb117 Pin 6×42,galvanized
steering wheel frame with brake,black
GB297,circular cone running pulley
bearing 30205
wheel axle sleeve
brake rod,black
cover
GB6172.1 Hex nut M10,galvanized
adapter sleeve,galvanized
reset spring
Gb5780 Hex bolt M14×100,galvanized
Gb95 Plain washer 14,galvanized
Gb93 Spring washer 14,galvanized
Gb6170 Hex nut M14,galvanized
Gb95 Plain washer 20,galvanized
iron core PU wheelφ180×50,PU red,
iron coreblack
nylon wheelφ180×50(flower shape wheel)
nylon wheel φ180×50(flat)
GB276,deep groove ball bearing6204,
two-side dusty cover
1
1
1
1
1
1
1
1
1
1
1
1
1
1
1
1
1
1
1
1
1
1
2
3
4
5
6
7
8
9
10
11
12
13
14
15
16
17
18
19
20
21
22
23
24
2
1
2
Guide wheel with brake

8
9
NO. Part Number Description Qty.
1
1
1
1
1
1
1
1
1
1
1
1
2
1
1
2
3
4
5
6
7
8
9
10
11
12
13
14
15
WC 02000224
WC02000352
WE05000002
WE03000004
WC02000019
WC02000353
WC02000348
WE01000004
WE05000012
WE05000013
WE04000012
WC02000225
WE05000014
WC02000226
WC02000285
WC02000435
WC 02000022
GB276,deep groove ball bearing6205,
two-side dusty cover
axle cover,galvanized
GB93 Spring washer 10,galvanized
GB70.1 Hex socket screw M10×25,galvanized
JB7940.4,Pressure distribution type forced
filling oil cup 6
trailing wheel,black
wheel axle sleeve
GB5780 Hex bolt M14×100,galvanized
GB95 Plain washer 14,galvanized
GB93 Spring washer 14,galvanized
GB6170 Hex nut M14,galvanized
GB297,circular cone running pulley bearing
30205
GB95 Plain washer 20,galvanized
iron core PU wheelφ180×50,PU red,iron
coreblack
nylon wheelφ180×50(flower shape wheel)
nylon wheelφ180×50(flat)
GB276,deep groove ball bearing6204,
two-side dusty cover
Guide wheel Guide wheel
2

10 11
1
1
2
3
4
5
6
7
8
9
10
11
12
13
14
15
16
17
18
19
20
21
WE 07000004
WC02000365
WC02000108
WC02000387
WC02000363
WC02000390
WC02000391
WC02000069
WC02000393
WC02000375
WC02000401
WE03000003
WC02000377
WE04000003
WC02000378
WE07000012
WC02000397
WC02000395
WC02000388
WC02000399
WC02000400
GB894.1 Circlip for Shaft 20,black
pressure spring
spring cover,galvanized
seal ringUHS14
pump core
trundle,galvanized
roller shaft,galvanized
GB308,steel ball S7
spring seat
bolt
reverssliding bearing30/23×20×8
GB73 Screw M8×20,galvanized
unloading plate,black
GB6172.1 Hex nut M8,galvanized
melt,galvanized
GB894.1 Circlip for Shaft 8,black
extension spring
pedal stand,black
dusty seal ring DH14
handle seat,black
reverssliding bearing30/23×20×11.5
NO. Part Number Description Qty.
Cylinder assembly 1
11
1
11
1
11
1
11
1
11
2
11
1
11
1
11
1
11
1
11
2

12 13
1
1
1
1
WC 02000394
WC02000396
WC02000392
WC02000398
WE 06000016
22
23
24
25
26
27
rubber sleeve
pedal,black
spring
pin roll,galvanized
GB117 Pin 4×18,black
1
1
WE 03000016 GB70.1 Hex socket screw M5×16,galvanized
Cylinder assembly2

