EVAPCO eco-Air Series User manual

AIR COOLED · ADIABATIC · FLUID COOLERS · CO2GAS COOLERS · REFRIGERANT CONDENSERS
EVAPCO Controller User’s Manual
For EVAPCO authorized parts and
service, contact your local EVAPCO
representative today!

2
Controller User Manual
Table of Contents
Introduction ............................................................................................................................................................................................... 3
EVAPCO Controller ............................................................................................................................................................................ 3
Installation and Wiring .............................................................................................................................................................................. 3
Safety .................................................................................................................................................................................................. 3
Panel Installation Considerations ........................................................................................................................................................ 4
Temperature/Pressure Sensor Installation ......................................................................................................................................... 4
Wiring Considerations ......................................................................................................................................................................... 6
Operation and Servicing ..................................................................................................................................................................... 6
Screen Navigation .................................................................................................................................................................................... 7
Navigating the Display ........................................................................................................................................................................ 7
Modifying a Value ............................................................................................................................................................................... 8
Navigating the Scheduler .................................................................................................................................................................... 8
Operator Interface Screens .................................................................................................................................................................... 10
Welcome Screen ............................................................................................................................................................................... 10
Home Screen .................................................................................................................................................................................... 10
Status Screen ................................................................................................................................................................................... 12
Alarms Screen .................................................................................................................................................................................. 13
Main Menu Screen ............................................................................................................................................................................ 14
On/Off Unit Screen ............................................................................................................................................................................ 15
View Setpoints Screen ...................................................................................................................................................................... 16
Scheduler Screens ............................................................................................................................................................................ 17
Input/Output Screens ........................................................................................................................................................................ 19
Service Screens ................................................................................................................................................................................ 19
Manufacturer Screens ....................................................................................................................................................................... 33
Terminology ............................................................................................................................................................................................ 34
Alarm Event Description ......................................................................................................................................................................... 35
Cover page image: HVAC cooling application, Maryland, USA

3
Controller User Manual
Introduction
EVAPCO Controller
Congratulations on the purchase of your eco-Air unit with the EVAPCO Controller. The EVAPCO Controller will ensure your eco-Air
unit is operating in the most efficient manner possible while using minimal resources. Along with proper eco-Air unit maintenance,
the EVAPCO Controller will ensure that your eco-Air unit provide years of service at peak efficiency.
The EVAPCO Controller serves as a single connection point for the eco-Air unit and contains all of the protection and logic devices
required to run the eco-Air unit in the most efficient manner possible.
In order to reduce downtime, Evapco recommends keeping a stock of spare fuses. Consult the wiring diagram for the quantity, type,
and fuse size required. Contact your local EVAPCO representative for replacement or spare parts.
This bulletin includes a description of the screens and parameters that are available through the display located on the front of the
EVAPCO Controller. Also included in this bulletin are the functions of the EVAPCO Controller. Please note that the screens displayed
on your EVAPCO Controller display may vary slightly from the images shown in this document.
Become familiar with the EVAPCO Controller by thoroughly reading and understanding the content of this bulletin. A detailed wiring
diagram can be found in the data pocket inside of the EVAPCO Controller.
If you should require any additional information about the operation or maintenance of this equipment, contact your local EVAPCO
representative. You may also visit www.evapco.com for more information.
Installation and Wiring
Safety
Qualified personnel should use proper care, procedures, and tools when operating, maintaining, or repairing this equipment or any
other connected equipment in order to prevent personal injury and/or property damage. The warnings listed below are to be used
as guidelines only.
Warning: EVAPCO eco-Air units should never be operated without fan screens and access doors properly secured and in
place.
Warning: Avoid working on electrical circuits while they are live. Proper lock-out/tag-out and all applicable safety practices
must be followed prior to servicing any equipment.
Warning: Before opening the panel door, allow sufficient time for VFD’s to discharge after removing power. VFD’s contain
capacitive circuits which maintain a charge even after power is removed.
Warning: The three-position selector switch is not intended to replace or act as a disconnect to disable the EVAPCO ecoAir
unit and/or de-energize the EVAPCO Controller. Be sure to follow lock-out/tag-out and all applicable electrical
safety practices before servicing any equipment.
Warning: Do not attempt to service or enter the eco-Air unit even if the unit status is indicated as being off. Unless power is
completely removed from the eco-Air unit, it may be possible for the eco-Air unit to start at any time without notice.
Be sure to follow lock-out/tag-out and all applicable electrical safety practices before servicing any equipment.

