Fisher DS13 User manual

IEC 61508
SIL2
Betriebsanleitung
DS13
Differential pressure switch
09005217 • BA_EN_DS13 • Rev. ST4-A • 04/20
*09005217*

Table of contents FISCHER Mess- und Regeltechnik GmbH
ii BA_EN_DS13
Table of contents
1 Safety instructions .......................................................................................................... 3
1.1 General................................................................................................................................... 3
1.2 Personnel Qualification........................................................................................................... 3
1.3 Risks due to Non-Observance of Safety Instructions............................................................. 3
1.4 Safety Instructions for the Operating Company and the Operator ......................................... 3
1.5 Unauthorised Modification...................................................................................................... 3
1.6 Inadmissible Modes of Operation........................................................................................... 3
1.7 Safe working practices for maintenance and installation work............................................... 4
1.8 Pictogram explanation............................................................................................................ 4
2 Product and functional description ............................................................................... 5
2.1 Delivery scope........................................................................................................................ 5
2.2 Equipment versions................................................................................................................ 5
2.3 Intended use........................................................................................................................... 6
2.4 Function diagram.................................................................................................................... 6
2.5 Design and mode of operation ............................................................................................... 6
3 Assembly.......................................................................................................................... 7
3.1 General................................................................................................................................... 7
3.2 Process connection ................................................................................................................ 7
4 Start-up ............................................................................................................................. 9
4.1 General................................................................................................................................... 9
4.2 Control elements .................................................................................................................... 9
4.3 Opening the enclosure ........................................................................................................... 9
4.4 Switch point setting................................................................................................................. 10
4.5 Function test........................................................................................................................... 10
5 Servicing........................................................................................................................... 11
5.1 Maintenance ........................................................................................................................... 11
5.2 Transport ................................................................................................................................ 11
5.3 Service.................................................................................................................................... 11
5.4 Disposal.................................................................................................................................. 11
6 Technical data.................................................................................................................. 12
6.1 General Information................................................................................................................ 12
6.2 Input variables ........................................................................................................................ 12
6.3 Output parameters.................................................................................................................. 12
6.4 Operating conditions............................................................................................................... 13
6.5 Construction design................................................................................................................ 13
7 Order Codes ..................................................................................................................... 16
8 Attachments ..................................................................................................................... 19
8.2 EU Declaration of Conformity................................................................................................. 21

FISCHER Mess- und Regeltechnik GmbH Safety instructions | 1
BA_EN_DS13 3
1 Safety instructions
1.1 General
This operating manual contains basic instructions for the installation, operation
and maintenance of the device that must be followed without fail. It must be
read by the installer, the operator and the responsible specialist personnel be-
fore installing and commissioning the device.
This operating manual is an integral part of the product and therefore needs to
be kept close to the instrument in a place that is accessible at all times to the re-
sponsible personnel.
The following sections, in particular instructions about the assembly, commis-
sioning and maintenance, contain important information, non-observance of
which could pose a threat to humans, animals, the environment and property.
The instrument described in these operating instructions is designed and manu-
factured in line with the state of the art and good engineering practice.
1.2 Personnel Qualification
The instrument may only be installed and commissioned by specialized person-
nel familiar with the installation, commissioning and operation of this product.
Specialized personnel are persons who can assess the work they have been
assigned and recognize potential dangers by virtue of their specialized training,
their skills and experience and their knowledge of the pertinent standards.
1.3 Risks due to Non-Observance of Safety Instructions
Non-observance of these safety instructions, the intended use of the device or
the limit values given in the technical specifications can be hazardous or cause
harm to persons, the environment or the plant itself.
The supplier of the equipment will not be liable for damage claims if this should
happen.
1.4 Safety Instructions for the Operating Company and the
Operator
The safety instructions governing correct operation of theinstrument must be
observed. The operating company must make them available to the installation,
maintenance, inspection and operating personnel.
Dangers arising from electrical components, energy discharged by the medium,
escaping medium and incorrect installation of the device must be eliminated.
See the information in the applicable national and international regulations.
Please observe the information about certification and approvals in the Tech-
nical Data section.
1.5 Unauthorised Modification
Modifications of or other technical alterations to the instrument by the customer
are not permitted. This also applies to replacement parts. Only the manufacturer
is authorised to make any modifications or changes.
1.6 Inadmissible Modes of Operation
The operational safety of this instrument can only be guaranteed if it is used as
intended. The instrument model must be suitable for the medium used in the
system. The limit values given in the technical data may not be exceeded.
The manufacturer is not liable for damage resulting from improper or incorrect
use.

