FläktGroup GL Series Operating manual

Technical Service Manual CA16
GL-SERIES AND HEAMO
FOR INTERNAL USE ONLY

Technical Manual CA16 GL-Series & HeaMo
2PR-2015-5341-GB ·
Subject to modifications ·R1-07/2019
Contents
1USER INTERFACE................................................................................................ 3
1.1 Menu structure ............................................................................................................ 4
1.2 Switching the unit on and off ......................................................................................... 6
1.3 Setting the operating mode ...........................................................................................8
1.4 Setting adjustment methods........................................................................................ 10
1.4.1 Proportional step adjustment on inlet probe ............................................................... 11
1.4.2 Proportional step adjustment on inlet probe + integral on inlet probe............................. 13
1.4.3 Quick mind adjustment ........................................................................................... 14
1.4.4 Modulating adjustment of screw compressors ............................................................. 16
1.4.5 Adjustment method for centrifuge compressors .......................................................... 17
2ALARMS............................................................................................................ 21
3TABLE OF MASKS .............................................................................................. 28
4TABLE OF MASKS W3000 BASE......................................................................... 73
5PARAMETERS TABLE ......................................................................................... 80
5.1 Table of parameter limits (depending on unit configuration) ............................................. 92
6DIAGRAMS ....................................................................................................... 94
6.1 Freecooling ............................................................................................................... 96
6.2 Condensation ............................................................................................................ 98
7HARDWARE ...................................................................................................... 99
7.1 HARDWARE “B”, board configuration with JUMPER 5V-24V ............................................. 100
8INPUT/OUTPUT CONFIGURATION TABLE ........................................................101
8.1 HARDWARE “L”........................................................................................................ 101
8.1.1 Units with hermetic compressors ............................................................................ 101
8.1.2 Units with centrifuge compressors .......................................................................... 104
8.2 HARDWARE “XL”...................................................................................................... 105
8.3 HARDWARE “B” ....................................................................................................... 108
8.4 EXPANSIONS........................................................................................................... 110
8.4.1 Units with hermetic compressors ............................................................................ 110
8.4.2 Units with alternative and screw compressors........................................................... 115
8.4.3 Units with centrifuge compressors .......................................................................... 122
9CONNECTING SEVERAL BOARDS......................................................................123
9.1 “BASE-EXPANSION” Connection ................................................................................. 123
9.2 “MASTER-SLAVE” connection ..................................................................................... 125
9.3 “Mixed” connection................................................................................................... 126
10 TERMINAL CONFIGURATION ...........................................................................128
10.1 Setting the keypad address ....................................................................................... 128
10.2 Setting the board address ......................................................................................... 129
10.3 Plan network configuration ........................................................................................ 130
10.3.1 Plan network connection (local) .......................................................................... 130
10.3.2 Configuring the plan network (global) .................................................................. 131
10.4 Connecting the remote keypad .................................................................................. 132
10.4.1 “T” shunt......................................................................................................... 132
10.4.2 Remote keyboard up to 200 metres..................................................................... 133
10.4.3 Remote keyboard from 200 metres up to 500 metres............................................. 134
10.4.4 Remote keypad for more than one unit ................................................................ 135
Notice: The W3000 controller software is protected by a digital signature.
This means that it can only work on boards supplied by FläktGroup and not on boards
purchased from other dealers.
Based on C0240111-09-07-GB

GL-Series & HeaMo Technical Manual CA16
PR-2015-5341-GB ·
Subject to modifications
·R1-07/2019 3
1 USER INTERFACE
There are three types of user interface:
Depending on the type of user interface installed, there are more or less keys available for controlling the
unit and for accessing system information.
Key
Description
W3000,
W3000 base
W3000
compact
[MENU key]: accesses the main menu.
[UP key]: moves around the masks and sets control parameter values
[DOWN key]: moves around the masks and sets control parameter
values
[ENTER key]: confirms entered data.
[ESC key]: goes back one level in the mask tree if you are in the header
masks, or returns to the unit controller.
[ALARM key]: displays the alarms and resets normal operating
conditions.
---
[SETPOINT key]: directly accesses the setpoint menu.
---
[ON/OFF key]: switches the machine on and off.
For each compressor, the following LED's are also located on the W3000 user interface:
Symbol
Colour
Description
Green
If the LED shines steady the compressor is on, if it flashes the compressor
is demanded
Red
The compressor is blocked by a compressor or circuit alarm
Green
The compressor is in the “chiller” mode
Green
The circuit is in the “freecooling” mode
Green
The compressor is in the “heat pump” mode
Green
If the LED shines steady the circuit is in the “recovery mode”, if it flashes
there is a “recovery alarm”
Green
If the LED shines steady the circuit is in the “defrost mode”, if it flashes it
is in the “drip mode”
W3000
W3000 compact
W3000 base

Technical Manual CA16 GL-Series & HeaMo
4PR-2015-5341-GB ·
Subject to modifications ·R1-07/2019
1.1.Menu structure
The tree structures for moving around the various menus are shown below.
Termoregolatore
Selezione
Menù utente
Menù Alarm
Password
utente
Password
costruttore
Power On
Selezione
Menù unità
Selezione
Menù setpoint
Selezione
Menù I/O
Selezione
Menù orologio
Selezione
Menù costruttore
Esc
Esc
Tasto
Menù
Tasto
Alarm
Esc
Esc Menù utente
Menù costruttore
Menù setpoint
Menù I/O
Menù orologio
Esc
Esc
Esc /
Esc /
Esc /
Esc /
Menù unità
Esc
Esc
Esc /
Esc /
Esc Visual. Alarm
Visual. utente
Visual. costruttore
Visual. setpoint
Visual. I/O
Visual. orologio
Visual. unità
Esc /
Esc /
Esc /
Esc /
Esc /
Esc /
Esc /
Esc / Visual. Termoreg.
Tasto
Setpoint
Selezione
Menù storico
Esc Menù storicoEsc / Visual. storicoEsc /
Figure 1.1: menu tree for W3000-W3000 compact
Termoregolatore
Selezione
Menù utente
Menù Alarm
Password
utente
Password
costruttore
Power On
Selezione
Menù unità
Selezione
Menù setpoint
Selezione
Menù I/O
Selezione
Menù orologio
Selezione
Menù costruttore
Esc
Esc
Tasto
Menù
Tasto
Alarm
Esc
Esc Menù utente
Menù costruttore
Menù setpoint
Menù I/O
Menù orologio
Esc
Esc
Esc /
Esc /
Esc /
Esc /
Menù unità
Esc
Esc
Esc /
Esc /
Esc Visual. Alarm
Visual. utente
Visual. costruttore
Visual. setpoint
Visual. I/O
Visual. orologio
Visual. unità
Esc /
Esc /
Esc /
Esc /
Esc /
Esc /
Esc /
Esc / Visual. Termoreg.
Tasto
Setpoint
Figure 1.2: menu tree for W3000 base
Thermoregula
tor
Menu
key
Unit menu
selection
Setpoint
menu
selection
I/O menu
selection
Clock menu
selection
User
menu
selection
Select service
menu
User
Password
Service
password
Alarm menu
Unit menu
Setpoint
menu
I/O menu
Clock menu
User menu
Service menu
Alarm
key
Setpoint
key
Display
Thermoregulat
or
Display alarm
Display unit
Display
setpoint
Display I/O
Display clock
Display user
View service
Thermoregula
tor
Display
Thermoregul
ator
Menu
key
Unit menu
selection
I/O menu
selection
Setpoint
menu
selection
Clock menu
selection
Select log
menu
Select
service
menu
Manufacturer
menu
selection
Service
password
Factory
Password
Service
menu
Manufacture
r
menu
View service
Display
manufacture
r
Alarm
menu
Display alarm
Alarm
key
Setpoint
key
Unit menu
Setpoint
menu
I/O menu
Clock menu
Log menu
View log
Display unit
Display
setpoint
Display I/O
Display
clock