4
Controller User Manual
The following safety issues need to be addressed by those responsible for the installation, maintenance, and repair of the EVAPCO
Controller:
• Access to the control panel (including the disconnect switch(es)).
• Sizing and protection of electrical circuits feeding the control panel(s) and branch circuits feeding the controlled equipment.
• Proper grounding of electrical circuits.
• Qualification of persons who will install, maintain, and service the electrical equipment.
Panel Installation Considerations
When the EVAPCO Controller does not ship factory mounted on the eco-Air unit, the EVAPCO Controller should be placed in close
proximity to the eco-Air unit to reduce the wire lengths required. If the EVAPCO Controller is within sight of or mounted on the eco-
Air unit, the EVAPCO Controller may be used as the main electrical disconnect for the eco-Air unit. Otherwise, separate electrical
disconnects may be required. Consult applicable electrical codes to make this determination. Avoid mounting the EVAPCO Controller
with a southern exposure. This will minimize the amount of solar heat gain the system will experience and will make it easier to view
the operator interface.
Temperature/Pressure Sensor Installation
EVAPCO eco-Air fluid coolers are supplied with a thermowell (1/2” NPT threads) and a RTD temperature sensor. The thermowell and
temperature sensor should be installed in the common return pipework of the eco-Air fluid cooler unit. Thermowells must be installed
in the horizontal sections of the coil piping. A small amount of thermal paste should be added to the thermowell before the RTD sensor
is inserted to ensure a more accurate fluid temperature measurement.
Figure 1
The suggested temperature sensor location for fluid coolers. Piping shown by dashed lines provided and installed by others.

5
Controller User Manual
EVAPCO eco-Air condensers are supplied with a pressure transducer (1/4” NPT threads). The pressure transducer should be located
in the common compressor hot gas discharge pipework. It is recommended that a shut-off valve be located between the pipework
and the pressure transducer to allow the transducer to be more easily replaced should it become damaged.
Figure 2
The suggested pressure sensor location for condensers. Piping shown by dashed lines provided and installed by others.
When the EVAPCO Controller ships factory mounted to the eco-Air unit, the supplied temperature or pressure sensor must be wired
to the junction box location on the connection end of the eco-Air unit (Figure 3). If the EVAPCO Controller does not ship factory
mounted, the supplied temperature or pressure sensor must be wired to the EVAPCO Controller. Consult the supplied wiring
diagram for a determination if the junction box is supplied.
The junction box is highlighted and circled.
Each EVAPCO Controller is supplied with one ambient air sensor that is located near the Controller enclosure. Should the
EVAPCO Controller not be factory mounted, the ambient temperature probe will need to be wired to the remote location of the
Controller. Consult the supplied wiring diagram for proper termination of the ambient air sensor.
Figure 3

