Motion AXIS STUIFMEEL Thomson PC-Series User manual

Thomson PC-Series™
Precision Linear Actuator
Installation Manual
Edition 2014-01
DW110697GB

Thomson
Thomson PC-Series™ Precision Linear Actuator - Installation Manual - June 20142
Version History
Edition Reason for revision
2014-01 First edition
Warranty
The Thomson PC-Series™ is warranted to be free from defects in materials and workmanship for a
period of twelve (12) months from date of delivery. The application of this product is the responsibility
of the buyer and Thomson makes no representation or warranty as to the suitability of the product for
any particular use or purpose. For a copy of the entire warranty for this product that is contained in our
standard terms and conditions of sale, please go to http://www.thomsonlinear.com/website/com/
eng/support/terms_and_conditions.php.
Disclaimer
Technical changes to improve the performance of the equipment may be made without prior notice!
All rights reserved. No part of this work may be reproduced in any form (by printing, photocopying,
microlm or any other method) or processed, copied or distributed by electronic means without the
written permission of Thomson.

Thomson
Thomson PC-Series™ Precision Linear Actuator - Installation Manual - June 2014 3
Contents
1. General ...................................................................................................... 4
1.1 About this manual................................................................................................. 4
1.2 Target group ......................................................................................................... 4
1.3 Symbols used....................................................................................................... 4
1.4 Transport and storage .......................................................................................... 4
1.5 Disposal................................................................................................................ 4
1.6 Support................................................................................................................. 4
2. Safety 5
2.1 Safety notes ......................................................................................................... 5
3. Standards.................................................................................................. 5
3.1 EC Declaration of conformity................................................................................ 5
4. Installation ................................................................................................ 6
4.1 Name plate ........................................................................................................... 6
4.2 Terminology .......................................................................................................... 6
4.3 Operation environment ........................................................................................ 6
4.4 General mounting guidelines................................................................................ 7
4.5 Mounting of the unit using the mounting holes..................................................... 8
4.6 Mounting of the unit using the extension tube rod end......................................... 9
4.7 Mounting of the unit using the mounting accessories ........................................ 10
4.8 Mounting of sensor brackets .............................................................................. 15
4.9 Mounting of sensors in the sensor brackets....................................................... 15
4.10 Motor installation on inline style actuators without RediMount system .............. 15
4.11 Motor installation on actuators with RediMount system ..................................... 15
5. Service and maintenance ...................................................................... 18
5.1 General............................................................................................................... 18
5.2 Cleaning ............................................................................................................. 18
5.3 Lubrication.......................................................................................................... 18
5.4 Replacement of coupling on inline models with RediMount ange .................... 19
5.5 Replacement of belt gear timing belt.................................................................. 20
6. Technical specications ........................................................................ 22
6.1 Technical data .................................................................................................... 22
6.2 Type designation key.......................................................................................... 23
6.3 Screw tightening torque...................................................................................... 23
Contents

Thomson
Thomson PC-Series™ Precision Linear Actuator - Installation Manual - June 20144
General
1. General
1.1 About this manual
This manual decribes how to install the Thomson PC-Series precision linear actuator mechanically and
electrically. It also contains, among other things:
• technical data
• dimensional drawings
• type designation key.
It is important to carefully read this manual before installing the actuator and to have the correct
qualications needed to perform the installation.
1.2 Target group
This manual addresses qualied mechanical and electrical personnel.
1.3 Symbols used
This symbol is shown to highlight a general warning, general instruction or as a warning for a
mechanical hazard.
1.4 Transport and storage
The actuator may only be transported and stored in the original packaging supplied by Thomson. The
temperature during transportation and storage must be between -40 to +85 °C (-40 to +185 °F). Avoid
shocks to the package. If the package is damaged, check the actuator for visible damage and notify the
carrier, and if appropiate also Thomson.
1.5 Disposal
Where required by law, used packaging and actuators are taken back by Thomson for professional
disposal if the transportation cost is taken over by the sender. Please contact Thomson for information on
where to ship it.
1.6 Support
In case you need technical support or any information related to this product, please contact the nearest
Thomson Service Center. See the back of this manual. You can also visit www.thomsonlinear.com for
information on this product and how to get in touch with us.