GL-Series & HeaMo Technical Manual CA16
PR-2015-5341-GB ·
Subject to modifications
·R1-07/2019 5
The menus are briefly described below:
•The “Unit Menu” displays information such as temperature, pressure and circuit states.
•The “Setpoint menu” is used to set the setpoints for the various available functions. Different
setpoints can be set depending on the available operating modes (chiller, heat pump and recovery).
Dual setpoint values can also be set for chiller and heat pump operation (only if the digital input is
fitted and the “dual setpoint” function is enabled in the “user menu”).
•The “I/O menu” shows the status of the digital inputs and values read from the analogue inputs.
It also shows the status of the digital outputs and the voltage supplied to the analogue outputs.
If expansions are necessary (depending on the configuration parameters), the inputs and outputs
of the latter are also shown.
•Parameters relative to user programming of the unit can be displayed and set in the “User menu”.
•Unit configuration parameters can be displayed and set in the “manufacturer menu”.
•Service engineers can view and set parameters in the “Assistance menu”.
•The list of alarm events recorded by the unit can be displayed in the “Log menu” (only accessible
if the clock card is installed).
•The “Clock menu”, if the clock board is present, is used to set and display the date and time and
configure the time bands (except for W3000 base).
After enabling time bands from the “enable time bands” parameter in the “user menu”, time bands
can be set and specific operating modes and different setpoints can be set according to
requirements.
Several time bands (up to 10) of different types (A, B, C and D) can be set during the day.
Figure 1.3 shows an example: the beginning of the first time band is set at 00:00 and the end of
the tenth time band is set at 23:59; the end of one time band determines the beginning of the
following one.
To use a smaller number of bands, set the time a band ends to the same time it begins, and that
band will be ignored. Summer and winter setpoints and unit On/Off switching can be set for each
time band. If the unit is switched Off, it will remain in the “Off from time bands” mode.
Figure 1.3: example of setting time bands
Adjustment
Unit off

Technical Manual CA16 GL-Series & HeaMo
6PR-2015-5341-GB ·
Subject to modifications ·R1-07/2019
1.2. Switching the unit on and off
Caution: connect the unit to the power supply at least 8 hours before starting it; if this is not
done, the guarantee will become null and void.
There are different procedures for starting or stopping the unit: using the user interface keys or selecting
from the display. The following procedures have a priority. In the event of conflicts between different
settings, the following priorities apply:
- highest priority: on/off from keypad - on/off from parameter
on/off from digital input
on/off from time bands
- lowest priority: on/off from protocol
using the [ON/OFF] key:
For W3000 and W3000 base
Proceed as follows:
•SWITCHING ON: press the [ON-OFF] key.
•SWITCHING OFF: press the [ON-OFF] key.
In the W3000, the message Com. : ON appears on the display
In the W3000 base, the message “On” appears on the display with the LED on, or “OFF” with the
LED off.
using the On/Off parameter:
For W3000 and W3000 compact
The “Com: On/Off” parameter can be displayed on the user interface. “Off” means that the unit is
switched off while “On” means that the unit is switched on.
Proceed as follows:
•SWITCHING ON: Move to the “On/Off” parameter by pressing [Enter] and then press [Up] or
[Down] until “On” appears. Press [Enter] again to confirm. If “On” continues to be displayed it
means that the unit has been switched on.
•SWITCHING OFF: Move to the “On/Off” parameter and change to “Off” using the same
procedure used to switch the unit on. Press [Enter] again to confirm. If “Off” continues to be
displayed it means that the unit has been switched on.
using the digital input:
Only if the digital input is fitted.
Open the “user menu” and check that the “On/Off enable from digital input” parameter is set to
“Yes”.
When the contact is open the unit is “Off”, when the contact is closed the unit is “On”.
Proceed as follows:
•SWITCHING ON:Close the remote On/Off contact. The “On from digital input” message appears
in the main mask to show that the unit has been switched on.
•SWITCHING OFF:Open the remote On/Off contact. The “Off from digital input” message
appears in the main mask to show that the unit has been switched off.

GL-Series & HeaMo Technical Manual CA16
PR-2015-5341-GB ·
Subject to modifications
·R1-07/2019 7
In the W3000 base the following procedure is used: press [MENU] / select the “User” menu using
the [UP] or [DOWN] keys / press [ENTER] to access the menu / press enter to type in the password
/ press [UP] or [DOWN] to choose the password and [ENTER] to confirm / use the [UP] or [DOWN]
keys to choose the “dI 0” (Enable from digital input) mask / press [ENTER] to view the current
setting of the parameter (“Y” or “N”) / press [ENTER] to modify the parameter (the display flashes)
/ press [UP] or [DOWN] to select one of the two alternatives.
Press the “digital input” button on the panel to switch the unit on and off.
using time bands:
For W3000 and W3000 compact (if the clock board is fitted)
Make sure that the “Clock board not installed” is not displayed in the “clock menu”.
Check that the “Time bands enabled” parameter in the “user menu” is set to “Yes”.
•SWITCHING ON: set the required switching on time in the “clock menu”. The unit switches on
when the set time is reached. The “On from time bands” message appears in the main mask
to show that the unit has been switched on. N.B.: The unit does not switch on if it is set to “Off
from keypad” or “Off from digital input”.
•SWITCHING OFF: set the required switching off time in the “clock menu”. The unit switches off
when the set time is reached. The “Off from time bands” message appears in the main mask
to show that the unit has been switched off.
using the supervision protocol:
Only if the serial board is fitted.
Check that the “Supervisor enable” and “On/Off enable from supervisor” parameters in the “user
menu” are set to “Yes”.
Proceed as follows:
•SWITCHING ON: Send the switching on command from the protocol. The “On from supervisor”
message appears in the main mask to show that the unit has been switched on. N.B.: The unit
does not switch on if it is set to “Off from keypad” or “Off from digital input”.
•SWITCHING OFF: Send the switching off command from the protocol. The “Off from supervisor”
message appears in the main mask to show that the unit has been switched off.
In the W3000 base the following procedure is used: press [MENU] / select the User menu using the
[UP] or [DOWN] keys / press [ENTER] to access the menu / press enter to type in the password /
press [UP] or [DOWN] to choose the password and [ENTER] to confirm / use the [UP] or [DOWN]
keys to choose the “SPr” (Enable from supervisor) mask / press [ENTER] to view the current setting
/ press [ENTER] to see the display flashing / press [UP] or [DOWN] to modify the setting and press
[ENTER] to confirm.

