Flowserve GESTRA NRG 26-21 User manual

1
GESTRA Steam Systems
GESTRA
NRG 2621
Installation Instructions 81877402
Level Electrode
NRG 26-21
EN
English

2
Contents
Usage for the intended purpose ..............................................................................................................4
Safety note .............................................................................................................................................4
Danger ...................................................................................................................................................4
Attention.................................................................................................................................................4
ATEX (Atmosphère Explosible).................................................................................................................4
Note on the Declaration of Conformity / Declaration by the Manufacturer ..........................................4
Important Notes
Page
Explanatory Notes
Scope of supply......................................................................................................................................5
System description .................................................................................................................................5
Function .................................................................................................................................................5
Design....................................................................................................................................................5
NRG 26-21 ...........................................................................................................................................12
Attention...............................................................................................................................................12
Note .....................................................................................................................................................12
Tools.....................................................................................................................................................12
Examples of installation ........................................................................................................................13
Key.......................................................................................................................................................14
Installation
NRG 26-21 ......................................................................................................................................... 6, 7
Name plate / marking .............................................................................................................................7
Dimensions.............................................................................................................................................8
Technical Data
NRG 26-21 .............................................................................................................................................9
Key.......................................................................................................................................................11
Design
NRG 26-21 ...........................................................................................................................................10
Key.......................................................................................................................................................11
Functional Elements

3
Electrical Connection
NRG 26-21 ...........................................................................................................................................15
Wiring diagram.....................................................................................................................................16
Setting measuring range.......................................................................................................................16
Tools.....................................................................................................................................................16
Checking electrical connection .............................................................................................................20
Checking measuring voltages ...............................................................................................................20
Contents – continued –
Commissioning
Page
Danger .................................................................................................................................................22
Disposal................................................................................................................................................22
Decommissioning
NRG 26-21 ...........................................................................................................................................20
Note .....................................................................................................................................................20
Operation
Fault-finding list for troubleshooting......................................................................................................21
Operational Malfunctions
Factory setting......................................................................................................................................17
Establishing active measuring range.............................................................................................17 – 19
Attention...............................................................................................................................................17
Note .....................................................................................................................................................20
Basic Settings

4
Important Notes
Danger
When loosening the electrode live steam or hot water might escape.
This presents the danger of sever scalding.
It is therefore essential not to dismantle the electrode unless the boiler pressure is
verified to be zero.
The electrode is hot during operation.
This presents the risk of severe burns to hands and arms.
Installation and maintenance work should only be carried out when the system is cold.
Usage for the intended purpose
Use level electrode NRG 26-21 only in conjunction with level switches NRR 2..., NRS 2... or NRT 2... for
indicating liquid levels.
Note that the equipment must not be used in explosion risk areas.
Safety note
The equipment must only be installed and commissioned by qualified and adequately trained per-
sonnel.
Maintenance and retrofitting must only be performed by entrusted personnel who – through adequate
training – have achieved a recognised level of competence.
Attention
The name plate specifies the technical features of the equipment. Note that any piece of
equipment without its specific name plate must neither be commissioned nor operated.
ATEX (Atmosphere Explosible)
According to the European Directive 94/9/EC the equipment must not be used in potentially explosive
areas.
Note on the Declaration of Conformity / Declaration by the Manufacturer
For details on the conformity of our equipment according to the European Directives see our Declaration
of Conformity or our Declaration of Manufacturer.
The current Declaration of Conformity / Declaration of Manufacturer are available in the Internet under
www.gestra.de/documents or can be requested from us.

5
Explanatory Notes
System description
The level electrode NRG 26-21 works according to the capacitance measurement principle. The
NRG 26-21 is used for signalling different levels in electrically conductive and non-conductive liquids:
nLevels maintained within the control band defined by two preset limits
The preamplifier NRV 2-29 is integrated in the terminal box of the level electrode.
Function
Design
The principle of capacitance measurement is applied to determine the level. The electrode rod and
the vessel wall form a capacitor. If the level of the dielectric located between the two capacitor plates
changes, the current which flows through the plates changes proportionally to the level.
A dielectric is defined as an insulating substance, which excludes many liquids such as water. In
order to receive a useful measuring result the measuring rod, which is submerged to varying depths
in the liquid, must be completely insulated. After the calibration of the zero point / measuring range
(0 % / 100 %), the level can be read off from a remote display unit. The level measuring range can be
changed during operation.
NRG 2621
Screwed design ¾", DIN ISO 228-1, Fig. 2
Scope of supply
NRG 2621
1 Level electrode NRG 26-21 with joint ring D 27 x 32 DIN 7603, 1.4301 bright annealed
1 Installation manual