14 15
1
1
1
1
1
1
2
2
1
1
1
1
1
1
2
1
1
1
1
2
1
1
1
2
3
4
5
6
7
8
9
10
11
12
13
14
15
16
17
18
19
20
21
NO. Part Number Description Qty.
22
WC 02000358
WC02000382
WE07000004
WE03000023
WC02000383
WC02000364
WC02000385
WC02000384
WC02000362
WC02000386
WC02000110
WC02000369
WC02000115
WC02000381
WC02000389
WC02000376
WC02000045
WC02000374
WC02000375
WC02000372
WC02000370
WC02000371
cylinders(1.6),black
GB3452.1,O-ringφ15×2.65
GB894.1 Circlip for Shaft 20,black
GB818 Screw M6×10,galvanized
GB982,sseal washer 6
guide sleeve
GB3452.1,O-ringφ31.5×2.65
GB3452.1,O-ringφ34.5×2.65
hood,galvanized
GB3452.1,O-ringφ31.5×3.55
dusty seal ring DHS31.5
left pluf screw
GB3452.1,O-ringφ16×1.8
flow-limiting valve assembly
GB982,sseal washer 12
plug screw,galvanized
safety valve
adjustable spring
bolt
pump core
pump core spring
valve pocket
1
1
1
1
1
1
1
1
23
24
25
26
27
28
29
30
31
32
33
WC 02000132
WC02000373
WC02000069
WC02000366
WC02000368
WC02000367
WC02000117
WC02000361
WC02000360
WC02000380
WC 02000379
GB3452.1,O-ringφ9.0×1.8
sealing washer
GB308,steel ball S7
dirt-proof boot
unloading spring
unloading rod
GB3452.1,O-ringφ6.9×1.8
piston
piston rod(1.6)
guid ring for piston ZS35
seal ringYXD35
2
1
1

16 17
1
2
3
4
5
6
7
8
9
10
11
12
13
14
15
16
17
18
19
20
21
NO. Part Number Description Qty.
22
WC 02000721
WC02000355
WE04000009
WE01000002
WC02000357
WE05000004
WE03000016
WC02000330
WE03000014
WE04000015
WE04000013
WE04000005
WE01000006
WE04000022
WC02000710
WC02000709
WC01000020
WE03000004
WC02000338
WE03000004
WE05000002
WE
05000009
outer mast,5012
locking ring,galvanized
GB6170 Hex nut M10,galvanized
GB5781 Hex bolt M10×50,galvanized
gauze,black
GB95 Plain washer 5,galvanized
GB70.1 Hex socket screw M5×16,galvanized
gauze pad,black
GB70.1 Hex socket screw M8×20,galvanized
GB889.1 Hex lock nut M8,galvanized
GB802 Cap Nut M10,galvanized
GB6170 Hex nut M5,galvanized
GB5783 Hex bolt M16×40,galvanized
GB6170 Hex nut M16,galvanized
Support shaft Ⅱ,galvanized
Support shaft I,galvanized
Black cylinder assembly (1.6)
GB70.1 Hex socket screw M10×25,galvanized
EOS-HS handle
GB70.1 Hex socket screw M10×25,galvanized
GB93 Spring washer 10,galvanized
GB95 Plain washer 10,galvanized
1
1
3
1
1
11
11
1
4
4
2
11
8
8
2
2
1
2
1
3
3
3
Forks carriage

19
18
1
2
3
4
5
6
7
8
9
10
NO. Part Number Description Qty.
WC 02000722
WE07000010
WE03000019
WC02000231
WC02000224
WE07000007
WC02000232
WC02000283
WE07000011
WC02000284
WC 02000711
fork guide plate,black
GB894.1 Circlip for Shaft 25,black
GB77 Hexagon flat set screw M12×20,galvanized
steel wheel
GB276,deep groove ball bearing6205,
two-side dusty cover
GB893.1 Cieclip for hole 52,black
steel wheel cap
axle (830),galvanized
GB894.1 Circlip for Shaft 32,black
adjustable bolt,galvanized
telescope-feed fork,black
11
1
4
8
4
4
4
4
1
2
2
2
1
2
3
4
NO. Part Number Description Qty.
WC 02000748
WC02000260
WE04000012
WC 02000222
chain
bolt
GB6170 Hex nut M14,galvanized
single row running pulley chain CL connect 12A-1
2
2
4
4
Roller chain
Handle assembly

