Erreka ULTRA Operating instructions

7
ULTRA
Quick installation and programming guide English
WARNING
This quick guide is a summary of the complete installation manual. The manual contains safety warnings and
other explanations which must be taken into account. The most recent version of this guide and the
installation manual are available at the "Downloads" section on Erreka's website:
http://www.erreka-automation.com
The options and functions described in this guide apply for the firmware version indicated on the circuit. The
firmware, as part of a process of continuous improvement, is subject to new functionalities or upgrades being
included as a result of new versions which are not necessarily compatible with previous ones. For this reason,
some options or functions may differ or be unavailable if your firmware is older than shown in this guide.
E289A
D289A
L
L
Electrical wiring
A: Main power supply
3x1,5mm2(max. 30m)
B: Flashing light
2x0,5mm2
C: Photocells (Tx / Rx)
2x0,5mm2/ 4x0,5mm2(max. 30m)
D: Key switch
2x0,5mm2 (max. 25m)
Elements of the complete installation
Unlocking
Unlocking should be
carried out with caution.
The internal spring may
cause jolting if the barrier
is not balanced or the arm
is not mounted.
Unlocking
(manual operation):
turn the key (L) clockwise
until it stops.
Locking
(motorised operation):
turn the key (L) anti-clockwise
until locked.
The drawing shows a right-side
barrier (ULS6ECD, ULS45ECD,
ULS3ECD)
ONLY UNLOCK THE
BARRIER IF THE ARM IS
INSTALLED.
MSU-021/01 V1.18b or later

8
Choosing the spring and anchoring orifice
The balancing spring and its anchoring orifice depend
on the length (L) of the barrier arm:
ULS3EC Barriers:
•Arm 2.0m < L < 3.0m:
spring D= 4.5mm, orifice 1
•Arm 1.5m < L < 2.0m:
spring D= 4.5mm: orifice 2
ULS45EC Barriers:
•Arm 2.5m < L < 4.0m:
spring D= 5.5mm, orifice 2
•Arm 4.0m < L < 4.5m:
spring D= 6.5mm: orifice 2
ULS6EC Barriers:
•Arm 4.5 m < L < 6.0 m:
2 springs D = 6.5 mm, orifice 2
AUL03/AUL04/AUL08 rubber band and/or AUL05/
AUL06/AUL09 LED strip can be used indistinctly.
Using other accessories may influence the choice of
spring and orifice.
If the spring or anchoring orifice needs to be
changed, do it before installing the barrier and
the arm.
P289L
21
P289C1
Arm assembly
Choose the barrier in accordance with the assembly
side and length of the arm:
ULS6ECD: right, 100x45mm, 6m;
ULS45ECD: right, 100x45mm, 4.5m;
ULS3ECD: right, 80x45mm, 3m;
ULS6ECI: left, 100x45mm, 6m;
ULS45ECI: left, 100x45mm, 4.5m;
ULS3ECI: left, 80x45mm, 3m.
Lock the operator and mount the arm.
Changing the anchoring orifice
+
–
P289J
M
1
2
S
V
1Place the barrier arm in
upright position.
2Turn the tensioning handle
(M) anti-clockwise until the
spring is tensionless.
3Release the anchor bolt (1)
and mount it in the other
orifice.
4Balance the barrier as
described below.
Changing the spring
1Place the arm in upright position.
2Turn the tensioning handle (M) anti-
clockwise until the spring is tensionless.
3Release the anchor bolt (1).
4Take down the spring box (S), releasing
the pivot (V).
5Completely unscrew the tensioning
handle, remove the spring and position
the new spring in place. Finally, screw the
tensioning handle.
6Mount the spring box (S), inserting the
pivot (V).
7Secure the anchor bolt in the appropriate
orifice, (1) or (2).
8Balance the barrier as described below.
If the spring or anchoring orifice needs to be changed, do
it before installing the barrier and the arm.
The illustrations and explanations refer to ULS3C, ULS45EC barriers, which have a single
balancing spring. The procedure for ULS6EC barriers is similar, bearing in mind that the
spring and its adjacent elements are duplicated.