6
Controller User Manual
Wiring Considerations
Consult the supplied wiring diagram for detailed wiring information. All field wiring is indicated by dashed lines on the wiring diagram.
All wiring in and out of the EVAPCO Controller should be with copper conductors and wire lengths must be kept as short as
possible. Consult the detailed wiring diagram for field wiring connections of each device. Applicable electrical codes for the location
should be followed during the sizing and installation of the field wiring. All fittings attached to the EVAPCO Controller must be
Type 4. All wiring must be through the bottom of the EVAPCO Controller. Top entry into the EVAPCO Controller is not
permitted. Any damage caused to any component within or connected to the EVAPCO Controller due to a top entry
connection is not warrantable!
For wiring the EVAPCO Controller to each NEMA fan motor, Belden® VFD cable 295XX (XX denotes gauge) or equivalent should be
used. The shield of the VFD cable needs to be bonded to ground at both ends of the cable.
While the EVAPCO Controller does provide provisions for connection to a BAS (Building Automation System), this connection is not
required for the EVAPCO Controller to operate.
Operation and Servicing
On eco-Air units equipped with NEMA fan motor(s), the EVAPCO Controller contains a three-position selector switch (Bypass-Off-
Auto) located behind the HMI door. The operation of each position is as follows:
Auto: The Auto position allows the EVAPCO Controller to operate the eco-Air unit based on the logic programmed into the
Controller. Note that the unit must be switched on before the eco-Air unit will begin to operate. Please see the On/Off Unit
Screen section of this document for more information.
Off: In the Off position, the EVAPCO Controller will be powered; however, output commands will not be sent to any of the
attached equipment. This position is used for programming the VFD.
Bypass: In the Bypass position, the logic program is bypassed which allows the fan motor(s) to energize independent of sensor
temperature or setpoints. Power is routed around the VFD and thus the fan motor(s) will operate at full power, across- the-line.
The VFD will still be energized when the selector switch is in the Bypass position.
The door protecting the HMI must be shut unless an operator is using the HMI interface. This will protect the HMI interface from
contamination and increase the life of the HMI.
The EVAPCO Controller is supplied with air filters that must be inspected every 90 days. Depending on the installation environment,
more frequent inspection and/or replacement may be required. A dirty filter can cause the internal panel temperature to increase and
may cause component failure. Permanently removing the filter will allow dirt and particulates to enter the enclosure and may cause
premature failure.
Please consult the proper Operation and Maintenance Instructions for start-up and maintenance guides for the eco-Air unit attached
to the EVAPCO Controller.

7
Controller User Manual
Screen Navigation
Navigating the Display
The operator interface contains a 7” touch screen LCD display that allows the user to navigate the various screens as well as view
and modify several setpoints that affect the operation of the eco-Air unit.
The operator interface of the EVAPCO Controller.
Figure 5 provides an overview of the various screens and menus of the EVAPCO Controller. Pressing the Back button will return to
the previous screen. The status button is only present for units equipped with either precooling or EC type fans.
Figure 5
Controller screen flowchart.
Figure 4

8
Controller User Manual
Modifying a Value
To change a parameter on a given screen, first navigate to the desired screen. In this example, the setpoint temperature will be
modified. Once at the desired screen, press the value associated with the parameter and enter the value in the number pad that
appears.
Figure 6
The number pad to change a parameter for the setpoint temperature.
Navigating the Scheduler
Several functions of the EVAPCO Controller can be scheduled to operate during certain periods of the year or at certain times of the
day. In this example, consider a noise restriction from 8:00pm to 5:30am starting Friday night and ending Saturday morning. During
the noise restriction hours, the fan speed will be limited via the Quiet Mode. After navigating to the proper scheduler, the screen shown
in Figure 7 will be displayed.
The Scheduler Screen.
Figure 7

9
Controller User Manual
Each block represents a half hour increment of time. By touching a block, the P icon will appear, and the function will be activated for
that timeframe. Note that the first block represents 12:00am to 12:30am.
The 8:00pm to 12:00am blocks are selected.
Proceed to Saturday by pressing the Next button. Continue to press the blocks to extend the timeframe to 5:30am.
Figure 8
Figure 9
Quiet Mode is active from 12:00am to 5:30am on Sunday.

10
Controller User Manual
Operator Interface Screens
Welcome Screen
When the EVAPCO Controller is first energized, the system will do a self-diagnostic test and load all the interface screens. While the
screens are loading, the EVAPCO logo (Figure 10) appears. After the screens have loaded, the HMI will transition to the Main Home
Screen. If there is no interaction with the HMI for more than fifteen minutes, the EVAPCO logo will reappear. Touching the HMI will
return the screen to the Main Home Screen.
The EVAPCO Controller Welcome Screen.
Home Screen
The Main Home Screen shown in Figure 11 displays the process temperature, ambient temperature, command fan speed, active
setpoint, and the inlet pressure. The inlet pressure is only shown if the eco-Air unit is a condenser. Note, if the eco- Air unit is a
condenser, the process temperature is the saturated condensing temperature derived from the temperature versus pressure
relationship of the refrigerant (see the Service Screens section for more information).
Figure 10
Figure 11
The Main Home Screen.