1 | Safety instructions FISCHER Mess- und Regeltechnik GmbH
4 BA_EN_DS13
1.7 Safe working practices for maintenance and installation work
The safety instructions given in this operating manual, any nationally applicable
regulations on accident prevention and any of the operating company's internal
work, operating and safety guidelines must be observed.
The operating company is responsible for ensuring that all required mainten-
ance, inspection and installation work is carried out by qualified specialized per-
sonnel.
1.8 Pictogram explanation
DANGER
Type and source of danger
This indicates a direct dangerous situation that could lead to death or serious
injury (highest danger level).
1. Avoid danger by observing the valid safety regulations.
WARNING
Type and source of danger
This indicates a potentially dangerous situation that could lead to death or ser-
ious injury (medium danger level).
1. Avoid danger by observing the valid safety regulations.
CAUTION
Type and source of danger
This indicates a potentially dangerous situation that could lead to slight or seri-
ous injury, damage or environmental pollution (low danger level).
1. Avoid danger by observing the valid safety regulations.
NOTICE
Note / advice
This indicates useful information of advice for efficient and smooth operation.

FISCHER Mess- und Regeltechnik GmbH Product and functional description | 2
BA_EN_DS13 5
2 Product and functional description
2.1 Delivery scope
• Differential pressure switch DS13
• Operating Manual
2.2 Equipment versions
2.2.1 Pressure chamber
Stainless steelAluminium
Fig.1: Material options for the pressure chamber
2.2.2 Electrical connection
Number cable Cable socket/plug connection
Fig.2: Options for the electrical connection
2.2.3 Type plate
This type plate serves as an example of the information that is stated. The data
shown is purely fictive, but does correspond to the actual conditions. For more
information, please see the order code at the end of these instructions.
Devices pressure and voltage-free
Switching capacity: 5A/250V AC
Article no.
Measuring range
P max.
Prod. No.
0 - 1 bar
25 bar
DS13 02NA01B1
1806610.01.002
Made in Germany
MESS- UND
REGELTECHNIK
GmbH
D-32107 Bad Salzuflen
Serial number
P stat. max. 16 bar
Order code
Fig.3: Type plate

2 | Product and functional description FISCHER Mess- und Regeltechnik GmbH
6 BA_EN_DS13
2.3 Intended use
The DS13 is a switching device for differential pressure, over and under-pres-
sure for gaseous and fluid media. This series is ideally suited for various meas-
uring tasks in rough environments.
Typical application cases are the monitoring of tanks, filters and compressors.
Please contact the manufacturer before using this unit with dirty or aggressive
media because the unit needs to be adapted in terms of the parts that come into
contact with the media.
The device can be used as a functional safety components (SIL) as agreed with
the manufacturer (see order code).
The device is to be exclusively used for the applications agreed between the
manufacturer and the user.
2.4 Function diagram
5
6
1
1
2
3
4
+
Fig.4: Function diagram
1Pressure chamber 2Tappet
3Micro-switch 4Switch point setting
5Measuring diaphragm 6Measuring springs
2.5 Design and mode of operation
A sturdy non-sensitive diaphragm measuring unit that is suitable for measuring
differential pressure, and over and under-pressure is used as a measuring sys-
tem. The unit uses the same measuring principle for all three measuring applic-
ations.
In the rest position, the spring forces on both sides of the membrane are bal-
anced out. Due to the pressure or under-pressure to be measured, a single-
sided force is created on the membrane which shifts the membrane system
against the measurement range springs up to compensation of the spring
forces. In case of overload, the membrane supports against the metallic support
surfaces.
A centrally positioned tappet transfers the movement of the membrane system
onto the operating elements of the micro-switches.