9
P289G
+
–
Balancing the barrier
Unlock
THE BARRIER MUST BE BALANCED FOR
PROPER OPERATION.
•In order to complete the balancing, connect the
power supply and check operation: the barrier
should move smoothly, without jolts or jerks.
•If it does not move smoothly, without any jolts or
jerks, reduce the tension of the spring using the
tensioning handle.
The barrier may not be balanced when moving
the handle; if this is the case, change the
anchoring orifice (from 1 to 2) or the balancing
spring. Repeat these steps until the barrier is
balanced and moves smoothly.
ULS6EC barriers have two springs and two
knobs for tensioning.
Balancing is done by acting equally on the two
knobs, to ensure the tensioning of both springs is
approximately the same.
The tensioning handle is only accessible with
the arm in upright position.
P289H
AB
C
Stopper adjustment
•Unlock the operator and move the barrier
by hand to check its position in the
stoppers. If it is not correct, adjust the
corresponding stopper, (A) or (B).
•Lock the operator and check operation. If
necessary, adjust the rod (C).
P289I
FCA
FCC
LA
LC
Limit switch adjustment
Unlock the operator and move the barrier by hand to
check the adjustment of the LA and LC cams which
drive the FCA and FCC limit switches.
The limit switch has two LEDs which indicate whether
it is enabled or not:
•The closing LED (FCC) is red
•The opening LED (FCA) is green
Travel will not be programmed correctly
unless the cams are correctly adjusted.
P289M
OK
LED Strip
If the LED strip is installed (AUL09 for 3 m Barriers;
AUL05 for 4.5 m barriers; AUL06 for 6 m barriers),
use the hole furthest from the arm to pass the
cable inside the barrier.

10
N
L
ST1
ST2
SG.A
FCA
FCC
P289Z
General connections
Opening photocells (SG.A): place DIP6 in
ON to enable testing.
Closing photocells (SG.C): place DIP9 in ON
to enable testing.
Photocell testing Encoder
For the correct operation of the
encoder, ensure DIP7 is in ON.
(photocells without testing)
(photocells with testing)
230V, máx. 60W
F1 Motor fuse (5x20):
230VAC: 2,5A
125VAC: 6,3A
F2 Electronic fuse
(5x20; 230VAC: 500mA)
F3 FT and AUX24V outputs fuse
(5x20; 315mA)
DL1 Barrier open
DL2 Radio code programming
indicator / Receiving radio
code
DL3 Radio code or operation
programming
DL4 Opening relay enabled
DL5 Closing relay enabled
DL6 Opening limit switch contacts
closed
DL7 Closing limit switch contacts
closed
DL8 Opening safety device
contacts closed
DL9 Closing safety device contacts
closed
DL10 Pedestrian key command
contacts closed
DL11 Total key command contacts
closed
DL12 Radio key command
DL13 Encoder signal
Operator working: DL13
comes on intermittently,
since the encoder sends the
signal in the form of pulses.
Operator shutdown: DL13
may be on or off, indistinctly,
depending on the position of
the encoder (high pulse or
low pulse).
DL14 Power supply
STOP pushbutton enabled (emergency stop)
: DL1 and DL3 flash simultaneously every 0.5 seconds.
Opening or closing photocell testing error:
DL1 and DL3 flash simultaneously every 2 seconds.
LED strip connections
The LED strip is an optional accessory which can be bought
separately. It includes: a traffic light card (SMF), a power source
(PWR LED), an LED strip (LED) and the cables and glands
necessary.
There are two references:
•AUL09: for 3m barriers
•AUL05: for 4.5m barriers.
•AUL06: for 6m barriers.
The "Transparent rubber" accessory MUST be installed in
order to install the LED strip.
This rubber is supplied separately, in lengths of 6m (AUL03),
4.5m (AUL04) and 3m (AUL08).
V+
COM
N
L
LED (AUL05 / AUL06)
PWR LED
(AUL05/AUL06)
V
R
COM
P289Y

11
E289L
SW2 functions during programming (DIP1 = ON)
DIP1=ON: programming enabled (DL3 lights up)
DIP1=ON and DIP2=ON: open/close programming
DIP1=ON and DIP4=ON: radio code programming
Radio code programming (only with RSD receiver)
1 Connect the electrical power
supply and close the barrier by
keeping PUL1 pressed down.
2 Select the code in the transmitter. 3 Place the DIPs as shown in the
figure (DIP1=ON, DIP4=ON). DL3
lights up to show programming
mode enabled.
R289A R289C
R289B
4 Press the button for the required
channel. DL2 flashes to show
programming is complete.
5 Place DIP1 and DIP4 in OFF.
DL3 remains off.
6 Disconnect and reconnect the
electrical power supply.
I
II
R289D
R289E
If a receiver other than RSD is used, see the corresponding instructions.
Open/close programming
1 Connect the electrical power supply
and close the barrier by keeping
PUL1 pressed down.
2 Place the DIPs as shown in the
figure (DIP2=ON, DIP1=ON).
DL3 lights up to show
programming mode enabled.
3 Press ST1 to start opening.
R289A
G289Z
G289A
The barrier is supplied with
open/close settings
programmed at factory.
4 Wait for it to come to a stop at the
end of its travel. 5 Press ST1 to start closing. 6 Wait for it to come to a stop at the
end of its travel.
G289C
G289D
G289F
7 Place DIP1 and DIP2 in OFF. DL3
remains off.
R289E