Technical Manual CA16 GL-Series & HeaMo
8PR-2015-5341-GB ·
Subject to modifications ·R1-07/2019
1.3. Setting the operating mode
Caution: Do not switch from chiller to heat pump unless the inlet temperature is above 15°C.
Do not switch from heat pump to chiller unless the inlet water temperature is below 30°C.
There are various ways of setting the operating mode of the unit.
The set operating mode may be any one of the following, as long as they are compatible with the unit:
Operating mode
Description
W3000 base
chiller
ch
Chiller
chiller+rec
Chiller plus recovery
heatpump
hp
Heat pump
summer ch
Chiller in summer mode
summer ch+rec
Chiller plus recovery in summer mode
summer rec
Recovery in summer mode
recovery
Recovery only
summer auto
Automatic in summer mode
winter hp
Heat pump in winter mode
winter rec
Recovery in winter mode
winter auto
Automatic in winter mode
auto
Automatic
The following procedures have a priority: in the event of conflicts between opposing settings the following
priorities apply:
- highest priority: change through parameter
chiller/heat pump from digital input
ch/ch+rec from digital input
- lowest priority: change through protocol
Using the parameter:
Make sure the unit is “Off”. Access the “setpoint menu” and display the “Operating mode” parameter. Move
to the “Operating mode” parameter by pressing [Enter] and modify the parameter by pressing [Up] or
[Down]. Press [Enter] again to confirm. If the set message continues to be displayed it means that
operating mode has been changed.
In the W3000 base the key sequence is: switch off the unit using the [ON/OFF] key / press the [setpoint]
key / select MODE with the [UP] or [DOWN] keys / press [Enter] / press [Enter]. At this point the cursor
flashes. Press the [UP] or [DOWN] keys to select either “ch”= chiller or “hp”= heat pump. Press [Enter] to
confirm.
Using the digital input:
Only for heat pump units and only if the digital input is present.
Check that the “Chiller/Hp enable from digital input” parameter in the “user menu” is set to “Yes”.
When the contact is open the unit is in the “heat pump” mode, when the contact is closed the unit is in the
“chiller” mode. Switching the digital input switches the unit off, changes the operating mode and switches
the unit on again.
In the W3000 base access the “user menu” / select “DI S” by pressing the [UP or DOWN] key/ press [Enter]
to view the current setting / press [Enter] to see the current setting flashing and change it using the [UP
or DOWN] key / press [Enter] to confirm the new setting.

GL-Series & HeaMo Technical Manual CA16
PR-2015-5341-GB ·
Subject to modifications
·R1-07/2019 9
Using the recovery from digital input command:
Only for “chiller plus recovery” units and only if the digital input is present. This mode is not present in the
W3000 base.
Proceed as follows: check that the “Recovery control enable from digital input” parameter in the “Recovery
menu” is set to “Yes”.
When the contact is open the unit is in the “chiller+rec” mode, when the contact is closed the unit is in the
“chiller” mode. Switching the digital input switches the unit off, changes the operating mode and switches
the unit on again.
Using the supervision protocol:
Only applicable if the serial board is fitted.
Check that the “Supervisor enable” and “Enable operating mode from supervisor” parameters in the “user
menu” are set to “Yes”.
Make sure the unit is “Off”. Send the change operating mode command from the protocol. The operating
mode only changes if the unit is switched off.
In the W3000 base press [ON/OFF] to switch the unit off. Access the “user menu” / press [UP] or [DOWN]
to select “SV M”/ press [Enter] to view the set mode / press [Enter] to see the setting flashing / press [UP]
or [DOWN] to modify the setting / press [Enter] to confirm the new setting.
Send the change operating mode command from the protocol. The operating mode only changes if the unit
is switched off.

Technical Manual CA16 GL-Series & HeaMo
10 PR-2015-5341-GB ·
Subject to modifications ·R1-07/2019
1.4. Setting adjustment methods
Depending on the type of compressor used, various adjustment methods may be selected.
Compressor
Unit
Adjustment method
Hermetic
Water/water heat pump
•Quick Mind on outlet probe
•Quick Mind on inlet probe
•Proportional step on inlet probe
•Proportional step on inlet probe + integral on inlet probe
Water/water chiller
Evaporating units
Water/air heat pump
Water/air chiller
Chiller with heat recovery
Chiller with free-cooling
•Proportional step on inlet probe
•Proportional step on inlet probe + integral on inlet probe
Energy Raiser
Heat pump with heat recovery
Alternative
Chiller with free-cooling
•Proportional step on inlet probe
•Proportional step on inlet probe + integral on inlet probe
Energy Raiser
Heat pump with recovery
Chiller with heat recovery
Water/water heat pump
Water/water chiller
Evaporating units
Water/air heat pump
Water/air chiller
Screw
Water/water heat pump
•Modulating on outlet probe
•Proportional step on inlet probe
•Proportional step on inlet probe + integral on inlet probe
Water/water chiller
Evaporating units
Water/air heat pump
Water/air chiller
Chiller with heat recovery
Chiller with freecooling
Energy Raiser
•Proportional step on inlet probe
•Proportional step on inlet probe + integral on inlet probe
Heat pump with recovery
Centrifuge
Water/water chiller
•Proportional on inlet probe + integral on outlet probe
Water/air chiller
Table 1.1: adjustment methods available by compressor type
The various adjustment methods are described below.

