Fervi t047/230v Operating instructions

USE AND
MAINTENANCE MANUAL
Milling Drilling Machine with tapping device
Art. T047/
230V
Art. T047/400V
TRANSLATION OF THE ORIGINAL INSTRUCTIONS
fervi.com

MACHINES AND
ACCESSORIES
Page
2
of
43
PREFACE
Please ensure you have read this manual before operation
TRANSLATION OF
THE ORIGINAL INSTRUCTIONS
Reading this instruction manual is required before operating any of the machinery. The
guarantee that the machine will function and perform properly is strictly dependent upon the
application of all the instructions contained in t
his manual.
Operator Qualifications
The workers responsible for the use of this machine must have all the necessary
information and instruction and should be given adequate training in relation to safety
regarding:
a)
Conditions of use for the equipmen
t;
b)
Foreseeable abnormal situations, pursuant to Article 73 of Legislative Decree
81/08.
We guarantee the Machine complies with the specifications and technical instructions
described in the Manual on the date of issuance and listed herein; On the other
hand,
the machine may also be subject to important technical changes in the future, without
the manual being updated.
Therefore, contact FERVI for information about modifications that may have been
implemented.
REV. 1
September 2013
fervi.com

MACHINES AND
ACCESSORIES
Page
3
of
43
CONTENTS
1
INTRODUCTION
................................
................................
........................
5
2
GENERAL SAFETY WARNI
NGS
................................
................................
...
7
2.1
Gener
al safety rules for machine equipment
................................
..............................
7
2.2
Safety regulations regarding the electric system of machine
-
tools
..........................
10
2.3
Technical as
sistance
................................
................................
................................
10
2.4
Other provisions
................................
................................
................................
......
10
3
TECHNICAL SPECIFICAT
IONS
................................
................................
.
11
4
INTENDED USE AND DES
CRIPTION OF THE MACH
INE
.............................
12
4.1
Usage environment and support surface
................................
................................
..
12
4.2
Main units of the milling dril
ling machine
................................
................................
13
4.3
Identification plate
................................
................................
................................
..
14
4.4
Plates and pictograms
................................
................................
..............................
14
4.4.1
Plates on the side of the machine
................................
................................
............
14
4.4.2
Plates and pictograms
................................
................................
...........................
15
4.4.3
Spindle speed plates
................................
................................
.............................
17
4.5
Accessories supplied
................................
................................
................................
17
5
SWITCHES AND CONTROL
LEVERS
................................
..........................
18
5.1
Control button
s and indicator lights
................................
................................
.........
18
5.2
Commands for adjusting the speed of the spindle
................................
....................
20
5.3
Spider for vertical displacement of the spi
ndle
................................
........................
21
5.3.1
Graduated adjustment of the vertical displacement of the spindle
...............................
21
5.4
Adjusting the Work Table
................................
................................
.........................
22
5.4.1
Table height adjustment handle
................................
................................
..............
22
5.4.2
Handwheel for the longitudinal calibrated feed of the table
................................
.........
23
5.4.3
Handwheel for the transverse calibrated feed of the table
................................
..........
23
5.5
Adjusting the head
................................
................................
................................
...
24
5.5.
1
Head height adjustment handle
................................
................................
..............
24
5.5.2
Nuts and graduated scale for adjusting the inclination of the head
..............................
25
6
MACHINE SAFETY
DEVICES
................................
................................
.....
26
6.1
Grounding
................................
................................
................................
................
26
6.2
Safety devices
................................
................................
................................
..........
27
6.2.1
INTERLOC
KING MOVEABLE GUARD
................................
................................
.........
27
6.2.2
Guard fixed on the milling piston rod pin
................................
................................
..
27
7
TRANSPORT AND INSTAL
LATION
................................
............................
28
7.1
Transport
................................
................................
................................
.................
28
7.2
Mechanical installation
................................
................................
............................
29
7.3
Electrical installation
................................
................................
...............................
29
7.4
Commissioning
................................
................................
................................
.........
29
8
OPERATION
................................
................................
............................
30
8.1
Preparing for milling
................................
................................
................................
30
8.1.1
Mounting the tool for milling
................................
................................
...................
31
8.1.2
Locking the work table
................................
................................
..........................
31
8.2
Preparation for drilling
................................
................................
............................
32
8.2.1
Mounting the tool for drilling / tapping
................................
................................
.....
32
9
MAINTENANCE
................................
................................
........................
33
9.1
Routine maintenance
................................
................................
...............................
33
fervi.com