6
Type approval no.
TÜV · WR · 01-320
Service pressure
PN 40, 32 bar g at 238 °C
Connections
Screwed ¾", DIN ISO 228-1
Materials
Terminal box: PPO (Noryl®)
Sheath: 1.4301 X5 CrNi18-10
Screwed union: 1.4571 CrNiMoTi17-12-2
Measuring electrode: 1.4571 CrNiMoTi17-12-2
Electrode insulation: PTFE
Supply voltage
12 V
Length supplied / measuring range
$Max. installation length at 238 °C
%Measuring range
$ %
373 300
477 400
583 500
688 600
794 700
899 800
1004 900
1110 1000
1214 1100
1319 1200
1423 1300
1528 1400
1636 1500
2156 2000
NRG 2621
Technical Data

7
Technical Data – continued –
NRG 2621 – continued –
Sensitivity
Range 1: Water ≥0.5 µS/cm
Range 2: Water ≥20 µS/cm
Range 3: Fuel oil EL εr2.3
Cable entry
Cable gland with integral cable clamp M 16
Protection
IP 65 to DIN EN 60529
Max. admissible ambient temperature
70 °C
Weight
approx. 1.8 kg
Name plate / marking
Fig. 1
32 bar (464psi)
238°C (460°F)
T amb = 70°C (158 °F)
NRG 26-21
Betriebsanleitung beachten
See installation instructions
Voir instructions de montage
Pmax
Tmax
PN 40 G 3/4 1.4571 IP 65
Mat.Nr.:
GESTRA AG D-28215 Bremen
TÜV.WR/WRS.09-317 TÜV.WR.06-320
Equipment designation Safety note
Disposal note
CE marking
Pressure rating, thread type,
material number,
type approval number
Manufacturer Material number

8
Technical Data – continued –
Dimensions
%Constant length (no elongation)
Fig. 2
∅ 42
¾"
$%
37
26
280

9
1
Design
Fig. 3
Fig. 4
N 1
N 10
0.5
∅ 33
¾" DIN 228
NRG 2621
2
4
3

10
Functional Elements
Fig. 5
Preamplifier NRV 2-29 integrated in the terminal box
7
5
!
0
9
NRG 2621
6
8
MAX 70 C
MAX 95%
%
IP 65
"
§

11
1Thermal insulation provided on site, d = 20 mm (without thermal insulation of steam boiler)
2Seating surface
3Joint ring D 27 x 32, DIN 7603 – 1.4301
4Electrode thread ¾", DIN ISO 228-1
5Screw M4
6Cover
7Seal
8Terminal strip
9Cable entry M16 (PG 9)
0Sealing plate
!Terminal box (with preamplifier NRV 2-29)
"Code switch
§Contact plate
$Max. installation length at 238 °C
%Measuring range
Key
Design / Functional Elements

12
Attention
nThe seating surface of the threads and flanges provided on the vessel or boiler
standpipe must be accurately machined, Fig. 4.
nDo not bend electrode rod when mounting.
nDo not lag electrode body.
nDo not insulate electrode thread with hemp or PTFE tape.
Installation
NRG 2621
1. Check seating surfaces of threads or flange provided on vessel or boiler standpipe, Fig. 4.
2. Place joint ring 3onto seating surface 2of the electrode, Fig. 3.
Use only joint ring (of stainless steel 1.4301) D 27 x 32 to DIN 7603 supplied with electrode.
3. Apply a light smear of silicone grease (e. g. DOW Corning 111 Compound) to electrode thread 4.
4. Screw level electrode into threads or flange provided on vessel or boiler standpipe and tighten with
a 41 mm open-end spanner. The torque required for tightening is 160 Nm when cold.
Note
nFor the approval of the boiler standpipe with connecting flange the relevant local or
national regulations must be considered.
nSee four examples of installation of page 13.
Tools
nOpen-end spanner 41 mm A. F.