20
21
1
2
3
4
5
6
7
8
9
10
11
12
13
14
15
16
NO. Part Number Description Qty.
WJ 10800036
WJ10800037
WJ10800038
WJ10800039
WJ10800040
WJ10800041
WJ10800042
WJ10800043
WJ10800044
WJ10800045
WJ10800046
WJ10800047
WJ10800048
WJ10800049
WJ10800050
WJ 10800051
EOS-HS handle-finger handle
EOS-HS handle-position sheet
EOS-HS handle-torsion spring
EOS-HS handle-cooper roller
EOS-HS handle-handle weldment
EOS-HS handle-connecting sheet of pull pole
EOS-HS handle-pull pole
EOS-HS handle-chain
EOS-HS handle-adjusting bolt
EOS-HS handle-Pin
EOS-HS handle-Pin
EOS-HS handle-Pin
EOS-HS handle-Pin
EOS-HS handle-Pin
EOS-HS handle-nut
EOS-HS handle-fastening nut
1
1
1
1
1
1
1
1
1
1
1
1
1
1
1
2
Handle assembly Handle assembly
Table of contents
Popular Compact Loader manuals by other brands
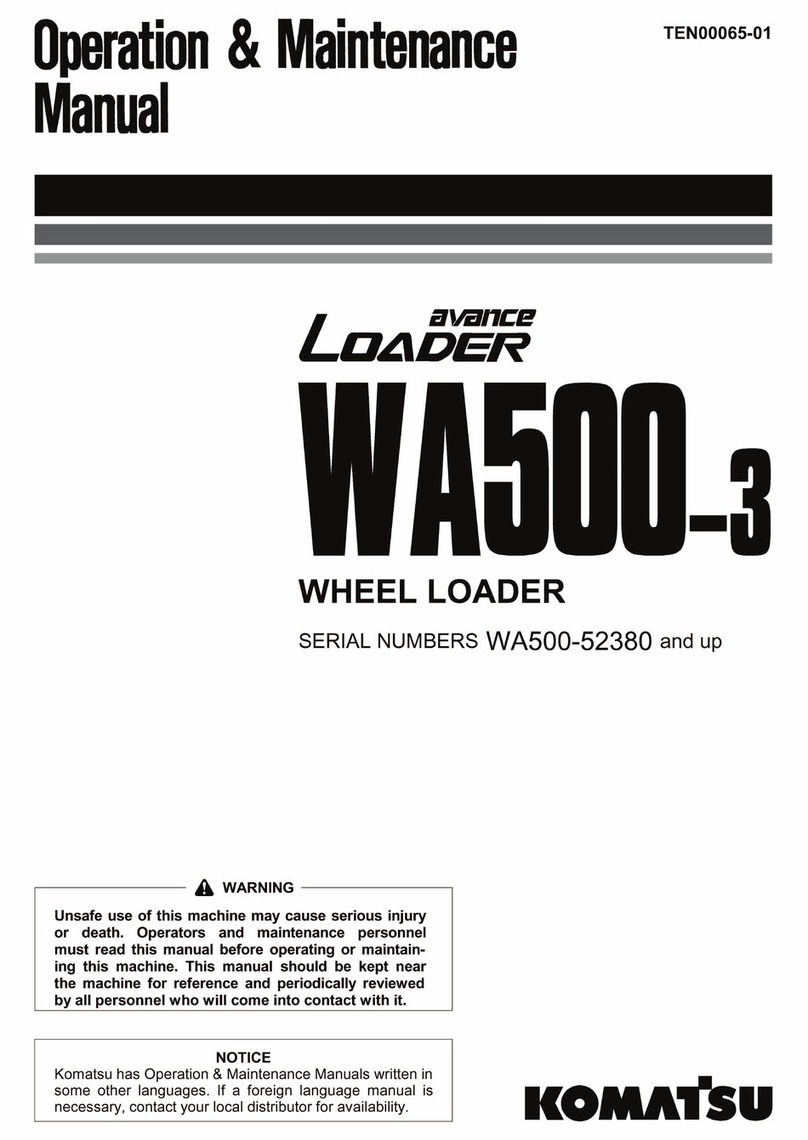
Komatsu
Komatsu Avance WA500-3 Operation & maintenance manual