MACHINES AND
ACCESSORIES
Page
4
of
43
10
TROUBLESHOOTING
................................
................................
.............
34
11
DISPOSAL OF COMPONEN
TS AND MATERIALS
................................
......
35
12
ELECTRICAL CIRCUIT
................................
................................
...........
36
12.1
WIRING DIAGRAM OF THE CONTROL PANEL
................................
.........................
37
13
PARTS OF THE MACHINE
................................
................................
......
38
fervi.com

MACHINES AND
ACCESSORIES
Page
5
of
43
1
INTRODUCTION
This manual is considered an integral part of the machine it was attached to at the time of
purchase.
The manufacturer holds all ownership to material and intellectual property
of this manual;
any disclosure or copying, even partial, of this publication without prior written consent is
forbidden.
The purpose of this manual is to convey the necessary knowledge for the use and
maintenance of
Milling
Drilling Machine with tapping
device (Art. T032)
and to create a
sense of responsibility and knowledge of the capabilities and limits of this machine entrusted
to the operator.
As the machine is entrusted to experienced and skilled operators, the following machine must
be perfectly kno
wn by the operator if you want it to be used safely and effectively.
Operators must be properly trained and prepared, so make sure that this manual is read and
consulted by the staff responsible for commissioning, operation and maintenance of the
Milling D
rilling Machine
. This is to make all operations the safest and most effective
possible for those who carry out these tasks.
Therefore, it is imperative to strictly comply with the requirements in this manual, a
necessary condition for safe and satisfactory
operation of the machine.
Before starting operation, installation and usage of the
Milling Drilling Machine
, authorized
personnel must:
read this technical document carefully;
know which protections and safety devices are available on the machine, their l
ocation and
how they work.
The manufacturer waives any and all responsibility for damage to people and/or
things caused by non
-
observance of the instructions in this manual.
The
Milling Drilling Machine
has been designed and built with mechanical guards
and
safety devices designed to protect the operator / user from possible injury. It is strictly
forbidden to modify or remove guards, safety devices and caution labels. If you do so
temporarily (for example, for the purposes of cleaning or repair), make su
re that no one can
use the machine.
Operators will be held fully responsible for any changes they have made to the
machine; the manufacturer will not be held responsible for any damage to persons
and/or property resulting from maintenance performed by un
qualified personnel
and in a manner that differs from the operating procedures shown below.
G
RAPHIC REPRESENTATIO
N OF SAFETY
,
OPERATIONAL AND RISK
WARNINGS
The following boxes are designed to attract the attention of the reader / user for the
proper
and
safe
use of the machine:
fervi.com

MACHINES AND
ACCESSORIES
Page
6
of
43
Attention
This highlights behavioural rules to prevent damage to the machine and/or the occurrence of
dangerous situations.
Residual Risks
This highlights the presence of dangers that cause residual risks to which the ope
rator must
pay attention in order to avoid injury or damage to property.
Operator Qualifications
Workers responsible for machine operation must have all necessary information and education
and should be given adequate safety training in: a) machine op
erating conditions, b)
foreseeable abnormal situations, pursuant to Article 73 of Legislative Decree 81/08
For safe and simple use of the
Milling Drilling Machine (Art. T047)
, you must read this
manual carefully to acquire full knowledge of the machine a
nd the general precautions to be
observed during operation.
. In other words, durability and performance are strictly dependent
on how they are used.
Even if already familiar with this sort of machine, it is necessary to follow the instructions
herein, in a
ddition to the general precautions to be observed while working.
Acquire full knowledge of the machine.
Read this manual carefully to understand: operation, safety devices and all necessary
precautions. All this is to allow safe use of the equipment.
Wear
appropriate clothing for the job.
The operator must appropriate clothing. To prevent the occurrence of unpleasant
accidents.
Maintain the machine with care.
Using the Machine
The machine must only be used by qualified personnel trained to use the mach
ine by
authorized personnel.
fervi.com