11
Controller User Manual
If the eco-Air unit is equipped with a pre-cooling system, the status of the solenoid valves are shown at the right hand side of the
screen as shown in Figure 11.
Image
Description
Pre-cooling system is inactive (solenoid valve is closed).
Pre-cooling system is active (solenoid valve is open).
Table 1
The states of the pre-cooling system status indicator.
While there is an active alarm, the Alarms button in the lower left corner of the main home screen (see Figure 12) will highlight. Press
the Alarms button to go directly to the System Alarms Screen.
Main Home Screen with an active alarm.
Figure 12

12
Controller User Manual
Status Screen
The Status Screens provide real time status of the solenoid valves and EC type fans. These status screens are only available with
units equipped with precooling or EC type fans. Note that all values shown on the Status Screens are read only. To view additional
status screens, press the Status button on the main home screen.
When the eco-Air unit is equipped with a precooling system, the Precooling Status screen will be present. The screen indicates the
various timers associated with the control of the precooling system along with the rotation sequence of the solenoid valves.
The increment and decrement timers of the pre-cooling system.
In Figure 13, the Stage #1 and Stage #2-#4 incremental timers indicate if the precooling system is getting ready to activate (increase)
or deactivate (decrease) based on the process temperature. If the process temperature rises past the active temperature setpoint and
the fan speed reaches the current Energy Saving Fan Speed, the increase timer will begin to increment. Once the timer reaches a
predetermined value, the precooling system will activate. Conversely, if the process temperature falls below the process setpoint while
the precooling system is active, the decrease timer will begin to increment until a predetermined value is reached. Once the value is
reached, the associated precooling solenoid valve will close.
If the minimum run time function is enabled, the precooling system remains active for a predetermined amount of time. The times
shown in the Minimum Run Time section will begin to increment until it reaches a predetermined value. The precooling system will
remain active until the minimum on time is satisfied.
When scheduled or manually enabled, the precooling system will undergo a flushing and drying sequence for a predetermined about
of time. Each cycle remains active until the timers shown in the Flush Timers section reach the appropriate duration.
When the precooling system contains multiple stages or solenoid valves, the solenoid or precooling section that enables first will rotate
to balance the run time of the section. The stage will rotate whenever all the valves close. For example, if the eco-Air unit contains
two stages, the first time the precooling system activates, stage one will be activated first followed by stage two. After both stages are
switched off, the next time the precooling system is activated, stage two will be activated first followed by stage one.
Figure 13

13
Controller User Manual
When the eco-Air unit is equipped with EC fan motors, the status and current speed of the fan motors may be viewed. Depiction of
the fans is not reflective of the arrangement of fans on the unit. The live fan motor speeds are in rpm.
Fan Status Screen
Image
Description
EC fan motor is off or is not communicating with the controller.
EC fan motor is online and communicating with the controller.
Table 2
The states of the EC fan motor status indicator.
Alarms Screen
The System Alarms Screen displays all active alarms as well as a log of previous alarms. To scroll through the list, a single touch
scroll up and down is used. The Acknowledge button will change any active alarm from the Active state to Ack. This function is
only meant to record the time at which an active alarm has been acknowledged. The Clear History button will delete all the alarm
entries in the table. Caution: this action cannot be undone, and any alarms cleared will never reappear in the table unless a new
instance of that alarm occurs afterwards. Refer to the Alarm Event Description for a description of the possible alarms.
Figure 15
The Alarms Screen.
Figure 14

14
Controller User Manual
Alarms will appear in the log as either Active, Ack, or Return. Table 3 illustrates each of the three states. The date and time columns
of the table indicate when the alarm was triggered. If an alarm is acknowledged, while active, the time stamp will be displayed in the
ACK Time column. After the condition that triggered the alarm is cleared, the time stamp will be displayed in the RTN Time column.
Status
Image
Active
Ack
Return
Table 3
The states of alarms.
Some alarms require a reset on the operator interface after the triggering condition has cleared. An example is the Vibration Switch
Triggered alarm. When a vibration switch trips, the Reset button will be highlighted as shown in Figure 16 . After the switch is reset
on the unit, the Reset button must be pressed to clear the alarm.
The Alarms Screen with active alarm.
Figure 16