Thomson
Thomson PC-Series™ Precision Linear Actuator - Installation Manual - June 2014 5
Safety and Standards
2. Safety
2.1 Safety notes
• Only properly qualied personnel are permitted to perform mechanical and electrical
installation, service or maintenance on this product. Properly qualied personnel are familiar with
mechanical or electrical installation work and that have the appropiate qualications for their jobs.
• Read this manual and any other available documentation before working on the equipment.
that the actuator is or shall be a part of.
• Keep strictly to the data in this manual and on the name plate on the actuator and never
exceeed the performance limits stated herein.
• Never work on the actuator or its installation with the power on.
• Never unplug any cables or connectors during operation or with power on.
• Immediately stop using the actuator if it seems faulty or broken in any way and notify an
appropiate person so that corrective actions can be taken.
• Never try to open the actuator as that will compromise the sealing and the function of the
actuator. There are no serviceable components inside.
• Grease may be present on the extension tube. Contact is non-hazardous. Film should not be
removed.
3. Standards
3.1 EC Declaration of conformity
We, Tollo Linear AB
declare that this products corresponds with the directive 2006/42/EC annex 2.1.B, RoHS II directive
2011/65/EU, WEEE directive 2002/96/EC, low voltage directive 2006/95/EC (EN60204-1:2006+A1:2009)
and also with the directive of electromagnetic compatibility 2004/108/EC (EN55014-1:2006+A1:2009,
EN61000-6-3:2007, EN61000-3-2:2006+A2:2009, 61000-3-3:2008) and that the standard EN ISO
12100:2010, Safety of machinery, have been applied.
Thomson Precision Linear Actuator PC
Product Description
Can be used when the machine or the system, which it shall be, a part of is in accordance with the
demands in the EEC Machinery Directive and/or other relevant regulations.
Kristianstad 2014-04-14
Date
Anders Trygg Business Unit Manager
Name Title Signature

Thomson
Thomson PC-Series™ Precision Linear Actuator - Installation Manual - June 20146
4. Installation
4.1 Name plate
The name plate can be found on the actuator cover tube. It will tell you which model of actuator you
have and its basic performance data. Please study the name plate to see what type of actuator you have
before starting any installation or service on the actuator. If you need any assistance from Thomson,
please tell us the manufacturing date and the designation of the actuator(s) in question.
4.2 Terminology
A. inline style PC-Series actuator without RediMount system
B. inline style PC-Series actuator with RediMount system
C. parallel style PC-Series actuator with belt gear and RediMount system
Installation
1. input shaft 5. front adaptor 9. access plug for coupling clamping element
2. motor ange plate 6. RediMount system 10. belt gear with Redimount system
3. grease port 7. cover tube
4. front plate 8. extension tube

Thomson
Thomson PC-Series™ Precision Linear Actuator - Installation Manual - June 2014 7
4.3 Operation environment
Operation temperature range is between -20 to +70° Celcius. Protection degree against the ingress of
water and particles is IP65.
4.4 General mounting guidelines
The unit can be mounted in any direction but do not mount the actuator so that the cover tube is
subjected to any bending or twisting forces.
Mount actuator so that the the maximum permissible load and load torques for the input shaft or the
extension tube never are exceeded during stand still or operation. See table T6.1.1 for load and load
torque data for each model.
Make sure to install the actuator so that the extension tube never runs in to the mechanical end stops.
The distance between the mechanical end stops (Send) are the ordering stroke (Smax) plus 2.5 (± 0.5)
mm of extra travel in both ends (Safe).
Warning! Do not hold the extension tube while the unit is energized.
Warning! The extension tube is not self holding - in a vertical application a brake is required to
hold the load at stand still. If it is removed the extension tube may start moving with the possible
risk of injury to people or damage to the equipment.
Warning! Never run in to the mechanical ends of the unit.
Installation
Min. -20° C Max. +70° C IP65

Thomson
Thomson PC-Series™ Precision Linear Actuator - Installation Manual - June 20148
4.5 Mounting of the unit using the mounting holes
All PC-Series actuators have mounting holes in the front plate while the parallel style also have mounting
holes in the rear plate on the belt gear. The mounting holes can be used to attach the unit to the support
or to the mounting accessories designed for the purpose (see point 4.7). Make sure to follow the general
mounting guidelines (see point 4.4) when using the mounting holes.
4.5.1 Mounting of the unit using the front plate mounting holes
See below drawings for hole pattern, size and thread depth of the front mounting holes. Note that the
mounting holes on PC32 and PC40 has a 14 mm long unthreaded part before the thread starts.
PC25 PC32 PC40
4.5.2 Mounting of the unit using the rear plate mounting holes on parallel style units
See below drawings for hole pattern, size and thread depth of the rear mounting holes.
PC25 PC32 PC40
Mounting hole size Total mounting hole depth [mm] Outer unthreaded depth [mm] Inner threaded depth [mm]
PC25 M3 14 0 14
PC32 M6 44 14 30
PC40 M6 44 14 30
Mounting hole size Mounting hole thread depth [mm]
PC25 M5 8
PC32 M6 8
PC40 M6 8