MACHINES AND
ACCESSORIES
Page
7
of
43
Figure
1
-
Overall view
2
GENERAL SAFETY WARNI
NGS
2.1
General safety rules for machine equipment
Accident
The operation of drilling or tapping always presents a risk of injury associated with the
poss
ibility of accidental contact of parts of the body with the tool in motion, detachment of
splinters from the workpiece, tool breakage, or ejection of a badly blocked piece.
There is no "intrinsic" means of safety, just as there is no worker who, while car
eful, can
"always" avoid an accident. Therefore, DO NOT underestimate the risks associated with
using the machine and concentrate on the work in progress.
Risks related to Using the Machine
Despite the implementation of all safety devices for safe us
e of the machine, it is necessary
take note of all the requirements for the prevention of the accidents reported in various parts
of this manual.
Risks related to Using the Machine
Every person who is responsible for the use and maintenance of the ma
chine should have first
read the instruction manual, particularly the chapter on safety information.
It is recommended that the plant safety manager get written confirmation of the above.
Risks associated with using the machine
During all work phases
with the machine, you should proceed with great caution in order
fervi.com

MACHINES AND
ACCESSORIES
Page
8
of
43
to avoid damage to persons, to the property or to the machine itself.
Please use the machine only for its expected uses (drilling or tapping).
Don't tamper with the safety devices equipping t
he machine.
Operator Protection
Before starting any work on the machine, the operator must wear the appropriate personal
protective equipment (PPE) such as gloves and eye protection (see section 6.5 of this
manual).
1.
Always check the efficiency and in
tegrity of the machine.
2.
Before connecting the machine to the mains, make sure that the rotating parts are not
damaged or badly worn. Make sure that the switch is in the neutral position.
3.
Do not start the machine in an enclosed or poorly ventilated area, or
in the presence of a
flammable and/or explosive atmosphere. Do not use the machine in damp and/or wet
locations, or those exposed to rain.
4.
Avoid starting accidentally.
5.
Before starting the machine, get used to ensuring that no remaining maintenance and
ser
vice keys are inserted.
6.
Keep the workplace tidy and free from obstruction; disorder causes accidents.
7.
Make sure that your work environment is forbidden to children, strangers and animals.
8.
Do not perform tasks on the machine other than those for which it wa
s designed. Only
use the machine in the manner in which it was intended, as described in this instruction
manual.
9.
Work without disturbances.
10.
Work areas must be well lit.
11.
Always wear eye protection and protective gloves while working. If dust is produced, u
se
the appropriate masks.
12.
Wear appropriate clothing. Loose clothing, dangling jewelry, long hair, etc.., can get
caught in the spindle and moving parts, causing irreparable injury.
13.
Firmly secure the workpiece before starting the drill.
14.
Always use the tool
(tip or tap) in an appropriate manner. Perform only the work for
which the tool is made. Do not use the tool for inadequate work.
15.
Only use suitable resistance tools in relation to the work that is to be done. This is to
avoid risky and unnecessary overload
ing for the operator, which may be harmful for the
life of the tools themselves.
16.
Do not pick up moving tools or other moving parts. To stop the spindle on the machine,
always only use the stop command device.
17.
17. Do not remove the shavings from the table
with hands, even at a standstill. To do
this, use tongs or a palette knife.
18.
When the cutting tools need to be replaced or the speed needs to be changed, stop the
motor and wait for the spindle to stop.
19.
Do not leave the machine until the spindle and the to
ol are completely stopped.
20.
After the work is completed, clean the tool and check its efficiency.
21.
Replace worn and/or damaged parts, check that the repairs and protections work properly
before operating. Eventually, if necessary, have it checked by Service
staff. Use only
original spare parts.
22.
Cut the mains voltage supply of the machine when:
the machine is not being operated;
it is left unattended;
performing maintenance or registration, because the machine does not work properly;
fervi.com