GL-Series & HeaMo Technical Manual CA16
PR-2015-5341-GB ·
Subject to modifications
·R1-07/2019 11
1.4.1. Proportional step adjustment on inlet probe
Some examples of proportional “step” adjustment on the inlet temperature probe:
Chiller (n° steps =2)
Pout
Tin
proportional band
Figure 1.4: Tin is the inlet variable, Pout is the percentage of delivered power (chiller).
▄= Set + proportional band/2
Heat pump (n° steps =2)
Pout
Tin
proportional band
Figure 1.5: Tin is the inlet variable, Pout is the percentage of delivered power (heat pump).
▄= Set + proportional band/2

Technical Manual CA16 GL-Series & HeaMo
12 PR-2015-5341-GB ·
Subject to modifications ·R1-07/2019
The following tables show some typical values for the parameters in question. The theoretical maximum and
minimum outlet temperature values refer to operation at nominal flow rates ( with a thermal head at the
evaporator of 5 °C and sufficient water in the system to ensure a litre / KW ratio equal to or greater than 7).
N°
steps
Setpoint
(°C)
Proportional band
(°C)
Theoric min. outlet T
(°C)
Theoric max. outlet T
(°C)
2
9.5
2.5
5.7
10.8
4
7
5
5.7
8.3
Table 1.2: normal setpoint and proportional band values according to the number of steps (chiller).
N°
steps
Setpoint
(°C)
Proportional band
(°C)
Theoric min. outlet T
(°C)
Theoric max. outlet T
(°C)
2
42.5
2.5
41.2
46.3
4
45
5
43.7
46.3
Table 1.3: normal setpoint and proportional band values according to the number of steps (heat pump).

GL-Series & HeaMo Technical Manual CA16
PR-2015-5341-GB ·
Subject to modifications
·R1-07/2019 13
1.4.2. Proportional step adjustment on inlet probe + integral on inlet
probe
This adjustment method is based on the sum of two components: proportional and integral.
The proportional component generates the percentage demand for activating/deactivating the steps, as
illustrated in the previous paragraph “Proportional step adjustment on inlet probe”.
The integral component adds the integral error to the proportional component at regular intervals (integral
time: parameter 55.02). The integral error is calculated according to the following formula:
Integral error =
Inlet temperature –Setpoint
x 100
[%]
Proportional band
However, the integral component is limited (integral limit: parameter 55.03) to prevent the adjustment
from becoming unstable.
If the inlet temperature varies by 5% or more in one second, a rapid change, therefore, the integral
component is not calculated.
Set point
Set point
+
P. band
Tin
Compr.
On
2
1
0 %
50 %
100 %
Integral
+ limit
- limit
Prop.
+
Integral
0 %
50 %
100 %
Integral
time
Integral
time
Integral
time
Integral
time
Integral
time
Example
2-step unit
Band: 5°C
Integral limit: 15%
Fig 1.6 Example of a 2 step adjustment in the chiller mode

Technical Manual CA16 GL-Series & HeaMo
14 PR-2015-5341-GB ·
Subject to modifications ·R1-07/2019
1.4.3. Quick mind adjustment
Users only need set the required setpoint as the other parameters are adapted to the system by the Quick
Mind algorithm. The values normally used are:
SETPOINT Chiller on inlet
11.0 °C
SETPOINT Chiller on outlet
7.0 °C
SETPOINT Heat pump on inlet
42.5 °C
SETPOINT Heat pump on outlet
45.0 °C
QUICK MIND is a self-adapting algorithm for adjusting the temperature of the water treated by an all-in-
one unit. The following figure shows how this adjustment is made:
Tin/Tout
ZONA NEUTRA
Setpoint
Attivazione compressoriDisattivazione compressori
ESTATE
Tin/Tout
ZONA NEUTRA
Setpoint
Attivazione compressori Disattivazione compressori
INVERNO
Figure 1.7: QUICK MIND adjustment model (chiller and heat pump)
The setpoint remains within a dead area. If the temperature also remains within this area, no change is
made to the number of active compressors.
When the temperature leaves the dead area following a change in system load, the compressors are either
activated or deactivated in order to return the temperature to the dead area.
The amplitude of the neutral zone depends on the dynamic characteristics of the system and, in particular,
on the amount of water it contains and the load. The self-adapting algorithm is able to “measure” system
dynamics and calculate the minimum dead area in order to respect compressor activation times and the
maximum number of start-ups per hour.
Both return and delivery temperatures can be adjusted.
Special functions are also present which reduce the number of compressor start-ups in the event of very
low loads or start-ups of units with significantly higher or lower temperatures than the setpoint.
Compressors
deactivated
SUMMER
WINTER
DEAD AREA
DEAD AREA
Compressors
deactivated
Compressors
activated
Compressors
activated

GL-Series & HeaMo Technical Manual CA16
PR-2015-5341-GB ·
Subject to modifications
·R1-07/2019 15
2 compressors - with maximum permitted number of start-ups per hour 8
Litres/kW
10.5
9.5
8.5
7.5
6.5
5.5
4.5
3.5
2.5
out
3.2
3.2
3.4
3.4
3.6
3.8
4.0
4.4
5.2
2 compressors - with maximum permitted number of start-ups per hour 12
Litres/kW
10.5
9.5
8.5
7.5
6.5
5.5
4.5
3.5
2.5
out
3.0
3.0
3.0
3.2
3.2
3.4
3.6
3.8
4.3
4 compressors - with maximum permitted number of start-ups per hour 8
Litres/kW
10.5
9.5
8.5
7.5
6.5
5.5
4.5
3.5
2.5
out
1.8
1.8
1.8
1.8
1.8
1.9
2.0
2.3
2.7
4 compressors - with maximum permitted number of start-ups per hour 12
Litres/kW
10.5
9.5
8.5
7.5
6.5
5.5
4.5
3.5
2.5
out
1.8
1.8
1.8
1.8
1.8
1.9
2.0
2.3
2.7
Table 1.4: maximum theoretical delivery temperature range at constant part load (depending on the quantity of water
contained in the system)
An example of real data acquired during operation with the Quick Mind adjuster on the delivery side is
shown below.
Reference is made to the following figure:
Fase di avviamento controllato = Controlled starting phase
Adattamento zona neutra = Adaptation to dead area
Temperatura uscita evaporatore = Outlet temperature of evaporator
Temperatura ingresso evaporatore = Inlet temperature of evaporator
1 compressore attivo = 1 compressor active
2 compressori attivi = 2 compressors active
Figure 1.8: example of real data with quick-mind outlet adjustment (x-axis: time in [s]; y-axis: Tout in [°C] ).
This is an example of start-up with a very high initial temperature compared with the setpoint (7°C). About
10 seconds after data acquisition began, one compressor switches on. The second compressor does not
switch on immediately as the algorithm which handles start-up checks if one compressor is enough to
return delivery temperature to the setpoint and avoid unnecessary start-ups. As the delivery temperature
is still at 12 °C after about 200 seconds, the second compressor is also switched on, otherwise it would
take too long to reach setpoint.
Following the controlled starting phase, the delivery temperature falls until it “enters” the dead area. The
algorithm (at t= 350 s) begins to adapt the amplitude of the dead area in order to respect compressor
safety times. As can be seen, the dead area is later reduced (t= 780 s, 950 s) to the absolute minimum
amplitude which allows safety times to be respected. It can also be seen that the compressors are activated
and deactivated when the outlet temperature reaches the upper or lower limits of the dead area. The
example shows that outlet temperature varies by about 3.5 °C during regular operation.