FISCHER Mess- und Regeltechnik GmbH Assembly | 3
BA_EN_DS13 7
3 Assembly
3.1 General
The device is designed for wall mounting.
NOTICE!At the factory, the device is calibrated for vertical installation and
only this installation position is allowed.
To ensure safety during installation and maintenance, we recommend installing
a suitable shut-off valve on the system (see accessories). A shut-off valve offers
the following advantages:
• The device can be depressurized or decommissioned.
• The device can be disconnected from the power supply within the applic-
able system for repairs or inspections.
• A function test of the device can be performed on-site.
3.2 Process connection
• By authorized and qualified specialized personnel only.
• The pipes need to be depressurized when the instrument is being connec-
ted.
• Appropriate steps must be taken to protect the device from pressure surges.
• Check that the device is suitable for the medium being measured.
• Maximum pressures must be observed (cf. Tech. data)
The pressure connections are marked with (+) and (-) symbols on the device.
When the differential pressure is measured, the higher pressure is connected to
the (+) side and the lower pressure to the (-) side.
+
Fig.5: Process connection
The pressure lines must be kept as short as possible and installed without any
tight bends to avoid delays.
The pressure lines must be installed at an inclination so that when fluids are
measured no air pockets are created or when measuring gases, no water pock-
ets are created. If the required inclination is not reached, water or air filters must
be installed at suitable places.
In the case of fluid measuring media, the pressure lines must be vented be-
cause different fluid columns in the lines will distort the measurements.
If water is used as a measuring medium, the unit must be protected against
frost.
Pulsating pressure on the system side can lead to wear and functional prob-
lems. To safeguard this, we recommend installing absorption elements in the
pressure line.

3 | Assembly FISCHER Mess- und Regeltechnik GmbH
8 BA_EN_DS13
Fluid media
Settable reactor pins below the closing cap
G¼
Fig.6: Controllable damping reactor
In the operational status, the reactor pins need to be set so that the measure-
ment display follows the pressure changes with a delay.
Gaseous media
8
Fig.7: Capillary throttle coils

FISCHER Mess- und Regeltechnik GmbH Start-up | 4
BA_EN_DS13 9
4 Start-up
4.1 General
All electrical supply, operating and measuring lines, and the pressure connec-
tions must have been correctly installed before commissioning. All supply lines
are arranged so that there are no mechanical forces acting on the device.
Check that the pressure connections do not leak before commissioning.
4.2 Control elements
Switch point setting
Switch 1 Switch 2
Fig.8: Control elements
• Depending on the enclosure model, the switch point setting is accessible in
different ways.
• The enclosure must be opened to set the zero-point.
4.3 Opening the enclosure
1
2
1
2
3
4
PH2
Fig.9: Remove the cover hood
1. Remove the attachment screws (1) with a screwdriver. Ensure that the seal-
ing rings (2) do not get lost. The protection class is no longer guaranteed
without these sealing rings.
2. Remove the Makrolon in the hood (3) and the seal (4).
3. It is assembled in reverse order. The seal (4) must lie precisely in the
groove of the hood before the hood is screwed on.

