eta System Separation Module User manual

2021-02-17
EN
0000000219
V.006
X.35.15, X.51.0
939003-002
System Separation Module
Operating Instructions

ETA Heiztechnik
Gewerbepark 1
A-4716 Hofkirchen an der Trattnach
Tel: +43 (0) 7734 / 22 88 -0
Fax: +43 (0) 7734 / 22 88 -22
www.eta.co.at

General General information
3
1 General
1.1 General information
Copyright
All contents of this document are property of ETA
Heiztechnik GmbH and are protected by copyright.
Any reproduction, transfer to third parties or use for
other purposes is prohibited without written permission
from the owner.
Subject to technical changes
We reserve the right to make technical modifications
without notice. Printing and typesetting errors or
changes of any kind made in the interim are not cause
for claims. Individual configurations depicted or
described here are only available optionally. In the
event of contradictions between individual documents
regarding delivery scope, the information in our current
price list applies.
Software Description
The software version described in this documentation
corresponds to the version valid at the time of publica-
tion. The software version installed on your product
may differ from that described in this documentation.
A software update to a more recent version can
always be performed. With the appropriate au-
thorisation, the required files can be found at
"www.eta.co.at".
Explanation of symbols
Instructions and information
Layout of safety instructions
SIGNAL WORD!
Type and source of danger
Possible effects
• Measures for avoiding the danger
Types of safety instruction
CAUTION!
On non-compliance with this safety instruction, there is
a risk of material damage.
WARNING!
On non-compliance with this safety instruction, there is
a risk of physical injury.
DANGER!
On non-compliance with this safety instruction, there is
a risk of major physical injury.
1.2 Warranty, guarantee and liability
Requirements
We can only accept liability for the function of our
products if they are correctly installed and operated.
This is only possible if the conditions below are
complied with.
Installation in a dry, frost-proof room
A dry, frost-proof room is required for the installation.
pH value between 8 and 9
The pH value of water used to fill the heating system
must be between 8 and 9.
Frost protection for the secondary side
The maximum frost protection content must be
adjusted to the local conditions and checked on an
annual basis if frost protection is required, for example,
on the secondary side for outdoor heating systems.
Permissible water hardness
In order to protect the heat exchanger from calcifica-
tion, the water hardness of the heating water must be
taken into account. Observe the indications outlined in
ÖNORM H 5195-1, see 8 "Water hardness".
Expanding the control system
Only components provided by us may be used for
expanding the control system, unless these are
generally available standard devices, such as thermo-
stats.
Regularly perform cleaning and maintenance
Cleaning and maintaining the product is essential. The
required steps and intervals are either contained in this
documentation or included as a separate document.
Proper installation
The installing contractor is liable for proper installation
according to the corresponding installation instructions
and the relevant rules and safety regulations. If you as
customer have installed the heating system partly or
entirely without relevant training and in particular

4 www.eta.co.at
Warranty, guarantee and liability General
without up-to-date practical experience, without having
the installation checked by a trained and responsible
expert, we exclude defects in our delivery and conse-
quential damages resulting from this cause from our
warranty, guarantee and liability.
Repairs
Repairs are only permitted using spare parts provided
by us. The only exceptions are common standardised
parts such as electrical fuses or fastening materials, as
long as they possess the required features and do not
restrict the functionality of the system.
Repair of defects
For repairs of defects carried out by the customer or by
a third party, ETA shall only bear the costs or remain
obligated by warranty if this work was approved in
writing in advance by the customer service of ETA
Heiztechnik GmbH.

CE-Conformity
5
2 CE-Conformity
CE declaration of conformity
We hereby declare that the product in its standard design as stated here corresponds to the above provisions. The
sole responsibility for issuing this declaration of conformity lies with the manufacturer. The technical documentation
for this product is managed by ETA Heiztechnik GmbH. Signed for and on behalf of:
Manufacturer: ETA Heiztechnik GmbH
4716 Hofkirchen an der Trattnach, Gewerbepark 1, Austria
Product: System separation module with energy-saving pumps
Types: ETA system separation module
EU Directives:
2006/95/EC Legislation relating to electrical equipment: Low Voltage Directive
2004/108/EC Legislation relating to electromagnetic compatibility
2011/65/EU Directive on the restriction of the use of certain hazardous substances in electrical and
electronic equipment (RoHS 2 guideline)
Applied standards:
EN 60335-1:2020 Household and similar electrical appliances - Safety -
Part 1: General requirements
IEC 61000-6 1/2:2005 Electromagnetic compatibility (EMC):
Generic standards - Immunity for residential, commercial and light-industrial environments
(1) and industrial environments (2)
IEC 61000-6 3/4:2011
+ A1:2011
Electromagnetic compatibility (EMC):
Generic standards - Emission standard for residential, commercial and light-industrial en-
vironments (3) and industrial environments (4)
Hofkirchen, 12/01/2021 Ing. Johann Eibelhuber
Quality assurance
DI Ferdinand Tischler
Management

6 www.eta.co.at
Technical data Description
3 Description
3.1 Technical data
Connections and components
1 Flow for secondary side
2 Return for secondary side
3 Safety valve with connection for membrane
expansion vessel
4 High-efficiency pump of secondary side
5 Primary side high-efficiency pump
6 Return for primary side
7 Flow for primary side
8 Flow temperature sensor for secondary side
9 Flow temperature sensor for primary side
10 Circuit board [EM-C]
11 Bleed screw
Dimensions
Technical data
Free residual pump head: primary side
Underfloor heating:
13 kW; 75/33 °C; 0.27 m³/h = 7.00 mWs
Radiator heating:
40 kW; 75/50 °C; 1.39 m³/h = 3.00 mWs
Free residual pump head: secondary side
Underfloor heating:
13 kW; 35/28 °C; 1.62 m³/h = 2.20 mWs
Radiator heating:
40 kW; 65/45 °C; 1.74 m³/h = 1.50 mWs
Connections
DN20 (3/4") internal thread
Pump: primary side
Speed-regulated high-efficiency pump (model
"WILO Para RS 15-130/7-50/iPWM1-9")
Pump: secondary side
High-efficiency pump (model "WILO Para 15-
130/6-43/SCU-9"), for differential or constant
pressure operation with bleed function.