15
Controller User Manual
Main Menu Screen
The Main Menu Screen is available by touching the Menu button on the operator interface. The Main Menu Screen is used to
navigate to additional screens that allow users to modify the current operation of the system or to view additional monitoring
information.
The Main Menu Screen
On/Off Unit Screen
The On/Off Control screen shows and allows the operator to set the current operational status of the eco-Air unit. When the eco-Air
unit is not controlled via an external source (i.e. BAS), the On/Off Control screen is the only way to disable the eco-Air unit without
removing power. Note that the EVAPCO Controller must be switched on locally before the unit will operate even if the EVAPCO
Controller is being controlled via a BAS or digital input.
The On/Off Unit Screen.
Figure 17
Figure 18

16
Controller User Manual
The various operational states of the eco-Air unit are explained in the following table:
Status
Description
Unit On
Unit is operational.
Off by BMS
Unit is being controlled via a BAS and may be enabled by sending an enable signal
to the EVAPCO Controller.
Off by Digital Input
Unit is being controlled via a digital input and may be enabled by sending an enable
signal to the EVAPCO Controller.
Off by HMI
Unit is turned off manually and may only be enabled via the On/Off Control Screen.
Off by Alarm
The unit has been turned off due to an alarm.
Table 4
The operational states of the unit and their descriptions.
View Setpoints Screen
The View Setpoints Screen allows viewing of all setpoint parameters. For a detailed description of the setpoints and instructions on
how to change the various setpoints and options, please see the Service Screens section of this document.
Figure 19
One of the screens that allows viewing, but not editing of setpoints and options.

17
Controller User Manual
Scheduler Screens
The Scheduler Screens allows the internal clock of the EVAPCO Controller to be set as well as the scheduling of several routines. If
enabled, the following routines may be programmed during certain periods of certain days:
Routine
Function
Example Use
Quiet Mode
Limits the maximum fan speed to the
value set for quiet operation.
There is noise restriction during nighttime periods due to close
proximity of residences.
Setpoint #2
Switches the active setpoint to an
alternate value.
The cooling load is for an office building which does not require as
much cooling during off hours.
Daily Flush
The pre-cooling system is activated
to run water over the adiabatic
pads.
The unit installation site is located next to a field. The flush routine
runs at night to rinse any debris that may have been sucked onto the
adiabatic pads during unit operation.
Table 5
The various functions that may be scheduled hourly.
For instruction on setting the scheduler, please see the Navigating the Schedule section of this document. Note that unless the desire
routine is set to run via the scheduler (except the flush routine), the scheduler will not operate as selected.
If equipped with a precooling system, the precooling system may be set to run only during certain dates. In climates that are subject
to freezing temperatures or if there is a reduced cooling load during certain periods of the year, the scheduler may be used to disable
the precooling system. Note that all pipework that is susceptible to freezing must be heat traced to avoid damage. When the
scheduler is enabled, the precooling system will only operate during the dates shown in the screen. When in the Enabled state, the
precooling system will activate when required as long as all conditions (e.g. enabled for scheduler, ambient is above lower limit, etc.)
are satisfied. When changed to Disabled, the precooling system will not activate even if additional cooling is required.
The precooling system scheduler.
Parameter
Description
Default
Flushing Time
The amount of time that water flows over the
adiabatic pads.
0 minutes
Drying Time
The amount of time that the fans run in reverse
(EC Type Only) during the flushing routine.
0 minutes
Fan Speed
The fan speed (reverse) during the dry cycle of
the flushing routine.
0%
Table 6
The flushing routine parameters.
Figure 20

18
Controller User Manual
The internal clock of the EVAPCO Controller may be set in the screen shown in Figure 21. If any of the scheduler functionality of the
EVAPCO Controller is used, it is vital that the clock be set to the proper time. The clock is used to add timestamps to the alarms
shown in the System Alarms screen. To adjust the time, the New Date:, Day of Week:, and New Time: must all reflect the desired
date/time. After entering the information press the Update button.
The Clock Adjustment Screen.
Daylight savings can be enabled in the screen shown in Figure 21. Table 7 gives a description of the functionality based on the zone
that is selected.
Zone
Description
Disabled
Daylight saving functionality is disabled
Europe
Daylight saving functionality will start on last Sunday of March at
1:00 a.m. DST and end on last Sunday of October at 2:00 a.m.
US/Canada
Daylight saving functionality will start on second Sunday of
March at 2:00 a.m. local time and end on first Sunday of
November at 3:00 a.m.
Table 7
The DST Parameter Selection.
Figure 21