Thomson
Thomson PC-Series™ Precision Linear Actuator - Installation Manual - June 2014 9
4.6 Mounting of the unit using the extension tube rod end
The extension tube rod end always have either a male or a female threaded rod end mounted from the
factory. A spherical joint (see point 4.7.1) or a clevis (see point 4.7.2) can also be mounted to the male
threaded rod end, either from factory or by the customer as a seperate part in which case you must
follow the below instructions plus the instructions for the spherical joint or the clevis. The designation on
the name plate and the ordering key (table T6.2.1) will help you determine which rod end accessory the
unit is equipped with. If a spherical joint or a clevis is delivered as a seperate part you have to determine
which of them it is (see part number on the accessory packaging labels) and the actuator model (see
the name plate) and follow the appropriate instruction to mount it (see point 4.7.1 or 4.7.2). If in doubt,
contact customer support
1. Male threaded rod end
2. Female threaded rod end
The extension tube can handle some side load (see table T6.1.1 for load and load torque data for each
model) but in order to improve overall performance and life it is good practice to follow the below points
even if the side loads do not exceed the maximum permitted levels.
• Make sure the extension tube travel in a straight line in relation to the cover tube.
• Try to align the center of the load with the extension tube travel center.
• Avoid side loads altogether if possible.
A B
PC25 22 M10 × 1.25
PC32 22 M10 × 1.25
PC40 26 M12 × 1.25
A B
PC25 15 M10 × 1.25
PC32 15 M10 × 1.25
PC40 18 M12 × 1.25

Thomson
Thomson PC-Series™ Precision Linear Actuator - Installation Manual - June 201410
4.7 Mounting of the unit using the mounting accessories
The unit can be shipped with mounting accessories mounted from the factory, in this case the
designation on the name plate and the ordering key (table T6.2.1) will help you determine which
accessory the unit is equipped with and which mounting instruction below to follow. Some of these
mounting accessories can also be ordered as seperate parts and be mounted to the actuator by the
customer. In this case you have to determine which accessories (see part number on the accessory
packaging labels) and actuator model (see the name plate) you have and select appropriate instructions.
If in doubt, contact customer support.
4.7.1 Spherical joint
To be able to mount a spherical joint the
extension tube must be equipped with a male
threaded rod end. Screw the joint on to the
rod end and secure it with the jam nut. Use a
solid pin to connect the joint to the load. Keep
in mind that any play between the pin and the
joint may affect the accuracy.
4.7.2 Front clevis
To be able to mount a separate front clevis the
extension tube must be equipped with a male
threaded rod end. Screw the clevis on to the rod
end and secure it with the jam nut.
A (REF.) * B (REF.) * C D (Ø) E (H9) F G H p/n
PC25 50 64 28 10 10.5 14 19 17 D607 406
PC32 50 64 28 10 10.5 14 19 17 D607 407
PC40 58 74 32 12 12 16 22 19 D607 408
* assuming 2 mm gap from jam nut to shoulder.
* assuming 2 mm gap from jam nut to shoulder.
A (REF.) * B (REF.) * C D (Ø h11) E (B11) F p/n
PC25 47 59 20 10 10 20 D607 409
PC32 47 59 20 10 10 20 D607 410
PC40 56 70 24 12 12 24 D607 411

Thomson
Thomson PC-Series™ Precision Linear Actuator - Installation Manual - June 2014 11
4.7.3 Rear clevis - for PC25 parallel style models
The rear clevis it mounted to
the rear plate of the belt gear
housing. All necessary screws
to attach it to the actuator is
included. Make sure to tighten
all four screws according to table
T6.3.1. Use a solid pin to connect
the joint to the load. Keep in mind
that any play between the pin and
the joint may affect the accuracy.
4.7.4 Rear clevis - for PC32 and PC40 parallel style models
The rear clevis it mounted to the
rear plate of the belt gear housing.
All necessary screws to attach it to
the actuator is included. Make sure
to tighten all four screws according
to table T6.3.1. Use a solid pin to
connect the joint to the load. Keep
in mind that any play between the
pin and the joint may affect the
accuracy.
A B C D E (Ø H9) F G H (h14) I p/n
PC25 36 45 92 51 8 64 72 16 38 D607 412
A B C D E (Ø H9) F G H (H14) I p/n
PC32 35,5 60 117 64,5 10 65.5 75,5 26 45 D607 413
PC40 42,5 70 136 73,5 12 75.5 88 28 52 D607 414