4 | Start-up FISCHER Mess- und Regeltechnik GmbH
10 BA_EN_DS13
4.4 Switch point setting
1
2
Switch point setting
1.2 x 8
Fig.10: Switch point setting
1. Remove the plugs (1) and the seals (2) in the hood and/or open the bayonet
ring enclosure.
2. The required switch points can be set on the reference scale guide with a
screwdriver. The achievable accuracy is 5 %.
3. Replace the plug and/or the bayonet ring after completing the settings.
4.5 Function test
Remove both plugs in the hood for testing. Carry out the test for both mi-
croswitches. After the test, the switch points need to be reset.
Checking the switch points when the system is depressurized.
• No measurement is shown and the measurement display points to zero.
• Turn the switch point setting button toward the zero-point until the micro-
switch is activated.
• Check whether the signal is available on the terminals.
Test when the system is operational
• A measurement is shown.
• Turn the switch point setting button toward the measurement until the micro-
switch is activated.
• Check whether the signal is available on the terminals.
After the successful test, commission the device again otherwise contact our re-
pair department.

FISCHER Mess- und Regeltechnik GmbH Servicing | 5
BA_EN_DS13 11
5 Servicing
5.1 Maintenance
The instrument is maintenance-free. We recommend the following regular in-
spection to guarantee reliable operation and a long service life:
• Check the function in combination with downstream components.
• Check the leak-tightness of the pressure connection lines.
• Check the electrical connections.
The exact test cycles need to be adapted to the operating and environmental
conditions. In combination with other devices, the operating instructions for the
other devices also need to be observed.
5.2 Transport
The measuring device must be protected against impacts. It should be transpor-
ted in the original packaging or a suitable transport container.
5.3 Service
All defective or faulty devices should be sent directly to our repair department.
Please coordinate all shipments with our sales department.
WARNING
Process media residues
Process media residues in and ondismantled devices can be a hazard to
people, animals and the environment. Take adequate preventive measures. If
required, the devices must be cleaned thoroughly.
Return the device in the original packaging or a suitable transport container.
5.4 Disposal
Please help to protect the environment by always disposing of the work pieces
and packaging materials in compliance with the valid national waste and recyc-
ling guidelines or reuse them.

6 | Technical data FISCHER Mess- und Regeltechnik GmbH
12 BA_EN_DS13
6 Technical data
6.1 General Information
Reference conditions (acc. to IEC 61298-1)
Temperature +15 … +25 °C
Relative humidity 45 … 75 %
Air pressure 86 … 106 kPa 860 … 1060 mbar
Installation position vertical
6.2 Input variables
Measuring
ranges
Measuring accur-
acy
Allowed static op-
erating pressure
Overpres-
sure
Under-
pressure
0 … 250 mbar ± 6.25 mbar 6 bar 25 bar - 1 bar
0 … 400 mbar ± 10 mbar 6 bar
0 … 0.6 bar ± 0.015 bar 10 bar
0 … 1 bar ± 0.025 bar 16 bar
0 … 1.6 bar ± 0.04 bar 25 bar
0 … 2.5 bar ± 0.625 bar 25 bar
0 … 4 bar ± 0.1 bar 25 bar
0 … 6 bar ± 0.15 bar 25 bar
0 … 10 bar ± 0.25 bar 25 bar
0 … 16 bar ± 0.4 bar 25 bar
0 … 25 bar ± 0.625 bar 25 bar
-0.6 … 0 bar ± 0.015 bar 10 bar
-1 … 0 bar ± 0.025 bar 16 bar
-1 … +0.6 bar ± 0.04 bar 25 bar
-1 … +1.5 bar ± 0.0625 bar 25 bar
-1 … +3 bar ± 0.1 bar 25 bar
-1 … +5 bar ± 0.15 bar 25 bar
Rated pressure of the measuring
system
25 bar
Test pressure 1.5 times the rated pressure
Zero-point setting Arranged in the front panel of the scale
Measuring accuracy ± 2.5% of the upper range value
6.3 Output parameters
Switch contacts 1 to 2 micro-switches
Switching function (per contact) Changeover contact
Switch point setting Can be set to reference scales from outside
Smallest settable value 5% of the upper range value
Switch hysteresis 2.5% of the upper range value
Per contact AC DC
Switching voltage 250 V 30 V
Switching current 5 A 0.4 A
Switching output 250 VA 10 W