MACHINES AND
ACCESSORIES
Page
9
of
43
the tool is replaced;
it i
s being moved or transported;
cleaning.
23.
It is recommended that users of this publication, for maintenance and repair, have a basic
knowledge of the mechanical principles and procedures inherent in repair technique.
24.
The company safety officer is required to
make sure that machine operators
have read and understood this manual in its entirety.
fervi.com

MACHINES AND
ACCESSORIES
Page
10
of
43
2.2
Safety regulations regarding the electric system of machine
-
tools
Risks associated with using the machine
1.
Do not modify the electrical system in any way. Any attem
pt in this regard may jeopardize
the operation of electrical devices, causing malfunction or accident.
2.
Work carried out in the electrical system of the machine must, therefore, be carried out
only by qualified and authorized personnel.
3.
If one hears unusual
noises, or feels something strange, immediately stop the machine.
Then carry out an inspection and, if necessary, perform any repairs as required.
1.
The supply voltage must correspond to that stated on the identification plate and in the
technical specifi
cations:
Do not use any other power supply.
2.
The use of a life
-
saving device on the electric power supply is recommended. For more
detailed information, contact a trusted electrician.
3.
The power plug must be equipped with a grounding conductor. Any extensi
on cords must
be of equal or greater length than the power cord on the machine.
4.
The power supply cable (and its possible extension cable) should never come in contact
with hot objects, sharp edges, wet or oiled surfaces.
5.
The power cord should be checked re
gularly and before each use to check for signs of
damage or wear. If these are not in good condition, do not use the machine and replace
the cable.
6.
Do not use the power cord to detach its plug from the socket.
2.3
Technical assistance
For any problem or reques
t for clarification, please do not hesitate to contact the support
service of the retailer from whom you purchased the product.
2.4
Other provisions
It is forbidden to tamper with safety devices
The first thing to do when starting work is to check for the pre
sence and integrity of the
protections and the operation of the safety devices.
If any defect is detected, do not use the Milling Drilling Machine !!
Even more so, it is strictly forbidden to modify or remove guards, safety devices,
labels and indication
signs.
fervi.com

MACHINES AND
ACCESSORIES
Page
11
of
43
3
TECHNICAL SPECIFICAT
IONS
Size
Height (mm)
1960
Width (mm)
740
Depth (mm)
790
Masses
Net mass (kg)
380
Gross mass (kg)
390
Power supply
Rated voltage (V)
230
-
400
Frequency (Hz)
50
Power (W)
1500
General Characteristics
Drilling capac
ity (mm)
Cast iron:
40
Steel:
32
Tapping capacity (mm)
22
Spindle travel (mm)
130
Distance spindle
-
pillar (mm)
260
Column diameter (mm)
115
Morse taper
CM / MT 4
Sleeve diameter (mm)
76
Longitudinal table movement (mm)
375
Radial
table movement (mm)
190
Acoustic pressure level (dB (A))
67.2
Speed (r/min)
230 V
75 ÷
16
00
Speed (r/min) 400 V
75 ÷ 3200
Speed number 230 V
6
Speed number 400 V
12
fervi.com

MACHINES AND
ACCESSORIES
Page
12
of
43
4
INTENDED USE AND DES
CRIPTION OF THE
MACHINE
Milling Drilling Machines (Art. T0
47)
are machine
-
tools designed for executing some
simple mechanical operations, such as:
drilling (max drilling capacity: 32 mm for steel);
tapping;
milling.
The machine is made to perform such machining of different materials, changing the tool
depending
on the operation to be performed and the material of the work
-
piece.
The machine has 16 different spindle rotation speeds. The motor runs at constant speed,
therefore the machine is equipped with a specific power transmission system with gears for
varyin
g the spindle rotation speed.
The latter can be set using the appropriate adjustment levers. In any case, the adjustment of
the spindle speed must always be performed with the machine
stopped and not powered
.
The tool feed is manual.
Intended use and ma
terials
The machine has been designed and manufactured for the use specified. Any use and lack of
respect for the technical parameters established by the manufacturer may be dangerous to
operators; therefore, the manufacturer cannot assume any liability
for resulting damages.
4.1
Usage environment and support surface
The Drilling Machine is equipped with a support base and must be installed and used on flat
surfaces, with ergonomic features and adequate resistance.
It is very important to remember that the
machine weight is about 400 kg. For this reason,
before installing the machine it is necessary to identify an area having a surface of adequate
hardness and strength, capable of supporting such weight.
You should leave enough space around the machine to en
sure proper maintenance and
cleaning of all parts of the machine.
The Drill can operate in enclosed working environments (production departments,
warehouses, etc.), i.e. those that are protected from the weather and where there is no
danger of fire or expl
osion.
The operating temperature is within the range of +5 / +50°C.
The environment must also be sufficiently illuminated so as to ensure operation in maximum
safety (at least 50 lux is recommended).
Risks associated with the work environment
ALWAYS c
omply with the instructions about the machine's work environment, especially about
the safety and strength features of the surface.
fervi.com