12
DIP Modes and functions Option Effect
DIP1 OFF
DIP2 Advance warning
ON the flashing light comes on and the operation begins after a 3
second warning
OFF the flashing light comes on and the operation begins
immediately
DIP3 Key commands using ST1 and ST2 ON ST1: opening command; ST2: closing command
OFF ST1: opening and closing commands; ST2: no function
DIP4 Automatic or step-by-step mode
ON automatic mode (the barrier closes automatically once standby
time has passed, adjusted using T.E.)
OFF step-by-step mode (the barrier only closes when receiving the
key command)
DIP5 Automatic mode optional
(only if DIP4 = ON)
ON during standby, the barrier obeys the key commands (can be
closed before standby time finishes)
OFF the barrier cannot be closed until standby time finishes; key
commands will cause standby time to restart
DIP6 Opening photocell testing ON testing enabled
OFF testing disabled
DIP7 Encoder ON encoder enabled
OFF encoder disabled
DIP8 Interlocking mode (with FT1)
ON interlocking mode enabled: the barrier closes if SG.C is enabled
during standby time (in automatic mode)
OFF interlocking mode disabled
DIP9 Closing photocell testing ON testing enabled
OFF testing disabled
DIP10 No function always place in OFF
Function and mode selection using SW2 (DIP1 = OFF)
T.LG: fan operation time
Regulate the time the operator cooling fan is working.
•Minimum value: 3 seconds; maximum value: 90
seconds
T.E: barrier open standby time
If automatic or optional automatic operation mode has
been programmed, adjust T.E. to set standby time with
the barrier open (before starting to close automatically).
•Minimum value: 0 seconds; maximum value: 90
seconds
P.M: motor torque
Use P.M. to adjust the maximum motor power value.
Torque adjustment, respecting the maximum
closing forces set out in Standard EN12453:2000.
Make the measurements as described in Standard
EN 12445:2000.
Potentiometer adjustment
Table of contents
Popular Other manuals by other brands
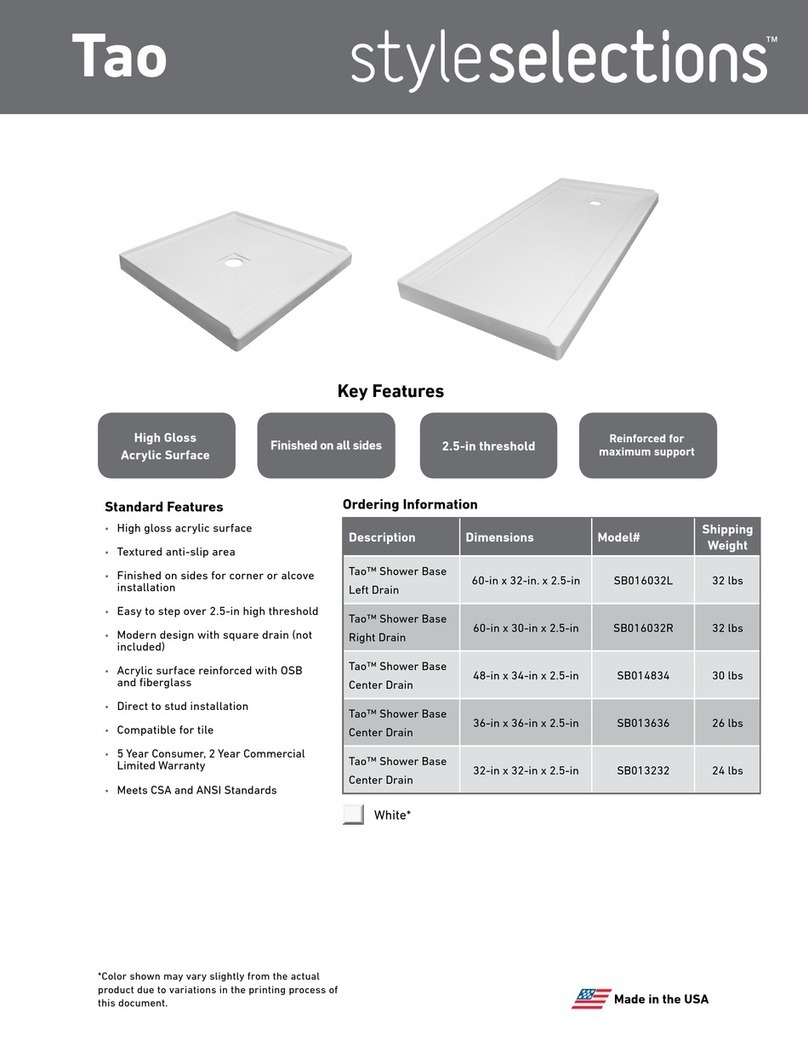
LOWE'S
LOWE'S Style Selections Tao SB016032L manual