13
Installation – continued –
Examples of installation
&
DN 100
Fig. 8
∅20
20
24.5 24.5
∅20
Fig. 6 Fig. 7
DN 50
≤ 90°
DN 50
¾"
¾"
¾" ¾"
≥10
∅20
≤ 90°
≤ 90°
∅ 20
∅
20
20
≥ 10
∅20
DN 20
DN 20
Fig. 9
≤20
¾"
≤10
20
Centre distance
/
(
)
a
e
f
=
&
)
e
c
/
=
g
(
b
&
=
)
e
/
DN 20
&
/
(
)
a
e
f
=

14
&Flange PN 40, DN 50, DIN 2527
Flange PN 40, DN 100, DIN 2527
/For the approval of the boiler standpipe with connecting flange the relevant regulations must be
considered.
(Vent hole
)High water (HW)
=Electrode rod d = 15 mm
aProtection tube DN 80
bProtection tube DN 100
cElectrode distance ≥ 14 mm (LW)
dElectrode distance ≥ 40 mm (LW)
eLow water (LW)
fReducer DIN 2616-2, part 2 K-88.9 x 3.2 - 42.4 x 2.6 W
gReducer DIN 2616-2, part 2 K-114.3 x 3.6 - 48.3 x 2.9 W
Key
Installation – continued –

15
Electrical Connection
Electrical connection via four pole connector.
Note that screened four core cable, e. g. I-Y(St)Y 2 x 2 x 0.8 or LICYC 4 x 0.5 mm2is required for wiring
the electrode.
Max. length 100 m with conductivities from 10 μS/cm.
Max. length 30 m with conductivities from 0.5 μS/cm.
1. Undo screw 5, Fig. 5.
2. Take the terminal box off the level electrode, leaving the sealing plate 0on the contact plate §.
3. Remove cover 6with seal 7.
4. Detach cable gland 9from terminal box !.
5. Run cable through cable gland 9of the terminal box !and connect the terminals of the terminal
strip 8according to the wiring diagram.
6. Replace cover 6and insert screw 5.
7. Put terminal box onto the level electrode and fix it firmly by tighten screw 5.
NRG 2621

16
Tools
nScrewdriver for cross-recess head screws, size 1
nScrewdriver for slotted screws, size 2.5, completely insulated to VDE 0680
nOpen-end spanner 17 mm A. F.
Electrical Connection – continued –
Setting measuring range
Adjust the preamplifier NRV 2-26 integrated in the terminal box !to the operating conditions
prevailing in your installation before putting the level electrode into operation. Make sure that the
measuring range setting is correct for your application and check whether the fluid to be controlled is
electrically conductive or not before commissioning the electrode.
Wiring diagram
Fig. 10
≥ 0 V ≤ 7 V DC
12 V DC
NRG 2621

17
Basic Settings
Factory setting
The default setting of the code switch "is the max. measuring range for water (conductivity
≥ 20 μS/cm. The max. measuring range is the length %(distance between lower and upper measuring
point) plus 26 mm, see Fig. 11.
The level electrode features the following factory set default values:
nMeasuring range up to 350 mm: Code switch "position 4, 5 ON, 1, 2, 3, 6 OFF
nMeasuring range 350 mm to 750 mm: Code switch "position 4 ON, 1, 2, 3, 5, 6 OFF
nMeasuring range 750 mm to 1500 mm: Code switch "position 3 ON, 1, 2, 4, 5, 6 OFF
nMeasuring range 1500 mm to 2500 mm: Code switch "position 2 ON, 1, 3, 4, 5, 6 OFF
Lower measuring range
26
Attention
nIf Xis clearly smaller than %change the code switch according to the diagrams h,
iand jto adapt the setting to the fluid used in the installation.
Establishing active measuring range
A control range may be established within the measuring range of the electrode.
Establish the length of the control range using the code switch ", see Fig. 5, Fig. 11
XSelected control range (= active measuring range) in [mm]
%Max. measuring range at 25 °C
hDiagram for water, conductivity ≥20 μS/cm
iDiagram for water, conductivity ≥5 μS/cm
jDiagram for fuel oil EL, dielectric constant εr2.3
Fig. 11
37
X
%
ON
1 2 3456
"