FISCHER Mess- und Regeltechnik GmbH Technical data | 6
BA_EN_DS13 13
6.4 Operating conditions
Increase ambient temperature -10 … +70 °C
Media temperature -10 … +70 °C
Storage temperature -15 … +75 °C
Enclosure protection class IP55 as per EN 60529
NSR EN 61010-1:2010
RoHS EN 50581:2012
SIL2 EN 61508:2010 Parts 1-7
6.5 Construction design
Process connection Inner thread G¼
Inner thread ¼-18 NPT
Brass, CrNi steel Connection shank G½ B DIN EN 837
Connection shank G¼ B DIN EN 837
Connecting shanks ¼-18 NPT
Brass, CrNi steel, galvanised
steel
Cutting ring connection in brass for 6 mm pipe
Cutting ring connection in brass for 8 mm pipe
Cutting ring connection in brass for 10 mm pipe
Electrical connection Permanently wired numbered cables
7-pin plug connection
Cable socket
Installation position vertical
Dimensions See dimensional drawings
Weight Pressure chamber in aluminium 1.2 kg
Pressure chamber in stainless steel 3.5 kg
6.5.1 Werkstoffe
Parts in contact with the
medium
Pressure chamber Aluminium GkAlSi10(mg); painted black
Aluminium GkALSi10(mg); HART-COAT© sur-
face protection
Chromium nickel steel 1.4305
Chromium nickel steel 1.4571
Measuring diaphragm NBR
VITON®
Inconel 718
Seals NBR
VITON®
Other inner parts Rustproof steel 1.4310, 1.4305
Process connection
Connection shanks
Brass
Chromium nickel steel
Process connection
Cutting ring screw connection
Brass
Galvanised steel
Chromium nickel steel

6 | Technical data FISCHER Mess- und Regeltechnik GmbH
14 BA_EN_DS13
Parts with no contact with the
medium
Cover hood IP55 Makrolon
Bayonet ring housing IP65 Stainless steel 1.4301
Dial face and needle Aluminium
Setting buttons AlCuMgPb 3.1645
6.5.2 Dimensional drawings
All dimensions in mm unless otherwise stated
The following are the dimensional diagrams for the pressure chambers in alu-
minium. The dimensional diagrams for the pressure chambers in stainless steel
are similar. For this reason, there is no illustration.
Electrical connection variant
92
Cable connection socket or
7-pin plug connection
M20 x 1.5
Cutting ring-
Screw connection
Ø5
92
30°
30°
82
Ø127
Ø116Bolt circle
46
Ø104
16.5 26
103
108
Fig.11: Dimensional picture

FISCHER Mess- und Regeltechnik GmbH Technical data | 6
BA_EN_DS13 15
Process connection variants
G¼
Ø21
0,8
13.5
77
13
3
Ø5
Ø9.5
Fig.12: Process connection
SW
G¼
l1
L
l3
l2
l4
d2
d1
G
G¼
19
ØD
SW
DIN EN 837 Cutting ring
Connecting shanks d1 d2 l1 l2 A/F
G¼B 5 9.5 13 2 19
G½B 6 17.5 20 3 22
Cutting ring screw connection ØD A/F
Pipe diameter 6, 8, 10 19
SW
G¼
l1
L
l2
N
NPT outside
Connecting shanks N L l1 l2 A/F
NPT outside ¼-18 NPT 42 12 18 19