Description Function
7
3.2 Function
Mode of operation
On the underside of the module, the heat from heat
producer (e.g.: buffer) reaches the primary side of the
heat exchanger. The speed-regulated primary pump
only conveys enough heating water from the buffer for
the feed temperature required by the heat consumer
on the secondary side to be achieved.
Fig. 3-1: Primary and secondary circuits
A high-efficiency pump is installed on the secondary
side for the heat consumer; its operating mode must be
set manually. The pump characteristic curves can be
viewed under 7 "Commissioning".
Both temperature sensors constantly provide the
ETAtouch control system with information about the
feed temperatures of the primary and secondary sides.
All components have already been connected at the
factory. Power is supplied via a 230 V Schuko socket.
Only the CAN-bus connection to the ETAtouch con-
trol panel may be established.
Contact thermostats are required for underfloor
and wall heating in order to protect the second-
ary side against overheating. If the secondary side is
at risk of frost, an additional contact thermostat must
be installed for the primary side in order to prevent the
heat exchanger from freezing.
Details about contact thermostats can be found under
6.3 "Contact thermostat".
Uncouple the module hydraulically
Run separate piping between the system separa-
tion module and the buffer, and do not install in the flow
between the heat producer and the buffer. Otherwise,
the heat exchanger of the module will be unintention-
ally heated.
Correct connection
Wrong connection

8 www.eta.co.at
Secondary side characteristic curve Description
3.3 Secondary side characteristic
curve
Secondary side characteristic curves
Example: underfloor heating with 15 kW and 10 K
spread is attached on the secondary side. The
performance chart shows a flow rate of approx.
1.30 m³/h.
=> 1.30 m³/h a free residual pump head of 3.5 m
occurs on the secondary side with a pressure loss of
approx 1.6 m.
Performance chart
Free residual pump head
1 Pump head
2 Module pressure loss
3 Free residual pump head
Primary spread
Flow - return
Secondary spread
Flow - return
75 °C - 35 °C = 40 K 35 °C - 30 °C = 5 K
75 °C - 33 °C = 42 K 35 °C - 28 °C = 7 K
75 °C - 30 °C = 45 K 35 °C - 25 °C = 10 K
75 °C - 45 °C = 30 K 60 °C - 40 °C = 20 K

Description Primary side characteristic curve
9
3.4 Primary side characteristic curve
Primary side characteristic curves
Example: using the table, a primary side spread of
45 K results for the secondary side underfloor heating
(15 kW, 10 K spread).
The performance chart results in a primary side
flow rate of approx. 0.29 m³/h at 15 kW output and
45 K spread.
=> 0.29 m³/h a free residual pump head of 7.0 m
occurs on the primary side with a pressure loss of
approx 0.2 m.
Performance chart
Free residual pump head
1 Pump head
2 Module pressure loss
3 Free residual pump head
Primary spread
Flow - return
Secondary spread
Flow - return
75 °C - 35 °C = 40 K 35 °C - 30 °C = 5 K
75 °C - 33 °C = 42 K 35 °C - 28 °C = 7 K
75 °C - 30 °C = 45 K 35 °C - 25 °C = 10 K
75 °C - 45 °C = 30 K 60 °C - 40 °C = 20 K

10 www.eta.co.at
Installation
4 Installation
Mounting the module on the wall
Mark the position of both mounting screws at the top
and bottom on the wall.
Mount the fixing screws in the wall, hang the module
and fix it in place.
Mounting the screw joints
Mount the screw joints for the secondary side. The
pressure gauge and ball valve on the flow and the
safety valve and a ball valve on the return. Include flat
seals with all screw joints.
Fig. 4-1: Screw joints for the secondary side
Mount both ball valves on the primary side with the
included flat seals.
Fig. 4-2: Screw joints for the primary side
Installing the piping
Connect the piping from the heat producer on the
primary side and to the heat consumer on the second-
ary side.

Installation
11
Installing outlet pipes for the safety valve
A safety valve with 3 bar opening pressure has already
been installed for the secondary circuit at the factory. A
membrane expansion vessel can be connected to this
T-piece.
Fig. 4-3: T-piece with safety valve
DANGER!
Safety valve outlet
The safety valve outlet must be directed to the ground
in a pipe so nobody is endangered by hot water or
steam.
The safety valve outlet must be fed to the sewage
system (e.g. duct) via a clearly visible, open route
(siphon funnel). This will ensure that malfunctions,
especially a failure of the safety valve to close, can
be detected. If no connection is available to the
sewage system, the outlet must be directed to the
ground in a pipe.
For frost protection in the secondary circuit, guide
the safety valve outlet into a canister
DANGER!
Safety valve outlet
The safety valve outlet must be directed to a canister
with sufficient dimensions in a pipe so nobody is
endangered by hot water or steam.
The safety valve outlet must be directed into the
canister via a clearly visible, open route (siphon
funnel) so that malfunctions, especially a failure of
the safety valve to close, can be detected. In the
same way, the frost protection is collected when
opening the safety valve and can be filled again.
Establishing a CAN-bus connection to the boiler
Establish the bus connection between the boiler and
the module with the supplied CAN-bus line. Also see
6.2 "CAN bus installation" for more information.
Contact thermostats required for underfloor and
wall heating
For safety reasons, contact thermostats must be
installed for operation with underfloor and wall
heating. In the event of a malfunction, they switch off
the affected heating circuit to protect it from
excessively high flow temperatures.
They are available separately and pre-wired.
Fig. 4-4: Contact thermostat
In case of risk of frost, install an additional contact
thermostat as frost protection
If the secondary side is filled with frost protection
because it is designed as an outdoor heat-
ing system, for example (heating of paths, drives...), a
contact thermostat must be installed for the primary
side in order to prevent the heat exchanger from
freezing.
This is clamped so that the secondary pump switches
off as soon as the temperature set on the contact
thermostat is exceeded (e.g.: 10 °C).