Technical Manual CA16 GL-Series & HeaMo
16 PR-2015-5341-GB ·
Subject to modifications ·R1-07/2019
1.4.4. Modulating adjustment of screw compressors
With screw compressors, modulating adjustment is performed on the outlet probe.
Modulating adjustment is only available on “Bitzer” screw compressors.
set point t [min]
Tout [°C]
ZN
B(increase)
C(decrease)
Reference is made to the figure
to the left:
The setpoint remains within a
dead area. If the temperature
also remains within this zone,
no change is made to the
number of active compressors
or their load percentages
(position of modulating
chamber).
When the temperature rises
above zone B following a change
in the system load, the
compressors are activated in
order to return the temperature
to the dead area.
Inside zone B, if the outlet
temperature derivative is
positive, compressor power is
increased in order to return the
temperature to the dead area
(ZN). The further away the
temperature is from the
setpoint, the greater the
increase is.
Figure 1.9: modulating adjustment for screw compressors
When the temperature falls below zone C following a change in the system load, the compressors are either
deactivated in order to return the temperature to the dead area.
Inside zone C, if the outlet temperature derivative is negative, compressor power is decreased in order to
return the temperature to the dead area (ZN). The further away the temperature is from the setpoint, the
greater the decrease is.
The amplitude of the neutral zone depends on the dynamic characteristics of the system and, in particular,
on the amount of water it contains and the load. The self-adapting algorithm is able to “measure” system
dynamics and calculate the minimum dead area in order to respect compressor activation times and the
maximum number of start-ups per hour.
When a second or subsequent compressor is switched on, the ones that are already running are forced to
a minimum, and the subsequent power increases/decreases are applied to all the compressors.

GL-Series & HeaMo Technical Manual CA16
PR-2015-5341-GB ·
Subject to modifications
·R1-07/2019 17
1.4.5. Adjustment method for centrifuge compressors
Adjustment is combined on the inlet temperature and integral on the outlet temperature.
Some diagrams outlining how this works are shown below.
Suppose we have a single compressor unit.
set point
(0% P09.42)
Set point + Proportional
band (100%)
Min
Max
Absorbed
power
[Kw]
% compressor
switch-on (P09.43)
Thermoregulator
power
request
[%]
Figure 1.10: Adjustment for a single-compressor unit. Min=theoretical minimum electrical power absorbed by a
compressor, Max=theoretical maximum electrical power absorbed by a compressor
Let us take a close look at how the compressor is activated.
When the system return temperature lies in zone A (figure 1.11a) or less than the setpoint, the compressor
is off. The amplitude of zone A normally coincides with the temperature difference at the evaporator with
the compressor running at minimum power.
When the return temperature exceeds zone A (figure 1.11b), the compressor is switched on and then
switches off if the temperature falls below the setpoint.
If the return temperature lies in zone B (figure 1.11c), the power of the compressor is modulated according
to system requirements.
set point
set point
+
proportional band
start compressor 1
t [min]
Tin [°C]
A
OFF
ON
set point
set point
+
proportional band
start compressor 1
t [min]
Tin [°C]
OFF
ON
A
Figure 1.11 a)
Figure 1.11 b)

Technical Manual CA16 GL-Series & HeaMo
18 PR-2015-5341-GB ·
Subject to modifications ·R1-07/2019
set point
set point
+
proportional band
start compressor 1
t [min]
Tin [°C]
OFF
ON
max
min
Pass [Kw]
B
Figure 1.11 c)
Suppose we have a unit with more than one compressor.
Set point + Banda
proporzionale (100 %)
2x Min
Max
% accensione
2° compressore
Min
% accensione
1° compressore
Potenza
richiesta del
termoregolatore
[%]
Potenza
assorbita
[Kw]
set point
(0%)
Figure 1.12: Adjustment for a twin-compressor unit. Min=theoretical minimum electrical power absorbed by a compressor,
Max=theoretical maximum electrical power absorbed by a compressor.
Absorbed
power
[Kw]
%
compressor 1
switch-on
%
compressor 2
switch-on
Set point + prop.
band (100 %)
Thermoregulator power
Request [%]

GL-Series & HeaMo Technical Manual CA16
PR-2015-5341-GB ·
Subject to modifications
·R1-07/2019 19
Let us take a close look at how the compressor is activated.
The amplitude of zone A coincides with the temperature difference at the evaporator, with all the
compressors running at minimum power.
Zone A is the sum of the zones of each single compressor (A1+A2+…).
When the temperature lies in one of the An zones, the power of the active compressors is modulated
according to system requirements.
When moving from an An zone to the one just above it, the active compressors are taken to minimum
power while waiting for the next one to be switched on. After that, they continue to be modulated in the
new zone.
When moving from an An zone to the one just below it, one of the compressors is switched off while the
others are kept at a minimum.
set point
set point
+
banda proporzionale
start 1° compressore
t [min]
Tin [°C]
A1
min
max
A2
start 2° compressore
max
min
Compr.1
Compr.2
A
B
Pass [Kw]
Pass [Kw]
Figure 1.13: adjustment for a twin-compressor unit
S e t p o i n t
+
p r o p o r t i o n a l b a n d
s t a r t c o m p r e s s o r 2 °
s t a r t c o m p r e s s o r 1 °

Technical Manual CA16 GL-Series & HeaMo
20 PR-2015-5341-GB ·
Subject to modifications ·R1-07/2019
The following figure, instead, gives an example of the integral contribution of the adjustment method.
Set point
Set point
+
P. band
Tin
Pass
[KW]
Max
Min
0 %
Start
compressor
(P09.43)
100 %
Integral
+ limit
(P39.07)
- limit
(P39.07)
Integral
time
Integral
time
Integral
time
Integral
time
Integral
time
Example
1-compressor unit
Band: 6°C
Integral limit: 20%
Integral time: 90 s
Set point
Set point
+
P. band
Tout
Figure 1.14: Adjustment for a single-compressor unit: integral contribution
This manual suits for next models
1
Table of contents
Other FläktGroup Heating System manuals
Popular Heating System manuals by other brands