7 | Order Codes FISCHER Mess- und Regeltechnik GmbH
16 BA_EN_DS13
7 Order Codes
Process connection
Switching elements
Electrical connection
Type
Measuring range
Code no.
Measuring diaphragm
Pressure chamber
D S 1 3
1 2 5 6 7 83 4 9 10 11 12 13
Optional information
e.g. SIL
Measuring diaphragm
[1.2] Measuring range NBR / VITON Inconel 718
82 0 … 250 mbar x
83 0 … 400 mbar x
01 0 … 0.6 bar x
02 0 … 1 bar x
03 0 … 1.6 bar x
04 0 … 2.5 bar x
05 0 … 4 bar x
06 0 … 6 bar x
07 0 … 10 bar x
08 0 … 16 bar x
09 0 … 25 bar x
30 -0.6 … 0 bar x
31 -1 … 0 bar x
32 -1 … +0.6 bar x
33 -1 … +1.5 bar x
34 -1 … +3 bar x
35 -1 … +5 bar x
[3] Measuring dia-
phragm
Sealant Comment
NNBR NBR
VVITON®VITON®
DInconel 718 NBR Only measuring ranges 0 … 25
bar
EInconel 718 VITON®Only measuring ranges 0 … 25
bar
[4] Pressure chamber Comment
AAluminium Only measuring range ≤ 0 ... 16
bar
DAluminium HART COAT®
WStainless steel 1.4305
VStainless steel 1.4571

FISCHER Mess- und Regeltechnik GmbH Order Codes | 7
BA_EN_DS13 17
[5.6] Process connection Material
01 Inner thread G¼
04 Inner thread ¼-18 NPT
06 Connection shanks with external thread G¼ B Brass
11 Connection shanks with external thread G¼ B CrNi steel
14 Connecting port G½ with outer thread ¼-18
NPT
CrNi steel
20 Cutting ring connection in brass for 6 mm pipe Galvanised steel
21 Cutting ring connection in brass for 8 mm pipe Galvanised steel
22 Cutting ring connection in brass for 12 mm pipe Galvanised steel
24 Cutting ring connection in brass for 6 mm pipe CrNi steel 1.4571
25 Cutting ring connection in brass for 8 mm pipe CrNi steel 1.4571
26 Cutting ring connection in brass for 12 mm pipe CrNi steel 1.4571
28 Cutting ring connection in brass for 6 mm pipe Brass
29 Cutting ring connection in brass for 8 mm pipe Brass
30 Cutting ring connection in brass for 12 mm pipe Brass
87 1 x connection shank with external thread G½ B CrNi steel
[7] Switching Elements
A1 adjustable micro-switch
B2 adjustable microswitches
[8] Electrical connection
11 metre numbered cable; permanently wired
22.5 metre numbered cable; permanently wired
55 metre numbered cable; permanently wired
KCable connection socket
W7-pin plug connection
SDNV-GL approved version with 3 m connection cable
[9-13] Optional information
##### Code for special models e.g. SIL
The code is generated as agreed with our sales team.

7 | Order Codes FISCHER Mess- und Regeltechnik GmbH
18 BA_EN_DS13
Accessories
Please go to our website fischermesstechnik.de for data sheets for the measur-
ing device accessories.
DZ11 Installation set for retrofitting from wall mounting to switch panel in-
stallation. Please state the precise device type of the DS13 because
there are different switch panel installation sets depending on the
model.
DZ23/24 The shut-off valve DZ23 in a three spindle model and DZ24 in a four
spindle model can be particularly beneficial when mounting the differ-
ential pressure measuring and switch device DS13.
The following can be used for example:
• is a system is to be depressurized or taken out of operation
• for repairs or tests to disconnect differential pressure devices
within the affected systems from the mains supply
The shutoff devices can therefore also be used for function tests on
site. In contrast to DZ23, the DZ24 also has a venting valve to vent
the connected pipe system. The shut-off and venting valves are de-
signed for the rated pressure level PN40. The housing can be selec-
ted in aluminium, brass or chrome-nickel-steel 1.4301. There are
various pressure connections available for process-side screw con-
nections or connection threads.
MZ Measuring device accessory (throttles, siphons, etc.)