19
Controller User Manual
Input/Output Screens
Figure 22 displays the current state of all digital inputs, digital outputs, analog inputs, and analog outputs of the EVAPCO Controller.
This screen is primarily used for troubleshooting and start-up purposes to determine if the correct signals are being sent to and from
the EVAPCO Controller.
Service Screens
The Service Screens allow the user to change setpoints, timers, and other parameters that affect the operation of the eco-Air unit.
The Service menu is inaccessible until logging in. Figures 23 illustrate the steps that need to be taken to unlock the Service button.
The password for the Service level log in is 1234. If an incorrect password is entered, the screen will show Invalid Password.
Figure 23
Service level log in to access the Service Menu.
Figure 22
The Digital I/O Status Screen and the Analog I/O Status Screen.

20
Controller User Manual
After logging in and pressing the Service button, the screen will display the service submenu options as shown in Figure 24. If the
unit is enabled the options for I/O Test and BMS & Network will not be available. Turn the unit off to enable these options, as shown
in Figure 25.
The service submenu.
The service submenu while the unit is turned off.
Figure
24
Figure 25
Table of contents
Other EVAPCO Controllers manuals
Popular Controllers manuals by other brands

Honeywell
Honeywell SEC-H-600 installation instructions
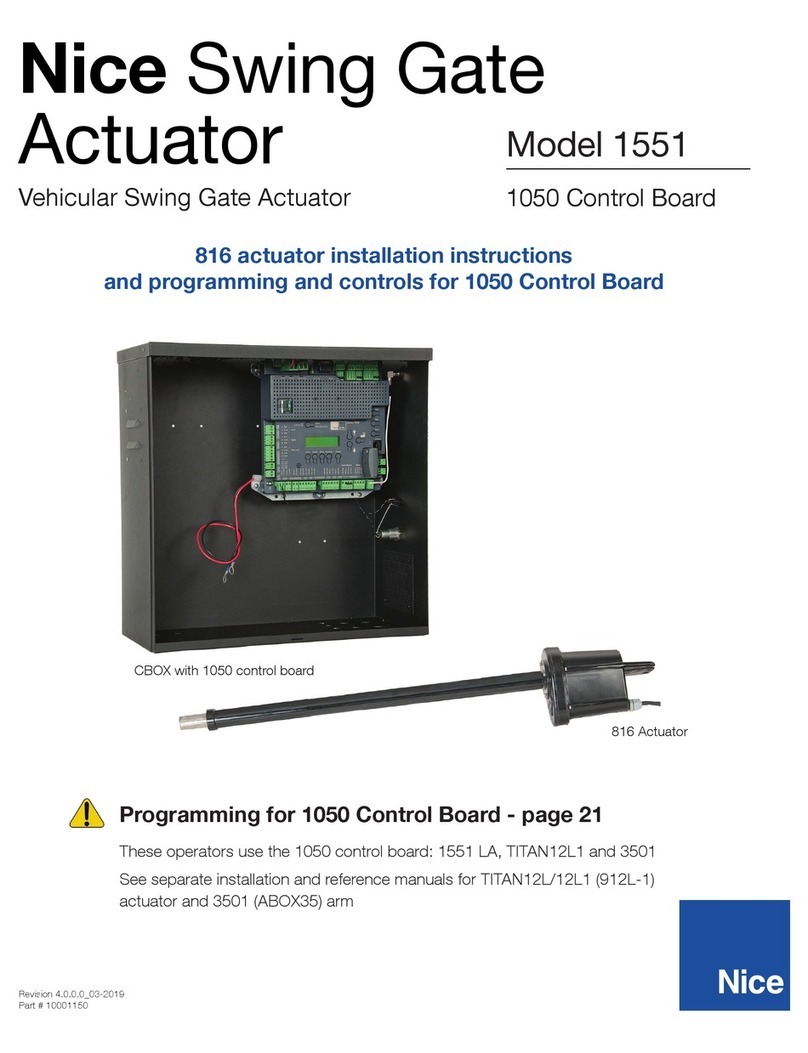
Nice
Nice 1551 installation instructions