12 www.eta.co.at
Configuration
5 Configuration
Content of this configuration
Only the steps required for the configuration of this
product are described below. The configuration of the
complete heating system is described in the "Configu-
ration" manual supplied with the boiler.
Software version X.31.3 or later
The configuration requires software version X.31.3 or
later.
An update must be performed first if an older version is
installed.
Starting the configuration assistant
The process of starting the configuration assistant
differs depending on the installed software version.
Software version X.35.X and earlier
• Increase the authorisation to [Service]. Then open
the [Toolbox] menu by pressing the button and
the [Configure system] button.
Software version X.36.0 and later
• In the system settings , increase the authori-
zation to [Service] and open the system configura-
tion menu with the [Systems configuration] button.
Start the configuration assistant with the
[Starting the assistant] button.
Description for software version X.36.0 and later
The following description and screen shots represent
the software interface of version X.36.0 and later.
Factory configuration
The function blocks for the system separa-
tion module [SSM], a heating circuit [HC] and
system [Sys] (for the outside temperature sensor) are
installed at the factory.
Select settings for the frost protection of the
secondary circuit
In the function block of the system separation
module it must be set whether the secondary side
is endangered by frost (i.e. filled with frost protection)
or not. If the secondary circuit is endangered by frost
the control system protects the modules heat
exchanger.
To set, open the settings of the system separation
module in the function block and select the operating
mode [Operation below freezing point]. If the
secondary side receives frost protection [Yes] is to be
selected. If not, [No] is set.

Configuration Example 1
13
5.1 Example 1
Hydraulic schematic
The buffer is connected to the [GM-C] circuit board in this example.
Circuit
board Function blocks Description
EM-C 3 SSM System separation module
Settings:
Operation below freezing point [Yes] or [No]
Options:
Module is a consumer within an ETA system.
EM-C 3 Heating circuit Heating circuit as underfloor heating
The heating circuit pump is already
contained within the system separa-
tion module.
Settings:
HC type Underfloor heat.
Heating circuit pump none
Heating circuit mixing valve no
Room sensor None
EM-C 3 Sys System
Settings:
Outside temperature sensor via board input

14 www.eta.co.at
Example 1 Configuration
Connections
= type [Heating water]
Show external malfunction message on the
screen
No
Output all fault messages No
Circuit
board Function blocks Description
Circuit
board
Function blocks Description
GM-C 0 BufferFlex Buffer storage tank
Settings:
Temperature sensor number 3
Combination tank No
Consumer levels 1
Solar heating system not present
Start relief for log boiler No
Producers Consumers
GM-C 0: BufferFlex: Consumer level 1 (top) EM-C 3: SSM: Prim. flow
EM-C 3: SSM: Sec. flow EM-C 3: HC: .

Electrical connections Requirements
15
6 Electrical connections
6.1 Requirements
Electrical connection must only be made by
qualified specialist personnel
The electrical installation must only be performed
by specialist personnel with the corresponding
qualifications.
Power supply of the module
Power is supplied to the module via the power
plug that has already been mounted; this is
performed independent of the boiler. However, the
power supply can also be securely wired to the
electronic distributor.
DANGER!
Electric shock
There are live parts on the circuit boards. If
touched, they can cause injury and
property damage.
Before beginning any work, isolate the system
completely from all power sources, ensure that it
cannot be switched back on, and verify that it is
safely isolated from the power supply.
CAUTION!
Flexible stranded conductors
If flexible stranded conductors are not used for the
wiring, the contacts in the plug connections will be
subjected to excessive mechanical strain. In this case,
the warranty for the electronics would become null and
void.
Only flexible stranded conductors may be used for
the wiring.
6.2 CAN bus installation
Establishing a CAN bus connection
To establish the CAN-Bus connection to the boiler,
there a two terminals and the associated cable in the
delivery scope.
Fig. 6-1: CAN-bus cable
Only clamp the "Sch" shield on one side. Do not
connect the "+" and "Gnd" wires.
Example: connection to circuit board [GM-C]
A terminal resistor (yellow jumper) must be set at
the end of the CAN-Bus. If both CAN-Bus
terminals are allocated, the terminal resistor must be
removed on this circuit board.
In the example listed above, the terminal resistor must
be removed from the circuit board [GM-C] at [X4] and
set on circuit board [EM-C] at [X1].