18
Basic Settings – continued –
Establishing active measuring range – continued –
Ascertain the type of fluid to be monitored. Establish the active measuring range [mm] for your
application. Use diagrams h, ior jto determine the required code switch settings for water and
fuel oil EL.
Example: Max. measuring range at 25°C: 1500 mm, active measuring range: 1000 mm,
switch 3 of the code switch must be set to ON and all other switches to OFF.
If the fluid to be monitored is not water or fuel oil EL, the voltage must be measured in order to
determine the switch position. For this purpose switch on the mains switch of the associated level
switch NRR 2..., NRS 2... or NRT 2... .
1. Open the cover 6of the terminal box !.
2. Fill vessel until its max. liquid level is reached and then connect a voltmeter between the terminals
“1” (+) and “M” (–). Before starting the measurement set all switches of the code switch to OFF.
3. Now operate each individual switch in turn: first only 1 to ON, then only 2 to ON, then only 3 to ON,
then only 4 to ON, then 4 +5 to ON and then 4 + 5 + 6 to ON. As soon as with one of the switch
positions the value measured by the voltmeter exceeds 7 V, select the preceding switch position.
4. After having set the code switch, put cover 6onto the terminal box !and fix it by fastening the
screw 5.
2 ON3 ON
4 ON
7
6
5
4
3
2
1
0200 400 600 800 1000 1200 1400 1600 1800 2000
0
4+5 ON
Code switch
Example
AA A
A
BBBB
Active measuring range (control range) [mm]
Output voltage UM[V] DC
A= completely submerged
B= completely exposed
Fig. 12
hDiagram for water, conductivity ≥ 20 μS/cm

19
Basic Settings – continued –
Establishing active measuring range – continued –
7
6
5
4
3
2
1
0200 400 600 800 1000 1200 1400 1600 1800 2000
0
4 ON4+5 ON
4+5+6 ON
Code switch
AA
A
B
B
B
Active measuring range (control range) [mm]
Output voltage UM[V] DC
A= completely submerged
B= completely exposed
7
6
5
4
3
2
1
0200 400 600 800 1000 1200 1400 1600 1800 2000
0
2 ON3 ON
4 ON
4+5 ON
Code switch
AAA
A
BB B B
Active measuring range (control range) [mm]
Output voltage UM[V] DC
A= completely submerged
B= completely exposed
Fig. 13
i
Fig. 14
j
Diagram for water, conductivity ≥ 25 μS/cm
Diagram for fuel oil EL, dielectric constant εr2.3