Thomson
Thomson PC-Series™ Precision Linear Actuator - Installation Manual - June 201412
4.7.5 Front mounting plate
The front mounting plate it mounted to the
front plate of the cover tube. All necessary
screws to attach it to the actuator is
included. Make sure to tighten all four
screws according to table T6.3.1.
4.7.6 Foot mount for inline style models
The foot mount consists of
a front and rear bracket. All
necessary screws are to attach
it to the actuator is included.
Make sure to tighten all
attachement screws according
to table T6.3.1.
A B C D E F p/n
PC25 60 10 6.6 (2×) - 40 76 D607 415
PC32 64 10 7.0 (4×) 32 45 80 D607 416
PC40 72 10 9.0 (4×) 36 52 90 D607 417
A (JS15) B C D E F G H I J K L p/n
PC25 30 26 52 37 6.6 6.6 16 64 15 22 8.5 28 D607 418
PC32 32 32 65 45 6.6 6.6 24 78 15 35 8.5 35 D607 419
PC40 36 36 70 52 9 6.6 28 85 15 36 8.5 38.5 D607 420

Thomson
Thomson PC-Series™ Precision Linear Actuator - Installation Manual - June 2014 13
4.7.7 Foot mount for parallel style models
The foot mount consists of a front
and rear bracket. All necessary
screws are to attach it to the
actuator is included. Make sure
to tighten all attachement screws
according to table T6.3.1.
4.7.8 Fixed front trunnion
The xed front trunnion consist
of a plate with two shafts. All
necessary screws are to attach
it to the actuator is included.
Make sure to tighten all
attachement screws according
to table T6.3.1. Contact your
local bearing supplier for advice
on suitable bearings between
the trunnion pins and the
support.
A B C D E F G H p/n
PC25 30 26 26 37 6,6 16 16 40 D607 421
PC32 32 32 32 45 6,6 24 24 45 D607 422
PC40 36 36 52 52 9 28 28 52 D607 423
A (REF.) B (h14) C (h14) D (e9) E p/n
PC25 66 42 12 12 14 D607 424
PC32 74 50 12 12 14 D607 425
PC40 95 63 16 16 19 D607 426

Thomson
Thomson PC-Series™ Precision Linear Actuator - Installation Manual - June 201414
4.7.9 Fixed rear trunnion for parallel style models
The xed rear trunnion consist of a plate with
two shafts. All necessary screws are to attach
it to the actuator is included. Make sure to
tighten all attachement screws according
to table T6.3.1. Contact your local bearing
supplier for advice on suitable bearings
between the trunnion pins and the support.
4.7.10 Movable cover tube trunnion
The movable trunnion consists
of two clamp units that are put
around the prole of the unit
at desired position and joined
and locked in place by the lock
screws. Make sure to tighten
the lock screws according to
table T6.3.1. Contact your local
bearing supplier for advice on
suitable bearings between the
trunnion pins and the support.
A (REF.) B (h14) C (h14) D (e9) E p/n
PC25 66 42 12 12 14 D607 433
PC32 74 50 12 12 14 D607 434
PC40 95 63 16 16 19 D607 435
A B C (h14) D (Ø e9) E F (h14) p/n
PC25 45 51 45 12 19 12 D607 427
PC32 74 65 50 12 25 12 D607 428
PC40 95 75 63 16 28 16 D607 429

Thomson
Thomson PC-Series™ Precision Linear Actuator - Installation Manual - June 2014 15
4.8 Mounting of sensor brackets
The bracket can be installed over the left or
right corner of the cover tube surface under
which the sensor magnet travels. The correct
cover tube surface is marked with a magnet
sign sticker (1). The bracket (2) is secured
using the worm drive clamp (3) that are put
around the cover tube and the bracket. Make
sure the clamp tigthening screw is correctly
positioned in the slot of the bracket.
4.9 Mounting of sensors in the sensor brackets
The sensor is inserted in the slot of the sensor bracket
and locked in to position by the clamp screw (1).
If the sensor is mounted in the immediate
vicinity of magnetisable components, the
switching characteristics of the sensor may change.
4.10 Motor installation on inline style actuators without RediMount system
The motor installation on a PC-Series actuator
without a RediMount ange require either a
suitable bell house type of ange and a coupling
or a gearbox to be mounted between the motor
and the actuator. The ange dimensions for each
actuator size can be found in the table bellow.
Make sure that the maximum permissible drive
shaft force and torque are not exceeded (see
table T6.1.1.) at any time during stand still or
operation.
4.11 Motor installation on actuators with RediMount system
The motor installation on a PC-Series actuator with a RediMount ange require a suitable motor for the
RediMount ange type the actuator in question is equipped with. Follow point 4.11.1 or 4.11.2 during
installation depending on if the actuator are of inline or parallel style. Make sure that the maximum
permissible drive shaft force and torque are not exceeded (see table T6.1.1.) at any time during stand still
or operation. For removal of a motor see point 4.11.3.
A B C D E F G
PC25 6 14.5 2.5 44 M4 24 27
PC32 8 16.5 2.5 44 M6 32,5 34
PC40 12 18.6 2.4 44 M6 38 41