Vallox
Vallox 132 E Series Technical specifications
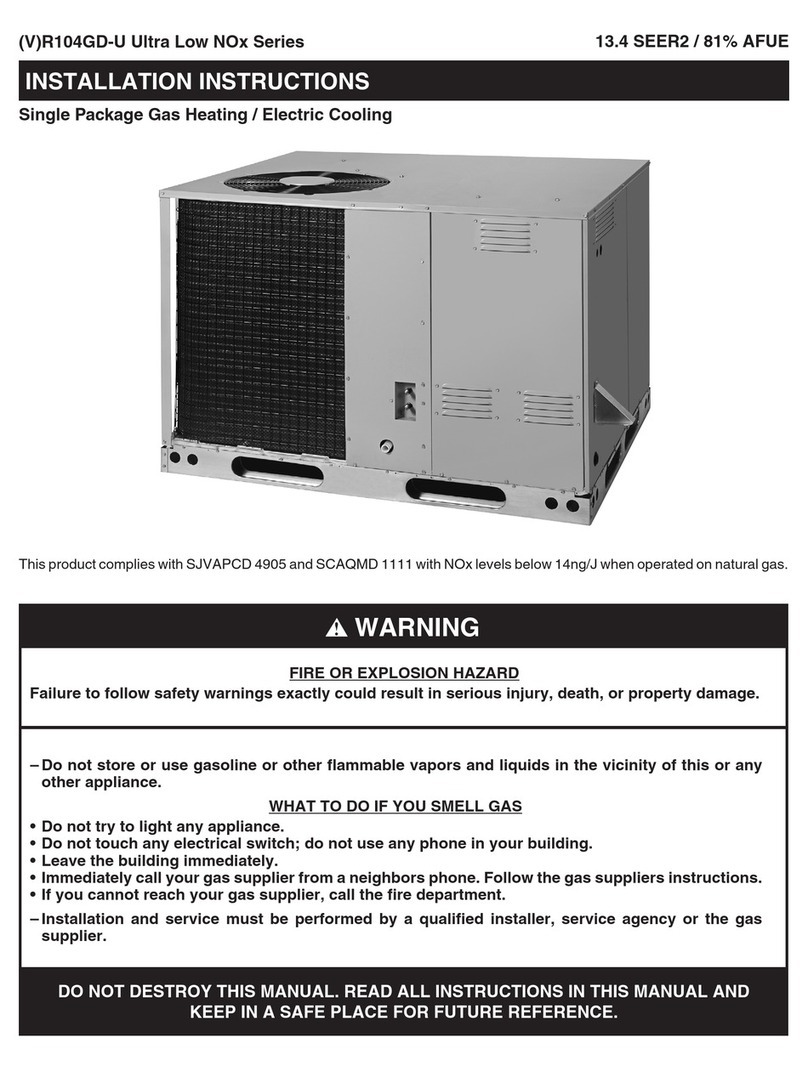
Trane
Trane VR104GD-U Series installation instructions
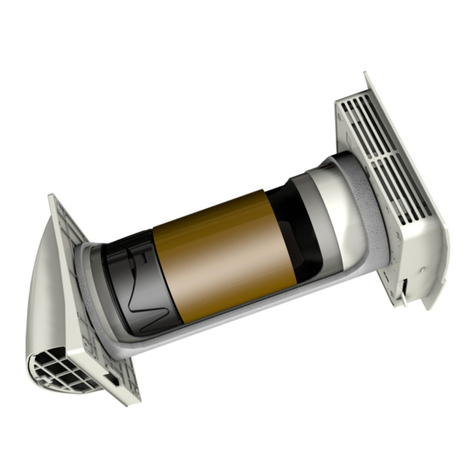
MERK
MERK MEnV 180 Pro Operating & assembly instructions
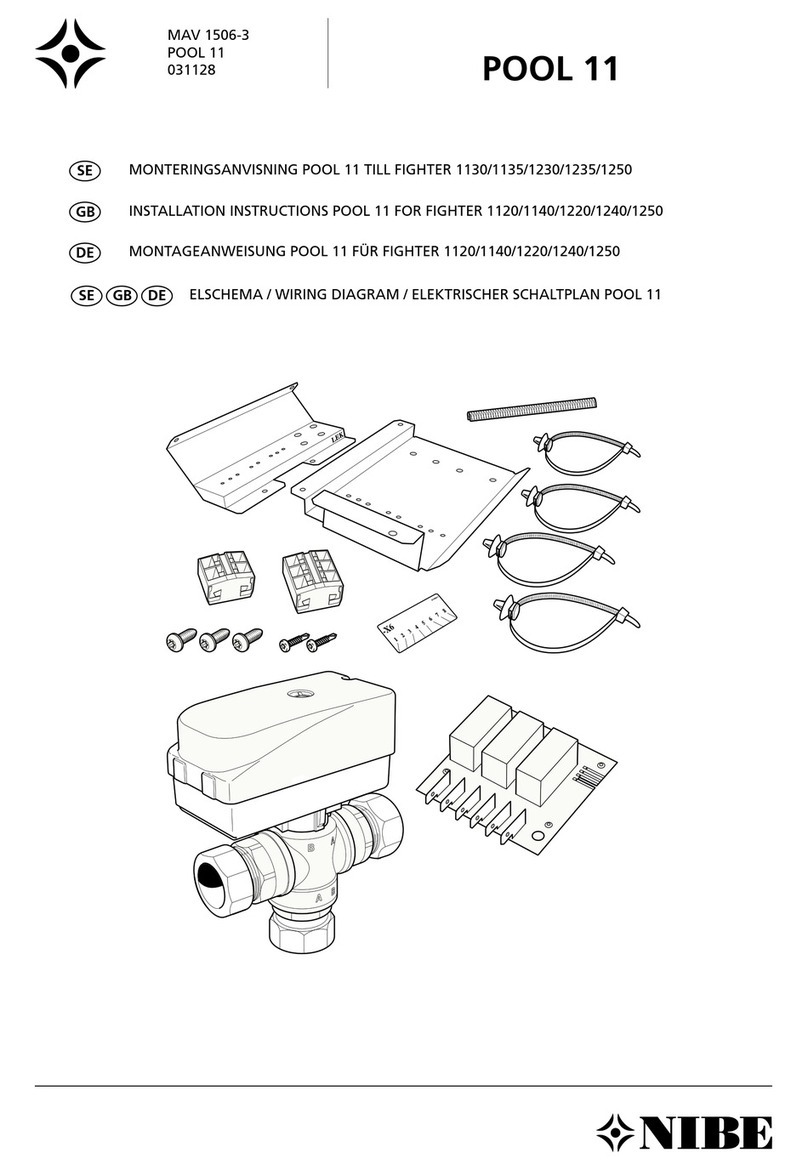
Nibe
Nibe POOL 11 installation instructions
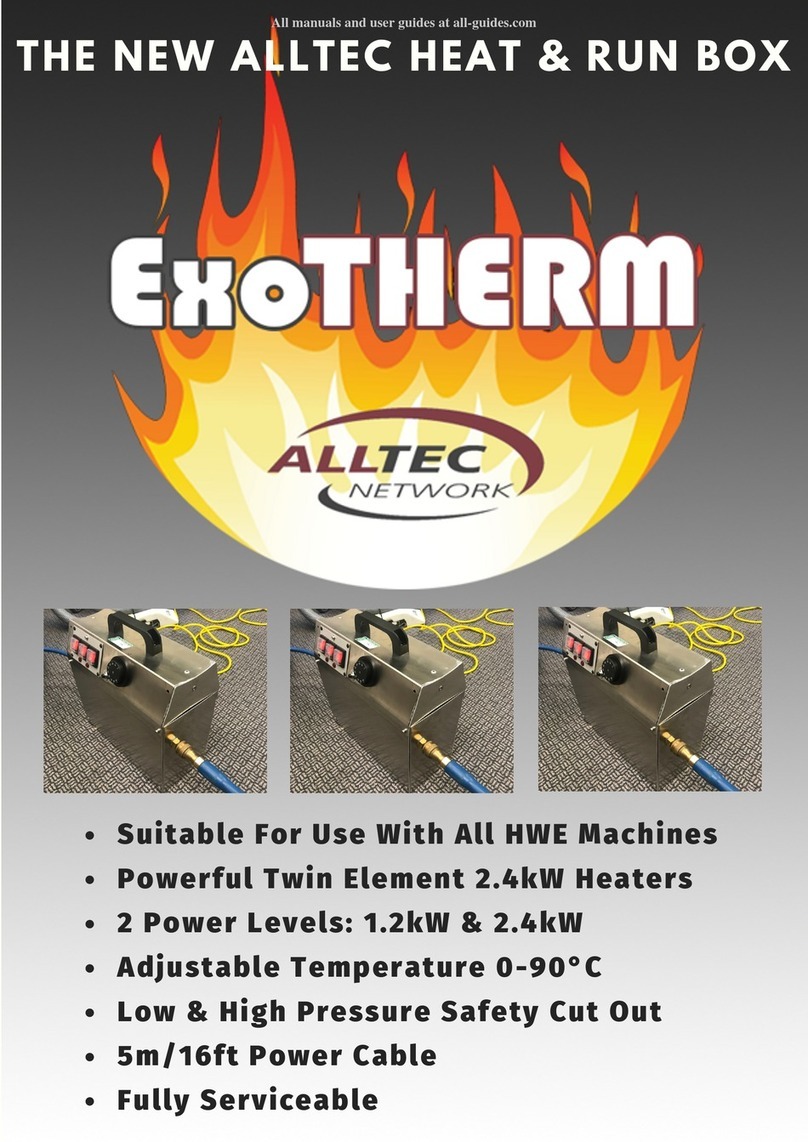
ALLTEC
ALLTEC ExoTHERM manual
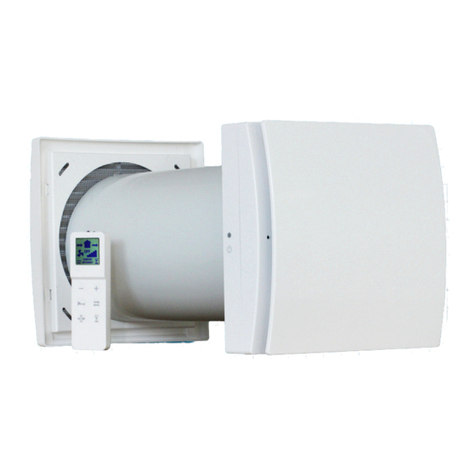
Lindab