20
Commissioning
1. Make sure that the system NRG 26-21 is wired according to the wiring diagram, Fig. 10.
2. Make sure that the mains voltage of the associated level switch agrees with the ratings on the name
plate.
Checking electrical connection
The supply voltage of the electrode can be measured between terminals “3” and “M” in the terminal
box !. The voltage should be 12 V d. c. If this voltage is not measured, the electrode has to be checked
at our works or by a works official.
The level-proportional voltage UMcan be measured between terminals “1” (+) and “M” (–).
Raise the liquid level in the vessel to the max. point of the control range (completely submerged), e. g.
1000 mm, and measure the voltage.
Compare the value measured with the value of the corresponding diagram (in chart h, UMfor
1000 mm is 4.6 V). The following values must be obtained in any case:
Level electrode completely exposed: UM≥ 0 V, level electrode completely submerged: UM≤ 7 V.
If the level electrode is submerged and UM= 0 V or UM> 7 V is measured, the level electrode has to be
checked in our service department.
Checking measuring voltages
Operation
Operation in steam and (pressurised) hot water plants in accordance with TRD 401, TRD 602, TRD
604, EN 12952; EN 12953 or other national regulations or according to the guidelines of classification
societies.
NRG 2621
Note
nShould malfunctions occur during the commissioning procedure refer to chapter
“Operational Malfunctions” on page 21 in order to analyse and correct them.
Basic Settings – continued –
nWhen the measuring points of the electrode are established when the equipment is