Thomson
Thomson PC-Series™ Precision Linear Actuator - Installation Manual - June 201416
4.11.1 Motor installation on inline style models with RediMount system
1. Make sure the extension tube is fully retracted
and then remove the sealing plug.
2. Press the motor shaft on to the coupling inside
of the ange.
3. Bolt the motor to the ange using four screws.
Tighten the screws according to table T6.3.1.
4. Use a hexagon key to tighten the coupling
around the motor shaft. Correct tightening
torque for PC25 models = 0.85 Nm and for
PC32 and PC40 = 2.0 Nm.
5. Put the sealing plug back.

Thomson
Thomson PC-Series™ Precision Linear Actuator - Installation Manual - June 2014 17
4.11.2 Motor installation on parallel style models with RediMount system
1. Make sure the extension tube is fully retracted
and then remove the sealing plug.
2. Press the motor shaft on to the coupling inside
of the belt gear ange.
3. Use a hexagon key to tighten the coupling
around the motor shaft. Correct tightening
torque for PC25 models = 0.85 Nm and for
PC32 and PC40 = 2.0 Nm.
4. Bolt the motor to the ange using four screws.
Tighten the screws according to table T6.3.1.
5. Put the sealing plug back.
4.11.3 Removal of motor from a unit with RediMount system
If removing a motor from a unit with RediMount system the extension tube must be fully extended to
make it possible to losen the coupling.

Thomson
Thomson PC-Series™ Precision Linear Actuator - Installation Manual - June 201418
5. Service and maintenance
5.1 General
Regularly perform occular control of the PC-Series unit and the installation it is a part of and service and
repair if needed. If in doubt, please contact Thomson for advice.
5.2 Cleaning
The PC-Series actuators are designed to withstand water wash down. If the actuator needs to be
cleaned, clean it gently and do not use any tools that mechanically can damage the actuator. If
detergents are to be used during cleaning it is recommended to stay within pH 3.5 – 8.5.
5.3 Lubrication
Lubrication is needed after 600 hours of operation or 6 months depending on which happens rst.
Perform lubrication as described below.
1. Make sure the extension tube is fully retracted to the mechanical end position. Retraction to the
mechanical end position may only be done if the actuator is unloaded and the retraction motion may not
exceed the maximum torque and speed listed in table T5.3.1. Failing to do so may damage the actuator.
Once in the mechanical end position the retraction must be stopped immediately.
2. Lubricate via the grease port (1) with a grease gun (nipple type DIN3405 D1/A) using a grease of type
Urethyn E/M1 (semi-synthetic, high temperature grease containing an organic thickener) with the amount
listed in T5.3.2.
T5.3.1 - Max. retraction torque and speed
Model Max. torque [Nm] Max. speed [m/s)
PC25 0.25 0.25
PC32 0.25 0.25
PC40 0.50 0.25
T5.3.2 - Grease amount and type
Model Grease Amount [cm3/10 cm stroke] Grease type
PC25 0.75
Urethyn E/M1PC32 0.75
PC40 1.00