Festo
Festo LRP-1/8-6 operating instructions
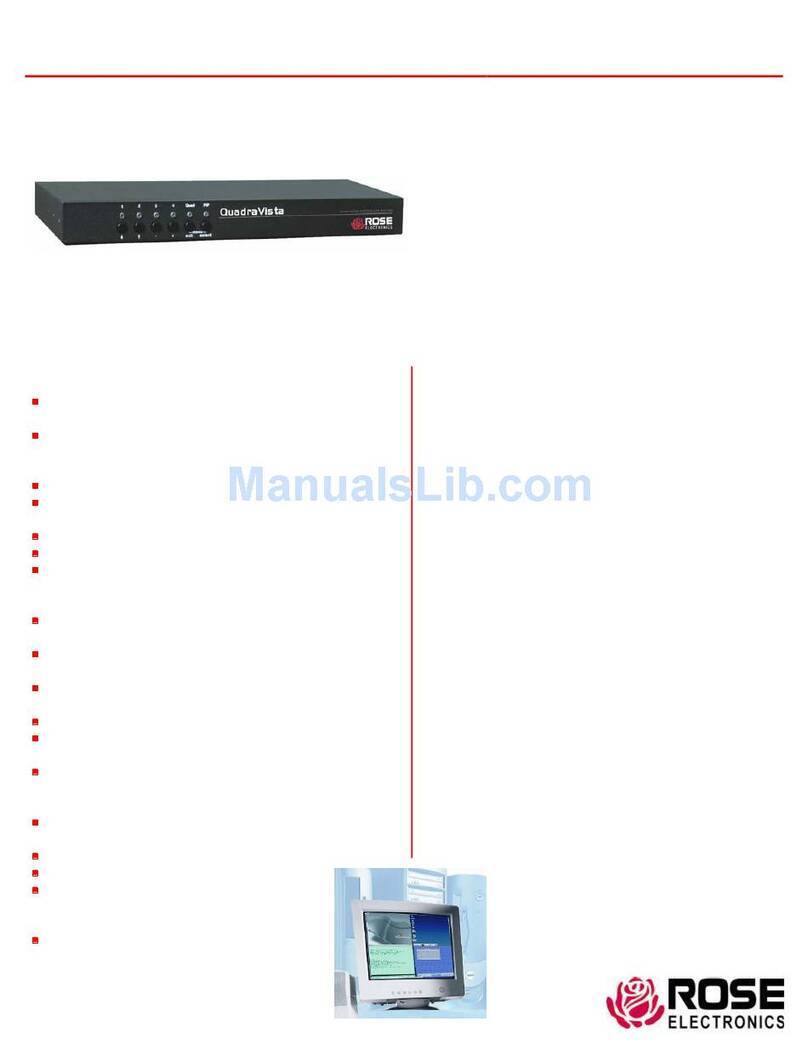
Rose electronics
Rose electronics QuadraVista QV-4KVMDVI Specifications
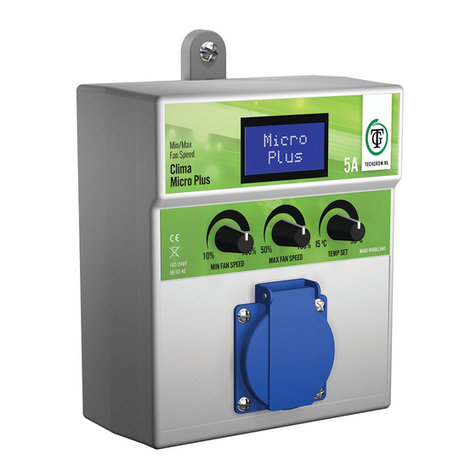
TechGrow
TechGrow Clima Micro Plus Min/Max Fan Speed user manual

SICK
SICK Flexi Classic operating instructions