cold, the measuring points will shift as the temperature increases due to the thermal
expansion of the electrode rod. The setting must then be corrected.
Note
Table of contents
Popular Measuring Instrument manuals by other brands
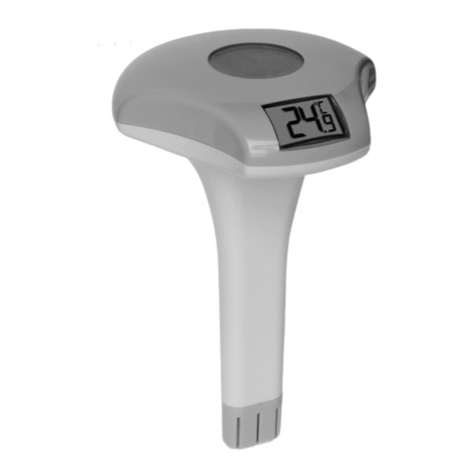
TFA
TFA 30.2033.20 instruction manual
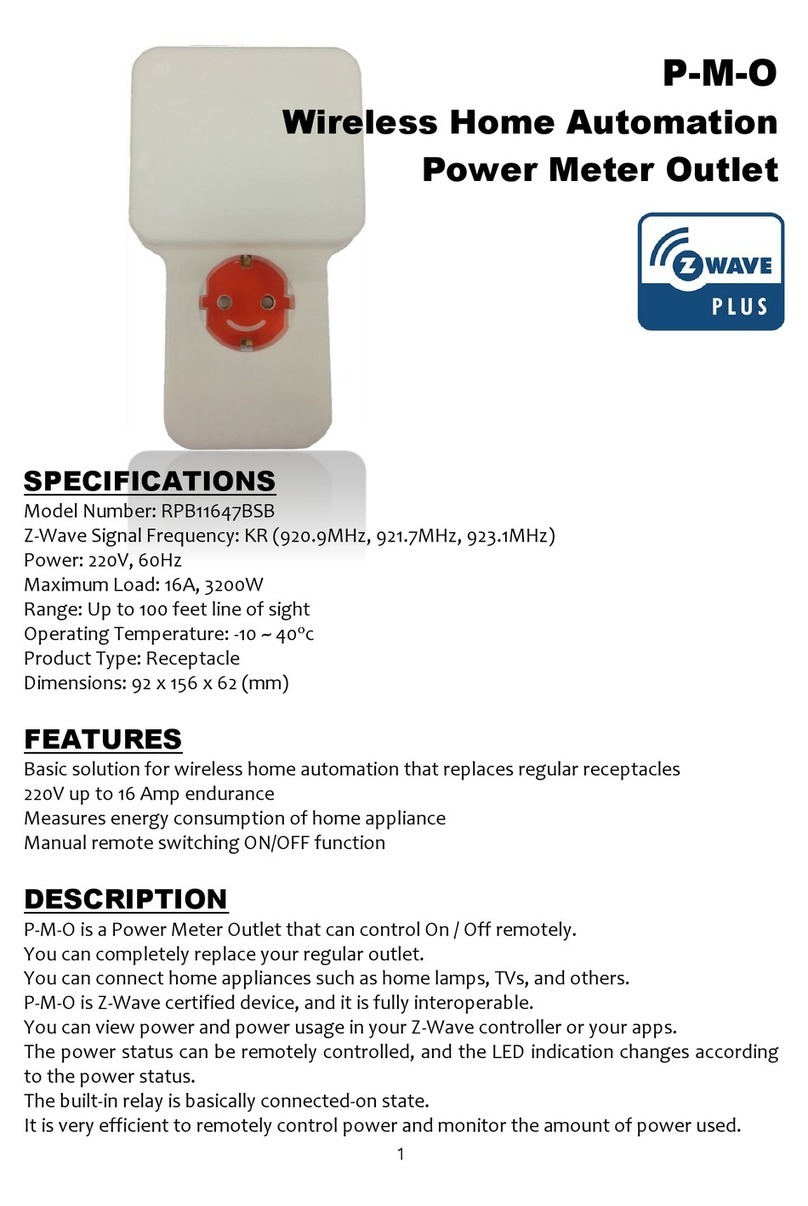
Z-Wave
Z-Wave RPB11647BSB user manual
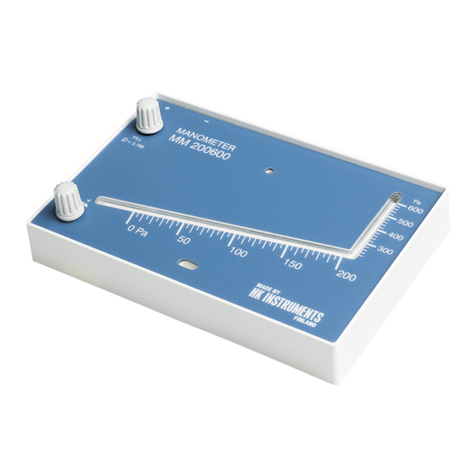
HK Instruments
HK Instruments MM Series installation instructions
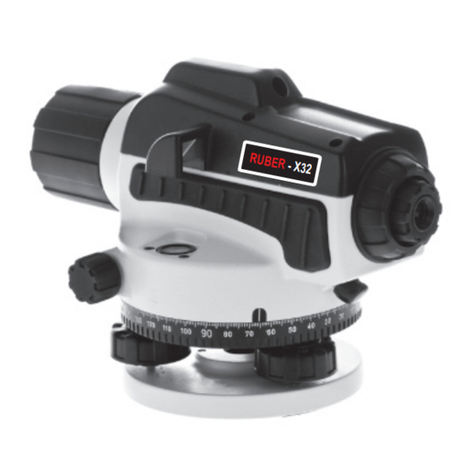
ADA INSTRUMENTS
ADA INSTRUMENTS Ruber-X32 operating manual
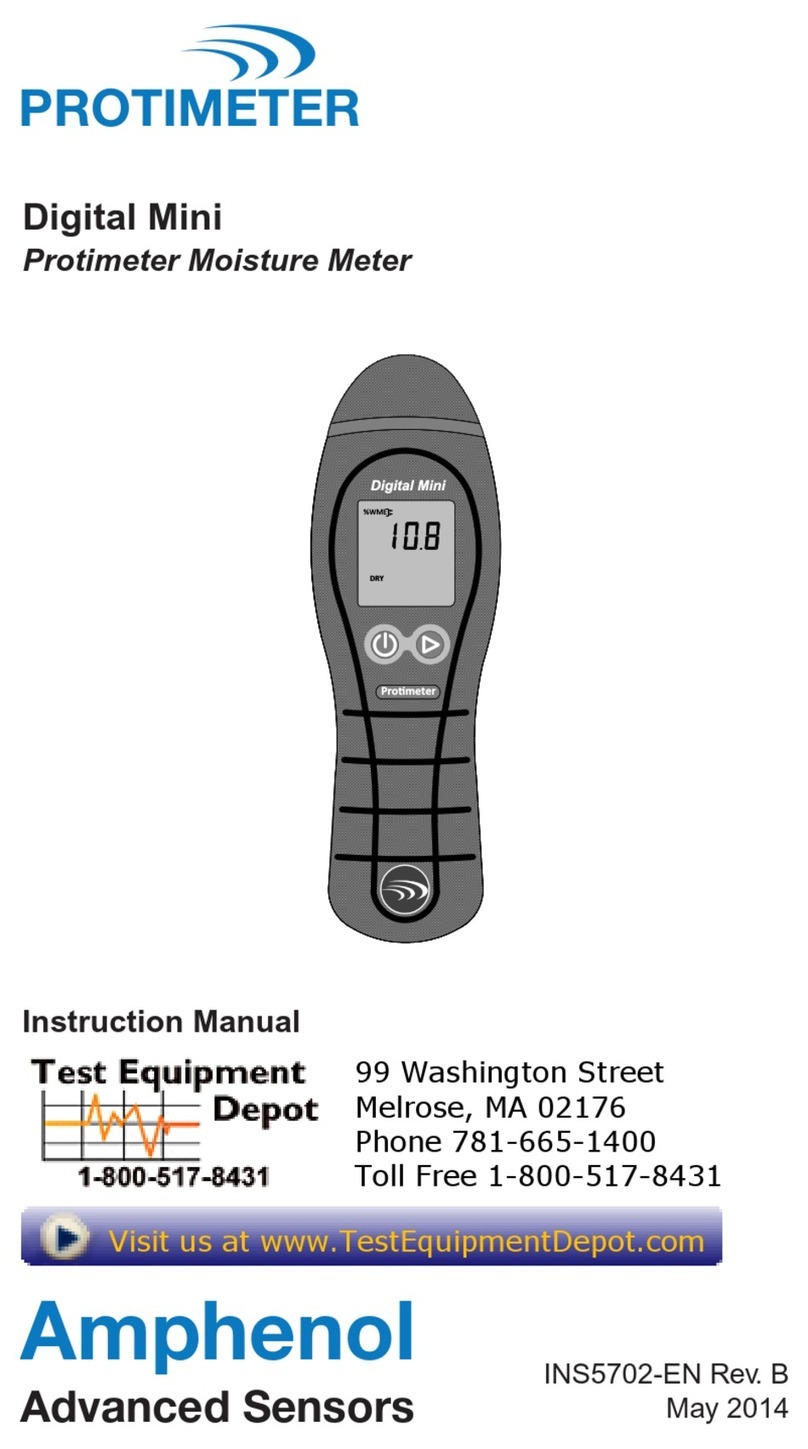
Protimeter
Protimeter Digital Mini BLD5702 instruction manual
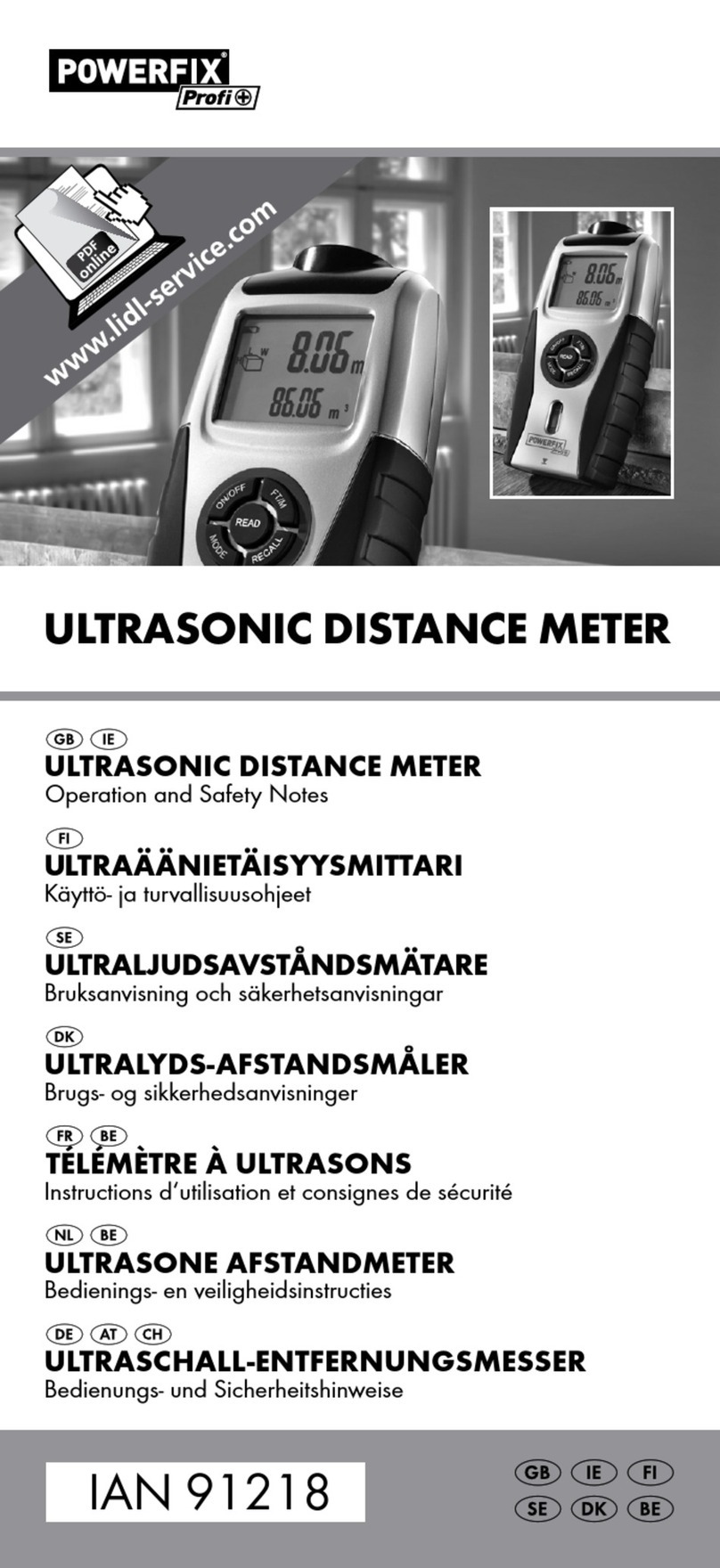
Powerfix Profi
Powerfix Profi 91218 Operation and safety notes