Thomson
Thomson PC-Series™ Precision Linear Actuator - Installation Manual - June 2014 19
5.4 Replacement of coupling on inline models with RediMount ange
The coupling may break at overload in which case it can be replaced per the instructions bellow. Make
sure when replacing a broken coupling that all other components are intact.
1. Remove cover lid (12) and loosen screws on the coupling half (11) closest to the motor and remove it.
2. Remove screws (6) and remove the motor.
3. Make sure the extension tube on the unit (1) is fully retracted (this may not be changed until the
screws (7) are tightened again).
4. Remove screws (7) and the ange plate (3), the sealings (4) and the bell house (2).
5. Looosen the lock screw on the coupling half closest to the unit (9) and remove it.
6. Push on the new coupling and make sure the parts of the new coupling (9, 10 and 11) are fully
pressed together.
7. Make sure the coupling are at the correct LC distance as listed in table T5.4.1.
8. Tighten the lock screw on coupling half as listed in table T5.4.2.
9. Make sure the sealing (4) is correctly positioned against the bell house (2) and the ange plate (3)
before tightening screws (7) according to table T6.3.1
10. Mount the motor and tigthen screws (6) according to table T5.4.2.
11. Tighten the lock screw on coupling half (11) according to table.
12. Check so that the o-ring (12) is not damaged, in which case it should be replaced, and put back the
cover lid (12).
13. Test run the unit without any load 2 - 3 cycles to see that it runs smoothly and without any noise.
T5.4.1 - Distance LC
Model LC [mm]
PC25 10.0
PC32 7.0
PC40 14.0
T5.4.2 - Coupling half lock screw tightening torque
Model Nm
PC25 0.85
PC32 2.00
PC40 2.00

Thomson
Thomson PC-Series™ Precision Linear Actuator - Installation Manual - June 201420
5.5 Replacement of belt gear timing belt
The belt may break at overload in which case it can be replaced per the instructions bellow. Make sure
when replacing a broken belt that all other components are intact.
T5.5.1 - Screw size and tightening torque
Model Screw in position Number of screws and sizes Tightening torque [Nm]
PC25
18 4 × M5 6.50
19 2 × M4 3.30
4 × M3 1.35
20 2 × M4 3.30
PC32
18 4 × M6 11.10
19 6 × M4 3.30
20 4 × M4 3.30
PC40
18 4 × M6 11.10
19 6 × M5 6.50
20 4 × M5 6.50
This manual suits for next models
3
Table of contents
Other Motion Controllers manuals
Popular Controllers manuals by other brands
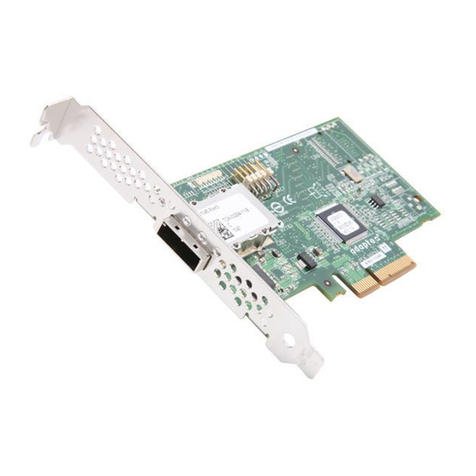
Adaptec
Adaptec 1405 quick start guide
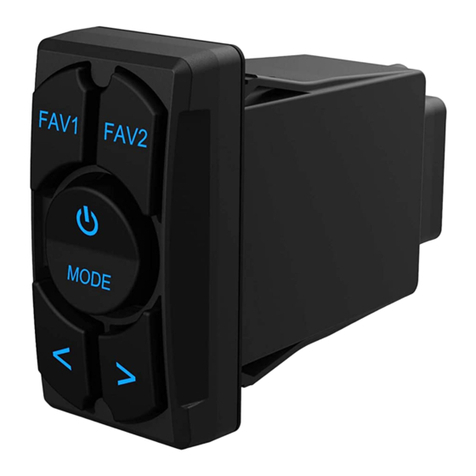
Wet Sounds
Wet Sounds WWX-RGB-RS owner's manual
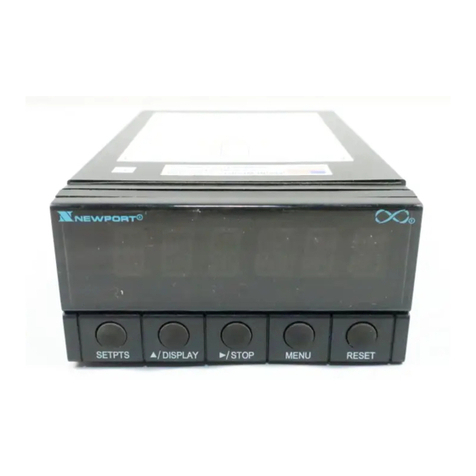
Newport Electronics
Newport Electronics INFINITY INF7 Operator's manual
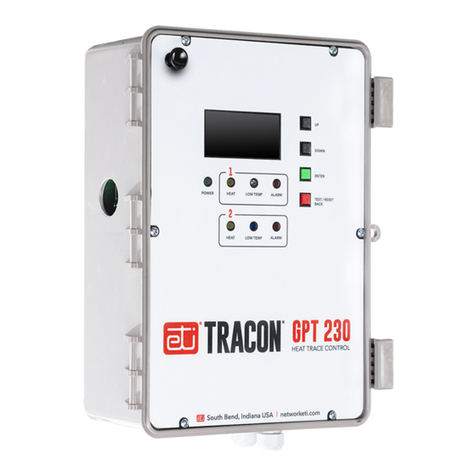
ETI
ETI Tracon GPT 230 Quick Reference Installation Guide
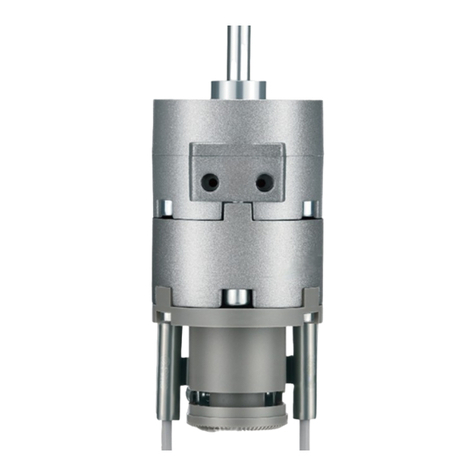
SMC Networks
SMC Networks CRB10 Operation manual