16 www.eta.co.at
Contact thermostat Electrical connections
Check the node numbers if the circuit boards are
the same design
If multiple circuit boards of the same design (e.g.: two
[EM-C]) are connected to one another via CAN-bus,
those circuit boards must have different and
consecutive node numbers. In this way they are
recognized in CAN-bus and can be configured.
Therefore, compare the node numbers of the
individual circuit boards of the same design and
set them as needed using the node switch.
6.3 Contact thermostat
Contact thermostat as overheating protection
An additional contact thermostat (ready wired) is
available for protection of the underfloor and wall
heating. It switches off the pump in order to protect the
consumer from feed temperatures that are too high.
1 "NC" contact
2 "NO" contact
3"COM" contact
4 Adjustment dial for activation temperature
The contact thermostat is inserted between the
circuit board terminal and the pump.
Fig. 6-2: Connection of the contact thermostat
Contact thermostat as frost protection
If the secondary side is filled with frost protection
because it is designed as an outdoor heat-
ing system, for example (heating of paths, drives...), a
contact thermostat must be installed for the primary
side in order to prevent the heat exchanger from
freezing. This is mounted on the primary circuit return
and clamped electrically so that the secondary pump
switches off as soon as the temperature set on the
contact thermostat is exceeded (e.g.: 10 °C).
Fig. 6-3: Contact thermostat for primary circuit as frost
protection
1 "NC" contact
2 "NO" contact
3 "COM" contact
4 Adjustment dial for activation temperature

Electrical connections Contact thermostat
17
If a contact thermostat is already mounted on the sec-
ondary side for overheating protection, the additional
contact thermostat is clamped serially to the [EM-C]
circuit board.
1 Contact thermostat for primary circuit (as frost
protection)
2 Contact thermostat for secondary circuit (as
overheating protection)
3 Secondary pump

18 www.eta.co.at
Circuit board EM-C4 Electrical connections
6.4 Circuit board EM-C4
Terminals marked with the symbol are not factory pre-wired.
Terminal Function Default assignment
CAN Node CAN-bus node switch Position "3"
F1 Fuse T 3,15 A (Mains power input)
S100 Supply 230 V Mains power input
S101 230 V output Secondary pump
S102 LA 230 V output Primary pump
S102 LZ 230 V output Free
S103 230 V input Water shortage switch (bridged)
S600 T1 Temperature input Secondary side flow temperature
S600 T2 Temperature input Primary side flow temperature
S600 T3 Temperature input Outside temperature sensor
S600 T4 Temperature input Free
S600 T5 Temperature input Free
S600 T6 Temperature input Free
S601 RS-485 bus Free (digital room sensor)
S602 PWM output / analogue output Free
S603 PWM output Speed control for primary pump
S604 24 V input Free
S605A CAN bus From boiler
S605B CAN bus Free
X1 CAN-Bus terminal resistor
X2 RS-485 terminal resistor
X3 Boot jumper

Commissioning Filling the heating system
19
7 Commissioning
7.1 Filling the heating system
Monitoring the screw joints
Due to vibration and thermal expansion, all screw
joints must be inspected and tightened prior to
commissioning.
Permissible media
• Heating water according to ÖNORM H 5195-1.
The permissible water hardness for the heating
water can be determined from the table in Section
8 "Water hardness".
The requirements of ÖNORM H 5195-1 apply
as minimum requirements for the heating
water. If stricter country-specific regulations exist,
they are to be heeded.
• Water/glycol mixtures with a glycol ratio of
minimum 20% and maximum of 30%
Glycol has a higher viscosity than water.
When admixing glycol, the pumping data
must be corrected according to the mixing ratio.
Proper use includes compliance with these instruc-
tions as well as the information and labelling on the
pump.
Filling and bleeding the heating system
Fill the heating system and take note of the maximum
water pressure. Carefully bleed the heating system
after filling.
Bleeding before commissioning
There is a bleed screw on the top of the module for
bleeding the primary side.
Fig. 7-1: Bleed screw
Bleeding the pump
The heating system must be filled and bled
before the pump can be bled. The pump automat-
ically bleeds itself when starting for the first time. If it
does not, carry out the following steps.
1. If the pump is not in operation, start it manually. To
do this, carry out the following intermediate steps:
a) Up to software version X.35.X
Raise the authorisation to [Service]. Switch to
the inputs and outputs menu in the function
block of the heating circuit [I/O menu] .
Select the heating circuit pump and press the
[Terminal] button. In the open window, switch
on the output manually by pressing the [On]
button.
b) Software version X.36.0 and later
Raise the authorisation to [Service]. Switch to
the inputs and outputs menu in the function
block of the heating circuit . Tap on the
symbol on the heating circuit pump. The pump
is turned on manually with the [On] button, and
turned off by pressing the [Off] button.
2. If the pump is in operation, press the control button
on the pump for 3 seconds.
Fig. 7-2: Venting
3. The venting function now starts and lasts for 10
minutes. The upper and lower LED rows flash
alternately every second.
To cancel, press the control button again for 3
seconds.
After venting, the LED display shows the
operating mode of the pump that was previously
set. After bleeding, the operating mode of the pump
may need to be adjusted.