Lindab PENNY QN Instructions for installation, use and maintenance manual
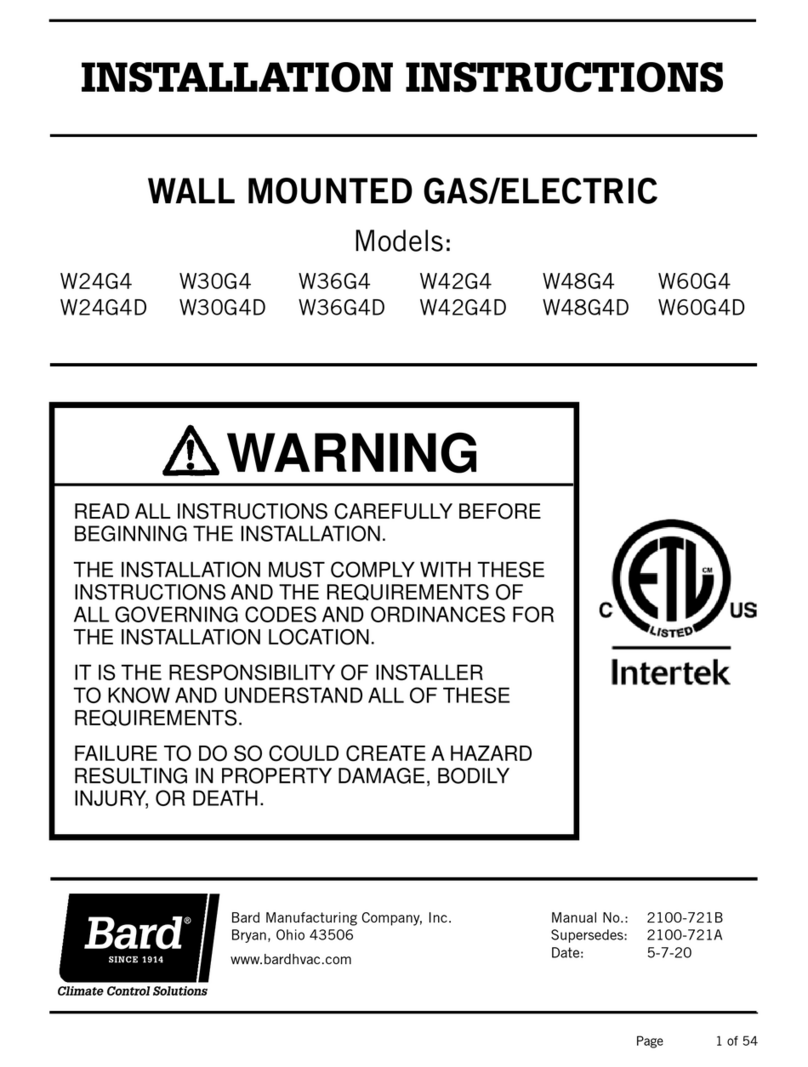
Bard
Bard W24G4 installation instructions
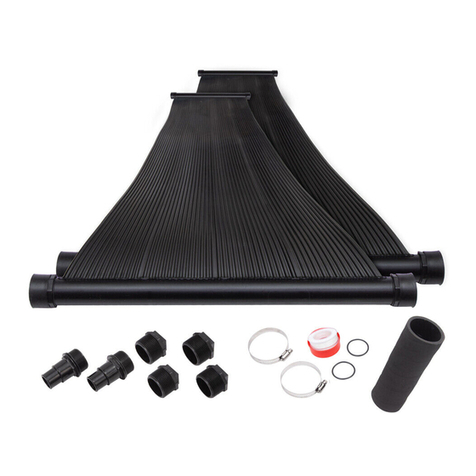
Sunsolar Energy Technologies
Sunsolar Energy Technologies SQ-2212 Installation & operation manual
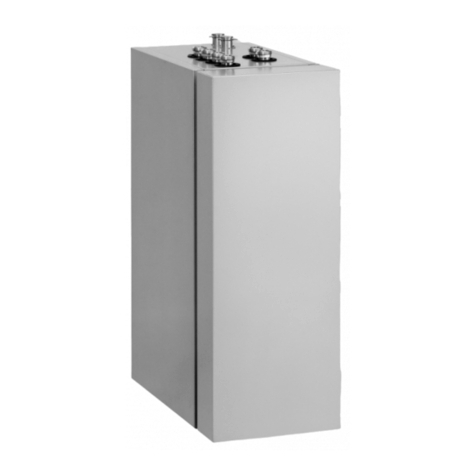
Viessmann
Viessmann AC-Box Installation and service instructions for contractors
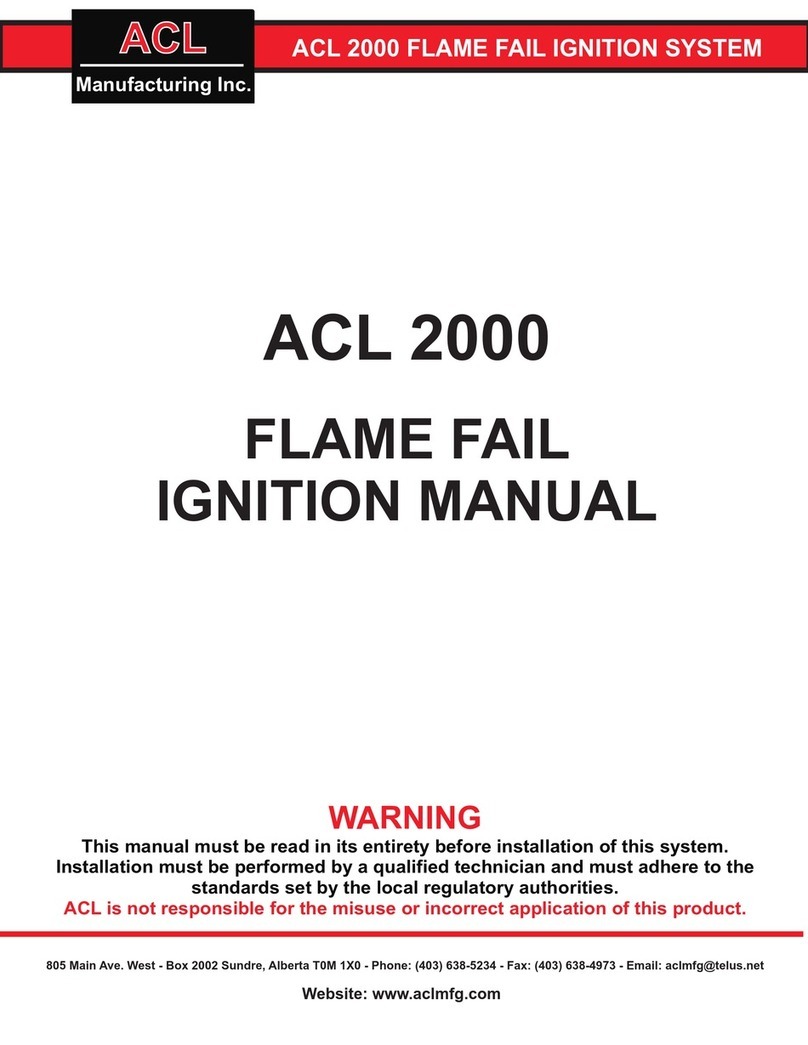
ACL
ACL 2000 manual