Pressure Tech
Pressure Tech THE SS-414 Series Operating and service manual
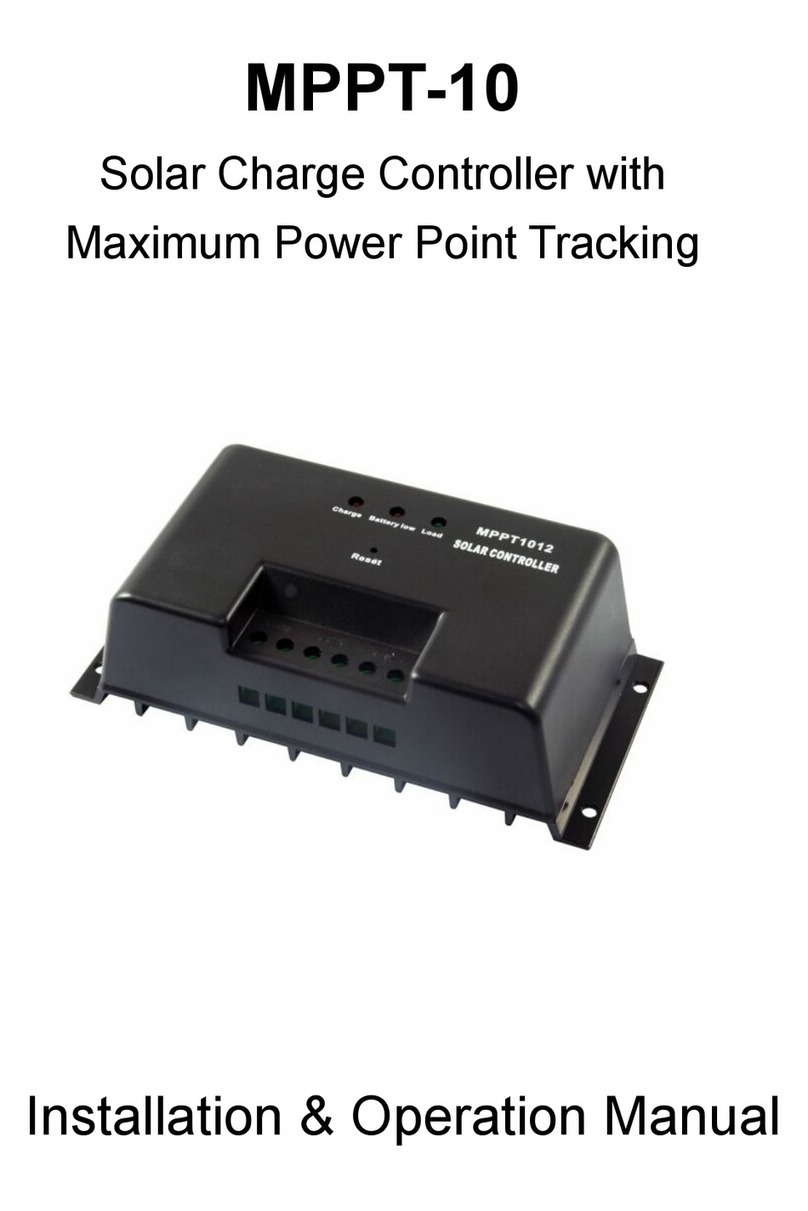
Solar
Solar MPPT-10 Installation & operation manual
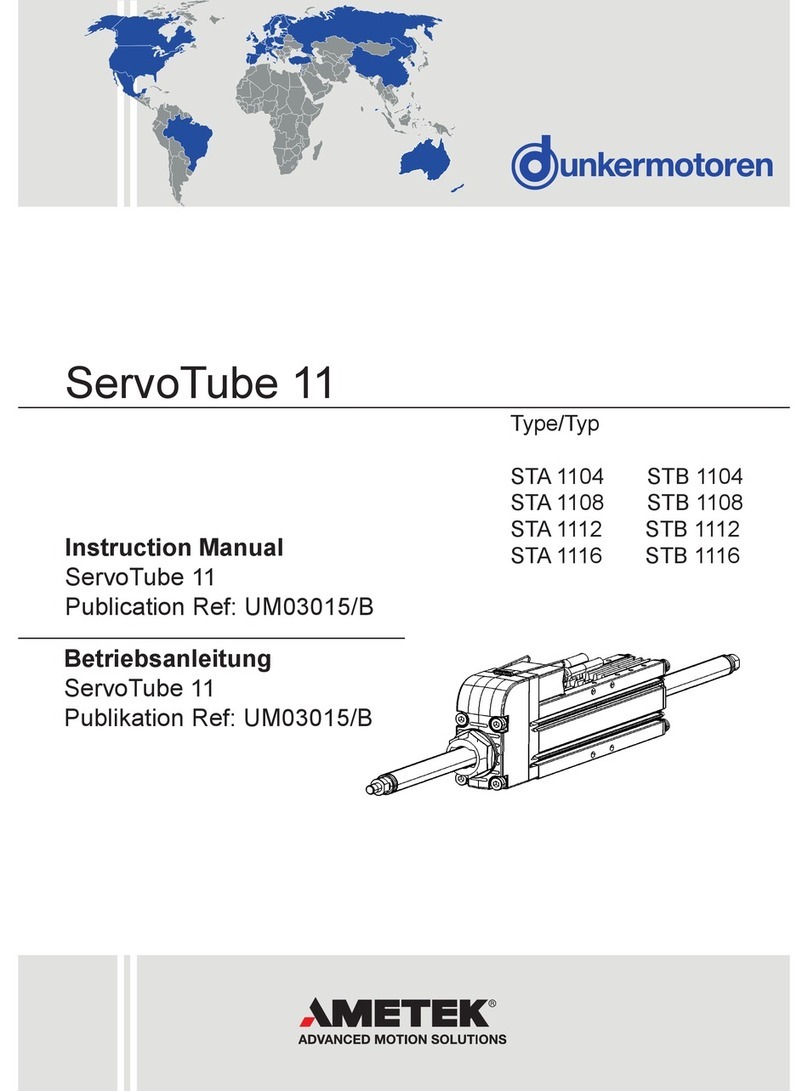
dunkermotoren
dunkermotoren STA Series instruction manual