20 www.eta.co.at
Setting the pump Commissioning
7.2 Setting the pump
Operating modes of the pump
1 Operation: differential pressure variable (Δp-v)
2 Operation: differential pressure constant (Δp-c)
3 Operation: constant speed
4 Operating phase
5 Operating button for setting the operating mode
and operating phase
Differential pressure variable (Δp-v)
• The differential pressure target value "H" is
increased linearly from "½ H" to "H" over the flow
rate "Q." The differential pressure produced by the
pump is set to the respective differential pres-
sure target value.
This operating mode is recommended for
radiators for reducing flow noises on the
thermostat valves.
Differential pressure constant (Δp-c)
• The differential pressure is held constant at the set
differential pressure target value "H".
This operating mode is recommended for
underfloor heating, large pipelines and all ap-
plications without a changeable piping characteris-
tic curve (e.g. hot water, charging pumps).
Table of contents
Popular Heating System manuals by other brands
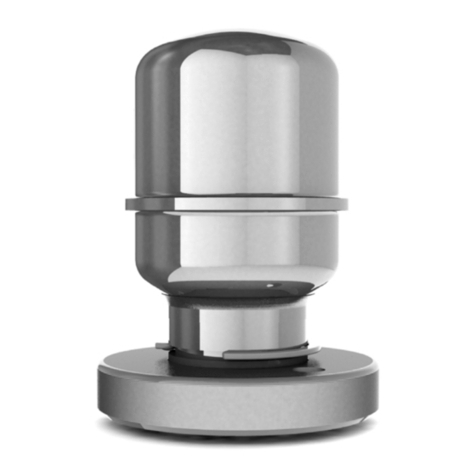
Armstrong
Armstrong SH-2000 Installation and operation manual
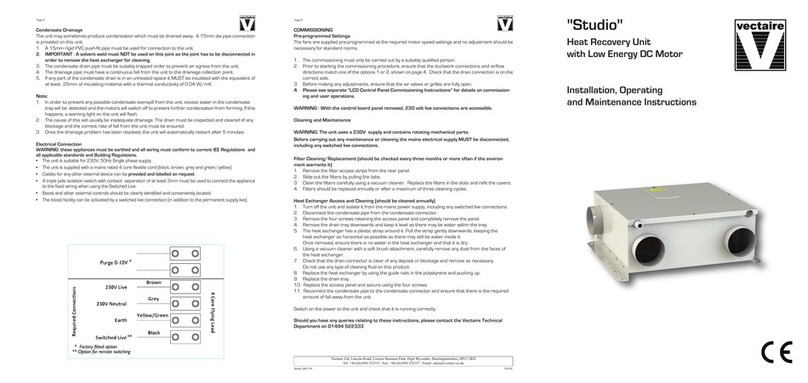
Vectaire
Vectaire Studio Installation, operating and maintenance instructions

Viessmann
Viessmann VITOBLOC 200 Technical description
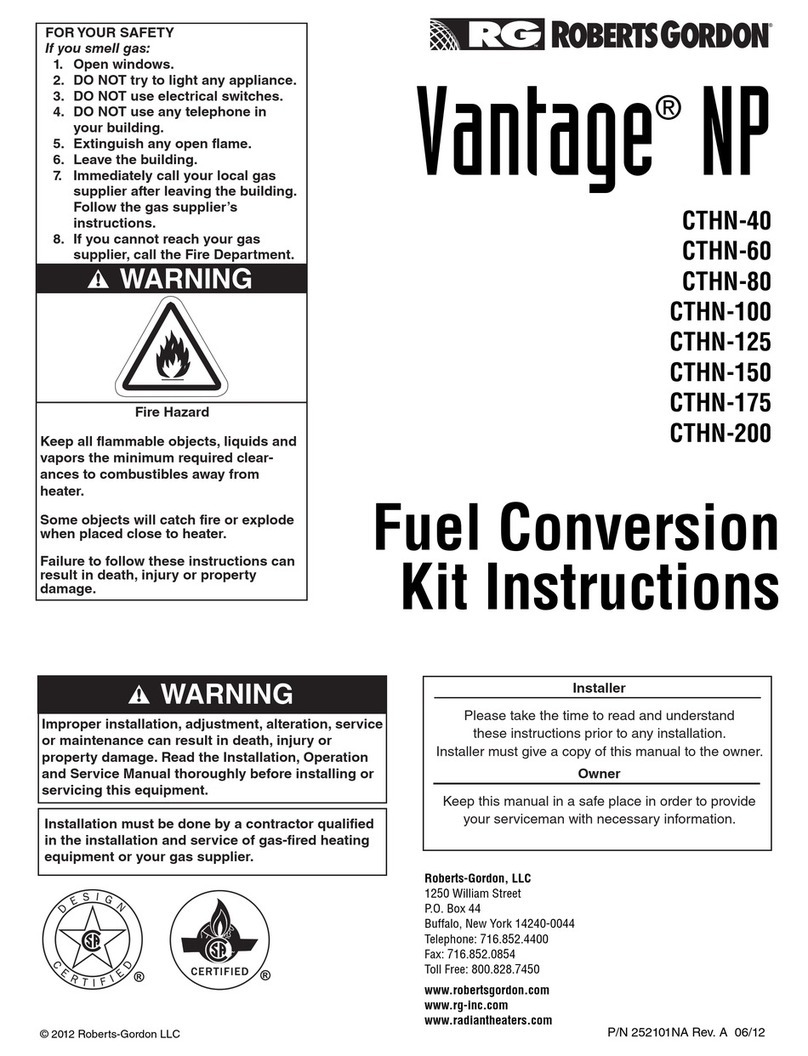
Roberts Gorden
Roberts Gorden VANTAGE NP CTHN-40 Kit instructions