Vent-Axia
Vent-Axia HR300 Installation and maintenance instructions
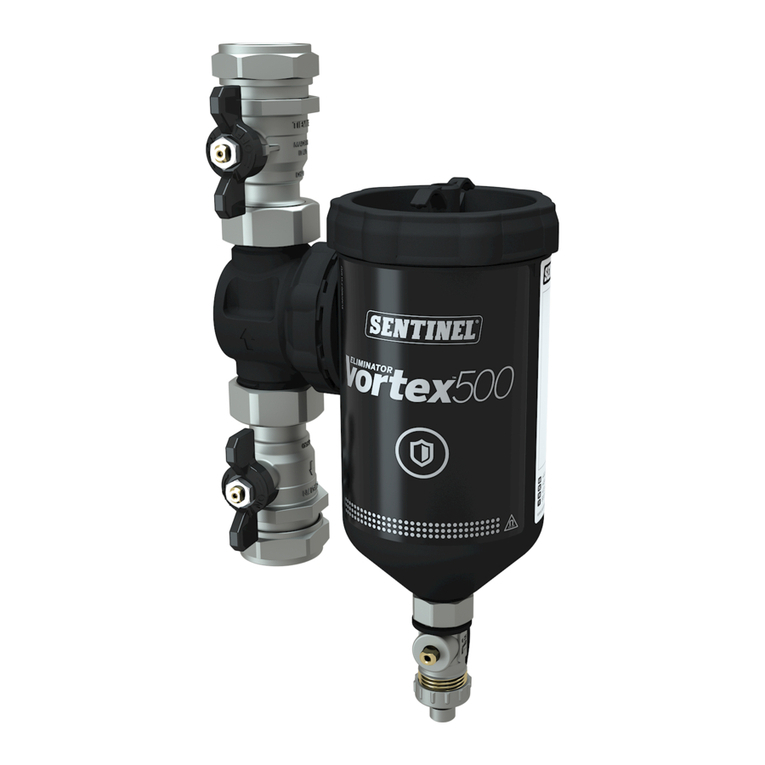
Sentinel
Sentinel ELIMINATOR installation manual