Comunello
Comunello Liwin instruction manual

Bard
Bard MC4000 SERIES Installation & parts manual
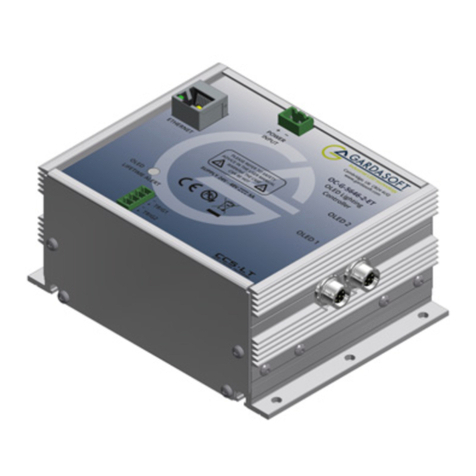
GARDASOFT
GARDASOFT OC-G-5646-2-ET user manual
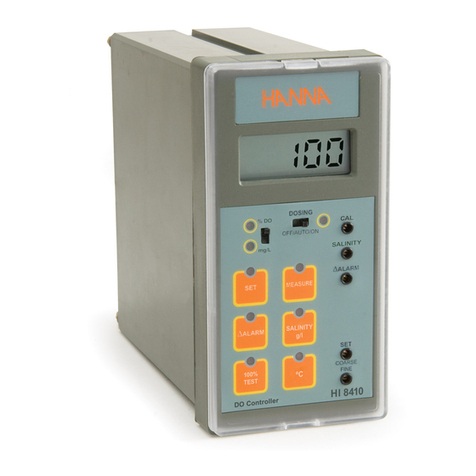
Hanna Instruments
Hanna Instruments HI 8410 instruction manual