FISCHER Mess- und Regeltechnik GmbH Attachments | 8
BA_EN_DS13 19
8 Attachments
8.1 SIL Certificate
Fig.13: SIL_4479913759902

8 | Attachments FISCHER Mess- und Regeltechnik GmbH
20 BA_EN_DS13
Fig.14: SIL_4479913759902
Table of contents
Other Fisher Switch manuals
Popular Switch manuals by other brands
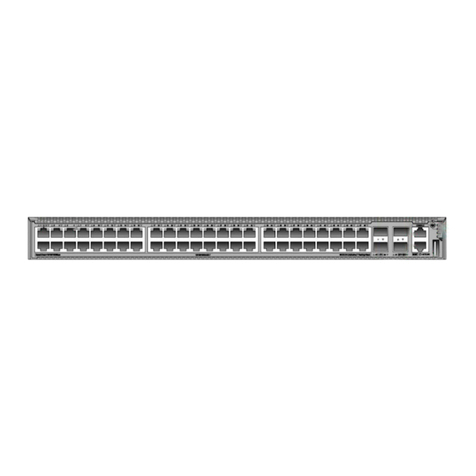
H3C
H3C S5590-HI Series manual
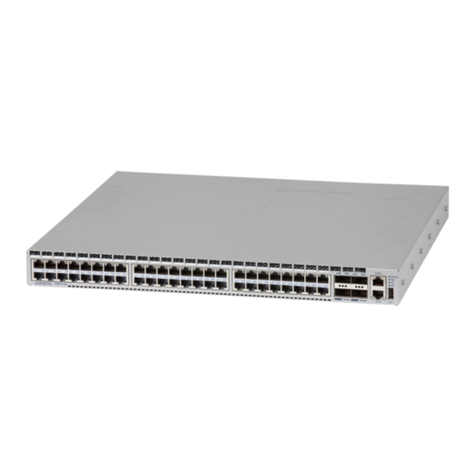
Arista