MACHINES AND
ACCESSORIES
Page
13
of
43
4.2
Main units of the milling drilling machine
Figure
2
-
Overview of the Machine.
1.
Speed controller;
2.
Handwheel for slow feed with calibrated depth;
3.
Spindle protection device (interlocked guard)
4.
Handwheel for calibrated transverse feed;
5.
Electric motor;
6.
CE Plate;
7.
Spindle quick descent Lever / Spider;
8.
S
pindle;
9.
Work table;
10.
Handwheel for calibrated longitudinal feed;
11.
Handle for height adjustment of work table.
12.
Base
13.
Coolant pump
4
1
2
8
9
11
12
10
13
5
6
7
3
fervi.com

MACHINES AND
ACCESSORIES
Page
14
of
43
4.3
Identification plate
On the machine, the identification plate is located on the side of the head (see figure below).
Figure
3
–
CE plate.
4.4
Plates and pictograms
4.4.1
Plates on the side of the machine
On the left side of the machine, near the main switch for disconnecting the power supply
there are the following plates:
Figure
4
–
Left side pictograms.
fervi.com

MACHINES AND
ACCESSORIES
Page
15
of
43
4.4.2
Plates and pictograms
T047/230V
Figure
5
-
Pictograms T047/400V60
-
PLEASE READ THE INSTRUCTIONS BEFORE USING
THE MACHINE
-
BEFORE CARRYING OUT ANY ADJUSTMENT OR
MAINTENANCE ON THE MACHINE, DETACH ITS
PLUG FROM THE POWER SUPPLY SOCKET.
-
BEFORE OPERATING, SECURE SOLIDLY TO THE
TABLE THE PIECE TO
BE MACHINED.
-
FOR OTHER INFORMATION ON SAFETY, PLEASE
CONSULT THE INSTRUCTION MANUAL.
fervi.com

MACHINES AND
ACCESSORIES
Page
16
of
43
PLATE IN ITALIAN
PLATE IN ENGLISH
-
LEGGERE ATTENT
AMENTE LE ISTRUZIONI PRIMA
DI UTILIZZARE LA MACCHINA
-
PRIMA DI INTERVENIRE SULLA MACCHINA PER
QUALSIASI REGOLAZIONE O PER MANUTENZIONE
TOGLIERE LA SPINA DALLA PRESA DI CORRENTE
-
FISSARE SALDAMENTE ALLA TAVOLA IL PEZZO DA
LAVORARE PRIMA DI OPERARE
-
PER ALT
RE INFORMAZIONI SULLA SICUREZZA SI
CONSIGLIA DI CONSULTARE IL MANUALE
D’ISTRUZIONI.
-
PLEASE READ THE INSTRUCTIONS BEFORE USING
THE MACHINE
-
BEFORE CARRYING OUT ANY ADJUSTMENT OR
MAINTENANCE ON THE MACHINE, DETACH ITS PLUG
F
ROM THE POWER SUPPLY SOCKET.
-
BEFORE OPERATING, SECURE SOLIDLY TO THE
TABLE THE PIECE TO BE MACHINED.
-
FOR OTHER INFORMATION ON SAFETY, PLEASE
CONSULT THE INSTRUCTION MANUAL.
ATTENZIONE
È VIETATO ESEGUIRE LAVORI SU
APPARECCHIATURE ELETTRICHE SOTTO
T
ENSIONE
EVENTUALI DEROGHE DEVONO ESSERE
AUTORIZZATE DAL CAPO RESPONSABILE
IN CONDIZIONI DI PARTICOLARE PERICOLO DEVE
ESSERE PRESENTE UN’ALTRA PERSONA OLTRE A CHI
ESEGUE IL LAVORO
INIZIARE I LAVORI SOLO AD AVVENUTA
ATTAZIONE DELLE MISURE DI SICUREZZA
In ot
temperanza al Dgs.81/08 relativo alla prevenzioni
infortuni
ATTENTION
IT IS PROHIBITED TO WORK ON LIVE ELECTRICAL
EQUIPMENT
ANY EXCEPTIONS MUST BE APPROVED BY THE HEAD
MANAGER
UNDER PARTICULARLY DANGEROUS CONDITIONS,
ANOTHER PERSON MUST BE PRESENT WHO IS NOT
PERFORMING THE WORK
ONLY BEGIN WORKING WHEN SAFETY MEASURES
HAVE BEEN IMPLEMENTED
In accordance with Legislative Decree 81/08 on accident
prevention
NON
RIMUOVERE
I DISPOSITIVI DI
SICUREZZA
DO NOT
REMOVE
THE SAFETY DEVICES
fervi.com