Aqua Medic
Aqua Medic Mistral 200 Operation manual
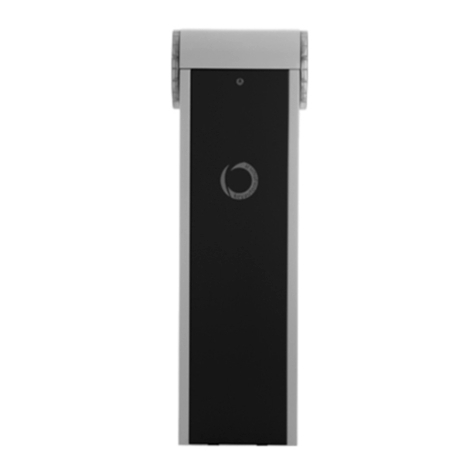
Keyautomation
Keyautomation ALT3KF Series Instructions and warnings for installation and use

medemagroup
medemagroup Joystick DX2 user guide
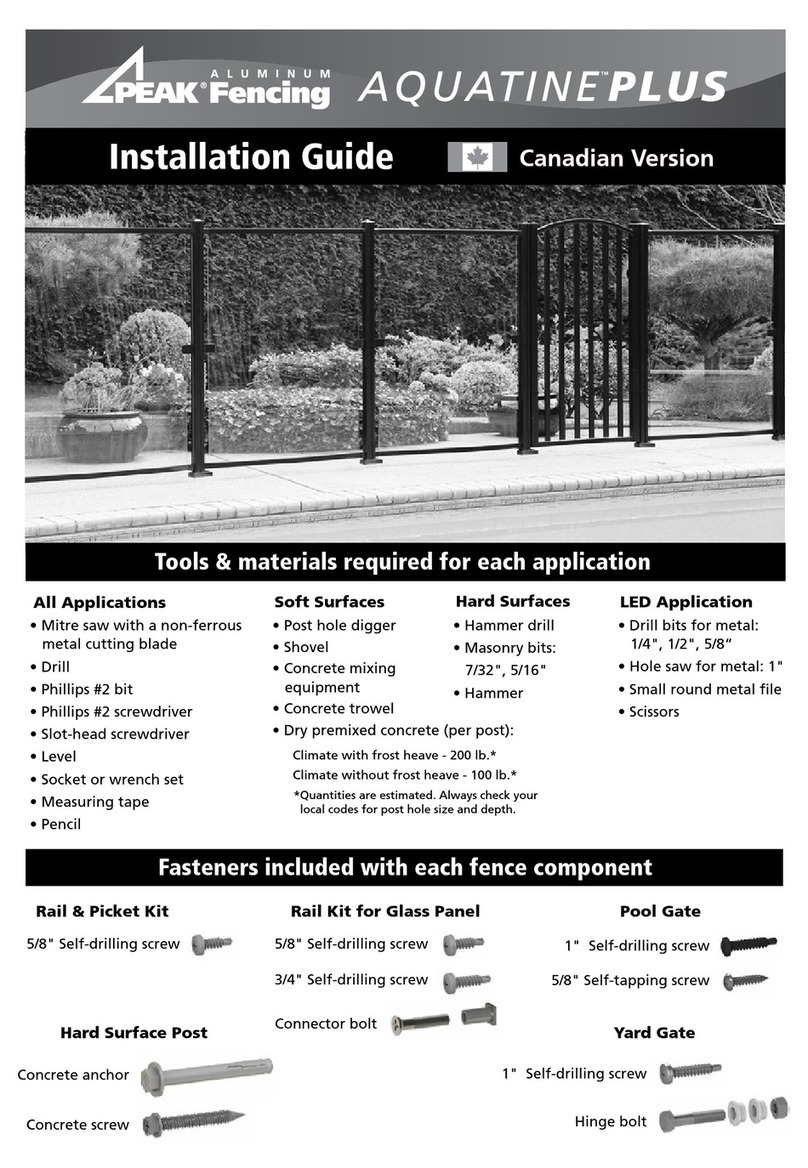
Peak
Peak AQUATINE PLUS installation guide

Martin Audio
Martin Audio AQ28 - SCHEMATICS manual