Arista DCS-7050TX-48 quick start guide
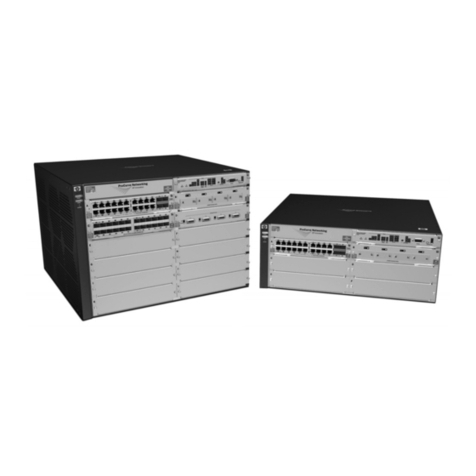
HP
HP ProCurve 5400zl Series Installation and getting started guide
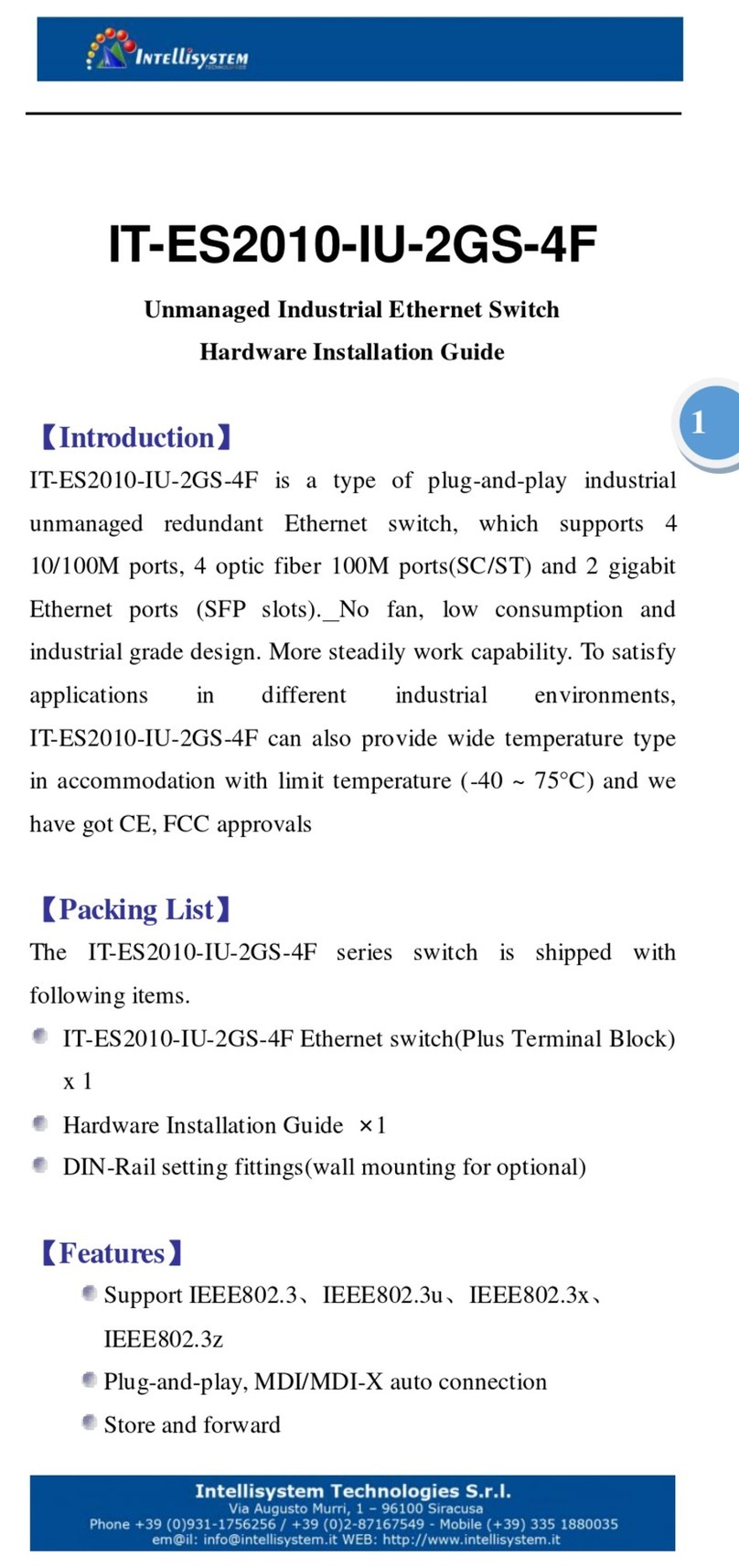
Intellisystem
Intellisystem IT-ES2010-IU-2GS-4F Series Hardware installation guide
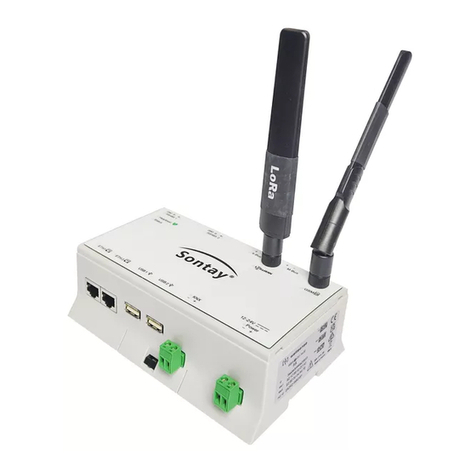
Sontay
Sontay RF-LW-HUB manual
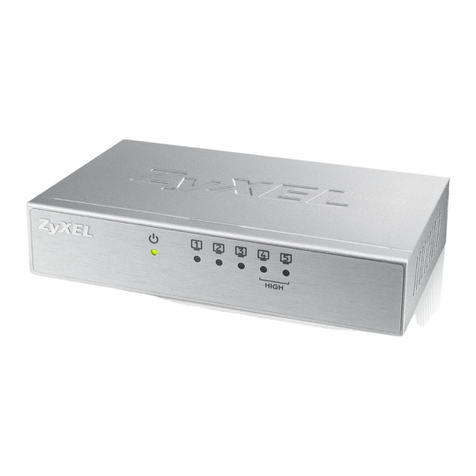
ZyXEL Communications
ZyXEL Communications ES-105S user guide