MACHINES AND
ACCESSORIES
Page
17
of
43
4.4.3
Spindle speed plates
The plate indicating of the speed of rotation of the spindle corresponding to different gearbox
configurations is on the front part of
the head (
Figure
6
).
Figure
6
-
Spindle speed change plate
, respectively 230V, 400V
Adjusting the Speed
It is absolutely forbidden to change the rotation speed while the
spindle is moving.
4.5
Accessories supplied
Along with the machine, a pack is supplied containing the accessories.
fervi.com

MACHINES AND
ACCESSORIES
Page
18
of
43
5
SWITCHES AND CONTROL
LEVERS
5.1
Control buttons and indicator lights
At the front part of the
Milling Drilling Machine (T047)
, on the left of hea
d and spindle
there is the following control panel.
Figure
7
-
Drill control panel
T047 400V
.
A.
POWER INDICATOR LIGH
T
O
n the control panel there is a WHITE indicator light that turns on when the ma
chine is
powered.
B.
BLACK ROTARY SELECTO
R FOR NORMAL STOP AN
D SELECTION OF OPERA
TING
MODE: DRILLING / TAP
PING
This rotary switch selects the operating mode of the machine:
Drilling and milling (DRILL / MILL);
Tapping (TAP).
press the green C and D buttons
in drilling mode depending on the rotation of
drilling to make the machine start.
In tapping mode, the spindle will automatically rotate in a clockwise direction as
soon as the sleeve is lowered slightly. Upon reaching the preset depth the rotation
of the
tip will stop for a short time thanks to the internal timer and will start to
rotate in reverse to extract the tap.
A
C
E
G
B
D
F
fervi.com

MACHINES AND
ACCESSORIES
Page
19
of
43
C.
GREEN START SWITCH (
CLOCKWISE ROTATION)
When pressed, the clockwise rotation of the spindle will start.
Risk of injury
Before startin
g the Drill, make sure all guards are properly in place.
D.
GREEN START SWITCH (
ANTICLOCKWISE ROTATI
ON)
When pressed, the anticlockwise rotation of the spindle will start.
Risk of injury
Before starting the Drill, make sure all guards are properly in pl
ace.
E.
RED STOP BUTTON
When pressed, it interrupts the rotation of the machine.
F.
BLACK ROTARY SELECTO
R TO START THE COOLA
NT PUMP
Turn the selector to the right, positioning it on the green circle to turn on the machine's
coolant pump. To turn off the pump
turn the selector, positioning it on the red circle.
G.
EMERGENCY STOP BUTTO
N (RED, MUSHROOM
-
HEAD)
When pressed, it interrupts the rotation of the machine.
Upon pressing the emergency stop button, the spindle will keep rotating
by inertia for a few seconds
before stopping completely. Don't approach
the tool until it has fully stopped !
Risk of injury
It is absolutely forbidden to by
-
pass, inhibit or modify the safety device established by the
emergency stop button and its circuitry.
In case of emerg
ency
In an emergency, press the red button to stop the milling.
Checking the Emergency Button
Before starting any work on the machine, the operator must ensure that the emergency stop
button works.
fervi.com