Worldwide Construction And Forestry Division
Worldwide Construction And Forestry Division 624KR Technical manual
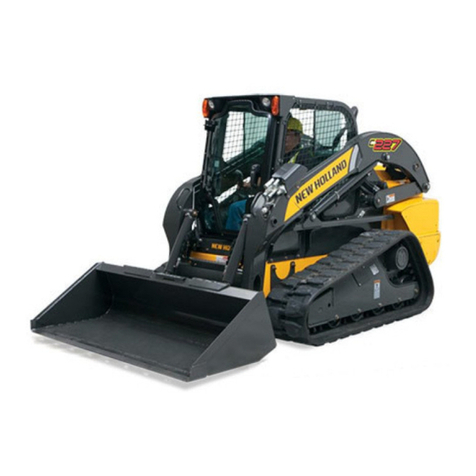
New Holland
New Holland 200 Series Service manual
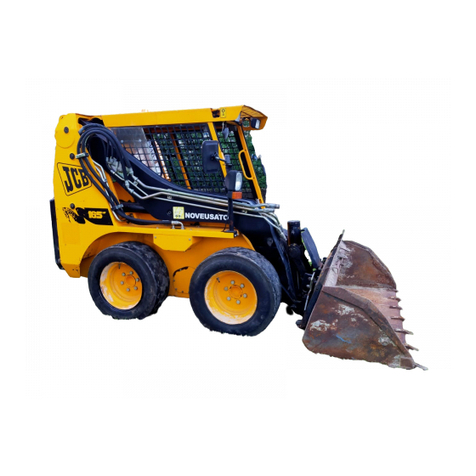
jcb
jcb ROBOT 150 Service manual
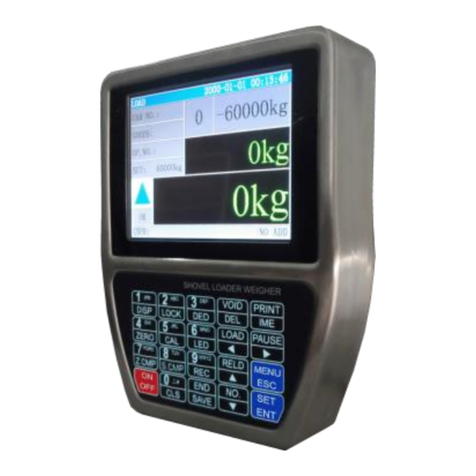
Kobastar
Kobastar N59 Operation manual
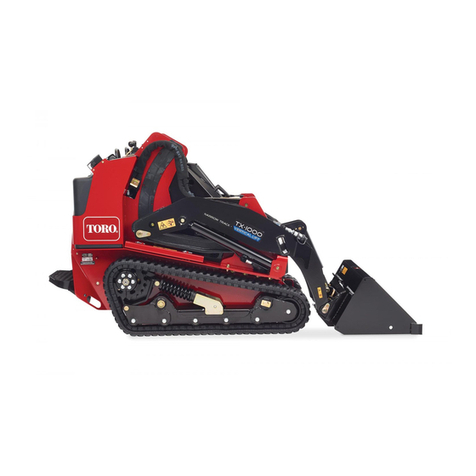
Toro
Toro TX 1000 Operator's manual