Energotech
Energotech EnergoInfra Industry EIR3000 Mounting and installation
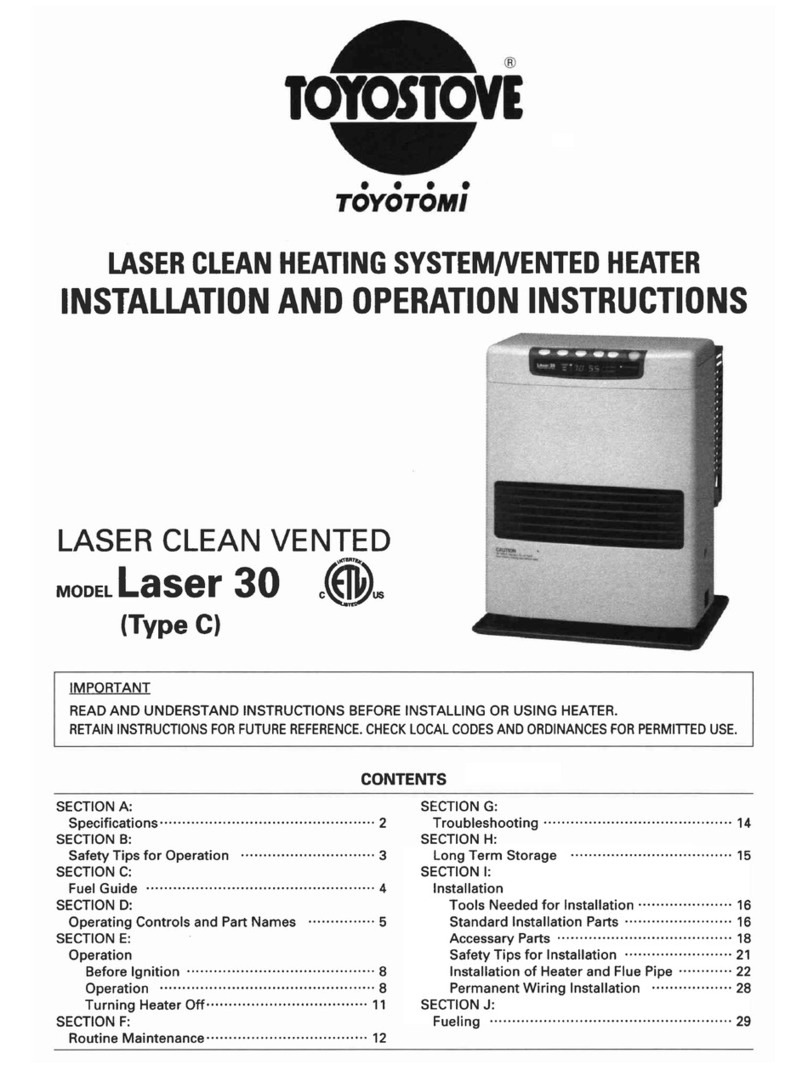
Toyostove
Toyostove Laser 30 Type B Installation and operation instructions
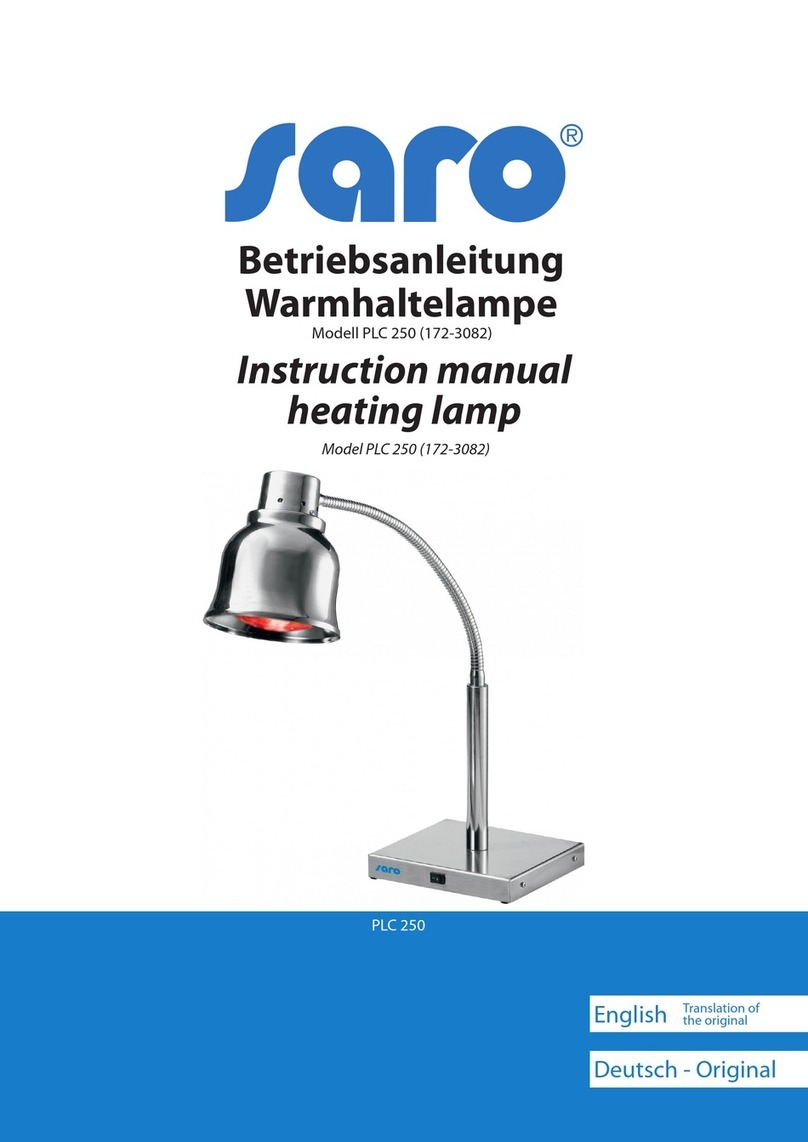
saro