MACHINES AND
ACCESSORIES
Page
20
of
43
5.2
Commands for adjusting the speed of the spindle
To
adjust the speed of rotation of the spindle, use the controls located at the front of the
head, and in particular:
The levers (ref. G and H in
Figure
8
) for speed change with gears;
The rotary selector (ref. I) to
choose the rotation speed of the motor.
Figure
8
-
Speed adjustment.
The 230V model does not have a rotary switch (ref I Figure 10), this is only a feature of the
400V model.
To adjust the speed of
the Drill T047, move levers G and H to the desired position, according
to that indicated on the spindle speed plate located below the selector I (
Figure
6
and
Figure
8
).
F
or example, to set a speed of 600 r/min, proceed as follows:
1.
Set the rotary selector for the speed of the motor to I (ref. I in
Figure
8
);
2.
Position the lever G for adjustment of the spindle speed at H;
3.
Position the
lever H for adjustment of the spindle speed at 1;
Adjusting the Speed
It is absolutely forbidden to change the rotation speed of the spindle while the spindle is
moving.
Motor rotation speed
Remember to always set the correct rotation speed of th
e electric motor by means of the
rotary selector switch located on the control panel (ref. I in
Figure
8
).
G
I
H
fervi.com
This manual suits for next models
1
Table of contents
Other Fervi Drill manuals
Popular Drill manuals by other brands

FE Powertools
FE Powertools 150 RLX Operator's manual

DeWalt
DeWalt XR Li-Ion DCD999 instruction manual
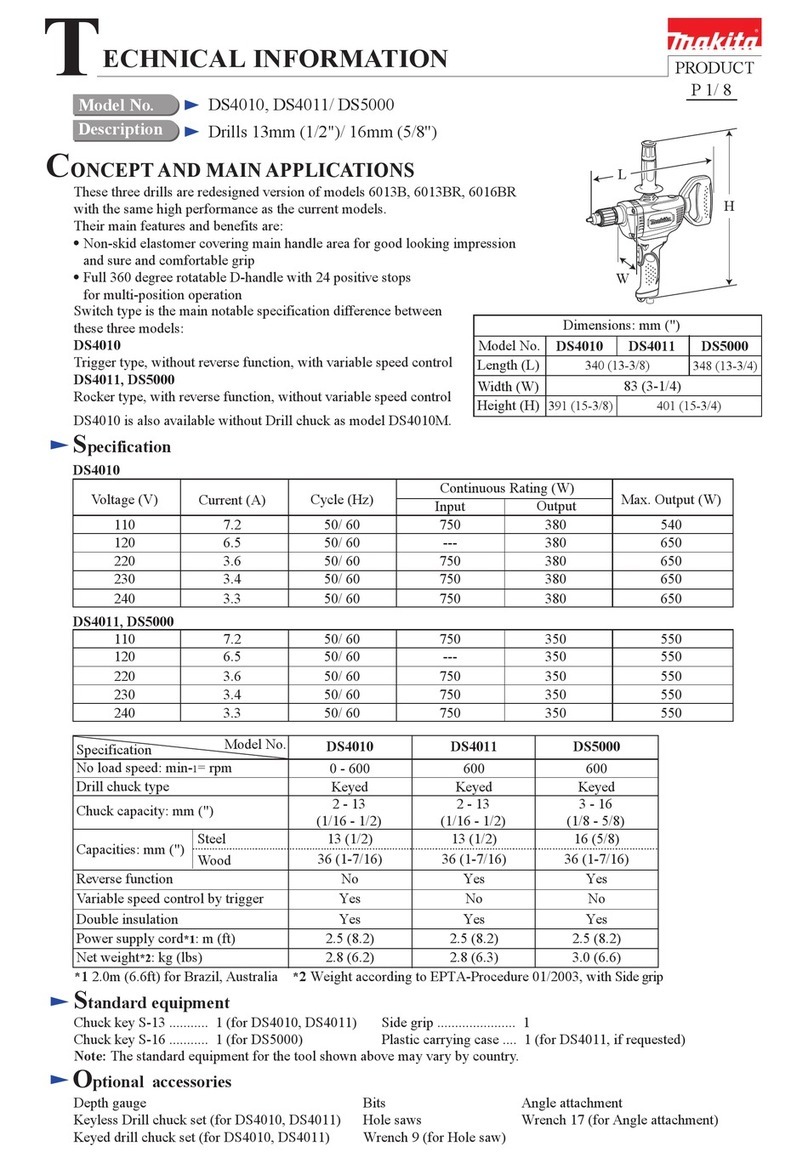
Makita
Makita DS4010 technical information

Wolfcraft
Wolfcraft 3406000 Translation of the original operating instructions
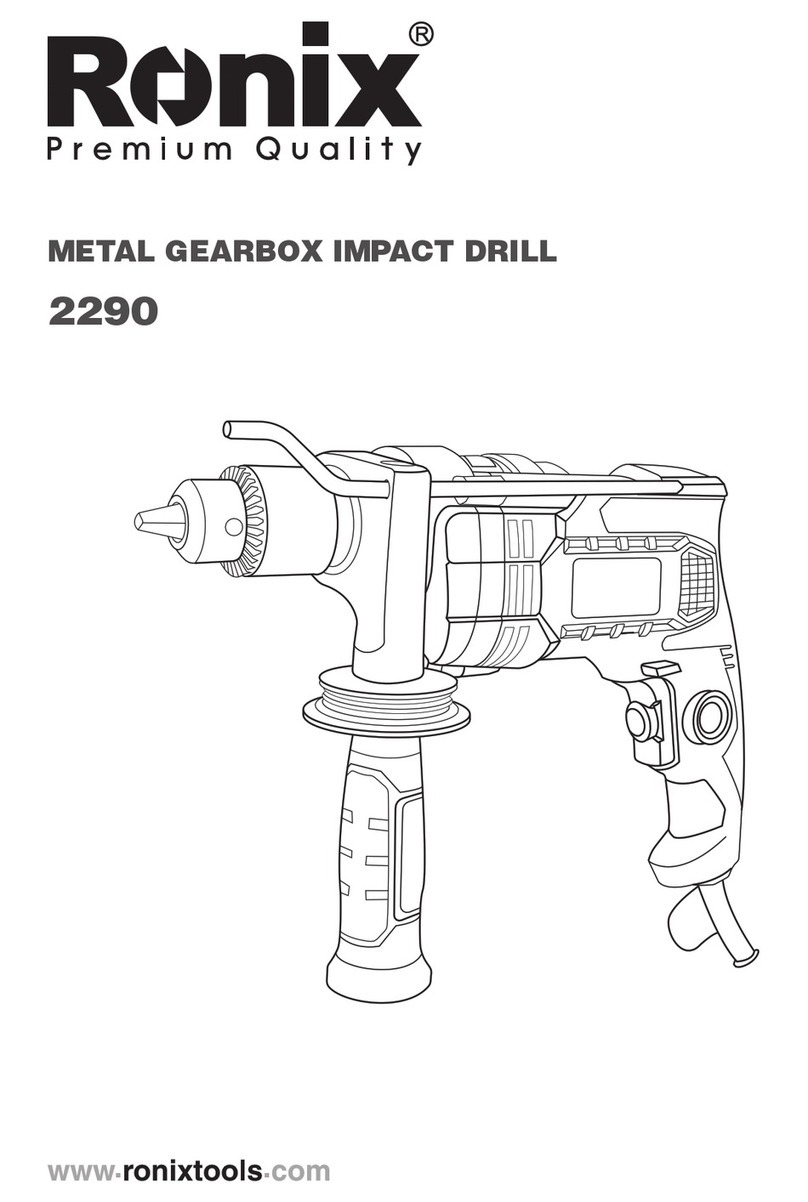
Ronix
Ronix 2290 quick start guide

Skil
Skil 2466 2566 2866 Operating/safety instructions