saro PLC 250 instruction manual
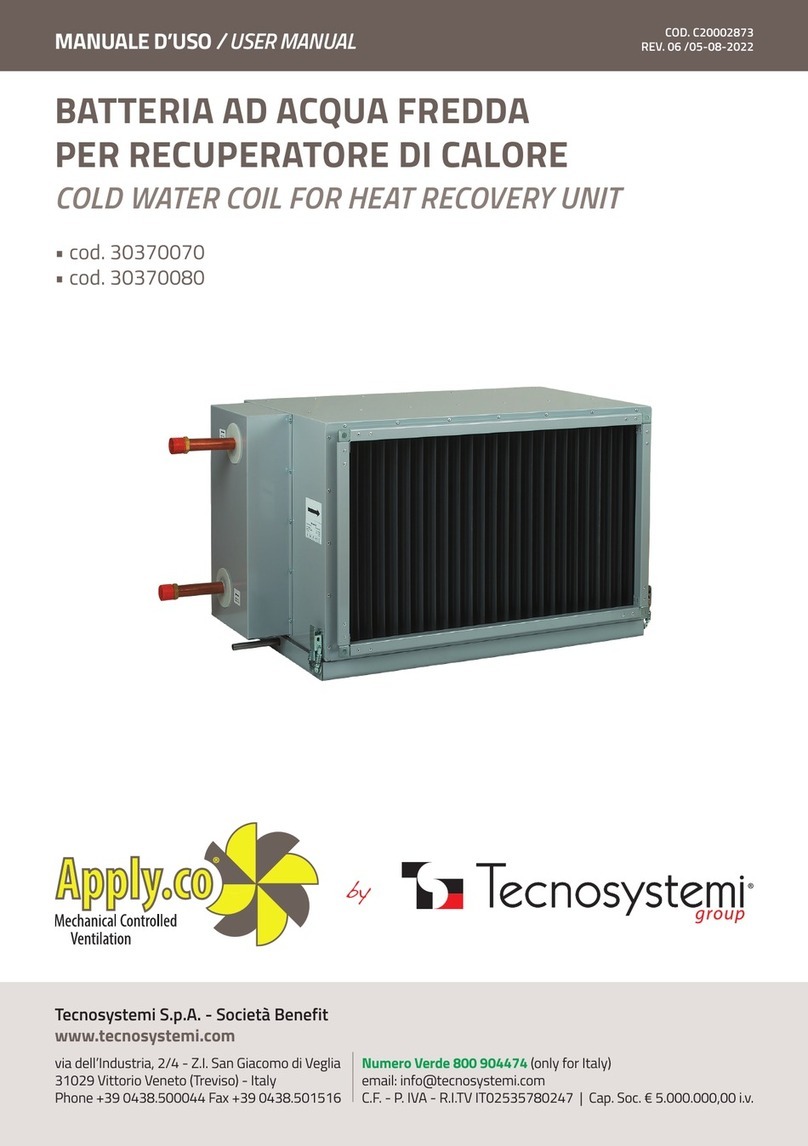
Tecnosystemi
Tecnosystemi Apply. co 30370070 user manual
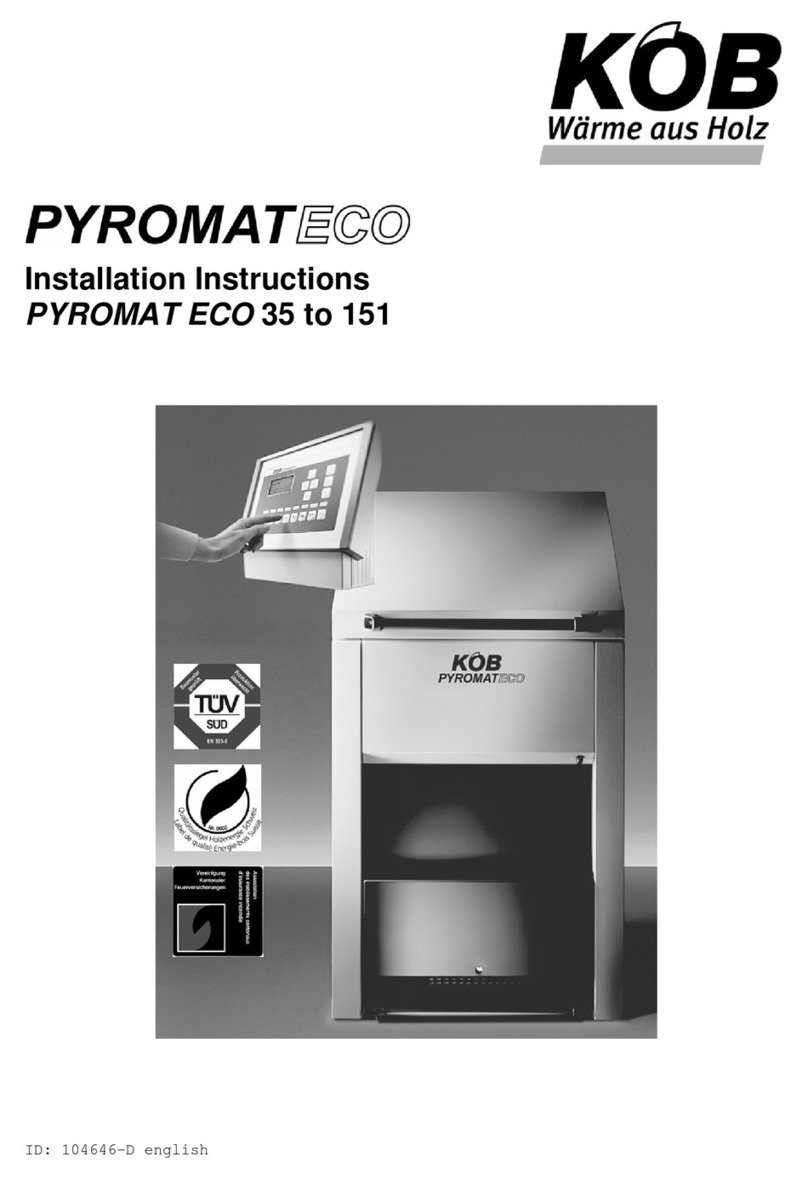
KOB
KOB KOB PYROMAT ECO SERIES installation instructions
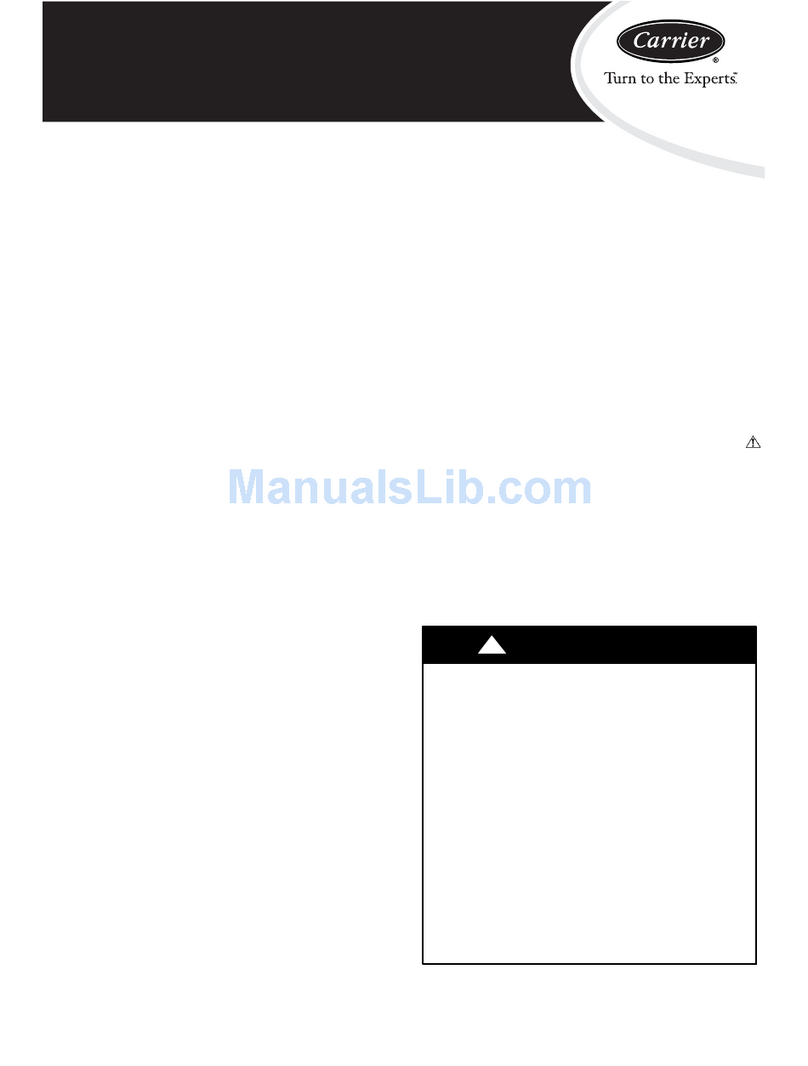
Carrier
Carrier 6 User's information manual
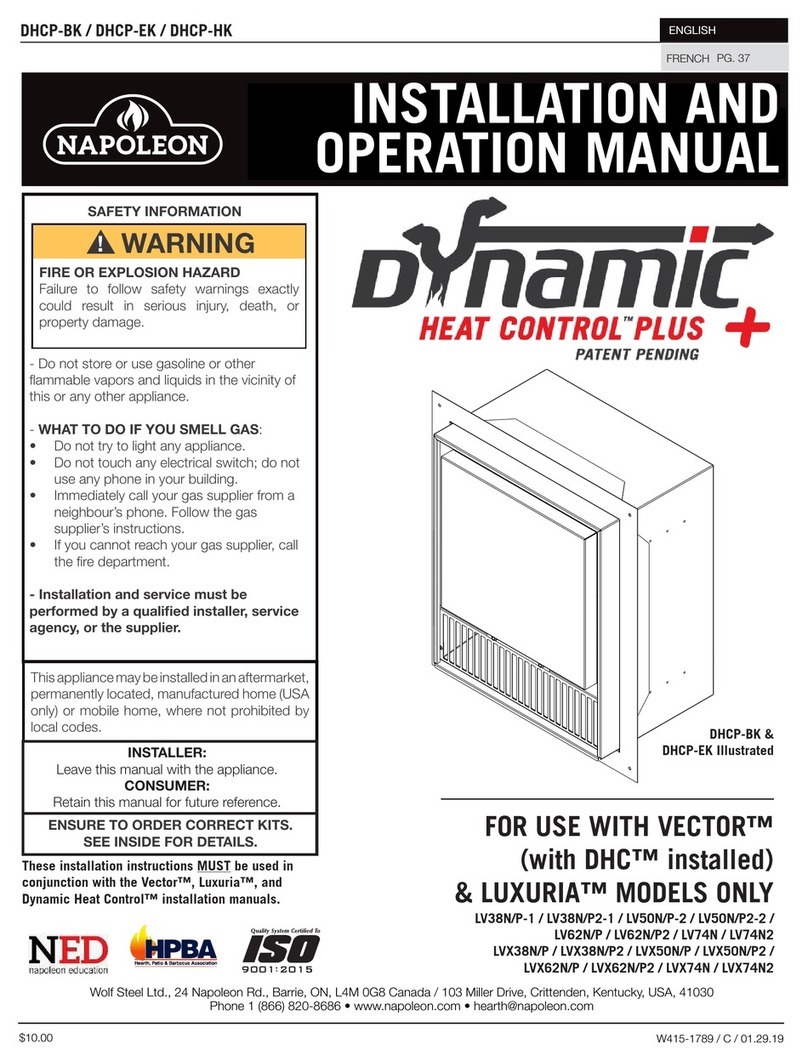
Napoleon
Napoleon DYNAMIC HEAT CONTROL PLUS Series Installation and operation manual

System air
System air SAVE VTC 700 user manual